Electronet ELMAG 200 User manual

NK Instruments Pvt. Ltd.
B-501/504, 5th floor, Raunak Arcade, Near THC Hospital, Gokhale Road, Naupada,
Thane(W) 400602. Maharashtra INDIA Telefax Nos.: 91-22-25301330 / 31 / 32
Skype: nitinkelkarskype Gtalk: nkinstruments2006
Authorised Dealer
ELECTRONET
USER MANUAL FOR
FULL BORE ELECTROMAGNETIC
FLOW METER
MODEL NO. :- ELMAG 200

ELECTRONET
UM-ELMAG 200-R3
ORDERING DTAILS
Instrument Name : Full Bore Type Electromagnetic Flow Meter
Model No. : ELMAG 200
Serial No. :
Code Description As Applicable
Line Size
01
02
03
05
06
07
08
09
10
11
12
13
14
15
16
17
18
19
½ Inch (15NB)
¾ Inch (20NB)
1 Inch (25NB)
1½ Inch (40NB)
2 Inch (50NB)
2½ Inch (65NB)
3 Inch (80NB)
4 Inch (100NB)
5 Inch (125NB)
6 Inch (150NB)
8 Inch (200NB)
10 Inch (250NB)
12 Inch (300NB)
14 Inch (350NB)
16 Inch (400NB)
18 Inch (450NB)
20 Inch (500NB)
24 Inch (600NB)
Lining Material
01
02
03
PTFE
Rubber
Other
Flange Material
01
02
03
CS/MS
SS304
SS316
20 28 Inch (700NB)
21 32 Inch (800NB)
22 36 Inch (900NB)
23 40 Inch (1000NB)
24 Other
Calibration Range
01
Flow Direction
01
02
Forward
Reverse
04 1¼ Inch (32NB)

ELECTRONET
UM-ELMAG 200-R3
Code Description As Applicable
Electronic Enclosure
01
02
Aluminum die cast
SS304
Output
01
02
03
04
4-20mA DC
4-20mA DC + Pulse Output
4-20mA DC + HART Output
All (4-20mA DC + Pulse Output +HART Output)
Communication Output
01
03
RS485
RS232
04 GSM
Power Supply
01
02
90-260V AC,50Hz
24V DC
03 48V DC
Alarm Output
01
02
Low
High
03 Batch
Cable Gland
01
02
M20 x 1.5 double compression
1/2" NPT(F)
03 3/4 ET
Electrode Material
01
02
03
04
SS316L
Hastalloy C
Platinum
Other
Coil Housing Material
01
02
03
MS
SS304
SS316
Accessories
01
02
Power cable
Cable gland
03 Magnetic key chain
04 ‘U’ clamp
06 Other
05 Grounding Ring
02 Data Logger

ELECTRONET
UM-ELMAG 200-R3
CONTENTS
1. INTRODUCTION.......................................................................................................... 01
1.1 Item Supplied......................................................................................................... 01
1.2 Device Identification............................................................................................... 01
1.3 Reading User Manual............................................................................................. 01
1.4 Warranty Terms...................................................................................................... 01
2. SAFETY INSTRUCTIONS........................................................................................... 02
2.1 General Instructions............................................................................................... 02
2.2 Storage Precautions............................................................................................... 02
2.3 Installation Location Precautions............................................................................ 02
3.APPLICATION.............................................................................................................. 03
4. OPERATING PRINCIPLE............................................................................................ 04
5. TECHNICAL DETAILS................................................................................................ 05
5.1 Electronic Unit Specifications................................................................................. 05
5.2 Flow Sensor Specifications.................................................................................... 05
6. ASSEMBLY OVERVIEW.............................................................................................. 06
7. KEY BOARD DETAILS................................................................................................ 07
8. TERMINATION DETAILS............................................................................................. 07
8.1 HART Communication Details ............................................................................... 08
8.2 GSM Module Details............................................................................................... 08
9. INSTALLATION DETAILS............................................................................................ 10
9.1 How to install Flow Meter...................................................................................... 10
9.2 Cable glanding procedure..................................................................................... 11
9.3 Safety Precautions............................................................................................... 12
9.4 Installation Position............................................................................................... 13
9.5 Pipe System.......................................................................................................... 14
10. OPERATIONAL FLOW CHARTS.............................................................................. 17
10.1 General Overview of Operations.......................................................................... 17
10.2 Alarm Setting Mode.............................................................................................. 18
10.3 Configure Mode.................................................................................................... 19
10.4 Alarm Configuration.............................................................................................. 22
10.5 Configure Instrument Method............................................................................... 23
10.6 Real Time Clock Configuration ............................................................................ 27
10.7 View Logged Data................................................................................................. 28
10.8 Batch Mode Opration.......................................................................................... 28

ELECTRONET
UM-ELMAG 200-R3
10.9 Avrage Flow Rate................................................................................................ 29
10.10 SMS Format On Mobile...................................................................................... 29
10.11 Online Diagnostic Features................................................................................ 29
11. MODBUS (RS 485) COMMUNICATION DETAILS.................................................... 30
12. DO'S & DONT'S.......................................................................................................... 34
13. TROUBLE SHOOTING PROCEDURE...................................................................... 34

ELECTRONET
UM-ELMAG 200-R PAGE 01 OF 34
1. INTRODUCTION
1.1 Item Supplied :
ELMAG 200 flow meter
User Manual
Calibration Certificates
User Manual CD
Inspection :
— Check for mechanical damage due to possible improper handling during shipment. All
claims for damage are to be made promptly to the shipper.
— Make sure the scope of delivery and the information on the name plate corresponds to the
ordering information.
1.2 Device Identification :
The Model no. and Specification are found on name plate, located on top of electronic
housing. Check the Model no. & Specifications you have ordered.
1.3 Reading User Manual :
— This manual should be provided to the end user.
— Before use, read this manual carefully and compare the instrument specification.
— The contents of this manual may be changed without prior notice.
1.4 Warranty terms :
— The terms of this instrument that are guaranteed are described in the quotation. We will
make any repairs that may become necessary during the guaranteed term free of
charge.
— Please contact our sales office if this instrument requires repair.
— If the instrument is faulty, contact us with concrete details about the problem and the
length of time it has been faulty, and state the model and serial number. We would
appreciate the inclusion of images or additional information.
— The results of our examination will determine whether the meter will be repaired free of
charge or on an at-cost basis.
ELECTROMAGNETIC FLOW METER
MODEL NO.:
SUPPLY :
RANGE :
SR. NO.:
LINE SIZE :
OUTPUT :
MAX. W. P.:
TAG NO.:
Electronic Unit
name plate

ELECTRONET
UM-ELMAG 200-R3 PAGE 02 OF 34
2. SAFETY INSTRUCTIONS
2.1 General Instructions:
— This flow meter was carefully calibrated at the factory before shipment. When meter is
delivered, visually check that no damage has occurred during transportation
— Read User manual carefully and understand instructions & directions provided in this
manual.
— In general, devices from the manufacturer may only be installed, commissioned, operated
and maintained by properly trained and authorized personnel.
— Look at the ordering detail to ensure that the device is delivered according to your order.
Check for the correct supply voltage printed on the nameplate.
— Before powering up the meter, consider the following:
– Is the meter installed according to the direction of flow as marked on the meter.
– Has the wiring been carried out correctly and have all safety procedures been adhered to.
Is the supply voltage correct.
– Has the flow meter been properly earth.
– Lethal power supply voltages may be present, do not apply power with the signal
converter cover or terminal box cover removed.
— The following principles should be considered during installation:
– If there is a noisy power supply voltage (especially peaks generated, usually by motors),
use an external power supply filter between the flow meter and power supply.
– Protect the flow meter and the internal lining of the sensor pipe from mechanical damage,
especially during installation or cleaning.
– Do not expose the flow meter to intense vibration.
2.2 Storage Precautions:
• Store the device in a dry, dust-free location.
• Avoid continuous direct sunlight.
• Store the device in its original packing.
• Storage temperature: 0 to 55°C
2.3 Installation Location Precautions:
— Installation of the Electromagnetic flow meter must be performed by expert engineer or
skilled personnel. No operator shall be permitted to perform procedures relating to
installation.
— The Electromagnetic flow meter is a heavy instrument. Be careful that no damage is
caused to personnel through accidentally dropping it, or by exerting excessive force on the
electromagnetic flow meter. When moving the electromagnetic flow meter, always use a
trolley .
— When the electromagnetic flow meter is processing hot fluids, the instrument itself may
become extremely hot. Take sufficient care not to get burnt.
Note : IP68 Certification is valid if cable glanding is done as per mentioned cable
glanding procedure (Point no. 9.2, page no.11&12) also safety precautions must
be strictly maintained

ELECTRONET
UM-ELMAG 200-R3 PAGE 03 OF 34
ELMAG 200 is microprocessor based full bore type electromagnetic flow meter specially used
for various industrial applications. This flow meter accurately measures the flow rate of
conductive liquids & slurries in closed pipes. Due to simple, rigid & obstruction less design the
flow meter is a maintenance free instrument in place of conventional mechanical flow measuring
device. ELMAG 200 standard configuration is a sensor with transmitter integrated in one unit. It’s
performance is independent of temperature, pressure, density and viscosity of the medium.
ELMAG 200 is a flanged meter available in sizes from DN 10 to DN 1000. The rugged flow sensor
is constructed from completely welded construction. In the instrument, the sensor and the
electronics form one mechanical entity. A retransmission output of 4-20 mA is provided. The use
of ‘Pulsed DC ’ excitation technology offers highest ability & better measuring accuracy in the
form of electrical signal 4 - 20 mA DC linearly proportional to volumetric flow.
Sensor : The sensor consists of metering pipe; electrodes and coils. It is accommodated in
welded and a fully encapsulated steel enclosure.
Electronics :The conditioning electronics circuitry is housed in a cast aluminum connection box.
The termination of this electronics is given in the same housing through cable glands for the
required connecting cables.
Applications:
CApplications include measurement of flow on conducting liquids and slurries (even
highly corrosive and abrasive) in chemical and petrochemicals, pharmaceutical, fertilizers,
foodstuffs, dairy, sugar, breweries, paper, steel, mining industries etc.
CMonitoring water flow in cooling systems in steel plants, power plants etc.
CMeasuring flow of clean water, effluent, sludge etc. In pollution and environmental control.
CThe isolated 4-20 mA output proportional to flow can be fed to PLCs, DCS or remote mounted
indicator.
3. APPLICATION

ELECTRONET
UM-ELMAG 200-R3 PAGE 04 OF 34
4. OPERATING PRINCIPLE
The flow meter is designed for electrically conductive fluids. Measurement is based on Faraday’s
law of induction, according to which a voltage is induced in an electrically conductive body, which
passes through a magnetic field.
The following expression is applicable to the voltage:
U = K x B x v x D
Where:
U = induced voltage
K = an instrument constant
B = magnetic field strength
v = mean velocity
D = pipe diameter
Thus the induced voltage is proportional to the mean flow velocity, when the field strength is
constant. Inside the electromagnetic flow meter, the fluid passes through a magnetic field applied
perpendicular to the direction of flow. An electric voltage is induced by the movement of the fluid
(which must have a minimum electrical conductivity). This is proportional to the mean flow
velocity and thus to the volume of flow. The induced voltage signal is picked up by two electrodes,
Which are in contact with conductive fluid and transmitted to the signal converter.This method of
measurement offers the following advantages:
1) No pressure loss through pipe.
2) Since the magnetic field passes through the entire flow area, the signal represents a mean
value over the pipe cross-section; therefore, only relatively short straight inlet pipes x DN from
the electrode axis are required upstream of the primary head.
3) Only the tube liner and the electrodes are in contact with the fluid.
4) The signal produced is an electrical voltage, which is an exact linear function of the mean flow
velocity.
Fig.1

ELECTRONET
UM-ELMAG 200-R3 PAGE 05 OF 34
5. TECHNICAL DETAILS
5.1 Specifications:
Instrument Name : Full Bore Type Electromagnetic Flow Meter
Model No. : ELMAG 200
Media : Conductive Liquids & slurries
Calibration Range : As per customer requirement
Display : 16X2 Alphanumeric LCD, 6 digit for flow rate & 8 digit
for totaliser
Power Supply : 1) 90-260V AC, 50Hz
2) 24V DC
3) 48V DC
Power Consumption : Less than 10VA
Response Time : 2Sec.
Accuracy : +/-0.5% of full scale
Linearity : +/-0.5% of full scale
Isolation : 1.4KV Between input & Power supply
Output : 1) 4-20mA DC
2) Pulse output (Open collector OR 12V DC
Amplitude)
3) Relay O/P(1c/o,1Amp @ 230V AC for
Low/High/Batch alarm)
Communication Output : 1) 4-20mA DC with HART
2) RS485 supporting MODBUS RTU Protocol
3) RS232
4) GSM
Flow Direction : 1) Forward 2) Reverse
0
Temperature : 1) Ambient : 0 to 55 C
0
2) Storage : 0 to 55 C
Relative Humidity : 10-95% RH, non condensing
Cable Entry : M20 x1.5 Double Compression Cable Gland,
½” NPT
Mounting : In Line - Horizontal / Vertical
Transmitter Enclosure : Aluminum Die cast
Protection Class : IP66
5.1.1 Electronics Unit Specifications:
5.1.2 Flow Sensor Specifications:
Line Size : 15NB to 1000NB
Material of Construction : 1) Coil housing : MS / SS
2) Electrode : SS 316L / Hastalloy C / Platinum
3) Flange : CS / MS / SS 304 / SS 316
4) Lining : Rubber / PTFE
Mechanical Connections : Flange / SMS union / Threaded / Tri clover
Media conductivity : > 20 μs/cm
Limit flow velocities of measured liquid : 6 m/s
Viscosity : 200cp (max.)
Direction of Flow : Direction of Arrow on Meter
Protection class : IP68
Process Temperature : 1) 0 to 85° C(For Rubber Lining)
2) 0 to 120° C(For PTFE Lining)
2
Operating Pressure : 0 to10Kg/cm

ELECTRONET
UM-ELMAG 200-R3 PAGE 06 OF 34
6. ASSEMBLY OVERVIEW
DIMENSIONAL DETAILS OF FLANGE(AS PER ASA150 # B-16.5):
Fig.2 FRONT VIEW Fig.3 SIDE VIEW WITH FLANGE DETAILS
Ø DBC
Ø Bolt Hole
Lining
R
D
FD
Note : All dimensions are in ‘mm’
Line Size
Inch NB
Flange
Diameter
D (mm)
Diameter of
Raised Face
R (mm)
200
2 ½ ” 65 177.8 4
104.8 19.0
22.2
½” 15
88.9 4
34.9 20015.9 11.1
3/4” 20
98.4 4
42.9 20015.9
12.7
1 ” 25 107.9 4
50.8 20015.9 14.3
200
1 ½ ” 40 127.0 4
73 15.9
17.5
2” 50
152.4 4
92.1 20019.0
19.0
Diameter of
Bolt Hole
(mm)
No.
of
Holes
Flange to Flange
Distance (FD)
(mm)
Thickness
of
Flange
3 ” 80 190.5 4
127.0 20019.0
23.8
4” 100
228.5 8157.2 25019.0
23.8
250
5 ” 125 254.0 8185.7 22.2
23.8
6” 150 279.4 8215.9 300
22.2
25.4
8” 200 342.9 8269.9 350
22.2
28.3
10” 250 406.4 12
323.8 45025.4
30.2
12” 300 482.6 12
381.0 50025.4
31.8
14” 350 533.4 12
469.9 50028.6
34.9
16” 400 596.9 16
533.4 60028.6
36.5
18” 450 635.0 16584.2 600
31.7
39.7
20”
24”
500
600
698.5
812.8
20
20
139.7
60.3
69.8
79.4
98.4
120.6
Diameter of
Bolt Hole Circle
DBC (mm)
152.4
190.5
215.9
241.3
298.4
361.9
431.8
476.2
539.7
577.8
635.0
749.3
692.1
692.1
600
600
31.7
34.9
42.9
47.6
125
125
155
265
605
555
605
355
605
405
605
205
245
285
485
185
165
145
Housing
OD
(mm)
Grounding
Ring
* Note : Flange to flange distance (FD) Tolerance : 1) 1/2"(15NB) to 6"(150NB) : +/-3mm
2) 8"(200NB) to 24"(600NB) : +/-5mm
ELECTRONET
ELECTROMAGNETIC FLOW METER
ELMAG-200
0000.00 m3/Hr
000000.02 m3 L
200
1 ¼ ” 32 117.5 4
63.5 15.9
15.9
88.9
155

ELECTRONET
UM-ELMAG 200-R3 PAGE 07 OF 34
7. KEY BOARD DETAILS
8. TERMINATION DETAILS
PProgram Key : This key is used to toggle between Run mode and Program mode.
Increment Key : This key is used to :-
1) Increment the numerical value of any digit, from 0 to 9, by one at
each time.
2) Go to the next parameter in Program mode.
3) To start Batch operation
Shift Key : This key is used to :-
1) Shift the cursor to the next digit.
2) To stop Batch operation
Enter Key : This key is used to :-
1) Validate the function or value of parameter.
2) To toggle between totaliser & batch totaliser in batch mode.
3) Press this key for 5 to 6 sec. to reset totaliser
Fig 5 . 24V DC operated flowmeter Rear View
Fig 4 . 230V AC operated flowmeter Rear View
P
NO
NC
1
8
2
9
3
10
4
11
13
7
5
12
14
4-20 mA DC
RET. OUTPUT
L
N
E
230V AC
Power Supply
6
NA
Not Applicable
T1
T2
T3
R
S
4
8
5
R
S
2
3
2
G
S
M
Relay O/P
For
Alarm
I+
+
I-
GND
OC
PULSE
O/P OF
12V DC
AMPLITUDE
Open
Collector
Output
T1 A TXD
T2 B RXD
T3 GND GND
RS 485 RS 232 /
GSM
P
NO
NC
1
8
2
9
3
10
4
11
13
7
5
12
14
4-20 mA DC
RET. OUTPUT
+
-
NA
24V DC
Power Supply
6
NA
Not Applicable
T1
T2
T3
R
S
4
8
5
R
S
2
3
2
G
S
M
Relay O/P
For
Alarm
I+
+
I-
GND
OC
PULSE
O/P OF
12V DC
AMPLITUDE
Open
Collector
Output
T1 A TXD
T2 B RXD
T3 GND GND
RS 485 RS 232 /
GSM
NO NC NA
P
NOT
APPLICABLE
T2 T3
T1
RS485
RS232
GSM
I-I+
GND
+
OC
PULSE O/P
OF12V DC
AMPLITUDE
T1
T2
T3
RS485 RS232
GSM
A
B
GND
TXD
RXD
GND
230V AC
POWER
SUPPLY
LN E
1 2 3456 7 98 10 11 12 13 14
NO NC NA
P
NOT
APPLICABLE
T2 T3
T1
RS485
RS232
GSM
I-I+
GND
+
OC
PULSE O/P
OF12V DC
AMPLITUDE
T1
T2
T3
RS485 RS232
GSM
A
B
GND
TXD
RXD
GND
24V DC
POWER
SUPPLY
+
-
NA
1 2 3456 7 98 10 11 12 13 14

ELECTRONET
UM-ELMAG 200-R3 PAGE 08 OF 34
Fig 6 . Rear View
HART Communicator
250W Resistance
I+
I-
8.1 HART Communication Details :
a) Instructions:
1) Connect 250Ω resistor across I+ & I- terminal at flow meter termination.
2) Now connect the HART communicator probe across the 250Ω resistor.
3) For HART functionality checking refer communicator manual
b) Loop Diagram :
8.2 GSM Module Details :
9 Pin D type connector
(Comm. port for GSM)
3 Pin Allied connector(M/F)
for power supply
Antena
94.0
20.099.0
80.0
99.0
Fig.7 GSM Module
Pin
No. Description
1
2
3
4
5
6
7
8
9
No Connection
TXD
RXD
No Connection
GND
No Connection
9 Pin D Type
Connector Details
No Connection
No Connection
No Connection
NO NC NA
P
NOT
APPLICABLE
T2 T3
T1
RS485
RS232
GSM
I-I+
GND
+
OC
PULSE O/P
OF12V DC
AMPLITUDE
T1
T2
T3
RS485 RS232
GSM
A
B
GND
TXD
RXD
GND
230V AC
POWER
SUPPLY
LN E
1 2 3456 7 98 10 11 12 13 14

ELECTRONET
UM-ELMAG 200-R3 PAGE 09 OF 34
Loop Diagram Flow Meter with GSM Module :
Fig 8 . Loop Diagram
3 Pin Ahuja connector 9 Pin D type connector
3 Pin Allied connector(M/F)
for power supply
SIM Tray Open Switch SIM Tray
Fig.9 GSM Module SIM Try Open Switch position Fig.10 GSM Module SIM Try position
Procedure for Insert or Remove SIM Card :
1) Switch o ffpower supply.
2) Press SIM Tray open switch (As shown in fig 9).
3) By pressing open switch, Open the SIM tray insert SIM (As shown in fig 10).
4) Insert the tray & Power ON GSM Module.
ELECTRONET
ELECTROMAGNETIC FLOW METER
ELMAG-200
0000.00 m3/Hr
000000.02 m3 L

ELECTRONET
UM-ELMAG 200-R3 PAGE 10 OF 34
9.1 How to Install Flow Meter :-
9. INSTALLATION DETAILS
1) Flowmeter can be installed in any position either vertical or horizontal.
2) The meter may be installed in horizontal or vertical pipelines. If a vertical pipeline installation is
desired, the meter should be installed with the direction of flow being upwards, to ensure a full
pipe under low flow conditions. If a horizontal installation is desired the measuring electrodes
should be installed in the horizontal plane in order to prevent entrained air or gasses collecting at
the electrodes. The effect of this would be that the meter would give inaccurate and unstable
readings.
3) For horizontal installation, the electrode axis should always be in horizontal plane.
4) The flow meter should be installed away from electrical motors, transformers, inverter and
other power sources in order to avoid interference with measurement. Install the flow meter in a
location where it is not exposed to direct sunlight.
5) Be sure to choose a gasket with inner and outer diameters that does not protrude inside the
piping If the inner diameter of the gasket is too large, or outer diameter of the gasket is too small,
fluid leakage may result.
Fig.11 Gasket Alignment
Fig.11a Fig.11b
Fit gaskets ensuring
proper alignment.
Poorly aligned gasket s
can cause leaks and
flow errors.
Fig.12 Flow Meter Installation With Reducer
INLET SIDE
10 D
7º
7º
5 D
D = DIAMETER
OUTLET SIDE
6) If pipeline is bigger than the size of flow meter, use Reducers as shown in Fig-10
7) At inlet side, straight run to be maintained 10 times of flow meter bore size ‘ D’and similarly 5
times of ‘D’at outlet side.
8) Flange size to be selected as per pipeline and flow meter size.
D
ELECTRONET
ELECTROMAGNETIC FLOW METER
ELMAG-200
0000.00 m3/Hr
000000.02 m3 L

ELECTRONET
UM-ELMAG 200-R3 PAGE 11 OF 34
9.2 Cable Glanding procedure :
a) Cable Glanding For Armoured Cable :
Assembly Method :
1) Grease all the threads.
2) Peel the end of the cable, considering that the length "X" until the wiring position
must include the body length between threads.
3) Cut the metal mesh leaving an useful length as long as the conic zone of the
clamping and earthing cone plus 1or 2 mm.
4) Thread the tighten nut with the weather proof gasket inside (1), the reduction body
(3), the clamping and earthing ring so that the main side cone remains at the cut end
of cable.
5) Open the metal mesh in such a way that it "copies" the adjustment cone. Thread it.
6) Thread the body gland, with water tightness washer to the other cable glands side.
7) Thread the body gland at the entry with the appropriate wrench until it has been
adjusted definitively.
8) Then thread the union body (3) and the lock nut (1) with a considerable adjustment
(with the appropriate wrench).
9) In case of cable glands for "e mode" protection or weather proof, add the water
tightness washer (8).
Tighten nut (1)
Watertight gasket (2)
Union body(3)
Adjusting O ring(4)
Adjusting Cone (5)
Flame-proof
gasket(6)
Body gland (7)
Water tightness
washer (8)
Nut (with watertight gasket) (1)
Union body(3)
Adjusting ring(4)
Adjusting Cone (5)
Body gland (7)
Water tightness washer (8)

ELECTRONET
UM-ELMAG 200-R3 PAGE 12 OF 34
b) Cable Glanding For Non Armoured Cable :
Assembly Method :
1) Grease all the threads.
2) Thread in the cable, the tighten nut (1), the adjustment bushing (2) and body gland
(4) with the flameproof gasket (3) toward of the side of the other part of the cable
gland.
3) Thread the body gland at the entry with the appropriate wrench until it has been
adjusted definitively.
4) Thread all the parts with a considerable adjustment (with the appropriate wrench).
5) In cases of cable glands for “e” protection or weather proof, add the watertightness
washer.
9.3 Safety Precautions :
a) Flow meter must be properly grounded or earth according to local electric codes.
b) Install signal wiring separate from the high voltage power cable.
c) After termination cabling , fit back cover properly to maintain IP certification.
Tighten nut (1)
Adjustment bushing (2)
Flame proof gasket(3)
Body gland(4)
Water tightness washer (5)
Tighten nut (1)
Adjustment bushing (2)
Body gland with
flame-proof gasket (3-4)
Water tightness washer (5)

ELECTRONET
UM-ELMAG 200-R3 PAGE 13 OF 34
10D
Pipe
Support
Pipe
Support
Valve
Pipe
Support
Pipe
Support
Flow
In
Valve
Flow
Out
Valve
5D
9.4 Installation Position:
Fig.13 FLOW METER INSTALLATION IN HORIZONTAL POSITION
a) Horizontal Position:
b) Vertical Position:
10D 5D
Pipe
Support
Pipe
Support
Valve
Non Return
Valve
Flow
In
Valve
Pipe
Support
Flow
Out
Fig.14 FLOW METER INSTALLATION IN VERTICAL POSITION
ELECTRONET
ELECTROMAGNETIC FLOW METER
ELMAG-200
0000.00 m3/Hr
000000.02 m3 L
ELECTRONET
ELECTROMAGNETIC FLOW METER
ELMAG-200
0000.00 m3/Hr
000000.02 m3 L

ELECTRONET
UM-ELMAG 200-R3 PAGE 14 OF 34
Important: Valves should always be mounted on the downstream side of the flow sensor!
a £ 7°
Valve
2. If it becomes necessary to use reducers, the inner angle must not exceed 7°.
5D 10D
5D 10D
5D 10D
Non Return Valve
9.5 Pipe System :
1.The flow sensor must be mounted in a location which is free from interfering elements like
valves, Ts, bends, pumps, etc. to ensure a laminar flow without turbulence upstream of the flow
sensor. For that reason the flow sensor must be mounted in a straight pipe at a distance from
interfering elements of minimum 10 x DN upstream and minimum 5 x DN downstream.
The minimum length to keep the angle below 7° can be checked by means of the formula below:
L= (D - d) / (2 x tana) where "D" is the large diameter and "d" the small diameter of the reducer.
Example: If a flow sensor in dimension DN 65 is mounted downstream of a 80 mm pipe,the
reducer must then have a length of minimum 108.80 mm in order to keep the inner angle
below 7°.
3. Flange connections must be assembled concentrically on both the upstream and the
downstream side. Due to improper connection assuring accuracy of flow meter will be affected.
Note:- Gaskets and grounding rings must also be mounted concentrically!
f = d
a £ 7°f = D
Mismatch pipe fitting
ELECTRONET
ELECTROMAGNETIC FLOW METER
ELMAG-200
0000.00 m3/Hr
000000.02 m3 L
ELECTRONET
ELECTROMAGNETIC FLOW METER
ELMAG-200
0000.00 m3/Hr
000000.02 m3 L
ELECTRONET
ELECTROMAGNETIC FLOW METER
ELMAG-200
0000.00 m3/Hr
000000.02 m3 L
ELECTRONET
ELECTROMAGNETIC FLOW METER
ELMAG-200
0000.00 m3/Hr
000000.02 m3 L
ELECTRONET
ELECTROMAGNETIC FLOW METER
ELMAG-200
0000.00 m3/Hr
000000.02 m3 L
ELECTRONET
ELECTROMAGNETIC FLOW METER
ELMAG-200
0000.00 m3/Hr
000000.02 m3 L

ELECTRONET
UM-ELMAG 200-R3 PAGE 15 OF 34
4. The flow sensor should always be filled with liquid. For that reason the flow sensor must not be
mounted at the highest point of the pipe system or in free outlets, where gravity could empty or
partially empty the pipe.
5. The flow sensor can be mounted vertically or horizontally . If the flow sensor is mounted
vertically , the flow direction should always be upwards. In that way the effect from possible
bubbles in the liquid will be significantly reduced, just as it will ensure that the flow sensor is
always filled with liquid. In case the liquid is carrying particles, for example when measuring
sludge, sewage, etc.,the flowsensor must be mounted vertically .
ELECTRONET
ELECTROMAGNETIC FLOW METER
ELMAG-200
0000.00 m3/Hr
000000.02 m3 L
ELECTRONET
ELECTROMAGNETIC FLOW METER
ELMAG-200
0000.00 m3/Hr
000000.02 m3 L
ELECTRONET
ELECTROMAGNETIC FLOW METER
ELMAG-200
0000.00 m3/Hr
000000.02 m3 L
ELECTRONET
ELECTROMAGNETIC FLOW METER
ELMAG-200
0000.00 m3/Hr
000000.02 m3 L
Table of contents
Popular Measuring Instrument manuals by other brands
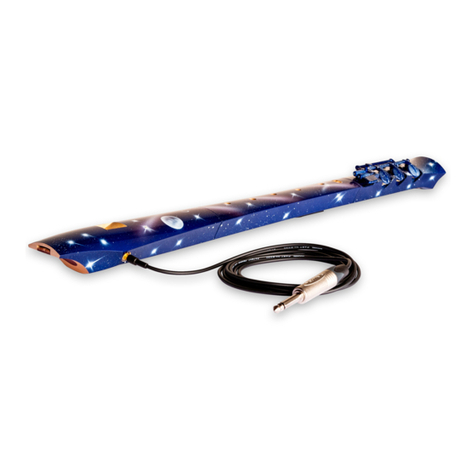
Mollenhauer
Mollenhauer ELODY Instructions for use
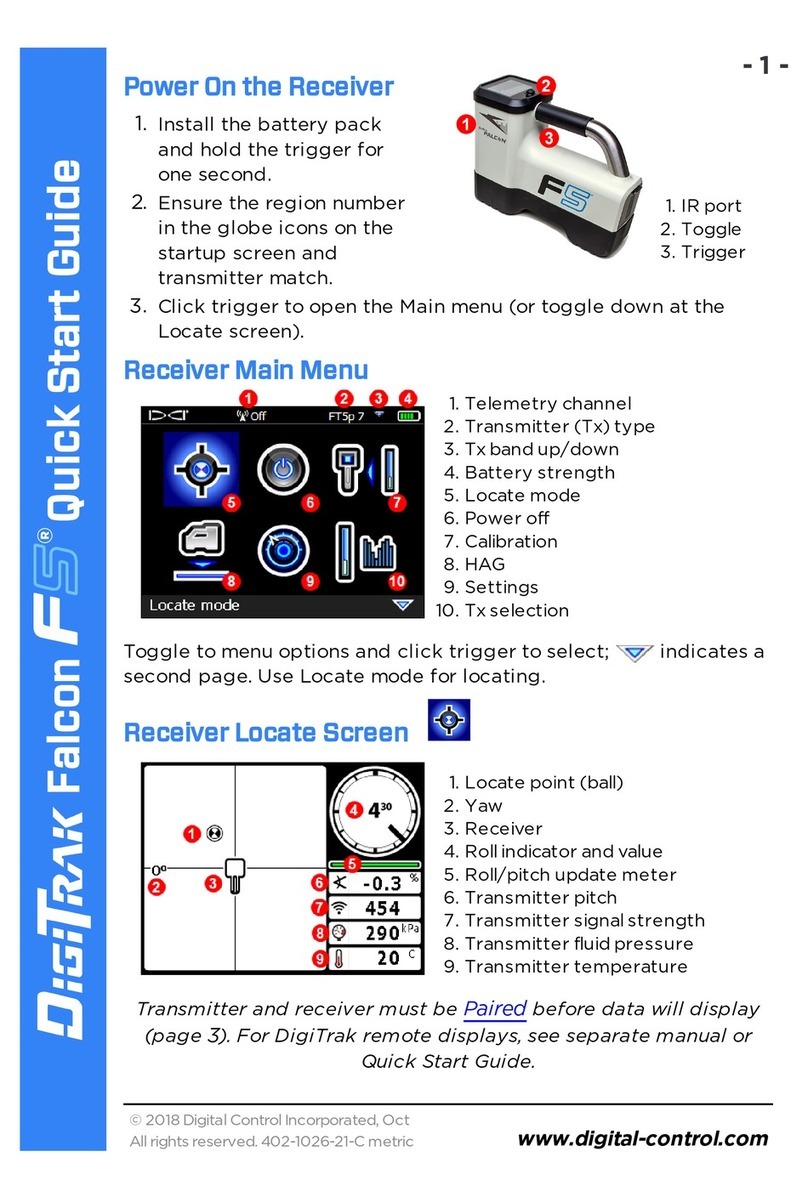
DigiTrak
DigiTrak FALCON F5 quick start guide
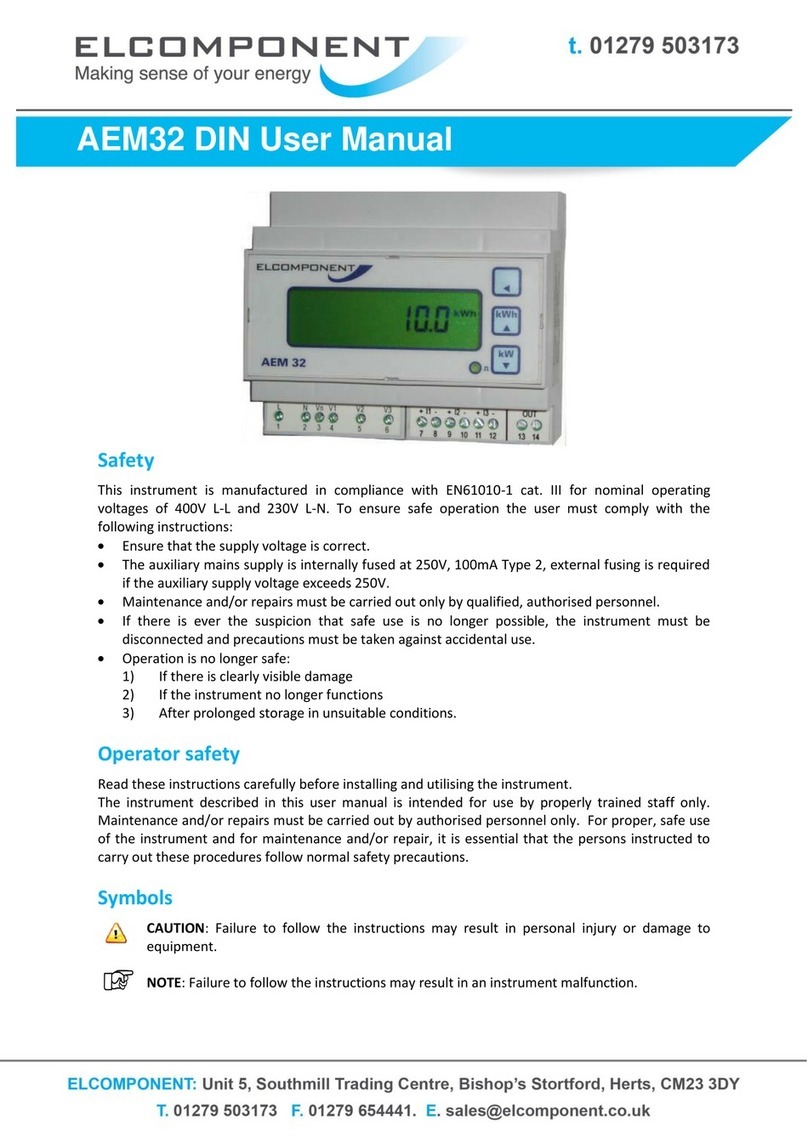
Elcomponent
Elcomponent AEM32 user manual

Endress+Hauser
Endress+Hauser RID16 operating instructions
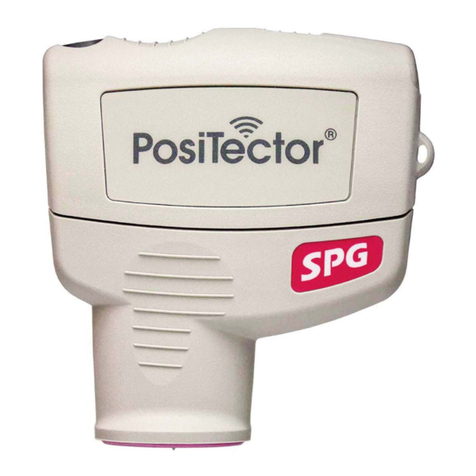
DeFelsko
DeFelsko POSITECTOR SMARTLINK instruction manual
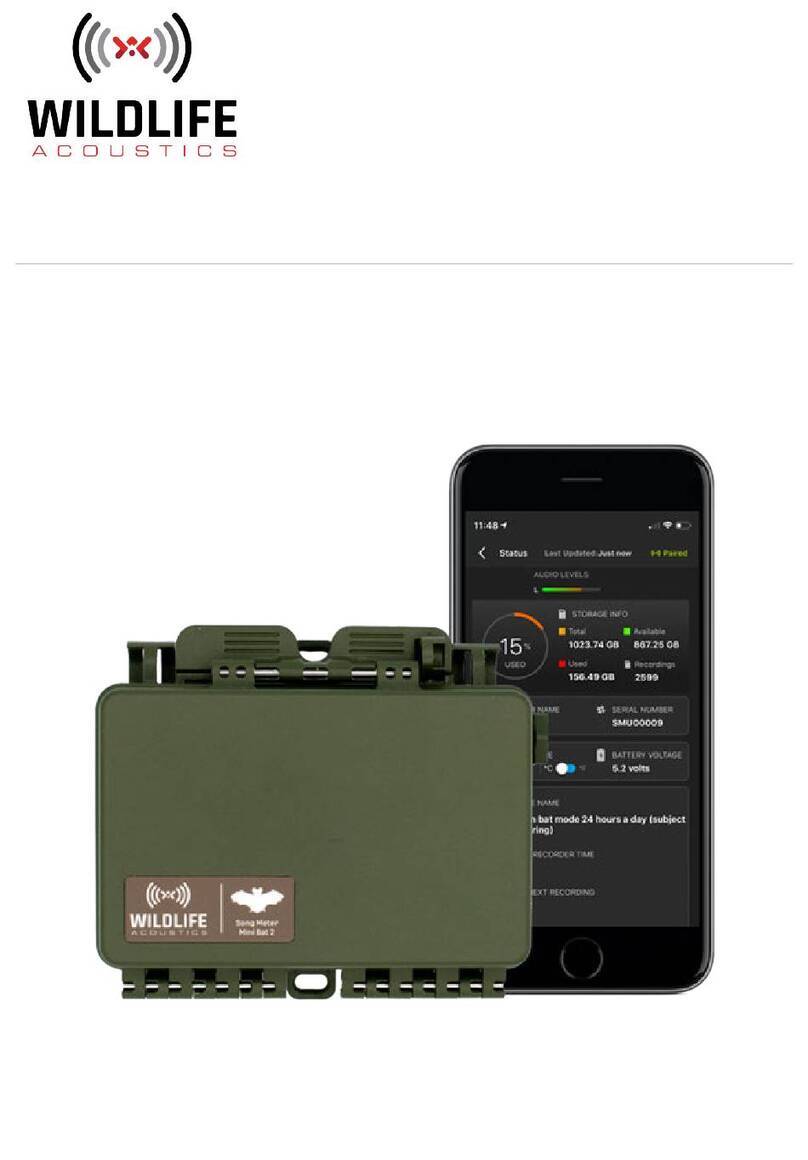
Wildlife Acoustics
Wildlife Acoustics Song Meter Mini Bat 2 user guide