DIELEN VARIOMASS User manual

Instruction Manual
mass flow meter for compressed air
_______________________________________________
Druckluftbilanzierungssystem
VARIOMASS
VARIOMASS
7
8
0
.
1
2
3
4
5
6
9
MAX
MENU
ENTER
i
EXIT
DIELEN
K2
K1
VARIOMASS
MENU
ENTER
EXIT
DIELEN
MAX
i
K1
K2
7
8
0
.
1
2
3
4
5
6
9
C
Fault
Version: English V10/02

2
Table of Contents
page
0. Introduction ..................................................................................................................... 3
1. Technical Data's ............................................................................................................. 4
1.1 Transmitter ................................................................................................................ 4
1.2 Sensor ....................................................................................................................... 4
2. Mounting ......................................................................................................................... 6
2.1 Checking sensor probe length.................................................................................... 6
2.2 Installation of the sensor ............................................................................................ 7
2.3 Mounting for insertion meters .................................................................................... 9
2.4 Mounting for In-Line meters........................................................................................ 12
2.5 Installation of the transmitter ..................................................................................... 12
3. Electrical connection ...................................................................................................... 14
3.1 Transmitter in the DIN enclosure................................................................................ 14
3.2 Transmitter in the wall mounting enclosure................................................................ 16
3.3 Sensor ....................................................................................................................... 16
4. Power up the system....................................................................................................... 18
4.1 Key function ............................................................................................................... 18
4.2 Check preset value..................................................................................................... 19
4.3 Change preset value................................................................................................... 20
4.4 Options ...................................................................................................................... 24
4.5 Set maximum flow value record ................................................................................ 26
4.6 Reading maximum flow value ................................................................................... 27
5. Totalizer............................................................................................................................ 29
5.1 totalizer setup ............................................................................................................ 29
5.2 reading totalizer.......................................................................................................... 30
5.3 reading time................................................................................................................ 30
6. Data Logger...................................................................................................................... 31
6.1 Introduction ................................................................................................................ 31
6.2 Select time period of saving interval .......................................................................... 31
6.3 Programming Data logger ......................................................................................... 32
6.4 Check preset value of Data logger ............................................................................ 33
6.5 Read out Data logger ................................................................................................ 34
6.6 Technical Data ........................................................................................................... 37
6.7 Data Communication problem ................................................................................... 37
7. VARIOMASS model numbering system ....................................................................... 38
8. VARIOMASS meter with multiple sensor selection..................................................... 39

3
0. Introduction
This manual is for all VARIOMASS insertion thermal mass flow meter for standard pipe sizes from
62 mm (2 ½ ") up to 500 mm (20") and the In-Line thermal mass flow meter from ½“ up to 2“ pipe
sizes.
Unpacking your instrument:
- The insertion non linear mass flow meter has shaft mounted tube fitting which is bored through
and a connecting cable of 6 meter (optional up to 100 meter) length
process option: ball valve retractor assembly (BVR) with or without flange.
- The In-Line non linear mass flow meter has a standard flow body with the thread end
of NPT-M according the ordered pipe size from ½“ up to 2“.
Optional DIN or ANSI flanges are available in the desire sizes
- The remote flow transmitter which is designed for panel mounting (incl. mounting bracket for
screw driver) or mounted within a NEMA 4 wall mounting enclosure.
Please note that the serial number of the sensor (SN#) must be combined with the same serial
number of the transmitter (SN#)!
Please handle all parts with care.
The Password for the transmitter Menu is: 1 3 7 9
This manual is from the Software-Rev. No.: 2.8 and higher

4
1. Technical Data's:
1.1 Transmitter (Remote Electronic):
power supply: 230 VAC with 50 Hz./ 60 Hz.(optional 110 VAC or 24 VDC)
ambient temperature range: 0° to + 45°C
protection class: IP 54 for panel mounting
(Option: NEMA 4 (IP 65) with watertight field enclosure)
Display modus: - actual flow rate in Nm³/h, m³/min or L/min or SCFM optional with standard
(Norm) conditions of 20°C, 1 bar absolute and 0% relative humidity
- total flow (since installation) in m
3
or L (Liter) or SCF optional
- 2 flow totalizer (programmable and reset able)
- date / time
- flow range
- pipe diameter
- output signal (current)
Options: - RS 232 (V.24) interface
- RS 485 Bus interface incl. Software WINVAR for PCs
- Pulse output signal
- 2 Relay alarm contacts
- Data Logger with 4 MB memory
1.2. Sensor (flow meter)
The insertion flow meter are designed for flow ranges and pipe sizes listed in table 1.1
pipe size (mm) max. flow range: min. flow range: first value:
65
0 - 900 Nm³/h
0 - 90 Nm³/h
1 Nm³/h
80
0 - 1.400 Nm³/h
0 - 140 Nm³/h
2 Nm³/h
100
0 - 2.300 Nm³/h
0 - 230 Nm³/h
3 Nm³/h
125
0 - 3.500 Nm³/h
0 - 350 Nm³/h
4 Nm³/h
150
0 - 5.000 Nm³/h
0 - 500 Nm³/h
6 Nm³/h
200
0 - 9.000 Nm³/h
0 - 900 Nm³/h
11 Nm³/h
250
0 - 14.000 Nm³/h
0 - 1.400 Nm³/h
18 Nm³/h
300
0 - 20.000 Nm³/h
0 - 2.000 Nm³/h
25 Nm³/h
350
0 - 27.000 Nm³/h
0 - 2.700 Nm³/h
35 Nm³/h
400
0 - 36.000 Nm³/h
0 - 3.600 Nm³/h
45 Nm³/h
450
0 - 45.000 Nm³/h
0 - 4.500 Nm³/h
57 Nm³/h
500
0 - 55.000 Nm³/h
0 - 5.500 Nm³/h
71 Nm³/h
Table 1.1. flow range as a function of the pipe size
The In-Line flow meter are designed for flow ranges and pipe sizes listed in table 1.2
Model
No Pipe size:
inside pipe
diameter“dI":
flow body length
"L"
end pipe
thread "N"
max.
flow range
V-2 ½ " (12,7 mm)
15,8 mm
7" (178 mm)
½ " NPT
0 to
20 Nm³/h
V-3 ¾ " (19,0 mm)
20,9 mm
7" (178 mm)
¾" NPT
0 to
100 Nm³/h
V-4 1" (25,4 mm)
26,6 mm
8" (203 mm)
1" NPT
0 to
150 Nm³/h
V-5 1 ¼ " (31,8
mm)
35,0 mm
10" (254 mm)
1 ¼ " NPT
0 to
250 Nm³/h
V-6 1 ½ " (38,1
mm)
40,9 mm
15" (381 mm)
1 ½ " NPT
0 to
350 Nm³/h
V-7 2" (50,8 mm)
52,5 mm
20" (508 mm)
2" NPT
0 to
600 Nm³/h
Table 1.2. maximum flow ranges as a function of the pipe size

5
process temperature: normal : 0°C up to 70°C max.: 150°C for ceramic or 200°C for SS sensor
ambient temperature: - 10°C up to + 50°C
process pressure: 4 to 12 bar g (other on request)
gas media: pressured air (optional other gases)
Sensor material: Stainless Steel (316 SS) or optional ceramic
process connection: Insertion meters: tube fitting R ½ " or optional flange
In-Line meters: NPT thread or optional flange
accuracy: 2% of reading with optimum up- and downstream area
sensor response time: a) Stainless steel: τ63 about 1 second
b) Ceramic: τ63 about 0,1 second

6
2. Mounting
2.1 Checking sensor probe length
2.1.1 Insertion meters
The probe length of the shaft "L" is adequate to the inside diameter of the pipe.
L
d
O 90 mm
65
73
Sensor window
probe shaft
UP
Abb. 1a) insertion flow meter with stainless steel sensor
The probe shaft length "L" is 12“ (305 mm) or 16" (406 mm) depending on the pipe sizes diameter
from 62 mm up to 500 mm.
The probe shaft diameter "d" is ½ " (12,7 mm) with a sensor window at the end (s. Abb. 1a).
By using the BVR (Ball valve retractor assembly) option the max. pipe size for the 16“ sensor shaft
length is 305 mm (12“) and for the 12“ sensor shaft length 102 mm (4“).
2.1.2 In-Line Meters
The flow body length "L" for the IN-LINE Meters depends on the ordered pipe size (s. Abb.1b). The
pipe sizes are from ½" up to 2" (s. table 1.2).

7
L
di
O 90 mm
73
thread size N
Abb. 1b) dimensions of the In-Line Meters
2.2 Installation of the sensor
Proper installation of the flow section assembly is of great importance. It is important to install the
flow meter at a position where the gas is dry or above the dew point temperature.
A minimum of 10 x diameter up- and 5 x diameter downstream area without any equipment which
disturb the flow profile are necessary.
The total straight flow section of the pipe should be divided into 2/3 as up- and 1/3 as downstream
area (s. Abb. 2).

8
flow section
2/3 flow section
1/3 flow section
FLOW
cable gland
senor enclosure
D
min. 10 x D
min. 5 x D
Abb. 2a) Insertion meter: straight flow section with two 90°-elbows
total flow section
2/3 flow section 1/3 flow section
FLOW direction
In-Line meter with flanges
FLOW
D
10 x D 5 x D
UPSTREAM
Abb. 2b) In-Line Meter: flow area with two 90°-ellbows
The pipe installation can be horizontal or vertical without any effect of the accuracy of the flow
meter.
Note:
For In-Line meters with a flow conditioner you only need 2 x D Upstream and 1 x D Downstream
area. For different pipe sizes than the flow meter or flexible horse on the inlet side of the flow meter
use 3 x d up and 2 x d downstream area.

9
2.3 Mounting for Insertion Meters
2.3.1 Process connection
The process connection should be a welding socket with ½ " inside thread or optional a counter
flange. The welding process connection should be in a right angle to the pipe and should match the
center of the pipe (s. Abb. 3).
di
M
welding socket R 1/2"
middle line
M = app. 20 to 60 mm
Abb. 3a) process connection with welding socket
As an option we supply the fitting with a flange (DIN or ANSI) which is customer sized.
di
counter flange
welding socket
pipe
Abb. 3b) process connection with counter flange

10
2.3.2 tube fitting
The standard process connection for the insertion flowmeter is a shaft mounted tube fitting
"SWAGELOK " which is bored through. This fitting can be combined with a flange (DIN or ANSI)
with a thread for R 1/2" for the process connection. Use Teflon band to fix the SWAGELOK fitting
with the pipe welding socket.
This SWAGELOK fitting has two Teflon ferrules (front and back) which allows to retract the probe
shaft without any deformation on the stainless steel shaft. For low pressure the nut can be hand
tight and for higher pressure turn the nut additional 1 1/2 round clockwise.
Use an „Inbus“ screw driver on the external adjustment for proper tight (s. Abb. 4).
Inbus screw
R 1/2" thread
Abb. 4) tube fitting Swagelok
2.3.3 flow direction specification
The window of the sensor has to be open in the flow direction. The UPSTRAM mark on the probe
shaft must be located correctly. It faces the direction of the flow. The additional arrow mark on the
sticker of the sensor enclosure defines the correct flow direction ("Durchflußrichtung" means Flow
Direction). The normal flow direction is from right to left looking from behind of the sensor enclosure
(s. Abb. 5) and the cable gland is in an angle of 90° to the flow direction.
UPSTREAM
probe shaft RTD
Sensor
sensor window flow direction
UP
UP STREAM mark
Abb. 5) UPSTREAM mark on the sensor probe
2.3.4 Position of flow
The middle of the sensor window has to be install to the point of the maximum flow velocity. The
point of maximum velocity should be in the center of the pipe when using the necessary up- and
downstream area (s. Abb. 6).

11
b = 33 mm
b/2
welding couple
60 mm
with 1/2" thread
Sensor probe length "L"
20 mm Di/2 "A"
Sensor enclosure
Swagelok-bored through
fitting
PG cable cland
Abb. 6a) Insertion Sensor with standard Swagelok fitting
20 mm
welded 1/2" couple
170 mm
Di/2 A
ball valve
Abb. 6b) Insertion Sensor with BVR (ball valve retractor assembly)
Die minimum probe length (L
min
) for Option K (BVR) is (s. Abb. 6b):
Lmin = 20 mm + Di / 2 + A + 170 mm
The middle position for the sensor window is as easy to find:
Please insert the probe shaft to the other side of the pipe and retract it for the length:
D
i
/2 - 20 mm
Example:
The pipe inside diameter (D
i
) is 100 mm and the probe shaft was inserted up to the other side of the
pipe, so the middle position for the sensor window you have to retract the probe for 30 mm (100/2
mm - 20 mm).

12
2.4. Mounting for In-Line Meters
The standard process connection for the In-Line Meters is NPT - M thread and the thread size is
depending on the pipe size of the flow body.
Note:
The necessary upstream area is 10 x D (Diameter) and the downstream area is 5 x D (Diameter)
with from the beginning and end of the flow body. No elbow or reduction are allowed within the flow
section area.
As an Option DIN or ANSI-flanges are available.
The flow direction (example from left to right or right to left) on the flow body (see the arrow) must
be the same as the flow direction of the gas (s. Abb. 7).
L
thread N
FLOW
IN
OUT
Abb. 7) In-Line Sensor with NPT thread
2.5 Installation of the transmitter
The transmitter of the VARIOMASS can be a DIN enclosure for panel mounting or a wall mounting
enclosure with the protection class IP 65 (NEMA 4).
2.5.1 Installation of the DIN enclosure
The transmitter electronic of the flow meter is in a DIN rack enclosure for panel mounting with the
outline dimensions of 96 mm x 96 mm x 140 mm (s. Abb. 8).

13
137
ca. 150 mm
91,5
VARIOMASS
7 8
0
.
12 3
456
9
MAX
MENU
ENTER
i
EXIT
DIELEN
96
96
K2
K1
Abb. 8a) dimensions of the DIN transmitter enclosure
The panel cutout should be 92 mm x 92 mm. Use a crew driver for the installation of the mounting
bracket to fix the enclosure with the panel.
2.5.2 Installation of the wall mounting enclosure
This optional wall mounting enclosure has the protection class NEMA 4 (IP 65) (s. Abb. 8b).
Use the 4 mounting wholes on the bracket to fix the enclosure with the wall.
VARIOMASS
MENU
ENTER EXIT
DIELEN
MAX
i
K1
K2
78
0
.
123
456
9
C
Fault
cable conjunction box
screw
cable gland
Abb 8b) wall mounting enclosure

14
3. Electrical connection
3.1 Transmitter in the DIN enclosure
Please keep the electronic dry and clean and install all wiring without power supply.
The ambient temperature of the electronic should not go above 45°C.
3.1.1 Power supply
On the back side of the electronic are the terminal blocks for input and output signals (s. Abb. 9).
The power supply for the remote transmitter electronic is 230 VAC / 50 Hz. (220 VAC and 60 Hz. is
also possible) or optional 110 VAC or 24 VDC with a maximum current of 1 Ampere. Only the
terminal description "L1" and "N" is for the power supply and the "PE" is the power supply ground
(Earth). See a special note (sticker) on the back side of the electronic for other power supply than
230 VAC. Only for the 24 VDC version "L1" is for + 24 VDC and "N" is Ground (minus) and "PE" is
the "Earth" connector.
3.1.2. Sensor cable
The interconnecting cable between the sensor and the transmitter is a 4 wire conductor overall
shield cable (AWG 18) and must be connected to the terminal block with the 5 PINS called
"SENSOR".
PIN description for the sensor cable:
PIN# 1: (P) 24 VDC power supply (+) output for the sensor
PIN# 2: (I) non linear mA signal input (+)
PIN# 3: (R) (Return) ground power supply (-) for the sensor
PIN# 4: (G) ground input sensor signal (-)
PIN# 5: (PE) shield of the sensor cable
RS 232 RS 485
L1 PE NNC NO CNC NOC
P I R G PE
+ - + -
+ -
EXT+ 24V
Analog Outputs
IU
power supply Relay contacts
puls
Sensor cable
K1 K2
Abb. 9) back side of the transmitter layout
3.1.3 Analog output
The linear analog output (voltage & current) of the transmitter is on the 8-PIN terminal block with the
following description:
PIN# 5 (+I) current output 0/4 to 20 mA Plus (+)
PIN# 6 (-I) current output ground Minus (-)
PIN# 7 (+U) voltage output 0 to 10 VDC Plus (+)
PIN# 8 (-U) voltage output (Ground) Minus (-)

15
3.1.4 Serial output RS 232 (Option)
On the 9 pin sub D connector with the male connector you find the messages RS232 on the back
side of the transmitter.
Signal PIN-No. Description
RXD 2 Receive Data
TXD 3 Transmit Data
CTS 8 Clear To Send
DTR 4 Date Terminal Ready
GND 5 Ground
1
2
3
4
5
6
7
8
9
GND
DTR
CTS
RXD
TXD
Abb. 10) RS 232 as a 9 PIN Sub-D-connector
For a matrix printer we have tested the following configuration:
Baud rate No. 1: 9600 baud
Bit muster No. 2: 8 Data and 1 Stop bit
Data protocol No. 1: No Handshake (No Parity)
print every 10 Seconds
We have use the following cable configuration for a Matrix printer (EPSON):
transmitter (VARIOMASS): TXD GND CTS
PIN 9 connector: 3 5 8
I I I
receiver printer (EPSON) RXD GND DTR
PIN 25 connector: 3 7 20
Note:
For you printer cable configuration see your printer manual section serial input port
For a PC with a Terminal program we use the following cable configuration:
transmitter (VARIOMASS): RXD TXD GND CTS
PIN 9 connector: 2 3 5 8
I I I I
receiver (PC) at COM 1 TXD RXD GND DTR
PIN 9 connector: 3 2 5 4

16
3.2 Transmitter in the wall mounting enclosure
When you open the conjunction box of the wall mounting enclosure with a screw driver you find
the following terminal strip:
1234567
Sensor cable
8 9
Analog output
+ U - U + I - I
10
P I R G PE
11 12 13 14 15
Puls output
- + Ext 24V
16 17 18 19 20
RS 232
RT CT 0 V TX RX
21
RS 485
GND B A
22 23 24
K1
NO NC C
25 26 27
K2
NO NC C
28 29 30
Fault
NC NO C
31 32 33
power supply
L1 N PE
Jumper for
puls output
RS 232 RS 485
power supply
fuse
24 V
12 V
5 V
EXT.
Relay contacts
Abb. 11) Terminal strip of the wall mounting enclosure
On the terminal strip with the name "L1" and "N" connect the power supply of 230 VAC (or
optional 110 VAC or 24 VDC) and on pin "PE" the ground of the power supply. The sensor
connecting cable has a plug in connector which has to be turn clockwise until it is tighten.
The Analog output (voltage and current) are on pin # 6 to # 9 as follows:
PIN # 6 (+ V) voltages 0 to 10 VDC Plus
PIN # 7 (- V) voltages ground Minus
PIN # 8 (+ I) current 0/4 to 20 mA Plus
PIN # 8 (- I) current ground Minus
The options as Serial Port (RS 232), Relay output or RS 485 BUS are on PIN 5 to 20, see
separate wire diagram paper in your terminal strip box of the enclosure.
3.3 Sensor
The sensor gets it power supply (24 VDC) from the transmitter and sends the non linear voltages
output to the transmitter. The transmitter laniaries the non linear sensor signal.
Therefore use only the 4 color conductor PVC cable (AWG 18) overall shield which comes with the
sensor. It is not necessary to open the sensor enclosure because the interconnecting cable is
already fixed on the circuit board.
The sensor enclosure has the protection class IP 65 (NEMA 4) and is design for ambient
temperature - 10°C up to +50°C. Inside the sensor enclosure you find the circuit board with the
terminal block TB1 (s. Abb. 12). Do not disconnect the inner cable on TB2 which takes the signal
from the RTD`s. We use the following PIN on the sensor side and connect it with the transmitter
side:
Terminal block TB1 inside sensor: Terminal block transmitter:
PIN# 1: (P) + 24 VDC power supply input →PIN# 1 (P)
PIN# 2: (R) ground (-) power supply input →PIN# 3 (R)
PIN# 3: (I) (+) non linear signal output →PIN# 2 (I)
PIN# 4: (G) (-) ground output →PIN# 4 (G)
PIN# 5: (V) not used
PIN# 6: (G) not used

17
G T G F
O O O O
4 3 2 1
O O O O O O
1 2 3 4 5 6
P R I G V G
TB 2
TB 1
o o o o
(500 Ohm) (50 Ohm)
+ 24 VDC (P)
Return (R) + 0 ... 20 mA non linear (I)
(0 ... 20 mA Signal) Ground (G)
Power Supply signal output:
J1
passive RTD
active RTD
Sensor elements
green
yellow brown
white
Abb. 12) Sensor circuit board layout

18
4. Power up the system
Before power up the system be sure that all wiring is correct. Please check the power supply (230
VAC or optional 110 VAC or 24 VDC) is only on the PIN called "L1" & "N" on the terminal block.
Important note:
If you find no sticker on the transmitter enclosure with the optional power supply of 110 VAC or 24
VDC than the standard power supply of 230 VAC is necessary. If you have a 24 VDC version do not
apply a power supply of 110 VAC or 230 VDC.
After power up the system the following message should be read on the LCD Display:
V A R I O M A S S R
e v 2 . X
T e s t a c t i v e . . .
This means that the system is doing a Hardware- and Software testing for about 30 seconds
after that the following message is only for a second to read:
T e s t O . K . !
After this the systems goes automatically into the standard readout of the flow rate:
f l o w r a t e
0 m 3 / h
Now the system has to be configured.
4.1 key function
09
. .
for input numbers from 0 to 9
"up" key for the behind value/level
"down" key for the next value/level []
time key
i
Information key (Information modus) or select key
EXIT
EXIT key for leaving the program or Information modus
ENTER
Enter key for setting O.K. (YES) in the program (MENU)
Sum key for all totalizer values and for the data logger program

19
MENU
Menu key starts the program level
MAX
Maximum key for maximum flow values
Note:
After pressing a key the system went into the standard readout (flow rate) after 30 seconds
without pressing any further key (except in the program - MENU). With the [EXIT] key you will go
into the standard readout (flow rate) at any time. After programming do not disconnect the power
supply for at least 5 minutes to store all changes in the EPROM.
4.2 Check preset value
The actual time will be displayed by pressing the key:
t i m e
h h : m m
d a t e D D . M M . Y Y
Press [EXIT] key to go to the standard readout.
Press the
i
key for reading all preset value:
f l o w r a n g e
0 t o X X X X m 3 / h
next press the arrow down key [] to reach the next step
z e r o s h i f t u p
t o :
0 m 3 / h
next press [] key
p i p e d i a m e t e r
X X
X . X m m
next press [] key
o u t p u t s i g n a l
0 m A t o 2 0 m A
next press [] key
T a g N o .
0
next press [] key

20
S e r i a l N o .
X X X X X X X X
The shown Serial Number (SN) must be the same as the SN of the sensor. With the [EXIT] key
you can leave the Information level or automatically after 30 seconds..
4.3 Change preset value
Press the [MENU] key to go to the program level
The following information will be on the display:
e n t e r c o d e a n d
E N T E R
Please enter the code (Password): [1] [3] [7] [9] and than press the [ENTER] key
For pressing [ENTER] again you will go into the main program level
or Press [EXIT] for leaving the main program level
4.3.1 Date/time
In the main program level you can set the new time and/or date:
s e t d a t e a n d
t i m e ?
For: YES - press [ENTER] or press arrow up key [▲] for changing the menu language:
4.3.1.1) Language selection
L a n g u a g e
s e l e c t ?
or alternative if you have a German menu language:
S p r a c h e
a u s w a e h l e n ?
Press the [ENTER] to change the language
D e u t s c h
You will read "Deutsch" for German language or
Table of contents
Popular Measuring Instrument manuals by other brands
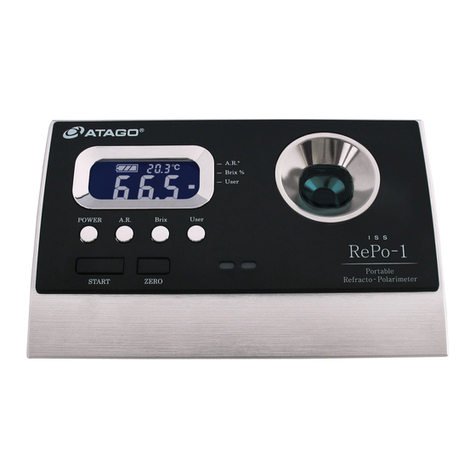
ATAGO
ATAGO RePo-1 instruction manual
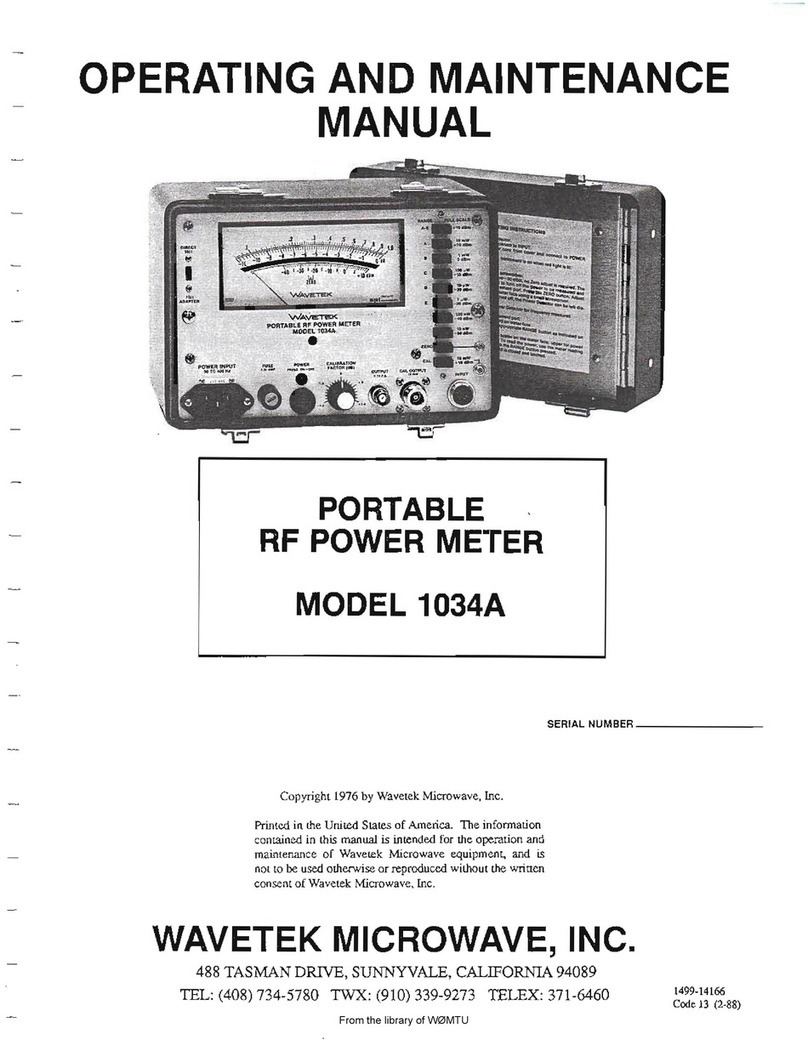
Wavetek
Wavetek 1034A Operating and maintenance manual
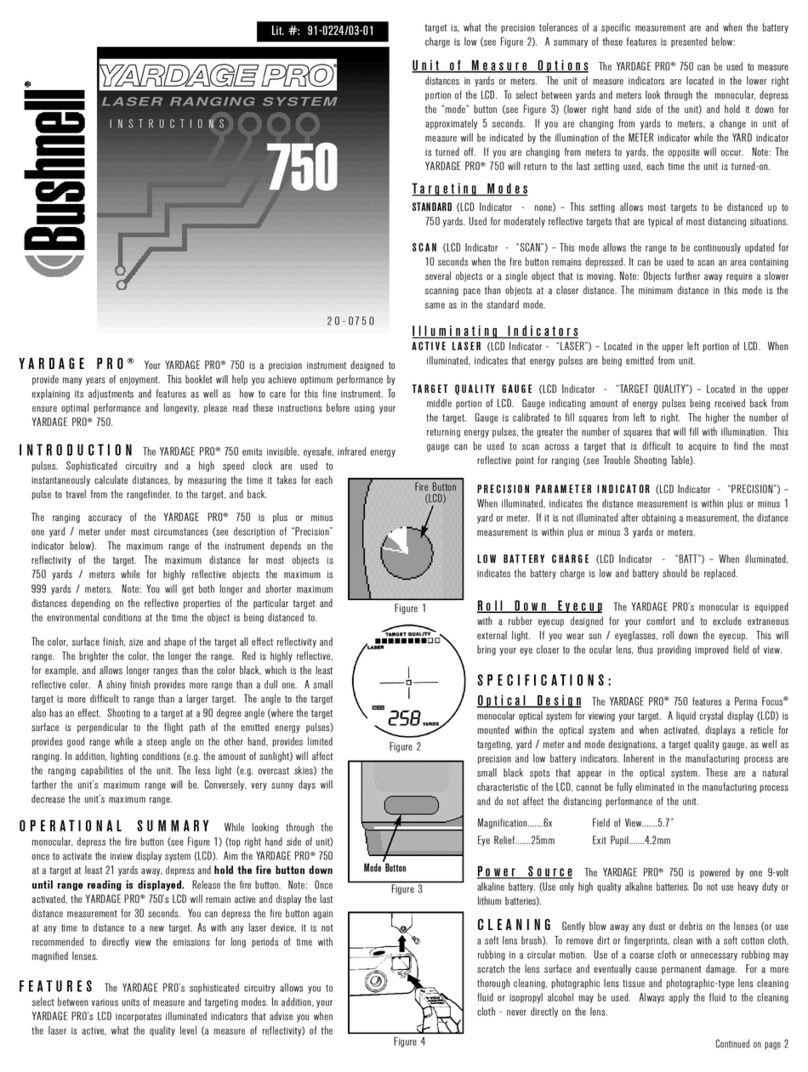
Bushnell
Bushnell Yardage Pro 20-0750 user guide
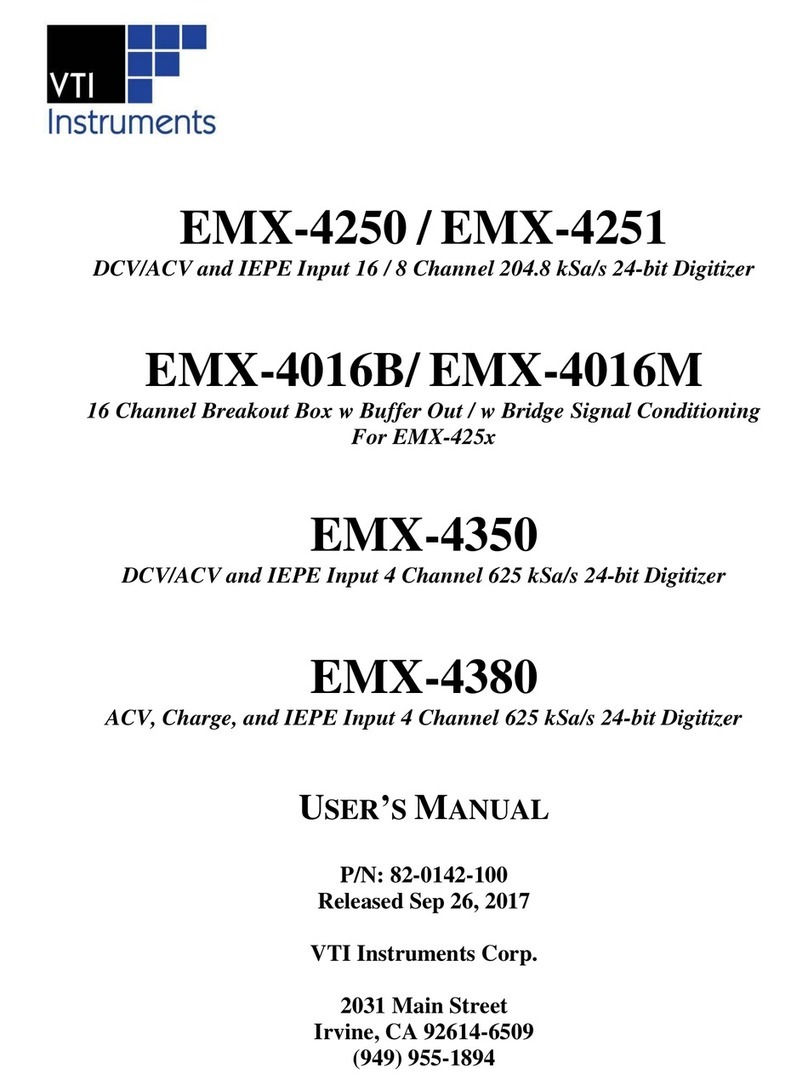
VTI Instruments
VTI Instruments EMX-4250 user manual
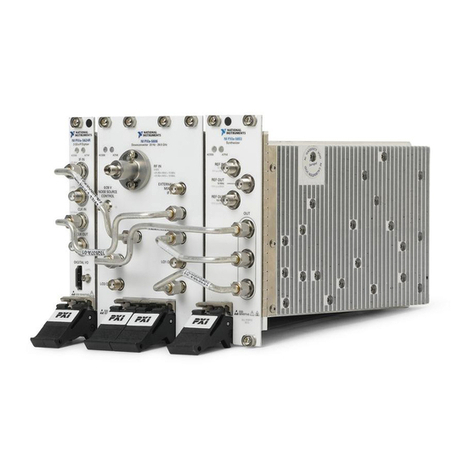
National Instruments
National Instruments PXIe-5668 Getting started guide
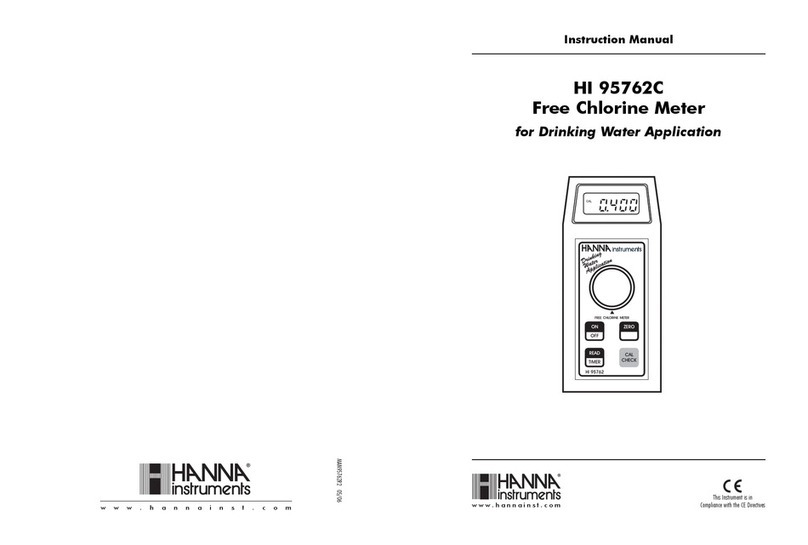
Hanna Instruments
Hanna Instruments HI 95762C instruction manual
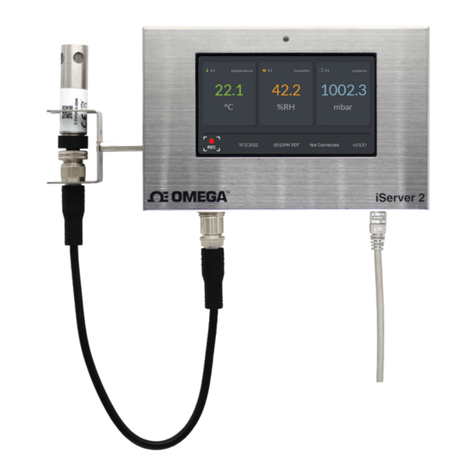
Omega
Omega iServer 2 Series user guide
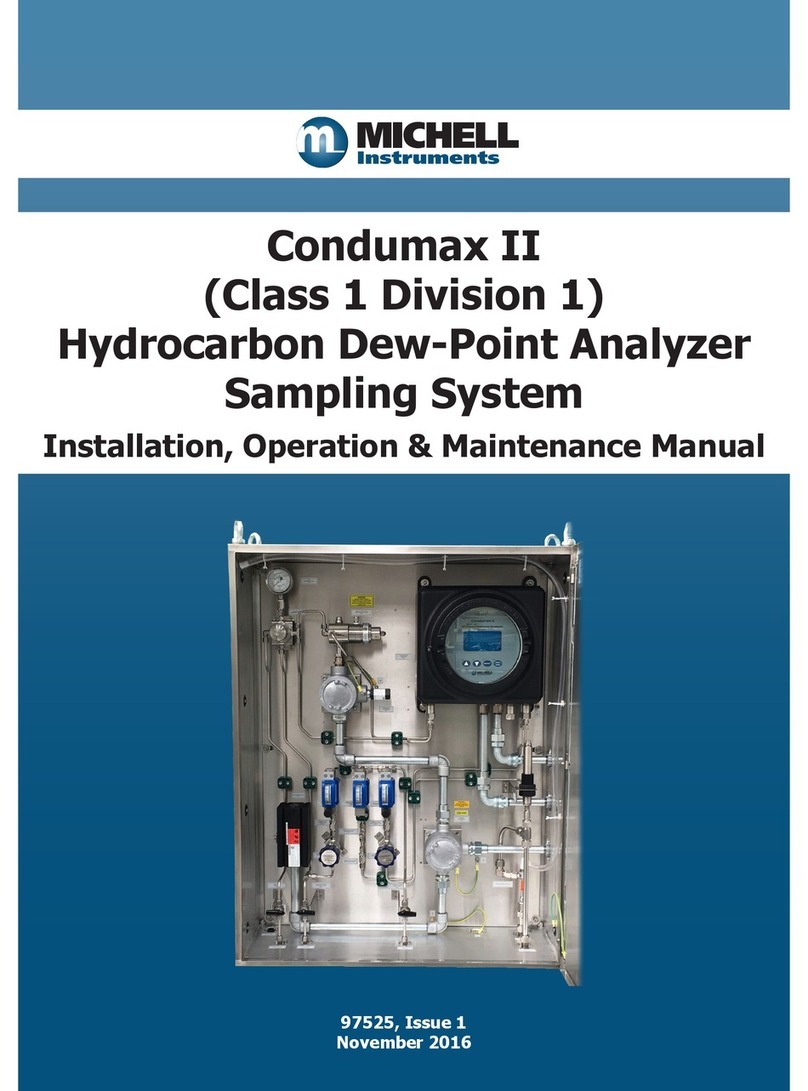
Michell Instruments
Michell Instruments Condumax II Installation operation & maintenance
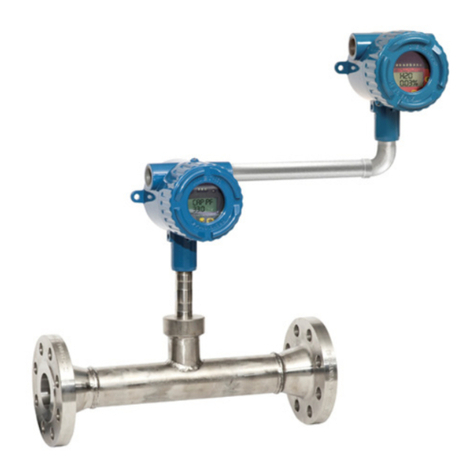
Ametek
Ametek Drexelbrook Universal IV CM Installation and operating instructions
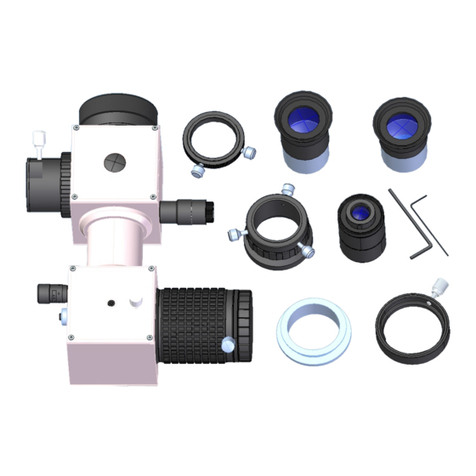
Baader Planetarium
Baader Planetarium MPE DADOS user manual
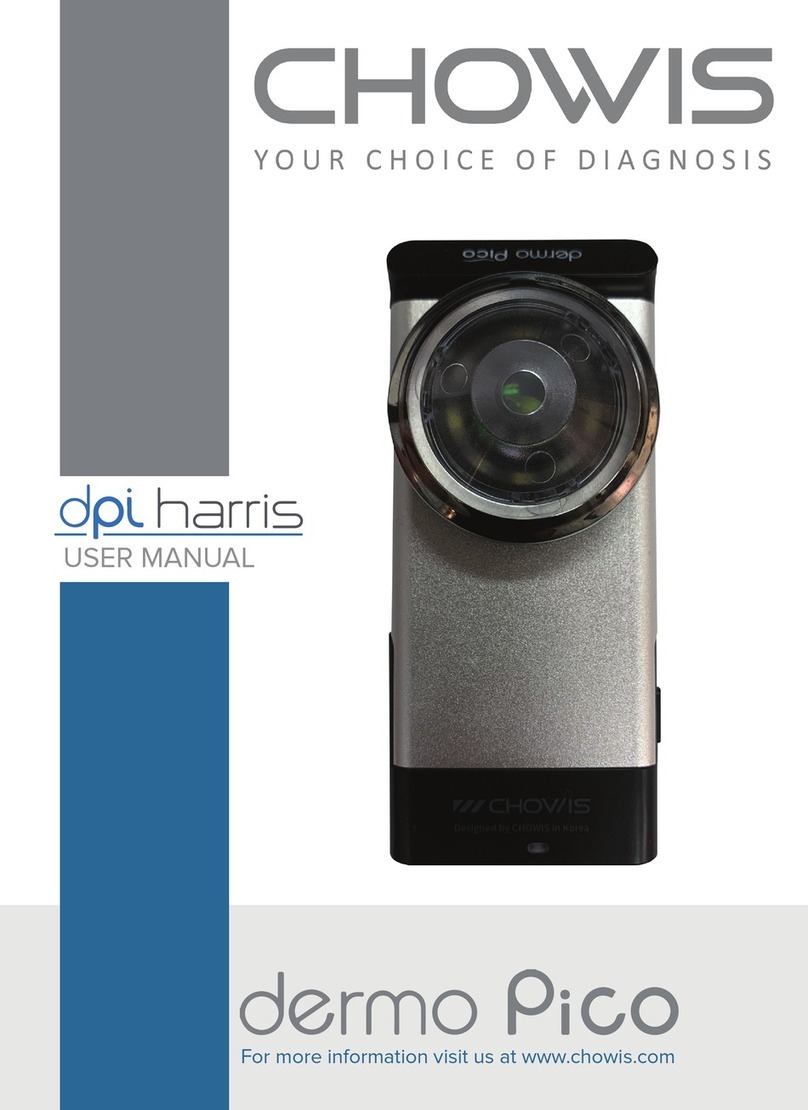
CHOWIS
CHOWIS dpi harris user manual
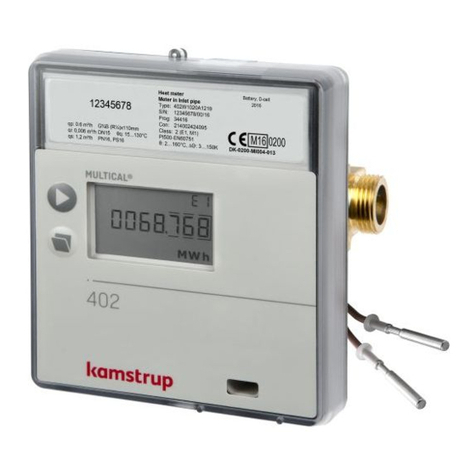
Kamstrup
Kamstrup MULTICAL 402 Installation and user guide