eDAQ Potentiostat User manual

e-corder
®
www.
eDAQ
.com
eDAQ Potentiostats, User Manual
Potentiostat,
Picostat &
QuadStat
Potentiostat
Overload
Picostat
Overload
WE WE WE WE
QuadStat
RE RE RE RE
AE AE AE AE
Channel 1 Channel 2 Channel 3 Channel 4
164

ii eDAQ Potentiostats
This document was, as far as possible, accurate at
the time of printing. Changes may have been made
to the software and hardware it describes since
then: eDAQ Pty Ltd reserves the right to alter
specifications as required. Late-breaking information
may be supplied separately. Latest information and
information and software updates can be obtained
from our web site.
Trademarks of eDAQ
e-corder
and PowerChrom are registered trademarks
of eDAQ Pty Ltd. Specific model names, such as
e-corder
201, PowerChrom 280, Picostat and
QuadStat are trademarks of eDAQ Pty Ltd. Chart
and Scope are trademarks of ADInstruments Pty Ltd
and are used under license by eDAQ. EChem is a
trademark of eDAQ Pty Ltd.
Other Trademarks
Mac OS, and Macintosh, are registered trademarks
of Apple Computer, Inc. Windows 98, Windows
Me, Windows 2000, and Windows XP are
trademarks of Microsoft Corporation.
PostScript, and Acrobat are registered trademarks of
Adobe Systems, Incorporated.
All other trademarks are the properties of their
respective owners.
Products: Potentiostat (EA161)
Picostat (EA162)
QuadStat (EA164)
Document Number: UM-EA161/2/4-1105
Copyright © November 2005
eDAQ Pty Ltd
6 Doig Avenue
Denistone East, NSW 2112
Australia
http://www.eDAQ.com
email: [email protected]
All rights reserved. No part of this document may be
reproduced by any means without the prior written
permission of eDAQ Pty Ltd.

eDAQ Potentiostats iii
Contents
1 Overview
1
How to Use this Manual 2
eDAQ Amps 2
Checking the unit 3
2 The Potentiostat
5
The Front Panel 6
The Electrode Connector 6
Electrode Cable 7
The Online Indicator 8
The Overload Indicator 8
The Back Panel 9
E Out, I Out and E In Connectors 9
I
2
C Connectors 10
Grounding Connector 10
Connecting the Potentiostat 11
First Use 13
Potentiostat Control Window 14
Maintenance 22
3 The Picostat
25
The Front Panel 26
Electrode Connector 26
Electrode Cable 27
The Online Indicator 27
The Overload Indicator 28
The Back Panel 29
E Out, I Out and E In Connectors 29
I
2
C Connectors 29
Grounding Connector 30
Connecting the Picostat 31
First Use 33
Picostat Control Window 35
Maintenance 39
4 The QuadStat
41
The Front Panel 42
Electrode Connectors 42
Electrode Cables 42
The Online Indicators 43
The Overload Indicators 43
The Back Panel 45
E Out, I Out and E In Connectors 45
I
2
C Connectors 46
Grounding Connector 46
Connecting the QuadStat 48
Using a Common Reference and Auxiliary
50
Using Multiple References and Auxiliaries
51
First Use 52
QuadStat Control Window 54
QuadStat Potential Window 58
Maintenance 59
Potentiostat
Overload

iv eDAQ Potentiostats
5 Techniques
61
Introduction 62
Linear Scan Techniques 63
Fast Cyclic Voltammetry 63
Chronoamperometry with Chart 65
On Windows computers 66
On Macintosh 68
Analysis of Chronoamperometry 70
Chronoamperometry with Scope 74
Chronocoulometry 75
Chronopotentiometry 77
Chart software on Windows computers 79
Chart software on Macintosh 80
Scope software 82
Controlled Potential Electrolysis 82
Controlled Current Electrolysis 83
Amperometric Sensors 84
Biosensors 85
Microdialysis Sensor 86
Dissolved Oxygen (dO
2
) Sensors 86
Nitric Oxide (NO) Sensors 87
A Technical Aspects
89
Potentiostat 89
Picostat 91
QuadStat 92
B Troubleshooting
95
C Specifications
101
Potentiostat 101
Picostat 104
QuadStat 106
D Electrochemical Equations
109
Linear Sweep and Cyclic Voltammetry 109
Chronoamperometry 111
Chronocoulometry 112
Index
113
License & Warranty
117

eDAQ Potentiostats 1
CHAPTER ONE
1
Overview
There are three eDAQ potentiostat models:
• Potentiostat (EA161), Chapter 2. Single channel, three electrode
potentiostat/galvanostat with gain ranges of 20 nA to 100 mA;
• Picostat (EA162), Chapter 3. Single channel, three electrode, high
sensitivity potentiostat with gain ranges of 10 pA to 100 nA; and
• QuadStat (EA164), Chapter 4. Four channel, three electrode
potentiostat with gain ranges of 2 nA to 1 mA with current signal
offset.
They are a part of the family of fully–software controlled modular
preamplifiers (eDAQ Amps) which are designed for use with the
e-corder
®
system.
Some of the uses of the Potentiostat, Picostat, and QuadStat, are
mentioned in Chapter 5, and also in the
EChem Software Manual
which describes the use of the optional EChem software.
NOTE
This manual is for the
EA161 Potentiostat. If
you have an older model
EA160 Potentiostat then
please ask us to send
you the appropriate
manual.

2 eDAQ Potentiostats
How to Use this Manual
This manual describes how to set up and begin using your Potentiostat
(Chapter 2), Picostat (Chapter 3), or QuadStat (Chapter 4). Their use
with Chart and Scope software is also described (Chapter 5).
The appendices provide technical and troubleshooting information.
See the
EChem Software Manual
for a description of the use of these
potentiostats with the optional EChem software.
eDAQ Amps
The Potentiostat, Picostat and QuadStat are part of a family of
preamplifiers known as eDAQ Amps.
The Potentiostat, Picostat, and QuadStat are designed for performing
voltammetric and amperometric experiments. As with other eDAQ
Amps, they are designed to be operated under full software control and
are automatically recognised by Chart, Scope or EChem software
which control their gain range, signal filtering, and other settings.
The eDAQ Amp family also include the:
• pH Amp, suitable for connection of pH, ion selective, and
potentiometric (ORP) electrodes
• Bridge Amp, suitable for sensors requiring a DC Wheatstone
bridge connection. Also provides DC excitation
• GP Amp, suitable for high output sensors requiring a high
impedance DC Wheatstone bridge. Also provides DC excitation.
See our web site at www.eDAQ.com for more information.

Chapter 1 — Overview 3
Checking the unit
Before you begin working with the Potentiostat, Picostat, or QuadStat
please check that:
• all items described in the packing list are included; and that
• there are no signs of damage that may have occurred during
transit.
Contact your eDAQ distributor if you encounter a problem.
You should also become familiar with the basic features of your
e-corder
system, which are discussed in the
e-corder
Manual
which will
be installed as a pdf file on your computer when you install the
software.

4 eDAQ Potentiostats

eDAQ Potentiostats 5
CHAPTER TWO
2
The Potentiostat
This chapter describes how to connect and use your model EA161
Potentiostat. If you have an older model EA160 Potentiostat please refer
to the documentation that came with your unit or contact eDAQ at
IMPORTANT:
Always make sure that the
e-corder
is turned off before
you connect or disconnect the Potentiostat. Failure to do this may result
in damage to the
e-corder
and/or the Potentiostat.
NEW FEATURES:
If you have used the older EA160 Potentiostat before,
then you will notice that the EA161 has new front and back panels,
and incorporates several new features: iR compensation; ZRA mode;
High Z mode; and also has a High Stability option for stabilization of
the Potentiostat in situations where oscillation would otherwise be
encountered. Signal accuracy and signal-to-noise ratio have also been
improved. Note that the EA161 Potentiostat now uses the same
electrode cable as the EA162 Picostat.

6 eDAQ Potentiostats
The Front Panel
The front panel of the Potentiostat is shown in Figure 2–1.
The Electrode Connector
The electrode connector of the Potentiostat provides connection pins for
the Working, Auxiliary and Reference electrode lead wires. The
connector also provides connections for the lead shields which protect
the signals in the cable wiring from electrical interference (noise
pickup).
The pin assignments of the Potentiostat electrode connector are shown
in Figure 2–2. The Auxiliary and Reference electrode leads have
Potentiostat
Overload
Overload
indicator light
Electrode connector,
Lemo socket,
to electrodes
Online indicator light
Working Electrode Auxiliary Electrode
Reference Electrode
Reference Electrode Shield
Working Electrode Shield Not connected
Alignment dot
Figure 2–1
The Potentiostat front
panel.
Figure 2–2
The Potentiostat electrode
connector as seen when
looking at the front
panel.

Chapter 2 — The Potentiostat 7
coaxial shields which are maintained at the respective electrode
potential.
Electrode Cable
The Potentiostat is supplied with an electrode cable comprising three
leads, with each lead terminated by an alligator clip. The Reference
and Working electrode leads are shielded to protect the signals from
external interference. The alligator clips allow connection to a wide
variety of electrodes, and the leads are color–coded to indicate the
type of electrode to which they should be attached (Table 2–1).
For normal three–electrode potentiostat, page 15, or galvanostat,
page 16, use, the reference electrode must never be connected to
either the auxiliary (red) or working (green) leads, otherwise the current
that would be passed through the electrode could effectively destroy it
as a reference potential source.
When two–electrode potentiostat, or galvanostat, operation is required
the auxiliary and reference leads (red and yellow) should be attached
to the single ‘counter electrode’. The green lead is attached to the
working electrode.
When using in
ZRA
(zero resistance ammeter) mode, connect the
working (green) and auxiliary (red) leads to the two electrodes (or
circuit test points) across which to measure the current, page 16. The
reference lead (yellow) can be connected to a reference electrode (or
circuit test point) to measure the potential difference to the auxiliary
(and working) leads.
When using
High Z
(high impedance) mode, connect the working
(green) lead to one electrode and the reference lead (yellow) lead to a
reference electrode to measure the potential difference between the
leads, page 16. The auxiliary lead (red) can be connected to a third
To ensure good grip, the
electrode cable alligator
clips use a spring made
from a good quality steel
(stainless steel is
unsuitable for springs).
Avoid wetting of the
alligator clips, especially
with electrolyte solutions
which can hasten
corrosion. If the alligator
clips are wetted then
immediately disconnect
from the Potentiostat,
rinse the clips with a
little deionized water
from a wash bottle, to
remove the electrolyte,
and immediately dry by
patting with paper
tissue. The whole cable
must then be allowed to
dry thoroughly (several
hours at least) before
reuse.
Never immerse any part
of the electrode cable in
water, or other liquid!
Color Electrode
Yellow Reference
Green Working
Red Auxiliary
Table 2–1
Color–coding on the
leads of the electrode
cable.

8 eDAQ Potentiostats
electrode (or test point) to provide a ZRA current signal at E Out, Figure
2–3.
The Online Indicator
Located at the bottom right of the front panel is the Online indicator.,
Figure 2–1. When lit, it indicates that the software (such as EChem,
Chart or Scope) has located and initialised the Potentiostat. If the light
does not go on when the software is run, check that the Potentiostat is
properly connected. If there is still a problem, please refer to
Appendix B, page 95.
The Overload Indicator
Located on the left-hand side of the front panel is the Overload
indicator, Figure 2–1. When lit, this indicates that the Potentiostat is (or
has gone) out of compliance, which usually occurs because of an open
circuit or excessive resistance in the electrochemical cell. Higher
resistances can be often be encountered when electrodes are fouled by
the products of electrolysis reactions. The Potentiostat tries to
compensate by increasing the compliance potential (that is, the
potential between the auxiliary and working electrodes). If the
compliance voltage exceeds specification (about 11 V) potential control
of the cell is lost and drifting, or oscillation, of the signal can be seen.
Any data collected during this period is unreliable and should be
discarded.
The Overload indicator will light as soon as there is an overload and
will stay on until the recording has stopped.
If the indicator light comes on repeatedly, and your connections are
good, then try bringing your electrodes closer together, and/or
increasing electrolyte concentration, and/or modifying your
experimental conditions to avoid fouling of the electrodes. Redesigning
your electrochemical cell may be necessary. Normally cells are
designed to keep the reference and working electrodes very close
together, however, when a potential overload occurs, you also need to
consider the distance between the auxiliary and working electrodes.
Note that a potential overload is quite different from a current overload
condition. A current overload is caused when the current signal

Chapter 2 — The Potentiostat 9
exceeds the full scale limits of the range setting of the current channel,
and is usually caused by a low resistance between the electrodes.
The Back Panel
The back panel of the Potentiostat is shown in Figure 2–3.
E Out, I Out and E In Connectors
The Potentiostat back panel has three BNC connectors labelled E Out,
I Out, and E In. The E In is connected to the Output of the
e-corder
,
usually Output + is used.Reverse the polarity of the Potentiostat by using
e-corder
Output –.
E Out I Out E In
Input Output
I C
Bus
I C
2
BNC output
connectors
DB-9 pin, I2C connectors
4 mm socket,
ground connection
BNC input
connector
Digital Ground
Regulated –17 V DC
Regulated +8 V DC
Regulated +17 V DC
Power lines
SCL
DSC
SDA
DSD
INT
I2C control signals
Digital Ground
Regulated –17 V DC
Regulated +8 V DC
Regulated +17 V DC
SCL
DSC
SDA
DSD
INT
I2C control signals
Input Output
1
69
5 5
96
1
Figure 2–3
The Potentiostat back
panel.
Figure 2–4
The pin assignments for
the I2C DB-9 connectors.

10 eDAQ Potentiostats
The Potentiostat provides two signals: the current signal (I Out)
indicating the current flow between the working and auxiliary
electrodes, and the potential signal (E Out) indicating the potential
difference between the working and reference electrodes. Note that the
E Out signal is inverted with respect to the applied potential.
For most situations I Out is connected to e-corder input channel 1, and
E Out to e-corder input channel 2. However, when you are using Chart
software and recording data from various sources on more that just two
channels you may want to connect the Potentiostat to other e-corder
input channels.
I2C Connectors
The Potentiostat back panel, Figure 2–3, has two DB-9 pin ‘I2C bus’
connectors labelled Input and Output. The Input connector provides
power to the Potentiostat and carries the various control signals (for
gain range and filter selection) to and from the e-corder. A cable is
provided with the Potentiostat for this purpose. The pin assignments are
shown in Figure 2–4.
The Output connector can be used for the attachment of other eDAQ
Amps.
More information about the I2C connector can be found in your
e-corder Manual.
Grounding Connector
The Potentiostat back panel, Figure 2–3, has a 4 mm grounding socket.
This enables connection of a Faraday cage (with the green grounding
cable included with the Potentiostat) the use of which can greatly
diminish electrical noise. The Potentiostat is supplied with a green
colored ground cable terminated with a 4 mm pin (attaches to
Potentiostat back panel) and an alligator clip (for attachment to
Faraday cage). If your Faraday cage is already earthed by its own
ground connection then you should not use this cable (otherwise a
second pathway to earth would exist which could result in a ‘ground
loop’ and increased signal interference! You can try grounding the
Faraday cage via its own connection to earth, or via the Potentiostat
ground cable — but not by both methods simultaneously.
▲
WARNING!
The I2C connectors are
for the power and
control of eDAQ Amps,
page 2, and should not
be used for connection
to any other device.

Chapter 2 — The Potentiostat 11
The construction of the Faraday cage can range from a simple
cardboard box covered with aluminium foil, in which the
electrochemical cell is located, to a more sophisticated copper mesh
enclosure or sheet-metal box. But in all cases, it is essential that the
Faraday cage be electrically grounded to act as an effective shield
against electrical interference.
The Potentiostat itself is grounded via its connection to the e-corder unit
which is in turn earthed via the three pin mains power connector. It is of
course important that the power socket that you are using is well
earthed.
Connecting the Potentiostat
Your Potentiostat will have been supplied with an I2C cable (DB–9 pin
connectors at either end), and three cables with BNC connectors at
either end.
First make sure that the e-corder is turned off. Then connect the I2C
cable to the I2C connector on the back panel of the e-corder, and the
other the other end to the I2C Input connector on the back panel of the
Potentiostat. Use the three BNC cables to connect the back panel of the
Potentiostat to the front panel of the e-corder as shown in Table 2–2.
With these connections, when you use the software to set a more
positive voltage, a more oxidising potential will be applied at the
working electrode.
Potentiostat rear panel e-corder front panel
I Out Input 1
E Out Input 2
E In Output +
Potentiostat rear panel e-corder front panel
I Out Input 1
E Out Input 2
E In Output –
Table 2–2
Potentiostat to e-corder
connections as shown in
Figure 2–5 and Figure
2–6.
Table 2–3
Potentiostat to e-corder
connections, reverse
polarity.

12 eDAQ Potentiostats
Such an arrangement is shown in Figure 2–5 and Figure 2–6.
To operate the Potentiostat with the reverse polarity make the
connections as shown in Table 2–3. With these connections, when you
use the software to set a more positive voltage, a more reducing
potential will be applied at the working electrode.
Check that all connectors are firmly attached. Loose connectors can
cause erratic behaviour, or may cause the Potentiostat to fail to work.
Trigger
Power
Status Output
Input 1 Input 3Input 2
Input 4
401
Overload
Potentiostat
Figure 2–5
The Potentiostat shown
connected to an
e-corder, front view, as
described in Table 2–2.
Figure 2–6
The Potentiostat shown
connected to an
e-corder, back view.

Chapter 2 — The Potentiostat 13
The Potentiostat uses two e-corder input channels during normal
operation. The reminder of this chapter assumes that you have
connected the current signal to e-corder Input Channel 1 and the
potential signal to e-corder Input Channel 2. (It is possible when using
Chart or Scope software to connect the Potentiostat to other e-corder
input channels, in which case the description that follows would change
accordingly).
When using EChem software, Channel 1 is always set to be the current
signal (the I channel), and Channel 2 is automatically set to be the
potential signal (the E channel). Thus when using EChem software you
must always connect the current signal (I Out) to Input Channel 1, and
the potential signal (E Out) to Input Channel 2 of the e-corder.
Channel 2 normally displays the applied potential, and its settings are
controlled using the standard Input Amplifier dialog box, described in
the Chart Software Manual and Scope Software Manual which are
installed as pdf files in the eDAQ Documentation folder on your
computer hard disk.
First Use
After you have installed the software, connected the e-corder and
computer as described with the booklet supplied with the e-corder
system, and connected the Potentiostat as described above, you are
ready to begin.
When the e-corder is turned on, and Chart software started, the
Potentiostat Online indicator (green) should light.
From the Channel 1 Function pop-up menu, select the ‘Potentiostat’
command, which opens the Potentiostat Control window, Figure 2–7
(Windows), or Figure 2–8 (Macintosh).
This window allows you to preview the current signal without actually
recording the signal to your computer’s hard disk. (If the menu says
‘Input Amplifier’ instead of ‘Potentiostat’ then the software has not
recognised the Potentiostat. Exit the software, check all your
connections and try again).
By default, the control window opens with the Potentiostat in Standby
mode, that is with the reference and working electrodes isolated so that

14 eDAQ Potentiostats
no current will flow through your electrodes. To connect to the
Potentiostat lead wires you must select Real mode. When you click
Cancel or OK the Potentiostat will revert to Standby mode until
recording is started.
Now select Dummy mode operation. You will need to adjust the gain
range to 20µA to accommodate your signal amplitude. You can now
adjust the applied potential with the slider bar, or by entering the exact
potential with the A-button. The resulting current signal should obey
Ohm’s law:
I = E/R
so that an applied potential of 1 V should produce a current of 10 µA,
while other potential settings should produce corresponding currents.
Potentiostat Control Window
With Chart software, the Potentiostat Control window is accessed from
the Potentiostat command in the Channel Function pop-up menu. Figure
2–7 shows the control window on a Windows computer, and Figure
Select low-pass
filter
Select input range
Pause/resume scrolling
Signal display area
Select
operating
mode
Applied potential controls iR Compensation controls
Select cell
mode
Select Potentiostat in
Channel pop-up menu
Mains filter
on/off
Stabilization
on/off
Zero point
calibrations
Signal invert
Figure 2–7
Potentiostat controls with
Chart software
(Windows).

Chapter 2 — The Potentiostat 15
2–8 on a Macintosh computer. These windows control the various
current ranges and filtering options for the Potentiostat.
With Scope software, the corresponding controls are shown in Figure
2–9.
Modes of Operation
The EA161 Potentiostat can be operated in several different modes by
selecting the appropriate radio button:
• Potentiostat (Chart, Scope or EChem software), described below.
For three–electrode use connect the working (green), reference and
auxiliary (red) leads appropriate electrodes (or circuit test points)
The current signal is provided at I Out, Figure 2–3. The potential
signal is provided at E Out. When two–electrode potentiostat
Select
operating
mode
Select Potentiostat in the
Channel pop-up menu
Signal display area
Drag ticks and
labels to adjust axis
Pause/Resume
scrolling
Axis expansion/
contraction
Set applied
potential
Select low-
pass filter
Select cell
mode
Select input
range
Mains filter
on/off
Set iR
compen-
sation
Invert current
signal
Figure 2–8
Potentiostat controls with
Chart software
(Macintosh).

16 eDAQ Potentiostats
operation is required the auxiliary and reference leads (red and
yellow) should be attached to the single ‘counter electrode’.
• Galvanostat (Chart and Scope software), page 77 – 82. Connect
the electrodes as described for potentiostat operation, above. Note
especially that the potential signal is provided at I Out, Figure 2–3.
The current signal is provided at E Out.
• ZRA,zero resistance ammeter, (Chart and Scope software).
Connect the working (green) and auxiliary (red) leads to the two
electrodes (or circuit test points) across which to measure the current,
the current signal is provided at I Out. The auxiliary (red) lead is
earth return. The reference lead (yellow) can be connected to a
reference electrode (or circuit test point) to measure the potential
difference to the auxiliary (and working) leads. The high impedance
potential signal (if used) is supplied at E Out, Figure 2–3.
• High Z, high impedance voltmeter (Chart and Scope software).
Connect the working (green) lead to one electrode and the reference
lead (yellow) lead to a reference electrode to measure the potential
difference between the leads. The high impedance potential signal
is delivered at I Out. The auxiliary lead (red) can be connected to a
third electrode (or test point) to provide a ZRA current signal at E
Out, Figure 2–3.
Please make sure the electrode lead wires are connected appropriately
to your experiment, before operating in any of these modes. In
particular, incorrect placement of leads may damage the reference
electrode, if one is being used.
Signal Display
The current signal is previewed in the scrolling display area. Note that
the signal is not being recorded to hard disk at this stage, and that
when the window is closed the signal trace will be lost.
By using the Dummy or Real modes you can investigate the effect of the
Applied Potential, page 21, on the current signal.
You can stop/start the signal scrolling by clicking the Pause/Resume
button .
NOTE. When using
early models of EA161
Potentiostat (serial
numbers 161-001 to
161-022) as a ZRA you
should connect the
working electrode lead,
and the cable of the
Grounding Connector
(page 10), to the two
electrodes (or circuit test
points) across which to
measure the current.
This manual suits for next models
2
Table of contents
Other eDAQ Laboratory Equipment manuals
Popular Laboratory Equipment manuals by other brands

Baker
Baker SterilGARD III Advance Operator's manual
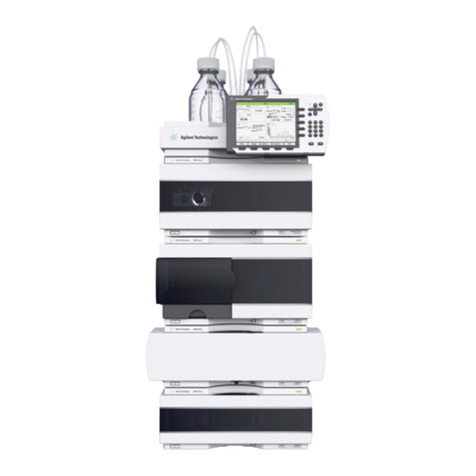
Agilent Technologies
Agilent Technologies 1260 Infinity user manual

Phcbi
Phcbi PR-L5181W-PA operating instructions

Pfeiffer Vacuum
Pfeiffer Vacuum Prisma QMS 200 operating manual
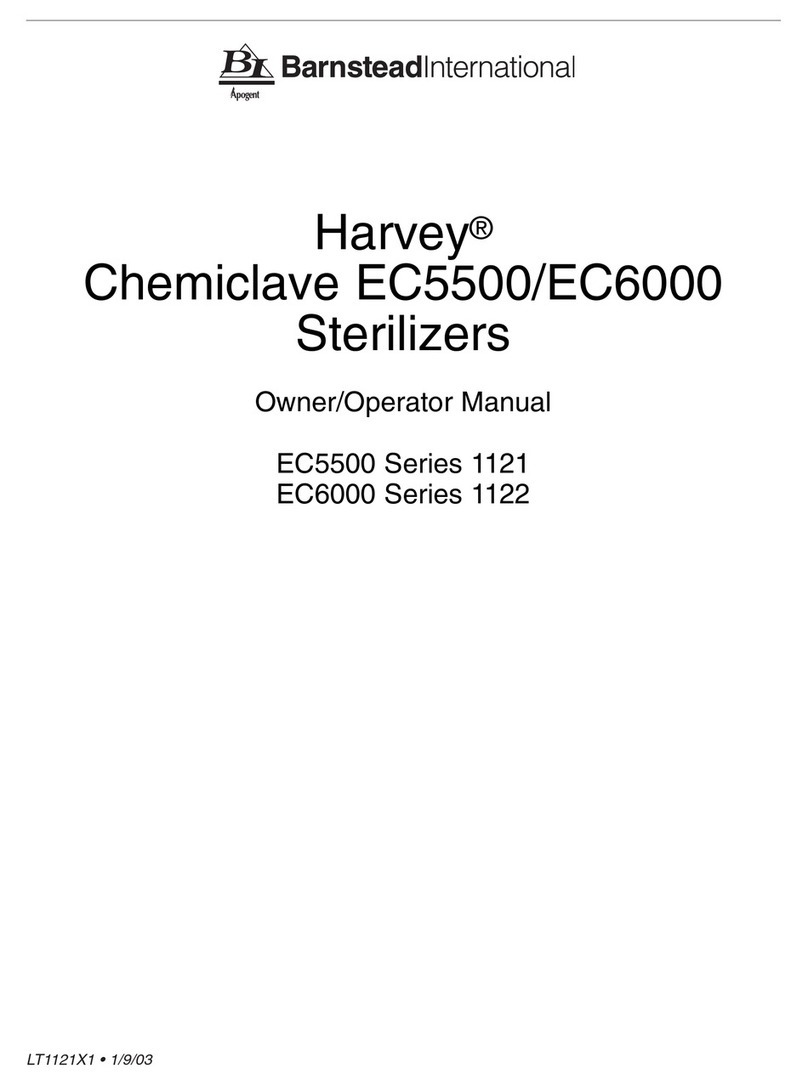
Barnstead
Barnstead Harvey EC6000 Owner's/operator's manual

Beckman Coulter
Beckman Coulter TLA-55 Instructions for use
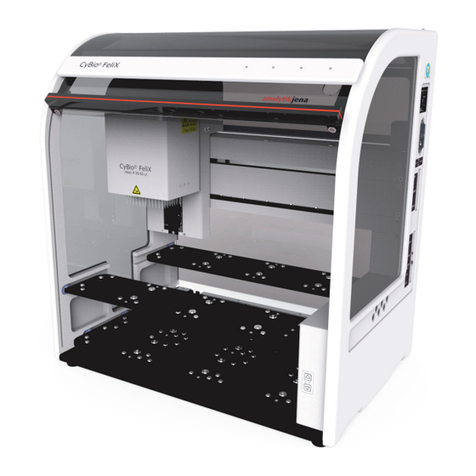
Endress+Hauser
Endress+Hauser Analytik Jena CyBio FeliX operating instructions
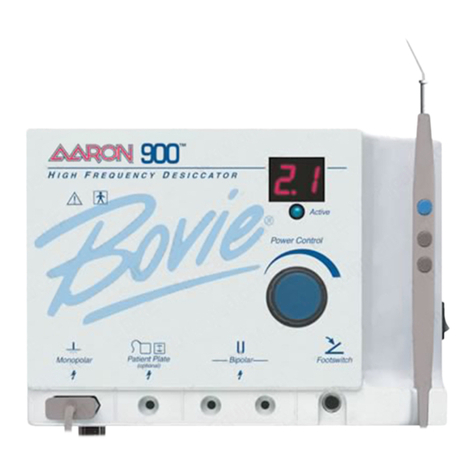
Bovie
Bovie AARON 800-EU user guide
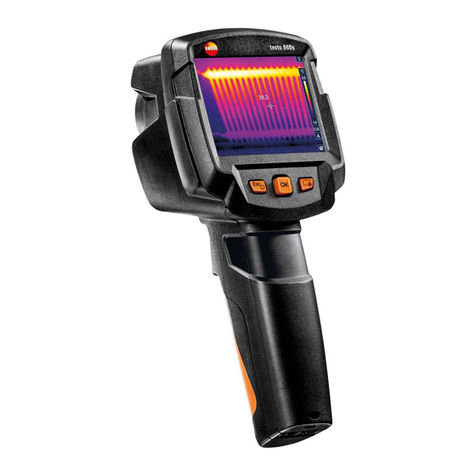
TESTO
TESTO 865s instruction manual
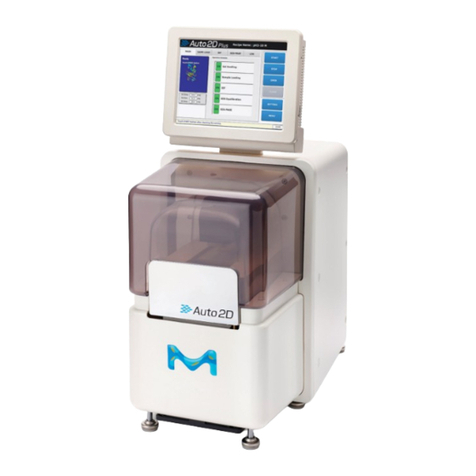
Merck
Merck Millipore Auto2D Plus quick start guide

SciCan
SciCan Statim 2000 Service manual

INOXPA
INOXPA MCR Series Installation, service and maintenance instructions