Elmo HARmonica Quick start guide

Elmo HARmonica
Hands-on Tuning Guide
September 2003

Important Notice
This document is delivered subject to the following conditions and restrictions:
This guide contains proprietary information belonging to Elmo Motion Control Ltd.
Such information is supplied solely for the purpose of assisting users of the Elmo
HARmonica servo drive in tuning the device.
The text and graphics included in this manual are for the purpose of illustration and
reference only. The specifications on which they are based are subject to change
without notice.
Information in this document is subject to change without notice. Corporate and
individual names and data used in examples herein are fictitious unless otherwise
noted.
Doc. no. HARTG0903
Copyright 2003
Elmo Motion Control Ltd.
All rights reserved.
Revision History
Document version 1.0: September 2003
Elmo Motion Control Ltd.
64 Gisin St., P.O. Box 463
Petach Tikva
49103
Israel
Tel: +972 3 929-2300
Fax: +972 3 929-2322
Elmo Motion Control Inc.
900H River St.
Kennedy Industrial Park
Windsor, CT 06095
USA
Tel: +1 860 683-0095
Fax: +1 860 683-0336
Elmo Motion Control GmbH
Steinbeisstrasse 41
D-78056
Villingen-Schwenningen
Germany
Tel: +49 07720 8577-60
Fax: +49 07720 8577-70
www.elmomc.com

Contents
1. Introduction ............................................................................................................................ 1
2. Tuning Current....................................................................................................................... 1
3. Tuning Velocity...................................................................................................................... 1
3.1 Auto-tuning Velocity................................................................................................... 1
3.1.1 Step 1................................................................................................................. 1
3.1.2 Step 2................................................................................................................. 2
3.1.3 The Auto-tuning Procedure............................................................................ 3
3.2 Manually Tuning Velocity.......................................................................................... 3
3.2.1 Manual Tuning with a Low-pass Filter........................................................14
3.2.2 Manual Tuning of a PI Controller with a Notch Filter...............................17
3.3 Advanced Manual Tuning.........................................................................................20
4. Tuning Position.....................................................................................................................25
4.1 Introduction.................................................................................................................25
4.2 Tuning the Position Loop ..........................................................................................26
4.3 Lowering the Speed....................................................................................................32


1. Introduction
When a new motor is connected to the HARmonica servo drive, you should use the
Composer Wizard to set the motor parameters and to tune the control loops. The
Wizard will assist you in choosing the optimal drive parameters, step-by-step.
In the Wizard dialog, you are asked to enter the maximum continuous current and
maximum velocity of the motor.
2. Tuning Current
Each time you connect a new motor to the drive, you must tune the current loop of
the drive. Current tuning is fully automatic: The Composer creates a step command
to the current loop and finds the optimum PI parameters according to step response
iterations.
3. Tuning Velocity
3.1 Auto-tuning Velocity
3.1.1 Step 1
If you are tuning the drive for a velocity application, select Auto Tuning for
Speed Design from the Select the Tuning Type drop-down list.
If you are tuning the drive as a velocity drive under a position controller, select
Auto Tuning for Speed Design from the Select the Tuning Type drop-down
list.
There is no need to perform velocity auto-tuning if you intend to auto-tune the drive
as a position controller.
1

3.1.2 Step 2
1. From the Auto Tuning Mode drop-down list:
Select Expert tuning for bounded if position boundaries cannot be
exceeded.
Select Expert tuning for free motion if there is no restriction on the system
motion.
2. Using the Response slider to select the system margin you require:
Choose a value towards Fast and Sensitive if you require a more responsive
(agile) system.
Choose a value towards Slow and Stable if you need a more robust system,
which is required in a number of cases, among them:
Machines whose mechanics may vary, as when handling loads of
different masses
A machine type that uses one type of control parameters, although the
mechanics of each machine may differ from each other.
3. Use the System Noise slider to select the level of plant noise. The trade-offs are
obvious: Fast and Noisy to Slow and Quiet.
4. Activate the auto-tuning procedure by clicking Run Auto Tuning.
2Elmo HARmonica Tuning Guide
HARTG0903

3.1.3 The Auto-tuning Procedure
The auto tuning procedure is built on the following steps.
1. The tuner creates a velocity step command and finds a low bandwidth control
loop, to enable the motor to move while performing system identification.
2. The tuner injects a current command at different frequencies, while moving the
motor at a constant speed. The tuner records the velocity and position response
to the current different frequencies.
3. The tuner calculates the open loop transfer function of the mechanical system as
sent to the drive (including sensors and delay influence).
4. The tuner calculates the drive transfer function in order to control the system.
5. The composer displays the step response of the control system.
3.2 Manually Tuning Velocity
1. From the Select the Tuning type drop-down list, select Manual Tuning. The
following dialog box will be displayed.
2. Set KP to 10 and KI to 0.
3. Be sure that the Advanced Filter is OFF.
4. Set the Displacement to a maximum of +/-1000. If the position boundaries do
not allow this displacement, reduce it as needed.
5. Set the Velocity to 20000 cnt/sec.
6. Uncheck the Profiler Mode check button.
7. Click Run Test. The Wizard will perform a step command and will record the
system response, displayed in a two-pane scope window.
3

8. In the first pane, you can see the Velocity and the Velocity command and in the
second, you can see the Current command. If the current command has reached
the peak current, reduce the velocity command and repeat the test, multiplying
KP by 2.
If machine vibrations are dangerous, multiply KP by 1.5 each time,
instead of 2.
9. Repeat step 8 until you reach one of the following:
The step response exhibits an overshoot of about 20%.
The step response is unacceptable;, for example, it shows resonant
oscillation.
The system exhibits a large overshoot and undershoot, a sign of being close
to instability. In this case, decrease KP by at least a factor of 2.0.
4Elmo HARmonica Tuning Guide
HARTG0903

5

6Elmo HARmonica Tuning Guide
HARTG0903

7

8Elmo HARmonica Tuning Guide
HARTG0903

Here we can see that we have reached a 25% overshoot and the beginning of
oscillations.
10. At this point reduce KP to 75% of its value and repeat the test.
9

We can see that the oscillations have disappeared and the overshoot has been
reduced to 10%.
11. At this point, we can add KI to the controller. If one of the phenomena
described in step 9 has returned, revert to the previous value of KP.
12. In order to set the first value of KI, measure the rise time of the step.
10 Elmo HARmonica Tuning Guide
HARTG0903

In this case, it is 0.0016 sec.
13. Set KI/KP to 1/rise time = 625.
KI = (KI/KP) * KP = 75,000
If machine vibrations are dangerous, set KI/KP to 0.5/rise time and
increase KI until an undershoot or oscillations occur.
14. Set the KI value and repeat the test.
15. We can see that the system has reached saturation. Therefore, reduce the speed
to 15000 cnt/sec. The following performance results:
11

This shows a nice response with no undershoot or oscillations. The system has
stabilized after 3.25 msec.
16. Had the KI been too great, oscillations or too large an undershoot would have
occurred. To observe this case, increase KI to 90,000.
We can see a large undershoot. If a response such as this occurs, reduce KI until
you reach a satisfactory response.
17. A robust system is required in a number of circumstances, among them:
Machines whose mechanics may vary, as when handling loads of different
masses
A machine type that uses one type of control parameters, although the
mechanics of each machine may differ from each other.
12 Elmo HARmonica Tuning Guide
HARTG0903

In either of these cases, the gain must be reduced to enable a larger system
margin. To see this, reduce KP and run the test:
18. Set the following parameters:
Rise time = 0.0018 sec
KI/KP = 1 / Rise time = 555
KI = 80 * 555 = 44400
We can see we that the resulting settling time is 5.75 msec.
There is no reason to attempt to reach the highest bandwidth. Reducing the
bandwidth can help attain a much more stable system.
13

3.2.1 Manual Tuning with a Low-pass Filter
Going back to KP = 40 and KI = 0we can see high frequency vibrations in both the
Velocity and Current command.
Adding a low-pass filter with a high frequency will reduce the RMS noise of the
current and will help us achieve a quieter system.
14 Elmo HARmonica Tuning Guide
HARTG0903

Adding the low-pass filter results in an overshoot at KP = 80.
A KP of 100 gives an overshoot of 20% and the beginning of oscillations.
15

Reducing KP to 75 results in the following performance:
Rise time = 0.002 sec results in KI/KP = 500.
When adding a low-pass filter, do not set the KI/KP higher than filter
frequency.
16 Elmo HARmonica Tuning Guide
HARTG0903
Table of contents
Popular Control System manuals by other brands

SALUPO
SALUPO IMPEDANCE 1 SQ701. Series Instruction and installation manual
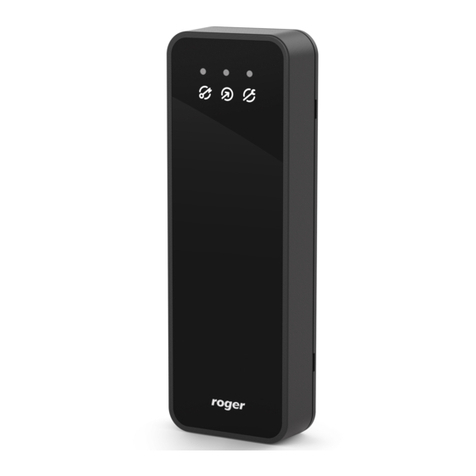
Roger
Roger PRT12MF-DES operating manual

Fagor
Fagor 8070 BL Programming manual
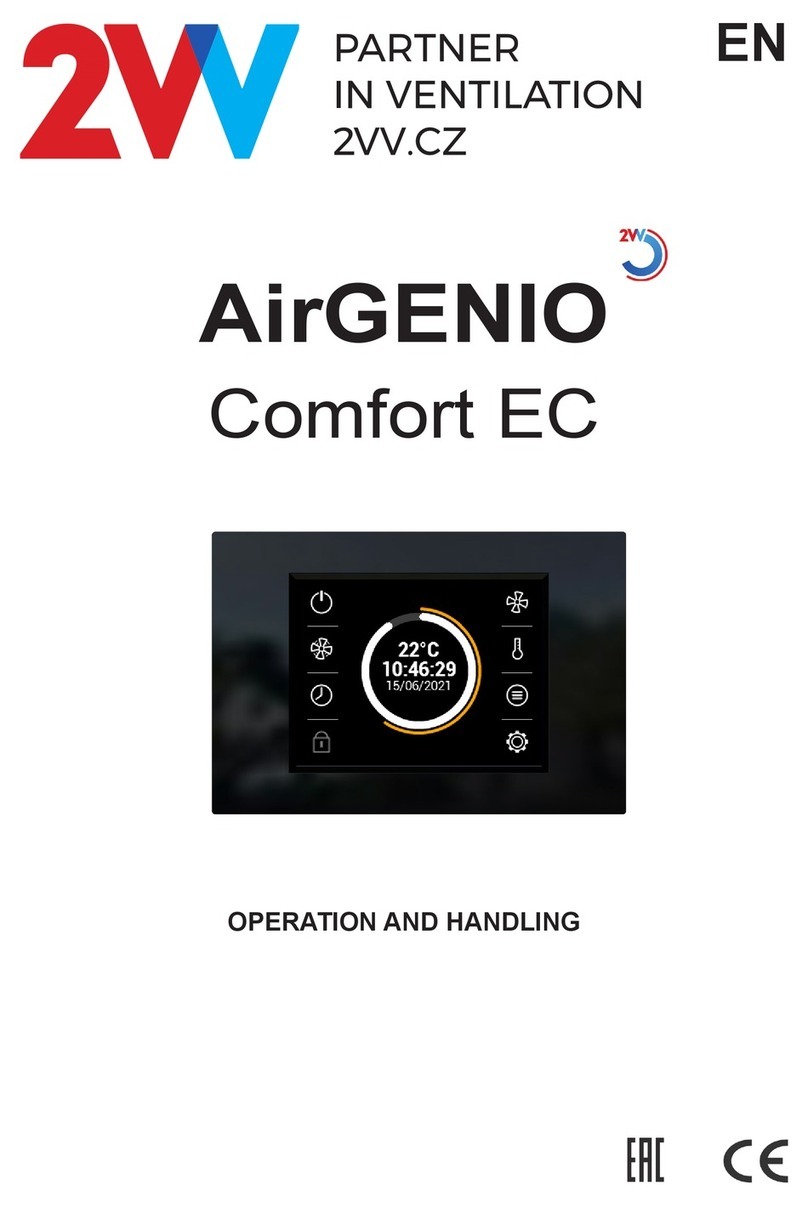
2VV
2VV AirGENIO Operation and use
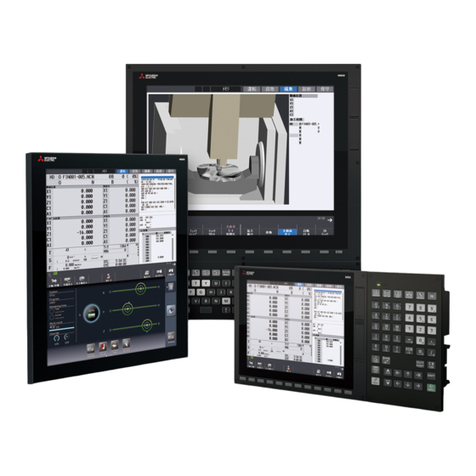
Mitsubishi Electric
Mitsubishi Electric M800VW Series Programming manual
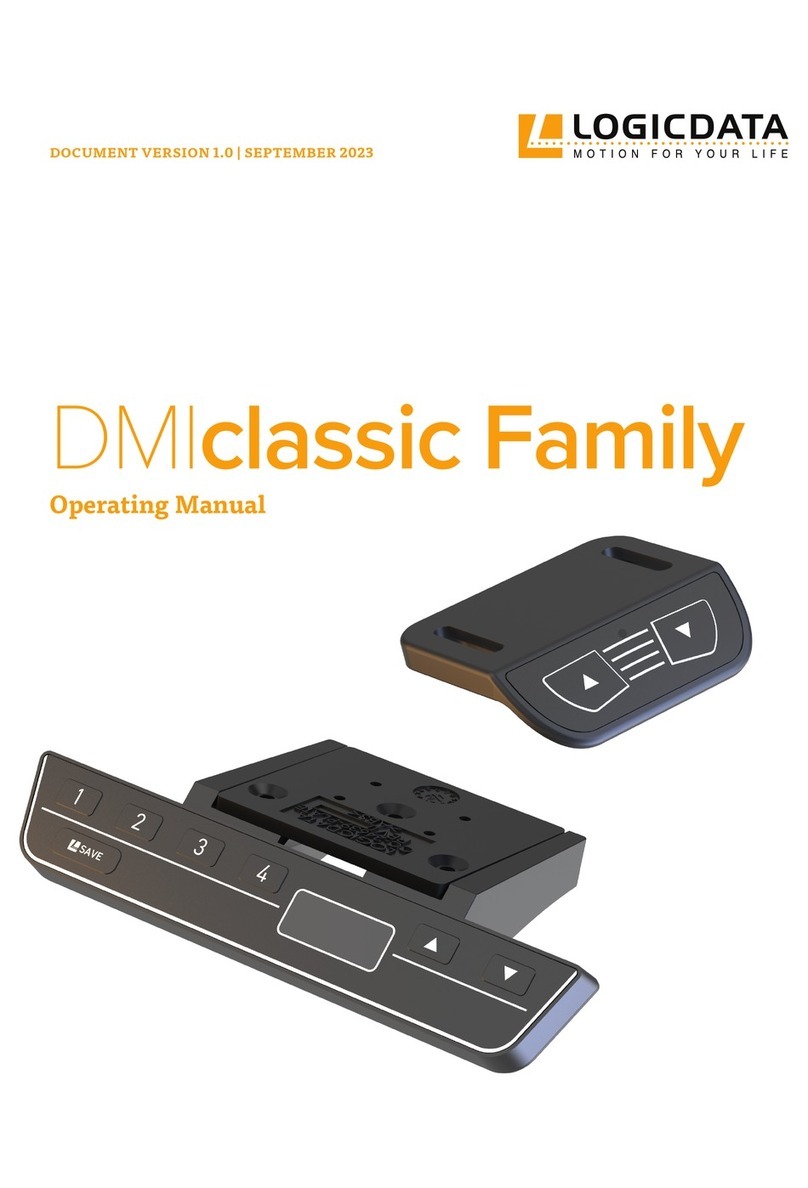
LOGICDATA
LOGICDATA DMIclassic Series operating manual