CR-Tec ER PLUS Series User manual

3
POSITIONS
POSI
Positioning
Battery
Backup
BBPR
ER PLUS
Electric Actuators
Installation and Operation Manual
IP66
89 lb-in
Anticondensation
heater
50%
Duty cycleEnclosure protection
885 lb-in

Index
General information.......................................................................................................
Description
Transport and storage
Maintenance
Warranty
Return of goods
Safety instructions
Position indicator ..........................................................................................................
Emergency manual override .........................................................................................
Dimensions ....................................................................................................................
Electric wiring ................................................................................................................
Warnings
Wiring Instructions
Electric diagram
Electronic boards
BBPR models ................................................................................................................
Description
Specifications
Electronic board
LED meaning
Electric diagram
POSI models..................................................................................................................
Description
Electronic board
Wiring Instructions
Electric diagram
Parameter selection sequence
3-position models..........................................................................................................
Description
Contacts state
Electric diagram
Technical data ...............................................................................................................
This product meets the European Directive 2012/19/UE about electrical and electronic equipment (DEEE). It mustn't
be mixed with common waste. Please, recycle or dispose of them according to your country laws.
1
2
2
3
4
8
10
13
14
CR-TEC Engineering Inc. • info@crtec.com • www.crtec.com • 203-318-9500

INTRODUCTION
This manual has been made to guide you through the installation and use of our ER PLUS electric actuators. Please, read it carefully before
using our products and be sure to keep it.
DESCRIPTION
These electric actuators have been designed to perform the control of a valve with 90° rotation (or 180° in case of 3-position version). We
cannot be held responsible for any other use. You can however consult us for any other application.
ATTENTION OWNERS AND USERS
Thank you for purchasing the device. This equipment will provide safe and productive operation as long as it is used in accordance with the
instructions in this Manual and is properly maintained. Importantly, unless the user is adequately trained and supervised, there is a possibility
of death, serious personal injury, property damage or damage to the equipment.
Owners and users of this equipment bear the responsibility to make certain that this equipment is used properly and safely. READ THIS
MANUAL carefully, learn how to use and service this equipment correctly, and strictly follow all of the instructions contained in this Manual
and the requirements of local law. Failure to do so could result in death, serious personal injury, property damage or damage to the equip-
ment. This Manual should be considered a permanent part of your machine and should be kept available for easy reference by any user.
Owners should not permit anyone to touch this equipment unless they are over 18 years of age, are adequately trained and supervised, and
have read and understand this Manual. Owners should also ensure that no unauthorized personnel come in contact with this equipment.
If this equipment, or any of its parts, becomes damaged or needs repair, stop using the equipment and contact an experienced service indi-
vidual immediately. If the warning labels or this Manual are misplaced, damaged or illegible, or if you require additional copies, please contact
us for these items at no charge.
Please remember that this Manual and the warning labels do not replace the need to be alert, to properly train and supervise users, and to
use common sense when using this equipment.
If you are ever uncertain about a particular task or the proper method of operating this equipment, don’t hesitate to contact us.
TRANSPORT AND STORAGE
The forwarding agents being held as responsible for damages and delays of the delivered goods, the consignees are obliged to express if
applicable their reserves, prior to accept the goods. The goods delivered directly ex works are subject to the same conditions.
The transport to the place of destination is carried out by using rigid packing material.
The products must be stored in clean, dry, and ventilated places preferably on appropriate palettes or shelves.
MAINTENANCE
Maintenance is ensured by our factory. If the supplied unit does not work, please check the wiring according to the electric diagram as well
as the power supply of the concerned electric actuator.
For any question, please contact our after-sales service.
To clean the outside of the actuator, use a lint and soapy water. DO NOT USE CLEANING PRODUCT WITH SOLVENT OR ALCOHOL
SAFETY INSTRUCTIONS To be read prior to the installation of the product
The electric power supply must be switched-off before any intervention on the electric actuator (i.e. prior demounting its cover or manipu-
lating the manual override knob).
Any intervention must only be carried out by a qualified electrician or other person instructed in accordance with the regulations of electric
engineering, safety, and all other applicable directives.
Strictly observe the wiring and set-up instructions as described in the manual: otherwise, the proper working of the actuator can not be
guaranteed anymore. Verify that the indications given on the identification label of the actuator fully correspond to the characteristics of
the electric supply.
Respect all safety rules during fitting, dismantling and porting of this apparatus.
Lifting and carrying through strapping the hand wheel is not allowed.
Do not lift the actuator by the handle (ER10/ER20).
Do not mount the actuator « upside down ». Risks:
Declutching mechanism failure
Possible flow of the grease on the electronic board
Do not mount the actuator less than 30 cm of a electromagnetic disturbances source.
Do not position the equipment so that it is difficult to operate the disconnecting device.
1
CR-TEC Engineering Inc. • info@crtec.com • www.crtec.com • 203-318-9500

Position indicator
Handle with position indicator for ER10/20 and
round indicator for ER 35/60/100
Modular position indicator with three removable position markers (3 yellow +
2 black), adjustable according the type of valve to be actuated
Valve 0° 180°
2-way:
0° = close
90° = open
3-way (L):
3-way (T):
Ex : T1
90°
Emergency manual override
The priority functioning mode of this actuator is electric. Be sure than the power supply is switched off before using the manual
override
1. Turn the knob to position MAN (counter-clockwise) and hold it in position.
2. Turn the outgoing drive shaft of the actuator with the help of an adjusting spanner.
3. In order to re-engage the reduction, release the knob (spring return).
1
2
3
CR-TEC Engineering Inc. • info@crtec.com • www.crtec.com • 203-318-9500
2

Dimensions
Visual position indicator
Nylon
PA6
cover
F03/F05-F04 plate
Ou / Or
Sleeve
9
Nylon GF
PA6 Housing
Clutch
knob 11
Square / Star (mm) Depth (mm)
14 16
17 19
22 24
ISO F flange Diameter (mm)
F03 36
F04 42
F07 70
M threaded Depth (mm)
M5 14.2
M5 14.2
M8 16.4
Screws quantity
4
4
4
F05 50 M6 14.2 / 16.4 4
ER10/20/35
Star 14 (mm)
ER35/60/100
Star 22 (mm)
Handle for manual override
3
CR-TEC Engineering Inc. • info@crtec.com • www.crtec.com • 203-318-9500

CR-TEC Engineering Inc. • info@crtec.com • www.crtec.com • 203-318-9500
4
As stipulated in the applicable regulation, the connection to earth contact is compulsory for devices with working voltages exceed-
ing 42V.
The actuator is always powered, so it must be connected to a disconnection system (switch, circuit breaker) to ensure the actuator
power cut, correctly located, easily reached and marked as being the disconnecting device for the equipment.
An Inrush current may occur when actuators are switched on. Therefore it is necessary to limit the number of actuators on the
same line. Alternatively an inrush current limiter at the output of the circuit breaker may be used.
The terminal temperature can reach 90°C
For a use with a long power supply wiring, the induction current generated by the wires mustn't be higher than 1mA
To optimize the installation security, please connect the failure feedback signal (D1 and D2).
In order to ensure the IP66 tightness, the cable gland for feedback wiring must be used (7 to 12mm cable). Otherwise, the
cable gland must be replaced by a ISO M20 IP66 cap.
Protective
earthing
Ground Direct
voltage
Alternating
voltage
Dangerous
voltage
Electric wiring
Warnings
Instructions
Our cable glands are designed for cables with a diameter between 7mm and 12mm.
The actuator can support MAINS supply voltage fluctuations up to ±10 % of the nominal voltage.
It is necessary to connect all actuators to an electrical cabinet
Remove the position indicator, unscrew the four screws and take off the cover.
SUPPLY AND CONTROL WIRING
Ensure that the voltage indicated on the actuator ID label corresponds to the voltage supply.
Connect the wires to the connector in accordance with the required control mode. (see diagram p.21 (or p.26 for POSI)
models )
To ensure the correct functioning of the anti-condensation heaters, the actuator must be permanently power supplied
WIRING OF THE FEEDBACK SIGNAL (Except POSI: p.25)
Our actuators are equipped with two simple limit switch contacts normally set either in open position, either in closed position
(see wiring diagram DSBA0436). As per factory setting, the white cam is used to detect the open position (FC1) and the black
cam is used to detect the closed position (FC2).
The auxiliary limit switches must be connect with rigid wires. If the applied voltage is higher than 42V, the user must foresee a
fuse in the power supply line.
The voltages applied to each feedback switch (FC1 and FC2, SNAA690000 electronic board) must be exactly the same .The
reinforced insulation between the feedback signal and the motor control authorizes voltages up to 250V AC.
Unscrew the right cable gland and insert the cable.
Remove 25mm of the cable sheath and strip each wire by 8mm.
Connect the wires to the terminal strip in accordance with the diagram p.21 (or p.26 for POSI models ).
Tighten the cable gland (Ensure that it’s well mounted to guaranty the proofness).
Connection to feedback microswitches:
4 to 24 V DC and 12 to 250 V AC
minimum current 100 mA
maximum current 5 A (resistive), 0.5 A (motor), 0.125 A (capacitive loads)
SETTING OF END LIMIT SWITCHES
The actuator is pre-set in our factory. Do not touch the two lower cams in order to avoid any malfunctioning or even damage to
the actuator.
To adjust the position of the auxiliary contacts, make rotate the two superior cams by using the appropriate wrench.
Re-mount the cover, fasten the four screws and attach the position indicator.

Wiring the electrical connector:
1. Remove the connector screw first, and then use a flat screwdriver to pry apart the two
connector halves. Note that the screw placed in the connector locks the two halves
together.
2. The center terminal is an optional ground that is normally used with AC current, and not
normally used with DC current.
3. When used with a solenoid valve, the polarity for the power con-nections is not
important. The two power wires can each be con-nected to either of the side terminals.
With electric motor actua-tors, the polarity should be observed for both AC and DC
opera-tion.
4. Place the connector on the electric motor actuator or solenoid valve coil and hold in
place with the supplied screw.
5. There are two different types of connectors that you may be using, ½” NPT Conduit and
Lead Wire. If you are using the Lead Wire type, a jacketed multi-conductor wire is
recommended. A rubber grommet is compressed around the jacketed conductor to
make a seal. If a tight seal is not important, then any type of wiring can be used.
ELECTRIC WIRING
INSTRUCTIONS - DIN Electrical Connector
5
CR-TEC Engineering Inc. • info@crtec.com • www.crtec.com • 203-318-9500

SNAA690000
FCF
FC0
A
+
—
~
~
FC2
FC1
A
3 2 1
15V-30V 50/60Hz (12V-48V DC)
100V-240V 50/60Hz (100V-350V DC)
C
B
M
18 17
BBPR
version
ON/OFF control
compulsory
GND
COMMON FC1
COMMON FC2
FEEDBACK FC1
FEEDBACK FC2
9 8 7 6 5 4
D2
D1
2
3
1
The terminal temperature can reach 90°C
The used wires must be rigid (feedback voltages : 4 to 250V AC/DC)
FEEDBACK
COMMON FC1/FC2 FEEDBACK FC1FEEDBACK FC2
1
2
3
ECD.1A
Grey connector
9 8 7 6 5 4
1
2
3
SUGGESTED CUSTOMER WIRING
N
-
Open Close
Ph
+
N
-
Open
Ph
+
Modulating 3-point control On-off control
GND GND
2
3
1 2
3
1
REP DESIGNATION
FCO Open limit switch FC1 Auxiliary limit switch 1
FCF Close limit switch FC2 Auxiliary limit switch 2
D1/D2 Failure report Terminal strip (24V DC / 3A max)
POWER SUPPLY : 3P+T DIN43650 CONNECTOR
IF CONNECTOR OPTION (ECD.1A)
IF WIRING TROUGH THE CABLE GLAND
CR-TEC Engineering Inc. • info@crtec.com • www.crtec.com • 203-318-9500
6

Power supply and Control boards
for ER 10-20-35
* Fuses for multivolt boards
- SNAA720100 board: 2A / T 250V (Multicomp MST 2A 250V)
- SNAA720000 board: 500mA / T 250V (Multicomp MST500MA 250V)
- SNAA730100 board: 5A / T 125V (Littelfuse 39615000000)
- SNAA730000 board: 3,15A / T 250V (Multicomp MST 3,15A 250V)
** Possible defects : limitation of current, thermic limitation or program error
=> check that the valve torque is not superior to the maximum torque stand by the actuator
=> check that the actuator do not exceed the duty cycle indicated (possible overheat)
To re-start the actuator, reverse the sense of rotation or switch the power off and on.
SNAA720100
15V-30V 50/60Hz (12V-48V DC)
SNAA720000
100V-240V 50/60Hz (100V-350V DC)
A
B
G
C
F ED
A EF D
B C
G
REP DESIGNATION REP DESIGNATION
A Earth screw E** LED 3 : detected failure
B Power supply and control terminal F LED 1 : power supply presence
D LED 2 : microprocessor ok
*C* Protection fuses G Failure report terminal strip (24V DC - 3A max)
Power supply and Control boards
for ER 35-60-100
SNAA730100
15V-30V 50/60Hz (12V-48V DC)
SNAA730000
100V-240V 50/60Hz (100V-350V DC)
A B G A B
E
F
D
CC C C
E
F
D
G
7
CR-TEC Engineering Inc. • info@crtec.com • www.crtec.com • 203-318-9500
Electronic boards

BBPR models
Actuators with battery backup position recovery system (on-off wiring mandatory)
BBPR models integrate a battery pack monitored by an electronic board inside the actuator. Its function is to re-
lay in case of power supply failure on terminal PIN 1,2 and 3 of the actuator. The BBPR system can be set on
different position like normally open (NO) or normally closed (NC). It depends on the application.
The electronic board monitors the battery pack and check the status of battery (cycle load and failure)
If a battery failure is detected , a contact on PIN 65 and 66 switch off. It’s possible to use this contact to be
aware that there is a failure on battery in the actuator without remove cover and plan the replacement.
BBPR option requires ON/OFF mode.
Loading electronic board
Battery voltage
14.4 V DC
Battery capacity 600 mAh
Charging current 180 mA
initial battery charge duration
3,5 h
Charging status feedback relay 24 V DC - 1 A max
Failure feedback relay (D3/D4)
24 V DC - 3 A max
Temperature
-10 °C to +40 °C
The factory default configuration is "normally closed"
Following a power failure, the BBPR unit will reset after 4 minutes
C1
C2
C5
C4
C6
J1
L7L5L3
L4 L6
C3
L2
L1
DESCRIPTION
C1 17 (-) · 18 (+) power supply connector
C2 F (+) · F (-) · T (+) Battery unit connector
C3 A · B · C Motor connector
C4 1) D3 · D4 Failure feedback connector
C5 1) 65 · 66 Charging feedback connector
C6 A · 0 · B RS485 connector
J1 Bluetooth®activation jumper
1) The auxiliary cables must be connected to inside installation only
CONNECTEUR
DESCRIPTION
L3 ACT
green
Battery status :
Slow blinking (1s) : battery charged.
Rapid blinking (0.5s) : battery charging
L4 ERROR
red
Error detected:
Timestamp memory empty/scheduler selected
Clock failure
Excessive temperature
Excessive torque
L5 HORO
Orange Weekly scheduler functioning mode
L6 MANU
Orange manual / Bluetooth®functioning mode
L7 WIRE
Orange Electric wiring mode
LED
L1 D19
green Actuator operating into opening
L2 D18
red Actuator operating into closing
CR-TEC Engineering Inc. • info@crtec.com • www.crtec.com • 203-318-9500
8

Charging/control BBPR board
Power supply board
100V-240V 50/60Hz (100V-350V DC)
15V-30V 50/60Hz (24V-48V DC)
65
66
F+
F-
F+ : red wire
F- : black wire
T+ : yellow wire
Charging
feedback Charged battery : contact
closed
D2
D1
T+
Battery unit
D3
D4
Failure
feedback
A
0
B
RS485
4
AC
1 3
N
Ouvrir
Ph
2
C
17
18 18
17
B
A
4
5
6
7
A B
COMMON FC1
FEEDBACK FC1
COMMON FC2
FEEDBACK FC2
SNAA690000
M
SNBA130000
BBPR : electric diagram
BBPR : setup
Thanks to AXMART®, it’s possible to set the Initial security position that the actuator will
reach in case of power failure.
it’s also possible to access to battery parameters in real time.
For any further information, refer to the operation manual with the reference DSBA3304.
The BBPR actuators can be only on-off mode wired.
The factory default configuration is "normally closed"
CR-TEC Engineering Inc. • info@crtec.com • www.crtec.com • 203-318-9500
9

POSI model
Various control types (control signal on terminals N°15 and N°16)
On request, our cards can be set in factory. The consign and the feedback signal can have different forms (current or voltage).
Without any information from the customer, the cards are set for current 4-20mA (control + feedback signal)
Control in modes 0-10V and 0-20mA
In case of outside event, absence of control signal (accidental wires cut for example) but in presence of power, the actuator will travel
to defined position (open or closed valve).
In standard our actuators will close themselves in absence of control signal but there are other possibilities on request.
Control in mode 4-20mA
In case of outside event, absence of control signal (accidental wires cut for example) but in presence of power, the actuator will stay in
its position.
In the both cases, when the control signal is restored, the actuator reach automatically the position corresponding to control signal
value.
P6 positioning electronic board (0-20mA / 4-20mA / 0-10V)
G
D
F
E
N
L
I
H
C
B
A
M
J
K
REP DESIGNATION
A 24V AC/DC power supply terminal trip
B Setpoint signal terminal trip
C Feedback signal terminal trip
D Adjustment button MEM
E Adjustment button CLOSE
F Adjustment button OPEN
G K1 shunt
H K2 shunt
I K3 shunt
J Green and red LEDs
K Yellow LED : power supply indication
L Potentiometer
M Motor connexion
N Heating resistor connector
Actionneur déjà préréglé en usine
P6 positioning board wiring (input and output signal)
In order to avoid electromagnetic perturbations, it is compulsory to use shielded cables (cables longer than 3m).
Unscrew the gland and pass the cable.
Connect the setpoint signal between terminals 15 and 16.
Terminal 15 is the negative polarity (-) and terminal 16 is the positive polarity (+).
Connect the feedback signal between terminals 13 and 14.
Terminal 13 is the positive polarity (+) and terminal 14 is the negative polarity (-).
Tighten the cable gland (Ensure that it’s well mounted to guaranty the proofness).
Factory setting : by default, 4-20mA input and output signals with normal rotation direction.
To proceed to a new setting of the card : please see page 27, “Parameter selection sequence”.
To check the proper operation of the card : please see page 27, “Normal operating mode”.
CR-TEC Engineering Inc. • info@crtec.com • www.crtec.com • 203-318-9500
10

POWER SUPPLY : 3P+T DIN43650 CONNECTOR
N
-
Ph
+
1 2
3
GND
3 2 1
15V-30V 50/60Hz (12V-48V DC)
100V-240V 50/60Hz (100V-350V DC)
1 2
3
1817
GND
SNAA690000
FCF
FC0
+
—
~
~
FC2
FC1
FEEDBACK
SIGNAL
SETPOINT
SIGNAL
SNAA380000
16 15 14
13
+
0-20mA / 4-20mA / 0-10V
17 18
– – +
C
P6
POSI
A B
9 8 7 6 5 4
FEEDBACK
COMMON FC1
COMMON FC2
FEEDBACK FC1
FEEDBACK FC2
D2
D1
A
Motor
=
The control voltage must be S.E.L.V. (Safety Extra Low Voltage).
The terminal temperature can reach 90°C.
The feedback must be connect with rigid wires. If the applied voltage is higher than 42V, the user must foresee a fuse in the
power supply line.
For a use with a long power supply wiring, the induction current generated by the wires mustn't be higher than 1mA.
The used wires must be rigid (feedback voltages: 4 to 250V AC/DC).
The card resolution is 1°
10 kOhm input impedance if control with voltage (0-10V)
100 Ohm input impedance if control with current (0-20mA ou 4-20mA)
REP DESIGNATION
FC0 Open limit switch
FCF Close limit switch
FC1 Auxiliary limit switch 1
FC2 Auxiliary limit switch 2
D1/D2 Failure report Terminal strip (24V DC / 3A max)
11
CR-TEC Engineering Inc. • info@crtec.com • www.crtec.com • 203-318-9500

PARAMETER SELECTION SEQUENCE
1 K1, K2 and K3 shunts positioning
Position the shunts as follows (before modification, switch off the card):
2 Selection of the flow direction of the valve
2.1 Normal flow direction (by default)
Press the OPEN button and apply the operating voltage to the card while keeping this button
pressed.
The green LED lights up. Release the OPEN button.
Disconnect the card.
2.2 Inverse flow direction
Press the CLOSE button and apply the operating voltage to the card while keeping this button
pressed.
The red LED lights up. Release the CLOSE button.
Disconnect the card.
3 Selection of the type of input control signal
3.1 Voltage control signal 0-10V
Press the MEM button and apply the operating voltage to the card while keeping this button
pressed.
The red LED will light up 3 times. Release this button.
Disconnect the card.
3.2 Current control signal 0-20mA
Press the MEM and OPEN buttons and apply the operating voltage to the card while keeping these
buttons pressed.
The red LED will light up 3 times. Release these buttons.
Disconnect the card.
3.3 Current control signal 4-20mA (by default)
Press the MEM and CLOSE buttons and apply the operating voltage to the card while keeping these
buttons pressed.
The red LED will light up 3 times. Release these buttons.
Disconnect the card.
4 Learning mode
Press the OPEN and CLOSE buttons and apply the operating voltage to the card while keeping
these buttons pressed.
The 2 LEDs will light up. Release these buttons and the 2 LEDs will run out. The card is now in the
learning mode.
Press the CLOSE button to put the valve in its closed position. The red LED will light up.
Store this selected closed position by pushing MEM + CLOSE, the red LED will light up 2 times as a
confirmation of acknowledgement.
Press the OPEN button to put the valve in its open position. The green LED will light up.
Store this selected open position by pushing MEM + OPEN, the green LED will light up 2 times as a
confirmation of acknowledgement.
Now, the positions selected have been stored. Disconnect the card.
NORMAL OPERATING MODE
Apply the operating voltage to the card. The green LED will light up 3 times.
Under normal operating conditions, the green LED will light up when the drive motor opens the
valve, and the red LED will light up when the drive motor closes it.
If both LEDs remain ran out, it means that the drive motor has not been triggered.
In the case of an over torque, the motor stops and the 2 LEDS lights then together to indicate the action
of the torque limiter. To re-start it, you must either reverse the sense of rotation, either switch the power
off and on.
G
R
R
R
R
G R
R
R
G
G
G
G R
K3 ONK3 OFF
Setpoint
signal
Feedback
signal
Shunt K1
Shunt K3
A B A B
0-10V 0-10V ON OFF ON OFF OFF
0-10V 0-20mA ON OFF OFF ON OFF
0-10V 4-20mA ON OFF OFF ON ON
0-20mA 0-10V OFF ON ON OFF OFF
0-20mA 0-20mA OFF ON OFF ON OFF
0-20mA 4-20mA OFF ON OFF ON ON
4-20mA 0-10v OFF ON ON OFF OFF
4-20mA 0-20mA OFF ON OFF ON OFF
4-20mA 4-20mA OFF ON OFF ON ON
Shunt K2
CR-TEC Engineering Inc. • info@crtec.com • www.crtec.com • 203-318-9500
12

3-position model
Actuator with a third position
GF3 option allow actuator to be drive and stop in 3 positions. These 3 positions could be between 0° to 180°.In standard actuators
are setting in our workshop at 0° 90° 180° that’s fit with standard 3 ways ball valve. Others positions still available but customer have
to price on the order witch position is request.
These 3 positions are controlled by 4 switches (FCO,FCF,FCIO and FCIF) and 3 switches for feed back signal
Switches FC1,FC2 are NO contact ( close the circuit in extreme position) and FC3 is a NC contact (open the circuit in intermediate
position)
Terminals
6 & 9 4 & 8 F4 & F9
0° Closed Open Closed
inter Open Open Open
180° Open Closed Closed
REP DESIGNATION REP DESIGNATION
FCO Open limit switch FC1 Auxiliary limit switch 1
FCF Close limit switch FC2 Auxiliary limit switch 2
FCIO Intermediate open limit switch FC3 Auxiliary limit switch 3
FCIF Intermediate close limit switch D1/D2 Failure report Terminal strip
(24V DC / 3A max)
The terminal temperature
can reach 90°C
M
SNAA710000
FCF
FC0
A
+
—
~
~
9 6 8 4
FC2
FC1
F9 F4
F7 F8
B
FCIF
FCIO
A
3 2 1
15V-30V 50/60Hz (12V-48V DC)
100V-240V 50/60Hz (100V-350V DC)
C
GND
F6 F7 F8
4
N / -
I F O
Ph / +
R B N
COMMON FC1
FEEDBACK FC1
FEEDBACK FC2
FEEDBACK FC3
COMMON FC2
COMMON FC3
FEEDBACK
F6
D2
D1
FC3
POWER SUPPY
13
CR-TEC Engineering Inc. • info@crtec.com • www.crtec.com • 203-318-9500

TECHNICAL DATA
Type (1/4 turn electric actuator) ER10 ER20 ER35 ER35 ER60 ER100
Housing type Small housing (see p.19)
IP protection (EN60529) IP66
(dusts, water spraying « flow <12.5 L/min »)
Corrosion resistance (outdoor and
indoor use)
Housing: PA6 UL94V0 + 25% GF and cover: PA6 UL94V0
Raw material : 304L Stainless Steel or Steel + Zn treatment
Temperature -10°C to +55°C (BBPR GS2: -10°C to +40°C)
Hygrometry maximum relative humidity 80 % for temperatures up to 31 °C decreasing linearly
to 50 % relative humidity at 40 °C
Pollution degree
Altitude altitude up to 2 000 m
Extended environmental conditions Outdoor use and in WET LOCATION
Sound level 61 dB
Weight 1 Kg 2.1 Kg
MECHANICAL DATA
Nominal torque 10Nm 20Nm 35Nm 35Nm 60Nm 100Nm
1/4 turn travel time (standard ER) 11s 11s 25s 7s 12s 23s
1/4 turn travel time (slow ER) 41s 79s 119s
1/4 turn travel time (ER POSI) 25s 41s 79s 119s
Mounting actuator base (ISO5211) Star 14
F03-F04-F05
Star 22
F05-F07
Swing angle 90° (others on request)
Mechanical end stops 90° +/- 5°
Manual override Out axle
Direction of rotation Anticlockwise to open
ELECTRICAL DATA
Voltage ±10% 100 V to 240 V AC 50/60 Hz and 100 V to 350 V DC
15 V to 30 V AC 50/60 Hz and 12 V to 48 V DC
Frequency 50/60Hz
Power consumption 15W (0.08A) cos j = 0.75 45W (0.15A) cos j = 0.75
Overvoltage category TRANSIENT OVERVOLTAGES up to the levels of OVERVOLTAGE CATEGORY ll
TEMPORARY OVERVOLTAGES occurring on the MAINS supply
Torque limiter Electric
Duty cycle (CEI34) 50%
Limit switches maximal voltage 4 to 250V AC/DC
(Overvoltage category II)
Limit switches maximal current 1mA to 5A max
Electrical wiring 1 ISO M20 cable gland and 1 DIN43650 3P+T connector
Inrush current Circuit breaker type D, nominal current according the number of actuators (max. 4 ac-
tuators) or use a inrush current limiter at the output of the circuit breaker.
large housing (see p.19)
Voltage ±10%
(BBPR GS2)
100 V to 240 V AC 50/60 Hz and 100 V to 350 V DC
24 V to 30 V AC 50/60 Hz and 24 V to 48 V DC
CR-TEC Engineering Inc. • info@crtec.com • www.crtec.com • 203-318-9500
14

CR-TEC Engineering Inc.
15 Orchard Park Road, Unit 18
Telephone 203-318-9500 • Fax 203-245-2575
[email protected] • www.crtec.com
Catalog DSBA3200 © 2/02/2023 CR-TEC Engineering Inc.
CR-TEC Engineering Inc.
This manual suits for next models
5
Table of contents
Other CR-Tec Controllers manuals
Popular Controllers manuals by other brands

Sunricher
Sunricher SR-2833t1 quick start guide
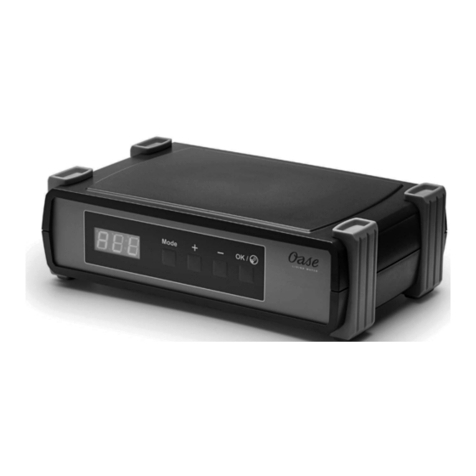
Oase
Oase StreamMax Pump Controller operating instructions
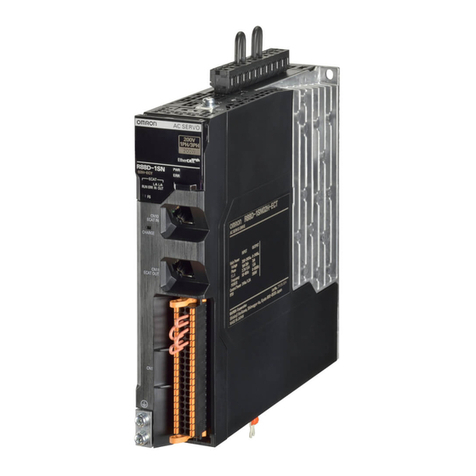
Omron
Omron R88M-1M Series user manual

Gira
Gira 0570 00 operating instructions
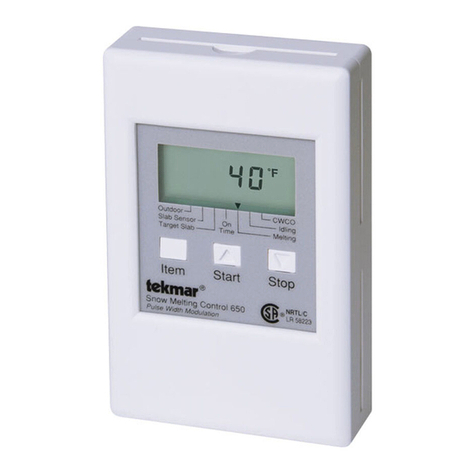
Tekmar
Tekmar D 650 Data brochure
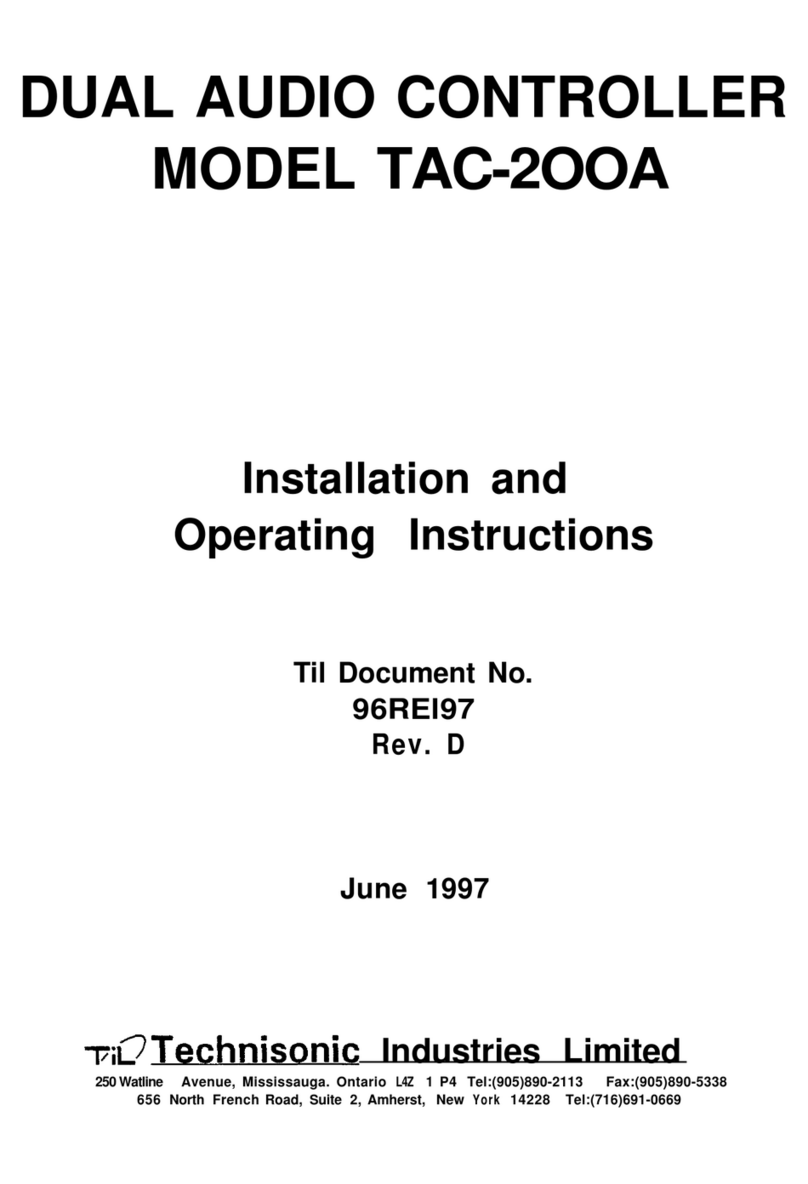
Technisonic Industries Limited
Technisonic Industries Limited TAC-2OOA Installation and operating instructions