Fireye BurnerPRO User manual

1
®
DESCRIPTION
The Fireye BurnerPRO is a compact, microprocessor based, primary flame safeguard control system
designed to provide the proper burner sequencing, ignition and flame monitoring for on-off, multi-
stage, or modulating burners used in commercial heating and process equipment firing oil and gas
fuels. The BurnerPRO flame safeguard offers two built-in amplifiers, which allows for use in UV
only, FR only, and UV+FR applications. Flame monitoring for UV is accomplished by using avail-
able UV scanners: UV90L, UV1AL & UV5. Flame monitoring for FR version is accomplished by
using available ionization rod: 69ND1. The FR amplifier circuitry is subjected to permanent self-
checking, which allows it for use in applications that require burner cycle that runs for more than 24
hours. When operated as a UV control, the system is considered non-permanent, which requires a
burner recycle at least once every 24 hours.
The valve proving feature checks for leakage through the safety shutoff valves prior to burner start-
up or immediately after a burner shutdown. The Modbus interface provides the ability to write cus-
tom timing parameters, as well as reading status information during burner operation.
Through seven SMART LEDs, the control provides current operating status and lockout information
in the event of a safety shutdown. Refer to the BurnerPRO ordering information section in this docu-
ment for the various combinations of control functions and timings.
A complete BurnerPRO system includes the BP110/230, flame scanner and wiring base. The Burn-
erPRO performs a safe-start check on every burner cycle. If flame is detected prior to a start or
during the purge cycle, the fuel valves are not energized and the control locks out. The ‘POC’ input
is also monitored to verify that the main fuel valves are always in the proper state prior to the start of
a burner cycle. The LEDs & alarm terminal are used to annunciate the presence of a lockout condi-
tion.
Expanded functions of the BurnerPRO:
•Non-volatile lockout capability
•Air-flow proving, Gas valve proving, & Modbus access
•A run/check feature allows the operator to stop the program sequence in different
positions (Purge, Ignition, PTFI, MTFI, AUTO) for system troubleshooting
•Modbus, Remote and local Reset ability
•Two built-in amplifiers (UV, FR, UV+FR) for flexibility in applications
•Smart LEDs provide on board diagnostic lockout information
•Extended temperature operation (-40°C to 60°C)
•High capacity relay contacts
FIREYE®
BurnerPRO™
MICROPROCESSOR-BASED
INTEGRATED BURNER
MANAGEMENT CONTROL
with UV & FR Flame Amplifiers,
Valve Proving Feature and Modbus Interface
BP-1003
SEPTEMBER 21, 2018

2
TABLE OF CONTENTS
BURNERPRO SPECIFICATIONS. . . . . . . . . . . . . . . . . . . . . . . . . . . . . . . . . . . . . . . . . . . . . . . . . . . . . . . . . . . . . . . . . 3
PART NUMBERS AND APPROVALS . . . . . . . . . . . . . . . . . . . . . . . . . . . . . . . . . . . . . . . . . . . . . . . . . . . . . . . . . . . . . 5
ORDERING INFORMATION . . . . . . . . . . . . . . . . . . . . . . . . . . . . . . . . . . . . . . . . . . . . . . . . . . . . . . . . . . . . . . . . . . . . 6
INSTALLATION. . . . . . . . . . . . . . . . . . . . . . . . . . . . . . . . . . . . . . . . . . . . . . . . . . . . . . . . . . . . . . . . . . . . . . . . . . . . . . . 8
WIRING BASE . . . . . . . . . . . . . . . . . . . . . . . . . . . . . . . . . . . . . . . . . . . . . . . . . . . . . . . . . . . . . . . . . . . . . . . . . . . . . . . . . . . . . . . . . . . . . . . . 8
TERMINAL WIRING . . . . . . . . . . . . . . . . . . . . . . . . . . . . . . . . . . . . . . . . . . . . . . . . . . . . . . . . . . . . . . . . . . . . . . . . . . . . . . . . . . . . . . . . . . 10
PROCEDURE. . . . . . . . . . . . . . . . . . . . . . . . . . . . . . . . . . . . . . . . . . . . . . . . . . . . . . . . . . . . . . . . . . . . . . . . . . . . . . . . . . . . . . . . . . . . . . . . . 11
LED INDICATORS . . . . . . . . . . . . . . . . . . . . . . . . . . . . . . . . . . . . . . . . . . . . . . . . . . . . . . . . . . . . . . . . . . . . . . . . . . . . . . . . . . . . . . . . . . . . 12
LED RUN-TIME STATUS INDICATOR . . . . . . . . . . . . . . . . . . . . . . . . . . . . . . . . . . . . . . . . . . . . . . . . . . . . . . . . . . . . . . . . . . . . . . . . . . . . .13
FLAME SCANNERS . . . . . . . . . . . . . . . . . . . . . . . . . . . . . . . . . . . . . . . . . . . . . . . . . . . . . . . . . . . . . . . . . . . . . . . . . . 14
INSTALLATION - UV SCANNERS . . . . . . . . . . . . . . . . . . . . . . . . . . . . . . . . . . . . . . . . . . . . . . . . . . . . . . . . . . . . . . . . . . . . . . . . . . . . . . . 15
WIRING - UV SCANNERS. . . . . . . . . . . . . . . . . . . . . . . . . . . . . . . . . . . . . . . . . . . . . . . . . . . . . . . . . . . . . . . . . . . . . . . . . . . . . . . . . . . . . . 15
INSTALLATION - 69ND1 FLAME ROD . . . . . . . . . . . . . . . . . . . . . . . . . . . . . . . . . . . . . . . . . . . . . . . . . . . . . . . . . . . . . . . . . . . . . . . . . . . 16
WIRING - FLAME ROD . . . . . . . . . . . . . . . . . . . . . . . . . . . . . . . . . . . . . . . . . . . . . . . . . . . . . . . . . . . . . . . . . . . . . . . . . . . . . . . . . . . . . . . . 17
MAINTENANCE - FLAME ROD. . . . . . . . . . . . . . . . . . . . . . . . . . . . . . . . . . . . . . . . . . . . . . . . . . . . . . . . . . . . . . . . . . . . . . . . . . . . . . . . . 17
SYSTEM OPERATION . . . . . . . . . . . . . . . . . . . . . . . . . . . . . . . . . . . . . . . . . . . . . . . . . . . . . . . . . . . . . . . . . . . . . . . . 18
OPERATIONAL SEQUENCE DIAGRAM . . . . . . . . . . . . . . . . . . . . . . . . . . . . . . . . . . . . . . . . . . . . . . . . . . . . . . . . . . . . . . . . . . . . . . . . . . . .19
EXPLANATION OF SEQUENCE STATES . . . . . . . . . . . . . . . . . . . . . . . . . . . . . . . . . . . . . . . . . . . . . . . . . . . . . . . . . . . . . . . . . . . . . . . . . . .20
SEQUENCE TIMING . . . . . . . . . . . . . . . . . . . . . . . . . . . . . . . . . . . . . . . . . . . . . . . . . . . . . . . . . . . . . . . . . . . . . . . . . . . . . . . . . . . . . . . . . . 22
DESCRIPTION OF FUNCTIONS OF OPERATING CONTROLS . . . . . . . . . . . . . . . . . . . . . . . . . . . . . . . . . . . . . . 24
CONNECTION TO AN EXTERNAL ACTUATOR . . . . . . . . . . . . . . . . . . . . . . . . . . . . . . . . . . . . . . . . . . . . . . . . . . 25
EXAMPLE WIRING 1 . . . . . . . . . . . . . . . . . . . . . . . . . . . . . . . . . . . . . . . . . . . . . . . . . . . . . . . . . . . . . . . . . . . . . . . . . 26
EXAMPLE WIRING 2 . . . . . . . . . . . . . . . . . . . . . . . . . . . . . . . . . . . . . . . . . . . . . . . . . . . . . . . . . . . . . . . . . . . . . . . . . 27
EXAMPLE WIRING 3 . . . . . . . . . . . . . . . . . . . . . . . . . . . . . . . . . . . . . . . . . . . . . . . . . . . . . . . . . . . . . . . . . . . . . . . . . 28
COMMUNICATIONS . . . . . . . . . . . . . . . . . . . . . . . . . . . . . . . . . . . . . . . . . . . . . . . . . . . . . . . . . . . . . . . . . . . . . . . . . 29
MODBUS CONNECTION DIAGRAM . . . . . . . . . . . . . . . . . . . . . . . . . . . . . . . . . . . . . . . . . . . . . . . . . . . . . . . . . . . . . . . . . . . . . . . . . . . . . .30
MODBUS MESSAGE TABLE / MAP. . . . . . . . . . . . . . . . . . . . . . . . . . . . . . . . . . . . . . . . . . . . . . . . . . . . . . . . . . . . . . . . . . . . . . . . . . . . . . . .32
VALVE PROVING . . . . . . . . . . . . . . . . . . . . . . . . . . . . . . . . . . . . . . . . . . . . . . . . . . . . . . . . . . . . . . . . . . . . . . . . . . . . 35
PRESSURE SWITCH SELECTION . . . . . . . . . . . . . . . . . . . . . . . . . . . . . . . . . . . . . . . . . . . . . . . . . . . . . . . . . . . . . . . . . . . . . . . . . . . . . . . . .36
PROVING STEPS . . . . . . . . . . . . . . . . . . . . . . . . . . . . . . . . . . . . . . . . . . . . . . . . . . . . . . . . . . . . . . . . . . . . . . . . . . . . . . . . . . . . . . . . . . . . . . .37
CALCULATING VALVE PROVING TEST TIMES . . . . . . . . . . . . . . . . . . . . . . . . . . . . . . . . . . . . . . . . . . . . . . . . . . 38
LOCKOUTS . . . . . . . . . . . . . . . . . . . . . . . . . . . . . . . . . . . . . . . . . . . . . . . . . . . . . . . . . . . . . . . . . . . . . . . . . . . . . . . . . 40
LOCKOUT LED ERROR / LOCKOUT CODES . . . . . . . . . . . . . . . . . . . . . . . . . . . . . . . . . . . . . . . . . . . . . . . . . . . . . . . . . . . . . . . . . . . . . 41
LOCKOUT CODE EXPLANATION. . . . . . . . . . . . . . . . . . . . . . . . . . . . . . . . . . . . . . . . . . . . . . . . . . . . . . . . . . . . . . . . . . . . . . . . . . . . . . . . .43
Boiler operation, maintenance, and troubleshooting shall only be conducted by trained personnel. Persons trouble-
shooting lockouts or resetting the control must respond properly to troubleshooting error codes as described in this
product bulletin.
Jumpers being used to perform static test on the system must only be used in a controlled manner and must be
removed prior to the operation of the control. Such tests may verify the external controllers, limits, interlocks, actua-
tors, valves, transformers, motors and other devices are operating properly. Such tests must be conducted with man-
ual fuel valves in the closed position only. Replace all limits and interlocks not operating properly, and do not bypass
limits in interlocks. Failure to follow these guidelines may result in an unsafe condition hazardous to life and prop-
erty.
WARNING!!!
WARNING: The equipment described in this manual is capable of causing property damage, severe
injury, or death. It is the responsibility of the owner or user to ensure that the equipment described is
installed, operated and commissioned in compliance with the requirements of all national and local codes.

3
®
BURNERPRO SYSTEM SPECIFICATION
Supply Voltage:
BP110 110 VAC (+20%, -15%) 50/60 Hz, single phase
BP230 230 VAC (+10%, -15%) 50/60 Hz, single phase
Power Consumption:
7 VA
Temperature Rating:
Operating: -40°C to +60°C (-40°F to 140°F)
Storage: -50°C to +85°C (-58°F to 185°F)
Flame Amplifier Rating:
UV: Terminals 22 & 23, 300VDC 3mA(max)
FR: Terminals 24 & Earth, 330VAC (max), 3uA min/10uA max flame current
Protection Category:
IP40 standard version
Control Dimensions:
With wiring base (60-2944-1); 4.15” L x 4.15" W x 5.0" H (105mm x 105mm x 127mm)
Shipping Weight:
Approx. 2.5 lbs. (1.13kg)
OPERATING TEMPERATURE LIMITS
Relative Humidity:
90% R.H. (Non-Condensing)
LOAD RATINGS:
Maximum connected load must not exceed 2000VA.
ELECTRICAL RATINGS
VA ratings (not specified as pilot duty) permit the connection of transformers and similar devices
whose inrush current is approximately the same as their running current.
CONTROL MAXIMUM MINIMUM
BP110, BP230 140°F 60°C -40°F -40°C
UV90L-1 194°F 90°C -40°F -40°C
UV1AL-3, -6 200°F 94°C -40°F -40°C
UV5-1 140°F 60°C -4°F -20°C
Terminal Typical Load Maximum Rating
@120V-50/60 Hz
Maximum Rating
@230V-50/60 Hz
Alternate Rating
6-7 Burner/Blower
Motor
2 F.L.A. *
8 L.R.A.
2 F.L.A. *
8 L.R.A.
240 VA Pilot Duty
(Motor Starter Coil)
9-10-11-20 Modulator 240 VA Pilot Duty
16-17-18-19 Fuel/Igniton 240 VA Pilot Duty
3 Alarm 125 VA Pilot Duty
* F.L.A. = full load amps; L.R.A = locked rotor amps

4
VA Pilot Duty ratings permit the connection of relays, solenoid valves, lamps, etc. whose total oper-
ating load does not exceed the published rating and whose total inrush does not exceed 10 times the
rating.
Running and locked rotor ratings are intended for motors. VA and VA Pilot Duty loads may be added
to a motor load provided the total load does not exceed the published rating.
OPERATIONALTIMINGS
The BurnerPRO is pre-programmed from the factory with a set of operational timings necessary for
the safe operation of the burner system. However, operational timings can be modified via the mod-
bus port. The operational timings are governed by regional and local codes. It is important that the
appropriate operational timing is selected for the burner application.
Table 1: Timing Information
See Table 7 on page 23 for expanded timing information.
Times are in seconds BURNERPRO SERIES TIMINGS
TIMING DESCRIPTION S1 S2 S3 S4 S5 S6
t1Purgetime 35.53137603730
t3' Pre-ignition time (piloted) 4 6 2.5 2.5 2.5 1
TSA’ Ignition safety time (PTFI) 2 3 5 5 5 10
t6 Post-purge time 12 18 15 15 15 15
t9 Interval between Main Fuel Piloted and removal of Pilot (MTFI) 2 3 5 5 5 10
FFRT Flame Failure Response Time (FFRT) 1.0 4 4
NOTICE: This equipment generates and can radiate radio frequency energy, and if not
installed and used in accordance with the instruction manual may cause interference to
radio communications. It has been tested and found to comply with the limits for a Class B
computing device pursuant to Subpart J of part 15 of FCC Rules, which are designed to
provide reasonable protection against such interference when operated in a commercial/
industrial environment.

5
®
PART NUMBERS AND APPROVALS
Table 2: Agency Approvals
Fireye Part Number
Control
BP110UVFR-SxM
BP110UVFR-SxMP
BP110UVFR-S1M
BP110UVFR-S1MP
BP110UVFR-S2M
BP110UVFR-S2MP
BP110UVFR-S3M
BP110UVFR-S3MP
BP110UVFR-S4M
BP110UVFR-S4MP
BP110UVFR-S5M
BP110UVFR-S5MP
BP110UVFR-S6M
BP110UVFR-S6MP
BP230UVFR-SxM
BP230UVFR-SxMP
BP230UVFR-S1M
BP230UVFR-S1MP
BP230UVFR-S2M
BP230UVFR-S2MP
BP230UVFR-S3M
BP230UVFR-S3MP
Wiring Base
60-2981-1 XX
Scanners
UV90L-1 XX
UV1AL-3 XX
UV1AL-6 XX
UV5-1 XX

6
X = CERTIFICATION IN HAND
APPROVAL/CERTIFICATION
UL: MCCZ File MP1537 Controls, Primary Safety - Listed
MCCZ7 File MP1537 Controls, Primary Safety Certified for Canada
CE: CE-0063CS1687
DVGW:
DIN-CERTCO:
Table 3 : Ordering Information
Item Part Number Description
1 BP230UVFR-SxM BurnerPRO Single Burner Control, 230VAC 50/60Hz, User defined timings, with UV & FR amplifiers, Modbus
2 BP230UVFR-SxMP BurnerPRO Single Burner Control, 230VAC 50/60Hz, User defined timings, with UV & FR amplifiers, Modbus & VP
3 BP230UVFR-S1M BurnerPRO Single Burner Control, 230VAC 50/60Hz, Series 1 timings, with UV & FR amplifiers, Modbus
4 BP230UVFR-S1MP BurnerPRO Single Burner Control, 230VAC 50/60Hz, Series 1 timings, with UV & FR amplifiers, Modbus & VP
5 BP230UVFR-S2M BurnerPRO Single Burner Control, 230VAC 50/60Hz, Series 2 timings, with UV & FR amplifiers, Modbus
6 BP230UVFR-S2MP BurnerPRO Single Burner Control, 230VAC 50/60Hz, Series 2 timings, with UV & FR amplifiers, Modbus & VP
7 BP230UVFR-S3M BurnerPRO Single Burner Control, 230VAC 50/60Hz, Series 3 timings, with UV & FR amplifiers, Modbus
8 BP230UVFR-S3MP BurnerPRO Single Burner Control, 230VAC 50/60Hz, Series 3 timings, with UV & FR amplifiers, Modbus & VP
9 BP230UVFR-S4M BurnerPRO Single Burner Control, 230VAC 50/60Hz, Series 4 timings, with UV & FR amplifiers, Modbus
10 BP230UVFR-S4MP BurnerPRO Single Burner Control, 230VAC 50/60Hz, Series 4 timings, with UV & FR amplifiers, Modbus & VP
11 BP110UVFR-SxM BurnerPRO Single Burner Control, 230VAC 50/60Hz, User defined timings, with UV & FR amplifiers, Modbus
12 BP110UVFR-SxMP BurnerPRO Single Burner Control, 230VAC 50/60Hz, User defined timings, with UV & FR amplifiers, Modbus & VP
13 BP110UVFR-S1M BurnerPRO Single Burner Control, 110VAC 50/60Hz, Series 1 timings, with UV & FR amplifiers, Modbus
14 BP110UVFR-S1MP BurnerPRO Single Burner Control, 110VAC 50/60Hz, Series 1 timings, with UV & FR amplifiers, Modbus & VP
15 BP110UVFR-S2M BurnerPRO Single Burner Control, 110VAC 50/60Hz, Series 2 timings, with UV & FR amplifiers, Modbus
16 BP110UVFR-S2MP BurnerPRO Single Burner Control, 110VAC 50/60Hz, Series 2 timings, with UV & FR amplifiers, Modbus & VP
17 BP110UVFR-S3M BurnerPRO Single Burner Control, 110VAC 50/60Hz, Series 3 timings, with UV & FR amplifiers, Modbus
18 BP110UVFR-S3MP BurnerPRO Single Burner Control, 110VAC 50/60Hz, Series 3 timings, with UV & FR amplifiers, Modbus & VP
19 BP110UVFR-S4M BurnerPRO Single Burner Control, 110VAC 50/60Hz, Series 4 timings, with UV & FR amplifiers, Modbus
20 BP110UVFR-S4MP BurnerPRO Single Burner Control, 110VAC 50/60Hz, Series 4 timings, with UV & FR amplifiers, Modbus & VP
21 BP110UVFR-S5M BurnerPRO Single Burner Control, 110VAC 50/60Hz, Series 5 timings, with UV & FR amplifiers, Modbus
22 BP110UVFR-S5MP BurnerPRO Single Burner Control, 110VAC 50/60Hz, Series 5 timings, with UV & FR amplifiers, Modbus & VP
23 BP110UVFR-S6M BurnerPRO Single Burner Control, 110VAC 50/60Hz, Series 6 timings, with UV & FR amplifiers, Modbus
24 BP110UVFR-S6MP BurnerPRO Single Burner Control, 110VAC 50/60Hz, Series 6 timings, with UV & FR amplifiers, Modbus & VP

7
®
SCANNER SELECTION
BurnerPRO Wiring Base
60-2981-1 Standard base with terminal block and knockouts, 4.2”L x 4.2”W x 1.22”H
61-7429-1 Grounding wire/leash, 10” length
FIREYE P/N DESCRIPTION BULLETIN
UV SCANNER
UV90L-1 UV scanner, Front and side (90o) lateral view, terminal block hook-up SC-108
UV1AL-3, -6 UV scanner, 1/2” NPT connector, front view, 3ft/6ft cable, shielded leads SC-108
4-742-1 Replacement UV tube for UV90L-1
UV5-1 UV Scanner, front and side viewing, 6.5ft leads SC-108
FLAME ROD
69ND1-1000K4 Flame rod 1/2” NPT mount, 12” length SC-103
69ND1-1000K6 Flame rod 1/2” NPT mount, 18” length SC-103
69ND1-1000K8 Flame rod 1/2” NPT mount, 21” length SC-103

8
FIGURE 1.
MOUNTING RECOMMENDATIONS
Wiring Base
Mounting of the base can be accomplished with 2 screws. The recommended screw sizes are #10
PAN HD x 5/8inch (5mm PAN HD x 16mm) and #10 PAN HD x 3/8 inch (5mm PAN HD x 10mm).
Refer to Figure 2 for mounting dimensions.
Grounding Wire
Each BurnerPRO control is fitted with a grounding wire. Attach the open end of the grounding wire
to a ground terminal on the wiring base (see figure 2 below). Undo the screw terminal with a screw-
driver and place the ground lug over the terminal. Re-install the screw over the ground lug. Do not
attach the grounding wire to a Neutral (N) terminal.
FRONT VIEW
BOTTOM VIEW
CHASSIS/AMPLIFIER
110 VAC, 50/60 Hz
BP110UVFR-Sxxx
230 VAC, 50/60 Hz
BP230UVFR-Sxxx
WIRING BASE
60-2981-1
UV1AL
UV90L

9
®
FIGURE 2.
Note: The location should be free from excessive vibration and within the ambient temperature rating.
NOTICE: Installation, setup, and commissioning of the BurnerPRO control must be done by
's and don’ts of the
trained personnel. The personnel must know the do
authorized and
particular burner and must have relevant experience in the theories and practices of combustion
control. Fireye cannot accept any liability for any consequences resulting from inappropriate,
negligent or incorrect installation, commissioning or adjustment of operating parameters of the
equipment. BurnerPRO does not have any user serviceable parts. If the unit has a problem,
return the unit to your local distributor, or contact Fireye directly.

10
TABLE 4: TERMINAL WIRING
Terminal No. Type Description Rating
1 Power Line voltage supply 110VAC (+20%, -15%), 50/60Hz
230VAC (+10%, -15%), 50/60Hz
single phase
2 Power Line voltage common
3 Output Alarm See Load Ratings
4 Output Lockout Limits 110/230 VAC, 1mA
5 Input Recycle Limits 110/230 VAC, 1mA
6 Output Combustion Air Blower
See Load Ratings
7 Output Combustion Air Blower
8 Input Actuator Feedback 110/230 VAC, 1mA
9 Output High Fire Purge (Open) See Load Ratings
10 Output Low Fire Purge (Minimum) See Load Ratings
11 Output Closed (Economy) See Load Ratings
12 Input Valve Proving / Proof of Closure 110/230 VAC, 1mA
13 Input Combustion Air Switch Test 110/230 VAC, 1mA
14 Input Combustion Air Prove 110/230 VAC, 1mA
15 Input Valve Proving / Special function 110/230 VAC, 1mA
16 Output Ignition See Load Ratings
17 Output Pilot See Load Ratings
18 Output Main Fuel Valve 1 (MV1) See Load Ratings
19 Output Main Fuel Valve 2 (MV2) See Load Ratings
20 Output Release to Modulate (AUTO) See Load Ratings
21 Input Remote Reset 110/230 VAC, 1mA
22 Output UV Sensor (S1) 300 VDC, 3mA
23 Input UV Sensor (S2) Sensor Common/return
24 Output FR Sensor (S3) 300 VAC, 1mA
N Power Line Voltage Common
Earth Ground
CAUTION: Published load ratings assume that no contact be required to handle inrush cur-
rent more often than once in 15 seconds. The use of control switches, solenoid, relays, etc.
which chatter can lead to premature failure. It is important to run through a test operation
(with fuel shut off) following the tripping of a circuit breaker, a blown fuse, or any known
instance of chattering of any external current consuming devices.

11
®
INSTALLATION PROCEDURE
Install the wiring base where the relative humidity never reaches the saturation point. The Burner-
PRO is designed to operate in a maximum 90% relative humidity environment. Do not install the
BurnerPRO where it can be subjected to vibration in excess of 0.5G continuous maximum vibration.
Allow at least one inch clearance (2.5 cm) around control for service and installation.
1. Wiring must comply with all applicable codes, ordinances and regulations.
2. Wiring must comply with NEC Class 1 (Line Voltage) wiring or equivalent regional code.
3. Torque rating on terminal block screws is 4.4 in/lbs to 5.3 in/lbs.
4. Limits and interlocks must be rated to simultaneously carry and break current to the ignition
transformer, pilot valve and main fuel valve(s).
5. Recommended wire routing of lead wires:
a. Do not run high voltage ignition transformer wires in the same conduit with any other
wires.
b. Do not route flame detector lead wires in conduit with line voltage circuits. Use separate
conduit where necessary.
6. Maximum wire lengths:
a.The maximum lead wire length is 200ft. (61 meters) to terminal inputs (Operating limits,
interlocks, valves, etc.).
b. Flame Detector lead wires: see section on flame scanners
c. Remote reset: The maximum length of wire is 500 feet (152 meters) to a normally open
remote reset push-button, but should remain within sight and sound of the burner.
A good grounding system should be provided to minimize the effects of AC quality problems. A
properly designed ground system meeting all the safety requirements will ensure that any AC voltage
quality problems, such as spikes, surges and impulses have a low impedance path to ground. A low
impedance path to ground is required to ensure that large currents involved with any surge voltages
will follow the desired path in preferences to alternative paths, where extensive damage may occur to
equipment.
BEFORE INSTALLING THE BURNERPRO CONTROL
WARNING: Controls require safety limits utilizing isolated mechanical contacts. Electronic
limit switches may cause erratic operation and should be avoided.
CAUTION: Ensure that electric power is turned off. Refer to SN-100 for recommended
grounding techniques. Ensure that wiring base terminal is connected to protective earth.
Be aware that power to some interlocks (operating controls, air flow switches, modulating
circuits, etc.) may be derived from sources other than what is controlling the BurnerPRO.

12
LED INDICATORS
The BurnerPRO control module has seven (7) LED indicator lights to annunciate the operating status of the
control, as well as provide the reason for the last lockout condition. The "Open Damper" and "Close
Damper" LEDs provide easy set-up of the modulating motor end switches. Each LED has a graphic symbol
to describe its function (see Table below).
Table 5:Status LEDs
The “SMART” LEDs provide a flame strength display during check mode. In check mode, the status LED is yellow,
the fan LED is blinking and LEDs 2-6 grow up from status forming a bar graph. Each LED lit represents 20% of the
total flame signal. See Table 6, Note 1. (5 LEDs lit is 100%, 2 LEDs is 40%)
FAN Lights when the blower motor is energized (terminal 6) and flashes when the RUN/CHECK switch is in the
“CHECK” position during Minimum, Open, PTFI, and MTFI.
OPEN
DAMPER
Will blink when the modulator motor is being driven to the high fire position. Once the high purge switch
closes, this LED will light constant. The LED provides the status of the purge sequence.
CLOSE
DAMPER
Will blink when the modulator motor is being driven to the low fire position. Once the low fire switch closes,
this LED will light constant. This LED provides the status of the low fire start interlock circuit.
AUTO Will light when the control releases to automatic modulating control.
IGNITION Will blink during Pilot Trial For Ignition (PTFI). Will light constant during Main Trial For Ignition (MTFI).
FLAME Will light whenever flame is detected by the flame scanner.
ALARM In the event of a lockout condition, the Alarm LED is illuminated and the remaining LEDs will light up to indicate
the lockout condition. See “Safety Lockout Codes.”
RESET During normal operation, the Reset LED is GREEN. In the event of a lockout condition, the Reset LED is illumi-
nated RED. When Modbus is made, the Reset LED is illuminated YELLOW.

13
®
Table 6: LED Run-time Status Indicator
NOTES:
1.The LEDs form a progress bar indicating Flame Signal Strength for aiming sensors during commissioning (The LEDs “Grow”
upwards away from Status at 20% intervals of flame strength.)
2.The LEDs indicate the error or lockout code for troubleshooting
3.The LEDs change from ON to BLINKING to OFF showing the modulator operation
OPERATION
LED ●= ON FAN OPEN
DAMPER
CLOSED
DAMPER AUTO IGNITION FLAME STATUS
ICON
OFF / NO
POWER OFF
NOT READY /
DIAGNOSTICS Green
READY /
STANDBY ●Green
CHANGING
(note 3) ●
OFF
Blinking
●
●
Blinking
OFF
Green
WAITING TO
CLOSE
Blinking
Green Green
OPEN
(before ignition) ●● Green
MINIMUM
(before ignition) ●● Green
IGNITION ●●●Green
PTFI ●●●
Blinking
Green Green
MTFI ●● ●Green
AUTO ●●●Green
MINIMUM
(During Flame) ●● ●Green
OPEN
(During Flame) ●● ●Green
ECONOMY ●● Green
CHECK
OPEN Blinking ●Yellow
CHECK
MINIMUM Blinking ●Yellow
CHECK
PTFI/MTFI/AUTO Blinking ●Note 1 ●Note 1 ●Note 1 ●Note 1 ●Note 1 Yellow
FAULT /
LOCKOUT ●Note 2 ●Note 2 ●Note 2 ●Note 2 ●Note 2 ●Note 2 Red
END OF CYCLE ●●●●Green

14
FLAME SCANNERS
INSTALLATION - UV SCANNERS
Where possible, obtain the burner manufacturer’s instructions for mounting the scanner. This infor-
mation is available for most standard burners. The scanner mounting should comply with the follow-
ing general instructions:
1. Position the UV1AL, UV90L or UV5 scanner within 39 inches (1 meter) of the flame to be
monitored.
2. Select a scanner location that remains within the ambient temperature limits of the UV scanner.
3. The UVlAL scanner is designed to seal off the sight pipe up to 1 PSI pressure. Higher furnace
pressures must be sealed off. To seal off positive furnace pressure up to 50 PSI for the UV1AL
scanner, install a quartz window coupling (P/N: 60-1257). Add cooling air to reduce the scanner
sight pipe temperature.
4. Install the scanner on a standard NPT pipe (UV1AL: 1/2”) whose position is rigidly fixed. If the
scanner mounting pipe sights through the refractory, do not extend it more than halfway
through. Swivel flanges are available if desired (P/N: 60-302). The sight pipe must permit an
unobstructed view of the pilot and/or main flame, and both pilot and main flames must com-
pletely cover the scanner field of view.
5. Smoke or unburned combustion gases absorb ultra-violet energy. On installations with negative
pressure combustion chambers, a small hole drilled in the UV1AL sight pipe assists in keeping
the pipe clean and free from smoke. For positive pressure furnaces, provide clean air to pressur-
ize the sight pipe, if necessary.
6. Two UV1AL scanners may be installed on the burner if it is necessary to view two areas to
obtain reliable detection of the flame. They must be wired in parallel.
7. To increase scanner sensitivity with UV1AL scanner, a quartz lens permits location of the scan-
ner at twice the normal distance. Use 1/2” x 1 1/2” pipe nipple between UV1AL scanner and the
coupling.
8. Request the assistance of any Fireye field office for recommendations of a proper scanner instal-
lation on a non-standard application.
UV90L
UV1AL
SCANNER MUST HAVE UNOBSTRUCTED
VIEW OF FLAME
NOT THIS NOT THIS BUT THIS
FLAME MUST COMPLETELY COVER
SIGHT OPENING
NOT THIS NOT THIS BUT THIS

15
®
TYPICAL SCANNER INSTALLATIONS
WIRING - UV SCANNERS
To connect the scanner to the control, the UV1AL scanner is supplied with 36" or 72"
(0.9 m or 1.8 m) of flexible cable. The UV90L is supplied with a terminal board. Use two #18 AWG
conductors to connect the UV90L to the control. The UV5 is supplied with 80” (2m) of flexible cable
(detachable).
If it is necessary to extend the scanner wiring, the following instructions apply:
There is no polarity associated with the scanner wiring. Scanner wires must be installed in a separate
conduit. The wires from several scanners may be installed in a common conduit.
1. Selection of Wire
a. Wiring: For extended scanner wiring up to 500 feet (152 M), and for shorter lengths to reduce
signal loss, use a shielded wire (Belden 8254-RG62 coaxial cable, or equal) for each scanner
wire. The ends of the shielding must be taped and not grounded.
b. Avoid asbestos insulated wire.
c. Multi-conductor cable is not recommended without prior factory approval.
2. High voltage ignition wiring must not be installed in the same conduit with flame detector wires.
The maximum UV signal
from a flame is found in the
first one-third of the visible
flame taken from the point
where the flame begins. The
scanner sight pipe is aimed
at this area.
DO NOT EXTEND
MORE THAN
HALF-WAY INTO
REFRACTORY
SCANNER
FORCED
CLEAN AIR
(FROM DISCHARGE
OF FAN)
METHODS OF COOLING SCANNER
INSULATING
TUBING
SEALING UNION FORCED
AIR
EXTEND SIGHTING TUBE
6”(152.4) OR 8”(203.2)
DO NOT EXTEND MORE THAN
HALF-WAY INTO REFRACTORY

16
INSTALLATION - 69ND1 FLAME ROD
The 69NDl flame rod proves a gas pilot flame and/or main gas flame. It is a spark plug type unit. It
consists of 1/2' “NPT” mount, a KANTHAL flame rod, a glazed porcelain insulating rod holder and
a spark plug connector for making electrical connections. The 69ND1 is available in 12", 18" or 24"
(0.3m, 0.46m, 0.6m) lengths.
The flame rod may be located to monitor only the gas pilot flame or both the gas pilot and main gas
flames. Mount it with a l/2" “NPT” coupling.
The following instructions should be observed:
1. Keep your flame rod as short as possible.
2. Keep your flame rod at least 1/2" from any refractory.
3. Your flame rod must enter the pilot flame from the side so as to safely prove an adequate pilot
flame under all draft conditions.
4. If the flame is nonluminous (air and gas mixed before burning), extend the electrode tip at least
1/2" into the flame, but not more than halfway through.
5. If the flame is partly luminous, the electrode tip must extend only to the edge of the flame. It is
not necessary to maintain uninterrupted contact with the flame.
6. It is preferable to angle the rod downward to minimize the effect of sagging and to prevent it
from coming in contact with any object.
7. An adequate grounding surface for the flame must be provided. The grounding surface in actual
contact with the flame must be at least 4 times greater that the area of the portion of the flame
rod in contact with the flame. It is essential to adjust the flame rod and ground area ratio to pro-
vide a maximum, signal reading.
Note: Interference from the ignition spark can alter the true signal reading by adding to, or subtract-
ing from it. This trend sometimes may be reversed by interchanging the primary wires (line voltage)
to the ignition transformer. This interference can also be reduced by the addition of grounded shield-
ing between the flame rod and ignition spark.
8. Proven types of flame grounding adapters, as shown below, may be used to provide adequate
grounding surface. High temperature stainless steel should be used to minimized the effect of
metal oxidation. This assembly may be welded directly over the pilot or main burner nozzle.
WRONG POSITION
OF ROD
INADEQUATE FLAME
PILOT BURNER
CORRECT POSITION
OF PILOT FLAME
CORRECT
POSITION
OF ROD
BOMB FIN GROUNDING ASSEMBLY THREADED ROD ASSEMBLY

17
®
WIRING - FLAME ROD
For proper operation of flame rectification systems, it is necessary to maintain at least 20 megohms insulat-
ing resistance in the flame rectification circuit.
1. The scanner should be wired using metal cable or rigid conduit.
2. High voltage wiring must not be installed in the same conduit with scanner wiring.
Selection of Scanner Wire
1. Use #14, 16, or 18 gauge wire with 90 C, 600 volt insulation for up to 20 feet distance.
2. The type of insulation used with flame rectification is important, since it must protect against current
leakage resistance to ground. Use Belden 8254-RG62 Coaxial Cable (or equal) for runs greater than 20
feet. Maximum wiring run not to exceed 100 feet.
MAINTENANCE - FLAME ROD
Type 69ND1 Flame Rod
The flame rod and its insulator should be kept clean by washing routinely with soap and water. Rods should
be routinely replaced as they oxidize.
Flame Signal Strength
Routine observation of the flame signal strength will forewarn any deterioration in the capability of the
flame detector or its application.

18
SYSTEM OPERATION
The fixed series timings determine the functional operation of the BurnerPRO control (e.g. purge tim-
ing, trial for ignition timings, etc.) The BurnerPRO offers a single multi-functional button and its func-
tions are as follows:
RESET
The BurnerPRO control provides two methods of resetting the control in the event of a safety lockout:
The push button reset and terminal 21 remote reset. Both reset methods can be used to stop the control
in its firing sequence at anytime to force a user/emergency lockout. A reset of the control can be
accomplished by momentarily pressing the reset button or engaging the remote reset terminal.
CHECK MODE
The push button reset switch has an added feature that allows the user to freeze the operational
sequence at certain times (Purge, Ignition, PTFI, MTFI, and AUTO). This is known as CHECK
MODE and it is designed to aid in set-up, start-up and check-out of the burner and its associated inter-
locks. This feature is very useful in pilot aiming and adjustment during commissioning or mainte-
nance.
The check mode rules are:
•If the push button reset is held for at least 3 seconds, the status LED changes from green to yellow
to signal that the control is in check mode.
•Momentarily pressing the push button reset while in check mode transitions the control into nor-
mal operating sequence, thus disabling check mode.
•The control locks out during Purge, Ignition, or PTFI states if check mode is active longer than 30
minutes
•The control allows check mode in MTFI for 2 minutes. The control automatically cancels check
mode after 2 minutes in MTFI state and resumes normal operation.
•When in check mode during PTFI, MTFI and AUTO states, the control uses the open, close, auto,
ignition, and flame LEDs to annunciate the flame signal strength. Every illuminated LED (starting
with the flame LED) represents a 20% signal strength.
•It should be noted that the control will still perform safety checks in the background while in
CHECK mode to ensure the safe operation of the burner. The control will proceed to lockout if it
detects an unsafe condition.

19
®
FIGURE 3. OPERATIONAL SEQUENCE
,1,7,$/6<67(0&+(&.
2873876$5(2))
2873876$5(2))
287387,621
,13876&+(&.('
)25)$/6()/$0(
35(&21',7,216)25
%851(567$5783
,1387,621
,1387,621
,1387,621
(&2120<
32&
&$67
)(('%$&.
/2&.287
8VHUHVHWWRH[LW
ORF RXWVWDWH
&$//)25+($7
5(&<&/( ,138721
35(3$5()25385*(&<&/(
287387,621
,1387,621
287387,621
&$%
/,0,76
32&
029(72385*(
287387,621
,1387,621
23(1
&$3
,1387021,725(')(('%$&.
385*(
3XUJH7LPHU&RXQWGRZQ
,1387,621
&$3
,138721)520
02'02725
)(('%$&.
,13876&+(&.('
)25)$/6()/$0(
029(72,*1,7,21
,*1,7,21
287387,621
,*1,7,21
,1387021,725('
)(('%$&.
287387,621
0,1,080
,138721)520
02'02725
)(('%$&.
3,/2775,$/
287387,621
3,/27
0$,1GLUHFW 287387,621
3,/2775,$/FRQW«
,*1,7,21 287387,62))
0$,175,$/
287387,621
0$,1
5(/($6(7202'8/$7,21
5(/($6( 287387,621
029(726+87'2:1
5(&<&/( ,1387,62))
0$,1GLUHFW 287387,62))
0$,1SLO WHG 287387,62))
6+87'2:1
(&2120< 287387,621
5(/($6( 287387,62))
0,1,080 287387,6212))
&$% 287387,62))
3RVW3XUJH7LPHU&RXQWGRZQ
32:(521
32:(5('
+27
32:(5('
1(875$/
)$,/
3$66
3$66
3$66
)/$0(
)/$0(
3$66
,13876&+(&.('
)25)$/6()/$0(
)/$0(
3$66
,13876&+(&.('
)25)$/6()/$0(
)/$0(
3$66
,13876&+(&.('
)25)$/6()/$0(
)/$0(
3$66
)/$0(6,*1$/
35(6(17
)/$0(
)/$0(6,*1$/
35(6(17
)/$0(
)/$0(6,*1$/
35(6(17
)/$0(
3$66
3$66
)/$0(6,*1$/
$)7(5%851
35(6(1725)/$0(
/266$//2:('
)/$0(
&$//)25+($7
6$7,6),('
3$66
,13876&+(&.('
)25)$/6()/$0(
)/$0(
)$,/
)$,/
)$,/
)$,/
)$,/
0$,175,$/FRQW«
3,/27 287387,62))
)/$0(6,*1$/
35(6(17
)/$0(
3$66
3$66
)$,/
)$,/
)$,/
)$,/
)$,/
21
$/$50
2))
/,0,76
2))
&$%
2))
23(1
2))
0,1,080
21(&2120<
2))
,*1,7,21
2))
3,/27
2))0$,1GLUHFW
2))
0$,1SLO WHG
2))
5(/($6(
,QWHUQDO3RZHU2Q6HOI7HVW
)/$0($)7(5%851
$//2:('
)/$0(
,13876&+(&.('
)25)$/6()/$0(
)/$0(
)$,/
3$66
,13876&+(&.('
)25)$/6()/$0(
)/$0(

20
NOTES:
1)Presence of flame at this point results in a lockout.
2)When CAST (terminal 13) is open and POC (terminal 12) is open at this point, control locks out after 10 minutes. When
CAST is open and POC is closed, control remains in same state indefinitely.
3)Control locks out if FEEDBACK (terminal 8) is not present after 10 minutes.
4)CAP (terminal 14) input is required to proceed. Otherwise, control locks out, after 10 minutes.
5)FEEDBACK (terminal 8) must remain present. Otherwise, control locks out, after 10 minutes.
6)Presence of real flame is mandatory. Otherwise, control locks out. Flame failure results in Post-Purge at lockout.
7)The control locks out if POC (FVES) cannot be proven closed upon call for heat.
8)Presense of flame for more than 60sec at this point will result in a lockout.
9)CAP (Terminal 14) input must remain present. Otherwise, control will lockout.
EXPLANATION OF SEQUENCE STATES
1) POWER ON
This is the application of power to the control. It's important that a single phase (110/230 VAC 50/60 Hz) is
applied to the control and the inputs to the control are sourced from the same phase.
2) INITIAL SYSTEM CHECK
During this state, the control undergoes an internal Power-On Self-Test (POST) to verify that the hardware
and software are operating properly. The non-volatile lockout feature forces the control to move to lockout
if the last lockout condition was not cleared prior to power off. The control further checks the critical input
and output terminals to make sure they are in the proper state. The control expects the flame to be com-
pletely extinguished at this point.
3) PRECONDITIONS FOR BURNER STARTUP
The control verifies that the air-flow switch is in the Normally Closed position via the Combustion Air
Switch Test (CAST) input and a verification of the main fuel shutoff valve (POC/FVES) is performed as
well. Flame must not be present at this point. Failure to prove POC or CAST input will lead to a halt in the
state sequence or the control will proceed to lockout.
4) CALL FOR HEAT
The recycle limit (terminal 5) is energized to alert the control to start a burner cycle.
5) PREPARE FOR PURGE CYCLE
The control turns on the combustion blower (terminals 6 & 7).
6) MOVE TO PURGE
The control commands the damper actuator to move to the OPEN (high fire) position. It expects the actua-
tor to report a successful transition to the OPEN position by energizing the FEEDBACK input (terminal 8).
The control also checks to make sure that the airflow switch is operating by monitoring the CAP input.
7) PURGE
The control purges the combustion vessel for a period of time (length of purge is based on the control series
installed).
8) MOVE TO IGNITION
Upon successful purging, the control moves to ignition by energizing the MINIMUM output (terminal 10).
It expects the actuator to report a successful transition to the MINIMUM (LOW FIRE) position by energiz-
ing the FEEDBACK input (terminal 8). Flame must not be present at this point.
9) IGNITION
The control energizes the ignition transformer by activating terminal 16. It's critical that the damper actua-
tor remain at the MINIMUM (LOW FIRE) position during this state. Flame must not be present at this
point.
Other manuals for BurnerPRO
1
This manual suits for next models
24
Table of contents
Other Fireye Control System manuals
Popular Control System manuals by other brands

3M
3M SST manual

HAUTAU
HAUTAU WLAN-Box Installation and operating instructions

Agrilight
Agrilight AGRIBOX pro Installation and user manual

Jäger
Jäger APRS I-GATE Operator's manual
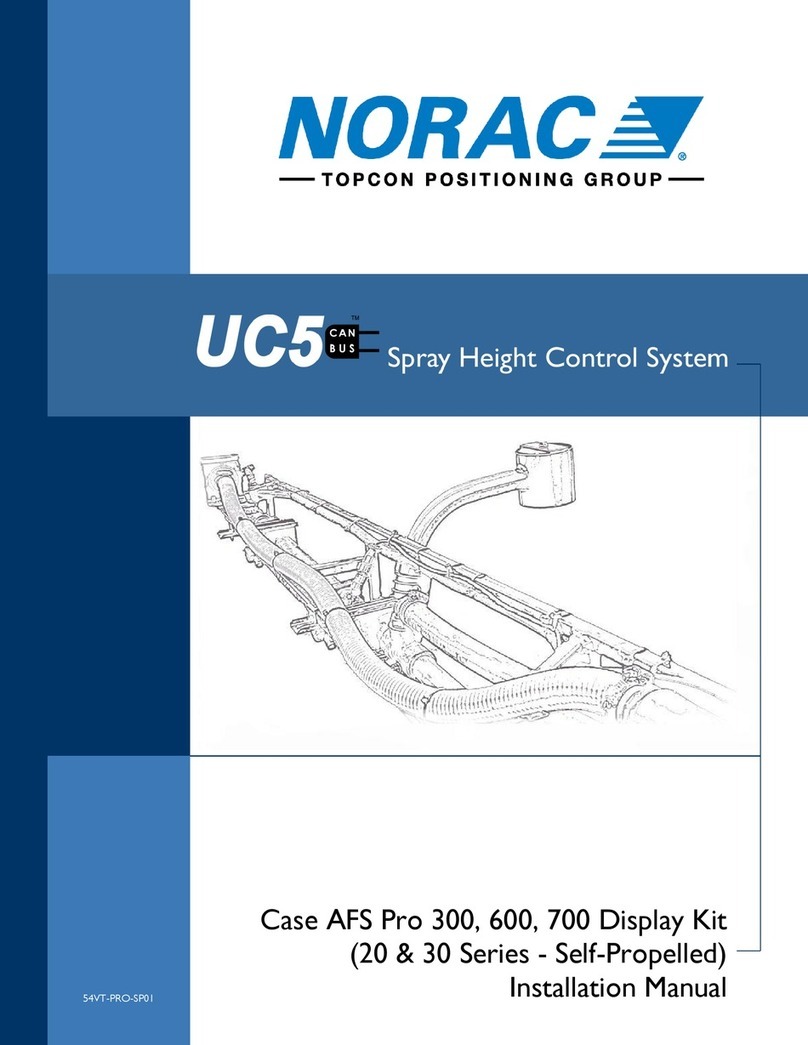
Norac
Norac Case AFS Pro 300 installation manual
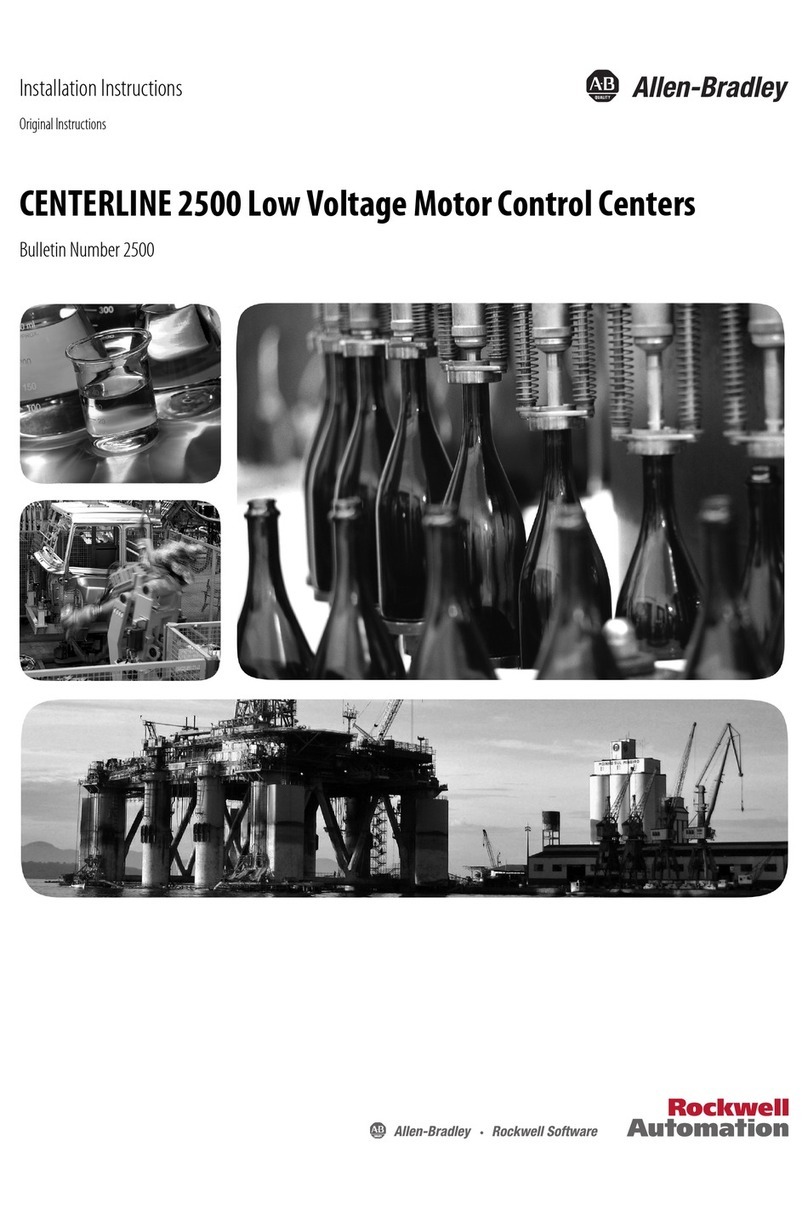
Rockwell Automation
Rockwell Automation Allen-Bradley CENTERLINE 2500 installation instructions