Estun EWAS Series User manual


ESTUN Arc Welding Robot- EWAS series
Robot Body Operation Instructions
M-1201EN-04

Thank you for purchasing ESTUN robots.
Before using the robot, be sure to read the SAFETY PRECAUTION and understand the content.
ESTUN endeavor to improve the products. All specifications and designs are subject to change
without notice.
In this manual, all specifications and information are checked on a regular basis. Nevertheless,
discrepancies cannot be precluded, for which reason we are not able to guarantee total conformity.
ESTUN assumes no responsibility for any direct or indirect losses arising from use of this manual and
products described herein.
Keep this manual handy for easy access at all times.
No part of this manual may be reproduced in any form.
ESTUN Robotics. All Rights Reserved Copyright.
Service Line: 400-025-3336
ADD: No.1888, Ji Yin Avenue, Jiangning Area, Nanjing, ChinaPost Code: 211102
TEL: +86-025-58328532
WEB: www.estun.com
E-mail: [email protected]om

SAFETY
S-1
SAFETY
This chapter describes the precautions which must be followed to ensure the safe use of the robot. Before
using the robot, be sure to read this chapter thoroughly.
ESTUN robots must be transported, mounted and operated in accordance with national laws, regulations
and standards. Appropriate safeguards must be correctly performed to protect the users. Before using (mounting,
operating, maintaining, repairing) the robot, be sure to read and understand this manual and its relevant
manuals. Be sure to have familiarization with the knowledge of robot system and the safety precaution. Even if
all instructions are followed, this is not a guarantee that the robot will not cause injuries or damage.
DEFINITION OF USER
The personnel can be defined as follows.
Operator
Turns the robot power ON/OFF.
Starts the robot program from the panel.
Programmer
Operates the robot.
Teaches the robot inside the safety area.
Maintenance engineer
Operates the robot.
Teaches the robot inside the safety area.
Maintenance (repair, adjustment, replacement).
Operator must not work in the safety area.
Programmer and maintenance engineer can work in the safety area.
During operation, programming, and maintenance of the robot, the operator, programmer, and maintenance
engineer should take precautions to ensure the safety by wearing the following safety items.
Clothes for operation
Safety shoes
A helmet
SPECIAL TRAINING
Tasks in the safety area include transportation, setting, teaching, adjustment, maintenance, etc.
Training course must be performed before operating the robot.
For more information about training course, contact ESTUN.
DEFINITION OF SAFETY NOTATIONS
Precautions and information are defined as follows.
Symbol
Definitions
WARNING
!
Danger notation
Death or serious injury will be expected to occur if the user fails to follow the approved
procedure.
CAUTION
!
Caution notation
Minor or moderate injury of the user or equipment damage will be expected to occur if
the user fails to follow the approved procedure.
IN F O
Information
A supplementary explanation helps users operating the robot more efficiently.

SAFETY
S-2
SAFETY OF THE USER
(1) The robot should be transported and installed as procedures recommended by ESTUN. Wrong
procedures may cause severe injuries or damage due to the robot fall.
(2) Draw an area clearly indicates the safety area. Install a fence or hang a warning board to ensure the
safety operation of the robot, and keep unauthorized personnel outside the safety area.
(3) Never hang any tools above the robot. Falling of these tools may cause damage to equipment.
(4) Never lean on the cabinet. Never touch any buttons without permission. Unexpected movement of the
robot may cause personnel injuries and equipment damage.
(5) Take precautions for falling parts to avoid injuries when disassemble the robot.
(6) Turn off the power when adjusting peripheral equipment.
(7) Peripheral equipment must be grounded.
(8) The robot should be operated in a low speed in the first operation. The speed should be added
gradually to check if there is any abnormal situation.
(9) Do not wear gloves when using the teach pendant. Operate with gloves may cause an operation error.
(10) Programs, system variables, and other information can be saved on the memory card or USB
memories. Be sure to save the data periodically in case that the data is lost.
(11) Never forcibly move any axis of the robot. Move the axes forcibly may cause injuries or damage.
(12) Take precautions when wiring and piping between the robot, the cabinet, and peripheral equipment.
Put the pipes, wires or cables through a pit or covered with a protective lid, to avoid stepped by
personnel or run over by a forklift.
(13) Unexpected movement may occur on any operating robot, which will cause severe injuries or damages
in the working area. Test (safe door, brake, safe indicators, etc.) must be performed on each safety
measures before using the robot. Before turn on the system, make sure that no one is in the working
space.
(14) Never set motion range or load condition exceeds the rated range. Incorrect setting may cause
personnel injury and equipment damage.
(15) Observe the following precautions when teaching inside the working space of the robot:
Do not enable the system unless the mode is switched to manual, and make sure that all auto-
control is cut off.
Speed must be limited under 250mm/s at manual mode. Only authorized person with fully
understand of the risks can adjust the robot to rated speed manually.
Be careful about rotating joints to prevent hair and clothes involved. Take precautions of injury or
damage caused by the manipulator or other auxiliary devices.
Check the motor brake to avoid personnel injuries caused by unexpected situation.
Always have an escape plan in mind in case the robot comes towards you unexpectedly.
Ensure that there is a place to retreat to in case of emergency.
WARNING
!
Never stand beneath the robot in case of unexpected movement or the system be turned
on inadvertently.
CAUTION
!
Make sure there is a CO2 fire extinguisher at hand.
SAFETY OF OPERATORS:
(1) Before operating the robot, check that the SERVO ON indicator goes out when the EMERGENCY
STOP button on the right of the front door of the controller and the pendant are pressed. And confirm
that the power is turned off.
(2) Never allow unauthorized personnel to touch the controller during operation. This may result in
unexpected movement of the robot, severe injuries and material damage.
(3) When attaching tools to the robot, be sure to turn off the power of the controller and the peripheral
equipment, and display a warning sign. Turning the power on during equipment installation may cause
electric shock or injury due to unexpected movement of the robot.
(4) Emergency stop
Emergency stop is an external button of the controller that can stop the robot operation.
When emergency button is pressed, the power of the robot (except the power of the servo) is cut off.

SAFETY
S-3
The system will not run unless the pressed emergency button being released and the system being turned
on.
There are several emergency stop buttons in a robot system to stop the robot in case of
emergencies. The red button, as shown in the left figure, can be mounted on the teach
pendant and the controller. Certainly, the emergency buttons can be mounted by special
requirement.
Emergency stop button should be mounted where is easy to reach, so that the buttons
can be pressed down immediately in case of emergencies.
WARNING
!
Operators must take precautions to avoid high voltage from cables of servo motors,
grippers and other devices.
CAUTION
!
Emergency button is used in case of emergency only. Do not use it to stop the robot for
normal operation.
SAFETY OF PROGRAMMERS:
While teaching the robot, the programmer must enter the robot operation area. The programmer must
ensure the safety especially.
CAUTION
!
Turn on or off the system by press or release Mot button on the teach pendant.
To use the teach pendant safely, the following precautions should be taken.
Be sure that the enable switch is effective at any time.
Turn off the enable switch when pausing, programming or testing the system.
Teach pendant must be taken with the programmer when teaching in the work space, to avoid
inadvertent operation by unauthorized person.
Teach pendant must not be left within the work space of the robot, as injury or damage can occur
if the robot comes in contact with the teach pendant.
SAFETY OF MAINTENANCE ENGINEERS:
(1) Heated parts
Some parts of the robot are heated when the robot is operating, especially the servo motor and
reducer. If a maintenance engineer needs to touch such a part, the user should wear heat-resistant gloves
or use other protective tools.
CAUTION
!
Try to feel the temperature of heated parts before touching them, to avoid burn injuries.
After turning off the power supply, wait until the heated parts cool down before
performing any maintenance.
(2) Disassembly parts
Open the cover or shell only after interior parts such as gears are not moving any more. Never open
the cover or shell when the gear or bearing is moving. Use auxiliary device to keep interior part to its
position.
Observe the following precaution when performing the first test after installation, inspection or
maintenance:
a) Clear tools to proper locations outside of the working space of the robot.
b) Make sure that all precaution measures are available.
c) Make sure that there is no one in the working space of the robot.
d) Pay special attention to working condition of the maintenance parts when performing test.
Never use the manipulator as a ladder when performing maintenance. Never climb on the manipulator
to avoid falling down.
(3) Pneumatic / hydraulic pressure
There may be air/liquid residue in the system when the air pump or hydraulic pump is turned off.
Before checking the pneumatic or hydraulic parts, release remaining pressure from the system to avoid

SAFETY
S-4
personnel injury or equipment damage.
CAUTION
!
Install a safety valve in case of accident.
(4) Although the power supply need to be turned on during fault diagnosis, it must be turned off when
perform maintenance.
(5) Brake inspection
Brake may be wearing in daily operation. So brake inspection should be performed by the following
procedure:
a) Move each joint to the position where the joint bears maximum load.
b) Turn off the robot. The brake works.
c) Mark each joint.
d) Check if the joint moves over a period of time.
(6) Greasing
Personnel injury or equipment damage may occur during greasing. Observe the following precautions
before greasing.
Take additional care of safety by wearing safety items (such as gloves) to avoid injury from heated
oil or reducer.
Open the oil chamber with caution and keep away from the opening. Oil may spray due to oil
pressure.
Feed the oil according to required quantity and never fill up the oil chamber. Check the oil indicator
when finished.
Never mix different types of oil into one reducer. Clean the oil chamber thoroughly before changing
oil type.
Oil draining must be performed thoroughly. Check the oil indicator when finished.
IN F O
Operate the robot for a short period of time before oil draining to heat the oil.
SAFETY OF THE TOOLS AND PERIPHERAL EQUIPMENT
Peripheral device may still be running even after the system has been turned off. Personnel injury may
occur due to damaged power lines.
SAFETY OF THE ROBOT MECHANICAL UNIT
For abnormal or emergency situations, e.g. persons trapped in or pinched by the robot, the robot axes
should be moved. (Contact ESTUN for more details about dismantling).
Small arms can be moved by hand. Lager arms should be moved by crane or other handling
equipment.
Fasten the robot firmly before releasing the brake to avoid secondary injury caused by falling arms.
STOP TYPE OF ROBOT
There are three types of robot stop.
Power-off stop
Servo power is turned off and the robots stops immediately. Servo power is turned off when the robot
is moving, the path of the deceleration in uncontrolled.
The following processing is performed at Power-off stop:
An alarm is generated and servo power is turned off immediately.
Execution of the program is paused.
Frequent Power-off stop of the robot during operation can cause failures of the robot. Avoid system
designs that require routine or frequent Power-off stop conditions.
Alarm stop

SAFETY
S-5
The robot system sends alarm (not include power-off alarm), and the robot is decelerated until it stops
by control instructions.
The following processing is performed at Alarm stop:
An alarm (not include power-off alarm) is generated due to overload, system faulty, etc.
Control instruction is send from servo system. The robot operation is decelerated until it stops.
Execution of the program is paused.
Servo power is off.
Hold
The robot is decelerated until it stops, and servo power remains on.
The following processing is performed at Hold:
The robot operation is decelerated until it stops. Execution of the program is paused.
LABELS
(1) Electric Shock Warning
Fig 0.1 Electric Shock Warning
This label indicates hazardous voltage or electric shock.
(2) High-temperature Warning
Fig 0.2 High-temperature Warning
Be cautious about a section where this label is affixed, as the section generates heat. If you have to
inevitably touch such a section when it is hot, use a protection provision such as heat-resistant gloves.
(3) No Step-on Warning

SAFETY
S-6
Fig 0.3 Step-on prohibitive Warning
Never step on or climb the robot or controller as it may adversely affect the robot or controller and may
get hurt if you lose your footing as well.
(4) Personal Injury Warning
Fig 0.4 Personal Injury Warning
Never enter the operation area while the Manipulator is moving. This is extremely hazardous and may
result in serious safety problems.
(5) No Disassembly Warning
Fig 0.5 No Disassembly Warning
Never perform disassembly arbitrarily where the warning is affixed. Contact ESTUN for disassembly.
(6) Handling Identification

SAFETY
S-7
Fig 0.6 ER8-1450-HW Transport Identification
Fig 0.7 ER8-1500-CW Transport Identification

SAFETY
S-8
Fig 0.8 ER8-2000-CW Transport Identification
Fig 0.9 ER8-2000-HW、ER8-2000-HW-T Transport Identification

PREFACE
P-1
PREFACE
This manual describes the following manipulators.
Model
Load capacity
ER8-1450-HW
8kg
ER8-1500-CW
8kg
ER8-2000-CW
8kg
ER8-2000-HW
8kg
ER8-2000-HW-T
8kg
Related manual
ESTUN Robot Ewas Series - Mechanical Unit Operator’s Manual
ESTUN RCS2 System Operator’s Manual
ESTUN Robot S1F Control Cabinet Operation Instructions
ESTUN Robot S1E Control Cabinet Operation Instructions

c-1
CONTENTS
CONTENTS
SAFETY .............................................................................. 1
PREFACE ............................................................................. 1
1. TRANSPORTATION AND INSTALLATION .................................................. 1
1.1 TRANSPORTATION...................................................... 1
1.1.1. Transport by a forklift ................................................. 3
1.2 INSTALLATION.......................................................... 5
1.3 INSTALLATION CONDITIONS............................................. 9
2. CONNECTION WITH THE CONTROLLER .................................................. 7
3. SPECIFICATIONS .................................................................. 8
3.1 ROBOT CONFIGURATION................................................ 8
3.2 EXTERNAL DIMENSIONS AND OPERATING SPACE ....................... 12
3.3 ZERO POINT POSITION AND MOTION LIMIT.............................. 16
3.4 WRIST LOAD CONDITION ............................................... 22
3.5 ADDITIONAL LOAD CONDITION ......................................... 23
4. EQUIPMENT INSTALLATION TO THE ROBOT ............................................ 26
4.1 FLANGE DIMENSION....................................................... 26
4.2 EUIPMENT MOUNTING FACE ............................................... 27
4.3 PIPES AND TUBES......................................................... 32
5. CHECK AND MAINTENANCE ........................................................... 34
5.1 DAILY CHECKS ........................................................ 34
5.2 PERIODIC CHECKS AND MAINTENANCE................................. 35
5.5.1. POSITION OF OIL INLET/OUTLET ON EACH AXIS ..................... 40
5.5.2. PROCEDURE OF GREASING ........................................ 45
5.5.3. PROCEDURE FOR RELEASING REMAINING PRESSURE WITHIN THE
GREASE BATH ..................................................... 46
6. CALIBRATION ..................................................................... 47
6.1 INTRODUCTION........................................................ 47
6.2 QUICK ZERO POSITION CALIBRATION ...................................... 47
6.3 MECHANICAL ZERO POSITION CALIBRATION ............................ 48
6.3.1. ZERO POSITION CALIBRATION METHOD............................. 48
6.3.2. CALIBRATION IN EACH AXIS ........................................ 48
7. TROUBLESHOOTING ................................................................. 54
7.1 TOOLS.................................................................... 54
7.2 TROUBLESHOOTING ...................................................... 54
7.3 REPLACING THE SERVO MOTOR ........................................... 55
APPENDIX ........................................................................... 31
APPENDIX A BOLT TORQUE LIST ................................................... 31
APPENDIX B SPECIFICATION OF BOLT............................................... 31
APPENDIX C ER8-1450-HW Suggested spare parts list(for single unit)...................... 33
APPENDIX D ER8-1500-CW Suggested spare parts list(for single unit)...................... 33
APPENDIX E ER8-2000-CW Suggested spare parts list(for single unit)...................... 33
APPENDIX F ER8-2000-HW Suggested spare parts list(for single unit)...................... 33
APPENDIX G ER8-2000-HW Suggested spare parts list(for single unit)...................... 33

TRANSPORTATION AND INSTALLATION
1
1. TRANSPORTATION AND INSTALLATION
1.1 TRANSPORTATION
WARNING
!
When transport the robot, be sure the robot is in safe condition, or it may result in
serious personnel injury and/or equipment damage.
Turn each axis to transportation gesture before move the robot and be sure to keep the gesture during
transportation until it be properly installed and mounted. Transportation gesture of each axis is shown
below. Perform the transportation properly, or it may result in personnel injury or equipment damage.
Position
J1-axis
J2-axis
J3-axis
J4-axis
J5-axis
J6-axis
ER8-1450-HW
0°
-75°
+75°
0°
+45°
0°
ER8-1500-CW
0°
-75°
+75°
0°
0°
0°
ER8-2000-CW
0°
-50°
+70°
0°
0°
0°
ER8-2000-HW
ER8-2000-HW-T
0° -80° +80° 0° +90° 0°
Refer to theoretical weight of main parts shown below to install, disassemble and transport the robot.
Parts
Weight(kg)
ER8-1450-HW ER8-1500-CW ER8-2000-CW
ER8-2000-HW
ER8-2000-HW-T
Robot
170
165
281
286
Big arm casting
19.4
19
38.4
39.7
Base assembly
(Including rotation base)
100.8
99
177.8
178.3
Small arm assembly
(Including motor casing
and motors of J3,J4 J5
axes)
28.6 25 32.4 45
Wrist (including motors
of J6-axis)
11.6
11
11
11.8
IN F O
Some parts with less weight are not listed. Contact ESTUN
For ER8-1450-H robot ,fixed bracket should be mounted before transport the robot and be removed
before install the robot. Refer to the following figures when remove the bolts on fixed bracket.
M8 screw mounting hole*2
M8 screw mounting hole*2

TRANSPORTATION AND INSTALLATION
2
Fig 1.1 Robot fixed bracket(ER8-1450-HW)
Fig 1.2 Robot fixed bracket(ER8-1500-CW)
Fig 1.1 Robot fixed bracket(ER8-2000-CW)
M6 screw mounting hole*2
M8 screw mounting hole*2
M8 screw mounting hole*2
M8 screw mounting hole*2
M8 screw mounting hole*2
M8 screw mounting hole*2

TRANSPORTATION AND INSTALLATION
3
Fig 1.2 Robot fixed bracket(ER8-2000-HW、ER8-2000-HW-T)
1.1.1.Transport by a forklift
The robot described in this manual can be transported by a forklift. Use eight bolts to fix the 4 fixed
plates on the forklift to the robot base, use a forklift to heave the robot. Make sure that the fixed bolts of the
robot are removed before transportation.
Notes:Transportation conditions:① need crane with minimum capacity 1t;②the rod shall has capacity of
500kg;
③
according to Standard GB/T825-1988.
④
M12 bolt
Fig 1.5 The robot lifting and transportation instructions(ER8-1450-HW)
M8 screw mounting hole*2
M8 screw mounting hole*2
M8 screw mounting hole*2
M6 screw mounting hole*2
Robot
center of
gravity

TRANSPORTATION AND INSTALLATION
4
Notes:Transportation conditions:① need crane with minimum capacity 1t;②the rod shall has capacity of
500kg;
③
according to Standard GB/T825-1988.
④
M16 bolt
Fig 1.6 The robot lifting and transportation instructions(ER8-1500-CW)
Notes:Transportation conditions:① need crane with minimum capacity 1t;②the rod shall has capacity of 500kg;③
according to Standard GB/T825-1988.
④
M16 bolt
Fig 1.7 The robot lifting and transportation instructions(ER8-2000-CW)
Robot
center of
gravity
Robot
center of
gravity

TRANSPORTATION AND INSTALLATION
5
Notes:Transportation conditions:① need crane with minimum capacity 1t;②the rod shall has
capacity of 500kg;
③
according to Standard GB/T825-1988.
④
M16 bolt
Fig 1.8 The robot lifting and transportation instructions(ER8-2000-HW、ER8-2000-HW-T)
CAUTION
!
The sling shall be suppled by the customer. Please remove the sling bolts before running
the body.
1.2 INSTALLATION
CAUTION
!
Make sure the system is properly grounded before installation.
The following precautions must be fully understood and observed before installing the robot.
Ensure that the information in the Safe Use Notice has been read and understood;
Ensure that robots are installed by qualified installers and that installation procedures comply with
local legal rules;
Check whether the outer packaging of the robot is bumped or damaged; Unpack the robot and
check whether the robot product is damaged from the appearance;
Ensure that when installing the robot, the lifting equipment can bear the weight of the lifting robot
parts, see 1.1 Handling;
The environmental conditions of robot storage and installation must meet the 1.3 installation
conditions.
When mounting the robot base, consider its structure and the force upon it. Concrete on the base may not
have any crack and conform to the specified codes. The bearing capacity and compaction of the concrete
foundation should be in accordance with the design guideline. Concrete strength level C20/C25 should be in
accordance with the following codes:
GB50010-2010 Code for design of concrete structures
GB/T50081-2002 Standard for test method of mechanical properties on ordinary concrete
Robot
center of
gravity

TRANSPORTATION AND INSTALLATION
3
Rotate horizontally
Rotate vertically
Horizontal force Fh
Torque Mr
Vertical force Fv
Torque Mk
Emergency stop
4800 N 3750 N·m 5750N 4165N·m
Accelerating
1600N 1250N·m 2300N 1666N·m
Fig 1.9 Robot base specification(ER8-1450-HW)
Rotate horizontally
Rotate vertically
Horizontal force Fh
Torque Mr
Vertical force Fv
Torque Mk
Emergency stop
4800 N 3750 N·m 5500N 4165N·m
Accelerating
1600N 1250N·m 2200N 1666N·m
Fig 1.10 Robot base specification(ER8-1500-CW)
This manual suits for next models
5
Table of contents
Other Estun Robotics manuals
Popular Robotics manuals by other brands
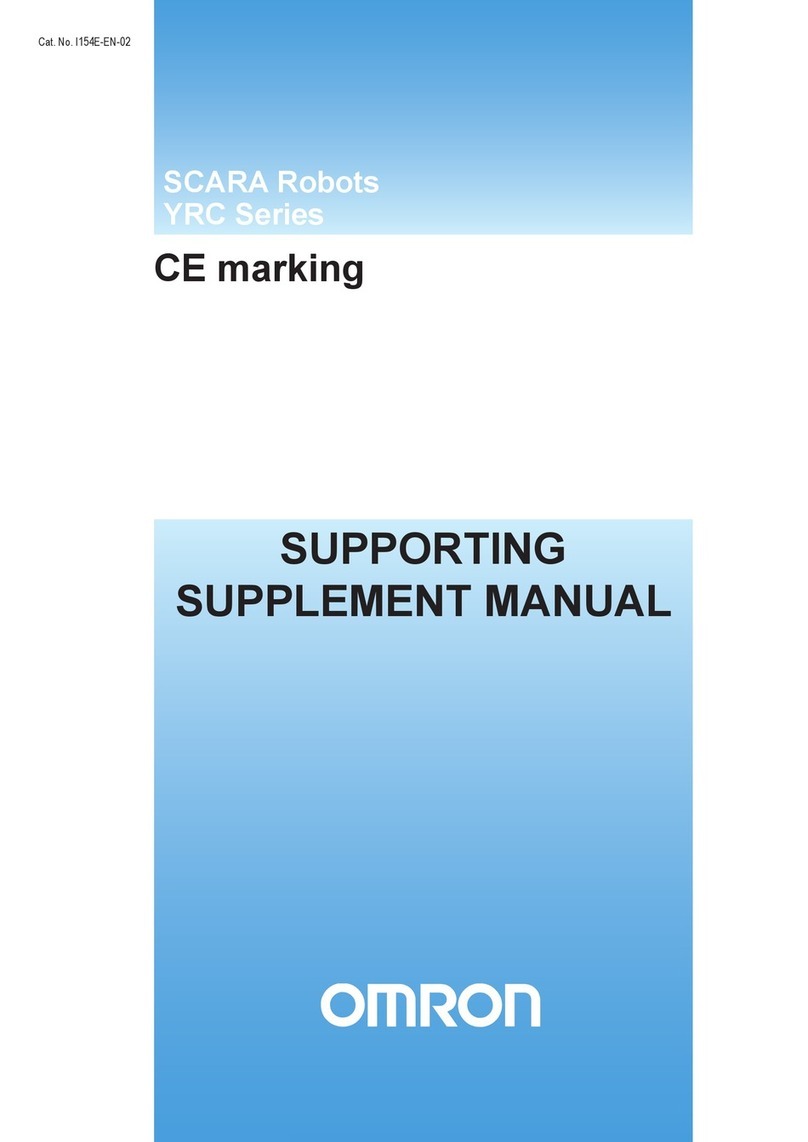
Omron
Omron SCARA YRC Series Supporting supplement manual
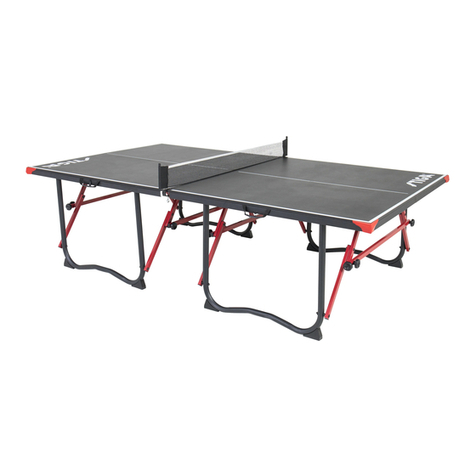
Stiga
Stiga Play The Best T8485W owner's manual

Plymovent
Plymovent MULTISMART ARM MSA-125-3 product manual
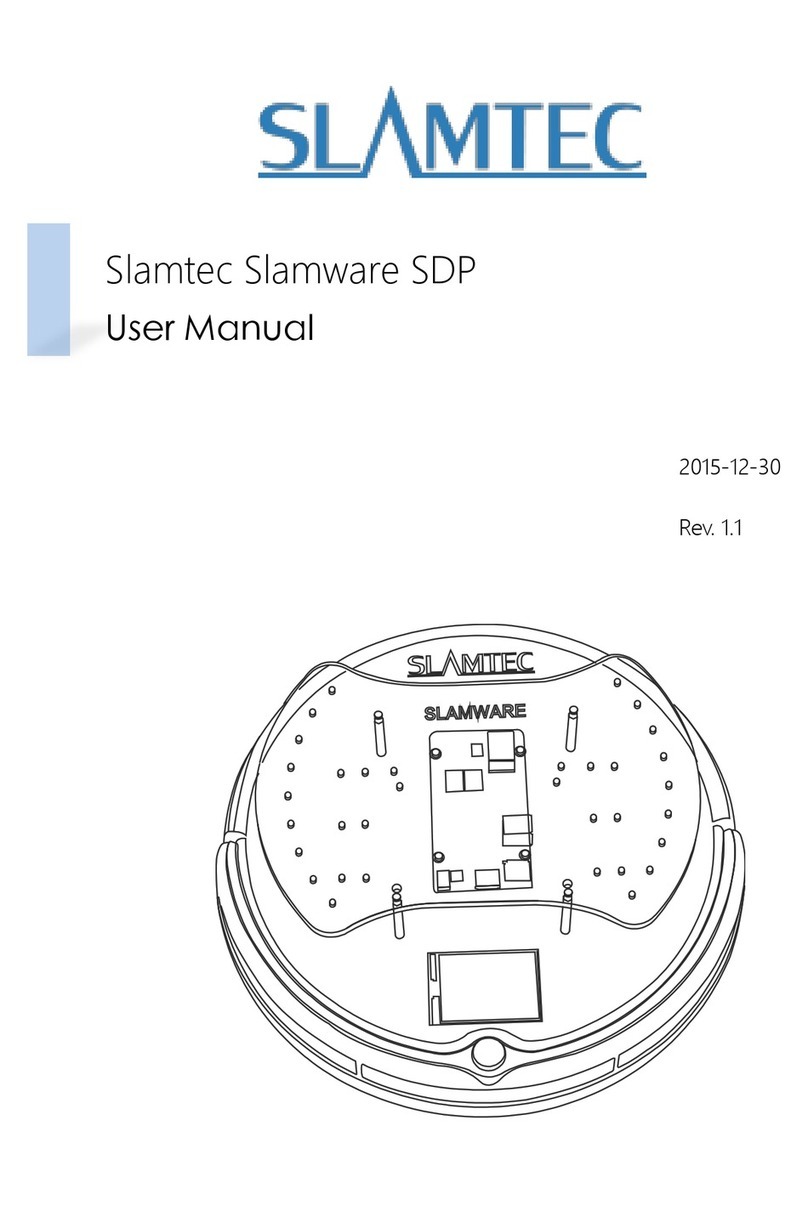
Slamtec
Slamtec Slamware SDP user manual
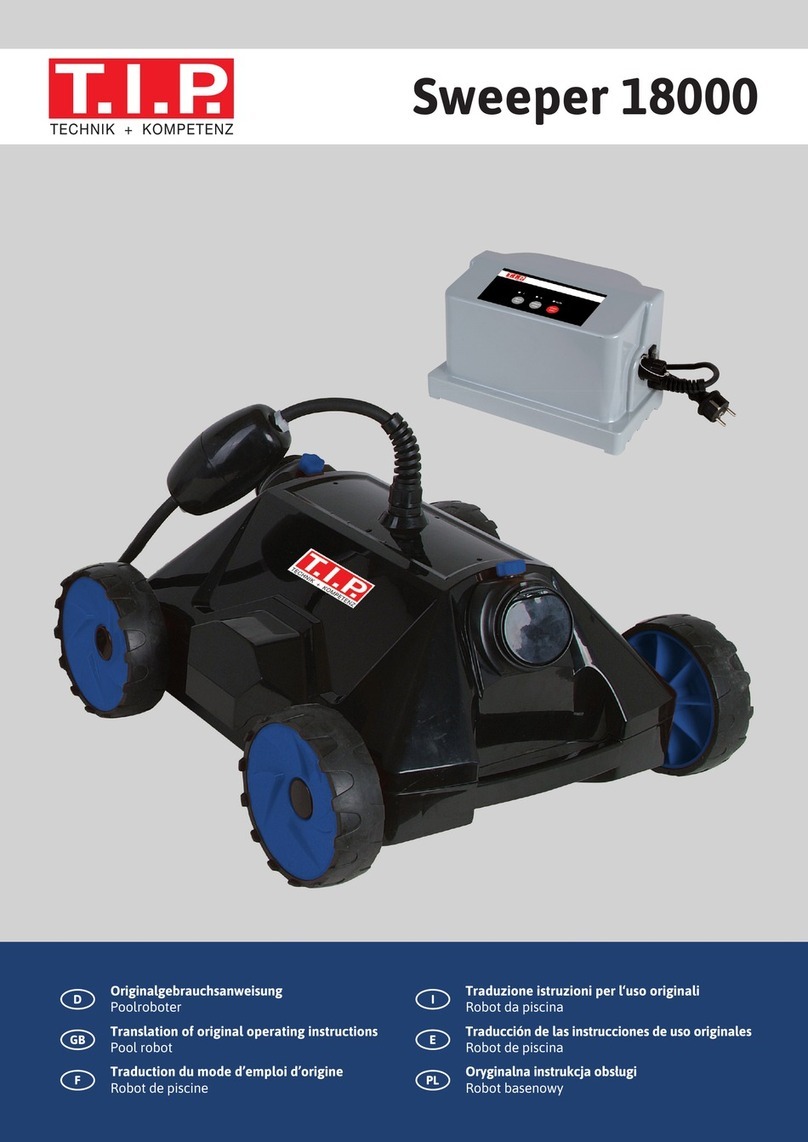
T.I.P.
T.I.P. Sweeper 18000 Operating instruction
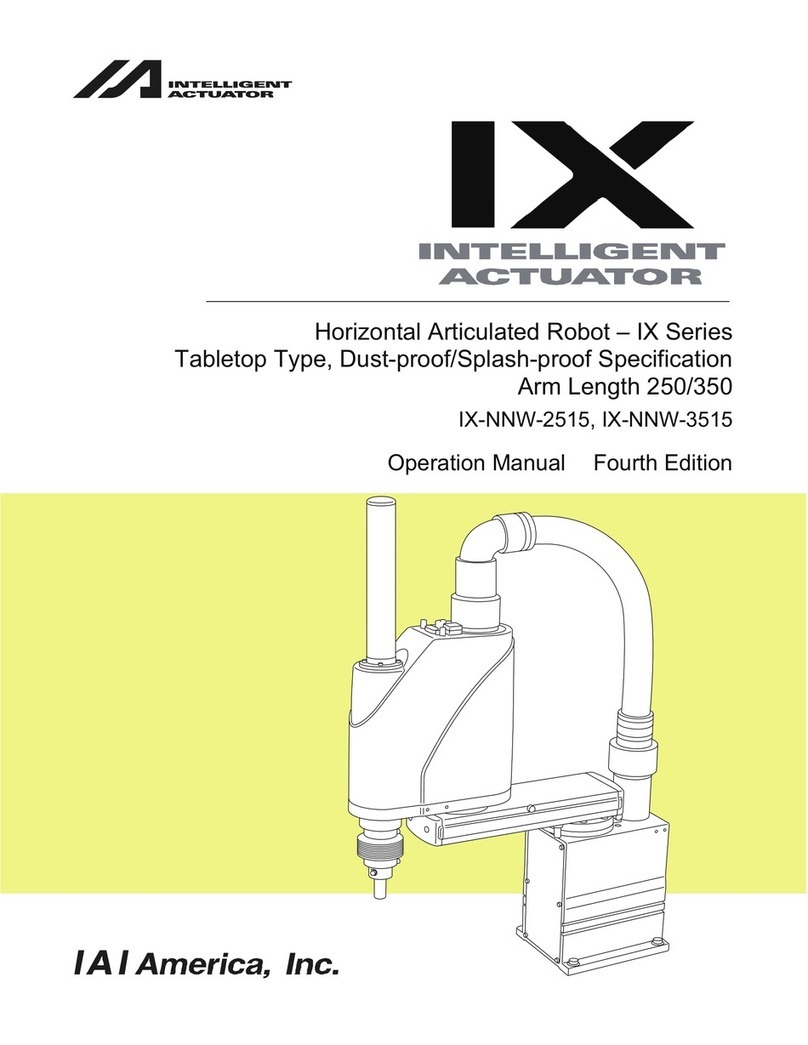
IAI
IAI Intelligent Actuator IX Series Operation manual