Coronado 83.00 Operating instructions

Diagnostic Overview
A/C cooling problems fit into two basic failure catego-
ries: refrigerant or electrical. The goal of this trouble-
shooting guide is to provide the information neces-
sary to determine what part is causing the problem.
We expect the technician to use approved tools and
shop practices, symptom-driven diagnostics, and
warranty component evaluation guides to properly
asses component failures. Refer to www.access-
freightliner.com for available tool information, ser-
vice training, and warranty documentation.
For system performance testing, ambient tempera-
ture must be above 70°F (21°C) to produce reliable
results. In order to quickly determine if your symp-
toms are refrigerant or electrical, two main tools
should be utilized by the technician: ServiceLink and
a refrigerant gauge set.
General Diagnostic Procedure
1. Perform the preliminary checks.
2. Perform an initial system inspection.
3. Make a determination about which system is
suspected (refrigerant or electrical), and follow
the symptoms through to a suspected part.
4. Repair the problem.
5. Verify that all of the refrigerant connections re-
moved during the service are properly sealed
using an approved refrigerant leak detector.
6. Verify that the problem has been resolved.
System Overview
The blend air system uses constant discharge tem-
perature control (CDTC) to regulate the temperature
in the vehicle. The CDTC is a closed-loop system
that uses the climate control panel settings and the
temperature sensors to control and maintain the out-
let temperature of the system. The blend air system
has an electronically-controlled, brushless, direct cur-
rent (BLDC) blower motor that does not require a
resistor block to control the blower speed.
In the blend air system, all air is directed through the
evaporator. The amount of air needing to be re-
heated is controlled by the temperature control door,
which directs that amount of air through the heater
core.
The cab HVAC assembly consists of a blower motor,
evaporator, heater core, CDTC sensor, evaporator
temperature sensor, and three electric actuators that
drive the air direction control doors. The doors per-
form the following functions:
•temperature control door—controls how much
air is directed through or around the heater
core
•air selection mode door—directs airflow to the
face, floor, or defrost outlets
•recirculation door—controls the amount of out-
side air that enters the HVAC unit
The cab climate control panel (front control unit) con-
tains the microprocessor that controls the system.
The sleeper or auxiliary HVAC assembly consists of
a brushless blower motor, evaporator, heater core,
auxiliary control unit, air filter, CDTC temperature
sensor, and an electric actuator that drives the tem-
perature control door.
The refrigerant system consists of a compressor,
condenser, receiver-drier, thermal expansion valve(s),
and pressure sensors.
Heater and Air Conditioner Troubleshooting
83.00
General Information
Coronado Workshop Manual, Supplement 5, June 2012 050/1

Preliminary Checks
NOTE: Pay attention to the refrigerant system
components for evidence of oil seepage and
other potential leaks that will be checked during
subsequent diagnostic steps.
Before testing the operation of the air conditioning
system, check the following items:
1. Inspect the drive belt and mounting fasteners for
signs of wear or looseness.
2. Visually inspect the clutch for signs of overheat-
ing, damage, or wear. If necessary, check the
clutch gap. For instructions, see Sec-
tion 83.04, Subject 140.
3. Check for road debris buildup on the condenser
coil fins. Using air pressure and a whisk broom
or a soapy spray of water, carefully clean off the
condenser. Be careful not to bend the fins.
4. Inspect the fresh and recirculation air filter ele-
ments, and inspect the intake-air ducting for de-
bris.
5. With the engine off, and Optimized Idle (if appli-
cable) disabled, turn the compressor drive plate
by hand to feel for grinding or harshness inside
the compressor.
Initial Inspection
1. Connect refrigerant pressure gauges and Ser-
viceLink to the vehicle.
2. Start the vehicle and select A/C mode and a cold
temp setting to request compressor engagement.
If the following conditions are met, the clutch
should engage.
•The key is in the ignition ON position so
that both IGN and ACC circuits are pow-
ered.
•Refrigerant system high side pressure is
between 20 psi (140 kPa) 450 psi (3100
kPa). Pressure reading is taken at the bi-
nary switch.
•System voltage is between 8.5 and 17
volts.
•Evaporator temperature is above 44°F
(6.5°C). Temperature is taken in the main
heater box, as a direct input to the front
control unit (FCU).
•The blower feedback from the main HVAC
unit is connected.
At this point you should be seeing some indication of
a problem, either electrical or refrigerant.
Electrical—If there are any faults that affect the FCU,
or if the system requirements are being met but the
clutch is still not engaging, there may be an electrical
problem related to the FCU, or the voltage signal to
the compressor.
Refrigerant—If the low side pressure is drawing
down far below 20 psi (140 kPa), or if the high side
pressure is rising above 450 psi (3100 kPa), there is
a refrigerant-related problem.
Post-Repair Procedures
After repair work is completed, verify that the repair
resolved the problem.
1. Verify that all of the refrigerant connections re-
moved during the service are properly sealed
using an approved refrigerant leak detector.
2. Check for fault codes. There should be no active
fault codes that indicate the problem still exists.
3. If there is still a problem, repeat the appropriate
tests, and make repairs as needed.
4. Verify again.
Heater and Air Conditioner Troubleshooting
83.00
Diagnostic Process
Coronado Workshop Manual, Supplement 5, June 2012 310/1

Refrigerant System Tests
Use the following procedure to evaluate the perfor-
mance of the air conditioning system. If the system
does not operate within the following guidelines, fur-
ther diagnosis and repair may be necessary. The
dash outlet temperature will fluctuate during each
clutch cycle, and the temperature reading should be
taken at the lowest value.
1. Park the vehicle out of direct sunlight, shut down
the engine, and chock the tires.
2. Open the hood and leave the hood open for the
entire test.
3. Open the driver and passenger doors and leave
the doors open for the entire test.
4. Note the current ambient air temperature.
NOTE: High relative humidity reduces cooling
and could increase the dash outlet temperatu-
res, and high-side system pressures.
5. Using the ambient air temperature readings
noted in the previous step, find the temperature/
pressure specifications in Table 1 that best
match your ambient conditions.
6. Connect the test gauges to the high and low side
service ports.
7. Place a thermometer in the center dash outlet. If
the vehicle is a SleeperCab, place another ther-
mometer in the lower sleeper outlet.
NOTE: EPA10 and owner-set idle limits may
prevent the warm-up run from continuing without
occasional throttle inputs.
8. Start the engine and run the A/C for 15 minutes.
9. Set the engine speed to 1500 rpm and engage
the engine fan.
10. Set the cab climate control panel to the following
settings:
•air selection switch to face mode
•air conditioning on
•blower speed switch to high
•temperature control switch to full cold
•recirculation switch off
11. On SleeperCabs, set the sleeper climate control
panel to the following settings (or initiate "bunk
override" mode):
•blower speed switch to high
•temperature control switch to full cold
12. Allow the system to stabilize at least five minutes
or until the dash and sleeper outlet temperatures
have reached a minimum, then compare the sys-
tem values to the information in Table 1. The
results should be close to those listed, but minor
discrepancies are not a guarantee that the sys-
tem has a refrigerant system problem.
Possible causes of refrigerant system com-
plaints:
•Too much oil - High high-side pressure,
poor heat rejection at the condenser
•Too much refrigerant - High high-side pres-
sure, good cooling
Approximate Temperature/Pressure Specifications at Moderate Humidity (less than 50%)
Ambient Air Temp. Center Dash
Outlet Temp.
Service Port Pressures A/C
Compressor
Status
A/C Compressor
Status
Comments
High Side
psi (kPa)
Low Side
psi (kPa)
65–75°F (18–24°C) 44–50°F (7–10°C) 94–124 (648–855) 18–25 (124–172) approximately
50% duty cycle Cycling on
evaporator freeze
protection
75–85°F (24–29°C) 45–60°F (7–16°C) 114–125 (786–862) 20–26 (138–179) approximately
75% duty cycle
85–95°F (29–35°C) 55–70°F (13–21°C) 135–170 (931–1172) 23–28 (158–193) On On steady
95–105°F (35–41°C) 65–80°F (18–27°C) 160–200 (1003–1379) 25–30 (172–207) On On steady
Table 1, Approximate Temperature/Pressure Specifications at Moderate Humidity (less than 50%)
Heater and Air Conditioner Troubleshooting
83.00
Refrigerant System Tests
122SD and Coronado Workshop Manual, Supplement 9, June 2014 320/1

•No enough refrigerant - Low high-side
pressure, low low-side pressure, poor co-
oling
•Debris in the system - TXV plugged or un-
controllable, compressor turns hard,
receiver/dryer is icing
•Contaminated or incorrect refrigerant - Very
inconsistent system pressures and duct
temps
Thermal Expansion Valve
Testing
General
The thermostatic expansion valve (TXV) (see Fig. 1)
is a controlling device that regulates the flow of refri-
gerant into the evaporator. It is actuated by changes
in evaporator pressure and the superheat of the refri-
gerant gas leaving the evaporator. Superheat is defi-
ned as any temperature of a gas above the boiling
point for that liquid. For example, when a refrigerant
liquid boils at a low temperature of 40°F (4.5°C) in
the evaporator and then the refrigerant gas increases
in temperature, superheat has been added. If this
refrigerant changed from a liquid to a gas or vapor at
40°F (4.5°C) and then the refrigerant vapor increa-
sed in temperature to 50°F (10°C), then it has been
superheated by 10°F (6.5°C). The refrigerant ente-
ring the evaporator is metered at a rate that matches
the amount of refrigerant being boiled off in the eva-
porator. In addition to metering refrigerant, the TXV
also provides a pressure drop in the system, separa-
ting the high-pressure side of the system from the
low-pressure side. To operate properly, the TXV must
have a steady flow of liquid refrigerant supplied to it
by the high side of the system. Issues such as an
excessively low refrigerant charge, or contaminates
in the system can interrupt this flow of liquid to the
valve. In these cases, symptoms may surface ma-
king it seem as if the valve is inoperative or plugged.
These symptoms can include poor performance, low
low-side pressures (even a vacuum) ,etc. Before re-
placing a TXV, it is important to verify that there are
no contaminates in the system and that the refrige-
rant charge is correct, by performing a refrigerant
identification and thorough leak check of the entire
system. The TXV is often incorrectly replaced as the
primary failed part, but is rarely the cause of a per-
formance issue. In rare instances the power element
of the TXV can loose its charge, reducing the range
of the TXV, but there is no other situation that can be
considered a failure of the TXV. Due to the similarity
of symptoms that these root causes have on A/C
performance, proper diagnosis is essential to making
the correct repairs to the A/C system.
Diagnostics
To determine if the TXV is functioning, watch the low-
side pressure while the compressor is engaged. The
influence from the TXV modulating can be seen as
the low-side gage needle "wags." As the load on the
system changes from ambient conditions, the TXV
may not wag as much, and care must be taken to
prevent false diagnosis. The function of the individual
TXVs in a dual evaporator system will be combined
to produce the total pressure needle waging that is
observed. If a TXV failure is suspected, connect the
gage set to the properly charged refrigerant loop,
and run the compressor. Watch for the low-side gage
needle to wag, indicating that the TXV is working.
Depending on the load, the low-side pressure may
progress from moderate to high, but the needle will
simultaneously wag as the average pressure chan-
ges.
11/26/2007 f831781
2
4
5
5
5
5
7
8
1
3
6
1. Screw (2)
2. Washer
3. Nut
4. Refrigerant Lines to J-Block
5. Seal
6. Stud
7. Thermal Expansion Valve
8. Refrigerant Lines to Evaporator
Fig. 1, Thermal Expansion Valve Installation
Heater and Air Conditioner Troubleshooting
83.00
Refrigerant System Tests
122SD and Coronado Workshop Manual, Supplement 9, June 2014320/2

Leak Detection
General
The information in this section is intended to convey
a general method of leak detecting that should be
used to enhance the usefulness of a leak detector
being used in accordance with operator’s instructions
provided by the manufacturer. No technician should
attempt to perform leak detection without reading and
understanding the owners manuals for the tools
being used, and should expect to review those ins-
tructions from time to time, to ensure the proper
method continues to be used. The process described
here was developed using the published list of re-
commended tools and warranty evaluation guides as
a basis for the expectations for repair competence.
The only way to confirm that a refrigerant leak exists
is by finding a failed or damaged component. A UV
flashlight and goggles can be used to provide an in-
dication of a leak, but a approved electronic leak de-
tector must be used to confirm the existence of a
leak, and approximate the leak rate. The connections
used for A/C refrigerant are intended to seal properly,
but given the high level of sensitivity provided by cu-
rrent leak detecting equipment, the detector may indi-
cate a leak even though the connection meets the
design specifications. To balance this, the "Accepta-
ble Leak Rates by Component" table in Specifica-
tions contains the qualifying leak rates for the com-
ponents used on P2 vehicles. The leak rates, in oz/
yr, correspond to the sensitivity values required for all
detectors that meet the SAE J2791 functional specifi-
cations. By switching between the sensitivity levels, it
is possible to discern between leaks of varying sizes
and qualify each potential leak. It is expected that a
leak rate relates to each component, as it arrives at
the factory, but the Mini-Statoseals that connect the
components together are specified separately. Addi-
tionally, due to the possible difficulty of distinguishing
between two minor leaks at a multi-port connection,
the leak rate for two Mini-Statoseals should be consi-
dered a condemning value if it is not completely clear
which seal is leaking.
Method
IMPORTANT: The refrigerant system should be
warmed up from completion of the initial inspec-
tion, but the engine is off.
IMPORTANT: Refrigerant oil residue on a part
may be an indication of a refrigerant leak in that
area, but it is not an acceptable method of de-
termining if a part is defective.
1. Shut down the engine.
2. Before testing for compressor leaks, blow shop
air near the compressor shaft seal to clear any
refrigerant that may have collected.
3. Install caps before testing the service ports.
4. Minimize the amount of wind blowing through the
test area, as this will make small leaks harder to
find.
5. Set the detector on the most sensitive setting.
6. Start at a point along the refrigerant loop, and
methodically follow the refrigerant path, test all
around O-ring connections and crimped ends
until you reach the starting point.
7. When the detector indicates a suspected leak,
move it away from the suspect area, then re-
check to the location after the detector has clea-
red.
•If the detector continues to indicate a leak,
adjust the sensitivity of the detector to
match the designed leak specifications
shown in "Acceptable Leak Rates by Com-
ponent" Table, in Specifications, and re-
test the suspected area to confirm the leak.
•Mark any confirmed leaks, then change the
sensitivity back to high and continue chec-
king the system.
8. After the entire system has been checked, reco-
ver the refrigerant, investigate each leak point to
determine what component failed, and how, then
repair leak.
9. Recharge the refrigerant system, then use the
electronic leak detector to confirm that each con-
nection opened during the repair is sealed within
the design specifications provided in the "Accep-
table Leak Rates by Component" table in Speci-
fications.
Sanden Compressor Testing,
Pressure or Pumping Test
NOTE: This test is meant to be performed after
a failure has been repaired, which may have
Heater and Air Conditioner Troubleshooting
83.00
Refrigerant System Tests
122SD and Coronado Workshop Manual, Supplement 9, June 2014 320/3

caused damage to the compressor due to low
refrigerant or oil levels.
Compressors cause refrigerant to flow through the
system by creating a pressure differential, high and
low pressures. If the compressor can be forced to
produce a high pressure in excess of 350 psi (2415
kPa) it is a good compressor.
IMPORTANT: The compressor pumping test
must be performed with the refrigerant system
charged to the factory specifications, and
functioning properly. This test should only be run
for a short time period. Shut the system down
immediately once 350 psi (2415 kPa) is achie-
ved.
1. Confirm the system is charged per the OEM re-
quirement before proceeding.
2. Disable the engine cooling fan. The condenser
can also be blocked with sheet of cardboard.
The purpose is to limit heat removal from the
system and build compressor discharge pres-
sure.
3. Start engine and engage the compressor clutch.
Compressors operating within specification
should be capable of reaching 350 psi (2415
kPa).
4. Shut the system down immediately, once 350 psi
(2415 kPa) is achieved.
Denso A/C Compressor
Pressure Test
NOTE: This test is meant to be performed after
a failure has been repaired, which may have
caused damage to the compressor due to low
refrigerant or oil levels. Compressors cause re-
frigerant to flow through the system by creating
a pressure differential, high and low pressures.
The compressor pressure test must be perfor-
med with the refrigerant system discharged, and
the refrigerant lines disconnected.
If the A/C system is experiencing a low "high side"
pressure, or a high "low side" pressure, test the per-
formance of the compressor as follows.
1. Place your thumb over the suction port of the
compressor and slowly rotate the compressor. An
even suction should be felt as the compressor is
turned.
2. Place your thumb over the discharge port and
slowly rotate the compressor. An even pressure
should be felt as the compressor is turned.
3. If an uneven pressure is felt on either the suction
or discharge port while turning the compressor,
internal damage has occurred, and the compres-
sor will not perform properly.
Heater and Air Conditioner Troubleshooting
83.00
Refrigerant System Tests
122SD and Coronado Workshop Manual, Supplement 9, June 2014320/4

Electrical Component
Checking
Blower Motor
General Information
The blower used in the blend air HVAC system is a
brushless DC motor (BLDC). The front control unit
(FCU) or auxiliary control unit (ACU) provides a DC
voltage signal to the motor to control speed. This
eliminates the need for a resistor block as used on
the water-valve controlled HVAC system. The blower
motor provides a feedback signal to the FCU or ACU
to indicate blower speed and error conditions.
Delayed Speed Change
When the blower speed is changed on the control
panel, a delay in actual speed change is normal. The
speed will ramp up or down at 1000 rpm per second.
Therefore, if the fan is off and then turned on high
speed, it will take approximately six seconds for the
fan to actually reach full speed.
Starting Sequence Protection Mode
In case the blower motor does not start (the feed-
back line indicates zero speed), the FCU or ACU will
apply five consecutive starting sequences. If all five
starting sequences are unsuccessful, the blower
motor electronic module enters a starting sequence
protection mode. The module will no longer attempt
to start the blower motor until the control signal from
the FCU or ACU is reset to zero. See "Blower Motor
Stall Protection Mode." This means one of the follow-
ing must occur:
•Turn the blower speed switch to the off posi-
tion, then back on.
•Cycle the ignition switch.
•Disconnect/reconnect the blower motor con-
nector.
Possible reasons the blower motor may enter the
starting sequence protection mode include:
•locked blower motor rotor
•open circuit in blower motor feedback signal
line
•faulty blower motor
Temperature Protection Mode
The blower motor has an internal temperature sensor
connected to the blower motor electronic module.
The electronic module monitors the blower tempera-
ture and enters a protection mode when normal tem-
perature is exceeded. When the blower motor enters
protection mode, the blower speed is reduced to
1000 rpm to reduce the load on the motor. When the
motor temperature has lowered to the normal range,
the blower speed resumes operation according to the
control panel settings.
If the temperature continues to rise or remains too
high after the blower speed is initially reduced, the
speed is further reduced to minimum speed (about
400 rpm) and then the blower motor stops. Once the
blower motor temperature returns to normal, the
blower speed resumes operation according to the
control panel settings. No reset is required.
Blower Motor Voltage Protection
Mode
The blower motor electronic module monitors the
voltage supply to the motor and enters a protection
mode when the voltage is too high or too low. The
protection mode works as described in Table 1.
Blower Motor Stall Protection Mode
The blower motor electronic module monitors the
blower for a locked rotor condition. If the rotor is
locked starting from an off condition, the electronic
module will attempt a starting sequence before enter-
ing this protection mode. See "Starting Sequence
Protection Mode." If the blower rotor locks up and
stalls from a running condition, the blower will imme-
diately enter this protection mode. The blower motor
will not restart until the blower speed control signal
has decreased to minimum by cycling the ignition, or
turning the blower speed control from ON to OFF,
then back to ON, and the stall condition has disap-
peared.
Speed/Diagnostics Feedback Line
The blower motor supplies diagnostic and speed in-
formation to the FCU/ACU. See Table 2 and
Table 3.
Heater and Air Conditioner Troubleshooting
83.00
Electrical System Tests
122SD and Coronado Workshop Manual, Supplement 9, June 2014 330/1

Blower Motor Voltage Protection Mode Conditions
Voltage at the Motor Results
under 8.5 VDC Blower motor will shut off and will not restart until the voltage reaches 10.5 VDC and will operate at
reduced speed if voltage is under 12 VDC.
8.5 to 12.0 VDC Blower motor will operate at reduced speed. The reduced speed varies with voltage. The lower the
voltage, the slower the blower speed.
12.0 to 17.0 VDC Blower motor operates normally at user selected speed.
over 17.0 VDC Blower motor will shut off. Will not restart until voltage reaches 16 VDC.
Table 1, Blower Motor Voltage Protection Mode Conditions
Blower Motor Feedback Signal From Blower to FCU or ACU*
Speed/Error
Conditions Signal Duty Cycle
Blower Speed
Three one-millisecond pulses per revolution. Blower speed is determined by the
time between each set of three pulses. Time can be viewed using an oscilloscope.
rpm=1/(time between sets of three pulses) x 60
NA
Error—temperature
protection mode 10Hz 25%
Error—voltage
protection mode 10Hz 50%
Error—blocked rotor 10Hz 75%
*Blower speed and diagnostic information are both provided by the BLDC blower motor on the feedback signal wire; however, the FCU and ACU only use the
blower speed information.
Table 2, Blower Motor Feedback Signal from Blower to FCU or ACU
Blower Speed Control Signal From FCU or ACU to Blower*†
Knob Position FCU Signal (DC
volts)‡Blower Speed (rpm) Blower Speed Comments
0 0.0 to 0.74 0 Constant speed in this range
1 0.75 to 1.0 400 Constant speed in this range
2 1.5 800
Speed varies linearly with voltage in this range.
3 2.0 1200
4 2.5 1600
5 3.0 2000
6 3.5 2400
7 4.0 2800
8 4.5 3200
9 5.0+ 3600
Heater and Air Conditioner Troubleshooting
83.00
Electrical System Tests
122SD and Coronado Workshop Manual, Supplement 9, June 2014330/2

Blower Speed Control Signal From FCU or ACU to Blower*†
Knob Position FCU Signal (DC
volts)‡Blower Speed (rpm) Blower Speed Comments
10 5.5+ 4000 Constant speed above this range
*Error conditions can be monitored on the feedback signal line using a digital multimeter equipped with a duty cycle function.
†Blower speed and diagnostic information are both provided by the BLDC blower motor on the feedback signal wire; however, the FCU and ACU only use the
blower speed information.
‡These values are based on a system operating voltage of 13.5 VDC.
Table 3, Blower Speed Control Signal from FCU or ACU to Blower
A/C Clutch Circuit
General Operation
The air conditioner compressor clutch is controlled by
the FCU. When certain inputs to the FCU are met,
the FCU sends the A/C request signal to the A/C
clutch relay located in the PDM. This signal is +12
VDC. The request signal causes the A/C clutch relay
to make contact between the common and normally
open contacts of the relay. This allows current to flow
through the relay, then through the binary pressure
switch and to the A/C compressor clutch, thus en-
gaging the compressor.
In steady state operation, compressor cycling is con-
trolled by two things: evaporator temperature sensor
and an internal FCU timer that prevents the com-
pressor from cycling more than four times per min-
ute. The A/C request signal does not become active
until the evaporator temperature sensor is at least
44°F (7°C). See Table 4. Once the signal is active
and as long as the other conditions are met, the sig-
nal remains active until the evaporator temperature
sensor reaches 37°F (3°C), then becomes inactive.
The A/C request signal does not activate again until
the temperature is above 44°F (7°C). With the A/C
on in warm or humid weather, the evaporator tem-
perature will most likely remain between 37 and 44°F
(3 to 7°C), thus keeping the compressor on continu-
ously.
When the blower speed control is set to any speed
other than OFF, and the air selection switch is set to
any setting other than one of the defrost modes, the
user may request A/C by pressing the A/C button.
The light on the button turns on and the FCU is
placed in A/C mode, thus allowing the compressor to
engage when other conditions are met. If the air se-
lection switch is in any of the defrost settings, then
the A/C mode is turned on automatically and cannot
be turned off by pressing the A/C button.
FCU A/C Request Rules*
Input Input Type State All Inputs Must Be for the FCU to Send A/C Request Signal
Ignition power +12V On
Evaporator temperature
sensor Sensor Above 44°F (7°C)
A/C switch/light Control panel On
Air selection switch Control panel Any A/C or defrost setting except when rear override is active
Temperature control switch Control panel Any
Fan switch Control panel Any setting other than off except when rear override is active; fan will
be at least minimum speed.
Compressor cycling timer Internal FCU logic 15 seconds elapsed since A/C request last active
Heater and Air Conditioner Troubleshooting
83.00
Electrical System Tests
122SD and Coronado Workshop Manual, Supplement 9, June 2014 330/3

FCU A/C Request Rules*
Input Input Type State All Inputs Must Be for the FCU to Send A/C Request Signal
Main Blower Feedback Signal Rotational Signal
(Hz) No active faults from the blower feedback signal
*If any input state does not meet the conditions listed in this table, A/C request will not be sent. The only exception is when the sleeper unit requests A/C sup-
port by going into rear override mode. See "Cab Override."
Table 4, FCU A/C Request Rules
A/C Mode
The auxiliary HVAC system has the ability to request
A/C causing the FCU to engage the compressor. For
more information, see "Cab Override."
Once the HVAC system is in A/C mode, the system
is able to send the A/C request when all the condi-
tions are met. See Table 4. When the system is in
A/C mode, the light on the A/C button comes on.
Just because the system is in A/C mode does not
necessarily mean that the A/C compressor should be
engaged. See Table 4 for A/C request rules.
NOTE: If the air selection switch is changed to
defrost when in A/C mode, the A/C mode will
remain active and the light on the A/C button
will remain on. When in defrost, the user will not
be able to cancel A/C mode by pressing the A/C
button. If the mode is changed back to A/C, the
A/C mode will remain on, but the user will be
able to turn it off by pressing the A/C button.
See Fig. 1.
NOTE: The A/C mode is remembered after an
ignition cycle. If the A/C mode indicator was on
because the A/C button was pressed before an
Blower Speed
Setting
A/C Mode Off/
Light Off
OFF
ON
YES
NO
YES
NO
A/C Button
Pressed?
A/C Mode On/
Light On
A/C Button
Pressed?
ON Blower Speed
Setting
A/C Mode Off/
Light Off
06/18/2002 f040615
OFF
Fig. 1, A/C Mode Function When Not in Defrost Mode
Heater and Air Conditioner Troubleshooting
83.00
Electrical System Tests
122SD and Coronado Workshop Manual, Supplement 9, June 2014330/4

ignition cycle or battery kill switch cycle, the
FCU will remember this mode and activate it
again after the cycle.
Defrost Mode
When the HVAC system is in defrost mode, A/C
mode is automatically activated and the system is
able to send the A/C request when all the conditions
are met. When the system is in defrost mode, the
light on the A/C button is on. Just because the sys-
tem is in defrost mode does not necessarily mean
that the A/C compressor should be engaged. See
Table 4 for A/C request rules.
NOTE: If the mode is taken out of defrost, A/C
mode and the light will be deactivated unless
the system was in A/C mode prior to being in
defrost mode. When the system is in defrost
mode, A/C mode cannot be disabled by press-
ing the A/C button. See Fig. 2.
A/C Request
Once A/C mode is activated, the A/C compressor
clutch can be engaged when all the engagement
rules are met. The A/C request rules are described in
Table 4.
Recirculation
Recirculation Mode
Recirculation (recirc) mode allows the driver to
choose between fresh air or recirculated air moving
through the HVAC system. When recirc mode is se-
lected, all of the air through the front HVAC unit is
recirculated within the cab, except when the unit is in
partial recirc mode, which is explained in "Partial Re-
circ Mode."
Using the recirculation mode prevents dusty or
smoky air from entering the cab and provides better
air conditioning performance since the cab air is al-
ready cooled and less humid than outside air. Humid-
ity holds a lot of heat.
Partial Recirc Mode
After recirc mode has been on for 20 minutes, the
system enters partial recirc mode to introduce a con-
trolled amount of fresh air to the cab. This prevents
the air from becoming stagnant if left in recirc mode.
The recirc door partially opens to one of two partially
open positions depending on vehicle speed. When
the vehicle is stopped or moving very slowly, the re-
circ door opens to its widest partially open position.
When the vehicle is moving at slow to moderate
speeds, the recirc door opens to its most narrow par-
tially open position. Pressing the recirc button again
resets the 20-minute timer and the system goes into
full recirc again. See Table 5 for information on par-
tial recirc.
Recirc Diagnosis
To see the recirc door, remove the heater and air
conditioner cover and the recirculation air filter. See
Fig. 3. When the system is not in recirc mode, the
recirc door is fully open. When the system is in recirc
mode, the recirc door is closed tight. See Fig. 3.
06/19/2002
Blower Speed
Setting
A/C Mode Off/
Light Off
YES
ON
NO
Mode in
Defrost?
A/C Mode On/
Light On
f040616
OFF
Fig. 2, A/C Mode Function When in Defrost Mode
Heater and Air Conditioner Troubleshooting
83.00
Electrical System Tests
122SD and Coronado Workshop Manual, Supplement 9, June 2014 330/5

Partial Recirc Operation
Condition Vehicle Speed
Partial
Recirc Door
Opening
Partial Recirc Door Opening
Approximate Height:
inch (mm)
Initial partial recirc position after 20 minutes of
full recirculation
Under 5 mph (8 km/h) Wide 1-1/4 (32)
Over 5 mph (8km/h) Narrow 1/8 to 1/4 (3 to 6)
1
2
f831537
07/22/2002
A
C
D
2
2
4
B
2
3
2
A. In recirc mode the recirc door is in the fully closed position.
B. Recirc door in the narrow, partially open position.
C. Recirc door in the widest, partially open position.
D. In non-recirc mode the recirc door is in the fully open position.
1. Recirculation Air Filter Retainer
2. Recirc Door
3. Narrow Partially Open Position of approximately1/8 to 1/4 in (3 to 6 mm)
4. Widest Partially Open Position of approximately1-1/4 in (32 mm)
Fig. 3, Recirc Door Operation
Heater and Air Conditioner Troubleshooting
83.00
Electrical System Tests
122SD and Coronado Workshop Manual, Supplement 9, June 2014330/6

Partial Recirc Operation
Condition Vehicle Speed
Partial
Recirc Door
Opening
Partial Recirc Door Opening
Approximate Height:
inch (mm)
Partial recirc position once initial position is
reached
Under 2 mph (3 km/h) Wide 1-1/4 (32)
2–8 mph(3–13 km/h) No change
Either 1-1/4 (32) or 1/8 to 1/4 (3
to 6) depending on vehicle speed
prior to entering the 2 to 8 mph (3
to 13 km/h) range.
Over 8 mph (13km/h) Narrow 1/8 to 1/4 (3 to 6)
Table 5, Partial Recirc Operation
To check partial recirc, turn the engine on and acti-
vate the full-recirc mode for 20 minutes. After 20 min-
utes, with the vehicle idling in the shop, the recirc
door should open to its widest partially open position.
To check if the recirc door adjusts to the narrow, par-
tially open position, have someone drive the vehicle
over 8 mph (13 km/h) while observing the recirc
door. See Fig. 3. Compare the width of the recirc
door opening to the values in Table 5. If the recirc
door does not function as described, check the recirc
actuator motor and wiring. If okay, the FCU is prob-
ably faulty.
Override
Bunk Override
The auxiliary unit can be controlled from the front
control panel by using the bunk-override switch.
When the upper half of the bunk override switch is
pressed to the momentary ON position, the front unit
broadcasts a snapshot of the front temperature and
blower speed settings to the auxiliary unit. The auxil-
iary unit matches these settings. The temperature
and blower speed settings on the front unit can be
changed without affecting the auxiliary unit, until the
bunk override switch is pressed in the momentary
ON position again.
When the lower half of the bunk override switch is
pressed, bunk override mode turns off and the auxil-
iary unit reverts to the auxiliary control settings. If the
auxiliary control panel settings are changed when the
system is in bunk override mode, bunk override will
be canceled and the auxiliary unit will operate using
the auxiliary control panel settings. See Table 6 for
information on bunk override functionality.
NOTE: If bunk override is activated and then the
front blower or temperature settings are
changed and the ignition key is cycled, then the
bunk override will be active again, but the auxil-
iary unit will track the new front settings.
Cab Override
When the auxiliary unit requires minimum A/C sup-
port, it sends a J1587 message requesting that the
FCU go into cab-override mode and also sends a
message indicating that cab-override mode is ON in
the ACU. The FCU receives this request and, if not
already in A/C mode, goes into cab-override mode
and sends a J1587 message to the ACU indicating
that cab-override mode is ON in the FCU. The FCU
then sets the blower speed to minimum speed to
prevent evaporator core freezing and to allow air to
flow across the evaporator temperature sensor to
allow compressor cycling. If the blower was previ-
ously set to a speed above minimum, that speed will
be maintained. The FCU also turns on the A/C mode
indicator on the A/C switch. The FCU will now oper-
ate the A/C compressor per A/C request rules. See
Table 4.
Heater and Air Conditioner Troubleshooting
83.00
Electrical System Tests
122SD and Coronado Workshop Manual, Supplement 9, June 2014 330/7

Bunk Override Functionality
Action J1587 Messaging/Control Bunk Override
Indicator
Press the upper half of the bunk
override switch to turn it on; initially
off
When the bunk override switch is pressed to the momentary
ON position (bunk override mode previously off), the FCU
sends a J1587 message to the auxiliary unit requesting that
the auxiliary unit go into bunk override mode.
The auxiliary unit then goes into bunk override mode and
sends a J1587 message to the front unit indicating that bunk
override mode in the auxiliary unit is on. Upon receiving this
message, the front unit responds by broadcasting a J1587
message that bunk override mode in the front unit is on as
well.
The front unit then sends a different J1587 message to the
auxiliary unit containing the control set points as follows:
•blower speed setting
•temperature control setting
•temperature door position
On
NOTE: The indicator
on the bunk override
switch turns on when
the upper half of the
switch is pressed.
The auxiliary unit receives this message and disregards its
own temperature and blower speed settings and adjusts its
settings to match the front unit settings. The auxiliary unit
uses the temperature door position setting as a starting
point, then it goes into constant discharge temperature
control (CDTC) operation to maintain the new desired
temperature. Blower speed is adjusted to match the front
control setting. At this point, the front control panel blower
and temperature settings can be changed without affecting
the auxiliary unit blower speed and temperature.
NOTE: With DataLink Monitor connected to some early blend
air systems, the auxiliary unit will continuously update its
control settings to match the front unit when the system is in
bunk override mode. This is not how the system operates
without DataLink Monitor connected to the vehicle.
The auxiliary unit will maintain the new temperature and
blower settings until one of the following occurs:
•temperature or blower speed settings changed on the
auxiliary control panel
•the bunk override switch is pressed to the momentary
ON or OFF position
•ignition is cycled
NOTE: If bunk override was active before an ignition cycle, it
will also be active after the ignition cycle, but the auxiliary
unit will track the current front setting at the time the ignition
is switched on again.
Heater and Air Conditioner Troubleshooting
83.00
Electrical System Tests
122SD and Coronado Workshop Manual, Supplement 9, June 2014330/8

Bunk Override Functionality
Action J1587 Messaging/Control Bunk Override
Indicator
Press the upper half of the bunk
override switch again to the
momentary ON position; bunk
override was already on
When the system is already in bunk override mode and the
upper half of the bunk override switch is pressed to the
momentary ON position, the front control unit sends a new
J1587 to the auxiliary unit containing the following new set
points:
•blower speed setting
•temperature control setting
•temperature door position
The auxiliary unit receives this message and disregards the
previous temperature and blower control settings and adjusts
its settings to match the new front unit settings (this assumes
the front blower setting or temperature setting was changed
after the initial bunk override). The auxiliary unit uses the
temperature control door position setting as a starting point.
Then it goes into CDTC operation to maintain the new de-
sired temperature. Blower speed is adjusted to match the
front control setting.
NOTE: With DataLink Monitor connected to some early blend
air systems, the auxiliary unit will continuously update its
control settings to match the front unit when the system is in
bunk override mode. This is not how the system operates
without DataLink Monitor connected to the vehicle. On these
early systems you will not be able to change the front
settings and update the auxiliary unit with a press of the
bunk override switch.
The auxiliary unit will maintain the new temperature and
blower settings until one of the following occurs:
•temperature or blower speed settings changed on the
auxiliary control panel
•the bunk override switch is pressed to the momentary
ON or off position
•ignition is cycled
On
Press the lower half of bunk over-
ride switch to the momentary off
position; bunk override mode was
on
When the bunk override switch is pressed to the momentary
off position (bunk override mode previously on), the FCU
sends a J1587 message to the auxiliary unit requesting that
the auxiliary unit go out of bunk override mode.
The auxiliary unit then goes out of bunk override mode and
sends a J1587 message to the front unit indicating that bunk
override mode in the auxiliary unit is off. Upon receiving this
message, the front unit responds by broadcasting a J1587
message that it too is out of bunk override mode.
The auxiliary unit now adjusts its temperature and blower
speed to its own settings on the auxiliary control panel and
resumes CDTC operation.
Off
Heater and Air Conditioner Troubleshooting
83.00
Electrical System Tests
122SD and Coronado Workshop Manual, Supplement 9, June 2014 330/9

Bunk Override Functionality
Action J1587 Messaging/Control Bunk Override
Indicator
Blower or temperature settings on
auxiliary control panel changed;
bunk override mode was on
When the system is in bunk override mode and the auxiliary
blower speed or temperature settings are then changed on
the auxiliary control panel, the auxiliary unit goes out of bunk
override mode and sends a J1587 message to the front unit
indicating that it is no longer in bunk override mode.
The front unit receives this message and broadcasts a J1587
message that it too is out of bunk override mode. The
indicator light on the bunk override switch turns off.
Once out of bunk override mode, the auxiliary unit now
adjusts its temperature and blower speed to its own settings
on the auxiliary control panel and resumes CDTC operation.
Off
Ignition turned off then back on;
bunk override mode was on before
the ignition was turned off
When the system is in bunk override mode and the ignition is
turned off, then back on, bunk override mode is off. The
auxiliary unit will operate to its auxiliary control panel blower
and temperature settings.
On
Table 6, Bunk Override Functionality
When the auxiliary unit no longer requires minimum
A/C support, it sends a J1587 message requesting
that the front unit go out of rear override mode and
also sends a message indicating that rear override
mode is off in the auxiliary unit. The front unit re-
ceives this request, goes out of rear override mode,
and sends a J1587 message indicating that rear
override mode is off in the auxiliary unit. If the front
blower speed setting was in the off position, the
blower will now shut off. The A/C mode indicator light
will turnoff.
Actuator Stepper Motors–
Temperature, Recirc, and Mode
General Information
The actuator stepper motors are used to precisely
position the temperature control, recirc, and air selec-
tion mode doors within the front HVAC unit, and the
temperature control door in the auxiliary HVAC unit.
The motors can operate in both forward and reverse
direction. Each motor has four motor windings with
diodes wired in series with each winding. The motor
direction and position is controlled by the FCU/ACU
applying power and sequencing ground through the
four motor windings.
Actuator Stepper Motor Test
Procedures
Test the Battery in the Stepper
Motor Tester
NOTE: It is very important to check the battery
in the stepper motor tester before testing the
stepper motor. A weak battery will lead to incor-
rect test results. See Fig. 4.
1. Press the toggle switch on the stepper motor tes-
ter to NORMAL and set the rotary switch to posi-
tion 4.
2. Connect a digital multimeter, set to read DC volt-
age, as follows:
•positive lead to the red jack on the stepper
motor tester
•negative lead to pin 6 of the stepper motor
tester lead (green wire). See Fig. 5.
3. The reading on the digital multimeter should be
at least 1.5 VDC. If the reading is less than 1.5
VDC, replace the battery by removing the four
capscrews that attach the back cover to the step-
per motor tester.
The tester uses a single AA 1.5 VDC battery. It is
recommended that you use an alkaline battery.
Heater and Air Conditioner Troubleshooting
83.00
Electrical System Tests
122SD and Coronado Workshop Manual, Supplement 9, June 2014330/10

Test the Actuator Stepper Motor
NOTE: The stepper motor has four windings,
each with an in-series diode. The stepper motor
can be tested on or off the vehicle.
1. Connect the stepper motor tester to the stepper
motor. If the stepper motor is being tested while
on the vehicle, disconnect the electrical connec-
tor from the stepper motor.
For locations of the actuators and actuator re-
placement instructions, see Section 83.04, Sub-
ject 150.
2. Set the digital multimeter to read milliamps
(mA) DC. Make sure that the test leads on the
multimeter are in the appropriate jacks for mea-
suring amperage.
3. Connect the positive lead from the multimeter to
the red jack on the stepper motor tester.
4. Connect the negative lead from the multimeter to
the black jack. See Fig. 6.
5. Press the toggle switch to NORMAL.
6. Set the rotary switch to position 1 and note the
reading on the multimeter.
7. Move the toggle switch to REVERSED and note
the reading on the multimeter.
8. Repeat the previous three steps for the 2, 3, and
4 rotary switch positions on the tester. Compare
your readings to the readings in Table 7.
9. If your readings do not match the readings in
Table 7, replace the actuator. For instructions,
see Section 83.04, Subject 150.
10. If the stepper motor was tested on the vehicle,
connect the electrical connector to the stepper
motor.
REVERSED NORMAL
J−46315
Rev. 2
Actuator motor coil/diode circuit
1
23
4
METER
Set meter to read mA
SPX KENT−MOORE
11/26/2002
1
2
f831554
1. Toggle Switch 2. Rotary Switch
Fig. 4, Actuator Stepper Motor Tester
12/06/2002 f831556
Fig. 5, Place the Negative Lead to Pin 6 of the Stepper
Motor Tester Lead
11/27/2002 f831555
Fig. 6, Testing a Stepper Motor
Heater and Air Conditioner Troubleshooting
83.00
Electrical System Tests
122SD and Coronado Workshop Manual, Supplement 9, June 2014 330/11

Acceptable Readings for the Actuator Stepper Motor Test
Condition Toggle Switch Position Conclusion Action
Normal Reversed
If the readings in all four
rotary switch positions are... 10–14 mA less than 0.2 mA Normal None; actuator is okay
electrically.
If the readings in any one or
more of the rotary switch
positions are...
15–350 mA less than 0.2 mA Shorted or partially shorted
motor coil
Replace actuator.
less than 0.2 mA less than 0.2 mA Open diode or motor coil*
0.3–9.9 mA less than 0.2 mA
Check tester battery and
retest. If battery okay, motor
winding has high
resistance.
19–24 mA 19–24 mA Shorted diode
*If the reading for each rotary switch and toggle switch position is less than 0.2 mA, check the fuse in the digital multimeter.
Table 7, Acceptable Readings for the Actuator Stepper Motor Test
Actuator Circuit Diagnosis
See Table 8 for the actuator circuit test procedures.
Evaporator Temperature Sensor
General Information
The evaporator temperature sensor is located on the
evaporator. The sensor input to the FCU is used to
control the A/C compressor in order to prevent
evaporator freezing. The sensor has a negative tem-
perature coefficient (NTC), which means that its re-
sistance decreases as temperature increases.
Evaporator Temperature Sensor
Circuit Test
See Table 9 for the evaporator temperature sensor
circuit test procedures.
Actuator Circuit Test
Test
No. Test Test Procedure Test Result Action
1 Check for fault codes.
Check if any one of the following
fault codes is active:
f040619
07/02/2002
146 s005 05
146 s006 05
146 s009 05
200 s009 05
Group A Group B
146 s005 06
146 s006 06
146 s009 06
200 s009 06
Single fault in Group A
is active. Go to test no. 2.
All three MID 146 faults
are active in Group A. Go to test no. 6.
Single fault in Group B
is active. Go to test no. 8.
No faults listed in
Group A or B are
active.
No problem found.
Heater and Air Conditioner Troubleshooting
83.00
Electrical System Tests
122SD and Coronado Workshop Manual, Supplement 9, June 2014330/12

Actuator Circuit Test
Test
No. Test Test Procedure Test Result Action
2
Check voltage to the
actuator.
NOTE: In order to
measure a valid
voltage, it may be
necessary to move
the respective control
:for recirc, press the
recirc button; for mix
door actuator, move
the temperature
control switch; for the
mode actuator, move
the air selection
switch.
For code 146 s005 05 (front unit)
disconnect the recirc actuator
connector, turn the ignition on,
measure voltage between
connector pin 1 and ground.
For code 146 s006 05 (front unit)
disconnect the mode actuator
connector, turn the ignition on,
measure voltage between
connector pin 1 and ground.
For code 146 s009 05 (front unit)
disconnect the temperature
actuator connector, turn the
ignition on, measure voltage
between connector pin 1 and
ground.
For code 200 s006 05 (auxiliary
unit) disconnect the temperature
actuator connector, turn the
ignition on, measure voltage
between connector pin 1 and
ground.
NOTE: See Fig. 7,Fig. 8, and
Fig. 9.
Approximately 12V Go to test no. 3.
Much less than12V.
Check wire between pin 1 of the
actuator and the FCU/ACU for
open circuit. If okay, replace
FCU/ACU. Go to test no. 9.
Heater and Air Conditioner Troubleshooting
83.00
Electrical System Tests
122SD and Coronado Workshop Manual, Supplement 9, June 2014 330/13

Actuator Circuit Test
Test
No. Test Test Procedure Test Result Action
3
Check for short to
ground on return side
of actuator.
For code 146 s005 05 (front unit)
disconnect all three actuator
connectors and the FCU
connector. At the recirc actuator
connector, check continuity
between connector pin 3 and
ground. Repeat for pins 4, 5, and
6.
For code 146 s006 05 (front unit)
disconnect all three actuator
connectors and the FCU
connector. At the mode actuator
connector, check continuity
between connector pin 3 and
ground. Repeat for pins 4, 5, and
6.
For code 146 s009 05 (front unit)
disconnect all three actuator
connectors and the FCU
connector. At the temperature
actuator connector, check
continuity between connector pin
3 and ground. Repeat for pins 4,
5, and 6.
For code 200 s009 05 (auxiliary
unit) disconnect the temperature
actuator connector and the ACU
connector. At the temperature
actuator connector, check
continuity between connector pin
3 and ground. Repeat for pins 4,
5, and 6.
NOTE: See Fig. 7,Fig. 8, and
Fig. 9.
Continuity to ground on
any pin.
Locate short to ground, repair as
necessary, then go to test no.
9.
No continuity to ground
on any pin. Go to test no. 4.
Heater and Air Conditioner Troubleshooting
83.00
Electrical System Tests
122SD and Coronado Workshop Manual, Supplement 9, June 2014330/14
Table of contents
Popular Heater manuals by other brands

Comfort Zone
Comfort Zone CZQTV00 Series manual
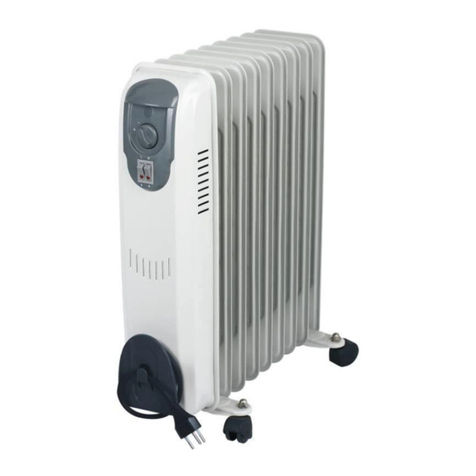
Go-On
Go-On DF-200M6-9 instruction manual
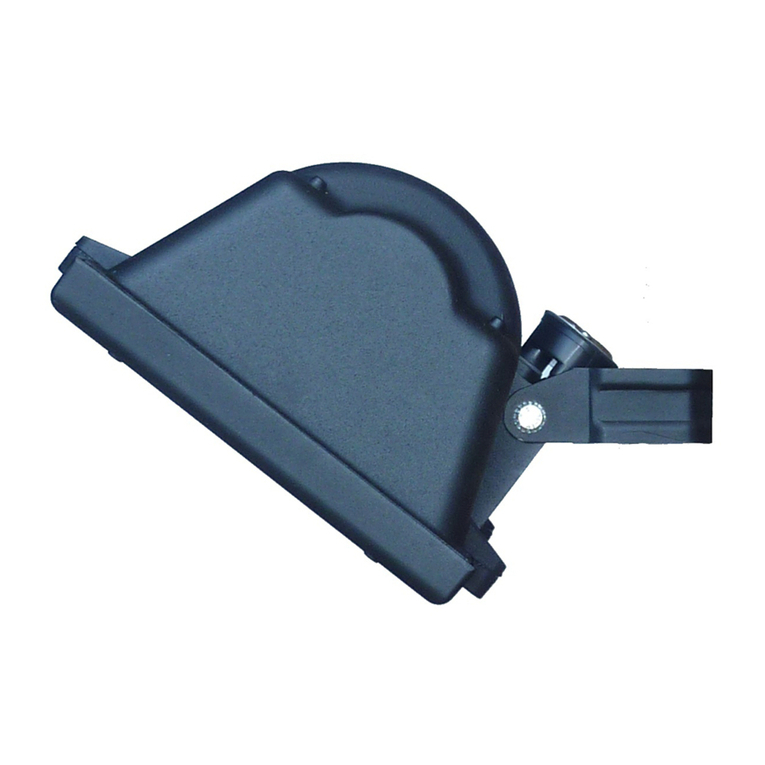
MO-EL
MO-EL 778R Use and maintenance
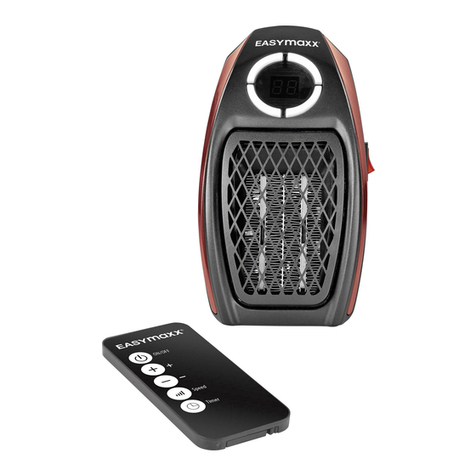
easymaxx
easymaxx H03 operating instructions
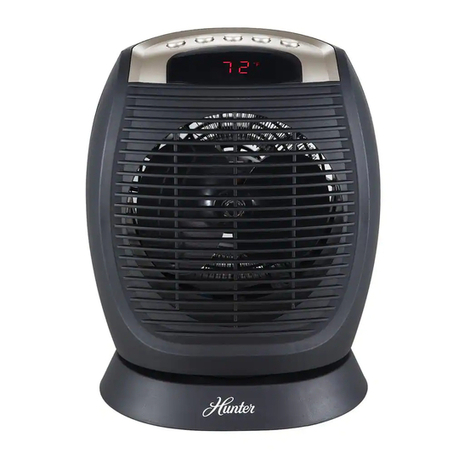
ProFusion
ProFusion HFU15-E instruction manual
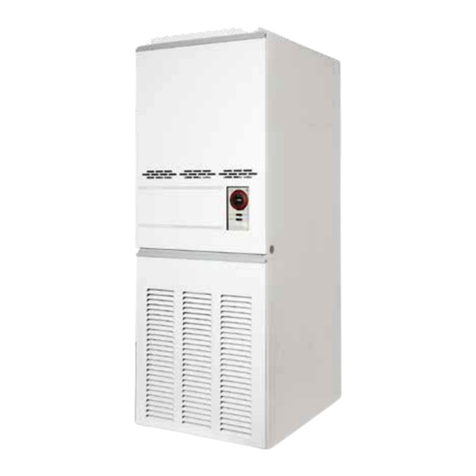
Johnson & Starley
Johnson & Starley HI-SPEC J90 Installation, commissioning & servicing instructions