Evolution EVC-H User manual

DocumentNo. NISM/EVC-H/01
Date NOV 2003
NITTAN (UK) LTD.
Hipley Street, Old Woking, Surrey, England, GU22 9LQ. UK
Tel: +44 (0) 1483 769555 Fax: +44 (0) 1483 756686 Web Site: www.nittan.co.uk E-mail: [email protected]
EVC-H CONVENTIONAL HEAT DETECTOR
INSTRUCTION MANUAL
evolution
Quality System Certificate No. 041
Assessed to BS EN ISO 9001:2002

Ref No:
DATE:
PAGE: ISSUE:
evolution
EVC-H HEAT DETECTOR
INSTRUCTION MANUAL NOV 2003
of16
NISM/EVC-H/01
01
evolution.....
The EVC-H Heat Detector forms part of a brand new range of fire detectors
from Nittan (UK) Ltd called evolution.
The EVC-H is an elegantly designed, low profile detector which is
aesthetically pleasing, thus enabling it to blend unobtrusively into modern
working environments.
The EVC-H is compatible with other existing conventional fire detection
systems.

Ref No:
DATE:
PAGE: ISSUE:
evolution
EVC-H HEAT DETECTOR
INSTRUCTION MANUAL NOV 2003
of26
NISM/EVC-H/01
01
CONTENTS:-
Section1 - Introduction - Page 2
Section2 - Operation - Page 2
Section3 - DetectorModels - Page 3
Section4 - BaseModels - Page 3
Section5 - Installation - Page 3
Section6 - Connections - Page 3
Section7 - Maintenance&
Cleaning - Page 4
Section8 - Specification - Page 5
Section9 - EMC - Page 5
Section10 - Dimensions - Page 5
Section11 - Response
Characteristics - Page 6
Section 1 - INTRODUCTION
The EVC-H is an attractively styled, fast response, low
profileheatdetector.
It has been designed to replace any previous Nittan heat
detector.
EVC-Hfeatures:
*Lowprofile,stylishappearance
*Differentresponsegradesavailable
*Non-polarisedterminals
*Unauthorisedheadremovalsignalfacility
* Low monitoring current
* Patented OMNIVIEWTM 360oLED alarm indicator
*Remoteindicatoroutput
* Compatible with STB-4, STB-4SD and STB-4SE
bases
Section 2 - OPERATION
TheEVC-Hrangeof heat detectors are nonmechanical
and use a thermistor of low thermal mass as the sensing
element giving a fast response. Although these
detectorsoperateonafixedtemperaturethresholdonly,
their fast response makes them generally suitable for
usewhererate-of-risedetectorswouldbeused.
Fig. 1. Block Diagram of EVC-H Detector Circuit
FIG.1
RECTIFIER
AND
FILTER
OPERATION
INDICATOR
SWITCHING
UNIT
VOLTAGE
STABILISER
+ve
(3)
-ve
(1)
-ve
(6)
SENSING
THERMISTOR
INTERNAL
REFERENCE
COMPARATOR
UNIT
Rem.Ind.(5)

Ref No:
DATE:
PAGE: ISSUE:
evolution
EVC-H HEAT DETECTOR
INSTRUCTION MANUAL NOV 2003
of36
NISM/EVC-H/01
01
the sensor is undertaken. At commissioning, the dust
covershouldberemovedanddiscarded.
NOTE: THE PLASTIC DUST COVER MUST BE
REMOVED FROM THE SENSOR IN ORDER FOR THE
SENSORTOFUNCTIONCORRECTLY.
Section 6 - CONNECTIONS
Connections are made to the detector base. The con-
nections used depend on the type of base and the
functions required. See Section 4 'Base Models', to
identify the required type of base and functions sup-
ported. See below Figures 2, 3 & 4 for wiring to the
detector'sbase:-
Section 3 - DETECTOR MODELS:
TheEVC-Hrangeofheatdetectors arecurrentlyavail-
able in two versions. Others can be made
availableupondemand
i) EVC-H-A2
ii) EVC-H-C
Theseversionshave three terminalsforconnectiononto
thetwowirezone circuit. Theremainingterminal(5)
providesaswitchedcurrentsinkfunctionwhichoperates
when the detector goes into alarm condition, suitable for
the operation of auxiliary function such as a remote
indicator.
Section 4 - BASE MODELS
A variety of bases are available for use with the
EVC-H detectors. It is important to use the correct base
for each application. The available base models are:
i) STB-4 base: forstandard use with EVC-H series heat
detectorwhenauxiliaryoutputnotused.
ii) STB-4SD base: This is identical to the standard
STB-4 base, but also includes a schottky diode for head
removal fault monitoring. The schottky diode is used in
some fire systems to ensure power is
maintained,intheeventofanunauthorised detector
headremoval, to other detectors further on the zone.
iii) STB-4SE base: Similar to STB-4 base, except
deeper.
iv)STB-4SE-24VRbase:Relaycontactbase.
Section 5 - INSTALLATION
In normal use, the EVC-H detector will be installed at
ceiling level. Pass field wiring through cable hole in
centre of base from rear of base. Offer up and affix
base to the ceiling or conduit fitting with screws via the
base mounting holes. Connect field wiring to base
terminalsasdetailedinbelowsection'Connections',
making sure that wiring will not obstruct fitting of detec-
tor head. Fit detector head by inserting into base and
turning clockwise until notch in detector rim aligns with
base locking screw. The OMNIVIEWTM indicator per-
mits visibility from any angle.
Fit the plastic dust cover supplied over the sensor to
keep out dust etc, until the system is commissioned. If
the dust cover is not fitted and the environment is
slightly dusty, such as when building work is being
completed, for example, problems of false alarms are
likely to occur after commissioning unless cleaning of
STB-4-SD base
STB-4 base
STB-4 and STB-4-SE bases
E.O.L
3
1
6
1
6
1
6
3
5
5
Max.currentthrough
(5)=:20mA(total)
+
R.I.L
+
3
If+vesupplyderivedfromzone,
thenRILmustbeLEDtype
_
_
Max.currentthrough
(5)=:20mA(total)
+
_
+
_
E.O.L
E.O.L
FIG.2
FIG.3
FIG.4

Ref No:
DATE:
PAGE: ISSUE:
evolution
EVC-H HEAT DETECTOR
INSTRUCTION MANUAL NOV 2003
of46
NISM/EVC-H/01
01
Section 7 - MAINTENANCE AND CLEANING
Maintenance:
TheEVC-Hdetector isahighqualityproduct engineered
for reliability. In order to obtain optimum performance,
periodicmaintenanceisrequired. Ifproperpreventative
maintenance is not carried out, there is a likelihood of
malfunction, including false alarms.
Servicing:
Servicing of the system should be carried out in accord-
ance with the requirements of BS 5839 Part 1, Fire
Detection and Alarm Systems for Buildings: Code of
Practice for System Design, Installation and Servicing.
Themaintenanceproceduresdescribedbelow,should
beconductedwiththefollowingfrequency:
Onemonth after installation: RoutineInspection
andevery3months
thereafter.
Every6months: OperationalTest.
Every12months: Functional Test and
Cleaning.
Allabovefrequenciesofmaintenancearedependenton
ambient conditions.
RoutineInspection:
i) Ensure that the detector head is secure and undam-
aged.
ii) Check that the heat entry apertures are in no way
obstructed.
iii) Ensure that the surface of the detector’s outer cover
is clean. If there are deposits due to the presence of oil
vapour, dust etc, then the detector should be cleaned in
accordancewiththecleaninginstructionsdetailedlater
in this manual. It may be advisable to ensure that such
cleaningisconductedregularly in future.
iv)Ensurethatnoequipmentwhichmaygenerate
excessive heat has been installed in the vicinity of the
detector since the last routine inspection. If such
equipment has been installed, then you should notify
the Safety Officer or other competent authority that its
presence may cause false alarms.
OperationalTest
The purpose of the Operational Test is to confirm the
detector’scorrectoperation in response to aheat
condition.
i) Take any necessary precautions at the control panel
to limit the sounding of the alarm sounders/bells and
anyfireservicesummoningdevice.
ii) Test the detector with heat from a warm air gun
designed for heat detector testing (e.g. 'No Climb - Solo'
heat sensor tester). Check that the detector gives an
alarmconditionwithin10-20secondsdependingupon
thedetectorgradeandtheappliedairtemperature.
Check that the LED indicator on the detector illumi-
nates.
N.B. Hot air blowers sold for paint stripping, solder-
ingpipesetc,generatesufficientheattodamage the
detectorandshould notbeused fortestingheat
detectors.
iii) After the detector has given the alarm condition,
reset the detector from the control. It may be neces-
sary to allow some short time to elapse before resetting
the detector, to allow any residual heat from the test to
disperse.
iv) Beforeproceeding to the nextdetector, ensure that
the detector just tested does not re-operate due to the
presenceofresidual heat.
FunctionalTest:
The Functional Test checks the detectors operation.
These detectors may be returned to our factory for
FunctionalTesting.
Cleaning:
Note:ThesensorheadshouldNOTbedisassembled.
i) Carefuly remove the heat detector from its base.
ii) Use a soft, lint-free cloth, moistened with alcohol for
sticky deposits, to clean the plastic cover.
iii) Using a soft bristle brush (e.g. an artists paintbrush)
carefullybrush between thevanes and thermistorin a
linearmotionawayfrom the apertures on theplastic
case.
iv) Ensure that no debris is left on or around the ther-
mistor once cleaning is complete.
v) If the unit needs further cleaning or is damaged or
corroded,pleasereturnthecompletedetectortoNittan
(UK) Ltd. for service.

Ref No:
DATE:
PAGE: ISSUE:
evolution
EVC-H HEAT DETECTOR
INSTRUCTION MANUAL NOV 2003
of56
NISM/EVC-H/01
01
Section 8 - SPECIFICATIONS
ModelReferences: EVC-H-A2,EVC-H-C
ComputerReferences: EVC-H-A2-F04N82501
EVC-H-C-F04N82503
SensingElement
&Principle: Thermistoroflowthermal
mass.
SupplyVoltage: 24V dcnominal(range16
to32V)
VoltageRipple: 20%maximum
AlarmVoltage: 6V d.c. in series with 375R
between+(terminal3)and
-(terminals1,6)at25oC
MonitoringCurrent: 30
µ
A maximum at 24Vd.c.
AlarmCurrent: 50 mA maximum at
25deg. C
ChargingTime: 20seconds
AmbientTemperature
Range: EVC-H-A2 -10 oC to +55 oC
EVC-H-C -10 oC to +80 oC
IPRating: 41
Section 9 - EMC
Installation
The installation shall be in accordance with the
regulationseitheroftheapprovalbodyforanapproved
system, or otherwise, to the national code of practice/
regulations for the installation of the fire alarm system,
e.g. BS 5839 part 1.
ElectromagneticCompatibility(EMC)
On a site where there is an unusually high level of
potentialelectricalinterference,e.g.whereheavy
currentsarebeingswitched or where high levels of R.F.
are prevalent, then care must be taken in the type and
routing of cables. Particular care should be given to
theseparation of zone wiring from the cable carrying the
interference.
15mm
43mm
∅104mm
Section 10 - DIMENSIONS

Ref No:
DATE:
PAGE: ISSUE:
evolution
EVC-H HEAT DETECTOR
INSTRUCTION MANUAL NOV 2003
of66
NISM/EVC-H/01
01
Section 11 - RESPONSE CHARACTERISTIC GRAPHS
EVC-H Rate of Rise Response (Degree C/Min)
0
10
20
30
40
50
60
70
80
90
100
0 5 10 15 20 25 30 35 40 45 50
Response Time (Minutes)
Temperature
A2
C
1deg/m
3deg/m
5deg/m
10deg/m
20deg/m
L Limit Others
U Limit Others
20 10 5 3
1
Table of contents
Popular Smoke Alarm manuals by other brands

Dors
Dors 1100 user manual

Teletek electronics
Teletek electronics SensoMAG S30 Installation instruction

Firex
Firex 110-1011E owner's manual
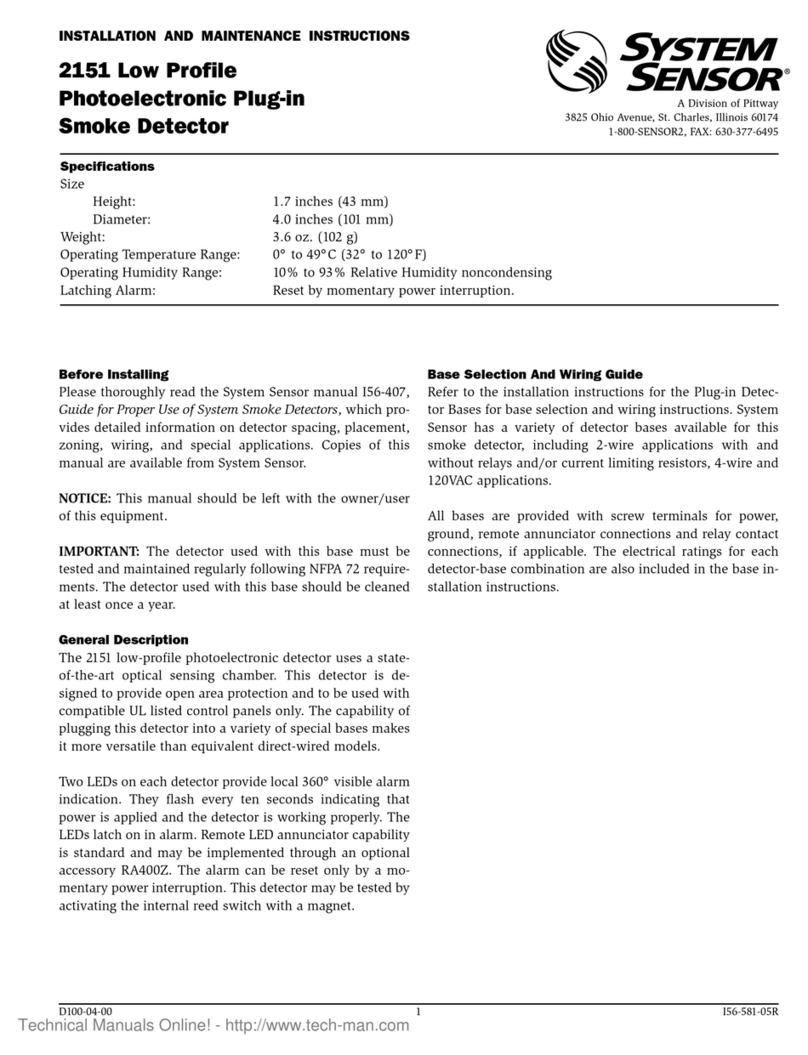
Pittway
Pittway System Sensor 2151 Installation and maintenance instructions

SpreadNet
SpreadNet SN980-SMOKE installation instructions

BRK electronic
BRK electronic Dicon M300 owner's manual