Entron EN1000 series User manual

ENTRON Controls, LLC. • 700120S • Page 1
INSTRUCTION MANUAL
700120S
EN1000/EN1001
SERIES CONTROLS
MICROPROCESSOR BASED
Weld Sequence Controls
With
Solid State Thyristor Contactors
INCLUDES:
Appendix E – EN1000/EN1001 Bench Controls
Appendix F – EN1003 Controls
Wiring Diagrams
Cabinet StyleEN1000EN1001
S421180421270
T/D/LS/LF/FP421210421269
E421212421268
D/T421387421377
C421498421499
IMU421424421423
Intended for use with firmware versions 619016-002Z and higher
Distributed by:
www.resistanceweldsupplies.com
888-654-WELD (9353)
PRODUCTION ENGINEERING
1344 Woodman Dri
Dayton, Ohio 45432

Page 2 • 700120S • ENTRON Controls, LLC.
THIS PAGE IS
INTENTIONALLY
BLANK

ENTRON Controls, LLC. • 700120S • Page 3
ENTRON Controls, LLC.
MICROPROCESSOR BASED WELDING CONTROLS
INSTALLATION AND OPERATION MANUAL FOR:
Model Series EN1000/EN1001
NEMA Type: ALL
ENTRON Controls, LLC., reserves the right to alter the contents of this
manual without previous notice.
ENTRON Controls, LLC.
Greer, South Carolina 29650
CAUTION
READ THIS MANUAL COMPLETELY BEFORE ATTEMPTING
TO INSTALL OR OPERATE THIS CONTROL

Page 4 • 700120S • ENTRON Controls, LLC.
TABLE OF CONTENTS
1.0 GENERAL DESCRIPTION ................................................................................. 9
1.1 STANDARD FEATURES ............................................................................................. 10
1.2 CONTROL PANEL LAYOUT ........................................................................................ 11
2.0 PROGRAMMABLE FUNCTIONS ..................................................................... 12
2.1 CONTROL FUNCTIONS ............................................................................................. 12
2.2 SEQUENCE TIMED PARAMETERS ........................................................................... 14
2.3 OTHER PROGRAMMABLE SEQUENCE PARAMETERS.......................................... 15
3.0 INSTALLATION .................................................................................................................... 17
3.1 INSTALLATION AND MOUNTING DIAGRAMS – “S” CABINET ................................. 17
3.2 INSTALLATION AND MOUNTING DIAGRAMS – “E” CABINET ................................. 18
3.3 INSTALLATION AND MOUNTING DIAGRAMS – “T/D” AND “L” CABINET ................ 19
3.4 INSTALLATION AND MOUNTING DIAGRAMS – “C” CABINET ................................. 20
3.5 INSTALLATION AND MOUNTING DIAGRAMS – FLAT PLATE AND IMU .................. 21
3.6 WELDING TRANSFORMER PRIMARY WIRING ....................................................... 23
3.7 EXTERNAL SCR CONTACTOR WIRING ................................................................... 23
3.8 CONTACTOR SPECIFICATIONS ............................................................................... 25
3.9 COOLING REQUIREMENTS FOR CONTACTORS .................................................... 27
4.0 GENERAL OPERATING REQUIREMENTS ............................................................... 28
4.1 OPERATING VOLTAGE .............................................................................................. 28
4.2 FUSING AND SAFE OPERATION .............................................................................. 30
4.3 TERMINAL STRIP DIAGRAMS AND CONNECTIONS ............................................... 31
4.3.1 TERMINAL STRIP TS1/PCB2 ...................................................................................... 31
4.3.2 TERMINAL STRIP CONNECTIONS .................................................................... 33
4.3.3 TERMINAL STRIP TS1 INSIDE THE CABINET .................................................... 35
4.4 INITIATION .................................................................................................................. 36
4.4.1 SINGLE STAGE PILOT INITIATION .................................................................... 36
4.4.2 TWO STAGE PILOT INITIATION ........................................................................ 36
4.5 OTHER TERMINAL STRIP INPUTS ........................................................................... 36
4.6 NON-VOLATILE MEMORY ERROR ........................................................................... 38
4.7 ISOLATION CIRCUITRY DESCRIPTION .................................................................... 40
5.0 INTRODUCTION TO DATA PROGRAMMING ........................................................... 42
5.1 GENERAL PROGRAMMING....................................................................................... 42
5.2 PROGRAM LOCKOUT OPTIONS .............................................................................. 43
5.2.1 PROGRAM LOCKOUT KEY SWITCH OPTION .................................................... 43
5.2.2 USING PROGRAM LOCKOUT KEY SWITCH FOR ERROR CLEARING ................ 43
5.3 SEQUENCE (SCHEDULE) PARAMETERS PROGRAMMING ................................... 44
5.3.1 USING PROGRAMMING SHORTCUTS ...................................................................... 45
5.4 EXTENDED FUNCTIONS ........................................................................................... 46
5.4.1 IDENTIFICATION NUMBER ......................................................................................... 47
5.4.2 SEAM WELDING MODE ..............................................................................................47
5.4.3 SCHEDULE SELECT....................................................................................................50
5.4.4 AUTOMATIC VOLTAGE COMPENSATION AND MONITORING ................................ 57
5.4.5 CLEAR ALL FUNCTIONS ............................................................................................. 59
5.4.6 BACK-STEP / TEMPERATURE LIMIT SWITCH .......................................................... 60
5.4.7 PROCESS OUTPUTS ..................................................................................................61
5.4.8 BEAT OPERATION INITIATION MODES ..................................................................... 66
5.4.9 87° DELAY .................................................................................................................... 68
5.4.10 MANUAL POWER FACTOR PROGRAMMING ............................................................ 69
5.4.11 POWER FACTOR MEASURING .................................................................................. 69
5.4.12 SQUEEZE DELAY ........................................................................................................70
5.4.13 BLOCKING DELAY .......................................................................................................70
5.4.14 TURNS RATIO ..............................................................................................................70
5.4.15 CONSTANT CURRENT MODES .................................................................................. 71
5.4.16 RANGE .......................................................................................................................... 72
5.4.17 CURRENT OFFSET ..................................................................................................... 73
5.4.18 PIN LOCKOUT MODE ..................................................................................................76

ENTRON Controls, LLC. • 700120S • Page 5
TABLE OF CONTENTS (cont.)
6.0 GENERAL OPERATING INSTRUCTIONS....................................................... 77
6.1 WELD SEQUENCE EXAMPLE ................................................................................... 77
6.2 CYCLE MODES .......................................................................................................... 78
6.2.1 NON-REPEAT ................................................................................................... 78
6.2.2 REPEAT ........................................................................................................... 79
6.2.3 CHAINED ......................................................................................................... 79
6.2.4 SUCCESSIVE ................................................................................................... 81
6.2.5 CONDITIONAL SUCCESSIVE ............................................................................ 82
6.2.6 WAIT-HERE ...................................................................................................... 83
6.3 SLOPE MODES .......................................................................................................... 84
6.3.1 NO SLOPE .................................................................................................................... 85
6.3.2 UPSLOPE ..................................................................................................................... 85
6.3.3 DOWNSLOPE ............................................................................................................... 85
6.4 VALVE MODES ........................................................................................................... 86
7.0 STEPPER ON EN1000/EN1001 SERIES CONTROLS ........................................... 87
7.1 SCHEDULE MAP ........................................................................................................ 88
7.2 STEPPER PROGRAMMING ....................................................................................... 89
7.2.1 EXTENDED FUNCTION PROGRAMMING ................................................................. 89
7.2.2 WELD SEQUENCE PROGRAMMING ......................................................................... 89
7.2.3 STEP COUNTS PROGRAMMING ............................................................................... 89
7.2.4 LAST STEP AND LAST COUNT PROGRAMMING ..................................................... 90
7.2.5 QUICK SETUP INSTRUCTIONS FOR STEPPER ....................................................... 91
7.3 SEQUENCE (SCHEDULE) INITIATION IN STEPPER MODE .................................... 92
7.3.1 SCHEDULE SELECT OPTIONS FOR STEPPER MODE S.t.S.t.
S.t.S.t.
S.t.=0101
0101
01 ................................ 92
7.3.2 SCHEDULE SELECT OPTIONS FOR STEPPER MODE S.t.S.t.
S.t.S.t.
S.t.=0202
0202
02 ............................... 92
7.4 STEPPER OPERATION .............................................................................................. 93
7.4.1 OPERATION ALGORITHM FOR STEPPER MODE S.t.S.t.
S.t.S.t.
S.t.=0101
0101
01 ........................................ 93
7.4.2 STEPPER OPERATION FOR STEPPER MODE S.t.S.t.
S.t.S.t.
S.t.=0202
0202
02 ............................................ 94
7.5 STEPPER RESET ....................................................................................................... 95
7.5.1 MANUAL STEPPER RESET ........................................................................................ 95
7.5.2 AUTOMATIC STEPPER RESET .................................................................................. 95
7.5.3 STEPPER RESET USING EXTERNAL SWITCH INPUT ............................................ 96
7.6 USING STEPPER AS A COUNTER ............................................................................ 96
7.7 DISPLAYING STEPPER COUNT DURING OPERATION ........................................... 96
7.8 END OF STEPPER ..................................................................................................... 96
8.0 CONSTANT CURRENT OPERATION (EN1001 only) ...................................... 97
8.1 HARDWARE SETUP ................................................................................................... 97
8.2 SOFTWARE PARAMETERS SETUP .......................................................................... 98
8.2.1 SECONDARY PRESET-RANGE COMPENSATION OR MONITORING MODE
WITH ROGOWSKI COIL .............................................................................................. 99
8.2.2 PRIMARY PRESET-RANGE COMPENSATION OR MONITORING MODE
WITH CURRENT TRANSFORMER ............................................................................. 99
8.2.3 SECONDARY AUTO-RANGE COMPENSATION OR MONITORING MODE
WITH ROGOWSKI COIL ........................................................................................... 100
8.2.4 PRIMARY AUTO-RANGE COMPENSATION OR MONITORING MODE
WITH CURRENT TRANSFORMER .......................................................................... 100
8.3 DISPLAYING CURRENT AFTER WELD SEQUENCE .............................................. 101
8.3.1 USING CONSTANT CURRENT PROCESS OUTPUTS ........................................... 102
8.3.2 SETTING LIMIT WINDOW FOR CONSTANT CURRENT ........................................ 103
8.4 LEARNING-TYPE SETUP PROCESS FOR AUTO-RANGE WORKING MODE ...... 103
8.4.1 SETTING UP CURRENT REGULATOR ................................................................... 104
8.4.2 SETTING UP CURRENT REGULATOR – BOARDS W/PROMS
BEFORE 619016-001R ............................................................................................... 105
9.0 APPLICATIONS AND PROGRAMMING EXAMPLES .................................... 106
9.1 SPOT MODE EXAMPLES ......................................................................................... 106
9.1.1 SPOT WITH REPEAT MODE .................................................................................... 106
9.1.2 PULSATION WITH SUCCESSIVE MODE ................................................................ 106
9.1.3 QUENCH-TEMPER WITH CHAINED MODE............................................................ 107

Page 6 • 700120S • ENTRON Controls, LLC.
TABLE OF CONTENTS (cont.)
9.1.4 UPSLOPE AND DOWNSLOPE WITH CHAINED MODE ......................................... 107
9.1.5 BUTT WELD WITH CHAINED MODE ....................................................................... 108
9.1.6 FORGE DELAY WITH CHAINED MODE .................................................................. 108
9.2 SEAM MODE EXAMPLES ........................................................................................ 110
9.2.1 CONTINUOUS SEAM MODE ..................................................................................... 110
9.2.2 INTERMITTENT SEAM MODE .................................................................................. 110
9.2.3 WELD CURRENT DELAY .......................................................................................... 110
9.2.4 SEAM MODE S.E.S.E.
S.E.S.E.
S.E.=0606
0606
06 .................................................................................................. 111
9.3 BRAZING APPLICATION .......................................................................................... 112
9.3.1 AUTOMATIC BRAZING MODE .................................................................................. 112
9.3.2 MANUAL BRAZING MODE ........................................................................................ 112
9.4 SQUEEZE DELAY APPLICATION ............................................................................. 113
9.4.1 SQUEEZE DELAY OPERATION ................................................................................ 113
9.4.2 SQUEEZE DELAY PROGRAMMING ......................................................................... 113
9.5 RETRACTION APPLICATION ................................................................................... 114
9.5.1 MOMENTARY CLOSURE ........................................................................................... 114
9.5.2 MAINTAINED CLOSURE ............................................................................................115
9.5.3 AIR OVER OIL RETRACTION.................................................................................... 117
9.6 MULTIPLE SCHEDULE OPERATION ....................................................................... 122
9.7 PROCESS OUTPUT 2626
2626
26 ............................................................................................. 123
9.7.1 VALVE 1 – WELDING HEAD SOLENOID OUTPUT FOR ELECTRODES ............... 123
9.7.2 VALVE 2 – MAGNETIC ISOLATION CONTACTOR OUTPUT CR1 ......................... 124
9.7.3 VALVE 3 – ALARM OUTPUT CR2 ............................................................................ 124
9.8 HALF CYCLE CURRENT MONITORING.................................................................. 125
9.8.1 ENABLE HALF CYCLE WELDING ............................................................................ 125
9.8.2 PROGRAM A HALF CYCLE WELD ........................................................................... 125
9.8.3 ENABLE CURRENT MONITORING .......................................................................... 125
10.0 OPTIONS FOR EN1000 AND EN1001 SERIES CONTROLS ....................... 126
10.1 MM2 MEMORY MODULE ......................................................................................... 126
10.2 INTEGRATED PRESSURE SENSE AND CONTROL SYSTEM ............................... 126
10.3 24 VDC VALVE OUTPUTS ........................................................................................ 127
10.4 CURRENT SENSORS............................................................................................... 127
10.5 PROGRAM LOCKOUT KEY SWITCH ...................................................................... 127
10.6 1 OF 7 VALVE EXTENSION BOARD ........................................................................ 127
10.7 SCHEDULE SELECT S49 OPTION .......................................................................... 127
10.8 RS485 OPTIONS ...................................................................................................... 127
10.9 ENLINK 1000/1001 SOFTWARE .............................................................................. 128
10.10 REMOTE TERMINAL RT4jr. ...................................................................................... 128
10.11 ISOLATED ADAPTERS – S485 AND U485 .............................................................. 128
10.12 RS232 OPTIONS ...................................................................................................... 128
10.13 HALF-CYCLE OPTION ............................................................................................. 128
11.0 ERROR CODES AND TROUBLESHOOTING ............................................... 129
11.1 ERROR CODES ........................................................................................................ 129
11.2 TROUBLESHOOTING .............................................................................................. 131
11.3 TROUBLESHOOTING GUIDE .................................................................................. 134
11.4 WELD CONTROL WITH OPTIONS BLOCK DIAGRAM ........................................... 136
12.0 WARRANTY AND SERVICE .......................................................................... 137
APPENDICES
APPENDIX A ERROR CODES ........................................................................................... 138
APPENDIX B PROGRAMMING AND SETUP .................................................................... 139
APPENDIX C S49 SCHEDULE SELECT OPTION INSTALLATION ................................... 146
APPENDIX D WELDSAFE 5000 ......................................................................................... 149
APPENDIX E EN1000/EN1001 BENCH CONTROLS ........................................................ 154
APPENDIX F EN1003 THREE PHASE DC CONTROLS ................................................... 158
APPENDIX G EN1000 SERIES RESPONSE TIMES .......................................................... 161
APPENDIX H IMU MOUNTING OPTIONS ......................................................................... 162
APPENDIX I PROGRAMMING WORKSHEETS ............................................................... 164

ENTRON Controls, LLC. • 700120S • Page 7
FIGURES
FIGURE 1-1 EN1000/EN1001 SYSTEM......................................................................................... 9
FIGURE 1-2 CONTROL PANEL LAYOUT .................................................................................... 11
FIGURE 3-1 INSTALLATION AND MOUNTING DIAGRAMS FOR STYLE “S” CABINET ............ 17
FIGURE 3-2 INSTALLATION OF STYLE “E” CABINET – 300A & 1200A CONTACTOR ............. 18
FIGURE 3-3 INSTALLATION OF STYLE “E” CABINET – 1800/2200/3200A CONTACTOR ........ 18
FIGURE 3-4 MECHANICAL MOUNTING DIAGRAM FOR “E” CABINET .................................... 18
FIGURE 3-5 INSTALLATION OF STYLE “T/D” & “L” CABINETS – 1200A CONTACTOR ........... 19
FIGURE 3-6 INSTALLATION OF STYLE “T/D” & “L” CABINETS –
1800/2200/3200A CONTACTOR .............................................................................. 19
FIGURE 3-7 MECHANICAL MOUNTING DIAGRAM FOR “T/D” AND “L” CABINETS ................. 19
FIGURE 3-8 INSTALLATION DIAGRAM FOR STYLE “C” CABINET ........................................... 20
FIGURE 3-9 MOUNTING DIAGRAMS FOR STYLE “C” CABINET .............................................. 20
FIGURE 3-10 INSTALLATION AND MOUNTING DIAGRAMS FOR 11x11 FLAT PLATE ............... 21
FIGURE 3-11 INSTALLATION AND MOUNTING DIAGRAMS FOR 21x21 FLAT PLATE .............. 21
FIGURE 3-12 INSTALLATION AND MOUNTING DIAGRAMS FOR 13x19 FLAT PLATE .............. 22
FIGURE 3-13 INSTALLATION AND MOUNTING DIAGRAMS FOR IMU ....................................... 22
FIGURE 3-14 EXTERNAL SCR CONTACTOR CONNECTIONS ................................................... 24
FIGURE 3-15 DEMAND CURRENT VS. PERCENT DUTY CYCLE ............................................... 26
FIGURE 4-1 VOLTAGE OPERATION JUMPERS SETTINGS ...................................................... 28
FIGURE 4-2 VALVE TRANSFORMER JUMPERS SETTINGS .................................................... 29
FIGURE 4-3 WARNING, DANGER AND CAUTION LABELS ....................................................... 30
FIGURE 4-4 TERMINAL STRIP/FIRING BOARD ......................................................................... 31
FIGURE 4-5 COMPONENT PLACEMENT ON NEW TERMINAL STRIP/FIRING BOARD .......... 32
FIGURE 4-6 TERMINAL STRIP FOR “T/D” CABINET ................................................................. 35
FIGURE 4-7 INITIATION INPUTS ON TERMINAL STRIP TS1 .................................................... 36
FIGURE 4-8 OTHER INPUTS ON TERMINAL STRIP TS1 .......................................................... 37
FIGURE 4-9 FLASHING 1414
1414
14 OR 3232
3232
32 ERRORS ................................................................................. 38
FIGURE 4-10 WRONG ROUTING OF LOW AND HIGH VOLTAGE WIRES .................................. 39
FIGURE 4-11 BETTER ROUTING OF LOW AND HIGH VOLTAGE WIRES .................................. 39
FIGURE 4-12 RECOMMENDED ROUTING OF LOW AND HIGH VOLTAGE WIRES ................... 39
FIGURE 4-13 ISOLATION CIRCUIT BLOCK DIAGRAM ................................................................ 40
FIGURE 5-1 FOUR-DIGIT DATA DISPLAY ................................................................................... 42
FIGURE 5-2 COPY SCHEDULE UP BY 1 .................................................................................... 45
FIGURE 5-3 COPY SCHEDULE UP BY 10 .................................................................................. 45
FIGURE 5-4 CLEAR SCHEDULE DATA ....................................................................................... 45
FIGURE 5-5 SELECTING FUNCTIONS ....................................................................................... 46
FIGURE 5-6 EXTENDED FUNCTIONS MODE ............................................................................ 46
FIGURE 5-7 VIEWING EXTENDED FUNCTIONS ....................................................................... 46
FIGURE 5-8 DUAL TWO-STAGE FOOT SWITCH INITIATION .................................................... 52
FIGURE 5-9 MULTIPLE TWO-STAGE FOOT SWITCH INITIATION ............................................ 52
FIGURE 5-12 SWITCH CLOSURE CONNECTIONS ..................................................................... 54
FIGURE 5-13 MULTIPLE PILOT SWITCH CONNECTIONS .......................................................... 55
FIGURE 5-14 CLEAR SCHEDULE DATA ....................................................................................... 59
FIGURE 5-15 BACK-STEP SEQUENCE EXAMPLE ...................................................................... 60
FIGURE 5-16 USING LIGHT CURTAIN .......................................................................................... 67
FIGURE 6-1 NON-REPEAT SEQUENCE ..................................................................................... 78
FIGURE 6-2 REPEAT SEQUENCE .............................................................................................. 79
FIGURE 6-3 CHAINED SEQUENCE ............................................................................................ 80
FIGURE 7-1 STEPPER ENABLING ............................................................................................. 87
FIGURE 7-2 SELECT WELD/HEAT .............................................................................................. 89
FIGURE 7-3 PROGRAM WELD COUNT ...................................................................................... 89
FIGURE 7-4 PROGRAM LAST STEP ........................................................................................... 90
FIGURE 7-5 PROGRAM LAST COUNT ....................................................................................... 90
FIGURE 7-6 ALGORITHM ............................................................................................................ 93
TABLE OF CONTENTS (cont.)

Page 8 • 700120S • ENTRON Controls, LLC.
FIGURE 8-1 JUMPER SETTING: PRIMARY CURRENT TRANSFORMER ................................ 98
FIGURE 8-2 JUMPER SETTING: SECONDARY ROGOWSKI COIL ........................................... 98
FIGURE 8-3 JUMPER SETTINGS .............................................................................................. 104
FIGURE 9-1 SPOT WITH REPEAT MODE ................................................................................. 106
FIGURE 9-2 PULSATION WITH SUCCESSIVE MODE ............................................................. 106
FIGURE 9-3 QUENCH-TEMPER WITH CHAINED MODE ........................................................ 107
FIGURE 9-4 UPSLOPE AND DOWNSLOPE WITH CHAINED MODE ...................................... 107
FIGURE 9-5 BUTT WELD WITH CHAINED MODE ................................................................... 108
FIGURE 9-6 FORGE DELAY WITH CHAINED MODE ............................................................... 109
FIGURE 9-7 CONTINUOUS SEAM MODE ................................................................................ 110
FIGURE 9-8 INTERMITTENT SEAM MODE .............................................................................. 110
FIGURE 9-9 NON-BEAT SEAM MODE ...................................................................................... 111
FIGURE 9-10 USING TWO STAGE INITIATION IN BRAZING MODE ......................................... 112
FIGURE 9-11 SQUEEZE DELAY OPERATION ............................................................................ 113
FIGURE 9-12 MOMENTARY RETRACTION CONNECTIONS .................................................... 115
FIGURE 9-13 MAINTAINED CLOSURE RETRACTION CONNECTIONS ................................... 116
FIGURE 9-14 AIR OVER OIL RETRACTION CONNECTIONS.................................................... 118
FIGURE 9-15 AIR OVER OIL RETRACTION TIMING DIAGRAMS ............................................. 121
FIGURE 9-16 SCHEDULE SELECT ............................................................................................. 122
FIGURE 9-17 PROCESS OUTPUT 2626
2626
26 WIRING ........................................................................... 123
TABLES
TABLE 2-1 SLOPE MODES ....................................................................................................... 15
TABLE 2-2 CYCLE MODES ....................................................................................................... 15
TABLE 2-3 VALVE CODES ......................................................................................................... 16
TABLE 3-1 EXTERNAL SCR CONTACTOR CONNECTIONS ................................................... 23
TABLE 5-1 EXTERNAL SCHEDULE SELECT WITH FS7 AND FS11 ....................................... 51
TABLE 5-2 S49 EXTERNAL SCHEDULE SELECT.................................................................... 54
TABLE 5-3 STEPPER SELECTION USING SS1, SS2, SS4, SS8 ............................................. 55
TABLE 5-4 ORIGINAL AVC VALUES ......................................................................................... 57
TABLE 5-5 AVC PARAMETER VALUES .................................................................................... 57
TABLE 5-6 PROCESS OUTPUT CODES AND DESCRIPTIONS .............................................. 62
TABLE 5-7 CONSTANT CURRENT MODES ............................................................................. 71
TABLE 5-8 MAXIMUM AND MINIMUM VALUES FOR rr
rr
r.A..A.
.A..A.
.A. ......................................................... 72
TABLE 6-1 VALVE CODES ......................................................................................................... 83
TABLE 6-2 VALVE MODES AND VALVE OUTPUTS.................................................................. 86
TABLE 7-1 SCHEDULE MAP USED FOR STEPPER PROGRAMMING ................................... 88
TABLE 7-2 STEPPER CODES ................................................................................................... 89
TABLE 7-3 STEPPER SELECTION USING FS7 AND FS11 ..................................................... 92
TABLE 7-4 STEPPER SELECTION USING SS1, SS2, SS4, SS8 ............................................. 92
TABLE 7-5 PROGRAMMING FOR STEPPER MODE 0202
0202
02 ........................................................... 94
TABLE 8-1 OPERATING RANGES FOR PRESET-RANGE SELECTION WITH
ROGOWSKI COIL .................................................................................................... 99
TABLE 9-1 EXTERNAL SCHEDULE SELECT WITH FS7 AND FS11 ..................................... 122
TABLE OF CONTENTS (cont.)
FIGURES (cont.)

ENTRON Controls, LLC. • 700120S • Page 9
1.0 GENERAL DESCRIPTION
TheEN1000/EN1001Control is a microprocessorbased welding control. Itcanperform Upslope,
Downslope, Quench, Temper, Pulsation, Seam, and Spot, all of which can be combined to
providefor any possible welding schedule imaginable. It can store as many as 11base parameters
in each of 50 unique schedules. These are held in non-volatile memory for storage. In addition,
schedules can be chained together to provide more complex welding sequences. Despite the
seemingly complicated possible welding schedules, both the EN1000 and EN1001 Controls
are simple to program and operate.
The control provides accurate, predetermined execution of welding schedules for specific
numbers of cycles upon an external command. Initiation commands can be given by the closure
of a normally-open switch installed as part of the welding machine. The initiation switches
need not remain closed for the duration of the weld, but must be opened after the welding
interval is completed in order to re-initiate the control.After a weld has been started, the control
cannot be re-initiated until the previous sequence is completed.
The EN1000 and EN1001 Controls are designed to operate in conjunction with a welding
transformer rated for the 60 Hz or 50 Hz output frequency.These controls can be used either on
60 Hz or 50 Hz, without any additional settings or changing parameters. These controls are not
designed to operate with mid-frequency transformers with 500 Hz to 2000 Hz operating
frequency rating.
The EN1001 differs from EN1000 as it has a Constant Current mode of operation, see Section
5.4.15 and Section 8.0.
Figure 1-1. EN1000/EN1001 System

Page 10 • 700120S • ENTRON Controls, LLC.
1.1 STANDARD FEATURES (All Models)
DIGITAL PHASE SHIFT CURRENT CONTROL – Varies the output waveform duty cycle
from 0% to 99%, adjustable in 1% steps by means of Front Panel push buttons and direct
reading LED displays.
FUNCTION TIMING – Control uses Front Panel push buttons and direct reading LED displays
to program parameter timing in 1 cycle steps. Timing of SQUEEZE, HOLD, and OFF are
achieved by counting each cycle of the line current directly. This method of timing allows this
control to be used on either 50 Hz or 60 Hz power without special adjustments.
NO ADJUSTMENT is required for timing to change from 60 to 50 Hz operation.
OPERATING CONDITIONS – Temperature Range: 0°C to 70°C (32°F to 158°F).
POWER SUPPLY MONITORING – Control monitors VCC power supply and, whenever
this voltage goes below safe operating range, the message d.o.u.n.d.o.u.n.
d.o.u.n.d.o.u.n.
d.o.u.n. will be displayed on DATA
display. After this condition, control must be reset by activating Emergency Stop input or by
reapplying the power to the control.
PRESSURE SWITCH FIRING – Terminal Strip connection which allows the control to be
initiated from a Pressure Switch closure. Remove the jumper from TS1-PS1 andTS1-GND and
connect Pressure Switch leads. Pressure Switch is not furnished with control.
EMERGENCY STOP – Terminal Strip connection which allows all control functions to be
reset upon opening of the Emergency Stop Switch. After an Emergency Stop, the control will
not re-initiate automatically upon release of the switch. The control must be re-initiated
through the initiation circuits. The display will be flashing E.S.E.S.
E.S.E.S.
E.S. when TS1-ES1 is open. Remove
the jumper from TS1-ES1 and TS1-GND and install a normally closed switch. Emergency Stop
Switch is not furnished with control.
VALVE CONTROL TRANSFORMER – Provides the necessary voltage for powering the
welding machine solenoid valve(s). Input voltage may be either 240 VAC or 480 VAC (see
Wiring Diagram). Valve transformer output is 115 VAC (optional low voltage transformer for
certain operations provides a 24/48 VAC output). A 50 VA transformer is provided in “S”
Cabinets, and 150 VAtransformer is standard in “T/D”, “C” and NEMAenclosures (250 VAor
500 VA transformers optional).
This control may be configured for external valve power. See Section 4.3 for Terminal Strip
(TS1) external valve power connection.
When external valve power is used, 24-240 VAC or 24 VDC, valve transformer
must be disconnected at TS3-VL1 and TS3-VL2. Caution must be used to
properly insulate the wires from T3-X1 and T3-X2 leads after removing from TS3.
NOTICE
CAUTION
NOTICE

ENTRON Controls, LLC. • 700120S • Page 11
1.2 CONTROL PANEL LAYOUT
1 - WELD/NO WELD push button 17 - SLOPE MODE function indicator LED*
2 - NO WELD mode indicator LED 18 - SLOPE COUNT function indicator LED
3 - WELD mode indicator LED 19 - POWER light (red)
4 - DATAdisplay 20 - SCHEDULE 1s push button
5 - DATA10s push button 21 - SCHEDULE 10s push button
6 - DATA1s push button 22 - SCHEDULE display
7 - SQUEEZE function indicator LED 23 - WELD light (white)
8 - WELD/HEATfunction indicator LED 24 - PROGRAM LOCKOUT key switch
9 - PERCENT CURRENT function indicator LED 25 - OPERATE mode indicator LED
10 - HOLD function indicator LED 26 - PROGRAM/OPERATE push button
11 - SELECT push button 27 - PROGRAM mode indicator LED
12 - OFF function indicator LED 28 - ENTER push button
13 - IMPULSES function indicator LED 29 - VALVE 3 indicator LED
14 - COOL function indicator LED 30 - VALVE 2 indicator LED
15 - VALVE MODE function indicator LED 31 - VALVE 1 indicator LED
16 - CYCLE MODE function indicator LED*
* For operator convenience, codes for SLOPE MODE and CYCLE MODE functions are printed
on the left side of the Control Panel.
On EN1000 Control Panel layout, there is no added text for CONSTANT CURRENT modes.
Figure 1-2. Control Panel layout

Page 12 • 700120S • ENTRON Controls, LLC.
2.0 PROGRAMMABLE FUNCTIONS
SCHEDULES – The EN1000/EN1001 can store up to 50 schedules, numbered from 00 to 49.
Aweld sequence may include more than one schedule.A chain of schedules, for example, may
be used to add a forge operation during a weld sequence, or add a quench and temper sequence
to a schedule. In the simplest form, a weld schedule may include SQUEEZE, WELD, and
HOLD only. In a more complex form, a schedule may include: SQUEEZE and PRESSURE or
FORCE for the electrode, WELD time and STEPPER count, CURRENT in [%] or [kA] and
HI/ LO CURRENT limits when using CONSTANT CURRENTmode, HOLD, etc.All of these
features may be accessed by means of Front Panel parameters.
EXTENDED FUNCTIONS – The EXTENDED FUNCTIONS are used instead of Jumper or
Dip-switch settings. They are accessible from the Front Panel by simply clicking the SELECT
push button until FUNCTION indicator LED reaches SLOPE COUNT, then click once more.
At this point, the top display (DATA) will show EFEF
EFEF
EF. By clicking the SCHEDULE push buttons,
the EXTENDED FUNCTIONS are visible in the bottom display (SCHEDULE). For most
features, such as CHAINED schedules or SUCCESSIVE initiations, it is not necessary to enable
functions. For some others such as STEPPER (S.t.S.t.
S.t.S.t.
S.t.), it is necessary to just enable a Front-Panel
accessible EXTENDED FUNCTION. For others, it is necessary to add optional hardware to
the base control, such as the Integrated Pressure Sense Control System or Constant Current
operation.
2.1 CONTROL FUNCTIONS – See Figure 1-2. Control Panel layout
WELD/NO WELD PUSH BUTTON (1) – This push button is active at all times. It puts the
control in the WELD mode (enables the weld firing pulse) or NOWELD mode (disables firing).
This function is accessible while in OPERATE mode or while welding with few exceptions
(generally during error conditions).
WELD (3)/NO WELD (2) INDICATOR LEDs – These lights indicate the firing status of the
control. The LEDs toggle whenever the WELD/NO WELD push button is pressed.
DATA PUSH BUTTONS (5) & (6) – The right button increments DATA display (4) by one,
and the left button increments by ten. When either digit reaches the maximum, it resets to zero.
For parameters which allow programming of all four digits, the right button affects the two
right-hand digits – click to increment by one; press and hold to increment by ten. The left
button affects the two left-hand digits – click to increment by 100; press and hold to increment
by 1000. Only active in the PROGRAM mode.
FUNCTION INDICATOR LEDs (7-10 & 12-18) – The indicator LEDs light up to indicate
the active SCHEDULE parameter. They correspond to the programmable functions listed on
the Control Panel as the operator presses SELECT to view function values.
SELECT PUSH BUTTON (11) – Use the SELECT push button to choose any SCHEDULE
parameter.As the buttonis pressed, the corresponding LED will light up to indicate the parameter
data in the DATA display. Holding the SELECT push button momentarily will reverse the
direction of the LED movement when the button is released.

ENTRON Controls, LLC. • 700120S • Page 13
EXTENDED FUNCTIONS – One of the features found while paging through the functions
by using the SELECT push button is the EXTENDED FUNCTIONS (EFEF
EFEF
EF). The EXTENDED
FUNCTIONS are a second layer of parameters that apply to all the schedules and can modify
the way the control operates (see Section 5.4). To view the EXTENDED FUNCTIONS, press
SELECT until all LEDs are off and DATA display shows EFEF
EFEF
EF.
POWER LIGHT (19) – The red POWER lamp indicates when power is applied to the control.
WELD LIGHT (23) – The white WELD lamp is connected directly across the welding
transformer and will light when voltage is present at the welding transformer. The brilliance of
the WELD light is an indication of the programmed PERCENT CURRENT and therefore
provides a visual indication of the percent of RMS voltage supplied to the welding transformer.
SCHEDULE DISPLAY (22) – The SCHEDULE display shows the number of the active
schedule. The EN1000/EN1001 can store up to 50 schedules numbered from 00 to 49.
SCHEDULE PUSH BUTTONS (20) & (21) – The right button increments SCHEDULE
display by one, and the left button increments by ten. When either digit reaches the maximum,
it resets to zero.
There are two ways to select the active schedule:
1. INTERNAL: Use the SCHEDULEpushbuttons andselectthe desired schedule. Initiation
on FS3 to GND will select the schedule shown in the display (see Section 5.4.3).
2. EXTERNAL: Use a combination of FS7/SS1 AND FS11/SS3 to select one of four
schedules (see Section 5.4.3).
PROGRAM/OPERATE PUSH BUTTON (26) – This push button will put control in
PROGRAM or OPERATE mode. PROGRAM (27) and OPERATE (25) LEDs indicate which
mode control is in:
PROGRAM mode is the mode in which the individual schedules can be entered or modified.
Data such as WELD time, PERCENT CURRENT, VALVE select, etc., can only be
changed in the PROGRAM mode.
OPERATE mode is the normal operating mode for the control. This is the only mode in
which the control can be initiated for a weld. When the control is in OPERATE mode,
the control is in a Ready (to initiate) state.
PROGRAM LOCKOUT KEY SWITCH (24) (Optional) – A PROGRAM LOCKOUT key
switch can be ordered as a factory-installed option. It may also be added later by the customer,
if desired. To install the key switch, remove the key switch hole-plug from the Front Panel and
mount the switch using the nut and lock-washer provided. Connect the plug from the switch
onto the mating 2-prong connector (J1) on the back of the Display Circuit Board.
To put the control in PROGRAM mode using the PROGRAM LOCKOUT key switch:
Rotatethe key45 degreesclockwise and hold,while holdingthe key inthis position,
pressandreleasethe PROGRAM/OPERATEpush button, then release the key.The
OPERATE LED will now turn off and the PROGRAM LED will turn on, indicating
programmability of all functions.
2.1 CONTROL FUNCTIONS (cont.) – See Figure 1-2. Control Panel layout

Page 14 • 700120S • ENTRON Controls, LLC.
To put the control back in the OPERATE mode:
Press the PROGRAM/OPERATE push button again. The control will return to the
OPERATE mode without the necessity of rotating the key.
See Section 5.4.18 for detailed information on PIN LOCKOUT mode.
ENTER PUSH BUTTON (28) – The ENTER push button is used to store the data shown
from the DATA display into the non-volatile memory which retains data with the power off.
If ENTER is not pressed before other data is viewed (by pressing the SELECT push button)
or before returning to the OPERATE mode, the data will not be stored; however, it is not
necessary to press the ENTER push button to save the four-digit DATA display.
VALVE INDICATOR LEDs (29, 30, & 31) – These three LEDs indicate, in the OPERATE
mode, when the solenoid valves are activated in the control program. In the PROGRAM mode,
these same LEDs indicate the valve chosen for the weld sequence (schedule) being programmed.
Codes for valve selection are given in Table 2-3.
2.2 SEQUENCE TIMED PARAMETERS (Count Functions)
SQUEEZE .................................................... Programmable from 0 to 99 cycles (50/60 Hz)
WELD/HEAT ................................................ Programmable from 0 to 99 cycles (50/60 Hz)
HOLD ........................................................... Programmable from 0 to 99 cycles (50/60 Hz)
OFF .............................................................. Programmable from 0 to 99 cycles (50/60 Hz)
IMPULSES ................................................... Programmable from 1 to 99
COOL ........................................................... Programmable from 0 to 99 cycles (50/60 Hz)
SLOPE COUNT ........................................... Programmable from 0 to 99 cycles (50/60 Hz)
NO ADJUSTMENT is required for timing to change from 60 to 50 Hz operation.
SQUEEZE COUNT (7) – The time duration for the electrodes to close on the work and
build up pressure before WELD time begins.
WELD/HEAT COUNT (8) – The time during which current will flow through the welding
transformer (during one impulse in impulse welding). It starts after SQUEEZE or after the
closure of a Pressure Switch, whichever occurs last.
HOLD COUNT (10) – The time during which the electrodes will remain in contact with
the work to allow the weld nugget to congeal. It starts after the WELD time.
OFF COUNT (12) – In the REPEAT mode, the time duration between HOLD count and
SQUEEZE count to allow the work to be repositioned.
COOL COUNT (14) – The time between heat IMPULSES (in multiple impulse welding).
SLOPE COUNT (18) – The number of additional WELD cycles during which PERCENT
CURRENTincreasesordecreasesto achieve SLOPE (gradual increase or decrease in current).
2.1 CONTROL FUNCTIONS (cont.) – See Figure 1-2. Control Panel layout
NOTICE
NOTICE

ENTRON Controls, LLC. • 700120S • Page 15
2.3 OTHER PROGRAMMABLE SEQUENCE PARAMETERS
IMPULSES (13) – The number of heat IMPULSES that will occur in a schedule.
PERCENT CURRENT (9) – The percentage of conduction time provided to the welding
transformer primary from 0 to 99%, adjustable in 1% steps. This parameter is also used to set
HIGH and LOW limits in CONSTANT CURRENT mode (see Section 8.3.2).
SLOPE MODE (17) – Determines direction of the ramp with respect to programmed weld
PERCENT CURRENT. See Section 6.3 for detailed information on SLOPE MODE functions.
Table 2-1. SLOPE MODES
CYCLE MODE (16) – The manner in which the control performs schedules is determined by
the code programmed into this function as described in Table 2-2. See Section 6.2 for detailed
information on CYCLE MODE functions.
Table 2-2. CYCLE MODES
The CYCLE MODE and SLOPE MODE function codes are printed on the Control Panel,
adjacent to the ENTER push button, for operator convenience.
NOTICE
SLOPE MODE Description
00 NO SLOPE
01 UPSLOPE
02 DOWNSLOPE
CYCLE
MODE MODE Description
00 NON-REPEAT The control can be initiated for only one sequence (see
Section 6.2.1)
01 REPEAT After initiation, the control internally re-initiates as long as
the initiation switch is maintained closed (see Section 6.2.2)
02 CHAINED
Several schedules can be chained together so that several
consecutive schedules can be sequenced from one initiation
(see Section 6.2.3)
03 SUCCESSIVE Several schedules can be sequenced successively upon
separate initiations (see Section 6.2.4)
04 CONDITIONAL
SUCCESSIVE
Valves remain active at the end of HOLD (this is indicated
by blinking HOLD indicator LED ) until control is re-
initiated and next schedule will be sequenced (see Section
6.2.5)
05 WAIT-HERE
After FS3 initiation, wait either in SQUEEZE or WELD-
COOL or HOLD part of the sequence until control is re-
initiated with FS7 or FS11 and schedule 10 or 20 will be
sequenced (see Section 6.2.6)

Page 16 • 700120S • ENTRON Controls, LLC.
VALVE MODE (15) – The three solenoid valves are activated based on the code programmed
as shown in Table 2-3.
Table 2-3. VALVE codes
When in the PROGRAM mode and selection of a VALVE code is being made, the VALVE
indicator LEDs (29, 30, 31) will indicate the selected valve(s). The valve output will not be
energized while in PROGRAM mode.
TheVALVE code indicated above can be programmed for differentfeaturessuch as PROCESS
OUTPUT (see Section 5.4.7).
2.3 OTHER PROGRAMMABLE SEQUENCE PARAMETERS (cont.)
NOTICE
VALVE3 VALVE2 VALVE1
00 OFF OFF OFF All valves off None
01 OFF OFF ON Valve 1 active SV1-SV2
02 OFF ON OFF Valve 2 active SV3-SV4
03 OFF ON ON Valves 1 & 2 active SV1-SV2 & SV3-SV4
04 ON OFF OFF Valve 3 active SV5-SV6
05 ON OFF ON Valves 1 & 3 active SV1-SV2 & SV5-SV6
06 ON ON OFF Valves 2 & 3 active SV3-SV4 & SV5-SV6
07 ON ON ON Valves 1, 2 & 3 active SV1-SV2, SV3-SV4 & SV5-SV6
VALVE Indicator LEDs
DescriptionVALVE code Valve Outputs on TS1
Since the VALVE codes are in binary form, valve assignments are clarified in this table.

ENTRON Controls, LLC. • 700120S • Page 17
3.0 INSTALLATION
The EN1000 and EN1001 Series Controls can be provided in different cabinet styles.
3.1 INSTALLATION AND MOUNTING DIAGRAMS – “S” CABINET
The installation and mounting diagrams for “S” Cabinet are shown in Figure 3-1. Available
contactors for “S” Cabinet – 150A, 300A, and 1200A.
Figure 3-1. Installation and mounting diagrams for Style “S” Cabinet

Page 18 • 700120S • ENTRON Controls, LLC.
3.2 INSTALLATION AND MOUNTING DIAGRAMS – “E” CABINET
Style “E” Cabinet installation and mounting diagrams are shown in Figures 3-2, 3-3 and 3-4.
Figure 3-2. Installation of Style “E”
Cabinet – 300A & 1200A Contactor Figure 3-3. Installation of Style “E”
Cabinet – 1800/2200/3200A Contactor
Figure 3-4. Mechanical mounting diagram for “E” Cabinet

ENTRON Controls, LLC. • 700120S • Page 19
3.3 INSTALLATION AND MOUNTING DIAGRAMS – “T/D” AND “L”
CABINET
Style “T/D” and “L” Cabinet installation and mounting diagrams are shown in Figures 3-5, 3-6
and 3-7.
Figure 3-5. Installation of Style “T/D” and
“L” Cabinets – 1200A Contactor Figure 3-6. Installation of Style “T/D” and
“L” Cabinets – 1800/2200/3200A Contactor
Figure 3-7. Mechanical mounting diagram for “T/D” and “L” Cabinets

Page 20 • 700120S • ENTRON Controls, LLC.
3.4 INSTALLATION AND MOUNTING DIAGRAMS – “C” CABINET
Style“C” Cabinetinstallation and mounting diagramsare shown in Figures3-8 and 3-9.Available
contactors for “C” Cabinet – 300A and 1200A.
Figure 3-9. Mounting diagrams for Style “C” Cabinet
TERMINAL
BOARD
CIRCUIT
T2
T1
R70
F2
410319
R71
F3
L1
T3
FIRING
BREAKER
F1
CUTOUT THRU
REAR PANEL TO
REAR OF CABINET
FOR CUSTOMER
WIRING
L1
L2
L1
1200A
L2
IN
WATER
CONTACTOR
WATER
OUT
TERMINAL STRIP TS1
H1
GROUND
LUG
Figure 3-8. Installation diagram for Style “C” Cabinet
Other manuals for EN1000 series
2
This manual suits for next models
1
Table of contents
Other Entron Controllers manuals
Popular Controllers manuals by other brands
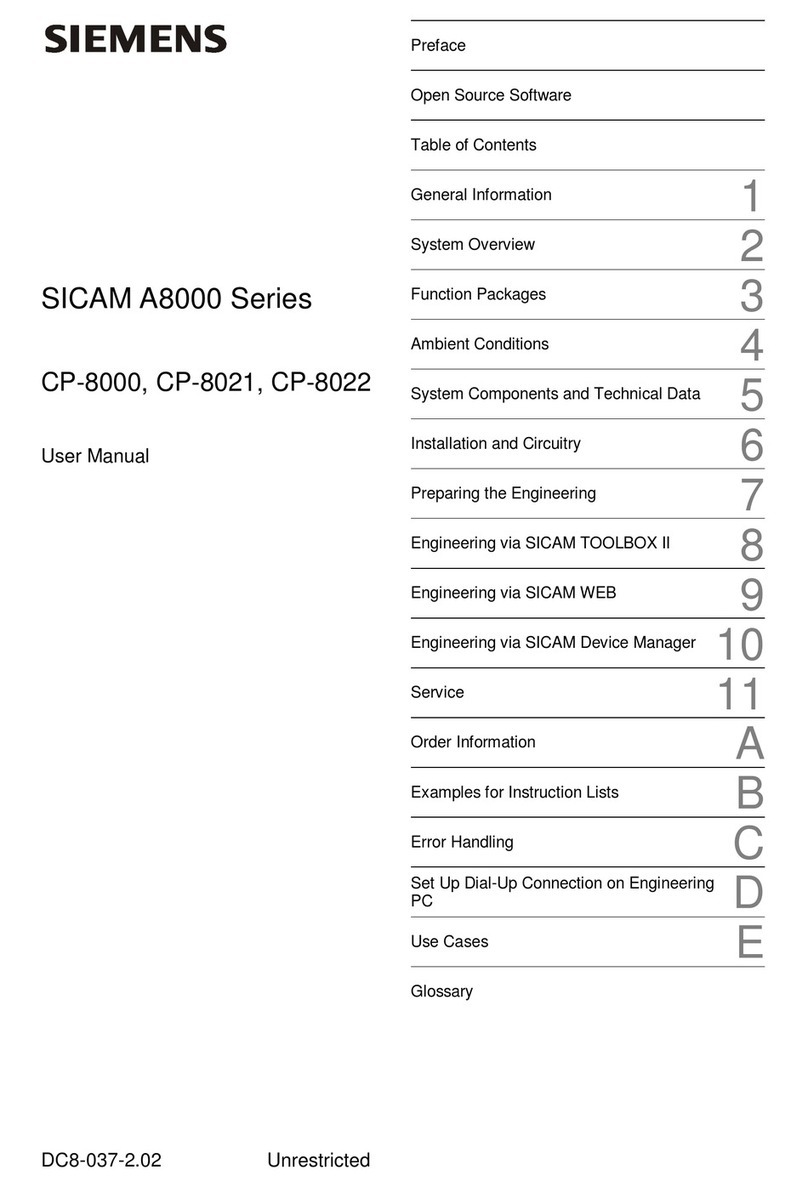
Siemens
Siemens CP-8000 user manual
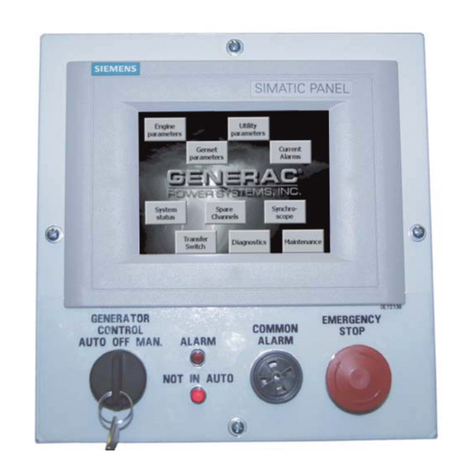
Generac Power Systems
Generac Power Systems PowerManager PM-GC manual
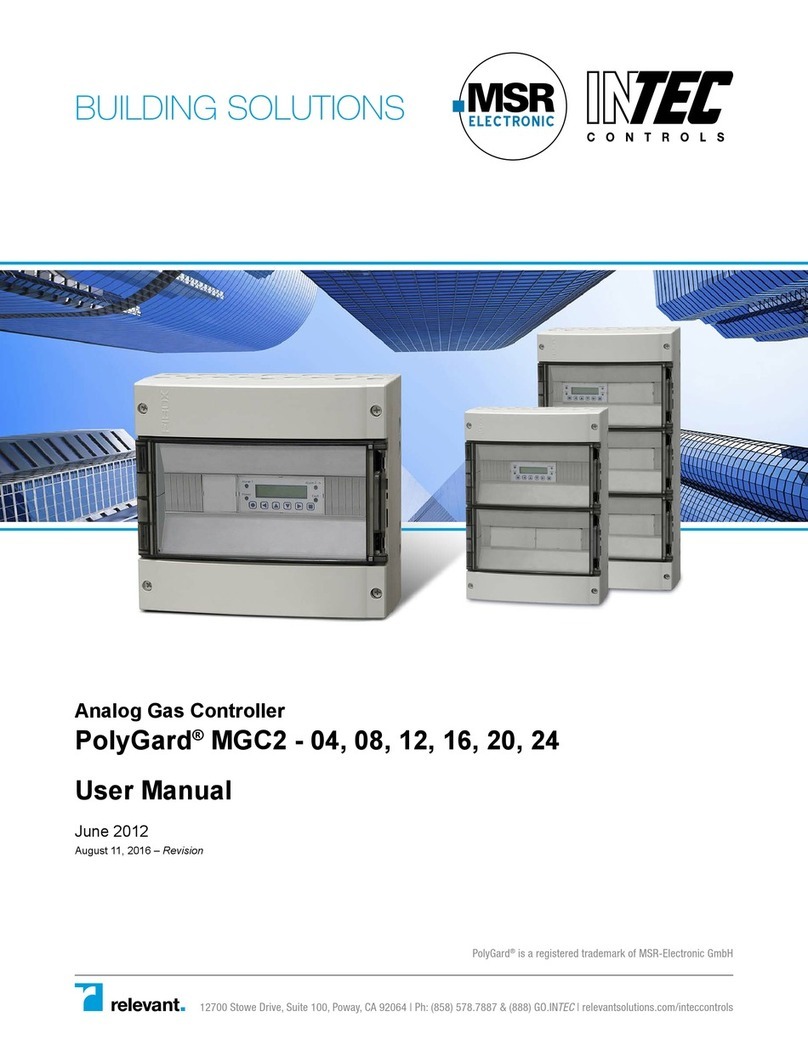
Intec Controls
Intec Controls PolyGard MGC2-04 user manual
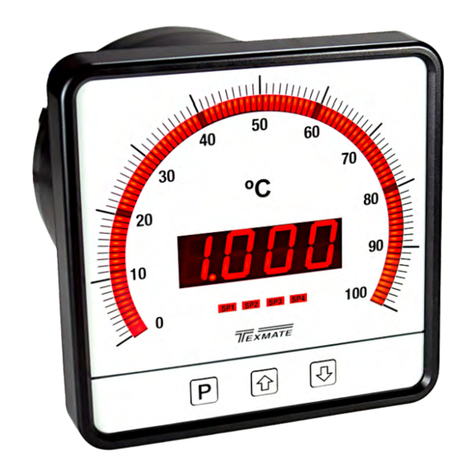
Texmate
Texmate CL-B101D40-RTD manual

Samson
Samson TROVIS 5757-7 Mounting and operating instructions
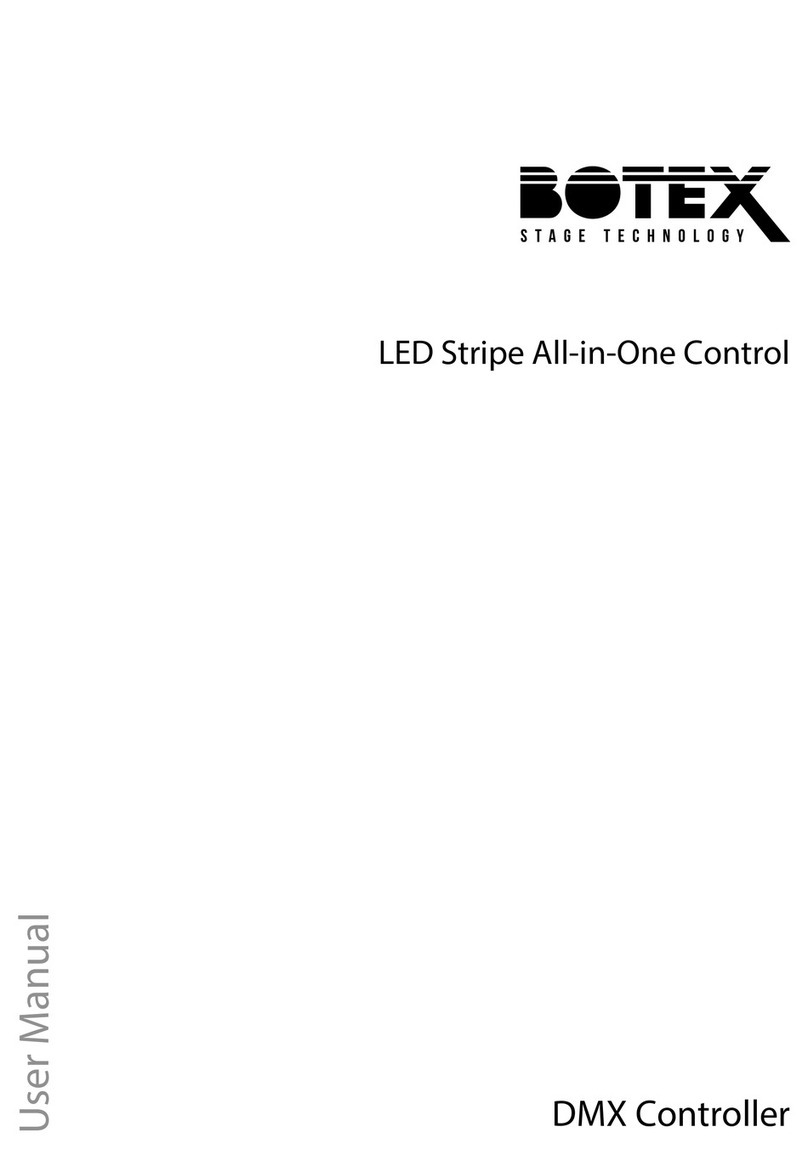
thomann
thomann Botex LED Stripe All-in-One Control user manual