Erskine Attachments Cold Planer 18 User manual

Cold Planer 18 & 24
For
Skid Steer Loaders
Operator’s Manual
Maintenance
Parts Information
Read the Manual Before Use
Some dust created by power sanding, sawing, grinding, drilling, and other
construction activities contains chemicals known to the State of California to cause cancer, birth
defects or other reproductive harm. Some examples of these chemicals are:
Lead from lead based paints,
Crystalline silica from bricks and cement and other masonry products, and
Arsenic and chromium from chemically treated lumber.
Your risk from these exposures varies, depending on how often you do this type of work. To reduce
your exposure to these chemicals: work in a well ventilated area, and work with approved safety
equipment, such as those dust masks that are specially designed to filter out microscopic particles.

2
TABLE OF CONTENTS
REFERENCE INFORMATION
Write the serial number for your attachment in the spaces below. Always refer to this serial
number when calling for service or parts.
Serial Number………….._____________
YOUR ATTACHMENTS DEALER
ADDRESS:
PHONE:
CONTACT:
SAFETY
3-4
SERIAL NUMBER/DECAL LOCATION
5-6
MOUNTING INSTRUCTIONS
7-8
OPERATING INSTRUCTIONS
9-12
ROUTINE MAINTENANCE
13-15
PARTS INFORMATION
16-21
GENERAL SPECIFICATIONS
22
TROUBLESHOOTING
23-25
NOTES
26
WARRANTY
27
NOTE: Erskine Attachments LLC reserves the right to make
improvements in design or changes in specifications at any time without
notice and without incurring any obligations to install them on units
previously sold.

3
The user is responsible for inspecting the machine
daily, and for having parts repaired or replaced when
continued use of the machine would cause damage,
excessive wear to other parts or make the machine
unsafe for continued operation.
If an operating procedure, tool device, maintenance
or work method not specifically recommended is
used, you must satisfy yourself that it is safe for you
and others. You must also ensure that the
attachment will not be damaged or made unsafe by
the procedures you choose.
Erskine Attachments LLC cannot anticipate every
possible circumstance that might involve potential
hazard. The safety messages found in this manual
and on the machine are therefore not all inclusive.
The signal words CAUTION, WARNING, or
DANGER are used to indicate hazards.
Indicates a potentially
hazardous situation which, if not avoided,
may result in minor or moderate injury.
Indicates a potentially
hazardous situation which, if not avoided,
could result in death or serious injury.
Indicates a potentially
hazardous situation which, if not avoided,
will result in death or serious injury.
The word IMPORTANT, is used in the text when
immediate damage will occur due to improper
technique or operation.
The word NOTE is used to convey information that
is out of context with the manual text; special
information such as specifications, techniques,
reference information, and other information of a
supplementary nature.
SAFETY
DO NOT use or perform maintenance on this machine until this manual has been
read and understood. In addition, read the Operation and Maintenance Manual(s)
pertaining to the attachment and the attachment carrier (“Loader”).

4
Improper operation can cause serious
injury or death.
Pre-operation
This attachment is designed to be used for both
asphalt and concrete milling operations. NEVER
use this machine for any other purpose.
Read the operators manual for the “Skid Steer
Loader.” NEVER allow untrained people to
operate.
Operating instructions must be given to everyone
before operating this attachment and at least once
a year thereafter in accordance with OSHA
regulations.
NEVER exceed the maximum recommended input
power or speed specifications for the attachment.
Over-powering or over-speeding the attachment
may cause personal injury and/or machine
damage.
Keep all shields, guards, and covers in place.
Do not modify equipment or add attachments that
are not approved by Erskine Attachments LLC.
Use adequate safety warning lights and devices as
required by local regulations. Obey all local laws
and regulations regarding machine operation on
public property.
Operation
Always wear eye protection that meets z87.1 or
use with a loader enclosure that provides similar
protection.
Hydraulic connections may be hot after use. Use
gloves if connecting or disconnecting after use.
Check and be sure all operating controls are in
neutral before starting the engine.
Milling concrete and asphalt can release dust
containing silica. According to OSHA, exposure to
silica can result in respiratory diseases (affecting
your ability to breath), including silicosis, lung
cancer, and kidney disease. Refer to OSHA for
more information about controlling exposure to
silica. Occupational use of this attachment may be
subject to OSHA regulations specific to respirable
silica.
SAFETY ________ _
Operation (continued)
Keep people away from loader, attachment and
discharge when in use. This attachment sends
objects flying and has rotating parts. NEVER
direct discharge toward people –rocks and
debris can be thrown.
NEVER operate near embankments or terrain
that is so steep that rollover could occur.
Always stay in the operator position when using
the attachment.
Before leaving the operators position, disengage
hydraulic drive, lower the attachment to rest flat
on the ground, stop engine, set park brake, and
wait for all motion to stop.
NEVER place hands in the discharge area or
clear debris while the engine is running.
Avoid High Pressure Fluids Hazard
Escaping fluid under pressure can
penetrate the skin causing serious
injury.
Avoid the hazard by relieving the
pressure before disconnecting
hydraulic lines.
Use a piece of paper or cardboard, NOT BODY
PARTS, to check for suspected leaks. Wear
protective gloves and safety glasses or goggles
when servicing or performing maintenance on
hydraulic systems.
If an accident occurs, see a doctor immediately.
Any fluid injected into the skin must be surgically
removed within a few hours or gangrene may
result.
Maintenance
NEVER make adjustments, lubricate, clean, or
perform any service on the machine while it is in
operation.
Make sure the attachment is serviced on a daily
basis. Improper maintenance can cause serious
injury or death in addition to damage to the
attachment and/or your equipment.

5
SERIAL NUMBER AND SAFETY DECAL LOCATIONS
Serial Number Location:
It is important to refer to the serial number of the attachment when making repairs or ordering parts. Early or later
models (identification made by serial number) may use different parts, or it may be necessary to use different
procedures in doing a specific operation.
D
Part Number: 200001
Location: On left endplate of
frame near valve
Quantity: 1
B
Part Number: 314890
Location: On left endplate
Quantity: 1
A
Part Number: 421519
Location: Under front shield
Quantity: 1
C
Part Number: 501612
Location: On end plates
and frame LH & RH
Quantity: 4

6
SERIAL NUMBER AND SAFETY DECAL LOCATIONS
Safety Decals Locations:
The locations of the safety decals are shown. If
these decals are missing, damaged, or painted over
they must be replaced. Call Erskine Attachments
LLC (218-435-4045) for replacement decals.
M
Part Number: 314492 (RED ANGLE)
Location: On pivot w/a below depth gauge
Quantity: 1
J
Part Number: 314493 (RED DEPTH)
Location: On each gauge pointer
Quantity: 2
G
Part Number: 319439
Location: On valve block shield
Quantity: 1
I
Part Number: Model Decal
314877 (CP24) or 314878 (CP18)
Location:
On front shield
Quantity: 1
F
Part Number: 320025
Location:On endplates of
frame near rear
Quantity: 2
Small Brand Decal
Location: On endplate near valve and on
right depth shoe
Quantity: 2
E
Part number: 320359
Location: On LH endplate of
frame near front
Quantity: 1
H
Part number: 203234
Location: On each side of cutter
frame
Quantity: 2
K
Part Number: 314875
Location: Top LH tube of Frame
Quantity: 1
L
Part Number: 313391
Location: RH rear of Cutter frame
Quantity: 1
N
Part Number: 314796
Location:
On back of main body weldment
Quantity: 1
Large Brand Decal
Location: On front of cutter shield
Quantity: 1

7
MOUNTING INSTRUCTIONS
After uncrating the attachment, use the following procedure to mount the Cold Planer to the loader.
WARNING! Coupler wedges or pins must extend through the holes in the attachment
mounting plate. Levers must be fully down and locked. Failure to secure wedges or pins
can allow attachment to come off and cause injury or death.
1. Use the steps, treads, and grab handles
to get on and off the loader and
attachment.
2. Sitting in the operator’s seat, lower seat
bar and fasten the seat belt.
3. Drive the loader to the rear of the
attachment. Put the loader quick attach
coupler into the attachment mounting
bracket.
4. Tilt the loader coupler backward a small
amount until it is fully engaged in the
attachment mounting bracket.
5. Stop the engine and engage the park
brake.
6. Secure the coupler locking mechanism
that attachesthe attachment to the loader.
Hydraulic Connections
Mounting Plate Connections

8
MOUNTING INSTRUCTIONS
7. Connect the hydraulic quick couplers from the
attachment to the loader.
IMPORTANT: Make sure the quick couplers
are fully engaged. If the quick couplers do not
fully engage, check to see that the couplers
are the same size and brand. Donotforcethe
quick couplers together.
IMPORTANT: Wipe the ends of the hydraulic
quick couplers (both lead and loader) with a
rag to remove any possible contamination.
Contamination can cause hydraulic
components to fail and is not covered under
warranty.
NOTE: See the Loader’s Operation and
Maintenance Manual.
NOTE: Attachment is shipped with 12FJX (1-
1/16” Female JIC Swivel) fittings on the ends
of the lead hoses
8. Connect the wire harness to the loader’s wire
harness receptacle. (Disregard if a pistol grip
controller is supplied with the attachment.)
Make sure the hoses are properly routed to fit
your specific loader. If the hoses are not
routed correctly, hoses may get pinched or
rub on tires. Be sure tocheck thehoserouting
through the full range of intended motion of
the attachment before operating it.
More than one routing may be acceptable
depending on the loader. Pick the routing that
best suits your loader.
IMPORTANT: Proper hose routing is the
responsibility of the owner and/or operator.
Pinched or stretched hoses are not covered
under warranty.
Mounting is now complete and you are ready to
use the attachment. Use the above instructions in
a reverse order to dismount the attachment from
the loader.
14 Pin Wire Harness Connection
CP24 Ready for Operation

9
OPERATING INSTRUCTIONS
Operation
1. With the operator in the seat of the loader, the
seat belt fastened and the seat bar lowered (if so
equipped), start the engine.
2. Activate the high flow auxiliary hydraulic system
to start the drum rotation, and then making sure
to increase the loader engine to full throttle.
IMPORTANT: Engine must be at idle speed when
engaging auxiliary hydraulic system.
NOTE: Certain loaders may not operate in high
flow mode without a special wire harnesses.
Others require the control switches to beoperated
in a specific way. It may also be necessary to
switch the hose couplers around to match your
loader. (See the loader’s operation and
maintenance manual)
3. With the loader boom lowered completely and the
auxiliary hydraulics engaged, slowly rotate the
loader coupler forward until the attachment skid
shoes are in contact with the ground.
4. Before advancing with the loader, slowly raise the
left and right skid shoes until the desired depth of
cut is achieved. (Up to 6” for most models)
NOTE: For optimal performance, the majority of the
weight of the front of the skid steer should be placed
upon the planer with the loader arms fully lowered.
The transfer of skid steer weight to the attachment will
result in a smoother and faster milling operation. The
loader arms should never be placed in the float
condition: excessive vibration will result.
NOTE: In some cases the drum rotation may stall
when the load on the planer is too high. This is most
likely the result of excessive ground speed. The
hydraulic reliefs on board the loader are designed to
prevent damage to the hydraulic system by diverting
all flow from the planer motor. If this occurs, stop or
slightly reverse the forward progress of the skid steer
and allow the drum to return to full operating speed
before continuing.
NOTE: Be aware that the wheel motor will lose power
while the other auxiliary functions are in operation.
Depth of Cut Indicator
Cutting Head Rotate Indicator

10
OPERATING INSTRUCTIONS
Cutting Head Rotation and Side Shift Operation
1. Roll the skid steer arms fully back and raise the
planer 12 to 15 inches off the ground.
IMPORTANT: Planer must be raised above the
ground while operating the side shift and head
oscillation adjustment features.
2. Activate the auxiliary hydraulic system in reverse
flow to operate the functions.
NOTE: The planer head is designed not to rotate
when the oil flow is activated in the reverse
direction, although a small amount of rotation may
be seen with some loaders.
3. Proceed to use the left or right side shift control on
the pistol grip harness as specified in the manual.
If these functions are controlled by the loader, see
the skid steer specific control instructions.
Pistol Grip Harness Control
Skid Loader Cab Controls
CAT D Cab Controls

11
Large Area Multi-Pass Milling
Multiple passes can be used to remove material down to depths greater than the Planer’s single pass
capabilities. This is done by milling the entire surface, removing all the spoil, and then returning to mill
the entire surface again and so on until the required depth is achieved.
OPERATING INSTRUCTIONS
Large Area Single Pass Milling
The independently controlled skid shoes allow
for continuous milling at a consistent depth
across large areas. This is achieved by setting
the desired depth of cut for the skid shoe on the
unmilled side of the planer and setting the other
skid shoe down so that it will cut flush with the
previously milled surface. The skid shoe that is
on the previously milled surface can be used as
a physical guide for the planer and slid
alongside the edge of the pavement that is
currently being milled by the planer.
Pass 3
Pass 2
Pass 1
NOTE: Spoil should be removed from the surface prior to attempting each additional pass.
Pass 1
Pass 2
Pass 3
Previously
milled surface
Unmilled surface

12
OPERATING INSTRUCTIONS
Pass 1
Pass 2
Pass 3
Pass 4
Manual cleanup
areas
Manhole cover /
storm drain
Taper Cuts
The independently controlled skid shoes and
rotating head allow for tapered cuts along the
perimeter of any paved surface. This works well
for patching old pavement, or joining new paved
surfaces together by creating a smooth
transition between the surfaces being joined.
The suggested method is to plunge the planer
head down to the deepest part of the taper for
the first pass, then proceed either direction from
the first pass until the desired profile is
achieved.
Milling Around Foreign Objects
The side shift feature gives the
operator a clear line of sight down
alongside the planer head which
allows milling to be achieved up close
to objects that cannot otherwise be
milled. The suggested method is to
mill a minimum of four passes around
the object and then manually clean up
the areas that weren’t able to be
milled.
The side shift feature can also be
used to mill up next to curbs. This can
be accomplished by removing the
right skid shoe and side shifting the
planer head completely to the right
side. (See page 17 for skid shoe
removal.)
IMPORTANT: Make sure the
operator has a clear line of sight
alongside the planer head so that
damage will not occur to the planer
or manhole cover / storm drain.

13
DAILY INSPECTION
Follow the cold planer service schedule for routine maintenance.
Check the following items every 8 hours of operation:
1. Check teeth and holders for cracks or excessive damage. Replace if necessary.
2. Check entire attachment for weld cracks or excessive damage. Repair if necessary.
3. Check all hardware. Retighten if necessary.
4. Check shields. Repair if damaged or replace if necessary.
5. Check for damaged or missing decals. Replace if missing.
6. Check for damaged or leaking hydraulic hoses or fittings. Replace if necessary.
7. Lubricate all pivot points.
8. Spray the drum with diesel fuel to allow the teeth to rotate freely in the holders.
9. Grease the three main bearings. No more than 2 pumps of grease every 40 hours.
___ _ ROUTINE MAINTENANCE
WARNING! Lower the attachment to rest, shut down the engine, relieve the
hydraulic pressure to the attachment, wait for all motion to stop, and set park
brake before leaving the operator’s seat to perform service of any kind. If
servicing attachment while attached to a skid loader, make sure that the
hydraulic couplers are disconnected.
It is the operator’s responsibility to make daily inspections of the loader and attachment for damage, loose bolts,
fluid leaks, or anything else that could cause a potential service or safety problem. Preventive maintenance is
the easiest and least expensive type of maintenance.
IMPORTANT: Bolts and set screws can loosen after initial usage. After the first hour of operation check all
bolts and set screws.
IMPORTANT: Fluids such as engine oil, gear lube, and hydraulic fluid must be disposed of in an environmentally
safe manner. Some regulations require that certain spills and leaks be cleaned in a specific manner. Check local,
state, and federal regulations for the correct disposal.
8

14
ROUTINE MAINTENANCE
Pick Inspection, Setup, Removal, & Installation
Inspection:
The factory installed carbide picks are specifically
designed to be a wear product. The life expectancy
of the picks will depend greatly on the hardness, the
abrasiveness, and the thickness of the material
being cut. It is also very critical that the picks rotate
freely in the holders to maintain even and consistent
wear throughout the life of the picks. A normal pick
wear progression is depicted to the right. The pick
seen furthest to the right is an example of one that
should be replaced, with the carbide almost gone
and the body is nearly worn to the base.
IMPORTANT: Continued use of the picks beyond
this point will have adverse effects, such as poor
productivity, possible cutter head failure, and other
costly repairs.
NOTE: Examples of abnormal pick wear causes and
solutions are on page 23.
NOTE: See the parts explosion on page 17 for
replacement pick packages and part numbers.
Cold Planer Tooth Replacement
Always wear safety glasses
when performing this operation. Hardened
tools can shatter causing injury.
1. Open the front cover to allow free access to the
cold planer drum.
2. Make sure the cold planer cutter head is
positioned in such a way that the drum is allowed
to rotate freely.
3. The tooth removal tool included with the planer
should be used to remove the teeth from their
holders.
4. To remove a tooth, place the fork end of the tool
into the grove in the tooth and strike raised area
on the tool with a hammer until the tooth is
removed.
5. To install a new tooth, place the fork end of the
tool into the grove in the tooth and set the shank
end of the tooth over the hole in the tooth holder.
6. Then strike the raised area on the tool with a
hammer until the tooth is fully seated into the
tooth holder.
7.
Old Tooth Removal
New Tooth Installation
Pick Wear Progression
Replace

15
Recommended Lift Points
for Drum Removal
ROUTINE MAINTENANCE
Cold Planer Drum Replacement
1. Position the cold planer in a location that will allow
the use of a hoist to lift the planer off the drum.
2. Remove the right side skid shoe (11) first, by
removing the two large retaining washers (25) and
then the guide plate (16). See page 19.
3. Remove the eight M20 hex flange nuts that secure
the drum to the wheel motor.
4. The drum should slide away from the motor easily
with the use of a pry bar. Watch the teeth for any
clearance issues when sliding out the drum.
5. Lift the planer off the old drum using the
recommended lift points.
6. Hoist the planer down on top of the new drum and
reinstall the parts and hardware in a reverse order.
IMPORTANT: Make sure the drum is oriented in the
proper direction when installing. The proper orientation
is as follows. When facing the hub side of the motor,
rotation will be in a CCW direction. Therefore the teeth
on the drum should also be pointing in a CCW direction.
See image to the left for verification.
Drum Rotation Direction

16
PARTS INFORMATION___________________
ITEM
QTY
PART NO.
DESCRIPTION
STOCK NO.
1
1
314700
MOUNT FRAME CP W/A
1.1
1
319500
MOUNT FRAME CP MULTIHOG W/A
MULTIHOG MOUNT ONLY
2
1
314701
BODY MAIN 24 W/A
1
314838
BODY MAIN 18 W/A
3
1
314702
PIVOT 24 COLD PLANER W/A
1
314839
PIVOT 18 COLD PLANER W/A
3.1
1
319501
PIVOT MOUNT CP MULTIHOG 18 W/A
MULTIHOG MOUNT ONLY
1
501502
PIVOT MOUNT CP MULTIHOG 24 W/A
MULTIHOG MOUNT ONLY
4
2
314405
SKID SHOE CP W/A
5
10
13207
BOLT HEX
1/2 X 1-1/4 NC GR 5
6
4
15307
BOLT HEX
5/8 X 1-1/4 NC GR 8 YZ
7
4
33630
WASHER LOCK
5/8”
8
2
314449
BUSH 1.25 X .53 X .70
11
1
319504
PLATE SKID SHOE RH CP PAINTED
314706
SKID SHOE RH W/A
OBSOLETE
16
2
314777
PLATE GUIDE PAINTED
17
2
314808
PLASTIC U-CHANNEL 24
2
314861
PLASTIC U-CHANNEL 18
18
1
314779
BACKING PLATE 26 PAINTED
1
314860
BACKING PLATE 20 PAINTED
20
1
314810
PLASTIC ROTATION DISK
25
4
314656
WASHER .53ID X 2.75OD X .25 Z
26
4
318058
BUSHING 1.75 x 1.27 x .63
(USE ANTI-SIEZE)
32
2
316026
PIN 1 X 5 W/A
34
18
33626
WASHER LOCK 1/2
38
4
37212
NUT REV LOCK
3/8 NC
56
2
315308
PIN LYNCH 1/4
70
5
13107
BOLT HEX
3/8 X 1-1/4 NC GR 5
72
10
13212
BOLT HEX (USE LOCK TITE)
1/2 X 2-1/4 NC GR 5
75
1
37217
NUT REV LOCK
3/4 NC
81
2
314894
WASHER PLASTIC .53 X 2.75
82
2
13207
BOLT HEX (USE LOCK TITE)
1/2 x 1-1/4 NC GR 5
88
1
13371
BOLT HEX
3/4 X 4-1/2 NC GR 5

17
PARTS INFORMATION___________________

18
PARTS INFORMATION___________________
ITEM
QTY
PART NO.
DESCRIPTION
STOCK NO.
3
2
314405
SKID SHOE CP W/A
4
1
314703
LIFT ARM 24 LH W/A
1
314842
LIFT ARM 18 LH W/A
5
1
314704
LIFT ARM 24 RH W/A
1
314841
LIFT ARM 18 RH W/A
6
1
314707
COVER FRONT 24 W/A
1
314843
COVER FRONT 18 W/A
7
2
314709
DEPTH GAUGE POINTER W/A
8
1
314708
DEPTH GAUGE W/A
9
1
314710
DRUM 24 COLD PLANER W/A
1
314840
DRUM 18 COLD PLANER W/A
10
1
319503
PLATE SKID SHOE LH CP PAINTED
1
314705
SKID SHOE LH W/A
OBSOLETE
11
2
314449
BUSH 1.25 X .53 X .70
12
1
314786
SHIELD CYLINDER 24 LT PAINTED
(314797 UNPAINTED)
1
314865
SHIELD CYLINDER 18 LT PAINTED
(314864 UNPAINTED)
13
1
314787
SHIELD CYLINDER 24 RT PAINTED
(314798 UNPAINTED)
1
314867
SHIELD CYLINDER 18 RT PAINTED
(314866 UNPAINTED)
16
2
314777
PLATE GUIDE PAINTED
(314761 UNPAINTED)
21
3
314817
BRG 2 PLW BLK
22
1
314812
TRIM HOLE COLD PLANER
25
4
314656
WASHER .53ID X 2.75OD X .25 Z
26
4
318058
BUSHING 1.75 x 1.27 x .63
30
3
400041
PIN 1 X 4 W/A
31
48
314830
TOOTH BULLET CP/RS CONCRETE
18” COLD PLANER
60
314830
TOOTH BULLET CP/RS CONCRETE
24” COLD PLANER
33
1
314741
ROD HINGE PIN .38 X 25.5 Z
24” COLD PLANER
1
314868
ROD HINGE PIN .38 X 19.5 Z
18” COLD PLANER
34
18
33626
WASHER LOCK
1/2"
35
26
33630
WASHER LOCK
5/8"
36
6
37214
NUT REV LOCK
1/2 NC
38
6
37212
NUT REV LOCK
3/8 NC
40
1
103880
WASHER LOCK
3/8”
41
1
36306
NUT HEX FULL
3/8 NC
42
2
65076
PIN COTTER 1/8 X 1
55
10
15311
BOLT HEX
5/8 X 2 NC GR 8 YZ
56
2
315308
PIN LYNCH 1/4
24”
3
315308
PIN LYNCH 1/4
18”
65
2
24949
SCREW SET 5/16 X 1/2 DOG POINT
69
2
317605
RUBBER LATCH BRACKET
70
5
13107
BOLT HEX
3/8 X 1-1/4 NC GR 5
72
10
13212
BOLT HEX
1/2 X 2-1/4 NC GR 5
76
1
33022
WASHER FLAT1”
18” COLD PLANER ONLY
77
1
314844
ARM PIVOT 18 W/A
18” COLD PLANER ONLY
78
1
314863
PIN 1 X 3.31 Z
18” COLD PLANER ONLY
79
10
41125
RIVET 3/16 STEEL #64
80
6
33012
WASHER FLAT
1/2"
81
2
314894
WASHER PLASTIC .53 X 2.75
82
2
13207
BOLT HEX
1/2 X 1-1/4 NC GR 5
83
9
19929
BOLT 3/8 X 3/4 NC FLG GR 5

19
PARTS INFORMATION___________________

20
PARTS INFORMATION
ITEM
QTY
PART NO.
DESCRIPTION
STOCK NO.
14
1
314781
PLATE PIVOT KEEPER PAINTED
(314774 UNPAINTED)
15
1
314784
SHIELD CP VALVE PAINTED
(314783 UNPAINTED)
19
1
314809
PLASTIC RETAINER DISK
25
4
314656
WASHER .53ID X 2.75OD X .25 Z
34
8
33626
WASHER LOCK
1/2"
35
22
33630
WASHER LOCK
5/8"
37
2
32467
BOLT FLG THRD RLNG
3/8 X 3/4 NC GR 5
40
4
103880
WASHER LOCK
3/8"
55
12
23510
BOLT SOCKET CAP SCREW
5/8 X 1-3/4 NC GR 5
66
1
320795
TOOL PICK REMOVAL ASPH/CONCRT
REPLACED 314874
1
314874
TOOL BIT REMOVER ASSEMBLY
REPLACED BY 320795
73
4
13205
BOLT HEX
1/2 X 1 NC GR 5
83
9
19929
BOLT 3/8 X 3/4 NC FLG GR 5
86
3
103116
BOLT HEX
3/8 X 1 UNC GR5
This manual suits for next models
1
Table of contents
Popular Compact Loader manuals by other brands

Southworth
Southworth PalletPal 360Air owner's manual
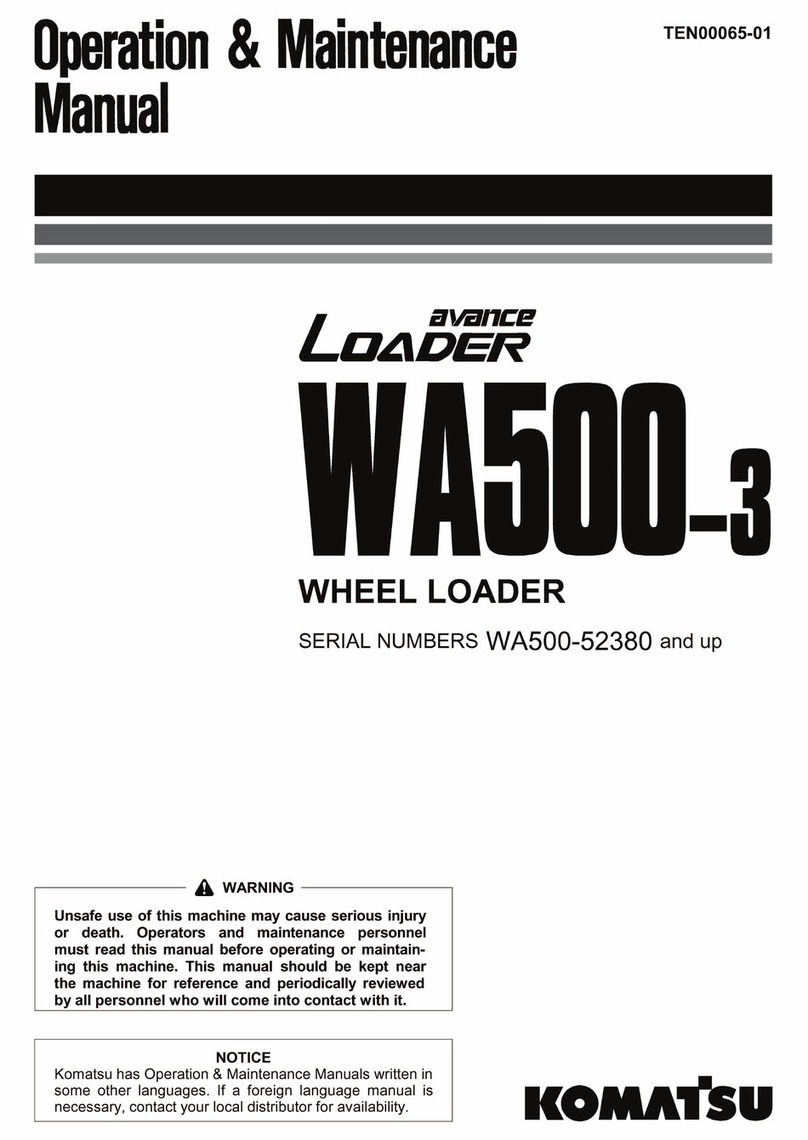
Komatsu
Komatsu Avance WA500-3 Operation & maintenance manual
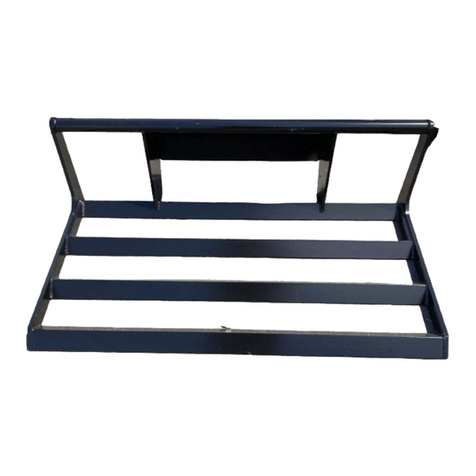
Toro
Toro 23165 Operator's manual
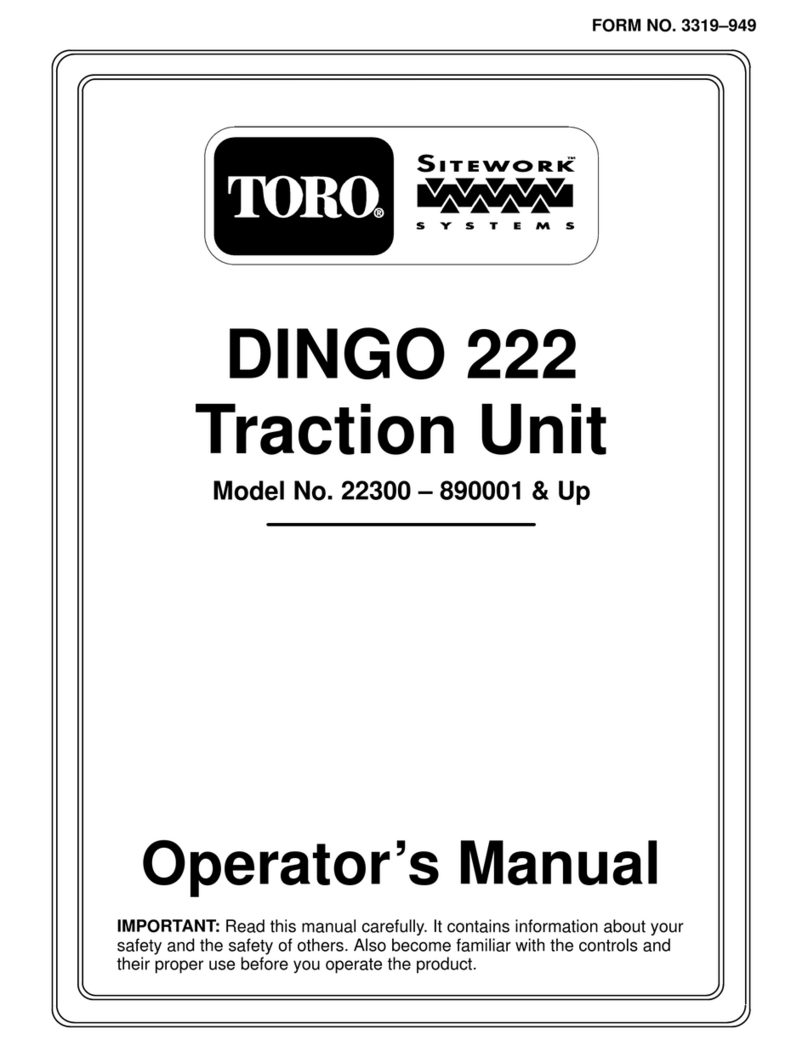
Toro
Toro 22300 Operator's manual
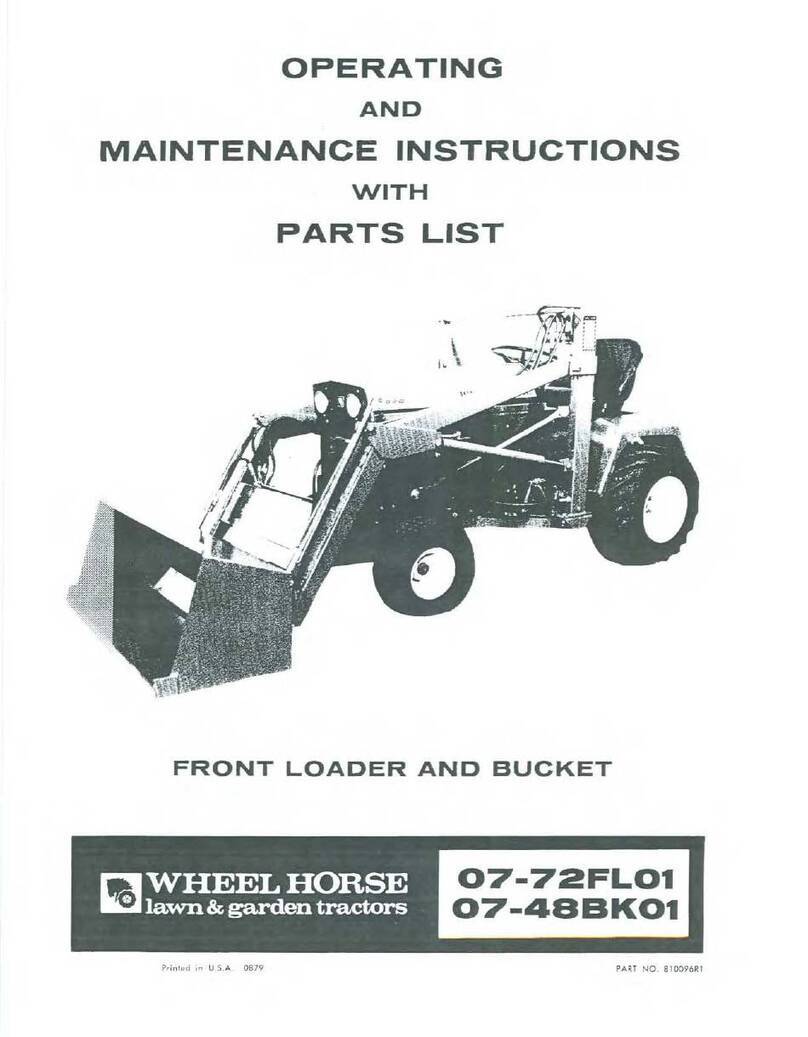
Wheel Horse
Wheel Horse 07-72FL01 Operating and Maintenance Instructions with Parts
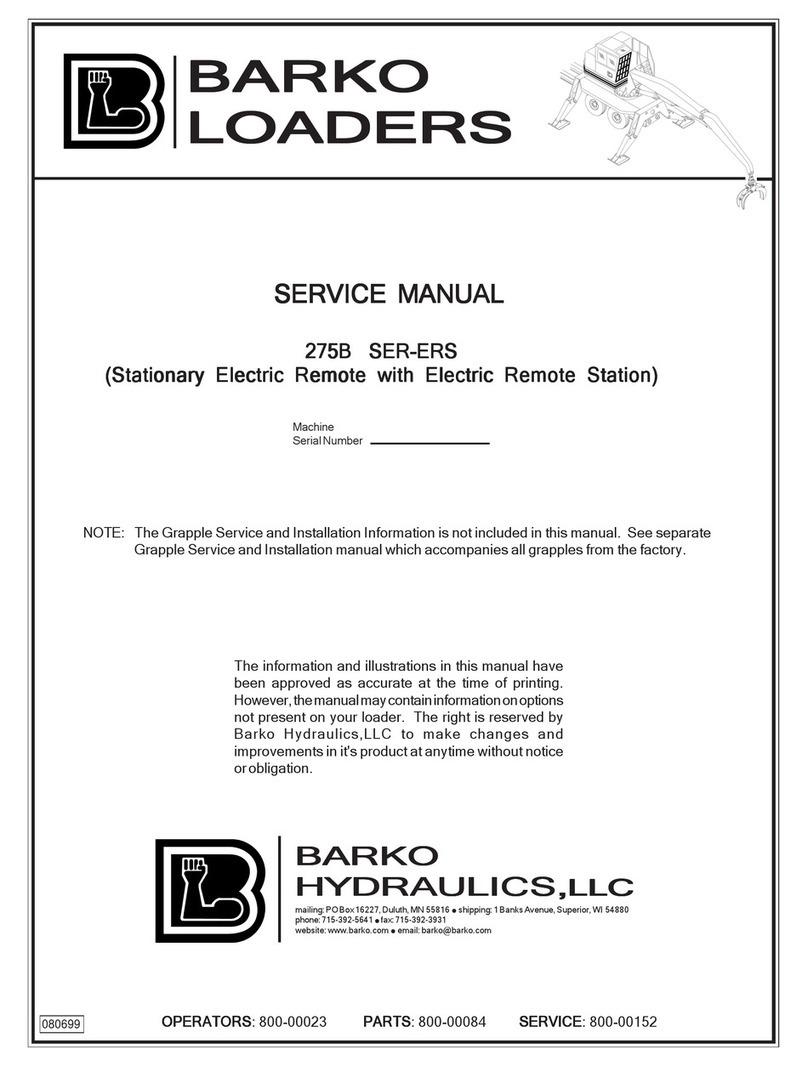
Barko Hydraulics
Barko Hydraulics BARKO LOADERS 275B SER-ERS Service manual