Detcon 1000 User manual

Detcon Model 1000
H2S Process Analyzer - Electrochemical Sensor
INLET
SAMPLE
10 PSIG (CONSTANT)
SAMPLE PRESSURE
INLET
AIR AIR
INLET
SAMPLE OUTLET
SAMPLE
SAMPLE
FLOW AIR
FLOW
MODEL NO.
SERIAL NO.
INPUT VOLTAGE
FREQUENCY
CURRENT LOAD
AREA CLASSIFICATION
detcon inc.
3200 A-1 Research ForestDr.
The Woodlands, TX 77381
www.detcon.com
PART NO.
Operator’s Installation and Instruction Manual
Detcon Model 1000 Series H2S Analyzer consists of two major assemblies:
1. The Model 1000 Series gas sample-conditioning assembly.
2. The Model DM-624 H2S gas sensor (using Alcohol Free - Electrochemical Sensor or
Hi-Range Electrochemical Sensor)
DETCON, Inc.
4055 Technology Forest Blvd.,
The Woodlands, Texas 77381
Ph.281.367.4100 / Fax 281.298.2868
www.detcon.com
May 3, 2018• Document #2945• Revision 2.9

Model 1000 H2S Echem
Model 1000 H2S Echem Instruction Manual ii
This page left intentionally blank

Model 1000 H2S Echem
Model 1000 H2S Echem Instruction Manual iii
Table of Contents
1. Introduction.............................................................................................................................................. 1
1.1 DM-624 Sensor .................................................................................................................................... 1
1.2 Electrochemical Sensor........................................................................................................................ 2
1.3 Microprocessor Control Circuit............................................................................................................ 2
1.4 Base Connector Board.......................................................................................................................... 3
1.5 Interference Data.................................................................................................................................. 4
1.6 Enclosures ............................................................................................................................................ 4
2. Specifications............................................................................................................................................ 5
3. Installation................................................................................................................................................ 6
3.1 Mounting.............................................................................................................................................. 6
3.2 Gas Connections and Sampling System Notes..................................................................................... 6
3.3 Electrical Connections.......................................................................................................................... 9
3.4 Relays and RS-485 Setup................................................................................................................... 10
4. Start Up................................................................................................................................................... 12
5. Operating Software ............................................................................................................................... 13
5.1 Programming Magnet Operating Instructions.................................................................................... 13
5.2 Operating Software............................................................................................................................. 13
5.2.1 Normal Operation ...................................................................................................................... 13
5.2.2 Calibration Mode....................................................................................................................... 14
5.2.3 Program Mode ........................................................................................................................... 14
5.2.4 Software Flow Chart .................................................................................................................. 16
6. Calibration and Maintenance............................................................................................................... 16
6.1.1 Zero Calibration......................................................................................................................... 17
6.1.2 Span Calibration ........................................................................................................................ 17
7. Programming Alarms............................................................................................................................ 19
7.1 Alarm Reset........................................................................................................................................ 19
7.2 Other Alarm Functions....................................................................................................................... 19
8. Programming Features.......................................................................................................................... 19
9. RS-485 Protocol ..................................................................................................................................... 20
10. Display Contrast Adjustment ............................................................................................................... 22
11. Low Flow Fault Options........................................................................................................................ 22
12. Sensor Replacement............................................................................................................................... 23
13. Troubleshooting..................................................................................................................................... 23
14. Spare Parts ............................................................................................................................................. 24
15. Warranty................................................................................................................................................ 26
16. Flow Diagrams ....................................................................................................................................... 27
17. Wiring Diagram..................................................................................................................................... 29
Appendix C....................................................................................................................................................... 30
Revision Log.................................................................................................................................................. 30

Model 1000 H2S Echem
Model 1000 H2S Echem Instruction Manual iv
Table of Figures
Figure 1 DM-624 Sensor...................................................................................................................................... 1
Figure 2 Construction of Electrochemical Sensor................................................................................................ 2
Figure 3 Functional Block Diagram..................................................................................................................... 3
Figure 4 DM-624 Control Circuit......................................................................................................................... 3
Figure 5 Connector Board Terminals................................................................................................................... 3
Figure 6 Enclosures.............................................................................................................................................. 4
Figure 7 Unit Dimensions .................................................................................................................................... 6
Figure 8 Port Identification .................................................................................................................................. 7
Figure 9 Optional Bubbler Bottle......................................................................................................................... 8
Figure 10 Installation Wiring Connections .......................................................................................................... 9
Figure 11 Alarm Jumpers................................................................................................................................... 10
Figure 12 RS-485 Dip Switches......................................................................................................................... 11
Figure 13 Programming Magnet ........................................................................................................................ 13
Figure 14 DM-624 Software Flow Chart ........................................................................................................... 16
Figure 15 Analyzer Parts Identification ............................................................................................................. 24
Figure 16 DM-624 Replacement Parts............................................................................................................... 25
Figure 17 Unit Flow Diagram ............................................................................................................................ 27
Figure 18 Pump Box Flow Diagram .................................................................................................................. 28
Figure 19 Wiring Diagram................................................................................................................................. 29
List of Tables
Table 1 Hexadecimal Conversion ...................................................................................................................... 11
Table 2 Sample Flow Rate ................................................................................................................................. 12
Table 3 Sample Flow Rate ................................................................................................................................. 17
Shipping Address: 4055 Technology Forest Blvd., The Woodlands Texas 77381
Mailing Address: P.O. Box 8067, The Woodlands Texas 77387-8067
Phone: 888.367.4286, 281.367.4100 • Fax: 281.292.2860 • www.detcon.com • sales@detcon.com

Model 1000 H2S Echem
Model 1000 H2S Echem Instruction Manual Rev. 2.9 Page 1 of 30
1. Introduction
The Detcon Model 1000 Series H2S Process Analyzer is a 110/220VAC or 24VDC powered analyzer that
provides a select gas sample mixture to an on-board DM-624 H2S gas sensor assembly. The range of gas
analysis can span from 0-10ppm up to 0-5% (see Table 2 Sample Flow Rate). The range of analysis is
determined at time of order.
When located outdoors, the H2S Process Analyzer package should be appropriately covered from direct
weather exposure. The Model 1000 Series H2S Process Analyzer can optionally be ordered with a full NEMA
4 enclosure.
The “Power Supply” enclosure on the upper right side of the unit houses a 24VDC power supply, a 24V DC-
DC Converter, and a terminal PCB labeled for all input and output field wiring. The “Pump/Flow” enclosure
located on the upper left houses an air dilution pump, an activated carbon scrubber, and optional air flow fault
and sample flow fault alarm PCB’s.
The analyzer requires a constant, liquid-free, 10±2psig sample pressure, which is provided by the customer or
may be supplied by Detcon as a separate gas sample handling system.
The on-board gas sample conditioning system includes a stainless steel pressure gauge (0-30psig), and a Genie
membrane filter to provide the analyzer with absolute condensate liquid protection. On the bypass port of the
Genie membrane filter, a 15 psig over-pressure relief valve and flow control valve are also provided. The flow
control valve can be used as a continuous sample bypass and liquid exhaust vent. A dedicated air and sample
mixture is maintained via 2 control valves and 2 rotameters. The Sample is then delivered to the Model DM-
624 H2S gas sensor for analysis. An optional on-board span gas cylinder is provided for span calibration, and
a selectable 3-way valve is provided for manually switching between sample monitoring and span calibrations.
An optional Acetic Acid Bubbler apparatus is available to scrub the gas sample when it contains high
concentrations of VOC’s as found in some injection spray H2S scavenger chemistries. An optional live heat
tracing feature may be used to prevent condensation after the Genie Membrane Filter.
®
1.1 DM-624 Sensor
Figure 1 DM-624 Sensor

Model 1000 H2S Echem
Model 1000 H2S Echem Instruction Manual Rev. 2.9 Page 2 of 30
Detcon MicroSafe™ Model DM-624, toxic sensors are non-intrusive “Smart” sensors designed to detect and
monitor for H2S gas in the ppm range. A primary feature of the sensor is its method of automatic calibration,
which guides the user through each step via instructions displayed on the backlit LCD. The sensor features
field adjustable, fully programmable alarms and provides relays for two alarms plus fault as standard. The
sensor comes with two different outputs: analog 4-20mA, and serial RS-485. These outputs allow for greater
flexibility in system integration and installation. The microprocessor-supervised electronics are packaged as a
plug-in module that mates to a standard connector board. Both are housed in a condulet that includes a glass
lens window that allows for the display of sensor readings as well as access to the sensor’s menu driven
features via a hand-held programming magnet.
1.2 Electrochemical Sensor
The sensor is an electrochemical cell. Each cell consists of three electrodes embedded in an electrolyte
solution all housed beneath a diffusion membrane. Sensitivity to specific target gases is achieved by varying
composition of any combination of the sensor components. Good specificity is achieved in each sensor type.
The cell is diffusion limited via small capillary barriers resulting in long service life of up to 3 or more years
depending on the application.
NOTE: This particular sensor cell is unique in that it has no cross-sensitivity to alcohol vapors
and thus is a good choice for measuring H2S in natural gas pipelines.
Figure 2 Construction of Electrochemical Sensor
DM-624 Electrochemical Sensor Principle of Operation
Method of detection is by an electrochemical reaction at the surface of an electrode called the sensing
electrode. Air and gas diffuse through the stainless steel filter and the capillary diffusion barrier. The
controlling circuit maintains a small external operating voltage between the sensing and counter electrodes of
the proper bias and magnitude so that no current flows to or from the reference electrode while its potential is
maintained at the correct fixed voltage — usually ground. The electrochemical reaction creates a change in
current flow from the counter electrode to the sensing electrode. This change in current is proportional to the
gas concentration and is reversible. The quick response of the sensor results in continuous monitoring of
sample gas conditions.
1.3 Microprocessor Control Circuit
The control circuit is microprocessor based, and is packaged as a plug-in field replaceable module, facilitating
easy replacement and minimum down time. Circuit functions include a basic sensor pre-amplifier, on-board
power supplies, microprocessor, back lit alpha numeric display, alarm status LED indicators, magnetic
programming switches, an RS-485 communication port, and a linear 4-20mA DC output.

Model 1000 H2S Echem
Model 1000 H2S Echem Instruction Manual Rev. 2.9 Page 3 of 30
Figure 3 Functional Block Diagram
Figure 4 DM-624 Control Circuit
1.4 Base Connector Board
The base connector board is mounted in the enclosure and includes: the mating connector for the control
circuit, reverse input and secondary transient suppression, input filter, alarm relays, lugless terminals for all
field wiring, and a terminal strip for storing unused programming jumper tabs. The alarm relays are contact
rated 5 amps @ 250VAC, 5 amps @ 30VDC and coil rated at 24VDC. Gold plated program jumpers are used
to select either the normally open or normally closed relay contacts.
Figure 5 Connector Board Terminals

Model 1000 H2S Echem
Model 1000 H2S Echem Instruction Manual Rev. 2.9 Page 4 of 30
1.5 Interference Data
DM-624 series electrochemical H2S sensors are subject to interference from other gases. This interaction is
shown in the following table as the relation between the amount of the interfering gas applied to the sensor,
and the corresponding reading that will occur (in ppm).
Gas Interference
Carbon monoxide 300ppm ≤1.5ppm
Chlorine 1ppm = -0.2ppm
Ethyl mercaptan 3ppm = 1ppm
Ethylene 100ppm = 0
Hydrogen 1% = < 5ppm
Hydrogen chloride 5ppm = 0
Hydrogen cyanide 10ppm = 0
Nitric oxide 35ppm < 2ppm
Nitrogen dioxide 5ppm = -0.5ppm
Sulfur dioxide 5ppm < 1ppm
Methyl mercaptan 2ppm = 1ppm
1.6 Enclosures
The sensor is packaged in a cast metal enclosure. The enclosure is fitted with a threaded cover that has a glass
lens window. Magnetic program switches located behind the transmitter module faceplate are activated
through the lens window via a hand-held magnetic programming tool allowing non-intrusive operator interface
with the sensor. All calibration and alarm level adjustments can be accomplished without removing the cover.
++
24VDC
OUT
2.1A
18-36
VDC
IN
Flow Fault (optional)
Pump/Scrubber Power Supply/
Terminal PCB Sensor (side view) Sensor
Right
Left
Figure 6 Enclosures
A 24VDC power supply and termination PCB for the power, relay contacts, 4-20mA output, and/or RS485
signal are located in the upper right enclosure. The pump and optional low flow fault assemblies are located in
the upper left enclosure.

Model 1000 H2S Echem
Model 1000 H2S Echem Instruction Manual Rev. 2.9 Page 5 of 30
2. Specifications
Sensor Type
Electrochemical cell
Measurement Range
0-10ppm H2S, up to 0-5 % H2S
Accuracy/Repeatability
±10% of reading or ±0.5ppm, whichever is greater
Response/Clearing Time
T80 < 1 minute
Operating Temperature
-40°F to +122°F: -40°C to +50°C
Outputs
Linear 4-20mA DC; RS-485 Modbus™; 3 relays (alarm 1, alarm 2, and fault), Contacts rated 5 amps
Input Voltage
110~220VAC; 18~36VDC
Power Consumption
700mA (16.8 watts)
Electrical Classification
Non Hazardous Area
Sensor Life/Warranty
Sensor: 6 month conditional warranty; Transmitter: 2 year warranty
Analyzer Weight
70 lbs.
Dimensions
29” X 29” X 8”

Model 1000 H2S Echem
Model 1000 H2S Echem Instruction Manual Rev. 2.9 Page 6 of 30
3. Installation
3.1 Mounting
Securely mount the Model 1000 analyzer panel or NEMA 4 enclosure (optional) in accordance with Figure 7.
Figure 7 Unit Dimensions
3.2 Gas Connections and Sampling System Notes
1. Install a length of tubing from the desired sample point to the sample input port (as shown in Figure 8).
Sample draw tubing should be 316 stainless steel of ¼" O.D.
NOTE: A constant pressure of 10±2psig should be provided to the analyzer for proper operation. In
applications where line pressure varies significantly, two-stage pressure regulation is recommended to
hold the constant pressure. Ideally, the pressure drop from the source to 10psig for analyzer should be
taken as close to the pipeline as possible. This speeds up response time to actual gas concentration
changes. An insertion probe membrane device is advisable to use for pipeline sources with high levels of
condensates, mist, and contamination.

Model 1000 H2S Echem
Model 1000 H2S Echem Instruction Manual Rev. 2.9 Page 7 of 30
AIR
FLOW
INLET
SAMPLE
SAMPLE
FLOW
10 PSIG (CONSTANT)
SAMPLE PRESSURE
INLET
AIR AIR
MODEL NO.
SERIAL NO.
INPUTVOLTAGE
FREQUENCY
CURRENT LOAD
AREACL ASSIFICATION
detconinc.
3200A-1 Resear ch Forest Dr.
TheWoodlands, TX 77381
www.detcon.com
PARTNO.
Sample Inlet Port
Pressure Gauge
Sample Bypass and Liquid
Rejection Exhaust Vent.
NOTE:
These may be
combined into a
single vent
Sample Calibrate
H
2
S Vent
Cal Gas
Figure 8 Port Identification
2. Whenever possible, the Sample Bypass flow control valve of the Genie membrane filter should be used to
minimize the sample lag time between the sample tap and the analyzer location. It can also be used as a
means to exhaust condensed liquids in the sample line away from the Genie filter and prevent a “loss of
flow” condition. Set a flow of 100-200cc/min. and vent to a safe area using ¼” O.D. tubing.
3. Connect to the Over-pressure Relief valve and vent to a safe area. The pressure relief valve is set at
Detcon to open at 15-20psig. For convenience sake, the sample bypass and over-pressure relief can be
vented together.
4. Install a length of ¼" OD stainless steel tubing from the vent port to an area deemed safe for venting as
shown below. Venting pressure should be in the range of 0±1psig and ambient pressure is highly
preferred.
5. When the optional Acetic Acid Bubbler apparatus is used, prior to applying power and applying gas flow
the bubbler should be filled to the maximum fill level with a 5% acetic acid solution. (Standard white
vinegar is also acceptable).

Model 1000 H2S Echem
Model 1000 H2S Echem Instruction Manual Rev. 2.9 Page 8 of 30
AIR
FLOW
SAMPLE
FLOW
Sample Calibrate
Sample Bypass and Liquid
Rejection Exhaust Vent.
NOTE:
These can be
combined into a
single Vent.
Over Pressure Relief Vent
Pressure Guage
Air Inlet Port
Sample Inlet Port
H
2
S Vent
Port
Optional
Acetic
Acid
Bubbler
Bottle
Figure 9 Optional Bubbler Bottle

Model 1000 H2S Echem
Model 1000 H2S Echem Instruction Manual Rev. 2.9 Page 9 of 30
3.3 Electrical Connections
AIR
FLOW
SAMPLE
FLOW
+ +
24VDC
OUT
2.1A
18-36
VDC
IN
++
24VDC
OUT
2.1A
18-36
VDC
IN
++
24VDC
OUT
2.1A
18-36
VDC
IN
4-20mA, RS485,
Alarm/Fault Sensor Relays
Low Flow Air/ Sample Relays
(Optional)
117VAC / 24VDC In
Customer Connections
+24VDC
-24VDC
(Ground)
INPUT
+
-
Figure 10 Installation Wiring Connections
1. For AC powered unit connect 117/220VAC to the terminal connector labeled “VAC IN” (JP8A) inside the
enclosure on the upper right. If applicable, connect 24VDC to the Terminal Connector Board labeled
“VDC IN” (JP7A) (See Figure 10.)
2. The 4-20mA and/or RS-485 signal outputs should be wired from the terminal PCB and then out the right
side of the “Power Supply” enclosure (Figure 10).
3. Discrete alarm relay contacts are provided for three alarms: Fault, Low and High. The contacts consist of
common and choice of normally open or normally closed. Contact output selections are jumper
programmable on the sensor connector board. See DM-624 wiring diagram for details. These connections
also should be wired out of the right side of the “Power Supply” enclosure. (Figure 10).
4. Optional Low Flow Fault alarms for Sample gas and Air are available. They provide a form “C” relay
contact (common, normally open and normally closed) rated 1 amp at 30VDC/0.24 amp at 125VAC.
Relay contacts are pre-wired to the I/O connector PCB located in the “Power Supply” enclosure and are
labeled “FLO FLT1” and “FLO FLT2” respectively (Figure 10).

Model 1000 H2S Echem
Model 1000 H2S Echem Instruction Manual Rev. 2.9 Page 10 of 30
3.4 Relays and RS-485 Setup
Program the alarms via the gold plated jumper tab positions located on the CPU board (Figure 11). Alarm 1
and Alarm 2 have three jumper programmable functions: latching/non-latching relays, normally
energized/normally de-energized relays, and ascending/descending alarm set points. The fault alarm has two
jumper programmable functions: latching/non-latching relay, and normally energized/normally de-energized
relay. The default settings of the alarms (jumpers removed) are normally de-energized relays, non-latching
relays, and alarm points that activate during descending gas conditions.
Figure 11 Alarm Jumpers
If a jumper tab is installed in the latch position that alarm relay will be in the latching mode. The latching
mode will latch the alarm after alarm conditions have cleared until the alarm reset function is activated. The
non-latching mode (jumper removed) will allow alarms to de-activate automatically once alarm conditions
have cleared.
If a jumper tab is installed in the energize position, that alarm relay will be in the energized mode. The
energized mode will energize or activate the alarm relay when there is no alarm condition and de-energize or
de-activate the alarm relay when there is an alarm condition. The de-energized mode (jumper removed) will
energize or activate the alarm relay during an alarm condition and de-energize or de-activate the alarm relay
when there is no alarm condition.
If a jumper tab is installed in the ascending position that alarm relay will be in the ascending mode. The
ascending mode will cause an alarm to fire when the gas concentration detected is greater than or equal to the
alarm set point. The descending mode (jumper removed) will cause an alarm to fire when the gas
concentration detected is lesser than or equal to the alarm set point. Except in special applications, H2S
monitoring will require alarms to fire in “ASCENDING” gas conditions.
Any unused jumper tabs should be stored on the connector board on the terminal strip labeled “Unused
Jumpers”.
If applicable, set the RS-485 ID number via the two rotary dip switches located on the preamp board (see
Figure 12). There are 256 different ID numbers available, which are based on the hexadecimal numbering
system. If RS-485 communications are used, each sensor must have its own unique ID number. Use a
jeweler’s screwdriver to set the rotary dipswitches according to Table 1 Hexadecimal Conversion. If RS-485
communications are not used, leave the dipswitches in the default position, which is zero/zero (0)-(0).
Replace the plug-in control circuit and replace the junction box cover.

Model 1000 H2S Echem
Model 1000 H2S Echem Instruction Manual Rev. 2.9 Page 11 of 30
Table 1 Hexadecimal Conversion
ID#
SW1
SW2
ID#
SW1
SW2
ID#
SW1
SW2
ID#
SW1
SW2
ID#
SW1
SW2
ID#
SW1
SW2
none
0
0
43
2
B
86
5
6
129
8
1
172
A
C
215
D
7
1
0
1
44
2
C
87
5
7
130
8
2
173
A
D
216
D
8
2
0
2
45
2
D
88
5
8
131
8
3
174
A
E
217
D
9
3
0
3
46
2
E
89
5
9
132
8
4
175
A
F
218
D
A
4
0
4
47
2
F
90
5
A
133
8
5
176
B
0
219
D
B
5
0
5
48
3
0
91
5
B
134
8
6
177
B
1
220
D
C
6
0
6
49
3
1
92
5
C
135
8
7
178
B
2
221
D
D
7
0
7
50
3
2
93
5
D
136
8
8
179
B
3
222
D
E
8
0
8
51
3
3
94
5
E
137
8
9
180
B
4
223
E
F
9
0
9
52
3
4
95
5
F
138
8
A
181
B
5
224
E
0
10
0
A
53
3
5
96
6
0
139
8
B
182
B
6
225
E
1
11
0
B
54
3
6
97
6
1
140
8
C
183
B
7
226
E
2
12
0
C
55
3
7
98
6
2
141
8
D
184
B
8
227
E
3
13
0
D
56
3
8
99
6
3
142
8
E
185
B
9
228
E
4
14
0
E
57
3
9
100
6
4
143
8
F
186
B
A
229
E
5
15
0
F
58
3
A
101
6
5
144
9
0
187
B
B
230
E
6
16
1
0
59
3
B
102
6
6
145
9
1
188
B
C
231
E
7
17
1
1
60
3
C
103
6
7
146
9
2
189
B
D
232
E
8
18
1
2
61
3
D
104
6
8
147
9
3
190
B
E
233
E
9
19
1
3
62
3
E
105
6
9
148
9
4
191
B
F
234
E
A
20
1
4
63
3
F
106
6
A
149
9
5
192
C
0
235
E
B
21
1
5
64
4
0
107
6
B
150
9
6
193
C
1
236
E
C
22
1
6
65
4
1
108
6
C
151
9
7
194
C
2
237
E
D
23
1
7
66
4
2
109
6
D
152
9
8
195
C
3
238
E
E
24
1
8
67
4
3
110
6
E
153
9
9
196
C
4
239
F
F
25
1
9
68
4
4
111
6
F
154
9
A
197
C
5
240
F
0
26
1
A
69
4
5
112
7
0
155
9
B
198
C
6
241
F
1
27
1
B
70
4
6
113
7
1
156
9
C
199
C
7
242
F
2
28
1
C
71
4
7
114
7
2
157
9
D
200
C
8
243
F
3
29
1
D
72
4
8
115
7
3
158
9
E
201
C
9
244
F
4
30
1
E
73
4
9
116
7
4
159
9
F
202
C
A
245
F
5
31
1
F
74
4
A
117
7
5
160
A
0
203
C
B
246
F
6
32
2
0
75
4
B
118
7
6
161
A
1
204
C
C
247
F
7
33
2
1
76
4
C
119
7
7
162
A
2
205
C
D
248
F
8
34
2
2
77
4
D
120
7
8
163
A
3
206
C
E
249
F
9
35
2
3
78
4
E
121
7
9
164
A
4
207
C
F
250
F
A
36
2
4
79
4
F
122
7
A
165
A
5
208
D
0
251
F
B
37
2
5
80
5
0
123
7
B
166
A
6
209
D
1
252
F
C
38
2
6
81
5
1
124
7
C
167
A
7
210
D
2
253
F
D
39
2
7
82
5
2
125
7
D
168
A
8
211
D
3
254
F
E
40
2
8
83
5
3
126
7
E
169
A
9
212
D
4
255
F
F
41
2
9
84
5
4
127
7
F
170
A
A
213
D
5
42
2
A
85
5
5
128
8
0
171
A
B
214
D
6
Figure 12 RS-485 Dip Switches

Model 1000 H2S Echem
Model 1000 H2S Echem Instruction Manual Rev. 2.9 Page 12 of 30
4. Start Up
Upon completion of all tubing connections and field wiring the Model 1000 Series Process Analyzer is ready
for startup. Note that after power is applied, varying readings may occur during sensor warm-up. Allow at
least 1 hour for stabilization (24 hours is best). With sample gas and air flowing, apply system power and
observe the following normal conditions:
a) DM-624 “Fault” LED’s are off.
b) A reading close to the anticipated H2S level should be indicated upon conclusion of a 1-minute “warming
up” cycle.
NOTE: All alarms will be disabled for 1 minute after power up. In the event of power failure,
the alarm disable period will begin again once power has been restored.
1. If applicable make sure the optional Acetic Acid Bubbler is filled with the proper solution. (5% acetic
acid solution or standard white vinegar.)
2. Set the sample pressure to 10psig and verify the proper set point at the pressure gauge
3. Set the airflow through the Air sample rotameter. Adjust the rotameter flow valve to 250cc/min and in
alignment with the “→” mark on the rotameter.
NOTE: Sample flow rates must be actual rotameter set-point flow rates, after properly
accounting for rotameter gas density effects, see Table 2.
Table 2 Sample Flow Rate
DM-624 Range
(ppm)
Sample Flow
(cc/min)
Air Flow
(cc/min)
Span Gas Flow
(cc/min)
H
2
S Cal Gas
(ppm)
0-10
200 Labeled “S→”
500
250 Labeled “C→”
10
0-20
200 Labeled “S→”
500
250 Labeled “C→”
10
0-25
200 Labeled “S→”
500
250 Labeled “C→”
10
0-50
200 Labeled “S→”
500
250 Labeled “C→”
10 or 25
0-100
200 Labeled “S→”
500
250 Labeled “C→”
25 or 50
0-150
200 Labeled “S→”
500
250 Labeled “C→”
25 or 50
0-500
80 Labeled “S→”
1000
100 Labeled “C→”
100
0-1000
200 Labeled “S→”
500
250 Labeled “C→”
100 or 250
0-5000
200 Labeled “S→”
800
250 Labeled “C→”
1,000 or 2,500
0-10,000
80 Labeled “S→”
800
100 Labeled “C→”
2,500 or 5,000
0-5%
200 Labeled “S→”
1000
250 Labeled “C→”
1% or 2.5%
4. Adjust the sample mass flow controller valve per table above to meet the designated sample flow target
mark labeled as “S→”. The “C→” indicator on the rotameter shows what Flow rate to calibrate at if the
cal gas is N2. If the cal gas is in methane, then span gas flow should be set to “S→”.
NOTE: A displayed methane (typical natural gas) sample flow of 200cc/min. is actually equal
to 250cc/min. of nitrogen when accounting for the 20% gas density affect on the rotameter. A
displayed methane flow of 80cc/min. is actually 100cc/min. when accounting for the density
effect.
5. Set the airflow rotameter per the Air Flow value in Table 2 that corresponds to the DM-624 Sensor Range.
6. Proceed with calibration per Section 6 Calibration and Maintenance.

Model 1000 H2S Echem
Model 1000 H2S Echem Instruction Manual Rev. 2.9 Page 13 of 30
5. Operating Software
5.1 Programming Magnet Operating Instructions
Operator interface to MicroSafe™ gas detection products is via magnetic switches located behind the
transmitter faceplate. DO NOT remove the glass lens cover to calibrate or change programming parameters.
Two switches labeled “PGM 1” and “PGM 2” allow for complete calibration and alarm level programming
without removing the enclosure cover, thereby eliminating the need for area de-classification or the use of hot
permits.
Figure 13 Programming Magnet
A magnetic programming tool (Figure 13) is used to operate the switches. Switch action is defined as
momentary contact, 3-second hold, and 30-second hold. In momentary contact use, the programming magnet
is waved over a switch location. In 3-second hold, the programming magnet is held in place over a switch
location for 3 or more seconds. In 30-second hold, the programming magnet is held in place over a switch
location for 30 or more seconds. Three and 30-second hold is used to enter or exit calibration and program
menus while momentary contact is used to make adjustments. The location of “PGM 1” and “PGM 2” are
shown in section 1.3.
NOTE: If, after entering the calibration or program menus, there is no interaction with the
menu items for more than 30 seconds, the sensor will return to its normal operating condition.
5.2 Operating Software
Operating software is menu listed with operator interface via the two magnetic program switches located under
the faceplate. The two switches are referred to as “PGM 1” and “PGM 2”. The menu list consists of 3 items
which include submenus as indicated below.
01. Normal Operation
a) Current Status
02. Calibration Mode
a) Zero
b) Span
03. Program Menu
a) Program Status
b) Alarm 1 Level
c) Alarm 2 Level
d) Calibration Level
5.2.1 Normal Operation
In normal operation, the display tracks the status of the sensor and gas concentration and appears as: “##.##
PPM H2S”. The milliamp current output corresponds to the monitoring level and range of the sensor, where
Full Scale is 20mA.

Model 1000 H2S Echem
Model 1000 H2S Echem Instruction Manual Rev. 2.9 Page 14 of 30
5.2.2 Calibration Mode
Calibration mode allows for sensor zero and span adjustments. It uses an “AUTO SPAN” sequence with built
in diagnostics to ensure adequate sensor response and signal stability “1-ZERO 2-SPAN”.
Zero Adjustment
Zero is set with no H2S target gases present. “AUTO ZERO”
Span Adjustment
Span adjustment is performed with a target gas concentration of 10 ppm H2S in nitrogen. Span gas
concentrations other than 10 ppm may be used “AUTO SPAN”. See Table 3 Sample Flow Rate.
5.2.3 Program Mode
Program Mode provides a program status menu (View Program Status) to check operational parameters.
Program Mode also allows for the adjustment of alarm set point levels, the calibration gas level setting,
View Program Status
View Program Status is a listing that allows the operator to view the gas, range, and software version number
of the program, as well as the current alarm settings, calibration gas level setting, offset value, RS-485 ID
number, heater voltage, and estimated remaining sensor life.
The following procedure is used to view the programming status of the sensor:
a) Enter the programming menu by holding the programming magnet stationary over “PGM 2” for 15
seconds. When the display changes to “VIEW PROG STATUS”, withdraw the magnet. Scroll through
the programming menu by momentarily waving the programming magnet over either “PGM 1” or “PGM
2”. The menu options are: View Program Status, Set Alarm 1 Level, Set Alarm 2 Level, and Set Cal
Level.
b) Scroll to the “VIEW PROG STATUS” listing and hold the programming magnet over “PGM 1” for 3
seconds. The display will automatically scroll, at five second intervals, through the following information
before returning back to the “VIEW PROG STATUS” listing.
Gas type and software version number.
Alarm set point level of alarm 1. The menu item appears as: “ALM1 SET @ ##PPM”
Alarm firing direction of alarm 1. The menu item appears as: “ALM1 ASCENDING” or descending.
Alarm relay latch mode of alarm 1. The menu item appears as: “ALM1 NONLATCHING” or latching.
Alarm relay energize state of alarm 1. The menu item appears as: “ALM1 DE-ENERGIZED” or
energized.
Alarm set point level of alarm 2. The menu item appears as: “ALM2 SET @ ##PPM”
Alarm firing direction of alarm 2. The menu item appears as: “ALM2 ASCENDING” or descending.
Alarm relay latch mode of alarm 2. The menu item appears as: “ALM2 LATCHING” or non-latching.
Alarm relay energize state of alarm 2. The menu item appears as: “ALM2 DE-ENERGIZED” or
energized.
Alarm relay latch mode of the fault alarm. The menu item appears as: “FLT NONLATCHING” or
latching.
Alarm relay energize state of the fault alarm. The menu item appears as: “FLT ENERGIZED” or de-
energized.
Calibration gas level setting. The menu item appears as: “CalLevel @ ##PPM”
Identification of the RS-485 ID number setting. The menu item appears as: “485 ID SET @ ##”
Estimated remaining sensor life. The menu item appears as: “SENSOR LIFE 100%”

Model 1000 H2S Echem
Model 1000 H2S Echem Instruction Manual Rev. 2.9 Page 15 of 30
c) Exit back to normal operations by holding the programming magnet over “PGM 2” for 3 seconds, or, the
sensor will automatically return to normal operation in 30 seconds.
Alarm 1 Level Adjustment
The alarm 1 level is adjustable over the range 10% to 90% of range. For hydrogen sulfide gas sensors, the
level is factory set at 20% F.S. The menu item appears as: “SET ALM1 @ ### PPM”.
Alarm 2 Level Adjustment
The alarm 2 level is also adjustable over the range 10% to 90% of range. For hydrogen sulfide gas sensors, the
level is factory set at 60 % Full Scale. The menu item appears as: “SET ALM2 @ ### PPM”
Calibration Level Adjustment
The Calibration level is adjustable from 10% to 90% of range. The menu item appears as: “CAL LEVEL @
## PPM”

Model 1000 H2S Echem
Model 1000 H2S Echem Instruction Manual Rev. 2.9 Page 16 of 30
5.2.4 Software Flow Chart
Figure 14 DM-624 Software Flow Chart
6. Calibration and Maintenance
The Model 1000 Series H2S Process Analyzer is calibrated prior to shipment. Only minimal adjustment
should be required at time of commissioning. However, it is highly recommended that a zero and span
calibration be performed twice in the first week of operation to assure optimum system performance. After
that, a recalibration interval of every month is recommended.
Maintenance
When the Acetic Acid Bubbler option is used, the 5% acetic acid solution (or white vinegar) should be kept
near the Max fill mark on the bottle. The level should be checked monthly and the entire solution contents
should be changed every 6 months.
Other manuals for 1000
1
This manual suits for next models
1
Table of contents
Other Detcon Measuring Instrument manuals
Popular Measuring Instrument manuals by other brands

ABB
ABB C1900 Series user guide
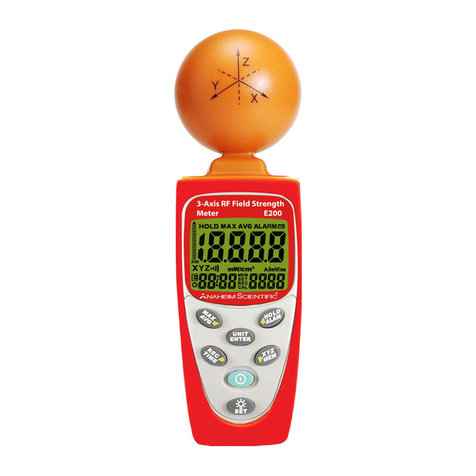
Anaheim Scientific
Anaheim Scientific E200 user manual
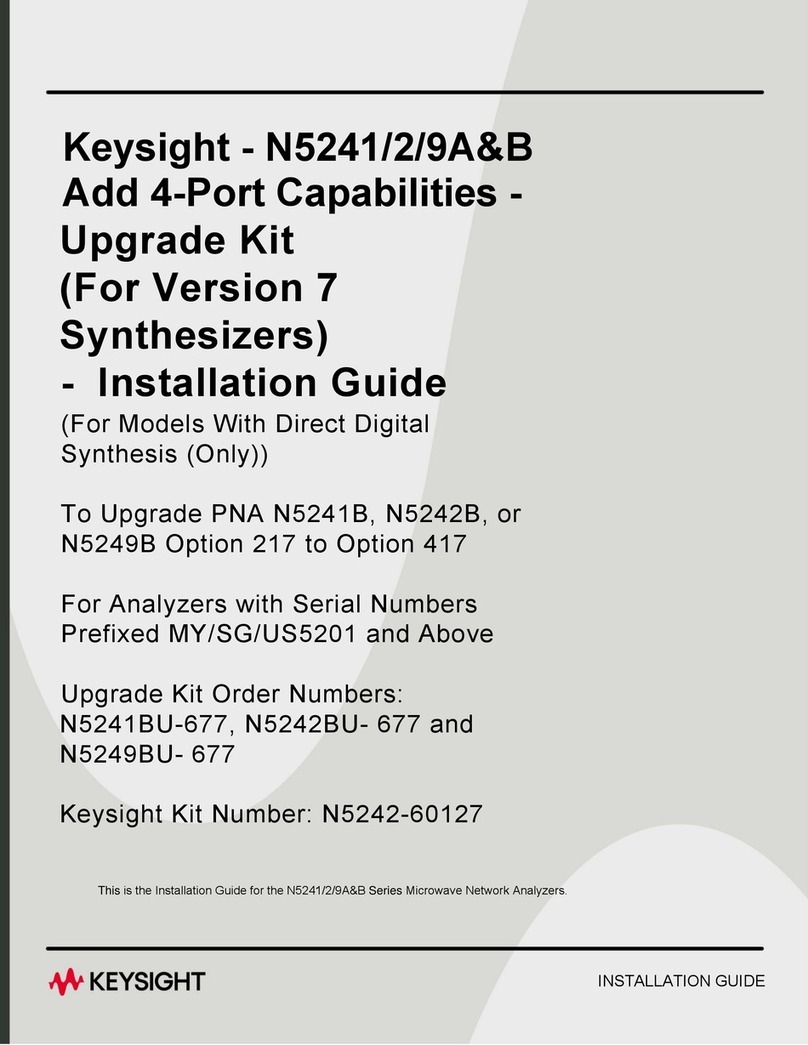
Keysight Technologies
Keysight Technologies N5241BU-677 installation guide
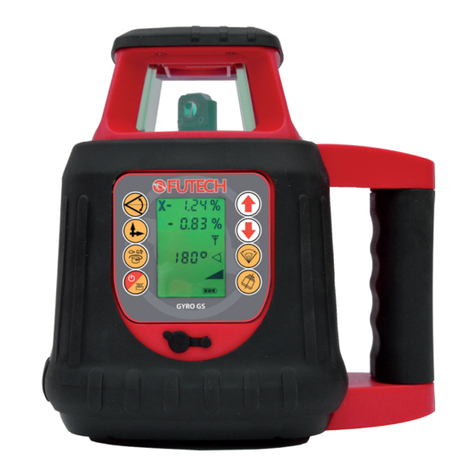
Futech
Futech Gyro GS user manual
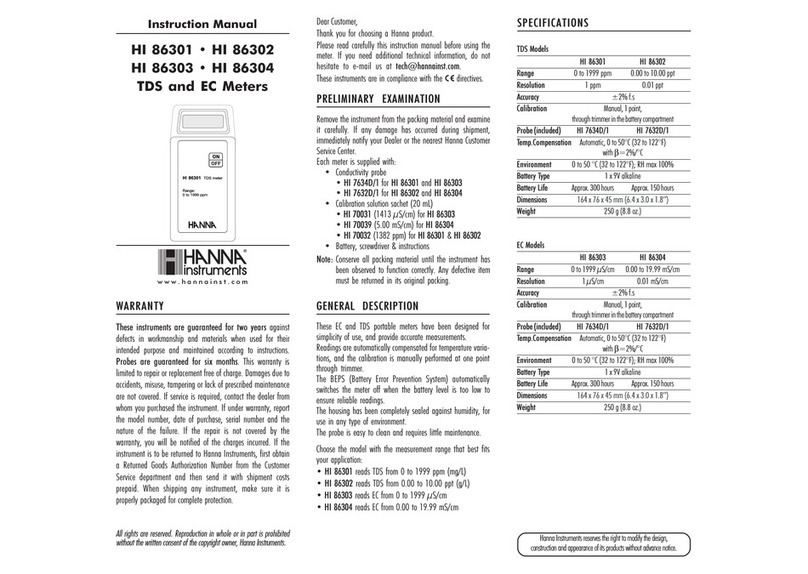
Hanna Instruments
Hanna Instruments HI 86301 instruction manual
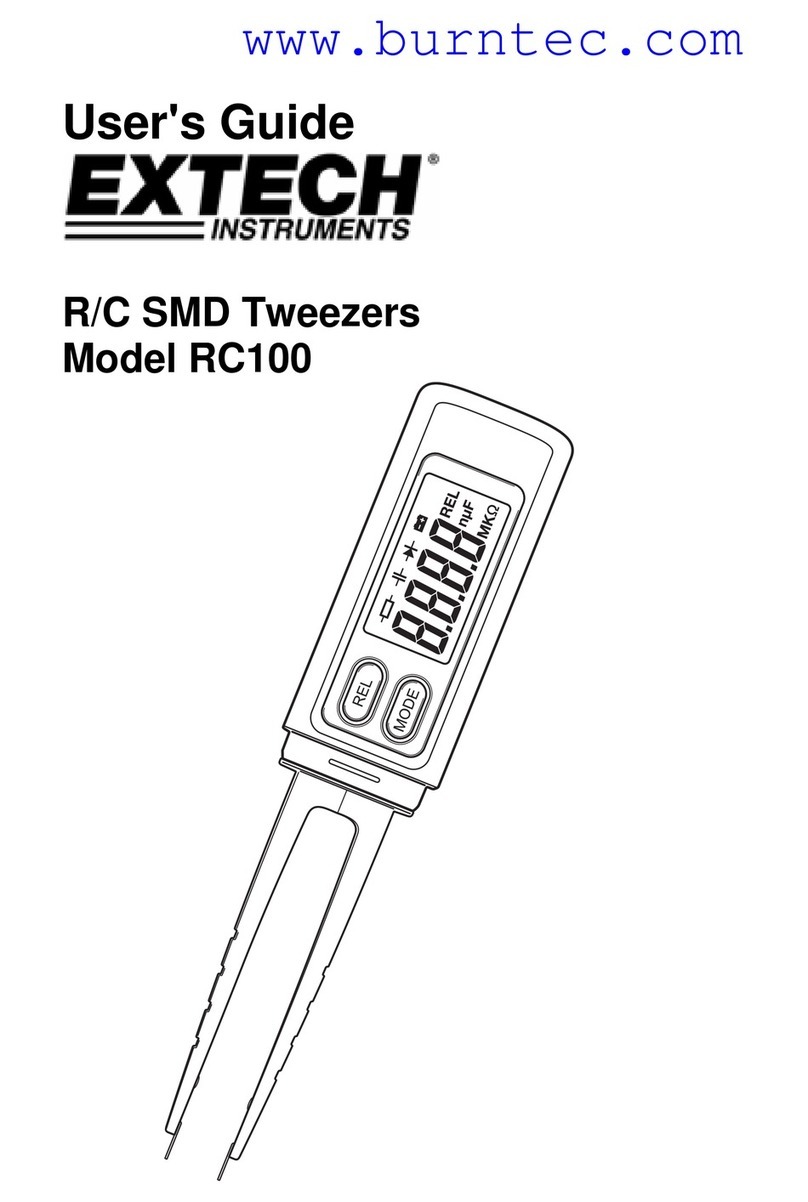
Extech Instruments
Extech Instruments RC100 user guide