Danfoss VLT series User manual

0 - 1
Introduction Safety Precautions 0 - 2
Required Tools 0 - 3
Section One Description of Operation 1 - 1
Sequence of Operation 1 - 4
Section Two Fault Indicators and Messages 2 - 1
Troubleshooting Tips 2 - 5
Troubleshooting Flowchart 2 - 6
Symptom/Cause Chart 2 - 9
Section Three Static Test Procedures 3 - 1
Dynamic Test Procedures 3 - 6
Section Four Component Replacement Procedures 4 - 1
Section Five Current Limit Trips 5 - 1
Ground Fault Trips 5 - 3
Overcurrent Trips 5 - 3
Overvoltage Trips 5 - 4
Fault Memory 5 - 6
Section Six Spare Parts Tables 6 - 1
Appendix Component Locations 7 - 1, 7 - 5
Block Diagrams 7 - 2, 7 - 6
○○○○○○○○○○○○○○○○○○○○○○○○○○○○
○○○○○○○○○○○○○○○○○○○○○○○○○○○○○○○
○○○○○○○○○○○○○○○○○○○○○○○○○
○○○○○○○○○○○○○○○○○○○○○○○○○○
○○○ ○○○○○○○○○○○○○○○○○○
○○○○○○○○○○○○○○○○○○○○○○○○○○○
○○○○○○○○○○○○○○○○○○○○○○○
○○○○○○○○○○○○○○○○○○○○○○○○○○
○○○○○○○○○○○○○○○○○○○○○○○○○○
○○○○○○○○○○○○○○○○○○○○○○○○○○○○
○○○○○○○○○○○○○○○○○○○○○○○○○○○○○
○○○○○○○○○○○○○○○○○○○○○○○○○○○○○
○○○○○○○○○○○○○○○○○○○○○○○○○○○○○
○○○○○○○○○○○○○○○○○○○○○○○
○○○○○○○○○○○○○○○○○○○○○○○○
○○○○○○○○○○○○○○○○○
○○○○○○○○○○○○○○○○○○○○○○○○○○○○○○○○
○○○○○○○○○○○○○○○○○○○○○○○○○○○○○
○○○○○○○○○○○○○○○○○○○○○○○○○○○
Table of Contents

0 - 2
INTRODUCTION The purpose of this manual is to provide technical information and instructions
thatwillenabletheusertoidentifyfaultsandaffectrepairsonthefollowingDanfoss
Series 3000 and 3500 Adjustable Frequency Drives:
VLT 3002-3022, 230V VLT 3502-3532, 230V
VLT 3002-3052, 380, 460V VLT 3502-3562, 380, 460V
The manual has been divided into five sections. The first section covers the
description and sequence of operations. Section two covers fault messages and
provides troubleshooting charts both in the form of flow and symptom/cause.
Sectionthreedescribesthevarioustestsandmethodsusedtoevaluatethedrives'
condition. Section four covers the removal and replacement of the various
components. Section five discusses application-specific information.
Electrostatic discharge. Many electronic components are sensitive to static
electricity. Voltages so low that they cannot be felt, seen or heard can reduce the
life, affect performance, or completely destroy sensitive electronic components.
When performing service, proper ESD equipment should be used to prevent
possible damage from occurring.
ESD SAFETY
Bob
VLT®Series Service Manual

0 - 3
!
WARNING:
FOR YOUR SAFETY:
The Adjustable Frequency Drive (AFD) contains dangerous voltages
when connected to the line voltage. Only a competent technician
should carry out the service.
1) DO NOT touch the electrical parts of the AFD when the AC line is
connected. After the AC line is disconnected wait at least 15 minutes
before touching any of the components.
2) When repairs or inspection is made the AC line must be disconnected.
3) The STOP key on the control panel does not disconnect the AC line.
4) During operation and programming of the parameters the motor may start
without warning. Activate the STOP key when changing data.
The following tools will be sufficient to troubleshoot and repair all units covered by
this manual:
Digital multi-meter
Clamp-on ammeter
Analog voltmeter
Flat head screw drivers
Phillips screw drivers
Torx drivers - T10, T15, T20, T27
Socket 7mm
Pliers
Torque wrench
TOOLS REQUIRED:
VLT®Series Service Manual

1 - 1
Section One
DESCRIPTION OF
OPERATION Refer to the overall schematic in the Appendix.
This manual in not intended to give a detailed description of the unit's operation.
It is intended to provide the reader a general overview of the function of each of
the unit's main assemblies. With this information, the repair technician should
have a better understanding of the unit's operation and therefore aid in the
troubleshooting process.
The VLT is divided primarily into three sections commonly referred to as: logic,
interface, and power.
Thecontrolcardcontains the majority of the logicsection. Theheartofthecontrol
card is a microprocessor which controls and supervises all functions of the unit's
operation. In addition, a separate PROM contains the parameter sets which
characterize the unit and provide the user with the definable data enabling the
unit to be adjusted to meet the customer's specific application. This definable
data is then stored in an EEPROM which provides security during power-down
and also allows flexibility for future changes as needed. A custom integrated
circuit generates the PWM waveform which is then sent on to the Interface/ILD
Card gate drive circuits.
Also, part of the logic section is the keyboard/display
mounted on the control card. The keyboard provides
the interface between the digital logic and the human
programmer. The LCD (Liquid Crystal Display) provides
the operator/programmer with menu selection, unit
status and fault diagnostic information. Programming
is accomplished through the use of four of the eight
keysavailableon the keyboard.Theadditionalfour keys
provide various local controls, depending on the type of
unit.
Aseriesof customer terminals areprovidedfortheinput
of remote commands such as: Run, Stop and Speed
Reference. Terminals are also provided to supply
outputs to peripheral devices for the purpose o f
monitoringandcontrol.Two programmablerelayoutputs
arealsoavailableto interface the unit with other devices.
Inaddition, the controlcardiscapableof communicating
via a serial link with outside devices such as a personal
computer or a programmable logic controller.
The control card provides two voltages for use from the
customer terminal strip. The 24VDC is used primarily
to control functions such as: Start, Stop and Forward/
Reverse.The 24VDC isprovidedfromaseparatesection
oftheunit's power supply and is delivered tothe control
card from the Interface/ILD Card via the two conductor
ribbon cable.
LOGIC SECTION
MICROPROCESSOR
ADRESS
DATA
RAM EPROM
EEPROM
VVC
CONTROL
POWER
POWER
FEEDBACK
ANALOG
INPUTS
ANALOG
OUTPUTS
DIGITAL
INPUTS
DIGITAL
CHANNEL
2
1
1
1
D
A
D
A
KEYBOARD
DISPLAY
RELAY

1 - 2
LOGIC SECTION
Section One
A 10VDC supply is also available for use as a speed reference when connected to
an appropriate potentiometer. These two voltage references are limited in the
amount of available current they can provide (see specifications in Instruction
Manual). Attempting to power devices which draw currents in excess of that
available may result in an eventual failure of the power supply. In addition, if the
supply is loaded too heavily, sufficient voltage will not be available to activate the
control inputs.
During the troubleshooting process it is important to remember that the control
card can only respond to the commands it receives. It is also possible that due to
a failure, the Control Card will not respond to control commands. For this reason
it is necessary to isolate the fault to the control commands, control programming,
or the drive itself. If, for example, the drive stops unexpectedly, the control
commands should first be checked. This would include confirming that contact
closures and analog input signals are present at the proper terminals of the drive.
Never assume that a signal is present because it is supposed to be. A meter
should be used to confirm the presence of signals at the drive terminals.
Secondly, the programming of the drive should be confirmed to insure that the
terminals used are set to accept the signals connected. Each digital and analog
input terminal can be programmed to respond in very different ways. If there is a
concern whether the remote controls are functioning correctly it is possible to
take local control of the drive to confirm proper operation. A word of caution here:
prior to taking local control, insure that all other equipment associated with the
drive is prepared to operate. In many cases safety interlocks are installed which
can only be activated through the use of a normal remote control start.
As there must be a command in order for the Control Card to respond, there may
also be situations where the Control Card displays unknown data or that
performance may be affected such as in the case of speed instability. In these
cases the first thought may be to replace the Control Card. However, this type of
erroneous operation is usually due to electrical noise injected onto control signal
wiring. Although the Control Card has been designed to reject such interference,
noise levels of sufficient amplitude can, in fact, affect the performance of the
Control Card. In these situations it is necessary to investigate the wiring practices
used. For example, the control signal wiring should not be run in parallel with
highervoltagewiring,includingpower,motor,andbrake resistorleads. The reason
being that voltages can be induced from one conductor onto another through
capacitiveor inductive coupling. Thistypeofproblemcanbecorrectedby rerouting
the wiring or through the use of shielded cable. When using shielded cable it is
importanttoproperlyterminate the drain wire.Thedrainwireshould be terminated
only at the drive end of the cable. Specific termination points are provided on
each unit. The opposite end of the shielded cable drain wire is then cut back and
taped off to prevent it from coming in contact with other terminals or acting as an
antenna.

1 - 3
The logic to power interface isolates the high voltage components of the power
section from the low voltage signals of the logic section. This is accomplished by
use of the Interface/ILD Card*. All communication between the control logic and
the rest of the unit passes through the Interface/ILD Card. This communication
includes: DC Bus voltage monitoring, line voltage monitoring, feedback from the
current sensors, temperature sensing, and control of the gate drive firing signals.
TheInterfaceCardcontains aSwitch Mode Power Supply (SMPS)which provides
the unit with 24VDC, ±13VDC, and 5VDC. The switch mode type supply is used
due to its efficiency and linearity. Another benefit of the SMPS is that it uses the
DC Bus voltage as a power source. In the event of a power loss the power supply
remains active for a longer period of time versus conventional power supplies.
During the troubleshooting process it is important to determine whether the
Interface Card is receiving or sending the signal that appears to be at fault. For
example, the gate-drive signals are generated by the Interface Card. Conversely
an over-temperature fault can result from the Interface Card receiving an "open"
from the heatsink thermal switch. If the fault could stem from a signal received by
the Interface Card, it is necessary to isolate the fault to either the signal source or
the Interface/ILD card. It is critical to check all possibilities to avoid costly errors
andlongdowntime. In any case, the Interface/ILD Cardis relativelyeasy to change,
so if it is suspect, a quick exchange will confirm a faulty board.
* The Input Line Driver (ILD) Card is used on VLT 3002-3004, 230V; VLT 3502-
3504, 230V; VLT 3002-3008, 380V/460V, and VLT 3502-3511, 380V/460V.
All other units covered by this manual use the Interface Card.
Section One
LOGIC TO POWER
INTERFACE
INPUT LINE DRIVER (ILD)
CARD
POWER SECTION The power section contains the Rectifier, the DC Capacitor Bank and the IGBT
power components. Also included in the power section are the DC Bus Coils and
the Motor Coils. During the troubleshooting process, extreme care is required
when probing into the power section components. The DC Bus voltage can rise
well over 700VDC on 460V units. Although this voltage begins to decrease upon
removal of input power, it can take up to fifteen minutes to discharge the DC
Capacitor Bank to safe levels.
A fault in the power section will usually result in at least one of the customer
provided line fuses being blown. Replacing fuses and re-apply power without
further investigation is not recommended. The tests listed under Static Test
Procedures in Section Three should be performed to insure that there are no
shorted components in the power section. It is recommended that the motor
leads be disconnected from the unit prior to re-applying power. This precaution
opens the path for short circuit currents through the motor in case a faulty
component remains.
R
S
T
M
3Ø
INVERTER
DC BUSRECTIFIER
SIMPLFIED PWM POWER SECTION

1 - 4
SEQUENCE OF
OPERATION VLT 3002-3004, 230V, VLT 3502-3504, 230V
VLT 3002-3008, 380V/460V VLT 3502-3508, 380V/460V
When input power is first applied, the Rectifier Module converts the line voltage
into a DC voltage. The rectified output is then connected to the DC Bus filter
establishing a fixed DC Bus voltage. To limit the inrush charge current in the DC
Buscapacitors,threeNegative TemperatureCoefficient (NTC) resistorsareadded
inseries withtheinputs oftheRectifierModule. NTCresistorsdecreaseinresistance
astemperatureincreases.Providingthat the charging processproceeds normally,
the power supplies will come up and provide the Control Card with low voltage
control power. At this time the Control Card display will indicate that the unit is
ready for operation.
Following a run command and a speed reference, the Control Card delivers three
Pulse Width Modulation (PWM) signals to the ILD Card. The ILD Card in turn
receives these three signals and creates the six individually isolated gate drive
signals.Thesegate pulses arefed directly tothe Insulated Gate Bi-polar Transistor
(IGBT) output power devices. The IGBTs are switched on and off to develop the
PWM waveform which is ultimately delivered to the motor. As the unit operates,
the ILD Card monitors the unit's operational status. Currents and voltages out of
specified limits or excessive temperatures will result in the ILD Card responding to
the fault. The ILD Card sends the appropriate fault message to the Control Card
and in virtually all cases causes the unit to trip. Section 2 of this manual describes
thefault messages and providesdirectionin determiningthecauseandthe solution
for the fault.
Section One
VLT 3006-3032, 230V, VLT 3508-3532, 230V
VLT 3011-3052, 380V/460V VLT 3511-3562, 380V/460V
When power is first applied, the normally open Bus Contactor forces the input line
current to flow through the Positive Temperature Coefficient (PTC) resistors. PTC
resistors increase in resistance as the temperature increases. The
+VDC
–VDC
Bus
Capacitors
NTCs
Rectifier
Module
MOVs
MOV
MOV
Bus Coil

1 - 5
SEQUENCE OF
OPERATION PTC resistors are placed in series with the inputs of the Rectifier Module to limit
the initial charge current of the DC Bus capacitors. The rectified line voltage is
then applied to the DC Bus filter. As the DC Bus voltage increases, the Interface
Card power supplies energize. As the power supplies stabilize, the Interface Card
sends a signal to the Relay Card to pull in the Bus Contactor. The Relay Card
energizesthe contactor coilwithashortburst of ahighamplitude,full-wave rectified
voltage to pull in the Bus Contactor. The Relay Card then switches the Bus
Contactor coil voltage to a lower rectified holding voltage. As soon as the DC Bus
Contactor closes, the PTC resistors are effectively removed from the circuit and
the DC Bus Capacitors quickly finish charging. 1
Providing that the charging process proceeds normally, the Interface Card power
supplies will provide the Control Card with low voltage control power and the
Control Card display will indicate that the unit is ready for operation.
Following a run command and a speed reference, the Control Card delivers a
PWM signal (one per Phase) to the Interface Card. The Interface Card in turn
receives these three signals and creates six individual isolated gate drive pulses.
Fromherethegatepulses arefeddirectlyto theInsulated Gate Bi-polar Transistor
(IGBT) output power devices. The IGBTs are switched on and off to develop the
PWM waveform which is ultimately delivered to the motor.
As the unit operates, the Interface Card monitors the unit's operational status.
Currents and voltages out of specified limits or excessive temperatures will result
in the Interface Card responding to the fault. The Interface Card sends the
appropriate fault message to the Control Card and in virtually all cases causes the
unitto trip. Section Two of this manualdescribes thefault messagesand provides
direction in determining the cause and the solution for the fault.
Section One
1The VLT 3511, 380/460V units have the Bus Contactor relay and PTC resistors
mounted on the ILD Card.
+VDC
–VDC
Bus
Capacitors
MOV
Bus Coil
Bus Coil
MOVs
Bus
Contactor
Rectifier
Module
PTCs
*
*
Only two PTC resistors
on some units

2 - 1
Section Two
FAULT INDICATORS
AND MESSAGES
STATUS MESSAGES
Avarietyofmessagesaredisplayed by the controlcard. Somemessages indicate
the operational status of the unit while others provide warnings of an impending
fault. In addition, there are the alarm messages which indicate that the unit's
operation has stopped due to a fault condition. In this section we will deal with
only those messages which interrupt the unit's operation. A complete list of
status messages can be found in the Instruction Manual. The particular type of
status, warning, or alarm message will be indicated on the bottom line of the
display.
CURRENT LIMIT
This message will flash in the display when the unit is operating above the current
limit setting as recorded in parameter 209. Parameter 310 may be set to provide
a fixed time delay after which the unit will trip.
REF FAULT
This message will flash in the display should any live zero signal be operating
outside of its range. For example, 4-20mA has been selected as the speed
reference. Should the current loop be broken, the display will flash "REF FAULT".
Parameters 414 and 415 may be used to select the unit's response to this
condition.
NO 24 VOLT
This message will flash if the 24 volt power supply is missing or out of tolerance.
The 24 volt supply is used only for the customer's remote connections.
NO MOTOR
This message will flash if Motor Check has been activated in parameter 313,
terminal 27 is enabled and no motor is detected.
REFERENCE.000000
CURRENT0LIM..000
100.0%

Section Two
2 - 2
WARNING MESSAGES VOLTAGE LOW
This message will flash when the DC Bus voltage has fallen below the lower limit.
This is an indication of low line voltage. This is only a warning message, however.
If the condition persists, it will result in a unit trip on "Under Voltage".
* Refer to table for specific value.
VOLTAGE HIGH
This message will flash when the DC Bus voltage has exceeded the upper limit.
This is an indication of high line voltage or regenerative energy being returned to
the bus. This is only a warning message, however, if the condition persists, it will
result in a unit trip on "Over Voltage".
* Refer to table for specific value.
INVERT TIME
Thismessagewill flash when the inverter ETR value hasreached98%. Theinverter
ETR (Electronic Thermal Relay) begins counting up as soon as the output current
exceeds 105% of the unit's continuous current rating. At an inverter ETR value of
100%, the unit trips on "Invert Time".
MOTOR TIME
Thismessage will flash ifMotorThermalProtectionhasbeenactivated in parameter
315, "Warning" has been selected as the Data Value, and the Motor ETR value
has reached 98%. The Motor ETR value begins counting up if the motor is run at
slow speed or if the motor is consuming more than 116% of the motor's nominal
rated current as entered in parameter 107. At a Motor ETR value of 100%, the
unitwill respond based on thesetting in parameter315. If Trip hasbeen selected,
the unit will trip on "Motor Time".
OVERCURRENT
This message indicates at least one of the three output phases has reached the
unit's peak current rating. During this time the control card attempts to initiate
current limit. If the current rises too fast or the control card cannot control the
condition by means of current limit, the unit will trip on "Over Current".
* DC BUS VOLTAGE LIMITS VLT 3002-3052
VLT 3502-3562
VLT Rating 230VAC 380VAC 460VAC
SMPS stop 190 360 360
SMPS start 210 410 410
Undervoltage trip, inverter stopped 210 400 460
inverter enabled 230 430 500
Control Card undervoltage warning 235 440 510
Control Card overvoltage warning 370 665 800
(brake applied*, parameter 300) (395) (705) (845)
Overvoltage trip, inverter stopped 410 730 880
inverter enabled 380 680 820
* Only on VLT Series 3000 units.
REFERENCE.000000
VOLTAGE0LOW.000.
100.0%

2 - 3
Section Two
ALARM MESSAGES Alarm messages will be indicated by the following messages appearing in the
display and the red Alarm LED will flash on the unit keypad. All alarm messages
result in the unit's operation being interrupted and require a Manual or Automatic
reset. Automatic reset can be selected in parameters 309 and 312. In addition,
themessage"Trip"or "Trip Locked" will be displayed. If "Trip Locked" is displayed,
theonlypossible resetis to cyclepower and then perform amanual reset. Manual
reset is accomplished by means of the front panel push button or by a remote
contact closure on the appropriate control terminal. Remedies listed with each
alarm message give a basic description of the corrective action which can be
taken to correct the fault condition. For a more detailed explanation, see the
Symptom/Cause Section and the Application Section. Also note the numbers in
parenthesisby each alarmmessage. These are the codeswhich will appearin the
Fault memory, parameter 602.
INVERTER FAULT (1)
This message indicates a fault in the power section of the unit. This fault returns
a "Trip Locked". Also see Testing The Inverter Section.
OVER VOLTAGE (2)
This message indicates the DC Bus voltage upper limit has been exceeded. This
fault can be caused by high line voltage or regenerative energy being returned
from the motor. To remedy this fault condition, reduce the line voltage or extend
the Decel Ramp. This fault returns a "Trip". Also see Over Voltage Trips.
UNDER VOLTAGE (3)
This message indicates the DC bus voltage has fallen below the lower limit. To
remedy this fault, increase the line voltage to the correct value for the unit rating.
This fault returns a "Trip". Also see Testing the Soft Charge Circuit.
OVER CURRENT (4)
This message indicates a short circuit on the output of the inverter. This fault may
also be caused by the unit reaching it's peak current rating so rapidly that the unit
cannot respondwith currentlimit. An examplemay berunning the driveat speed
and closing an output contactor connecting the drive to a high inertia load. To
remedy this fault, check the output wiring and motor for short circuits. This fault
returns a "Trip Locked". Also see Over Current Trips.
Menu
Data
Jog Fwd
Rev
Stop
Reset Start
+
–
Alarm On
TRIP0LOCK000000
INVERTER0FAULT00
ALARM

Section Two
2 - 4
ALARM MESSAGES GROUND FAULT (5)
This message indicates a leakage to ground on the output of the inverter. To
remedy this fault, check the output wiring and motor for ground faults. It is also
necessary to ensure that the VLT has been properly grounded. This fault returns a
"Trip Locked". Also see Ground Fault Trips.
OVER TEMP (6)
This message indicates that the unit's heatsink temperature or the unit's internal
ambient temperature has exceeded permissible limits. All units covered by this
manual use a resetting thermal switch. The thermal switch is located on either the
ILD Card or is mounted on the heatsink of units which use the Interface Card. To
remedythe fault, correcttheovertemperaturecondition.Thisfaultreturnsa"Trip."
Also see Overtemp Trips.
INVERT TIME (7)
This message indicates the unit has delivered greater than 105% of the unit's
continuous current rating for too long (inverse time function). Prior to this fault
condition the "Invert Time" warning will be displayed. To remedy this fault, reduce
themotorload to at or below the unit's continuouscurrentrating. Thisfault returns
a "Trip Locked". During the trip the counter will count down. Upon reaching 90%,
the "Trip Locked" will change to "Trip".
MOTOR TIME (8)
This message indicates the motor has consumed greater than 116% of the value
enteredinparameter 107(motornominalcurrent)fortoolong (inversetimefunction).
This fault may also be caused from running the motor at a low speed and high
current for too long a period of time. This trip will only occur if the "Motor Thermal
Protection" has been activated in parameter 315. Prior to the trip the "Motor
Time" warning will be displayed. To remedy this fault, reduce the load on the
motor or raise the motor's speed. This fault returns a "Trip Locked". During the
trip the counter will count down. Upon reaching 0% the "Trip Locked" will change
to "Trip".
CURRENT LIMIT (9)
This message will be displayed if the unit has run in current limit for a time which
exceeds the setting in parameter 310. To remedy this fault, reduce the motor's
loadorverifythatthecorrectsettingshavebeenenteredin parameter 209 (Current
Limit) and parameter 310 (Current Limit Trip Delay). This fault returns a "Trip". See
Current Limit Trips.
MOTOR TRIP (15)
This message will be displayed if parameter 400 is set to "Thermistor" and motor
thermistor connected between terminals 50 and 16 has increased to a resistance
of 3KΩ. To remedy this fault remove the motor over temperature condition. This
fault returns a "Trip". The Reset Button can be held to allow access to the
parameters.
EXCEPT FAULT
This fault is usually the result of electrical noise caused by a poor earth ground
connection to the VLT. This fault may also be seen if Adaptive Motor Tuning is
attempted on a motor many times larger than the drive rating (parameter 106).
(This fault is accompanied by the PC address where an illegal value was found,
also see page 4-1.)
TRIP0LOCK000000
GROUND0FAULT000
ALARM

2 - 5
Section Two
GENERAL
TROUBLESHOOTING TIPS Prior to diving into a repair, here a few tips that if followed will make the job easier
and may prevent unnecessary damage to good components.
1. First and foremost respect the voltages produced by the drive. Always verify
the presence of line voltage and bus voltage before working on the unit.
Also remember that some points in the drive are referenced to the negative
bus and are at bus potential even though you may not expect it.
2. Never power up a unit which has had power removed and is suspected of
being faulty. If a short circuit exists within the unit, applying power is likely
to result in further damage. The safe approach is to conduct the Static Test
Procedures. The static tests check all high voltage components for short
circuits. The tests are relatively simple to make and can save money and
downtime in the long run.
3. The safest method of conducting tests on the drive is with the motor
disconnected. In this way a faulty component that was overlooked or the
unfortunate slip of a test probe will generally result in a unit trip instead of
further damage.
4. Following the replacement of parts, test run the unit with the motor
disconnected. Start the unit at zero speed and slowly ramp the speed up
until the speed is at least above 40 Hz. Monitor the phase to phase output
voltage on all three motor terminals to check for balance (an analog voltmeter
will work best here). If balanced the unit is ready to be tested on a motor. If
not, further investigation is necessary.
5. Never attempt to defeat fault protection devices within the drive. This will
only result in unwanted component damage and may result in personal
injury as well.
6. Always use factory approved replacement parts. The unit has been
designed to operate within certain specifications. Incorrect parts may effect
performance and result in further damage to the unit.
7. Read the instruction and service manuals. A thorough understanding of
the unit is the best approach. If ever in doubt consult the factory or an
authorized repair center for assistance.

Section Two
2 - 6
2)
Is the output phase to
phase voltage and
current balanced?
YES NO
1)
Symptom
Motor operation unstable
3)
Test the inverter
section, page 3-4
4)
Verify correct settings have
been entered in Group 1
"Load & Motor"
5)
Symptom
Motor will not run
8)
Are fault messages displayed?
NO YES
6)
Is there light in the display?
NO YES
See Diagnostics section,
"Alarm Messages".
See Item 18,
page 2-8
VLT 3002-3022, 230V VLT 3502-3532, 230V
VLT 3002-3052, 400/500V VLT 3502-3562, 400/500V
7)
Is the correct line voltage
present on the input terminals?
L1/R (91), L2/S (92), L3/T (93)
NO YES
See Item 11,
page 2-7 See Item 12,
page 2-7

2 - 7
Section Two
16)
Replace the Interface/
ILD Card.
Does the fault disappear?
YES NO
12)
Disconnect all control signal
plugs on the control card.
Does the fault disappear?
NO YES
10)
Is the correct line voltage
present on the input terminals?
L1/R (91), L2/S (92), L3/T (93)
YES NO
9)
Symptom
No information in display
11)
Check Input Disconnect
and fusing.
If fuses are blown, check
for a short circuit in the
Power Section.
13)
The fault may be caused
by a short circuit in the
control signals.
Check control wiring for
proper connection.
15)
Test the soft charge
circuit, input rectifier,
and DC Bus capacitors.
17)
Replace the Control Card.
Does the fault disappear?
NO YES
Resume operation
YES NO
Resume operation Replace the
Relay Card
– +
– +
14)
Is the DC Bus voltage OK? Should read 1.4 x the AC line V.
Measure the DC Bus voltage between terminal +VDC and –VDC.
Also refer to pages 3-1 and 3-2.

Section Two
2 - 8
18)
Motor stationary, info in
display but no fault
message displayed
19)
Start VLT by pressing Start
on the keypad.
21)
Replace the Control Card, if
this does not help, the fault
might be electrical noise.
Check whether the following
precautions have been taken:
• Have shielded cables been
used?
• Are the shields correctly
terminated?
• Is the unit properly
grounded to earth?
Correct the motor wiring.
Insure motor overloads are
reset and output contactor
closed.
25)
Replace Control Card.
Does the motor run?
NO
26)
Replace Interface/ILD Card.
Does the motor run?
NO
27)
Consult factory.
CAUTION:
Prior to running in Local,
insure all other equipment
associated with the VLT is
ready to function
or has been isolated.
20)
Is the display frozen, i.e., the
display cannot be changed
or is undefinable?
NO YES
22)
Is the motor connected
correctly/
YES NO
24)
Verify that the control signals
are connected to the correct
terminals and the appropriate
parameter settings have
been entered.
23)
Try to run the VLT in local.
Refer to CAUTION at left.
Local control parameters.
On VLT Series 3000:
003 = Local
004 = Frequency reference
change by means of + and –
On VLT Series 3500:
003 = keypad HOA
Press the Local/Hand key
change speed by the + and –
Does the motor run?
YES NO

2 - 9
Section Two
SYMPTOM/CAUSE CHARTS
SYMPTOM/CAUSE charts are generally directed towards the more experienced technician. The intent of these charts is to
provide a range of possible causes for a specific symptom. In doing so, these charts provide a direction, but with limited
instruction.
SYMPTOM POSSIBLE CAUSES
1. Control Card Display Is Not Lit.
2. Blown Input Line Fuses
3. Motor Operation Unstable
(Speed Fluctuating)
4. Motor Draws High Current But
Cannot Start. (May appear to rock
back and forth.)
Incorrect or missing input voltage
Incorrect or missing DC bus voltage
Remote control wiring loading the power supply
Defective Control Card
Defective Interface/ILD Card
Defective Relay Card
Defective or disconnected ribbon cables
Shorted Rectifier module
Shorted IGBT
Shorted DC Bus
Shorted brake IGBT
Mis-wired Dynamic Brake option
Start compensation set too high
Slip Compensation set too high
Improper current feedback
PID Regulator or Auxiliary Reference mis-adjusted
Control signal noise
Start voltage set too high
Open winding in motor
Open connection to motor
One inverter phase missing. Test output phase balance.

Section Two
2 - 10
SYMPTOM/CAUSE CHARTS
SYMPTOM POSSIBLE CAUSES
5. Motor Runs Unloaded But Stalls
When Loaded. (Motor may run
rough and VLT may trip.)
6. Unbalanced Input Phase Currents
Note: Slight variations in phase
currents are normal. Variations
greater than 5% require
investigation.
7. Unbalanced Motor Phase Currents
Note: Slight variations in phase
currents are normal. Variations
greater than 5% require
investigation.
Current Limit set too low
One half of one inverter phase missing. Test output phase balance.
Input line voltage unbalanced
Faulty connection on input wiring
Fault in plant power transformer
Input Rectifier module faulty (open diode).
Open motor winding
Faulty motor connection
Fault in inverter section (see Symptom No. 6.)

3 - 1
Section Three
All tests will be made with a meter capable of testing diodes. Use a digital VOM
set on diode scale or an analog ohmmeter set on R x 100 scale. Before making
any checks disconnect all input power, motor and brake option connections.
CAUTION:
Allow sufficient time for the DC Bus to fully discharge before beginning
testing. The presence of bus voltage can be tested by setting your
voltmeter for 1000VDC and reading the voltage at the labeled terminals
shown in the drawings.
The purpose of making static tests on the input rectifier is to rule out failures in this
device, either shorted or open diodes. Failure of the rectifier module will usually
result in blown line fuses. It should be noted that blown input line fuses can also
be the result of shorts in the IGBT module(s) or a damaged bus capacitor. See
Testing the Inverter Section and Testing the Bus Capacitors. For measurements
where an open-circuit is expected the meter may show some initial continuity as
the DC Bus capacitors charge up. This is normal and to be expected.
VLT 3002-3004, 230V VLT 3502-3504, 230V
VLT 3002-3008, 380V/460V VLT 3502-3511, 380V/460V
1. Remove the Control Card to expose the ILD Card. Locate the UDC connector
on the ILD Card (MK102). The red lead at the top side of the connector will
be used for the (+UDC) test point and the black lead at the bottom of the
connector will be the (–UDC) test point. The +UDC and –UDC fast-on
terminals on the DC Card (as shown) can also be used.
2. Connect the positive (+) meter lead to (+UDC). Connect the negative (–)
meter lead to terminals 91 (L1), 92 (L2), and 93 (L3) in turn. Each reading
should be open.
3. Reverse the meter leads connecting the negative (–) meter lead to (+UDC)
and the positive (+) meter lead to power terminals 91 (L1), 92 (L2), and 93
(L3) in turn. Each reading should show a diode drop.
4. Connect the positive (+) meter lead to the red lead (–UDC). Connect the
negative (–) meter lead to power terminals 91 (L1), 92 (L2), and 93 (L3) in
turn. Each reading should show a diode drop.
5. Reverse the meter leads connecting the negative (–) meter lead to the
(–UDC) and the (+) meter lead to power terminals 91 (L1), 92 (L2), and 93
(L3) in turn. Each reading should show open. Test is complete.
Incorrect readings could indicate a faulty Rectifier Module. See Removal and
Replacement Instructions. If there is an open circuit reading when a diode drop
reading is expected, see Testing the Soft Charge Circuit.
TESTING THE INPUT
RECTIFIER
STATIC TEST PROCEDURES
+UDC
–UDC
NTC
Resistors

Section Three
3 - 2
Red Lead
Black Lead
–UDC +UDC
STATIC TEST PROCEDURES
TESTING THE INPUT
RECTIFIER
DC Bus
Capacitors
Bus
Contactor Balance
Resistors
VLT 3006-3022, 230V VLT 3508-3532, 230V
VLT 3011-3052, 380V/460V VLT 3516-3562, 380V/460V
1. Remove any plastic shields covering the DC Bus Capacitors and locate the
18 gauge red and black leads connected to the Bus Capacitor bus bars as
shown. These leads indicate the positive (+UDC) and negative (– UDC) DC
Bus test points. The number and location of the bus capacitors will vary
between units.
2. Connect the positive (+) meter lead to (+UDC). Connect the negative (–)
meter lead in turn to the terminals (1/L1), (3/L2), and (5/L3) as labeled on
the top side of the Bus Contactor. Each reading should be open.
3. Reverse the meter leads connecting the negative (–) meter lead to (+UDC)
and the positive (+) meter lead in turn to the terminals (1/L1), (3/L2), and (5/
L3) on the top side of the Bus Contactor. Each reading should read a diode
drop.
4. Connect the positive (+) meter lead to (–UDC). Connect the negative (–)
meter lead in turn to the terminals (1/L1), (3/L2), and (5/L3) on the top side
of the Bus Contactor. Each reading should show a diode drop.
5. Reverse the meter leads connecting the negative (–) meter lead to (–UDC)
and the positive (+) meter lead in turn to the terminals (1/L1), (3/L2), and (5/
L3) on the top side of the Bus Contactor. Each reading should show open.
Test completed.
Incorrectreadingsindicate afaultyrectifiermodule.SeeRemovaland Replacement
Instructionson page 4-4 If therectifiermodule is shorted, it isimportant to inspect
the Bus Charge Contactor. See page 3-3 for testing the soft-charge circuit.
Other manuals for VLT series
15
This manual suits for next models
10
Table of contents
Popular Transducer manuals by other brands
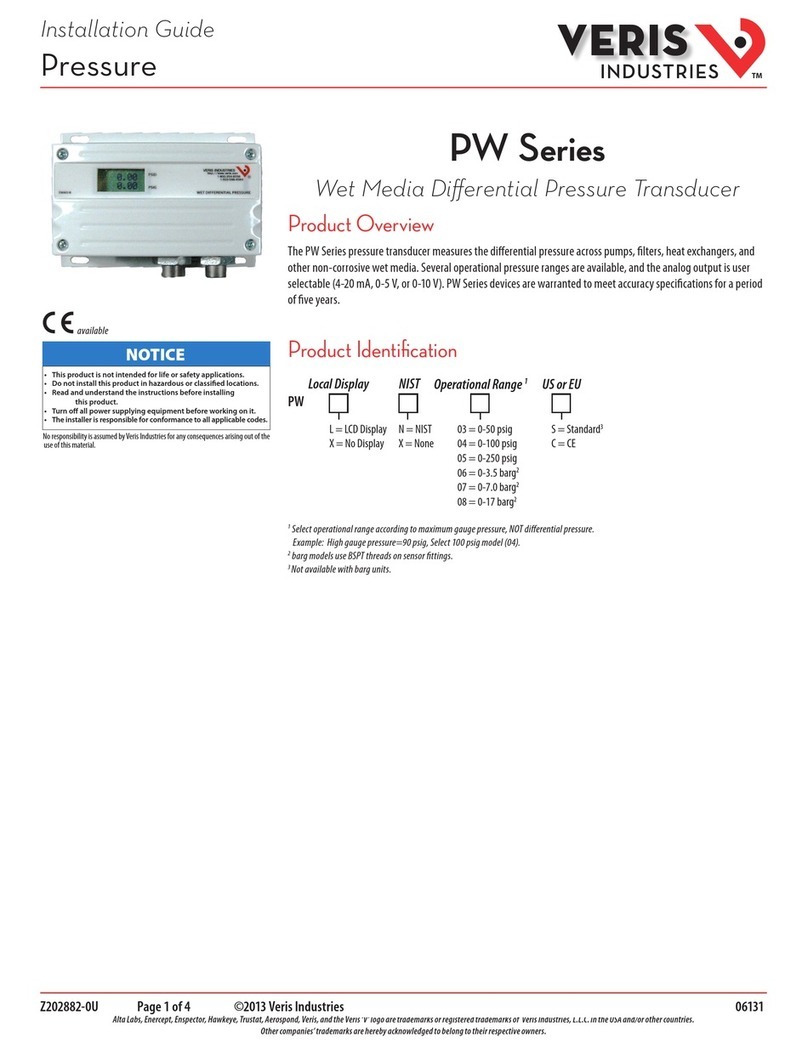
Veris Industries
Veris Industries PWXN07C installation guide
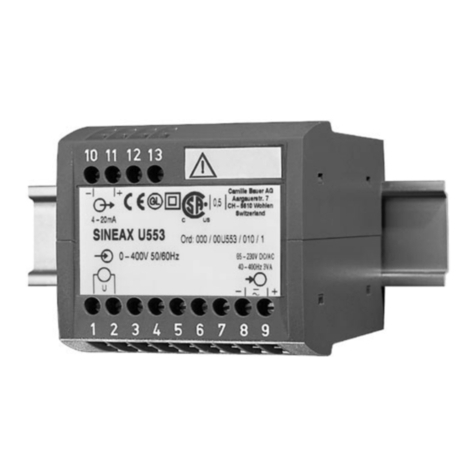
Camille Bauer
Camille Bauer SINEAX U553 operating instructions
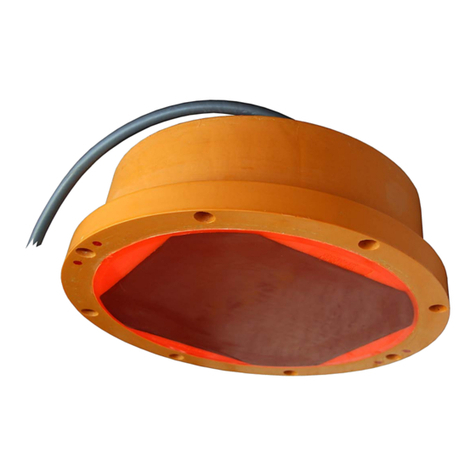
Simrad
Simrad 38-7 - INSTALLATION REV D installation manual
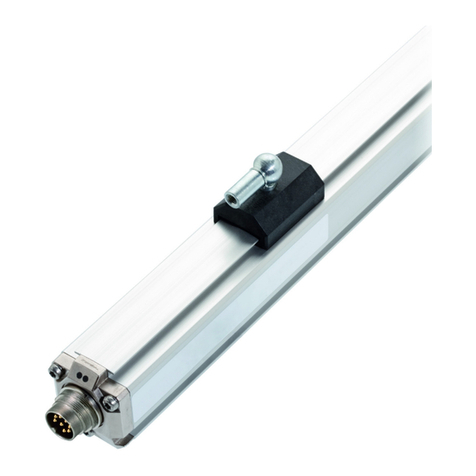
Balluff
Balluff BTL7-S5-M Series user guide
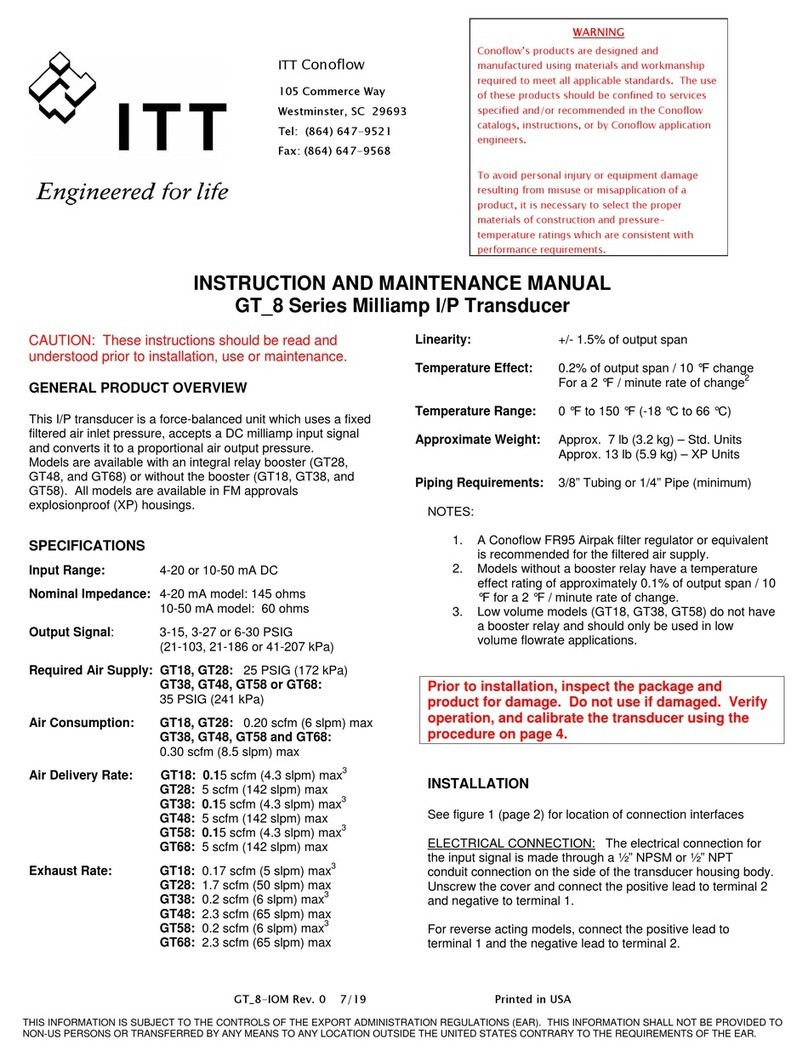
ITT
ITT GT 8 Series Instruction and maintenance manual
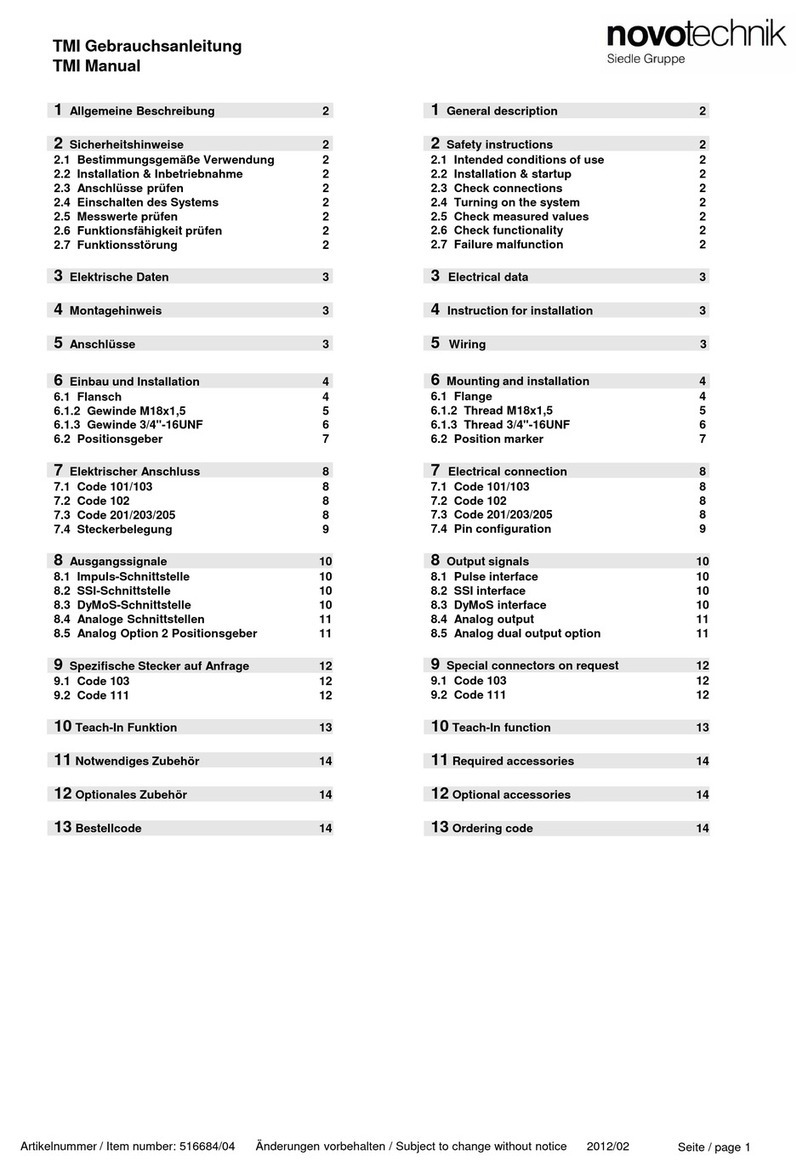
novotechnik
novotechnik TMI Series manual