ero electronic LDE User manual

170.IU0.LXE.0D0
UU
UU
UUSER MANUALUSER MANUAL
USER MANUALUSER MANUAL
USER MANUAL
UU
UU
UISTRUZIONI D'USOISTRUZIONI D'USO
ISTRUZIONI D'USOISTRUZIONI D'USO
ISTRUZIONI D'USO
LDE
LME
Lxe-0-C00-B.pmd 28/01/2004, 14:591

INDICE
A. DIMENSIONIEFORATURA ........................A.3
1. MONTAGGIO ................................................. 1
2. COLLEGAMENTIELETTRICI ......................... 2
3. IMPOSTAZIONIHARDWARE
PRELIMINARI ................................................. 6
4. CONFIGURAZIONE ........................................ 6
4.1 Operatività dei pulsanti ........................ 6
4.2 Eventuale protezione dei parametri...... 6
4.3 Accesso alla configurazione ................ 7
4.4 Parametridiconfigurazione .................. 7
5. MODOOPERATIVO..................................... 15
5.1 Preliminari............................................ 15
5.2 AlgoritmoSMART ................................ 15
5.3 Inibizione del segnale di uscita.......... 16
5.4 Visualizzazione del set point
impostato(modelloLDE)..................... 16
5.5 SelezioneSP/SP2............................... 16
5.6 Modifica diretta del set point .............. 16
5.7 Descrizione dei modi timer ................. 17
5.8 Riarmomanualedell'allarme................ 20
5.9 Funzione "Soft Start" .......................... 21
5.10 Lamp test ............................................ 21
5.11 Operatività dei pulsanti ...................... 21
5.12 Indicatori ............................................. 21
5.13 Parametrioperativi .............................. 22
6. MESSAGGIDIERRORE .............................. 25
6.1 Segnalazioneanomaliadellamisura .. 25
6.2 Messaggidi errore .............................. 26
6.3 Lista degli errori possibili.................... 26
7. CARATTERISTICHETECNICHE................... 27
7.1 Specifiche tecniche ............................ 27
7.2 Ingressi ............................................... 27
7.3 Azioni di controllo ............................... 28
7.4 Uscite .................................................. 29
7.5 CPI - Configuration Port Interface...... 29
8. MANUTENZIONE .......................................... 29
B. DEFAULTPARAMETERS ............................B.1
I
A. 2
GB
INDEX
A. OUTLINEANDCUTOUTDIMENSIONS......A.4
1. MOUNTING .................................................... 1
2. ELECTRICALCONNECTIONS ........................ 2
3. PRELIMINARYHARDWARE
SETTINGS...................................................... 6
4. CONFIGURATION .......................................... 6
4.1 Pushbutton function ............................. 6
4.2 Possible protection of the parameters . 6
4.3 Access to the configuration procedure 6
4.4 Configurationparameters ..................... 7
5. OPERATIVEMODE ..................................... 15
5.1 Preliminarycomments ......................... 15
5.2 SMARTalgorithm ................................ 15
5.3 Inhibition of the out signal .................. 16
5.4 Displaying the set point set
(modelLDE)......................................... 16
5.5 SP/SP" selection ................................ 16
5.6 Direct modification of the set point .... 16
5.7 Timermodedescription ....................... 17
5.8 Manual reset of the alarm................... 20
5.9 Soft Start Ffunction ............................ 21
5.10 Lamp test ............................................ 21
5.11 Function of the pushbuttons .............. 21
5.12 Indicators ............................................ 21
5.13 Operativeparameters ......................... 22
6. ERRORMESSAGES .................................... 25
6.1 Measurement anomalysignal ............ 25
6.2 Error messages .................................. 26
6.3 List of possible errors ........................ 26
7. TECHNICALCHARACTERISTICS ................ 27
7.1 Technical specifications ..................... 27
7.2 Inputs.................................................. 27
7.3 Control actions.................................... 28
7.4 Outs .................................................... 29
7.5 CPI - Configuration Port Interface...... 29
8. MAINTENANCE ............................................ 29
B. DEFAULTPARAMETERS ............................B.1
Ixe-0-B00.p65 10/18/02, 3:43 PM2

A. 3
A. DIMENSIONI E FORATURA
LDE LME
Ixe-0-B00.p65 10/18/02, 3:43 PM3

A. 6
Ixe-0-B00.p65 10/18/02, 3:43 PM4

1
GB
1. MOUNTING
Select a mounting location where there is
minimum vibration and the ambient temperature
ranges between 0 and 50°C (32 and 122°F).
The instrument can be mounted on a panel up to
15 mm thick with a square cutout of 45 x 45 mm.
For outline and cutout dimensions refer to
page A.4.
The surface texture of the panel must be better
than 6.3 µm.
The instrument is fitted with a rubber panel gasket.
To assure IP65 and NEMA 4 protection, insert the
panel gasket between the instrument and the
panel as shown in Fig. 1.
While holding the instrument against the panel
proceed as follows:
1) insert the gasket in the instrument case;
2) insert the instrument in the panel cutout;
3) pushing the instrument against the panel, insert
the mounting bracket;
4) with a screwdriver, turn the screws with a
torque between 0.3 and 0.4 Nm. Fig. 1 PANEL MOUTING
screws
bracket
gasket
panel
lxe-1-B00.p65 10/18/02, 3:46 PM1

2
GB
MEASURING INPUTS
NOTE: Any external components (like zener
barriers etc.) connected between sensor and input
terminals may cause errors in measurement due
to excessive and/or not balanced line resistance or
possible leakage currents.
TC INPUT
Fig. 3 THERMOCOUPLE CONNECTION
NOTES:
1) Do not run input wires together with power line
cables.
2) For TC wiring use proper compensating cable
preferablyshielded.
3) When a shielded cable is used, it should be
connected at one point only.
2. ELECTRICAL CONNECTIONS
Connections are to be made with the instrument
housing installed in its proper location.
Fig. 2 REAR TERMINAL BLOCK
10
9
+
_
10
9
+
_
Shield
Shield
+
-
lxe-1-B00.p65 10/18/02, 3:46 PM2

3
GB
RTD INPUT
Fig. 4 RESISTANCE TEMPERATURE
DETECTOR CONNECTION
NOTES:
1) Do not run input wires together with power line
cables.
2) Pay attention to the line resistance; a resistance
higher than 20 Ω/wire may cause measurement
errors.
3) When shielded cable is used, it should be
grounded at one side only to avoid ground loop
currents.
4) The impedence of the 3 wires must be the
same.
8
RTD
10
9 8
RTD
10
9
11
12
Log. input 2
LOGIC INPUT
Safety note:
1) The "OUT 3" and the "logic input" options are
mutually exclusive.
2) Do not run logic input wiring together with
power cables.
3) Use an external dry contact capable of
switching 8 mA, 8 V DC.
4) The instrument needs 300 ms to recognize a
contact status variation.
5) The logic input is NOT isolated by the
measuringinput
Fig. 5 - LOGIC INPUT WIRING
The logic input can be programmed as:
A) Set point selector
A.1) In this case it will operate as follows:
logic input operat. set point
open SP
close SP2
B) Start timer
In this case it will operate as described at
paragraph 5.10 (Timer modes description).
lxe-1-B00.p65 10/18/02, 3:46 PM3

4
GB
3) Use copper conductors only.
4) Do not run input wires together with power
line cables.
5) The "OUT 3" and the "logic input" options are
mutually exclusive.
The following recommendations avoid serious
problems which may occur it when using relay
output to drive inductive loads.
INDUCTIVE LOADS
High voltage transients may occur when switching
inductiveloads.
These transients may introduce disturbances
through the internal contacts which can affect the
performance of the instrument.
The internal protection (varistors) assures correct
protection up to 0.5 A of inductive component but
the OUT 1 NC contact is not protected.
The same problem may occur when a switch is
used in series with the internal contacts.
Fig. 7 EXTERNAL SWITCH IN SERIES WITH
THE INTERNAL CONTACT
In these cases an additional RC network should
be installed across the external contact as shown
in Fig. 7
The value of the capacitor (C) and resistor (R) are
shown in the following table.
R
C
LOAD
POWER
LINE
RELAY OUTS
Fig. 6 RELAY OUTS
The OUT 1 NO contact and the OUT 2 and OUT 3
contactsareprotectedbyvaristorsagainstinductive
load with inductive component up to 0.5 A.
The OUT 1 contact rating is 3A/250V AC on
resistive load.
The OUT 2 and OUT 3 contact rating is 2A/250V
AC on resistive load.
The number of operations is 1 x 105at specified
rating.
NOTES:
1) To avoid electric shock, connect the power
line at the end of the wiring procedure.
2) For power connections use No 16 AWG or
larger wires rated for at least 75°C.
7
6C
NO
OUT 2
14
15 C
NO
OUT 3
1
3
2C
NC
NO
OUT 1
lxe-1-B00.p65 10/18/02, 3:46 PM4

5
GB
In every case the cable connected to the relay
outs must be routed as far away as possible from
input or communication cables.
VOLTAGE OUTS FOR SSR DRIVE
Fig. 8 SSR DRIVE OUT WIRING
It is a time proportioning out.
Logic level 0: Vout < 0.5 V DC.
Logic level 1: Maximum current = 20 mA.
- 14 V + 20 % @ 20 mA
- 24 V + 20 % @ 1 mA.
NOTE: This out is NOT isolated.
AdoubleorreinforcedIsolationbetweeninstrument
output and power supply must be assured by the
external solid state relay.
LOAD
(mA)
<40 mA
<150 mA
<0.5 A
C
(mF)
0.047
0.1
0.33
R
(W)
100
22
47
P.
(W)
1/2
2
2
OPERATING
VOLTAGE
260 V AC
260 V AC
260 V AC
+
__
+
2
1
OUT 1
SOLID STATE
RELAY
POWER LINE WIRING
Fig. 9 POWER LINE WIRING
NOTES:
1) Before connecting the instrument to the supply,
make sure that the line voltage corresponds to
that indicated on the rating plate.
2) Toavoid electricshock,connectthepowerlineat
the end of the wiring procedure.
3) ForsupplyconnectionsuseNo16AWGorlarger
wires rated for at least 75°C.
4) Use copper conductors only.
5) Do not run input wires together with power line
cables.
6) For 24 V AC/DC the polarity does not matter.
7) The power supply input has NO fuse protection.
Please,provide aTtype1A,250Vfuseexternally.
8) The safety regulations for equipment
permanently connected to the mains require
that there is a switch or circuit breaker in the
building electrical system and that this:
- isnearthedeviceandcaneasilybereachedby
theoperator;
- is marked as the device ON/OFF device.
NOTE: A single switch or circuit-breaker can drive
more than one instrument.
4
R (S,T)
R (S,T)
N
5N
Power Line
100 V to 240 V AC (50/60Hz)
or 24 V AC/DC
lxe-1-B00.p65 10/18/02, 3:46 PM5

6
GB
3. PRELIMINARY HARDWARE
SETTINGS
These instruments can detect the opening of the
input circuit (TC or RTD). This failure is displayed
as an overrange condition.
For the thermocouples only one can select, by
means of jumpers SH1 and CH1 indicated in Fig.
9, the type of indication to be obtained when the
thermocouple is open (see table at the bottom of
thepage).
To gain access to the jumpers the instrument must
be taken out of its case.
SH1 CH1
Fig. 10 SH1 and CH1 JUMPERS
SH1 CH1 Indication
open close overrange(standard)
close open underrange
4. CONFIGURATION
4.1 PUSHBUTTON FUNCTION
FUNC This saves the new value of the
selected parameter and goes to the
next parameter (increasing order).
SMT This scrolls back the parameters
without saving the new value.
sThis increases the value of the selected
parameter.
tThis decreases the value of the
selectedparameter.
4.2 POSSIBLE PROTECTION OF THE
PARAMETERS
Access to the configuration and the display and
modification of the operative parameters, can be
protected by a secret code. The code is entered in
configuration, by means of parameters P11 and
P14.
P11 = 0 All the operative parameters can be
displayed and modified. Access to the
configuration is free.
P11 = 1 and P14 = On All the operative
parameters can be displayed but not modified,
apart from SP (Set Point), SP2 (second set point)
and t (time of the timer function). Access to the
configuration is only possible by entering the
master key code when requested.
P11 = 1 and P14 = OFF No operative parameter
can be displayed and modified, apart from SP,
SP2 and t. Access to the configuration is only
possible by entering master key when requested.
P11 = 2/499 In this case the value programmed in
P11 represents a numerical key which can be
used to protect access to the configuration and, in
operative mode, the modification of the
lxe-1-B00.p65 10/18/02, 3:46 PM6

7
GB
numerical value (or the selection code). In the
model LDE, the display shows the parameter code
and the numerical value alternatively.
To alter the value set or the option selected press
sor tand confirm with FUNC.
The parameter for loading the default parameters
is shown in section B at the end of the manual.
4.4 CONFIGURATION PARAMETERS
P1 - Type of input and standard range
Type of input Range
0 TC type L 0 / +900 °C
1 TC type J 0 / +999 °C
(LME)
0 / +1000 °C
(LDE)
2 TC type K 0 / +999 °C
(LME)
0 / +1370
(LDE)
3 TC type N 0 / +999 °C
(LME)
0 / +1400 °C
(LDE)
4 RTD type Pt 100 -199 / +800 °C
(LME)
-200 / +800 °C
(LDE)
5 RTD type Pt 100 -19.9 / +99.9 °C
(LME)
-199.9 / +400.0 °C
(LDE)
6 TC type T 0 / +400 °C
8 TC type L 0 / 999 °F
(LME)
0 / 1652 °F
(LDE)
9 TC type J 0 / 999 °F
(LME)
0 / 1832 °F
(LDE)
10 TC type K 0 / 999 °F
(LME)
0 / 2498 °F
(LDE)
11 TC type N 0 / 999 °F
(LME)
0 / 2552 °F
(LDE)
12 RTD type Pt 100 -199 / 999 °F
(LME)
-328 / 1472 °F
(LDE)
13 TC type T 0 / 752 °F
parameters (SP, SP2 and t can always be
modified).
If the modification of the parameters has been
enabled, the passage in configuration is free.
If not it will be allowed by entering, when
requested, the numerical value programmed in
P11, or master key code.
P11 = 500/999 As for the previous point, with the
difference that alarm thresholds (AL and AL2) can
be modified as well as SP, SP2 and t.
In the two previous cases, with P14 = On, the
parameters set as not modifiable can however be
displayed. With P14 = OFF they are not.
To set P11 and P14 see section 4.4.
4.3 ACCESS TO THE CONFIGURATION
PROCEDURE
To access the configuration, press SMT and
FUNC simultaneously (press first SMT and
immediately afterwards FUNC) keeping both the
pushbuttons pressed for three seconds.
In the model LME the lower display will show CnfCnf
CnfCnf
Cnf,
the upper OFFOFF
OFFOFF
OFF. In model LDE OFFOFF
OFFOFF
OFF and CnFCnF
CnFCnF
CnF will
appearalternatively.
Press sor twithin 10 seconds to set ONON
ONON
ON, then
confirm with FUNC.
If the device is in the protected condition (see
previous section), the lower display (LME) shows
Cnf, the upper a dashed line (instead of OFFOFF
OFFOFF
OFF). In
model LDE the two wordings appear alternately.
By means sor tenter the value entered in P11,
or master key value. Press FUNC to confirm.
The instrument is now in configuration mode, and
the display shows CnfCnf
CnfCnf
Cnf steadily for both models.
Via FUNC we advance to the first parameters.
In configuration, the lower display shows the code
of the parameter (P1-P26), the upper the
lxe-1-B00.p65 10/18/02, 3:46 PM7

8
GB
NOTE: When P1 has been changed, the P2 and
P10 parametrer will be forced to the minimum
value of the selected range while the P3
parameter will be forced to the maximum value of
the selected range .
P2 = Initial scale value
Initial scale value for input from thermocouple/
ResistanceTemperature Detector.
NOTES:
1) When P2 has been modified, the rLrL
rLrL
rL parameter
will be aligned to it and rHrH
rHrH
rH parameter will be
forced to P3 value is rHrH
rHrH
rH < rLrL
rLrL
rL.
2) When P2 has been modified, if the alarms are
programmed as process alarms (P5=1 and/or
P22=1) and the alarm thresholds are out of
range, AL.1AL.1
AL.1AL.1
AL.1 and/or AL.2AL.2
AL.2AL.2
AL.2 will be aligned to P2.
P3 = Full scale value
Full scale value for input from thermocouple/
ResistanceTemperature Detector.
NOTES:
1) The minimum input span (P3 - P2) is 300°C or
600°F for TC input and 100°C or 200°F for RTD
input.
3) When P3 has been modified, the rHrH
rHrH
rH parameter
will be aligned to it and rlrl
rlrl
rl parameter will be
forced to P2 value is rlrl
rlrl
rl > rHrH
rHrH
rH.
4) When P3 has been modified, if the alarms are
programmed as process alarms (P5=1 and/or
P22=1) and the alarm thresholds are out of
range, AL.1AL.1
AL.1AL.1
AL.1 and/or AL.2AL.2
AL.2AL.2
AL.2 will be aligned to P3.
P4 = Out 1 action
This parameter is not modifiable when P5 = 5
rEUrEU
rEUrEU
rEU = reverse action (Heating)
dirdir
dirdir
dir = direct action (Cooling)
P5 = Function of Out 2
0 = Not used or used as event (P22 = 6, 7, 9, 10)
1 = Alarm 1 output - Process alarm
2 = Alarm 1 output - Band alarm
3 = Alarm 1 output - Deviation alarm
4 = Alarm 1 output - Instrument failure alarm
5 = Cooling out
NOTES:
1) Setting P5 = 1, 2, 3:
- if parameter OLHOLH
OLHOLH
OLH is less than 0, it is set to 100;
- if parameter IPIP
IPIP
IP is less than 0, it is set to 30;
- if parameters AL1AL1
AL1AL1
AL1 is out of range, it will be
aligned to the lowest value.
2) Setting P5 = 0 or 4:
- if parameter OLHOLH
OLHOLH
OLH is less than 0, it is set to 100;
- if parameter IPIP
IPIP
IP is less than 0, it is set to 30;
3) Setting P5 = 5:
- parameter P4 automatically assumes the
value “rEUrEU
rEUrEU
rEU”;
- if parameter P16 is out of range, it will be
aligned to the lowest value;
- if parameter Pb is not 0 and is lower than 1.5,
it is set to 1.5.
4)Setting P5 different 0:
- if P22 parameter is equal to 6, 7, 9 or 10 it will
be forced to 0.
t
Input
t
Input
t
Out
t
Out
Reverse Direct
lxe-1-B00.p65 10/18/02, 3:47 PM8

9
GB
P6 = Out 2 configuration
P6 is skipped when P5 = 0.
If P5 = 1, 3 or 4;
H.A.H.A.
H.A.H.A.
H.A. =
High alarm
with automatic reset
L.A.L.A.
L.A.L.A.
L.A. =
Low alarm
with automatic reset
H.L.H.L.
H.L.H.L.
H.L. =
High alarm
with manual reset
L.L.L.L.
L.L.L.L.
L.L. =
Low alarm
with manual reset
When P5 = 4, the "high" or "low" selection has no
effect.
If P5 = 2:
H.A.H.A.
H.A.H.A.
H.A. =
out of band
with automatic reset
L.A.L.A.
L.A.L.A.
L.A. =
in band
with automatic reset
H.L.H.L.
H.L.H.L.
H.L. =
out of band
with manual reset
L.L.L.L.
L.L.L.L.
L.L. =
in band
with manual reset
When P5 = 5 this parameter selects the cooling
medium.
AIrAIr
AIrAIr
AIr = air OILOIL
OILOIL
OIL = oil H2OH2O
H2OH2O
H2O = water
NOTE: Modifying parameter P6 automatically
updates the values of the cooling cycle time and
the cooling gain.
P6 C2 RC
Air 10 (s) 1
OIL 4 (s) 0.8
H2O 2 (s) 0.4
P7 = Alarm 1 action
Only available when P5 is different from 0 or 5.
rEUrEU
rEUrEU
rEU = reverse (relay de-energized in alarm
condition)
dirdir
dirdir
dir = direct (relay energized in alarm condition)
P8 = Stand-by of the alarm 1
Only available when P5 is 1, 2 or 3.
OFFOFF
OFFOFF
OFF = stand-bydisabled
ONON
ONON
ON = stand-byenabled
NOTE: For band or deviation alarm, the alarm
stand-by function disables the alarm indication at
instrument start up and after a set point
modification until the process variable reaches the
alarmthreshold.
For process alarm, the stand-by function is
activated at start up only.
P9 = OFFSET applied to the measured value
This OFFSET is applied along the whole span.
When P1= 5 P9 is programmable from -19.9
to 19.9°C.
When P1 ≠5 P9 is programmable from -199
to 199°C or °F.
P10 = Threshold of the “Soft Start” function
The “Soft start” function limits the maximum out
power (see OLHOLH
OLHOLH
OLH operative parameter) for a
programmable time (see tOLtOL
tOLtOL
tOL operative parameter)
at the instrument start up when the measured
value is lower then the programmed threshold.
P10 is the threshold value, in engineering units.
Changing P1 parameter value, P10 parameter will
be forced to the minimum range value of the new
selectedrange.
Real curve
Readout
Adjusted
curve
Input
P9
lxe-1-B00.p65 10/18/02, 3:47 PM9

10
GB
P11 = Safety lock
0= device unlocked. All the parameters can be
modified
1= device locked. None of the parameters can be
modified except SPSP
SPSP
SP, SP2SP2
SP2SP2
SP2 and tt
tt
t.
2 to 499 = SPSP
SPSP
SP, SP2SP2
SP2SP2
SP2 and tt
tt
tcan be always modified.
Select the secret code (to be remembered).
500 to 999: Selecting a secret code between
these two numbers, everything will occur as
explained above except that when the device
is “Locked” the parameters that can be
modified are the set points, the time and the
alarmthresholds.
NOTE: at a successive visualization of the P11
parameter, the instrument shows the value 2for
any set of P11 between 2 and 999.
P12 = Out maximum rate of rise
This limit will be used if PbPb
PbPb
Pb is different from 0 only.
Programmable from 1 to 25% of the out signal per
second.
Over 25%/s the instrument displays “InFInF
InFInF
InF” to
indicate the exclusion of the limitation.
This limit have no effect if the selected contol
algorithm is ON/OFF type (PB=0)
P13 = Not used
P14 = Protected parameters display
This parameter is available if P11 is not 0.
This parameter enables/disables the display of the
protected parameter during "operative mode".
OFFOFF
OFFOFF
OFF = the protected parameters are not displayed
ONON
ONON
ON = the protected parameters are displayed
P15 - SMART function enabling/disabling
0 = The SMART function is disabled
1 = SMART function enabling/disabling is
NOT protected by the safety code.
2 = SMART function enabling/disabling is
protected by the safety code.
P16 - Maximum value of the proportional band
automatically settable by the SMART
function
This parameter is available if P15 is not 0. It can
assume the following values:
model LME:
between P17 or P18 and 99.9%
model LDE:
between P17 or P18 and 100.0%
P17 - Proportional minimum band value
automatically settable by the SMART
function ( one control out only)
This parameter is only displayed if P5 is not 5 and
P15 is not 0.
It may be programmed from 1.0% to the value of
P16.
P18 - Proportional minimum band value
automatically settable by the SMART
function (two control outs, heating/
cooling)
This parameter is only present if P5 is 5 and P15
is not 0.
This parameter may be programmed from 1.5% to
the value of P16.
lxe-1-B00.p65 10/18/02, 3:47 PM10

11
GB
P19 = Automatic calculation of "relative
cooling gain"
This parameter is only present if P5 is 5 and P15
is not 0.
OFFOFF
OFFOFF
OFF = the SMART function does NOT calculates
the "relative cooling gain".
ONON
ONON
ON = the SMART function calculates the
"relative cooling gain".
P20 = Minimum integral time value calculated
by the SMART function
This parameter is only present if P15 is not 0.
It can assume the following values:
model LME:
between 0.1 (10 seconds) and 2.0 (2
minutes)
model LDE:
between 00.01 (1 second) and 2.00
(2 minutes).
P21 = Extension of the anti-reset-wind up
Span: from -30 to +30 % of the proportional band.
NOTE: a positive value increases the high limit of
the anti-reset-wind up (over set point) while a
negative value decreases the low limit of the anti-
reset-wind up (under set point).
P22 - Option selection (Out 3 or digital input)
0 = no option is present
1 = Alarm 2 output - Process alarm
2 = Alarm 2 output - Band alarm
3 = Alarm 2 output - Deviation alarm
4 = Digital input used for SP/SP2 selection.
5 = Timer mode 1 (see below)
6 = Timer mode 2 (see below)
7 = Timer mode 3 (see below)
8 = Timer mode 4 (see below)
9 = Timer mode 5 (see below)
10=Timer mode 6 (see below)
11=Timer mode 7 (see below)
Note:
1) Select P22 value in accordance with the
installedhardware.
2) Setting P22 equal to 1, 2 or 3, if AL2AL2
AL2AL2
AL2 parameter
is out of range, it will be aligned to its low limit.
3) Setting P22 equal to 4, 5 or 8, if SP2SP2
SP2SP2
SP2 parameter
is out of range, it will be aligned to rLrL
rLrL
rL value.
4) Setting P22 equal to 6 or 7, P5 parameter will
be forced to 0 and if SP2SP2
SP2SP2
SP2 parameter is out of
range, it will be aligned to rLrL
rLrL
rL value.
5) Setting P22 equal to 9 or 10, P5 parameter will
be forced to 0.
6) When P22 parameter pass from a value equal
or greater than 9 to e value lower than 9, at the
next start up the controll output will be forced to
"enabled".
Timer functions
Notes about all timer modes:
1)Atpoweroffthetimevalueandstatuswillbereset.
2)The time parameter (tt
tt
t) can always be modified
but the new value become operative at the next
start time only.
lxe-1-B00.p65 10/18/02, 3:47 PM11

12
GB
Timer mode 1 [P22=5]
If the logic input remains in open condition for
more than a programmed time the instrument
goes automatically at a stand by temperature
(SP2).
The time count is reset when the logic input is
closed.
For other details see paragraph "5.7 Timer
modes description".
Timer mode 2 [P22=6]
When the contact is closed, the instrument
controls using SP as operative set point.
When the contact has been opened the instrument
selects SP2 as operative set point and starts the
time count down.
Note that the guarantee soak function can be
applied to this timer mode (see P26 parameter)
When the time count is equal to 0 the instrument
comes back to the SP set point and the output 2
will be energized.
The Out 2 reset will be made when the logic input
will be closed again.
For other details see paragraph "5.7 Timer
modes description".
Timer mode 3 [P22=7]
When the contact is closed, the instrument
controls using SP as operative set point.
When the contact has been opened the instrument
operate as follows:
- it selects SP2 as operative set point
- it starts the time count down
- it energizes the Output 2
Note that the guarantee soak function can be
applied to this timer mode (see P26 parameter)
When the time count is equal to 0 the instrument
comes back to the SP set point and the output 2
will be reset.
For other details see paragraph "5.7 Timer
modes description".
Timer mode 4 [P22=8]
The instrument operates using SP set point and
the timer is normally reset.
When the instrument detects the transfer from
contact open to close it selects SP2 as operative
set point and starts the time count down.
Note that the guarantee soak function can be
applied to this timer mode (see P26 parameter)
When the time count is equal to 0 the instrument
comes back to the SP set point.
For other details see paragraph "5.7 Timer
modes description".
lxe-1-B00.p65 10/18/02, 3:47 PM12

13
GB
Timer mode 5 [P22=9]
The instrument start in "Power OFF" mode and it
remains in "Power OFF" mode until the contact is
closed.
When the contact has been opened the instrument
starts the control using SP set point and starts the
time count down.
Notes:
1) The guarantee soak function can be applied to
this timer mode (see P26 parameter)
2) The transfer from "Power OFF" mode to
AUTOMATIC mode starts the "Soft start" and
the "alarm masking" functions (if programmed).
When the time count is equal to 0 the instrument
comes back to the "Power OFF" mode and the
output 2 will be energized.
The Out 2 reset will be made when the logic input
will be closed.
For other details see paragraph "5.7 Timer
modes description".
Timer mode 6 [P22=10]
The instrument starts in "Power OFF" mode and it
remains in "Power OFF" mode until the contact is
closed.
When the contact has been opened the instrument
operate as follows:
- it starts the control using SP set point.
- it starts the time count down
- it energizes the Output 2
Notes:
1) The guarantee soak function can be applied to
this timer mode (see P26 parameter)
2) The transfer from "Power OFF" mode to
AUTOMATIC mode starts the "Soft start" and
the "alarm masking" functions (if programmed).
When the time count is equal to 0 the instrument
comes back to the "Power OFF" mode and the
output 2 will be reset.
For other details see paragraph "5.7 Timer
modes description".
Timer mode 7 [P22=11]
The instrument starts in "Power OFF" mode and it
remains in "Power OFF" mode until a transfer from
open to close of the logic input is detected.
When the instrument detects the transfer from
contact open to close it starts the control using SP
set point and starts the time count down.
Notes:
1) The guarantee soak function can be applied to
this timer mode (see P26 parameter)
2) The transfer from "Power OFF" mode to
AUTOMATIC mode starts the "Soft start" and
the "alarm masking" functions (if programmed).
When the time count is equal to 0 the instrument
comes back to the "Power OFF" mode .
For other details see paragraph "5.7 Timer
modes description".
lxe-1-B00.p65 10/18/02, 3:47 PM13

14
GB
P23 = Alarm 2 configuration
P23 is skipped when P22 ≠1, 2 or 3.
If P22 = 1 or 3
H.A.H.A.
H.A.H.A.
H.A. =
High alarm
with automatic reset
L.A.L.A.
L.A.L.A.
L.A. =
Low alarm
with automatic reset
H.L.H.L.
H.L.H.L.
H.L. =
High alarm
with manual reset
L.L.L.L.
L.L.L.L.
L.L. =
Low alarm
with manual reset
If P22 = 2:
H.A.H.A.
H.A.H.A.
H.A. =
out of band
with automatic reset
L.A.L.A.
L.A.L.A.
L.A. =
in band
with automatic reset
H.L.H.L.
H.L.H.L.
H.L. =
out of band
with manual reset
L.L.L.L.
L.L.L.L.
L.L. =
in band
with manual reset
P24 = Alarm 2 action
P24 is available when P22 is 1, 2 or 3.
rEUrEU
rEUrEU
rEU = reverse (relay de-energized in alarm
condition)
dirdir
dirdir
dir = direct (relay energized in alarm condition)
P25 = Stand-by of the alarm 2
P25 is available when P5 is 1, 2 or 3.
OFFOFF
OFFOFF
OFF = stand-bydisabled
ONON
ONON
ON = stand-byenabled
NOTE: The alarm stand-by function disables the
alarm indication at instrument start up and after a
set point modification until the process variable
reaches the alarm threshold.
P26 = treshould of the guarantee soak function
P26 is available when P22 is greater than 5.
This function stop automatically the time count
down when the measured value is out of the band
defined by the set point plus and minus P26 value.
- When P1 = 5 : P26 is programmable from 0.1 to
50.0 eng. units.
- When P1 ≠5 : P26 is programmable from 1 to
500 eng. units.
Above max value the display shows “OFF” and
this finction is disabled.
The configuration procedure is completed and the
instrument shows "CnFCnF
CnFCnF
CnF" on the display.
To quit the configuration, press SMT and FUNC
simultaneously (press first SMT and immediately
afterwards FUNC) keeping both the pushbuttons
pressed for three seconds.
lxe-1-B00.p65 10/18/02, 3:47 PM14

15
GB
5. OPERATIVE MODE
The display and modification of the operative
parameters can be protected by a secret code.
For more information see section 4.2.
5.1 PRELIMINARY COMMENTS
It is assumed, at this point, that the instrument has
been correctly configured as indicated in
Section 4.
- Model LME displays the value measured on the
upper display: the lower display is normally
used to display the operating set point (below
this condition is defined as “Normal display”).
- Model LDE displays the value measured (below
this condition is defined as “Normal display”) or,
alternatively, the operating set point (in this
case the SP led lights up).
To change from the display of the set point to
that of the value measured, or vice versa, press
pushbutton s.
All the parameters can be displayed sequentially
by pressing the FUNC pushbutton.
- Model LME displays the abbreviated name of
the parameter selected on the lower display, on
the upper display the value set.
- Model LDE displays alternatively the name of
the parameter and its value: during the
modification it displays only the value.
5.2 SMART ALGORITHM
This function gives best process control.
To enable the SMART function, press the SMT
pushbutton for more than 1.5 s, when the
instrument is in normal display mode. The SMT
LED will be lit continuously or flash according to
the algorithm automatically selected.
When the SMART function is enabled, the control
parameters (PBPB
PBPB
PB, TITI
TITI
TI, TDTD
TDTD
TD and rCrC
rCrC
rC) can be displayed
but not modified.
When it is dasired to disable the SMART function,
press the SMT pushbutton again (for more than
1.5 s) to turn the "SMART" OFF. The instrument
maintains the actual control parameters setting
and allows parameter modification.
NOTES:
1) During operation of the SMART function, the
relative cooling gain (if controlled by SMART) is
limited within the following ranges:
Cooling medium Span
Air 0.85 to 1.00
OIL 0.80 to 0.90
H2O 0.30 to 0.60
2) TheSMARTfunctionusesaderivativetimeequal
to 1/4 of the integral time.
3) The limits of the proportional band settable by
the SMART function are programmed by
parameters P16, P17 and P18 .
4) The lower limit of the integral time settable by
the SMART function is programmed by
parameter P20 .
5) When ON/OFF control is programmed (Pb=0),
the SMART function is disabled.
6) SMART enabling/disabling can be protected by
the safety lock (see parameter P15).
lxe-1-B00.p65 10/18/02, 3:47 PM15

16
GB
5.3 INHIBITION OF THE OUT SIGNAL (Power
OFF mode)
These products allow to turn the out signal OFF
manually to stop the control.
To turn the out signal OFF, press the s
pushbutton first and then press the FUNC
pushbutton.
NOTE:When this function is managed by the timer
function (timer modes 5, 6 and 7) the manual
enabling of this function is inhibit.
Keeping them both pressed for more than 3
seconds, the instrument will show “OFFOFF
OFFOFF
OFF” instead of
the set point value.
The instrument will display “OFFOFF
OFFOFF
OFF” instead of
indicating the set point; the out signal will switch
OFF and the instrument will work as a simple
indicator.
When the control outs are disabled, the alarms are
also disabled and forced to the no-alarm condition.
The modification of the control parameters is still
enabled.
Toreturntonormalcontrol,pressthespushbutton
first and then press the FUNC pushbutton.
Keeping them both pressed for more than
3 seconds, the instrument returns to normal
display mode.
The transfer from "Output Power OFF" mode and
normal control restarts "Alarm masking", "Soft
start" and "Output max rate of rise" functions as in
presence of e power up.
NOTES :
1) If the out is turned OFF when the SMART
function is performing the first part of the SMT
algorithm (LED SMT flashing), the SMART
function will be aborted and when the
instrument comes back to the normal control,
the SMART function will be disabled.
If the out is turned OFF when the SMART
function was performing the second part of the
SMT algorithm (LED SMT lit), the SMART
function will be stopped and, when the
instrument comes back to the normal control,
the smart function will also be activated.
2) If the instrument is turned OFF with the out
power off function enabled, at the next start up
this function will automatically be enabled
again.
5.4 DISPLAYING THE SET POINT SET
(model LDE)
To display the set point set, press the t
pushbutton. The SP led lights up.
The set point value will appear on the display.
To return to the display of the value measured
press pushbutton tagain.
5.5 SP/SP2 SELECTION
When P22 < 4 the set point 2 is not anailable.
When P22 = 4, it is possible to select the operating
set point (SP or SP2) by the logic input only (termi-
nals 11 and 12).
When P22 > 4 the set point selection is managed
by timer function and no manual selection is
available
5.6 DIRECT MODIFICATION OF
THE SET POINT
The instrument allows to modify the selectedc set
point value without to use the FUNC pushbutton.
When direct access to the selected set point
modification is required, proceed as follow:
1) Press pushbutton s or t for more than
2 seconds; the set point value will be
displayed and it will start to change.
lxe-1-B00.p65 10/18/02, 3:47 PM16
This manual suits for next models
1
Table of contents
Languages:
Other ero electronic Controllers manuals
Popular Controllers manuals by other brands
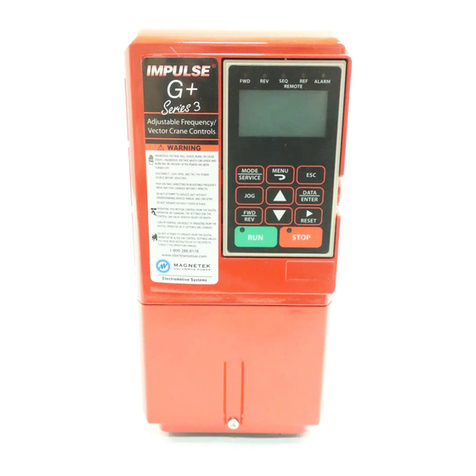
Magnetek
Magnetek IMPULSE G+ Series 3 Product guide

Elodrive
Elodrive BS-04P2E quick start guide
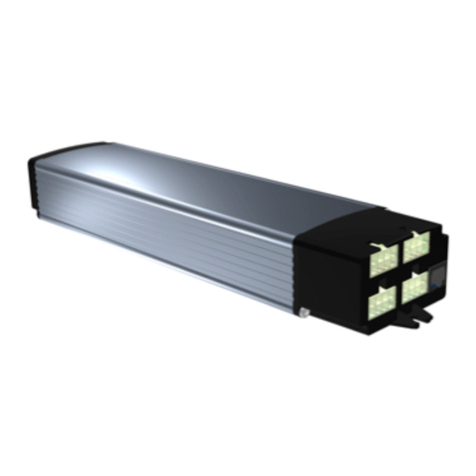
MOVETEC
MOVETEC LTC Series Installation and operating instruction
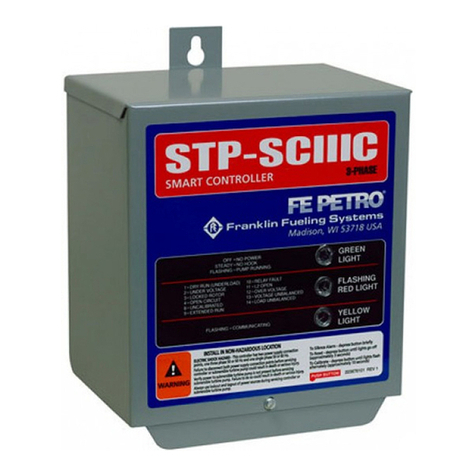
Franklin Fueling Systems
Franklin Fueling Systems STP-SCIIIC installation guide
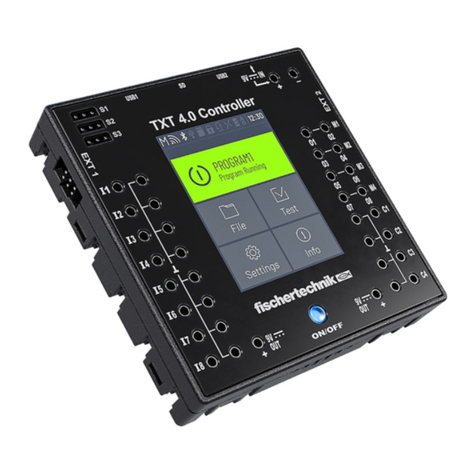
fischertechnik
fischertechnik ROBOTICS TXT 4.0 operating manual
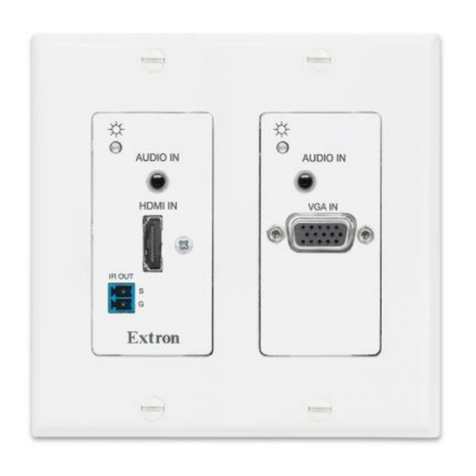
Extron electronics
Extron electronics MLC 104 IP PLUS quick start guide