Deus CT1 24 Technical specifications

Rev. 10 - 23/05/2022 LG
- DEUS - CT1 24 Display
BA
ELECTROMECHANICAL GEAR MOTOR FOR SLIDING GATES
WITH CONTROL UNIT
INSTRUCTIONS AND WARNINGS FOR INSTALLATION, USE AND MAINTENANCE
GB
CONTROL UNIT TOUCH
WITH DISPLAY
DEUS 4HP for gates Max 400Kg
DEUS 6HP for gates Max 600Kg
DEUS 4HS for gates Max 400Kg

P.2
WARNING
Important safety instruc!ons.
For personal safety it is important to follow these instruc!ons. Keep these instruc!ons.
The device must be disconnected from the power supply during cleaning and maintenance opera!ons
and the replacement of components.
Do not allow children to play with the gate control devices. Keep remote controls away from children.
Monitor the moving gate and keep people away as long as the automa!on is moving.
Be careful when opera!ng the manual release device as the leaves could move with the wind and cause
damage to people or things.
Check the system frequently, in par!cular the hinges and mechanical stops, check for signs of wear or
damage.
Do not use, if repair or adjustment is required, as an installa!on failure can cause injury. Check monthly
that the safety devices are func!oning and efficient.
If necessary, adjust or recheck, incorrect adjustment can present a hazard.
If the interven!on does not restore the correct func!oning of the automa!on, contact the authorized
technical assistance center.
The automa!on must not be installed at an al!tude above 2,000 m above sea level.
In accordance with the installa!on rules, insert a device that ensures complete disconnec!on from the
power supply with a contact opening distance in overvoltage category III.
If the power cable is damaged, it must be replaced by the manufacturer or its technical
assistance service or in any case by a person with a similar qualifica!on, in order to prevent any risk.
WARNING
Automa!on for sliding gates.
The gate can operate unexpectedly, therefore do not allow
anyone or anything to stop in the gate movement area.
WARNING
Important safety instruc!ons.
Follow all instruc!ons as incorrect installa!on can cause
serious damage.
Permanently fix the warning labels against entrapment in a very visible point or near any fixed control
devices.
Permanently fix the manual release label adjacent to its control unit.
A$er installa!on, make sure that the mechanism is properly adjusted and that the movement motor
reverses movement when the door hits an object.
A$er installa!on, make sure that the parts of the gate do not clu%er public roads or sidewalks. A$er
installa!on, make sure that the protec!on systems work as expected.
This informa!on must also be included in the instruc!ons.
This appliance can be used by children under 8 years of age and by people with reduced physical
abili!es, sensory or mental impairments or lack of experience or necessary knowledge, as long as they
are under surveillance or a$er they have received instruc!ons rela!ng to the safe use of the appliance
and the understanding of the dangers inherent in it.
Children must not play with the device.
Cleaning and maintenance opera!ons intended to be carried out by the user must not be carried out
by children without supervision.
DANGER

P.3
GENERAL INDEX
1 - TECHNICAL DATA OF THE ENGINE --------------------------------------------------------------------------------------- P. 4
1.1 - Dimensions and limits of use
2 - INSTALLATION ---------------------------------------------------------------------------------------------------------------- P. 5
2.1 - Installa!on of the gearmotor components
2.2 - Installa!on and fixing of the anchoring plate
2.3 - Installa!on and fixing of the gearmotor
2.4 - Rack moun!ng
2.5 - Manual release
2.6 - Wiring and connec!ons
2.7 - Inser!on of electric cables in the gearmotor
3 - ELECTRONIC CONTROL UNIT CONNECTIONS ------------------------------------------------------------------------ P. 9
3.1 - Wiring and connec!ons
3.2 - Control unit connec!ons
3.3 - Electrical connec!on
4 - CONTROL UNIT CONFIGURATION -------------------------------------------------------------------------------------- P.12
4.1 - Reset default parameters
4.2 - Automa!c ini!al setup
5 - REMOTE CONTROL SETTINGS ------------------------------------------------------------------------------------------- P.13
5.1 - Total opening remote learning
5.2 - Par!al/Pedestrian opening remote learning
5.3 - Remote control learning on Relay contact
5.4 - Remote control learning via radio
5.5 - Remove one transmi#er, all transmi#ers
6 - SETTINGS ---------------------------------------------------------------------------------------------------------------------- P.15
7 - VISUALIZATION OF THE INPUT STATUS VIA DISPLAY --------------------------------------------------------------- P.17
8 - CONNECTION WITH EMERGENCY BATTERIES ----------------------------------------------------------------------- P.18
9 - GENERAL INFORMATION -------------------------------------------------------------------------------------------------- P.19
9.1 - Manufacturer's data
9.2 - Intended use
10 - SAFETY INSTRUCTIONS AND WARNINGS ---------------------------------------------------------------------------- P.19
10.1 - Prescrip!ons and general warnings
11 - INSTALLATION WARNINGS ---------------------------------------------------------------------------------------------- P.20
11.1 - Prescrip!ons and warnings for installa!on
12 - TESTING AND COMMISSIONING -------------------------------------------------------------------------------------- P.20
12.1 - Tes!ng
12.2 - Commissioning
13 - SAFETY INSTRUCTIONS AND WARNINGS --------------------------------------------------------------------------- P.21
13.1 - Prescrip!ons and warnings for use
14 - MAINTENANCE ------------------------------------------------------------------------------------------------------------ P.22
14.1 - Requirements and warnings for maintenance
14.2 - Ordinary maintenance
15 - DEMOLITION AND DISPOSAL ------------------------------------------------------------------------------------------ P.22

P.4
DEUS4HS
DEUS4HP DEUS6HP
335
8
170
285
300
Z16 87
45
Min 81 / Max 91
Vac 230 50/60Hz
W 230
A 1
Vdc 24
W 120
A 6
N 400
dB LpA-70
D
IP 55
°C
mm 335 X 170 H 300
Kg 4
CT1 24 Display
m/min 13,8
%80
Min 20
Kg 400
Nm 15
140 120
55
300 300
12 10
13,8 20,4
80 80
20 20
600400
-20 / +70
1 - TECHNICAL DATA OF THE ENGINE
Type Permanent Grease
1.1 - Dimensions and limits of use.
The gearmotor installaon area must provide the space necessary for maintenance and manual
release operaons.
Check the overall dimensions by referring to the image below.
Type
Without limit switch - Double magnec encoder
24V irreversible mechanical gearmotor for sliding gates.
Supply voltage Line
Power 230Vac
Line current 230Vac
Engine type
Maximum motor power
Maximum motor current
Thrust
Maximum starng torque
Maximum speed
Intermience
Connuous working me
Maximum gate weight
Lubricaon
Stop switch
Sound pressure
Motor insulaon
Protecon level
Operang temperature
Dimensions of the motor
Weight
Electronic control unit

P.5
DX
SX
200
350
250
DX
SX
200
350
250
2
1
ATTENTION:
If the gearmotor is subjected to severe working condi!ons or if the weight of the gate
exceeds 300 kg, the anchoring plate must necessarily be fixed by "drowning" it in the concrete.
Le -hand closing
2 - INSTALLATION
Right-hand closing
2.1 - Installaon of the gearmotor components.
The gearmotor installa!on area must provide the space necessary to carry out maintenance and
manual release opera!ons.
2.2 - Installaon and fixing of the anchoring plate.
a) Respect the dimensions in the image.
b) In order to place the anchor plate correctly, respect its orienta!on (LEFT - RIGHT) as shown in
the image.
c) Respect the height dimensions as indicated in the image with pinion Z16.
d) Posi!on the pipes of the electric cables, leaving them protruding and capping them, to
prevent them from filling up with debris.
A$ach the anchor plate to the concrete base with 2 expansion anchors or submerge in the
fresh concrete the two "L".

P.6
mm1
a) Remove the gearmotor cover by unscrewing the screws; place the gearmotor on the anchoring
plate and screw the two M10 bolts with rela!ve washers.
b) Make any ver!cal adjustment of the gearmotor by adjus!ng the 4 dowels, leveling it; adjust
the gearmotor so that it is parallel to the gate.
Fix the gearmotor defini!vely by locking the two M10 bolts and rela!ve washers with a
special wrench.
2.4 - Rack assembly
2.3 - Installa!on and fixing of the gearmotor
Release the gearmotor, properly fix the rack to the gate with the supplied screws.
Leave 1mm gap between the pinion and the rack teeth.
Verify that the complete movement occurs without obstacles and impediments. Check the
presence of the leaf stop mechanical limit switches on both sides.
ATTENTION
MECHANICAL STOP

P.7
1
2
3
2.5 - Manual release
ATTENTION:
• Disconnect the power supply before proceeding.
• Manual release can cause uncontrolled movement of the gate,
due to mechanical damage, or condi!ons of mechanical imbalance.
• This command allows you to release the gearmotor transmission and move the
leaf manually; It can be used in the event of a power failure or system failure.
Manual release takes place using a key which must be kept in a safe place.
a) slide the lock protec!on to the le".
b) insert the key into the lock and turn it 90 ° an!clockwise.
c) rotate the lever 90 °.
d) the gearmotor is now unlocked.
ATTENTION

P.8
Before proceeding with the connec!ons, carefully read the sec!ons related to SAFETY. All wiring
and connec!on opera!ons must be performed with the control board disconnected.
Power supply; if the disconnec!on device is not visible, post a warning plate: “ATTENTION:
MAINTENANCE IN PROGRESS”.
The internal wiring of the electromechanical actuator that has been made by the company must
not be modified.
2.7 - Inser!on of electric cables in the gearmotor
ATTENTION: the cables used must be suitable for the type of installa!on; this evalua!on is the
responsibility of the installer.
• The power cord must not be lighter than 60245 IEC 57 (HO5RN-F).
• Inside the power cord, one wire must be yellow and green for grounding.
• The coa!ng of the power cable must consist of a polychloroprene sheath.
• All cables must be stripped to the minimum necessary, maximum 6 mm, as close as possible
to the connec!on terminals, to avoid accidental contact with live parts if the cable comes off
from the terminal.
• Do not pre-!n the cables that are to be screwed to the terminals.
• Use the power cord fastener.
a) Remove the cover from the gearmotor.
b) Open the holes provided in the cable gland membrane, then insert the cables necessary for
the connec!ons (keep the 230V cables separate from those at very low voltage).
Leave the cables approximately 40 cm longer.
c) Insert and make sure that the cable membrane is well adherent to the base of the gearmotor
to prevent access to insects and dirt.
For safety reasons it is mandatory to connect the motor grounding.
Crimp the yellow-green wire of the power cable into the eyelet placed in the aluminum base.
2.6 - Wiring and connec!ons
Yellow-Green Cable
Accessory connec!on
Low voltage
Power
230Vac 50Hz

P.9
F1
8A-T
F2
250mA-F
3 - ELECTRONIC CONTROL UNIT CONNECTIONS
The installer must connect the 230 Vac 50 Hz power supply and the various devices provided
for automa!on.
The connec!ons between the control unit, motor, encoder and transformer are already made
by the manufacturer and must not be modified in any way
ATTENTION:
To facilitate connec!on to the control unit, remove the connector with the help of a
screwdriver. Once the wiring is complete, insert it in the correct posi!on.
With clamps, block the wires in the slots adjacent to the connector. Use cables of suitable
sec!on and type.

P.10
1
2
6
15 - 16
16
17
3.2 - Control unit connec!ons
Terminal
Descrip!on
ANTENNA: Antenna braid input, use RG58-50 Ohm cable.
COMMON COMMANDS: For the inputs: STOP - OPEN - CLOSE - STEP BY STEP - SECURITY - PHOTO.
6 - 7
STOP: NC input Determines the gate’s halt.
Safety devices such as an emergency stop bu!on can be connected to it. When the command is
released, the automa"c closing is never performed, movement is only restored with a new
command.
OPENING: NO input Determines the opening of the gate.
CLOSING: NO input Determines the closure of the gate.
13 - 14
NC = Normally Closed Contact - NO = Normally Opened Contact
Brown
+ Encoder
- Encoder
Motor
- Before proceeding with the wiring and connec"ons, carefully read what is wri!en in the
REQUIREMENTS AND WARNINGS FOR SAFETY and INSTRUCTIONS AND WARNINGS FOR
INSTALLATION.
- All wiring and connec"on opera"ons must be carried out with the power supply disconnected.
If the device is not visible, a warning plate must be affixed: “ATTENTION: UNDER MAINTENANCE”.
ANTENNA: Antenna input
Func!on
Encoder A - B
OPENING SAFETY: NC input for opening safety devices.
During the gate opening cycle, the interven"on of the safety determines a short inversion.
FLASHING: 24 Vdc 5 W max output, for connec"ng the flashing light.
STEP BY STEP: NO input Determines the gate movement according to the following cycles:
SEMIAUTOMATIC: Open, Pause, Close, Pause.
CONDOMINIUM: Open (with automa"c closing ac"ve).
SEMIAUTOMATIC: Open, Stop, Close, Stop.
SEMIAUTOMATIC: Opens, Closes.
SEMIAUTOMATIC: Man’s switch.
6 - 8
6 - 9
6 - 10
6 - 11
3.1 - Wiring and connec!ons
RELAY CONTACT: Contact output Mul"func"on relay, with OPTION [8]:
Opened gate light - Courtesy light - Radio contact.
+
-30 Vdc OUTPUT: To power auxiliary devices, max 200mA.
Cable colorTerminals
6 - 12
PHOTOCELL: NC input for photocells or safety devices.
It does not intervene during the gate opening cycle.
During the closing cycle of the gate, it reverses the movement un"l it is completely opened.
Green yellow
White
Blue / Red
Black / Red Transformer - / Transformer +
6 - 8/9 PEDESTRIAN: With the simultaneous ac"va"on of the two inputs 8 and 9, the gate opens in
pedestrian mode following the se%ngs in the SETTINGS menu [6].
2 - 3
1
4
5 - 6
7 - 8

P.11
Relay 1A
30 Vdc 200mA Max
N.O.
COM.
FUSE
FUSE
AB
MICRO
MOS
INTEGRATED
RADIO FREQUENCY
COND.
COND.
Relay1
Relay2
MOS
Diode
RESISTENCE
CONN.
LM E2 MC330
Relay
16 +
17 -
6
12
N.O.
7
N.C.
16 +
15 -
AB
N.O. N.O.
F1 F2
F1 = 8A - T
F2 = 250mA - F
8
69
610
6
N.O.
8 9
6
6
PHOTOCELLS
OPENS
STOP
LED FLASHING LIGHT
28 Vdc Max 2W
CLOSES STEP BY STEP
OPENED GATE LIGHT
PEDESTRIAN
28 Vdc Max 2W
3.3 - Electrical connec!on
N.O.
COM.
FLASHING
GATE LIGHT
COURTESY LIGHT
ANTENNA
COMMON COMMANDS
STOP
CLOSES PEDESTRIAN
STEP BY STEP
OPENING SAFETY
OPENS
EXIT
CLOSING PHOTO
Control unit output
1
2
3
4
5
6
7
8
Encoder +
Encoder A
Encoder B
Encoder -
Motor
Motor
Transformer -
Transformer +

P.12
FO F
230V
NO
230V
OFF
ON
BA
BA BA
5”
BA BA
BA
1
234
FO F
230V
NO
230V
OFF
ON
BA
BA BA
Press and hold the B buon, aer 5" the icon [ [ ] flashes, release the buon, the gate moves slowly
to the le in search of the first mechanical stop which must be the Opening stop, if not, to reverse
the movement to the right, press and release the B buon, the direcon of rotaon changes
as well as the display icon [ ] ].
The control unit performs a first automac maneuver at low speed, Opening and Closing with a
short pressure on the mechanical limit switches to store the complete cycle.
It then performs two more maneuvers to store the torque profile in opening and closing with the
default operang parameters.
At the end of the cycle, the [ - ] icon comes on to confirm that the automaon is ready to work.
Once the setup is completed, the B buon becomes a STEP-BY-STEP command if pressed.
Turn off the power, press and hold the buons Aand B at the same me, power on and hold
buons pressed unl a [ H ] flashes on the display; now release the buons, all the
parameters are reset to factory default.
Press
4 - CONTROL UNIT CONFIGURATION
4.2 - Automac inial setup
Opening
Mechanical Stop
STOP
Closing STOP
Mechanical Stop
Opening Closing
PLEASE NOTE
Any safety devices (Photocells or Stop) must be connected before
programming, otherwise they are NOT acve.
It is possible to acvate them later by following chapter 6 Opon 9.
Before proceeding with programming, make sure that the Opening
and Closing mechanical stops are present.
4.1 – Reset default parameters
Press
ATTENTION
Press

P.13
5”
BA
BA BA
BA BA
5”
BA BA
BA BA
5”
BA BA
BA
BA
BA X2
5 - REMOTE CONTROL SETTINGS
5.1 – Total opening remote learning
Press and hold the Abuon, aer 5" on the display the icon [ A] comes on; release the buon,
press the key of the remote transmier that you want to program within 5"; the correct storage
is highlighted by a brief flash on the display; in order to program addional transmiers, press in
sequence the keys on the transmiers, if no signal is transmied aer a few seconds the [ -]
icon comes on to confirm that the automaon is ready to work.
5.2 – Par al/Pedestrian opening remote learning
5.3 – Remote control learning on Relay contact
Press
Press
Press
Press
Press Press
Press
Press Press
Press
Press and hold the Abuon, aer 5" on the display the [ A] icon comes on, release the Abuon,
press and release the Bbuon, the [ P] icon comes on the display, now press the key of the remote
transmier that you want to program within 5"; the correct storage is highlighted with a short flash
on the display; in order to program addional transmiers, press in sequence the keys on the
transmiers, if no signal is transmied aer a few seconds the [ -] icon comes on to confirm that the
automaon is ready to work.
Press and hold the Abutton, after 5"on the display the icon [ A] comes on, now release the button,
press the Bbutton twice and release; on the display the [ L] icon comes on, now press the key of the
remote transmitter that you want to program within 5"; the correct storage is highlighted with a
short ash on the display; in order to program additional transmitters, press in sequence the keys
on the transmitters, if no signal is transmitted after a few seconds the [ -] icon comes on to conrm
that the automation is ready to work.
PLEASE NOTE - The function is available only if Option 4 or 5 of Menu 8 is active

P.14
5”
BA BA
5”
BA BA BA
5”
BA
+
5.4 – Remote control learning via radio
5.5 – Remove one transmi!er, all transmi!ers
Press and hold Aand B bu!ons simultaneously for 5", the [ r] icon flashes on the display, now
release the bu!ons, press the key on the transmi!er that you want to remove (single
cancella$on) or press simultaneously Aand B to remove all remote transmi!ers.
Press
Press
Press
With the gate Opened and safety enabled: STOP and / or PHOTO.
1 - Press and hold for 10" in a row the key of a remote transmi!er previously programmed:
you enter the total opening setup, the memory is ready for storage, the flashing light flashes
once briefly.
Now press the key on the new remote transmi!er that you want to program, the correct
storage is confirmed with steady light for a few seconds; you can program only one radio
control at once.
2 - Press again the same radio control bu!on for 3" in a row: you enter the par$al opening
setup, the memory is ready for storage, the flashing light performs two short flashes.
Now press the key on the new remote transmi!er that you want to program, the correct
storage is confirmed with steady light for a few seconds; you can program only one radio
control at once.
3 - Press again the same remote transmi!er bu!on for 3" in a row: you enter the
mul$func$on relay radio control setup, the memory is ready for storage, the flashing light
preforms 3 short flashes.
Now press the key on the new remote transmi!er that you want to program, the correct
storage is confirmed with steady light for a few seconds; you can program only one radio
control at once.
Remove single remote control
Remove all remote transmi!ers
Press

P.15
BA BA
1”
1239
BA BA
A + 0.1.2.3.4.5.
B - 5.4.3.2.1.0.
Press and hold the Bbu!on, immediately a"er press the Abu!on, then release both bu!ons; now
every #me you press the bu!on A, the display will show the op#on number [ 0] - [ 1]…[ 9] for 5”;
in order to confirm the desired op#on press B.
Now the display indicates with the icon [ .] the adjusted level that goes from 0 to 5; with bu!ons A
and Byou can adjust the level according to the table shown below; a"er 5” the system
automa#cally quits and stores the last level.
Press Press Press Press
[0] - Opera!ng Op!ons
[0] Semi-automa#c (Default)
[1] Condominium
[2] Open - Stop - Close - Stop
[3] Opens - Closes
[4] Man’s switch
[5] . . . . . . . . . . . . . . . .
[1] - Automa!c Closing
[0] No (Default)
[1] 5”
[2] 10”
[3] 30”
[4] 60”
[5] 120”
[2] - Speed Level
[0] Minimum
[1] -----
[2] -----
[3] (Default)
[4] -----
[5] Maximum
Press
Opening Closing
6 - SETTING

P.16
EN12453
EN12445
5 Cm.
[3] - Obstacle Detec!on Sensi!vity
[0] Minimum
[1] -----
[2] (Default)
[3] -----
[4] -----
[5] Maximum
[4] - Slowdown Space Adjustment
[0] Minimum
[1] -----
[2] (Default)
[3] -----
[4] -----
[5] Maximum
[5] - Slowdown Speed level
[0] Minimum
[1] -----
[2] (Default)
[3] -----
[4] -----
[5] Maximum
[6] - Pedestrian opening
[0] 10% Of complete cycle
[1] 20%
[2] 30% (Default)
[3] 40%
[4] 50%
[5] 60%
[7] - Reversal Point Adjustment
[0] Minimum
[1] -----
[2] (Default)
[3] -----
[4] -----
[5] Maximum
Minimum Maximum
Minimum Maximum

P.17
BA BA BA
[8] - Relay Output
[0] Gate Open Light (Default)
[1] Courtesy light 30 "
[2] Courtesy light 1 '
[3] Courtesy light 3 '
[4] Impulsive radio contact
[5] Step-by-step radio contact
[9] - Enable NC safety inputs 7 - 11 - 12
With opon 9 it is possible to manually enable the safety inputs according to the
indicaons given here.
With the Red Led ON the corresponding NC input is enabled, with the Led OFF the input
is disabled.
Press Ato advance the sequence, when the segment is on, the contact is acve.
Press Press Press
Input 7
STOP
Input 11
SAFETY
IN
OPENING
Input 12
PHOTO
ATTENTION
PLEASE NOTE
Aer enabling the safety inputs, check their correct funconing.
7 – VISUALIZATION OF THE INPUT STATUS VIA DISPLAY
Press and release the Abuon, for 30 "it is possible to view the status of the inputs, according
to these rules:
Led On = Contact closed Led Off = Contact opened.
Press Aagain to quit the displayed menu.
11-SAFETY IN
OPENING 12-PHOTO
7-STOP
8-OPENS 9-CLOSES 10-STEP BY STEP
REMOTE TRASNMITTER

P.18
230 Vac
AGEX
+
-
+
-
FUSE
FUSE
AB
MICRO
MOS
INTEGRATED
RADIO FREQUENCY
COND.
COND.
Relay1
Relay2
MOS
Diode
RESISTENCE
CONN.
LM E2 MC330
Relay
1
2
3
4
5
6
7
8
F = 4A - T
Battery Fuse
5x20
8 - CONNECTION WITH EMERGENCY BATTERIES (OPTIONAL AGEX KIT)
The backup ba!eries allow you to have an emergency solu"on in cases of power failure; the
autonomy is around 8 hours and/or approximately ten maneuvers.
For the connec"ons follow the diagram shown here.
Transformer output
Card Input
Batteries
Switching Transformer
Electronic control unit
Red
Black

P.19
9 - GENERAL INFORMATION
It is strictly forbidden to copy or reproduce this instruc!on manual without wri"en permission and subsequent verifica!on by LIFE home integra!on.
Transla!on into other languages (of the manual) is strictly forbidden without previous wri"en authorisa!on from and subsequent verifica!on by LIFE
Home Integra!on.
All rights on this document are reserved.
LIFE home integra!on will not accept responsibility for damage or malfunc!ons caused by incorrect installa!on or improper use of products and
Users are therefore recommended to read this manual carefully LIFE home integra!on will not accept responsibilit y for damage or malfunc!ons caused
by the use of the automa!on together with the devices of otrer manufacturers; such ac! on will render the warranty void.
LIFE home integra!on will not accept responsibility for damage or injury caused by non-compliance with the installa!on, set up, maintenance and use
indica!ons contained in this manual and the safety instruc!ons described in the SAFETY INSTRUCTIONS AND WARNINGS chapter.
With the aim of improving its products, LIFE home integra!on reserves the right to bring about altera!ons to them at any !me, without giving
prior no!ce.
His document conforms to the state of the automa!on which it is provided for sale.
9.1 - Informa!on on the manufacturer
LIFE home integra!on is the manufacturer of the motor DEUS and the owner of all rights concerning this document.
• Manufacturer: LIFE Home Integra!on
• Address: Via Sandro Per!ni, 3/5 - 31014 Colle Umberto (TV) Italia
• Telephone: + 39 0438 388592
• Fax: + 39 0438 388593
• h"p: www.homelife.it
• e-mail : info@homelife.it
The iden!ty plate bearing the informa!on on the Manufacturer is fixed to the electromechanical operator.
The plate specifies the type and date (month/year) of manufacture of the product.
For further informa!on on technical and/or commercial issues and technician call-out and spares requests, Customer may contact the Manufacturer
or area representa!ve from which the product was purchased.
9.2 - Intended use
• The electromechanical operator DEUS has been exclusively designed to sliding gates.
Any usage differing from that described above is forbidden .
• The electromechanical operator may only be used with other LIFE products.
• The manufacturer declines all responsibility for damage caused by improper use. All risks are the fi"er's responsibility and the warranty shall be
rendered void .
• The electromechanical operator may not be installed or used in poten!ally explosive environments.
• The metal gate must be installed conform to current European standards and Direc!ves.
• The electromechanical operator may only be used when in perfect working order and in compliance with the intend use, in the awareness of safety
and hazard condi!ons and in compliance with the instruc!ons for installa!on and use.
• Any dysfunc!ons that may pose threats to safety must be eliminated immediately .
• The electromechanical operator may not be used in environments prone to flooding.
• Do not use the operator in environmental condi!ons characterised by harsh atmospheric agents (e.g. salty air).
10 - SAFETY INSTRUCTIONS AND WARNINGS
10.1 - General instruc!ons and warnings
• This manual is designed for PROFESSIONAL FITTERS only. Installa!on of the control unit requi res prac!cal and theore!cal knowledge of
mechanics, electrics and electronics as well as current sector legisla!on and regula!ons.
• Once the electromechanical operator has been installed, it is forbidden for users to perform any opera!on on the control unit this instruc!on
manual, which, as men!oned previously, are intended for use by qualified personnel only.
• Fi"ers must operate in compliance with the laws direc!ves.
He/she must also make constant reference to harmonised standards EN 12453 and EN 12445.
• Indica!ons given in this manual must always be observed when installing, connec!ng, adjus!ng, tes!ng and se&ng the control unit. The Manuf
acturer declines all responsibility for damage or injury caused by non-observance of the instruc!ons contained in this manual.
• The Manufacturer declines all responsability if the fi"er doesn't take care about over men!oned.
• Keep this manual in a safe and easily accessible place so that it can be consulted rapidly when necessary.
• During installa!on, connec!on, trial run and usage of the control unit, observe all applicable accident preven!on and safety regula!ons.
• For safety and op!mal func!on of the control unit, use only original spares, accessories, devices and fastening apparatus.
• Do not perform altera!ons on any control unit device or component. This opera!on may cause malfunc!ons, and put the products out of
manufacturer responsability
• If liquids contacts the control unit, disconnect the electricity supply and contact the Manufacturer's Assistance Service immediately;
Infact this situa!on maybe very dangerous for user.
• In the event of long periods of inac!vity, in order to prevent the leakage of harmful substances from the ba"ery.
• If faults or problems that cannot be resolved using the informa!on contained in this manual, contact the Manufacturer's assistance service.
• The Manufacturer declines all responsibility for damage to electromechanical operator func!oning caused by non-compliance to the storage
instruc!ons given below.
• The electromechanical operator must be stored in closed, dry places, at room temperatures between -20 and +70'C and raised off the ground.
• Keep the electromechanical operator away from sources of heat and flames, that maybe cause malfunc!ons, fires or hazard situa!ons.

P.20
11- INSTALLATION WARNINGS
ATTENTION : Important safety instruc!ons. Follow all instruc!ons carefully, incorrect installa!on may cause serious injury.
Before start installa!on we highly recommend reading the instruc!ons and warnings contained in this manual carefully (see the SAFETY INSTRUCTIONS
AND WARNINGS Chap) and observing the instruc!ons it contains.
11.1 - Instruc!ons and warnings for installa!ons
• Before start installa!on read the. SAFETY INSTRUCTIONS AND WARNINGS chapter carefully
• The PROFESSIONAL FITTER electromechanical operator is responsible to perform risk analysis and to regulate the automa!ons
safety devices.
• The Fi"er must check that the temperature range declared on the electromechanical operator is in accordance to the place in when the device is
installed.
• Normally open/off bu"ons installed for the ac!va!on of the operator must be posi!oned so that they are within view of the gate but distant
from moving parts. Unless said commands operate using keys, they must be posi!oned at a minimum height of 1.5m and not accessible to to
unauthorised persons.
• During installa!on, make constant reference to harmonised standards EN 12453 and EN12445.
• Ensure that the individual devices to be installed are compa!ble with the electromechanical operator. Do not proceed if even just one device is
unsuitable for the intended use.
• Ensure that the place of installa!on of the central unit is not prone to flooding, does not contain sources of heat or naked flames, fires or hazard
situa!ons in general.
• During installa!on, protect control unit components in order to prevent liquids (e.g. rain) and/or foreign bodies (earth, gravel, etc) penetra!ng inside.
• Connect the control unit to a power supply line created in compliance with current regula!ons and earthed and fi"ed with a power supply sec!oning
switch.
• Connect the gearmotor only to an electrical power supply line carried out according to the regula!ons in force; device for complete disconnec!on of
the line in condi!ons of overvoltage category III in accordance with na!onal regula!ons in force.
• Wrapping materials must be disposed of in compliance with local regula!ons.
• Wear protec!ve goggles when making holes for clamping.
In the event of work at heights of over 2m from the ground, for example for the installa!on of the indicator lamp or aerial, fi"ers must be equipped
with with ladders, safety harnesses, protec!ve helmet, and all other equipment required by law and the standards governing this kind of work.
12 - TESTING AND TRIAL RUN
• The tes!ng and trial run must be performed by a COMPETENT PERSON supervised and aided by a PROFESSIONAL FinER.
It is the responsibility of the person who tests and sets up the automa!on (of which the control unit is a part) to perform the checks required in
accordance with the risks exis!ng and to check conformity with the relevant legisla!on and standards, in par!cular with EN standard 12445, which
governs the methods for performing trials on gate automa!ons and EN standard 12453 that specifies the performance requisites concerning safety
of use.
• The tes!ng and trial run are the most essen!al phases of installa!on for guaranteeing maximum opera!ng safety.
• The checks and procedures for tes!ng may also be used for rou!ne checks on the automa!on and its devices.
• The automa!on may only be tested if a non-hazardous force tolerance has been set. Force tolerance must be adjusted to a minimum value so as to
exclude the danger of injury during closure.
• Adjust the maximum force in line with EN standard 12445.
• Never touch the gate or moving parts when they are in mo!on.
• Remain at a safe distance when the gate is in mo!on: only pass when the gate is completely open and immobile.
• In the event of malfunc!ons (noisiness, jerky movements, etc.) suspend the use of the automa!on immediately: failure to observe this rule may
entail serious hazards, risks of accidents and/or serious damage to the gate and the automa!on .
• Always remember that the following residual risks exist when the gate is in movement:
a) impact and crushing against the main closure edge (against the single leaf or between the two leaves);
b) impact and crushing in the opening area;
c) cshearing between the moving and the fixed guides and support during movement;
d) mechanical risks caused by movement.
12.1 - Tes!ng
During tes!ng, ensure that the measurement of the gate's impact force has been performed in accordance with EN standards 12445 and 12453.
• Check that the indica!ons given in the SAFETY INSTRUCTIONS AND WARNINGS and INSTRUCTIONS AND INDICATIONS FOR INSTALLATION
chapters have been carefully observed.
• Ensure that the automa!on is correctly adjusted and that the protec!on and release systems are working correctly.
ATTENTION: once the automa!on has been tested, the parameters set must not be altered. If further adjustments (e.g. altera!ons to the voltage
value) are made, all the checks required for tes!ng and compliance with EN standard 12445 must be repeated.
Table of contents
Popular Engine manuals by other brands
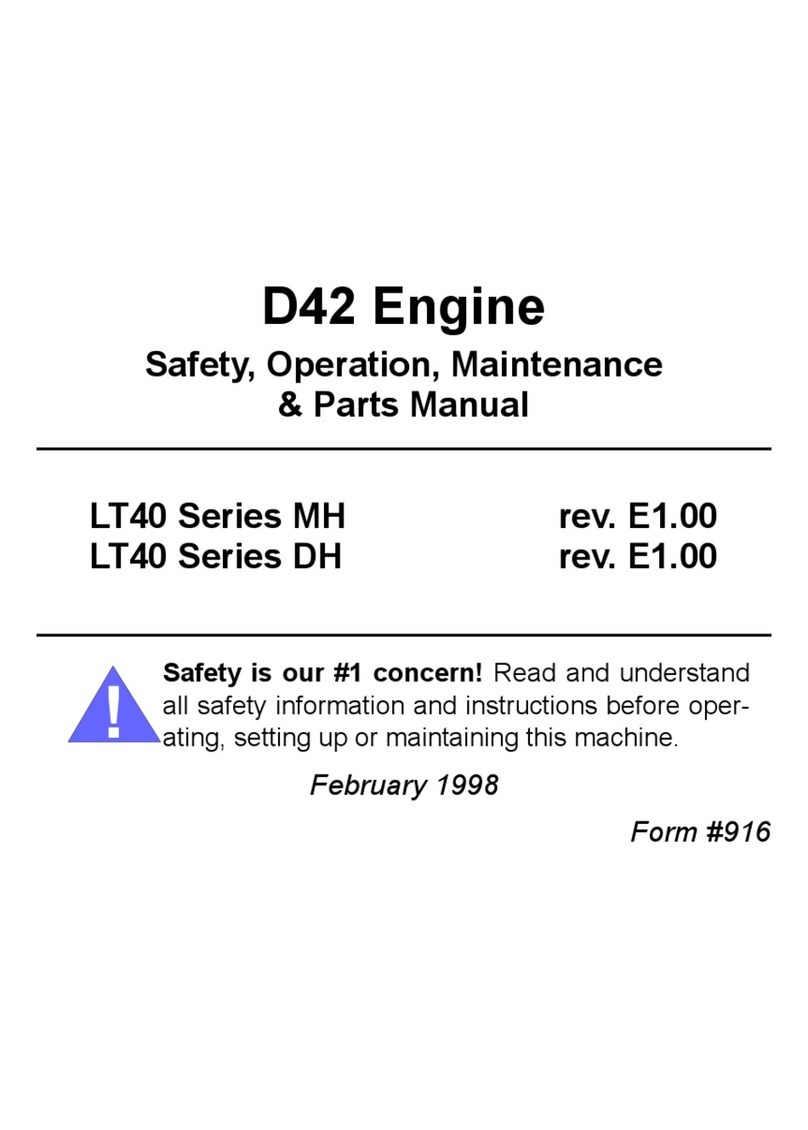
woodmizer
woodmizer D42 Safety, Operation, Maintenance & Parts Manual

AOK
AOK BASIC AM35 quick start guide

Oriental motor
Oriental motor PK Series operating manual
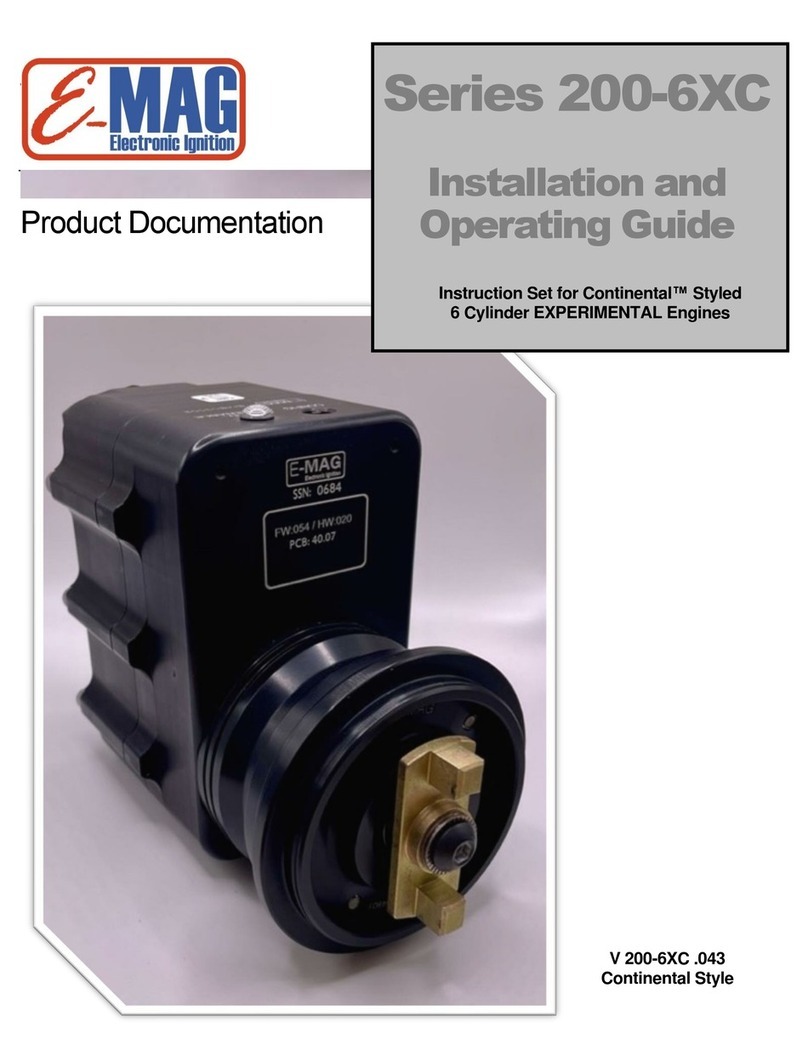
E-MAG
E-MAG 200-6XC Series Installation and operating guide

PRO-TEK
PRO-TEK Samurai 321B instruction manual
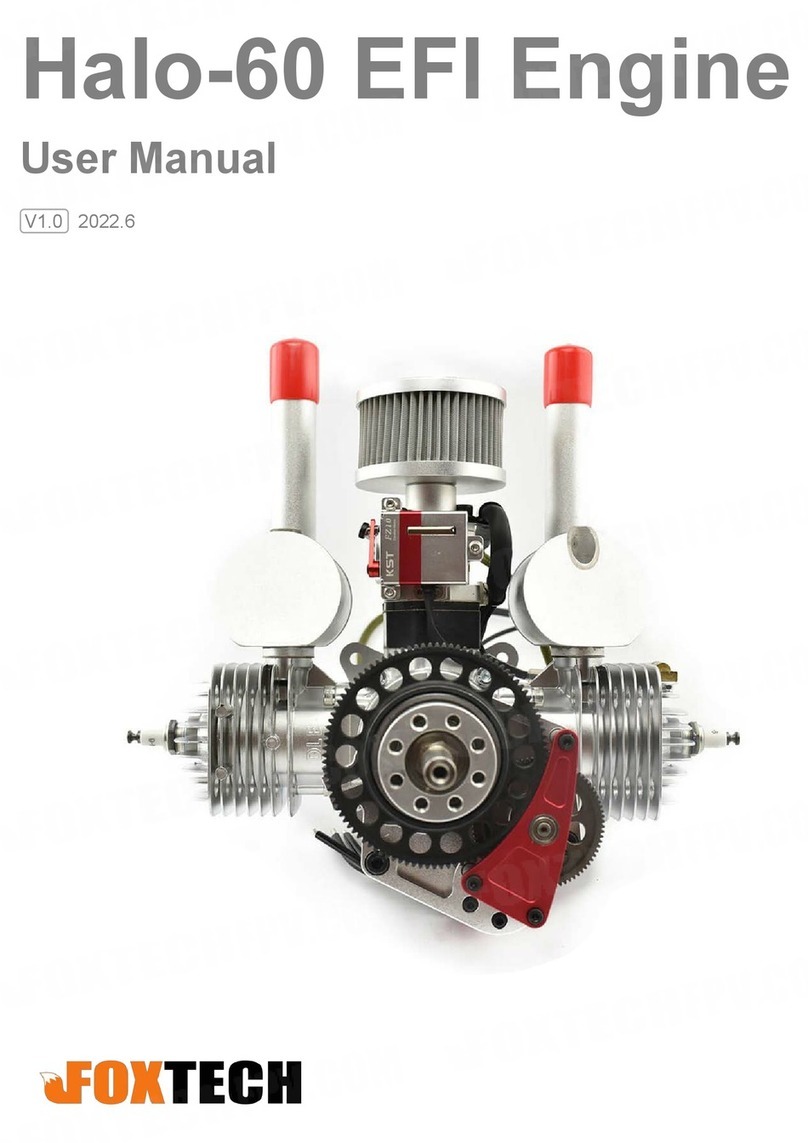
Foxtech
Foxtech Halo-60 EFI user manual