ELITE VALVE E5600 DBB Manual

ELITE VALVE
2305 Wyecroft Road
Oakville, ON
Canada, L6L 6R2
P: 519-756-3100
www.elitevalve.com
OM5600-Rev A
operation &
maintenance manual
MODELS:
E5600 DBB
PERIMETER SEAT
KNIFE GATE VALVES
(SIZES 3” TO 48”)

i
Table of Contents
Table of Contents ..............................................................................................................................i
Guarantee.................................................................................................................................... - 1 -
Disclaimer.................................................................................................................................... - 1 -
Description .................................................................................................................................. - 1 -
Instructions.................................................................................................................................. - 2 -
Inspection.................................................................................................................................... - 2 -
Parts............................................................................................................................................. - 2 -
Component Identification ........................................................................................................... - 3 -
General Installation..................................................................................................................... - 3 -
Operation .................................................................................................................................... - 5 -
Lubrication................................................................................................................................... - 6 -
Transverse Seal............................................................................................................................ - 6 -
Packing Adjustment..................................................................................................................... - 6 -
Top Works Disassembly............................................................................................................... - 6 -
Valve Repair................................................................................................................................. - 6 -
Gate Inspection ........................................................................................................................... - 7 -
Gate Repair and Replacement..................................................................................................... - 7 -
Seat Inspection............................................................................................................................ - 7 -
Reassembling the Valve............................................................................................................... - 7 -
Troubleshooting .......................................................................................................................... - 8 -
Sales and Service ......................................................................................................................... - 8 -

- 1 -
Guarantee
Elite Valve warranties its products against manufacturing defects, and failure as a result
of manufacturing defects, for a period of one year from the date of purchase unless
otherwise specified on the original Sales Order Acknowledgement.
This warranty is limited to the performance of the valve and valve components where
assembled by Elite Valve. The company will repair, replace or refund the purchaser for
those components at its discretion provided that no modifications or alternations have
been made to these components. Furthermore, this warranty is limited to the
components in question and will not cover any other damages, either directly or
indirectly caused by the failure of said components.
Elite Valve’s warranty is void where any modifications have been made to the product or
product’s components, and thereby releases Elite Valve, its agents, and employees from
all obligations.
Disclaimer
Elite Valve reserves the right to incorporate the latest design and material changes
without notice or obligation. Design features and materials of construction as described
in this manual are for informational purposes only. Certified engineering drawings are
available upon request.
Description
Elite Valve’s knife gate valves can be made from almost any metal, but their typical
constructions are with stainless steel components. Elite Valve’s model E5600 knife gate
is available in sizes 3” to 48".
The E5600 knife gate valve features a split body design with a captured, removable and
replaceable perimeter seat. It is ideal for abrasive applications where the seat surface is
expected to wear quickly. Replacement becomes an economical means of maintaining
the valve and minimizing your process downtime. A guideline for replacing your seat can
be found later in this manual.
Injectable horizontal transverse seals and scrapers act to wipe process fluid, while
providing a liquid-tight seal against the gate. The full port design permits maximum flow,
while supporting the gate along the edges through the entire travel length. The
contoured seat design provides a flushing action during closing, eliminating solids build-
up while also providing metal-to-metal seating.

- 2 -
Instructions
These instructions are intended for personnel who are responsible for the installation,
operation and maintenance of your Elite Valve model E5600 knife gate valve. Personnel
involved in the installation or maintenance of valves should always be aware of the
potential emission of process material and should take all necessary safety precautions.
Always wear the required personal protective equipment when dealing with any
hazardous materials. Always handle valves that are removed from service with the
assumption that process material remains within the valve.
Inspection
Your Elite E5600 knife gate valve has been packaged to provide protection during
shipment. Carefully inspect the unit for damage upon arrival and file a claim with the
carrier if damage is apparent.
Parts
Order parts from your local sales representative. Recommended spare parts are listed
on the assembly drawing. These parts should be stocked to minimize your downtime.
When ordering parts, please provide the model number of the valve in question. This
can be found on the associated assembly drawing, or directly on the valve itself. See
Figure 1 below for the model number location.
Figure 1: Model Number Location

- 3 -
Component Identification
For your reference, see Figure 2 below to identify your knife gate valve components.
Figure 2: Component Identification
General Installation
Install the valve between ANSI Class 125 or Class 150 pipeline flanges with gaskets.
Before installation, remove foreign material such as weld spatter, oil, grease, and dirt
from the valve and pipeline.
Use the values for bolt torque found in Table A below. Observe the following points to
prevent distortion of the valve body and gate when the flange bolts are tightened:

- 4 -
Maintain alignment of the mating pipeline flanges
Select the length of the flange bolts for the blind holes in chest area of the
valve so they do not bottom out when tightened
Tighten the flange bolts evenly in a crisscross pattern
When bolting the valve in-line, use standard flange bolt torque less 25%
Adjust after start-up as required for gasket leaks etc.
Note: over torqueing will result in seizing of the gate against the seat ring
Valve Size
(in)
Torque
(ft-lbs)
3
32-38
4
32-38
6
56-65
8
56-85
10
54-63
12
54-63
14
82-95
16
82-95
18
117-135
20
117-135
24
165-190
30
165-190
36
282-325
42
282-325
48
282-325
Table A: Recommended Flange Bolt / Stud Torque Range in ft-lbs
If your valve is equipped with yoke mounted bolt style limit switches and target, travel
adjustments can be made by positioning the bolts and target in their slotted mounting
holes.
The ideal installation for a solid flow application is to mount the valve horizontally, which
allows gravity to assist the valve keep itself clean of product build up. The following
figures illustrate correct and incorrect installations for cylinder actuated, horizontally
mounted knife gate valves. Due to the cylinder’s weight, it must be supported externally
to prevent valve gate and cylinder rod misalignment.

- 5 -
Figure 3: Incorrect Horizontal Alignment
Figure 4: Correct Horizontal Alignment
Operation
The gate is positioned by the valve’s actuator or handwheel. When in the closed
position, the actuator slides the gate over the valve seat and withdraws the gate from the
seat into the open position. Note: if over-travel occurs when opening the gate (gate loses
contact with transverse seal), the bottom of the gate could get caught on top of the seal

- 6 -
and cause considerable damage (e.g. bending the gate, crushing the seal, etc.). For this
reason, there should be no adjustments made to the pre-set gate travel.
Lubrication
Knife gate valves that are equipped with handwheel or gear operators will normally have
a grease fitting for lubricating the threaded drive bushing. This fitting requires periodical
lubrication depending on the frequency of valve operation. Refer to the “Actuator
Instructions” for lubrication requirements for actuators.
Transverse Seal
The transverse seal is contained within slots on both bodies and compressed by the
gate. It has rigid back-up strips (which double as scrapers) to prevent extrusion, and is
reinforced by injectable packing.
Packing Adjustment
If the transverse seal leaks, tighten the adjustment screws on the sides of the bodies just
enough to stop the leak. Over-tightening will cause excessive operating forces and
decrease the life of the seal. Do not compress the packing more than is needed to stop
leaks. More packing can be added through the adjustment screws on the sides of the
bodies.
Top Works Disassembly
The following is a guide to disassembling the top works in order to conduct further
maintenance operations:
1. Set the valve to the open position
2. Ensure that energized actuator power sources are removed or locked and that
pipe process pressure is relieved before removing the top works assembly
3. Remove clevis bolts
4. Remove bolts that connect the yoke plates to valve body
5. Remove top works
Valve Repair
Valve repair typically consists of replacing seat, gates, and transverse seals. The seat
and transverse seal replacement are typically carried out simultaneously because they
wear evenly when made of the same material. Also see the troubleshooting section near
the end of this manual to determine the required action for certain conditions.

- 7 -
Gate Inspection
Gate repair or replacement may be necessary in the event that the packing leaks after
adequately tightening the packing follower. To remove the gate, the valve must be
removed from the process pipeline:
1. Place the valve in the fully open position
2. Ensure there is the process pipeline is free of product
3. Disconnect all components and energy sources connected to the valve (i.e.
pressurized air or hydraulic hoses, electrical wires, etc.)
4. Remove flange bolts and remove the valve from the pipeline
5. Separate the body halves by removing the socket head cap screws
Inspect the gate for wear by looking for deep scratches or galling. If the gate appears to
have deep scratches caused by product embedded in the transverse seal, attempt to
carefully remove the embedded product from the packing without damaging the seal. If
there is a large amount of embedded product, it may be necessary to replace the seal or
even the gate if it is damaged enough.
Gate Repair and Replacement
Repairing a gate with some light scratches is achievable by light polishing. Lightly polish
back and forth across the scratch (not in the direction of the scratch) along the entire
scratch.
Repairing gates with deep scratches can be achieved by a grinding process capable of
small flatness tolerances (e.g. Blanchard grinder or surface grinder). Remove no more
than .035”.
If the valve continues to leak after a repair attempt, it is evident that the gate should be
replaced. Please contact Elite Valve for assistance in gate replacement.
Insert the repaired or replaced gate back into the valve body. The 45º beveled edge on
the bottom of the gate should be on the same side as the seat retainer so that it makes
contact with the body. Proceed with the instructions for reassembling the valve.
Seat Inspection
In order to carry out a seat inspection, the valve must be removed from the process
pipeline. Follow the same instructions as Gate Inspection above.
Reassembling the Valve
1. Place the gate on the Seat Side Body half
2. Reinsert the O-ring seat starting at one end and laying it in the machined groove
3. Replace the transverse seal with the anti-extrusion strips

- 8 -
4. Inject packing as required
5. Place Non-Seat Side Body half on top of the body and bolt together
6. Place the top works assembly onto the valve body.
7. Fasten the yoke plate bolts into the body hand tight plus half a turn only
8. Secure the gate to the stem using the clevis bolts
9. Stroke the valve open and closed several times to allow the stem and gate to ‘self-
align’ *
10. Secure the top works assembly to the valve by tightening the yoke plate bolts
11. Reconnect the stem to the gate with the clevis bolts
12. If the actuator is a powered actuator, reconnect power to the actuator
13. Pressurize the pipeline and inspect packing for leakage
14. If packing leaks, tighten the adjustment screws on the side of the body. Tighten the
screws evenly and gently —just enough to stop the leak
* To promote longevity of the valve, it is best to ensure proper alignment of the gate and
stem to avoid uneven wear of cylinder bushings and lip seals, etc.
Troubleshooting
Condition
Possible Cause
Corrective Action
Transverse seal leaks, with no
evidence of galling on gate.
Transverse seal has
insufficient packing.
Add packing material to
transverse seal.
Transverse seal is worn or
torn.
Replace transverse seal.
Transverse seal leaks, and gate is
Transverse seal is worn or
torn.
Replace transverse seal and gate,
galled.
check seat for damage.
Valve leaks when fully closed,
Seat is worn or torn.
Replace seat.
with no evidence of galling on
gate.
Valve leaks when fully closed,
and gate is galled.
Seat is worn or torn.
Replace seat and
gate.
Table B: Troubleshooting
Sales and Service
For information about our worldwide locations, approvals and certifications, please visit
our website or feel free to contact Elite Valve directly.
Phone: 519-756-3100
Address: 2305 Wyecroft Road
Oakville, Ontario
Canada L6L 6R2
Web site: www.elitevalve.com
Table of contents
Popular Control Unit manuals by other brands
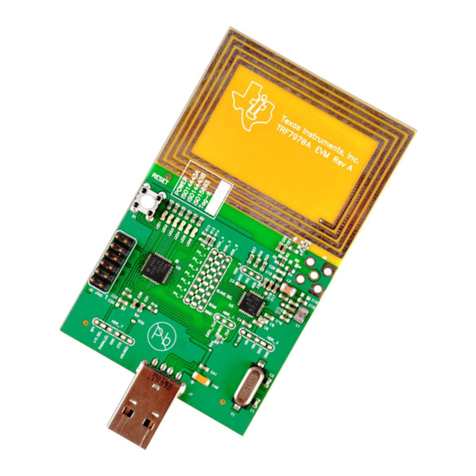
Texas Instruments
Texas Instruments TRF7970A BoosterPack user guide
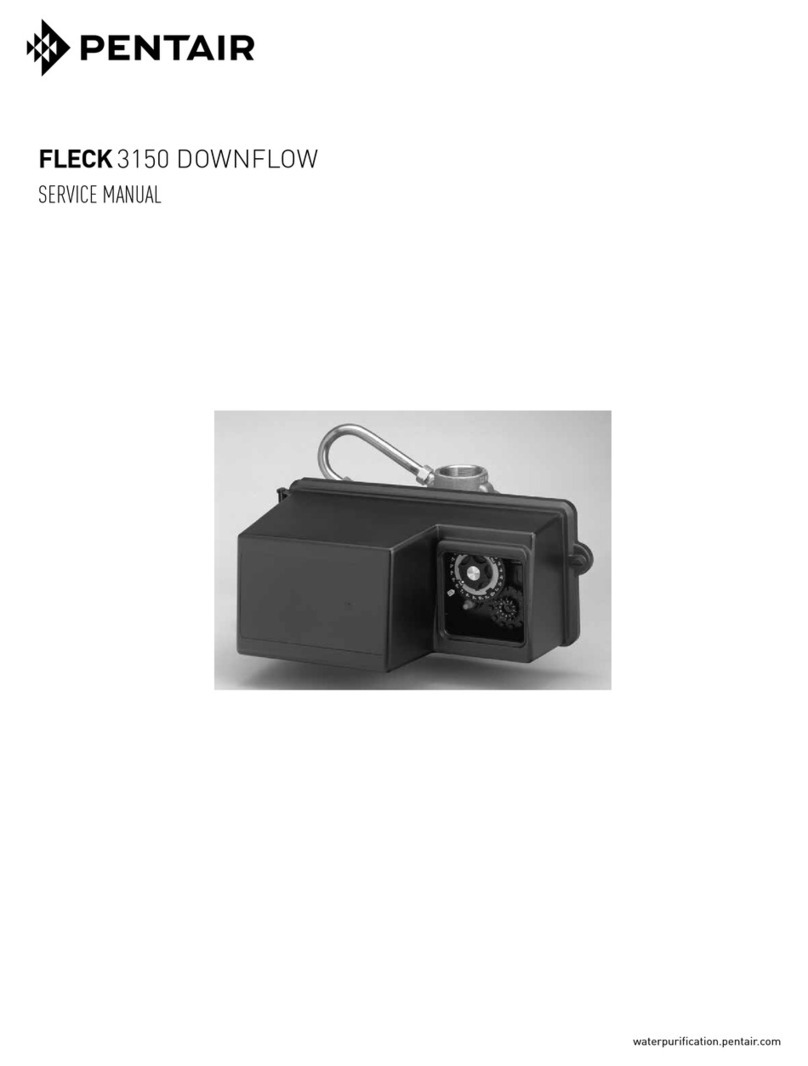
Pentair
Pentair FLECK3150 DOWNFLOW Service manual
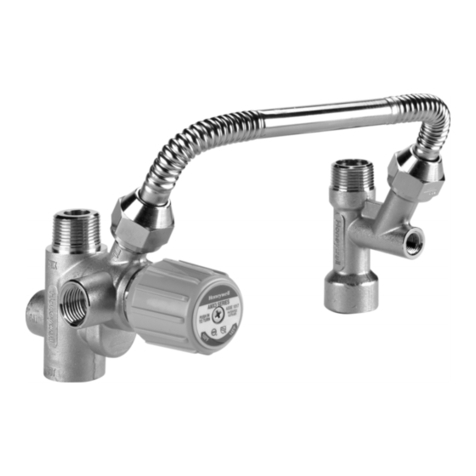
Honeywell
Honeywell DirectConnect AMX300 installation instructions

HP
HP Synergy 480 Gen10 user guide
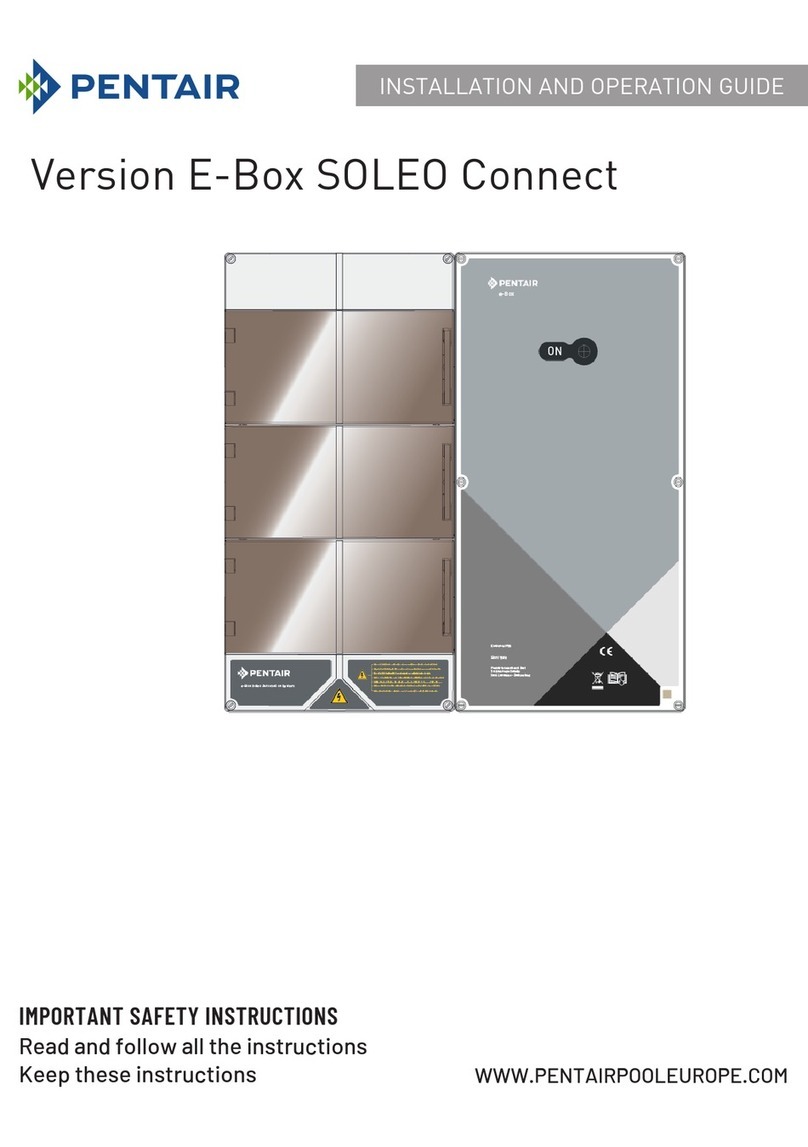
Pentair
Pentair E-Box SOLEO Connect Installation and operation guide
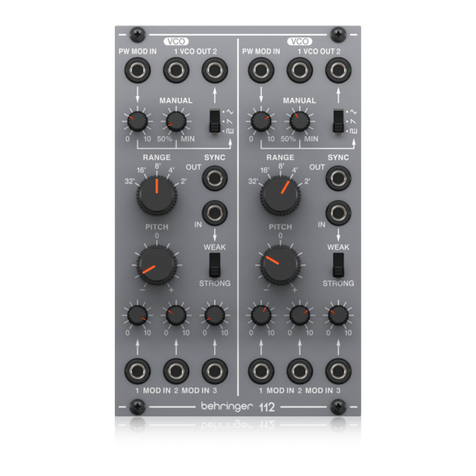
Behringer
Behringer 112 DUAL VCO quick start guide