CSA VRCD User manual

CSA waterworks line
Direct acting downstream pressure
reducer-stabilizer
Mod. VRCD
Rev. 1 –9/2014

Direct acting PRV Mod. VRCD
2
For further information please consult us at: www.comeval.es
Personnel involved in the installation or maintenance of valves should always be alert
to potential emission of water and pipeline material, and take the necessary safety
precautions. Always wear the suitable protection like helmets, gloves, googles, when
dealing and handling hazardous pipelines and valves.
Introduction
This manual will provide you with the information to properly install and maintain CSA direct acting
pressure reducers Mod. VRCD. The contents and the procedure are intended for technicians in
charge of CSA valves only, prior to a theoretical and practical training by CSA qualified or
authorized personnel.
Safety
All safety messages in the instruction manual are flagged with the following symbol meaning
danger, caution and warning. This means and makes reference to procedures that may lead to
equipment and system damage and to severe injury or death for the personnel involved.
Inspection
Your valve VRCD has been packaged to provide protection during shipment, however it can be
damaged during transport. Please carefully inspect the unit for damages or discrepancies with the
order upon arrival and report a claim immediately before unloading the goods.
Parts
Recommended spare parts are listed on the assembly drawing depicted on page 8.These parts
should be stocked to minimize delays in case of malfunction. When ordering spare parts please
make reference to the assembly drawing and indentification plate present on the valve.

Direct acting PRV Mod. VRCD
3
For further information please consult us at: www.comeval.es
Contents
Description - - - - - - - - - - - - - - - - - - - - - - - - - - - - - - - - - - - - - - - - - - - - - - - - - - - - - - - - - - - 4
Handling and storage - - - - - - - - - - - - - - - - - - - - - - - - - - - - - - - - - - - - - - - - - - - - - - - - - - - - 4
Fusion/Powder coated valves- - - - - - - - - - - - - - - - - - - - - - - - - - - - - - - - - - - - - - - - - - - - - - - 4
Installation - - - - - - - - - - - - - - - - - - - - - - - - - - - - - - - - - - - - - - - - - - - - - - - - - - - - - - - - - - - - 5
Maintenance - - - - - - - - - - - - - - - - - - - - - - - - - - - - - - - - - - - - - - - - - - - - - - - - - - - - - - - - - - -6
Set up - - - - - - - - - - - - - - - - - - - - - - - - - - - - - - - - - - - - - - - - - - - - - - - - - - - - - - - - - - - - - - - 6
Drawings- - - - - - - - - - - - - - - - - - - - - - - - - - - - - - - - - - - - - - - - - - - - - - - - - - - - - - - - - - - - - -7
Troubleshooting- - - - - - - - - - - - - - - - - - - - - - - - - - - - - - - - - - - - - - - - - - - - - - - - - - - - - - - - -9
Problem solving - - - - - - - - - - - - - - - - - - - - - - - - -- - - - - - - - - - - - - - - - - - - - - - - -- - - - - - - - 10
Disassembly- - - - - - - - - - - - - - - - - - - - - - - - - - - - - - - - - - - - - - - - - - - - - - - - - - - - - - - - - - 11
Reassembly------ - - - - - - - - - - - - - - - - - - - - - - - - - - - - - - - - - - - - - - - - - - - - - - - - - - - - - - 12

Direct acting PRV Mod. VRCD
4
For further information please consult us at: www.comeval.es
Valves with fusion/powder coated exterior paint require flat washers to be installed
under the flange nuts when installing the valve to the pipeline flange, to prevent the
paint from cracking or chipping.
Personnel involved in the installation or maintenance of valves should be constantly
alert to possible damages caused by an improper handling of the valve.
Description
The automatic direct acting PRV Mod. VRCD consists of a upstream pressure balanced single seat
globe pattern valve, piston actuated, and equipped with a spring located in the cover to impart the
force necessary for the proper working. The operating principle is explained on the technical
catalogue, for further explanations please contact us. The VRCD will automatically throttle and
modulate the water supply to maintain a pressure downstream, regardless of upstream pressure
fluctuations. The special design of CSA with built in self cleaning piston technology guarantees
long lasting performances with a dramatic reduction of the maintenance time, minimizing the risk of
friction and malfunctioning.
Handling and Storage
Lifting the valve improperly may damage it. Lift the valve with slings, chains or cables fastened
around the valve body or eyebolts if present, or fastened to bolts or rods through bolt holes in the
flanges. Do never lift the valve by the adjusting screw. If installation will be delayed, place valve
indoors in secure, weather tight storage. If temporary outside storage is unavoidable, make sure a
vermin proof rain cover is secured around/over the valve to keep off rain and mud. Skid and set the
assembly on a flat, solid, and well drained surface for protection from ground moisture, runoff and
pooled rain water. Do not leave the valve exposed to high humidity and excessive temperature
conditions.
Fusion/Powder Coated Valves

Direct acting PRV Mod. VRCD
5
For further information please consult us at: www.comeval.es
The difference in pressure generated by the valve when closed or during closing will
produce a thrust proportional to the pressure itself.
Anchorage blocks and way of preventing valve’s movement or shifting need to be
taken into account.
Installation
The float valve should always be installed in a horizontal position, meaning the axis of the valve
versus the ground level. Vertical installation is allowed up to the DN 100 mm prior to consult with
us. The valve has to be installed between two sectioning devices, one upstream and one
downstream to allow for maintenance, with a filter upstream of it to prevent dirt from creating
malfunctioning. For the recommended flow rate and differential pressure please refer to the sizing
information displayed in the catalogue or contact us sending the project data for further assistance.
Before installation, remove foreign material such as weld spatter, oil, grease, and dirt from
the pipeline.
Prepare pipe ends and install valves in accordance with the pipe manufacture’s instructions
for the joint used.
Tighten the flange bolts or studs in a crisscross pattern and minimum of four stages.
Place the valve in the right direction following the arrow moulded on the body
If not included in the order install a pressure gauge upstream to check the maximum static
pressure reached during closing and make sure it doesn’t exceed the valve’s design
pressure
Note to Engineer: The direct acting pressure reducing valve VRCD will regulate and
maintain a downstream pressure value according to the force of the spring, located inside
the cover, supplied with three different versions to cover :
Downstream pressure regulation from 1.5 to 6 bar (blue spring, standard)
Downstream pressure regulation from 5 to 12 bar (red spring, standard)
Downstream pressure regulation from 5 to 12 bar (blue spring, on request)
The spring range is usually indicated on the stainless steel identification plate and on the
order confirmation, should the pressure needed be outside of it contact us for an immediate
replacement of the spring, do not exert excessive torque on the spring or relief it completely

Direct acting PRV Mod. VRCD
6
For further information please consult us at: www.comeval.es
When the valve reacts to modulate, in reducing the downstream pressure, the effective pressure
variation on the line depends on the length of the entire system and part of the network subject to
the VRCD. This could take sometimes minutes, therefore allow for it before acting on the spring.
The flow rate is an effect of the pressure reduced by the VRCD for that specific system. A certain
outlet pressure value, for an instance 3 bar, wouldn’t produce the same flow rate everywhere as it
depends on headloss between the valve itself and the final boundary conditions.
Maintenance
The pressure reducer VRCD is sturdy and reliable, and it was designed to minimize maintenance.
A semi-annual visual inspection for the proper movement of the piston and the cleaning of the
compensation chamber is recommended. A routine maintenance for gasket, control, o-rings and if
needed replacements is recommended every 4 years and explained on page (11) ref picture 1 on
page 7. A possible malfunction can be identified by a leakage through the seat, normally caused by
dirt accumulated inside the body, seeping through the shaft and leaking through to the cover,
hunting and excessive variation of the downstream pressure.
Set up
Before the start-up of the valve make sure the instructions provided on the maintenance
section “Installation” on page 5 were properly followed and understood.
Operate very slowly on the following procedure to avoid stresses on the valve and
unexpected pressure surges.
The valve is initially isolated from the main line by means of the sectioning devices
upstream and downstream.
Open the upstream gate valve by 30%, then open slowly the downstream sectioning device
to generate some flow through the valve. Make sure the maximum nominal pressure is not
exceeded during this operation
Unless the valve has been ordered with a specific setting turn the adjusting screw (9)
anticlockwise to relief the spring (not completely), make sure VRCD will respond with a
smooth modulation by reducing the downstream pressure.
Open completely the upstream gate valve.
Let VRCD work and modulate according to the demand, act on the adjusting screw (9) by
turning it clockwise to increase the downstream pressure and check the pressure gauges.
Allow for enough time for the system to balance.
By means a pressure gauge upstream and downstream and a flow meter make sure that
both the flow rate and difference in pressure, in dynamic condition, doesn’t go above the
recommended values displayed in the catalogue.
Be sure to allow for 5 mt increase in the set pressure occurring between dynamic and static
(no flow) conditions

Direct acting PRV Mod. VRCD
7
For further information please consult us at: www.comeval.es
Drawings
Picture 1
9
8
7
4
5
21
10
14
11
12
25
29
1
24
15
20
28
23
19
22
27
18
3
26
13
17
16
6
2

Direct acting PRV Mod. VRCD
8
For further information please consult us at: www.comeval.es
DESCRIPTION
POS. MATERIAL
1 Body GJS 500-7
2 Cap GJS 500-7
3 Upper piston S.S. AISI 303
4 Spring SiCr
5 Upper ring S.S. AISI 304
6 Nuts S.S. AISI 304
7 Spring guide Brass/S.S. AISI304
8 Nut S.S. AISI 304
9 Driving screw S.S. AISI 304
10 Tap for pressure gauges Brass
11 Guiding screw S.S. AISI 303
12 Spacer Brass/S.S. AISI304
13 Sliding ring Ptfe
14 Lower piston Brass/S.S. AISI304
16 Studs S.S. AISI 304
15 Driving tap Brass/S.S. AISI304
17 Nuts S.S. AISI 304
18 Lower ring Bronze
19 Obturator sealing seat S.S. AISI 304
20 Obturator guide S.S. AISI 304
21 Gasket NBR
22 Gasket NBR
23 O-ring NBR
24 O-ring NBR
25 O-ring pair NBR
26 O-ring NBR
27 O-ring NBR
28 Plane gasket NBR/VULKOLAN
29 Gasket support Brass
Spare parts nr: 4 –13 –19 –21- 22 –23 –24- 25 –26 –27 –28

Direct acting PRV Mod. VRCD
9
For further information please consult us at: www.comeval.es
Troubleshooting
Condition
Possible Cause
Corrective Action
Valve leaks at flange joint.
Loose flange bolting.
Tighten flange bolting.
Blown flange gasket.
Replace flange gasket.
Miss-alignment or damage
to field piping and supports.
Adjust miss-alignment or
repair piping or supports.
Damaged flange face/s or
improper flange
connections.
Repair flange, replace
valve body or adjust flange
connections.

Direct acting PRV Mod. VRCD
10
For further information please consult us at: www.comeval.es
Problems solving
Problem
Cause
Solution
The valve
doesn’t close
There is dirt accumulated between
the obturator and the seat
Remove the valve and clean it inside to
remove dirt
The pressure downstream is below
the set point
Check the pressure coming into the
circuit
There is dirt inside causing friction
to the piston
Check the movement of the piston and
remove dirt or foreign materials
The plane gasket of the obturator/
seat and / body is damaged due
cavitation and the valve can’t
assure a watertight sealing any
more
Check the difference in pressure,
operating cycles of the valve, flow rate.
Make sure they don’t exceed the advised
values from our technical literature
The
valve
doesn’t
open
The spring is corroded and filled
with water, causing the loss of
force
Check if the VRCD has been submerged
by water, check the spring inside the
cover and replace if necessary
There is dirt accumulated between
the obturator and the body
Remove the valve and clean it inside to
remove dirt
There is dirt causing friction to the
piston during its movement
Check the movement of the piston and
remove dirt or foreign materials

Direct acting PRV Mod. VRCD
11
For further information please consult us at: www.comeval.es
Do not remove the nuts (17) holding the cover without having completely relieved the spring by
turning the screw (9) anticlockwise. Inattention may cause severe damages and injuries to the
personnel .
1) Disassembly
In order to carry out the proper maintenance of VRCD proceed as follows, ref drawing picture 1 on
page 7, for further info consult our technical support :
1. slowly close the upstream and downstream gate valves;
2. if the VRCD is installed in a location not suitable for maintenance, please remove it from
the pipe ;
3. turn the screw (9) anticlockwise to relief the spring (4)
4. remove the nuts holding the cover (17)) and take out the cover (2) and spring (4)
5. be sure not to loose the spring guide (7) when the spring is removed
6. push the upper piston (3) downwards
7. remove the driving tap (15), the hexagonal part of the guiding screw (11) will be visible
8. set the hexagonal part with a wrench and keep it steady while unscrewing the first nut
(6) holding the piston tight
9. push up the guiding screw (11) remove the second nut too (6)
10. pull out the upper piston (3) separating it from the lower piston (14), during this phase
make sure not to damage the o-ring (25), check the latter and replace it if necessary
11. check the lip gasket (21) for possible dirt or sign of wear , clean and replace it if
necessary
12. check the guiding ring (5) and the upper piston surface making sure no sign of ear,
scratches are present
13. pull out the lower piston (14) and check for the lip gasket (22) making sure there is no
sign of dirt, foreign materials or damages, clean or replace it if necessary.
14. remove the spacer (12)
15. drop down the remaining driving screw (11) with the obturator (20-28-29) block laying
on the bottom of the valve
16. push the driving screw (11) downwards through the hole where the tap was (15) , the
obturator block (20-28-29) remaining inside the body
17. extract the obturator block from the downstream side
18. paying attention to the o-ring (25), check it and replace if necessary
19. remove the gasket support (29) from the obturator guide (20) and check the status of
the plane gasket (28) for possible sign of cavitation, scratches, dirt. Clean and replace it
if necessary
20. check the downstream side of the reducer for possible sign of cavitation, holes
21. check the surface of the upper ring (5) , lower ring (18) and seat (19) for possible
scratches, dirt. Clean it and replace if necessary. If so make sure not to damage the
o.rings present for the water tightness of all of them.

Direct acting PRV Mod. VRCD
12
For further information please consult us at: www.comeval.es
1) Reassembly
In order to carry out the proper reassembly of VRCD follow the instruction explained on page 12 in
reverse. Pay attention to:
1) use a proper grease on the guiding bush, o-ring, lip gaskets to allow for the proper
movement of the mobile block.
2) Once the mobile block composed of the obturator block, upper and lower pistons, spacer, is
assembled check for the proper movement making sure there are not sign of friction or any
other element affecting it.
Contact us for further assistance
We reserve the right to incorporate our latest design and material changes without notice or obligation.
Design features, materials of construction and dimensional data, as described in this manual, are provided for your information only.
Table of contents
Other CSA Control Unit manuals
Popular Control Unit manuals by other brands
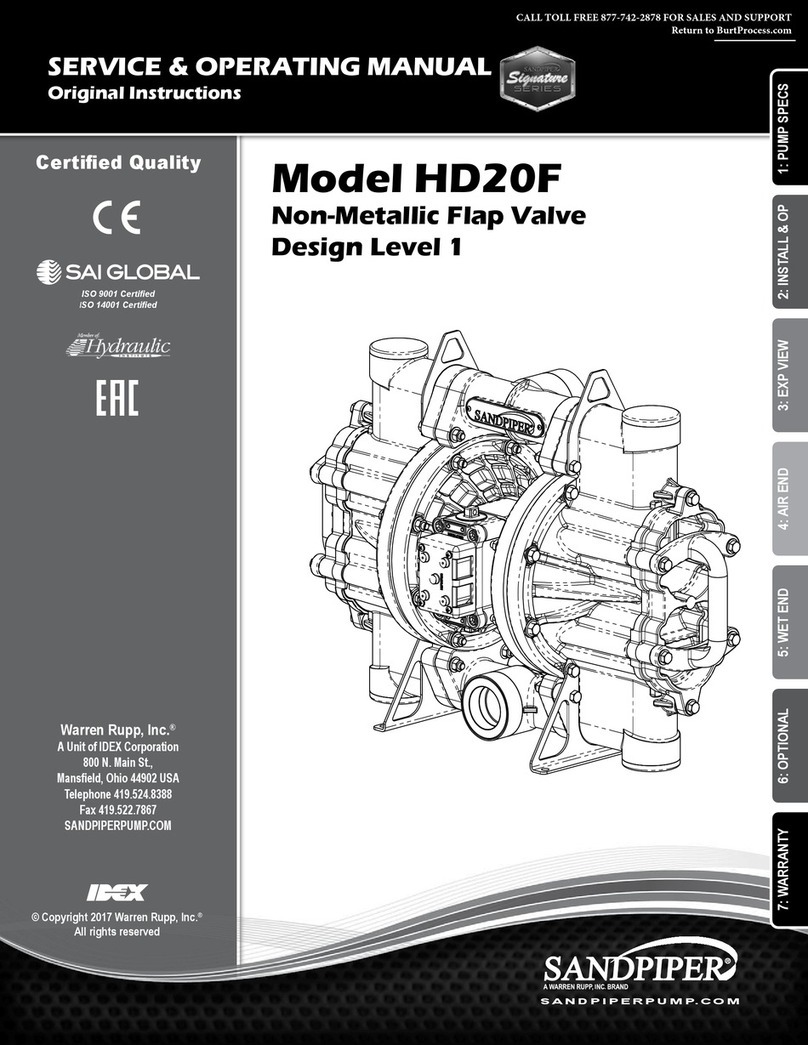
Warren rupp
Warren rupp Sandpiper HD20F Service & operating manual
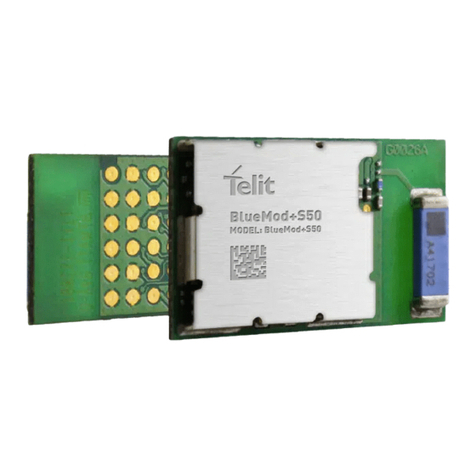
Telit Wireless Solutions
Telit Wireless Solutions BlueMod+S50/AI Hardware user's guide
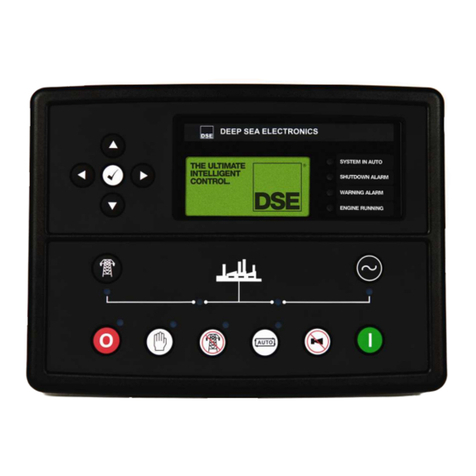
DSEGenset
DSEGenset DSE7400 Operator's manual
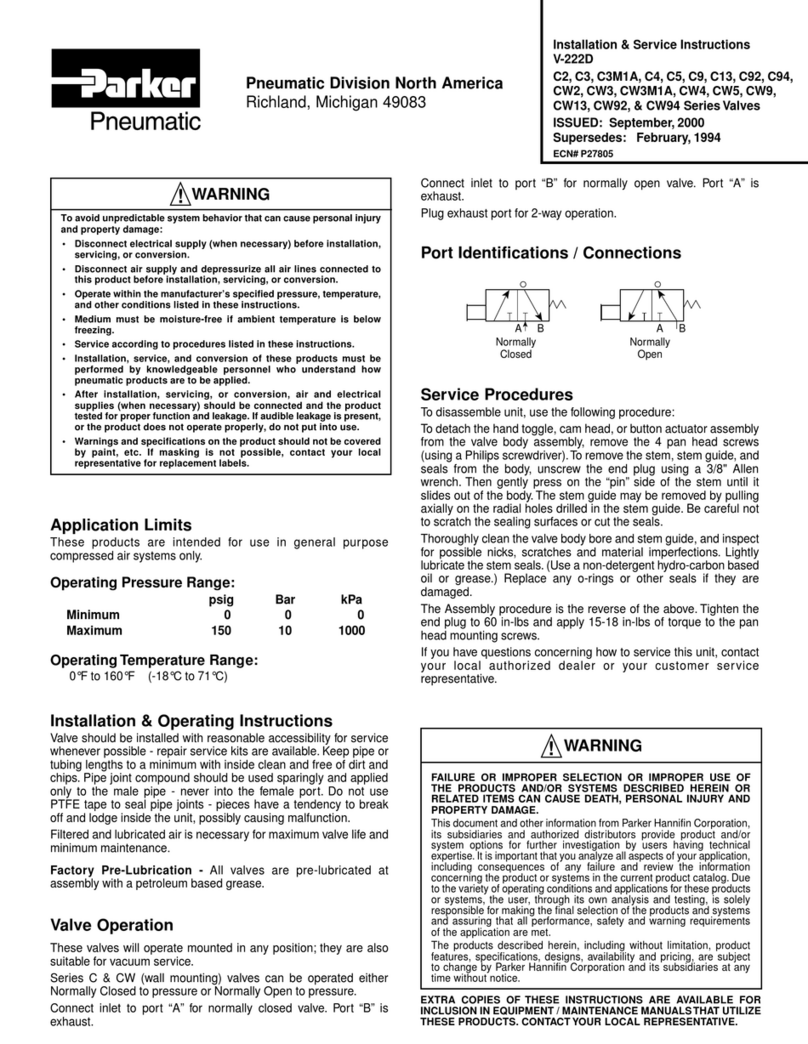
Parker
Parker C2 Series Installation & service instructions
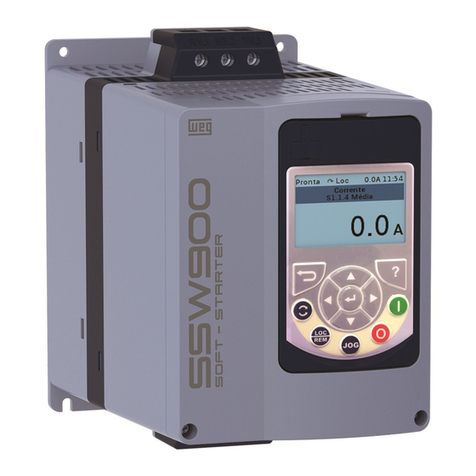
WEG
WEG SSW900-CDN-N Installation, configuration and operations guide
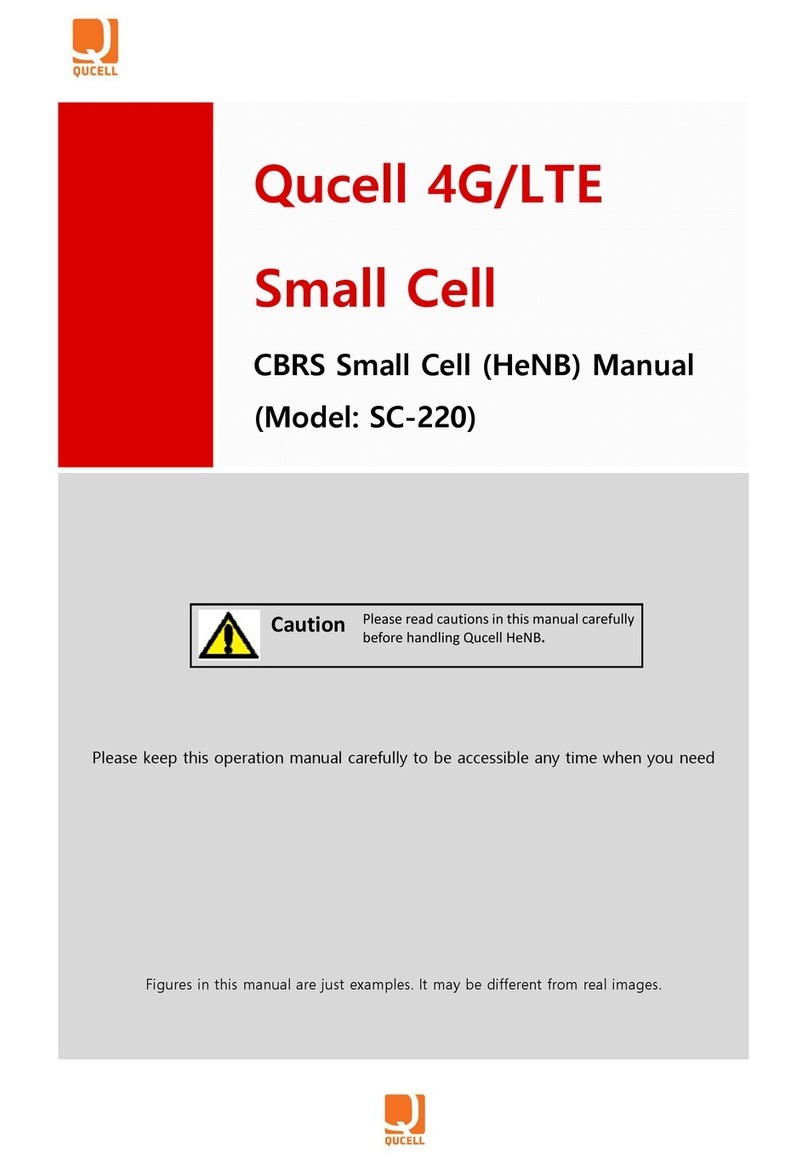
Qucell
Qucell SC-220 manual