MOVETEC LTC Series User guide

Installation and operating
instruction
LTC Series

Movetec Solutions ApS
-2 -
Table of Content
The LTC table controller - 5 -
Application - 5 -
Whom is this document prepared for - 5 -
Precondition for the use of this document - 5 -
Do not install system before programming! - 5 -
Safety instructions - 5 -
For all Laing Table Controllers and all accessories (products) please note: - 6 -
For the operation of height adjustable tables please note: - 6 -
Design of the table controllers - 6 -
Specifications - 7 -
Environmental conditions - 7 -
Dimensions - 8 -
Controller without OptoSense - 8 -
Controller with OptoSense - 9 -
Options - 9 -
Delivery contents - 9 -
Installation of the controllers - 10 -
Controllers without OptoSense - 10 -
Controller with OptoSense - 10 -
Controller with GyroSense - 11 -
Installation control panels - 12 -
Rectangular control panels - 12 -
Round control panels - 12 -
Oval control panels - 12 -
Electrical connection - 13 -
Connectable Motors - 14 -
Pin assignment controller - 14 -
- 14 -
Pin assignment motor - 14 -
Connection of the motors - 15 -
Connection of the control panels and other control options - 15 -
Control panels with cable - 15 -
Two control panels - 15 -
Up to 11 control panels - 16 -
OptoSense - 16 -
Wireless control panel - 17 -
Connection: - 17 -
Mounting: - 17 -
Pairing of the control panel to the controller - 17 -
Battery change - 18 -
Mains connection - 18 -

Instruction LTC 11_3 Movetec Solutions ApS
-3 -
Precondition start of operation of the controller - 19 -
Start of operation - 19 -
Current based collision detection - 19 -
GyroSense based collision detection - 20 -
Reference run - 20 -
Determine the stroke by the reference run - 21 -
Safety zone - 21 -
Safety Input - 21 -
Automatic motor recognition - 23 -
Control through control panels - 23 -
All Control panels - 23 -
Control panels with memory keys - 23 -
Control panels with height indication - 24 -
Configuration of the controller though the “LM” control panels (control panels without height
indication) - 24 -
Store memory positions with “LM” control panels - 24 -
User height limit adjustment by “LM” control panels - 25 -
Adjusting upper and lower limit - 25 -
Delete user height limits - 25 -
Change the sensitivity of the collision detection by “LM” control panels - 26 -
Initiate a reference run by “LM” - 26 -
Stroke limit adjustment by “LM” control panels - 26 -
Adjust upper and lower stroke limit - 26 -
Delete stroke limits - 27 -
Configuration of the controller though the “LD” control panels (with height indication) - 28 -
Operation of “LD” control panels with two buttons - 28 -
Store memory positions by the “LD” control panels - 28 -
Memory key handling by the “LD” control panels - 28 -
User height limit adjustment by the “LD” control panels - 29 -
Adjust upper and lower limit - 29 -
Delete user height limits - 29 -
Change the sensitivity of the collision detection by the “LD” control panels - 30 -
Initiate a reference run by the “LD” control panels - 30 -
Change height indication from centimeter to inch by the “LD” control panels - 30 -
Enter service menu by the “LD” control panel - 31 -
Rest user settings - 31 -
Stroke limitation adjustment by “LD” control panels - 32 -
Adjust stroke upper and lower limit - 32 -
Delete stroke limits - 33 -

Movetec Solutions ApS
-4 -
Shift height indication by the “LD” control panels - 33 -
Define rounding for height indication - 34 -
Activate BLE Module - 34 -
Reset controller name - 35 -
Activate the pairing mode - 35 -
Delete wireless control panel connections - 36 -
Reset private mode for APP - 36 -
Reset number of connected motors - 36 -
Reset Safety Adapter - 37 -
Controller control by OptoSense - 38 -
Synchronization of 2 Controllers by the control panel - 39 -
Synchronization of up to 6 controllers - 39 -
Port designation - 40 -
Configuration - 40 -
Connecting a PC to the HUB - 41 -
Connection of controllers to the HUB - 41 -
All controllers are configured the same way - 41 -
The configuration of the controllers to be connected is different - 41 -
Remaining connections - 42 -
Preconfigured HUB - 42 -
HUB startup - 42 -
Operation - 43 -
Identifier for the controller configuration - 43 -
HUB Menu handling - 43 -
Restart the HUB with „LD“ control panels - 44 -
Delete the configurations stored in the HUB with “LD” control panels - 44 -
Adjust the number of controllers connected to the HUB with “LD” control panels - 44 -
BLE Option - 45 -
WiFi Option - 45 -
Remote service through the Internet - 46 -
Connecting the cloud interface with the table controller - 46 -
Status and failure mode indicated by the LED - 48 -
Menu codes for control panels without height indication - 49 -
Menu codes indicated by the “LD” control panels - 50 -
Failure codes indicated by the control panels - 54 -
Sound signals - 60 -
Directives followed - 61 -
Approval for European Controllers (230V versions) - 61 -
Approval for USA and Canada (115V versions) - 61 -

Instruction LTC 11_3 Movetec Solutions ApS
-5 -
The LTC table controller
Thank you for purchasing our Controller. The well-shaped controllers can be
easily mounted below a table top or into a crossbar of a height adjustable table. A
variety of control panels and control modes enables the user to find the optimum
solution for many applications.
This instruction will show how to install and how to operate the controller.
Application
The LTC Controller series is designed and can be exclusively used to control
motors for the height adjustment of tables. Verify that the performance
parameters of the motors and the connections of the motors fit the parameters
and connections of the controller!
If used for other applications neither the function nor the safety can be ensured!
Therefore, such use is not permitted, and warranty will be voided if used in
applications outside the table height adjustment area.
Whom is this document prepared for
This document is an installation and operation instruction for the LTC series
Laing Table Controllers and its accessories. The document is dedicated to
manufacturers of height adjustable table frames and tables.
This document is not intended for end users!
Precondition for the use of this document
This document describes the installation and operation of the Controllers. It is
assumed, that the controller has been configured for the application in which it is
intended to be used! Program all parameters for the table the controller is
intended to be mounted to, before actual installation.
Do not install system before programming!
Safety instructions
Attention There are no user serviceable or repairable parts inside the controller!
Do not open the controller. If opened, the warranty will be void.

Movetec Solutions ApS
-6 -
For all Laing Table Controllers and all accessories (products) please note:
•Before any work is done with the products, read the instruction manual
and follow the instructions!
•The products may only be used as intended. Danger may occur if products
are used in another way or in other applications than the intended ones.
•The installation may only be performed by qualified personnel with the
required knowledge and the required capabilities!
•When making electrical connections, applicable electrical codes must be
observed in respect to the way the connection is made, as well as, who is
authorized to perform such connection.
•Electrical installations can only be made by authorized personnel!
•Operation outside the specified operation limits is not allowed!
•Operation outside the specified environmental limits is not allowed!
For the operation of height adjustable tables please note:
•Operation of a height adjustable table is only allowed after being instructed
by a person familiar with the product or after thorough study of the
instruction manual!
•Children are not allowed to play with the table!
•When operated, no persons are allowed on the table top!
•Danger of collision! The table must be placed in a way that it can operate
without colliding with any objects like drawers or window sills!
•Danger of injury by squeezing! The table must be placed and operated
so that no person can be squeezed between the table top or other parts of
the table and other objects in the vicinity of the table.
•Kids under the age of 8 and persons with mental or physical disabilities
are only allowed to operate the table if they have been sufficiently
familiarized with the operation of the table and if it is certain, that they will
not be over challenged by the operation of the table!
•Use of the table is only permitted in closed buildings where it can be
insured the no water or high humidity can get to the electrical parts!
The controllers are manufactured and tested using the utmost care. Should
there be a problem, please contact our service department.
Design of the table controllers
•Highly efficient switching power supply drives one, two, three or four motor
channels.
•The motor channels are controlled by a powerful processor.
•The processor can be configured to a wide variety of applications by an
easy to use configuration software.

Instruction LTC 11_3 Movetec Solutions ApS
-7 -
•The aluminum housing provides superior heat dissipation, that’s why in
most applications the cool down time is not determined by the controller
but by the motors connected to the controller.
•Port for the OptoSense Sensor
•GyroSense option
•Status indication by LED
•Remote service option by use of the Laing Cloud Interface
•A bus connection is provided for the following uses
oConnection of the control panels
oConfiguration of the controller (by PC)
oFirmware update
oSynchronization of up to six controllers.
•An internal extension port is provided for the following extension boards
oWiFi
oBLE
Specifications
Typ 3 Motor 4 Motor
Max. output power 380 W 380 W
Input Voltage 115 V 50/60 Hz 115 V 50/60 Hz
Input current
2 Motor
300 W
115 V 50/60 Hz
5,3 A 6,3 A 6,3 A
Frequency 50-60 Hz 50-60 Hz 50-60 Hz
Output voltage 24 V 24 V 24 V
Output current total 15 A 19 A 19 A
Motor channels 2 3 4
Max. current per channel 9 A 9 A 9 A
Standby power 250 mW 250 mW 250 mW
Synchronization by HUB or LD by HUB or LD by HUB or LD
Environmental conditions
For the controller and all accessories please note:
Maximum Environmental temperature for storage and transport -20°C to 60°C
-4°F to 140°F
Max. Environmental temperature for operation 5°C to 45°C

Movetec Solutions ApS
-8 -
41°F to 113°F
Max. Humidity for storage, transport and operation 95% non-condensing
Dimensions
Controller without OptoSense

Instruction LTC 11_3 Movetec Solutions ApS
-9 -
Controller with OptoSense
Options
The following options can be ordered with the controller
•WiFi Module, the controller will be supplied with an integrated WiFi
module. All table functions can be controlled through WiFi
•BLE module, the controller will be supplied with an integrated BLE module.
All table functions can be controlled through BLE, this can be done e.g. by
a smart phone app. This also is required for the wireless control panel.
•OptoSense option, the controller will be supplied with the OptoSense
sensor and a connector inside the controller for the OptoSense sensor.
This sensor allows the user to control the table by gestures.
•GyroSense Option, the controller will be supplied with an integrated
collision detection sensor.
Delivery contents
The controller will be supplied in bulk packages, these contain the controller only.
The power cable, the motor cables and control panels will be supplied in separate
bulk package boxes. The OptoSense sensors too will be supplied in separate
boxes. Fixing screws are not provided.

Movetec Solutions ApS
-10 -
Installation of the controllers
Controllers without OptoSense
The controller will be attached to the bottom of the table top by two screws, one
on each fixing point at the ends of the controller. A suitable fastener size is #8
wood screw. The length is determined by the thickness of the table top, however
it should be a minimum of ½ inch. When using other size screws, it is important,
that the shaft of the screw is not wider than the slot in the fixing point and that the
head is not bigger in diameter than 3/8 inch. The torque is determined by the
material of the table top, it is important, that the fixing points at the endcap of the
controller not be deformed!
The controller can also be mounted on the cross bar, in this case the mounting
can be done by M4 metric screws with a spring washer to secure the connection.
Important! When the GyroSense option is used, the controller must be mounted
onto the table top to insure proper operation.
Controller with OptoSense
The controller with OptoSense can only be mounted directly below the table top.
It cannot be mounted onto the cross bar!
The picture shows a cross section
through the controller and the table
top. It can be seen, that the centering
stud of the controller endcap reaches
into hole in the table top to position
the controller.
The picture shows the OptoSense
sensor, what has to be inserted
into the top of the controller
through a hole in the table top.

Instruction LTC 11_3 Movetec Solutions ApS - 11 -
First a 25/64” hole has to be drilled in the position where the OptoSense sensor
shall be located.
Then the controller will be positioned below the table top in a way that the
centering stud of the endcap on the motor connection side of the controller will
reach into the 25/64” hole. (see sketch).
Now the controller is positioned in reference to the table top. The controller can
now be screwed to the bottom of the table top by two screws one on each fixing
point at the ends of the controller. A suitable fastener size is #8 wood screw. The
length is determined by the thickness of the table top, however it should be
minimum ½ inch. When using other size screws, it is important, that the shaft of
the screw is not wider than the slot in the fixing point and that the head is not
bigger in diameter then 3/8 inch. The torque is determined by the material of the
table top, it is important, that the fixing points at the endcap of the controller will
not be deformed!
Now the OptoSense sensor can be inserted carefully into the hole in the table top
from the top of the table. Eventually the sensing element has to be rotated by a
maximum of 90° until it can be inserted with little force into the controller. Once
the edge of the transparent cover of the sensor reaches the table top the force
must be increased up to about 200N to insert the cover into the hole. The cover
must be pressed in until the rim of the cover reaches the surface of the table top.
The retention force of the transparent cap is dependent on the material of the
table top. Should the force be too big (too much force needed to insert) or too
little (sensor comes out easily) the diameter of the hole in the table top must be
adjusted in 4/1000th” steps up or down until the cover can be inserted with
maximum 200N and the sensor does not come out easily.
Controller with GyroSense
The sensing element of the GyroSense for the collision detection is contained in
the controller itself. This is why the controller with the GyroSense option must be
mounted directly to the bottom of the table top as otherwise the movement of the
table top cannot be properly sensed.
The standard setting assumes that the controller will be mounted in parallel to the
cross bar which connects the two legs of the table. Should the controller be
mounted perpendicular to the cross bar, the configuration of the controller must
be adapted to that. Without that, a reliable collision detection will not be possible.
For the successful function of the GyroSense, it is very important that the table
stands with all four legs on the floor so that it cannot wobble. If the table can
wobble the GyroSense may react to the wobbling instead of a collision.

Movetec Solutions ApS
-12 -
Installation control panels
Rectangular control panels
The square control panels will be mounted from the bottom to the edge of the
table top in a way that the keys will be easily accessible. The cable must be
attached to bottom of the table top in a way that it does not put tension on the
control panel or the controller but also does not hang loose.
Round control panels
For the installation of the round control panels a 2-3/8” through hole has to be
drilled into the table top. Then the cable will be put through the hole from the top,
then the control panel will be pressed from the top into the hole. Make sure the
control panel will only be pressed on the fringe or insert it by pressing with
a flat tool, covering the whole area of the control panel, on the control
panel. The cable must be attached to the bottom of the table top in a way that it
does not put tension on the control panel or the controller but also does not hang
loose.
Oval control panels
For the installation of the oval control panels an appropriate pocket and a ½” hole
have to be machined into the table top. The cable will be put through the hole
from the top, then the control panel will be pressed from the top into the pocket.
While inserting the control panel make sure the control panel will not be
pressed too hard, if required the size of the pocket has to be adjusted. The
cable must be attached to the bottom of the table top in a way that it does not put
tension on the control panel or the controller but also does not hang loose.

Instruction LTC 11_3 Movetec Solutions ApS - 13 -
The pictures show the required pocket for the oval control panels, to be machined
in the table top. Note, sizes in mm”
Electrical connection
The picture shows the output connection side of
the controller.
•1 Motor 1
•2 Motor 2
•3 Motor 3 (LTC 383 only)
•4 Motor 4 (LTC 384 only)
•5 Control panel and bus connection
4 3
2 1 5

Movetec Solutions ApS
-14 -
Connectable Motors
The controllers are designed to be connected to motors with the following ratings.
Besides the suitable rating, it is required that the motor connectors correspond to
the pin assignment shown under “Pin assignment for motors” below.
Nominal voltage 24 V
Maximum current 8 A
Number of hall sensors (90°) 2
Hall sensor supply voltage 5 V
Maximum current hall sensors 50 mA
Pin assignment controller
Pin assignment motor Pin assignment bus
1 Motor connection 1 9 +5V out
2 Hall sensor 1 10 RS 485 A
3 Ground 11 RS 485 B
4 Hall sensor +5 V 12 External +5V power
5 Optional 2 13 Analog control panel
6 Optional 1 14 Ground
7 Hall sensor 2
8 Motor connection 2
1
2
3
5
6
7
8
9
10
11
12
13
14
4

Instruction LTC 11_3 Movetec Solutions ApS - 15 -
Connection of the motors
The motors must have an 8 pole Molex plug and must comply with the
requirements described under “Connectable motors”
The motors may then be plugged into the connectors of the controller. When
plugged in, the snap in pin will retain the plug. Make sure to press the snap in pin
when unplugging a motor to avoid damage to the controller.
The motors must be connected in the order shown on the controller cover.
Connection of the control panels and other control options
Control panels with cable
The control panels with cable must be plugged into the connector (5) of
the controller. Make sure that the plug is locked by the snap in. To unplug
the snap in pin must be pressed, not doing so may result in controller
damage!
Two control panels
The controllers can be controlled by two control panels. To do so the Y-
connector has to be used. The connections must be made as shown on
the picture. One connection is made to the controller, one to a control
panel with height indication, one to a control panel without height
indication.

Movetec Solutions ApS
-16 -
Important! It is not possible to connect two control panels with height
indication or two control panels without height indication to one
controller. This will result in a malfunction of the controller! Should
more control panels be required see next step.
Up to 11 control panels
It is possible to control one controller by up to 11 control panels. To do so
the HUB LH 6 is required. The controller will be connected to one port of
the HUB, to the other ports of the HUB, control panels can be connected in
any combination of control panels with height indication and without height
indication.
Where a controller or control panel with height indication is connected a
control panel without height indication can be added by use of a Y-
connector.
The assignment of control panels to the HUB groups is done through the
HUB configuration. When more than one control panel controls one group,
the control panel activated first is in control, pressing a button on another
control panel while a control panel is still in use, will not have any effect.
This also applies to the control through OptoSense, BLE and Wifi.
OptoSense
When the OptoSense is used there is no control panel required!
The OptoSense is ready to use after insertion into the controller. In
addition to the OptoSense another control panel can be connected.

Instruction LTC 11_3 Movetec Solutions ApS - 17 -
Wireless control panel
Connection:
The wireless keyboard LM4RW can be connected to any controller what is
equipped with a BLE Module. Make sure the BLE Module in the controller is
activate through the Wizard or LD control panel before you go further.
Besides the wireless control panel additional control panels can be connected to
the controller.
Mounting:
It is mandatory, that the keyboard will be mounted in a position, from where
the movement of the table can be observed while pressing!
The LM4RW will be supplied with an adhesive tape on the bottom. Peel off the
protective film and glue the keyboard to the desired place. The place should not
be further away of the controller than about 5 feet. Where required the control
panel can be fixed with a screw too.
Pairing of the control panel to the controller
After plugging in to the mains, the controller it is ready for pairing for the first 15
seconds. If the controller is plugged in already, make sure, when you unplug it, to
wait until the LED in the controller goes off, so wait about 20 to 30 seconds and
only then plug it back in!
While the controller is ready for pairing, press the keyboard „UP“ and „Down“
keys on the control panel simultaneously, until you hear a sound from the motors
connected to the controller. If the melody goes upwards, the keyboard is paired to
the controller. Now the controller can be controlled by the keyboard.
When the keyboard has been paired to the controller before already, the pairing
action will result in an unpairing of the keyboard. This is indicated by a
descending melody given out by the motors. After being unpaired the controller
will not react to the keyboard commands any more.
The pairing can be started through the wizard too, on the „basic“ page. There the
pairing mode can be activated in the controller, pressing the „UP“ and
„Down“ key of the keyboard simultaneously within 15 seconds of activation of the
controller, will have the same effect as described above.
Up to 15 keyboards can be paired with one controller, and a keyboard can be
paired with an unlimited number of controllers.
To connect another keyboard or to connect the keyboard to another controller,
perform the described pairing procedure again with a different keyboard or a
different controller.

Movetec Solutions ApS
-18 -
When a keyboard is paired with more controllers, all controllers will start moving,
once they get the command by the keyboard. However, while the controllers start
and stop simultaneously, they will not be synchronized.
When more than one keyboard is paired to a controller, always the keyboard
pressed first, controls the controller. If another keyboard is pressed while the
movement, initiated by a keyboard is still in progress, this will not have any
effect.
Key functions, the key must be pressed and kept pressed:
Up Arrow: Table will move upwards
Down Arrow: Table will move downwards
“1” Key: Table will move to memory 1 position
“2” Key: Table will move to memory 2 position
Battery change
Once the controller will not react any more to the control panel the battery in the
control panel has to be changed. To do so, a blade has to be carefully inserted
between the top cover and the surface, the control panel is glued to, to lift off the
top cover. Then the battery can be changed on the PCB. It must be made sure,
that the key designation matches the printed designations on the PCB when the
cover is put back on the device.
Mains connection
After the connection of the motors and the control panels the controller can be
connected to the mains by plugging in the power supply cable to the connector
shown on the picture.
Make sure the power cable will be placed in a way what provides stain relief
to the plug so that the plug cannot be pulled out of the controller.

Instruction LTC 11_3 Movetec Solutions ApS - 19 -
Precondition start of operation of the controller
Before the start of operation make sure, that the parameter set suitable for the
table to be operated is loaded into the controller. If this not the case, the table
may make undesired movements, also required protection settings may not be
activated! Starting the controller with the wrong parameter set may result in
injury to the operator and damage to the table and the controller!
When operated, the table must be free of obstacles and must be able to
freely move over the whole movement range without hitting anything or
injuring anyone!
Start of operation
After mounting the controller and the control panels, making all electrical
connections and making sure that the right parameter set is loaded to the
controller, the table can be put into service.
Upon power up, the table makes a reference run to acquire the reference
position. To do so the “up” or “down” key must be pressed until the table reaches
the reference position (normally the lowest point or the position of a limit switch)
and further until the table elevates to the lowest programmed position. (this may
be about 25mm or 1” higher than the lowest position).
After the reference has been established, the table is ready for normal operation.
By pushing the “up” or the “down” key, the table can be moved between the
upper and the lower positions defined in the parameter set in the controller
specific for this table.
Current based collision detection
As a standard all controllers are equipped with a simple, current based collision
detection. This collision detection must be activated through the parameter set.
To achieve a satisfactory functioning of this features parameters specific to the
table must be defined and entered.
When activated the current based collision detection will stop the movement of
the table as soon as the table top hits an obstacle. After the stop the table top will
move in the opposite direction by the distance specified in the parameter set.
After that the “up” or “down” key have to be pressed again to move the table top.
Please note that the sensitivity of the current based collision detection on
down ward movements is reduced drastically if the table is loaded with
some weight!

Movetec Solutions ApS
-20 -
Should the performance of the current based collision detection not be
satisfactory, the use of the GyroSense Collision detection system is
recommended.
GyroSense based collision detection
The Laing GyroSense Systems provides collision detection between a table and
an obstacle. To enable that, controllers ordered with this option are equipped with
a very sensitive sensor that will sense even the smallest disturbance of the
table’s upward or downward movement.
This system ensures a reliable detection of a collision, as long as, the collision
leads to a very small change in position of the table top.
To sense such a change in position, the GyroSense equipped Controller must be
mounted to the table top. Placing the controller in the crossbar will not work!
Attention
Even if the system will sense reliably even very small unusual movements
of the table it cannot be 100% insured that this will avoid injuries of the
table users and persons around the table as also the mechanic of the table
and the environment of the table can cause such injuries! This is why no
liability can be accepted for personal injury or any other damage! It is the
user’s sole responsibility to make sure that personal injury and any other
damage is avoided throughout the operation of the table.
Reference run
At first start up, when the table legs have an uneven height or if the wrong height
is indicated, a reference run is required. For this the reference mode has to be
activated by pushing the down arrow 4 times.
When the reference mode is activated, all legs will move downwards with the
defined reference speed, when the “up” or “down” key is pressed. The
movements are synchronized until the first leg reaches its reference position,
after that the remaining legs will continue moving in the current mode until they
reach their reference position. After that the travel will be set to zero, that means
that the control panel will show the height above the floor. Then the drives move
upwards by the defined bottom margin.
The reference positions can be acquired by:
•Hitting the lower stop of the drive
•Reaching a middle switch
•Reaching a limit switch at the lower end what disconnects the motor
The method how to acquire the reference position must be set in the Wizard.
This manual suits for next models
3
Table of contents
Other MOVETEC Controllers manuals
Popular Controllers manuals by other brands
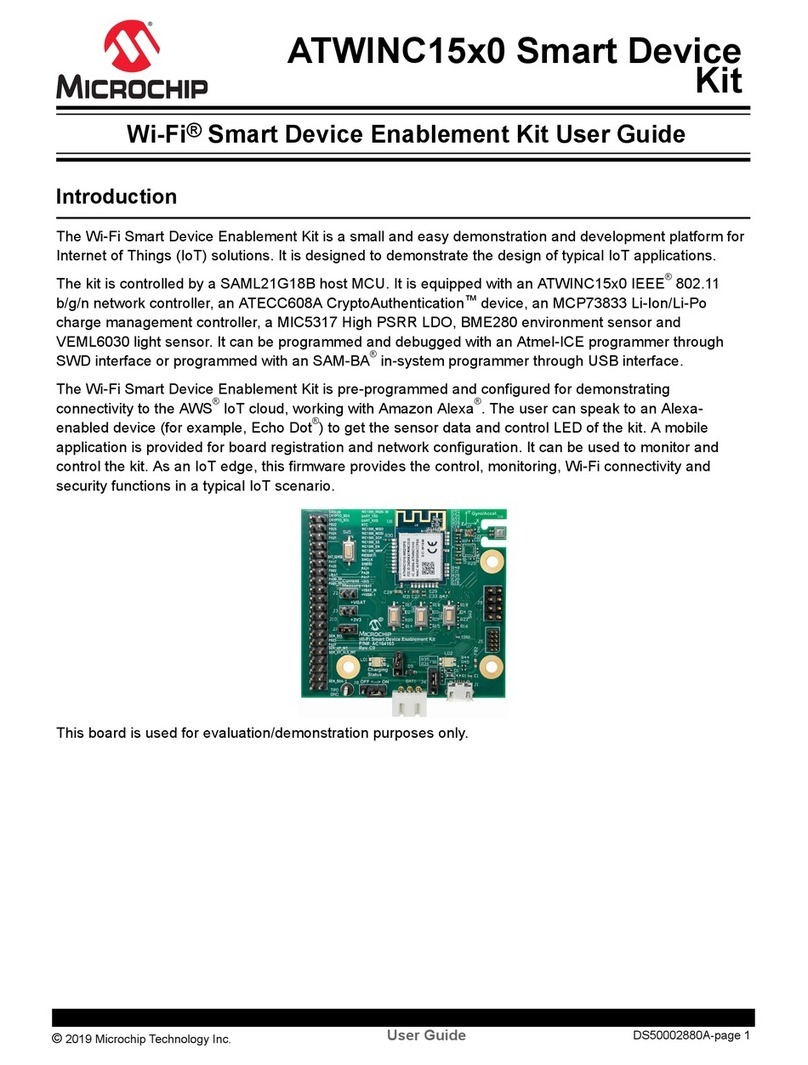
Microchip Technology
Microchip Technology ATWINC15x0 Series user guide
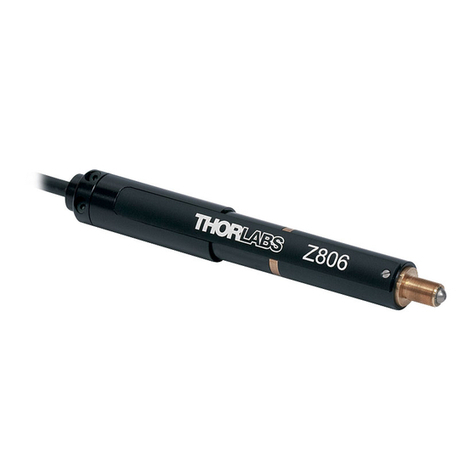
THORLABS
THORLABS Z8 Series user guide
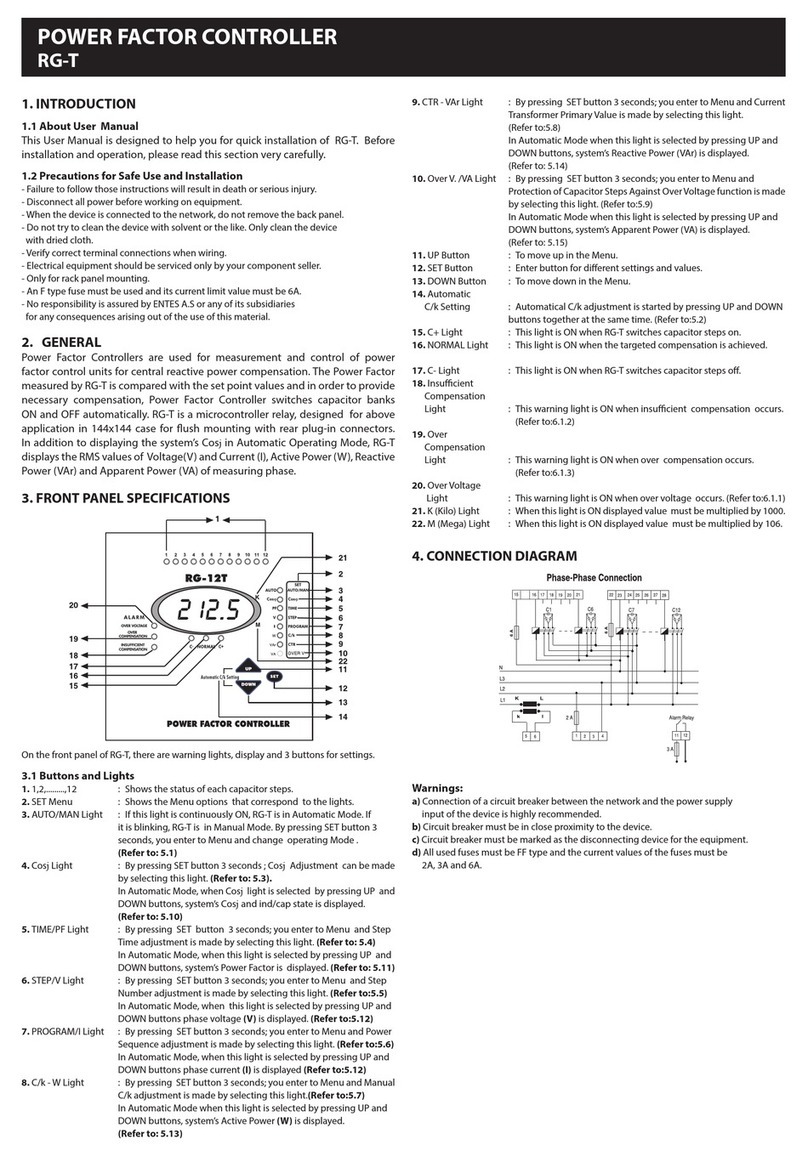
Entes
Entes RG-T quick start guide
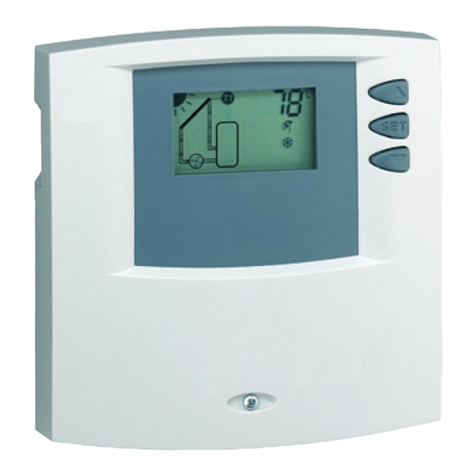
EAST COAST
EAST COAST tr 0301 Operating instructions and installation guide
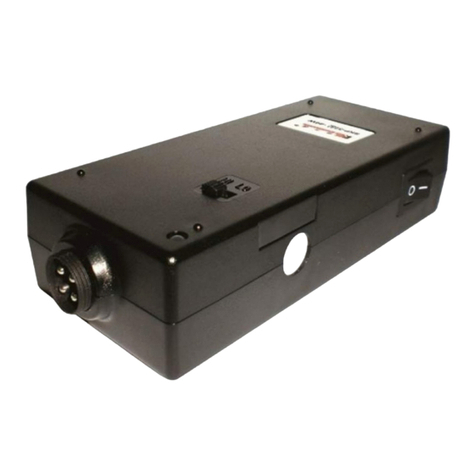
Kilews
Kilews SKP-32BC-60WN Operation and maintenance manual
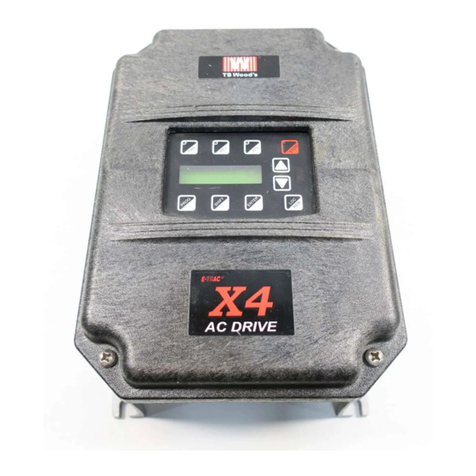
TB Wood's
TB Wood's X4 user manual