DIVERSITECH WB-4000-D Manual

Operation & Maintenance Manual
WB-4000-D
Visit our Website formore information on this product
www.diversitech.ca
1200 55th Avenue,Montreal, Quebec H8T 3J8
Tel: 1.800.361.3733 | Fax: 1.514.631.9480 | i[email protected]

1
CARTRIDGE DUST COLLECTOR
Weld Booth Model WB-4000D
IMPORTANT READ THIS MANUAL BEFORE INSTALLATION,
OPERATION OR SERVICE.
By nature and variety of dusts, it is impossible to list all potential hazards
related to dust control equipment or systems. Therefore, it is imperative that
the application and use of this equipment be discussed with an DIVERSITECH
distributor, and that this manual is read in its entirety and all personnel
involved with this equipment are instructed to comply with the statements
pertaining to safety.
•INSTALLATION
•OPERATION
•SERVICE

2
Table of Contents
PRECAUTIONARY STATEMENTS 3
INTRODUCTION 3
HOOD AND DUCT DESIGN 3
EXPLANATION OF OPERATION 3
INITIAL INSTALLATION CONSIDERATIONS 4
INSPECTION 4
MECHANICAL INSTALLATION 4
COMPRESSED AIR SUPPLY 5
ELECTRICAL/CONTROLS 5
PRE-START UP 7
FILTER INSTALLATION 7
START UP 7
SHUT DOWN 8
MAINTENANCE SAFETY 8
MAINTENANCE PROCEDURES 9
CARTRIDGE FILTER REPLACEMENT 10
TROUBLE SHOOTING CHART 11
WARRANTY STATEMENT 13
PARTIAL PARTS LIST 14

3
PRECAUTIONARY STATEMENTS
APPLICATION OF DIVERSITECH CARTRIDGE DUST COLLECTORS
1. Due to potential fire hazards, do not mix combustible materials with material that would be
a potential source of ignition.
Examples of Combustible Materials:
Wood Dust
Paper Dust
Lint from fabric or buffing wheels
Grinding dust from painted surfaces
Aluminum or magnesium dusts
Examples of Potential Ignition Sources
Grinding dust from ferrous metals
Hot ash or sparks from any source
2. Unless the equipment was originally designed for collection of explosive material and proper
disclaimer on record this equipment must not be used for the collection of any materials where
there is a risk of explosion. Pressure relief vents or explosion vents must not be applied to the
equipment or adjoining systems.
3. Equipment location, installation and operation must comply with all National and Local Fire
Codes. When in doubt contact the proper authorities.
4. The electrical installation must conform to all local codes and the National Electric Code.
5. Workers and operators are to be instructed to keep burning objects, such as cigarettes,
safely away from inlets leading to the equipment.
6. All personnel involved with the use of this equipment must comply with the statements
pertaining to worker safety as noted in this manual.
Introduction
DIVERSITECH Weld Booth Dust Collectors are designed to filter out solid particulate and dusts
such as Weld fume and grinding dust. The cleaned air is then returned to the work space to
eliminate the need to exhaust treated air. Once the unit is mounted, connection of electrical
power and compressed air complete the installation.
Note: If the unit has the optional fire suppression system please refer to the Fire Trace
Manual and Smoke Detector manual for maintenance information.
Explanation of Operation
During normal operation, contaminated air is pulled through the top section of the cartridge
collector cabinet. The cabinet design distributes the contaminated air uniformly across the
vertically arranged filter cartridges. A portion of the dust will collect on the surface of the
cartridge media as the dust free air passes through the media, through the vertical venturi,
into the horizontal clean air duct and to the blower for return to the work space. The dust that
collects on the cartridge media will be repelled into the downward air flow by the reverse jet
pulse cleaning system. This is controlled by a digital pulse control. At prescribed times a brief
burst of compressed air will be released to a row of cartridge filters, fired upwards through the
vertical venturi, into the core of the cartridge filter to impact the dust away from the filters
surface. The dust is caught by the downward flow and once again moved towards the settling
chamber. The dust drawer of the DIVERSITECH Collector contains no airflow inlets or outlets. In
fact, airflow is never close to the dust drawer. This eliminates the possibility of re-entrainment
of the dust once it gets into this section of the dust collector cabinet.

4
Initial Installation Considerations
The location of the unit(s) must be planned to maximize effective operation, service and
maintenance. Should questions arise or assistance is needed consult your DIVERSITECH
distributor.
After the installation, clearance must be available to service the following components:
1. Filters
2. Fan
3.Valves
4. Controls
5.Dustdrawer
Inspection
Upon receipt, the collector and the optional components must be checked for damage or loss
incurred during shipping. Damage must be noted on the bill of laden and a claim be filed with
the carrier immediately.
Mechanical Installation of Weld Booth WD-4000D
Note:
Should question arise concerning totalweight, consult your DIVERSITECH
Distributor or theDIVERSITECH Factory.
1. Unbolt and remove the master booth from skid. (Master booth is the one with the dust
collector on the top)
2. Rig and lift the master booth up and move it to the desired final position and anchor it
to the floor.
3. Unbolt and remove the slave booth from the skid. NOTE: THE SLAVE BOOTH CAN BE
INSTALLED TO LEFT, RIGHT OR REAR OF THE MASTER BOOTH.
4. Determine the desired location for the slave booth. Remove and RETAIN the access
cover from the desired side of the master booth. The slave booth ships with only a
cover on the back. (If the slave is to be positioned back to back with the master,
remove and RETAIN the back cover.)
5. On the inside of each booth there is a hinged door allowing access to the spark filters.
Open the hinged door and remove the spark filters in order to gain access to the nuts
and bolts holding the covers and to facilitate connection of the booths.
6. Set the slave booth in desired place and bolt both booths together using the holes
available.
7. Anchor the slave booth to the floor.
8. Install covers retained in earlier steps on all remaining openings on both booths.
9. Reinstall spark filters and secure hinged door.
10. Feed one light power supply cable through the hole provided in the top of the slave
booth and connect the power cable to the light.
11. Connect compressed air and electrical per Installation Manual.
Compressed Air Supply
The compressed air supply is used to reverse jet pulse the dust coated cartridge filters. A 1”
diameter (minimum) dedicated supply with 80-90 PSI is required. The air supply line to the
accumulator tank must include water, oil and particulate filtration. Water and/or oil in the
compressed air will reduce the effectiveness of the reverse jet pulse cleaning, destroy the

5
cartridge filters and cause excessive differential pressure across the filters resulting in greatly
reduced air flow along with premature filter replacement.
Note:
The air line must be free of oil and water. Oil and/or water will destroy
cartridge filters.
A customer supplied regulator with a 160 PSI gage must be installed to monitor air pressure.
Prior to the final connection of the air line to the collector manifold, the air line should be
purged. This will remove debris that could damage the valves and block the nozzles in the blow
pipes.
Electrical / Controls
Note:
All of the electrical installation must be performed by a qualified electrician
and in accordance with the local codes.
The blower motor operates with 208-230/460 volt, 60 cycle, and 3 phase electrical power
unless specified otherwise with the equipment order. Electrical power is connected to the
Motor Starter Control Box Located on the front of the collector. Inside the Motor Starter is a
decal that confirms the voltage the motor was set up for at the factory. Should this need to be
changed to the other voltage listed above, the motor will have to be rewired in accordance to
the data label on the motor. Access the motor from the blower door of the collector.
The blower motor will need to be energized through a motor starter with over load protection.
The electrical components must be sized and selected in accordance to the national electric
code.
Nominal Full Load Amperes are as follows:
Voltage
Horse Power 208V 230V 460V 575V
310.08.0 4.0 3.5
515.00 13.0 6.5 5.0
7.5 20.0 18.0 9.0 7.0
10 30.0 24.0 12.0 10.0
15 40.0 37.0 18.5 15.0
20 55.0 48.0 24.0 20.0
The blower is designed to rotate clock wise when viewed from the motor side. If the blower is
running in reverse, the air volume will be approximately 1/2 the designed air volume. Also,
excessive noise will be generated. Once the motor is wired, energize the blower motor for a
brief instant (“JOG”). Check the rotation and if it is in reverse, switch any two input wires of
the 3 phases, (T1, T2, and T3).
When the reverse jet pulse cleaning system is initiated, a digital pulse control timer controls
the air solenoid valves, releasing a brief burst of compressed air backwards through the filters
to expel the collected dust off the filter cartridges and down towards the settling area.
The sequential timer can be activated by monitoring differential pressure across the filters and
energizing the timer at a predetermined set point. The timer will continue the reverse jet
pulse cleaning until differential pressure is reduced to a predetermined pressure.
Note:

6
A manual that details the operation of the pulse control is available under
separate cover.
Pre-Start Up
Turn the fan “ON” for a brief instant (JOG) and check rotation. Rotation must be clockwise
when viewed “OVER THE MOTOR” from the discharge side. If the rotation is correct start
motor.
Check to assure that air leaks do not exist at the seams of any field assembled cabinet
components such as Duct connections or the booth connections
Check the compressed air system for leaks. Confirm 80 PSI minimum air pressure and 90
maximum air pressure.
Assure the compression couplings of the pulse valves are tight.
Check each valve to assure each valve pulses as required.
Check each valve for leaks. It is normal for the bleed air port to release a burst of air at each
pulse.
Check adequacy of air supply by assuring no less than 40% drop in pressure during pulse.
Filter Installation
Should the filter be shipped loose from the collector they must be installed as follows prior to
start up?
Be sure the horizontal flange around the venturi is clean. With care not to damage filter
cartridge place gasket side down on flange. Rotate filter slightly to assure no binding and
proper location on the flange.
Most DIVERSITECH dust collectors use two filters, stacked vertically on each venturi. Position
second filter directly on top of first filter, gasket side down and centered vertically with lower
filter.
Place filter cap with gasket side down on top of the top filter cartridge and centered on
opening. Turn “T” handle, clockwise, down against filter cap so that the dimple penetrates the
threaded bore of the “T” handle. Continue to rotate “T” handle until gaskets are
approximately 30% compressed.
Start Up
New filters should be properly pre-conditioned before start up. Factory pre-conditioned filters
are available from DIVERSITECH. Filters not pre-conditioned can be conditioned in the field.
Please contact your DIVERSITECH Distributor for assistance.
Start system fan and confirm the designed air volume and actual air volume are within 10%. If
the air volume is more than the designed volume adjustments should be made to reduce the
volume to the designed volume.

7
If air volume is low and the contaminant is not being captured, adjustments will need to be
made. Consult your DIVERSITECH Distributor.
Apply compressed air to the manifold. Turn the reverse jet pulse control on. Apply power to
other auxiliary equipment as required.
COMMENTS REGARDING FILTER DIFFERENTIAL PRESSURE DURING OPERATION:
Depending on dust loading and Air-To-Cloth Ratio, reaching equilibrium of filter differential
pressure will vary from a few hours to many weeks. Low dust loading will normally develop 2-
3”w.g. with normal loading 3-6”w.g. and with high loading 6 - 8”w.g.
Low dust loading typically shows a steady level of differential pressure with very little
fluctuations once equilibrium is reached. By contrast, heavy loading can produce significant
“Ups and Downs” in operating differential pressure.
Do make immediate “Off-Time” time reductions on the timer board dial if significant increases
in operating differential pressure are discovered. However, if differential pressure drops, do
not be too quick to increase “Off-Time”, and then only in small steps.
NOTE:
A critical step in start up is to reach an acceptable operating equilibrium point. This must
be reached gradually in order to not damage the filters by blinding. While achieving
equilibrium, you want to clean the filters more often than required instead of not often
enough. Gradually and tentatively increase valve “Off Time” until equilibrium is reached.
Also, making notes and recording the results will help gage the effectiveness of various
DIVERSITECH filters and filter pretreatment. Should questions arise contact your
DIVERSITECH distributor.
Shutdown
Shutdown consists of shutting down the blower motor. With systems that include a “Cycle
Down” feature the reverse jet pulse cleaning will be activated. This will clean the filter
cartridges while the unit is off line, for a preset amount of time. Once the cleaning cycle is
complete the collector is ready to be energized when needed.
Caution:
Off line cleaning can cause pressure waves to feed back through the inlet of
the collector and the attached duct work. Precautions might be needed to
prevent dusting.
Maintenance Safety
Care with the design of DIVERSITECH collectors has minimized safety hazards for the
maintenance and production personnel.
Caution:
Personnel involved with the DIVERSITECH collector must be familiar with
the operation and the information in this manual.

8
1. Only competent, safety conscious personnel should have access to the area.
2.Work crews should consist of 2 or more people.
3.All areas below the collector must be “OFF-LIMITS” when overhead work is performed.
4. Objects lifted by crane or hoist must be securely fastened and carefully handled to prevent
injury.
Maintenance Procedures
With sound periodic and routine maintenance programs you will receive a long service life from
your DIVERSITECH collector. Schedules should be changed as a result of experience,
determined after a reasonable period of operation.
IMPORTANT: Please remove the spark baffle filters in each booth on a monthly basis and
wash with detergent. Not cleaning these filters could result in a fire.
Routine maintenance consists of the following:
1.Observe the filter differential pressure at least once every 8 hours of operation. Each
application will vary. Refer to “Comments Filter Differential Pressure during Operation” at the
beginning of page 7.
2. Assure the collected dust is removed from the dust storage container as required.
3.Assure the predetermined cleaning schedule is proper to maintain pressure differential
equilibrium.
4.Confirm the reverse jet pulse cleaning takes place at the predetermined schedule.
5. Observe compressed air supply to confirm pressure of 80 PSI minimum.
6.Perform general house keeping on collector and surrounding area.
Periodic maintenance consists of the following:
1. Replace filters when reverse jet pulse cleaning is no longer effective to reduce differential
pressure to the normal operating range.
2. Clean the internal parts of the reverse jet pulse control with a quality electrical cleaning
chemical.
3.Clean the internal components of the fan control.
4.Remove any accumulated dust from the pressure port that is connected to the Magnehelic
Gage or Reverse Jet Pulse Control or both. This is located inside the dust collector on the dirty
air side.
5.Replace the cartridge filter caps after every 4th filter change or before if failure of gasket
seal occurs.

9
Note: Be certain the compressed air is off and the pressure relieved
before servicing any components that contain compressed air.
6. Follow the manufacturer’s maintenance schedule for the compressed air filters.
7.Tighten the couplings of the valves for the reverse jet pulse cleaning.
8.Remove any moisture that has accumulated in the compressed air manifold and
accumulator.
9.Inspect and clean diaphragm valves. A thorough cleaning normally rectifies operational
problems with valves; however any worn or damaged parts are to be replaced. Use the
following procedure to inspect and repair valves:
A.Main Diaphragm
a. Switch off air supply and drain the system.
b. Unscrew the main diaphragm cover bolts and remove the valve cover.
c. Inspect the spring and diaphragm for dust and damage. Remove dust with water and
replace damaged parts with diaphragm repair kits for 1” or 1.5” valves.
d. Replace valve cover and valve cover bolts.
B. Solenoid Diaphragm
a. Switch off air supply and drain the system.
b. Unscrew the bonnet bolts and remove the bonnet.
c. Inspect the diaphragm for dust and damage. Remove dust with water and replace
damaged parts with diaphragm repair kit for 1” or 1.5” valves.
d. Replace the valve bonnet and valve bonnet bolts.
C. Solenoid Coil
a. Switch off air supply and drain system.
b. Apply proper voltage to the coil and listen for a pronounced “Click” as the pole
moves.
c. If a pronounced “Click” occurs and the valve does not function follow instructions
for replacing the main diaphragm and solenoid diaphragm.
d. If the “Click” is not heard, replace the solenoid with either a part for the 1” valve or
for the 1.5” valve.
10. Check and replace if necessary the access door gaskets and dust drawer gaskets if
applicable.
Cartridge Filter Replacement
Note: Depending on the contaminant being collected, it is advised to wear a
dust respirator when handling dirty filters.
Turn the “T” handles counter-clockwise until clearance is obtained above the cartridge filter.
Remove top cover from top of filter. Slide plastic bag over filter and pull it down to cover top
filter and remove. Cover the bottom filter with a plastic bag and remove. Repeat this with all
filters.

10
Note: Discard filters according to all local codes and regulations. Please help
protect the environment.
Follow filter installation instructions on page 7 to replace filters.
Trouble Shooting Guide
Symptom
Possible Cause
Remedy
Blower does not start. a. Open electrical supply circuit.
b. Blower motor not wired for
available voltage.
Trace circuit back from correct
interruption.
Rewire motor within motor box for
proper voltage per motor data label.
Blower motor starts but
does not continue
operating.
a. Incorrect overload protection
installed.
b. Loose or incorrect termination of
motor wiring.
c. Incorrectly sized wire for motor
load.
Replace overload protection with
correctly sized components.
Check all termination’s of motor
wiring.
Rewire motor circuit with proper wire
size.
Dust Discharge from
Collector outlet. a. Filter cartridges not properly
installed.
b. Damaged filter cartridge.
c. Damaged filter cap(s).
d. Worn filter cap.
e. Loose filter clamping “T” Handle.
Reinstall filters according to page 8.
Replace damaged filters.
Replace damaged filter cap(s).
Replace all filter caps.
Tighten loose “T” Handle.
Insufficient Air Flow a. Blower rotating backwards.
b. Collector not sealed properly.
c. Blower exhaust area blocked.
d. Filter cartridges need to be
Check blower rotation. Blower should
be rotating clockwise when viewed
looking down over the motor. Refer to
page 5 under Electrical for changing
rotation direction.
Check that all access panels, doors,
dust drawers, drum lids and flex hose
connections are tight.
Check exhaust area for blockage and
eliminate all material that causes
restrictions.
Remove and replace filter cartridges

11
replaced.
per instructions on page 11.
Symptom
Possible Cause
Remedy
e. Compressed air volume
inadequate.
f. Compressed air pressure
inadequate.
g. Compressed air contaminated with
oil or water.
h. Pulse cleaning not working.
i. Pulse cleaning not set up as
required.
j. Reverse jet pulse valves not
operating.
Increase available air volume. Refer to
page 5.
Increase air pressure to Maximum of
100 PSI.
Eliminate source of contamination and
purge compressed air line.
Confirm input power to timer board or
controller. Refer to pulse control
manual for further information.
The “on-time” and “off-time” must be
set to optimize filter pressure
differential equilibrium. Refer to pages
6 and 7 of this manual and to the timer
board controller manual for additional
detail.
Clean, repair or replace valves.
Refer to page 8.

13
REPLACEMENT PARTS LIST
DIVERSITECH MODEL WB-4000DCA
PART DESCRIPTION PART NO. QTY. PER UNIT
Filter, Cartridge 351D91A3292 2493 X each
Plate, Filter Cap with gasket 1222 X each
“T” Handle, Filter Clamp 1224 X each
“T” Handle, Access Door Latch 1023 X each
Gasket, Door Seal 1214 X feet
Valve, 1.5” Double Diaphragm 1221 X each
Motor, XX HP 3 Phase, 3500 RPM, TEFC 1041 X each
Fan Wheel XX” 1052 X each
Venturi, Inlet, XX” 1054 X each
Control, Reverse Jet Pulse, IT-X 1458 1 each

DIVERSITECH
Visit our Website for more
information on this product
www.diversitech.ca
1200 55th Avenue
Montreal, Quebec H8T 3J8
Email: [email protected]
LIMITED EQUIPMENT WARRANTY
For a period of 2 years from the date of purchase, all Diversitech
products are warranted to be free from defects in material, workmanship,
and construction, when used in accordance with installation, maintenance
instructions, and expressly stated proper use application(s). Diversitech
Inc. will repair or replace, at our option, any defective parts which fail
during the warranty period. This warranty is limited to replacement parts
ONLY, and does not cover personal liability, property loss, normal wear;
and does not cover losses resulting from (or due to) improper
installation, inadaqueate maintenance, misapplication, misuse, or use
above rated capacities.
FREIGHT CLAIMS
Shipments must be inspected upon arrival. All Diversitech units are sold
ex-plant. Therefore, it is the receiver’s responsibility to file any freight
claims with the carrier for obvious or concealed damages. Damaged
shipments must be refused at time of receipt, by consignee.
RETURN MATERIAL POLICY
Prior to the return of material, for whatever reason, a return
manufacturing authorization number (RMA#) is required from the
Diversitech customer service department. This procedure is necessary for
proper control and handling of returned materials. Call 1-800-361-3733
All material must be returned prepaid. Credit will be given for returns
for warranty repair or replacement. Freight collect shipments, or freight
without an RMA, will not be accepted. It is the shipper’s responsibility to
ensure that material being returned to Diversitech is adequately packaged
for shipment to preclude damages.
Table of contents
Other DIVERSITECH Dust Collector manuals
Popular Dust Collector manuals by other brands

Alpha Professional Tools
Alpha Professional Tools Ecoguard G7 instruction manual
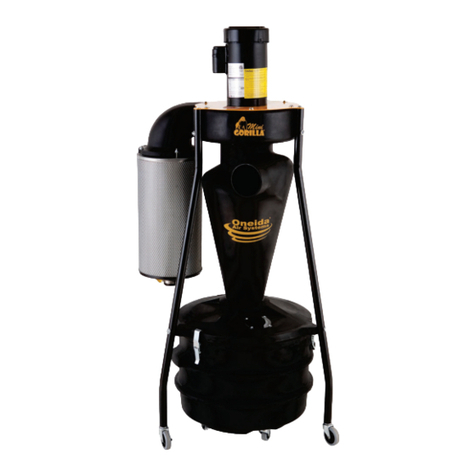
Oneida Air Systems
Oneida Air Systems Mini-Gorilla owner's manual
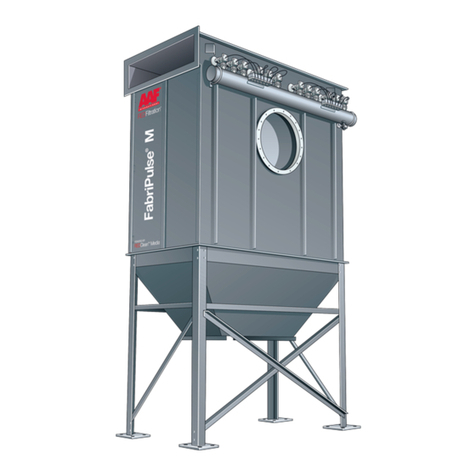
AAF
AAF FabriPulse M Installation, operation and maintenance manual
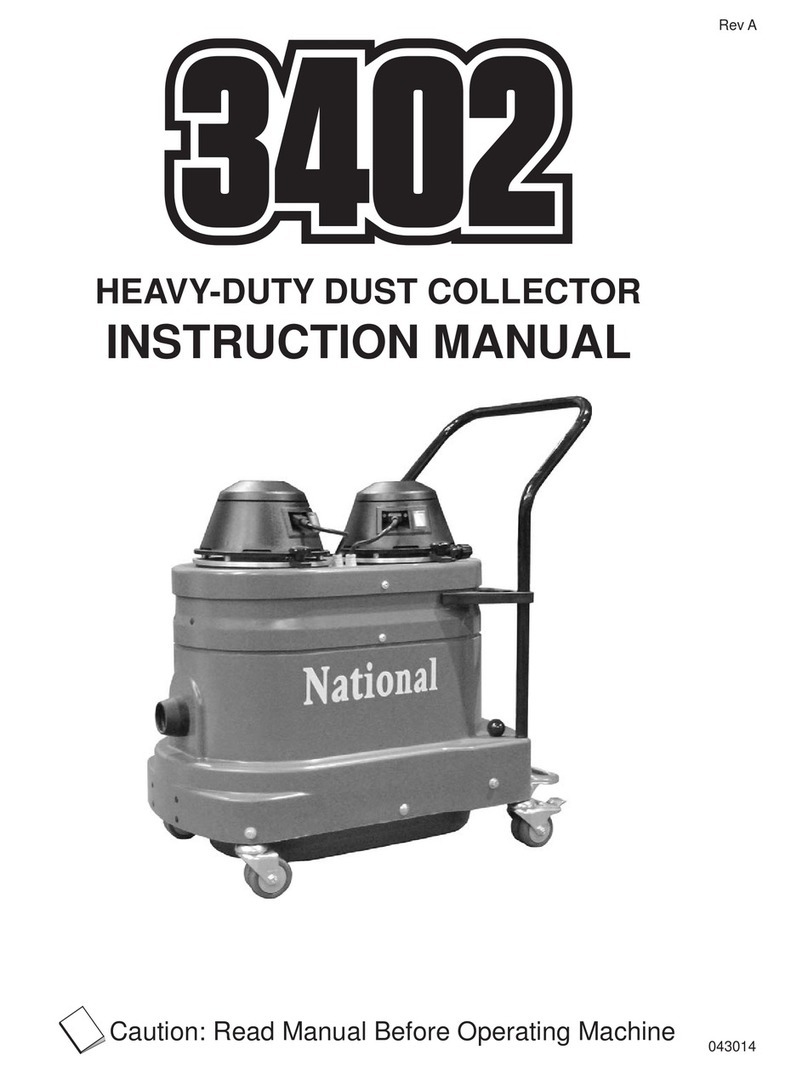
National
National 3402 instruction manual
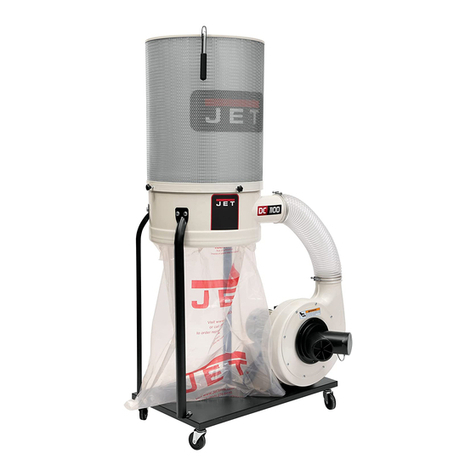
Jet
Jet DC-1100VX Series Operating instructions and parts manual
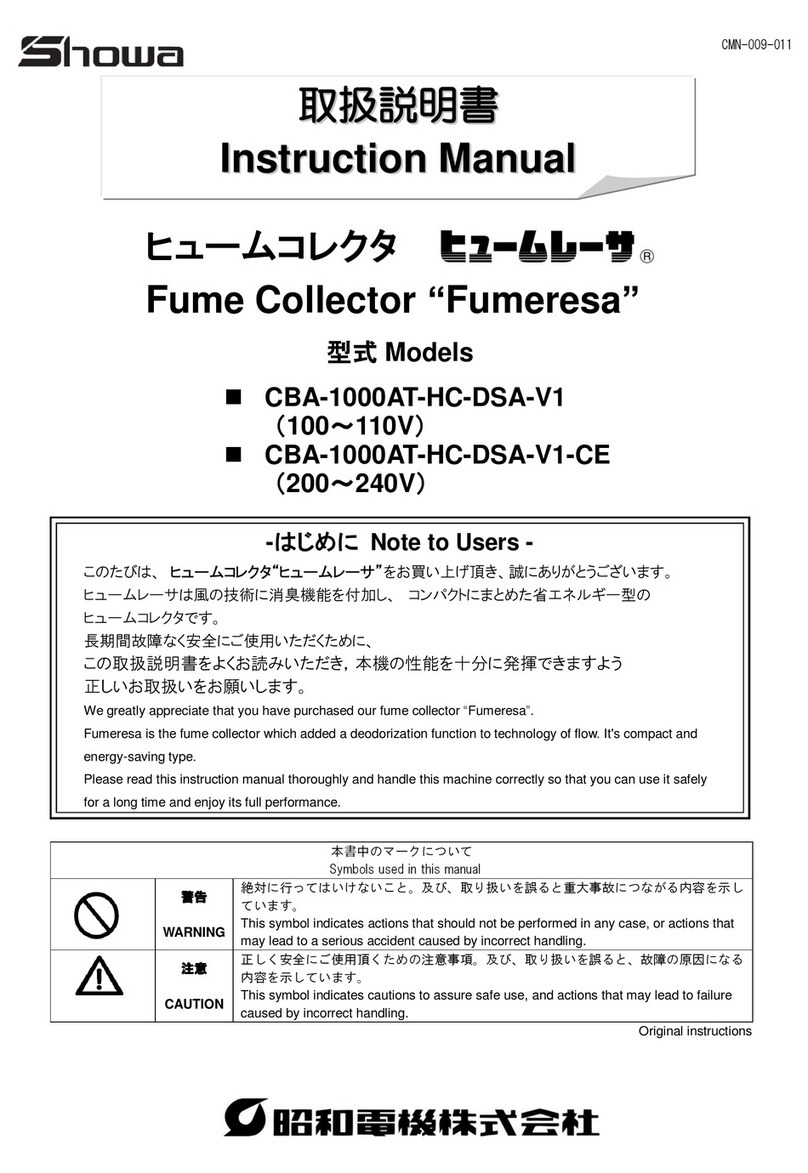
Showa
Showa Fumeresa CBA-1000AT-HC-DSA-V1 instruction manual