Conspec Controls CX Series Manual

6 Guttman Boulevard, Charleroi Industrial Park, Charleroi Pennsylvania 15022
(800) 487-8450; Fax: (724) 489-9772 Page 1 of 17 http://www.conspec-controls.com
Universal Transmitter
CX/CN Series
Operations
&
Maintenance
Manual

6 Guttman Boulevard, Charleroi Industrial Park, Charleroi Pennsylvania 15022
(800) 487-8450; Fax: (724) 489-9772 Page 2 of 17 http://www.conspec-controls.com
Warranty & Disclaimer Information
Due to Conspec Controls Inc.’s continuous effort to produce the highest quality monitoring
equipment possible, products described in this manual are subject to change at any time without
notice. While every effort has been made in preparing this manual to include all information
pertinent to the installation, maintenance, and calibration of the product, Conspec Controls Inc.
assumes no responsibility for errors, omissions, or any loss due to said errors or omissions.
A gas monitoring system alone cannot prevent hazardous conditions from occurring. The reliability
of a gas monitoring system, and the resultant safety level is dependent on, and the responsibility of
the user. The user’s responsibilities include, but are not limited to:
*Insuring that the correct equipment is specified for conditions at the particular site
*Following recommended installation and wiring guidelines
*Meeting all applicable safety and electrical codes
*Scheduling regular calibrations and servicing
*Replacing inoperative or questionable parts or units
WARRANTY
Conspec Controls Inc. provides warranty service for one (1) year from the shipping date on all
electronic and mechanical components. Sensor elements are considered a consumable part
subject to varying conditions which can affect their expected life. Sensor elements are covered
under warranty for a period of six (6) months. Damage to sensor elements due to overexposure of
the target gas, poisoning, or other factors beyond Conspec’s control are not covered under
warranty. Warranty service is limited to defects in materials and workmanship on units which fail
under normal use. Conspec will repair or replace any unit found to have failed due to defects in
materials or workmanship. This warranty is voided if the unit has been misused, damaged due to
incorrect wiring, or altered before return to the factory. Warranty claims that are denied will be
billed at the standard rate. Expedited shipping is not covered under warranty.
No other warranty is authorized other than the above.
Before returning a product for service, call Conspec Controls Inc. for a Return Authorization
Number (RA#) at (800) 487-8450. Returned units should be packaged securely as damages
incurred during shipping are not covered under warranty.

6 Guttman Boulevard, Charleroi Industrial Park, Charleroi Pennsylvania 15022
(800) 487-8450; Fax: (724) 489-9772 Page 3 of 17 http://www.conspec-controls.com
1.0 GENERAL DESCRIPTION
The Universal Gas Transmitter is a micro-controller based electronic sensor that accepts signals
delivered by several types of industry standard cells including Electrochemical, Catalytic Bead,
Infrared, Photo-Ionization & Thermal Conductivity to determine ambient levels of target gas. The
monitor can operate stand-alone, providing local display and alarm indication, or it can be
connected to a larger fixed point detection system by incorporating the 900773 MODBUS protocol
2W 485 communications trunk adapter board. Alternatively, a 4-20 mA current signal is provided
when the instrument is used as a remote sensor.
Alarm indicators are provided on the monitor. Normal condition will cause a green visual indicator to
blink once every two seconds. If the first level of alarm is exceeded, this indication will change to
one red blink every two seconds. When the second level of alarm is exceeded, the red visual
indicator will blink twice every two seconds. Available options include the 900773 Modbus - Alarm
Relay Board. The 900773 contains three SPDT relays that activate via the programmable alarm set
points. Optional self contained or remote audible and visual alarms can be connected with the
incorporation of the Relay Board. This also enables control devices to be activated during an alarm
condition. The monitor has a 2-line, 8-character alphanumeric Liquid Crystal Display that is used to
display status, readings, and prompts to the user. User configuration and status indication is
initiated via keypad entry. The standard keypad is a self-contained infrared encoder. The Universal
Transmitter is temperature compensated over its entire range of operation in software. The one-
person calibration feature is simple and adjustment free.
2.0 TECHNICAL DESCRIPTION
Control Voltage: 12-24 Volt DC, Approx. 100mA typical load
Analog Output: 4-20 mA current source standard
Operating Temperature: -20 to +50 degree Centigrade
Humidity: 10-95%, non-condensing
Accuracy: +/- 2% Full Scale
Repeatability: +/- 2% Full Scale
Stability: +/- 2% over 24-hour test, full temperature range

6 Guttman Boulevard, Charleroi Industrial Park, Charleroi Pennsylvania 15022
(800) 487-8450; Fax: (724) 489-9772 Page 4 of 17 http://www.conspec-controls.com
3.0 INSTALLATION INSTRUCTIONS
The Universal Transmitter is available in a NEMA 4X rated enclosure and a NEMA 7X rated
Explosion Proof enclosure for use in Classified Areas.
Locate a suitable location free of drips and drafts that allows the user to safely access the unit. The
Universal Transmitter shall be mounted so the detection head is pointing downward. Securely
mount the unit using industry approved methods and materials taking into account sound
mechanical and electrical practices.
It is the user’s responsibility to follow all applicable Federal, State, Local Building and
Electrical Codes including NEC Guide Lines.
The Universal Transmitter Card is powered via a 3-conductor 18-22AWG shielded cable.
Power to the Universal Transmitter should be isolated from process power. The use of an isolated
power supply (Clean Power) is strongly recommended when the Universal Transmitter is part of a
personnel safety system. In most cases, building and electrical codes require the use of Conduit to
protect electrical wiring and prevent tampering. Conspec recommends electrical wiring to the
Universal Transmitter is placed in conduit.
The wiring diagram on the next page details the connection of V+, GND, and SIG on the terminal
labeled J2.

6 Guttman Boulevard, Charleroi Industrial Park, Charleroi Pennsylvania 15022
(800) 487-8450; Fax: (724) 489-9772 Page 5 of 17 http://www.conspec-controls.com
Transmitter Wiring Diagrams:
Standard Transmitter Wiring Optional CDMA Silo Insertion Wiring
PN#
900739-12/24
12/24 VDC
1st Alarm N/O
1st Alarm Common
1st Alarm N/C
2nd Alarm N/O
2nd Alarm Common
2nd Alarm N/C
Sensor Fail N/O
Sensor Fail Common
Sensor Fail N/C
24V D C to J1 on 900739
A larm 1 to J4 N /C * on 900739
A larm 2 to J7 N /C * on 900739
P 16 43-2 T erm ina l
*N ote: W iring is in a failsafe
configuration. N /C held o pen
during norm al opera tio n and
closes when ala rm e d o r du ring
pow er lo ss *
900739-12/24V Relay Adapter Board 900739 Connection to Optional P1643-xx
(3) SPDTRated .5A @ 120VAC, 60W Remote Audio/Visual Alarm.
J2
1
J1
1
12-24 VDC
Ground
4-20mA Process Loop Signal
To Sensor
J2
1
J1
1
Dust Guard
Sensor Element
Silo Adapter Plate
Rigid Conduit Extension
XP Junction Box
4-20mA Process Loop Signal
Ground
12-24 VDC
900744- 100-240VAC/ +24V /.23A

6 Guttman Boulevard, Charleroi Industrial Park, Charleroi Pennsylvania 15022
(800) 487-8450; Fax: (724) 489-9772 Page 6 of 17 http://www.conspec-controls.com
4.0 MODBUS OVERVIEW
The Conspec 900745 communication board allows interconnection of a Universal Remote Sensor or
Combustible Remote Sensor to a standard 2-wire, RS-485, ModBus communication system. The UT
communicates ModBus RS485 via 2 wire, twisted-pair connection (18-22 AWG shielded)
900745 2W ModBus 485 Communications Board
Data Line Connections:
CONNECTOR
EIA/TIA 485 NAME
DESCRIPTION
J1-1
B -
Transceiver Terminal 1
J1-2
A +
Transceiver Terminal 2
Status LEDs:
D1…...…….Power (Green). Turns ON steady following a proper power initialization cycle.
D2…………Communication Fault (Red). Flashes once during power initialization cycle. Flashes again
each time a communication error occurs with the Universal Remote Sensor microprocessor.
D3…………Data Receive Indicator RX (Yellow). Illuminates when data is present on RS-485
communication bus, indicating the Master or another Slave is talking.
D4…………Data Transmit Indicator TX (Yellow). Illuminates when a response is being sent from this
Slave to the Master.

6 Guttman Boulevard, Charleroi Industrial Park, Charleroi Pennsylvania 15022
(800) 487-8450; Fax: (724) 489-9772 Page 7 of 17 http://www.conspec-controls.com
4.5 Optional Modbus / Relay Card
The Conspec 900773-24 (24V version, 900773-12 (12V) custom order) ModBus Relay Card (optional) is a
communication board with three relay outputs (1st Alarm, 2nd Alarm, Sensor Fail) in addition to allowing
interconnection to a standard 2-wire, RS-485, ModBus communication system. The UT communicates
ModBus RS485 via 2 wire, twisted-pair connection (18-22 AWG shielded)
ModBus / Relay Card Status LEDs
Status LEDs are visible on the ModBus Relay Board and are for troubleshooting purposes. They are as
follows: Power, Fault, RX, and TX. Power indicates unit is operational and has supply power going to it. Fault
indicates some type of communications or ModBus card fault. The RX and TX are ModBus communication
indicators will flash in accordance with communication received or sent.

6 Guttman Boulevard, Charleroi Industrial Park, Charleroi Pennsylvania 15022
(800) 487-8450; Fax: (724) 489-9772 Page 8 of 17 http://www.conspec-controls.com
Communication Settings:
Trunk Address, Parity, and Baud are read from the 900732 Universal Remote Sensor (URS) during power-
on initialization. These parameters are entered into the URS via the Command Code 130 entry method
found on page 8. Following parameter modification, a power cycle must take place for the new settings
to take effect. Default values are address = 1, parity = even, baud = 4800.
Parameter
Value
Trunk Address
1 –247
Parity
0 - None
1 - Even
2 –Odd
Baud
0 - 1200
1 - 4800
2 –9600
3 - 19200
5.0 911118 INFRARED KEYPAD ENCODER
The Universal Transmitter Card is configured using the 911118 Infrared Keypad Encoder (not
included). Command Codes consist of a number followed by the “ENTER” key labeled ‘E’. Entries
can be cleared by pressing the “CLEAR” key labeled ‘C’.
Keys ‘1’ and ‘2’ can also be used to increment/decrement by
a value of 1.
The 91118 Infrared Keypad Encoder uses (3) three ‘N’ size
1.5V batteries. Remove (2) two Phillips head screws on rear
of the encoder to replace.
911118 Infrared Keypad Encoder (not included)

6 Guttman Boulevard, Charleroi Industrial Park, Charleroi Pennsylvania 15022
(800) 487-8450; Fax: (724) 489-9772 Page 9 of 17 http://www.conspec-controls.com
6.0 COMMAND CODES
25 Unlock Monitor
Enter Command Code 25 to unlock the monitor. A prompt will be displayed requesting entry of the
User Password. The User Password is factory pre-programmed to “1”. When the User Password
is entered, the monitor will go into unlocked condition for a 15-minute period. In the unlocked
condition, instrument settings can be modified.
100 Programmable Parameters
View when locked. View and modify when unlocked.
Gas Type: Selects target gas and range.*
Decimals: Selects the number of digits represented in fractional form.*
Range: Selects range for 20 mA output signal.*
Span: Selects span calibration gas concentration.*
111 Gas Sensor Calibration
Enter Command Code 111 while the monitor is un-locked to activate the gas sensor calibration
routine. The Calibration routine is detailed on page 10.
120 Alarm Parameters
View when locked. View and modify when unlocked.
AL1-L: Alarm Level 1 low limit
AL1-H: Alarm Level 1 high limit
AL2-L: Alarm Level 2 low limit
AL2-H: Alarm Level 2 high limit
On Delay: Delay, in seconds, to onset of alarm condition
Off Delay 1: Delay, in seconds, required to reset alarm relay 1
Off Delay 2: Delay, in seconds, required to reset alarm relay 2
Alarm Type: 8-bit binary word used to define output relay alarm modes (See Page 8)
Sensor Fail Level: Sets limit of live concentration excursion beyond zero and range that defines
sensor fail
*Factory Programmed Value-User will not typically need to modify –Could render unable to detect faults with sensor
head

6 Guttman Boulevard, Charleroi Industrial Park, Charleroi Pennsylvania 15022
(800) 487-8450; Fax: (724) 489-9772 Page 10 of 17 http://www.conspec-controls.com
Command Code 120 contains a “Out Type” option that allows the operator to select how the
Transmitter will detect an alarm condition. The value entered will determine if the alarm outputs will
operate failsafe or non-failsafe. The value will also determine the manner in which the alarm outputs
will activate. The list below describes the operation and magnitude of bits 0-7.
Level 1 is always defined as being between 0.0 and AL1. Level 2 is always defined as being between
AL1 and AL2. Level 3 is always defined as being between AL2 and Max Range.
Bit 7* - Controls sensor fail relay fail safe. If you want the sensor fail relay output to be fail safe, set this bit to
a 1. If not, clear it to a 0. This bit has magnitude = 128.
Bit 6* - Controls relay output fail safe. If you want the alarm relay outputs to be fail safe, set this bit to a 1. If
you do not want fail safe mode on the alarm relay outputs, clear this bit to a 0. This bit has magnitude = 64.
Bit 5 - Relay 2 Active Level 3 control. If you want level 3 to activate relay 2, set this bit. If not, clear it.
Magnitude = 32.
Bit 4 - Relay 2 Active Level 2 control. If you want level 2 to activate relay 2, set this bit. If not, clear it.
Magnitude = 16.
Bit 3 - Relay 2 Active Level 1 control. If you want level 1 to activate relay 2, set this bit. If not, clear it.
Magnitude = 8.
Bit 2 - Relay 1 Active Level 3 control. If you want level 3 to activate relay 1, set this bit. If not, clear it.
Magnitude = 4.
Bit 1 - Relay 1 Active Level 2 control. If you want level 2 to activate relay 1, set this bit. If not, clear it.
Magnitude = 2.
Bit 0 - Relay 1 Active Level 1 control. If you want level 1 to activate relay 1, set this bit. If not, clear it.
Magnitude = 1.
Factory default for most monitors is 38. Bits 5, 2, and 1 are set for normal output operation. 32 + 4 + 2 = 38
*Previous manuals incorrectly state Bit 6 as sensor fail relay fail safe and Bit 7 as relay output fail safe.
130 Communication Parameters**
View when locked. View and modify when unlocked.
Address: ModBus slave address. Valid range: 1 - 247. Default = 1.
Parity: Selects ModBus communication parity. Default = 1
0 = none
1 = even
2 = odd
Baud: Selects ModBus communication baud. Default = 1.
0 = 1200
1 = 4800
2 = 9600
3 = 19,200
Contrast: Controls contrast of LCD display. Valid range: 0 - 60. Default = 4.
**Applies to Modbus Ready monitors only.

6 Guttman Boulevard, Charleroi Industrial Park, Charleroi Pennsylvania 15022
(800) 487-8450; Fax: (724) 489-9772 Page 11 of 17 http://www.conspec-controls.com
150 Signal Current Calibration*
Enter Command Code 150 while the monitor is un-locked to calibrate signal output current and
display contrast.
Each displayed parameter can be adjusted up or down by one incremental value per key stroke.
The ‘1’ key decreases value, while the ‘2’ key increases the value within operational limits.
170 Change User Password
Enter Command Code 170 while the monitor is un-locked to change User Password. The user
password is factory preset to “1”. The display will request entry of a new User Password. The new
password needs to be entered twice before being accepted. The password can be any number
from 1 to 9999.
200 Informational Screens
Enter Command Code 200 to display informational screens. The code version, input voltage,
ambient temperature, slope, and live signal values will be displayed one at a time. This information
is often useful during performance checks and troubleshooting following installation.
201 Informational Screens
Routine displays gas monitor type and sensor
*Factory Programmed Value-User will not typically need to modify

6 Guttman Boulevard, Charleroi Industrial Park, Charleroi Pennsylvania 15022
(800) 487-8450; Fax: (724) 489-9772 Page 12 of 17 http://www.conspec-controls.com
7.0 GAS CALIBRATION PROCEDURE
1. Unlock the monitor using Command Code 25 and the User Password factory preset to
“1”.
2. Initiate calibration by entering Command Code 111. The display will request zero gas
be applied to the sensor head. The LED status indicator will turn on green
continuously.
3. Apply zero gas to the sensor head using the calibration adapter (Conspec Part #
P3013-xx), tubing, and proper gas cylinder (Conspec PN# P1880-xx)
The display will indicate the raw decimal value of the sensor’s output.
4. When the raw value on the display has stabilized, press ENTER to accept. This
should take approximately 2-4 minutes. Remove the zero gas after the value has
been accepted.
5. The display will request span gas be applied to the sensor head. The LED status
indicator will turn red continuously. When the raw value has stabilized, press ENTER
to accept. This should take approximately 2 –4 minutes.
If the new calibration information is accepted, “Calibration Done” will be displayed for 30-60
seconds to allow the sensor to recover and prevent any alarms from tripping. The monitor will then
return to normal operation. To speed the recovery of the sensor it is recommended to remove the
calibration adapter immediately following calibration.
If the calibration information is not accepted “Calibra. Error” will be displayed. The pre-existing
calibration data will be reused at this point to help prevent an invalid calibration. Two common
reasons the calibration may be rejected are:
(1) Entering the data before the sensor has fully reacted to the target gas or:
(2) The sensor has passed its expected life and can no longer produce a signal within the
acceptable calibration limits. The sensor element is in most cases a consumable part that
periodically requires replacement. See page 13 for sensor replacement instructions.
Calibration gases, accessories, & kits can be purchased from Conspec for all
available gas detection transmitters and monitors supplied by Conspec.

6 Guttman Boulevard, Charleroi Industrial Park, Charleroi Pennsylvania 15022
(800) 487-8450; Fax: (724) 489-9772 Page 13 of 17 http://www.conspec-controls.com
8.0 SIGNAL CURRENT CALIBRATION
This feature allows the user to calibrate the 4-20mA Analog Output Signal. A Multi-Meter can be
connected in series with the SIG (signal) wire to the controller.
1. Unlock the monitor using Command Code 25 and the User Password factory preset to
“1”.
2. Initiate calibration by entering Command Code 150. The unit will display the Raw Analog
Zero Count
3. Use Key number “1” to decrease or “2” to increase the Raw Zero Count.
4. When the Multi-Meter reads 4.0mA, the user may press Enter to confirm
5. The monitor then prompts 20mA and displays the Raw Count.
6. Adjust the Raw Count with keys “1” & “2” until the Multi-Meter displays 20mA. Press the
Enter key to confirm.
The typical Raw Count for 4mA should be approximately 190, and 950 for the 20mA.
9.0 GAS LEVEL INDICATORS
Sensor Failure:
The Universal Transmitter Card is designed to detect failures in the sensor cell and
electrical connections. If the cell’s output is diminished the signal voltage will be
driven outside the limits for normal operation. This will be detected and constitute a
sensor failure.
The monitor will go into Temperature Error if ambient temperature falls outside the
range –20 to +50 degree C.
LED Status Indication:
Normal Mode: One short green flash, 2-second interval
Alarm Level 1: One short red flash, 2-second interval
Alarm Level 2: Two short red flashes, 2-second interval
Sensor Fail: Alternating red-green, 1-second interval
Calibration Span: Constant red
Calibration Zero: Constant green
Output Signal Current:
Normal Mode: 4.0 to 20.0 mA, linearly proportional from zero to full scale range
Sensor Fail: 2.0 mA
Temperature Error: 4.0 to 20.0 mA, linearly proportional from zero to full scale range
Start Up: 4.0 mA
Calibration Mode: Holds last translated output signal level until calibration completion.

6 Guttman Boulevard, Charleroi Industrial Park, Charleroi Pennsylvania 15022
(800) 487-8450; Fax: (724) 489-9772 Page 14 of 17 http://www.conspec-controls.com
10.0 MAINTENANCE & REPAIR GUIDELINES, REPLACEMENT PARTS
1. Maintenance: This Gas Detection Monitor requires evaluation every thirty (30) days to ensure
accuracy. The Monitor should be checked for accuracy by applying a known concentration of the
target gas that exceeds the programmed alarm levels. The displayed gas value will stabilize as the
gas fills the calibration chamber within the sensor head. When the programmed alarm levels are
breached, the alarm output for that level would be activated subsequently to the programmed alarm
delay duration. The displayed target gas value should match that of the concentration of test gas.
Any warning or control devices connected to the alarm outputs should remain connected during this
test to ensure proper operation of the entire gas detection system. Replace any inoperative or
questionable parts immediately. This gas detection monitor requires calibration every ninety (90)
days to ensure accuracy and to correct sensor drift. The gas detection “cell” located within the sensor
housing is in most cases, a consumable part with an expected life. The cell’s output decreases slowly
as it nears the end of its expected life. The rate at which the output decreases depends greatly on the
concentration and presence of target gas. This must be corrected by calibrating the monitor often to
ensure an accurate reading and dependable alarming and control of connected devices. Conspec
recommends that no modifications be made to this monitor without first consulting Conspec
Technical Services. Modifying this equipment without consulting the factory could result in unsafe
operation and/or unsafe atmospheric conditions. Modifying this equipment will void any warranty
authorized by Conspec Controls Inc.
2. Repair: Any monitor found to be defective or questionable should be returned to Conspec Controls
for evaluation and repair. Conspec requires any returned equipment to first be issued a Return
Authorization Number (R.A.#) by calling Conspec at (800) 487-8450 Mon.-Fri. 8am-5pm est.
Conspec also offers on-site Repair and Start-up service for Conspec Gas Detection Equipment.
3. Replacement Parts: Damaged or questionable parts should be replaced immediately upon
detection. Damaged or inoperative parts could contribute to hazardous and/or unsafe conditions. Any
consumable parts should be replaced if the reliability is questionable or within the part’s specific
expected life. Consumable parts include any filters, pump motors, sensors….etc.
Questions / Technical Support……….(800) 487-8450 Mon-Fri 8am-5pm est
Conspec Sales…………………………...(800) 487-8450 Mon-Fri 8am-5pm est
Fax………………………………………….(724) 489-9772
E-mail………………………………….……sales.usa@conspec-controls.com
Web site……………………………………www.conspec-controls.com

6 Guttman Boulevard, Charleroi Industrial Park, Charleroi Pennsylvania 15022
(800) 487-8450; Fax: (724) 489-9772 Page 15 of 17 http://www.conspec-controls.com
11.0 SENSOR REPLACEMENT
The sensor element on the CX/CN series transmitters is replaceable. No user serviceable parts are present
inside the sensor housing. Sensor elements can be ordered from Conspec Controls. To replace the sensor,
first disconnect power to the unit. It is normal for the monitor to display “Sensor Fail” after a new sensor has
been installed. To correct this message, the new sensor will require calibration.
Sensor Replacement:
NEMA 4X CN SERIES
The NEMA 4X CN Series sensor housing is opened by pulling downward and twisting sensor housing part B
until released from the compression seal on part A.
The replaceable cell can be removed by unplugging the cell from the cell holder card.
Plug the new cell into the cell holder card and replace sensor housing part B.

6 Guttman Boulevard, Charleroi Industrial Park, Charleroi Pennsylvania 15022
(800) 487-8450; Fax: (724) 489-9772 Page 16 of 17 http://www.conspec-controls.com
HAZARDOUS/CLASSIFIED AREA CX SERIES
*WARNING: Remove power or declassify area before opening the sensor housing.
The Hazardous/Classified Area CX Series sensor housing is opened by loosening the Allen screw and
unthreading sensor housing part B from part A.
The replaceable cell can be removed by unplugging the cell from the cell holder card.
Plug the new cell into the cell holder card and rethread sensor housing part B then retighten the Allen screw.
Contaminant/Small particulates Effects:
Dust, coal fines, and rust are all small particulates that are encountered often within industrial environments.
If preventative measures are not taken, these contaminants will likely block the flow of target gas into the
sensor chamber. Once blocked, it can be nearly impossible to clean some sensor housings, and the housing
may need to be entirely replaced. Preventive measures should be taken to avoid the sintered metal filter
from becoming clogged. Available options include PTFE Hydrophobic disc filters to prevent moisture, rust
and build up of small particulates.

6 Guttman Boulevard, Charleroi Industrial Park, Charleroi Pennsylvania 15022
(800) 487-8450; Fax: (724) 489-9772 Page 17 of 17 http://www.conspec-controls.com
Replacement Parts Notes:
This manual suits for next models
1
Table of contents
Popular Transmitter manuals by other brands

BWI Eagle
BWI Eagle AIR-EAGLE FM2 43-1000N4W-120VAC Product information bulletin
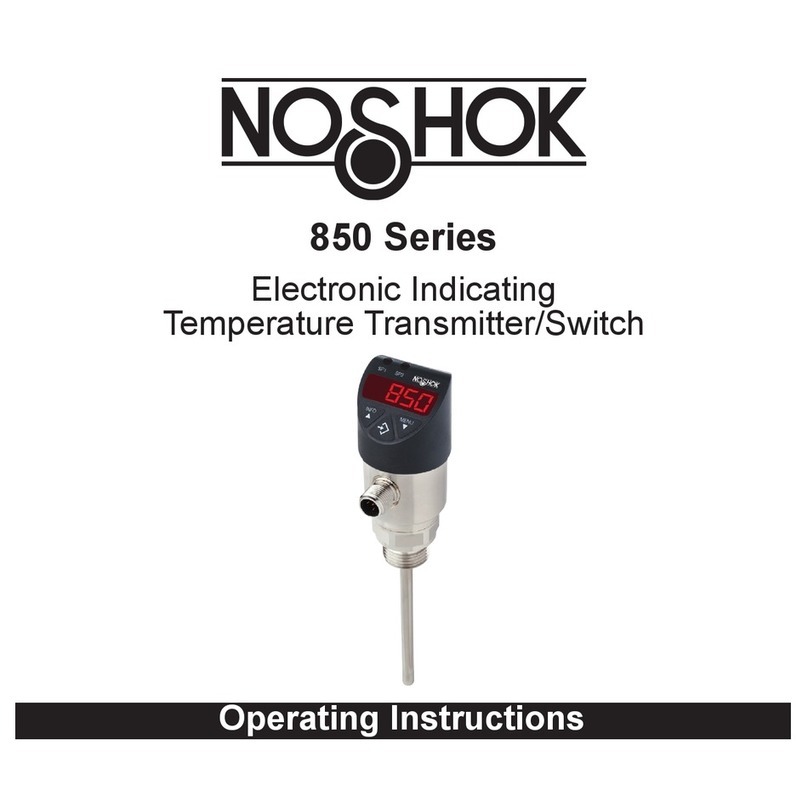
NOSHOK
NOSHOK 850 Series operating instructions

Emerson
Emerson Rosemount 2051L quick start guide
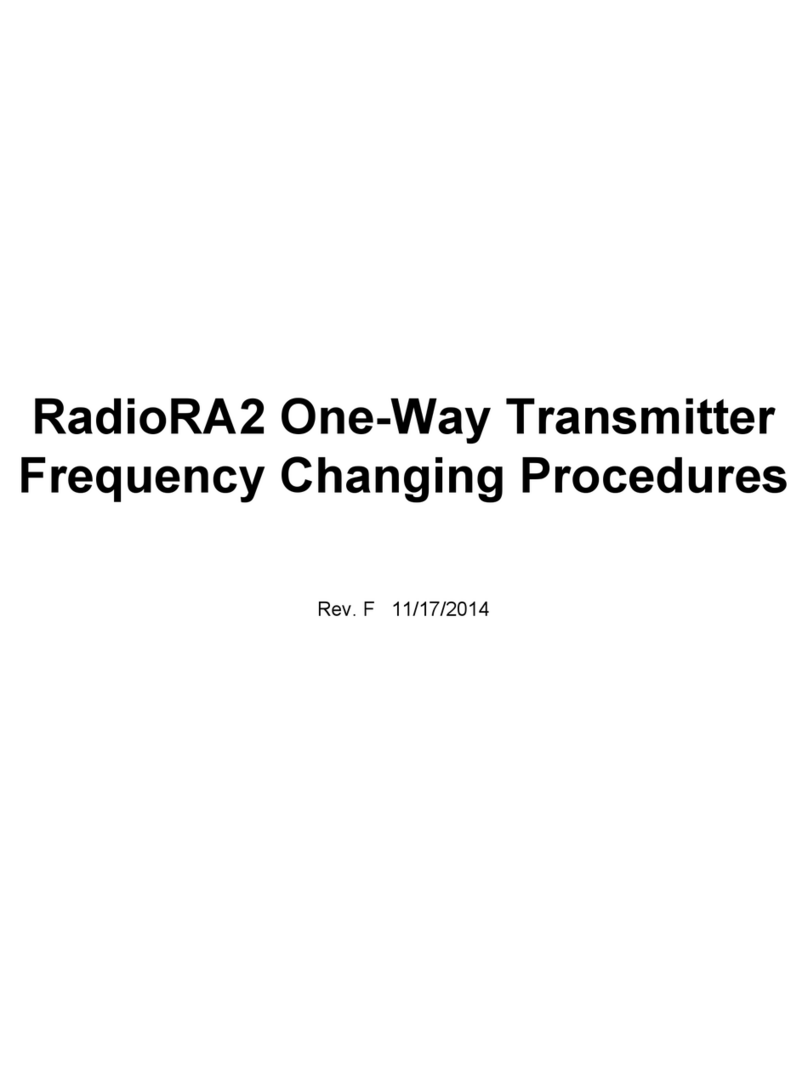
Lutron Electronics
Lutron Electronics RadioRA2 RRD-H1RLD instructions
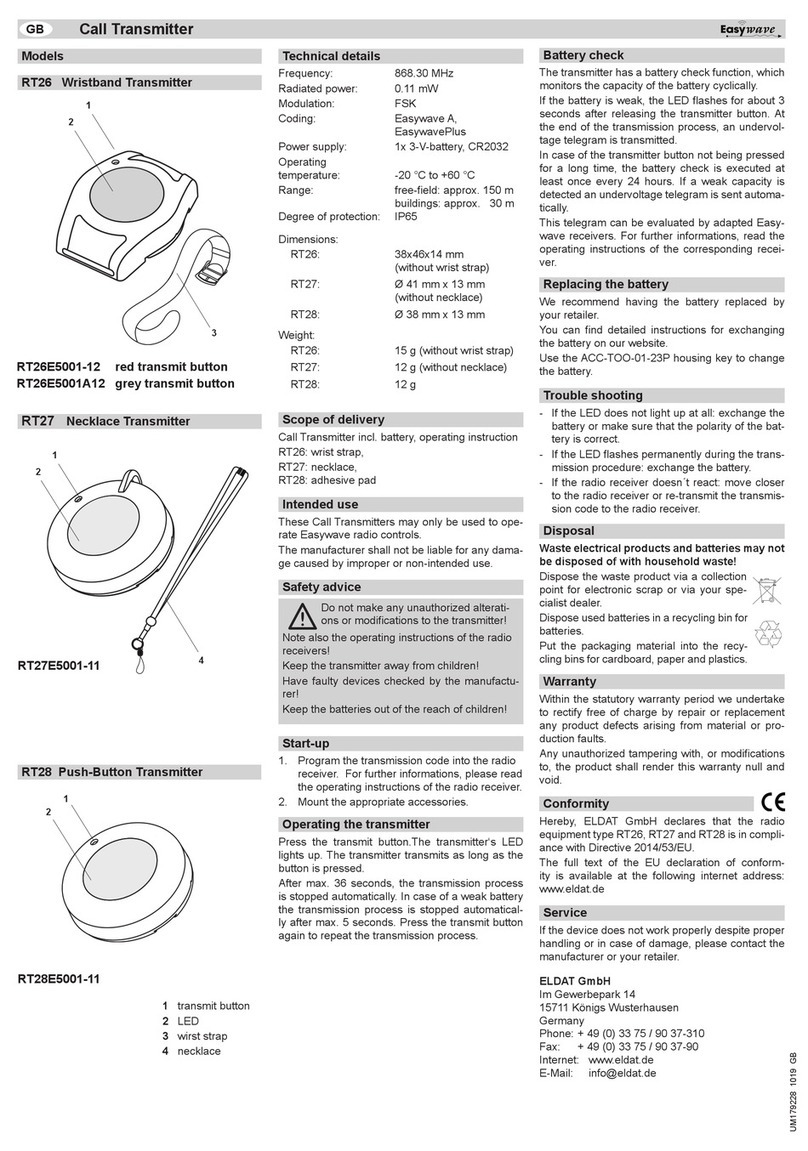
Easy wave
Easy wave RT26 quick start guide
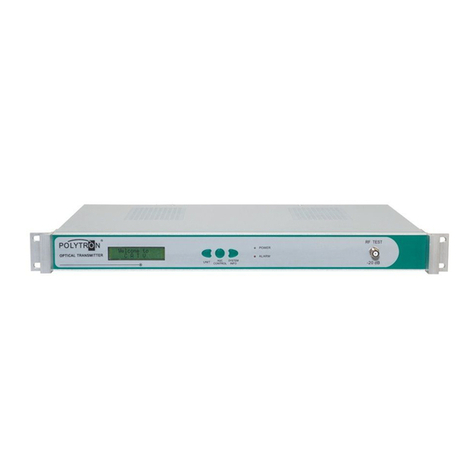
Polytron
Polytron OT 104 DFB operating manual