DUKER 4510 Series User manual

Issue 03 Düker GmbH –www.dueker.de page 1
Operating Instructions
Resilient Seated Butterfly Valves
Type 4510 double flanged
for water/ gas (PN 10/ 16/ 25)
Item no. of the operating instructions: 764848 Issue 03, 2018, 19 pages
Specifications subject to change without notice

Issue 03 Düker GmbH –www.dueker.de page 2
1Intended use 3
2Safety precautions 3
2.1 General safety instructions 3
2.2 Safety instructions for the owner/operator 3
2.3 Special risks 4
3Transport and storage 5
4Pressure test on the pipeline 6
5Installation into the pipeline 6
5.1 General information 6
5.2 Operational steps 7
6Functional description 7
7Drawing and parts list 8
7.1 Drawing 8
7.2 Part list 9
8Operation 10
9Troubleshooting 12
10 Service and maintenance 13
10.1 Maintenance 13
10.2 Replacing the profile sealing 13
10.3 Adjusting the retaining ring 16
10.4 Tightening torque gear flange 17
10.5 Tightening torque blind pin 18
10.6 Tightening torque retaining ring 18

Issue 03 Düker GmbH –www.dueker.de page 3
1 Intended use
After the installation into a pipeline, butterfly valves are only intended for stopping or allowing media to
pass within the range of the permitted operating conditions (temperature and pressure limit "PN" labeling on
the valve, unless stated otherwise).
These valves are preferably intended for liquid media, such as drinking water or gas. Any deviating operat-
ing conditions or areas of application are subject to manufacturer approval.
We will not assume any responsibility for consequential damage caused by
unauthorized modification of the valve and the accessories supplied
improper operating or operating conditions
acts of god
To control in continuous operation shut-off valves are not usable.
Cavitation is definitely to be avoided.
2 Safety precautions
2.1 General safety instructions
The safety regulations applicable to valves are the same as those for the pipeline in which they are installed.
These instructions only specify those safety instructions which have to be additionally noted and observed for
valves.
2.2 Safety instructions for the owner/operator
The owner/operator of the valve is responsible to ensure that the valve is only used as intended.
It is not in the responsibility of the manufacturer. Only competent persons, with suitable qualifications for
pressure pipes, operate and service the valve.

Issue 03 Düker GmbH –www.dueker.de page 4
Do not operate a valve whose permissible component operating pressure ("Ps") and maxi-
mum permissible operating temperature ("Ts") are not sufficient for the operating condition.
The area of application is marked on the valve.
Within the permissible operating temperatures, there is a risk of injury when working on the
piping components at temperatures below 10 ° C and above 40 ° C. Therefore, protective
measures should be taken in these cases.
Operating fluids must comply with the specification of the valve. The manufacturer assumes no
liability for corrosion damage caused by aggressive media. Failure to comply with this require-
ment can endanger life and limb and cause damage to the piping system.
The valve must be properly installed in the pipeline.
In the pipeline the usual flow velocities (e.g. according to EN 1074-1: 2.5 –5 m/s for liquids must not
be exceeded in continuous service.
Abnormal operating conditions such as vibrations, water hammers, erosion, cavitation and greater
fractions of solids in the medium –especially wearing solids –must be clarified with the manufacturer.
2.3 Special risks
Before opening and/ or repairing valve, the pipe must be completely depressurized. The pipe
should be completely emptied before replacing wearing part
For valves used as an end fitting: In normal service a blank flange or a cover must be
mounted on the free pipe connection or the valve must be securely locked in the
"SHUT/CLOSED" position. Caution on closing such a valve: Beware of risk of crushing!

Issue 03 Düker GmbH –www.dueker.de page 5
3 Transport and storage
All valves must be carefully transported and stored.
The valves are fully enameled or powder-coated. The coatings are shock-sensitive and must
be protected against impact stress.
The gaskets are sensitive to light: Unpackaged valves may only be exposed to bright daylight
or ultraviolet light for a very short time. This is why the openings are sealed with protective
caps. Valves must be stored in darkened rooms, in their original packaging with the protective
caps.
In the event of storage over an extended period of time, the storage location should be frost-
protected, cool, dry, dark and free of dust. Alternatively, the valves may also be packed in or-
der to fulfill these conditions.
The valve should be stored on a pallet or similar support and only transported with suitable tools such as
wide straps to its designated point of installation. Do not use chains!

Issue 03 Düker GmbH –www.dueker.de page 6
4 Pressure test on the pipeline
New installed pipelines should be carefully flushed first to wash out all foreign bodies.
Valve open: The test pressure may not exceed the value 1.5 x PN (see valve markings).
Valve closed: The test pressure may not exceed the value 1.1 x PN (see valve markings).
5 Installation into the pipeline
5.1 General information
Only original spare parts from the manufacturer may be installed.
The sealing surfaces of the flanges are designed for mating flanges with smooth sealing
strips, according EN 1092 or Stock Finish according to ANSI B 16.5. Other flange shapes
must be agreed with the manufacturer. Elastomer gaskets according to the DVGW Guidelines
W 270 are recommended, preference is to be given to flange seals with a metal core accord-
ing to EN 1514 Part 1.
The same instructions apply to the installation of Düker butterfly valves in a pipe as for the
connection of pipe elements according to EN 1092 and BS standards. It is assumed that the
corresponding instructions are known and are followed. They are not part of these operating
instructions. The following installation instructions additionally apply to butterfly valves
In order to prevent electrochemical corrosion, the formation of potentials should be avoided
when installed in pipes made of non-corrosive steel. Especially in humid environments, which
lead to condensation on the valve, it is therefore advisable to electrically disconnect the flange
connection elements.

Issue 03 Düker GmbH –www.dueker.de page 7
5.2 Operational steps
Transport the valve to the point of installation in its protective packaging.
Remove all packaging materials from the valve.
Check valve for transportation damage. Damaged valves must not be installed.
Check coating for damages. The coating may be mended with a repair kit.
Ensure that only valves whose nominal pressure and connection dimensions correspond to the
use conditions are installed. See markings on the valve.
Before installing, the valve and the pipe must be cleaned to remove dirt and hard bodies.
Perform a functional test before installation: The valve must open and close correctly.
The mating flange of the pipe must be concentric and plane-parallel.
Butterfly valves can be installed irrespective of the direction of flow.
The preferred installed position is in a horizontal pipe with vertical stem and hand wheel facing
upwards.
The valve should have an adequate ground support.
The connection screws must be uniformly tightened crosswise.
To ensure the function and compliance with the drinking water hygiene standards, only original
Düker original spare parts may be installed.
Whenpushing the valve and the seals into an installed pipe, the distance between the pipe ends
must be that all connection faces and seals remain undamaged. The gap should not be larger
than necessary, to ensure no additional stresses in the pipe during installation.
The valve must be installed stress-free.
6 Functional description
The butterfly valve is a valve for controlling the flow of a fluid in a pipeline. The valve is installed in the pipe
with flange connections. The Düker butterfly valves have a flow optimized, double-eccentrically mounted
disc. The profile seal can easily be readjusted and easily replaced.
The disc is connected to the drive shaft and guided out of the housing. The bearing shafts run in mainte-
nance-free bearings. Through internal and external O-rings, the shafts are sealed.
The butterfly valve can be operated either with hand wheel, Düker installation kit, electric actuator and hy-
draulic or pneumatic rotary actuators. The stop of the slider-crank mechanism is adjustable for the end posi-
tion "CLOSED".
The use of extensions to increase the operating torque during hand wheel operation is not permitted as this
will damage the valve. The valve is closed clockwise and opened in the opposite direction.

Issue 03 Düker GmbH –www.dueker.de page 8
7 Drawing and parts list
7.1 Drawing

Issue 03 Düker GmbH –www.dueker.de page 9
7.2 Part list
item
description
item
description
1
Body
16
O-Ring
2
Gear Box
17
O-Ring
3
Disk
18
O-Ring
4
Retaining Ring
19
Hexagon Head Screw
5
Shaft
20
Washer
6
Non-Drive Shaft
21
Threaded Sleeve lower part
7
Bearing Side A
22
Threaded Sleeve upper part
8
Bearing Side B
23
Grub Screw
9
Profile Seal
24
O-Ring
10
Blind pin
25
Straight Pin
11
Disk for Blind pin
26
Washer
12
Sealing Ring
27
Countersunk Screw
13
O-Ring
28
Countersunk Screw
14
Seal
29
Countersunk Screw
15
Connection Ring
30
Circlip

Issue 03 Düker GmbH –www.dueker.de page 10
8 Operation
butterfly valve with hand wheel
butterfly valve with electric actuator

Issue 03 Düker GmbH –www.dueker.de page 11
Allocation of electrical actuators
To operate normal hand forces are sufficient. When using a rotary device, make sure
that the maximum actuation torques do not exceed 200 Nm.
DN
PN
Düker
Gear Type
AUMA
Reduction Gear
Type
Turns for
OPEN -
CLOSE
MT nom.
Gear
Input
(Nm)
AUMA
Actuator
Type
100
10 - 16
SK I B / F10
-
27
30
SA 07.6
25
125
10 –16
25
150
10 –16
25
200
10
SK II B / F12
16
25
40
250
10
16
25
300
10
50
16
25
350
10
60
16
25
SK III B / F16
31
80
SA 10.2
400
10
SK II B / F12
27
60
SA 07.6
16
SK III B / F16
31
80
SA 10.2
25
450
10
16
25
500
10
110
16
25
SK IV B / F30
43
600
10
SK III B / F16
31
100
16
SK IV B / F30
43
110
25
GP 14.1 (4:1)
172
70

Issue 03 Düker GmbH –www.dueker.de page 12
9 Troubleshooting
Leakage at a connection to the pipeline:
Tighten the flange screws.
If leakage continues: Repair necessary.
Leakage at disc:
Check if valve is 100% closed. If so, check if the valve has been closed with the required torque.
If leakage persists, open / close the valve several times under pressure.
If the valve continues to leak, repair is necessary. Change the rubber seal.
Request replacement parts and instructions from Düker.
Further Hints:
Spare parts are to be ordered with all information of the marking on the valve. Only DÜKER original
parts may be installed.
If it is determined after removal that the housing and / or internal parts are not sufficiently resistant to
the medium, the manufacturer DÜKER should be contacted.
Dysfunction:
Remove and inspect the fitting. If the valve is damaged: Repair is necessary. Request replacement
parts and required instructions from DÜKER.
The valve is sealed by O-rings. Before the blind pin or the connecting ring on the valve is loos-
ened, the pressure in the pipeline must be completely reduced. When replacing wearing parts
(e.g. profile seal or O-rings), the line should be completely emptied. When disassembling the
capital 2 safety instructions must be strictly observed.
Please note that Düker GmbH assumes no liability for damage and malfunctions resulting from
non-compliance with the operating instructions.

Issue 03 Düker GmbH –www.dueker.de page 13
10 Service and maintenance
10.1 Maintenance
It is recommended to operate fittings that remain permanently in one position three to four times a year.
10.2 Replacing the profile sealing
Mark the positon of the retaining ring (4) to the disc (3) (yellow line).
4
3
3
2

Issue 03 Düker GmbH –www.dueker.de page 14
Loosen the countersunk screws (27) of the retaining ring when the valve is closed. Leave grub screws
(23) untouched, because they reproduce the tensioned position of the profile sealing.
27
33
23
3

Issue 03 Düker GmbH –www.dueker.de page 15
Move the disc (3) to the open position and remove the countersunk screws (27).
Remove the retaining ring (4) after removing the countersunk screws (27).
Replace profile sealing (9), remove soiling in sealing area. Check the exact location of the profile
sealing (9) in the retaining groove.
Fill threaded holes for the countersunk screws (27) with glass adhesive.
Tighten the countersunk screw (27) on the retaining ring (4) to the specified torque.
Move the valve disc (3) to the "CLOSED" position.
Pressure test; depending on the pressure level.
4
3
9 (used)
3
2
9 (new)
27
2

Issue 03 Düker GmbH –www.dueker.de page 16
In case of leakage, adjust retaining ring in closed position. To do this loosen grub screws (23) and tighten
countersunk screws (27) with permissible torque. After this operation, turn the grub screws (23) clockwise to
make contact with the surface of the butterfly disc (3).
10.3 Adjusting the retaining ring
The retaining ring (4) can be adjusted in the CLOSED position of the butterfly valve. For this purpose, the
grub screws (26) are released, while the countersunk screws (25) are tensioned with a permissible torque.
After this procedure, the grub screws (26) are to be fixed by turning clockwise
To ensure proper function and compliance with drinking water hygienic requirements, only origi-
nal Düker spare parts may be installed.

Issue 03 Düker GmbH –www.dueker.de page 17
10.4 Tightening torque gear flange
Gearbox attachment A2-70 und A4-70
Dimension
M10
M12
M16
M20
M24
Permissible torque [Nm]
35
150
180
290
500

Issue 03 Düker GmbH –www.dueker.de page 18
10.5 Tightening torque blind pin
10.6 Tightening torque retaining ring
Screws for fixing the blind pin
A2-70 und A4-70
Dimension
M10
M12
M16
M20
M24
Permissible torque [Nm]
35
150
180
290
500
Screws for fixing the retaining ring
Dimension
100 –300
350 –600
700 –1200
Permissible torque [Nm]
7 - 10
10 -12
12 - 15

Issue 03 Düker GmbH –www.dueker.de page 19
The distribution and reproduction of these Operating Instructions, utilization and communication of their con-
tents to others is authorized exclusively for the purpose of ensuring the correct installation and operation of
the Düker product treated in the document. For all other purposes, distribution, reproduction and utilization
of the contents, also in excerpts, is prohibited. Offenders will be held liable for the payment of damages. All
rights reserved in the event of the grant of a patent, utility model or design.
Table of contents
Other DUKER Control Unit manuals
Popular Control Unit manuals by other brands
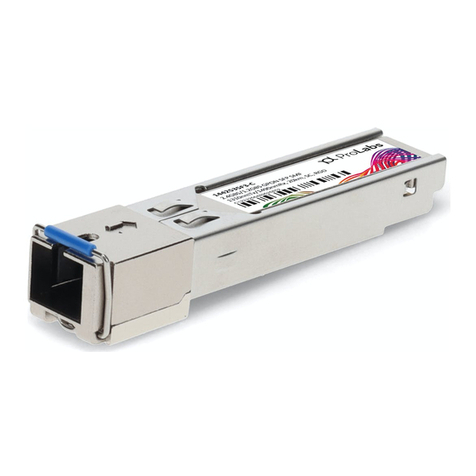
ADTRAN
ADTRAN SFP GPON ONU quick start

Trenz Electronic
Trenz Electronic TE0720 Schematics

Granville-Phillips
Granville-Phillips Series 354 instruction manual
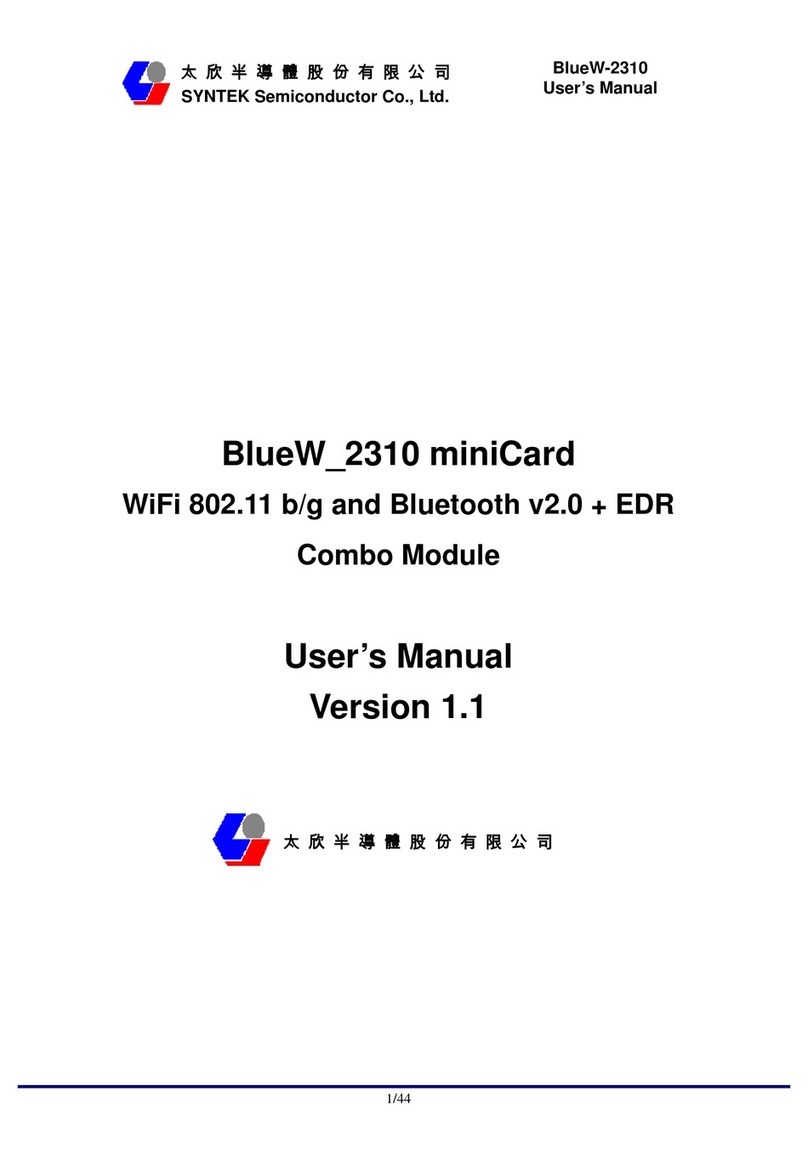
SYNTEK
SYNTEK BlueW 2310 miniCard user manual
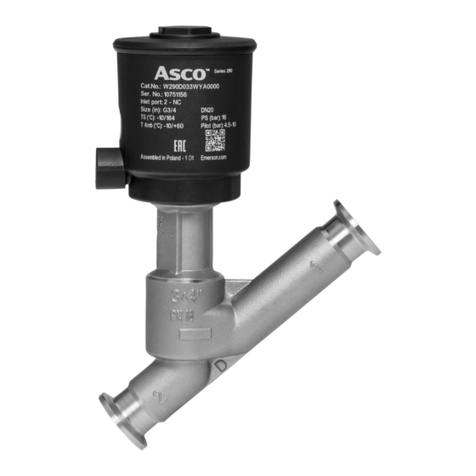
Asco
Asco 290 Series Installation and maintenance instructions
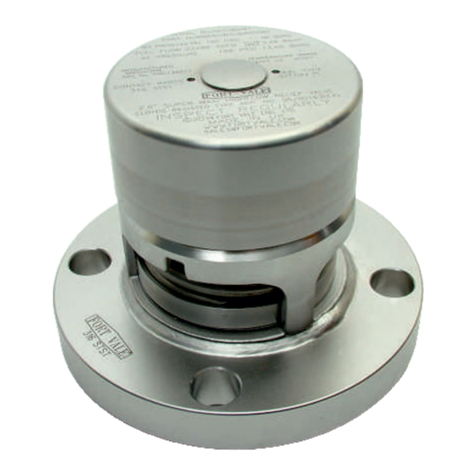
Fort Vale
Fort Vale Super Maxi 0R3/006 Series Maintenance manual

BFT
BFT MOOVI BT 30 Installation and user manual
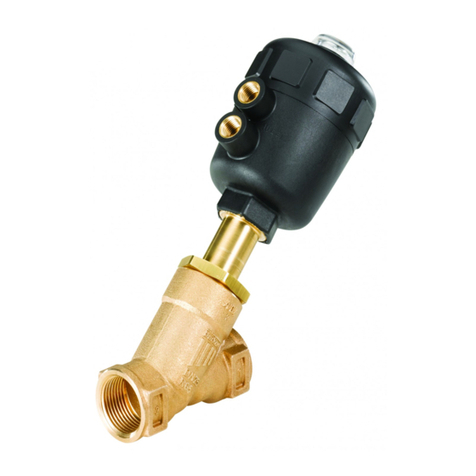
Burkert
Burkert Type 2000 operating instructions
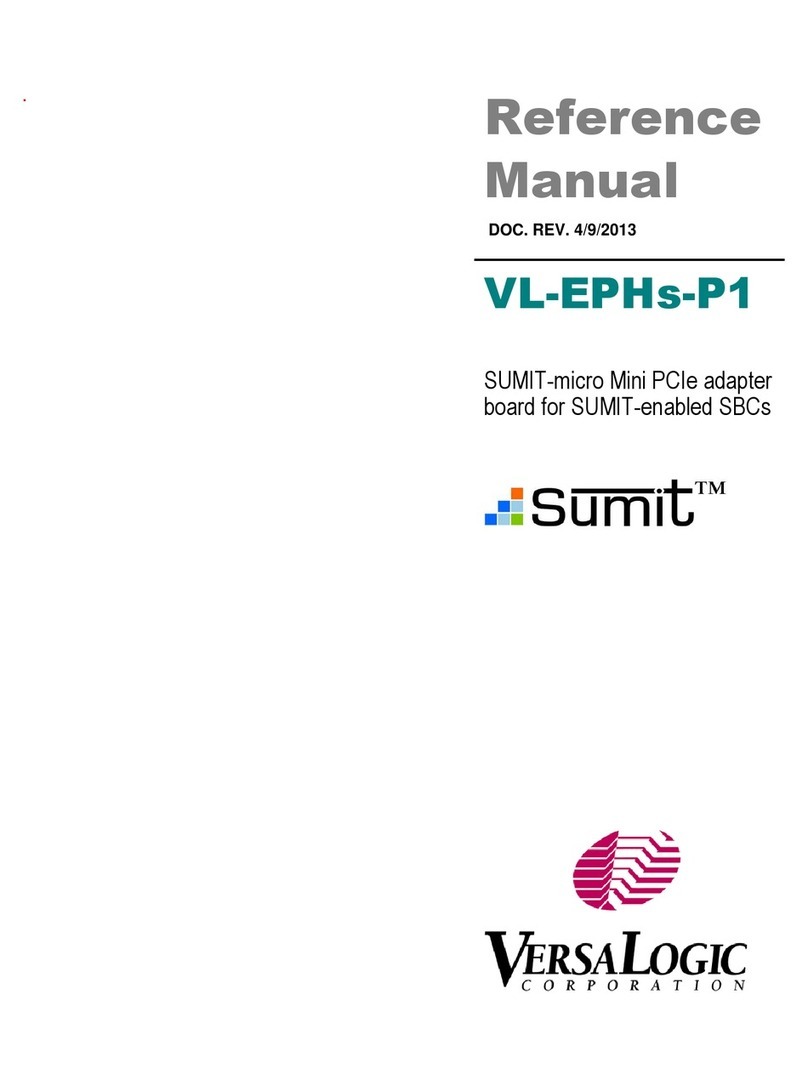
VersaLogic
VersaLogic VL-EPHs-P1 Reference manual
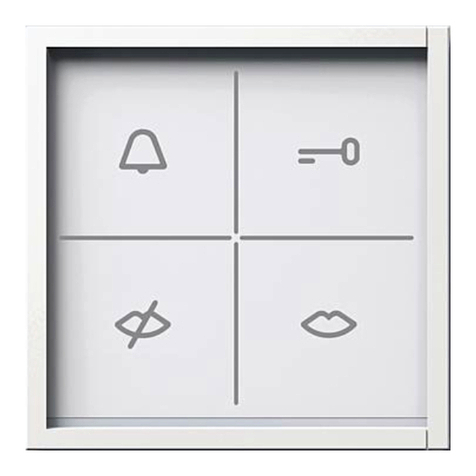
SSS Siedle
SSS Siedle ZAM 600-01 Product information
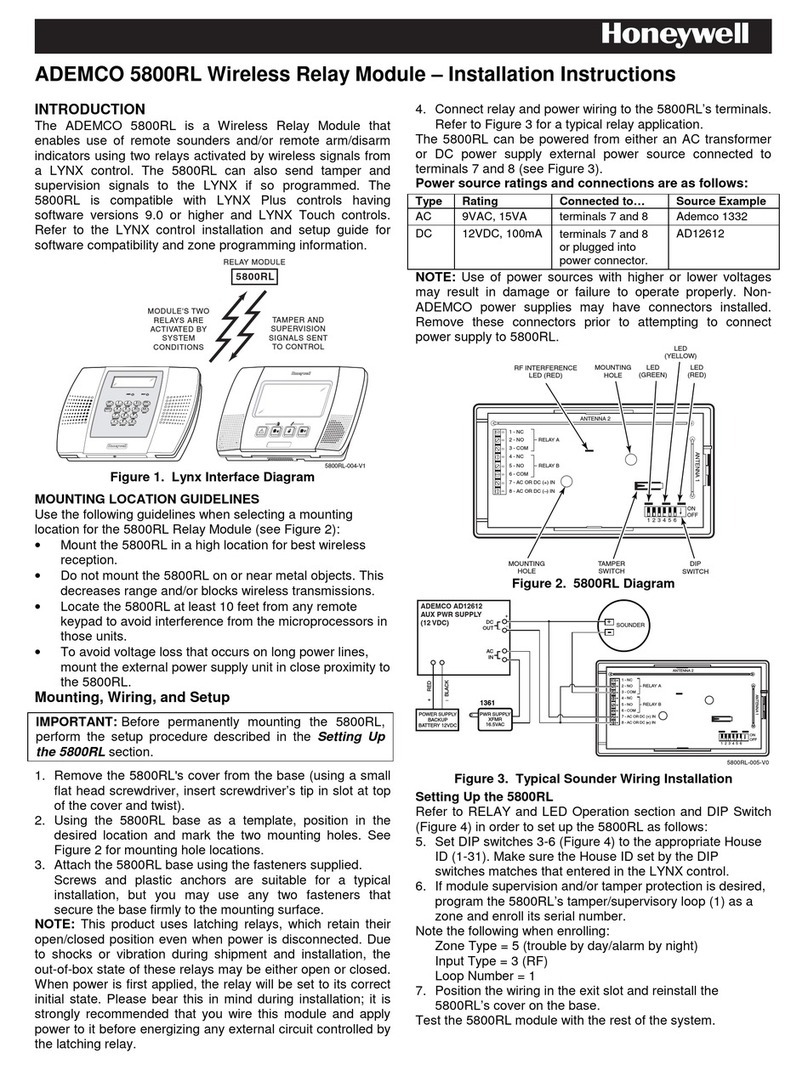
Honeywell
Honeywell ADEMCO 5800RL installation instructions
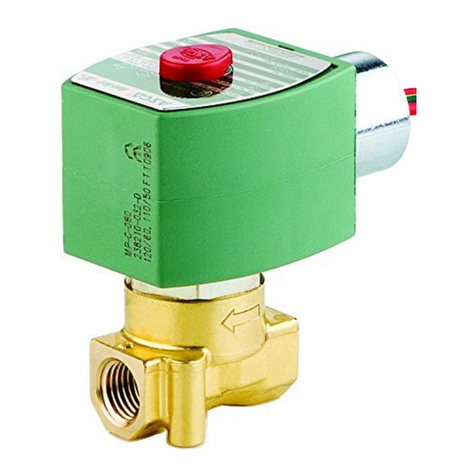
Asco
Asco 8262 series Installation & maintenance instructions