DIVERSITECH Diversi-Flush Parts list manual

DiversiTech bvba
de Keyserlei 5/58 | B-2018 Antwerpen | O +32 3 205 9312 | F +32 3 226 4482 | www.diversitech.eu
Diversi-FlushTM Usage Instructions
The Diversi-Flush™ Kit consists of a reusable injection tank (with built-in 200 psi
(13.78 bar) Pressure relief valve), nitrogen charging hose, and injection tool
assembly. The trigger injector on the tool assembly ensures more ecient use of
the solvent by allowing innite control of the ushes rather than the less ecient
method of ushing in one long burst. The Diversi-Flush™ Solvent is a dual purpose
blend designed to clean line sets and systems in preparation of changing from
R-22 to a blended HFC refrigerant (mineral oil to POE oil) as well as to ush the
contaminants from a system aer a compressor burn out. Typically, due to the
high acidic level of contamination in a burn out, more solvent will be required
in system ushes than in line set ushes. The Diversi-Flush™ Solvent is non-ozone
depleting and has low-toxicity.
Detailed Instructions
Compressor Burnouts
I. Equipment required
1. Diversi-Flush™ Kit including one 473 ml can of Diversi-Flush™ Solvent for every
17.5 Kw to 28 Kw of system capacity.
2. Re-sealable container to hold the contaminated ush material.
3. Nitrogen tank with regulator.
4. Refrigerant recovery machine.
5. Vacuum pump with accessories.
6. Absorbent shop cloths, rubber gloves and safety goggles.
II. Detailed Instructions
1. Evacuate the system using approved techniques and recovery equipment.
2. Take the electrical system oine
3. Remove the old compressor from the system
4. Remove lter drier cores as well as any check valves and reversing valves on
heat pump systems. It may be quicker and less expensive to by-pass the lter
drier, check and reversing valves with a by-pass loop.
5. Make sure a re-sealable waste container is attached to a discharge port to
capture the ushed acidic contaminants.
6. To maximize solvent contact time, restrict the ow at the discharge port. This
will minimize the amount of solvent needed to thoroughly clean the system.

7. Attach the hose and injector tool
assembly to the outlet side of the
pressure tank. Fill the Diversi-Flush™
Injector pressure tank with Diversi-
Flush™ Solvent. A tank may be lled
with up to 720 ml of Diversi-Flush™.
Connect the hose from the regulator
of the nitrogen tank to the inlet (ball
valve) side of the injector tank (g. A).
8. Set the nitrogen gauge at 50 psi (3.4
bar). Open the regulator valve on the
nitrogen tank then slowly open the
valve on the injector tank to pressurise
it. DO NOT EXCEED 200 psi (13.78 bar).
9. Close the valve on the injector tank and
nitrogen tank and then disconnect the
nitrogen hose from the injection tank.
10. Insert the rubber adapter in the inlet
port (g. B), maintaining the injector
tank in an upright position. Inject Diversi-
Flush™ Solvent in 3 second increments
in stages (30-60 ml/3.5 Kw). The number
of ushes will depend on the size of the
system and the contamination level.
11. Connect the hose from the nitrogen tank to the inlet port of the part that is being ushed
and purge the system at 150 psi (10.34 bar) for 1-2 minutes. This will ensure removal of
all trace amounts of oil residue and solvents. Check the solvent at the outlet port to be
sure all contaminants have been purged from the system. If the exiting solvent is not yet
clear repeat steps 10 and 11.
12. Next, install the new compressor, new lter drier core and check valves. If the system
was bypassed with a loop, remove and reconnect the lines.
• Pressure Relief Valve
• Hose
• Injector Tank
• (1) 473ml. Can of Diversi-FlushTM
• Injector Trigger Nozzle
• Diversi-FlushTM Adapter
Figure A

13. Using a vacuum pump, evacuate the system to a low micron reading. The typical
evacuation time is approximately 3 minutes per 3.5 Kw .
14. Check the system for leaks and recharge the system with refrigerant and oil as per the
equipment manufacturer’s recommendations.
15. Reconnect the electrical circuitry and test the system again following the manufacturers
recommendations.
16. Any unused Diversi-Flush™ Solvent can be stored in the injection tank and saved for
future use. Ensure all valves are closed on the injection tank to prevent solvent loss
during storage. Dispose of the waste solvent in accordance with national and local
waste disposal regulations.
Flushing Lines for R-22 to blended
HFC refrigerant Conversions
I. Equipment required
1. Diversi-Flush™ Kit including one 473 ml can of Diversi-Flush™ Solvent.
2. Re-sealable container to hold the contaminated ushed material.
3. Nitrogen tank with regulator.
4. Refrigerant recovery machine
5. Vacuum pump with accessories
6. Absorbent shop cloths, rubber gloves and safety goggles.
II. Detailed Instructions
1. Recover the refrigerant from system and disconnect and remove old equipment.
2. Make sure a re-sealable waste container is attached to the exit end of the lines to
capture the ushed material. Establish one end of the line set as the discharge point.
3. To maximise solvent contact time, restrict the ow at the discharge point. This will also
minimise the amount of solvent needed to thoroughly clean the system. For best results,
use the DiversiTech Line Set Flush Adapter to connect the liquid line and the suction line
at the disconnected indoor air handler. Inject solvent into the liquid line and collect
solvent at the suction line outdoors at the disconnected condensing unit.
4. Attach the hose and injector tool assembly to the outlet side of the pressure tank. Fill
the Diversi-Flush™ Injector pressure tank with Diversi-Flush™ Solvent. A tank may be lled
with up to 720 ml of Diversi-Flush™. Connect the hose from the regulator of the nitrogen
tank to the inlet (ball valve) side of the injector tank (g. A).
5. Set the pressure regulator on the nitrogen tank at 50 psi (3.4 bar), open the inlet valve at
the tank then slowly open the valve on the injector tank to pressurise it. DO NOT EXCEED
200 psi (13.78 bar).
6. Aer pressurising the Injection Tank, close the valve and disconnect the nitrogen ll
hose.
7. Line sets of dierent diameters, lengths and congurations will require dierent quantities
of Diversi-Flush™ Solvent to achieve complete removal of residual oils.
A. For liquid lines, a 473 ml can of Diversi-Flush™ will typically clean up to 150 metres of liquid
line: Insert the rubber adapter in the inlet of one of the line sets, maintaining the injector
tank in an upright position, inject Diversi-Flush™ Solvent in 3 second increments in stages.
The number of ushes will depend on the length of the line and the contamination level.
A typical line set will require 60 to 90 ml of Diversi-Flush™ to eectively remove the oil
residual in the line sets. Results will vary depending on contamination level.
B. For larger diameter pipes: Larger diameter line sets will require considerably more
Diversi-Flush™ Solvent due to increased volume of the larger pipes. The ushing process
will therefore require multiple 3 second injections of Diversi-Flush™ solvent to achieve
satisfactory results.

LIT-DUSE-FLUSH
Manufactured by
DiversiTech bvba
de Keyserlei 5/58
B-2018 Antwerpen
www.diversitech.eu
©2010 DiversiTech Corporation
Version No. 1.0, September 2010
8. Connect the hose from the nitrogen
tank to the inlet port (g. B) of the
part that is being ushed and
purge the system at 150 psi (10.34
bar) for 1-2 minutes. This will ensure
removal of all trace amounts of
oil residue and solvents. Check
the solvent at the outlet port to
be sure all contaminants have
been purged from the system. If
the exiting solvent is not yet clear,
repeat steps 7 & 8.
9. Connect the new equipment and,
using a vacuum pump, evacuate
the system to a low micron level.
The typical evacuation time is
approximately 3 minutes per 3.5
Kw.
10. Check the system for leaks,
then charge system with the
refrigerant and oil as per the
equipment manufacturer’s
recommendations.
11. Connect the electrical circuitry
and test the system again following
manufacturers recommendations.
12. Any unused Diversi-Flush™ Solvent
can be stored in the injection tank and saved for future use. Ensure all valves are closed
on the injection tank to prevent solvent loss during storage. Dispose of the waste solvent
in accordance with national and local waste disposal regulations.
These recommended quantities are based on typical ush situations during a conversion
from R-22 to a blended HFC refrigerant . In the event of compressor burn out double the
amount of solvent required to compensate for the added oil contamination load. This is for
lines only and do not calculate in any allowance for the system components connected
to the lines.
Figure B
Table of contents
Popular Other manuals by other brands
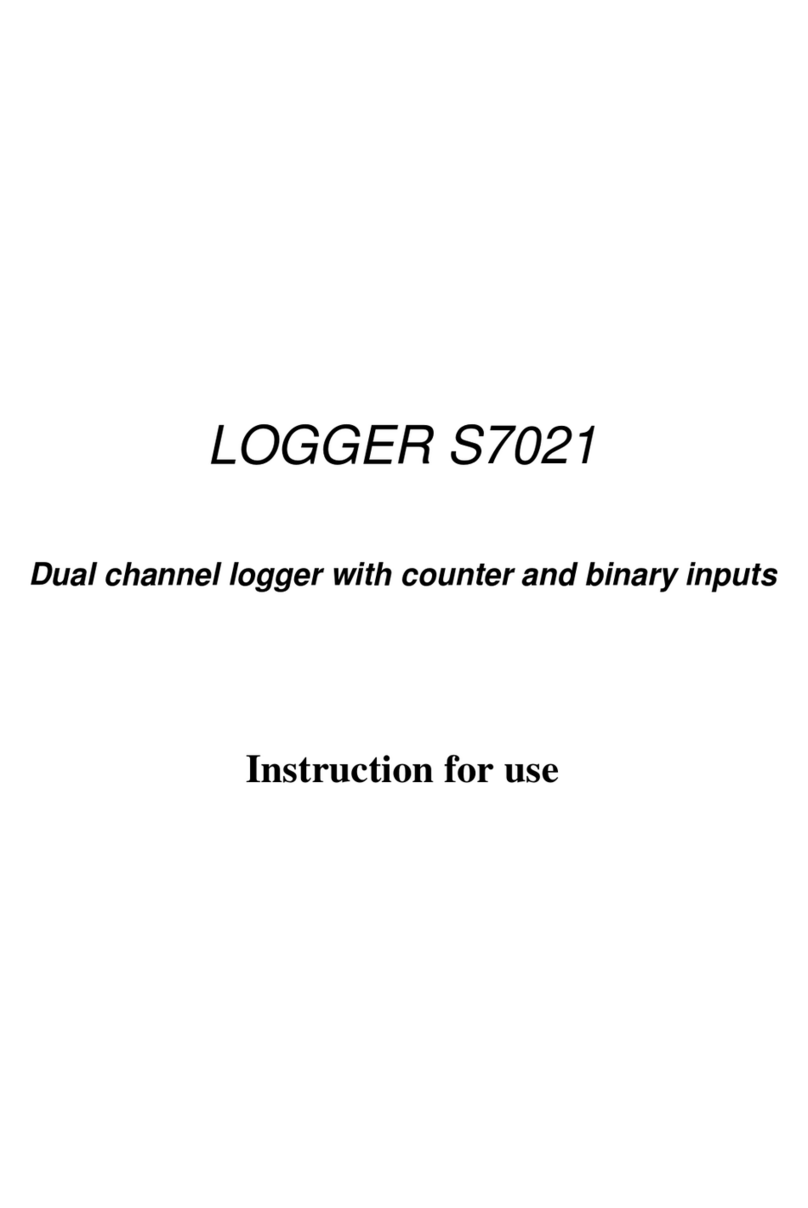
Comet
Comet S7021 Instructions for use

GRASS VALLEY
GRASS VALLEY Kaleido-X16 Hardware description and installation manual

Philips
Philips D2999 Service manual

National Flooring Equipment
National Flooring Equipment 3390 instruction manual

Drester
Drester WM-90 Series manual
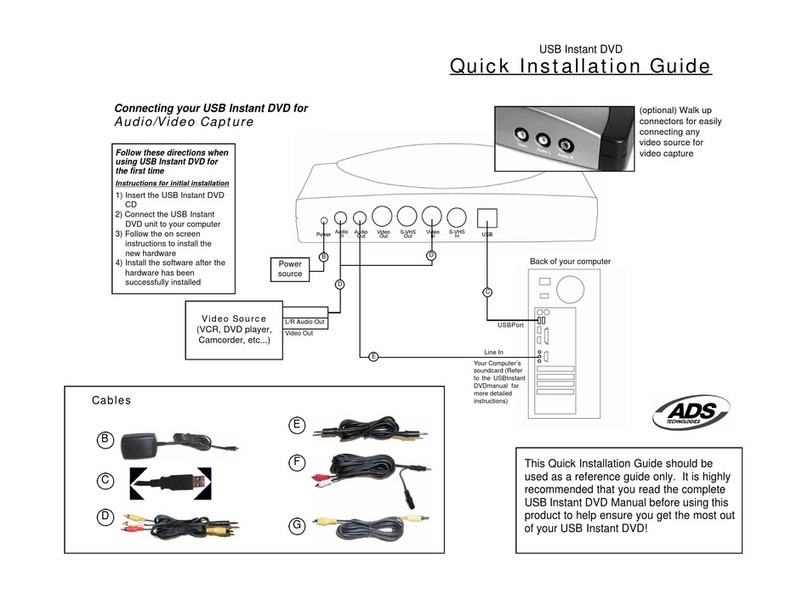
ADS Technologies
ADS Technologies Instant Video PCI Quick installation guide