Fastech EZI-STEP BT User manual

Operating Manual
www.fastech-motions.com

www.fastech-motions.com - 2
●
●
●
●
●
●
●
●
●
●
●
●
●
●
●
●
●
●
●
●
●
●
●
●
●
●
●
●
●
●
●
●
●
●
●
●
●
●
●
●
●
●
●
●
●
●
●
●
●
●
●
●
●
●
●
●
●
●
●
●
●
●
●
●
●
●
●
●
●
●
●
●
●
●
●
●
●
●
●
●
●
●
●
●
●
●
●
●
●
●
●
●
●
●
●
●
●
●
●
●
●
●
●
●
●
●
●
●
●
●
●
●
●
●
●
●
●
●
●
●
●
●
●
●
●
●
●
●
●
●
●
●
●
●
●
●
●
●
●
●
●
●
●
●
●
●
●
●
●
●
●
●
●
●
●
●
●
●
●
●
●
●
●
●
●
●
●
●
●
●
●
●
●
●
●
●
●
●
●
●
●
●
●
●
●
●
●
●
●
●
●
●
●
●
●
●
●
●
●
●
●
●
●
●
●
●
●
●
●
●
●
●
●
●
●
●
●
●
●
●
●
●
●
●
●
●
●
●
●
●
●
●
●
●
●
●
●
●
●
●
●
●
●
●
●
●
●
●
●
●
●
●
●
●
●
●
●
●
●
●
●
●
●
●
●
●
●
●
●
●
●
●
●
●
●
●
●
●
●
●
●
●
●
●
●
●
●
●
●
●
●
●
●
●
●
●
●
●
●
●
●
●
●
●
●
●
●
●
●
●
●
●
●
●
●
●
●
●
●
●
●
●
●
●
●
●
●
●
●
●
●
●
●
●
●
●
●
●
●
●
●
●
●
●
●
●
●
●
●
●
●
●
●
●
●
●
●
●
●
●
●
●
●
●
●
●
●
●
●
●
●
●
●
●
●
●
●
●
●
●
●
●
●
●
●
●
●
●
●
●
●
●
●
●
●
●
●
●
●
●
●
●
●
●
●
●
●
●
●
●
●
●
●
●
●
●
●
●
●
●
●
●
●
●
●
●
●
●
●
●
●
●
●
●
●
●
●
●
●
●
●
●
●
●
●
●
●
●
●
●
●
●
●
●
●
●
●
●
●
●
●
●
●
●
●
●
●
●
●
●
●
●
●
●
●
●
●
●
●
●
●
●
●
●
●
●
●
●
●
●
●
●
●
●
●
●
●
●
●
●
●
●
●
●
●
●
●
●
●
●
●
●
●
●
●
●
●
●
●
●
●
●
●
●
●
●
●
●
●
●
●
●
●
●
●
●
●
●
●
●
●
●
●
●
●
●
●
●
●
●
●
●
●
●
●
●
●
●
●
●
●
●
●
●
●
●
●
●
●
●
●
●
●
●
●
●
●
●
●
●
●
●
●
●
●
●
●
●
●
●
●
●
●
●
●
●
●
●
●
●
●
●
●
●
●
●
●
●
●
●
●
●
●
●
●
●
●
●
●
●
●
●
●
●
●
●
●
●
●
●
●
●
●
●
●
●
●
●
●
●
●
●
●
●
●
●
●
●
●
●
●
●
●
●
●
●
●
●
●
●
●
●
●
●
●
●
●
●
●
●
●
●
●
●
●
●
●
●
●
●
●
●
●
●
●
●
●
●
●
●
●
●
●
●
●
●
●
●
●
●
●
●
●
●
●
●
●
●
●
●
●
●
●
●
●
●
●
●
●
●
●
●
●
●
●
●
●
●
●
●
●
●
●
●
●
●
●
●
●
●
●
●
●
●
●
●
●
●
●
●
●
●
●
●
●
●
●
●
●
●
●
●
●
●
●
●
●
●
●
●
●
●
●
●
●
●
●
●
●
●
●
●
●
●
●
●
●
●
●
●
●
●
●
●
●
●
●
●
●
●
●
●
●
●
●
●
●
●
●
●
●
●
●
●
●
●
●
●
●
●
●
●
●
●
●
●
●
●
●
●
●
●
●
●
●
●
●
●
●
●
●
●
●
●
●
●
●
●
●
●
●
●
●
●
●
●
●
●
●
●
●
●
●
●
●
●
●
●
●
●
●
●
●
●
●
●
●
●
●
●
●
●
●
●
●
●
●
●
●
●
●
●
●
●
●
●
●
●
●
●
●
●
●
●
●
●
●
●
●
●
●
●
●
●
●
●
●
●
●
●
●
●
●
●
●
●
●
●
●
●
●
●
●
●
●
●
●
●
●
●
●
●
●
●
●
●
●
●
●
●
●
●
●
●
●
●
●
●
●
●
●
●
●
●
●
●
●
●
●
●
●
●
●
●
●
●
●
●
●
●
●
●
●
●
●
●
●
●
●
●
●
●
●
●
●
●
●
●
●
●
●
●
●
●
●
●
●
●
●
●
●
●
●
●
●
●
●
●
●
●
●
●
●
●
●
●
●
●
●
●
●
●
●
●
●
●
●
●
●
●
●
●
●
●
●
3
6
6
7
7
7
8
9
9
10
10
11
11
11
11
12
12
13
13
14
15
16
17
18
18
18
18
18
19
19
19
19
19
20
Table of Contents
1. Precautions
2. Main characteristics
3. Simple and Compact all-in-one Motor integrated with Drive
4. Ezi-STEP BT Part Numbering
5. Standard Combination
6. Combination with Brake
7. Specifications of Drive
8. Specifications of Motor
9. Torque Characteristics of Motor
10. Dimensions of Motor [mm]
11. Notes on Installation
12. Settings and Operation
12.1 Drive Status LED
12.2 Power Connector(CN1)
12.3 Input/Output Signal Connector(CN2)
12.4 Parameter Setting Connector(CN3)
13. System Configuration
13.1 Options
13.2 Connector Specifications
14. External Wiring Diagram [Ezi-STEP-BT-42/56 series]
15. External Wiring Diagram [Ezi-STEP-BT-86 series]
16. Control Signal Input/Output Description
17. Parameter Settings GUI [User Interface]
18. Setting Up Parameters
18.1 Setting Up Parameters
18.2 Resolution Selection
18.3 Stop Current Selection
18.4 Rotational Direction Selection
18.5 Pulse Input Selection
18.6 Alarm Reset Input Selection
18.7 Alarm Output Selection
18.8 Run/Stop Output Selection
18.9 Motor Number, Motor Coils Current
Appendix

www.fastech-motions.com - 3
※ Before operation ※
·Thank you for your purchasing Ezi-STEP BT.
·Ezi-STEP BT is an all-in-one Unit. For high-speed and high-precision drive of a stepping motor,
Ezi-STEP BT is an unique drive that adopts a new control scheme owing to an on-board high-
performance 32bit digital signal processor.
·This manual describes handling, maintenance, repair, diagnosis and troubleshooting of Ezi-STEP BT.
·Before operating Ezi-STEP BT, thoroughly read this manual.
·After reading the manual, keep the manual near the Ezi-STEP BT so that any user can read the
manual whenever needed.
1. Precautions
◆ General Precautions
·Contents of this manual are subject to change without prior notice for functional im provement, change of
specifications or
user's better understanding. Thoroughly read the manual provided with the purchased
Ezi-STEP BT.
·When the manual is damaged or lost, please contact with Fastech's agents or our company at the address
on the last page of the manual.
·Our company is not responsible for a product breakdown due to user's dismantling for the product, and such
a breakdown is not guaranteed by the warranty.
◆ Put the Safety First
·Before installation, operation and repairing the Ezi-STEP BT, thoroughly read the manual and fully understand
the contents. Before operating the Ezi-STEP BT please, understand the mechanical characteristics of the Ezi-
STEP BT and related safety information and precautions.
·This manual divides safety precautions into Attention and Warning.
·Although precaution is only a Attention, a serious result could be caused depending on the situation.
Follow safety precautions.
Attention : If user does not properly handle the product, the user may seriously or slightly injured
and damages may occur in the machine.
Warning : If user does not properly handle the product, a dangerous situation (such as an electric
shock) may occur resulting in deaths or serious injuries.

www.fastech-motions.com - 4
◆ Check the Product
Check the Product is damaged or parts are missing.
Otherwise, the machine may get damaged or the user may get injured.
Attention
◆ Installation
Carefully move the Ezi-STEP BT.
Otherwise the Product may get damaged or User's foot may get injured by dropping the
product.
Use non-flammable materials such as metal in the place where the Ezi-STEP BT is to be
installed.
Otherwise, a fire may occur.
When installing several Ezi-STEP BT in a sealed place, install a cooling fan to keep the
ambient temperature of the Ezi-STEP BT as 50℃ or lower.
Otherwise, a fire or other kinds of accidents may occur due to overheating.
The process of Installation, Connection, Operation, Checking and Repairing should be
done with qualified person.
Otherwise, a fire or other kinds of accidents may occur.
Attention
Warning
◆ Connect Cables
Keep the rated range of lnput Voltage for Ezi-STEP BT.
Otherwise, a fire or other kinds of accidents may occur.
Cable connection should follow the wiring diagram.
Otherwise, a fire or other kinds of accidents may occur.
Before connecting cables, check if input power is off.
Otherwise, an electric shock or a fire may occur.
The case of the Ezi-STEP BT is insulated from the ground of the internal circuit by the
condenser. Ground the Ezi-STEP BT.
Otherwise, an electric shock or a fire may occur.
Attention
Warning

www.fastech-motions.com - 5
◆ Operation
◆ Check and Repair
If a protection function(alarm) occurs, firstly remove its cause and then release(alarm reset)
the protection function.
If you operate continuously without removing its cause, the machine may get damaged or
the user may get injured.
Do not make Motor Free and make input signal to ON during operation.
Motor will stop and stop current will become zero. The machine may get damaged or the
user may get injured.
Make all input signals to OFF before supply input voltage to Ezi-STEP BT.
The machine may get damaged or the user may get injured by motor operation.
All parameter values are set by default factory setting value. Change this value after
reading this manual throughly.
Otherwise, the machine may get damaged or other kinds of accidents may occur.
Stop to supply power to the main circuit and wait for a while before checking or
repairing the Ezi-STEP BT.
Electricity remaining in the capacitor may cause danger.
Do not change cabling while power is being supplied.
Otherwise, the user may get injured or the product may get damaged.
Do not reconstruct the Ezi-STEP BT.
Otherwise, an electric shock may occur or the reconstructed product can not get
After-Service.
Attention
Attention

www.fastech-motions.com - 6
2. Main characteristics
3. Simple and Compact all-in-one Motor integrated with Drive
Saving installation space and ease of wiring by integrating drive circuits on the back side of a stepping motor.
3
Drive Output Signal Monitoring
Ezi-STEP provides loss of step, run/stop, over-current,
over-heat, over-voltage, power and motor connection
alarms that can be monitored by the controller and
visible by a motor-mounted flashing LED indicator.
4
Improvement of High-Speed Driving
Depending on the speed of a stepping motor, Ezi-
STEP automatically increases the supply voltage and
prevents the torque lowering due to the low operating
voltage to the motor caused by back-emf voltage, this
enables high-speed operation. Additionally, the software
damping algorithm minimizes the vibration and prevents
the loss-of-synchronization at high-speed.
1
Microstep and Filtering
The high-performance MCU operates at step resolutions
of 1.8 ° up to maximum 0.0072 ° (1/250 steps) and Ezi-
STEP adjusts PWM control signal in every 25 μsec,
which makes it possible for more precise current control,
resulting in high-precision Microstep operation.
High precision Microstep function and Filtering
2
Software Damping
Vibration suppression and High-speed operation (Patent
pending) Motor vibration is created by magnetic flux
variations of the motor, lower current from the drive
due to back-emf from the motor at high speeds and
lowering of phase voltages from the drive.
Ezi-STEP drive detects these problems and the MCU
adjusts the phase of the current according to the pole
position of the motor, drastically suppressing vibration.
This allows the smooth operation of the motor at high
speeds.
Vibration suppression and high-speed
operation
Software Damping OFF
※ This is real measured speed that using 100,000 [pulse/rev] encoder.
Software Damping ON

www.fastech-motions.com - 7
4. Ezi-STEP BT Part Numbering 5. Standard Combination
6. Combination with Brake
Ezi-STEP-BT-42S-BK-□
Product Name
User Code
42
:
42mm
56
:
56mm
86
:
86mm
S
: Small
M
: Medium
L
: Large
XL
:
Extra Large
Motor Flange Size
Motor Length
Brake
Blank : Without Brake
BK : Brake
BT : Built In
Drive Series Type
Unit Part
Number
Motor Model
Number
Drive Model
Number
Ezi-STEP-BT-42S
Motor & Drive Integrated
Ezi-STEP-BT-42M
Ezi-STEP-BT-42L
Ezi-STEP-BT-42XL
Ezi-STEP-BT-56S
Ezi-STEP-BT-56M
Ezi-STEP-BT-56L
Ezi-STEP-BT-86M
Ezi-STEP-BT-86L
Ezi-STEP-BT-86XL
Unit Part
Number
Motor Model
Number
Drive Model
Number
Ezi-STEP-BT-42S-BK
Motor & Drive Integrated
Ezi-STEP-BT-42M-BK
Ezi-STEP-BT-42L-BK
Ezi-STEP-BT-42XL-BK
Ezi-STEP-BT-56S-BK
Ezi-STEP-BT-56M-BK
Ezi-STEP-BT-56L-BK
Ezi-STEP-BT-86M-BK
Ezi-STEP-BT-86L-BK
Ezi-STEP-BT-86XL-BK

www.fastech-motions.com - 8
Motor Model BT-42 series BT-56 series BT-86 series
Input Voltage 24VDC ±10% 40~70VDC
Control Method Bipolar PWM drive with 32bit MCU
Current Consumption Max 500mA (Except motor current)
Operating
Condition
Ambient
Temperature
·In Use: 0~50℃
·In Storage: -20~70℃
Humidity ·In Use: 35~85% RH (Non-Condensing)
·In Storage: 10~90% RH (Non-Condensing)
Vib. Resist. 0.5g
Function
Rotation Speed 0~3,000 [rpm] *1
Resolution [ppr]
500 1,000 1,600 2,000 3,200 3,600 4,000 5,000 6,400 8,000 10,000 20,000 25,000 36,000 40,000 50,000
(Selectable by parameter) * Default: 10,000
Maximum Frequency 500kHz (Duty 50%)
Protection Functions Over Current Error, Over Speed Error, Step Out Error, Over Temperature Error, Over Regenerated
Voltage Error, Motor Connect Error, Motor Voltage Error, System Error, ROM Error
LED Display Power status(Green), Alarm status(Red)
STOP Current 20%~100% (Selectable by parameter) Be setted to set value of STOP Current after 0.1 second after
motor stop. * Default: 50%
Pulse Input Method 1 Pulse / 2 Pulse (Selectable by parameter)
1 Pulse: Pulse/Direction, 2 Pulse: CW/CCW * Default: 2 Pulse
Rotational Direction CW/CCW (Selectable by parameter)
Used when changing the direction of motor rotate. * Default: CW
Speed/Position
Control Command Pulse Train Input (Photocoupler Input)
I/O
Signal
Input Signals Motor Free / Alarm Reset (Photocoupler Input)
Output Signals Alarm, Run/Stop (Photocoupler Output)
*1 : Up to the resolution of 10,000[ppr], maximum speed can be reached by 3,000[rpm] and with the resolution more than 10,000[ppr], maximum speed
shall be reduced accordingly.
7. Specifications of Drive

www.fastech-motions.com - 9
MODEL
Ezi-STEP-BT-42
series
Ezi-STEP-BT-56
series
Ezi-STEP-BT-86
series
UNIT 42S 42M 42L 42XL 56S 56M 56L 86M 86L 86XL
DRIVE METHOD -BI-POLAR
NUMBER OF PHASES -2 2 2 2 2 2 2 2 2 2
VOLTAGE VDC 3.36 4.32 4.56 7.2 1.56 1.62 2.64 2.34 3.6 4.8
CURRENT per PHASE A1.2 1.2 1.2 1.2 3.0 3.0 3.0 6.0 6.0 6.0
RESISTANCE per PHASE Ohm 2.8 3.6 3.8 6.0 0.52 0.54 0.88 0.39 0.6 0.8
INDUCTANCE per PHASE mH 5.4 7.2 8.0 15.6 1.2 2.0 4.0 3.0 6.5 8.68
HOLDING TORQUE N·m 0.32 0.44 0.5 0.65 0.64 1.0 1.5 4.5 8.5 12
ROTOR INERTIA g·c m
2
35 54 77 114 180 280 520 1800 3600 5400
WEIGHTS g250 280 350 500 500 720 1150 2300 3800 5300
LENGTH(L) mm 34 40 48 60 46 55 80 78 117 155
PERMISSIBLE
OVERHUNG LOAD
(DISTANCE FROM
END OF SHAFT)
3mm
N
22 22 22 22 52 52 52 270 270 270
8mm 26 26 26 26 65 65 65 300 300 300
13mm 3 3 33 33 33 85 85 85 350 350 350
18mm 46 46 46 46 123 123 123 400 400 400
PERMISSIBLE THRUST LOAD NLower than motor weight
INSULATION RESISTANCE Mohm 100 MIN.(at 500VDC)
INSULATION CLASS -CLASS B(130℃)
OPERATING TEMPERATURE ℃0 to 55
Ezi-STEP-BT-42 series
0.6
0.5
0.4
0.3
0.2
0.1
0
10 500 1,000 1,500 2,000 2,500 3,000
24V
42S
42M
42L
42XL
Motor Voltage :
Torque[N.m]
Speed[rpm]
Ezi-STEP-BT-56 series
1.5
1.2
0.9
0.6
0.3
0
10 500 1,000 1,500 2,000 2,500 3,000
24V
Torque[N.m]
Speed[rpm]
56S
56M
56L
Motor Voltage :
Ezi-STEP-BT-86 series
86M
86L
86XL
Torque[N.m]
Speed[rpm]
10
8
6
4
2
0
10 500 1,000 1,500 2,000 2,500 3,000
70V
Motor Voltage :
8. Specifications of Motor
9. Torque Characteristics of Motor

www.fastech-motions.com - 10
11. Notes on Installation
1) Ezi-STEP BT is designed for indoor use only.
2) The ambient temperature of the room should be 0℃~50℃.
3) If the temperature of the product case is higher than 50℃, radiate heat of the
outside to cool down.
4) Do not install Ezi-STEP BT under direct rays, near magnetic or radioactive objects.
42mm
Model name Length(L)
42S 34
42M 40
42L 48
42XL 60
□
42
0
4-31
±0.2
0.1
4.5
±0.1
Ø
22.0
-0.05
0
+1
L+33.9
±1
L
±1
57
A
A
1.8
±0.2
20
±0.2
24
±0.5
Ø
0.075 A
4-M3 DP4.5
Ø
5
-0.011
0
0.025
86mm
Model name Length(L)
86M 78
86L 117
86XL 155
56mm
Model name Length(L)
56S 46
56M 55
56L 80
A
□
86
±0.5
4-69.5
±0.2
1.6
±0.2
2-25
±0.3
±1
Ø0.076
0.05
A
0.076
Ø
73
-0.05
0
4-Ø6.5 0 THRU
+0.3
L+46
±1
L
±1
10
±0.5
Ø
14
-0.013
0
2-13
-0.1
0
A
37
100.5
A
□
57.15
±0.25
4-47.14
±0.2
1.6
±0.25
15
±0.2
±0.5
Ø
0.075
0.025
0.1
4-Ø5
0
THRU
Ø
38.1
-0.039
5.8
±0.1
0
+0.3
L+36
±1
L
±1
73.5
5
±0.25
Ø
6.35
-0.013
0
A
20
A
10. Dimensions of Motor [mm]

www.fastech-motions.com - 11
12.1 Drive Status LED
◆ Protection functions and LED flash times
Indication Color Function ON/OFF Condition
PWR Green Power input indication Lights when power is ON Flashs when motor is
Free status.
ALM Red Alarm indication
Flash when protection function is activated
(Identifiable which protection mode is activated
by counting the blinking times)
Times Protection Conditions
1Over Current Error
The current through power devices in drive exceeds the limit value
*1
2Over Speed Error Motor speed exceed 3,000 [rpm]
3Step Out Error Abnormally motor do not followed pulsed input
5Over Temperature Error Inside temperature of drive exceeds 85℃
6Over Regeneratived
Voltage Error
Back-EMF more high limit value
BT-42/56 series: 50V, BT-86 series: 90V
7Motor Connect Error The power is ON without connection of the motor cable to drive
9Motor Voltage Erroe Motor voltage is out of limited value
BT-42/56 series: 20V, BT-86 series: 36V
11 System Error Error occurs in drive system
12 ROM Error Error occurs in parameter storage device(ROM) Alarm LED flash (Ex, Step Out Error)
※ BT-42, BT-56 series.
※ BT-86 series.
12.2 Power Connector(CN1)
NO. Function I/O
124VDC Input
2GND Input
3F.GND Input
4NC ----
NO. Function I/O
140~70VDC Input
2GND Input
4
2
3
1
2 1
12.3 Input/Output Signal Connector(CN2)
NO. Function I/O
1CW+(Pulse+) Input
2CW-(Pulse-) Input
3CCW+(Dir+) Input
4CCW-(Dir-) Input
5Alarm Output
6EXT_GND Input
7EXT_24VDC Input
8Alarm Reset Input
9Run/Stop Output
10 F.GND ----
*1 : Limit value depends on motor model
Drive status LED
Input/Output Signal connection(CN2)
Power connection(CN1)
Parameter setting communication connection(CN3)
2
1
10
9
12. Settings and Operation

www.fastech-motions.com - 12
Type Power Cable Signal Cable Parameter Setting Cable
Length supplied 30m 30cm -
Max. Length 2m 20m 3m
12.4 Parameter Setting Connector(CN3)
NO. Function I/O
1Tx Output
2Rx Input
3GND ---- 1 2 3
①
②
③
13. System Configuration

www.fastech-motions.com - 13
13.1 Options
① Power Cable
Available to connect between Power and Ezi-STEP BT.
Item Length [m] Remark
CBTS-P-□ □ □F
*1
CBTS-P-□ □ □M
*1
□ □ □
□ □ □
Normal Cable
Robot Cable
CBTL-P-□ □ □F
*2
CBTL-P-□ □ □M
*2
□ □ □
□ □ □
Normal Cable
Robot Cable
*1 : Ezi-STEP-BT-42/56 series
*2 : Ezi-STEP-BT-86 series
□ is for Cable Length. The unit is 1m and Max. 2m length.
③ Parameter Setting Cable
Available to connect between PC and Ezi-STEP BT.
This is used for change setting value of Resolution and
Stop Current etc.
Item Length [m] Remark
CBTS-C-□ □ □F □ □ □ Normal Cable
□ is for Cable Length. The unit is 1m and Max. 3m length.
② Signal Cable
Available to connect between Input/Output Control System
and Ezi-STEP BT.
Item Length [m] Remark
CBTS-S-□ □ □F
CBTS-S-□ □ □M
□ □ □
□ □ □
Normal Cable
Robot Cable
□ is for Cable Length. The unit is 1m and Max. 20m length.
Purpose Item Part Number Manufacturer
Power
(CN1)
BT-42/56
series
Housing
Terminal
5557-04R
5556T MOLEX
BT-86
series
Housing
Terminal
3191-2R
1381T MOLEX
Signal
(CN2)
Housing
Terminal
XADRP-10V
SXA-001T-P0.6 JST
Parameter
Setting
Drive Side
(CN3)
Housing
Terminal
5264-03
5263 MOLEX
PC Side D-SUB Connector
Terminal
717SD-ESD9S
7E-1675-09 AMPHENOL
13.2 Connector Specifications
Connector specifications for cabling to drive.
※ Above connector is the most suitable product for the drive applied. Another equivalent connector can be used.

www.fastech-motions.com - 14
※ Alarm Reset signal line is also used for Motor Free signal.
(For details, please refer to Control Signal Input/Output Description)
※ When connects I/O cable between controller and drive, please turn off the power of both controller and drive, in order to protect
the drive from any damage.
Shielded
Twisted Pair
Cable
14. External Wiring Diagram [Ezi-STEP-BT-42/56 series]

www.fastech-motions.com - 15
※ Alarm Reset signal line is also used for Motor Free signal.
(For details, please refer to Control Signal Input/Output Description)
※ When connects I/O cable between controller and drive, please turn off the power of both controller and drive, in order to protect
the drive from any damage.
Shielded
Twisted Pair
Cable
15. External Wiring Diagram [Ezi-STEP-BT-86 series]

www.fastech-motions.com - 16
◆ CW, CCW Input
This signal can be used to receive a positioning pulse
command from a user host motion controller. The user can
select 1-pulse input mode or 2-pulse input mode (refer
to switch No.1, SW1). The input schematic of CW, CCW is
designed for 5V TTL level. When using 5V level as an input
signal, the resistor Rx is not used and connect to the driver
directly. When the level of input signal is more than 5V, Rx
resistor is required. If the resistor is absent, the drive will be
damaged. If the input signal level is 12V, Rx value is 680ohm
and 24V, Rx value is 1.8Kohm.
◆ Motor Free Input
This input can be used only to adjust the position by manually
moving the motor shaft from the load-side. By setting the
signal [ON], the drive cuts off the power supply to the motor.
Then, one can manually adjust output position. When setting
the signal back to [OFF], the drive resumes the power supply
to the motor and recovers the holding torque. When driving a
motor, one needs to set the signal [OFF]. In normal operations
set the signal [OFF] or disconnect a wire to the signal.
◆ Alarm Reset Input
When a protection mode has been activated, a signal to this
Alarm Reset input cancels the Alarm output. By setting the
alarm reset input signal [ON], cancel Alarm output. Before
cancel the Alarm output, have to remove the source of alarm.
[Caution] If Alarm Reset input signal still remains [ON], motor will be
Free state. Keep in mind to change [ON]→[OFF] state.
1
Input Signal
Input signals of the drive are all photocoupler protected.
The signal shows the status of internal photocouplers
[ON: conduction], [OFF: Non-conduction], not displaying
the voltage levels of the signal.
◆ Alarm Output
The Alarm output indicates [OFF] when the drive is in a
normal operation. If a protection mode has been activated, it
goes [ON]. A host controller meeds to detect this signal and
stop sending a motor driving command.
When the drive detects an abnormal operation such as
overload of overcurrent of a motor, it sets the Alarm output to
[ON], flash the Alarm LED, disconnects the power to a motor
and stops the motor, simultaneously.
2
Output Signal
As the output signal from the drive, there are the
photocoupler outputs (Alarm, Run/Stop). The signal status
operate as [ON : conduction], [OFF : Non-conduction] of
photocoupler not as the voltage level of signal.
◆ Run/Stop Output
Run/Stop Output state is [ON] when motor positioning is
completed. It operates reversely compare to Normal mode,
when you set inverse mode.
Pin No. Function
1 CW+
2 CW-
3 CCW+
4 CCW-
Pin No. Function
5 Alarm
9 Run/Stop
6 EXT_GND
Pin No. Function
8 Alarm Reset
7 EXT_24VDC
Alarm Reset signal line is also used for Motor Free signal.
16. Control Signal Input/Output Description

www.fastech-motions.com - 17
Ezi-STEP BT drive utilizes various parameters for operation and some parameters can be changed upon the needs
of the user. Ezi-STEP BT provides Drive Setting Program for more convenient use. The screen shot in right side
is the sample of Drive Setting Program which is used for drive setting and parameter change. User can change
and set the parameter such as Resolution, Stop Current, level of Alarm Reset, Alarm, Motion Direction and so
on. By using this drive setting program, user can find the optimal condition to Ezi-STEP BT to fit with the user's
own system. Please be noticed that connection for drive setting program shall be done when the Ezi-STEP BT is
disable staus for safety reason.
※ Parameter setting program can be downloaded from website. (www.fastech-motions.com)
※ Parameter setting program can support Window 7/8/10.
※ Parameter setting program(GUI) can be updated without notice to improve the performance and convenience of user.
17. Parameter Settings GUI [User Interface]

www.fastech-motions.com - 18
18. Setting Up Parameters
18.1 Setting Up Parameters
18.2 Resolution Selection
18.3 Stop Current Selection
18.4 Rotational Direction Selection
RS-232C serial communication port of a computer is used to set up various parameters of the motor drive. The
set-up program is supplied with the product on a companion CD. It is recommended to make a copy of the pro-
gram in any folder on your computer. Then please execute the program, named “Ezi-STEP BT Setting.exe”, from
the folder.
Resolution means the number of pulses per one rotation of a motor.
Select a desired resolution by pressing in button on Ezi-STEP BT Setting screen.
The possible resolution values are 500~50,000.
Stop Current means the motor current value automatically set in 0.1 sec after motor stops. This is to prevent
the overheat ot a motor when the motor is under long time idling. Select a desired Stop Current by pressing in
button on Ezi-STEP BT Setting screen. The range of this value is 10~100 and the unit
is a percentage.
The direction of the motor rotation can be selected either in CW(Clockwose) or in CCW(Counter Clockwise). Select
a desired rotation direction by pressing in button on Ezi-STEP BT Setting screen.
: Please select an appropriate Prot No. and press button. Then it will display the various
parameter values previously stored in the drive.
: Save the parameter values displayed on the screen into the drive.
Press button to save the value selected into the drive.
※ The default factory setting is 10,000[Pulses/Revolution].
Press button to save the value selected into the drive.
※ The default factory setting is 50%.
Press button to save the value selected into the drive.
※ The default factory setting is CW(Clockwise).
: Display the parameter values stored in the drive.
※ Error Message
There is no response. (You may select wrong baudrate of wrong port no.) :
① Select wrong Port No.
② Select already used Port No. in other program.
③ Communication cable is not connected.
④ Power is not supplied to drive.

www.fastech-motions.com - 19
18.5 Pulse Input Selection
18.6 Alarm Reset Input Selection
18.7 Alarm Output Selection
18.8 Run/Stop Output Selection
18.9 Motor Number, Motor Coils Current
As the Pulsed inputs, a user can choose One-pulse-mode(Pulse/Dir) or two-pulse-mode(CW/CCW).
Select a desired pulse mode by pressing in button on Ezi-STEP BT Setting screen.
Input method of Motor Free/Alarm Reset can be selected. Select a desired method by pressing in
button on Ezi-STEP BT Setting screen.
Alarm signal output method can be selected when error happens. Select a desired method by pressing in
button on Ezi-STEP BT Setting screen.
Run/Stop output method can be selected that indicate the motor running status. Select a desired method by
pressing in button on Ezi-STEP BT Setting screen.
This parameter can not be changeable. The information of Motor Number is needed for A/S of drive.
Press button to save the value selected into the drive.
※ The default factory setting is two pulse input mode(CW/CCW).
Press button to save the value selected into the drive.
※ The default factory setting is Nomal.
Press button to save the value selected into the drive.
※ The default factory setting is Nomal.
Press button to save the value selected into the drive.
※ The default factory setting is Nomal.
※ Caution : When you select ‘Inverse’ :
It can be ‘Motor Free’ status when power is applied to Ezi-STEP BT during Signal Connector(CN2)
is not connected. The power LED(green) is flash to show the status of ‘Motor Free’

www.fastech-motions.com - 20
Connector of Drive wiring Connector of Motor
Pin layout Pin number Pin number Pin layout
1
2
3
1
2
3
4
5
6
7
8
9
1 6
5 9
1
2
3
Appendix
■ Cable for RS-232C
For cable extension between PC and Ezi-STEP BT drive.
WIRING DIAGRAM
Table of contents
Other Fastech DC Drive manuals
Popular DC Drive manuals by other brands
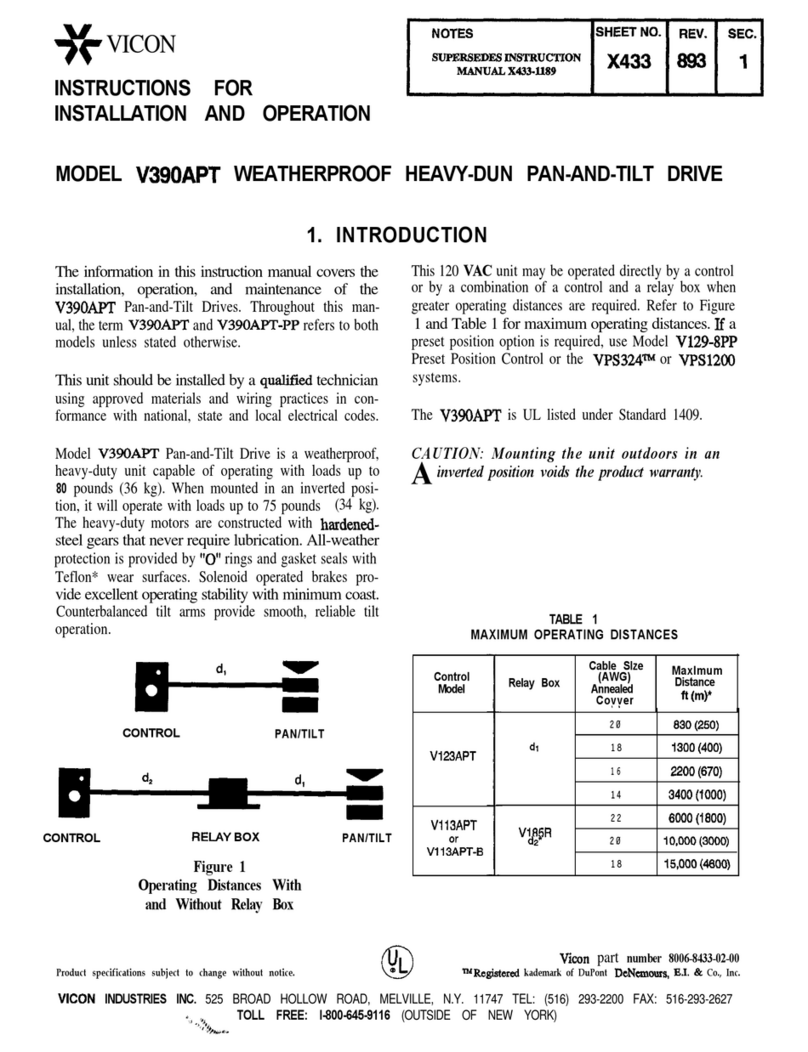
Vicon
Vicon V390APT Instructions for installation and operation
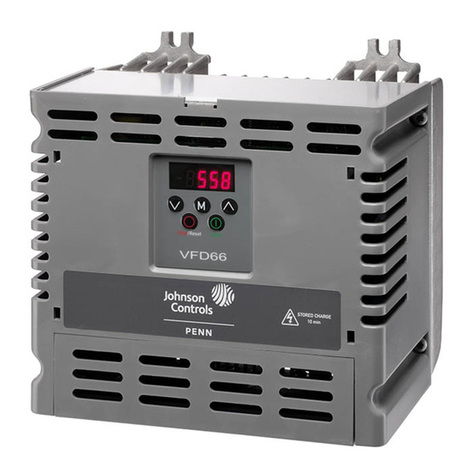
Johnson Controls
Johnson Controls VFD66 Series user guide

SEW-Eurodrive
SEW-Eurodrive ECDriveS Series operating instructions
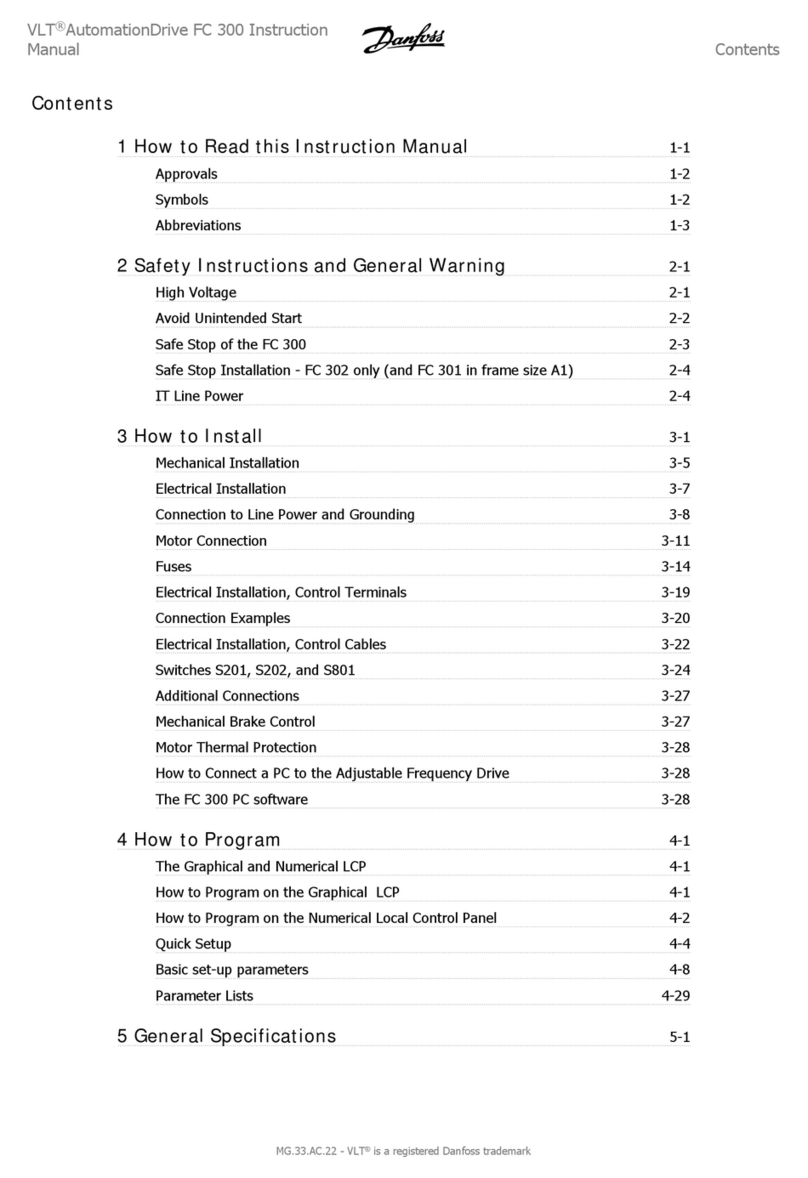
Danfoss
Danfoss VLT AutomationDrive FC 300 instruction manual
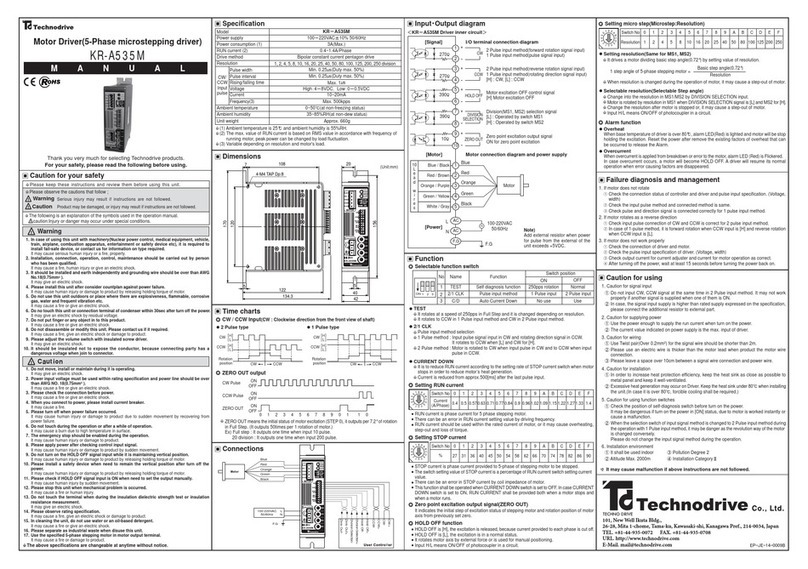
Technodrive
Technodrive KR-A535M manual
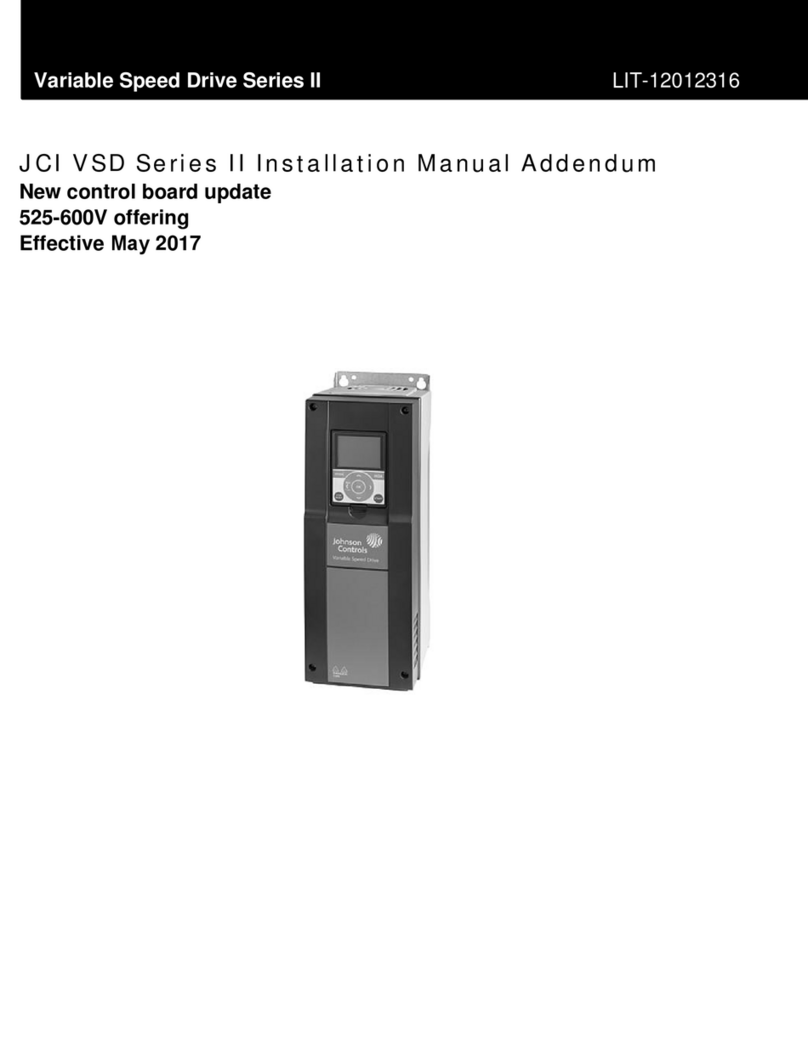
Johnson Controls
Johnson Controls VSD II Series Installation Manual Addendum