Dell E1709W User manual

Service Manual
- 0 -
Service Manual
LCD Monitor E1709W

1
Service Manual Versions and Revision
No. Version Release Date Revision
1
1.0
2008/08/25
Initial Release
Copyright
Copyright 2007 InnoLux Display. Corp. Ltd
All Rights Reserved
This manual may not, in whole or in part, be copied, Photocopied, reproduced, translated, or converted to any
electronic or machine readable form without prior written permission of Foxconn Tech. Corp. Ltd.
Dell E1709W Service Manual

Service Manual
2
Table of Contents
CHAPTER 1- PRECAUTIONS & SAFETY NOTICES .............................................................................................................................. 3
1. SAFETY PRECAUTIONS ........................................................................................................................................................ 3
2. PRODUCT SAFETY NOTICE .................................................................................................................................................. 3
3. SERVICE NOTES .................................................................................................................................................................... 3
CHAPTER 2- SERVICE TOOLS & EQUIPMENT REQUIRED ................................................................................................................. 4
CHAPTER 3- CIRCUIT THEORY.............................................................................................................................................................. 5
1. BLOCK DIAGRAM ....................................................................................................................................................................... 5
2. ELECTRONIC CIRCUIT THEORY ................................................................................................................................................... 7
3. FACTORY PRESET TIMING TABLE..................................................................................................................................... 13
4. POWER ON/OFF SEQUENCY..................................................................................................................................................... 13
5. D-SUB CONNECTOR PIN ASSIGNMENT ..................................................................................................................................... 14
6. AC OUTLET PIN ASSIGNMENT .................................................................................................................................................. 14
7. INNER CONNECTOR PIN ASSIGNMENT........................................................................................................................................ 14
8. KEY PARTS PIN ASSIGNMENTS.................................................................................................................................................. 16
CHAPTER 4- DISASSEMBLY & ASSEMBLY ........................................................................................................................................ 21
1. EXPLODED DIAGRAM ............................................................................................................................................................... 21
2. E1709WFPF DISASSEMBLY BLOCK .......................................................................................................................................... 22
3. ASSEMBLY BLOCK ................................................................................................................................................................... 23
CHAPTER 5- TEST AND ADJUSTMENT............................................................................................................................................... 24
1. FUNCTION KEY DEFINITIONS ..................................................................................................................................................... 24
2. OSD CONTROL....................................................................................................................................................................... 24
3. FACTORY MODE INTRODUCTION................................................................................................................................................ 26
4. BURN-IN PATTERN.................................................................................................................................................................... 27
5. AUTO COLOR BALANCE (AUTOMATICALLY CALIBRATE CHIP ADC PARAMETER BY USING CHIP INTERNAL DAC.)................................... 27
6. UPLOAD FIRMWARE TO MCU VIA VGA CABLE ............................................................................................................................ 26
7. AFTER REPAIR,TO ENSURE THE QUALITY YOU SHOULD DO THE FOLLOWING TEST AND ADJUSTMENT. .................................................. 27
CHAPTER 6- TROUBLE SHOOTING..................................................................................................................................................... 30
1. COMMON ACKNOWLEDGE......................................................................................................................................................... 30
2. NO POWER LED OFF .............................................................................................................................................................. 30
3. POWER NORMAL LED AMBER ................................................................................................................................................... 31
4. BACKLIGHT CAN’T BE TURNED ON .............................................................................................................................................. 32
5. NO PICTURE BACKLIGHT ON.................................................................................................................................................... 33
6. AT 32-GRAY SCALE PATTERN,COLOR LOST IN SOME SCALE........................................................................................................... 34
CHAPTER 7- RECOMMENDED PART LIST.......................................................................................................................................... 35
ATTACHMENT 1- BILL OF MATERIAL.................................................................................................................................................. 37
ATTACHMENT 2- SCHEMATIC.............................................................................................................................................................. 47
ATTACHMENT 3- PCB LAYOUT............................................................................................................................................................ 52

Service Manual
3
Chapter 1- PRECAUTIONS & SAFETY NOTICES
SAFETY PRECAUTIONS
This monitor is manufactured and tested on a ground principle that a user’s safety comes first.
However, improper used or installation may cause damage to the monitor as well as to the
user.
WARNINGS:
zThis monitor should be operated only at the correct power sources indicated on the rating
label on the rear cover of the monitor. If you’re unsure the power supply in your residence,
consult your local dealer or Power Company.
zUse only the specified power cord that comes with this monitor.
zDo not try to repair the monitor by yourself, as it contains no user-serviceable parts. This
monitor should only be repaired by a qualified technician.
zDo not remove the monitor cabinet. There is high-voltage parts inside that may cause
electric shock to human bodies.
zStop using the monitor if the cabinet is damaged. Have it checked by a service technician.
zPut your monitor only in a lean, cool, dry environment. If it gets wet, unplug the power
cable immediately and consult your closed dealer.
zAlways unplug the monitor before cleaning it. Clean the cabinet with a clean, dry cloth.
Apply non-ammonia based cleaner onto the cloth, not directly onto the class screen.
zDo not place heavy objects on the monitor or power cord.
PRODUCT SAFETY NOTICE
Many electrical and mechanical parts in this chassis have special safety visual inspections
and the protection afforded by them cannot necessarily be obtained by using replacement
components rated for higher voltage, wattage, etc. Before replacing any of these components
read the parts list in this manual carefully. The use of substitute replacement parts, which do
not have the same safety characteristics as specified in the parts list, may create shock, fire,
or other hazards.
SERVICE NOTES
zWhen replacing parts on circuit boards, clamp the solder wires around terminals before
soldering.
zKeep wires away from high voltage, high temperature components and sharp edges.
zKeep wires in their original position so as to reduce interference.
zAdjustment of this product please refers to the user’ manual.
zUse Pb free solder wire for circuit board preparation.

Service Manual
4
Chapter 2- SERVICE TOOLS & EQUIPMENT REQUIRED
1. SIGNAL GENERATOR
2. MULTIMETER
3. SCREW DRIVER
4. OSCILLOSCOPE
5. Soldering IRON
6. SOLDER (Lead free, RoHS compliance)
7. Color Analyzer
8. Fox_VISP_Programmer
9. Fox_VEDID_Programmer

Service Manual
5
Chapter 3- CIRCUIT THEORY
Block Diagram
There are 2pcs PCBA in this monitor, one is power& inverter board which is a single layer board,
and one is interface board&keypad which is OSD control. The system function block diagram as
below
This PWA is included switching power supplier, inverter for CCFL and interface board.(fig.1)
Power
Transformer
MOSFET
Photocoupler
+5V DC output
Snubber
&Schottky
Feedback
Control
Feedback
and OVP
PWM Control IC
LD7575
+12V DC output
2
1
ON/OFF Control
INL837
To Panel CCFL
Lamp2
Snubber
&Schottky
Power
MOSFET
Rectifier&
Filter
Circuit
AC Input
90V~264V
Brightness Control
+5VDC
To IF Board
+5V DC
AC Line Filter
Lamp1
Inverter
Transformer
Fig.1

Service Manual
6
Electronic Circuit Theory
2.1 Inverter PWM circuit
2.1.1) Inverter Control circuit :( fig.2)
R18 0R
R10
200k/Open
OLP1
C35A
R15
10K
ZD3
BAV70
3
2
1
R1
10R
R7
330k
C7
10nF
ON/OFF3
ISEN1
C14
10nF/25V X7R
R6
100K
C11/Open
0.1uF/25V
+5V
ZD5/Open BAW56
3
2
1
DIM3
R16
100K
R8
820K
T1A
R4
10K
U2
P6006HVG
1
2
3
4
6
7
8
5
S1
G1
S2
G2
D2
D1
D1
D2
R22
30K/Open
R13
1M
R17 10K/Open
R30
33R
C3
10nF/25V X7R
C13
10nF/25V
R28
5K/Open
C5
2.2uF/16V
R2
100K
R5
47K
OLP2
R3 10K
+5V
T1B
+12V
C10
2.2uF/10V
C27
120p/Open
C36A
U1
INL837
1
2
3
4
5
6
7
8 9
10
11
12
13
14
15
16
DRV1
VDDA
DIM
ISEN
PID
RSTR
RT
ENA VSEN
OVPT
LCT
SSTCMP
CT
TIMER
GNDA
DRV2
C8
47nF/16V
D9/Open
1N4148
C26
2700p
R29
33R
R11
3.3M
C9
270pF/16V NPO
C34A
PID_Input
R12
91K 1%
R20
100K
R14
1M
C16
27nF/Open
R26 0R
C25
2700p
C33A
C1
2.2uF/10V
C23
1nF/50V
R24
4.7K
C28
120p/Open
C22
1nF/50V
C6
33nF
R9
100K
ZD4/Open
BAV70
3
2
1
R21
100K
R23
30K/Open
C24
0.1uF/50V
C2
1nF
D10
1N4148
DIM
ISEN2
C18
27nF/Open
Fig.2
DC_5V through R1 and C1 will provide power for U1 on the pin2 (VDDA).
EN-ON/OFF voltage signal coming from scalar which is on IF BD will enable U1 to work. This
applies a level greater than approximately 2V to pin8 (ENA) enables the IC, A voltage less than 1V
will disable the IC. R3 is used to limit current.C3 and R16 is used to dump noise.
The soft-start function is provided by connecting C8 to pin12(SSTCMP), In the start-up mode,
current charges C8, its voltage controls the gradual increase in power to the transformer and
subsequently to the output load, this reduces in-rush current and provides reliable operation to the
CCFL.If no current is sensed approximately 2 seconds, U1 shuts off. Once the voltage at the pin4
(ISEN) reaches the lamp on threshold, the IC switches from the striking mode to the normal
operation mode and the PWM dimming control is activated.
DIM-ADJ duty cycle signal through R2 and C2 is on Pin 3(DIM), which adjusted will can
change the brightness of Panel. R15 is used to limit current. Internal LPWM dimming control is
determined by R11 and C7 connected to LCT (pin11), analog dimming is implemented by providing

Service Manual
7
a DC voltage to PID (pin5).
The striking frequency is determined by R12 and C9 connected to Pin 13(CT) and R6
connected to RSTR (Pin6).The operating frequency is determined by R12 and C9 connected to Pin
13(CT) and R7 connected to RT (pin7).
DRV1 and DRV2 of U1 are used to drive U2. DRV1 and DRV2 are controlled by build-in PWM
IC. U2 is switch which has two build-in IGBTs.
2.1.2) Output Circuit and Protection Circuit :( fig.3)
OLP1
C19
3pF/3KV
R31
470R 1%
C35A
+12V
C33A
C21
470uF/25V
4100-D02 NC
CN2
1
2
WH-01
CN3
1
2
R32
470R 1%
C17
3pF/3KV
T1A
R19
610R
C15
ty pe 15pF/3KV NP0 C20
100pF/50V OPEN
D1 1N4148
ISEN1
C30
100pF/50V OPEN
T1B
4100-D02 NC
CN1
1
2
WH-02
CN4
1
2
D2 1N4148
T1
DIP EEL19 SPW-054
1
6
4
3
10
7
fig.3
The transformer (T1) secondary winding leakage inductance and output capacitance (C15)
forms a lower pass filter, which converts the square-wave driving signal into a sinusoidal output
voltage signal for CCFL.
The over-voltage protection feature is implemented by using an external capacitor divider
(C17/C19) to sense the output voltage. The divide-down voltage signal is sent to the IC Pin9
(VSEN), thus regulating the output voltage.
The voltage signal on negative pole of D2 sensed through R19 comes to Pin4 of U1 (ISEN).
The CCFL current detected at resistor R19 is converted to a voltage level and input to the ISEN
pin.C6 is used to dump noise. Once the CCFLs are ignited and current is sensed through resistor
R19, capacitor C6 performs the loop compensation function. The voltage at IC pin12 (SSTCMP)
controls the drive duty cycle of the power MOSFETs to regulate the CCFL current.
If a CCFL is removed, fails or damaged during normal operation, CCFL current is no longer
sensed and the voltage on ISEN pin drops. Once the voltage at the ISEN pin is less than the lamp”
on” threshold, the shutdown timer is activated. The IC maintains the output voltage for
approximately 2-3seconds and once the timer expires, the IC will shutdown. To restart the IC, either
toggle the SST_CMP pin or recycle the power on the VDDA pin.

Service Manual
8
2.2 Power PWM circuit
2.2.1) Block diagram :( fig.4)
Fig.4
2.2.2) AC Input and EMI Filter :( fig.5)
fig.5
CN850 is a connector for connecting AC Power. F850 is a fuse to protect all the circuit AC.
Input voltage is from 90V to 264V. R850 and R851 are joined between two inputting main circuit
to prevent man from shock. L850 is used to clear up low frequency wave. C850 and C851 are
RT850
5R4A
VZ850
10561 NC
F850
3.15A 250V
C851
332 Y 2
C850
332 Y 2
R850
750K
C852
0.47uF X2
CN850
HF-301PCB 7MM
1 3
2
L850
CHK-007
4
3
1
2
R851
750K
EMI Filter Rectifier and
filter
Isolation power
transformer
Rectifier and filter Inverter circuit
PWM controller Switching element
Feedback Isolation
Rectifier and filter
LDO regulator

Service Manual
9
used to discharge the waves that L850 produced. High frequency waves are damped by C852.
2.2.3) High Voltage to Low Voltage Control Circuit :( fig.6)
fig.6
D850 is a rectifier in which there are 4 build-in diodes, inverting AC to DC.
C854 is used to smooth the wave from rectifier. R853 is a fuse resistor to protect the following
circuit when inrush current is too large. U850 is a highly integrated PWM controller. During the
startup, a high-voltage current source sinks current from the bulk capacitor to provide the startup
current as well as charge the Vcc capacitor C878, during the startup transient, the Vcc is lower
than the UVLO threshold thus the current source is on to supply a current with 1mA. Meanwhile,
the Vcc supply current is as low as 100uA thus most of the HV current is utilized to charge the
Vcc capacitor.
Whenever the Vcc voltage is higher than UVLO (on) to power on the LD7575 and further to
deliver the gate driver signal, the high-voltage current source is off and the supply current is
provided from the auxiliary winding of the transformer (T850). Pin8 (GATE) of U850 will output
square wave to drive Q850, and then the main current flow HV to GND by passing through T850,
Q850. Because of the change of current flow, wires in the other side of T850 will induct current.
When the sense voltage across the sense resistor R859, reaches the threshold voltage around
0.85V, the output GATE drive will be turned off. Every time when the output of power supply is
shorted or over loaded, the FB voltage will increase, the build-in PWM output will then be turned off.
Both will prevent the power supply from being overheated under over loading condition. The PWM
duty cycle is determined by this current sense signal and VFB, the feedback voltage. When the
voltage on sense pin reaches Vcomp = (VFB-1.0)/3, a switch cycle will be terminated immediately.
Vcomp is internally clamped to a variable voltage around 0.85 V for output power limit.

Service Manual
10
When Q850 are turned off, the main current flow will be consumed through D851, C875, R854
and D853. This will prevent Q850 from being damaged under large current impulse and voltage
spike.
2.2.4) DC_12V and 5V Output Circuit and Feedback circuit :( fig.7)

Service Manual
11
I851
TL431
K
R
A
D802
ED602
1
2
3
D801
ED602
1
2
3
C801
0.01/50V
R804
3K3 1%
R803
10K
C802 0.1/50V
R801 10R
CN853
CON8PIN
4
5
6
3
1
7
8
2
Snubber
C431
Ref
Cathode
Anode
GND
GND
NA
R802 20R/open
fig.7
D801 is used to rectify the inducted current. R801 and C861 are used to store energy when
current is reversed. The parts including C864 and L852 are used to smooth the current waves that
are from D801, and then 12V voltage is supplied.
D856 is used to rectify the inducted current. R863 and C863 are used to store energy when
current is reversed. The parts including C856, C858, C876 and L851 are used to smooth the
current waves that are from D856, and then 5V voltage is supplied.
12V and 5V supply voltage feed back to PWM controller U850 via R861, R871, R804 and I850.
R803, C801 and C802 used to control respond time.
2.3 I/F Board Circuit (see the Attachment 2- Schematic)
2.3.1 RGB CAPTURE
- Signal RED,GREEN,BLUE input through CN102 #1,#2,#3, Stop DC via C113, C114 and
C115, and then enter into U105 (TSUM1PER-LF-2) analog input PIN #13,#10,#8, and then
TSUM1PER-LF-2 deals with signal internally. D103, D104, D105 are ESD protector to
prevent U105 from ESD.
- Signal DDC_SCL (series clock) inputs via CN102#15, and then passes through ZD106 for
ESD protection, goes into EDID EEPROM IC U103 #6.
- Signal DDC_SDA (series data) inputs via CN102#12, and then passes through ZD103 for
ESD protection, goes into EDID EEPROM IC U103 #5.
- Signal TTL vertical sync. (Vsync) inputs via CN102 #14, and then clamped by ZD105 Zener,
passes through R134, and then goes into IC U105 (TSUM1PER-LF-2) #17.
- Signal TTL horizontal sync. (Hsync) inputs via CN102 #13, and then clamped by ZD104
Zener, passes throughFB101 & R133, and then goes into IC U105 (TSUM1PER-LF-2) #16.
- CN102#5 is defined as cable detect pin, this detector realize via R121 and U105#64, and
D102 is ESD protector.
- U103 +5V is supplied by PC via CN102#9 with D106 and ZD102 for ESD protection, or
supplied by Monitor self via D104.
- U103 is an EEPROM IC which is memory and EDID data saved in it.
2.3.2 Buttons Control

Service Manual
12
- Button “Power” on front bezel connects to U105 (TSUM1PER-LF-2) #58 through CN104 #1,
U105 #58 is defined as power on/off.
- Button “(” on front bezel connects to U105 (TSUM1PER-LF-2) #57 through CN104 #5, U105#57
Voltage is defined as “Plus”.
- Button “(” on front bezel connects to U105 (TSUM1PER-LF-2) #57 through CN104 #5, U105 #57
Voltage is defined as “Minus”.
- Button “Menu” on front bezel connects to U105 (TSUM1PER-LF-2) #63 through CN104 #6; U105
#63 Voltages is defined as “Menu”.
- Button “ENTER” on front bezel connects to U105 (TSUM1PER-LF-2) #59 through CN104 #4,
U105 #59 Voltage is defined as “ENTER”.
- LED Indicator on Front Bezel
a.When press button “power”, U105 (TSUM1PER-LF-2) #60 be send in low Voltage, make Q107#3
sends out high Voltage , and then to CN104#3 on keypad, LED Blue on.
b. When in “Suspend” mode, U105 (TSUM1PER-LF-2) #61 sends out a low Voltage, make
Q108#3 sends out high Voltage and then to CN104 #2 on keypad, LED Amber ON.
2.3.3 MATAR CHIP U105 (TSUM1PER-LF-2)
- U105 (TSUM1PER-LF-2) #33~#40 output 8 bit even and #41~#50 output 8 bit odd LVDS
digital data to panel control circuit through CN106.
- U105 (TSUM1PER-LF-2 ) #28 output PPWR ”H” potential to make Q104 conducted, and
then make Q101 conducted, +5V flow to CN103#1~#3 as Panel Vdd .
- U105 (TSUM1PER-LF-2) #55 output CCFL_ON/OFF”L” potential to control Inverter on/off.
- U105 (TSUM1PER-LF-2) #56 outputs Brightness “PWM” signals to control CCFL brightness.
- TCLK by Crystal 14.318MHz input to U105 (TSUM1PER-LF-2) #2.
- U105 (TSUM1PER-LF-2) #54 is RESET signals input pin
Please refer to TSUM1PER-LF-2 Pin Assignments table in page
2.3.4 Regulator Circuit
- +5V is from switching mode power supply for panel
- +3.3V is generated from Regulator U101 which is supplied by+5V through C104 filtering,
C102 is 3.3V output filter ,the output 3.3V supplies toU105, U108,U106, U102.
- +1.8V is generated from Regulator U102 which is supplied byU101-3.3V through C106
filtering.The1.8V via FB105 supplies to U105.
3. FACTORY PRESET TIMING TABLE
Standard Resolution Horizontal Frequency
(KHz) Vertical Frequency
(Hz)
640 x 480 31.469 59.940
640 x 480 37.500 75.000
800 x 600 37.879 60.317
800 x 600 46.875 75.000
1024 x 768 48.363 60.004
1024 x 768 60.023 75.029
1152x864 67.500 75.000
1280x1024 48.483 60.042
1280x1024 60.087 75.034
VESA
1440x900 55.935 59.887
IBM DOS 720 x 400 31.469 70.087

Service Manual
13
4. Power On/Off Sequency
Hardware power On/Off
When power cord plug into AC socket, Power provides 16V and DC_5V.
DC_5V is main voltage for panel and Regulator U101.
DC_3.3V is coming from Regulator U101; DC_3.3v is main voltage for U105. When DC_3.3V
input to U105 and U105 reset circuit active, U105 all registers will be set to default, that means
finish hardware power on.
When pull out power cord from AC socket, the system shut down instantly for no supply
Software power On/Off
- When press power key, U105 #58 receives low pulse, then (TSUM1PER-LF-2) U105 will be
wake up and send control signals(at 55,28pin) to on CCFL and switch 5.0v to panel module,
at the same time,U105 make the VGAcable input signal source display normal on panel if the
VGAcable input signal is active
-If power ON, U105 #60 (LED_Blue) will send out low potential, and then LED Blue on.
-If power saveing, U105 #61 (LED_Amber) will send out low potential, and then LED Amber
on.
-If power ON or power saving, when press power key, U105 #55 receives low pulse, then U105
will be sleeping and turn off backlight, at the same time, the panel will lose +5V.
The Panel_Vcc, Backlight_En, CLK/DATA output to panel will follow the following sequency.

Service Manual
14
Power supply for panel+5V VDD
90% 90%
10%
0V 10%
T1 T2
T3 T4
Signals Validdata
(Digital RGB, HS, VS, DE, CLOCK)
0V
T5 T6
Power supply for backlight
T1 (ms) T2 (ms) T3 (ms) T4 (ms) T5 (ms) T6 (ms)
SPEC (HSD) 0.5~10 0~50 0~50 >200 >200 >200
SPEC (LPL) 0.5~10 0.01~50 0.01~50 >500 >500 >200
5. D-SUB Connector Pin Assignment
6. AC input connector Pin Assignment
Pin Symbol Description
1 Line AC Line(Vin=100 to 240 Vrms,50/60Hz)
2 GND GND
3 Neutral AC Line(Vin=100 to 240 Vrms,50/60Hz)
7. Inner Connector Pin Assignment
7.1 CN103 (Connect M/B to Panel,)
Pin Symbol Description
1 Panel_Vcc Panel power supply (typ.5.0V)
2 Panel_Vcc Panel power supply (typ. 5.0V)
3 Panel_Vcc Panel power supply (typ. 5.0V)
4 NC
5 NC
Pin Symbol Pin Symbol Pin Symbol
1 Red 6 Red_GND 11 GND
2 Green 7 Green_GND 12 DDC_SDA
3 Blue 8 Blue_GND 13 Hsync
4 GND 9 PC+5V 14 Vsync
5 Cable Detect 10 GND 15 DDC_SCL
CN850
1 3
2

Service Manual
15
6 NC
7 GND_LVDS LVDS Ground
8 RXE3+ LVDS signal of even channel 3(-)
9 RXE3- LVDS signal of even channel 3(+)
10 RXEC+ LVDS signal of even channel clock (+)
11 RXEC- LVDS signal of even channel clock (-)
12 RXE2+ LVDS signal of even channel 2(+)
13 RXE2- LVDS signal of even channel 2(-)
14 GND_LVDS LVDS Ground
15 RXE1+ LVDS signal of even channel 1(+)
16 RXE1- LVDS signal of even channel 1(-)
17 GND_LVDS LVDS Ground
18 RXE0+ LVDS signal of odd channel 0(+)
19 RXE0- LVDS signal of odd channel 0(-)
20 RXO3+ LVDS signal of odd channel 3(+)
21 RXO3- LVDS signal of odd channel 3(-)
22 RXOC+ LVDS signal of even channel clock (+)
23 RXOC- LVDS signal of even channel clock (-)
24 GND_LVDS LVDS Ground
25 RXO2+ LVDS signal of even channel 2(+)
26 RXO2- LVDS signal of even channel 2(-)
27 RXO1+ LVDS signal of even channel 1(+)
28 RXO1- LVDS signal of even channel 1(-)
29 RXO0+ LVDS signal of odd channel 0(+)
30 RXO0- LVDS signal of odd channel 0(-)
7.2 CN1, CN2, CN3, CN4 (Connect to Panel Backlight,)
Pin Symbol Description
1 HV High voltage for lamp
2 LV Low voltage for lamp
7.3 CN104 (Connect to keypad, WAFER2*4P or compatible connector)
Pin Symbol Description
1 POWER OSD “POWER” control
2 LED Amber LED amber on/off control
3 LED Blue LED Blue on/off control
4 ENTER OSD “ENTER” control
5 PLUS/MINUS OSD “+/-” control and “AUTO/Brightness”adjustable hot key
6 MENU OSD “MENU” control
7 GND Ground
8 GND Ground

Service Manual
16
8. Key Parts Pin Assignments
8.1U105(TSUM1PER-LF-2)

Service Manual
17

Service Manual
18
8.2U108 (Serial Flash)
Pin Symbol I/O Description
1 CE# I The device is enabled by a high to low transition on CE#.
CE#
must remain low for the duration of any command
sequence.
2 SO I/O To transfer commands, addresses, or data serially into the
device.
3 WP# I/O The write protect (WP#) pin is used to enable/disable BPL
bit in
the status register.
4 VSS G Connect ground
5 SI I/O To transfer commands, addresses, or data serially into the
device
input are latched on the rising edge of the serial clock.
6 SCK I/O To provide the timing of serial interface.
Commands, addresses, or input data are latched on the
rising edge of the clock input, while output data is shifted
out on the
Falling edge of the clock input.
7 HOLD I/O To temporarily stop serial communication with SPI flash
memory without resetting the device.

Service Manual
19
8 VDD P To provide power supply.
8.3 U850 (LD7575, PWM Power Controller)
Pin Symbol I/O Description
1 RT To program the switching frequency. By
connecting a resistor to set the switching
frequency.
2 COMP I Voltage feedback pin. The PWM duty cycle is
controlled by COMP.
3 CS I Current sense for over current protection
4 GND Ground
5 OUT O PWM output
6 VCC I Power supply
7 NC Unconnected
8 HV I To provide the startup current for the controller.
8.4 U1 (INL837, CCFL Inverter controller IC)
Pin Symbol I/O Description
1 DRV1 O Drive output1
2 VDDA I Supply voltage input
3 DIM I Internal LPWM dimming or external PWM pulse
input for dimming function
4 ISEN I Current sense feedback
5 PID I Analog dim input
6 RSTR I Resistor to set striking frequency
7 RT I Resistor to set operating frequency
compensation range
8 ENA I ON/OFF control of IC
9 VSEN I Voltage sense
10 OVPT I Over-voltage/over-current protecting threshold
setting
11 LCT I Timing capacitor to set internal PWM dimming
frequency
12 SSTCMP I Capacitor for soft start time and loop
compensation
13 CT I Timing resistor and capacitor for operation and
striking frequency
14 TIMER I Timing capacitor to set striking time and
shutdown delay time
15 GNDA I Ground
16 DRV2 O Drive output2
Other manuals for E1709W
2
Table of contents
Other Dell Monitor manuals
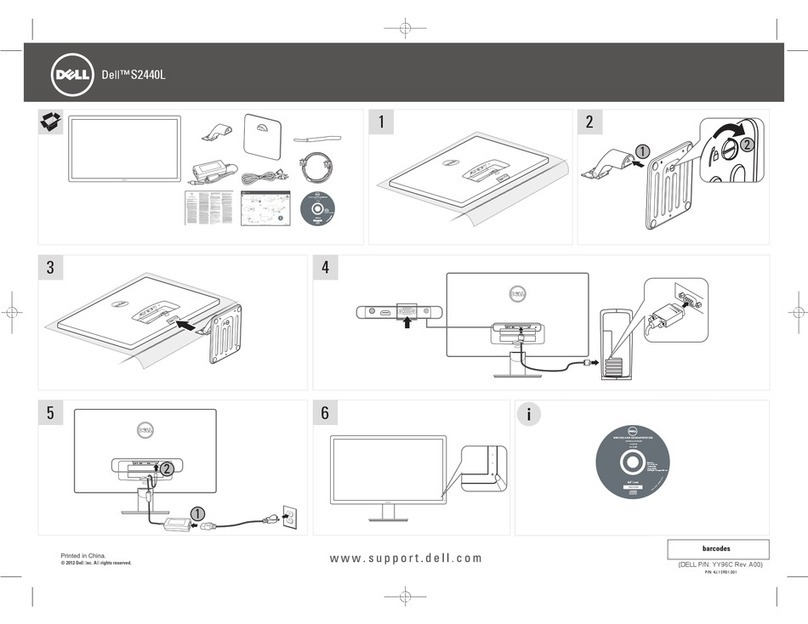
Dell
Dell S2440L Specification sheet
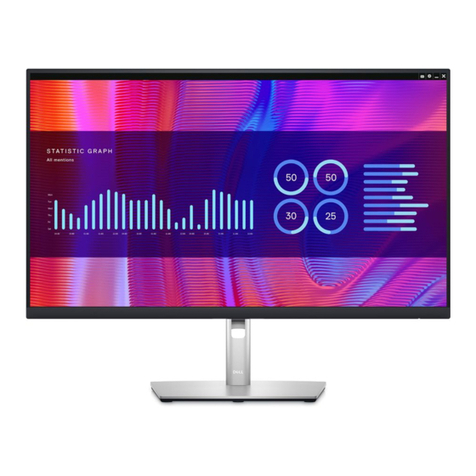
Dell
Dell P Series User manual
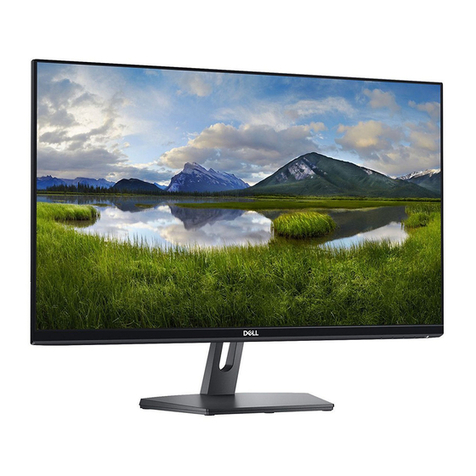
Dell
Dell SE2719HR User manual

Dell
Dell W2306C User manual
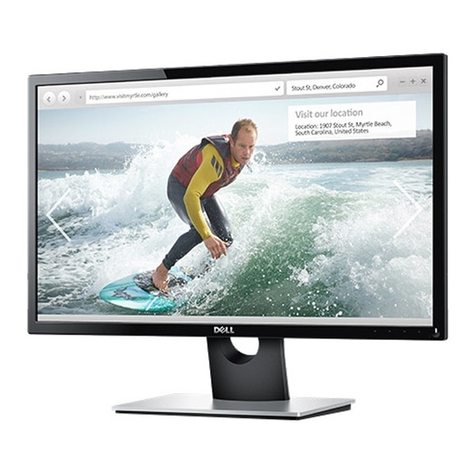
Dell
Dell SE2416HM User manual
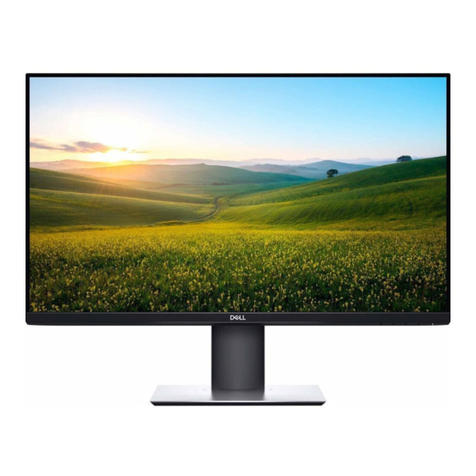
Dell
Dell P2720D User manual
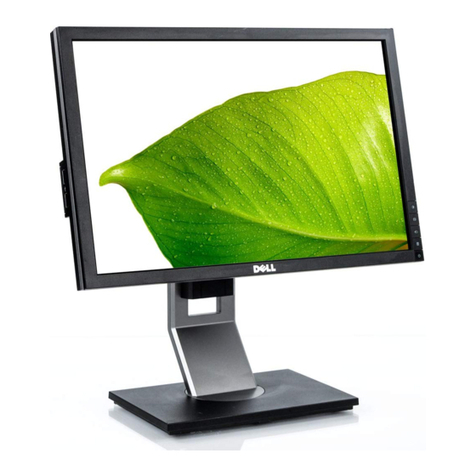
Dell
Dell 1909Wf User manual
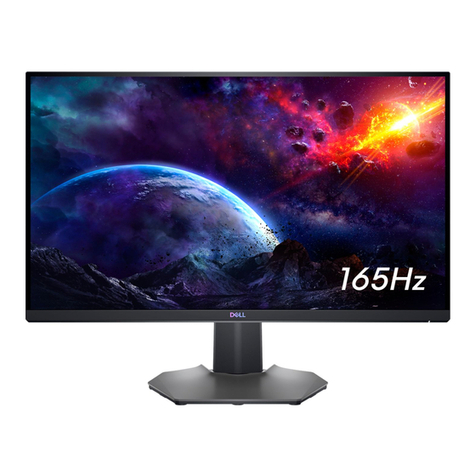
Dell
Dell S2721DGF User manual
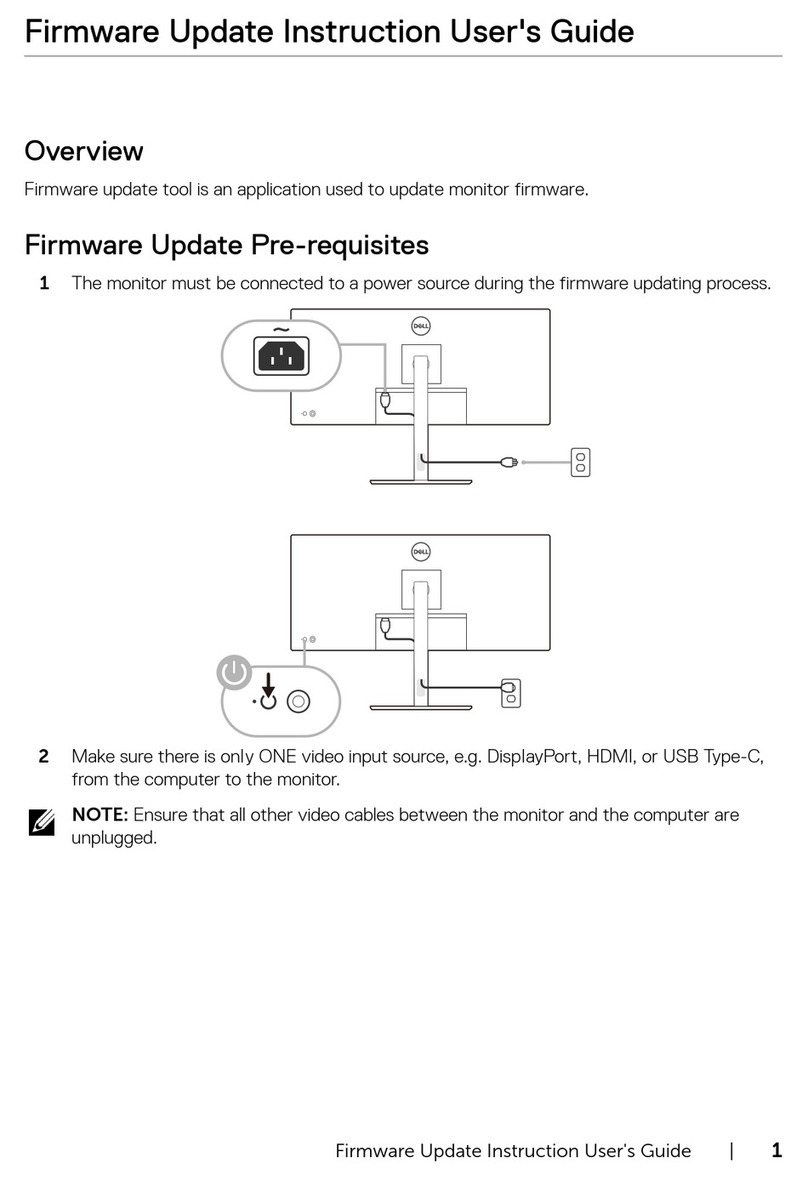
Dell
Dell P Series Use and care manual
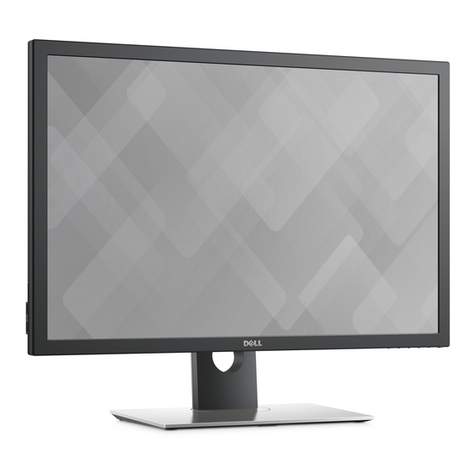
Dell
Dell UltraSharp UP3017 User manual

Dell
Dell E156FPc User manual
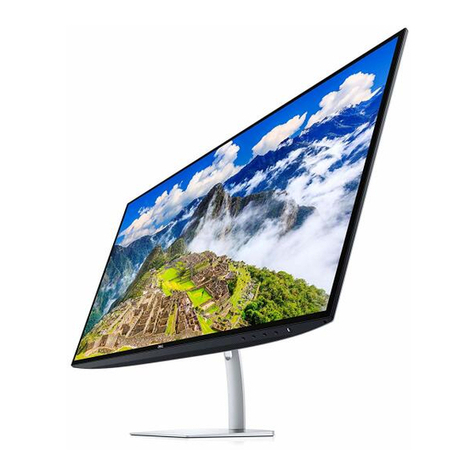
Dell
Dell S2719DC Instructions for use
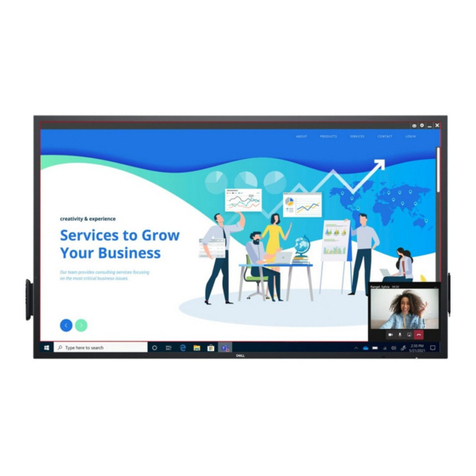
Dell
Dell C5522QT User manual
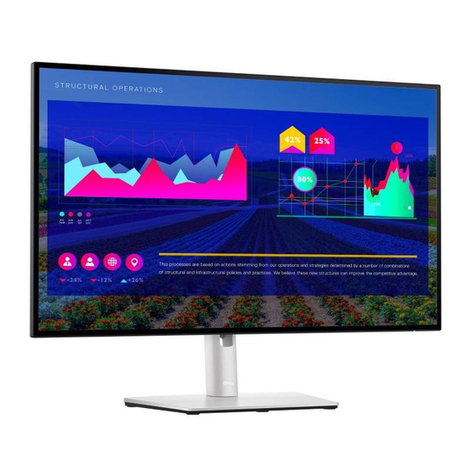
Dell
Dell UltraSharp 27 User manual
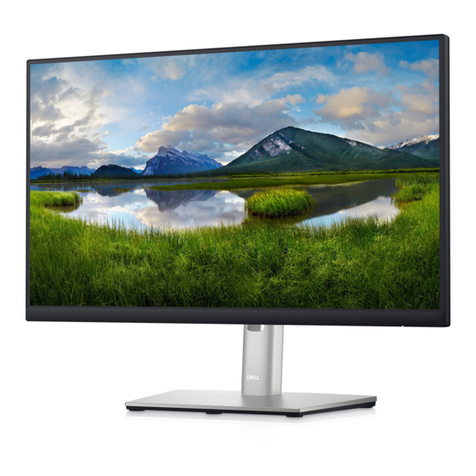
Dell
Dell P2223HC User manual
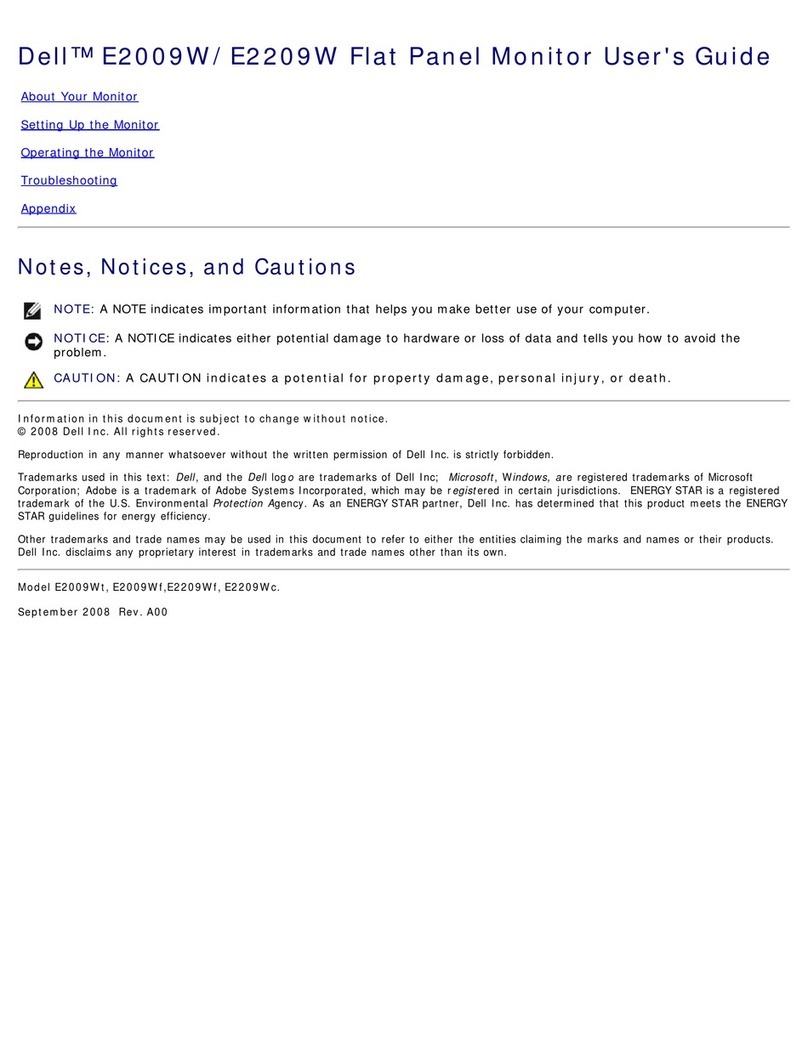
Dell
Dell E2209WFP User manual
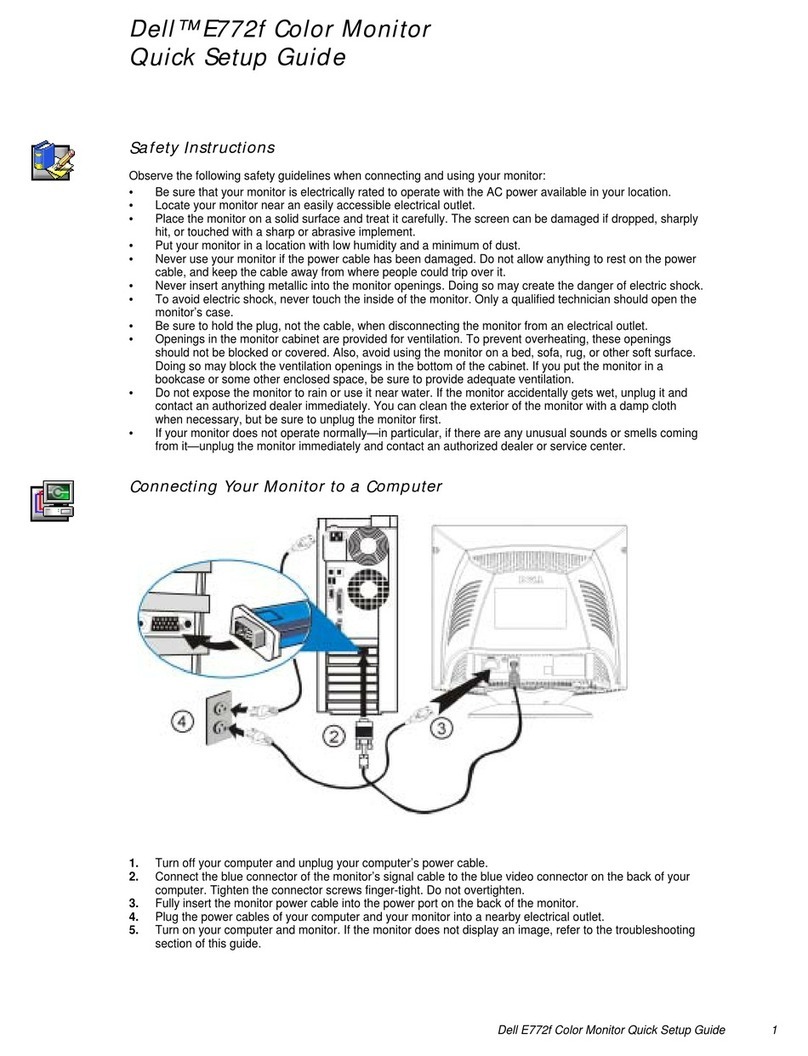
Dell
Dell E772f User manual
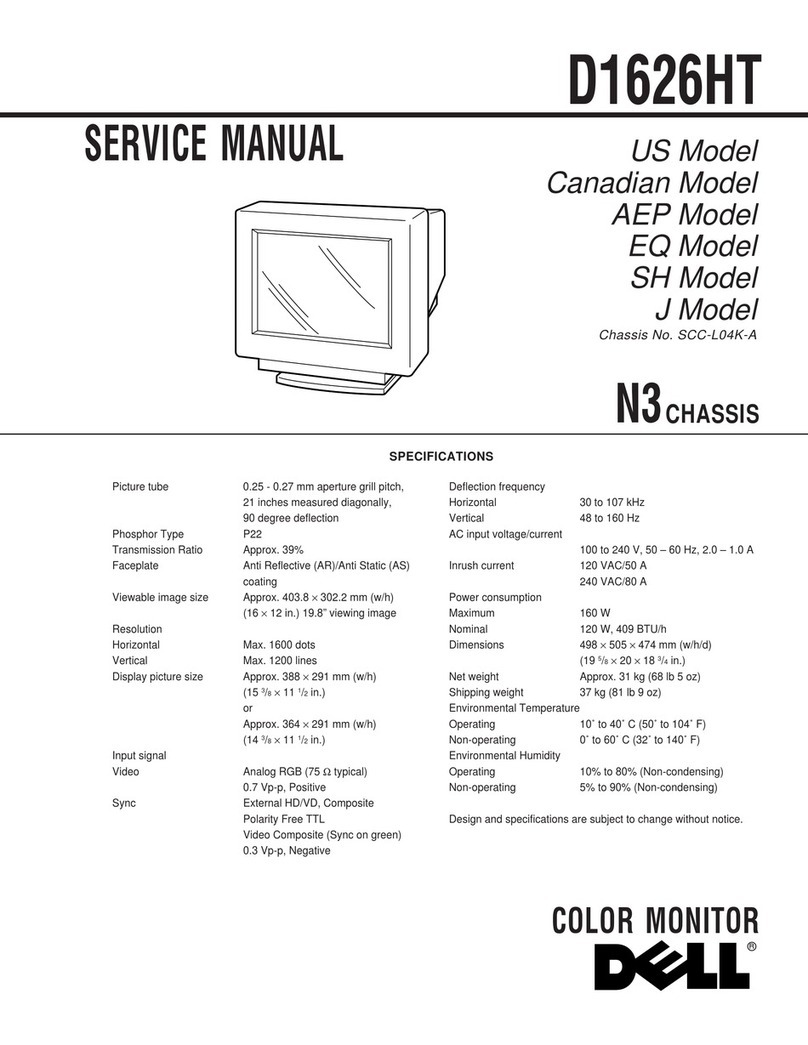
Dell
Dell D1626HT - UltraScan 1600HS - 21" CRT Display User manual
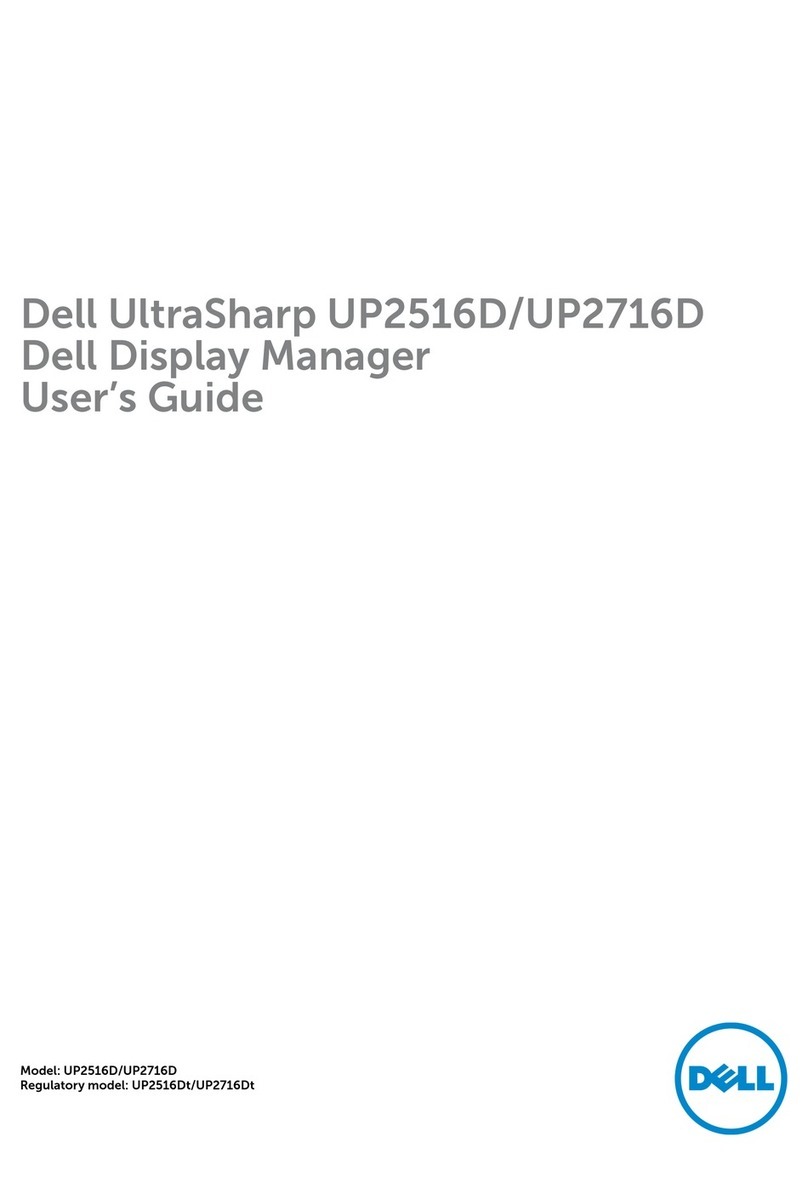
Dell
Dell UltraSharp UP2516D User manual
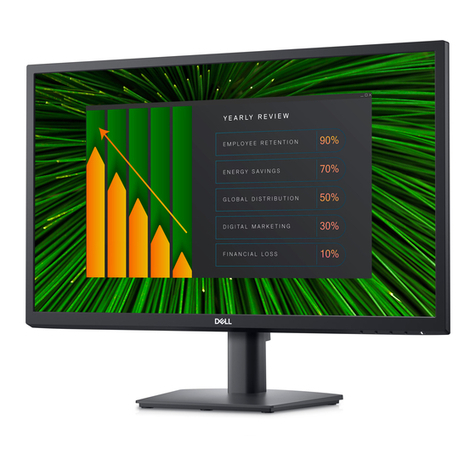
Dell
Dell E2423HN User manual