Controls J1939 iT4 User manual

Product Manual
Engine Display & Control Panel
J1939iT4Engines
Part Number: C4F-100
Revision: 1.1
______________________________________________________________________________________________________________________________________
Copyright Controls, Inc.
P.O. Box 368 • Sharon Center, OH 44274
Phone 330.239.4345 • Fax 330.239.2845 • www.controlsinc.com

CONTROLS, INCORPORATED
C O N T R O L S Y S T E M S & S O L U T I O N S
- 1 -
TABLE OF CONTENTS
CONTROL PANEL SETTINGS…….………………………………………………………………………….…….……….…………...2
PRIOR TO STARTING ENGINE
MANUAL OPERATION SETTINGS OVERVIEW
OPERATION SETTINGS………....………………………………………….………………………………………………………….....4
MANUAL OPERATION SPECIFICS
MODULE CONNECTORS……………………………………………………………………………………………………………………….5
ENGINE ALARMS, CODES AND MESSAGES………………………………………………………………….………......…...7
ENGINE ECU ALARMS/DE-RATE/SHUT DOWNS
PANEL ALARM ANNUNCIATION AND CODE READER
PANEL INDICATION LAMPS
ACTIVE AND STORED ENGINE ECU CODES
CONTROL PANEL SPECIFIC ALARMS AND SHUT DOWNS………………………………………….…………….9
CONTROL PANEL SPECIFIC SAFETY ALARMS
CONTROL PANEL ANALOG AND DIGITAL INPUTS…………………………………………………………..………….10
CONTROL PANEL RELAY OUTPUTS…………………………………………………………………..……………………….....…13
MENU SYSTEM……………………………………………………………………………………………..…………………………………….……15
MENU ACCESS, EXIT AND NAVIGATION
MENUS TO VIEW INFORMATION
MENUS TO CONFIGURE MODULE SETTINGS
EMISSIONS MONITORING…………………………………………………………………………………………………….……………….22
EMISSIONS INFORMATION
REGENERATION
STANDARD REGENERATION
SERVICE LEVEL REGENERATION
REGEN INHIBIT

CONTROLS, INCORPORATED
C O N T R O L S Y S T E M S & S O L U T I O N S
- 2 -
MODULE OPERATION
The modules are designed to be integrated into a panel that assumes a traditional key switch is
used. We recommend and can supply a 95060-23 key switch. Contact CI for purchasing. For the
purposes of explanation, the module is assumed to be powered through the Ignition position of the
key during Manual run operation and through the Accessory position during the Automatic
operations.
PRIOR TO STARTING ENGINE
Prior to starting the engine, select the required START/STOP and THROTTLE settings.
Reference the tables below to determine the appropriate operating modes. Details on each setting
are provided on the following pages.
CONTROL PANEL SETTINGS
Prior to starting the engine, select the proper throttle control mode and parameters required
for application.
Start/Stop Engine Engine Throttle Backup Floats
Method ON OFF Type Throttle Operation Available
Manual Key to Start Key to Off Vernier Manual UP/DOWN between selected min and max speeds -
Manual Key to Start Key to Off Multistate Select up to four separate operating speeds -
Start/Stop Engine Engine Throttle Backup Floats
Method ON OFF Type Throttle Operation Available
Floats Floats Close Floats Open Single Speed Single operating speed with warm up and cool down -
Floats Floats Close Floats Open Linear Engine speed adjusted between selected min and max speeds -
Floats Floats Close Floats Open Target Engine speed adjusted to maintain selected level or pressure -
Pressure On Pressure Off Pressure Single Speed Single operating speed with warm up and cool down Yes
Pressure On Pressure Off Pressure Linear Engine speed adjusted between selected min and max speeds Yes
Pressure On Pressure Off Pressure Target Engine speed adjusted to maintain selected pressure level Yes
Level On Level Off Level Single Speed Single operating speed with warm up and cool down Yes
Level On Level Off Level Linear Engine speed adjusted between selected min and max speeds Yes
Level On Level Off Level Target Engine speed adjusted to maintain selected level Yes
Auto Operation Options
Manual Operation Options
MANUAL OPERATION
1) Engine Start/Stop –Turn key to run position manually
2) Engine Throttle –Push up and down buttons

CONTROLS, INCORPORATED
C O N T R O L S Y S T E M S & S O L U T I O N S
- 3 -
Manual Operation Settings
The following bolded settings are required for manual (and automatic) operation in the Throttle
Configuration menu.
Throttle Configuration
Throttle Type - Throttle Type Selection (Default = Vernier)
E-Throttle Mode Selection
TSC Mode Selection
TSC Min Speed Selection (Default = 800 rpm)
TSC Max Speed Selection (Default = 2400 rpm)
TSC Ramp Rate Selection (Default = 100 rpm/sec)
Throttle Curve Selection
Multistate Speed 1 Selection
Multistate Speed 2 Selection
Multistate Speed 3 Selection
Multistate Speed 4 Selection
PWM Min Duty Cycle % Selection
PWM Max Duty Cycle % Selection
Manual Throttle Options
1) Vernier Throttle (Default)
Vernierthrottle is standard up and down throttle between the minimum and maximum
selections. The ramp rate is the rate of acceleration in rpm’s per second. The control panel
uses J1939 throttle, also called “torque speed control” or TSC1.
2) Multistate Throttle
Multistate throttle provides for one, two, three orfour specific operatingspeeds. Pressing the up
and down buttons adjusts engine speed between the selected multistate speed selections.
3) PWM Throttle
Pulse width modulation throttle is availablefor engines requiring this type of throttle
configuration.

CONTROLS, INCORPORATED
C O N T R O L S Y S T E M S & S O L U T I O N S
- 4 -
OPERATION SETTINGS
Manual Throttle Control
With the keyin the RUN position, the panel operates manually by pressing the up and down
buttons. An arrow will indicate increasing or decreasing engine speed.
1) Manual Operation –Standard Up / Down Throttle
Throttle Configuration Settings –Standard Throttle
Heading
Default
Range
Units
Your Settings
Min Control Speed
650
650-2750
RPM
Max Control Speed
2750
650-2750
RPM
2) Manual Operation –Multistate Throttle
Throttle Configuration Settings –Multistate Throttle
Heading
Default
Range
Units
Your Settings
Manual Throttle Operation
Multistate
Multistate
3
1-3
Speeds
Speed 1
650
650-2750
RPM
Speed 2
650
650-2750
RPM
Speed 3
650
650-2750
RPM
Multistate Speeds –Programmed speed settings must be in an increasing order. For
example, Speed 1 = 1000, Speed 2 = 1400, Speed 3 = 1500.
Up Arrow
Increase
Speed
Decrease
Speed

CONTROLS, INCORPORATED
C O N T R O L S Y S T E M S & S O L U T I O N S
- 5 -
MODULE CONNECTORS
Secondary Connector
23 Pin
Primary Connector
14 Pin

CONTROLS, INCORPORATED
C O N T R O L S Y S T E M S & S O L U T I O N S
- 6 -
Primary Connector (14 Pin)
Pin
Function
Pin
Function
1
Relay #2 -ECU Signal
8
J1939 Low
2
Relay #1 NO
9
Relay #3 Common
3
Relay #3 NO
10
Not Used
4
Relay #2 & #4 Common
11
Battery Positive
5
Relay #4 NO
12
Battery Negative
6
Relay #1 Common
13
Analog #1 Input
7
J1939 High
14
Digital #1 Input
Secondary Connector (23 Pin)
NOT AVALAILABLE ON THID MODEL
CAUTION:
Maximum current draw for signal circuits is 5 amps

CONTROLS, INCORPORATED
C O N T R O L S Y S T E M S & S O L U T I O N S
- 7 -
ENGINE ALARMS, CODES AND MESSAGES
Engine ECU Alarm/De-Rate/Shut Downs
It is important to understand panel operation with respect to engine safety protections, alarms, and
fault codes. The panel operateswith J1939 engines. These engines have an ECU (engine control
unit) which is essentially a computer that runs the engine. When engine parameters are out of
normal operating ranges, the ECU takes specific actions which can include the following:
1) Broadcast a trouble code
2) Broadcast a red or yellow lamp
3) De-rate the engine
4) Shut down the engine
5) Turn on alarm horn
It is the engine ECU that de-rates or shuts down the engine when it is not operating within normal
parameters. Thisincludes more common shut downs like high engine temperature and low oil
pressure but can encompass a large range of parameters depending on the ECU.
Panel Alarm Annunciation and Code Reader
This panel is configured to operate with standard J1939 engines where engine de-rate and
shutdowns are managed by the engine ECU. The panel communicates with the engine ECU and
serves asa trouble code reader. When the engine ECU broadcasts a trouble code (called an
SPN.FMI code) the panel does the following:
1) Illuminate the appropriate LED indicator lamp
a. Yellow Lamp = Alarm
b. Red Lamp = Engine Shut Down
2) Displays the trouble code (standard SPN.FMI code)
3) Displays a code description on the LCD screen
4) Displays the occurrence count of the code
5)
Occurrence
Count
SPN.FMI
Red Lamp
Code
Description

CONTROLS, INCORPORATED
C O N T R O L S Y S T E M S & S O L U T I O N S
- 8 -
Indicator Lamps
The panel has six lamp indicators.
Active and Stored Engine ECU Codes
The panelalso provides the ability to check the engine ECUfor all ACTIVE and STORED engine
ECU codes. These codes can be viewed via the Active Codes and Stored Codes menus. In
addition, the control panel has its own Alarm Event Log menu that shows the last 16 engine ECU
alarms as well as any control panel specific alarms.
Engine
Fault
Lamp
Regen
Inhibit
Lamp
Regen
Active
Lamp
Engine
Alarm
Lamp
DPF
Lamp
Pre
Heat
Lamp

CONTROLS, INCORPORATED
C O N T R O L S Y S T E M S & S O L U T I O N S
- 9 -
CONTROL PANEL SPECIFIC ALARMS AND SHUT DOWNS
The panel has its own engine safety alarms and shut downs that can be enabled. These alarms
and shut downs are managed by the control panel independentfrom the engine ECU. The
available options are listed below and can be accessed via the EngineSafety Configuration menu.
The panel is shipped from the factorywith these parameters disabled. They must be enabled to
activate.
Heading
Default
Range
Units
Sender Check Bypass
0:10
0:05 –1:00
Min:Sec
Fuel Level Check
Run
Off / Always / Run
Low Fuel Pre Alarm
20
0 - 100
%
Low Fuel Alarm
1
0 - 100
%
Fuel Alarm Delay
0:05
0:01 –1:40
Sec
Oil Pressure Check
Off
Off / Always / Run
Low Oil Press Pre Alarm
15
0 - 100
PSI
Low Oil Press Alarm
10
0 - 100
PSI
Oil Press Alarm Delay
5
0:01 –1:40
Sec
Temperature Check
Off
Off / Always / Run
Low Temp Pre Alarm
0
0 - 300
Deg F
Low Temp Alarm
0
0 - 300
Deg F
High Temp Pre Alarm
220
150 - 300
Deg F
High Temp Alarm
230
150 - 300
Deg F
Temp Alarm Delay
0:05
0:01 –1:40
Min:Sec
Battery Volts Check
Off
Off / Always / Run
Lo Battery Pre Alarm
12.0
0.0 –40.0
Volts
Hi Battery Pre Alarm
15.0
0.0 –40.0
Volts
Over Speed Check
Off
Off / Always / Run
Over Speed Alarm
3000
650 - 5000
RPM
Over Speed Alarm Delay
0:05
0:01 –1:40
Min:Sec
1) Off / Always / Run –Describes when the parameter will be monitored for alarm conditions. Run
refers to when the engine is running. Off disables the alarm conditions. Always enables the
alarm constantly regardless of engine state.
2) Alarm Delay –The time period, after Sender Check Bypass, that the parametermust be on the
alarm condition before the alarm becomes latched.

CONTROLS, INCORPORATED
C O N T R O L S Y S T E M S & S O L U T I O N S
- 10 -
CONTROL PANEL ANALOG AND DIGITAL INPUTS
The panel has one analog input and up to nine digital inputs available to monitorother components,
senders or signals. These inputs can be used for a number of purposes including alarms and shut
downs. The panel is shipped from the factory with the bolded inputs enabled and pre-wired in the
panel. The other inputs are available but not enabled or pre-wired in the panel.
Input
Heading
Default
Options
Connector
Pin
Analog 1
Function
None
14-pin
Primary
13
Digital 1
Normally
Open
Open / Closed
14-pin
Primary
14
Function
None
Message
None
Check
Off
Off / Always / Run

CONTROLS, INCORPORATED
C O N T R O L S Y S T E M S & S O L U T I O N S
- 11 -
1) Analog 1 Function Options
1) Fuel Level S-W –Fuel amount, in percentage,can be measured and displayed on the C3
module using a standard Stewart Warner scale sender of 240 ohms –33 ohms. 240 =
Empty and 33 = Full. Sender ground must be common with battery negative.
2) Fuel Level VDO –Fuelamount, in percentage can be measured and displayed on the C3
module using a VDO scale sender of 10 ohms –180 ohms. 10 = Empty and 180 = Full.
Sender ground must be common with battery negative.
3) Oil Pressure PSI –Oil pressure, in PSI, can bemeasured and displayed on the C3 module
using a standard Stewart Warner scale sender of 240 ohms –33 ohms. 240 = 0 PSI and
33 = 100 PSI. Sender ground must be common with battery negative.
4) Oil Pressure bar –Oilpressure, in bar, can be measured and displayed on the C3 module
using a standard Stewart Warner scale sender of 240 ohms –33 ohms. 240 = 0 barand
33 =7 bar. Sender ground mustbe common with battery negative.
5) Oil Pressure VDO PSI –Oil pressure, in PSI, can be measured and displayed on the C3
module using a standard Stewart Warner scale sender of 10 ohms –180 ohms. 10 = 0 PSI
and 180 = 150 PSI. Sender ground must be common with battery negative.
6) Oil Pressure bar –Oilpressure, in bar, can be measured and displayed on the C3 module
using a standard Stewart Warner scale sender of 10 ohms –180 ohms. 240 = 0 bar and
33 =10 bar. Sender ground must be commonwith battery negative.
7) Rheostat –Speed control can be accomplished by connecting a 5 K potentiometer in series
with the flex analog input. Engine speed will vary with the change in resistance value.
8) 0 - 5 VDC –Reserved for OEM applications.
9) Ratiometric - Reserved for OEM applications.
10)4-20mA - Reserved for OEM applications.
11)Switch –This setting allows for a switch to be connected rather than an analog sender. Set
Analog 1 Message to assign a label to the switch device.
12)None –Set to None when no functionality is required.
2) Digital Function Options
The digital inputs can be configured for different uses depending on the application. These
include the following.
1) Alarm –Engine shutdown when active with display message as assigned. A red lamp will
also be illuminated.
2) Pre Alarm –Warning message will be displayed along with a yellow lamp when active.
3) Low Float –For auto start applications where a dualfloat system is desired. Note, Digital1
Action must be configured for Auto Start.
4) Aux Throttle Up –Mimics the front panel key press for speed control.
5) Aux Throttle Down - Mimics the front panel key press for speed control.

CONTROLS, INCORPORATED
C O N T R O L S Y S T E M S & S O L U T I O N S
- 12 -
3) Digital Function Activation
1) Off / Always / Run –Describes when the parameter will be monitoredfor alarm conditions.
Run refers to when the engine is running. Off disables the alarm conditions. Always enables
the alarm constantly regardless of engine state.
2) Alarm Delay –The time period, after Sender Check Bypass, that the parameter must be on
the alarm condition before the alarm becomes latched.

CONTROLS, INCORPORATED
C O N T R O L S Y S T E M S & S O L U T I O N S
- 13 -
CONTROL PANEL RELAY OUTPUTS
A total of eight relays can be assignedfordifferent uses depending on application to provide relay
output signals to external devices such as horns, sirens, PLC’s or SCADA systems. Two 10 amp
relays and six 5 amp relays are available. Relay 2 and Relay4 are 10 amp, while Relays 1 through
3 and 5 through 8 are 5 amp.
The panel is shipped from the factory with the bolded outputs enabled and pre-wired
in the panel.
Relay
Heading
Default
Options
Relay 1
Function
None
Polarity
Positive
Positive / Invert
Initial State
Off
Off / On
Relay 2
Function
Fuel/Run
Polarity
Positive
Positive / Invert
Initial State
On
Off / On
Relay 3
Function
None
Polarity
Positive
Positive / Invert
Initial State
Off
Off / On
Relay 4
Function
None
Polarity
Positive
Positive / Invert
Initial State
Off
Off / On
Relay Functions –A totalof four relays can be assignedfordifferent uses depending on
application.
a. None –Assign to “none” when not used.
b. Start Warning –Relay will be active during auto start delay period. Typically used to
drive the lowside of an alarm horn or light.
c. Crank –Relay will be active during auto crank period. Used to drive a starter relay.
d. Preheat –Relay will be active during programmed preheat period. Used to drive a
preheat relay.
e. Fuel / Run –Relaywill be active during an engine start request and while the engine
is running. Used to drive the engine’s ECU circuit. Also active when requesting active
and stored J1939 codes.
f. Switch Trip –Relay will be active if digital input is active.

CONTROLS, INCORPORATED
C O N T R O L S Y S T E M S & S O L U T I O N S
- 14 -
g. Engine Run –Relaywill be active when engine RPM is greater than 600. Typically
used to drive an auxiliary circuit such as louvers or send a signal to a monitoring
station.
h. Alarm –Relay will be active when there is an alarm condition. Typically used to drive
an alarm horn or lamp. Also can be used to send a signal to a monitoring station.
i. Pre Alarm –Relay will be active when there is a pre alarm condition. Typically used to
drive an alarm horn or lamp. Also can be used to send a signal to a monitoring
station.
j. Pre Alarm & Alarm –Energizes an external audible alarm when a pre alarm or alarm
condition is present. Pressing the ENTER button will silence.
k. Alarm Horn –Energizes an external audible alarm when an alarm condition is
present. Pressing the ENTER button will silence.
l. Low Oil Press Alarm –Relay closes if a low oil pressure shutdown is detected.
m. Hi Coolant Temp Alarm –Relay closes if a high engine temperature shutdown is
detected.
n. Overspeed Alarm –Relay closes if an overspeed shutdown is detected.
o. Over crank Alarm –Relay closes if an over crank alarm is detected.
p. Low Fuel Level Alarm –Relay closes if a low fuel level shutdown is detected.
q. Input 2-9 –Closes if the associated input isactive.
r. Clutch 1 –Closes when Clutch 1 conditions are met
s. Clutch 2 –Closes when Clutch 2 conditions are met.
t. Throttle B1 –Reserved for OEM applications.
u. Throttle B0 –Reserved for OEM applications.
v. Custom 1 - Reserved for OEM applications.
2) Relay Polarity
a. Positive –Relay acts as a normally open contact.
b. Invert –Relay acts as a normally closed contact.
3) Relay Initialized State
a. On –Relay is activated upon power up.
b. Off - Relayis not activated upon power up.

CONTROLS, INCORPORATED
C O N T R O L S Y S T E M S & S O L U T I O N S
- 15 -
MENU SYSTEM
To Enter Menu System
Hold MENU button andpress ENTER button.
Menu Navigation
Press MENU button to scroll menu options.
Press the UP arrow button to enter menu.
Press the DOWN arrow button to reverse.
Exit Menu System
Hold MENU button andpress ENTER button.
To Change a Setting
Press the ENTERbutton to bringup brackets [ ].
Press UP arrow button and DOWN arrowbutton to change setting.
Press ENTER button to make selection, brackets disappear.
Recycle key to the OFF position after changing a setting.

CONTROLS, INCORPORATED
C O N T R O L S Y S T E M S & S O L U T I O N S
- 16 -
Main Menus
Main Menus
Sub Menus
Emissions Parameters
Regen Options (Auto, Inhibit, Request)
DPF Soot Load % View
DPF Ash Load % View
Time Since Last Regen View
Regen Active/Not Active View
Regen Inhibited/Not Inhibited View
DPF Out Gas Temperature View
DPF Differential Pressure View
Active Engine Fault Codes
View/Scroll Active Fault Codes
Stored Engine Fault Codes
View/Scroll Stored Fault Codes
Operation Event Log
View Last 32 Events (Start, Stop, Alarms)
Alarms Event Log
View Last 32 ECU and Controller Alarms)
Engine Parameters
View ECU Engine Information
(% Load, Torque, Oil Temp, etc.)
Engine Identification
Engine Model # View
Engine Serial # View
Module Information
Control Unit Part# View
Control Unit Software Version View
Controller Setup
Input Configuration
(1)
(PASSWORD PROTECTED)
Output Configuration
(2)
Throttle Configuration
(3)
Engine Safety Configuration
(4)
Module Configuration
(5)
CAN Configuration
(6)
Emissions Configuration
(7)
Configuration Menus
Viewing Menus
Configuration
Menus

CONTROLS, INCORPORATED
C O N T R O L S Y S T E M S & S O L U T I O N S
- 17 -
(1)
Input Configuration
Analog 1 Function (Default = None)
Digital Input 1 Setup –(NO/NC, Action, Message, When Active, Delay)
(2)
Output Configuration
Relay Output 1 Setup (Function, Polarity, Initial State)
Relay Output 2 Setup - Pre Set to Fuel/Run Signal
Relay Output 3 Setup (Function, Polarity, Initial State)
Relay Output 4 Setup (Function, Polarity, Initial State)
(3)
Throttle Configuration
Throttle Type (Default = TSC Vernier)
TSC Mode Selection (Default = Primary)
TSC Min Speed Selection (Default = 650 RPM)
TSC Max Speed Selection (Default = 2400 RPM)
TSC Bump Speed (Default = 20 RPM)
TSC Ramp Rate Selection (Default = 100 RPM/Second)
Throttle Curve Selection (Default = Linear)
Multistate Speed 1 Selection
Multistate Speed 2 Selection
Multistate Speed 3 Selection
Multistate Speed 4 Selection
(4)
Engine Safety Configuration
Sender Check Bypass Time Period Selection (Default = 0:10)
Fuel Level Check On/Off Selection
Low Fuel Level Pre Alarm % Selection (Default = 20%)
Low Fuel Level Alarm % Selection (Default = 1%)
Fuel Level Alarm Delay Time Selection (Default = 0:05)
Oil Pressure Check Selection (Default = Run)
Low Oil Pressure Pre Alarm Selection (Default = 6 PSI)
Low Oil Pressure Alarm Selection (Default = 5 PSI)
Oil Pressure Alarm Time Delay Selection (Default = 0:10)
Engine Temperature Check (Default = Run)
Engine Temperature Pre Alarm Selection (Default = 0 / 244 Degrees)
Engine Temperature Alarm Selection (Default = 0 / 245 Degrees)
Engine Temperature Alarm Time Delay Selection (Default = 0:10)
Battery Volt Check On/Off (Default = Off)
Low Battery Volt Pre Alarm Selection (Default = 12.0 Volts)
High Battery Volt Pre Alarm Selection (Default = 15.0 Volts)
Battery Volt Trim Setting, 100mV (Default = 5)
Over speed Alarm On/Off (Default = Off)
Over speed Alarm RPM Setting (Default = 3000 RPM)
Over speed Alarm Time Delay Selection (Default = 0:05)

CONTROLS, INCORPORATED
C O N T R O L S Y S T E M S & S O L U T I O N S
- 18 -
(5)
Module Configuration
English/Metric Selection (Default = English)
Hour Meter Source (Default = Engine ECU)
Hour Meter Setting (if not ECU)
Battery Volt Source (Default = J1939)
Pre Alarms Displayed (Default = 4)
Clear Operation Log Yes/No
Clear Alarm Log Yes/No
(6)
CAN Configuration
Source Address (Default = 44)
TSC1 Address (Default = 3)
Engine Address (Default = 0)
Engine Type (Default = John Deere)
Oil/Fuel Transmit On/Off
(7)
Emissions Configuration
DEF Level Check (Default = Off)
Low DEF Pre Alarm (Default = 16%)
TSC Regeneration Speed Selection (Default = 750 RPM)
Allow Service Regeneration Yes/No (Deere Only)
Regeneration Interlock On/Off
TSC Transmit Yes/No (stop TSC to engine during regeneration)

CONTROLS, INCORPORATED
C O N T R O L S Y S T E M S & S O L U T I O N S
- 19 -
EMISSIONS MONITORING
Emissions Information
The panel provides lamp indications, displaymessages and other emission related information.
This information is broadcastfrom the engine ECU and is captured and displayed by the panel. The
panel includes an Emissions Parameters viewing menu that allows the operator to view the following
emissions related information.
Heading
Default
Range
DPF Soot Load
View
Only
0 –200%
DPF Ash Load
View
Only
0 –200%
Time Since
Regeneration
View
Only
# of Hours Since
Last
Regeneration
Regeneration
Process
Current
Status
Active or Not
Active
Other manuals for J1939 iT4
1
Table of contents
Other Controls Engine manuals
Popular Engine manuals by other brands
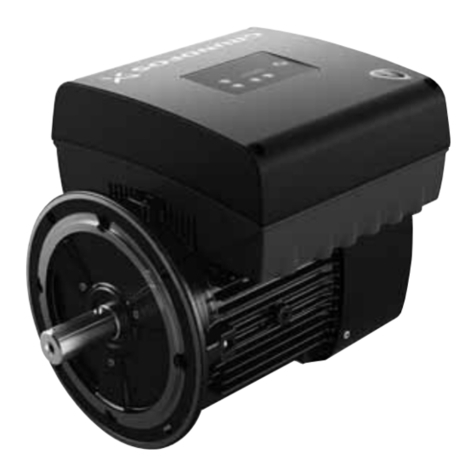
Grundfos
Grundfos MGE 112 Service Kit Instructions

Briggs & Stratton
Briggs & Stratton 12A800 Series owner's manual

Nice
Nice E MAT ST 324 Instructions for installation & use
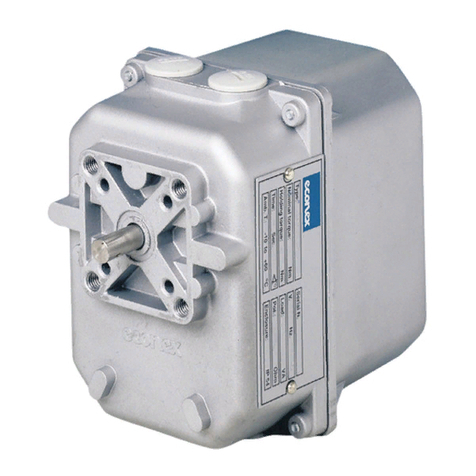
Econex
Econex AB1 Series Installation and operating instructions
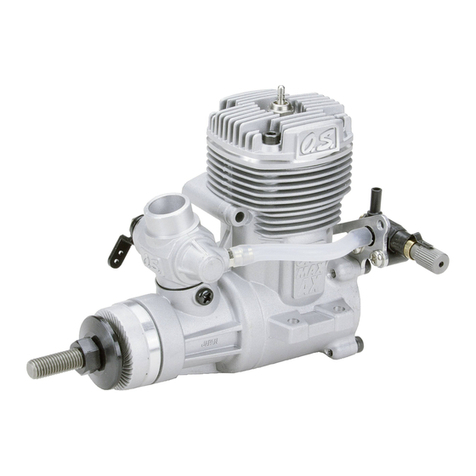
O.S. engine
O.S. engine MAX-46AX Owner's instruction manual
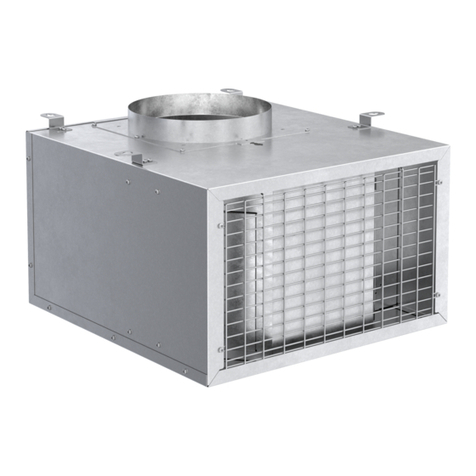
Thermador
Thermador VTR2FZ installation instructions