ELECTRODRIVE Tug Axis 5T User manual

Tug Axis 5T
Operating Manual

Tug Axis 5T Operating Manual—OM0021E
This manual contains important safety, installation and operating instructions for this
unit. Read this manual thoroughly and completely, and retain for future reference. This
unit can cause serious injury to personnel or damage to property if used incorrectly,
therefore do not use this machine for any other purpose apart from its intended use.
Using this unit incorrectly may void warranty.
Any damage audible or visible to this unit should be addressed at the time of discovery.
Electrodrive Pty Ltd can provide parts and service support on request through its
service partner company:
Serviced Equipment Pty Ltd
p: 1300 934 471
e: service@fallshaw.com.au
Made in Australia by:
Electrodrive Pty Ltd
2A Ayton Street, Sunshine North VIC Australia 3020
p: 1300 934 471 (within Australia)
p: +61 (03) 9300 8521 (International)
w: www.electrodrive.com.au
© Electrodrive

Tug Axis 5T—Operating Manual
3
Contents
Introduction..................................................................................................................... 5
Features ....................................................................................................................... 5
Operating instructions ................................................................................................... 6
Controls ........................................................................................................................ 7
Driving instructions ........................................................................................................ 9
Safety check ................................................................................................................. 9
Hitching to a trolley....................................................................................................... 9
Unhitching................................................................................................................... 11
Steering....................................................................................................................... 11
Charging ..................................................................................................................... 11
Maintenance ................................................................................................................. 12
Batteries...................................................................................................................... 12
Tyres............................................................................................................................ 12
Motor and transmission.............................................................................................. 12
Transmission............................................................................................................... 12
Brakes......................................................................................................................... 12
Motor .......................................................................................................................... 12
Motor controller .......................................................................................................... 12
Throttle lever ............................................................................................................... 13
Fuses .......................................................................................................................... 13
Self-resetting circuit breaker....................................................................................... 13
Warranty ........................................................................................................................ 14
Unauthorised maintenance......................................................................................... 14
Misuse ........................................................................................................................ 14
General wear items not covered under warranty........................................................ 14

4
Appendix 1: Machine rating conditions...................................................................... 15
Appendix 2: Wiring diagram ........................................................................................ 16
Appendix 2: Charging procedures for SLA batteries ................................................ 18
Appendix 3: Spare parts list......................................................................................... 19
Service log .................................................................................................................... 21

Tug Axis 5T—Operating Manual
5
Introduction
Move your existing manual trolleys with the battery powered Tug Axis 5T.
The Tug Axis 5T simply hooks on to your existing trolley with an auto-latching hitch. This
converts your heavy trolley into a powerful, easy to move motorised unit. Productivity is
greatly increased, and back or shoulder strain is eliminated.
Features
§Rated tow capacity: Up to 5000 kg.
§24 Volt DC power.
§Variable speed drive unit.
§Electro-magnetic park brake.
§Travel speed—up to 3 km/h.
§Robust steel chassis.
§Tiller handle steering that folds up to reduce space when not in use.
§Programmable motor controller.
§Automatic charger.
§Multiple speeds.

6
Operating instructions
Tiller control
Controls
Auto-latching
hitch
Tiller arm
Tiller post
Hitch release
Emergency stop
Key switch
Battery level indicator
Speed selector
Throttle lever
Optional horn Emergency back-o
button
Direction selector

Tug Axis 5T—Operating Manual
7
Controls
Key switch
The key switch must be turned clockwise to switch the unit on. When the unit is on, the
LED status indicator will be illuminated and the strobe light will ash. It is important to
note that the unit should be switched o and the key removed, whenever it is not in use.
This eliminates the risk of unauthorised movement and also prevents an unnecessary
use of battery power.
Emergency stop button and emergency back-o button
The controls have two emergency buttons.
1. Emergency stop button—in an emergency, push this button to stop the unit.
To release, slightly twist the button and it will pop back up.
2. Emergency back-o button—when pressed, the tug will momentarily travel
backwards to avoid pinning the operator against an obstacle, and then stop if the
throttle lever is not released. If this button is pressed when the throttle is released,
the tug will immediately stop. To reset the back-o function, switch o and switch
back on).
Only use the emergency buttons in an emergency.
Direction selector
Toggle the switch to select the desired
direction of travel (forward/reverse).
Throttle lever
This lever provides variable speed control
from zero up to 100% of the governed speed.
Releasing the lever will cause the tug to
decelerate and stop within three seconds.
Speed selector
The speed selector will always start in the SLOW position. Select a speed that you are
comfortable using. The speed can be changed whilst driving. It is advisable that you
operate this unit at a slow speed when entering a conned area.

8
Battery level indicator
The battery level indicator indicates the amount of charge left in the batteries. When it
appears to be running low, return the unit to the closest charging station to charge the
batteries. Being aware of the level of charge of the batteries will eliminate the possibility
of running low on power whilst away from the charging station. Red light only indicates
no usable battery power remaining.
Horn (where tted)
Push to sound the horn, release to turn o.
Charger socket
The charger socket is located on the body panel of the unit, next to the tiller post.
Brakes
When the speed control lever is released, the unit is slowed electrically by dynamic
braking until the machine and load comes to a complete stop.
Capacity
Refer to the serial sticker for the unit’s safe working load, located on the body adjacent
to the tiller post.

Tug Axis 5T—Operating Manual
9
Driving instructions
Safety check
Before using the powered tug, the operator should complete the following check:
1. The battery charger is not connected.
2. The direction selector works.
3. The emergency stop button is released.
4. The brakes operate correctly when the throttle lever is released.
5. The battery indicator shows adequate charge.
6. There is no visible damage to the unit.
7. Back-o button works correctly.
Hitching to a trolley
This tug is tted with an auto-latching hitch. Other hitches are also available.
1. Facing the tug, unhook the hitch release handle and move it backward.
This unlocks the auto-latching hitch.
1. Pull the hitch release
lever to unhook.
The trolleys’ hitch bar.

10
In all cases, ensure that the trolley being attached to has its brakes engaged (or chocked)
and is free from obstruction. Inspect the trolley and ensure that the trolley castors are in
good condition.
It is STRONGLY RECOMMENDED that the operator lead the tug and
trolley, rather than using the tug to “push” the trolley. This will ensure
that the operator has a safe unobstructed view ahead. This will also make
the tug and trolley easy to manoeuvre.
Towing a trolley with castors in poor condition can overload the tug,
and cause damage not covered under warranty.
This tug is not designed for use on inclined surfaces and doing so may
pose a risk of accident or injury. Use this Tug on level ground only.
2. Carefully reverse the tug back onto
the trolley’s tow bar until the tug hitch
sits over the tow bar.
3. Once aligned, move the tug forward.
This will automatically lock the tug hitch
over the trolley’s tow bar.

Tug Axis 5T—Operating Manual
11
Unhitching
Always make sure the trolley is on a at level surface and apply the castor brakes
(if tted) or chock the trolley wheels.
1. Unhook the hitch release handle by pulling towards operator to unlock the hitch.
2. Carefully drive the tug forward away from the trolley.
Steering
The tiller arm provides easy steering. The tug with an attached trolley can be
manoeuvred through tight areas.
This unit’s power transmission system is a transaxle arrangement.
Obstruction or resistance to one wheel will cause driving power to be
transmitted through to the wheel that is free. This may cause the tug to spin
out of control. Please ensure a clear and clean path ahead when operating
the tug.
Charging
Ensure regular recharging of batteries (charging overnight after a day’s usage is
recommended). Irregular charging may cause the batteries to prematurely fail.
Leaving a machine in storage without charge for periods greater than a month can also
lead to premature battery failure. This is not covered under warranty.
For detailed charging procedures refer to Appendix 2. Misuse of the battery will void
warranty.
Only use the battery charger supplied with this tug.
The automatic features of the supplied charger ensures that the sealed gel
batteries are not overcharged, and only a minimum amount of gas, if any at
all, are expelled during charging.

12
Maintenance
Batteries
If this unit is not being used for an extended period of time, it should be connected to
the battery charger to check the battery level on a regular basis, and placed on charge
overnight if required. This will ensure the batteries are kept in good condition.
The batteries are sealed and maintenance free. DO NOT attempt to open these
batteries. If the unit is not charged as above, the batteries may be exhausted and have
dropped below the charging threshold of the battery charger. The supplied charger
cannot begin to charge the batteries unless they have a small amount of charge. If this
occurs, contact Electrodrive or your local service agent.
A sign that the batteries need replacing is when they no longer hold charge.
Tyres
The tyres are rubber, giving it punture-proof characteristics. For replacement tyres,
please refer to the spare parts section in this document or contact Electrodrive.
Motor and transmission
The transaxle is a sealed unit and does not require regular maintenance.
Transmission
The tension in the transmission chain should be checked every 3 months. Ensure that
the chain has no more than ±10 mm deection. Light lubrication can also be applied in
3 month intervals.
Brakes
The dynamic braking system does not require regular maintenance.
Motor
Motor brushes should be inspected every six months and replaced every 2 years.
Remove the brush retaining cover for access to the brushes, should they need
replacing.
Motor controller
This unit is not serviceable. Any diculties experienced with speed control should be
referred to Electrodrive.

Tug Axis 5T—Operating Manual
13
Throttle lever
The throttle lever and cable do not require maintenance. Should the lever or cable suer
damage they should be replaced. If the handle loosens with wear, the hinge nut can
be gently tightened. However, rst conrm that the lever is in the correct position as it
may need to be reset. (Test by squeezing the lever slightly. The tug should slowly move,
release and the tug should completely stop).
Fuses
The control circuit is protected against inadvertent current over-loads. This fuse is
located adjacent to the controller under the top cover.
Self-resetting circuit breaker
This Tug is tted with a self resetting circuit breaker in case of momentary over-load.
This circuit breaker can be found beneath the top cover on the battery carrier. If the unit
repeatedly over-loads, test the machine, as the motor may be damaged, and continued
use could damage the unit further.

14
Warranty
Electrodrive Pty Ltd warrants that this product is free from defects in materials and
workmanship for a period of twelve months from the date of dispatch from the
Electrodrive plant. The battery has a six month warranty.
If a defect is reported, Electrodrive will repair or replace the defective part, at its own
discretion. This warranty does not apply if this unit has been misused, damaged, or
modied in any way.
Please be aware that modications and misuse will void your warranty. The following
activities (including, but not limited to) are examples of these:
Unauthorised maintenance
§The machine is re-wired by an unauthorised service agent.
§The motor controller is re-programmed by an unauthorised service agent.
§There are modications to the body or frame of the machine.
§Use of non-specied parts.
§The machine is serviced by an unauthorised service agent.
Misuse
§Shunting loads at speeds in excess of 2 km/h.
§Overloading the unit either during towing or lifting.
§Carrying people or other foreign objects.
§Exposed to rain or other precipitation, unless weatherproof option is installed.
§Using the emergency back-o system to change direction regularly.
§Exposed to a corrosive environment.
§Driven o road—potholes, gravel, etc.
§Driven on slopes.
§Not being charged adequately.
§Using the emergency stop button as an ON/OFF button.
General wear items not covered under warranty
§Tyres and castors.
§Drive wheels and motor brushes.
§Hand grips.

Tug Axis 5T—Operating Manual
15
Appendix 1: Machine rating conditions
Model Working Load Limit Max Load
TUGAXIS5TNH 5000 kg 5000 kg
The Tug Axis 5T has been designed to move the rated weight capacity on a level rm
surface. Variations in the working environment may impede the performance of this unit.
Such parameters include (but are not limited to) the following:
• Ramps and sloped surfaces.
• Soft surfaces (for example carpet).
• Slippery surfaces (gravel, water, oil on the ground, etc).
It is important that the Tug Axis 5T IS NOT to be operated outside of
the recommended conditions.
900 mm1740 mm
905 mm 650 mm

16
Notes
Appendix 2: Wiring diagram
10kΩ
PCB: EDEL2851
Membrane Control Board
JP4
JP5
JP1
Throttle
JP2 - E/Stop +
Keyswitch
JP3 - Output to controller
JP6 - Rear of board
Input from membrane
1
2
1
2
3
4
5
6
7
8
9
10
11
12
3
2
1
2
1
6
5
4
3
2
1
20
19
18
17
16
15
14
13
12
11
10
9
8
7
6
5
4
3
2
1
JP7
2
1
PCB: EDEL2856
Change of direction
Board
JP6
2
1
6
5
4
3
2
1
BATTERY GAUGE
+15v
+
+
+
+
+
++
+ + + + +
FAST
WALK
SLOW
<= DIRECTION =>
Control
Keyswitch
FUEL GUAGE
P/N: PCBARNF
P1
P2
P3
P4
WHITE
P5
P6
P7
P8
P9
P10
P11
P12
5k Throttle
potentiometer
Emergency Reverse
Back-off Button
EL2775: Tiller Membrane
12 CORE MULTI COLOUR
NC
NC
WHITE
Jumper 24v
Drawing Key
Cable 192/0.22 6mm2
Cable 14/.2 1.13mm2
Cable 7/0.2 0.22mm2
Black
Blue
Brown
Green
Grey
Orange
Pink
Purple
Red
Tan
White
Yellow
REV DCN/SI
DESCRIPTION
DATE
BY
CHD
APPD
0 6434
NEW WIRING DRAWING CREATED
21/08/2020
SV
AR
RP
TOLERANCE REQUIREMENTS
-
-
-
-
Purchased
COLOUR
PROCESS
TREATMENT
FINISH
Loom - Tiller membrane Loom P/N#CL1052
Dimensions in
milimeters unless
specified.
2A Ayton Street, North Sunshine, VIC 3020
Phone: (+61) 03 9300 8500 Fax: (+61) 03 9312 3441
Unless Otherwise Stated Are:
No Decimal Place = +/- 0.5
One Decimal Place = +/- 0.1
Two Decimal Places = +/- 0.05
TOLERANCES MUST NOT BE
CUMULATIVE UNLESS
OTHERWISE SPECIFIED.
Kg
LOCATION
DO NOT SCALE FROM DRAWING
REMOVE ALL BURRS & SHARP EDGES
DIMENSIONS MARKED WITH
ARE SIGNIFICANT INSPECTION DIMENSIONS.
MASS
N/A
1/2
MATERIAL
SCALE:
Part Number
PAGE:
SIZE:
A3
Rev
©
Tuesday, 15 September 2020
- This dimensioned drawing is the property of Fallshaw Pty Ltd. It is supplied only to aid the making of parts for Fallshaw, and must not be used against
their interests, supplied to 3rd parties, be copied, reproduced, used for manufacture or for any other purpose without the prior written permission of Fallshaw Pty. Ltd.
0
Description
F:\SVN\Electrodrive\Standard Parts\Eleccomps\Wiring diagrams\WIRTLHND
WIRTLHND
10kΩ
PCB: EDEL2851
Membrane Control Board
JP4
JP5
JP1
Throttle
JP2 - E/Stop +
Keyswitch
JP3 - Output to controller
JP6 - Rear of board
Input from membrane
1
2
1
2
3
4
5
6
7
8
9
10
11
12
3
2
1
2
1
6
5
4
3
2
1
20
19
18
17
16
15
14
13
12
11
10
9
8
7
6
5
4
3
2
1
JP7
2
1
PCB: EDEL2856
Change of direction
Board
JP6
2
1
6
5
4
3
2
1
BATTERY GAUGE
+15v
+
+
+
+
+
++
+ + + + +
FAST
WALK
SLOW
<= DIRECTION =>
Control
Keyswitch
FUEL GUAGE
P/N: PCBARNF
P1
P2
P3
P4
WHITE
P5
P6
P7
P8
P9
P10
P11
P12
5k Throttle
potentiometer
Emergency Reverse
Back-off Button
EL2775: Tiller Membrane
12 CORE MULTI COLOUR
NC
NC
WHITE
Jumper 24v
Drawing Key
Cable 192/0.22 6mm2
Cable 14/.2 1.13mm2
Cable 7/0.2 0.22mm2
Black
Blue
Brown
Green
Grey
Orange
Pink
Purple
Red
Tan
White
Yellow
REV DCN/SI
DESCRIPTION
DATE
BY
CHD
APPD
0 6434
NEW WIRING DRAWING CREATED
21/08/2020
SV
AR
RP
TOLERANCE REQUIREMENTS
-
-
-
-
Purchased
COLOUR
PROCESS
TREATMENT
FINISH
Loom - Tiller membrane Loom P/N#CL1052
Dimensions in
milimeters unless
specified.
2A Ayton Street, North Sunshine, VIC 3020
Phone: (+61) 03 9300 8500 Fax: (+61) 03 9312 3441
Unless Otherwise Stated Are:
No Decimal Place = +/- 0.5
One Decimal Place = +/- 0.1
Two Decimal Places = +/- 0.05
TOLERANCES MUST NOT BE
CUMULATIVE UNLESS
OTHERWISE SPECIFIED.
Kg
LOCATION
DO NOT SCALE FROM DRAWING
REMOVE ALL BURRS & SHARP EDGES
DIMENSIONS MARKED WITH
ARE SIGNIFICANT INSPECTION DIMENSIONS.
MASS
N/A
1/2
MATERIAL
SCALE:
Part Number
PAGE:
SIZE:
A3
Rev
©
Tuesday, 15 September 2020
- This dimensioned drawing is the property of Fallshaw Pty Ltd. It is supplied only to aid the making of parts for Fallshaw, and must not be used against
their interests, supplied to 3rd parties, be copied, reproduced, used for manufacture or for any other purpose without the prior written permission of Fallshaw Pty. Ltd.
0
Description
F:\SVN\Electrodrive\Standard Parts\Eleccomps\Wiring diagrams\WIRTLHND
WIRTLHND

Tug Axis 5T—Operating Manual
17
12 Volt
Battery
-
+
Curtis 1229-3201 Controller
P/N: CONCURTIS-1229
1
9
16
23
15
8
M1
M2
B+
B-
12 Volt
Battery
-
+
TRANSAXLE 600W
P/N: MOTTRAN600WAL
Park Brake
Drive
Motor
P1P2
P3
P4P5P6
BRAKE RELEASE
CONNECTOR
P12
P11
P10
P9
P8
P7
P6
P5
P3
P2
P1
P4
WHITE
FUEL GUAGE
P/N: PCBARNF
7
6
5
4
1
2
3
POW1 BATTERY PACK
24V 100AH
P/N: BATGEL12V100AHRE
CB1 Circuit Breaker 60A
P/N: EL1919
Charger Socket
P/N: PLG7PINHDNYLON
Stobe light
P/N: LHTAMBER24V
K
PROGRAMMER
K
F1 FUSE 3A
P/N: FUS003ACHG3AG
F2 FUSE 30A
P/N: FUSMAXIB30A
REL1
MAIN CONTACTOR
P/N: RELCONT24VONOFF
REL 2
INHIBIT RELAY
P/N: RELCO24V
P1P2P3
P4P5P6
1
2
3
456
7
8
X
X
BRAKE KEY RELEASE TO CONNECTOR DETAILS
ALTERNATIVE
POSITION
NC
NC
Drawing Key
Cable 192/0.22 6mm2
Cable 14/.2 1.13mm2
Cable 7/0.2 0.22mm2
Black
Blue
Brown
Green
Grey
Orange
Pink
Purple
Red
Tan
White
Yellow
REV DCN/SI
DESCRIPTION
DATE
BY
CHD
APPD
0 6434
NEW WIRING DRAWING CREATED
21/08/2020
SV
AR
RP
TOLERANCE REQUIREMENTS
-
-
-
-
Purchased
COLOUR
PROCESS
TREATMENT
FINISH
WIRE LOOM - 5T AXIS
Dimensions in
milimeters unless
specified.
2A Ayton Street, North Sunshine, VIC 3020
Phone: (+61) 03 9300 8500 Fax: (+61) 03 9312 3441
Unless Otherwise Stated Are:
No Decimal Place = +/- 0.5
One Decimal Place = +/- 0.1
Two Decimal Places = +/- 0.05
TOLERANCES MUST NOT BE
CUMULATIVE UNLESS
OTHERWISE SPECIFIED.
Kg
LOCATION
DO NOT SCALE FROM DRAWING
REMOVE ALL BURRS & SHARP EDGES
DIMENSIONS MARKED WITH
ARE SIGNIFICANT INSPECTION DIMENSIONS.
MASS
N/A
1/1
MATERIAL
SCALE:
Part Number
PAGE:
SIZE:
A3
Rev
©
Tuesday, 15 September 2020
- This dimensioned drawing is the property of Fallshaw Pty Ltd. It is supplied only to aid the making of parts for Fallshaw, and must not be used against
their interests, supplied to 3rd parties, be copied, reproduced, used for manufacture or for any other purpose without the prior written permission of Fallshaw Pty. Ltd.
0
Description
F:\SVN\Electrodrive\Standard Parts\Eleccomps\Wiring diagrams\WIRTUGCLS5T
WIRTUGCLS5T
12 Volt
Battery
-
+
Curtis 1229-3201 Controller
P/N: CONCURTIS-1229
1
9
16
23
15
8
M1
M2
B+
B-
12 Volt
Battery
-
+
TRANSAXLE 600W
P/N: MOTTRAN600WAL
Park Brake
Drive
Motor
P1P2
P3
P4P5P6
BRAKE RELEASE
CONNECTOR
P12
P11
P10
P9
P8
P7
P6
P5
P3
P2
P1
P4
WHITE
FUEL GUAGE
P/N: PCBARNF
7
6
5
4
1
2
3
POW1 BATTERY PACK
24V 100AH
P/N: BATGEL12V100AHRE
CB1 Circuit Breaker 60A
P/N: EL1919
Charger Socket
P/N: PLG7PINHDNYLON
Stobe light
P/N: LHTAMBER24V
K
PROGRAMMER
K
F1 FUSE 3A
P/N: FUS003ACHG3AG
F2 FUSE 30A
P/N: FUSMAXIB30A
REL1
MAIN CONTACTOR
P/N: RELCONT24VONOFF
REL 2
INHIBIT RELAY
P/N: RELCO24V
P1P2P3
P4P5P6
1
2
3
456
7
8
X
X
BRAKE KEY RELEASE TO CONNECTOR DETAILS
ALTERNATIVE
POSITION
NC
NC
Drawing Key
Cable 192/0.22 6mm2
Cable 14/.2 1.13mm2
Cable 7/0.2 0.22mm2
Black
Blue
Brown
Green
Grey
Orange
Pink
Purple
Red
Tan
White
Yellow
REV DCN/SI
DESCRIPTION
DATE
BY
CHD
APPD
0 6434
NEW WIRING DRAWING CREATED
21/08/2020
SV
AR
RP
TOLERANCE REQUIREMENTS
-
-
-
-
Purchased
COLOUR
PROCESS
TREATMENT
FINISH
WIRE LOOM - 5T AXIS
Dimensions in
milimeters unless
specified.
2A Ayton Street, North Sunshine, VIC 3020
Phone: (+61) 03 9300 8500 Fax: (+61) 03 9312 3441
Unless Otherwise Stated Are:
No Decimal Place = +/- 0.5
One Decimal Place = +/- 0.1
Two Decimal Places = +/- 0.05
TOLERANCES MUST NOT BE
CUMULATIVE UNLESS
OTHERWISE SPECIFIED.
Kg
LOCATION
DO NOT SCALE FROM DRAWING
REMOVE ALL BURRS & SHARP EDGES
DIMENSIONS MARKED WITH
ARE SIGNIFICANT INSPECTION DIMENSIONS.
MASS
N/A
1/1
MATERIAL
SCALE:
Part Number
PAGE:
SIZE:
A3
Rev
©
Tuesday, 15 September 2020
- This dimensioned drawing is the property of Fallshaw Pty Ltd. It is supplied only to aid the making of parts for Fallshaw, and must not be used against
their interests, supplied to 3rd parties, be copied, reproduced, used for manufacture or for any other purpose without the prior written permission of Fallshaw Pty. Ltd.
0
Description
F:\SVN\Electrodrive\Standard Parts\Eleccomps\Wiring diagrams\WIRTUGCLS5T
WIRTUGCLS5T
12 Volt
Battery
-
+
Curtis 1229-3201 Controller
P/N: CONCURTIS-1229
1
9
16
23
15
8
M1
M2
B+
B-
12 Volt
Battery
-
+
TRANSAXLE 600W
P/N: MOTTRAN600WAL
Park Brake
Drive
Motor
P1P2
P3
P4P5P6
BRAKE RELEASE
CONNECTOR
P12
P11
P10
P9
P8
P7
P6
P5
P3
P2
P1
P4
WHITE
FUEL GUAGE
P/N: PCBARNF
7
6
5
4
1
2
3
POW1 BATTERY PACK
24V 100AH
P/N: BATGEL12V100AHRE
CB1 Circuit Breaker 60A
P/N: EL1919
Charger Socket
P/N: PLG7PINHDNYLON
Stobe light
P/N: LHTAMBER24V
K
PROGRAMMER
K
F1 FUSE 3A
P/N: FUS003ACHG3AG
F2 FUSE 30A
P/N: FUSMAXIB30A
REL1
MAIN CONTACTOR
P/N: RELCONT24VONOFF
REL 2
INHIBIT RELAY
P/N: RELCO24V
P1P2P3
P4P5P6
1
2
3
456
7
8
X
X
BRAKE KEY RELEASE TO CONNECTOR DETAILS
ALTERNATIVE
POSITION
NC
NC
Drawing Key
Cable 192/0.22 6mm2
Cable 14/.2 1.13mm2
Cable 7/0.2 0.22mm2
Black
Blue
Brown
Green
Grey
Orange
Pink
Purple
Red
Tan
White
Yellow
REV DCN/SI
DESCRIPTION
DATE
BY
CHD
APPD
0 6434
NEW WIRING DRAWING CREATED
21/08/2020
SV
AR
RP
TOLERANCE REQUIREMENTS
-
-
-
-
Purchased
COLOUR
PROCESS
TREATMENT
FINISH
WIRE LOOM - 5T AXIS
Dimensions in
milimeters unless
specified.
2A Ayton Street, North Sunshine, VIC 3020
Phone: (+61) 03 9300 8500 Fax: (+61) 03 9312 3441
Unless Otherwise Stated Are:
No Decimal Place = +/- 0.5
One Decimal Place = +/- 0.1
Two Decimal Places = +/- 0.05
TOLERANCES MUST NOT BE
CUMULATIVE UNLESS
OTHERWISE SPECIFIED.
Kg
LOCATION
DO NOT SCALE FROM DRAWING
REMOVE ALL BURRS & SHARP EDGES
DIMENSIONS MARKED WITH
ARE SIGNIFICANT INSPECTION DIMENSIONS.
MASS
N/A
1/1
MATERIAL
SCALE:
Part Number
PAGE:
SIZE:
A3
Rev
©
Tuesday, 15 September 2020
- This dimensioned drawing is the property of Fallshaw Pty Ltd. It is supplied only to aid the making of parts for Fallshaw, and must not be used against
their interests, supplied to 3rd parties, be copied, reproduced, used for manufacture or for any other purpose without the prior written permission of Fallshaw Pty. Ltd.
0
Description
F:\SVN\Electrodrive\Standard Parts\Eleccomps\Wiring diagrams\WIRTUGCLS5T
WIRTUGCLS5T

18
Appendix 3: Charging procedures for
SLA batteries
§Always charge batteries when work is complete and the equipment is not required
for use.
§Opportunity charging is NOT recommended. This can also shorten battery life.
§Never leave batteries in a discharged state as this will shorten the batteries life.
§For maximum battery life, a battery must be recharged to 100% capacity. Recharging
less than 100% may result in premature battery failure. Batteries are not covered
under warranty if they are not recharged properly.
§If batteries are disconnected from the machine and not used for lengthy periods of
time, it is recommended to give them a maintenance charge once every two months.
Charging setup
§Ensure you have the correct charger for the batteries. The correct voltage and current
is important to ensure the full life of the batteries.
§Check all connections are tight and in good condition.
§The green charger LED will illuminate to conrm charging is in progress.
§If charger lights do not come on, call your service technician.
§When charger is plugged in, drive function of machine is automatically inhibited.
During charging
§Ensure there is enough airow to help keep the batteries as cool as possible.
§If the batteries are swollen turn o immediately and call your service technician.
§Always leave batteries on charge until the charge is COMPLETE. This is indicated
when charger LED turns o.
Charger manual
Please read BATCHA24V25A—Battery Charger Operating Manual for more information.

Tug Axis 5T—Operating Manual
19
Appendix 4: Spare parts list
Part number Description
EDACTGSTRU60STK Gas strut 60 stroke
EDBATGEL12V100AHRE Tug 12V 100Ah battery
EDBRG20630ID UC206 bearing suit shaft 30
EDBRG206PILHOU UCP206D1—pillow block cast
EDCIREXT20 Circlip-external-D1400-0200
EDCONCURTIS-1229 Curtis controller 1229-3201
EDEL1100 Blanking plug—13mm
EDEL1910 Circuit breaker—40Amp
EDEL1920 Circuit breaker—80Amp
EDEL2339 Emergency reverse system red
EDEL2380 Emergency stop button complete
EDEL2500 Glass fuse holder
EDEL2515 Fuse holder—maxi blade fuse
EDEL2720 Key switch with key-A126
EDEL2775 Membrane key pad suit tiller h
EDEL2835 Nylon mounting spacer male/female
EDEL2851 PCB membrane control board
EDEL2856 PCB tiller fwd/rev direction s
EDEL2920 Plug—4 way mini t
EDEL3010 Potentiometer—5K (internal)
EDEL3100 Relay 24volt for 48v system
EDGM1142 Bearing housing TT10 tow
EDGM1225 Bearing TT10 tow suit 35mm Sha
EDGM1400 Chain 08B1, 1/2" Tug HD 8B, TC
EDGM1480 Circlip—tiller hinge 1/2"
EDGM1501 Collar 1"x1/2" zinc plated
EDGM1810 Handgrip 7/8" x 5"—tiller BL
EDGM1950 Spring—lock/tow lever
EDGM2010 Rubber matting (1m width)
EDGM2040 Spring—tiller handle position

20
Part number Description
EDGM2051 Tiller pot spring straight leg
EDGM2150 Throttle cable and act arm
EDGM2170 Throttle lever
EDGM2171 Throttle lever guard
EDGM2210 Tiller pin—zinc plated
EDGM2306 Circlip external 30mm
EDJUR100/JZP J125 PU roller bearing
EDMOTTRAN600WAL Transaxle 600watt
EDPLG7PIN-P-30A-P Trailer charger plug 7PIN 30A
EDPLG7PIN-S-30A-A Trailer charger sock 7PIN 30A
EDSP1020 Sprocket 12T Bossed 08B, 20mm bor
EDSPHD08B34T Sprocket heavy duty 34T 8B-CHAIN
EDWH1186 Rim—8 x 3.3 suit press on ty
EDWH1463 Tyre press on 13.5x5.5x8
EDWIRTLHND Loom—Tiller membrane loom
EDWIRTUGCLS5T Wire loom—Tug Classic 5T
Table of contents
Other ELECTRODRIVE Jack manuals
Popular Jack manuals by other brands

TMG
TMG TMG-AJX22 product manual

Tractel
Tractel top BT 1.5 Operation and maintenance manual
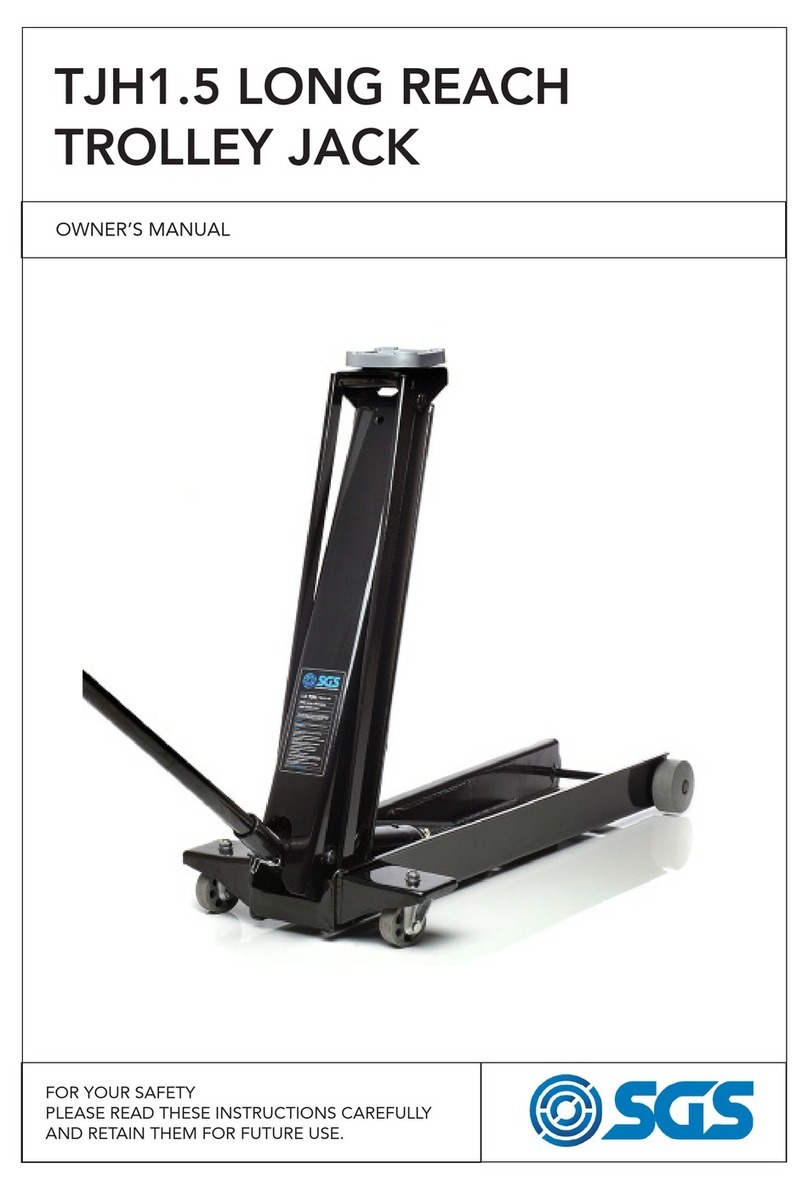
SGS
SGS TJH1.5 owner's manual
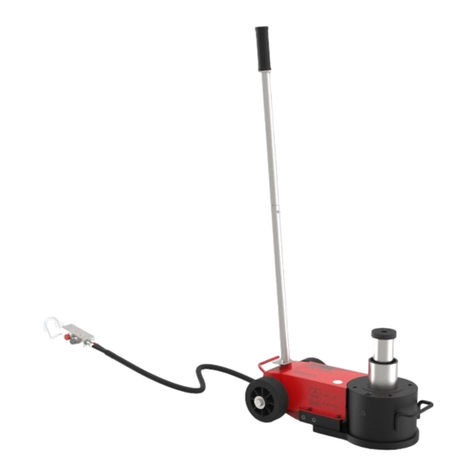
Cattini Oleopneumatica
Cattini Oleopneumatica YAK 215/P Operating and maintenance manual
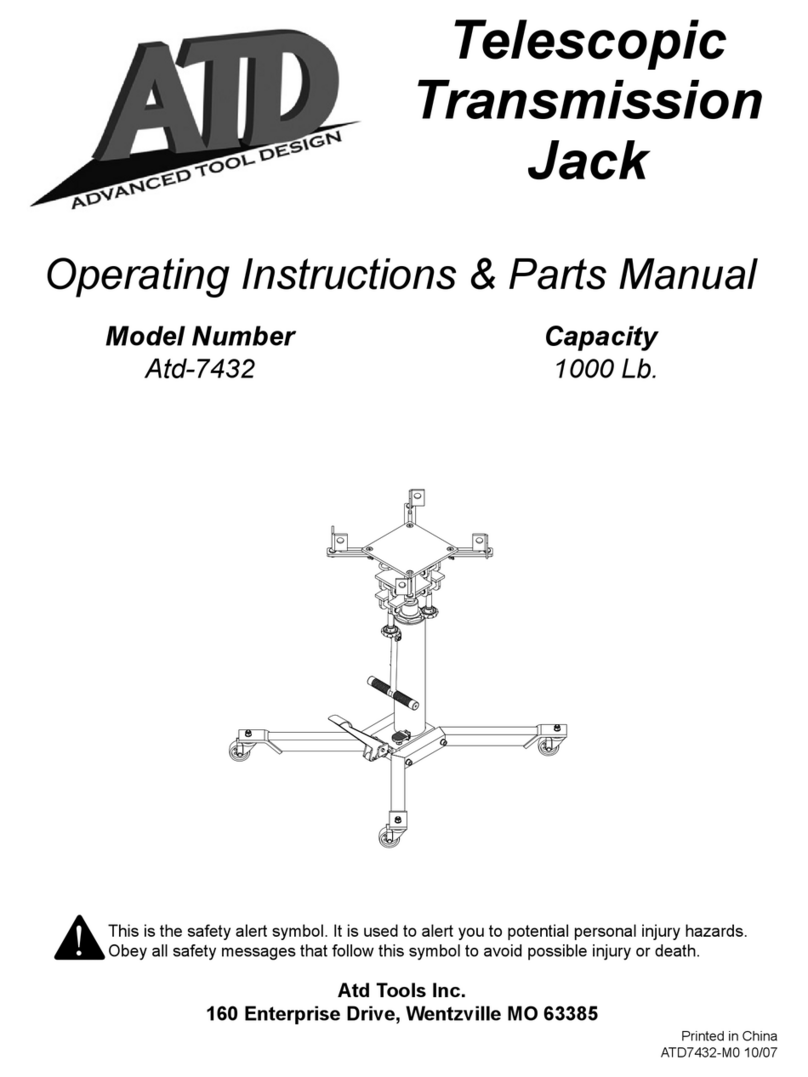
ATD Tools
ATD Tools Atd-7432 Operating instructions & parts manual
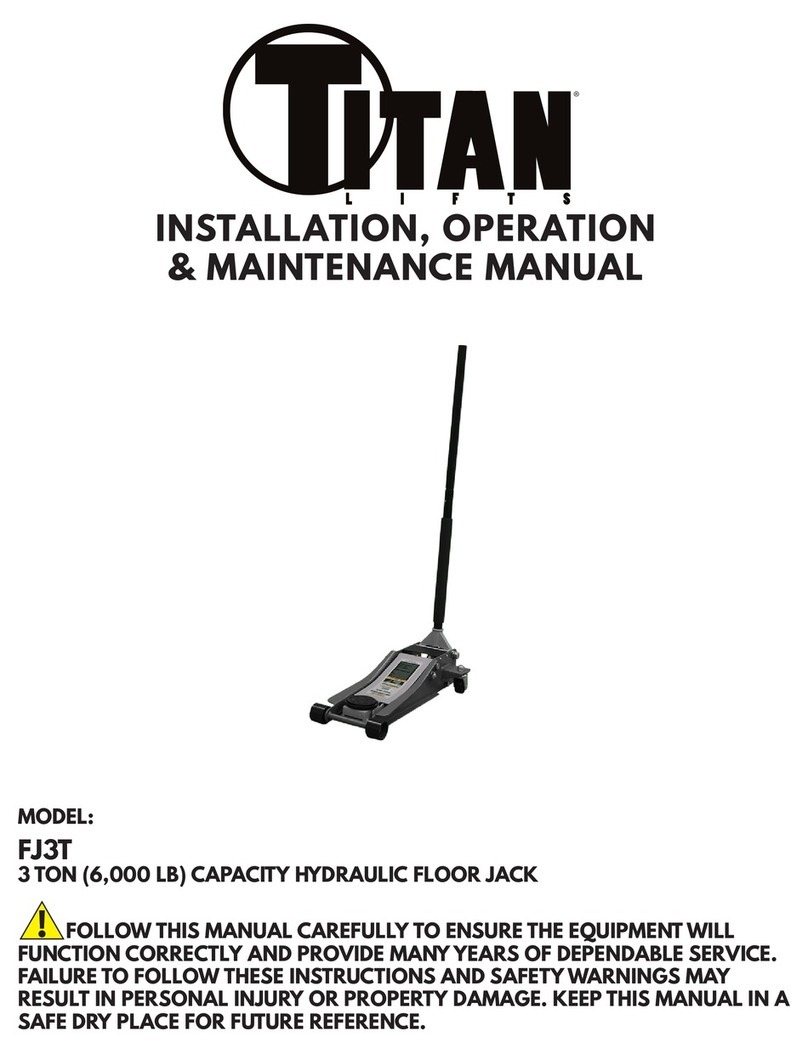
Titan
Titan FJ3T Installation, operation & maintenance manual