EcoloxTech E-1200 User manual

E-1200 System prebuilt
with pH Control
Installation &
Operation Manual
EcoloxTech
Tel. +1 954-900-6070
service.ecoloxtech.com

Table of Contents
System parts 3
System parts description 3
Backflow preventer 4
Water filter 4
Dosing unit 4
Holding tank 5
Pressure reduction valve 5
Flow control valve 5
Level / pump control 5
Installation 6
6
6
7
7
7
7
8
8
8
9
9
System process
Process steps
Water connection
System
Power connection
Level sensor / pump
Brine (NaCl)
E1200 brine hose connection.
Hydrochloric Acid
Level / Pump control
Ultrasonic level sensor
Distribution pump 9
System start-up 10
Step by step 10
Calibrating the level sensor 11
Pump start-up 11
Spare parts list 12

3
System parts
5
A
3
7
C
C
2
6
B
4
D
E
F
G
1. Backboard with pH control and system bracket
(backboard not shown on picture)
a. Back flow preventer
b. Water filter
c. Dosing units
d. Holding tank with float valve
e. Pressure reducer
f. Flow control
2. E-240 or 1200 unit
3. Control box Pump/level
g. Level sensor
4. HOCl storage tank
(option, not on picture)
5. Distribution pump
(option, not on picture)
6. Brine tank
(option, not on picture. 6 shows location)
7. Hydrochloric acid (HCl) connection
Picture 1 Shows system components, arrows shows flow direction

4
System parts description
Backflow preventer
The backflow preventer (a) is installed to protect the water system from
being contaminated in the case of a backflow. The backflow preventer
uses an atmospheric vent for any abnormal situation. This vent is
therefore to be kept unobstructed. Keep in mind that water might come
out of this vent.
The backflow preventer is flow directional.
Water filter
The water filter (b) will help keep the system running longer and make sure the final
product is as clean as possible.
On the top of the filter housing is a red button. This bottom is used to release pressure
when changing the filter.
The filter housing can be removed by twisting the housing to the left. To help remove
the hosing a specialty tool can be purchased.
See maintenance section for further information on filter change interval.
Dosing unit
The dosing unit (c) uses the waters pressure to mix in a
concentrate. The injection rate of the concentrate can be adjusted
using the scale at the bottom of the unit. The dose of concentrate
will be directly proportional to the volume of water entering the
unit, regardless of variations in flow or pressure. The ratio can be
adjusted using the scale shown in picture 5. Make sure the locking
ring at the bottom of the adjusting “handle” is loosened before any
movement of the adjusting ring. All adjustments should be made
without pressure on the unit. The eyelet in the white part of the
adjusting handle is used to set the current setting and is used when
adjusting the ratio. The dosing unit is flow directional, the flow
direction is indicated with an arrow, between the inlet and outlet.
There are two different versions of the same scale. One is a
percentage and the other is ratio. The scales are on opposite sides
of the unit and will do the exact same thing.
Picture 2 Backflow preventer
Picture 3
Water filter
Picture 4
Dosing unit
Picture 5 Dosing
unit scale

5
Holding tank
The holding tank (d) is filled automatic from dosing
unit (c). The level is controlled by the in-tank
installed float valve (picture 7).
The holding tank stores a mix of water and
Hydrochloric acid until it is used to lower the pH
of the feed water going to the system.
Nothing is added by the operator at this point and the screw lid
is only use to inspect and measure the content. The level of the
tank is maintained by the float valve installed inside the tank.
The float valve can be locked in the closed position and has a build in check valve.
The fill level is pre-adjusted from factory, but can be changed, if needed, by
adjusting the yellow floats position.
Pressure reduction valve
The pressure reduction valve (e), regulates the water pressure going to the
system. The (E-1200/E-240) system has a maximum allowed pressure of
50 psi. This is to protect the internal parts of the system.
The pressure reduction valve (e) is pre-adjusted from factory to 45 psi, so
no action is needed from the customer, side.
Flow control valve
The flow control valve (f) can adjust the flow though the system. The flow can be
adjusted to anything within the system flow range. For the E-1200 that is 4 to 24
liter/minute. E-240 is 1 to 5 liter/min.
Level / pump control
Tank level / pump control (3) is an option that can be added when ordering a
system. The programmable LED display will show tank level as a percentage,
and control start/stop of the system.
The programmable LED display will also protect distribution pump in some
specific operational situations if this option is added.
Picture 6
Holding tank
Picture 7 Pressure regulator
Picture 8
Flow control valve
Picture 9 Level / pump
control unit
Picture 6.a Float valve
Picture 6.b Float valve
in-side tank

6
Picture 10 Installation overview with part numbering.
Installation
The system is intended to be installed vertically on a wall. The system is intended to be installed
vertically on a wall and will not work correctly if laying down.
Installation hardware is not included with the system, and customer will have to supply their own.
1
9
5
13
3
7
8
2
10
6
14
4
12
16
System process
The colored arrows in picture 12, indicates the flow direction of water through the system. For every color change
of the arrows the water/product undergoes a change. This change can be the addition of an additive or a chemical
change thought the use of electrolysis. Dierent colors are also used to indicate additives used in the process.
Process steps
1)
Blue color. The blue color is normal water before any changes are made. The water inlet splits up into two separate
streams. The water that goes into dosing unit 3 is a low flow rate. The main part of the water goes though dosing unit 5.
2) Red color. The red color indicates the addition of the purple product (HCl). The HCl is added to the water in
dosing unit 3. The mix is stored in tank 4 and has a very low pH level at this point.
3) Yellow color. The Yellow is a mix of red (HCl and water) and blue (water). The dosing unit 5 controls the amount
of concentrate (red) that is needed to produce the desired pH level in the final solution. Location 6 & 7 does not
change the solution.
4) Green color: The green color is the final HOCl product. The final solution is made by adding brine (brown arrow)
to the electrolysis cell inside the system.
11
15

7
Water connection
Water is connected at location 15 on the drawing. The water is connected directly to the backflow
preventer (1). Use included barb connection if ¾” hose is used. Water pressure should not exceed 85 psi
at the inlet, as this is the max acceptable pressure of the pH control system (first part of the backboard).
Water purity should not exceed 80 TDS (total dissolved solids). Make sure the filter housing has a filter
installed.
System Water connection
The pH regulated water enters the system at this
location 8 (yellow arrow) and the final product (HOCl)
comes out at location 10 (green arrow) see picture 10.
The system located at position 9 on the overview can
either be a 240 or a 1200 unit. Which unit used depends
on the concentration and volume needed.
If the 240 unit is used, in and out locations are
switched. The E240 also uses push-fit connections.
The E240 has an internal Brine tank (NaCl) which needs
no additional setup. The E1200 uses an external brine tank which uses filter 13 in
picture 9, as a suction filter. The filter is lowered into the tank used for the brine.
Filter and additional hose is included in the system.
Additional information on the specific system can be found in the unit’s manual.
E1200 unit: https://www.ecoloxtech.com/pdf/e1200soperationmanual.pdf
E240 unit: http://ecoloxtech.com/pdf/e240soperationmanual.pdf
Power connection
Depending on what options have been chosen, the power is connected differently. The pH control part
of the setup does not use electrical power for its operation. The only power needed for operation is
therefore the E240/1200 unit. Both units connect directly to an outlet and are compatible with most
outlets around the world (100 – 230 Vac, 50/60Hz). Both have an on/off button on the side.
Level sensor / pump
With the addition of a level sensor the power connection is moved to the electrical box right over the
unit. Power cable comes with a US plug (US customers only) that goes into the electrical box and
distributes power from there. The power inlet cable is connected to a normal power outlet. Control box
is compatible with the same voltages as the systems. Customers outside the US will have to supply and
install a power plug that fits their region.
Picture 11
E-
1200 in/
out-put
Picture
12
E-
1200 unit,
brine
filter

8
Brine (NaCl)
The brine connection depends on the system being used. The
E240 unit has an internal brine tank, so no further action is
needed.
The E1200 unit uses an external brine tank (NaCl). Included in the
system is a 1/8” hose and filter (see picture 11 & 12). Use filter and
hose to connect external brine tank to the E1200 system.
E1200 brine hose connection.
Open front door of the E1200 unit to find the Electrolysis
cell (pic 15). The brine is connected to the E1200 system
though the hose seen in picture 14. The cell hose can be
found in the bottom left side of the E1200 unit next to the
Electrolysis cell. There are two hoses in this area, one goes
to the cell and the other is for the brine. The hose can also
be hidden behind the cell. The hose can also be rolled up on
top of the cell.
The brine tank is connected to the system using the hose in
picture 14. The hose is run out though the hole in the bottom
left side of the unit. Avoid having height differences in
system and brine tank location. System pump cannot handle more that 2-3 meters height difference.
Try to keep the length of the brine hose at a minimum.
Hydrochloric Acid
Hydrochloric Acid is connected at location (11) on picture
10 (purple arrow). The concentration of HCl to be used
is between 32-37%. If the finished HOCl product is used
directly on food, the HCL must be food grade.
Use included chemical resistant hose, filter and blue cable
ties for installation. Filter is secured to the hose using the
two blue cable ties before submerged into the HCL. Use full
strength 32-37% HCl.
Use appropriate PPE when handling hazardous chemicals.
Do not add HCl to the system anywhere else.
Picture 13
Brine (NaCl) filter
Picture 14 1/8 tubing for
brine tank
Picture 16 Location of HCL
additive to system
Picture 17
HCL filter
Picture 15 Electrolysis cell inside E1200 unit. Brine
hose connection

9
Level / Pump control
The control box (12) is installed if the optional level sensor was added. The
programmable LED display will show the tank level as a percentage of the sensor
scale. The LED display is used to control the unit start/stop. The will also stop the
distribution pump from running dry when tank level is too low or signal is outside
normal range.
There are 4 relays that control those functions. Relay 1 and 2 control the unit and
relay 3&4 the pump. Relay 1 is set to 95% and will stop the HOCl
production when reached. Relay 2 will start HOCl production when level goes below 50%. Relay 3 will stop the
pump from running when level goes below 10%. Relay 4 will stop pump when level shows 101.5% which is outside
normal operation.
The relay settings can be changed by the operator. Press the up or down arrow on the display when default screen
is displayed to access “fast set-point”. Press up/down arrow to choose the wanted relay to change. Press the “ok”
button to access the desired relay set-point. Relay 2 setpoint should always be lower than relay 1 setpoint.
Pressing the “ok” button when default screen is display will prompt you for a password. Enter the password to
change setup of the programmable LED unit.
Ultrasonic level sensor
The ultrasonic level sensor (14) connects to the control cox. The M12 connector used for
the sensor can only be installed in one position, make sure the M12 connector is connect
straight and all the way (do not use any tools). The ultrasonic level sensor is mounted to
the HOCl storage tank, in a way that leaves a free line of sight to the measured liquid.
The sensor has a dead band of 300 mm, meaning that the sensor has to be minimum
300 mm from the measured liquid. Maximum range of the default sensor is 3 meters.
The sensors signal strength is indicated on top of the sensor using a red LED. Make sure the red LED is on for the
sensor to work correctly.
Distribution pump
The optional distribution pump is a constant pressure pump that uses a build in VFD. The pump uses a pressure
sensor to measure the pumps output pressure. The pump speed is adjusted to maintain the correct pressure.
The pump connects to the Backboard control box with two cables. Cable 1 supply the needed power (Vac). The
second cable is used for pump protection in specific situations.
The pump starts on its own when the pressure in the outlet line drops. The pump stops again when the pressure in
the output line is higher than the setpoint. The pump pressure can be adjusted on the pump by pressing the arrows
on the top. The storage tank is connected to the pump inlet and all consumers connect to the output.
Picture 18 Control box
Picture 19 Level sensor
Relay number Description Setting %
1System is stopped at this setting 95
2System is started at this setting 50
3Pump is stopped, to avoid running dry 10
4Pump is stopped as level signal is outside normal range 101.5

10
System start-up
Make sure all topics in the installation part of this manual is resolved before starting the start-up phase. Depending
on our specific setup, you might have additional parts to consider.
Step by step
1.Make sure all relevant parts for your system is installed and ready, as described in the installation section.
2. Make sure system (9) is not turned on at this time.
3. Close flow regulation valve (7)
4. Disconnect hose from bottom of mixing tank (4).
a. Unscrew the ½ inch hose connection to allow water out of the small tank (4).
5. Open water connection to system (max 85 psi)
6. Vent dosing units, by pressing button on top of unit (3&5). Hold down the button until the water
flows out in a steady stream.
7. Prime the dosing unit (3) by running the unit until HCL is socked into the unit body. Dosing unit scale
can be adjusted to allow faster filling of hose and unit.
8. Adjust dosing unit scale to half way position.
9. Let dosing unit run and check pH level in mixing tank. Allow adequate time for changes to take effect
after anychanges. Mixing tank pH level should be between pH 1 and 1.5 depending upon feed water
pH. The pH level can be adjusted using the scale on dosing unit 1. Moving the ‘Handle” on the scale
up, lowers the pH level in the tank (4).
10. When desired pH level is reached the hose at the bottom of tank (4) can be reattached.
11. Let tank (4) fill with water at the correct pH level and make sure the float valve controls the level as
intended.
12. Adjust scale on dosing unit 5 to 50 % (half way).
13. There are two different ways to do the next part.
a. Run system
b. Disconnect water inlet (8) from system and let the solution run into a bucket for testing and then
drain.
For this start up instruction, I have chosen to use option b.
14. Open flow valve to allow the solution to flow into the bucket.
15. Let the solution run into the bucket and watch dosing unit 2 suck in the solution from mixing tank (4).
16. Test the pH level of solution running into the bucket. The pH level at this point should be 1 to 2 pH
below the desired final product. The exact pH level depends on the setting of the system.
17. The pH level can be adjusted using the scale on the second dosing unit. Adjusting the “handle” up
towards the unit body will lever the pH level of the solution.
18. When the correct pH level has been reached close the flow valve to stop the flow.
19. Reattached the hose to the system inlet (8)
20.Open the flow control valve. The valve can be adjusted to the desired flow rate later on.
The pressure regulator has been adjusted to 45 psi from factory and therefore does not need further adjustments.

11
21. Turn the system on.
a. If you have the control box turn that on as well.
22. If you have the control box and level sensor, then jump to the “calibrating the level sensor” before
continuing.
23. Run the complete system and test the pH of the final product. The pH does most likely need some
minor adjustment here to get the desired pH level.
24. Use the scale on dosing unit (5) (closest to the system) for fine adjustments of pH level. Do not
change the setting on the first dosing unit at this point.
25. Both dosing units’ adjustments can be locked after the final pH level has been reached.
Calibrating the level sensor
1. Make sure the sensor is on. The green LED on the unit should be lid. The red LED indicates the signal
strength of the signal the unit sees. Under normal operation this let is on, if the red LED is not on the
sensor is not at the right angle or we are outside the 3-meter range.
2. Install the sensor in the desired location. Make sure there are no edge the sensor can see. If the
sensor sees sharp edges the reading will be off.
3. Push and hold the “analog button” for longer than 2 seconds.
Power LED = off, Output LED = on
4. Hold a piece of cardboard at the position which equals 100% full tank.
5. The red LED (signal) must be on of flashing
6. ‘Click” analog button
Power LED = off, Output LED = flashing
7. Remove card board from 100% full and let the sensor see 0 % full
8. “Click” analog button
9. The red LED must be on or flashing
10. If the operation was successful the Power and Output LED will be on
Pump start-up
Prime the pump before use. Open the inlet and outlet valves (if installed) to allow the pump to fill up with HOCl.
Open up some of the outlet to allow HOCl to “escape” the setup. Some pumps need to be primed by losing a vent
bolt. To find specifics on this type of priming please see pump manual. Turn on the pump and watch operation.
Make sure pump is running without excess noise.
System is now ready for operation.

12
BRINE TANK
Spare parts list
1
3/4” FPT Dual Check Backflow
Preventer w/ Atmospheric Vent (SKU:
P-4501)
10 Dosatron Pump D14MZ2VFII
(SKU: P-4473) 19 3/4” MPT x 1/2” FPT Hex Bushing
(SKU: P-1030)
23/4” MPT Nipple Hex (SKU: P-4251) 11 3/4” FPT Compact PRV Prescal w/
Gauge (SKU: P-4500) 20 1/2” Compression x MPT Male 90 Deg
Elbow (SKU: P-4526)
3Filter Housing 3/4” FPT (SKU: P-1015)
5 Micron Filter Cartridge (SKU: P-1020) 12 3/4” FPT x MPT PVC 90 Degree Elbow
(SKU: P-4516) 21 1/2” OD Versilon FEP Tubing
(SKU: T-4552)
43/4” MPT x Socket PVC Male Adapter
Sch 40 (SKU: P-4512) 13 3/4” FPT PVC Gate Valve
(SKU: P-4377) 22 E-1200
(SKU: E-1200)
53/4” PVC Sch 40 Pipe
(SKU: T-1137) 14 3/4” Insert x 3/4” MPT Adapter Elbow
(SKU: P-1029) 23 1/4” OD Silicone Tubing
(SKU: T-1126)
63/4” Socket PVC Union
(SKU: P-4488) 15 3/4” Reinforced Tubing, 70 psi
(SKU: T-1040) 24 Foot Valve Strainer, 1/4” OD
(SKU: T-1026)
73/4” Socket PVC 90 Degree Elbow Sch
40 (SKU: P-4510) 16 3/4” Insert x 3/4” MPT Adapter
(SKU: P-1028) 25 Compact Float Valve, ¾”, Yellow/Black
(SKU: P-4519)
83/4” Socket x Socket x FPT PVC Tee
Sch 40 (SKU: P-4513) 17 3/4” Insert x 3/4” FPT Adapter Elbow
(SKU: P-4489) A316 SS Hose Clamp SAE #12 (SKU:
P-4431)
93/4” Socket x FPT PVC 90 Deg Elbow
Sch 40 (SKU: P-4515) 18 2.5 Gallon Rectangle Blow Molded Tank
(SKU: P-4523)
WATER
SUPPLY
1 5 5
5
5
5
15
37
2
2
6
6
4
8
9
20
19
18
10
17
17
21
21
10 11
12
13
15
15
16
22
23
24
16
14
A
AA
A
A
A
TANK OF MURIATIC
ACID FOR LOWERING
PH OF WATER SUPPLY
TANK HOLDING
HYPOCHLORUS ACID
GENERATED
Table of contents
Popular Water Filtration System manuals by other brands
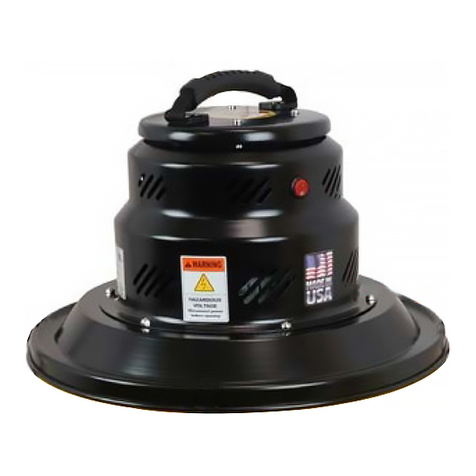
Clayton
Clayton WH-105-4 Safety, Operation & Maintenance
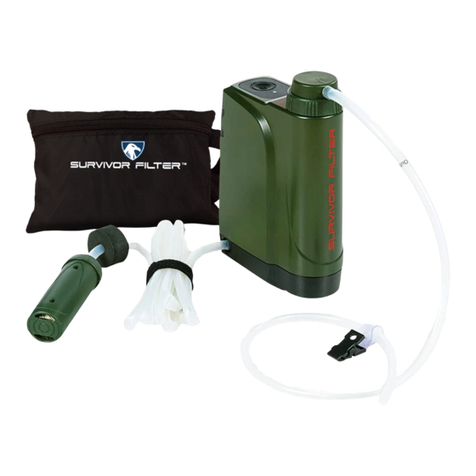
Survivor Filter
Survivor Filter PRO X Electric Survival Filter instruction manual
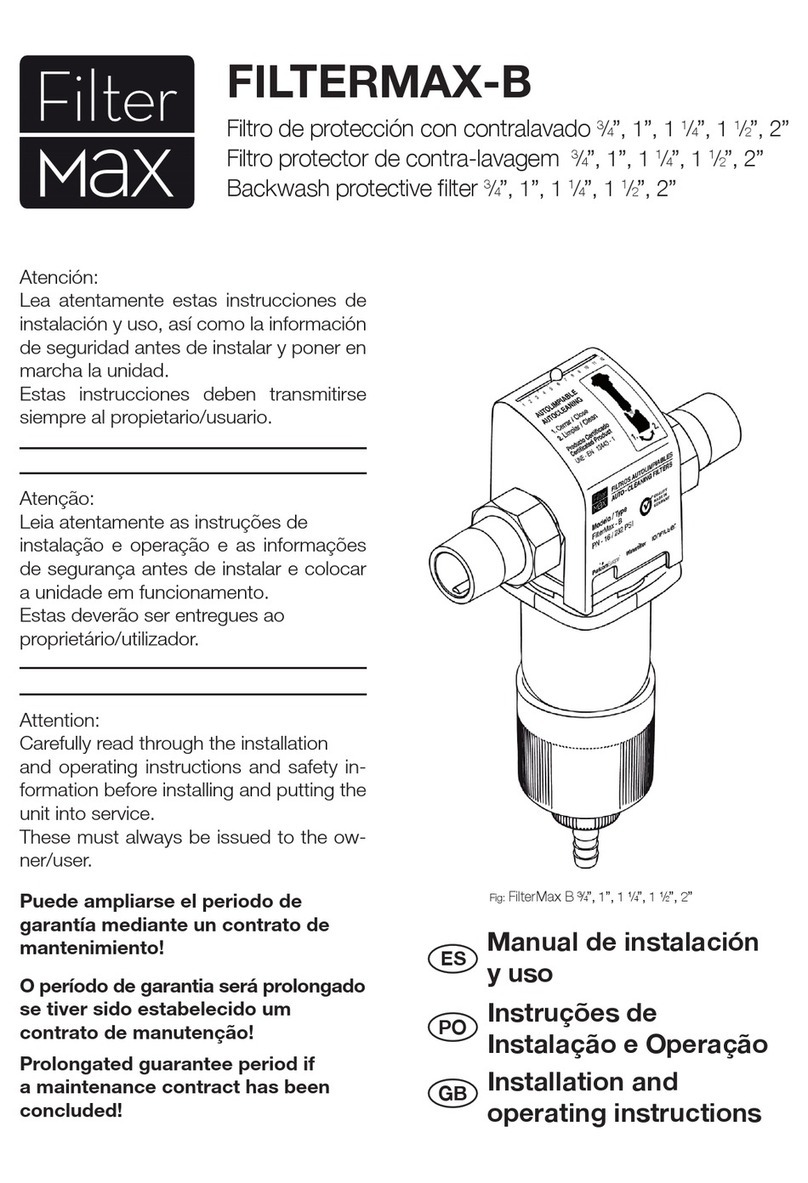
FILTERMAX
FILTERMAX FM-B Series Installation and operating instructions
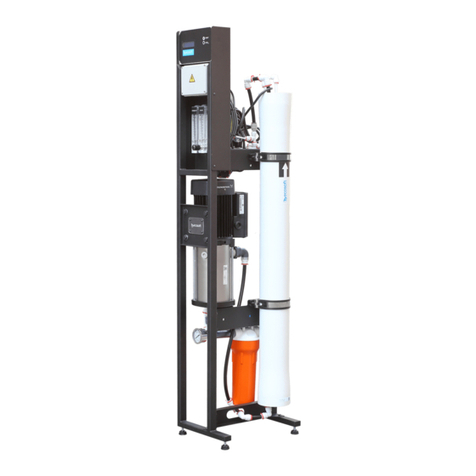
BWT
BWT ECOSOFT MO5000 instruction manual

Aqua Free
Aqua Free Germlyser G Instructions for use
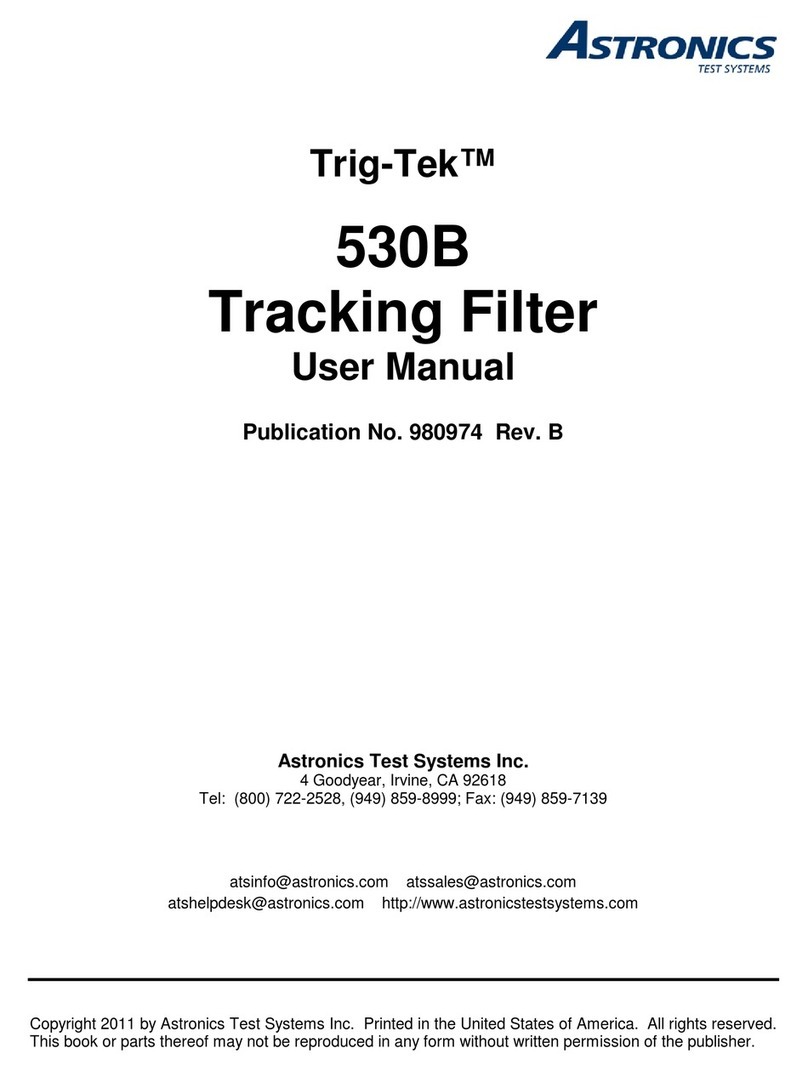
Astronics
Astronics Trig-Tek 203M user manual
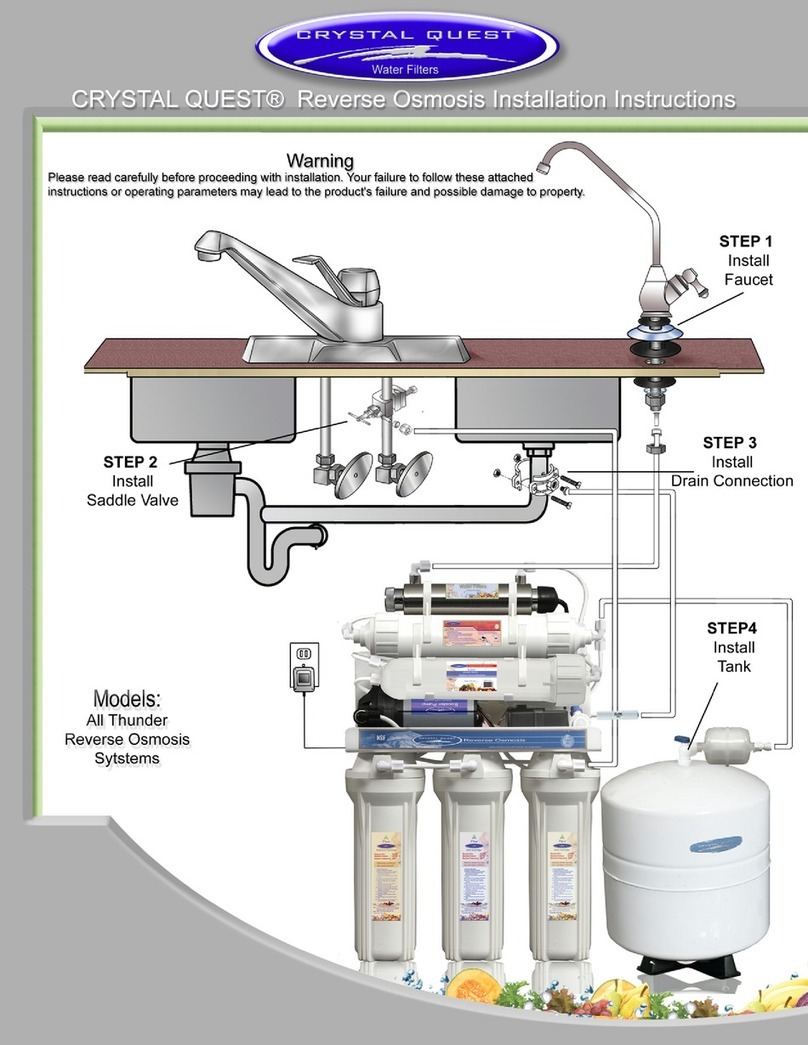
Crystal Quest
Crystal Quest Thunder Series installation instructions
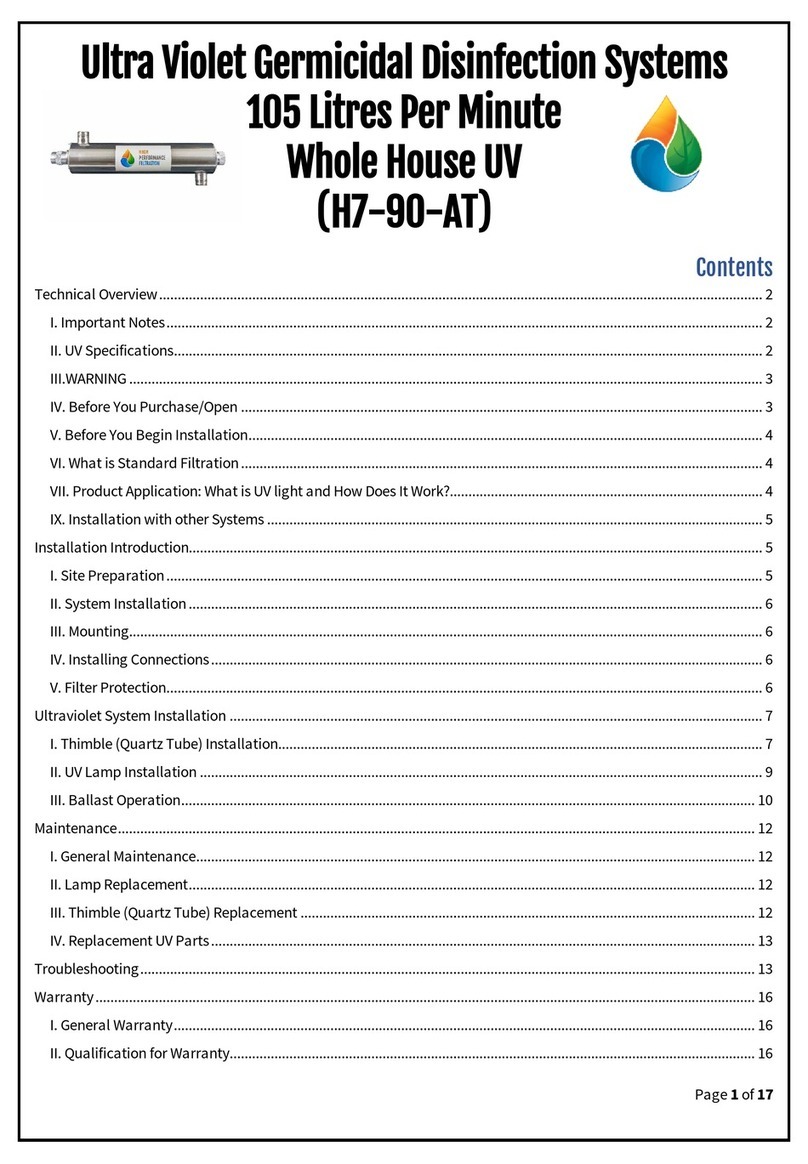
HPF
HPF H7-90-AT manual
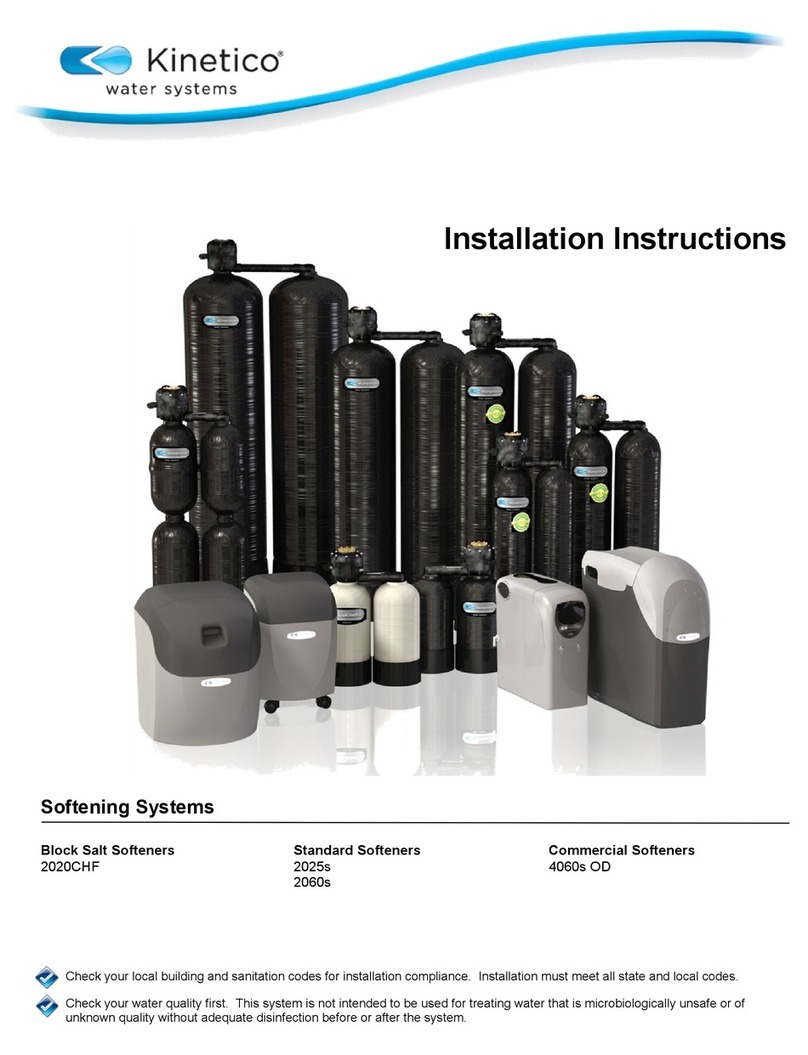
Kinetico
Kinetico 2025s Installation instructions manual
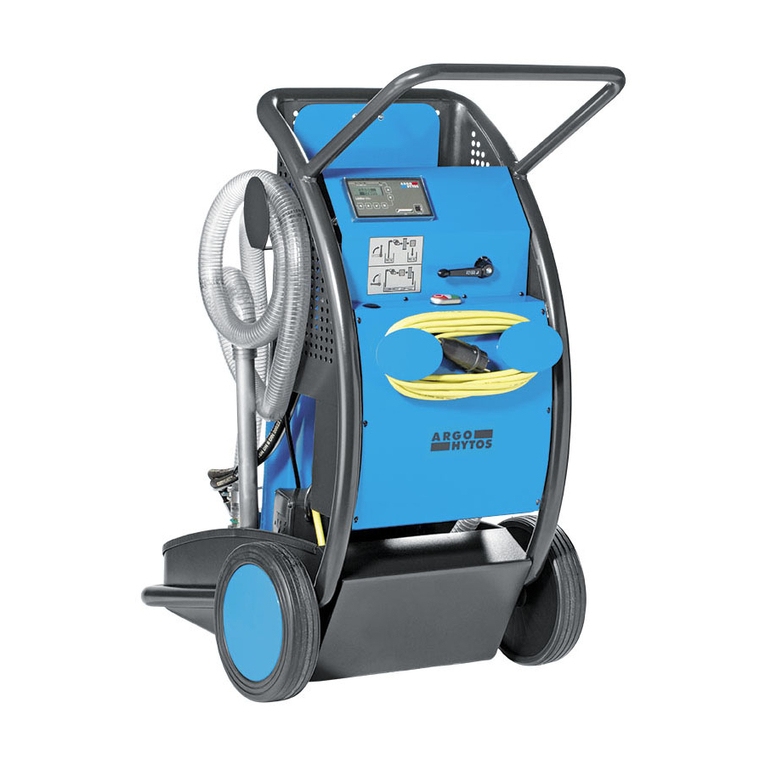
Argo-Hytos
Argo-Hytos Ecoline UMPC 045 manual
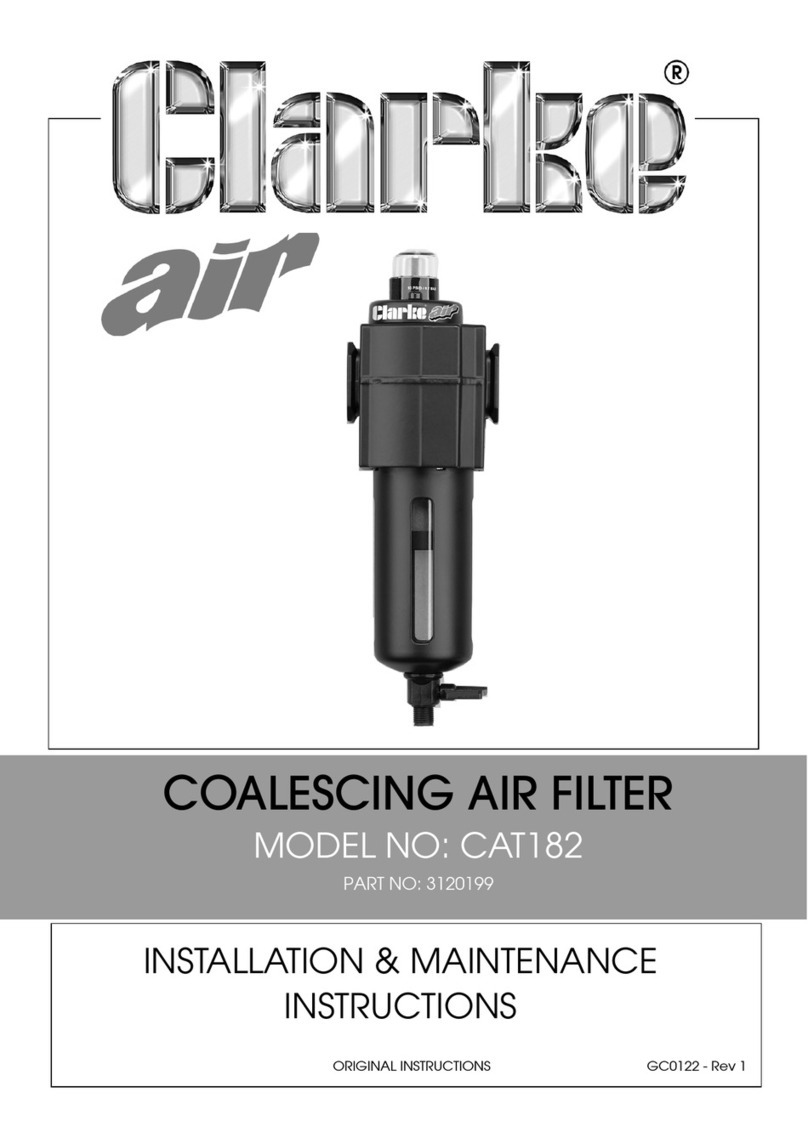
Clarke
Clarke CAT182 Installation & maintenance instructions
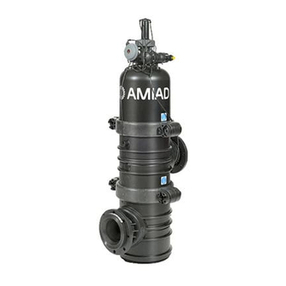
amiad
amiad 4" Sigma Pro Installation & operation manual