Micronor MR340-1 User manual

© COPYRIGHT 2018-2022, MICRONOR AG
REGENSDORF, SWITZERLAND
MR340-1
Fiber Optic Incremental Encoder
DIN Rail Mount Controller
Instruction Manual
Includes MR343 Linear Encoder
Application Information
Document: 98-0340-12
Revision: C
For Sales & Support in North America:
MICRONOR SENSORS, INC.
2085 Sperry Ave, Suite A-1
Ventura, CA 93003 USA
+1-805-389-6600
sales@micronor.com
www.micronor.com
HQ and Worldwide Support:
MICRONOR AG
Pumpwerkstrasse 32
CH-8105 Regensdorf
Switzerland
+41-44-843-4020
sales@micronor.ch
www.micronor.ch
Notice of Proprietary Rights
The design concepts and engineering details embodied in this manual, which are the property of MICRONOR AG,
are to be maintained in strict confidence; no element or detail of this manual is to be spuriously used, nor disclosed,
without the express written permission of MICRONOR AG. All rights are reserved. No part of this publication may
be reproduced, stored in a retrieval system, or transmitted in any form or by any means, electronic, mechanical,
photocopying, recording, or otherwise, without prior written permission from MICRONOR AG.
IMPORTANT NOTE
The MR340-1 Controller is a rebranding, part number change only
of the original MR302-1 DIN Controller. Any references to MR302-1
are applicable to the MR340-1 and vice versa. In addition, the former
MR303 Linear Encoder is now the MR343, and the former MR304
Mini Rotary Encoder is now the MR341.
The core dual wavelength 850nm/980nm optical technology of the
MR302 series replaces the 850nm/1300nm technology of the earlier
MR320 series, becoming the MR340 series. For more information on
the MR340 series Controller and Encoders and their compatibility
with earlier models, please consult Application Note AN127.

MICRONOR AG MR340-1 DIN Rail Module Controller
Page 2 of 74
Revision History
REV
Date
Technical
Representative
Notes
A
6/22/2018
DNH
Initial Release-Same as MR302-1
B
3/6/2019
DNH
Analog output mode definition corrected in table
C
9/12/2022
DNH
•Changed all MR302-1 DIN Controller references to
MR340-1
•Changed all MR303 Linear Encoder references to
MR343
•Changed all MR304 Rotary Encoder references to
MR341
•Deleted references to obsolete MR302-2 / MR340-
0 OEM Controller (also formerly MR340-0)
•
Updated product ownership to Micronor AG

MICRONOR AG MR340-1 DIN Rail Module Controller
Page 3 of 74
Table of Contents
Revision History ...........................................................................................................2
1. Product Description ............................................................................................. 6
1.1 Incremental Encoder Background..................................................................6
1.2 Fiber Optic Incremental Sensor ..................................................................... 6
2. Initial Preparation .................................................................................................8
2.1 Unpacking and Inspection ............................................................................. 8
2.2 Damage in Shipment ..................................................................................... 8
2.3 Standard Contents.........................................................................................8
2.4 Warranty Information .....................................................................................9
3. Installation and Operation.................................................................................. 10
3.1 Mounting the Sensor Unit............................................................................ 10
3.2 Mounting the MR340-1 Controller Module.................................................. 11
3.3 Optical Connections to the Controller ......................................................... 12
3.3.1 Cleaning Fiber Optic Connections........................................................ 13
3.4 Electrical Connections To Controller............................................................ 14
Main Electrical Connections.................................................................. 14
Interfacing With a Motor Drive.............................................................. 15
SSI and RS485 Interface Connections (J3)............................................. 16
USB Interface (J2).................................................................................. 17
Programmable Analog Output – Current or Voltage Connections........ 17
3.5 How To Install the MR343 Linear Encoder ................................................... 19
Film Mounting and Handling With MR343............................................ 19
Initial Optical Power Level Referencing When Using Film..................... 21
Indexing for Linear Absolute Position ................................................... 22
3.6 Power-up or Periodic Optical Sensitivity Calibration.................................... 23
Optical sensistivity calibration for linear sensors ................................... 23
Optical sensititivty calibration for rotary sensors................................... 23
3.7 Initial System Configuration and Power-Up Examples.................................. 24
Rotary Encoder Configuration and Operation....................................... 24
Linear Encoder With Film And Using HOMING Function...................... 26
Linear Encoder With Film Without HOMING Region ............................ 28
4. Modbus Serial Communications......................................................................... 30
4.1 Modbus Serial Interface ............................................................................... 30
4.2 MODBUS Communications Protocol ........................................................... 32
4.3 Detailed Description of Each Function......................................................... 40
Counter (Register 0x001) ...................................................................... 40
Speed /RPM output (Register 0x003).................................................... 40
Voltage Mode (Register 0x200)............................................................. 41
Voltage Scale (Register 0x201).............................................................. 42

MICRONOR AG MR340-1 DIN Rail Module Controller
Page 4 of 74
Voltage Filter (Register 0x203).............................................................. 43
Current Mode (Register 0x204)............................................................. 44
Current Scale (Register 0x205).............................................................. 47
Current Filter (Register 0x207) .............................................................. 47
Counter Reset Mode (Register 0x208) .................................................. 48
Counter Reset (Register 0x209)............................................................. 49
Quadrature Edge Multiplier (Register 0x211)........................................ 49
Turn Direction (Register 0x20B) ............................................................ 50
Line Driver Output Voltage (Register 0x214)......................................... 51
Analog Output Select (Register 0x215)................................................. 51
EEPROM SET (FC05-2).......................................................................... 52
4.4 Error Handling and Troubleshooting ........................................................... 53
Explanation of Status and Error Handling ............................................. 53
Explanation of Status and Error Indication ............................................ 53
Reading The Error Counters ................................................................. 58
5. Specifications ..................................................................................................... 59
5.1 MR340-1 DIN Rail Mount Controller ............................................................ 59
5.2 MR343 Linear Sensor ................................................................................... 60
6. ZAPPY® 302 SOFTWARE................................................................................... 61
6.1 How To Install and Use Zappy® 302............................................................ 61
6.2 ZAPPY® Menu Screens................................................................................ 61
System Functions screen....................................................................... 61
User Functions screen........................................................................... 63
Service Functions screen....................................................................... 64
Command List screen ........................................................................... 65
7. MR340 Theory of Operation............................................................................... 66
8. MR340-1 Reprogramming the Firmware ............................................................ 68
8.1 DAMAGED Firmware Recovery ................................................................... 71
9. Mechanical Reference Drawings......................................................................... 72
9.1 MR340-1 Controller .....................................................................................72
9.2 MR343 Linear Sensor ................................................................................... 72

MICRONOR AG MR340-1 DIN Rail Module Controller
Page 5 of 74
Figures
Figure 1. MR340 Series Fiber Optic Encoder System Family....................................... 6
Figure 2. Typical MR340 Encoder System connections to User’s Motion Control System 7
Figure 3. MR340 Controller works with MR343 Linear and all MR34X Rotary Sensors10
Figure 4. Keep LC Duplex connector ends protected when not in use ..................... 10
Figure 5. Mounting Controller to 35mm DIN Rail ..................................................... 11
Figure 6. Mounting Controller to Wall Using Screws................................................. 11
Figure 7. Connecting Sensor to Controller Optical Interface .................................... 12
Figure 8. Clean Receptacle with the supplied Cleaning Stick..................................... 13
Figure 9. Clean Optical Plug with supplied Clean Wipes .......................................... 13
Figure 10. Typical MR340 Encoder Sensor System connections to Motion Control System
........................................................................................................................... 14
Figure 11. J1-Connector Pin Assignments ................................................................ 15
Figure 12. Typical MR34X Rotary Encoder System connections to Motor Drive System15
Figure 13. Location of SSI, RS485/Modbus RTU, and USB Connections ................... 16
Figure 14. J3-Connector Pin Assignments ................................................................ 16
Figure 15. Hirose Plug for J3-Connector................................................................... 16
Figure 16. Connection for 4-20mA current loop ........................................................ 17
Figure 17. Connection for Voltage Output................................................................ 18
Figure 18. Positioning film inside MR343 sensor....................................................... 19
Figure 19. TD5334 Encoder Filmstrip dimensions..................................................... 20
Figure 20. Location of internal CAL button for initial optical level calibration ........... 21
Figure 21. ZAPPY® System Functions screen............................................................ 62
Figure 22. ZAPPY® User Functions screen................................................................ 63
Figure 23. ZAPPY® Service Functions screen............................................................ 64
Figure 24. ZAPPY® Command List screen ................................................................ 65
Figure 25. Block Diagram of MR340-1 Controller ..................................................... 66

MICRONOR AG MR340-1 DIN Rail Module Controller
Page 6 of 74
1. Product Description
1.1 Incremental Encoder Background
Incremental encoders are typically used to sense the motion and speed of a motor shaft.
Typically the encoder outputs two phase-shifted signals. Depending on the direction of
movement, the phase shift is either +90° or -90°, this signal is referred to as the Quadrature
Signal.
Typically these encoders incorporate electronics and are susceptible to electrical interferences
(EMI/RFI). Examples include:
•Pipe and tube welding produces extreme interference
•MRI machines operate under an extremely strong electromagnetic field
•Surgical robots must perform 100% reliably
•Aerospace actuators operate in and around other noise generating avionics
An all-optical, non-electronic passive solution such as the fiber optic encoder provides
completely immunity to such interferences.
1.2 Fiber Optic Incremental Sensor
The MR340 series is Micronor’s 3rd Generation fiber optic incremental encoder system. It’s
innovative all-optical design offers immunity to any electro-magnetic interference such as
lightning, radiation, magnetic fields and other harsh environmental conditions. The fiber optic
aspect of the sensor also makes it perfectly suited for long distance speed and position
sensing over hundreds of meters without being affected by ground loop problems.
Figure 1. MR340 Series Fiber Optic Encoder System Family

MICRONOR AG MR340-1 DIN Rail Module Controller
Page 7 of 74
Figure 2. Typical MR340 Encoder System connections to User’s Motion Control System

MICRONOR AG MR340-1 DIN Rail Module Controller
Page 8 of 74
2. Initial Preparation
2.1 Unpacking and Inspection
The unit was carefully inspected mechanically and electrically before shipment. When
received, the shipping carton should contain the following items listed below. Account for and
inspect each item before the carton is discarded.
In the event of a damaged instrument, write or call your nearest MICRONOR AG local
representative or Swiss HQ.
Please retain the shipping container in case re-shipment is required for any reason.
2.2 Damage in Shipment
If you receive a damaged instrument you should:
1) Report the damage to your shipper immediately.
2) Inform MICRONOR
3) Save all shipping cartons.
Failure to follow this procedure may affect your claim for compensation.
2.3 Standard Contents
MR340-1 Controller Module:
•MR340-1 Controller
•Instruction Manual (this document, one soft copy supplied per shipment when a
complete encoder/controller system is purchased.
MR341, MR342, MR344, MR345, MR346, MR348 Rotary Sensors:
•MR34X series sensor with optical interface option (IP-LC receptacle or Duplex LC
pigtail) as ordered. See individual data sheets for decoding of ordering part
number.
MR343 Linear Sensor:
•MR343 series sensor with Duplex LC optical pigtail as ordered. See individual data
sheet for decoding of ordering part number.
Both this Instruction Manual and ZAPPY® 302 software can be downloaded
from www.micronor.com

MICRONOR AG MR340-1 DIN Rail Module Controller
Page 9 of 74
2.4 Warranty Information
Warranty
MICRONOR AG warrants this product to be free from defects in material and workmanship for
a period of 1 (one) year from date of shipment. During the warranty period, we will, at our
option, either repair or replace any product that proves to be defective.
To exercise this warranty, write or call your local MICRONOR representative or contact
MICRONOR AG headquarters. You will be given prompt assistance and return instructions.
Send the instrument, transportation prepaid, to the indicated service facility. Repairs will be
made and the instrument returned transportation prepaid. Repaired products are warranted
for the balance of the original warranty period, or at least 90 days.
Limitations of Warranty
This warranty does not apply to defects resulting from unauthorized modification or misuse of
any product or part. This warranty also does not apply to Fiber Optic Connector interfaces,
fuses or AC line cords. This warranty is in lieu of all other warranties, expressed or implied,
including any implied warranty of merchantability of fitness for a particular use. MICRONOR
INC. shall not be liable for any indirect, special or consequent damages.
For sales and service in North America:
Micronor Sensors, Inc. Tel +1-805-389-6600
2085 Sperry Ave, Suite A-1 Email sales@micronor.com
Ventura, CA 93003 URL www.micronor.com
USA
HQ and Worldwide Sales & Support:
Micronor AG Tel +41-44-843-4020
Pumpwerkstrasse 32 Email sales@micronor.ch
CH-8015 Regensdorf URL www.micronor.ch
SWITZERLAND

MICRONOR AG MR340-1 DIN Rail Module Controller
Page 10 of 74
3. Installation and Operation
3.1 Mounting the Sensor Unit
A broad range of MR34X rotary and linear sensors will work in conjunction with the MR340-1
Controller. Each MR34X sensor requires its own dedicated MR340-1 Controller.
MR34X series Rotary Encoders offer resolution up to 1024ppr.
MR343 series Linear Encoder is a special read-head sensor that can be used to measure linear
movement. It is constructed of both non-metallic and non-ferrous materials. The sensor is safe
for use within or around MRI equipment, or within other extreme electromagnetic fields.
Figure 3. MR340 Controller works with MR343 Linear and all MR34X Rotary Sensors
When installing the sensor, be careful not to bend the fiber excessively. It is recommended to
keep the minimum bend radius 25mm (1”) or larger. Ensure the fiber outlet at the encoder is
protected from excessive pulling or bending.
Figure 4. Keep LC Duplex connector ends protected when not in use
Make sure fiber optic connector tips are always covered when not in use. Always clean and
inspect the connector ends before mating to interface.

MICRONOR AG MR340-1 DIN Rail Module Controller
Page 11 of 74
Be sure to use proper fiber optic cleaming tools and procedures such as the Micronor
MR321C Cleaning Kit. Improper tools and/or processes may damage or contaminate the
optical interface.
3.2 Mounting the MR340-1 Controller Module
The controller unit mounts on standard 35mm DIN rail or it can be screw mounted to a wall or
cabinet. For DIN rail mounting, insert clip to the unit and then clip onto DIN rail by bending
the clip tabs toward the enclosure. When screw mounting, remove clip from enclosure and
use screws to affix clip to the wall and then clip enclosure onto the plastic clip. Both mounting
schemes are shown below in Figure 3 and Figure 4.
Figure 5. Mounting Controller to 35mm DIN Rail
Figure 6. Mounting Controller to Wall Using Screws

MICRONOR AG MR340-1 DIN Rail Module Controller
Page 12 of 74
3.3 Optical Connections to the Controller
A duplex fiber optic cable is used to interconnect the sensor and controller. The sensor
incorporates a 1.5m optical pigtail (or as specified by customer). If a longer connection to the
controller is required, then an extension fiber cable having duplex LC connector may be used.
Remove the dust cap form the connector on the cable and open the spring-loaded cover of
the receptacle on the controller. Insert the LC connector as shown. There should be a positive
click when the connector is engaged properly.
Do not force the Fiber Optic Connector!
Figure 7. Connecting Sensor to Controller Optical Interface
This is the same fiber used in local area networks (LANs). The cable ends must be terminated
with high quality Duplex LC connectors and meet these optical performance requirements:
•Multimode Fiber 62.5/125µm, 0.275NA
•Insertion loss <0.5dB,
•Return loss >20dB
•End-face geometry per TELCORDIA GR-326-CORE or equivalent

MICRONOR AG MR340-1 DIN Rail Module Controller
Page 13 of 74
3.3.1 Cleaning Fiber Optic Connections
•Fiber Optic connectors must be kept clean from dust and other contaminants.
•Always keep unmated connectors covered with an appropriate dust cap.
•Do not touch the connector ends.
Before mating - clean BOTH connector ends as shown below in Figure 6 and Figure 7.
Figure 9. Clean Optical Plug with supplied Clean Wipes
Figure 8. Clean Receptacle with the supplied Cleaning Stick

MICRONOR AG MR340-1 DIN Rail Module Controller
Page 14 of 74
3.4 Electrical Connections To Controller
Figure 10.Typical MR340 Encoder Sensor System connections to Motion Control System
The MR340-1 controller requires a 24V DC power supply delivering a minimum of 100mA
current. The Fiber Optic Sensor shall be connected via the Duplex LC Fiber Optic cable. Fiber
Optic extension cables interconnected via Duplex LC mating adapters may also be used.
Connections from the controller to the users equipment depends on the application. For a
motor drive controlling the speed, the quadrature signals must be connected to the encoder
inputs of the motor drive. The user can configure the differential outputs to provide 5V, 12V or
24V signal levels. The factory setting is 5V. (Consult section 8.1 User Parameter Settings)
If the sensor system is used to display position or speed, an analog panel meter may be
connected to the analog signal output (SIG+/SIG-). The output can be programmed for either
Voltage (±10V) or current (4-20mA) as well as freely scaled to indicate either position or
speed. (Consult section 8.1 User Parameter Settings)
An external HOMING Input is available to connect a “Homing Switch” allowing the system to
calibrate to an absolute position at start-up. This input offers additional functionality. Consult
Section 3.7.2 for additional information.
Main Electrical Connections
The unit is powered by 24 VDC with maximum 100mA current consumption.
Encoder output levels are User Selectable via Zappy® 302: 5V, 12V or 24V
Serial Interface is Modbus RS485/RS422 compatible.
Default baud-rate 57600, 8bit, 1 stop, no parity
Default address 235

MICRONOR AG MR340-1 DIN Rail Module Controller
Page 15 of 74
J1 Interface Connections
10C Screw Terminal Plug, Accepts 14 AWG to 30 AWG wires
Phoenix P/N 1803659 (one supplied with the controller)
Pin
Function
Notes
1
+24V
Power Supply, 50mA Typical
2
GND
3
INPUT
+24V Homing Input for Calibrating
Absolute Position
4
GND
5
SIG+
User Selectable Analog Output:
±10V or 4-20mA
6
SIG-
7
A+
User Selectable A/B Quadrature Output
Level:
5V, 12V, 24V:
8
A-
9
B+
10
B-
Figure 11. J1-Connector Pin Assignments
Interfacing With a Motor Drive
One common application for any encoder is to provide position and velocity information to a
servo drive. In this example, the A/B quadrature signals are connected directly to the encoder
inputs of the servo drive which internally tracks the motor status.
Figure 12.Typical MR34X Rotary Encoder System connections to Motor Drive System

MICRONOR AG MR340-1 DIN Rail Module Controller
Page 16 of 74
SSI and RS485 Interface Connections (J3)
Connector J2 provides USB interface with Type B connection.
Connector J3 provides both RS485 and SSI interfaces.
Figure 13. Location of SSI, RS485/Modbus RTU, and USB Connections
Figure 14. J3-Connector Pin Assignments
Default Baud rate is: 57600, 8 bit data, 1stop bit, no parity bit
Connector Plug: Hirose P/N 3240-10P-C(50)
Digikey P/N H11343-ND
Mouser P/N 798-324010PC50
Recommended Cable:
Tensility International P/N 30-00534
Digikey P/N T1355-5-ND
Micronor P/N MR430-99-01 (available separately) is a pre-
assembled pigtail assembly with 1m pigtail
Figure 15. Hirose Plug for J3-Connector
RS485 via J3
SSI via J3
MR430-99-01
Color Code
Pin
Function
Function
Color
1
+5V
+5V
Brown
2
RS422 – RCV- (input)
Red
3
RS422 – RCV+(input)
Orange
4
RS422 – TX- (output)
Yellow
5
RS422 – TX+(output)
Green
6
GND
GND
Blue
7
SSI-CLK-
Purple
8
SSI-CLK+
Grey
9
SSI-DAT-
White
10
SSI-DAT+
Black
NOTE: Pin 1 (+5V Power) can be used to power an RS232 to RS485 converter.

MICRONOR AG MR340-1 DIN Rail Module Controller
Page 17 of 74
USB Interface (J2)
For configuring the controller parameters, the USB interface (J2) is best used along with the
ZAPPY®302 software. Communication is via the FTDI chip (www.ftdichip.com) and the
computer must have the Virtual Comp Port (VCP) interface driver installed. If internet access is
available, Windows operating systems will install the driver automatically when the unit is
plugged in the first time. If not, visit the FTDI website and search for the VCP driver
appropriate for your operating system.
Note: The controller module is not USB powered and requires an external 24V power supply.
Programmable Analog Output – Current or Voltage Connections
The analog output of the MR340-1 Controller is user settable for either current or voltage
output. This section assumes that the user has already programmed the analog output for
one of these modes – using the supplied ZAPPY®302 configuration software.
An internal relay configures the function of terminals 5 and 6 to either
current output or voltage output.
•When set to current mode, the terminals 5 & 6 are isolated.
•When set to voltage output, terminal 5 is the positive output
and terminal 6 is internally connected to system GND with
terminals 2 and 4.
Current Output Connection
The current output of the MR340-1 controller is an isolated, loop-powered current source. The
user must provide an in line power source for proper operation.
Figure 16. Connection for 4-20mA current loop

MICRONOR AG MR340-1 DIN Rail Module Controller
Page 18 of 74
The current loop requires a voltage source. However that voltage source may come from the
same power supply which powers both the encoder controller and the 4-20mA current
receiver.
The MR340-1 current output has an internal voltage requirement of 7.5V. Thus the maximum
burden including wiring resistance should be less than:
•Rbmax = (24V – 7.5V) / 20mA = 825ohm.
•In practice, the burden resistance should not exceed 500 ohms.
CAUTION
Before connecting a voltage source to the Current output, make sure to
set this parameter to current output. Otherwise the voltage output will
attempt to drive against the applied voltage source.
Voltage Output Connection
The current output of the MR340-1 controller is an isolated, loop-powered current source. The
user must provide in line power source for proper operation.
Figure 17. Connection for Voltage Output

MICRONOR AG MR340-1 DIN Rail Module Controller
Page 19 of 74
3.5 How To Install the MR343 Linear Encoder
Film Mounting and Handling With MR343
Although the film positioning within the sensor slit is not critical, it should be mounted in such
a way that it is as parallel to the sensor pick-up head as possible. Ideally the film should be
mounted so it is perpendicular to the sensor head and always lay against one side of the slit.
The film should be prevented from wobbling within the slit.
Emulsion side of film must face side where the fiber enters the sensor.
Be careful when handling film to not leave fingerprints.
After film strip is inserted into sensor, either use the supplied clip or cover to
secure film and maintain proper alignment.
Figure 18. Positioning film inside MR343 sensor
To protect the film from scratches where the light senses the lines, the assembly has a slight
recess. It is therefore important that the film is operated sliding at the bottom of the assembly.
The high precision optical read head is very high precision and is sensitive to scratches or dust
on the film. Scratches of 50µm or more can cause an erroneous pulse.

MICRONOR AG MR340-1 DIN Rail Module Controller
Page 20 of 74
Positioning the film affects the ultimate
performance of the system. Apply just
enough pull to the film so as it is stretched at
all times. Too much pull will increase pressure
on the read surface and may lead to high
wear of the film. Typically 50-100 grams of
pull force is sufficient.
When using a film with 0.4mm line spacing, it is posible to obtain 0.1mm resolution. Consult
Figure 15 below for recommended film strip dimensions. Each opaque and translucent cycle
will need to be a total of 400µm.
Figure 19. TD5334 Encoder Filmstrip dimensions
As can be seen in Figure 15, positional accuracy is given by the film itself and the shape of the
light beam. The film is made accurately to within ±3µm. The absolute edge accuracy is
approx. ±25% of the slit width. With the design, as shown above, the very worst case
deviation is ±50µm maximum. Typically ±25µm can be expected.
Thermal expansion of the film tape is typically 22µm/m/°C. With the temperature variation
within an MRI environment being minimal, this deviation is not a factor in accuracy when
operating at normal room temperature. The film base material is highly stable.
To obtain a balanced signal with a duty cycle of 50% and a phase shift of 90°, the distance
from the optical fiber to the film must be accurately controlled within the pick-up assembly.
This is a factory-only adjustment.
400µm
100µm
850nm
980nm
Table of contents
Other Micronor Controllers manuals
Popular Controllers manuals by other brands
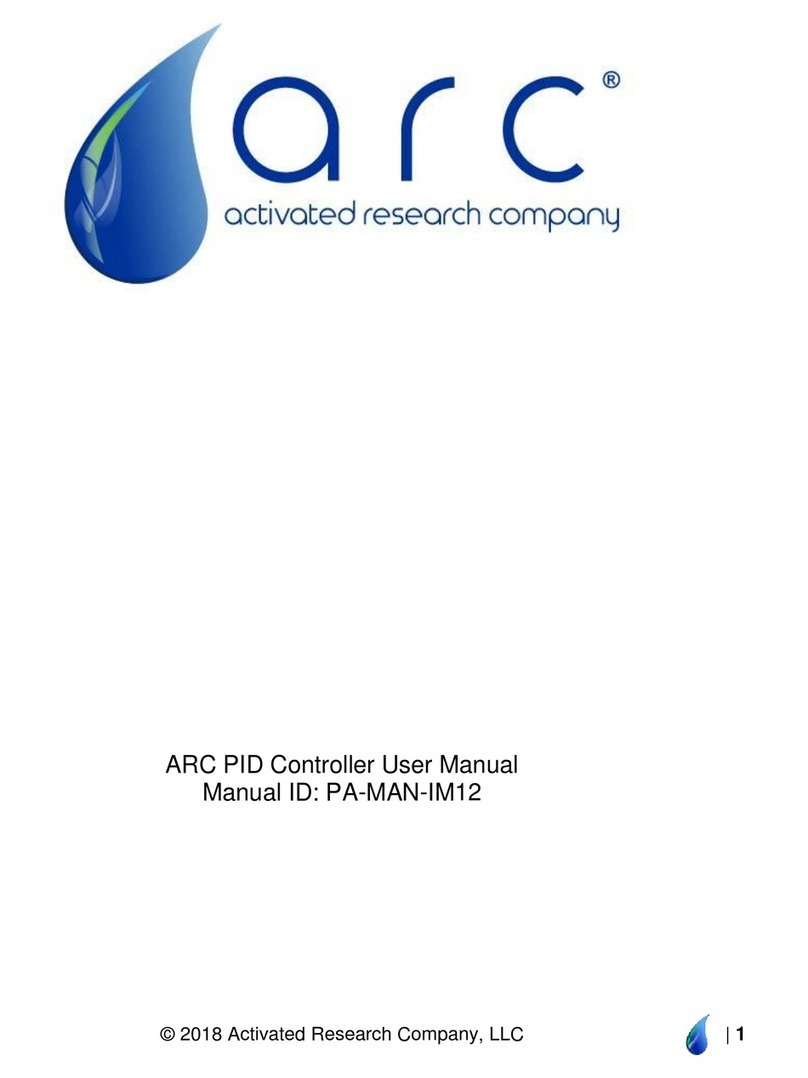
ARC
ARC PID user manual
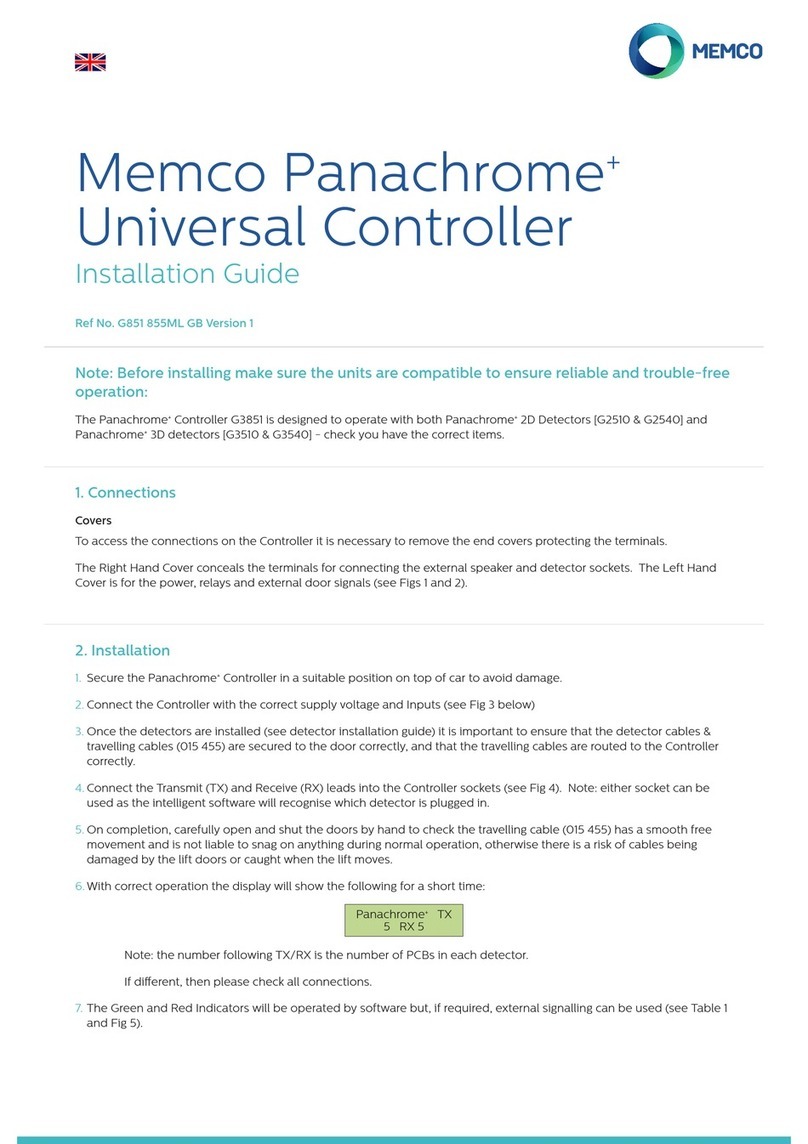
AVIRE
AVIRE Memco Panachrome+ installation guide
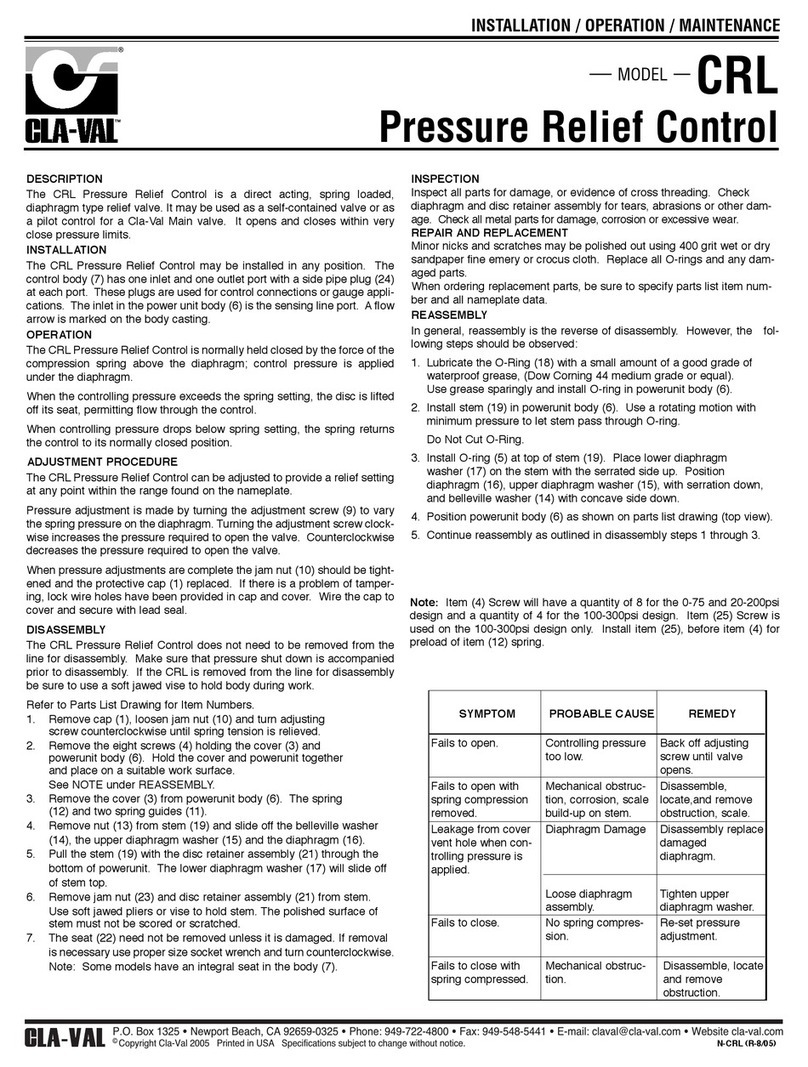
CLA-VAL
CLA-VAL CRL Installation, operation & maintenance manual
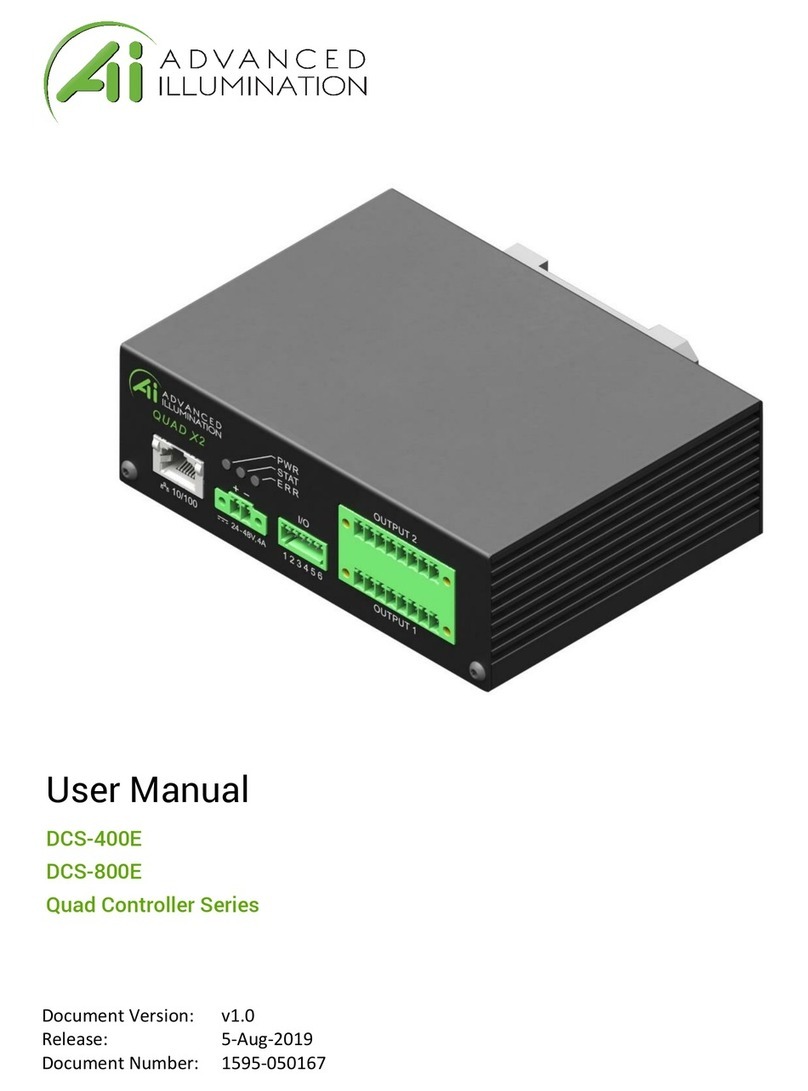
Advanced Illumination
Advanced Illumination Quad Controller Series user manual
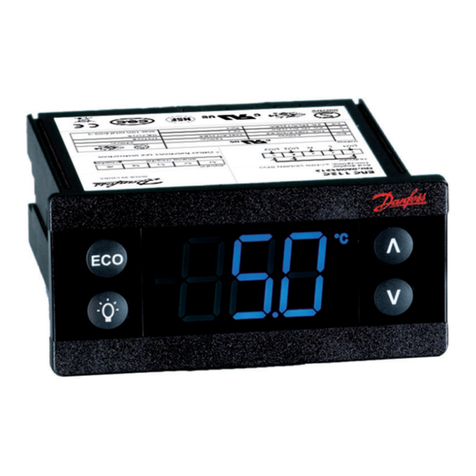
Danfoss
Danfoss erc 112 user manual
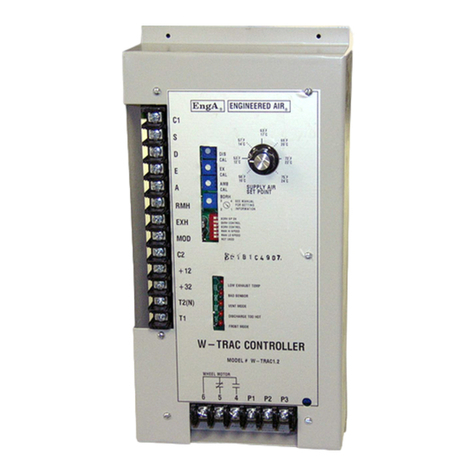
Engineered air
Engineered air EngA W-TRAC Installation, operation and maintenance manual