eneren RAW User manual

HF61GJ0600D / 04_23
USER MANUAL AND TECHNICAL MANUAL
RAW
EN
TRANSLATION OF THE ORIGINAL INSTRUCTIONS
AIR/WATER AEROTHERMAL HYDROTHERMAL UNITS
WITH INTEGRATED HYDRONIC MODULE


INTRODUCTION
RAW
REVERSIBLE AEROTHERMAL UNITS WITH INTEGRATED HYDRONIC MODULE
CWARNING
CAREFULLY READ THIS MANUAL BEFORE USING THE
UNIT.
CDECLARATION OF CONFORMITY
The declaration of conformity is attached separately to
the documents on board the unit, usually placed inside the
electrical compartment.
Dear Customer,
Thanking you for choosing our products, we are pleased to provide you this manual for the correct use of equipment.
Please read the recommendations described in the following pages carefully and keep the manual available to personnel
who will be responsible for managing and maintaining the unit.
Our company is at your complete disposal for any and all questions that you should require both in the unit starting phase
and at any time of its utilization.
Should scheduled and unscheduled maintenance be necessary, please contact our After-sales Technical Service for assis-
tance and spare parts.
Please nd here attached our direct contacts in case you may need assistenace:
RAW |UsER MANUAL AND TECHNICAL MANUAL
3

START-UP INSTRUCTIONS
1 YOUR INSTALLATION
All the tips required for a perfect installation of the equipment can be found in the installation manual.
2 REQUIRED ACCESSORIES FOR A PROPER INSTALLATION OF THE UNIT
To ensure ecient unit operation and validity of the guarantee, check the correct sizing of the following hydraulic compo-
nents installed inside the machine to make sure they match system connection requirements:
Safety valves. The setting of the installed safety valves must be 3 bar.
Expansion vessels. The installed expansion vessels have the following characteristics:
ŪUser side: 12L capacity and factory pre-charge 1 ± 20%
bar
ŪDHW side: 12L capacity and factory pre-charge 1 ± 20%
bar
3 FIRST START-UP
With at least 15 working days in advance, send the machine start request via email or fax to the following contact ENEREN:
Fax. 049 9588522
e-mail: [email protected]
Tel. 049 9271513
ENEREN Assistance will organize the intervention by putting you in contact with Authorized Technical Assistance Center of
the area.
All the preliminary checks and testing of the machine will be carried out together with your staff.
Your staff will be given instructions for the correct running of the machine.
4 WARRANTY ISSUE
For the warranty to be valid, the rst start-up by an Authorized Technical Assistance Center is mandatory
After testing, the Authorized Technical Assistance Center will issue a valid test certicate for the machine warranty.
5 CONNECTIONS
Here below are the minimum diameters for the pipes providing the connection to the units.
These diameters must be veried on the basis of the useful heads of the circulation pumps declared in the dedicated para-
graph of the following manual.
RAW size 006 009 012 015 017
Minimum diameter of the connection pipes inches 1” 1 1/2”
RAW |HF61GJ0600D
4

TABLE OF CONTENTS
1 INTRODUCTION � � � � � � � � � � � � � � � � � � � � � � � �p.3
2 START-UP INSTRUCTIONS� � � � � � � � � � � � � � �p.4
USER MANUAL � � � � � � � � � � � � � � � � � � � � � � � � �p.6
3 GENERAL DESCRIPTION � � � � � � � � � � � � � � � �p.7
3.1 PRECAUTIONS FOR USE. . . . . . . . . . . . . . . . . . . . . . .p.7
3.2 PREMISE . . . . . . . . . . . . . . . . . . . . . . . . . . . . . . . . . . .p.7
3.3 LIABILITY. . . . . . . . . . . . . . . . . . . . . . . . . . . . . . . . . . .p.7
3.4 INTENDED USE . . . . . . . . . . . . . . . . . . . . . . . . . . . . . .p.8
3.5 IDENTIFICATION OF THE UNIT . . . . . . . . . . . . . . . . .p.8
3.6 GENERAL INSTRUCTIONS . . . . . . . . . . . . . . . . . . . . .p.8
4 SAFETY INSTRUCTIONS� � � � � � � � � � � � � � � �p.10
4.1 GENERAL CAUTIONARY NOTES. . . . . . . . . . . . . . . .p.10
4.2 SAFETY PRESCRIPTIONS. . . . . . . . . . . . . . . . . . . . .p.11
5 DESCRIPTION OF THE PRODUCT AND
TECHNICAL DATA � � � � � � � � � � � � � � � � � � � � �p.14
5.1 MAIN COMPONENTS. . . . . . . . . . . . . . . . . . . . . . . . .p.14
5.2 OPERATING LIMITS. . . . . . . . . . . . . . . . . . . . . . . . . .p.15
5.3 CHARACTERISTIC CURVES OF THE
CIRCULATION PUMPS . . . . . . . . . . . . . . . . . . . . . . .p.18
5.4 CALIBRATION OF CONTROL DEVICES. . . . . . . . . . .p.18
5.5 LIQUID REFRIGERANT LINES AND REFRIGERANT
CHARGE . . . . . . . . . . . . . . . . . . . . . . . . . . . . . . . . . . .p.19
5.6 SYSTEM BOOKLET . . . . . . . . . . . . . . . . . . . . . . . . . .p.23
6 INSPECTION AND TRANSPORT � � � � � � � � �p.24
6.1 INSPECTION . . . . . . . . . . . . . . . . . . . . . . . . . . . . . . .p.24
6.2 LOCATION OF SAFETY DATA PLATES . . . . . . . . . . .p.24
6.3 RESIDUAL RISK AREAS. . . . . . . . . . . . . . . . . . . . . . .p.25
6.4 LIFTING AND CONVEYANCE. . . . . . . . . . . . . . . . . . .p.26
6.5 UNPACKING . . . . . . . . . . . . . . . . . . . . . . . . . . . . . . . .p.26
7 RETIRING THE UNIT � � � � � � � � � � � � � � � � � � �p.27
7.1 ENVIRONMENT PROTECTION . . . . . . . . . . . . . . . . .p.27
7.2 WASTE ELECTRICAL AND ELECTRONIC
EQUIPMENT MANAGEMENT. . . . . . . . . . . . . . . . . . .p.27
7.3 PACKAGING DISPOSAL. . . . . . . . . . . . . . . . . . . . . . .p.28
TECHNICAL MANUAL � � � � � � � � � � � � � � � � � �p.29
8 INSTALLATION � � � � � � � � � � � � � � � � � � � � � � � �p.30
8.1 POSITIONING AND INSTALLATION . . . . . . . . . . . . .p.30
8.2 REQUIREMENTS FOR THE INSTALLATION OF
UNITS WITH A2L REFRIGERANT . . . . . . . . . . . . . . .p.31
8.3 QUALITY OF THE WATER IN THE SYSTEMS . . . . . .p.33
8.4 GENERAL GUIDELINES FOR PLUMBING
CONNECTIONS . . . . . . . . . . . . . . . . . . . . . . . . . . . . .p.34
8.5 BUFFER TANK FOR HEATING AND COOLING
CIRCUIT . . . . . . . . . . . . . . . . . . . . . . . . . . . . . . . . . . .p.36
8.6 CONTROL AND SAFETY DEVICES . . . . . . . . . . . . . .p.36
9 ELECTRICAL CONNECTIONS � � � � � � � � � � � �p.39
9.1 GENERAL DESCRIPTION. . . . . . . . . . . . . . . . . . . . . .p.39
9.2 EXTERNAL ENABLING CONTROLS . . . . . . . . . . . . .p.39
9.3 REMOTE SUMMER-WINTER SWITCHING . . . . . . . .p.39
10 START-UP � � � � � � � � � � � � � � � � � � � � � � � � � � � �p.41
10.1 PRELIMINARY CHECKS . . . . . . . . . . . . . . . . . . . . . .p.41
10.2 START-UP THE UNIT . . . . . . . . . . . . . . . . . . . . . . . . .p.41
10.3 SELECTING THE OPERATING MODES . . . . . . . . . . .p.42
10.4 SETTING THE SET-POINTS. . . . . . . . . . . . . . . . . . . .p.43
10.5 CHECKS DURING OPERATION . . . . . . . . . . . . . . . . .p.43
10.6 STOPPING THE UNIT . . . . . . . . . . . . . . . . . . . . . . . .p.44
11 ROUTINE MAINTENANCE AND CHECKS � �p.45
11.1 WARNINGS. . . . . . . . . . . . . . . . . . . . . . . . . . . . . . . . .p.45
11.2 MAINTENANCE TABLE . . . . . . . . . . . . . . . . . . . . . . .p.45
11.3 REFRIGERATION CIRCUIT REPAIRS. . . . . . . . . . . . .p.46
11.4 TIGHTNESS TEST . . . . . . . . . . . . . . . . . . . . . . . . . . .p.46
12 TROUBLESHOOTING � � � � � � � � � � � � � � � � � � �p.47
12.1 UNIT ALARM . . . . . . . . . . . . . . . . . . . . . . . . . . . . . . .p.47
12.2 TROUBLESHOOTING. . . . . . . . . . . . . . . . . . . . . . . . .p.47
13 SAFETY DATA SHEET OF REFRIGERANT
� � � � � � � � � � � � � � � � � � � � � � � � � � � � � � � � � � � � � �p.48
14 MAINTENANCE TABLE � � � � � � � � � � � � � � � � �p.49
15 SYSTEM DIAGRAMS � � � � � � � � � � � � � � � � � � �p.50
16 NOTES � � � � � � � � � � � � � � � � � � � � � � � � � � � � � � �p.52
RAW |UsER MANUAL AND TECHNICAL MANUAL
5

USER MANUAL
RAW |HF61GJ0600D
6

3 GENERAL DESCRIPTION
3.1 Precautions for use
The operating rules contained in this manual are solely ap-
plicable for the units:
RAW
The instructions manual must be read and used as follows:
Ūevery unit operator and maintenance technician must
carefully read the entire manual and comply with that
stipulated therein;
Ūthe employer must ensure that the operator has the re-
quirements to operate the unit and has carefully read the
manual;
Ūread the instructions manual carefully and consider it an
integral part of the unit;
Ūthe instructions manual must be readily available to op-
erating personnel and maintenance technicians;
Ūkeep the manual throughout the life of the unit;
Ūmake sure that any update is included in the text;
Ūhand the manual to any other user or subsequent owner
of the unit;
Ūuse the manual in such a way so as not to damage its
content;
Ūdo not, for any reason, remove, tear or rewrite parts of
the manual;
Ūkeep the manual away from humidity and heat;
Ūif the manual is lost or partially damaged and therefore
the contents can no longer be read entirely, it is advisa-
ble to request a new manual from the manufacturer by
communicating the code found on the cover or the serial
number of the unit.
Pay utmost attention to the following symbols and their
meaning. Their purpose is to highlight specic information
such as:
SAFETY SYMBOLS
CWARNING
With reference to additions or rec-
ommendations for the correct use
of the unit.
ADANGER
With reference to dangerous situa-
tions that may occur with the use
of the unit to guarantee personal
safety.
BATTENTION
With reference to dangerous situa-
tions that may occur with the use
of the unit to prevent damage to
property and to the unit itself.
3.2 Premise
The operating rules described in this manual are an integral
part of the unit supply.
These rules are also intended for the previously trained op-
erator specically to operate this type of unit and contain
all the necessary and important information for operating
safety and optimal, proper use of the unit. Avoid hasty and
incomplete preparation that lead to improvisation and cause
many accidents.
Before starting to work, read through and strictly observe the
following suggestions:
Ūthe operator must always have the instructions manual
at his disposal;
Ūplan each action carefully;
Ūbefore starting work, make sure the safety devices func-
tion correctly and you have no doubts on how they work;
otherwise, do not start-up the unit;
Ūcarefully observe the warnings relating to special haz-
ards contained in this manual;
Ūpreventive and thorough maintenance guarantees con-
stantly high operating safety for the unit. Never delay
repairs and always have them carried out solely by qual-
ied personnel; only original spare parts are to be used.
3.3 Liability
The MANUFACTURER cannot be held liable for any personal
accident or damage to property, which may arise from:
Ūfailure to comply with the instructions provided in this
manual regarding unit management, use and mainte-
nance;
Ūviolent actions or incorrect manoeuvres when perform-
ing maintenance on the unit;
Ūalterations made to the unit without prior written author-
isation from the MANUFACTURER;
Ūincidents beyond the normal and correct use of the unit.
In any case, if the user attributes the incident to a defect in
the unit, he must prove that the damage caused was a main
and direct consequence of this “defect”.
BATTENTION
ŪWhen installing or servicing the unit, the rules stipulat-
ed in this manual must be complied with together with
those on board the unit and in any case all necessary
precautions must be taken.
ŪThe presence of pressurised uids in the refrigerant cir-
cuit and of electrical components can create hazardous
situations during installation and maintenance.
ŪTherefore, only qualied personnel may perform work on
the unit.
ŪTHE UNIT MUST BE STARTED UP FOR THE FIRST TIME
ONLY BY QUALIFIED PERSONNEL AUTHORISED BY THE
COMPANY PLACING IT ON THE MARKET.
ŪFAILURE TO COMPLY WITH THE RULES STIPULATED
IN THIS MANUAL AND ANY ALTERATION TO THE UNIT
WITHOUT PRIOR AUTHORISATION WILL IMMEDIATELY
MAKE THE WARRANTY NULL AND VOID.
ŪBefore performing any work on the unit, ensure it has
been disconnected from the power supply.
ŪFor maintenance service or repairs always and exclu-
sively use original spare parts. THE MANUFACTURER
declines all responsibility for damages that may occur
due to non-compliance with the above.
RAW |UsER MANUAL AND TECHNICAL MANUAL
7

ŪThe unit is covered by the warranty according to the con-
tractual agreements established at the time of sale.
ŪHowever, the warranty is rendered null and void if the reg-
ulations and user instructions stipulated in this manual
are not complied with.
ŪIn the event of a fault, do not try to repair it yourself or
have an unauthorised technician perform the repairs.
The warranty will otherwise be rendered null and void.
3.4 Intended use
RAW are air-water heat pumps which, without using any type
of combustion or ame, allow the entire home to be heated
or cooled and technical hot water to be produced for sani-
tary purposes in a completely autonomous way, thanks to
the exchange of heat with the outside air.
Their use is recommended within the functioning limits car-
ried in this manual, or else the warranty attached to the sales
contract would cease.
Any other use is to be considered inappropriate and the
manufacturer declines all liability for any damage caused to
persons, property or the unit that may derive from such use.
ADANGER
ŪPlace the unit in environments where there is no risk of
explosion, corrosion or re.
ŪImproper use could cause serious repercussions on the
unit.
ŪAll routine and special maintenance operations must be
performed with the unit off and the power supply discon-
nected.
ŪWait approximately 30 minutes after switching off the
unit before carrying out any maintenance operations to
avoid burns.
ŪThe indoor unit is only for indoor use, the outdoor unit is
only for outdoor use.
BATTENTION
ŪBefore performing any work on the unit, each operator
must be perfectly aware of how the unit and its controls
work and must have read and understood all the techni-
cal information in this manual.
ŪIt is forbidden to use the unit in conditions or for us-
es other than what is indicated in this manual and the
MANUFACTURER may not be held responsible for break-
downs, accidents or injuries due to failure to comply with
this prohibition.
ŪDo not repair high pressure pipes with welds.
ŪIt is forbidden to tamper with, alter or modify, even par-
tially, the systems or equipment described in the instruc-
tion manual, and in particular, the guards and warning
symbols required for personal safety.
ŪIt is also forbidden to operate in manners different from
those indicated or fail to perform operations necessary
for safety reasons.
ŪSafety instructions are particularly important, as well as
general information contained in this manual.
3.5 Identification of the unit
Each unit has an identication plate that is located on its
frame, which shows all the data necessary for the installa-
tion, maintenance and traceability of the machine.
Note the model, the serial number, the nal refrigerant
charge and the machine reference diagrams attached to this
manual so that they can be easily found in case of data plate
damaging and system maintenance.
Make a note of the information indicated on the silver name-
plate of the indoor unit (model RAW) and the outdoor unit
(RAW).
Manufatured byHiRef S.p.A.
Via Spagna,31-33 Z.I.-35020 Tribano(PD)-Italy Tel.+390499588511-Fax+390499588522
P.I.e C.F. 04226420281
2761
Modello - Model
Matricola - Serial Number
Codice ID - Code ID
Data di Produzione - Date of production
Categoria PED/2014/68/EU Category
Modulo di valutazione - Conformity Module
Max pressione ammissibile
Max allowed pressure PS [bar-r]
Max pressione ammissibile lato bassa
Max allowed pressure low side PS [bar-r]
Max/Min temp. stoccaggio - Max/Min storage temp
Potenza frigorifera - Cooling capacity*
EER*
Potenza termica - Heating capacity*
COP*
Refrigerante - Refrigerant [Ashrae 15/1992]/GWP
Carica refrigerante - Refrigerant charge [kg]
Refrigerante aggiunto - Refrigerant added [kg]
Carica totale - Total Charge [kg]
Ton. di CO2 equivalenti-Tonnes of CO2 equivalent
Tar press. lato ALTA-HIGH pressure Switch Set [bar-r]
Tar press. lato BASSA-LOW pressure Switch Set [bar-r]
Taratura valvola sicurezza refrigerante
Safety valve refrigerant Set [bar-r]
Taratura valvola sicurezza acqua
Safety valve water side Set [bar-r]
Alim. elettrica principale-Main Power supply
Alim. elettrica secondaria-Secondary Power supply
Potenza massima assorbita - Max. absorbed power [kW]
Corrente massima - Full load ampere FLA [A]
Corrente di spunto - Starting Current LRA [A]
Schema elettrico - Wiring diagram
Schema frigorifero - Refrigeration diagram
Peso a vuoto - Empty weight [kg]
* EN14511-2
Contains fluorinated greenhouse gases
3.6 General instructions
BATTENTION
ŪThis manual must be stored carefully in a place that is
known by the user of the unit, managers and operators
in charge of transport, installation, use, maintenance, re-
pairs and nal dismantling.
ŪThis manual indicates the intended use of the unit and
provides instructions regarding transport, installation,
assembly, adjustment and use. It provides information
regarding maintenance, ordering spare parts, the pres-
ence of residual risks and personnel training.
RAW |HF61GJ0600D
8

ŪPlease note that the use and maintenance manual is not
intended to be a substitute for adequate user experience.
ŪThis manual represents a reminder of the main opera-
tions to be performed by operators who have received
specic training, for example by attending training cours-
es held by the manufacturer, with reference to particular
maintenance operations.
ŪThis manual is to be considered an integral part of the
unit and must be stored near the unit in a special contain-
er until the unit is eventually demolished.
ŪRequest a new copy from the manufacturer if it is lost or
deteriorated.
ŪMake sure all the users have thoroughly understood the
operating instructions together with the meaning of any
symbols on the unit.
ŪPossible accidents can be avoided by following these
technical instructions drafted in accordance with the Ma-
chinery Directive 2006/42/EC and subsequent additions.
ŪIn any case, always comply with national safety regula-
tions.
ŪDo not remove or damage the safety devices, labels and
notices, especially those imposed by law.
ŪAdhesive labels intended for safer use are applied to the
unit, therefore, it is very important to replace them if they
become illegible.
ŪThis manual reects the applicable technology at the
time the unit is sold and cannot be considered inade-
quate due to subsequent updates based on new expe-
rience.
ŪThe MANUFACTURER has the right to update the pro-
duction and manuals, without being obliged to update
previous production and manuals, except for exceptional
cases.
ŪAny updates or additions to this use and maintenance
manual are to be considered an integral part of the man-
ual and may be requested via the contact phone num-
bers listed in this manual.
ŪContact THE MANUFACTURER for further information
and to submit any proposals on how to improve the man-
ual.
ŪTHE MANUFACTURER kindly asks you to report the ad-
dress of the new owner in case of transfer of the unit,
in order to facilitate forwarding any supplements of the
manual to the new user.
RAW |UsER MANUAL AND TECHNICAL MANUAL
9

4 SAFETY INSTRUCTIONS
BATTENTION
The safety instructions below should be read carefully after
understanding the operation of the unit, and before proceed-
ing with its installation, commissioning and/or maintenance.
Electrical equipment must be installed, used, and maintained
by qualied personnel.
Personnel must have skills and knowledge relating to the
construction, installation and operation of electrical equip-
ment and must have received adequate safety training.
4.1 General cautionary notes
The operating rules contained in this manual are an integral
part of the unit supply and are valid exclusively for the RAW
units. They contain all the useful and necessary information
for safe operation and ideal, recommended use of the unit.
The declaration of conformity is attached individually to the
literature kept on the machine, usually inside the control cab-
inet. Please follow the instructions given below:
ŪRead the instructions manual carefully and consider it an
integral part of the unit;
ŪEvery unit operator and maintenance technician must
carefully read the entire manual and comply with that
stipulated therein;
Ūthe employer is obliged to ensure that the operator sat-
ises the aptitude requisites for unit operation and has
carefully read the manual;
ŪThe instructions manual must be readily available to op-
erating personnel and maintenance technicians;
ŪKeep the manual throughout the life of the unit;
ŪMake sure that any update is included in the text;
ŪHand the manual to any other user or subsequent owner
of the unit;
ŪUse the manual so that the contents are not damaged -
entirely or in part;
ŪDo not, for any reason, remove, tear or rewrite parts of
the manual;
ŪKeep the manual with care; it must be available at the
unit, stored in a special container, to protect it from mois-
ture and heat, until nal scrapping of the machine. The
location where the manual is kept must be known to
the user of the unit, to the managers, to the persons in
charge of transportation, installation, use, maintenance,
repairs, and end-of-life dismantling and scrapping. If the
manual is lost or partially damaged, so that it is no longer
possible to read all of its contents, it is advisable to re-
quest a new one from the manufacturer;
ŪAvoid hasty and incomplete preparation that lead to
improvisation and cause many accidents. Pay close at-
tention to the safety symbols shown in the table on the
previous page and to their meaning.
Before starting to work, read through and strictly observe the
following suggestions:
ŪThe operator must always have the instruction manual
readily available at any time;
ŪPlan each action carefully;
ŪBefore starting work, make sure the safety devices func-
tion correctly and you have no doubts on how they work;
otherwise, do not start-up the unit;
ŪCarefully observe the warnings relating to special haz-
ards contained in this manual;
ŪPreventive and thorough maintenance guarantees con-
stantly high operating safety for the unit. Never delay
repairs and always have them carried out solely by qual-
ied personnel; only original spare parts are to be used.
THE MANUFACTURER shall not be liable for any accident to
persons or property which may occur due to:
ŪFailure to comply with the instructions provided in this
manual regarding unit management, use and mainte-
nance;
ŪViolent actions or incorrect manoeuvres when perform-
ing maintenance on the unit;
ŪAlterations made to the unit without prior written author-
isation from the MANUFACTURER;
ŪEvents that are, in any case, unrelated to the normal and
correct use of the unit;
ŪIn any case, if the user attributes the incident to a defect
in the unit, he must prove that the damage caused was a
main and direct consequence of this “defect”.
This manual reects the state of the art at the time of unit
sale: The MANUFACTURER reserves the right to update its
products and manuals without any obligation to update ear-
lier products and manuals, except in special circumstances.
These may not be considered inadequate only because they
have been subsequently updated based on new experience.
BATTENTION
When installing or when working on the chiller unit, it is nec-
essary to strictly comply with the regulations contained in
this manual, observe the instructions provided on-board the
unit and in any case, adopt all the necessary precautions.
ŪThe presence of pressurised uids in the refrigerant cir-
cuit and of electrical components can create hazardous
situations during installation and maintenance.
ŪAny action on the unit must be carried out by qualied
and authorised personnel. In the event of a fault, do not
attempt repairs on your own and do not let unauthorised
technicians carry out repairs, or the guarantee will no
longer be valid.
ŪThe initial start-up must be carried out exclusively by
qualied personnel authorised by the marketing entity
(see annex).
ŪBefore performing any work on the unit, be sure to have
disconnected power supply.
ŪFor maintenance service or repairs always and exclu-
sively use original spare parts. THE MANUFACTURER
declines all responsibility for damages that may occur
due to non-compliance with the above.
ŪThe unit is guaranteed according to the contractual
agreements entered into upon its sale: however, failure to
comply with the rules and instructions contained in this
manual and any modication in the unit not previously
RAW |HF61GJ0600D
10

authorised, will cause an immediate loss of guarantee
validity.
ŪThis manual describes the intended use of the unit and
provides instructions for its handling, installation, as-
sembly, adjustment and use. It supplies information on
the maintenance schedule, how to order spare parts,
the presence of residual risks, and staff training. There-
fore, before handling, installing, using or carrying out any
maintenance on the unit, read the manual very carefully.
ŪPlease note that the use and maintenance manual is
not intended to be a substitute for adequate user experi-
ence. For particularly complex maintenance operations,
this manual serves as a reminder of the main tasks to
carry out for operators having received specic training,
for example, in the form of training courses delivered by
the manufacturer.
ŪPlease ensure that all users have fully understood the
directions for use and the meaning of any symbols pro-
vided on the unit.
ŪPossible accidents can be avoided by following these
technical instructions drafted in accordance with the Ma-
chinery Directive 2006/42/EC and subsequent additions.
ŪIn any case, always comply with national safety regula-
tions.
ŪDo not remove or damage guards, decals, stickers and
wording, especially any that are required by law.
ŪAdhesive plates are applied to the unit to make it safer to
use, therefore, it is very important to replace them if they
are no longer legible.
CWARNING
The electrical wiring, hydraulic and refrigeration diagrams
and the technical data shown in this manual are supplied
for this product range. For detailed information on specic
models, refer to the specic documentation attached to the
each product. Any updates or additions to this use and main-
tenance manual are to be considered an integral part of the
manual and may be requested via the contact phone num-
bers listed in this manual. Contact THE MANUFACTURER for
further information and to submit any proposals on how to
improve the manual. THE MANUFACTURER kindly asks you
to report the address of the new owner in case of transfer of
the unit, in order to facilitate forwarding any supplements of
the manual to the new user.
4.2 Safety prescriptions
4.2.1 Thoroughly know the unit
The unit must only be used by qualied personnel, who are
expected to know the arrangement and function of all con-
trols, instruments, indicators, indicator lights and various
data plates.
4.2.2 Wear protective clothing
Each operator must use personal protective equipment such
as gloves, headgear, safety goggles, safety shoes, and hear-
ing protection.
OS
OS
4.2.3 Use safety equipment
A rst aid kit and a re extinguisher must be placed near the
unit.
OS
4.2.4 Fire extinguisher and a first aid kit
Check the presence and location of the re extinguisher.
Regularly check that the re extinguishers are charged and
their operating instructions are clearly understood.
It is required to be aware of where the rst aid box is kept.
Periodically check that the rst aid kit is stocked with disin-
fectants, bandages, drugs, etc.
The personnel must know what to do in the event of a re.
Make sure that emergency help phone numbers are readily
available.
In the event of a re, use a re extinguisher in compliance
with the regulations in force. Contact the re department.
CWARNING
The owner of the building where the unit is installed must
provide the required re extinguisher.
RAW |UsER MANUAL AND TECHNICAL MANUAL
11

4.2.5 General precautions
The Machinery Directive 2006/42/EC provides the following
denitions (Annex 1.1.1.1):
DANGER ZONE: any area next to and/or inside a machine,
where the presence of an exposed person constitutes a risk
for the safety and health of said person.
EXPOSED PERSON: any person found entirely or partially
within a danger zone.
OPERATOR: the person (or persons) appointed to install, set
up, adjust, maintain, clean, repair and transport the machine.
CWARNING
ŪBefore carrying out any operation or maintenance on the
unit it is mandatory to read and follow the instructions
given in the use and maintenance manual. During the
actual work, it would be too late: any not recommended
or wrong operation could then cause serious damage to
people or property.
ŪThe employer must inform in detail all operators about
the risks of accidents and particularly about risks related
to noise, required personal protective devices and gener-
al accident prevention rules provided by laws or interna-
tional standards and national standards in the Country of
destination of the unit.
ŪAll the operators must comply with international accident
prevention regulations and those applicable in the coun-
try of use in order to prevent potential accidents. Please
be reminded that the European Union has issued some
directives concerning the safety and health of workers,
among which the directives 89/391/EEC, 89/686/EEC,
89/654/EEC, 2009/104/EC, 89/656/EEC, 2003/10/EC,
92/58/EEC and 92/57/EEC that each employer has an
obligation to observe and to enforce. In the event that the
unit is installed outside the European union, always refer
to the regulations in force in the country of installation.
ŪBefore starting any work on the unit, each operator must
be perfectly familiar with its operation and its controls,
and have read and understood all the information con-
tained in this manual.
BATTENTION
It is forbidden to tamper with or replace parts of the unit un-
less this has been expressly authorised by the MANUFAC-
TURER.
The use of accessories, tools, consumables or spare parts
other than those recommended by the MANUFACTURER
and/or specied in this manual may be a hazard to operators
and/or damage the unit.
Any alteration to the unit that is not specically authorised
by the MANUFACTURER relieves the manufacturing compa-
ny from any civil or criminal liability.
CWARNING
ŪIt is strictly forbidden to remove or tamper with any safe-
ty devices.
ŪAny installation, ordinary and extraordinary maintenance
operations must be carried out with the unit stopped and
without power supply.
ŪOnce the unit has been cleaned, the operator must check
that there are no worn or damaged parts or parts that
are not safely xed, or if this is the case, ask the main-
tenance staff to x the problem. Special attention must
be paid to the state of repair of the pressurised pipes
or other parts exposed to wear. It must also be ensured
that there are no leaks of uid, or other dangerous sub-
stances. In these cases, it is forbidden for the operator to
restart the unit before the situation has been remedied. If
any of these occurrences are detected, the operator, be-
fore leaving the unit unattended, must display a warning
sign indicating that maintenance is in progress and it is
forbidden to start the unit.
ŪThe use of ammable uids in cleaning operations is
prohibited.
ŪPeriodically check the condition of the data plates and
arrange, if necessary, for them to be restored.
ŪThe operator work place must be kept clean, tidy and free
from any objects that may limit unhindered movement.
ŪOperators should avoid operating the device from unsafe,
uncomfortable positions that may affect their balance.
ŪOperators must be aware of possible risks of entrapment
and entanglement of clothes and/or hair in moving parts;
it is recommended to wear caps over long hair.
ŪWearing chains, bracelets and rings can also be danger-
ous.
ŪThe workplace must be adequately lit for the intended
operations. Insucient or excessively bright lighting can
imply safety risks.
ŪThe instructions, accident-prevention rules and warnings
contained in this manual must be observed at all times.
4.2.6 Safety information
The units have been designed and built according to the cur-
rent state of the art and the technical rules currently applica-
ble to uid chillers and heat pumps and/or uid chillers with
free-cooling exchange intended for cooling water or water
and anti-freezing agent mixtures, for housing air condition-
ing and industrial cooling systems. Compliance with the
laws, provisions, prescriptions, orders and directives in force
for these machines has been ensured.
The materials and the equipment parts used, as well as the
production, quality assurance and control processes meet
the highest safety and reliability requirements.
By using them for the purposes specied in this user man-
ual, by operating them with the required diligence and per-
forming accurate maintenance and overhauling in a work-
manlike manner, consistent performance and functionality
and durability can be ensured.
4.2.7 Accident prevention
The MANUFACTURER will not be liable for accidents, dur-
ing the use of the unit, due to failure by the user to comply
with laws, provisions, prescriptions and regulations applica-
ble to uid chillers and heat pumps and/or uid chillers with
free-cooling exchange system.
4.2.8 Operational safety
The MANUFACTURER will not be responsible in case of mal-
functions and damage if the unit:
Ūis used for purposes other than those intended;
ŪIs not handled and maintained according to the operat-
ing rules specied in this manual;
ŪIt does not regularly and consistently receive mainte-
nance as prescribed or non-original spare parts are used;
RAW |HF61GJ0600D
12

ŪIs modied or some components are replaced without
the MANUFACTURER’s written authorisation, especially
when the effectiveness of the safety systems has been
altered or minimised on purpose;
ŪIt is used outside the permissible temperature range.
4.2.9 Tools
Use only tools prescribed by the unit manufacturer; in order
to avoid personal injury, do not use worn or damaged, low
quality or makeshift tools.
If tools not recommended or modied without authorisation
are used, the manufacturer will no longer be liable for dam-
ages caused.
4.2.10 Personnel
Ordinary maintenance prescribed in this manual must only
be performed by authorised and trained personnel. For the
maintenance or overhauling of components not specied in
this manual, contact the MANUFACTURER.
4.2.11 Keep the unit clean
Oil and grease stains, misplaced tools or broken pieces are
harmful to people as they can cause slipping or falls. Always
keep the area where the unit is installed clean and tidy.
Do not use diesel fuel, oil or solvents to clean the unit as the
rst two leave an oily lm that makes it easier for dust to
stick, while solvents (even milder ones) damage the paint
nish and cause rusting.
If a jet of water penetrates the electrical equipment the con-
tacts oxidise and the unit may malfunction. Therefore, do
not use jets of water or steam on the sensors, connectors or
any electrical part.
4.2.12 Warning plates
Before starting any maintenance operation, turn off the unit.
If other people start the unit and operate the control buttons
while maintenance operations are being performed, serious
injury or even death may result.
To avoid these dangers, before carrying out maintenance,
hang caution signs around the unit.
4.2.13 Warnings for inspections and
maintenance
Display a sign with the warning: “INSPECTION IN PRO-
GRESS” on all sides of the unit.
Check the unit carefully following the list of operations con-
tained in this manual.
INSPECTION
IN PROGRESS
4.2.14 Care and maintenance
The cause of damages and accidents is often attributable to
wrong maintenance, such as:
ŪInadequate refrigerant;
ŪPoor cleaning in the unit setting;
ŪCircuit ineciency (damage to the nned coils, pipe con-
nections, tightening of pipes, screws, etc.).
Carry out maintenance work as required: this is also critical
for your own safety.
Never postpone scheduled repairs.
Only assign skilled or authorised personnel to repair tasks.
Always observe the following safety rules, even when you
are thoroughly familiar with the operations involved:
ŪAlways keep the unit and the surrounding area clean;
ŪBefore beginning to work, check the perfect eciency of
protective devices;
ŪMake sure that no unqualied or not specially appointed
persons enter the unit operating area.
RAW |UsER MANUAL AND TECHNICAL MANUAL
13

5 DESCRIPTION OF THE PRODUCT AND TECHNICAL DATA
5.1 Main components
5.1.1 Main components of the indoor unit
1 DHW tank
2 Technical DHW circuit pres-
sure gauge
3 User tank
4 User circuit pressure gauge
5 User and technical DHW
circuit temperature and ow
sensor
6 Y lters + throttle valves in
the User and technical DHW
circuit
7 Safety valves for User and
technical DHW circuit
8 Expansion vessel for User
and technical DHW circuit
9 DHW quick preparator
10 Technical DHW tank back-up
heater (optional)
11 User tank back-up heater
(optional)
12 Modulating pump kit and
3-way mixing valve for system
side distribution (optional)
13 Liquid receiver
14 User exchanger
15 DHW side heat exchanger
1
10
9
11
3
2
12
8
7
4
5
6
13
15
14
RAW |HF61GJ0600D
14

5.1.2 Main components of the outdoor unit
1 Inverter
2 Fan
3 Finned battery
4 Liquid level indicator
5 Compressor
6 4-way cycle reversal valve
7 Liquid separator
42
5
31
7
6
5.2 Operating limits
5.2.1 Limits for the temperature of water
produced
The units of the series can work with mixtures of water and
glycol, with glycol percentages up to 40%. If this percentage
is exceeded, please contact the sales department for a spe-
cial selection of pumps.
BATTENTION
Using glycol is necessary in all cases in which the tempera-
ture of the heat transfer uid drops below 5°C, i.e. even when
the unit is switched off or only running in summer mode,
should this temperature condition occur. This will prevent
water freezing and the resulting internal damage to compo-
nents.
CWARNING
The percentage of glycol must be selected according to the
lowest expected temperature.
In the following tables, the freezing temperatures of the mix-
ture are given as a function of the glycol content and the
recommended amount of glycol - respectively.
% by weight of glycol
Freezingtemperatureofthe
mixturewithethyleneglycol
(°C)
Freezingtemperatureofthe
mixturewithpropyleneglycol
(°C)
Adjustableantifreeze
temperaturesetforthemixture
with ethylene glycol (°C)
Adjustableantifreeze
temperaturesetforthemixture
withpropyleneglycol(°C)
00055
10 -3 -3 2 2
15 -5 -5 0 0
20 -8 -7 -3 -2
25 -11 -10 -6 -5
30 -14 -13 -9 -8
40 -22 -21 -17 -16
The use of glycol will determine a change in terms of heating
capacity, water ow and pressure drop.
The corrective factors to be used according to the percent-
age of glycol are shown in the following table.
RAW |UsER MANUAL AND TECHNICAL MANUAL
15

Glycolpercentagebyweight %0% 10% 20% 30% 40%
ETHYLENE-BASED
Developed heat capacity correc-
tion factor 1,00 1,00 0,99 0,99 0,98
Water ow correction factor 1,00 1,05 1,09 1,14 1,20
Pressure drop correction factor 1,00 1,16 1,35 1,58 1,86
PROPYLENE-BASED
Developed heat capacity correc-
tion factor 1,00 1,00 0,98 0,97 0,96
Water ow correction factor 1,00 1,02 1,04 1,07 1,10
Pressure drop correction factor 1,00 1,11 1,31 1,53 1,78
BATTENTION
The freezing temperature of the mixture must be at least 5 °
C lower than the minimum temperature expected at the heat
pump outlet. Otherwise it is possible to cause the formation
of ice inside the evaporator with consequent breakage of the
same.
CWARNING
All the temperatures on the perimeter of the operating areas
can only be reached as transients and if the unit runs beyond
these limits for a prolonged time, the software on board will
implement corrective actions to restore the unit within the
operating limits.
Thermal carrying uid water or mixture of water and antifreeze (max 40%)
Maximum water side pressure 3 bars
Maximum pressure on high pressure side [ps] 45,0 bar
Minimum operating temperature +42 °C
Minimum operating temperature 5 °C
Maximum pressure on low pressure side 28 bar-r (*)
Supply voltage +/- 10% compared to plate voltage
Maximum storage temperature +42 °C
Minimum storage temperature -20 °C (limit determined by on board electronics)
(*) this value can be reached only in storage conditions and determines the refrigerant saturation pressure of 28 bar-r on the low pressure side of the circuit, a value
which in fact denes the limits.
Water flow to the user exchanger
The nominal ow rate is based on a thermal differential of 5°
C between inlet and outlet water, in relation to the cooling ca-
pacity provided at the nominal water temperatures (12/7 °C).
The maximum allowed ow rate is associated with a ther-
mal differential of 3 °C. Higher ow rate values cause too big
pressure drops.
The min ow value allowed is the one belonging to a 8°C
temperature differential through the evaporator: minor ow
values could cause evaporating temperatures too low for the
compressors, with the group stopping or in any case bad dis-
tribution and risk of heat exchange in motion not turbulent or
not completely turbulent.
RAW |HF61GJ0600D
16

5.2.2 Operating limits
» RAW operating limits during cooling for produced water and outside air temperature
1 condensation control
2 standard unit
3 condensation control / glycol mix on user side
4 condensation control / glycol mix on user side / custom version on request
5 glycol mix on user side / custom version on request
6 Glycol mix on user side
-20 -15 -10 -5 0 5 10 15 20 25 30 35 40 45 50
25
20
15
10
5
0
-5
-10
-15
1 2
3 6
4 5
Sourse side air T [°C]
User outlet water T [°C] cooling
» RAW operating limits during heating for produced water and outside air temperature
1 standard unit
2 Δ T > 7°C user side
3 evaporation control
-25 -20 -15 -10 -5 0 5 10 15 20 25 30 35 40 45
70
65
60
55
50
45
40
35
30
25
20
31
2
Sourse side air T [°C]
User outlet water T [°C] heating
RAW |UsER MANUAL AND TECHNICAL MANUAL
17

5.3 Characteristic curves of
the circulation pumps
5.3.1 Circulation pumps on user and DHW
side
The circulation pumps of the User and DHW circuit located
in the primary circuit between the heat pump and the tanks
(always supplied inside the unit) have already been accurate-
ly sized, therefore, it is not necessary to check them against
the head-ow characteristic curve.
5.3.2 Circulation pump for system side
distribution (optional)
Working head of the pump mounted upstream of the Us-
er tank integrated in the indoor unit. Pressure drops of the
3-way mixing valve mounted upstream of the circulator have
been taken account in calculating the working heads.
The following circulator and 3-way valve are available inside
the unit if selected at the time of ordering in the “User side
hydraulic conguration” section. It is also possible to select
whether the kit should be controlled by the heat pump inter-
nal software or if dedicated terminals should be provided for
control from an external regulator.
0
20
40
60
80
1
00
1
20
140
1234 5 60
Available
pressure head
[kPa]
Water flow
LP
HP
[m
3
/h]
5.4 Calibration of control
devices
5.4.1 General description
All the control devices are set and tested in the factory be-
fore the unit is dispatched. However, after the unit has been
in service for a reasonable period of time you can perform a
check on the operating and safety devices. The settings are
shown in Table 5.4Setting of safety-control devicesp.18.
ADANGER
All service operations on the control equipment must be car-
ried out EXCLUSIVELY BY QUALIFIED PERSONNEL: incor-
rect calibration valuescan cause serious personal injuries
and damage the unit.
Many of the operating parameters and system settings are
congured by means of the microprocessor control and are
protected by passwords.
» SETTING OF SAFETY-CONTROL DEVICES
CONTROL DEVICE ACTIVATION DIFFERENTIAL REACTIVATION
Antifreeze thermostat °C +4 1Automatic
Maximum safety pressure switch bar 45 -10 Manual
Modulating condensation control bar 18 10 -
Minimum time between two starts on the same compressor s450 - -
Flow switch alarm delay s15 (start-up) 5 (running) -
Low pressure alarm delay s 0 -
5.4.2 Maximum pressure switch
The high pressure switch is of the manual reset type and
classiable as category IV under 97/23 EC. It directly stops
the compressor when the discharge pressure exceeds the
set value.
BATTENTION
Any kind of block or alarm must be promptly reported to the
After Sales Service!
RAW |HF61GJ0600D
18

CWARNING
The high pressure switch must be manually reset; this is
possible only when the pressure falls below the set differen-
tial (see Table 5.4Setting of safety-control devicesp.18).
5.4.3 Anti-freeze thermostat function
The anti-freeze sensor situated at the evaporator outlet
detects the presence of excessively low temperatures and
stops the unit.
Together with the ow switch and low pressure switch, this
device protects the evaporator from the risk of freezing as a
result of faults in the water circuit.
This device is a function included in the microprocessor con-
trol.
BATTENTION
If there are any alarms relating to the intervention of the pro-
tections described, the unit must request the intervention of
the Authorised Technical Service Centre, otherwise the war-
ranty will be considered null and void.
5.5 Liquid refrigerant lines and
refrigerant charge
All copper pipes are made to our specications for us to be
able to fully control their construction process and inherently
improve the quality of our products. Each pipe complies with
the requirements of directive 97/23PED and is inspected in
accordance with the FEM calculation code at the point most
stressed by 180° bending and at the maximum pressure al-
lowed by the safety devices - taking into account adequate
safety coecients.
As regards the external refrigeration lines, the indications
given in this paragraph and the diameter gures in the fol-
lowing table must be complied with. Make sure there are no
leaks and ensure pressure tightness of the refrigeration lines
with a leak test (see para. 11.4Tightness testp.46).
BATTENTION
The unit RAW is supplied with a pre-charge of refrigerant and
oil.
Check the table to learn about the basic refrigerant charge
and the line length requirements met by this charge; beyond
this value, provide by the agreed rst start-up date the refrig-
erant needed and, if necessary, oil as well, as shown in the
following tables.
The addition of the refrigerant and oil required for correct
operation of the unit will be carried out by the Authorised
Service Centre during the start-up phase.
To complete the operation, the line must have been under
negative pressure conditions for 6-8 hours up to maximum
24 hours before starting the unit.
If it is not possible to create vacuum shortly before start-up,
carry out the procedure anyway as indicated and then let the
pre-charge contained in the unit ow into the line.
CWARNING
Document the procedure by providing information to the
Service Centre on the pressures reached and the pressures’
hold time.
The following table provides indications on the pipes, the refrigerant and oil charges, depending on size changes:
» VERSION H: Multi functional heat pump
Refrigerant R410A-R454B
Oil type EmkarateRL-32-3MAF
Size RAW 006H 009H 012H 015H 017H
Precharge [kg] 2,2 2,2 2,5 2,8 2,8
Refrigerant charge limit [kg] 4,9 4,9 4,9 7,8 7,8
Basic oil charge [kg] 0,74 0,74 0,74 1,18 1,18
Line length requirements met by the basic charge [m] 11111
Linelength0-25m
Addition of refrigerant per metre of line beyond the length require-
ment met by the basic charge [g] 90 90 120 130 130
Addition of oil due to exceeding the refrigerant charge limit (for
each additional kg of refrigerant) [g/kg] 50 50 50 50 50
Addition of oil for each single siphon [g] 20 20 34 34 34
Refrigerantlinediameters
Suction lines (gas) [inch] 1/2” 1/2” 5/8” 3/4” 3/4”
Liquid line [inch] 3/8” 3/8” 1/2” 1/2” 1/2”
RAW |UsER MANUAL AND TECHNICAL MANUAL
19

» VERSION M: Total recovery multipurpose heat pump (ATTENTION: the unit includes three refrigerant lines)
Refrigerant R410A-R454B
Oil type EmkarateRL-32-3MAF
Size RAW 006M 009M 012M 015M 017M
Precharge [kg] 2,2 2,2 2,5 2,8 2,8
Refrigerant charge limit [kg] 4,9 4,9 4,9 7,8 7,8
Basic oil charge [kg] 0,74 0,74 0,74 1,18 1,18
Line length requirements met by the basic charge [m] 11111
Linelength0-25m
Addition of refrigerant per metre of line beyond the length require-
ment met by the basic charge [g] 100 100 150 160 160
Addition of oil due to exceeding the refrigerant charge limit (for
each additional kg of refrigerant) [g/kg] 50 50 50 50 50
Addition of oil for each single siphon [g] 20 20 34 34 34
Refrigerantlinediameters
Suction line 1 (gas) [inch] 1/2” 1/2” 5/8” 3/4” 3/4”
Suction line 2 (gas) [inch] 1/2” 1/2” 5/8” 3/4” 3/4”
Liquid line [inch] 3/8” 3/8” 1/2” 1/2” 1/2”
BATTENTION
Building refrigeration lines that do not comply with the in-
structions provided in this paragraph, or reaching a height
difference greater than 10 metres without the explicit author-
isation of Eneren, will result in the immediate termination of
the guarantee validity. It is also necessary to provide infor-
mation on the completion of the procedure to create vac-
uum conditions as indicated in the following paragraph,
otherwise, the unit cannot be started up and the resulting
costs will be charged as reported in the rst start-up request
document.
» Installation of the gas line with the remote unit located higher than the indoor unit
1 Indoor unit
2 Outdoor unit
3 Siphons h = 200 mm Radius = 2D every 5 m of height
4 Siphons to recover some height throughout long horizontal lines
5 Lines gradient between 1° and 3° to facilitate oil return
5000 5000
1° ÷ 3°
RAW |HF61GJ0600D
20
Table of contents
Popular Control Unit manuals by other brands
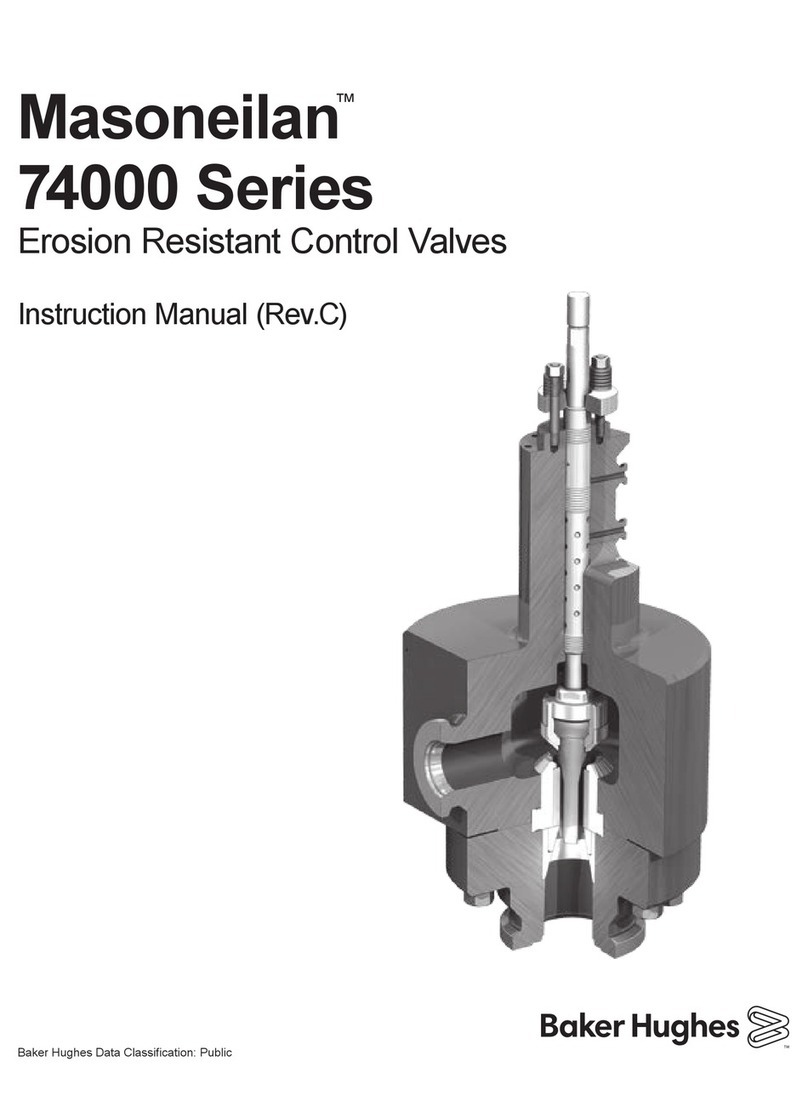
Baker Hughes
Baker Hughes Masoneilan 74000 Series instruction manual
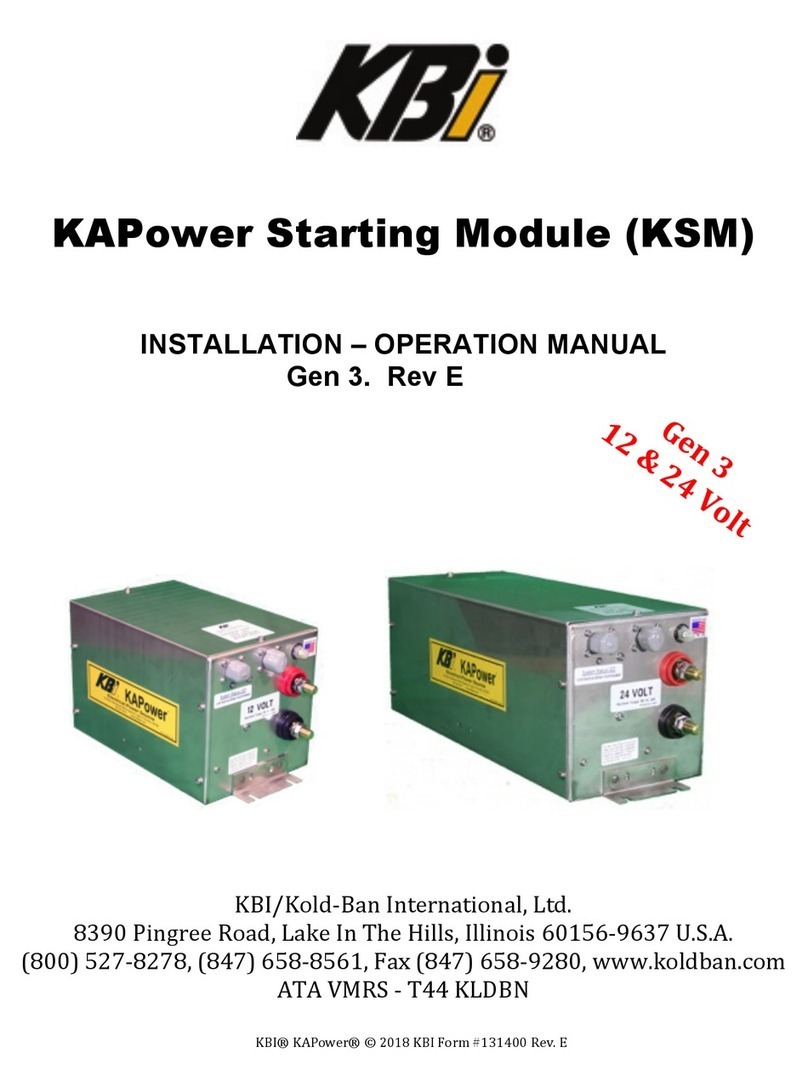
KBi
KBi KAPower Starting Module Installation & operation manual
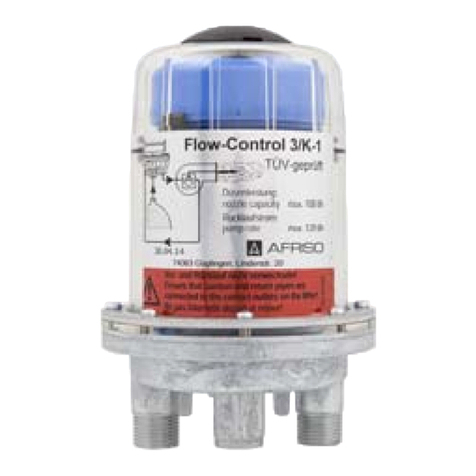
AFRISO
AFRISO Flow-Control Series operating instructions

schmersal
schmersal SRB 302X3 operating instructions
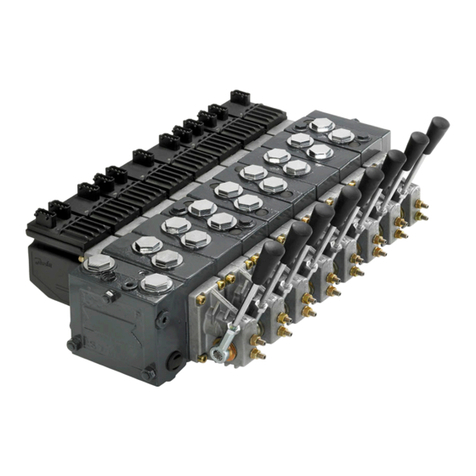
Danfoss
Danfoss PVG 32 technical information
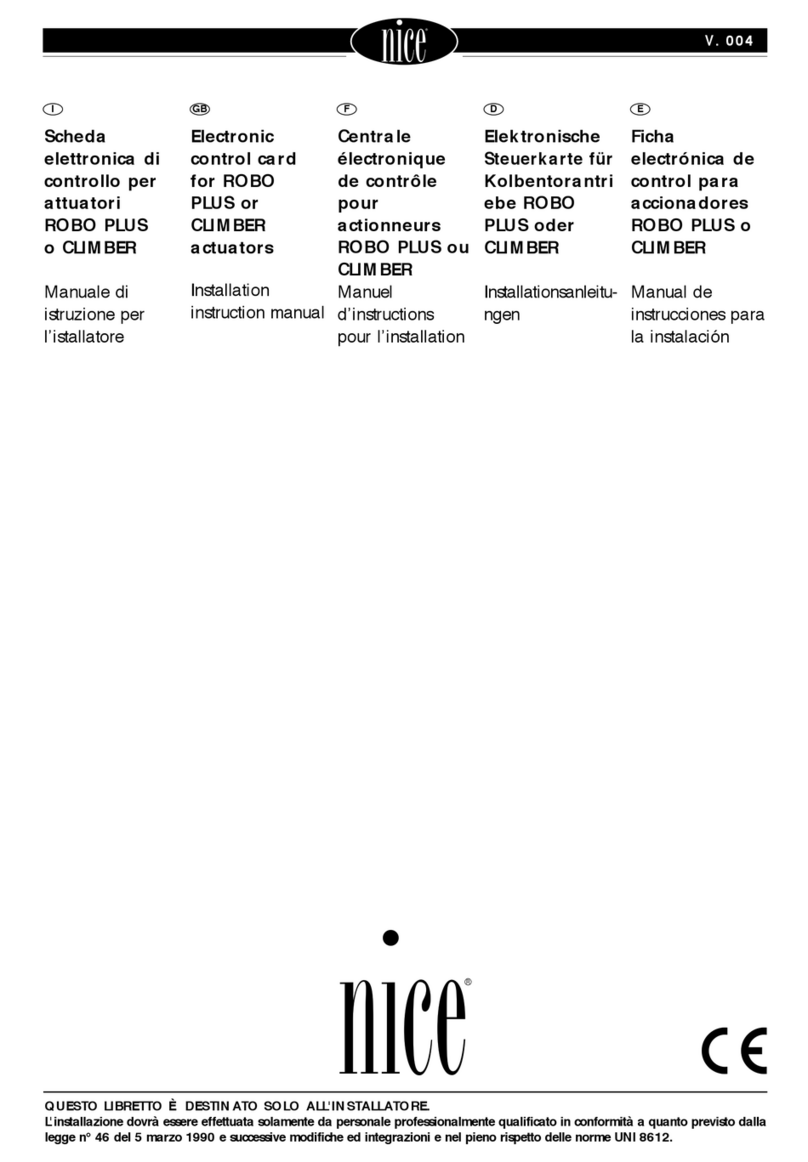
Nice
Nice ROBO PLUS Installation instructions manual
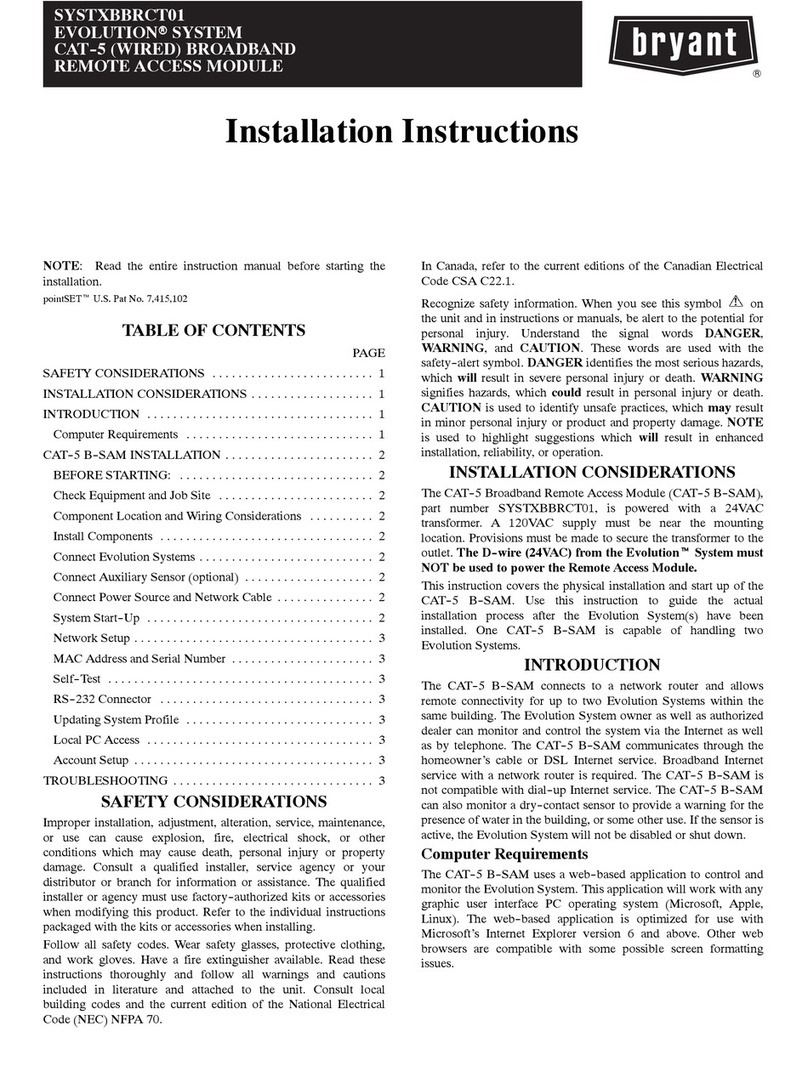
Bryant
Bryant EVOLUTION CAT-B-SAM installation instructions
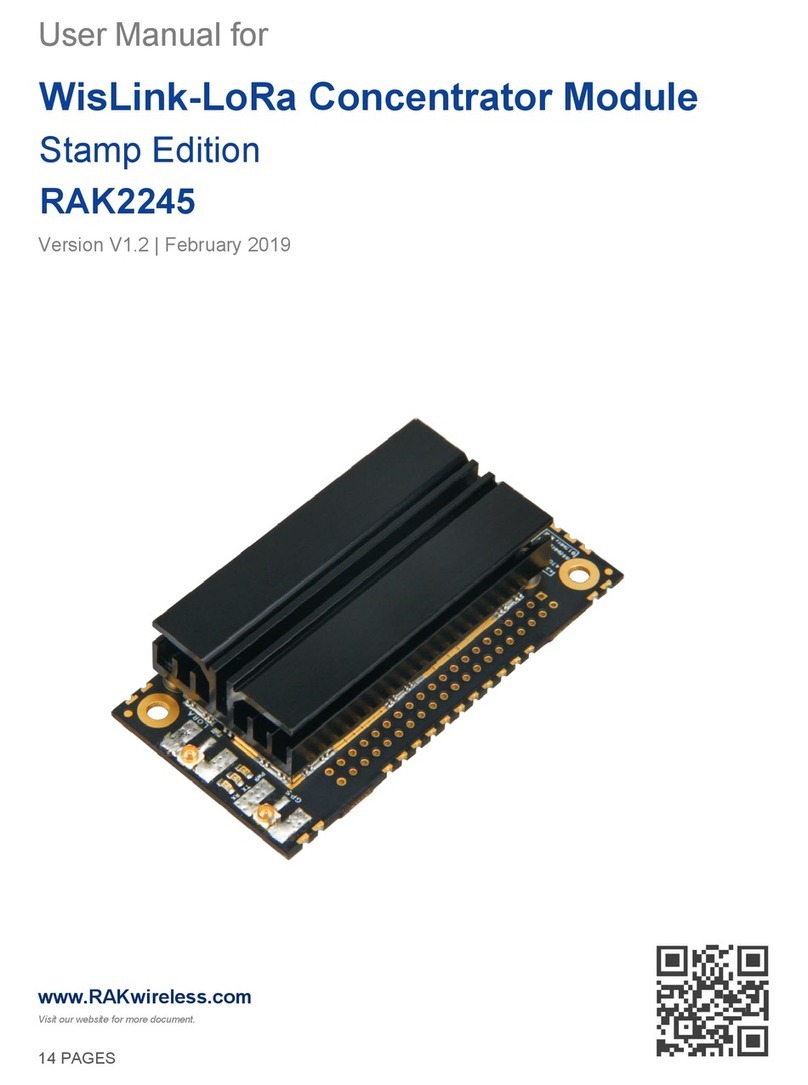
RAKwireless
RAKwireless WisLink-LoRa RAK2245 Pi HAT user manual
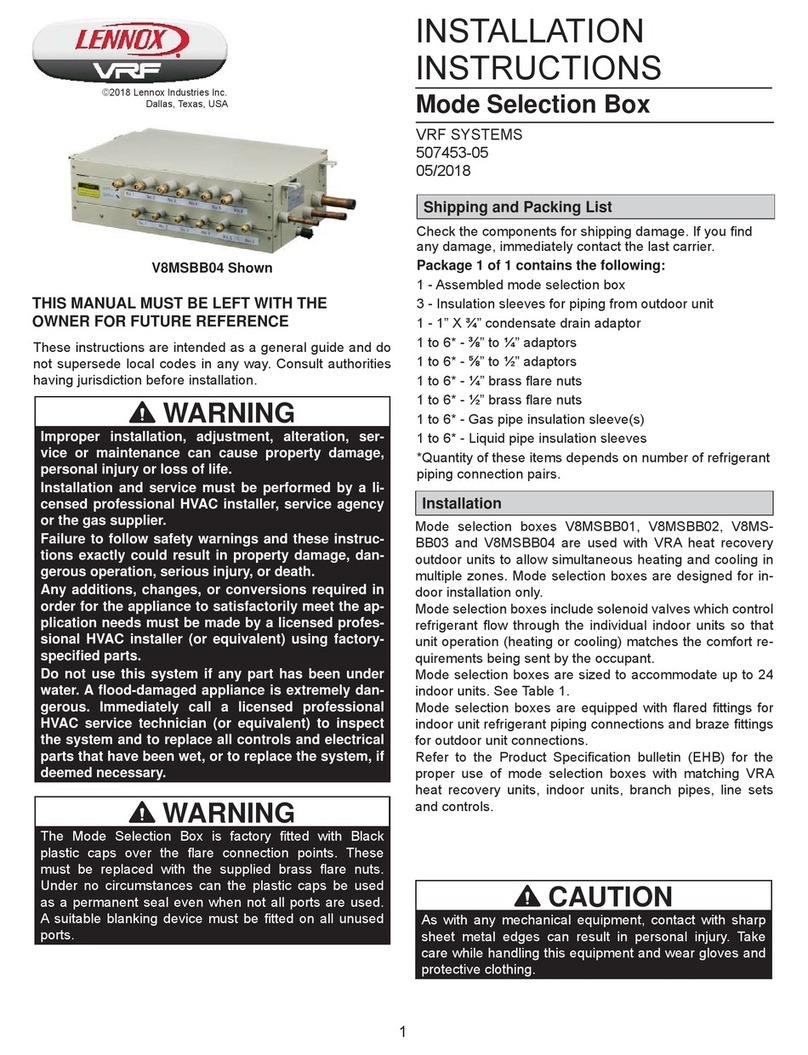
Lennox
Lennox V8MSBB01 installation instructions

AES Corporation
AES Corporation 7762 installation manual

VAT
VAT 650 Series Installation, operating, & maintenance instructions
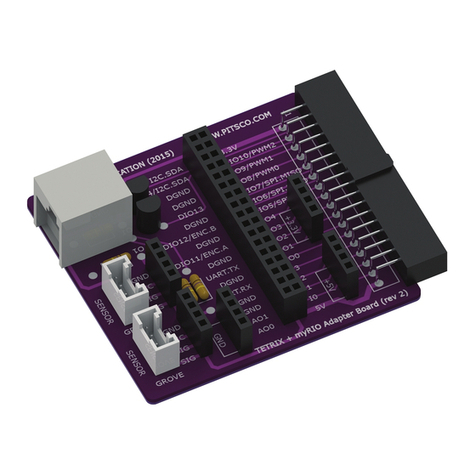
pitsco
pitsco Tetrix Max Programming guide