CVS RPO 200 User manual

Operating instructions
CVS Compressor RPO 200/300/400/600/800
Doc-ID: 5001 / BA / EN
Release: Rev. 20 / 28.03.2023
The operating instructions must be read by the operator of the compressor and before start-up!

2
Translation of the original operating manual
© CVS engineering GmbH
Großmattstraße 14
79618 Rheinfelden / Germany
Phone: +49 (0)7623 71741-0
Customer service: +49 (0)7623 71741-0
Internet: www.cvs-eng.de

CVS Compressor RPO 200/300/400/600/800
Contents
3
1General...............................................................................6
Information regarding the operating instructions ......6
Pictogram explanation ..............................................7
Limitation of Liability .................................................8
Copyright protection..................................................8
Scope of delivery and goods receiving.....................9
Spare parts ...............................................................9
Warranty conditions..................................................9
Customer Service ...................................................10
Declaration of Incorporation Declaration of
Conformity...............................................................10
2Safety ...............................................................................11
Intended use...........................................................11
Operator's responsibility .........................................11
Operating personnel ...............................................12
2.3.1 Requirements..........................................12
Personal protective equipment...............................12
Occupational safety and special risks ....................13
3Technical data .................................................................18
Dimensions RPO 200/300/400/60013).....................18
Dimensions RPO 600/80013)...................................19
Technical data.........................................................20
Rating plate.............................................................22
4Design and function of the compressed air system ...23
Design.....................................................................23
Function..................................................................25
4.2.1 Functional principle of the construction of
the compressor........................................27
Components............................................................28
4.3.1 Air filter (Fig. 5: Pos. 126)........................28
4.3.2 Oil filter (Fig. 5: Pos. 100/32)...................28
4.3.3 Minimum pressure valve (Fig. 7:
Pos. 150).................................................28
4.3.4 Electric motor (Fig. 7: Pos. 239)..............28
Oil cooler (Fig. 5: Pos. 190)....................................28
Thermostat (Fig. 5: Pos. 100).................................28
Safety and shutoff functions ...................................29
4.6.1 Safety valve 14 barg(Pos. 145)...............29
4.6.2 Safety temperature switch (Pos. 161).....30
Options....................................................................31
4.7.1 Sound proof hood....................................31
4.7.2 Oil level monitor (Pos. 227).....................31
4.7.3 Compressed air dryer..............................32
5Transport and storage....................................................33
Safety notes for transport .......................................33
Transport.................................................................33
Storage ...................................................................34
5.3.1 Storage for a period of more than 3
months.....................................................34
5.3.2 Recommissioning of stored
compressors............................................34
5.3.3 Storage or standstill of compressors
installed in the vehicle .............................34
6Installation and assembly ..............................................36

CVS Compressor RPO 200/300/400/600/800
Contents
4
Safety at installation and assembly........................ 36
Installation diagram................................................ 36
Installing the compressor....................................... 37
Drive....................................................................... 40
6.4.1 V belt drive.............................................. 40
Oil cooler................................................................ 41
6.5.1 Cooling oil lines....................................... 42
Line connection (pressure line).............................. 42
Cyclone separator.................................................. 43
Relief valve............................................................. 43
Safety equipment and control elements................. 44
6.9.1 Safety valve (on site).............................. 44
6.9.2 Pressure monitor (on site) ...................... 44
Oil level monitor (optional) ..................................... 44
Cyclone separator or micro filter............................ 45
Pulsations (pulsation damping valve) .................... 45
Sound proof hood................................................... 45
Electrical connection.............................................. 46
7Start-up and operation................................................... 47
Safety during start-up............................................. 47
Start-up .................................................................. 47
Operation after long standstill or after extended
storage ................................................................... 48
Longer standstill..................................................... 49
Operation ............................................................... 49
Operation modes.................................................... 49
7.6.1 Load intermittent duty (LA) ..................... 50
7.6.2 Load idle intermittent duty (LLA)............. 50
7.6.3 Load idle drying run intermittent duty
(LLTA)..................................................... 51
7.6.4 Load idle intermittent duty with externally
controllable drying run (LLA-T)............... 52
8Maintenance.................................................................... 53
Safety during maintenance work............................ 53
Cleaning................................................................. 53
Maintenance schedule........................................... 53
Oil level check and oil change ............................... 55
8.4.1 Oil level check......................................... 55
8.4.2 Fill oil....................................................... 56
8.4.3 Oil change............................................... 58
Safety valve at the compressor (Pos. 145)............ 60
8.5.1 Functional testing.................................... 62
8.5.2 Ventilate the compressor........................ 62
Cyclone separator (Pos. 204)................................ 63
8.6.1 Check the cyclone separator.................. 63
8.6.2 Clean the cyclone separator................... 64
Clean or blow out screen insert (Pos. 88) and oil
return nozzle (Pos. 85) of the oil return.................. 64
Air filter (Pos. 126) ................................................. 66
Oil filter (Pos. 100/32) ............................................ 68
Oil cooler (Pos. 190) .............................................. 70
Air deoiler element (Pos. 65) ................................. 71
Oil level monitor (Pos. 227).................................... 75
8.12.1 Checking the oil level monitor................. 75
8.12.2 Dismantling and cleaning of the oil level
monitor.................................................... 75

CVS Compressor RPO 200/300/400/600/800
Contents
5
Air suction regulator with non-return valve
(Pos. 30/55, Pos. 30/57).........................................77
Minimum pressure valve (Pos. 150).......................79
8.14.1 Maintenance of the minimum pressure
valve........................................................79
8.14.2 Check minimum pressure valve..............81
Compressor stage (Pos. 30)...................................82
Electric motor..........................................................82
Hose lines and compensators ................................82
9Malfunctions....................................................................83
Safety during troubleshooting.................................83
10 Spare and maintenance parts........................................87
10.1.1 Assembly drawing of compressor RPO
200…800 (drawing no.: 940 086-00) ......88
10.1.2 Compressor stage RPO 200…800
(drawing no.: 940 071-00).......................89
10.1.3 Oil temperature controller RPO 200…800
(drawing no.: 940 040-00).......................90
10.1.4 Assembly drawing of unit and accessories
RPO 200…800 (drawing no.: 250 176-
00) ...........................................................91
Maintenance parts ..................................................92
11 Decommissioning and disposal....................................93
12 EU Declaration of Incorporation....................................94
13 UK Declaration of Incorporation....................................95
14 EU Declaration of Conformity........................................96
15 UK Declaration of Conformity........................................97
Index.........................................................................................98

CVS Compressor RPO 200/300/400/600/800
General
6
1 General
Information regarding the operating instructions
These operating instructions provide important information on how
to deal with the compressor type RPO.
A precondition for safe operation is the observance of all safety
and handling instructions specified in these operating instructions.
Furthermore, all local accident prevention regulations and general
safety regulations valid for the application area of the compressor
must be observed.
Carefully read the operating instructions before starting any work! It
is a product component and must be kept in direct proximity of the
compressor, well accessible to the personnel at all times.
When passing the compressor on to third parties, the operating
instructions must also be handed over.

CVS Compressor RPO 200/300/400/600/800
General
7
Pictogram explanation
Warning notes
Warning notes are characterised by pictograms in these operat-
ing instructions. The warning notes are marked by signal words
expressing the extent of the hazard.
It is absolutely essential to observe the notes and to proceed
with caution in order to prevent accidents as well as bodily inju-
ries and property damage.
DANGER!
points to an immediately dangerous situation, which
can lead to death or serious injuries if it is not
avoided.
WARNING!
... points to an immediately dangerous situation,
which can lead to death or serious injuries if it is not
avoided.
ATTENTION!
... points to a potentially dangerous situation, which
can lead to minor or light injuries if it is not avoided.
CAUTION!
... points to a potentially dangerous situation, which
may lead to property damage if it is not avoided.
Hints and recommendations
NOTE!
… highlights useful hints and recommendations
as well as information for an efficient and trouble-
free operation.

CVS Compressor RPO 200/300/400/600/800
General
8
Limitation of Liability All specifications and notes in these operating instructions were
compiled with consideration to the valid standards and regulations,
the state of the art as well as to our long-standing knowledge and
experience.
The manufacturer is not liable for damages caused by:
Failure to follow the operating instructions
Improper use
Deployment of non-trained personnel
Arbitrary modifications
Technical changes
Use of non-approved spare and wear parts
The actual scope of supply may differ from the explanations and
illustrations described in this manual in case of special designs, if
additional order options are made use of, or due to latest technical
changes.
Incidentally, the responsibilities agreed upon in the delivery con-
tract, the general terms and conditions as well as the manufactur-
er's conditions of delivery and the statutory provisions valid at the
time of contract conclusion shall apply.
Warranty
The manufacturer guarantees the correct functioning of the ap-
plied process technology and the performance parameters identi-
fied.
The warranty period commences on the date the compressor is
delivered to the customer.
Components are exempted from the warranty and from claims
for defects as far as wear and tear damage is concerned.
→Also see page 92, Chapter 10.2.
Copyright protection Surrendering the operating instructions to third parties without writ-
ten permission of the manufacturer is not permitted.
NOTE!
Content details, texts, drawings, pictures and other
illustrations are protected by copyright and are sub-
ject to industrial property rights. Any improper use
shall be liable to prosecution.
Any type and form of duplication also of extracts as well as the ex-
ploitation and/or communication of the contents are not permitted
without the manufacturer’s written declaration of consent.

CVS Compressor RPO 200/300/400/600/800
General
9
Scope of delivery and goods receiving
Immediately check the delivery after receipt for completeness and
transport damages. The scope of delivery is indicated on the deliv-
ery note.
Proceed as follows in the case of outwardly recognisable transport
damage:
Do not accept the delivery or only under reserve.
Note the extent of damage on the transport documents or on
the delivery note of the forwarder.
Lodge complaint.
NOTE!
Lodge a complaint for each defect, as soon as it is
recognised. Compensation claims can only be sub-
mitted within the valid complaint periods.
Spare parts
WARNING!
Risk of injury by incorrect spare parts!
Incorrect or defective spare parts can result in
damage, malfunctions or total failure and also im-
pair safety.
Therefore:
–Use only the manufacturer's original spare
parts.
Procure spare parts directly from the manufacturer or from author-
ised dealers.
Warranty conditions
Warranty terms see "General Terms of Sale".

CVS Compressor RPO 200/300/400/600/800
General
10
Customer Service Our customer service can be contacted for any technical advice.
Information about the responsible contact person can be retrieved
by telephone, fax, E-mail or via the Internet at any time, refer to
manufacturer's address on page 2.
Declaration of Incorporation
Declaration of Conformity
Declaration of Incorporation and Declaration of Conformity, refer to
page 94ff.

CVS Compressor RPO 200/300/400/600/800
Safety
11
2 Safety
Intended use
The compressor type RPO is intended exclusively for the com-
pression of cleaned, atmospheric air.
Use the compressor only as intended.
All specifications in the operating instructions must be strictly ad-
hered to (technical data, operating data, permissible working
range), refer to the respective chapters in this regard.
All types of claims due to damage arising from improper use are
excluded. The operator alone shall be responsible for any damage
arising from improper use.
Operator's responsibility
The compressor is used for industrial purposes.
The operator of the compressor is therefore subject to the legal
obligations concerning occupational safety.
The provisions valid at the place of installation as well as the safety
and accident prevention regulations of the Institution for statutory
accident insurance and prevention must be observed. The operator
must in particular:
inform himself on the valid industrial safety regulations.
determine the additional hazards that arise from the special
working conditions at the compressor's place of installation by
means of a hazard assessment.
implement the necessary rules of conduct for operation of the
compressor at the place of installation by means of user instruc-
tions.
check at regular intervals during the compressor's entire period
of use whether the user instructions correspond to the current
state of the body of rules and regulations.
adapt the operation instructions, if necessary to the new regu-
lations, standards, and operating conditions .
clearly regulate the responsibilities for installing, operating,
maintaining and cleaning the compressor.
ensure that all employees working on or with the compressor
have read and understood the operating instructions. In addition
he must at regular intervals train the employees in how to deal
with the compressor and inform them about potential hazards.

CVS Compressor RPO 200/300/400/600/800
Safety
12
In addition, it is the operator's responsibility to ensure that:
the machine is always in a technically perfect condition.
the machine is maintained in accordance with specified mainte-
nance intervals.
all safety equipment is regularly checked for completeness and
correct functioning.
Operating personnel
2.3.1 Requirements
WARNING!
Risk of injury in case of inadequate qualifica-
tion!
Improper handling can lead to considerable bodily
injuries and property damage.
Therefore:
–Have any activities only carried out by the indi-
viduals designated for that purpose.
The operating instructions specify the following qualification re-
quirements for the different fields of activity:
Instructed persons
have been instructed during instructions provided by the opera-
tor with regard to the work assigned to them and possible haz-
ards arising from improper conduct.
Specialised staff
is due to its technical training, knowledge and experience as
well as due to its knowledge of the pertinent regulations able to
carry out the work assigned to it and to independently recognise
potential hazards.
Electrical specialised staff
is due to its technical training, knowledge and experience
as well as due to its knowledge of the pertinent regulations
able to evaluate, carry out the work assigned to it and to
independently recognise potential hazards.
Personal protective equipment
When handling the compressor, it is necessary to wear personal
protective equipment, in order to minimise health hazards.
Before carrying out any work, properly don the necessary pro-
tective equipment such as gloves, safety goggles, etc. and wear
during work.

CVS Compressor RPO 200/300/400/600/800
Safety
13
Occupational safety and special risks
The remaining risks that result from the hazard analysis are speci-
fied in the following section.
Observe the safety notes listed here and the warning notes in the
other chapters of these instructions to reduce health hazards and
to avoid dangerous situations.
Danger pictograms of the compressor
The relevant dangerous spots on the compressor are identified by
these pictograms:
DANGER!
Mortal danger due to electric current!
... identifies life threatening situations caused by
electric current. Non-observance of the safety
instructions can result in severe injuries or
death. Necessary work may only be carried
out by an electrical specialist.
DANGER!
General danger pictogram!
… denotes general dangerous situations for indi-
viduals. Non-observance of the safety instruc-
tions can result in severe injuries or death.
DANGER!
Danger of burns!
… denotes the presence of a hot surface.
DANGER!
Rotating parts!
… marks that there are rotating parts here. Non-
observance of the safety instructions can re-
sult in severe injuries or death.

CVS Compressor RPO 200/300/400/600/800
Safety
14
Hazard notes and occupational safety
For your own safety and that of the machine, the following in-
formation must be observed and complied with:
Improper operation
DANGER!
Danger due to improper operation!
–Only use compressor in a perfect technical
condition. Malfunctions that are relevant for
safety have to be promptly eliminated.
–Conversions of the compressor are not per-
missible and can impair safety.
–Before carrying out regular maintenance,
cleaning and repair work, switch off power
supply and secure compressor against re-
starting (switch off drives).
–Never bridge any safety equipment or put it
out of operation.
–Any work on the compressor and/or on electri-
cal equipment must be carried out by special-
ised staff.
–Repair and maintenance work may only be
carried out when the compressor is stationary.
For this, the compressor must be secured
against restarting!
–The compressor may not be under pressure
or negative pressure while work is being car-
ried out on it.
Close the shut-off valve on the plant side and
vent the line between the compressor and the
shut-off valve. Manually relieve the compres-
sor overpressure at the safety valve. Observe
pressure gauge!
–The drive's protective equipment may only be
removed when the compressor is stationary
and has to be correctly refitted after comple-
tion of work.
–Only dismantle accidental contact protection
after compressor and pressure pipe have
cooled down.
–It is an environmental protection requirement
that any liquids arising during maintenance
work (e.g. oil) must be collected and disposed
of in an environmentally compatible manner.

CVS Compressor RPO 200/300/400/600/800
Safety
15
Moving components
WARNING!
Risk of injury by moving components!
Powered rotating components can cause the
most serious injuries!
Therefore during operation:
–It is absolutely forbidden for persons to stay in
the hazard area or in the immediate vicinity!
–Do not put safety devices and/or functions out
of operation and do not render them inopera-
tive or bypass them.
–Never reach into open outlets and inlets or
into running equipment.
Before entering the hazard area:
–Switch off power supply and secure against
restarting.
–Wait for standstill of lagging components.
–Wait for automatic dissipation and/or dis-
charge of residual energies (compressed air).
Compressed air
WARNING!
Risk of injury due to compressed air!
Pneumatic energies can cause the most serious
injuries.
In the case of damage to individual components,
air can be discharged under high pressure and
injure e.g. the eyes. Therefore:
–Before starting any work, first depressurise
pressurised components. Pay attention to ac-
cumulators. Accumulator pressure must also
be completely relieved.
Signposting
WARNING!
Risk of injury by illegible pictograms!
Labels and signs can become dirty or unrecog-
nisable in the course of time.
Therefore:
–Always keep safety, warning and operating in-
structions in a well legible condition.
–Immediately replace damaged or obliterated
signs or labels.

CVS Compressor RPO 200/300/400/600/800
Safety
16
Improper transport
DANGER!
Danger by falling down or tilting of the com-
pressor!
The weight of the compressor may injure a per-
son and cause serious bruising!
Therefore:
–Depending on the dead weight and size of the
compressor, use a pallet on which the com-
pressor can be moved by means of a fork lift.
–For lifting the compressor, use suitable lifting
gear (slings, eye bolts etc.) that is designed
for the weight of the compressor.
–When putting the slings in position, take care
to avoid putting to much stress on individual
components.
–Only use the intended transport borings.
Start-up, operation
WARNING!
Risk of injury due to improper start-up and
operation
Improper start-up and operation can lead to seri-
ous bodily injuries or property damage. There-
fore:
–Have all work during initial operation exclu-
sively performed by the manufacturer's em-
ployees or by his authorised representatives
or by trained personnel.
–Start-up and operation may only be performed
by adequately qualified personnel that has
been authorised and instructed by the opera-
tor.
–Before the start of any work, ensure that all
covers and protective devices are correctly in-
stalled and function correctly.
–Never override any protective equipment dur-
ing operation.
–Pay attention to tidiness and cleanliness in
the working area! Loosely stacked or scat-
tered components and tools are accident
sources.

CVS Compressor RPO 200/300/400/600/800
Safety
17
Maintenance and troubleshooting
WARNING!
Risk of injury due to improper maintenance
and troubleshooting!
Improper maintenance and troubleshooting can
lead to serious bodily injuries or property dam-
age. Therefore:
–Maintenance work and troubleshooting work
may only be carried out by sufficiently quali-
fied and instructed personnel.
–Secure compressor against restarting, switch
off drives!
–Before starting any work, provide for sufficient
space and freedom of movement during as-
sembly.
–Pay attention to tidiness and cleanliness in
the assembly area! Loosely stacked or scat-
tered components and tools are accident
sources.
–The compressor is getting hot during opera-
tion! Allow it to cool down before starting any
work.
If components must be replaced:
–Pay attention to correct installation of spare
parts.
–Properly reassemble all fastening elements.
–Observe screw tightening torques.
–Before restarting, ensure that all covers and
protective devices are correctly installed and
function correctly.
–After completion of maintenance work and
troubleshooting, check correct functioning of
safety equipment.

CVS Compressor RPO 200/300/400/600/800
Technical data
18
3 Technical data
Dimensions RPO 200/300/400/60013)
Fig. 1: Dimensions RPO 200/300/400/600
1 Line to the oil cooler with blow out direction
"right"
2 Compressed air either "to the side" or "to the
rear". With the blow out direction "to the right",
only ""to the side" is possible.
3 Attachment borings M12 x 26. Required min.
screw-in depth: 24 mm.
4 Clearance for filter change (deoiling element, air
filter, oil filter)
5 Interior diameter for vent channel at the transi-
tion point. Expand the vent channel to keep the
accumulated pressure as low as possible.
6 Sense of rotation viewing the "maintenance side
of the compressor" or "the motor drive shaft":
left.
7 Weight indication: compressor without fill
8 With RPO 300 and RPO 400: Reduction flange
for electric motor
9 Terminal box for the motor is on top (standard).
As agreed, right and left are also possible.
12 Minimum distance from the wall
13 RPO600 see also chapter 3.2
A1 Illustration of the possible blowout directions of
the oil cooler
Down
Left
Right
Compressor
Type PRO

CVS Compressor RPO 200/300/400/600/800
Technical data
19
Dimensions RPO 600/80013)
Fig. 2: Dimensions RPO 800
1 Line to the oil cooler with blow out direction "right"
2 Compressed air either "to the side" or "to the rear".
With the blow out direction "to the right", only ""to
the side" is possible.
3 Attachment borings M12 x 26. Required min.
screw-in depth: 24 mm.
4 Clearance for filter change (deoiling element, air fil-
ter, oil filter)
5 Interior diameter for vent channel at the transition
point. Expand the vent channel to keep the accu-
mulated pressure as low as possible.
6 Sense of rotation viewing the "maintenance side of
the compressor" or "the motor drive shaft": left.
7 Weight indication: compressor without fill
8 Terminal box for the motor is on top (standard). As
agreed, right and left are also possible.
12 Minimum distance from the wall
13 RPO600 see also chapter 3.1
A1 Illustration of the possible blowout directions of the
oil cooler
Down
Left
Right

CVS Compressor RPO 200/300/400/600/800
Technical data
20
Technical data
Description
Unit
RPO 200
RPO 300
RPO 400
RPO 600
RPO 800
Size of oil cooler
–
see chapter 3.1
see chapter 3.2
Suction
volume flow 1), 2)
[l/min]
180/175
260/256
380/375
550/540
770/758
Final overpressure 3)
[barg]
10/12
Suction pressure
[mbar]
1000
Motor rated speed
[min–1]
1420
1420
1440
1455
1455
Power requirement at the
shaft 2)
[kW]
2,2/2,4
2,8/3,2
3,8/4,2
5,2/5,7
7,2/8,0
Final overpressure range
[barg]
3…10/12
Speed range
[min–1]
1000…2200
1000…2200
1000…2200
1000…2200
1000…2000
Sound pressure level 4) 5)
[dB(A)]
60
61
63
63
64
64
Oil content 6)
[l]
1,8/2,4
1,8/2,4
1,8/2,4
2/2,6
2/3
2/3
Remaining oil content of
the
compressed air 7)
[mg/m3]
≤5
Voltage of electric motor
[V AC]
3 x 400
Frequency of electric mo-
tor
[Hz]
50
Protection class of electric
motor
–
IP 55 (shake proof)
Design of electric motor
–
B35 or B85
Weight without
drive motor 8)
[kg]
58
58
57
55
61
67
Weight with
drive motor 8)
[kg]
76
80
84
93
99
111
Cooling suction
temperature 9)
[°C]
-40…+40
Activation duration10)
[%]
30…100
Tab. 1: Technical data
This manual suits for next models
4
Table of contents
Other CVS Air Compressor manuals
Popular Air Compressor manuals by other brands

Daystate
Daystate TYPE-2 Use and maintenance manual
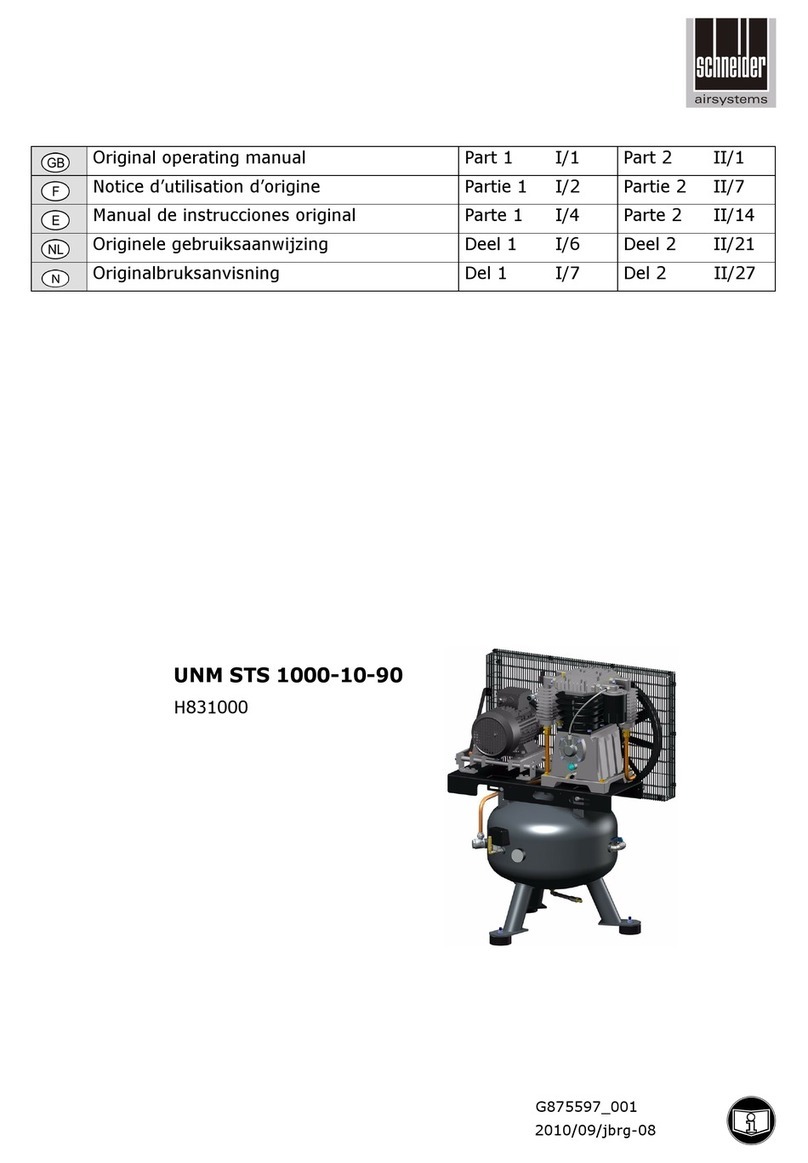
Schneider Airsystems
Schneider Airsystems H831000 operating manual

Porter-Cable
Porter-Cable JOB BOSS C3550 instruction manual

Gude
Gude 580/10/50 EU 400V Translation of original operating instructions
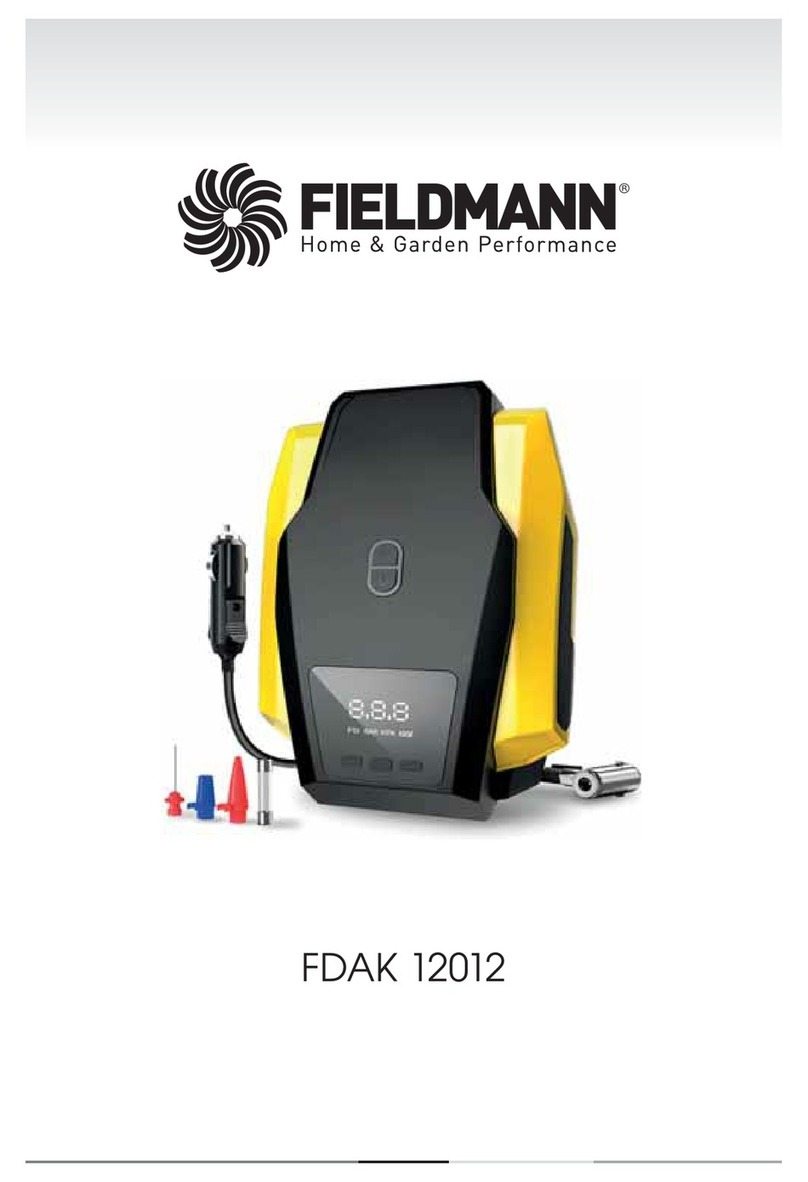
Fieldmann
Fieldmann FDAK 12012 instruction manual

California Air Tools
California Air Tools 1P1060S owner's manual