EWM M1.83-A-1 User manual

Operating instructions
EN
Control
M1.83-A-1
099-M183xA-EW501 Observe additional system documents! 15.7.2022

General instructions
WARNING
Read the operating instructions!
The operating instructions provide an introduction to the safe use of the products.
• Read and observe the operating instructions for all system components, especially the
safety instructions and warning notices!
• Observe the accident prevention regulations and any regional regulations!
• The operating instructions must be kept at the location where the machine is operated.
• Safety and warning labels on the machine indicate any possible risks.
Keep these labels clean and legible at all times.
• The machine has been constructed to state-of-the-art standards in line with any applicable
regulations and industrial standards. Only trained personnel may operate, service and re-
pair the machine.
• Technical changes due to further development in machine technology may lead to a differ-
ing welding behaviour.
In the event of queries on installation, commissioning, operation or special conditions at the in-
stallation site, or on usage, please contact your sales partner or our customer service department
on +49 2680 181-0.
A list of authorised sales partners can be found at www.ewm-group.com/en/specialist-dealers.
Liability relating to the operation of this equipment is restricted solely to the function of the equipment. No
other form of liability, regardless of type, shall be accepted. This exclusion of liability shall be deemed ac-
cepted by the user on commissioning the equipment.
The manufacturer is unable to monitor whether or not these instructions or the conditions and methods
are observed during installation, operation, usage and maintenance of the equipment.
An incorrectly performed installation can result in material damage and injure persons as a result. For this
reason, we do not accept any responsibility or liability for losses, damages or costs arising from incorrect
installation, improper operation or incorrect usage and maintenance or any actions connected to this in
any way.
© EWM AG
Dr. Günter-Henle-Strasse 8
56271 Mündersbach Germany
Tel.: +49 2680 181-0, Fax: -244
Email: info@ewm-group.com
www.ewm-group.com
The copyright to this document remains the property of the manufacturer.
Copying, including extracts, only permitted with written approval.
The content of this document has been prepared and reviewed with all reasonable care. The information
provided is subject to change; errors excepted.
Data security
The user is responsible for backing up data of all changes from the factory setting. The user is liable for
erased personal settings. The manufacturer does not assume any liability for this.

Contents
Notes on using these operating instructions
099-M183xA-EW501
15.7.2022
3
1 Contents
1Contents.......................................................................................................................................... 3
2For your safety ............................................................................................................................... 5
2.1 Notes on using these operating instructions.......................................................................... 5
2.2 Explanation of icons...............................................................................................................6
2.3 Safety instructions.................................................................................................................. 7
2.4 Transport and installation ....................................................................................................10
3Intended use.................................................................................................................................12
3.1 Use and operation solely with the following machines ........................................................12
3.2 Software version..................................................................................................................12
3.3 Documents which also apply ...............................................................................................12
3.3.1 Warranty...............................................................................................................12
3.3.2 Declaration of Conformity.....................................................................................12
3.3.3 Welding in environments with increased electrical hazards.................................12
3.3.4 Service documents (spare parts and circuit diagrams)........................................12
3.3.5 Calibration/Validation............................................................................................12
3.3.6 Part of the complete documentation.....................................................................13
4Machine description – quick overview ...................................................................................... 14
4.1 Welding data display............................................................................................................16
4.1.1Polarity setting......................................................................................................16
5Functional characteristics...........................................................................................................17
5.1 Gas test – setting the shielding gas volume........................................................................17
5.2 MIG/MAG welding................................................................................................................17
5.2.1 Definition of MIG/MAG welding tasks...................................................................17
5.2.2 Welding task selection..........................................................................................18
5.2.2.1 Basic welding parameters.....................................................................18
5.2.2.2 Operating mode ....................................................................................18
5.2.3 Welding type.........................................................................................................19
5.2.4 Welding power (operating point) ..........................................................................19
5.2.4.1 Selecting the welding parameter display mode ....................................19
5.2.4.2 Arc length..............................................................................................19
5.2.4.3 Arc dynamics (choke effect)..................................................................20
5.2.5 Operating modes (functional sequences).............................................................20
5.2.5.1 Explanation of signs and functions .......................................................20
5.2.5.2 Automatic cut-out.................................................................................. 20
5.2.6 Program sequence...............................................................................................26
5.2.7 Expert menu (MIG/MAG)......................................................................................27
5.2.8 Conventional MIG/MAG Welding (GMAW non synergic).....................................28
5.3 MMA welding .......................................................................................................................28
5.3.1 Welding task selection..........................................................................................28
5.3.2 Arcforce ................................................................................................................28
5.3.3 Hotstart.................................................................................................................29
5.3.3.1 Hotstart settings ....................................................................................29
5.3.4 Antistick ................................................................................................................ 29
5.4 TIG welding..........................................................................................................................30
5.4.1 Welding task selection..........................................................................................30
5.4.2 Adjusting the gas post-flow time...........................................................................30
5.4.3 Expert menu (TIG)................................................................................................31
5.4.4 Arc ignition............................................................................................................31
5.4.4.1 Liftarc ....................................................................................................31
5.4.5 Operating modes (functional sequences).............................................................32
5.4.6 Legend.................................................................................................................. 32
5.4.6.1 Automatic cut-out..................................................................................32
5.5 Machine configuration menu................................................................................................35
5.5.1 Selecting, changing and saving parameters ........................................................35
5.6 Power-saving mode (Standby) ............................................................................................36
6Maintenance, care and disposal................................................................................................. 37
6.1 General ................................................................................................................................37

Contents
Notes on using these operating instructions
4 099-M183xA-EW501
15.7.2022
6.2 Disposing of equipment........................................................................................................38
7Rectifying faults............................................................................................................................39
7.1 Software version of the machine control..............................................................................39
7.2 Error messages (power source)...........................................................................................39
7.3 Checklist for rectifying faults ................................................................................................40
7.4 Dynamic power adjustment..................................................................................................41
7.5 Resetting welding parameters to the factory settings..........................................................42
8Appendix .......................................................................................................................................43
8.1 JOB-List................................................................................................................................43
8.2 Parameter overview – setting ranges ..................................................................................44
8.3 Searching for a dealer..........................................................................................................45

For you
r safety
Notes on using these operating instructions
099-M183xA-EW501
15.7.2022
5
2 For your safety
2.1 Notes on using these operating instructions
DANGER
Working or operating procedures which must be closely observed to prevent imminent
serious and even fatal injuries.
•
Safety notes include the "DANGER" keyword in the heading with a general warning symbol.
• The hazard is also highlighted using a symbol on the edge of the page.
WARNING
Working or operating procedures which must be closely observed to prevent serious
and even fatal injuries.
• Safety notes include the "WARNING" keyword in the heading with a general warning sym-
bol.
• The hazard is also highlighted using a symbol in the page margin.
CAUTION
Working or operating procedures which must be closely observed to prevent possible
minor personal injury.
• The safety information includes the "CAUTION" keyword in its heading with a general warn-
ing symbol.
• The risk is explained using a symbol on the edge of the page.
Technical aspects which the user must observe to avoid material or equipment damage.
Instructions and lists detailing step-by-step actions for given situations can be recognised via bullet
points, e.g.:
• Insert the welding current lead socket into the relevant socket and lock.

For your safety
Explanation of icons
6 099-M183xA-EW501
15.7.2022
2.2 Explanation of icons
Symbol
Description
Symbol
Description
Indicates technical aspects which the
user must observe.
Activate and release / Tap / Tip
Switch off machine Release
Switch on machine
Press and hold
Switch
Incorrect / Invalid
Turn
Correct / Valid Numerical value – adjustable
Input
Signal light lights up in green
Navigation
Signal light flashes green
Output
Signal light lights up in red
Time representation (e.g.: wait 4 s / ac-
tuate)
Signal light flashes red
Interruption in the menu display (other
setting options possible)
Tool not required/do not use
Tool required/use

F
or your safety
Safety instructions
099-M183xA-EW501
15.7.2022
7
2.3 Safety instructions
WARNING
Risk of accidents due to non-compliance with the safety instructions!
Non-compliance with the safety instructions can be fatal!
• Carefully read the safety instructions in this manual!
• Observe the accident prevention regulations and any regional regulations!
• Inform persons in the working area that they must comply with the regulations!
Risk of injury from electrical voltage!
Voltages can cause potentially fatal electric shocks and burns on contact. Even low volt-
ages can cause a shock and lead to accidents.
• Never touch live components such as welding current sockets or stick, tungsten or wire
electrodes!
• Always place torches and electrode holders on an insulated surface!
• Wear the full personal protective equipment (depending on the application)!
• The machine may only be opened by qualified personnel!
• The device must not be used to defrost pipes!
Hazard when interconnecting multiple power sources!
If a number of power sources are to be connected in parallel or in series, only a tech-
nical specialist may interconnect the sources as per standard IEC 60974-9:2010: Instal-
lation and use and German Accident Prevention Regulation BVG D1 (formerly VBG 15)
or country-specific regulations.
Before commencing arc welding, a test must verify that the equipment cannot exceed
the maximum permitted open circuit voltage.
• Only qualified personnel may connect the machine.
• When taking individual power sources out of operation, all mains and welding current leads
must be safely disconnected from the welding system as a whole. (Hazard due to reverse
polarity voltage!)
• Do not interconnect welding machines with pole reversing switch (PWS
series) or machines
for AC welding since a minor error in operation can cause the welding voltages to be com-
bined, which is not permitted.
Risk of injury due to radiation or heat!
Arc radiation can lead to skin and eye injuries.
Contact with hot workpieces and sparks can lead to burns.
• Use hand shield or welding helmet with the appropriate safety level (depends on the appli-
cation).
• Wear dry protective clothing (e.g. hand shield, gloves, etc.) in accordance with
the applicable regulations of your country.
• Persons who are not directly involved should be protected with a welding curtain or suitable
safety screen against radiation and the risk of blinding!

For your safety
Safety instructions
8 099-M183xA-EW501
15.7.2022
WARNING
Risk of injury due to improper clothing!
During arc welding, radiation, heat and voltage are sources of risk that cannot be
avoided. The user has to be equipped with the complete personal protective equipment
at all times. The protective equipment has to include:
• Respiratory protection against hazardous substances and mixtures (fumes and vapours);
otherwise implement suitable measures such as extraction facilities.
• Welding helmet with proper protection against ionizing radiation (IR and UV radiation) and
heat.
• Dry welding clothing (shoes, gloves and body protection) to protect against warm environ-
ments with conditions comparable to ambient temperatures of 100 °C or higher and arcing
and work on live components.
• Hearing protection against harming noise.
Explosion risk!
Apparently harmless substances in closed containers may generate excessive pressure
when heated.
• Move containers with inflammable or explosive liquids away from the working area!
• Never heat explosive liquids, dusts or gases by welding or cutting!
Fire hazard!
Due to the high temperatures, sparks, glowing parts and hot slag that occur during
welding, there is a risk of flames.
• Be watchful of potential sources of fire in the working area!
• Do not carry any easily inflammable objects, e.g. matches or lighters.
• Ensure suitable fire extinguishers are available in the working area!
• Thoroughly remove any residue of flammable materials from the workpiece prior to starting
to weld.
• Only further process workpieces after they have cooled down. Do not allow them to contact
any flammable materials!

For your safety
Safety instructions
099-M183xA-EW501
15.7.2022
9
CAUTION
Smoke and gases!
Smoke and gases can lead to breathing difficulties and poisoning. In addition, solvent
vapour (chlorinated hydrocarbon) may be converted into poisonous phosgene due to
the ultraviolet radiation of the arc!
• Ensure that there is sufficient fresh air!
• Keep solvent vapour away from the arc beam field!
• Wear suitable breathing apparatus if appropriate!
Noise exposure!
Noise exceeding 70 dBA can cause permanent hearing damage!
• Wear suitable ear protection!
• Persons located within the working area must wear suitable ear protection!
According to IEC 60974-10, welding machines are divided into two classes of electro-
magnetic compatibility (the EMC class can be found in the Technical data):
Class A machines are not intended for use in residential areas where the power supply comes
from the low-voltage public mains network. When ensuring the electromagnetic compatibility of
class A machines, difficulties can arise in these areas due to interference n
ot only in the supply
lines but also in the form of radiated interference.
Class B machines fulfil the EMC requirements in industrial as well as residential areas, includ-
ing residential areas connected to the low-voltage public mains network.
Setting up and operating
When operating arc welding systems, in some cases, electro-magnetic interference can occur
although all of the welding machines comply with the emission limits specified in the standard.
The user is responsible for any interference caused by welding.
In order to evaluate any possible problems with electromagnetic compatibility in the surround-
ing area, the user must consider the following: (see also EN 60974-10 Appendix A)
• Mains, control, signal and telecommunication lines
• Radios and televisions
• Computers and other control systems
• Safety equipment
• The health of neighbouring persons, especially if they have a pacemaker or wear a hearing
aid
• Calibration and measuring equipment
• The immunity to interference of other equipment in the surrounding area
• The time of day at which the welding work must be carried out
Recommendations for reducing interference emission
• Mains connection, e.g. additional mains filter or shielding with a metal tube
• Maintenance of the arc welding system
• Welding leads should be as short as possible and run closely together along the ground
• Potential equalization
• Earthing of the workpiece. In cases where it is not possible to earth the workpiece directly,
it should be connected by means of suitable capacitors.
• Shielding from other equipment in the surrounding area or the entire welding system
Electromagnetic fields!
The power source may cause electrical or electromagnetic fields to be produced which
could affect the correct functioning of electronic equipment such as IT or CNC devices,
telecommunication lines, power cables, signal lines and pacemakers.
• Observe the maintenance instructions > see 6 chapter!
• Unwind welding leads completely!
• Shield devices or equipment sensitive to radiation accordingly!
• The correct functioning of pacemakers may be affected (obtain advice from a doctor if nec-
essary).

For your safety
Transport and installation
10 099-M183xA-EW501
15.7.2022
CAUTION
Obligations of the operator!
The respective national directives and laws must be complied with when operating the
machine!
• Implementation of national legislation relating to framework directive 89/391/EEC on the in-
troduction of measures to encourage improvements in the safety and health of workers at
work and associated individual guidelines.
• In particular, directive 89/655/EEC concerning the minimum safety and health requirements
for the use of work equipment by workers at work.
• The regulations applicable to occupational safety and accident prevention in the country
concerned.
• Setting up and operating the machine as per IEC 60974.-9.
• Brief the user on safety-conscious work practices on a regular basis.
• Regularly inspect the machine as per IEC 60974.-4.
The manufacturer's warranty becomes void if non-genuine parts are used!
• Only use system components and options (power sources, welding torches, electrode hold-
ers, remote controls, spare parts and replacement parts, etc.) from our range of products!
• Only insert and lock accessory components into the relevant connection socket when the ma-
chine is switched off.
Requirements for connection to the public mains network
High-performance machines can influence the mains quality by taking current from the mains net-
work. For some types of machines, connection restrictions or requirements relating to the maxi-
mum possible line impedance or the necessary minimum supply capacity at the interface with the
public network (Point of Common Coupling, PCC) can therefore apply. In this respect, attention is
also drawn to the machines' technical data. In this case, it is the responsibility of the operator,
where necessary in consultation with the mains network operator, to ensure that the machine can
be connected.
2.4 Transport and installation
WARNING
Risk of injury due to improper handling of shielding gas cylinders!
Improper handling and insufficient securing of shielding gas cylinders can cause seri-
ous injuries!
• Observe the instructions from the gas manufacturer and any relevant regulations concern-
ing the use of compressed air!
• Do not attach any element to the shielding gas cylinder valve!
• Prevent the shielding gas cylinder from heating up.

For your safety
Transport and installation
099-M183xA-EW501
15.7.2022
11
CAUTION
Risk of accidents due to supply lines!
During transport, attached supply lines (mains leads, control cables, etc.) can cause
risks, e.g. by causing connected machines to tip over and injure persons!
• Disconnect all supply lines before transport!
Risk of tipping!
There is a risk of the machine tipping over and injuring persons or being damaged itself
during movement and set up. Tilt resistance is guaranteed up to an angle of 10° (ac-
cording to IEC 60974-1).
• Set up and transport the machine on level, solid ground.
• Secure add-on parts using suitable equipment.
Risk of accidents due to incorrectly installed leads!
Incorrectly installed leads (mains, control and welding leads or intermediate hose pack-
ages ) can present a tripping hazard.
• Lay the supply lines flat on the floor (avoid loops).
• Avoid laying the leads on passage ways.
Risk of injury from heated coolant and its connections!
The coolant used and its connection or connection points can heat up significantly dur-
ing operation (water-cooled version). When opening the coolant circuit, escaping cool-
ant may cause scalding.
• Open the coolant circuit only when the power source or cooling unit is switched off!
• Wear proper protective equipment (protective gloves)!
• Seal open connections of the hose leads with suitable plugs.
The units are designed for operation in an upright position!
Operation in non-permissible positions can cause equipment damage.
• Only transport and operate in an upright position!
Accessory components and the power source itself can be damaged by incorrect connection!
• Only insert and lock accessory components into the relevant connection socket when the
machine is switched off.
• Comprehensive descriptions can be found in the operating instructions for the relevant ac-
cessory components.
• Accessory components are detected automatically after the power source is switched on.
Protective dust caps protect the connection sockets and therefore the machine against dirt and
damage.
• The protective dust cap must be fitted if there is no accessory component being operated on
that connection.
• The cap must be replaced if faulty or if lost!

Intended use
Use and operation solely with the following machines
12 099-M183xA-EW501
15.7.2022
3 Intended use
WARNING
Hazards due to improper usage!
The machine has been constructed to the state of the art and any regulations and stand-
ards applicable for use in industry and trade. It may only be used for the welding proce-
dures indicated at the rating plate. Hazards may arise for persons, animals and material
objects if the equipment is not used correctly. No liability is accepted for any damages
arising from improper usage!
• The equipment must only be used in line with its designated purpose and by trained or ex-
pert personnel!
• Do not improperly modify or convert the equipment!
3.1 Use and operation solely with the following machines
This description may only be applied to machines with the machine control M1.83-A-1
(Picomig puls TKG).
3.2 Software version
The software version of the machine control can be displayed in the machine configuration menu
(menu Srv)> see 5.5 chapter.
3.3 Documents which also apply
3.3.1 Warranty
For more information refer to the "Warranty registration" brochure supplied and our information regarding
warranty, maintenance and testing at www.ewm-group.com!
3.3.2 Declaration of Conformity
This product corresponds in its design and construction to the EU directives listed in the decla-
ration. The product comes with a relevant declaration o
f conformity in the original.
The manufacturer recommends carrying out the safety inspection according to national and in-
ternational standards and guidelines every 12 months.
3.3.3 Welding in environments with increased electrical hazards
Power sources with this marking can be used for welding in an environment with increased elec-
trical hazard (e.g. boilers). For this purpose, appropriate national or international regulations
must be followed. The power source must not be placed in the danger zone!
3.3.4 Service documents (spare parts and circuit diagrams)
WARNING
No improper repairs and modifications!
To prevent injuries and damage to the machine, only competent personnel (authorised
service personnel) are allowed to repair or modify the machine.
Unauthorised manipulations will invalidate the warranty!
• Instruct competent personnel (authorised service personnel) to repair the machine.
Original copies of the circuit diagrams are enclosed with the unit.
Spare parts can be obtained from the relevant authorised dealer.
3.3.5 Calibration/Validation
An original certificate is enclosed with the product. The manufacturer recommends calibration / validation
at intervals of 12 months.

Intended use
Documents which also apply
099-M183xA-EW501
15.7.2022
13
3.3.6 Part of the complete documentation
This document is part of the complete documentation and valid only in combination with all other
parts of these instructions! Read and observe the operating instructions for all system compo-
nents, especially the safety instructions!
The illustration shows a general example of a welding system.
Figure 3-1
Item
Documentation
A.1
Transport cart
A.2
Power source
A.3
Controller
A.4
Welding torch
A
Complete documentation

Machine description
– quick overview
Documents which als
o apply
14 099-M183xA-EW501
15.7.2022
4 Machine description – quick overview
Figure 4-1
Item
Symbol
Description 0
1
“Collective interference” signal light
2
“Excess temperature” signal light
3
Welding data display (3-digit)
Displays the welding parameters and the corresponding values > see 4.1 chapter
4
Push-button for welding parameter display mode / power-saving mode
--------- Welding current
--------- Material thickness
--------- Wire feed speed
Press for 2 s to put the machine into power-saving mode.
To reactivate, operate any control element > see 5.6 chapter.
5 Display, JOB
Shows the currently selected welding task (JOB number).
6 JOB-
LIST Welding task push-button (JOB)
Select the welding task from the welding task list (JOB-LIST). The list can be found in-
side the protective cap on the wire feeder and in the appendix to these operating in-
structions.
7
Welding parameter setting dial
For setting the welding performance, for selecting the JOB (welding task) and for set-
ting other welding parameters.

Machine description –
quick overview
Documents which also apply
099-M183xA-EW501
15.7.2022
15
Item
Symbol
Description 0
8 Operating mode button
----------Non-latched
--------Latched
-----Spots
------Interval
9
Runtime parameters button
For selecting the parameters to be set. Also for entering and exiting the menus for ad-
vanced settings.
----Choke effect/dynamics
----Gas post-flow time
----Spot time
----Pause time
10
Rotary knob for correcting the arc length (voltage correction)
11
Push-button for welding type
---Standard arc welding
------Pulsed arc welding
12
Push-button gas test / rinse hose package > see 5.1 chapter
13
Signal light polarity setting
14
Signal light polarity setting

Machine description
– quick overview
Welding data display
16 099-M183xA-EW501
15.7.2022
4.1 Welding data display
Figure 4-2
The push-button for the welding parameter display mode is next to the display.
Each time the push-button is pressed the display changes to the next parameter. After the last parameter
is reached the display continues with the first parameter.
The display shows:
• Nominal values (before welding)
• Actual values (during welding)
• Hold values (after welding)
MIG/MAG
Parameter
Nominal values
Actual values
Hold values
Welding current
/
[1]
Material thickness
Wire feed speed
Welding voltage
[1] traditional MIG/MAG
TIG/MMA
Parameter
Nominal values
Actual values
Hold values
Welding current
Welding voltage
After the welding, the display switches form hold values to nominal values by
• pressing the push-buttons or turning the rotary knobs of the control
• waiting for about 5 seconds
4.1.1 Polarity setting
The polarity setting displays the polarity required for the selected JOB on the machine con-
trol > see 4 chapter. The required polarity can then be set with the polarity selection plug.

Functional characteristics
Gas test – setting the s
hielding gas volume
099-M183xA-EW501
15.7.2022
17
5 Functional characteristics
5.1 Gas test – setting the shielding gas volume
If the shielding gas setting is too low or too high, this can introduce air to the weld pool and may cause
pores to form. Adjust the shielding gas quantity to suit the welding task!
• Slowly open the gas cylinder valve.
• Open the pressure regulator.
• Switch on the power source at the main switch.
• Set the relevant gas quantity for the application on the pressure regulator.
• Press the push-button “gas test / flush” to activate the gas test > see 4 chapter.
Shielding gas flows for around 25 seconds or until the button is pressed again.
Repeat rinsing process several times.
Setting instructions
Welding process
Recommended shielding gas quantity
MAG welding
Wire diameter x 11.5 = l/min
MIG brazing
Wire diameter x 11.5 = l/min
MIG welding (aluminium)
Wire diameter x 13.5 = l/min (100 % argon)
TIG
Gas nozzle diameter in mm corresponds to l/min gas throughput
Helium-rich gas mixtures require a higher gas volume!
The table below can be used to correct the gas volume calculated where necessary:
Shielding gas
Factor
75% Ar/25% He
1.14
50% Ar/50% He
1.35
25% Ar/75% He
1.75
100% He
3.16
5.2 MIG/MAG welding
5.2.1 Definition of MIG/MAG welding tasks
This machine range features simple operation with a very wide range of functions.
• JOBs (welding tasks consisting of welding process, type of material, wire diameter and type of shield-
ing gas) are pre-defined for all common welding tasks.
• Simple JOB selection from a list of pre-defined JOBs (sticker on the machine).
• The required process parameters are calculated by the system depending on the operating point
specified (single-dial operation via wire speed rotary dial).
• Conventional welding task definition using wire speed and welding voltage is also possible.
The welding task definition described below applies when defining MIG/MAG and cored wire weld-
ing tasks.
Pay attention to the signal light for the polarity setting!
It may be necessary to change the welding current polarity depending on the JOB selected or the
welding process.
• Reconnect the polarity selction plug if necessary.

Functional characteristics
MIG/MAG welding
18 099-M183xA-EW501
15.7.2022
5.2.2 Welding task selection
The following steps have to be carried out to select the welding job:
• Select basic parameters (material type, wire diameter and shielding gas type) and welding procedures
(select and enter JOB number by means of JOB-List > see 8.1 chapter).
• Select operating and welding type
• Adjust welding power
• Correct arc length and dynamics if necessary
• Adjust expert parameters for special applications
5.2.2.1 Basic welding parameters
The user must first determine the basic parameters (material type, wire diameter and shielding gas type)
of the welding system. These basic parameters are then compared with the welding job list (JOB-LIST).
The combination of the basic parameters gives a JOB number, which must now be entered on the control
unit. This basic setting must be rechecked or adjusted only when changing the wire or gas.
JOB-LIST
JOB
3s
Figure 5-1
The settings for spot time, pause time and wire feed speed apply to all JOBs. All other parameter
values are stored separately in each JOB. Changes are permanently saved in the currently se-
lected JOB.
If required, these parameter values can be reset to the factory settings > see 7.5 chapter.
5.2.2.2 Operating mode
The operating mode determines the process sequence controlled by the welding torch. Detailed descrip-
tions of the operating modes > see 5.2.5 chapter.
Figure 5-2

Functional cha
racteristics
MIG/MAG welding
099-M183xA-EW501
15.7.2022
19
5.2.3 Welding type
Different forms of MIG/MAG processes are collectively referred to as welding types.
Standard (welding with standard arc)
Depending on the set combination of wire feed speed and arc voltage, short arc, transitional arc or spray
arc can be used as arc types for welding.
Pulse (welding with pulsed arc)
A selective change in the welding current generates current pulses in the arc, which lead to a 1 drop per
pulse of material transfer. The result is an almost spatter-free process, suitable for welding all materials,
in particular high-alloy CrNi steels or aluminium.
Figure 5-3
5.2.4 Welding power (operating point)
5.2.4.1 Selecting the welding parameter display mode
The operating point (welding power) can be displayed or set as the welding current, material thickness or
wire speed.
Figure 5-4
5.2.4.2 Arc length
If required, the arc length (welding voltage) can be corrected from -5 V to +5 V for the individual welding
task.
Figure 5-5
The basic settings are now completed. Other welding parameters have already been set optimally in the
factory; they can, however, be modified to suit individual requirements.

Functional characteristics
MIG/MAG welding
20 099-M183xA-EW501
15.7.2022
5.2.4.3 Arc dynamics (choke effect)
This function can be used to adjust the arc between a narrow, hard arc with deep penetration (positive
values) and a wide and soft arc (negative values).
Figure 5-6
5.2.5 Operating modes (functional sequences)
5.2.5.1 Explanation of signs and functions
Symbol
Meaning
Press torch trigger
Release torch trigger
Shielding gas flowing
I
Welding output
Wire electrode is being conveyed
Wire creep
Wire burn-back
Gas pre-flows
Gas post-flows
Non-latched
Latched
t
Time
t1
Spot time
t2
Pause time
5.2.5.2 Automatic cut-out
Once the fault periods have elapsed, the automatic cut-out stops the welding process when it has been
triggered by one of two states:
• During ignition
5 s after the start of the welding process, no welding current flows (ignition error).
• During welding
The arc is interrupted for more than 5 s (arc interruption).
Table of contents
Other EWM Controllers manuals
Popular Controllers manuals by other brands
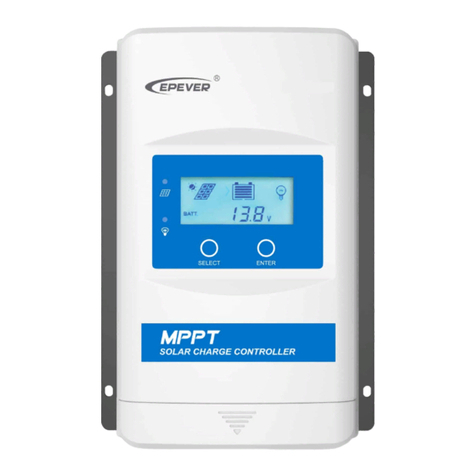
Epever
Epever XTRA Series user manual

Sanyo
Sanyo VSP-3000 Service manual
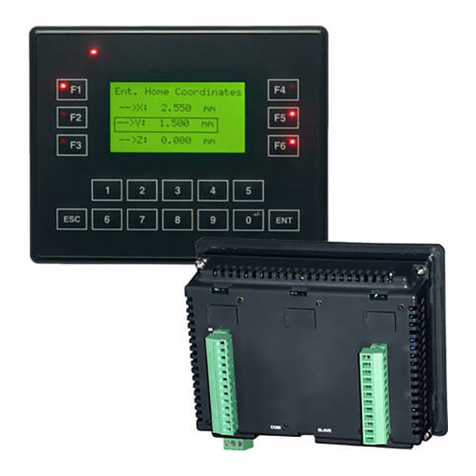
Toshiba
Toshiba OIS PLUS Series user manual
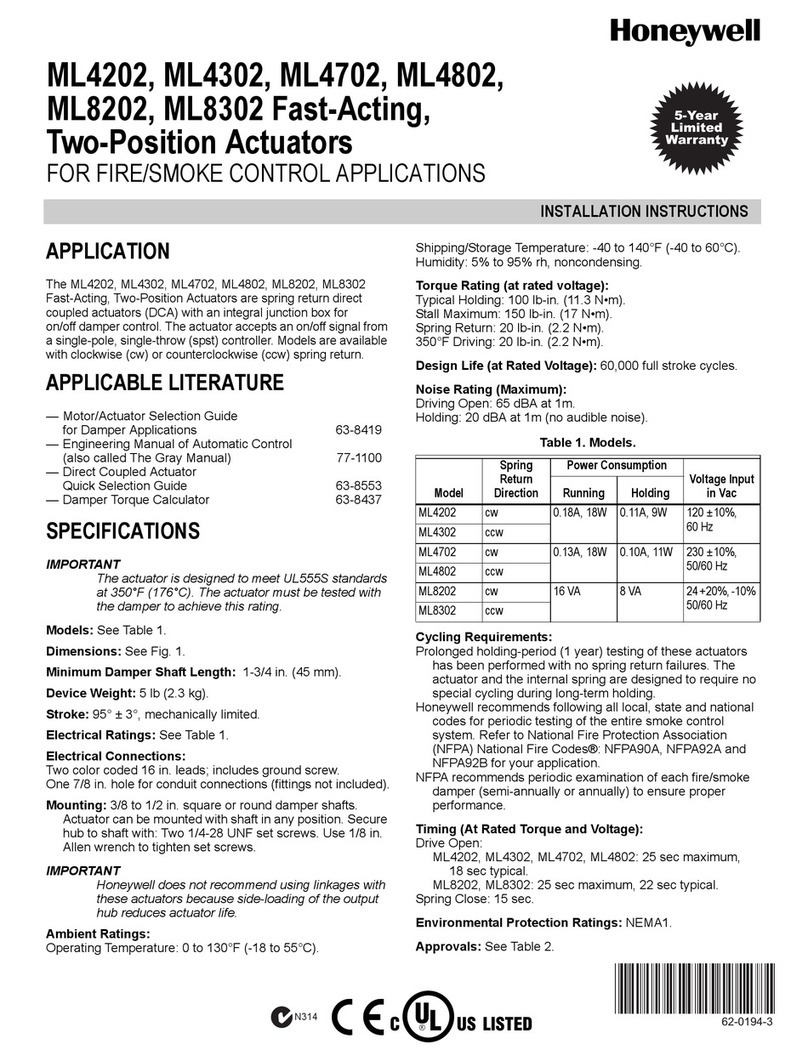
Honeywell
Honeywell FAST-ACTING, TWO-POSITION ACTUATORS ML4202 installation instructions
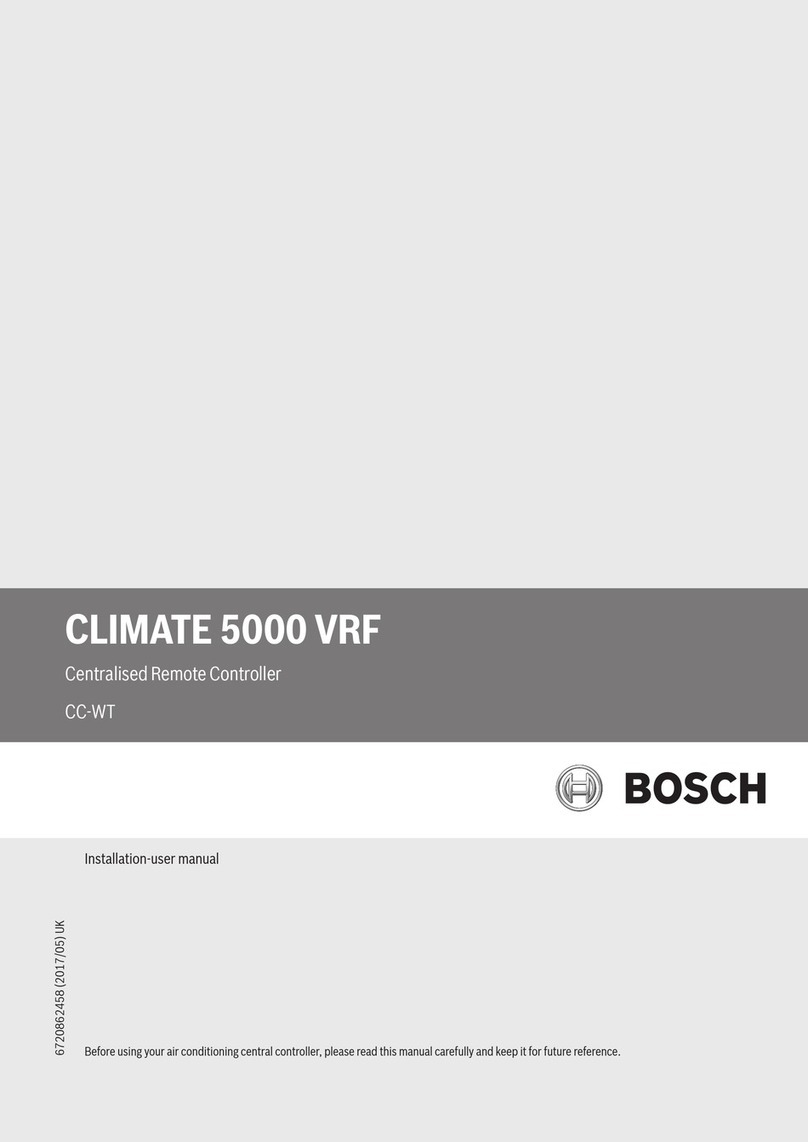
Bosch
Bosch CLIMATE 5000 VRF RDCI Series Installation & user manual
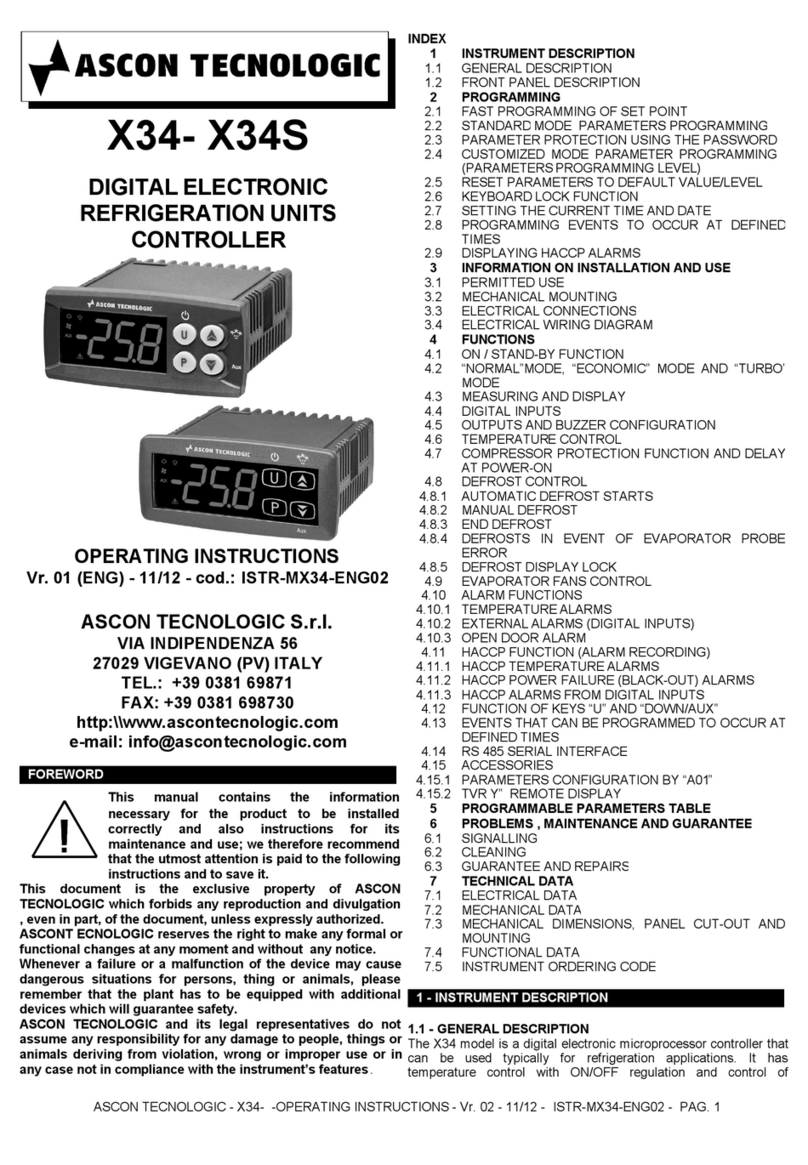
ascon
ascon X34S operating instructions
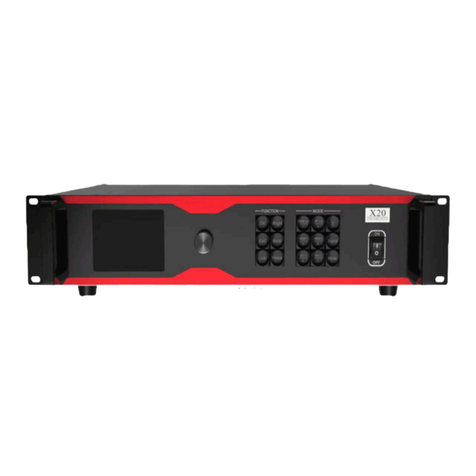
Colorlight
Colorlight X20 user manual
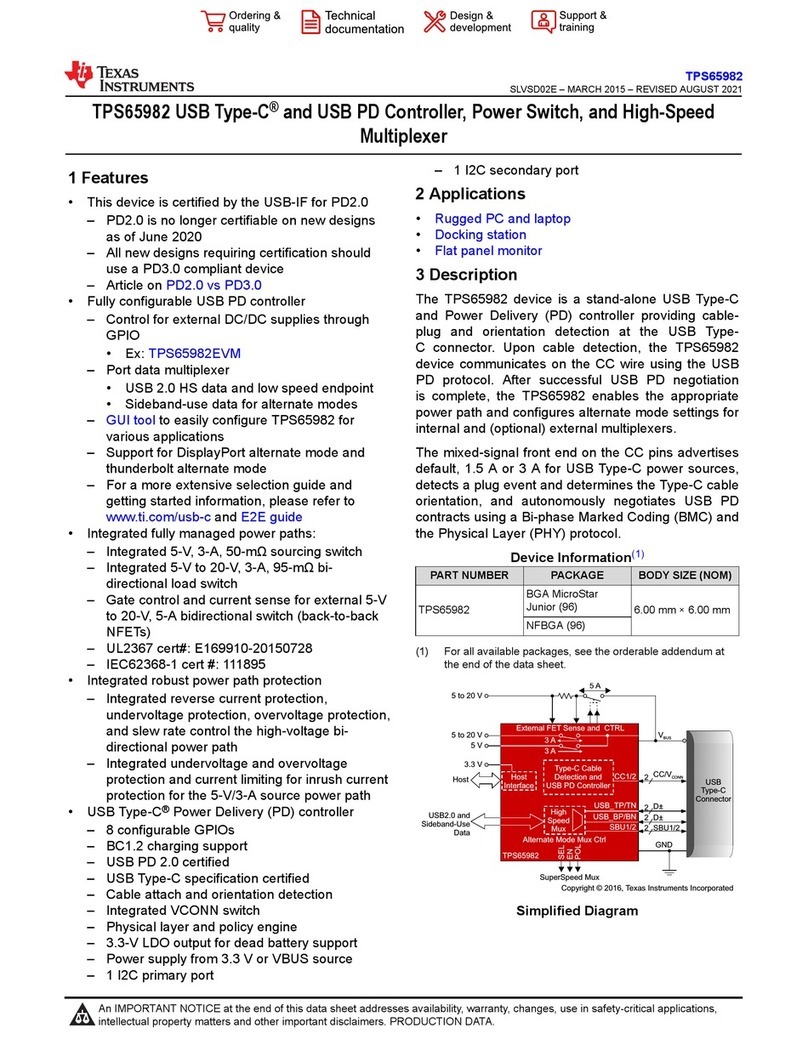
Texas Instruments
Texas Instruments TPS65982 manual
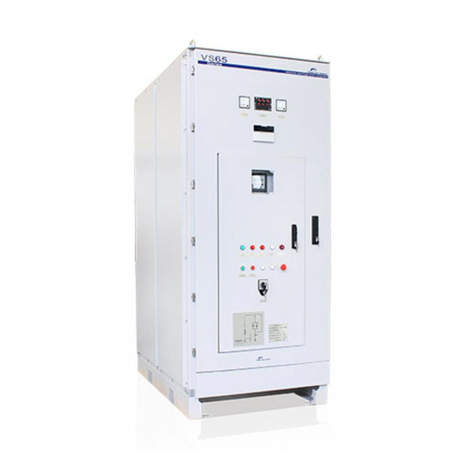
Power Electronics
Power Electronics VS65 Series Hardware and installation manual
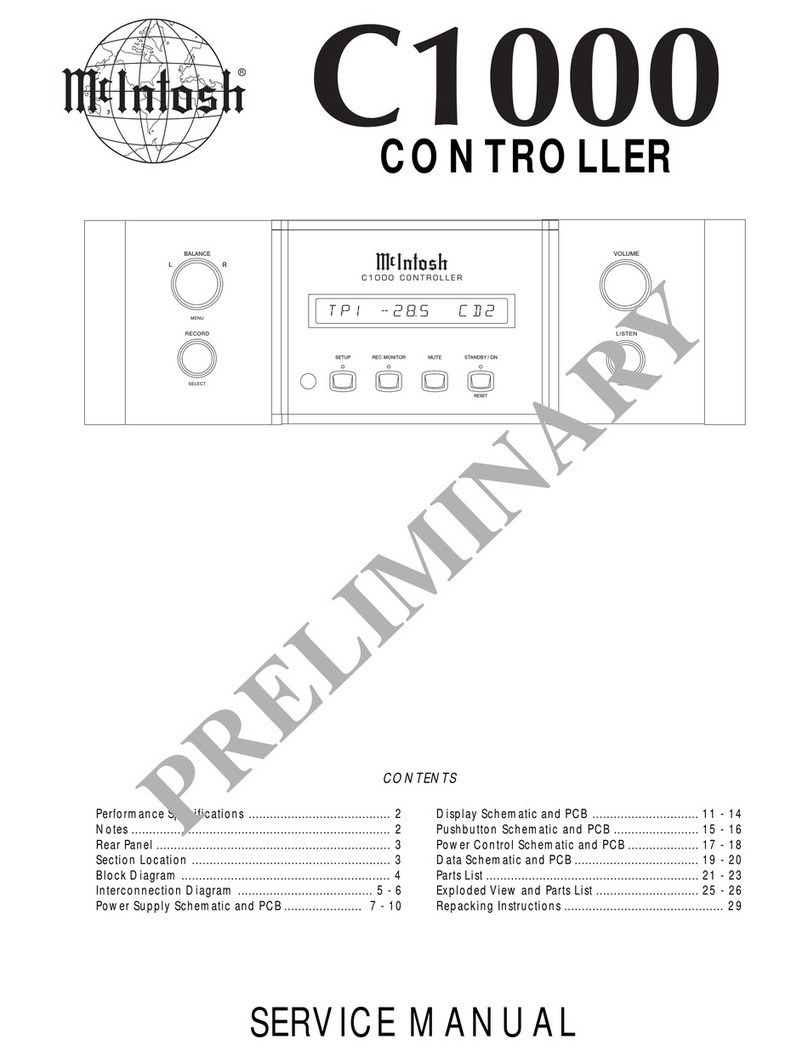
McIntosh
McIntosh C1000C - SERVICE Service manual
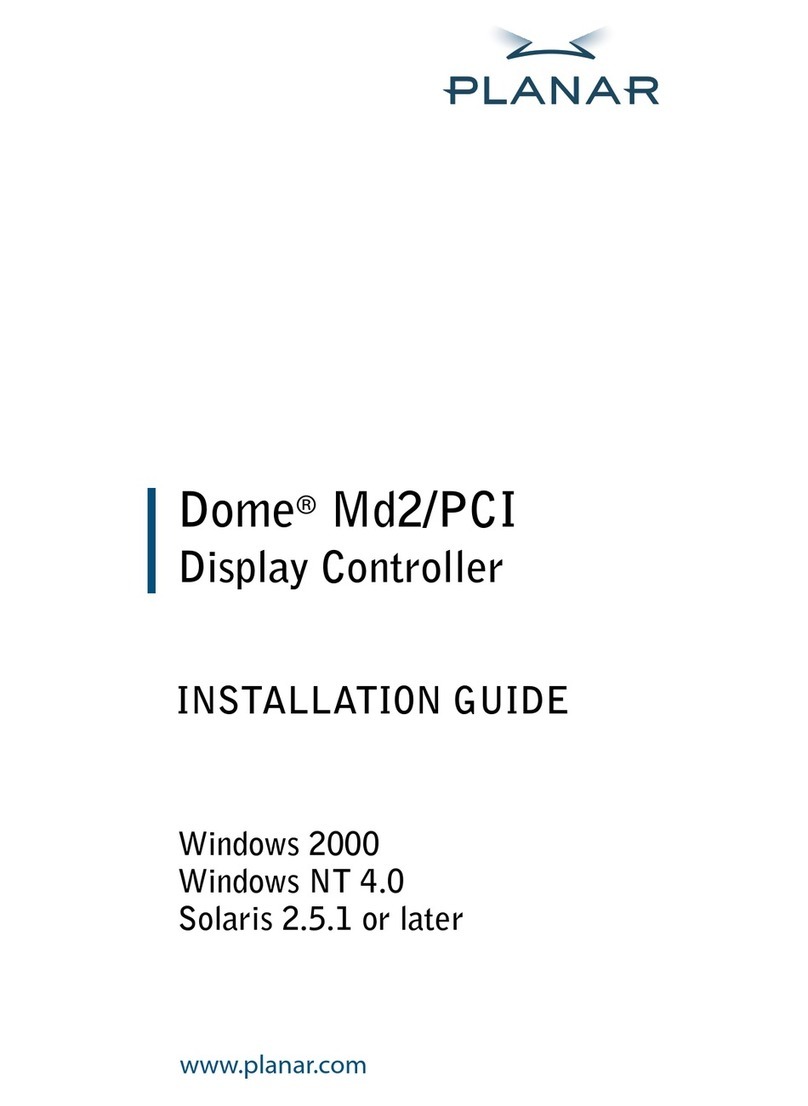
Planar
Planar Dome Md2/PCI installation guide
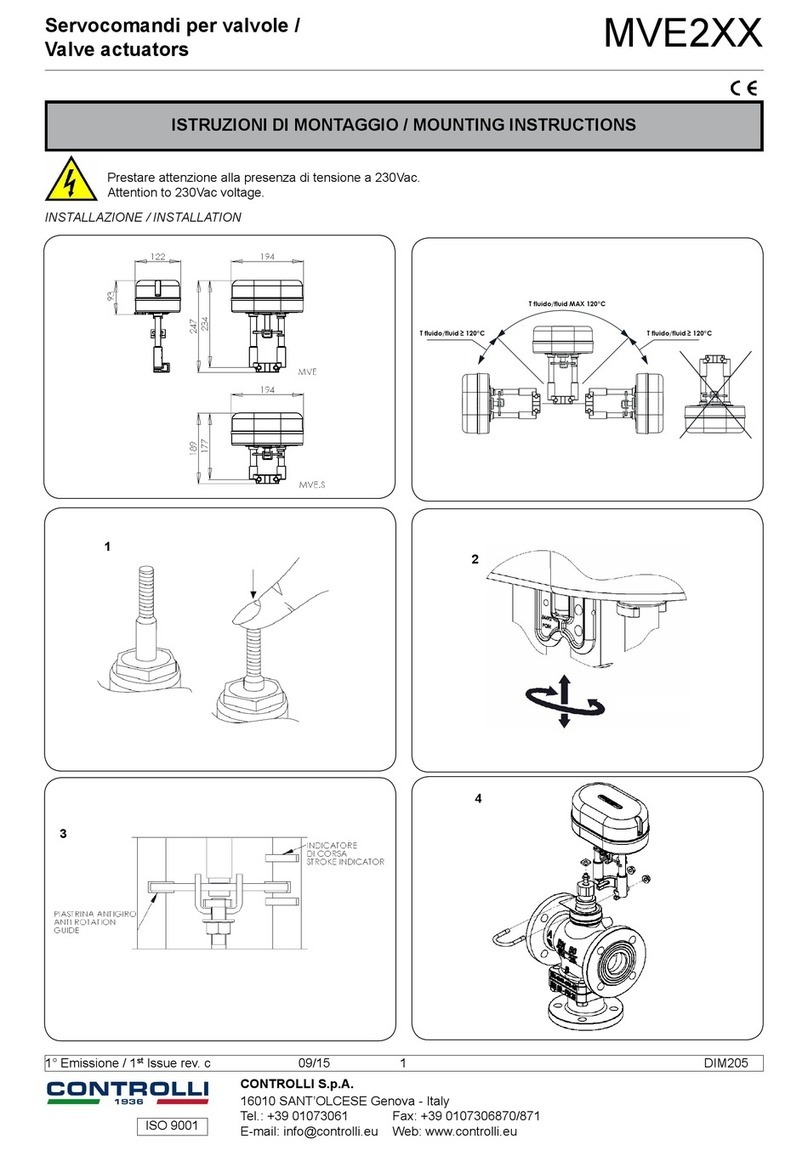
Controlli
Controlli MVE2XX Mounting instructions