E-MAG E-113 Troubleshooting guide

Product Documentation
Installation &
Operating Guide
V L113.6

Guide Applicable to E-MAG Ignition Models
E-113 and P-113 Ignitions on Lycoming 4 Cylinder
Engines.
Experimental Aircraft Only
E-Mag ignitions are not (currently) certified and are not approved for installation on certified
aircraft.
Warranty
Your E-MAG electronic ignition is warranted for one (1) year from the date of purchase.
Any unit returned must first receive a return authorization number prior to shipping (postage
paid). E-MAG will repair or replace ignition modules within the warranty period that, in E-
MAG’s sole opinion, have not been subjected to abuse or any attempted field repairs.
Note: This represents a reduction in our warranty compared to earlier releases. This has been done in response to the unexpected
impact our previous (3 year) warranty was having on our banking and credit card merchant account relationships. In lieu of a 3 year
“warranty” we have instituted an extremely lenient “policy” of service and support for our products covering 3 years or 1000 hours, which
ever comes first. Caution
The aircraft operator has the SOLE responsibility of determining how to appropriately and
safely control engine leaning. Nothing stated by E-MAG, its employees, owners, agents or
affiliates should be construed as overriding or invalidating the engine manufacturer’s
instructions (including lean operation warnings).
Patents Pending
Copyright © E-MAG Ignitions, All rights reserved.
649 Boling Ranch Road
Azle, Texas 76020
Phone (817) 448 0555

1
Table of Contents
OVERVIEW.......................................................................................................................................................................................................2
DRIVE GEAR....................................................................................................................................................................................................4
CONTROLS ......................................................................................................................................................................................................5
SPARK PLUGS & HARNESS ..........................................................................................................................................................................6
INSTALLATION AND TIMING........................................................................................................................................................................10
OPERATING NOTES......................................................................................................................................................................................13
WIRING DIAGRAM.........................................................................................................................................................................................15
CURRENT DRAW...........................................................................................................................................................................................16

2
Using This Manual
Your E-MAG is designed to make installation as straightforward and as simple as
possible. To further assist you, this manual includes a variety of comments and tips.
These tips are shown in italics and in dark blue for easier identification and printing.
Please note, the term “E-MAG” shall apply to both E-MAG and P-MAG models,
unless specifically stated otherwise.
Installation
Overview
Installing your E-MAG ignition will require you to:
1. Install the drive gear on your ignition.
2. Install wiring:
a. Attach three (four if you use the tack) leads to the Control Plug.
b. Spark plugs and the spark plug harness
c. MAP (manifold pressure) sensor tube
3. Install your E-MAG ignition on the engine, set the timing, select the
maximum timing advance.
CAUTION: Do NOT strike or apply significant inward force to the ignition
shaft. Doing so could cause it to shift, and lose proper position sensor
alignment.
CAUTION: Operating the ignition without all connections – 1) power, 2) ground, 3) p-
lead, 4) plug wires with plugs (and all plugs grounded) can result in damage to the
ignition and/or cause an electrical shock to the installer. Please resist the
temptation to do a quick (incomplete) hook up so you can watch the ignition spark or

3
make the LED light up. Firing the ignition without all connections could damage the
unit, and void your warranty.

4
Drive Gear
E-MAG ignitions are indexed to the engine through a drive
gear. The drive gear from a non-impulse magneto can be
recovered and, if in good condition, be reinstalled on your
E-MAG. Gears from an impulse magneto are different,
and cannot be reused.
To recover the drive gear from an existing magneto:
1. Remove the cotter key, castle nut, and washers. A strap wrench is helpful
while removing (or re-installing) the castle nut from the ignition shaft.
2. Remove the drive gear from the magneto shaft. A gear puller will be
necessary to remove the gear without damaging it, or the magneto.
NEVER strike the magneto or the gear.
3. Install the drive gear on the E-MAG shaft using the woodruff key,
washer(s), castle nut, and cotter key provided. Your kit includes three
washers (one thick and two thin). The thick washer should always be
used. The thinner washers can be used, as needed, to align the hole for
the cotter key with the castle nut when tightened. Make certain the cotter
key ends lay flat and do not extend past the open face of the gear. The
back wall of the accessory case will be close to the face of the drive gear,
and you don’t want any protrusions that can make contact and wear
against the back.
Woodruff Key
installed in shaft

5
Anchor Screws
Controls
Control Wiring – Control leads are connected to the ignition via a Control Plug that
captures each lead with a screw cage mechanism. The plug is then attached to the
ignition and secured with anchor screws on either side. A wiring diagram is included
at the end of this manual. The numbering system for the plug terminals is 1 thru 6 as
viewed looking at the cage screw heads with wires oriented below (see fig). The
wire/plug assignments are as follows: Use the cushioned anchor strap to provide a
mechanical strain relief for the wires.
1. “1” connects directly to a nearby
engine case ground using 18 gauge
wire. Note 1: You cannot rely on the
ignition’s mechanical attachment to the
engine to provide ground. Aluminum
anodizing acts as an electrical
insulator, so the clamp connection to
the anodized flange will not serve as a
reliable ground.
2. “2” Control Alternate (future use)
3. “3” Control Alternate (future use)
4. “4” connects to your ignition
ON/OFF (ground) p-lead switch
using 20 gauge wire or larger.
Note 1: If you are replacing a
magneto, your old P-Lead can
serve this purpose, and may
already be wired to a suitable
switch. Note 2: Non-starting
magnetos require a mechanism to
prevent them from firing during
start-up. Keyed ignition switches
have a jumper on the back that serves this purpose. When installing an E-
MAG in place of a non-starting magneto that was controlled by such a
switch, make sure you remove this jumper. You do NOT want a start-up
block on any circuit controlling your E-MAG(s).
5. “5” connects to your main 12 volt aircraft buss through a dedicated circuit
breaker (not provided) using 18 gauge wire. E-MAGs should use a 5-amp
breaker, and P-MAGs should use a 3-amp switchable breaker. The
switch is needed to test the P-MAG internal alternator during ground run
up – see Operating Notes. Note 1: Whenever the aircraft buss is
powered up, the ignition is “awake”. It draws a small amount of current
Tack
1
Control Plug
4 5 6
3
A
L
T
2
A
L
T

6
MAP hose
connection
LED
Cylinders 1 & 2
Cylinders 3 & 4
LED
Indicator
even when not firing the plugs. Use the main buss switch (or breakers if
necessary) to power down the ignitions when not in use
6. ”6” is a courtesy (optional) connection to provide a digital tack signal – two
pulses per revolution. Note 1: Collect your tack signal from only one, not
both, ignitions. This applies to dual E-MAG ignitions as well as split
systems (E-MAG in tandem with a magneto or other EI). Note 2: Your E-
MAG will generate a tack signal even when it is disabled at the key (or
other) p-lead ignition switch, so you won’t loose tack when you switch the
E-MAG OFF during a preflight ignition check. Note 3: E-MAG’s tack
output is a courtesy feature that is unrelated to the ignition’s primary
purpose. Due to the variety of instrument options available, our ability to
support and troubleshoot tack interface issues is limited.
MAP Sensor
Connect one end of the sensor hose
to the MAP nipple on the back of the
ignition case next to the coil base, and
secure with nylon clamp. Route the
line to a convenient connection point
(connecting hardware not included)
where you can tee into the line going
to your manifold pressure gauge.
Note 1: The MAP sensor is a fail-safe
input; i.e. if the tube comes loose or
fails in-flight, timing will retard to an
operable, but much less efficient
range.
Spark Plugs & Harness
Post Assignments – The plug wire
assignments are as follows:
1. Cylinders 1 and 2 connect to the
coil pair nearest the LED indicator
2. Cylinders 3 and 4 connect to the
coil pair furthest from the LED
indicator.
Note: It does not matter which cylinder is
connected to which post within a given

7
pair. They are completely interchangeable, which can be convenient to help fine
tune the wire lengths.
Aircraft Plugs - One advantage of electronic ignition is the ability to fire across a
wider spark plug gap (0.030” to 0.035” in the case of E-MAG). Some aircraft plug
styles are difficult/impossible to adjust this wide. Plug styles
similar to REM37BY have an extended electrode arm that is
easier to adjust. Caution: You will need to support the base
of the arm when adjusting plug gap, as it can break off where
it attaches to the rim.
Auto Plugs - There are a number of auto spark plug styles
and temperature ranges available through automotive outlets.
E-MAG has NOT undertaken studies to compare the relative durability/suitability of
different plugs. We do offer a standard “starter” plug for convenience. Customers
need to monitor plug condition and evaluate/adjust as necessary. We offer the
following list of plug alternatives that is reported (BY OTHERS) to work.
1. NGK BR8ES 2.5mm Center Electrode (our standard "set-up" plug)
2. NGK BR8ET 3-Ground Electrode
3. NGK BR8EV Gold Palladium Center Electrode
Auto Spark Plug Adapters - Plug adapters permit the
use of 14mm automotive type plugs with a ¾” reach.
[Not suitable with engines that use long-reach (13/16”)
aircraft plugs.] First, install adapters with the supplied
gasket on the spark plugs finger tight. Then, insert in
engine and tighten to 15 in/lb (standard plug torque).
Note: If you install and torque the adapters separately,
stresses will be more focused on the adapter neck and can cause it to fail during
installation.
E-MAG Aircraft Lead Kit – E-MAG’s aircraft plug leads
have traditional “cigarette and spring” threaded fittings
pre-installed on one end of our auto style wires. The hex
cap end attaches to standard 5/8” x 24 spark plugs.
There is currently no harness option for 3/4” x 20 plugs.
The other end connects to the coil and is trimmed, and
fitted in the same manner as our standard Auto Lead Kit –
see below. Note: Aircraft kits use our standard auto wire (not shielded). To date,
we've had no (zero) reports of noise problems from customers using this wire. Even
so, builders have the option, if needed, of adding a shield over the leads and
grounding them at the spark plug end.
E-MAG Auto Lead Kit – E-MAG’s auto style harness is provided as an assembly kit.
It gives the builder greater latitude in routing and permits a cleaner more custom

8
installation. Note: Auto leads should be kept
separated when installed. Do NOT bundle
them together as is common with shielded
aircraft wires, as this can cause them to be
inductively coupled. Wire looms can be
purchased at auto parts stores, but a simple
separator can be fabricated out of tie-wraps
and ¼” segments of left over MAP sensor hose – see photo.
Auto Lead Fabrication
1) Plan your route and lay out one lead at a time, starting with
the longest leads first. Cut leads with about three extra
inches. It will be easier to make the terminal connections at
your workbench, so mark the cut leads so you know where
they belong when you return.
2) Install COIL end boots and terminals (only) on each lead – see “Crimping
Terminals” below. Your lead kit includes 2 extra terminals with each set so
don’t panic if you make a “practice piece”.
3) Connect all four leads to the coil and review the wire
route. You might even install the wire separators (if
you plan to use them) so you can more accurately
determine the correct length. Cut the plug wire end
where it meets the plug tip. Install the spark plug
boots and terminals. Now that you’ve had some
practice with crimping terminals, it may be more
convenient to install them with the wires on the
engine.
4) Crimping Terminals
Identification: The shorter steel terminals and rounded boots are for the
spark plugs. The longer brass terminals and flat-
backed boots are for the coil end attachment.
a) First, run the wire through the boot so it’s a
couple of inches from the end. This will give
you room to work with the wire and terminal.
A light coating of silicone spray (not included)
is needed to lubricate the wire as you work it
through the boot. It is best to push the boot
down the wire (rather than pulling) to avoid
straining the wire core. Note: You can push
on the heel of the boot and straighten the opening so it is aligned with the
wire as you push it through.

9
Bend coil
terminal 90
degrees.
b) Use the Crimp Tool to trim 1” of shielding from the wire end. Use the
largest opening on the tool stripper (position “10”) to GENTLY cut the
shield. Make one cut, and then a second cut with the tool rotated 90
degrees to ensure you cut the insulation all the way around the core. You
can then twist the trimmed wire shield to complete the separation.
Continue twisting as you remove the shield from the core.
c) Free the terminals from their strips with wire cutters.
d) Fold the wire core back against the shield and position in the crook of the
terminal ears, and “Pre-Crimp” the terminal. Pre-Crimping will snug the
ears against the wire shield (for positioning) and point the tips of the ears
inward just enough so they fit in the “W Crimp” slot on the tool.
e) “Final Crimp” the terminal using the “W
Crimp” slot on the Crimp Tool. The ears
feed into the side that has the “W” point.
This way the ears will roll back toward
each other and imbed themselves in the
shield as the Final Crimp is formed.
Core wire is
folded back.
Pre-Crimp
jaws are
near tool
hinge.

10
“W Crimp”
Slot
Pre-Crimp
Jaws
Ears
Fold
Inw
ar
f) Push (not pull) the terminal to position it inside the boot. The longer coil
terminals will need to be bent 90 degrees (at the narrow section) before
positioning in the boot.
Installation and Timing
Note 1: If replacing an impulse magneto, you need to remove the magneto impulse
spacer. The studs that hold the spacer to the case will be too long for use with the E-
MAG. You’ll need to replace the long studs with shorter ones, or simply use suitable
length bolts (not provided).
Note 2: These instructions are strictly limited to the installation and handling of “E”
model and “P” model E-MAG ignition(s) ONLY. If you are installing dual E-MAGs,
pull the breaker AND the coil plug from BOTH ignitions. Reconnect them ONLY as
instructed and only for the ignition you are working with. If you have a companion
ignition by another manufacturer, BE ADVISED you need to follow all safety and
handling guidelines of that system – SEPARATE AND APPART from the instructions
provided here for your E-MAG.
Confirm all connections to the ignition as follows, but do not install the ignition in
the engine until instructed to do so:
•Control leads (12 volt, ground, ON/OFF P-lead), 1 (optional) tack
lead, and possibly a jumper between terminals #2 and#3 (see
below) all of which attach to the (6) position Control Plug. Insert

11
Jumper for
Low Advance
this plug into the receptacle and secure with the anchor screws on
each end.
•3 lead coil plug to should be DISCONNECTED so the plugs cannot
fire during these setup procedures.
•MAP Sensor tube.
•Spark Plug Leads - with sparks plugs installed in the engine (or
plugs grounded to engine case).
Variable Timing Limit:
The ignition will use engine rpm and manifold pressure to calculate the firing angle
over a range of operating conditions. There are two preprogrammed curves that can
be called up by the operator by use of a jumper between thermals #2 and #3. The
standard High advance curve will allow timing to
advance as much as 39 degrees. The low
advance curve will allow timing to advance as
much as 34 degrees.
•High Advance (up to 39 degrees) - NO
jumper.
•Low Advance (up to 34 degrees) - WITH
jumper.
Note 1: E-MAG has NOT tested the myriad of
fuel and engine configurations, and cannot
prescribe which setting is appropriate for a given
situation. In general, builders with high
compression engines or those experimenting with auto fuels might want to use the
low advance setting.
Note 2: Terminals #2 and #3 are an RS232 connection that will enable a number of
enhanced communication and control features. Watch for future announcements.
Index Ignition Timing:
1. Rotate your prop to the engine TDC (or TC) timing mark. Note 1: It does
not matter whether the engine is on the compression or exhaust stroke for
a particular cylinder. Note 2: On some engines, “TC” is stamped on the
ring gear, which aligns with a reference alignment hole on the starter. On
others, a ring gear mark is lined up with the engine case seem. Consult
you engine manual on how to locate TDC.
2. Setup mode is entered by turning 12 volt buss power ON, while the p-lead
switch is OFF (grounded). In setup mode the LED indicator (located at
the base of the coil) will light continuous RED. Turn the drive gear with
your fingers slowly until you see the LED turn GREEN. You will be looking
for a single (very precise) point in the ignition’s rotation, so turn the gear
slowly. The GREEN LED signals the ignition’s internal crank angle

12
sensor is at the ignition index. Note: If you turn the key switch ON, the
ignition will leave setup mode and go into run mode. In order to reenter
setup mode you must turn the switch OFF and turn 12 volt power OFF.
You can then apply 12 volt power WHILE the p-lead switch is OFF.
3. Without moving the drive gear, position the gasket on the E-MAG flange
and install the ignition in the engine accessory case. You will engage the
ignition drive gear with a gear inside the accessory case. Don’t worry if
you bump the gear and lose your LED light at this point, but try to avoid
moving the gear very far off the index (GREEN) position.
4. After the ignition is positioned in the case, install your mounting clips,
washer and nut (or bolt as the case may be). Tighten only finger tight at
this time.
5. Reacquire the GREEN LED indicator by slowly rotating the ignition. If you
don’t have sufficient adjustment range to reacquire the GREEN LED, you
can remove the ignition, rotate the gear a distance equal to one tooth
width, and reinsert the ignition. This should get the index (GREEN)
position within your adjustment range.
6. Once the GREEN LED is reacquired, secure the position by tightening the
mounting clips.
7. When finished setting the timing for both ignitions (and only then) you can
then reconnect the coil plug to the ignition.
Confirm Plug Wiring:
Before running the ignition, it’s a good practice to confirm you have plug wires
correctly assigned at the coil with the following test:
•Pull the spark plugs and reconnect them to the plug leads.
•Rest each plug on the engine case, or any convenient location, so long as
the plug is grounded.
•Rotate the prop by hand and confirm the plugs fire as follows:
oThe PAIR closed to the prop will fire slightly after TDC. Note:
Standard start-mode firing angle if 5 degrees after TDC, but this is not
critical for this exercise.
oThe PAIR furthest from the prop fires 180 degrees later, provided you
do not stop or reverse the prop rotation after seeing the first pair fire.
Note: The no-stop no-reversal requirement is part of the ignition’s
“bounce back abort” routine. This is one of several kickback
safeguards built into the E-MAG.

13
Composite Oil Sump CAUTION:
Programmable Start-Up Firing Angle, as well as Run Mode Starting Delay from
earlier versions, are features NOT included with the initial release of series 113
ignitions. Those features are of interest to builders using composite oil sumps. If you
are currently using a composite sump, and need these features, contact E-MAG for
instructions, and the latest updates before installing your E-MAG system.
Background - Wasted spark systems avoid the weight, mechanical
complexity, and high altitude operating issues associated with traditional
ignition distributors. In a wasted spark system, plugs are fired in pairs at A)
the charged cylinder that’s ready to ignite, as well as B) the opposing cylinder
during the exhaust stroke. This second spark is not intended to ignite, hence
the name “wasted spark”. However, when restarting an engine shortly after
shut down (a hot start), it is possible for fuel vapor to accumulate in the intake
manifold. This vapor can be ignited by what is normally the “wasted” side of
the spark during valve overlap. [Valve overlap is when intake and exhaust
valves are momentarily open at the same time.] Even so, in the test cell
instance where this was observed, the event itself was rather unremarkable.
It was heard only as a hard “puff” prior to engine start. However, in that
instance, the intake manifold channeled this “puff” to the sump, which was
later measured as a 15 to 20 psi pulse. This pulse cracked the light weight
composite sump installed on the test cell engine. An identical replacement
sump did the same thing during a second hot start. When replaced with a
standard aluminum sump, the problem did not recur on any subsequent (hot
or cold) starts.
Operating Notes
Starting - DO NOT use procedures suggested for other electronic ignitions (i.e.
power up the ignition after the prop is spinning.) To start the engine, simply turn ON
12 volt power to the ignition (presumably your main power switch), turn ON the
ignition p-lead (ground) switch, and then start the engine.
Electrical System Condition - E-MAG’s power dip (kick-back) protection guards
against severe voltage drops that occur when the starter is first engaged. However,
in the event of a compromised electrical system (low battery, long cable runs,
corroded terminals, cold engine, etc) buss voltage may not rebound as the starter
speeds up (as is normal). A properly designed and functioning electrical system is
essential for the system to work properly. If buss voltage stays below safe levels, the
power dip safety circuit will do what it is supposed to do – not allow the ignition to fire.
Note: Your starter is likely the largest load on the electrical buss. In emergency
situations, hand prop starting will avoid the starter motor induced voltage drop. Do

14
not attempt a hand prop start unless you are well versed in this procedure. See
Emergency Prop Starting below.
Stopping the engine - CAUTION: P-MAG (self-powered) models are similar to
magnetos in that the ignition kill switch is the only way to stop the ignition once the
engine is started.
Powering Down - With all E-MAG models, use your main power switch or breaker(s)
to power down the ignitions. The ignition OFF switch (p-lead) only tells the E-MAG to
stop generating spark. It does NOT cut power to the ignition. If you leave the craft
with your E-MAG(s) powered ON, they will draw down your battery over time.
P-MAG Alternator Check: - You can check the internal alternator operation on the
P-MAG during run-up (900+ rpm) by switching to the P-MAG ignition and cutting
power at the breaker (or other switch). If the built-in alternator is working, the engine
will continue to run. If it is not working, the engine will quit. NOTE: Do NOT turn 12
volt power OFF and ON to E-MAG (non-alternator) model ignition while the engine is
running. The ignition undergoes an initialization and calibration when first powered
up that assumes the engine is not running. If done while the engine is running, the
calibration will be off.
Emergency Power - The P-MAG alternator power output is proportional to engine
rpm. The ignition will automatically switch to whichever source (aircraft or internal
alternator) is offering greater power. Should it ever be called upon in an emergency
(aircraft power failure), the P-MAG internal alternator will take over automatically.
There is no need for operator action of any kind.
Emergency Prop Starting – Both the E-MAGs and P-MAGs need outside electrical
power to start. You cannot prop-start the engine with either ignition if the battery is
missing, or totally dead. However, a low battery that barely “bumps” the starter
motor, or can only “click” the solenoid will likely have enough energy to power the
ignition for prop starting. Caution: Do not attempt a prop start unless you are
trained and are comfortable with the procedure. The following is NOT a
thorough or complete guide on how to safely prop start an engine. At start-up
the E-MAG’s first fire will ONLY happen at TDC on the index cylinders (every other
compression stroke). Finding the index bank is easy if you can see the ignition.
Turn buss power ON with the ignition switch OFF. This will put the ignition(s) in
Setup Mode with the red LED lit (see section on “Installation and Timing”). In Setup
Mode, the sparks plugs should not be able to fire, so you can pull the prop through
one or possibly two compression strokes. Pause to rock the engine back and forth
over the engine TDC mark. When doing this over the index bank of cylinders, the
ignition(s) GREEN LED will light up. You can then back up the prop, and it will be
“set for start”. Then (and only then) turn the ignition switch ON and you are ready to
prop-start the engine. If you can’t see the ignitions, you can always prop start as
usual, and simply accept that you have a 50/50 chance of being properly set to fire
on any given attempt.

15
Wiring Diagram
*Series 113 ignitions provide a 12-volt tack signal with two pulses per revolution. Note: Tack signal
is NOT a primary ignition function. It is a courtesy signal we are happy to provide. Due to the
variety of instruments available, we can provide only limited tack signal trouble shooting and/or
customer support.
Connector Plug
(viewed from cage
screw side)
O
p
to Isolato
r
Opto Isolator
Inside
Case
Outside
Case
(Power and ground wiring should be
18 gauge. Other wires can be 20
gauge.)
+5 Volts
1. To ground on engine case 1
4. P-Lead (ignition switch to ground
stops ignition firing) 4
5. Aircraft Power (+13.8vdc) through
3(P-MAG) or 5(E-MAG) amp breaker 5
6. Optional Tack Output* - 12-volt
pulse 20 millisecond long - 2 ppr 6
2
Control Alternate
3
Control Alternate
Jumpers 2 & 3
for low advance
– see Variable
Timing Limit
+12 Volts

16
Current Draw
The chart below shows current draw with buss voltage at 13.8 volts (representing
normal buss voltage). If the buss voltage were to deteriorate (or go away), the curve
for the P-MAG would be much different. This chart is provided as an aid to builders
for planning their electrical loads under normal operating conditions.
E-MAG Ign. Current Map @ 13.8 nominal voltage
0.00
0.10
0.20
0.30
0.40
0.50
0.60
0.70
0.80
RPM
CURRENT
E-MAG model P-MAG model
E-MAG model 0.09 0.11 0.32 0.16 0.18 0.20 0.31 0.42 0.53 0.65 0.76
P-MAG model 0.09 0.11 0.32 0.16 0.17 0.23 0.30 0.15 0.02 0.00 0.00
0.00 0.00 200.00 300.00 400.00 500.00 1000.0
01500.0
02000.0
02500.0
03000.0
0
This manual suits for next models
1
Table of contents
Other E-MAG Engine manuals
Popular Engine manuals by other brands
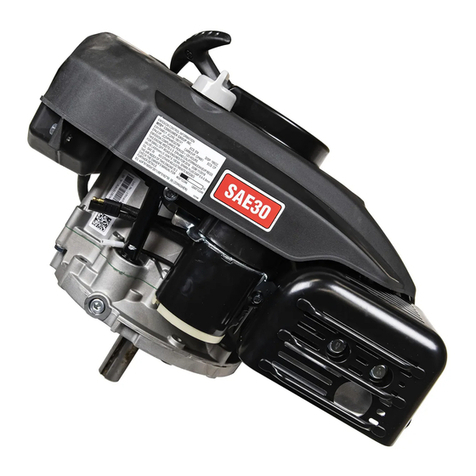
Cub Cadet
Cub Cadet 195 cc OHV Operator's manual
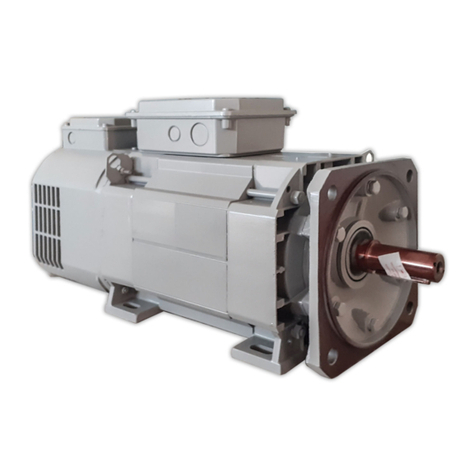
Oemer
Oemer QL Installation, use and maintenance manual
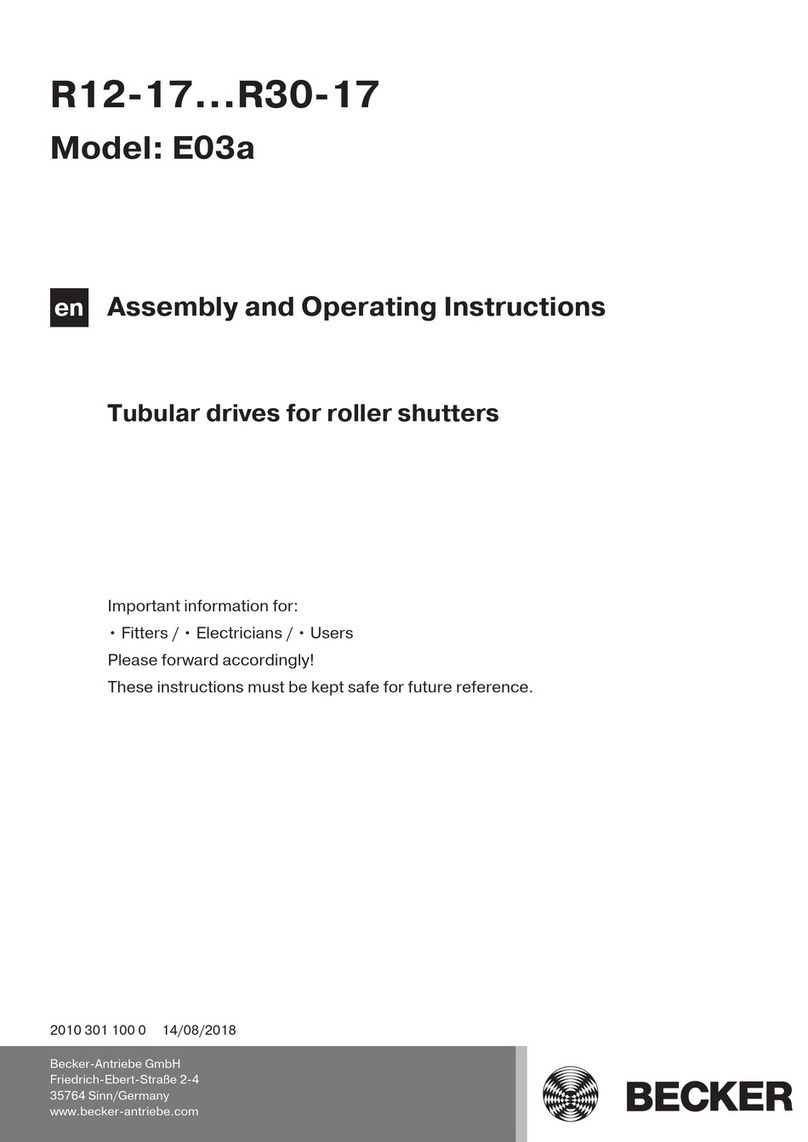
Becker
Becker E03a Assembly and operating instructions
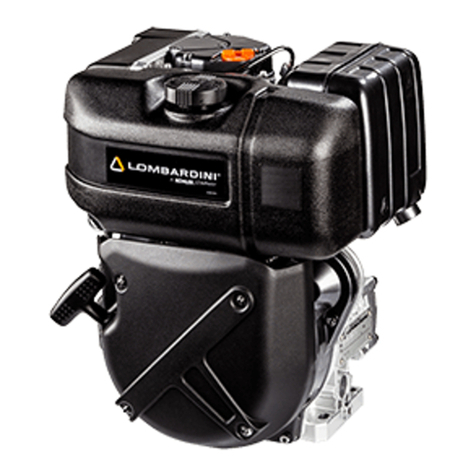
Kohler
Kohler LOMBARDINI 15 LD 225 Use & maintenance
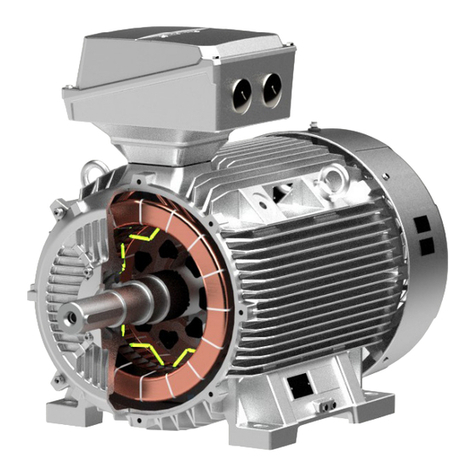
Siemens
Siemens SIMOTICS DP operating instructions

Guangxi Liuzhou Wuling Motors
Guangxi Liuzhou Wuling Motors LJ465Q-1ANE1 Instruction book

Briggs & Stratton
Briggs & Stratton Vanguard 540000 Series Operator's manual
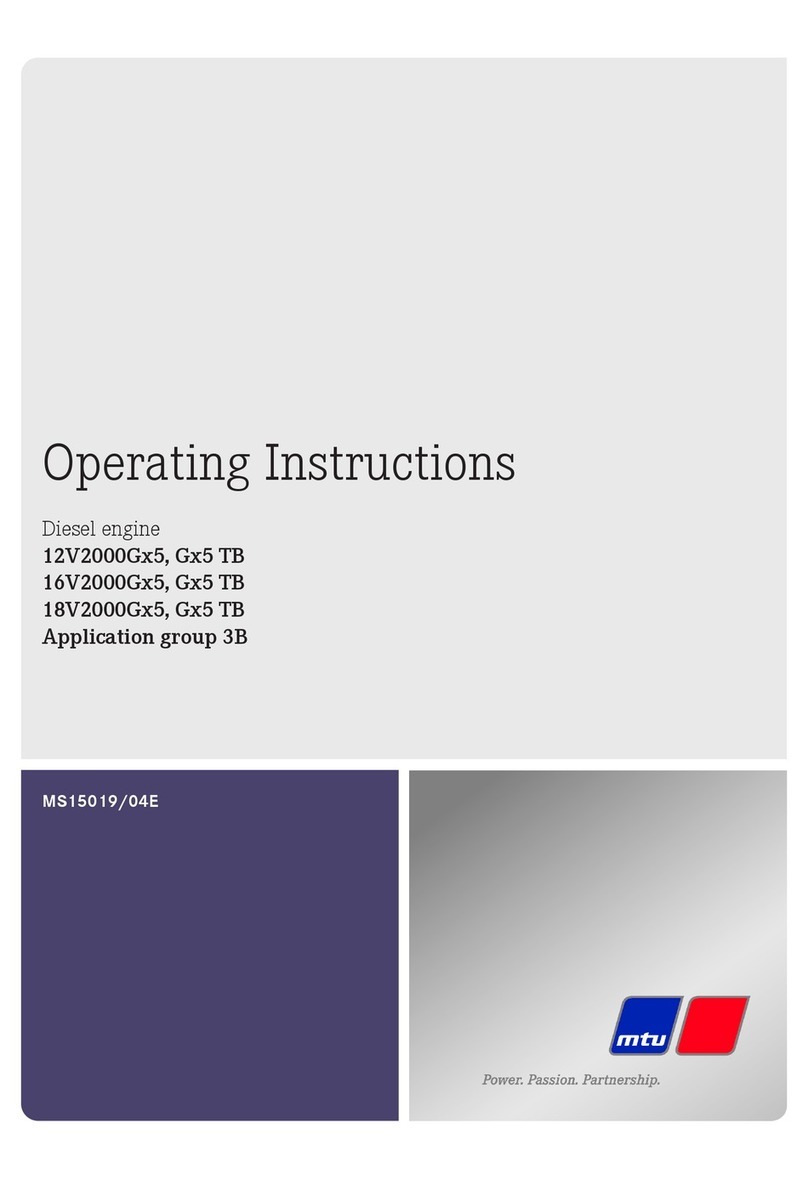
MTU
MTU 12V2000Gx5 operating instructions
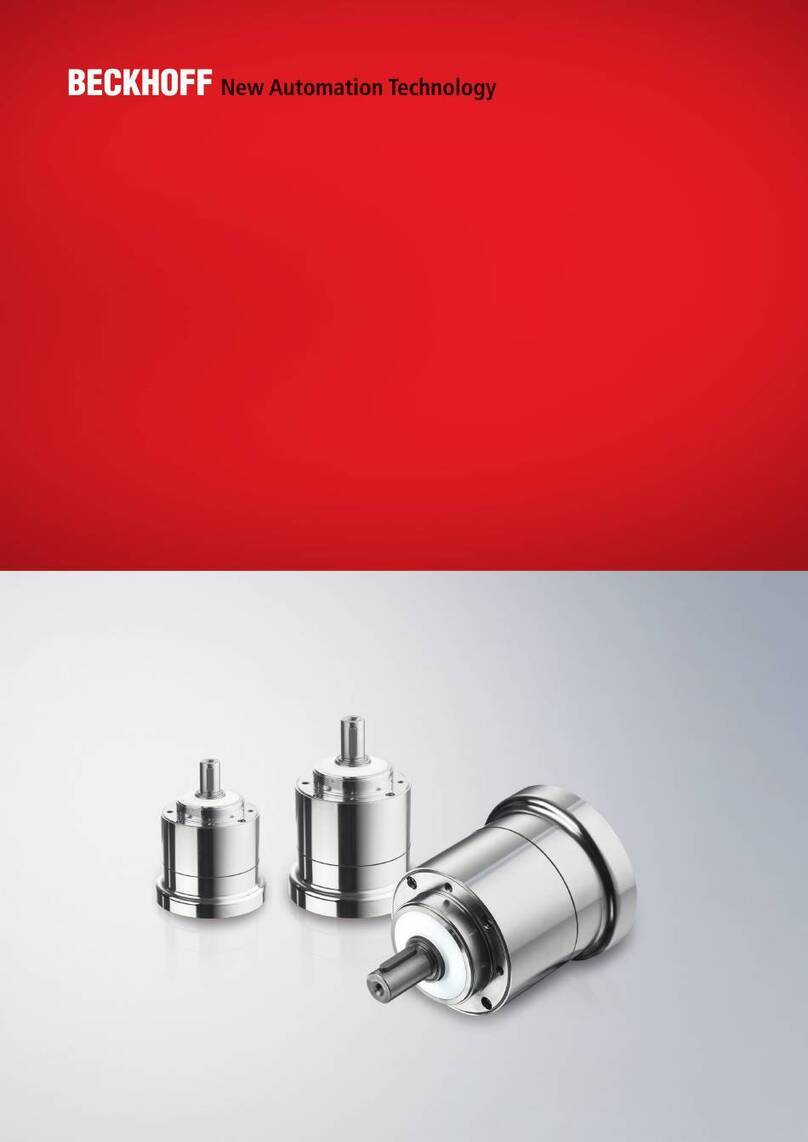
Beckhoff
Beckhoff AG2800 operating instructions
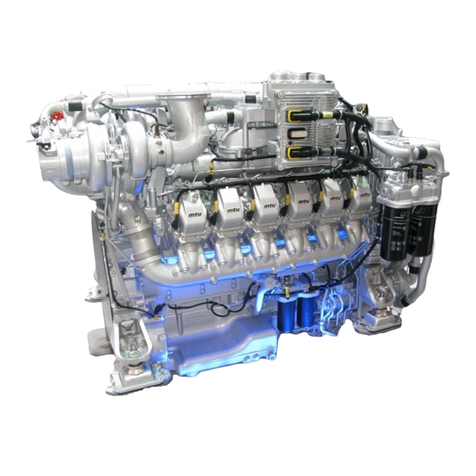
MTU
MTU 12V 2000 C66 operating instructions

Continental Refrigerator
Continental Refrigerator LTSIO-520-AE Overhaul manual
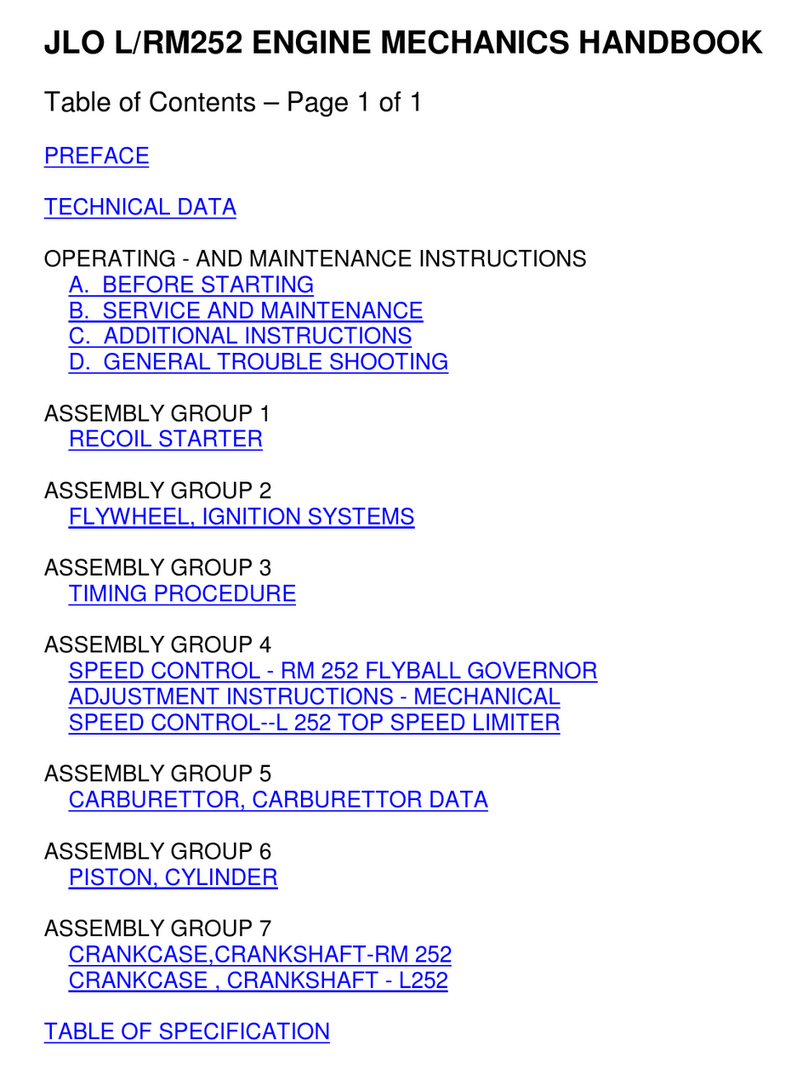
JLO
JLO L/RM252 Mechanics handbook