Electron Thermo 3920 Operating instructions

------------
Thermo
ELECTRON
CORPORATION
Model: 3920
Forma Environmental Charrlber
Operating and Maintenance Manual
Manual No: 7043920
Rev.
0

EnvrrorunentalChamber
__________________________________________________________________
_
Read This Instruction Manual.
Failure to read, understand and follow the instructions in
this manual may result in damage
to
the unit, injury
to
operat-
ing personnel, and poor equipment performance.
CAUTION!
All
internal adjustments and maintenance
must
be performed
by
qualifiedservice personnel.
Refer
to
the
serial
tag
on
the
back
of
this
manual.
The material in this manual
is
for information purposes only. The
contents and the product it describes are subject
to
change with-
out notice. Thermo Electron makes no representations or war-
ranties with respect
to
this manual. In
no
event shall Thermo be
held liable for any damages, drrect or incidental, arising out
of
or
related to the use
of
this manual.
CAUTION
Contains Parts and Assemblies
Susceptible to Damage by
Electrostatic Discharge (esd)
MANUAL NUMBER 7043920
20843 10/28/03 Release 9 aks
REV
ECRlECN
DATE
DESCRIPTION
By

Environmental Chamber
__________________________________
~'-
..
,.J
& Imporian'
operating
and/or
maintenance
Instruction,.
Read
the accompanying text
carefuUy.
•
Ce
symbole
attire
l'attention
de
I'utilisateur sur
des
instructions importantes deJonctionnement et/ou d'entretien.
II
peut
etre
utilise seul
ou
avec
d'autres symboles
de
securite. Lire attentivement
Ie
texte d'accompagnement.
Wichtige
Betriebs-
und/oder
Wartungshinweise.
Lesen Sie den nachJolgenden
Text
sorgfiiltig.
Importante instruccions
de
operacion
y/o mantenimiento. Lea el texto acompanante cuidadosamente.
&
Potential
ekctrictd
/wzords.
Only
qualified
persons
,houldper!",m
procedures
a"ocimed
with
tJUs
symboL
'I
Ce
symbole
attire
I'attention
de l'utilisateur sur
des
risques electriques potentiels. Seules
des
personnes qualifiees
doivent appliquer
les
instructions et
les
procedures associees a
ce
symbole.
GeJahr
von
Stromschliigen.
Nur qualifizierte Personen sollten
die
Tiitigkeiten ausJiihren,
die
mit
diesem
Symbol
beze-
ichnet
sind.
Potencial
de
riesgos
electricos.
Solo personas
das
capacitadadas
deben ejecutar
los
procedimientos
asociadas
con
este
simbulo.
___
"
==;:::::u;::;,:.e~:;:;:.e=:::::
::::-=~:::'::~-:
'OunltpOUT
eviter
des
blessures
possibles.
Geriite,
an
denen
Wartungs-
oder
Servicearbeiten durchgeJiihrt
werden,
miissen abgeschaltet und
abgeschlossen
wer-
den,
um
Verletzungen
zu
vermeiden.
El equipo
recibiendo
servicio
0 mantenimiento
debe
ser
apagado
y segurado paraprevenir danos.
A
Hot
,urfacer,)
present
which
may
cause
burn,
to
unprotected ,kin,
or
to
materlols
which
may
be
damaged
by ekvated
temperatures.
Presence
de
surJace(s)
chaude(s)
pouvant causer
des
brUlures
sur la peau non protegee,
ou
sur
des
matieres
pouvant
etre endommagees par
des
temperatures
elevees.
HeijJe
Oberfliiche(n)
kiinnen
ungeschiitzter Haut Verbrennungen
zUfiigen
oder
Schiiden an Materialien
verursachen,
die nicht
hitzebestiindig
sind.
Superficias calientes
que
pueden causar quemaduras apiel sin proteccion 0 a materiales que pueden
estar
danados
por
elevadas
temperaturas
.
...J
Always use the proper protective equipment (clothing, gloves, goggles, etc.)
...J
Always dissipate extreme cold
or
heat and wear protective clothing.
...J
Always follow good hygiene practices.
...J
Each individual is responsible for his
or
her own safety.
ii

Environmental Chamber
_________________________
----'~t:a-VlI,;C
Do
You
Need
Information or
Assistance
on
Thermo
Electron Corporation
Products?
If
you do, please contact us 8:00 a.m. to 6:00
p.m.
(Eastern Time) at:
1-740-373-4763 Direct
1-888-213-1790 Toll Free, U.S. and Canada
1-740-373-4189 FAX
http://www.thermo.com/forma Internet Worldwide Web Home Page
Our Sales Support staffcan provide information
on
pricing and give you
quotations. We can take your order and provide delivery infonnation on major
equipment items
or
make arrangements to have yourlocal sales representative contact
you.
Our
products are listed on the Internet and
we
can be contacted through our
Internet home page.
Our
Service Support staffcan supply technical infonnation about proper setup,
___
~op-eration~oLtroubleshooting~oLy:ourequipment.~We-canJilLyouLneeds£orspare-or----.~-
replacement parts or provide you with on-site service.
We
can also provide you with a
quotation on our Extended Warranty for your Thermo products.
Whatever Thenno products you need
or
use, we will be happy to discuss your
applications.
If
you are experiencing technical problems, working together, we will
help you locate the problem and, chances are, correct it yourself...over the telephone
without a service call.
When more extensive service is necessary, we will assist you with direct factory
trained technicians
or
a qualified service organization for on-the-spot repair.
If
your
service need is covered by the warranty, we will arrange for the unit
to
be repaired at
our expense and to your satisfaction.
Regardless
of
your needs, our professional telephone technicians are available
to assist you Monday through Friday from 8:00 a.m. to 6:00
p.m.
Eastern Time. Please
contact us by telephone
or
fax.
If
you wish to write, our mailing address
is:
Thermo Electron Corporation
Controlled Environment Equipment
Millcreek Road,
PO
Box 649
Marietta, OH 45750
International customers, please contact your local Thenno Electron distributor.
iii


Environmental Chamber
_____________________________
Table
of
Contents
Table of Contents
Section 1 - Receiving
...........................
.1
- 1 Section 4 - Routine Maintenance
.................
.4 -1
1.1
Preliminary Inspection
........................
1 - 1 4.1 Cleaning the Incubator
.......................
.4 -1
1.2 Visible Loss or
Damage
.......................
1 - 1
1.3
Responsibility for Shipping Damage
............
.1
-1 Section 5 - Service
..............
................
5 - 1
5.1 Accessing the Electrical Components
............
.5
-1
Section 2 - Installation and Set-Up .
...............
.2
-1 5.2 Replacing OverlUndertemp Probe and Thermostat .
.5
-1
2.1 Location
...................................
2 - 1 5.3 Replacing the Temperature Sensor
..............
.5
-1
a.
Choosing the Location
......................
2 - 1 5.4 Programming the Temperature Controller
........
.5
-1
b.
Preliminary Cleaning and Disinfecting
.........
2 - 1
a.
Removing the Mechanical Lockout
...........
.5
-1
c.
Installing the Shelves
......................
.2
-1 b. Removing the Software Lockout
..............
5 - 2
d.
Leveling the Unit
..........................
2 - 1 c. Controller Configuration
...................
.5
-2
2.2 Attaching the Drain Connections
................
2 - 1 d. Offset Calibration (TemplHumidity)
...........
5 - 2
2.3 Remote Data Output
.........................
.2
-1 5.5 Replacing the Optional Recorder and Probe(s)
....
.5
-3
a.
4-20 rnA Output
..........................
.2
-1
a.
Calibrating the Recorder
...................
.5
-4
b.
Remote
Alarm Contacts
.....................
2 - 1 5.6 Setting the Door Heater Control
................
.5
-4
2.4 Power Connection
............................
2 - 2 5.7
C02
Controller Calibration
....................
.5
-4
2.5 Start-Up
...................................
.2
-2
2.6 Setting the Overtemp Safety Thermostat
.........
.2
-2 Section 6 - Specifications
.........................
6 - 1
2.7 Setting the Undertemp Safety Thermostat
.........
2 - 2
2.8 Preparing the (Optional) CoBex Recorder
.......
.2
-2 Section 7 - Spare Parts .
..........................
7 - 1
a.
Installing the Battery
......................
.2
-2
b. Changing the
Chart
Paper
...................
2 - 3 Section 8 - Refrigeration Schematics
...............
8 - 1
c.-Changing-the-Een-.-.-.-
..
-.-.-.-.-.-
..
-
....
-...
-.-.-
...
-
..
-.-.2----3-------.-------
...
-.---.-
-------.--
..
--.
2.9 Honeywell Recorder (optional)
................
.2
-3 Section 9 - Electrical Schematics
..................
9 - 1
2.10 1900140 IR
C02
Option
......................
2 - 3
a.
Connecting the
C02
Source (Figure 2-4)
........
2 - 3 Warranty Information
b. Setting the C02 Content
...................
.2
- 4 Supplement
c. C02 Control and Indicators
..................
.2
- 4
Section 3 - Start Up and Operation .
................
3
-1
3.1
The Control Panel
............................
3-1
3.2 Setting the Operating Temperature (Figure 3-4)
.....
3-2
3.3 Air Exchange Ventilator Caps
...................
3-2
3.4 Heatless Dryer
PIN
1900139 (optional)
............
3 -2
iv


Environmental Chamber
____________________________
Installation and Set-Up
Section 1 - Receiving
~
[8J
DDD:~
0
••
@
o0
••
-_
......
[
-/
~
//
--
/
/~
--
~
/
--
1.1
....
....
u
Front View
Model
3920
1.1
Preliminary Inspection
This incubator was thoroughly inspected and carefully
packed prior to shipment and all necessary precautions were
taken
to
ensure its safe arrival. Immediately upon receipt,
before the incubator is moved from the receiving area, carefully
examine the shipment for loss
or
damage. Unpack the incubator
and inspect its interior and exterior for any in-transit damage.
1.2 Visible
Loss
or
Damage
If
any loss or damage is discovered, note any discrepancies
on the delivery receipt. Failure to adequately describe such evi-
dence of loss or damage may result in
the
carrier refusing to
honor a damage claim. Immediately call the delivering carrier
and request that their representative perform an inspection. Do
not discard any
of
the packing material and under no circum-
stances move the shipment from the receiving area.
c:
;::::::::::::::::::::::::::::
Side View
Model
3920
1.3 Responsibility for Shipping
Damage
For products shipped F.O.B. Marietta, Ohio,
the
responsi-
bility
of
Thermo Electron Corporation ends
when
the
merchan-
dise is loaded onto the carrier's vehicle.
On F.O.B. Destination shipments, Thermo
and
the carrier's
responsibility ends when your Receiving Department personnel
sign a free and clear delivery receipt.
Whenever possible, Thermo will assist
in
settling claims
for loss or in-transit damage.
1- 1


Environmental Chamber
_____________________________
.Installation and Set-Up
Section 2 - Installation and Set-Up
2.1
Location
a.
Choosing the Location
Locate the unit on a firm, level surface in an area
of
mini-
mum ambient temperature fluctuation. A minimum
of
twelve
(12) inches
of
clearance is required at the top
of
the incubator
and a minimum of twelve (12) inches
of
clearance is required at
the rear
of
the incubator. This space is necessary to allow ade-
quate air flow around the refrigeration system.
b.
Preliminary Cleaning and Disinfecting
Disinfect all interior surfaces with a general-use laboratory
disinfectant. Rinse thoroughly with sterile distilled water, then
70% ethanol. Dry with a sterile cloth as needed.
Disinfect the shelf channels and shelves, then rinse with
distilled water before installing.
Before using any cleaning or decontamination
method except those recommended by the
manu-
facturer, users should check with the manufactur-
er that the proposed method will not damage the
equipment.
Am
Accidental spills
of
hazardous materials on or
• inside this unit are the responsibility
of
the user.
c.
Installing the Shelves
The shelves may be installed at any level
in
the incubator.
Install a shelfchannel on each side. With the tabs pointing up,
attach the channel by
locating the rivet into a
slotted hole, far end flrst.
Pull the channel toward
the front and slide the
front rivet on the channel
into the slotted hole and
press down. Make sure
that the channels are
opposite each other so that
the installed shelf
wiII
be
Figure
2-1
level.
d. Leveling the Unit
Place a bubble-type level on a shelf inside the incubator.
Adjust the feet as needed; counterclockwise to lengthen or
clockwise to shorten. Level the unit front-to-back and left-to-
right.
2.2 Attaching the Drain Connections
The cabinet's 3/8" MPT drain line connection
is
located on
the rear (lower left side) of the cabinet. A P-trap (Figure 2-2) is
included with the unit and must be installed
on
the connection.
To
install the drain connection, push a piece
of
3/8"
ID
tub-
ing onto the trap and direct the tubing to a convenient drain.
Install a hose clamp on the tubing,
if
desired.
2.3 Remote Data Output
a.
4-20 Milliamp Output
The environmental chamber is equipped with 4-20 rnAout-
put for the remote transmission
of
temperature data. A terminal
strip is located on the back
of
the incubator for convenience.
Refer to Figure 2-3 for terminal pin identiflcation.
b.
Remote Alarm Contacts
Remote alarm connections are also included on the termi-
nal strip (Figure 2-2) providing Normally Open (N.O.) and
Normally Closed (N.C.) contacts. C
is
the Common terminal.
The remote alarm will activate when either the incubator's tem-
perature or humidity go out
of
the set alarm limits.
2 3 4 5 6 7 8 9
10
I I 1
z
c::J c::J
L.J
0 0
x:
N N
x:
z Z
I I
c::J
~
IW
TEMPERA
TURE
REMOTE
ALARM
4-20
MA
30V
lA
MAX.
(-20
TO
BOC)
Terninol Strip
Connection
Figure 2-2
2 - 1

Environmental Chamber
___________________________
Installation and Set-Up
2.4 Power Connection
See the serial tag on the side
of
the unit for electrical speci-
fications,
or
refer to the electrical schematics at the end
of
this
manual.
Connect the incubator to a grounded, dedicated
circuit. The powercord connector is
the
mains dis·
connect
device
for
the incubator. Position the
incubator so the unitcan be easily disconnected.
For Model 3920, plug the provided
10
ft.
power cord with
the NEMA 5-20P plug into the grounded dedicated electrical cir-
cuit.
2.5 Start·Up
Preset the controls as follows:
Overtemp Safety Thermostat
.............
Fully Clockwise
Undertemp Safety Thermostat
......
Fully Counterclockwise
Main Power Switch
...............................
ON
Temperature Controller
..................
Desired Setpoint
Door Heater
.........................
.40% (factory set)
Turn the Main Power switch on. The Power indicator and
Heat indicator will light. Turn the Refrigeration switch on and
the indicator will light.
&The
compressor
tmd
rejrigeralion
lights
will
not
,
come
on
if
the
chamber temperature is within
• +4°C
o/the
temperature controller.
&
The
defrost switch
must
be
turned
on
when
the
I temperature setpoint
is
10°C,
or
below.
IMPORTANT
USER
INFORMATION
Caution! Stored product should be
protected
by
an activated alarm system
capable
of
initiating atimely response
24 hours/day. Alarms provide interconnect
for centralized monitoring.
2.6 Setting
the
Overtemp Safety Thermostat
Allow the chamber temperature and humidity to stabilize
then set the overtemp safety thermostat
as
follows:
1.
Turn the overtemp control knob slowly counterclockwise
until the audible alarm sounds and the overtemp indicator
lights.
2.
Turn the overtemp control knob clockwise at least 2
degrees.
The
alarm should be silenced and the overtemp
2-2
indicator light should go out.
The
overtemp safety ther-
mostat is now set a few degrees above the control tem-
perature setpoint. When the chamber temperature rises to
the overtemp control point, the alarm system will acti-
vate, power to the heaters will shut off, and the chamber
temperature will be maintained at the overtemp control
point.
When an overtemp condition occurs, the cause must be
determined and corrected before normal operation under the
main temperature controller can be resumed.
Note: When the chamber temperature control setpoint is
changed, the overtemp safety thermostat must be reset to accom-
modate the change.
Note: The overtemp control is not directly calibrated. The num-
bers on the dial are for reference only.
2.7
Setting the Undertemp Safety Thermostat
Allow the chamber temperature and humidity to stabilize,
then set the undertemp safety thermostat as follows:
1.
Tum the undertemp control knob slowly clockwise until
the audible alarm sounds and the undertemp indicator
lights.
2. Tum the undertemp control knob counterclockwise at
least 2 degrees
on
the scale.
The
alarm should be silenced
and the undertemp indicator light should go out.
The undertemp safety thermostat is now set a few degrees
below the control temperature setpoint. When the chamber tem-
perature drops to the undertemp control point, the alarm system
will activate, power to the compressor will shut off, and the
chamber temperature will
be
maintained at the undertemp con-
trol point.
When an undertemp condition occurs, the cause must be
determined and corrected before normal operation under the
main temperature controller can be resumed.
Note: When the chamber temperature control setpoint is
changed, the undertemp safety thermostat must
be
reset to
accommodate the change.
Note; The undertemp control is not directly calibrated. The num-
bers on the dial are for reference only.
2.8
Preparing the (Optional) CoBex Recorder
a.
Installing the Battery
The seven-day circular chart recorder is located on the front
of
the incubator cabinet and is protected by a glass door.
To
prepare the recorder for operation, open the glass door
and snap the connector onto the 9-volt battery (Figure 2-4).
If
the unit is operating, the green
LED
lights steady.
If
the unit is
not turned on, the LED blinks.

Environmental
Chamber
____________________________
Installation
and
Set-Up
time line
groove
Figure 2-3
If
the
battery
is
weak
or not connected,
the
green LED will
flash.
Ifpower
is
lost
to
the
cabinet, the LED
will
also
flash. When replacing
the
9-volt battery, use only
an
alkaline style battery. Dispose ofthe old battery following
established environmental practices.
b.
Changing the Chart Paper
1.
Press the Change Chart button
(#3)
and
hold
it
for 1sec-
ond
until
the
pen
begins
to
move
to
the
left of the chart.
See
Figure
2-3.
2.
Remove
the
existing chart
by
unscrewing
the
center
knob
securing
it.
3.
Install the
new
chart,
positioning it so that
the
correct
time
line coincides
with
the
time line groove on the
chart plate.
4.
Replace
the
center
knob
and
screw
it
tightly against the
chart.
c. Changing the
Pen
1.
Using a small
flat
blade screwdriver, loosen the 2 screws
holding the
pen
arm
and
remove the pen
and
arm
as
an
assembly.
2.
Unsnap the plastic
hinge
securing the pen. Remove
and
discard the
old
pen.
3.
Install the
new
pen
by
snapping the hinge securely
around the
pen
arm.
4.
Re-install
the
pen
assembly
by
sliding the pen
arm
under
the
screws, positioning
the
pen
tip
in
the time line
groove. Tighten the
screws.
5.
Push
the Chart Change button
and
hold
it
for
1 second
until
the pen
begins
to
move
back onto
the
chart.
Note:
Make
sure that
the
pen
is
marking on
the
chart.
It
may
be necessary
to
gently lift
the
pen
onto the chart
paper.
2.9 Honeywell Recorder (optional)
The Honeywell,
DR
4500 Recorder
is
a
one
to
four-chan-
nel microprocessor-based, circular chart recorder.
The recorder
is
capable ofrecording both temperature
and
humidity and printing alphanumeric chart data
on
blank
heat-
sensitive chart. Refer
to
the Honeywell Configuration
Record
at
the end ofSection 5
and
the supplemental Honeywell
Recorder
manual.
2.10 IR C02 Option
This section applies to units with the IR C02 option
only.
a.
Connecting
the
C02 Source (Figure 2-5)
For
the
most economical
C02
inlet
use, the liquid C02 supply
tanks should be without
siphon tubes,
so
that only C02
gas enters
the
incubator injec-
tion system.
Two
tanks
may
be joined together with a man-
ifold to ensure a continuous Figure 2-4
C02 supply.
Install a two-stage pres-
sure regulator,
with
indicating gauges, at the supply
cylinder
outlet. The high-pressure gauge should have
an
indicating
range
of
0
to
2000 psig
to
monitor tank pressure. The low-pressure
gauge should have
an
indicating range of 0
to
30 psig
to
moni-
tor input pressure
to
the incubator injection system. Asuitable
two-stage pressure regulator
is
available.
The C02 source must be regulated at a pressure
level
between 5 and
10
psig. Higher pressure levels may
damage
the
C02 control system. The user should determine the most
eco-
nomical pressure level, between 5 and
10
psig appropriate
for
the desired C02 percentage in the chamber. Use only sufficient
pressure to maintain recovery time after door openings.
To
connect
the
C02 supply:
1.
Connect the C02 tubing
to
the 1/4" hose fitting installed
in
the C02 inlet.
2.
Check the tubing connection for leaks.
2-3

Environmental Chamber
___________________________
,Installation and Set-Up
b. Setting
the
C02 Content
The Watlow
SD
C02
controller's upper display shows the
actual
C02
content inside the chamber. The lower display
shows the
C02
setpoint.
Before setting the
C02
Content, allow the chamber temper-
ature and humidity to stabilize. Do not open door during the
stabilization period.
To set the
C02
content, press the
Up
or Down Arrow keys
on the Watlow
SD
Controller.
C.
C02
Control
and Indicators
• Sample
Port
(Figure 2-6)
The
sample port is used for checking
C02
percentage
in
the
incubator chamber by an independent test instrument (such as
with a Fyrite,
or
similar
C02
test instrument).
To
prevent
C02
loss, the sampleportmustbe capped when
it
is notin use.
• C02
Alarm
(Figure 2-6)
The
C02
alarm is factory set to activate when the chamber
C02
content deviates from configured alarm set points (see
configuration record). When a
C02
alarm occurs, the
C02
Alarm indicator
on
the control panel lights and the audible
alarm sounds.
The
C02
alarm high and low setpoints are established
through the Watlow SD
C02
controller (ALO, and AHI). Refer
to the Configuration Record included at the end
of
Section 5.
o 0
CO, sample port
alarm
o
6
POWER
Figure 2·5
2-4

Environmental Chamber
___________________________
---'Start-Up and Operation
Section 3 - Start Up and
Oper~tion
o
B
Fame
Enwonmenlal
Chamber
Figure
3-1,
Environmental
Chamber
Control
Panel
shown
with
optional
CoBex
Recorder
and
optional
C02
control
3.1
The Control Panel
A Main Power Switch and Indicator Light (Figure 3·2)
The main power switch controls power to the incubator.
Themain power indicator lights when the power switch
is
on
and the unit
is
receiving power.
Refrigeration Switch and Indicator Light (Figure 3·3)
B The refrigeration switch controls power to the refriger-
ation system.
The
refrigeration indicator lights when the
refrigeration switch is on and the compressor is receiving
power.
@@
~
0 0
co,
MI1J;4.po:..
",m
0
A
)8
"""",
Thermo
[LeemoN
conPORATlQ.\!
Figure 3·2
3
-1
o
TEmperaturecontrol
o
o
Defrost Refrlgeralbn
Off
Cool
Under terrp
safety
o
Heat
C Defrost Switch and Indicator Light (Figure 3-3)
The defrost switch controls power to the defrost sys-
tem. Setting the defrost switch to Auto will provide two
IS-minute defrost cycles during a twenty-four hour period.
The defrost indicator lights when the defrost switch is on
and the incubator is in a defrost cycle.
&m
The
defrost
switch
must
be
set
to
Auto
when
the
•
temperature
setpoint
is
10°C,
or
below.
D Cool Indicator (Figure 3·4)
The Cool Indicator is illuminated when the refrigera-
tion system is activated.
E
Heat
Indicator (Figure 3.4)
The Heat Indicator is illuminated when the heater is
activated.

Environmental Chamber
____________________________
Start-Up and Operation
F
Overtemp
Safety
Control,
Indicator
Light,
and
Audible
Alarm
(Figure 3.3)
The overtemp safety thermostat should be set slightly
above the operating temperature
of
the incubator. In the event
of
an
overtemp condition, the overtemp safety thermostat will:
• Activate the audible alarm and the overtemp indicator
light.
• Interrupt power to the heaters and maintain the incubator's
cabinet temperature at the overtemp safety control point.
Note:
The
overtemp control is not directly calibrated. The num-
bers on the dial are for reference only.
If
an overtemp condition occurs, the alarm can only
be
silenced
by
raising the overtemp safety thermostat setting.
However, the cause
of
the problem must be determined and cor-
rected before normal operation under the main temperature con-
troller is resumed.
G
Undertemp
Safety
Control,
Indicator
Light
and
Audible
Alarm
(Figure
3·3)
The undertemp safety thermostat should be set slightly
lower than the operating temperature
of
the incubator. In the
event
of
an undertemp condition, the undertemp safety thermo-
stat will:
• Activate the audible alarm and the undertemp indicator
light.
• Interrupt power to the refrigeration system and maintain
the incubator's cabinet temperature at the undertemp safety
control point.
Note:
The
undertemp control is not directly calibrated. The
numbers on the dial are for reference only.
If
an undertemp condition occurs, the alarm can only
be
silenced by lowering the undertemp safety thermostat setting.
However, the cause
of
the problem must be determined and cor-
rected before normal operation under the main temperature con-
troller is resumed.
3.2
Setting
the
Operating
Temperature (Figure
3-4)
H The Watlow tem-
perature controller's
upper numerical dis-
play shows the actual
temperature inside
the incubator chamber.
The lower display shows
the temperature setpoint.
®
CD-t----t_:~
__
1711
Ll
L2
L3
L4
DEV
%OUT
[~
~l
'--~'
S=RiES982
Figure
3·4
3 -2
l
_______
PROCESS
--------)
J Changing the Setpoint
To
raise or lower the setpoint, press the Up or Down
Arrow. Temperatures are set
in
.1°C increments.
3.3 Air Exchange Ventilator Caps
Air exchange for the incubator is regulated through the
manually adjustable intake and exhaust ventilator caps located
on the top
of
the cabinet.
When viewed from the front
of
the incubator, the intake
cap is on the left and the exhaust cap is on the right. The venti-
lator caps may be opened by turning counterclockwise, and
closed by turning clockwise.
For optimum performance
of
the unit, the vent caps should
be
closed at all times.
3.4 Heatless Dryer
PIN
1900139 (optional)
The optional heatless dryer provides dehumidification for
the incubator chamber. The dehumidify switch must be turned
on
for the dryer to operate. The dryer is controlled with the
humidity controller and should operate at 90 psi.
I

Environmental Chamber
______________________________
.Routine Maintenance
Section 4 - Routine Maintenance
4.1
Cleaning the Incubator
£
De-energize
aU
potentUd
.ource.
of
energy
to
this
r;
£JJ..
unit
and
lockoutltagout their controls. (O.S.H.A.
~
Regulation, Section 1910-147.)
The continued cleanliness
of
the stainless steel used in this
unit has a direct effect
on
the appearance and operation
of
the
unit. Use the mildest cleaning procedure that will do the job
effectively. Clean the outside
of
the incubator with soap and
water or with any non-abrasive commercial spray cleaner.
Clean the inside
of
the chamber with alcohol and/or soap and
water. Disinfect the interior panels with a general use laboratory
disinfectant, diluted according
to
the manufacturer's instruc-
tions. Rinse the surface thoroughly after each cleaning and wipe
the surfaces dry. Always rub in the direction
of
the finish pol-
ish lines.
&/1\
Do
not
use chlorinated solvents on stainless steel
• as they can cause rusting andpitting.
Do
not
use volatile oraromatic solvents
for
clean-
ing inside
the
cabinet
as
their residue can contam-
inate the cabinet environment.
The Thermopane glass door may be cleaned with commer-
cial glass cleaner or with a solution of ammonia and water.
4-1


PREVENTIVE MAINT'ENANCE
Environmental
Chambers
Your equipment has been thoroughly tested and calibrated before shipment. Regular preventive maintenance is important to keep your unit function-
ing properly. The operator should perform routine cleaning and maintenance on a regular basis. For maximum performance and efficiency, it is rec-
ommended that the unit
be
checked and calibrated periodically by a qualified service technician.
The following is a condensed list
of
preventive maintenance requirements. See the specified section
of
the instruction manual for further details.
Thermo Electron has qualified service technicians, using NIST traceable instruments, available in many areas. For more information on Preventive
Maintenance
or
Extended Warranties, please contact
us
at the number below.
Cleaning and calibration adjustment intervals are dependent upon use, environmental conditions and accuracy required.
Tips for all incubators:
• Do NOT use bleach or any disinfectant that has high chloros.
• Use sterile, distilled or demineralized water.
• Avoid spraying cleaner on the
C02
sensor.
• Do not use powdered gloves for tissue cultures.

Preventive Maintenance for Environmental Chambers
Refer to Manual Section Action Daily Weekly Yearly
Inspect door latch, hinges and door gasket seal o
3.3 Check air exchange ventilator caps for adjustment; open or close as required o
4.1 Perform a complete decontamination procedure. Wipe down interior, shelves, Between Experiments
side panels with disinfectant. Rinse everything well with sterile distilled water. More frequent decontamination may be
required, depending on use
and
environmental conditions.
5.4,5.7 *Verify and document all calibrations, at the minimum. o
Clean drip pan and drain lines o
Clean refrigeration system condenser o
Verify defrost cycle for below 10°C operation o
Change filters(under normal conditions) o
*Qualified service technicians only
**
Regular monitoring routines
of
the various levels in your unit is encouraged.

Environmental Chamber
___________________________________
Service
Section 5 - Service
fA
cooru::!~~~?~pm";
..
Susceptible
to
Damage
by
Electrostatic Discharge (esd)
& Se"icing must
be
performed
by
qualified
..
"ice
• personnel only!
~
De-energize
aU
potenJW1
sources
of
energy
to
thi,
o......lIfiliiI
unitandlockoutltagout their controls.
5.1
Accessing the Electrical Components
To
gain access
to
the electrical components, remove the
two screws located on the left side
of
the control panel with a
Phillips screwdriver. The control panel is hinged and will swing
open.
5.2 Replacing Over/Undertemp Probe
and
Thermostat
1.
Remove the incubator top right side air dam by remov-
ing the screws holding it in place.
2. Remove the top three screws from the top
of
the right
duct cover.
3.
Lean the duct sheet out, and remove the Permagum seal
from around the probe access hole.
4. Remove the 15" copper capillary overtemp probe by
extracting two plastic clips that hold the probe in place.
5. Open the control panel by removing the four screws
located on the top and bottom
of
the control panel.
I
i
I
, o D
!
i~
i i
remove
SCiews
6. Pull the probe up through the access hole and into the
control panel.
7. Follow the wires from the
probe
to the thermostat
mounted on the control panel. Clip the plastic ties hold-
ing the overtemp cable to the existing wiring.
S.
Pull the overtemp knob
on
the
control panel off.
9.
Remove the two screws that hold the overtemp assembly
to the control panel.
10. Disconnect the two wires from the back
of
the thermo-
stat assembly.
11.
Pull the entire assembly from the panel, and remove the
unit.
12. Replace the thermostat and probe.
Note: Reseal probe access hole with Permagum and tie-wrap
overtemp cable to existing wires after replacing probe.
5.3 Replacing the Temperature Sensor
1.
Follow instructions 1-6 from Section 5.2 to locate and
remove the probe from the chamber.
2.
Clip any plastic ties securing the probe wiring.
Disconnect the probe.
3.
Install the replacement probe in the chamber.
4.
Route the probe wire through the access hole into the
control housing.
5. Connect the probe to the appropriate controller wiring.
6.
Reseal the probe access hole with
Permagum
and tie-
wrap the probe wire to existing wires.
5.4 Programming the Temperature Controller
The Watlow temperature controller has been set at the fac-
tory to operate the incubator within the specifications listed in
Section 6
of
this manual. Reference copies
of
the Watlow con-
figuration records are included at the end
of
this section.
To
prevent tampering, mechanical and software lockouts
are employed in the system. These lockouts must only be
removed by persons skilled
in
configuring controller software.
&Re-programming eitherthe temperature orhumid-
, ity controllers alters the factory defaults and will
seriously alter the performance
of
the
incubator.
This may also void the warranty. Do
not
reconfig-
ure the controllers withoutfirst consulting the
Technical Services Department, (888) 213-1790.
a.
Removing the Mechanical Lockout
Make sure the unit is turned off.
Wearing a grounding wrist strap or maintaining constant
contact with the metal cabinet, press in the four locking tabs on
the frame
of
the Temperature controller. There are two tabs on
either side as shown in the front and side views in Figure 5-1.
When all tabs are unlocked, pull the controller module out
of
its
frame.
5-1
This manual suits for next models
1
Table of contents
Popular Laboratory Equipment manuals by other brands
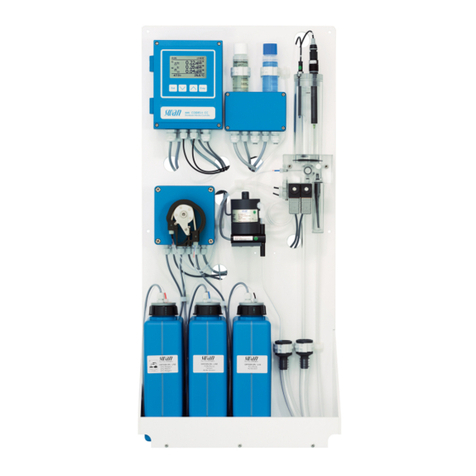
Swan Analytical Instruments
Swan Analytical Instruments AMI Codes-II CC Operator's manual

Forma Scientific
Forma Scientific 1184 manual

Noraxon
Noraxon Ultium EMG System user manual
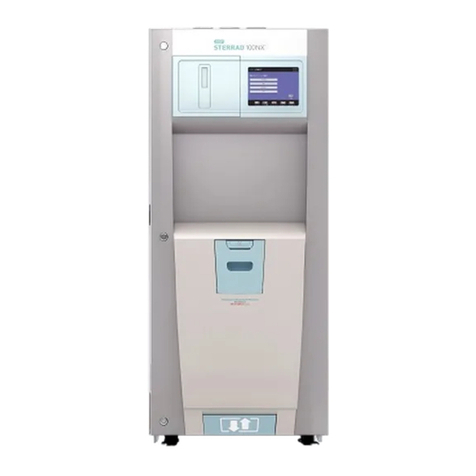
Johnson & Johnson
Johnson & Johnson Sterrad 100NX user guide
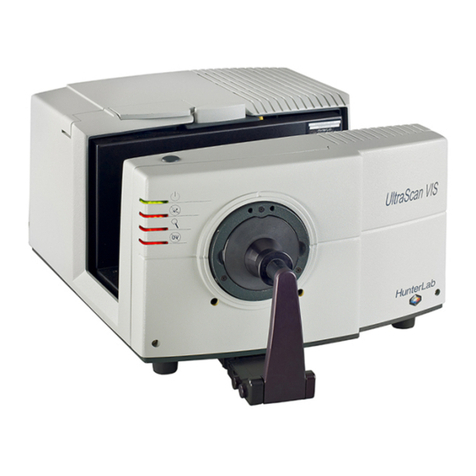
HunterLab
HunterLab EasyMatch QC user manual

Fisher Scientific
Fisher Scientific accuSpin 3 operating instructions