Det-Tronics R8471A User manual

Instructions 95-8398-02
Combustible Gas Controller
R8471A
Detector Electronics Corporation
6901 West 110th Street •Minneapolis, Minnesota 55438 USA
Tel: 612.941.5665 or 800.765.3473 •Fax: 612.829.8750 2/95

Section I - General Information
DESCRIPTION..........................................................1
FEATURES................................................................1
SPECIFICATIONS.....................................................1
SYSTEM OPERATION..............................................3
Sensor.................................................................3
Transmitter..........................................................3
Controller.............................................................3
Faceplate Description...................................3
Setpoints.......................................................4
Outputs.........................................................4
Automatic Diagnostics and Fault
Identification...........................................4
Operating Modes..........................................5
Section II - System Installation
INSTALLATION.........................................................7
Sensor Location ..................................................7
General Wiring Requirements.............................8
Sensor Separation...............................................9
Kit Description...............................................9
Sensor Installation......................................10
Wiring Requirements..................................10
Sensor Voltage Adjustment (K Series).......10
Sensor/Transmitter Wiring (without Sensor ...
Separation).................................................11
Controller Wiring................................................12
Field Wiring Connector...............................12
Controller Programming....................................15
Normally Open/Closed Relays....................15
Latching/Non-Latching Relays....................16
Normally Energized/De-Energized Relays .16
4 to 20 ma Output.......................................16
INSTALLATION CHECKLIST..................................16
Section III - System Startup
STARTUP PROCEDURE........................................16
SETPOINT ADJUSTMENT......................................17
Setpoint Display Mode ......................................17
Setpoint Adjustment Procedure.........................17
CALIBRATION.........................................................18
Conversion (K) Factor.......................................18
Calibration Procedure........................................19
Setting Controller Default Values................20
Transmitter Calibration Procedure
(K Series) .............................................20
Alternate Transmitter Calibration Procedure
(K Series) .............................................20
Controller Calibration Procedure ................22
Current Output Calibration ................................22
Section IV - System Maintenance
ROUTINE MAINTENANCE .....................................23
Manual Check of Output Devices......................23
Checkout in Normal Mode.................................23
Sensor Replacement.........................................23
Controller Calibration..................................24
Transmitter Calibration ...............................24
TROUBLESHOOTING.............................................24
LOSS OF SENSOR SENSITIVITY..........................24
REPLACEMENT PARTS.........................................26
DEVICE REPAIR AND RETURN ............................26
ORDERING INFORMATION...................................28
List of Illustrations
Figure 1 Controller Dimensions in Inches
(Centimeters)..........................................2
Figure 2 Controller Front Panel............................3
Figure 3 R8471 Controller Flow Chart..................6
Figure 4 Typical Installation Using Sensor Separa-
tion Kit with K Series Transmitter...........9
Figure 5 Sensor Separation with K Series
Transmitter...........................................11
Figure 6 Transmitter Wiring................................12
Figure 7 Dimensions of the Mounting Rack........13
Figure 8 Clip Positioning for Mounting Racks.....13
Figure 9 Terminal Configuration for R8471
Combustible Gas Controller.................14
Figure 10 A Typical System with Relay Outputs and
Non-Isolated Current Output................14
Figure 11 A Typical System with Relay Outputs and
Isolated Current Output........................14
Figure 12 Open Collector Output with Inductive Load
and Transient Suppression Device ......15
Figure 13 Programming Jumper Plugs and
Switches...............................................15
Figure 14 Calibration Sequence for K Series
Transmitter...........................................21
List of Tables
Table 1 Selectable Relay Options.......................2
Table 2 System Status Codes.............................5
Table 3 Maximum Wiring Distances - Controller
to K Series Transmitter...........................9
Table 4 Maximum Separation Distances - Sensor
to K Series Transmitter.........................10
Table 5 Troubleshooting Guide.........................25
Table of Contents
ii

Section I
General Information
DESCRIPTION
The R8471A Combustible Gas Controller monitors a 4
to 20 milliampere (ma) dc signal generated by a Det-
Tronics combustible gas sensor/transmitter assembly.
The single channel system operates in the range of 0
to 100% LFL (lower flammable limit). Controller
response includes actuation of solid state or optional
relay outputs for direct control of field response
devices, a full array of faceplate indicators, as well as
an optional 4 to 20 ma output for transmitting system
information to other monitoring devices.
FEATURES
•Controller accepts a 4 to 20 ma input, ensuring
compatibility with a variety of transmitters.
•Digital display, bar graph display, and high intensity
LEDs indicate important system status information.
•AutoCal feature ensures easy and accurate calibra-
tion.
•Microprocessor based controller is easily field pro-
grammable to meet the needs of a specific applica-
tion.
•Base model is furnished with solid state alarm and
fault outputs.
•Premium model is furnished with relay outputs and a
4 to 20 ma dc output.
•Current output is selectable for isolated/non-isolated
operation.
•Rack compatible with Det-Tronics R7400 series
flame controllers.
•Variety of racks available in 4U or 3U height config-
uration.
SPECIFICATIONS
CONTROLLER
OPERATING VOLTAGE—
24 vdc. Can operate in the range of 18 to 32 vdc.
MAXIMUM RIPPLE—
Ripple should not exceed 5 volts peak-to-peak. The
sum of dc plus ripple must be ≥18 vdc and ≤32 vdc.
POWER CONSUMPTION (controller only)—
Base model: 0.7 watt nominal, 1.3 watts maximum
(25 ma nominal, 50 ma maximum at 24 vdc.)
Premium model: 1.2 watts nominal, 3.5 watts maxi-
mum (50 ma nominal, 145 ma maximum at 24 vdc.)
TEMPERATURE RANGE—
Operating: +32°F to +140°F (0°C to +60°C)
Storage: –49°F to +185°F (–45°C to +85°C).
HUMIDITY RANGE—
5 to 99% RH, non-condensing.
OPERATING RANGE—0 to 100% LFL.
ACCURACY—
±3% of full scale over specified temperature range.
SOLID STATE OUTPUTS (Base model only)—
The outputs are open collector transistors with a 100K
resistor from the collector to emitter with the emitter
grounded, rated 100 ma at 32 volts dc maximum.
RELAY CONTACTS (Premium model only)—
Selectable normally open/normally closed contacts
rated 5 amperes at 30 vdc/250 vac. See Table 1 for
selectable relay options.
CURRENT OUTPUT (Premium model only)—
4 to 20 ma dc current, with a maximum loop resis-
tance of 600 ohms at 20 to 32 vdc.
INSTRUCTIONS
Combustible Gas Controller
R8471A
©Detector Electronics Corporation 1995 2/95 95-8398-02
DET-TRONICS®

DIMENSIONS—
See Figure 1.
SHIPPING WEIGHT (approximate)—
2.0 pounds (0.9 kilogram).
K SERIES TRANSMITTER
INPUT VOLTAGE—
24 vdc (10 to 28 vdc range).
POWER CONSUMPTION—
1.5 watts with sensor.
OUTPUT CURRENT—
Linear 4 to 20 ma.
ZERO SHIFT WITH TEMPERATURE—
0.02% LFL/°C at maximum gain.
GAIN SHIFT WITH TEMPERATURE—
0.01% LFL/°C at maximum gain.
TEMPERATURE RANGE—
Operating: 0°F to +167°F (–40°C to +75°C).
Storage: –49°F to +185°F (–45°C to +85°C).
SENSOR
RESPONSE TIME (with full scale gas applied)—
10 seconds to reach 50 percent of value of applied
gas, and 30 seconds to reach 90 percent of value of
applied gas.
ACCURACY—
±3 percent full scale up to 2.5 percent methane gas
by volume in air (50% LFL), ±5 percent full scale up
to 5 percent methane gas by volume in air (100%
LFL).
REPEATABILITY—
±5 percent, full scale.
ZERO DRIFT—
Less than 1% LFL per month.
OXYGEN EFFECTS—
The sensor will operate normally with the oxygen level
in the atmosphere at or above 10 percent concentra-
tion. Under oxygen enriched conditions the sensor
will respond normally, but the user should beware of
an increase in the explosive hazard. Contact the fac-
tory for information regarding use of the sensor in oxy-
gen deficient atmospheres.
HUMIDITY RANGE—
0 to 99% RH, non-condensing.
HUMIDITY EFFECT—
Less than ±5 percent full scale deviation at 10% to
90% RH.
SYSTEM APPROVAL—
The R8471A Combustible Gas Controller, base and
premium model in 3U and 4U height, has been tested
and approved by FMRC. It can be used with any
FMRC approved gas sensing device capable of gen-
erating a 4 to 20 ma input.
FMRC approval of the R8471A Combustible Gas
Controller, however, does not include or imply
approval of input devices such as sensors or trans-
mitters, or devices connected to the controller out-
puts. To maintain FMRC system approval, all equip-
ment connected to the controller must be FMRC
approved. Note that while the Det-Tronics com-
bustible gas sensor and K Series transmitter are fully
compatible with the R8471A Controller, they have not
been FMRC tested and approved for use with the
R8471A Controller.
2
Figure 1—Controller Dimensions in Inches (Centimeters)
Table 1—Selectable Relay Options
Relay Selectable Selectable Selectable
Normally Normally Latch/
Open/Closed Energized/ Non-Latch
De-Energized
Low Y Y Y
High Y Y N1
Auxiliary Y Y Y
Fault Y N2N3
Y = Yes N = No 1Latching only
2Normally energized 3No latching option
➛
➛
9.3 (23.6)
1.0
(2.5)
7.0*
(17.8)
➛
➛
➛
➛
A1526 *4U DIMENSIONS SHOWN, 3U HEIGHT IS 5.2 (13.3)

SYSTEM OPERATION
SENSOR
Det-Tronics combustible gas sensors use a catalytic
type sensing element and operate in the range of 0 to
100% LFL. Sensors are available in aluminum or
stainless steel housings, with a choice of three sens-
ing elements - standard, poison resistant, and high
temperature. With proper calibration, the sensor can
be used to detect a wide variety of combustible
gases. Contact Detector Electronics for assistance in
adapting the sensor to a specific application.
TRANSMITTER
The transmitter functions as the interface between the
sensor and the controller. It regulates operating
power to the sensor and generates a linear 4 to 20 ma
output signal proportional to 0 to 100% LFL com-
bustible gas concentration.
A transmitter output signal of less than 4 ma is dis-
played as a negative reading by the controller.
The sensor is normally threaded directly to the trans-
mitter enclosure. However, the sensor and transmitter
can be mounted separately using a Sensor
Separation Kit available from Detector Electronics.
The sensor, transmitter and separation kit are
designed for use in hazardous areas, and when prop-
erly installed will provide an explosion-proof installa-
tion.
Detector Electronics offers a variety of transmitter
models that operate in the 0 to 100% LFL range and
are compatible with the R8471 Controller. Refer to
the “Ordering Information” section for more informa-
tion.
CONTROLLER
Faceplate Description
The faceplate of the controller provides LEDs for iden-
tifying status conditions, a digital display and bar
graph display for indicating the sensor input, and
pushbuttons for programming, calibrating and reset-
ting the system. See Figure 2 for the location of indi-
cators and pushbuttons.
1. Digital Display—The digital display continuously
provides a % LFL reading of the sensor input in
both the Normal and Calibrate modes. In the
event of a fault, it identifies the nature of the fault
using an alpha-numeric code. In other operating
modes it shows the alarm setpoints and pro-
grammed calibration gas concentration. A nega-
tive zero drift condition is indicated by a minus (–)
sign in the left hand digit. If an over-range condi-
tion occurs, the display flashes and the highest
reading latches on. Since this display is always
on, it also functions as a power indicator.
2. Bar Graph Display—The 20 segment bar graph
display provides a reading of sensor input in 5%
LFL increments.
3. High Alarm LED—Flashes in response to a sensor
signal that exceeds the high setpoint.
4. Auxiliary Alarm LED—Flashes in response to a
sensor signal that exceeds the auxiliary setpoint.
5. Low Alarm LED—Flashes in response to a sensor
signal that exceeds the low setpoint.
NOTE
The alarm LEDs flash when the setpoint is
exceeded and are on steady (until reset) when
the gas level drops below the setpoint, whether
the corresponding alarm output is latching or
non-latching.
3 95-8398
Figure 2—Controller Front Panel

6. Cal LED—Illuminated while the controller is in the
calibrate mode.
NOTE
In the Setpoint Display or Setpoint Adjust mode,
a flashing alarm LED identifies the particular set-
point currently being indicated on the digital dis-
play. A flashing Cal LED indicates that the pro-
grammed calibration gas concentration in % LFL
is currently being shown on the digital display.
7. Fault LED—Flashes upon detection of a system
fault and is on steady during the power-up time
delay.
8. Reset Pushbutton—Used for various system pro-
gramming and calibration functions as well as for
resetting the controller.
9. Set Pushbutton—Used for various system pro-
gramming and calibration functions.
Setpoints
The R8471 Controller has independent Low, High,
and Auxiliary alarm setpoints, with corresponding out-
puts.
The programmed calibration gas concentration in %
LFL is also displayed and adjusted with the alarm set-
points. This value must be equal to the % LFL con-
centration of the calibration mixture that is used for
the span adjustment.
The adjustment range is:
Low alarm 5 to 50% LFL
High alarm 10 to 60% LFL
Auxiliary alarm 5 to 90% LFL
Calibration gas 30 to 99% LFL.
The alarm setpoints and calibration gas concentration
can be checked by pressing the Reset pushbutton
located on the front panel of the controller. See
“Setpoint Adjustment” and “Calibration” sections.
Outputs
The R8471 Controller is available in a Base version
and a Premium version. The differences between the
two models are the output configuration and program-
ming options.
Base Model—The base controller is furnished with
open collector transistor outputs (rated 100 ma at 32
volts dc) for the Low alarm, High alarm, Auxiliary
alarm, and Fault circuits. The normally de-energized
alarm outputs are energized when their correspond-
ing setpoints are exceeded. The fault output is nor-
mally energized and becomes de-energized upon
detection of a system fault.
Premium Model—The premium model is furnished
with a set of four relays in place of the four solid state
outputs. The relays have SPST contacts rated 5
amperes at 30 vdc or 250 vac.
This model also includes a selectable isolated/non-
isolated 4 to 20 ma dc current output for transmitting
system information to other monitoring devices. The
linear 4 to 20 ma output corresponds to levels from 0
to 100% LFL. If a system fault is detected, the output
drops to less than 1.0 ma. The current output can be
calibrated in the field to ensure maximum accuracy.
(Refer to the “Calibration” section for details.)
Programming Options (Premium model only)—Each of
the four relays is field selectable for either normally
open or normally closed contacts using jumper plugs
located on the printed circuit board inside the con-
troller. (See Table 1.)
The alarm relays are also switch programmable for
either normally energized or normally de-energized
operation. The fault relay is normally energized.
The low and auxiliary alarm relays are programmable
for either latching or non-latching operation. The high
alarm relay is always latching and the Fault relay is
non-latching. Latching relays are reset using either
the Reset pushbutton on the front panel of the con-
troller or an external reset switch.
The 4 to 20 ma circuit is selectable for isolated or
non-isolated operation.
Automatic Diagnostics and Fault Identification
The microprocessor based controller features self-
testing circuitry that continuously checks for faulty
sensor or open sensor wiring, low or high input volt-
age, and other problems that could prevent proper
system response. When power is applied, the micro-
processor automatically tests memory. In the Normal
operating mode, it continuously monitors the input
signal from the transmitter to ensure proper function-
ing. In addition, a “watchdog” timer is maintained to
ensure that the program is running correctly. If a fault
should occur:
— The Fault LED flashes.
— The digital display identifies the nature of the fault
using an alpha-numeric code. Refer to Table 2.
— The normally energized Fault output is de-ener-
gized.
— The dc current output drops to less than 1 ma.
4

NOTE
The fault code will be shown for about 2 seconds
out of every 5 seconds. The gas concentration
at the sensor will be displayed during the remain-
ing time. If more than one fault should occur, the
highest priority fault will be displayed. (Table 2
lists the faults in order of priority.)
An alarm condition will normally over-ride a fault con-
dition unless the fault condition occurred first (except
F10, F2X). However, faults that affect the actual func-
tion of the controller (F50, F60, F70, F9X) can impair
the ability of the controller to maintain an alarm out-
put.
All faults automatically reset except the F9X, F20, and
F10 faults. After the fault condition has been correct-
ed, the fault output automatically switches to the nor-
mal (energized) state, the dc current output returns to
normal, and the Fault LED turns off. Clearing F9X
faults requires removing operating power from the
controller for approximately one second.
CAUTION
The fault detection circuitry does not monitor the
operation of external response equipment or the
external wiring to these devices. It is important
that these devices be checked periodically to
ensure that they are operational.
Operating Modes
NOTE
The following section is intended to acquaint the
operator with the basic operation of the con-
troller. For complete step-by-step programming
and calibration procedures, refer to the corre-
sponding sections in this manual.
The controller can operate in any of the following
modes. Operating modes other than Normal are
selected by pressing the appropriate pushbutton(s)
located on the controller front panel. See Figure 3.
NORMAL
In the Normal operating mode with no alarm condi-
tion:
— Digital display is on and indicates the sensor input
in % LFL.
— Bar graph display reads the same as the digital
display.
— All LEDs are off.
— Alarm outputs are in their normal state (energized
or de-energized as programmed).
— DC current output signal level corresponds to sen-
sor input.
— Fault output is energized.
In the Normal operating mode with a low and/or auxil-
iary alarm condition occurring:
— Digital display and bar graph display indicate the
sensor input in % LFL.
— Low and/or Auxiliary LED flashes.
5 95-8398
Table 2—System Status Codes
Status Condition
F9X Initialization failure. (Subcodes are as fol-
lows.)
F91 EPROM sumcheck failure.
F92 Sensor failure during startup - current too
high or too low.
F93 Watchdog timer failure.
F94 RAM failure.
F95 Internal 5 volt power supply failure during
startup.
F96 External 24 volt power supply failure dur-
ing startup.
F97 Controller type invalid. Error in data from
RAM.
F98 Watchdog timer reset the controller.
F70 External reset button has been activated
for 15 seconds or longer. Self clearing
when button is released.
F60 External 24 vdc power input is not in the
18 to 32 vdc range.
F50 Internal 5 volt power supply is not in the
4.75 to 5.25 volt range.
F40 Sensor fault (after startup). Input is above
35 ma or below 2 ma.
F30 Negative zero drift. Sensor input is –9%
full scale or lower.
F2X Calibration error. (Subcodes are as fol-
lows.)
F20 General calibration fault, or calibration
aborted due to a higher priority fault.
F21 Time ran out while waiting for calibration
gas to be applied to the sensor.
F22 Sensor input is too low. The sensor cannot
generate enough offset to get an accurate
calibration. Replace sensor.
F23 Sensor is too sensitive for the controller to
read 100% full scale. Replace sensor.
F24 Zero gas level too high, or sensor zero
input over limit.
F10 Sensor reaching end of life. Consider
replacing the sensor within the next two
calibration periods.

— Low and/or Auxiliary alarm output changes state.
— Dc current output signal level corresponds to sen-
sor input.
— Fault output energized and LED off.
When the signal decreases below the low or auxiliary
setpoint:
— Digital display, bar graph display, and 4 to 20 ma
output continue to track the sensor input.
— With latching operation programmed: No change
to alarm outputs.
— With non-latching operation programmed: Alarm
outputs return to their normal state.
— Low and Auxiliary LEDs are on steady until reset.
In the Normal operating mode and a high alarm con-
dition occurring:
— Same as low or auxiliary alarm, but High LED is on
and high alarm output is actuated.
When the signal decreases below the high alarm set-
point:
— The high alarm is always latching and unaffected
by the latching/non-latching programming for the
low and auxiliary alarms. High LED is on steady
until reset.
In the event of a system fault:
— The normally energized Fault output is de-ener-
gized and the Fault LED is illuminated.
RESET
The Reset mode is the first mode that is entered by
pressing the Reset button located on the front panel
of the controller. (See Figure 3.) When the Reset but-
ton is momentarily depressed,all LEDs turn off and
all outputs return to their normal condition if no alarms
or faults are occurring (basic reset). When the Reset
button is held for 0.5 second,the LEDs turn off and
the outputs return to their normal condition even if an
alarm or fault condition still exists (forced reset).
Remote reset capability is also provided. (Remote
reset performs a forced reset.)
NOTE
The remote reset performs a reset function
only. It cannot be used for entering other
controller operating modes.
SETPOINT DISPLAY MODE
If the Reset button is held for approximately one sec-
ond, the digital display sequentially shows the pro-
grammed alarm setpoints and calibration gas con-
6
Figure 3—R8471 Controller Flow Chart
POWER-UP
TIME
DELAY
NORMAL RESET
< 0.5 SECOND 0.5 SECOND 1.0 SECOND
HOLD RESET
7 SECONDS
SET
1.0 SECOND
NO
YES
BASIC
RESET FORCED
RESET
RELEASE
RESET
RELEASE
RESET
RELEASE
RESET
SETPOINT
DISPLAY
HOLD
RESET
HOLD
RESET
HOLD
RESET
SENSOR
REPLACE
SETPOINT
ADJUST
CURRENT
CALIBRATE
RESET
PUSHED WITH
SET?
CALIBRATE
9.0 SECONDS
SET*
RESET
*MUST BE PRESSED BEFORE THE ZERO
CALCULATIONS ARE COMPLETED.
D1385

centration. Each value is displayed for approximately
2 seconds. After completing the sequence, the con-
troller automatically returns to the Normal operating
mode if the Reset button is no longer being
depressed.
This mode is used only for displaying the setpoints.
Use the “Setpoint Adjust” mode for changing setpoint
and calibration gas values.
CALIBRATE
The R8471 Controller uses a fully automatic calibra-
tion procedure that requires no adjustments to be
made by the operator. The Calibrate mode is entered
by pressing and holding the Reset button until com-
pletion of the “Setpoint Display” sequence described
above (approximately 9 seconds). The controller per-
forms the Zero adjustments, then signals the operator
when to apply and also when to remove the calibra-
tion gas. Upon completion of a successful calibra-
tion, the controller automatically returns to the Normal
operating mode.
If the operator fails to complete the calibration proce-
dure, if an error in calibrating occurs, or if a success-
ful calibration cannot be completed, the microproces-
sor will automatically return to the Normal mode (after
10 minutes) and continue to use the previous calibra-
tion data. A fault indication (“F2X” status) will be dis-
played until a reset occurs. If the microprocessor
determines that the sensing element is approaching
the end of its useful life, “F10” will be indicated on the
digital display. Refer the “Calibration” section for
complete information regarding calibration.
While in the Calibrate mode, all controller outputs are
inhibited, the CAL LED is illuminated, and the dc cur-
rent output goes to a preset level (adjustable from 0
to 20 ma).
SENSOR REPLACEMENT
This mode inhibits all controller outputs to allow sen-
sor replacement without removing power from the
controller. In addition, this mode automatically sets
the factory default values for sensor calibration.
Other programmed setpoint values are not affected.
CAUTION
Upon entering the Sensor Replacement mode,
all previously entered sensor calibration informa-
tion is lost. Sensor calibration must be per-
formed, even if the sensor was not replaced.
To enter the Sensor Replacement mode, first enter the
Calibrate mode as described above, then press the
Set button. To exit this mode, press the Reset button.
SETPOINT ADJUST
The Setpoint Adjust mode is entered by depressing
the Set button for approximately one second. In this
mode the alarm setpoints and calibration gas level
are sequentially displayed on the digital display for
approximately five seconds and the corresponding
LED flashes. To change the setpoint, depress the
Reset button to increase the displayed value or the
Set button to decrease the value. If no changes are
made for 5 seconds, the microprocessor automatical-
ly advances to the next setpoint. At the end of the
sequence, the microprocessor automatically returns
to the Normal operating mode.
DC CURRENT OUTPUT CALIBRATION
This mode is used to calibrate the 4 to 20 ma dc out-
put. To enter this mode, hold the Set button, then
press Reset. First the 0% LFL value (4 ma) is gener-
ated for approximately 7 seconds while the Low LED
flashes. Then the 100% LFL value (20 ma) is generat-
ed while the High LED flashes. Finally the current out-
put during calibration is generated while the CAL LED
flashes. The microprocessor automatically returns to
the normal operating mode at the end of the
sequence. Adjustments to the current output level
are made by pressing the Reset (increase) or Set
(decrease) button. This procedure requires a dc cur-
rent meter to monitor the actual controller dc mil-
liampere output.
Section II
System Installation
INSTALLATION
NOTE
The sensor is not included in the FMRC
approval.
NOTE
Refer to the sensor manual for complete infor-
mation regarding sensor installation.
SENSOR LOCATION
It is essential that the sensor be properly located to
enable it to provide maximum protection. The formula
for determining the most effective number and place-
ment of sensors varies depending on the conditions
at the job site. The individual performing the installa-
tion must rely on experience and common sense to
determine the quantity of sensors and the best sensor
locations to adequately protect the area.
7 95-8398

For additional information on determining quantity and
placement for sensors in a specific application, refer
to Instrument Society of America (ISA) Transaction
Volume 20, Number 2, titled “The Use of Combustible
Detectors in Protecting Facilities from Flammable
Hazards”.
The following factors should be considered for every
installation:
1. What kind of gas is to be detected? If it is lighter
than air (acetylene, hydrogen, methane, etc.),
place the sensor above the potential gas leak.
Place the sensor close to the floor for gases that
are heavier than air (benzene, butane, butylene,
propane, hexane, pentane, etc.) or for vapors
resulting from flammable liquid spills. However,
note that air currents can cause a gas that is
heavier than air to rise. In addition, if the gas is
hotter than ambient air, it could also rise.
2. How rapidly will the gas diffuse into the air?
Select a location for the sensor as close as practi-
cal to an anticipated source.
3. Ventilation characteristics of the immediate area
must also be considered. Movement of air can
cause gas to accumulate more heavily in one
area than another. The sensor should be placed
in the area where the most concentrated accumu-
lation of gas is anticipated. Also consider the fact
that many ventilation systems do not operate con-
tinuously.
4. The sensor should be pointed down to prevent
the buildup of moisture or contaminants on the fil-
ter and to ensure proper operation.
5. The sensor must be accessible for testing and
calibration. The use of the Sensor Separation Kit
will be required in some installations.
6. The sensor should be located in an area where it
is safe from potential sources of contamination
that can poison the sensing element.
7. Exposure to excessive heat or vibration can result
in premature failure of any electronic device and
should be avoided if possible. Shielding the
device from intense sunlight will reduce solar
heating and can increase the life of the unit.
Remember, the finest gas detector is of little value if
the gas cannot readily come into contact with it.
GENERAL WIRING REQUlREMENTS
NOTE
The wiring procedures in this manual are intend-
ed to ensure proper functioning of the device
under normal conditions. However, because of
the many variations in wiring codes and regula-
tions, total compliance to these ordinances can-
not be guaranteed. Be certain that all wiring
complies with applicable regulations that relate to
the installation of electrical equipment in a haz-
ardous area. If in doubt, consult a qualified offi-
cial before wiring the system.
In applications where the wiring cable is installed in
conduit, the conduit must not be used for wiring to
other electrical equipment.
The use of shielded cable is recommended for con-
necting the transmitter to the controller. If a sensor
separation kit is used, shielded cable must be used
between the sensor and the transmitter.
Since moisture can be detrimental to electronic
devices, it is important that moisture not be allowed to
come in contact with the electrical connections of the
system. Moisture in the air can become trapped with-
in sections of conduit. Therefore, the use of conduit
seals is required to prevent damage to electrical con-
nections caused by condensation within the conduit.
These seals must be watertight and explosion-proof
and are to be installed even if they are not required
by local wiring codes. A seal must be located as
close to the device as possible. In no case should this
seal be located more than 18 inches (46 cm) from the
device. When an explosion-proof installation is
required, an additional seal may be needed at any
point where the conduit enters a non-hazardous area.
Always observe the requirements of local codes.
When pouring a seal, the use of a fiberdam is
required to assure proper formation of the seal. The
seals should never be poured in temperatures that
are below freezing, since the water in the sealing
compound will freeze and the compound will not dry
properly. Contamination problems can then result
when temperatures rise above the freezing point and
the compound thaws.
The shielding of the cable should be stripped back to
permit the seal to form around the individual leads,
rather than around the outside of the shield. This will
prevent any siphoning action that can occur through
the inside of the shield.
8

It is recommended that conduit breathers also be
used. In some applications, alternate changes in
temperature and barometric pressure can cause
“breathing”, which allows the entry and circulation of
moist air throughout the conduit. Joints in the conduit
system and its components are seldom tight enough
to prevent this “breathing”. Moisture in the air can
condense at the base of vertical conduit runs and
equipment enclosures, and can build up over a peri-
od of time. This can be detrimental to electronic
devices. To eliminate this condition, explosion-proof
drains and breathers should be installed to automati-
cally bleed off accumulated water.
Three wire cable is used for connecting the
sensor/transmitter assembly to the controller. Three
conductor cable with a foil shield is recommended.
The shield of the cable should be open at the trans-
mitter junction box and connected to earth ground at
the controller.
The maximum distance between the transmitter and
controller is limited by the resistance of the connect-
ing wiring, which is a function of the gauge of the wire
being used. Table 3 shows the maximum wiring dis-
tance allowed for a given wire size when using K
Series Transmitters. For other transmitter models,
refer to the transmitter manual for specific instruc-
tions.
SENSOR SEPARATION
The Sensor Separation Kit is designed for use in
applications where the sensor and transmitter must
be installed in different locations.
NOTE
The illustrations in the following section show the
sensor separation kit used with a K Series
Transmitter. Although the basic wiring scheme
is similar for other transmitter models, factors
such as wiring distances and wire gauge will be
different in each case. Refer to the transmitter
manual for information specific to that model.
Kit Description
The sensor separation kit consists of the following:
— Junction box with connector board
— Shorting plug
— Calibration cup
— Separation kits used with Model 400/405
Transmitters also include a plug-in connector kit.
NOTE
When using a sensor separation kit with K Series
Transmitters, a transmitter extender plug is
required for adjusting sensor voltage. The exten-
der plug is not included in the separation kit.
Refer to the “Ordering Information” section for
part number.
The aluminum junction box is designed for use in haz-
ardous areas, and when properly installed will provide
an explosion-proof installation. The connector board
assembly, mounted inside the junction box, contains
the terminals for connecting the sensor and external
wiring.
See Figure 4 for an illustration of a typical system
using the Sensor Separation Kit.
9 95-8398
Table 3—Maximum Wiring Distances –
Controller to K Series Transmitter
Wire Size Maximum Controller to
Transmitter Distance
AWG Diameter
No. (millimeters) (feet) (meters)
18 1.024 1,800 550
16 1.291 2,900 900
14 1.628 4,600 1,400
12 2.053 7,300 2,200
Figure 4—Typical Installation Using Sensor Separation Kit with
K Series Transmitter
INSTALL SHORTING PLUG HERE
TO CONTROLLER
SEALS*
PLUG IN TRANSMITTER
MODULE HERE
TRANSMITTER LOCATION
*CONDUIT SEAL REQUIRED WITHIN
18 INCHES (48 CM) OF CONDUIT ENTRY
SENSOR LOCATION
CONNECT KEYED SENSOR
PLUG TO PIN CONNECTOR
CONNECT THE TRANSMITTER
TO THE CONTROLLER USING
3-WIRE SHIELDED CABLE.
GROUND THE SHIELD AT THE
CONTROLLER END ONLY
B1386
USING 3–WIRE SHIELDED CABLE,
CONNECT BLK–, RED CTR AND WHT+
TERMINALS IN SENSOR JUNCTION BOX
TO CORRESPONDING TERMINALS
LABELED “TO SENSOR” IN TRANSMITTER
JUNCTION BOX. GROUND THE SHIELD
AT THE TRANSMITTER BOX ONLY.

The shorting plug, which attaches to the connector
board, must be in place at all times that the sensor is
operating.
The calibration cup can remain on the sensor after
calibration without interfering with normal operation.
By connecting a length of tubing from the calibration
cup back to the transmitter location, the operator can
make calibration adjustments and also control the
flow of calibration gas from the same location.
IMPORTANT
The operator must frequently inspect the filter on
the calibration cup. This filter must be kept
clean. If the filter should become clogged by
environmental contaminants such as dirt, oil,
paint, etc., the flow of gas to the sensing element
will be restricted. This can significantly reduce
the sensitivity and response time of the sensor,
thereby impairing the ability of the system to
respond to a hazardous condition. Problems of
this nature will not be detected by the system’s
diagnostic circuitry or during routine calibration.
If the filter becomes dirty and cannot be properly
cleaned, the calibration cup must be replaced.
Sensor Installation
For proper operation, the sensor must be oriented
with the filter pointing down. Install the sensor in the
lower 3/4 inch NPT opening on the junction box.
Connect the conduit to the upper opening.
The sensor junction box can be mounted to a wall or
post, or it can be suspended by the conduit. The
junction boxes should be electrically connected to
earth ground.
Wiring Requirements
Three wire cable is used for connecting the sensor to
the transmitter and also for connecting the transmitter
to the controller. The use of shielded cable is
required for connecting the sensor and transmitter,
and is highly recommended for connecting the trans-
mitter and controller. Three conductor cable with a
foil shield is recommended. The shield of the cable
connecting the sensor and transmitter should be
open at the sensor junction box and connected to
earth ground at the transmitter junction box. The
shield of the cable connecting the transmitter and
controller should be open at the transmitter junction
box and connected to earth ground at the controller.
The maximum distance between the sensor and
transmitter is limited by the resistance of the connect-
ing wiring, which is a function of the gauge of the wire
being used. Note that maximum wiring distances
also vary with the specific transmitter model being
used. Table 4 shows the maximum separation dis-
tance allowed for a given wire size when using K
Series Transmitters. For other transmitter models,
refer to the transmitter manual for specific instruc-
tions.
Sensor Voltage Adjustment (K Series Transmitters
only)
When using a sensor separation kit with a K Series
Transmitter, an adjustment to the sensor voltage is
required to assure proper operation. This adjustment
should be performed at the time of system startup,
before calibration is performed.
The combustible gas sensor is designed to operate at
3.3 volts dc. Greater voltages will shorten sensor life
and lower voltages will reduce sensitivity to certain
gases. The sensor supply voltage is factory adjusted.
However, re-adjustment is necessary if the sensor
and transmitter are separated.
CAUTION
Sensor voltage adjustment requires the removal
of the junction box cover at both the sensor and
transmitter locations. The area must be de-clas-
sified when removing the junction box cover with
power applied to the system.
To adjust sensor voltage, connect a digital voltmeter
across +WHT and –BLK on the connector board
inside the sensor junction box (see Figure 5). Install
the transmitter extender plug between the transmitter
module and the connector board in the transmitter
junction box to allow access to potentiometer R18 on
the transmitter module. Adjust R18 to obtain a read-
ing of 3.3 volts on the voltmeter.
10
Table 4—Maximum Separation Distances – Sensor to K Series
Transmitter
Shielded Recommended Maximum
Wire Size Transmitter to
(AWG) Sensor Distance*
Feet Meters
18 50 15
16 75 23
14 125 38
*Sensor voltage adjustment is required.

SENSOR/TRANSMITTER WIRING (without Sensor
Separation)
The following section describes the installation and
wiring procedure for K Series Transmitters.When
using other transmitter models, mount and wire the
sensor and transmitter as described in the transmitter
manual.
1. Locate the sensors in positions that are best suit-
ed for covering the area to be protected, following
the previously discussed guidelines. Whenever
practical, they should be placed where they are
easily accessible for calibration.
NOTE
Do not apply power to the system with the junc-
tion box cover removed unless the area has
been de-classified.
2. Remove the cover from the transmitter junction
box.
NOTE
The transmitter and controller contain semicon-
ductor devices that are susceptible to damage by
electrostatic discharge. An electrostatic charge
can build up on the skin and discharge when an
object is touched. Therefore, use caution when
11 95-8398
Figure 5—Sensor Separation with K Series Transmitter
ADJUST SENSOR VOLTAGE TO
MEASURE 3.3 VDC BETWEEN
THE + AND –TERMINALS
WITH SENSOR AND SHORTING
PLUG INSTALLED
SENSOR VOLTAGE
ADJUST (REF. R18)
SHORTING PLUG
CONNECTOR BOARD
JUNCTION BOX
SENSOR
TRANSMITTER
EXTENDER PLUG
SENSOR SEPARATION
CONNECTOR BOARD
JUNCTION BOX
TRANSMITTER BOARD
USER SUPPLIED TUBING
(1/4 INCH I.D.)
APPLY CALIBRATION GAS HERE
WIRING TO CONTROLLER
TRANSMITTER LOCATION
WIRING TO SENSOR
CALIBRATION CUP
C1335

handling, taking care not to touch the terminals
or electronic components. For more information
on proper handling, refer to Service Memo form
75-1005.
3. Remove the transmitter module from the junction
box.
4. The junction box can be mounted to a wall or
post, or it can be suspended by the conduit. The
junction box should be electrically connected to
earth ground.
For proper operation, the sensor must be oriented
with the filter pointing down. Install the sensor in
the lower 3/4 inch NPT opening on the junction
box. Connect the conduit to the upper opening.
5. Attach the sensor to the junction box. The sensor
should be tight to ensure an explosion-proof
installation, however, do not overtighten. Attach
the wiring plug at the appropriate terminal loca-
tion. (See Figure 6.)
CAUTION
The sensor threads can be coated with an appro-
priate grease to ease both the initial installation
and future replacement of the sensor. Also lubri-
cate the cover threads. The recommended lubri-
cant is a silicone free polyalphaolefin grease,
part number 005003-001, available from
Detector Electronics. The use of other lubricants
is not recommended, since some materials can
cause irreversible damage to the sensing ele-
ment. Silicone based lubricants or compounds
must never be used.
6. Connect the power and current output leadwires
to the appropriate screw terminals inside the junc-
tion box. When using shielded cable, the shield
should be connected to earth ground at the con-
troller end only.
The wiring code is:
BLK – = Power supply negative (–)
RED CTR = Signal
WHT + = Power supply positive (+).
7. Check all field wiring to ensure that the proper
connections have been made, then pour the con-
duit seals and allow them to dry (if conduit is
being used).
8. Install the transmitter module inside the junction
box.
9. Place the cover back on the junction box.
CONTROLLER WIRING
Field Wiring Connector
The controller is furnished with a field wiring connec-
tor backplate that incorporates pressure type screw
terminals for connecting the external wiring and a cir-
cuit board edge connector for attaching to the con-
troller. The use of a mounting rack is recommended
for mounting the controller. The backplate is attached
to the back of the rack to allow easy removal of the
controller without disturbing the wiring. See Figures 7
and 8.
The controller is designed for installation in a non-haz-
ardous area.
Figure 9 shows the terminal configuration for the
R8471 Combustible Gas Controller.
Terminals 1 and 2— 4 to 20 ma dc output.
Non-Isolated Current Output –If the 4 to 20 ma
current loop is to be non-isolated, wire the system
as shown in Figure 10. Note that terminal 2 is not
used with a non-isolated current loop. Program the
unit for a non-isolated current loop as described in
the “Controller Programming” section.
Isolated Current Output –If an isolated current
loop is desired, wire the system as shown in Figure
11 and program the unit for an isolated current
loop as described in the “Controller Programming”
12
Figure 6—Transmitter Wiring
B1334
GROUND JUNCTION BOX
ACCORDING TO LOCAL CODES
SENSOR
BLK –
RED CTR
WHT +
J3
P3
J1
JUNCTION BOX
CONNECTOR BOARD
TRANSMITTER MODULE PLUGS IN HERE
CONDUIT SEAL REQUIRED HERE
CONDUIT

13 95-8398
Figure 7—Dimensions of the Mounting Rack
(A)
(B)
(C)
1.48 (37.59)
(D)
B1475
ALL CONTROLLER CAGES REQUIRE
A MINIMUM OF 10.12 INCHES (257.1 MM)
DEPTH CLEARANCE
(E)
Figure 8—Clip Positioning for Mounting Racks
1
A1476
FIRE CONTROLLERS ARE APPROX. TWO INCHES
WIDE AND REQUIRE TWO GUIDE RAILS FOR
INSERTION. PLACE THE RETAINING CLIP BETWEEN
RAILS TO FORM SETS, LEAVE A GAP BETWEEN SETS.
SET SETGAP
123 2
THE Q4004 CONTROLLER CAGE HAS BEEN MODIFIED
TO ACCOMMODATE EITHER FIRE OR GAS CONTROLLERS
OR ANY COMBINATION OF THE TWO.
BY FOLLOWING THE INSTRUCTIONS BELOW, THE CAGE
CAN BE SET UP TO ANY CONFIGURATION.
2TO INSERT A BLANK PANEL, PLACE A CLIP IN
THE TOP BRACKET IN LINE WITH THE CLIP IN THE
BOTTOM BRACKET.
3
GAS CONTROLLERS ARE APPROX. ONE INCH WIDE
AND REQUIRE ONE RAIL FOR INSERTION. PLACE CLIPS
IN LINE WITH GUIDE RAILS, CAGES WILL ACCEPT AS
MANY GAS CONTROLLERS AS RAILS PROVIDED.
CONTROLLER
POSITIONS FOR: HT: DIM. (A) DIM. (B) DIM. (C) DIM. (D) DIM. (E)
FIRE GAS INCH MM INCH MM INCH MM INCH MM INCH MM
8 16 4U 19.00 482.6 18.30 464.8 17.36 440.9 4.00 101.6 6.97 177.1
6 12 4U 15.06 382.6 14.36 364.7 13.42 340.9
4 8 4U 11.13 282.6 10.43 264.9 9.49 241.1
3 6 4U 9.16 232.7 8.46 214.9 7.52 191.0
2 4 4U 7.19 182.7 6.49 164.9 5.55 141.0
1 2 4U 5.22 132.6 4.52 114.8 3.58 90.9
16 3U 19.00 482.6 18.30 464.8 17.36 440.9 2.25 57.15 5.22 132.6
12 3U 15.06 382.6 14.36 364.7 13.42 340.9
8 3U 11.13 282.6 10.43 264.9 9.49 241.1
6 3U 9.16 232.7 8.46 214.9 7.52 191.0
4 3U 7.19 182.7 6.49 164.9 5.55 141.0
2 3U 5.22 132.6 4.52 114.8 3.58 90.9

section. Note that this wiring scheme requires an
external power source for the isolated current out-
put.
Terminal 3— Chassis ground. Ground the cable
shield at this terminal.
NOTE
If local wiring codes permit and if a ground fault
monitoring system is not being used, the minus
side of the dc power source can be connected to
chassis (earth) ground. Alternatively, a 0.47
microfarad, 100 volt capacitor can be installed
(terminal 5 to ground) for best immunity against
electromagnetic interference.
Terminal 4— Connect to the positive (+) side of the
18 to 32 vdc power source.
Terminal 5— Connect to the negative (–) side of the
dc power source.
Terminal 6— Make no connections to this terminal.
Terminal 7— 4 to 20 ma dc signal input from transmit-
ter/sensor assembly.
Terminal 8— A normally open momentary closure
switch can be connected between this
terminal and the negative (–) side of the
power source for remote reset.
Terminals 9 and 10— High Alarm Output.
Terminals 11 and 12— Auxiliary Alarm Output.
Terminals 13 and 14— Low Alarm Output.
Terminals 15 and 16— Fault Output.
14
Figure 10—A Typical System with Relay Outputs and Non-Isolated
Current Output
CURRENT OUTPUT
CHASSIS GROUND
POWER
SENSOR
EXTERNAL RESET
HIGH ALARM
HIGH ALARM / OC
AUX. ALARM
AUX. ALARM / OC
LOW ALARM
LOW ALARM / OC
FAULT
FAULT / OC
1
3
4
5
6
7
8
9
10
11
12
13
14
15
16
–
+
+
–
+
–
18 TO 32
VDC
POWER
SIGNAL
2
OC = OPEN COLLECTOR OUTPUT
(BASE MODEL ONLY) B1390
Figure 9—Terminal Configuration for R8471 Combustible
Gas Controller
ISOLATED OUTPUT
CURRENT LOOP
CHASSIS GROUND
POWER
SENSOR
EXTERNAL RESET
HIGH ALARM
HIGH ALARM / OC
AUX. ALARM
AUX. ALARM / OC
LOW ALARM
LOW ALARM / OC
FAULT
FAULT / OC
1
3
4
5
6
7
8
9
10
11
12
13
14
15
16
–
+
+
–
+
–
18 TO 32VDC
GROUND
POWER
SIGNAL
HIGH
ALARM
AUXILIARY
ALARM
LOW
ALARM
FAULT
RESET
24
VDC
+
–
+
–
SIG
TRANSMITTER
SENSOR
24-20 MA
B1382
R8471 CONTROLLER
*
*
*NO CONNECTION
Figure 11—A Typical System with Relay Outputs and Isolated
Current Output
ISOLATED OUTPUT
CURRENT LOOP
CHASSIS GROUND
POWER
SENSOR
EXTERNAL RESET
HIGH ALARM
HIGH ALARM / OC
AUX. ALARM
AUX. ALARM / OC
LOW ALARM
LOW ALARM / OC
FAULT
FAULT / OC
1
3
4
5
6
7
8
9
10
11
12
13
14
15
16
–
+
+
–
+
–
18 TO 32VDC
GROUND
POWER
SIGNAL
HIGH
ALARM
AUXILIARY
ALARM
LOW
ALARM
FAULT
RESET
24
VDC
+
–
+
–
SIG
TRANSMITTER
SENSOR
2
4-20 MA
A1391
R8471 CONTROLLER
*
*NO CONNECTION
24
VDC
+
–

PREMIUM CONTROLLER – The relay outputs (termi-
nals 9 to 16) are programmed for the desired opera-
tion using the procedure described in the “Controller
Programming” section.
BASE CONTROLLER – Connections to open collec-
tor transistor outputs are made at terminals 10, 12, 14,
and 16. Terminals 9, 11, 13, and 15 are not used.
See Figure 12 for an example of a typical connection
to an open collector transistor output.
NOTE
External equipment that can generate transients
when switching (such as relays) must have a
transient suppression device (diode) properly
connected across the coil at the time of installa-
tion. This will safeguard the output transistors of
the controller against possible damage. Figure
12 illustrates an inductive load with a diode used
for transient suppression.
CONTROLLER PROGRAMMING
Refer to Figure 13 to determine the location of pro-
gramming jumpers and switches. Table 1 shows the
selectable options for each relay.
NOTE
All of the controller jumper plugs must be
installed. The controller outputs will not function
properly if a jumper plug is missing.
Normally Open/Closed Relays
The four relays are individually programmed for either
normally open or normally closed contacts. This is
accomplished by placing a jumper plug on the appro-
priate pair of pins. Each relay has a set of three pins.
For normally open operation, place the plug on the
NO and center pins. For normally closed operation,
15 95-8398
100K
R7484
OPEN COLLECTOR OUTPUT
1N4004
TYPICAL
+24 VDC (+60 VDC MAXIMUM)
C1289
Figure 12—Open Collector Output with Inductive Load and
Transient Suppression Device
Figure 13—Programming Jumper Plugs and Switches

place it on the NC and center pins. The pin groups
are identified as follows:
J2 – High Alarm
J3 – Auxiliary Alarm
J4 – Low Alarm
J5 – Fault
The controller is programmed at the factory for nor-
mally open relay contacts.
Latching/Non-Latching Relays
The Low and Auxiliary alarm relays are programmable
for latching or non-latching operation. The High alarm
relay is always latching. Latching relay operation is
programmed using rocker switch 1 at SW1 (SW1-1).
For latching operation, place the switch in the closed
position. For non-latching operation, place it in the
open position. This switch is set at the factory for
non-latching relay operation.
Normally Energized/De-Energized Relays
The three alarm relays are also programmable for nor-
mally energized (fail-safe) or normally de-energized
operation. This is accomplished by setting rocker
switch 2 at SW1 (SW1-2). For normally energized
alarm relays, place the switch in the closed position.
For normally de-energized operation, place it in the
open position. This switch is set at the factory for nor-
mally de-energized operation.
The Fault relay is always normally energized, regard-
less of the setting of SW1-2.
4 to 20 ma Output
Isolated or non-isolated operation of the 4 to 20 ma
output can be selected using a jumper plug at J1.
For non-isolated operation, as illustrated in Figure 10,
place the jumper plug in the INT (internal power
source) position. Place the plug in the EXT position
for an isolated circuit, as illustrated in Figure 11. The
jumper is set at the factory for non-isolated operation.
INSTALLATION CHECKLIST
The following checklist is provided as a means of
double checking the system to be sure that all phases
of system installation are complete and have been
performed correctly.
1. Sensors are pointing down and junction boxes
are securely mounted.
2. Optional sensor accessories (dust/splash guards,
sample draw devices, etc.) are installed, clean,
and in good condition.
3. If a sensor separation kit is used, interconnecting
wiring is correct and shorting plug is installed.
4. All cable shields are properly grounded.
5. Conduit seals have been installed at all junction
box entries (if conduit is being used).
6. All transmitter modules are properly installed in
their junction boxes.
7. All junction box covers are tightly installed.
8. Transmitter to controller wiring is correct.
9. Power wiring to the controller is installed and
power source is operational.
10. External loads are properly connected to the con-
troller.
11. Controller is programmed as desired. Record this
information for future reference.
12. Controllers are properly installed in the mounting
enclosure.
13. Proper ventilation is provided to prevent over-
heating of the controller.
Proceed to System Startup, Setpoint Adjustment and
Calibration.
Section III
System Startup
STARTUP PROCEDURE
1. Output loads that are normally actuated by the
gas detection system should be secured (remove
power from all output devices) to prevent unde-
sired activation.
2. Check all external wiring for proper connection.
Be sure that the sensor has been connected
properly and that the transmitter module has been
installed properly.
3. Before installing the controller in the mounting
rack, inspect it to verify that it has not been physi-
cally damaged in shipment. Check the jumper
plugs and rocker switches on the controller for
proper programming, then slide the controller fully
into the mounting enclosure.
4. Apply power to the system.
16

NOTE
When power is applied to the controller, it enters
a time delay mode to allow the sensor output to
stabilize before beginning normal operation.
During this time the outputs are inhibited, the
FAULT LED is illuminated, and the current output
indicates a fault condition. This time delay can
last up to five minutes, but will end earlier if the
sensor output no longer exceeds any alarm set-
points.
5. If a sensor separation kit and K Series
Transmitters are being used, adjust the sensor
voltage to 3.3 vdc, following the procedure
described in the “Sensor Separation” section.
6. If desired, controller operation can be tested by
manipulating the transmitter output to a level that
exceeds the alarm thresholds. With K Series
Transmitters, this is done by adjusting the Zero
potentiometer. [The transmitter Span adjustment
may have to be increased (clockwise) to obtain a
full scale reading on the controller.] The output of
Model 400/405 Transmitters can be adjusted over
the entire operating range of the transmitter using
the optical calibration meter. Refer to the trans-
mitter manual for details. Note that this test will
actuate the controller outputs.
7. Put the controller in the Setpoint Display mode to
determine the present alarm setpoints and cali-
bration gas concentration. If changes are
required, perform the Setpoint Adjustment proce-
dure.
8. Perform the calibration procedure.
9. Check the 4 to 20 ma current loop for proper cali-
bration and adjust as required.
10. Remove mechanical blocking devices (if used)
and restore power to the output loads.
SETPOINT ADJUSTMENT
The adjustment range for the alarm setpoints and cali-
bration gas concentration is as follows:
Low alarm 5 to 40% LFL
High alarm 10 to 60% LFL
Auxiliary alarm 5 to 99% LFL
Calibration gas 30 to 99% LFL
The factory settings are:
Low alarm 20% LFL
High alarm 50% LFL
Auxiliary alarm 50% LFL
Calibration gas 50% LFL
To check the present levels, use the “Setpoint Display
Mode” described below. To change the values, use
the “Setpoint Adjustment Procedure”.
SETPOINT DISPLAY MODE
1. To enter the Setpoint Display mode, press and
hold the Reset button until the Low LED begins to
blink (approximately one second). Release the
Reset button. The low alarm setpoint will be
shown for two seconds on the digital display.
NOTE
The Reset button should be released as soon as
the controller has entered the Setpoint Display
mode (after one second). If the button is still
depressed at the end of the Setpoint Display
mode (9 seconds), the controller will automatical-
ly enter the Calibrate mode. If the operator is not
prepared to perform a calibration, a calibration
fault will occur. Recycle power to the controller
to exit the calibrate mode without affecting the
calibration settings.
2. At the end of the two second interval, the Low
LED goes out, the High LED begins to blink, and
the digital display shows the high alarm setpoint.
3. Two seconds later the High LED goes out and the
Auxiliary LED blinks. The digital display now
shows the programmed auxiliary alarm setpoint.
4. Two seconds later the Auxiliary LED goes out and
the CAL LED blinks. The digital display now
shows the programmed calibration gas concen-
tration.
5. After displaying the calibration gas concentration
for two seconds, the controller automatically
leaves the Setpoint Display mode and returns to
the Normal operating mode.
6. If adjustments to the setpoints are required, per-
form the Setpoint Adjustment procedure. When
the setpoint levels are acceptable, record this
information for future reference and perform the
Calibration procedure.
SETPOINT ADJUSTMENT PROCEDURE
1. Determine the required alarm setpoint levels and
calibration gas concentration. If the system will
be used to detect a gas other than the type being
used for calibration, a conversion (“K”) factor
must be used to determine the correct value to
be programmed into the microprocessor in step 5
below. Refer to the “Calibration “ section.
17 95-8398

2. Press and hold the Set button for one second.
The digital display indicates the present low alarm
setpoint and the Low LED blinks. Press the Reset
button to increase the reading or the Set button to
decrease the reading. (Holding the button will
cause the reading to change rapidly.)
3. When no changes to the setpoint level have been
made for 5 seconds, the Low LED goes out, the
High LED blinks, and the digital display shows the
high alarm setpoint. Press the appropriate button
(detailed in step 2 above) to obtain the desired
reading on the digital display.
4. When no changes to the setpoint level have been
made for 5 seconds, the High LED goes out, the
Auxiliary LED blinks, and the digital display shows
the auxiliary alarm setpoint. Press the appropri-
ate button to obtain the desired reading on the
digital display.
5. When no changes have been made for 5 sec-
onds, the Auxiliary LED goes out, the CAL LED
blinks, and the digital display indicates the cali-
bration gas concentration. Press the appropriate
button to change the calibration gas concentra-
tion as required.
6. When no changes have been made for 5 sec-
onds, the controller automatically returns to the
Normal operating mode.
7. Record the new values for future reference.
NOTE
The alarm setpoints, calibration gas concentra-
tion, and calibration data are stored in non-
volatile memory and are retained in the event of
a power loss. However, if power is interrupted
while performing the Setpoint Adjustment or
Calibration procedure, the entire procedure must
be repeated when power is restored.
CALIBRATION
Various factors affect the time interval between peri-
odic recalibrations. Exposure of the sensing element
to contaminants in the air, exposure to a high concen-
tration of combustible gas, or an extended period of
normal operation can cause changes in sensitivity.
Since each application is different, the length of time
between regularly scheduled recalibrations can vary
from one installation to the next. In general, the more
frequently a system is checked, the greater the relia-
bility. The sensor must be calibrated:
— Before a new system is initially put into service
— If the sensor is replaced
— If the transmitter is replaced
— If the controller is replaced
— If the sensor is exposed to a high level of com-
bustible gas.
CAUTION
Exposure to a high level of gas can have an
adverse effect on the sensitivity of the sensing
element. If the level of gas at the sensor should
reach 100% LFL, it is important that it be tested
and recalibrated if required. In some cases, it
may be necessary to replace the sensor.
If an over-range condition should occur, the digi-
tal display flashes and the highest reading latch-
es on until reset. The user must exercise caution
if an over-range reading is indicated, since a
highly explosive condition could exist. The haz-
ardous area should be checked with a portable
detection instrument to determine the actual level
of combustible gas present.
For best calibration results, allow a new sensor to
operate for several hours to ensure a stable output
before performing calibration. For the highest degree
of accuracy, perform a second calibration after 24
hours.
When a sensor is exposed to a different or new envi-
ronment, calibration should be checked frequently to
determine the proper interval between periodic cali-
brations.
NOTE
Loss of sensitivity can be caused by various fac-
tors. One common cause is by clogging of the
sensor filter by water, dirt, oil, paint, etc.
Problems of this nature are capable of totally
incapacitating the sensor, but it is only during
calibration that the problem will be discovered.
To assure the greatest level of reliability, calibra-
tion should be performed at regularly scheduled
intervals.
Before performing calibration, the operator should
examine the sintered metal filter of the sensor (flame
arrestor) to be sure that it is not missing or damaged.
If the filter is defective or missing, the sensor must not
be operated, since the exposed sensing element can
act as an ignition source. It should also be noted that
a dirty cover can significantly reduce the sensitivity of
the sensor.
CONVERSION (K) FACTOR
The output of the sensor to different types of gases
can vary considerably. To assure calibration accura-
cy, it is recommended that calibration be performed
18
Table of contents
Other Det-Tronics Controllers manuals
Popular Controllers manuals by other brands
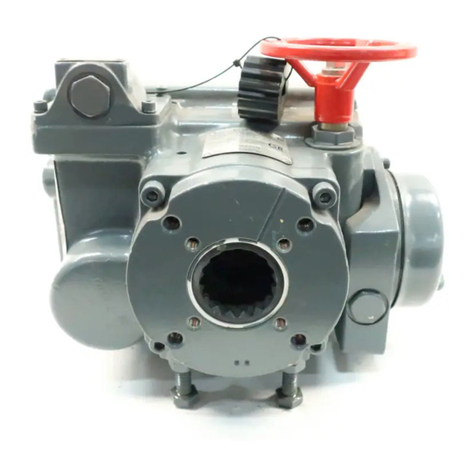
Emerson
Emerson El-O-Matic ELQ Series Installation, operation & maintenance manual
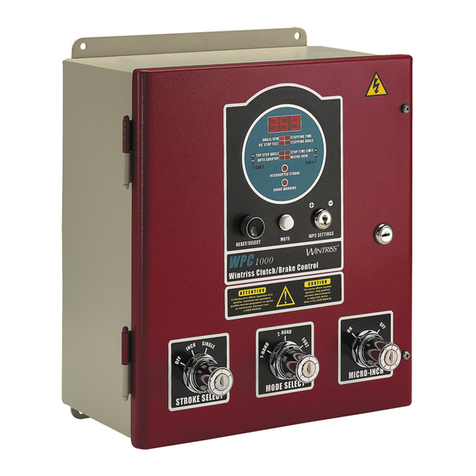
Wintriss
Wintriss WPC 1000 user manual
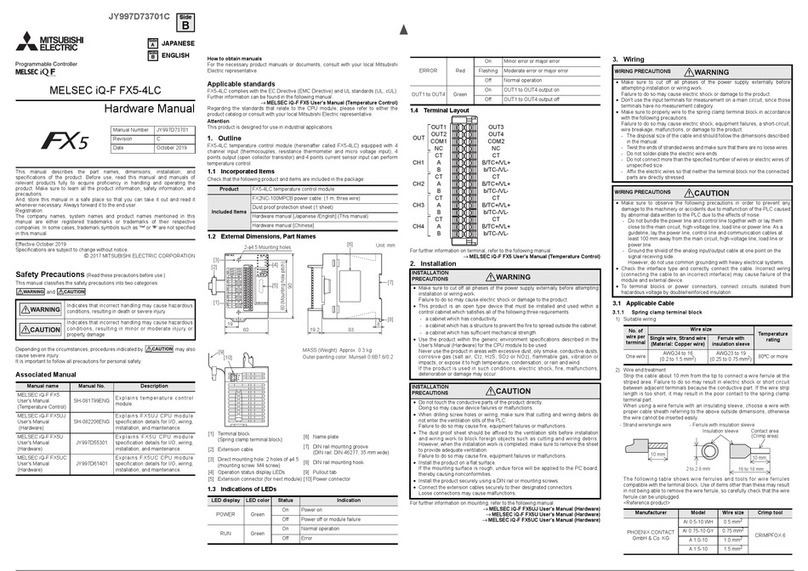
Mitsubishi Electric
Mitsubishi Electric FX5 MELSEC iQ-F FX5-4LC Hardware manual
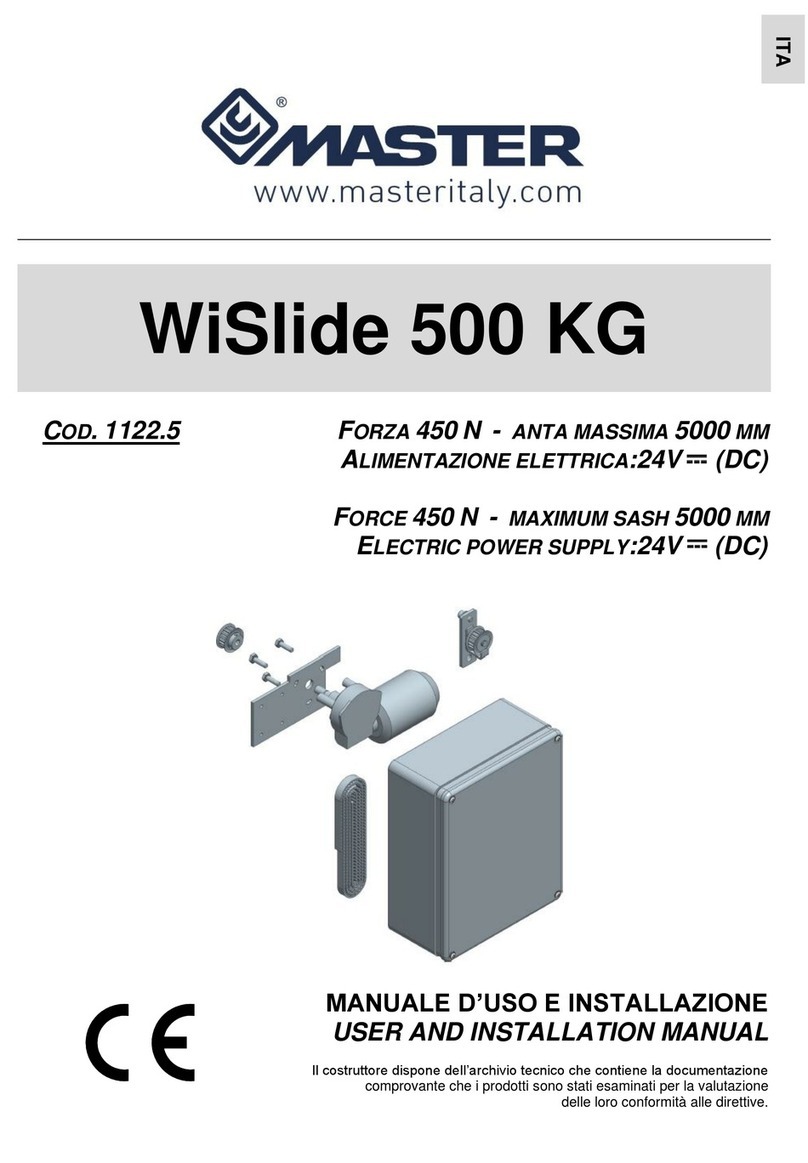
Master
Master WiSlide 500 KG User and installation manual
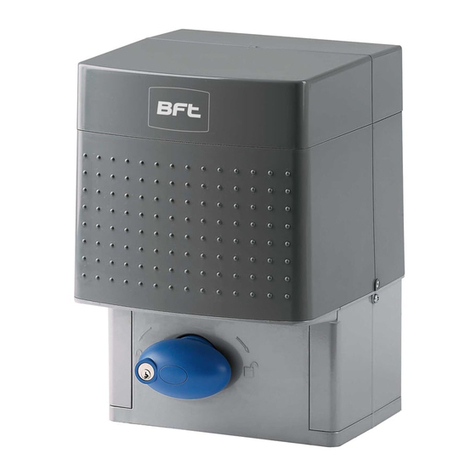
BFT
BFT ICARO Installation and user manual
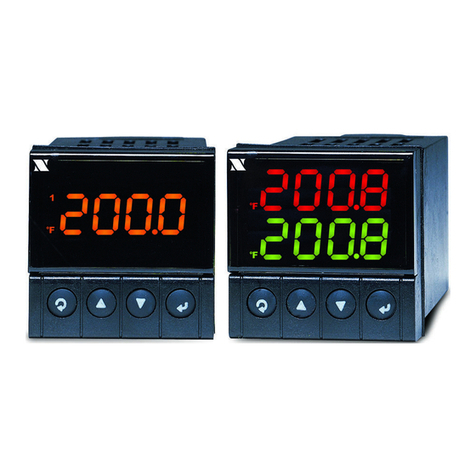
Omega
Omega CNI16 quick start guide
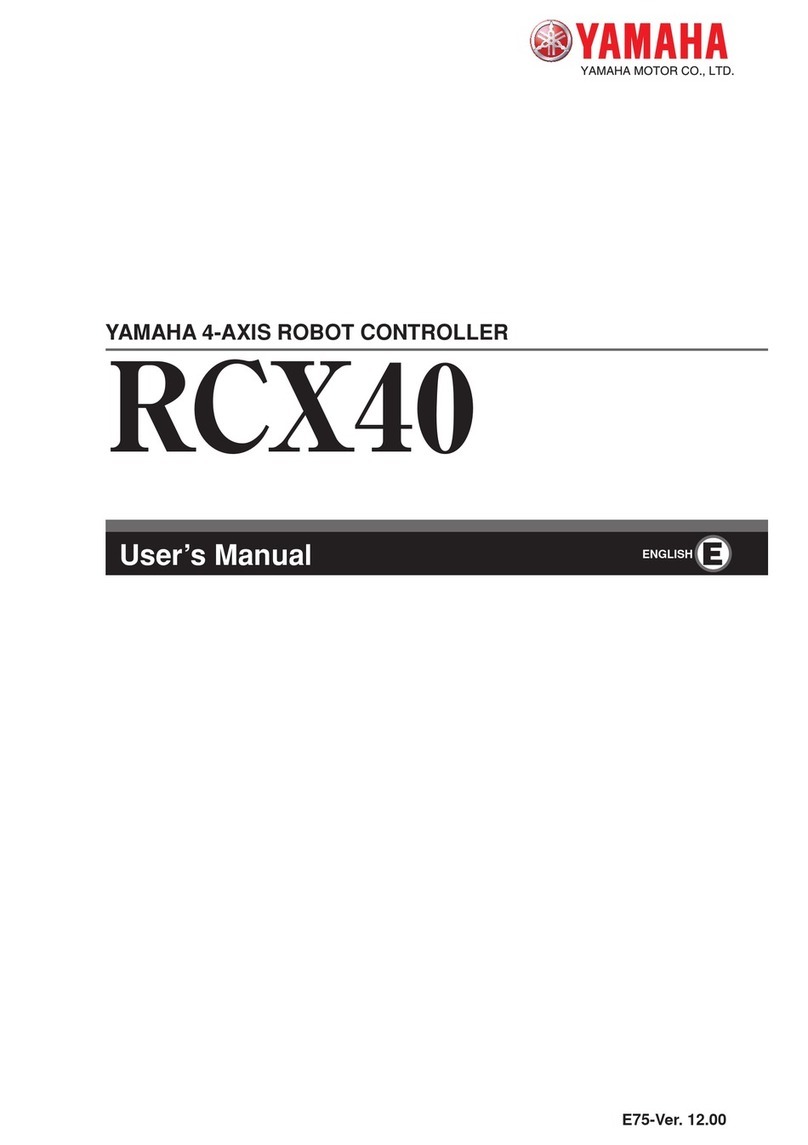
Yamaha
Yamaha RCX40 user manual
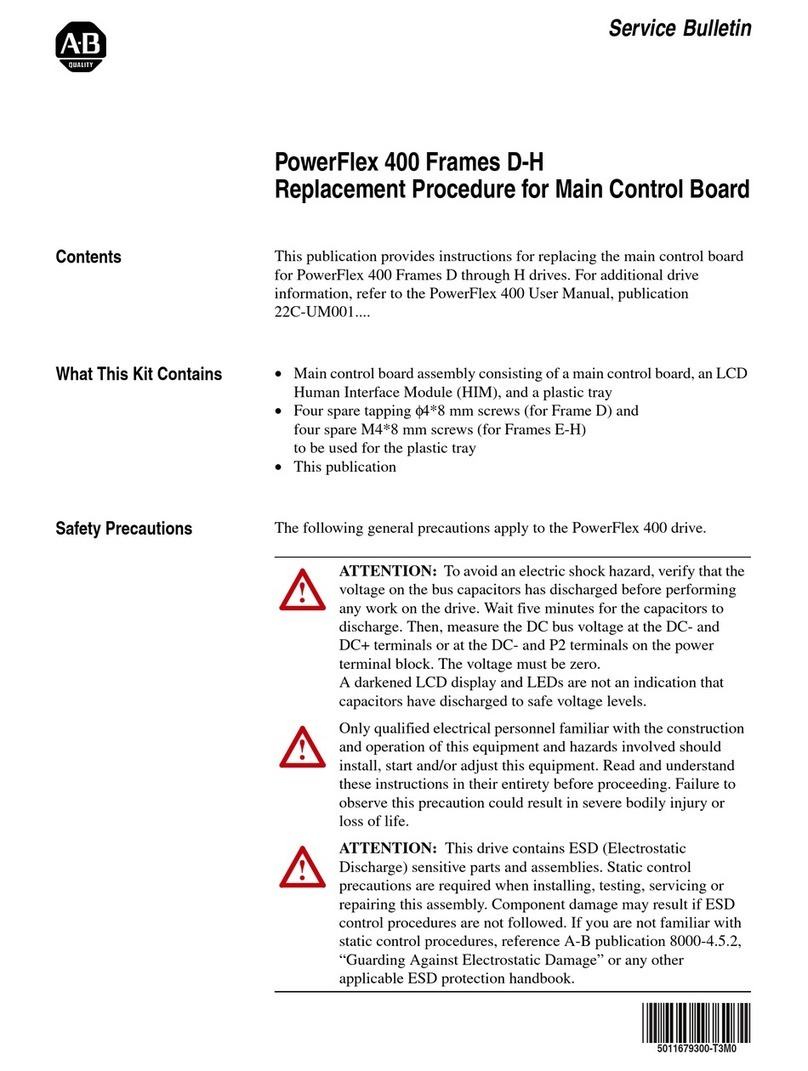
AB Quality
AB Quality PowerFlex 400 Frames D-H Service bulletin
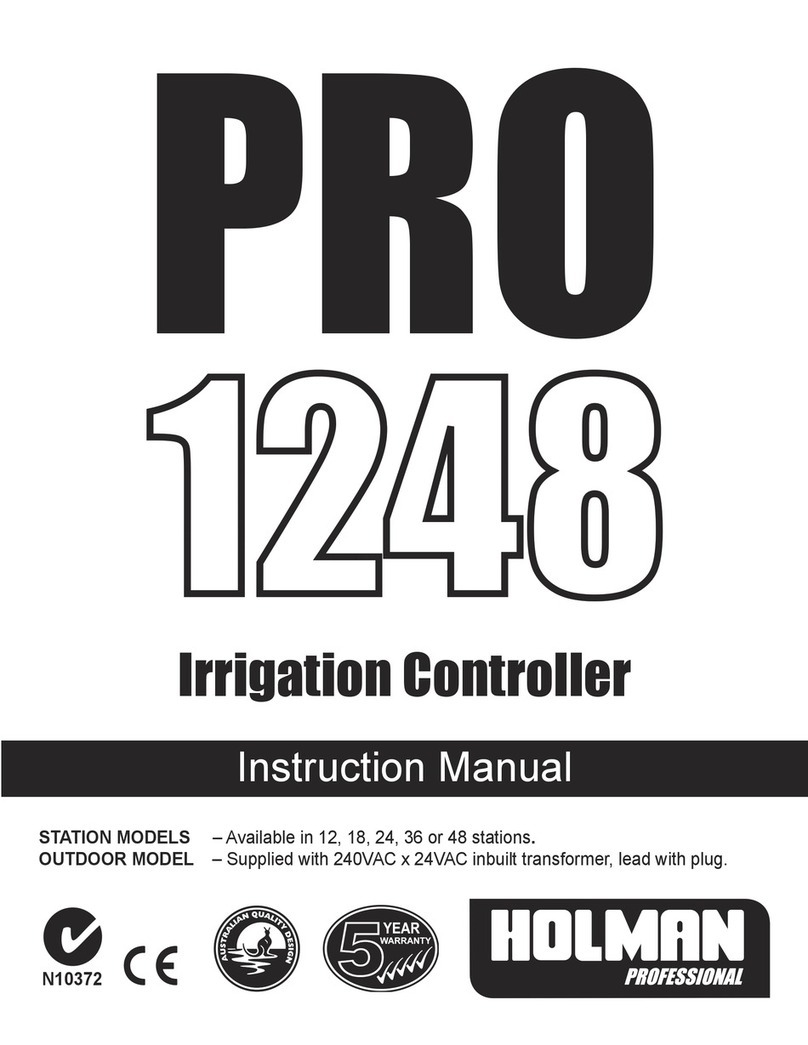
Holman
Holman pro 1248 instruction manual
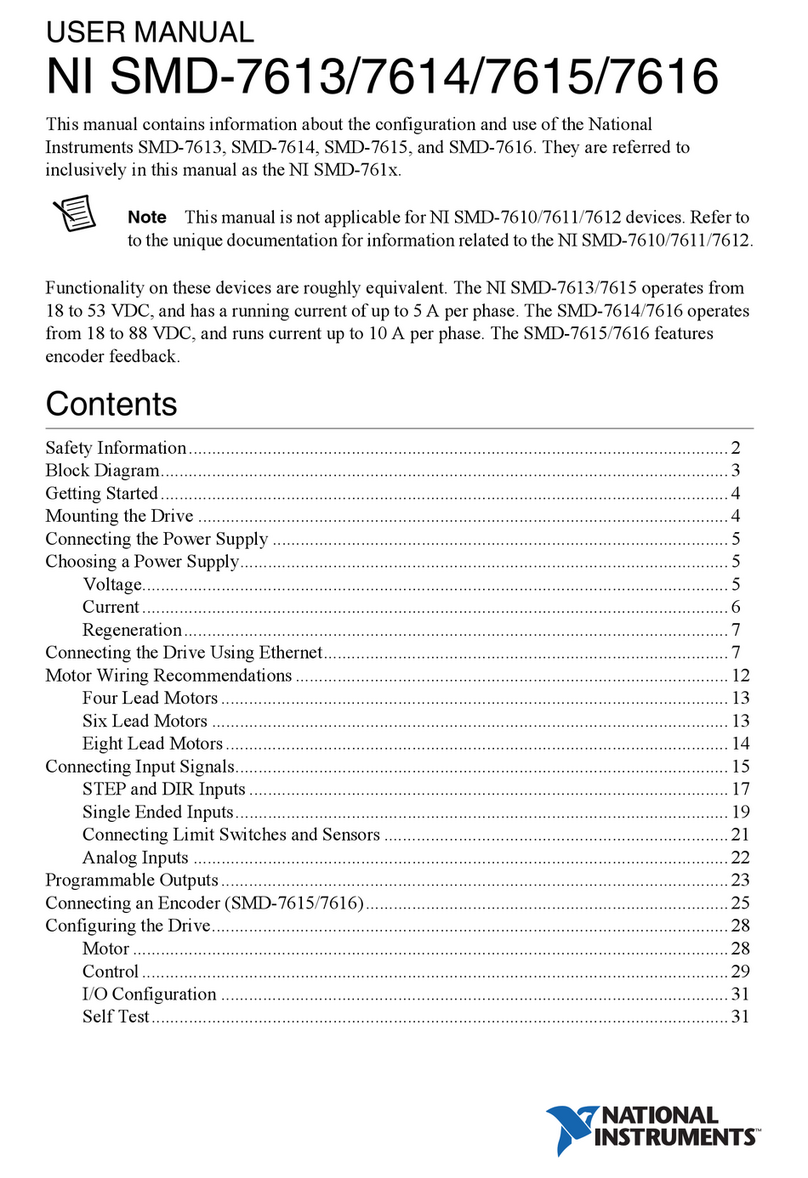
National Instruments
National Instruments NI SMD-7613 user manual
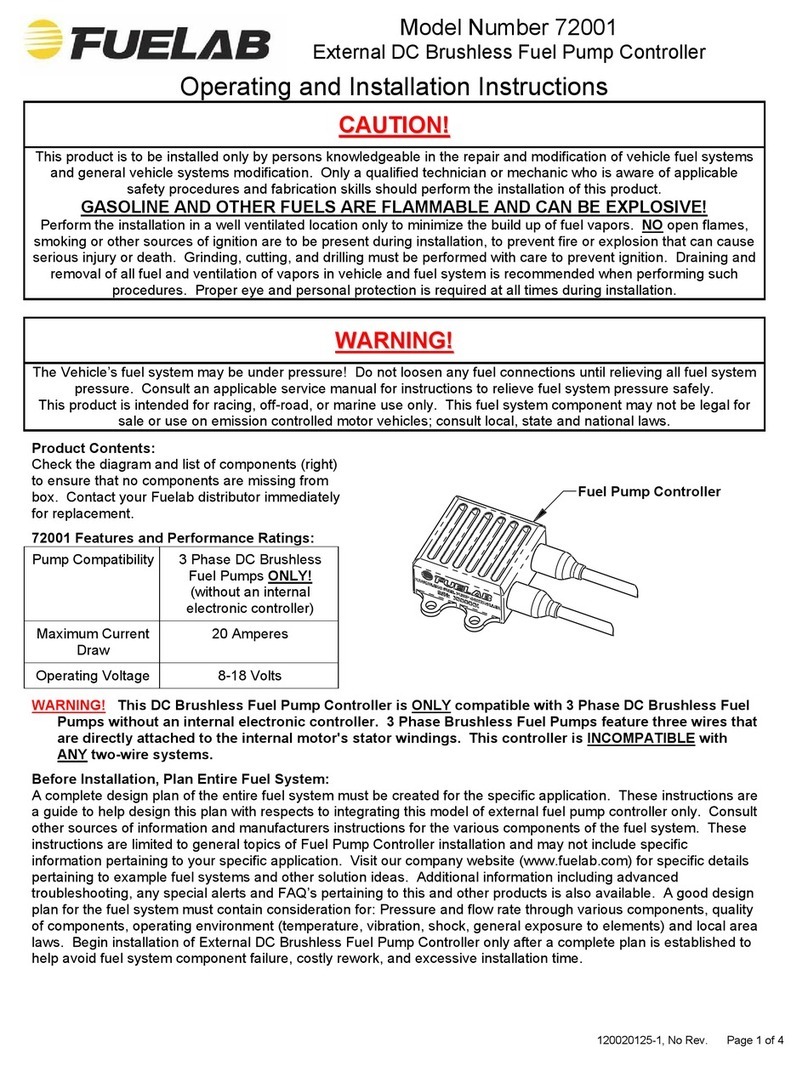
Fuelab
Fuelab 72001 Operating and installation instructions
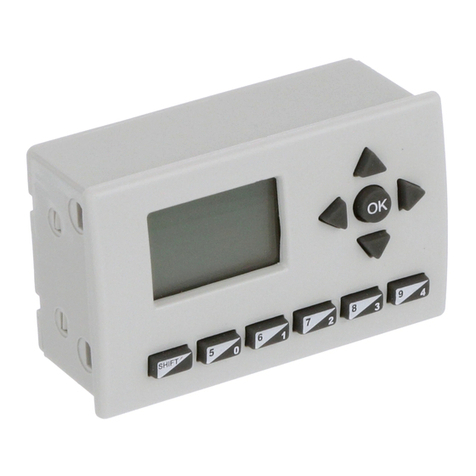
Phoenix Contact
Phoenix Contact Nanoline Series user manual