Darex XT-3000 User manual


2

3
Table of Contents
Safety Instructions................................................................................. page 4-5
Material Safety Data Sheet..................................................................... page 6
Auto Specification Sheet......................................................................... page 7
Quick Start Instructions ......................................................................... page 8
Connecting Auto Sharpening System to XT-3000................................... page 9-14
Auto Controller/Display Details............................................................ page 15-18
Auto Sharpening Fixture Details........................................................... page 19-23
Auto Sharpening Fixture Parts List....................................................... page 24
Auto Sharpening Fixture Schematic ..................................................... page 25
Geared Chuck Parts List ....................................................................... page 26
Geared Chuck Schematic ...................................................................... page 27
Auto Controller/Display Parts List........................................................ page 28
Auto Controller/Display Schematic ...................................................... page 29
Maintenance ......................................................................................... page 31-32
Trouble Shooting Guide ........................................................................ page 33
*For Technical Service visit our web site at http://www.darex.com
Or call Darex at 800-547-0222
Or contact your Darex Distributor PP17296KF Rev 0

4
Safety Instructions
FOR YOUR OWN SAFETY, READ INSTRUCTION MANUAL BE-
FORE OPERATING MACHINE!
Caution:
• WE DO NOT RECOMMEND OPERATING MA-
CHINE WITHOUT A VACUUM SYSTEM RUN-
NING
• GRINDING DUST INHALED/INGESTED CAN BE
HARMFUL TO YOUR HEALTH.
• GRINDING PARTICALS WILL CAUSE DAMAGE
TO THE INTERNAL COMPONENTS
Caution:
WHEN USING ELECTRIC TOOLS, BASIC
SAFETY PRECAUTIONS SHOULD ALWAYS BE
FOLLOWED TO PREVENT THE RISK OF FIRE,
ELECTRIC SHOCK AND PERSONAL INJURY,
INCLUDING THE FOLLOWING:
• WHEN MAINTENANCE OR MACHINE
ADJUSTMENTS ARE PERFORMED ON
SHARPENER ALWAYS: Push the emergency stop
button, unplug unit from power supply and use a
“LOCK OUT” “TAG OUT” procedure.
• FOLLOW INSTRUCTIONS ENTITLED “DAREX
XT-3000 Maintenance" in this Instruction Manual.
• NEVER TOUCH INTERNAL PARTS OF THE
SHARPENER WHEN THE SHARPENER IS ON The
rotating grinding wheel can cause injury.
• USE CAUTION WHEN REPLACING THE GRIND-
ING WHEEL Follow instructions entitled “How to
change a wheel”, on page 21 of the XT-3000
Instruction Manual.
• KEEP GUARDS IN PLACE and in working order.
See Decal at left.
• REMOVE WRENCHES Always check to see that any
tools have been removed from sharpener before
turning it on.
• KEEP WORK AREA CLEAN Cluttered areas and
benches invite accidents.
• DON'T USE IN DANGEROUS ENVIRONMENT Do
not use power tools in damp or wet locations, or
expose them to rain. Do not use tools in the
presence of flammable liquids or gases.
• KEEP WORK AREA WELL LIT
• STORE EQUIPMENT in a safe place when not in
use.
• DON'T FORCE TOOL It will do the job better and
safer at the rate for which it was designed.
• USE THE RIGHT TOOL Don’t force tool or
attachment to do a job it was not designed for.
• ALWAYS USE SAFETY GLASSES Also use face or
dust mask if cutting operation is dusty. Everyday
eyeglasses only have impact resistance lenses and
they are NOT safety glasses. See Decal at left.
• AVOID ACCIDENTAL STARTING Make sure switch
is in the “OFF" position before plugging it in.
• USE RECOMMENDED ACCESSORIES Consult the
owner's manual for recommended accessories. The
use of improper accessories may cause hazards. See
Decal at left.
• CHECK FOR DAMAGED PARTS Before further use
of the tool, a guard or other part that is damaged
should be carefully checked to assure that it will
operate properly and perform its intended function.
Check for alignment of moving parts, binding of
moving parts, breakage of parts, mounting and any
other conditions that may affect its operation. A
guard or other part that is damaged should be
properly repaired or replaced.
• NEVER LEAVE TOOL RUNNING UNATTENDED
Turn power off.
• USE PROPER EXTENSION CORD Make sure
extension cord is in good condition. When using an
Safety Instructions
extension cord be sure to use one heavy
enough to carry the current the Drill
Sharpener will draw. An undersize cord will
cause a drop in line voltage, resulting in a
loss of power and/or overheating.
• DO NOT USE DAMAGED OR UNSHAPED
WHEELS Use grinding wheels suitable for
speed of grinder.
• THE CONTINUOUS A-WEIGHTED sound
pressure level at the operator’s ear is not
over 60dB (A).
• RISK OF INJURY DUE TO ACCIDENTAL
STARTING. Do not use in an area where
children may be present.
• THE WEIGHTED ROOT MEAN SQUARE
ACCELERATION VALUE to which the arms
are subjected to does not exceed 2.5 m/s2.
• KEEP CHILDREN AWAY. All visitors should
be kept safe distance from work area.
• MAKE WORKSHOP KID PROOF with pad-
locks or master switches.
• WEAR PROPER APPAREL. Do not wear
loose clothing, neckties, rings, bracelets or
other jewelry which may get caught in mov-
ing parts. Nonslip footwear is recommended.
Wear protective hair covering to contain long
hair.
• DON’T OVERREACH. Keep proper footing
an balance at all times. .
• MAINTAIN TOOLS WITH CARE. Keep
tools sharp and clean for best and safest per-
formance. Follow instructions for lubricating
and changing accessories.
• DISCONNECT TOOLS before servicing,
when changing accessories, such as blades
and the like.
• NEVER STAND ON TOOL. Serious injury
could occur if the tool is tipped or if the
grinding tool is unintentionally contacted.
230v~,50Hz,6A
230v~,50Hz,8A

5
Safety Instructions
GROUNDING INSTRUCTIONS
• FOR ALL GROUNDED CORD CONNECTED
TOOLS:
• In the event of a malfunction or breakdown, ground-
ing provides a path of least resistance for electric
current to reduce the risk of electric shock. This tool
is equipped with an electric cord having an equip-
ment-grounding conductor and a grounding plug.
The plug must be plugged into a matching outlet that
is properly installed and grounded in accordance with
all local codes and ordinances. Do not modify the
plug provided if it will not fit the outlet, have the
proper outlet installed by a qualified electrician. Im-
proper connection of the equipment-grounding con-
ductor can result in a risk of electric shock. The con-
ductor with insulation, having an outer surface that is
green with or without yellow stripes, is the equip-
ment-grounding conductor. If repair or replacement
of the electric cord or plug is necessary, do not con-
nect the equipment-grounding conductor to a live
terminal. Check with a qualified electrician or service-
man if the grounding instructions are not completely
understood, or if in doubt as to whether the tool is
properly grounded. Use only 3-wire extension cords
that have 3-prong grounding plugs and 3-pole recep-
tacles that accept the tool’s plug. Repair or replace
damaged or worn cord immediately.
• GROUNDED, CORD-CONNECTED TOOLS IN-
TENDED FOR USE ON A SUPPLY CIRCUIT HAV-
ING A NOMINAL RATING LESS THAN 150
VOLTS: See Table 1 for minimum gauge cords.
Volts
120 V 25 / 7.5 50 / 15 100 / 30 150 / 45
240 V 50 / 15 100 / 30 200 / 60 300 / 90
Morethan Not morethan
0 6 18 16 16 14
6 10 18161412
10 12 16 16 14 12
12 16 14 12
Total length of cord (feet / meters)
Ampere Rating AWG
Not Recommended
Table 1 Minimum Gauge Cords

6
Material Safety Data Sheet
US DEPARTMENT OF LABOR Form Approved Occupational Safety and Health
Administration 0MB No 44-Ri 367
MATERIAL SAFETY DATA SHEET
Required under USDL Safety & Health Regulations for Ship Repairing, Shipbuilding and Chip breaking
129 CFR 1915, 1916.19171
SECTION I
MANUFACTURERS NAME: Darex LLC
EMERGENCY PHONE NO: (541) 488-2224
ADDRESS: 210 E. Hersey Street Ashland, Oregon 97520
CHEMICAL NAME & SYNONYMS Diazon-Electroplated Diamond/CBN Products, Diamond (uncoated)
Man-Made Diamond. RVG. MBG. MBS Product Families. Standard Series and 300 Series Diamond Micron Powder
TRADE NAME & SYNONYMS: Electroplated CBN Wheels, Electroplated Diamond Wheels
CHEMICAL FAMILY: Abrasive Any Grade
FORMULA: n/a SECTION II COMPOSITION
CHEMICAL NAME Nickel Industrial Diamond
REGULATED Yes No
CAS#: 7440-02-0 7882-40-3
AGIH TLV 1 0 mgm3 10.0 mg m3 (PNOC)
CARCINOGEN Yes No
Materials are regulated by OSHA 29 CFR 1910.1200, Hazard Communication Standard
SECTION III - PHYSICAL AND CHEMICAL DATA
BOILING POINT (F) n/a MELTING POINT n/a
SPECIFIC GRAVITY n/a VAPOR PRESSURE n/a
VAPOR DENSITY n/a EVAPORATION RATE n/a
SOLUBILITY IN WATER n/a SOLUBILITY IN ALCOHOL n/a SOLUBILITY IN OTHER
SOLVENT n/a PERCENT VOLATILE BY VOLUME (%) n/a
APPEARANCE AND ODOR Solid, Clear, White To Yellow To Dark Crystals Silver Color.
SECTION IV - FIRE AND EXPLOSION HAZARD DATA
FLASH POINT n/a
(METHOD USED) FLAMMABLE LIMITS LEL UEL
EXTINGUISHING MEDIA n/a
SPECIAL FIRE FIGHTING PROCEDURES: n/a
UNUSUAL FIRE AND EXPLOSION HAZARDS: n/a
SECTION V - HEALTH, FIRST AID AND MEDICAL DATA
PRIMARY ROUTE(S) OF ENTRY: Inhalation, Ingestion, Skin, Eye(s)
EFFECTS OF OVEREXPOSURE
INHALATION: Difficulty in breathing (Dust from wheel use).
INGESTION: If a dust, symptoms are variable.
SKIN: Irritation (especially if sensitive to Ni ).
EYE(S): Irritation (from Ni or diamond particle).
FIRST AID AND MEDICAL INFORMATION:
INHALATION: Move to fresh air. Give oxygen if necessary
INGESTION: Obtain medical attention.
SKIN: Wash thoroughly with water Obtain medical help if necessary
EYE(S): Flush thoroughly with water. Obtain medical assistance
OTHER POTENTIAL HEALTH RISKS
Nickel (Ni) is listed as a carcinogen Avoid long exposure. Consult medical personnel for first aid and medical information
SECTION VI - CORROSIVELY AND REACTIVITY DATA
STABILITY: Unstable ( ) Stable (x)
POLYMERIZATION: May occur ( ) Will not occur (x)
INCOMPATIBILITY: (Materials to avoid) n/a
HAZARDOUS COMPOSITIONS PRODUCTS: n/a
CONDITIONS TO BE AVOIDED: Contact with strong acids/caustics, enclosed areas.
SECTION VII - SPILL, LEAK AND DISPOSAL PROCEDURES
STEPS TO BE TAKEN IN CASE MATERIAL IS RELEASED OR SPILLED: Normal clean up procedure
WASTE DISPOSAL METHOD:
Waste will contain nickel. Dispose in accordance with all applicable Federal, state, and local regulations.
SECTION VIII – PERSONAL PROTECTION INFORMATION
RESPIRATORY PROTECTION:
Respiratory protection as needed see OSHA-29 CFR 1910.134
VENTILATION: LOCAL EXHAUST: strongly preferred
MECHANICAL (GENERAL): Use only if adequate to maintain below TLV’s.
PROTECTIVE GLOVES: As desired by user.
EYE PROTECTION: Recommended see OSHA29 CFR 11910.215
OTHER PROTECTIVE EQUIPMENT: Use standard precautions for grinding operations.
SECTION IX - STORAGE AND HANDLING PROCEDURES
NORMAL STORAGE AND HANDLING:
Store in clean, dry area, away from chemicals.
NORMAL USE: Use adequate ventilation (See Section VIII )
Form OSHA-20

7
Auto Sharpening System Specification Sheet
XT-3000 Auto Sharpening System
Specifications
Warranty - 1 year on defective parts
A) Geared Chuck:
Chuck Body Material - 303 Stainless
Knob and Cam Material - 12L14
Capacity - 3mm - 12mm or 12mm - 21mm
Gear Spline - 45 Tooth
Weight - 2.1lbs each (0.95kg)
B) Sharpening Fixture:
Gear Material - Acetal;
Gear Motor - 12 VDC, rated current 350 mA, typical current 150 mA
Home switch - Slotted Optical
Weight - 6.0 lbs ( 2.72 kg)
C) Controller/Display:
Housing Material - Glass filled, Acrylonitrile Butadiene Styreme (ABS)
STN Graphic LCD w/ Green LED back light
Weight - 1.5lbs (0.68 kg)
Power Inlet: Power Outlet:
Voltage: 115v~ Voltage: 115v~
Frequency: 60hz Current : 8A Max
Current: Fusing : 8A Time Lag
Grind Motor: 3.2A
Accessory: 8.0A
A
C
B

8
The Auto Sharpening System comes
equipped with a sharpening fixture, a
Controller/Display and a chuck/chucks.
Available chuck options listed below. The
Automated Sharpening System is for
use with the XT-3000 Expandable
Tool Sharpener
only
and not for use
with other sharpeners.
LEX400 - 115v w/3-12mm Chuck
LEX400i - 230v w/3-12mm Chuck
LEX450 - 115v w/12-21mm Chuck
LEX451i - 230v w/12-21mm Chuck
LEX500 - 115v w/3-21mm Chucks
LEX500i - 230v w/3-21mm Chucks
Detailed set up instructions begin on
page 9.
1. Remove from shipping box and re-
move all packaging material.
2. Attach sharpening fixture to XT base,
making sure the sharpening fixture is
secure. For more information on
mounting the sharpening fixture, see
page 9.
3. Attach Controller/Display with mount-
ing bracket provided, see page 10.
4. Connect DIN cable from sharpening
fixture to Controller/Display, see page
12.
5. Connect power from outlet source to
back of Controller/Display inlet, see
page 13.
6. Connect Pigtail Jumpers from the
back of Controller/Display to XT-3000
Base casting inlet. For detailed set up
information, see page 13.
7. The accessory receptacle is located at
the top of the power receptacle on the
back of the Controller/Display and will
allow you to use a dust extraction sys-
tem in conjunction with the use of the
XT3000. *We highly recommend
the use of a vacuum when the
machine is in use.
8. Make sure the grit tray is in place and
secure.
9. Un-box the chuck.
10. Align and secure the drill in the chuck.
(XT-3000 Instruction Manual
PP16180KF for Alignment details)
11. Insert chuck into Sharpening fixture.
Secure chuck in sharpening fixture, see
page 21.
12. Power on the machine by pushing the
rocker switch into the ON position,
this
will immediately start the grinding
wheel in motion
and power up the
Controller/Display screen.
13. Set up the LCD screen on the Control-
ler/Display, see pages 15-18.
14. (THIS STEP IS NOT NECESSARY
WHEN PURCHASING AND XT-3000
A COMPLETE) Calibrate Final Grind -
Drill Stick Out on sharpening fixture, see
pages 22-23.
15. Press Start on the Controller/Display
screen to begin sharpening. NOTE: The
sharpening fixture will immediately be-
gin to rotate and sharpen the drill. Make
sure hands and clothing are free of the
sharpening fixture.
16. Once the chuck has stopped, release
the chuck and remove from sharpening
fixture.
17. If a split point drill is desired, insert
chuck into splitting port. DO NOT re-
move drill from chuck until split is com-
plete. (See XT-3000 Instruction Manual,
PP16180KF, for Split Point details)
Quick Start Set Up

9
Attaching Sharpening Fixture to
Base Casting:
Make sure all contact areas are clean and free
of metal dust.
1. Rotate the locking lever so the flat edge is
on top, horizon-
tal and in a
straight line
with the base
casting.
2. Position the
sharpening fixture so that the 2 location holes
on the base of
the alignment
fixture are
aligned with
the 3/8 dowel
pins.
3. After sharpening fixture is in place, rotate
the locking lever clockwise until snug. This will
secure the sharpening fixture to the base.
Automated Sharpening System

10
Mounting Auto
Controller/
Display to
Base Casting:
1. Install and tighten
the two, 6mm BHSHC
screws from the stamped bracket to the control
box.
2. Align control box to main casting and transfer
punch or mark for drilling mounting screw holes.
3. Drill through
casting.
4. Using an alcohol wipe, thoroughly clean the
XT base casting surface where the adhesive will
make contact.
5. Peel adhe-
sive backing
from dual-lock
tape.
6. Carefully
align Controller/
Display to XT
base casting
and press
firmly.
5. Using 2, 10-24 thread forming screws,
insert into mounting bracket. While push-
ing hard, drive
in screws until
seated.
Automated Sharpening System

11
Connecting Sharpening Fixture
to Controller/Display:
1. Connect the mini DIN power cable coming
from the Sharpening Fixture to the mini DIN
receptacle located slightly underneath the bot-
tom of the Controller/Display.
Important: Be sure you have the DIN
pins and receptacle aligned correctly
before engaging. Improper connec-
tion can result in a blown optical
switch in the sharpening fixture which
will make the unit nonfunctional.
Automated Sharpening System

12
Power Connections - Back view
Automated Sharpening System
/Vacuum Receptacle
/From Controller/Display
/From Controller/Display
/To Power Source

13
Connecting AC Power to Auto
Controller/Display:
1. Located on the back of the Controller/
Display is the primary power receptacle.
Within this receptacle you will find a power
inlet and accessory receptacle.
2. Provided with the XT-3000 is a power cord.
Plug the cord into to a power outlet and into
the power inlet located on the back of the
Controller/Display.
Caution: Only one supply source can be
connected to this equipment!
Connecting Auto Controller/
Display to XT-3000:
1. Located on the back of the XT-3000 base
casting is the secondary power receptacle.
Caution: Do not connect a separate
power source to this Inlet!
2. The secondary accessory re-
ceptacle is located on the top and
the secondary power inlet is lo-
cated on the bottom of the recep-
tacle.
3. Connect
both pigtail
jumpers
coming from
the Control-
ler/Display to
the appropri-
ate positions
in the secon-
dary receptacle located at the back of the XT-
3000.
Automated Sharpening System

14
Connecting Vacuum:
The accessory receptacle on the back of the
Controller/Display is located in the
top position on the receptacle. This
will allow you to connect a dust
extraction system to be used dur-
ing sharpening.
*We highly recommend the
use of a dust extraction system
when the auto sharpening system is in
use. DAREX offers a vacuum system com-
patible with your XT3000.
Call DAREX for pricing.
• SA12075EA - 115V Vacuum
• SA12072EA - 230V Vacuum
Grit Tray/Vacuum Port Connec-
tion:
Grit tray
At the back of the machine, located underneath
the grinding motor is
the grit tray. Drill
grindings will
accumulate inside the
grit tray. The grit tray
has a magnetic liner
to attract and hold
these dust particles.
Do not let the tray
become more than
1/3 full.
To remove tray, unscrew brass thumb screw.
Remove tray and dump contents. Wipe excess
dust from the tray
with a rag.
Vacuum Port Connector
(Optional)
The grit tray has a knock out plug that can be
removed by hand
and replaced with
the vacuum tube
(SA16030TA).
Use this port to connect a vacuum hose to
the XT3000. This method of extracting dust
particles from
the machine
will keep it
cleaner and is
recommended.
Make sure the grit tray is in place and secure
before connecting the
vacuum hose.
Automated Sharpening System

15
CYCLE START/SELECT/SAVE:
CYCLE STOP/STOP/EXIT:
ARROW UP:
ARROW DOWN:
SYSTEM SETTING:
To operate the Auto Attachment you must first
power up the XT-3000 sharpener. Once pow-
ered up, the grinding wheel on the XT-3000
will begin to turn at full speed and the Control-
ler/Display screen will illuminate.
To access the complete menu, touch
the System Settings button located
on the left of the screen.
This will display the full menu:
• Clean Up Turns
• Auto/Manual Select
• Reset Bit Count
• Language Selection
• Motor Stall Delay
• Grind Sensitivity
• Factory Bit Count
• Software Version
Use the Arrow up and Arrow down but-
tons to view the entire menu. When
the text of the menu option has
changed to bold, the secondary menu
option can be accessed.
To select and enter into each secondary menu
touch
Pressing will allow you to exit the
screen you are working in.
Display Details

16
CLEAN UP TURNS:
By selecting “Clean up turns”,
The display shows:
The “Clean up turns” is active only when in “Auto”
Sharpening mode.
Pressing “Arrow up” advances clean up pass
by one.
Pressing “Arrow down” reduces pass by one.
Pressing “Save ”, stores and exits.
Pressing “Exit”, exits without saving.
AUTO/MANUAL SELECT:
By selecting “Auto/Manual”,
The display shows:
Pressing “Arrow up” or “Arrow down”
will highlight each menu option.
Display Details
Pressing “Save ”, stores and exits.
Pressing “Exit”, exits without sav-
ing.
AUTO:
By selecting “Auto”,
The display shows:
When “start” is pressed, the
sharpening fixture will begin to
sharpen.
During sharpening, you will see the num-
ber of rotations on the screen increase.
When the grind is complete, the pro-
grammed cleanup passes will appear and
begin to count down to 0. The sharpening
port will rotate to the home position and
stop.
At the end of each sharpening, the Bit
Count increases.
By pressing “stop” during the Auto
Cycle the unit stops and returns home.

17
RESET BIT COUNT:
By selecting “Reset Bit Count”,
The display shows:
Pressing “Arrow up”, or
“Arrow down”, will highlight each menu
option.
Pressing “Save”, resets the bit count,
only, if the “yes” is highlighted.
Pressing “Exit”, exits without saving.
LANUGUAGE SELECTION:
By selecting “Language Option”,
The display shows:
Pressing “Arrow up” or “ Arrow down”
will highlight each language option.
Display Details
MANUAL:
By selecting “Manual”,
The display shows:
By pressing “Arrow up”, the number of
Manual turns increases.
By pressing “Arrow Down”, the number
of Manual turns is decreased.
This automatically saves the new setting.
After pressing “Start”, the manual
sharpening begins.
The display starts counting down the number
of turns. At the end of sharpening, the Bit
Count increases.
By pressing “Stop”, the manual sharp-
ening ends.

18
Pressing “Select”, displays language se-
lection and exits.
Pressing “Exit”, exits without saving.
MOTOR STALL DELAY:
This screen will appear on the display:
“Motor Stall Delay is used to detect a prolonged
period of the Gear Motor not turning, sensing a
blocked or jammed condition. The available set-
tings are 2, 3 or 4 seconds; the factory default
is 3 seconds.
If the unit detects a 3 seconds lapse and the
chuck has not rotated at least a half turn, the
unit will shut itself off and “Sharpening Inter-
rupted” will appear.
The system will reset itself.
.GRIND SENSITIVITY:
The Grind Sensitivity is a measure of how
quickly the controller responds to the ma-
terial take off during AUTO grinding. A
lower number generally creates more
turns, a higher number means
fewer turns before the controller decides it
has reached the proper material removal.
This variable is set at a factory default of
25. When Darex CBN and Diamond wheels
are used, the setting of 25 is appropriate
and will not need to be changed.
FACTORY BIT COUNT:
This screen displays the accumulative
number of times the cycle start button has
been pressed. This number cannot be re-
set and will be used for warranty evalua-
tions.
SOFTWARE VERSION:
This screen displays the current version of
software. You will need to know the soft-
ware version for upgrade status and
troubleshooting.
Display Details

19
Alignment Instructions
Each chuck has an
orientation line
scribed on the chuck
dog of the cam.
To achieve the highest level of concentricity, in
the alignment step, insert the chuck into the
alignment port with the white line in the 12
o’clock position.

20
Other manuals for XT-3000
1
Table of contents
Other Darex Tools manuals
Popular Tools manuals by other brands
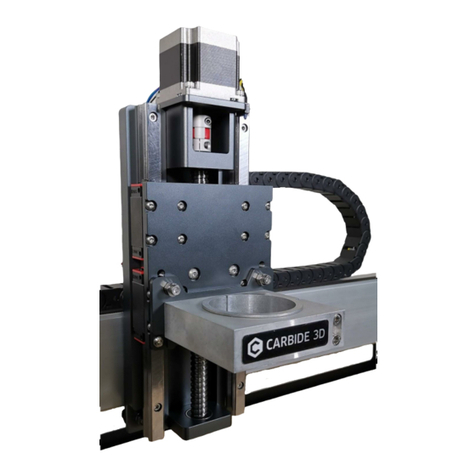
Carbide 3D
Carbide 3D HDZ 3.3 Assembly guide
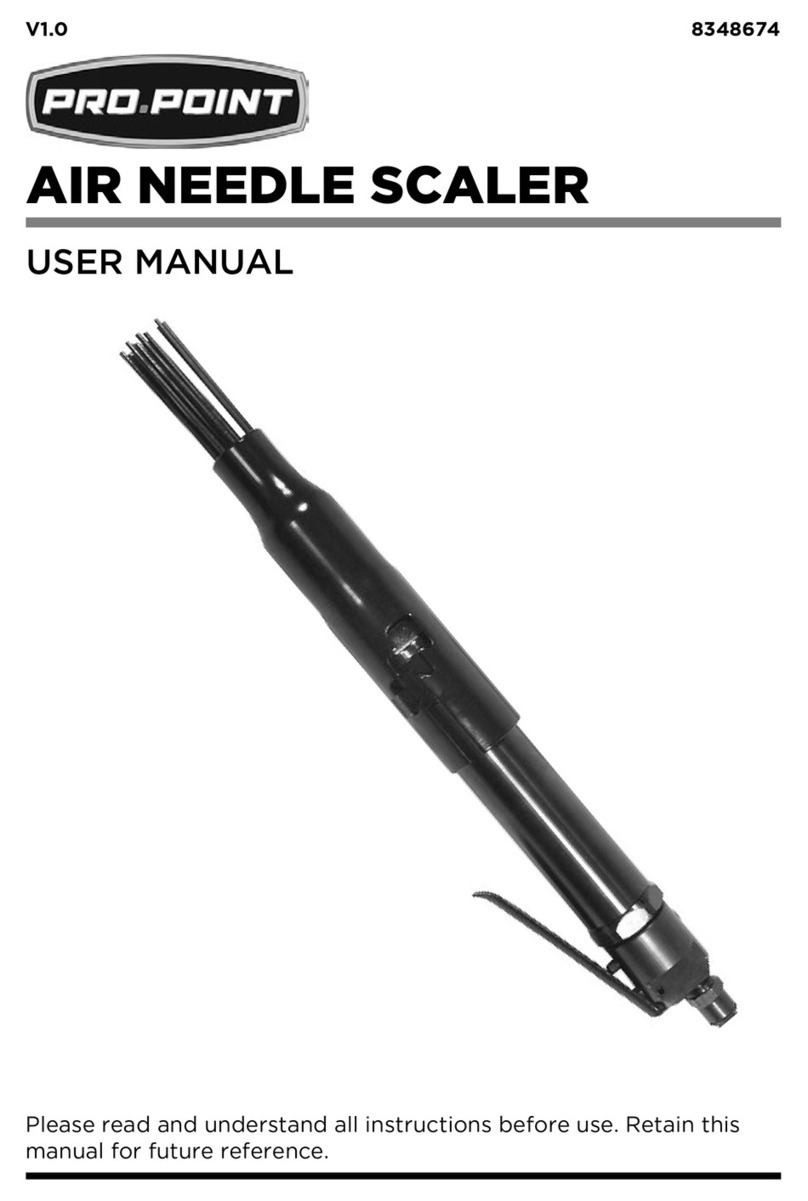
PROPOINT
PROPOINT 8348674 user manual

Blue Line
Blue Line CORNER FINISHER quick start guide
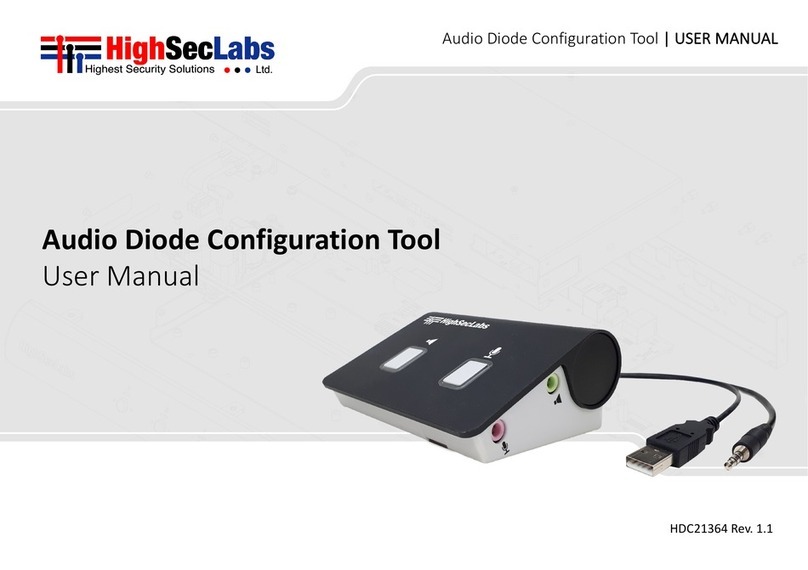
High Sec Labs
High Sec Labs HDC21364 user manual

Central Pneumatic
Central Pneumatic 97014 Set up and operating instructions

Black Hawk Automotive
Black Hawk Automotive Wheel Dolly BH8075 Operating instructions & parts manual