DROPSA VIP5 User manual

VIP5: Lubrication System
Controller
Control system for small and medium size
Lubrication Systems
Software Version 3.0
Quickstart Guide
User Operating and Maintenance
Manual
Original text translation
Warranty Information
CONTENT
1. INTRODUCTION
2. PRODUCT FEATURES
3. DESCRIPTION OF OPERATING PROCEDURES
4. FIXING AND INSTALLATION DETAILS
5. INPUTS/OUTPUTS
6. OPERATOR INTERFACE FRONT PANEL
7. OPERATING MODE
8. CYCLE MONITORING
9. SETUP PROGRAMMING
10. PROBLEMS AND SOLUTIONS
11. TECHNICAL SPECIFICATIONS
12. MAINTENANCE PROCEDURES
13. DISPOSAL PROCEDURES
14. ORDERING INFORMATION
15. MOVING AND SHIPPING
16. OPERATING PRECAUTIONS
17. WARRANTY
18. REVISIONS
19. DECLARATION OF COMPLIANCE
20. DISTRIBUTORS
Manual compiled in accordance with Directive C2094IE –WK 20/11
06/42 CE
http://www.dropsa.com

2/29
Quickstart Guide
10 STEPS TO SETUP YOUR VIP5 Controller
This section provides summary instruction for programming the VIP5 controller BASIC Menu and functionality.
The features in the basic menu can be used to control and monitor a majority of simple TIMER BASED;
PROGRESSIVE AND 33V INJECTOR lubrication systems, allowing to get your system up and operational in
minimal amount of time.

3/29
STEP 1 –Install and fix VIP5 Controller
The VIP5 Controller should be fixed using the 4 fixing holes.
For further information, refer to Section 4 of this manual.
STEP 2 –Connect power input and pump (or control solenoid) output to the VIP5 connector strip “M1”
Further details in section 5
STEP 3 –Connect the pump low level switch to pin 4 and 5 on connector strip “M2”
For complex connections involving
4..20mA please refer to section 5
If you do not have an end of cycle switch
(the controller will operate in timer only
mode) then skip to step 5
A
B
C
212 mm
(8.35 in.)
162 mm
(6.4 in.)
Ø 4,2 mm
(Ø 0.16 in.)
OUTPUT
COMMAND
POWER
INPUT

4/29
STEP 4A
If using a Progressive System - connect the Dropsa Ultrasensor/end of cycle switch to pins 13/14/15
on connector strip “M2”
STEP 4B
If using a 33V Injector System–connect the end of cycle pressure switch to pins 14 and 15 on
connector strip “M2”
For any other system, please refer to the connection diagrams in section 5
STEP 5 –Connect the remote alarm signal relay to your host machine to pins 1/2/3 on connector strip
“M2”

5/29
STEP 6 –You can now power on the VIP5 and enter setup programming mode
When you turn on the device, you can check the firmware version loaded: rel. 3.00
Press and hold the MODE key for 5 seconds to the setup programming menu
The VIP5 will display the first parameter LUBE Type
and the default value SEP
Now configure the parameters
STEP 7 –
Select the type of system: SEP, TIMER, PS, DUAL
By default, the system will be configured a SEP Progressive controller.
To change the configuration press the MODE key for per 5 seconds,
and use the arrow UP and DOWN keys to select the type of system parameter.
Select LUBE TYPE accounting to the type of system you have:
SEP :select this option for PROGRESSIVE SYSTEM with the end cycle switch ( eg. Dropsa
Ultrasensor). The VIP5 Controller will activate the pump and compete the cycle when the
cycle switch has changeover two times (0 -> 1 -> 0, or 1 -> 0 -> 1).
The pump is then switched off until the next lubrication cycle.
DUAL :select this option for more complex DUAL LINE SYSTEM . You should refer to the
advanced setting in section 8.
TIMER :select this option when you have NO CYCLE SENSOR. The VIP5 Controller will
activate the pup for the duration of the LUBE TIME . After this, the pump is switched off
until next lubrication cycle.
PS : select this option when have a pressure switch configuration in a 33V INJECTOR
SYSTEM. The VIP5 Controller will switch on the pimp and wait for pressure to be achieved. The
pup is the switched off until the next lubrication cycle.
When the correct type of system is selected, press OK key to set the next parameter.

6/29
STEP 7A
If TIMER mode is selected –Set the lube cycle timer value
If TIMER mode is selected, you must determine for how long the pump must run
during each lubrication cycle. For other operation modes, the run time of the pump
is automatically determined by the end of cycle monitoring switch.
Press MODE key to SET cycle time
Select UP and DOWN arrows to set the value
Press OK key to save the value
Press UP arrow ( NEXT function) to move onto the next parameter.
STEP 8
Set the pause time value ( PAUSE timer)
The PAUSE timer is used to set how often the VIP5 will active the pump and run a
lubrication cycle. By default, this is set to every 6 minutes
To change the setting, press MODE key
Then use UP and DOWN arrows to change value.
Once, you have selected your pause time, press OK key to save and return to the
parameter Menu
Press UP arrow ( NEXT ) to move onto the next parameter.

7/29
STEP 9
Set pump Type –You must tell the VIP5 if you are using a continuously energized pump system or if it requires
to be pulsed to work correctly.
CONTINUOUS : The VIP5 Controller by default, can operate both electric and
reciprocating pneumatic pumps that require a continuous command output.
Example of such pumps are Dragon Series, Sumo, Cannon Pump, Smart, Piccola,
Pneumatic Barrel Pumps. These are known as CONTINUOUS pump type.
PULSED : If however you are using a pump that requires a pulsed output the you
must selected PULSED.
Examples of such systems would be a Locopump piloted by an (3/2) air solenoid
valve.
To change the setting, press MODE button.
Then use the UP and DOWN arrows to change the value.
Once, you have selected your desired PUMP Type, press OK button to save and
return to the Parameter Menu.
STEP 10
Complete the Setup
At this point, the basic parameters have been set. The VIP5 Controller will ask if you
wanted to set the advanced options. These allow a much more granular control of
the lubrication cycle for complex systems and many more control options. You can
read about the other option in section 9 of the manual.
Press OK button to save the setting and exit programming mode.
Setup Completed -The VIP5 will now start a lubrication cycle

8/29
1. INTRODUCTION
Thank you for purchasing the Dropsa VIP5 –Lubrication Controller. This is the operating and user manual for the VIP5
Controller used to control and monitor small and medium sized lubrication system such as simple on/off systems, injector
systems, progressive divider systems and simple dual line systems.
It is possible to obtain the latest documentation by visiting our website, www.dropsa.com
This manual contains important operating and safety information for users of this product. It is essential that you carefully
read this manual and conserve a copy with the product so that other users may consult it at any time.
1.1 DEFINITION OF LUBRICATION AND STANDBY PHASE, LUBRICATION PHASE, AND LUBRICATION CYCLE
In this manual the LUBRICATION PHASE and LUBRICATION CYCLE refer to the specific instances when the lubrication pump
is operating to provide lubrication in a system.
The LUBRICATION CYCLE is made up of : Cycle Start -> Control of a sensor device -> Delay time to allow sensor device to
stabilize -> Wait Time before another Cycle Start. This sub-cycle can be repeated as many times as required and the
completion of this repetition is considered the LUBRICATION PHASE. Fig. 1 Illustrates this graphically.
The STANDBY PHASE defines the interval between each LUBRICATION PHASE.
Fig.1 A Lubrication Phase can comprise of many Lubrication Cycles
Cycle
Start
Control
Delay
Wait
Lubrication Phase
Lubrication Cycle
Lubrication Cycle can be repeated up to 250
times.

9/29
2. PRODUCT FEATURES
VIP5 is an advanced lubrication control that offers many operating possibilities and features in a single compact package. It
is an ideal product for small and medium systems as it offers considerable advantages over using a much bigger, expensive
PLC system to achieve the same result. Some of the key features are:
•Three separate inputs (to monitor Dual line pressure switches, progressive cycle switch, injector pressure switch and
external signals to use as a counter for standby or lubrication phase ).
•Signal Inputs can be NPN, PNP or a Clean Contact (or Namur style switching).
•Time or counter based determination of both Lubrication and Standby Phase.
•Counter based Lubrication phase can be used independently while monitoring correct function of a cycle switch, ideal
for use in impulse piloted system (e.g. chain and conveyor lubrication).
•Minimum Level Input.
•4..20ma Input for analog measurement of Reservoir Level.
•Ability to configure pump output for Electrical or pneumatic pump (pump On/Pump Off values can be set individually).
•General Alarm Output Relay can be a constant signal or generate a coded alarm to allow remote PLC to determine
nature of alarm.
•Integrated LCD Display for diagnostic and ease of use.
•Diagnostic and Lubricant Counters for Operation and Alarm conditions.
All configuration parameters can be set from the Setup menu via the LCD display using the front panel keys. No complex
internal switches need to be set.
3. DESCRIPTION OF OPERATING PROCEDURES
The VIP5 controller has three operating modes:
1. CYCLE
2. PULSE
3. FLOW
CYCLE and PULSE modes are designed for intermittent or continuous lubrication system that require the control of a pump
and monitoring of feedback signals to determine when lubrication has successfully completed.
FLOW is designed as a monitoring only operating mode that allows the user to monitor a pulse signal and determine the
actual flow rate. This is useful for process control and generally used in re-circulating systems.
3.1 CYCLE and PULSE Control System operating Principles.
The VIP5 control system is designed to control intermittent or continuous lubrication system with a variety of control
inputs. Intermittent operating principle is based on three distinct phases.
PRELUBE Phase -> Pre Lubrication that occurs during power up of a system.
LUBRICATION Phase (Lube –> Wait stages) -> This is when lubricant is provided (as above)
STANDBY Phase -> The system is inactive awaiting for the next LUBRICATION PHASE
Continuous operation is identical but does not have a STANDBY Phase.
Additionally, the VIP5 Control system can also be used as a simple monitoring device in the “FLOW” operating Mode
described later in this manual.

10/29
3.1.1 PRELUBE Phase
The user can specify a number of lubrication cycles (up to 999) which are initiated when the unit is powered on. If Prelube
is set to zero, the VIP5 controller will revert to its pre-powerdown status.
Prelube is activated:
When the VIP5 system is powered on.
After the RESET button is pressed.
After the VIP5 exists from the setup menu.
As indicated above, if Prelube is set to “0” value, the Prelube phase is omitted and when the system is powered on, the
system will continue from its previous position in the program.
3.1.2 LUBE (Lubrication) Phase
The Lubrication Phase is a set of Lubrication Cycles that can be repeated up to 999 times.
A Lubrication Cycle consists of activating the lubrication pump, then Control monitoring a feedback signal from a sensing
device if installed. There is then Delay period before switching off the pump, and a Wait period before the lubrication cycle
can be repeated. Specifically:
-Cycle (time) determine how long to wait for the control signal before determining an alarm condition.
-Control (Type) determines what kind of control signal (Single Line, Dual Line, Injectors). Alternatively a Timer only
setting means no monitoring will occur.
-Delay (time): Is how long to wait for the signal to be confirmed and switch off the pump (in Pressure switch
applications)
-Wait (time): determines how long to wait in a pump off condition before repeating the cycle. This is necessary in
injector systems and represents the minimum time required for the injectors to reset. In progressive systems for
example this can be set to zero.
3.1.3 STANDBY Phase
During the Standby the VIP5 switches off the pump and waits for the start of another Lubrication Phase. The duration of
the Standby phase can be determined by a countdown timer or a by an external pulse signal that can be used as a counter.
The VIP5 also allows a combination of both timer and external pulse signals to determine either the next Lubrication phase
or to signal an alarm if external pulse signals are not received within a pre-set time.
3.2 FLOW MODE OPERATING PRINCIPLES
The VIP5 can also be used as a simple Flow monitoring system. When Flow mode is selected the unit operates as a flow
display and monitors an external signal to calculate the flow based on external impulses. The User can additionally set a
minimum and maximum Flow limit. If the flow is out of these limits, the remote alarm contact and the alarm LED on the
front panel are both activated.

11/29
4. FIXING AND INSTALLATION DETAILS
FIXING DIAGRAM
The different VIP5 models are shown below with fixing dimensions.
4.1 UN-PACKING
Once the installation point has been identified, you can unpack the VIP5 from its shipping box. Check that the unit has
not been subject to any damage during transport. Dispose of the packaging in an appropriate manner, following local
waste regulations.
4.2 INSTALLATION
The VIP5 must be secured physically to a mounting location and cabled to all the required components of the
lubrication system.
A
B
C
95 mm
(3.7 in.)
95 mm
(3.7 in.)
Ø 3,5 mm
(Ø 0.13 in.)
PN: 1639144 /1639145/ 1639147
A
B
C
111,5 mm
(4.4 in.)
111,5 mm
(4.4 in.)
Ø 3,5 mm
(Ø 0.13 in.)
PN: 1639150 / 1639151 / 1639152 / 1639153
A
B
C
153 mm
(6 in.)
222 mm
(8.75 in.)
Ø 8 mm
(Ø 0.13 in.)
VIP5 Steel Box
VIP5 Panel Mount
VIP5 Plastic Box
132
PN: 1639140 / 1639141 / 1639142
A
B
C
212 mm
(8.35 in.)
162 mm
(6.4 in.)
Ø 4,2 mm
(Ø 0.16 in.)

12/29
The following are general recommendation:
•Install the unit in an easy to access location so that users can avoid unnatural postures and have good visibility of the
display.
•Leave 100mm or 4 inches around the unit of space to facilitate cabling and maintenance.
•Do not install the unit in dangerous or excessively aggressive environments with high levels of vibration or in the
vicinity of flammable substances.
•Always use the four fixing points as indicated in the diagram.
5. INPUTS/OUTPUTS
5.1 ELECTRICAL CONNECTIONS
The input and output connections for the lubrication devices and sensors can be achieved via the M1 and M2 terminal strip
located on the bottom of the VIP5 box.
The following are connection information for the M1 and M2 terminal strips.
IN
010
IN
420
POWER
PUMP
VIP5 INF
M1
M2
CN1
CN2

13/29
The following table lists INPUTS and OUTPUTS for the VIP5
Note 2 : for active sensors, the maximum current available is 100mA in total on +Ve.
When using clean contacts, the VIP5 will use 12 or 24V to monitor the contact.
*Note 1: If using NAMUR wire sensors, a 1.5kΩ to 2.5kΩ resistor should be installed between Signal and GND (see
paragraph 6.1 for wiring diagram)
Location
TYPE
PINOUT LABEL
DESCRIPTION
NOTES
Terminal
Number
M1
1
Output
Motor line 1 (+)
Pump/Solenoid Connection
max 10A @ 230V~
Power is supplied via
relay from pins 3 and 4
M1
2
Motor line 2 (-)
M1
3
Input
Power AC/DC input 1 (+)
Power connection for VIP5
12V/24V/110V~/230V~
Depending on Model
purchased.
M1
4
Power AC/DC input 2 (-)
M2
1
Output
Alarm contact NC
Remote alarm relay
Max 2A @ 30V ~
M2
2
Alarm contact COMMON
M2
3
Alarm contact NO
M2
4
Input
LL
Minimum Level Sensor
Open contact, or
PNP,NPN,NAMUR
(*see Note 1)
M2
5
GND
M2
6
Input
IN010
0-10V Volt analogical input
Not used
M2
7
Analog GND
M2
8
Input
IN 420
4-20 mA analogical input connection
point
Not isolated
M2
9
Analog GND
M2
10
Input
+Ve (see Note 2)
Input for external counting device.
PNP/NPN or clean contact.
Suspend input in CYCLE mode.
Clean contact,
PNP,NPN,NAMUR
(*see Note 1)
M2
11
PULSE
M2
12
GND
M2
13
Input
+Ve (see Note 2)
First Sensor Input for monitoring
system.
Eg. Pressure switch for injectors or
Cycle switch for progressive system
Suspend input in TIMER mode.
Clean contact,
PNP,NPN,NAMUR
(*see Note 1)
M2
14
P1
M2
15
GND
M2
16
Input
+Ve (see Note 2)
Second Input for monitoring system.
Eg second pressure switch on a dual
Line System
Clean contact,
PNP,NPN,NAMUR
(*see Note 1)
M2
17
P2
M2
18
GND

14/29
5.2 WIRING EXAMPLES
5.3 ACTIVATING THE BATTERY FOR REAL TIME CLOCK FUNCTIONS
By inserting the Jumper into the bridging pins, the battery function is activated and this allows the VIP5to operate with
the Date/time and status save function when the power is removed.
BATTERY
JUMPER:
Bridge pins to activate
battery
-
-
-
+
+
+
COM
NC
1
2
3
COM
NC
Note: Every time the battery jumper is removed and reinserted causes the DATE/TIME function to be
set to zero. Therefore it is recommended that after inserting the battery jumper, the date and time is
set.

15/29
5.4 PRECAUTIONS TO BE USED WHEN CARRING OUT WIRING
There are no specific safety risks associated with this device. Use general precautions that you would use when
operating an electrical device. All wiring should be carried out by a qualified electrician.
Before wiring the panel ensure correct voltage as indicated on the product label.
Only perform wiring operations once you are sure power is off and cannot be accidentally switched on.
A circuit breaker that is easy accessible must be used in the wiring of the pump. Ensure the break contact has a
contact distance of at least 3 mm
When using the 12-24V AC device, the power must come from a transformer in compliance with prescription of IEC
62558-2-6
In case of connection to 230 V~ or 110 V~, the connections on M1 (power and pump) must have reinforced isolation
up to the terminal connections. The cable must be routed to avoid damage to the outer isolation sheaf.
It is advisable to use a fuse or a differential isolation to protect the device. The device should have a recommended
value of 0,03 Ampere with 1 milllisecond maximum activation time. isolation capability ≥ 10kV and nominal ln=6A.
It is good practice to use cable ties that can help prevent cables being torn
6. OPERATOR INTERFACE FRONT PANEL
6.1 LAYOUT AND STATUS TABLE OF VIP5 FRONT PANEL
VIP5 Condition
PUMP ON LED
CYCLE INPUT LED
ALARM LED
Alarm
OFF
ON
ON
Standby Phase
OFF
ON
OFF
Lubrication Phase/Cycle
ON
ON
OFF
Setup
OFF
OFF
ON
Product
Identification
Label(on side)
Shows parameter and values
during set-up, or status and
counters during normal
operation.
BACK:
Previous Parameter or Setting
Decrease displayed value
NEXT:
Next Parameter or Setting
Increase displayed value
Alarm LED
Hardware Reset Button
Status and
description.
Cycle status LED
Shows cycle
control input
condition
Pump ON LED:
Pump ON
Pump OFF
Stand by
OK:
Exit from setup menu saving
changes
ESC:
Exit from setup menu
without saving changes
MODE (SET):
Change Value for selected parameter

16/29
LUBRICATION PHASE
REPEATED 1-250 Times
Lubrication Phase can be repeated
STOP
LUBE CONTROL WAIT
STOP
7. OPERATING MODE
VIP5has three different operating modes which are determined during the setup stage described previously.
These are: CYCLE, PULSE and FLOW.
7.1 CYCLE Mode
In Cycle mode a cycle sensor determines the completion of the LUBRICATION PHASE. If using timer setting, the Lubrication
Cycle will complete when the timer expire. The Standby phase is determined by a timer or by an external input counter.
7.2 PULSE Mode
In Pulse mode, the duration of the Standby Phase and the Lubrication Phase are both determined by an external counter.
The correct operation of the Lubrication Cycle can be monitored using a cycle sensor.
7.3 FLOW Mode
Using this mode allows the VIP5 to be used as a simple flow monitoring and display device.
Lubrication Cycle
Example 1) Standby and Lubrication determined by ON & OFF Timer
Example 2) Standby determined by a counter
Example 3) Standby determined by a counter and timer
combination.
the first of two events
0 –60.000 cycles
Example 4) Standby determined by a counter. Alarm signal given if the
external counter signals not detected within a set time.
1 min / 99 hours
1 –60.000 cycles
Pump in Stand by
Pump on
ALARM
Sul display del vip viene visualizzata la
quantità di flusso, rilevata mediante un
ingresso
Flow control
Flow control
Lubrificazione
Example:
Standby Phase determined by the Pause Counter, and
lubrication Phase determined by Cycle Counter.
[CYCLE Cnt >1 PAUSE Cnt > 0 ]
The Lubrication Phase is Suspended if no external
signals are recieved within a time specified by the
suspend Timer.
[SUSPEND T>0 ]
LUBRICATION PHASE
LUBE CONTROL WAIT
Alarm
Pump in Stand by
Pump on
ALARM
0 –60.000 cycles
1 –60.000 cycles
1 –60.000 cycles
Alarm
Alarm
0 min / 99 hours
0 –60.000 cycles
1 min / 99 hours
Flow Out of Range
Low Level, or
Thermal trip.
The display shows the current Flow rate
being detected in the system.
It is also possible to scroll through menus
to see totalizing flow counter
Flow Out of Range
Flow control
Lubrificazione
FIELD
CONTROL
COMPUTING
ALARM
OUTPUT
FLOW DATA
UPDATE
ALARM

17/29
7.4 PRELUBE
The Prelube cycle is a pre-lubrication cycle that is triggered when the system is powered on or reset. If the pre-lube cycle
value is set to 1 or greater the VIP5 will perform the set number of Lubrication Phases.
Note that if Each Lubrication Phase comprises two or more Lubrication Cycles, then the total cycles performed will be
equal to the Lubrication Cycles multiplied by the Prelube Cycles.
PRELUBE
1
YES
RUN n
LUBE Cycle
NO
NORMAL
OPERATION
POWER ON
OR RESET

18/29
8. CYCLE MONITORING
8.1 MONITORING OPTIONS.
There are four possible Cycle Monitoring Options, explained below.
1) TIMER –TIME ONLY
The Lubrication cycle is simply operated
according to a preset Timer value.
Therefore, no input is monitored to confirm
the correct completion of the lubrication
cycle.
2) PS –PRESSURE SWITCH
Pressure switch monitoring is typically used
in injector system.
The VIP5 will monitor input P1 to verify that
it is an OPEN contact at the start of the
cycle.
The pump is activated and the pressure
switch must CLOSE within a timeout period
otherwise a cycle alarm is generated.
Once the P1 contact is closed, a DELAY
timer checks that the switch is not broken
for a set time before switching off the
pump. This ensures that pressure spikes at
the start of a lubrication cycles on long lines
are filtered out.
A WAIT timer can be set to allow the
injectors to reset when using multi cycle
configuration.
LL
ALARM
MINIMUM LEVEL
MOTOR PUMP
PUMP
POWER
POWER
RESET BUTTON
P1
ALARM
PRESSURE SWITCH
POWER
LL
PUMP
POWER
MOTOR
PUMP
MIN. LEVEL

19/29
8.2 NOTES ON CONTROLLING A DIRECTIONAL VALVE IN A DUAL LINE SYSTEM:
When using hydraulic dual line system directional valves the pressure itself causes the valve to perform the line
inversion.
However, if using an electrically operated directional valve then a signal must be given to power the solenoid that
causes the valve to invert.
The VIP5 already has this control capability, but you must fit the equipment that included the Terminal Wiring board in
order to have the output present to power the solenoids. For further information contact the Dropsa technical sales
office.
3) SEP –SERIES PROGRESSIVE
Series progressive Operating mode is used
for Cycle switch monitoring typically on
progressive systems.
The Pump is switched on and P1 input is
monitored and must change state twice
within the timeout period otherwise a
timeout alarm will be generated.
Once P1 changes state twice, the pump is
switched off and VIP5 goes to standby or
the Lubrication Cycle is repeated for the
desired number of times
There is no WAIT time in this mode as
progressive systems do not need venting
time.
4) DL –DUAL LINE
Dual Line cycles generally use two pressure
switches connected to P1 and P2.
The VIP5 starts the pump and must see that
P1 switch is closed within the timeout time.
After this, the Lubrication lines are inverted
by use of a directional valve.
The P2 switch must also then be made
within the timeout timer setting.
A user configurable DELAY timer can be set
to filter pressure spikes as in the PS
operating mode.
LL
ALARM
POWER
ELETTROVALVE
PUMP
MINIMUM LEVEL
ULTRASENSOR
P1
POWER
EXPANDER
ALARM
POWER
POWER
MOTOR PUMP
PUMP
MINIMUM LIVEL
LL
P1
P2
P1
P2
LINE 1
LINE 2
INVERTER

20/29
9. SETUP PROGRAMMING
The following section explains how to navigate the VIP5 setup menus and contains detailed explanation of each parameter
and possible values.
9.1 Navigating around the setup menu.
The navigation map below shows how to navigate around the setup menu.
OPERATING
SETUP PARAMETERS
VALUES
To enter the SETUP menu from the OPERATING Mode, hold the (Mode) button for 5 seconds.
The (Up and Down) keys allow scrolling through the parameters.
By pressing the Mode button again, the indicated parameter value can be modified by using the Up and Down keys.
To exit, use the (OK) key, or (Esc) if you with to exit without saving
9.2 BASIC/ EXTENDED MENU
When turn on Vip5 Controller show a BASIC menu that allows user a quickly setup, there are only main parameters to
manage a lubrication cycle.
The "Quick start guide" section, placed early this manual, describes BASIC MENU programming mode.
The VIP5 Controller can operate or in stand-alone mode ( default) or inserted in a system of overall control which can
receive timing signals for starting and stopping of lubrication. VIP5 can also operate in exclusive monitoring lubrication
mode.
The Extended Menu allows to set all parameters that guarantee the total control of the system.
To see the complete list of extended parameters, see section 9.3.
LUBE sep: 1
01m56s STOP
5 sec
MODE -Cycle-
SET - - NEXT
MODE -Cycle-
SAVE - +
OR
set value
save
parameters
no save
parameters
save
parameters
no save
parameters
OR
saved
value
not saved
value
LUBE Type SEP
SAVE - +
OR
set value
OR
not saved
value
saved
value
LUBE Type SEP
SET BACK NEXT
+
SETUP MODE
Table of contents
Other DROPSA Controllers manuals
Popular Controllers manuals by other brands
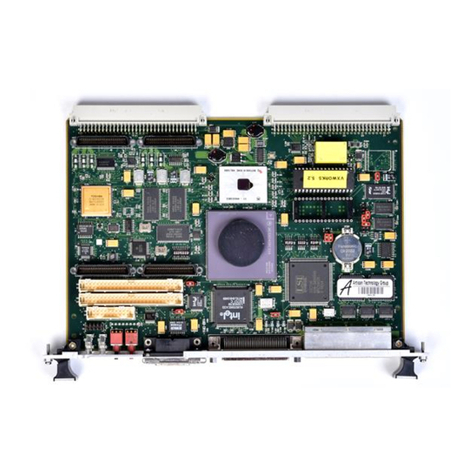
Motorola
Motorola MVME162P2 Series Installation and use
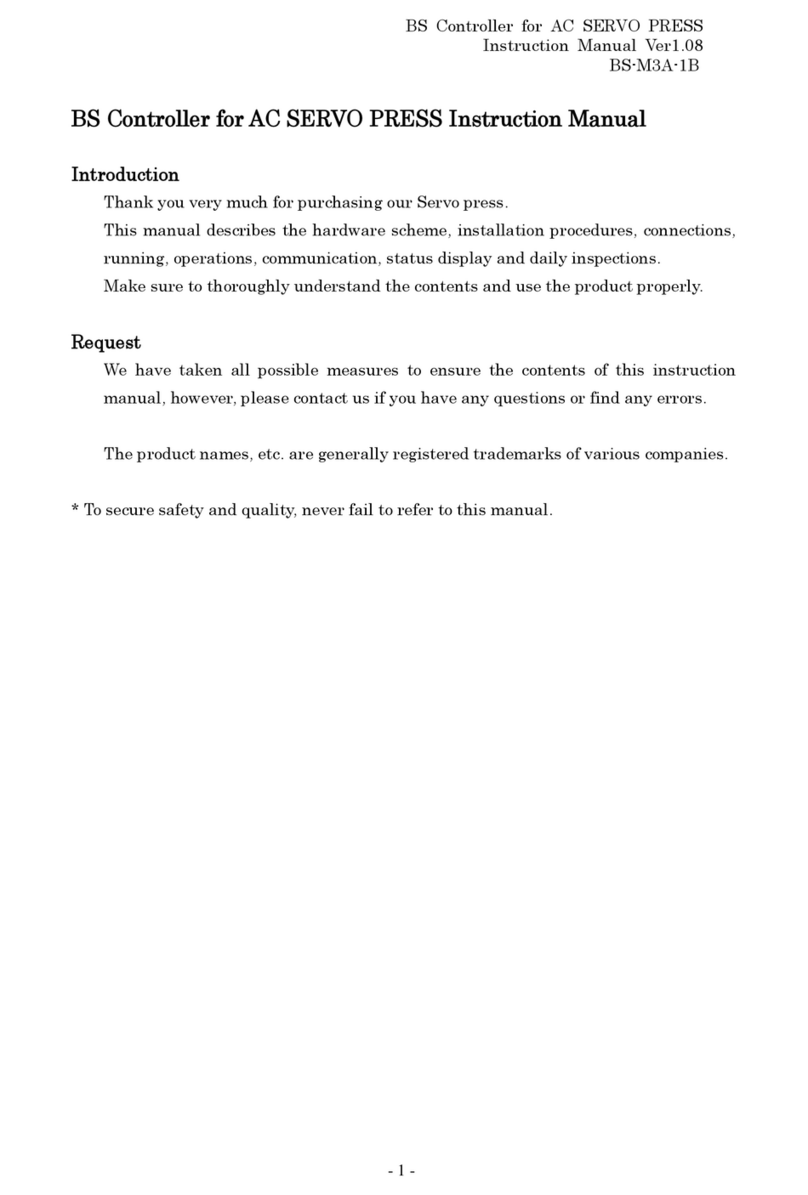
Coretec
Coretec BS Series instruction manual

Siemens
Siemens Albatros2 RVA78.690 user manual
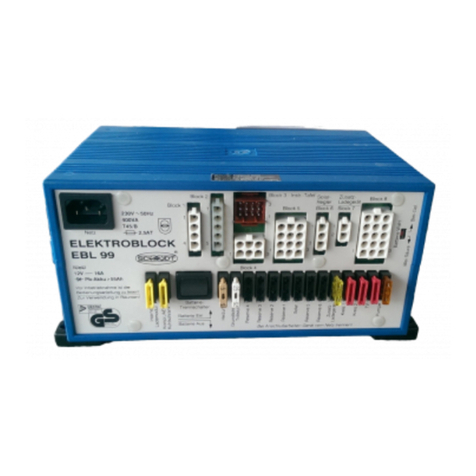
Schaudt
Schaudt Electrobloc EBL 99 G instruction manual
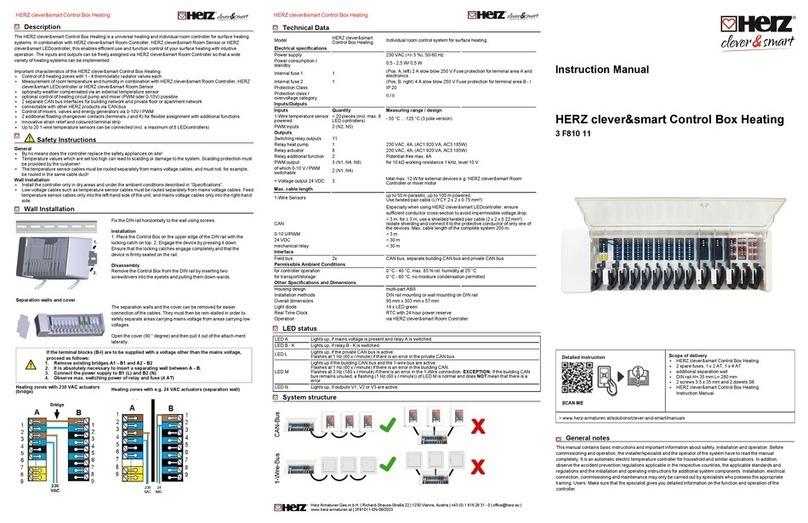
Herz
Herz clever&smart Control Box Heating instruction manual
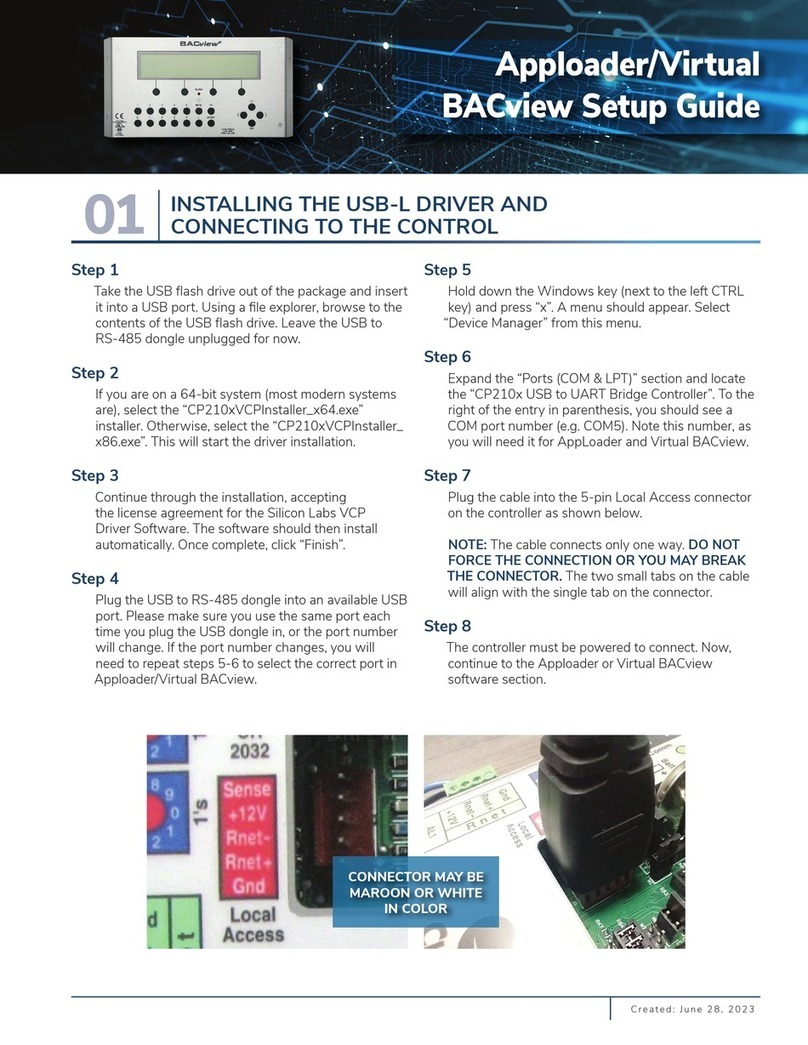
ClimateMaster
ClimateMaster BACview Setup guide