Fireye 6000 Series User manual

NXCEX-6000
January 4, 2019
6000 Series NXC20EX, and
NXC40EX Servos for
Class 1 Division 2. Hazardous
Locations

Health and Safety
SAFETYWARNINGSINTHISMANUAL
In this manual, we indicate potential safety issues by this symbol: .
Please read the safetyinformation before you do any task preceded by this symbol.
There are two levels of safetymessage: WARNINGS and CAUTIONS:
WARNING
Failure to observe a WARNING about the equipmentdescribedin this
manual can cause propertydamage, severe injury, or death.
CAUTION
Failure to observe a CAUTION may cause minor injuryor damage to
equipment.
Health and Safetywhen using Fireye NEXUS CombustionControl
Systems.
It is the responsibility of the owner or user to make sure that the equipment
described herein is installed, operated and commissioned in compliance with the
requirements of all national codes, and local jurisdictions that may prevail.

WARNINGS
1. When this equipment is fittedto an appliance, due regardmust also be
given to the requirements of that appliance.
2. Before attempting to install, commission or operate this equipment,
you MUSTread and fullyunderstand all relevant sectionsof this
manual. If in doubt about anyrequirements, please consult your
supplier.
3. Repairs to the controller must onlybe carried outbythe manufacturer
or their appointedagents.
4. Installation, commissioningor adjustment of this product MUSTONLY
be carried out bySUITABLY TRAINED ENGINEERS or PERSONNEL
QUALIFIED BY TRAINING AND EXPERIENCE.
5. After installation ormodificationsto the installation, all functions of
the equipment MUSTbe checkedto make sure safe and reliable
operation of the controller.
The manufacturer of this equipment accepts no liability for any consequences resulting
from inappropriate, negligent or incorrect installation, commissioning or adjustment of
operating parameters of the equipment.
This equipment must only be fitted to burners as detailed in the contract specification.
The supplier must approve in writing any change to the specification.
Do not leave Control panels uncovered while power is ON. If it is essential to do so while
rectifying faults, only personnel qualified by training and experience may be involved.
The time any coversare off must be kept to a minimum, and warning notices must be
posted.
Before attempting any work on this equipment or any equipment connected to this
equipment, the electrical supplies must be isolated.
Safety interlocks must not be removed or overridden. Correct any faults detected before
operating the controller.
NOTE: The manufacturer of this equipment has a policy of continual product improvement, and
reserves the right to change the specification of the equipment and the contents of this manual
subject to reviewby the certification body.

Manual overview.
Who is this Manual for?
This manual is intended for combustion system designers and engineers qualified by training,
competence and experience. They might be involved in the design and specification of
combustion systems, replacing system components or in the commissioning of new combustion
curves.
Scope of this Manual
In this manual, we cover the description, installation, maintenance, specification and approvals for
NXC20EX and NXC40EX actuators suitable for use Hazardous Locations Class 1 Division2
Groups C & D. For all other issues, including the commissioning of combustion systems and fault
finding, please refer to the Commissioning manual for the appropriate controller. This manual
does not cover Operator instructions.
Disclaimer
Nothing contained in thismanual constitutes a warranty of any kind in respectof the machine or of
the results to be achieved by its use. The only warranties given by Fireye in respect of any
machine are those expressly given by Fireye or your supplier in the contract under which it sells
the machine to its purchaser.
Warranty is void in the case that the equipment covered by this manual is operated outside of the
instructions, specifications and approvals stated herein.
The information contained in this manual is believed to be accurate at the date of publication.
However, Fireye give no guarantees in this respect, and reserves the right to alter future
publications.

Table of Contents
IMPORTANT: Please read the Healthand SafetyIssues before working on this equipment.
1. INTRODUCTION 2
1.1 Outline. ...............................................................................................................2
1.2 Controller compatibility. ........................................................................................2
2. DESCRIPTION OF SERVO 3
2.1 SERVO types and specification.............................................................................3
3. HOW TO INSTALL AND WIRE TO THE SERVO 5
3.1 Mechanical fixing. ................................................................................................6
3.2 Wiring Requirements............................................................................................6
4. SELECTING AND SETTING UP THE SERVO 10
4.1 Valve Control Direction.......................................................................................10
4.2 Locking the Servo to the Valve Shaft ...................................................................11
4.3 Closed position settings (P00).............................................................................12
5. ROUTINE MAINTENANCE OF THE SERVO 13

1. Introduction
1.1 Outline.
The servos described in this manual are special system components, designed for application in
combustion systems where the atmosphere may be of a hazardous nature for a limited time. The
limit of application is identified on each device and given in the specification section of this
manual.
This actuator type is fitted to combustion systems operating in an intermittent or continuous mode.
It is most likely that the equipment will be permanently powered unless off-line for plant
maintenance.
1.2 Controller compatibility.
Each device described in this manual is CANBus powered, and compatible with all Fireye NEXUS
6000 series controllers and expansion modules.

2. Description of Servos
2.1 Servo types and specification.
The servo motors approved for Hazardous Location operation are NXC20EX and NXC40EX
CANbus type, with 20Nm and 40Nm actuation force respectively.
2.1.1 Servospecification.
MotorType
Actuation time:
24V AC asynchronous servo chassis:
30 seconds for 90 degrees (50/60Hz)
Interface to 6000 series controllers.
ETC specific CANbus fromthe controller –
Terminals 1, 2 - 29.5Va.c. maximum (50/60Hz).
Terminals 3, 4 - Data (5V)
VA rating
NXC20EX = 18 VA
NXC40EX = 18 VA
Actuating torque
NXC20EX = 31 Nm (driving), 41 Nm (holding)
NXC20EX = 23 ft lbs (driving), 30 ft lbs (holding)
NXC40EX = 46 Nm (driving), 51 Nm (holding)
NXC40EX = 34 ft lbs (driving), 37 ft lbs (holding)
Accuracy (as specified by EN12067)
Positioning Repeatability
±0.3
± 0.3
Protection Category
Operating temperature
Conduit/gland connections
Mounting orientation
Weight
IP66 (NEMA 4)
-4 F to +140 F (-20 C to +60 C)
M20 x 1.5
Any
7.5 lb (3.4kg)
Suitability:
USL, CNL –Class 1, Division 2, Groups A, B, C
and D, OR non-hazardous locations only.
UL file E495355

2.1.2 Servodimensionsandmountingholeoptions.

3. How to install and wireto the actuators
This section contains basic installation information, wiring specification and connection details.
The process of installing the actuator(s) has 2 aspects:
Mechanical fixing
Electrical connection
WARNING
EXPLOSION OR FIRE HAZARD.
Hazard can cause damage to property, severe injuryor death
Do not connect or disconnect equipmentunless power has been
switched off, orthe area is known to be non-hazardous.
To prevent possible hazardous burner operation, you must verifythe
safetyrequirements each time a control is installed on a burner, or if the
installation is modified in anyway.
The enclosure of the actuators has a non-conductingcoating and may
generate an ignition-capable level of electrostaticcharges under extreme
conditions. The user should ensure that the equipment is not installed in
a location where it will be subjectedto external conditions (such as high-
pressure steam) which might cause a build up of electrostatic charges on
non-conducting surfaces.
WHEN INSTALLING THIS PRODUCT:-
Read these instructions carefully. Make sure you fully understand the product
requirements. Failure to follow them could damage the product or cause a hazardous
condition.
Check the ratings given in these instructions to make sure the product suits your
application.
After installation is complete, check that the product operates as described in these
instructions.
CAUTION
Wiring must comply with all methodsas required for Class 1 Division 2, as per
NEC and/or CEC.
Loads connected to the 6000 series controllers must not exceed those listed in
the specifications as given in this manual. Consider that if more than two of
these actuator types are required then the NXCBH Canbus Hub will be
required to provide the extra power for third and fourth actuators.
Choose the actuator sizing carefully to ensure that they operate within their
specification.
Make sure that the actuator is connected to ‘Earth’, to maintain electrical safety
and reduce the risk of electrostatic charging.

3.1 Mechanical fixing.
Brackets to support the weight of the actuator (7.5 lb) must be fabricated to suit the burner and
valve/damper components.
The actuators are provided with M6 tapped screw holes into the body. The maximum depth of
these holes is 12mm. The geometry of the actuator fixing holes is shown in the drawing 2.1.2.
Specific attention should be paid to the alignment of the output shaft and the spindle of the valve
or damper, because they must align ‘centred’. Select a flexible coupling when variations in
alignment are suspected.
3.2 Wiring Requirements.
This equipment must be installed using wiring methods as required for Class 1 Division 2 as per
the NEC and/or CEC.
Please pay particular attention to the wiring requirements for the actuator. These will protect the
equipment from electrical interference, earth loop problems, and damage to the controller and
modules.
3.2.1 General.
WIRING INSTALLATION MUSTBE CARRIED OUT BY A COMPETENT ELECTRICIAN.
The main controller MUST be mounted within a ‘burner cabinet’ or similar panel in a designated
‘safe’ area, and MUST be earthed to the overall enclosure to ensure safe and reliable operation;
use the largest cross-sectional area green/yellowearth wire available. Do not use a green/yellow
conductor for any purpose other than earth. The metal body of all other component parts
MUST be connected to earth using a green/yellowconductor.
To comply with EMC requirements, the controller and any optional units must be wired using the
specified cable sizes, and screen connections, observing any maximum cable length limitations.
Cabinet designers MUST segregate Line voltage and Extra Low Voltage (ELV) cables within the
burner cabinet, distribution panels and conduits.
The manufacturerof this equipment recommends the use of bootlace ferrules on all wire
ends, as a “best practice”.
Bootlace ferrules
All cabling that operates at more than 50 V must be multi-strand, single core, PVC insulated,
16/0.2 mm (0.5mm2), and must meet the requirements of NEC and/or CEC.
For cables carried in conduit, secure all cables at both ends, using a suitable anchorage method
in the cabinet. Ensure that cables, conduit and conduit connections meet the requirements for
hazardous area operation. No additional cable or conduit entry holes are permitted in the
casing or cover of the actuator.

Connect all signal cable ‘braid’ screens to earth using the screen termination clamps provided on
the controller. Connect all cable screens to earth at the controller only, unless stated otherwise.
Where CANBus wiring connects through one device to connect to another, terminals 5 and 6 are
common to maintain screen continuity.
The equipmentdescribed in this manual has been tested for compliance to safety directives listed
in the section headed ‘Actuator specification’. However, after it has been connected to a burner
and other associated controls, it is the responsibility of the installer to make sure the complete
installation meets the requirements of the directives relevant to the particular installation.
3.2.2 EarthConnection.
All sections of the control system with metal enclosures MUST be connected to earth.
Connect at the tag showing the Earth symbol, inside the cover on the body of the device (see
picture in 3.2.4). These connections are required to maintain the overall electrical safety of the
installation and ensure the EMC performance of the equipment. Failure to comply with the wiring
requirements will affect the performance of the system and may cause a hazardous condition to
occur.
DO NOT use the screen of the signal cable to provide the electricalsafety earth. You MUST make
a separate earth connection using colour coded earth wire of cross-sectional area 0.75mm2or
greater, as permitted by conduit sizing.
3.2.3 ELV signalcableScreenConnection(CANBus).
These types of cable may also employ a ‘foil with drain wire’. This is not suitable as a screen
because the cross section of the drain wire is insufficient to provide correct screening of the
signals. Also, there is no provision to connect the foil or drain at the main controller.
You must connect the ELV signal cable screens at the screen termination clamps only, unless
stated otherwise in this manual. The screen termination clamps on the controller are only to allow
connection of the cable screens to the main controller - they do not provide strain relief.
Terminal 5 in the actuator is for the termination of the cable screens and, where required, for
continuity of the screen when actuators are connected in a daisy-chain configuration (see picture
in 3.2.4).

3.2.4 Actuatorterminalconnections.
The terminals within the actuator followthe CANBus wiring system and are labelled to reduce the
possibility of wiring errors. This information is in the table below:
Terminal No.
Module
Function
Voltage Range
1
Actuator
24 Vac Supply
24 –29.5 Vac
2
Actuator
24 Vac Supply
24 –29.5 Vac
3
Actuator
CAN +
0 –5 V
4
Actuator
CAN –
0 –5 V
5
Actuator
Screen terminal
Not applicable
Safety Earth terminal
CAN terminals
Primary conduit
connection point.
3.2.5 Conduitandglandconnections.
The actuators described in this manual have been approved for use in Class 1, Division 2
locations and have IP66 (NEMA 4) enclosures. There are three threaded conduit or gland
connection points on the actuators, two of which have Exblanking plugs fitted. It is essential that
Ex type conduit, connectors and gland systems are selected, to ensure safe operation can be
maintained whilst this equipment is in operation in a hazardous area.
One of the connection points may be used as a test port, when required.

3.2.6 Actuatorassembly- safetychecks.
Ensure that all cable or conduit fittings are sealed correctly with reference to the
manufacturers specification.
Before attempting to fit the cover, ensure that the mating edges of the actuator body and
cover are not damaged. Deformed edges may cause further damage to the gasket
material and so render the device unsuitable for operation in a hazardous area.
When fitting the cover, ensure that cables do not become trapped or damaged by the
cover.
Ensuring that the O-rings under the cover screw heads are not damaged, then tighten the
cover screws evenly to ensure that the cover is seated evenly onto the actuator base and
red sealing gasket.

4. Selecting and setting up the actuators
CAUTION
Check actuators for any signs of damage before installation.
Do not start the operation of the combustion system before properlysetting the
limiting cam positions.
Protect actuators from shock or impact (e.g. dropping).
Do not use the actuator as a load bearing device (e.g. stepping or climbing
point).
Permanent over-loading or jamming the movement of the actuator may
damage it.
Actuators must be selected to match or exceed the load presented by the controlling valve or
damper.
Mounting brackets must be accurately aligned to eliminate side load on the actuator output shaft.
Fireye recommend that the coupling between the actuator and the valve/damper is pinned to
the shaft of both devices, after the actuator potentiometer and direction settings have been
made
4.1 Valve Control Direction
Make sure that each actuator travels inthe correct direction to match the mechanical configuration
of the burner. The default setting is for an actuator to move anti-clockwise (looking at the end of
the output shaft) when the actuator is driven ‘UP’.
You can reverse this using Option parameters 5.0 to 5.9. The default is 0 for anticlockwise
movement. Change it to a value of 1 for clockwise movement, as viewed looking onto the end of
the actuator drive shaft.
The actuators are synchronous a.c. type.

4.2 Locking the Actuator to the Valve Shaft
CAUTION
After the position of the actuator shaft relative to the valve shaft is correctlyset,
each actuator must be locked to its valve shaft or air damper shaft.
In order to prevent the joint between actuator and shaft moving, it is
recommended that the device used to link the two items is pinned together.
See the picture below.
The actuator zero point cannot be adjusted. Before connecting to the valve
shaft, first make sure the actuator direction is set, and it is driven to its
minimum point.
It is essential that the actuator and valve remain securely connected, to ensure
safe operation of the equipment.
The Coupling and shaft have been drilled to
size then a roll pin has been pressed into the
holes to fix the angular position.
Actuator or Valve Shaft
Coupling
The actuator output shaft and the spindle of the valve or damper must run ‘centred’, select a
flexible coupling when variationsin alignment are suspected.

4.3 Closed position settings (P00).
Each time a burner start-up sequence is initiated the controller will move the fuel and air damper
actuators to their respective ‘Closed’ positions (P00), to prove correct actuator operation. The zero
feedback position is preset at the factory to suit the majority of applications.

5. Routinemaintenanceof the actuators
WARNING
EXPLOSION OR FIRE HAZARD.
Hazard can cause damage to property, severe injuryor death.
Do not connect or disconnect equipmentunless power has been
switched off, orthe area is known to be non-hazardous.More thanone
power supplydisconnect maybe involved.
To prevent possible hazardous burner operation, you must verifythe
safetyrequirements each time a control is installed on a burner, or if the
installation is modified in anyway.
The enclosure of the actuators has a non-conductingcoating and may
generate an ignition-capable level of electrostaticcharges under extreme
conditions. The usershould ensure that the equipment is not installed in
a location where it will be subjectedto external conditions (such as high-
pressure steam) which might cause a build up of electrostatic charges on
non-conducting surfaces.
CAUTION
Before starting any maintenance or service work. Check that all permits are in
order and that safety and emergency procedures are clearly understood.
Cleaning of the Actuators should be carried out with a damp cloth.
On starting the burner, the actuator and allattached fittings/lever/rod
assemblies etcetera, will start to move.
After completion of any adjustment work, verify the proper function of all
attached fittings/levers, etc.
Never install or work on a defective actuator.
There are no user serviceable parts within the actuators, and the gearbox is manufactured with a
permanent grease lubrication and thus maintenance-free.
Maintenance will be limited to the following:
Verification of the position system.
Checking of Safety Earth bonding to the connection point.
Checking of the condition of cables, cable glands or conduit and conduit fittings.
Checking the condition of the body, cover, seals and gaskets - between the body
and cover.
Seal test - Under constant temperature conditions, the time interval required for an
internal pressure of at least 30mm (1.2”) water gauge belowatmospheric to rise to
half the initial value, shall be not less than 90s.

NXCEX-6000
January 4, 2019
This manual suits for next models
2
Table of contents
Other Fireye Servo Drive manuals
Popular Servo Drive manuals by other brands
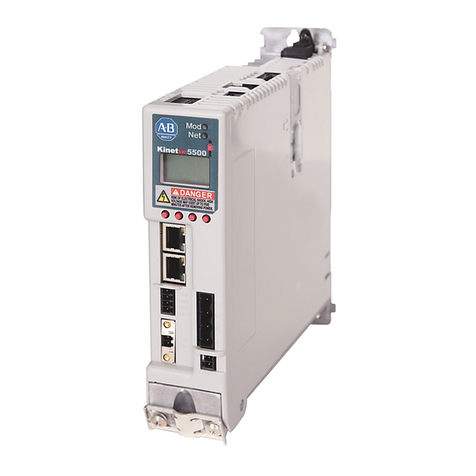
Allen-Bradley
Allen-Bradley Kinetix 5500 installation instructions
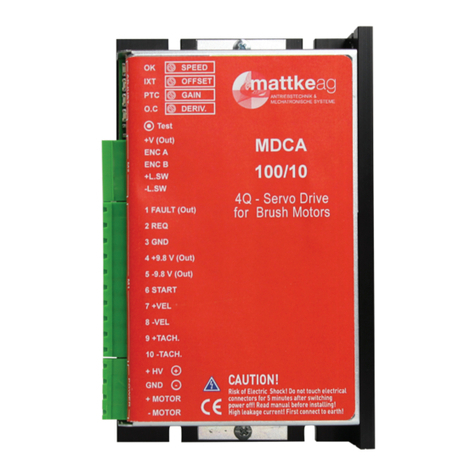
mattke
mattke MDCA Series manual
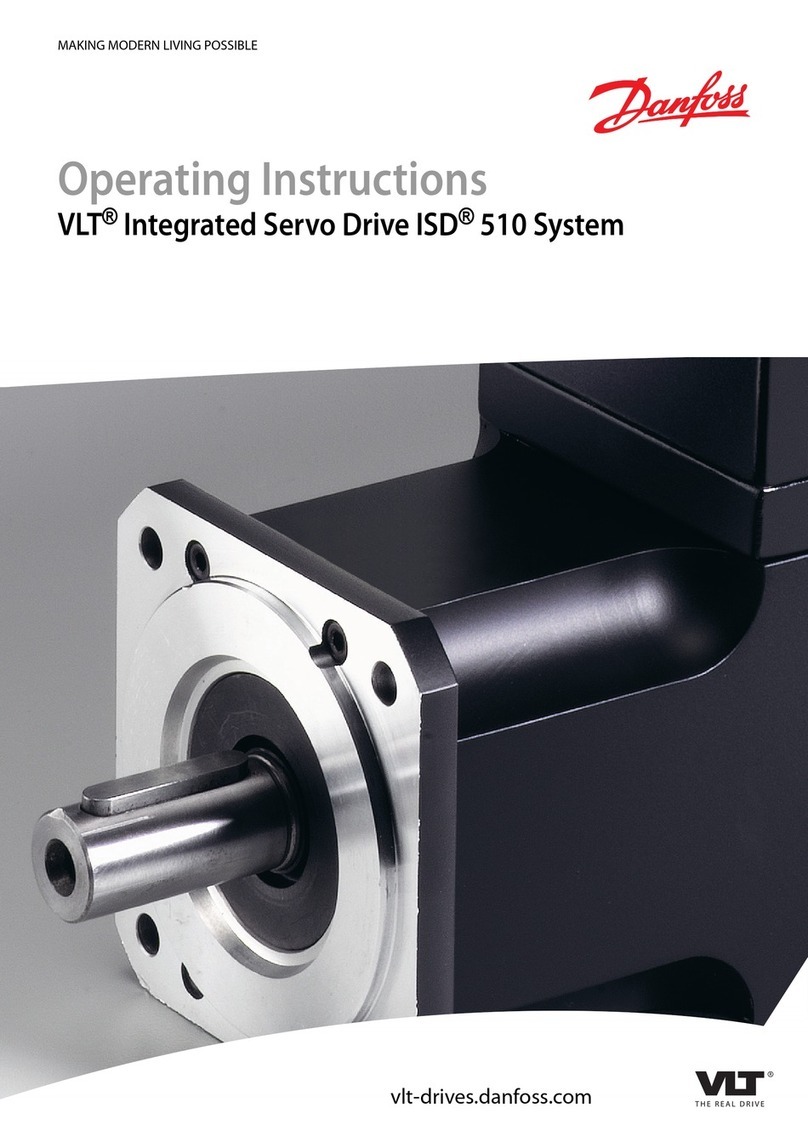
Danfoss
Danfoss VLT Integrated Servo Drive ISD 510 System operating instructions
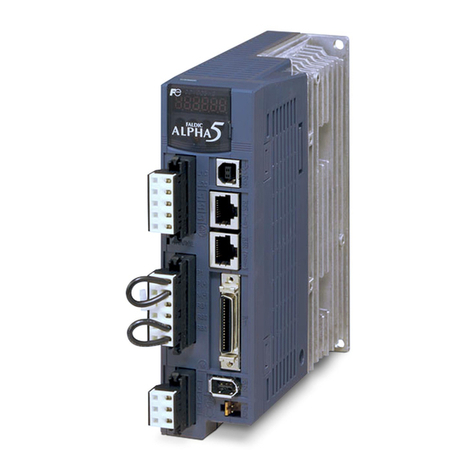
FujiFilm
FujiFilm ALPHA 5 RYT-SX user manual
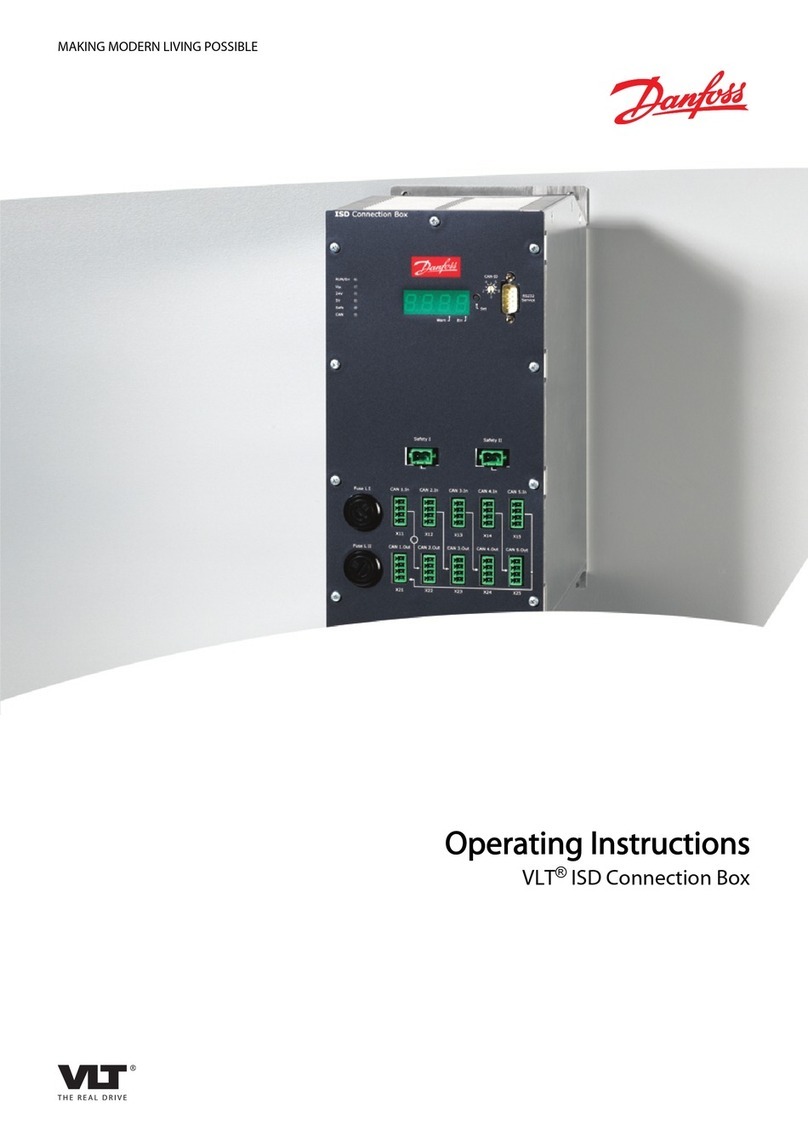
Danfoss
Danfoss VLT ISD Connection Box operating instructions
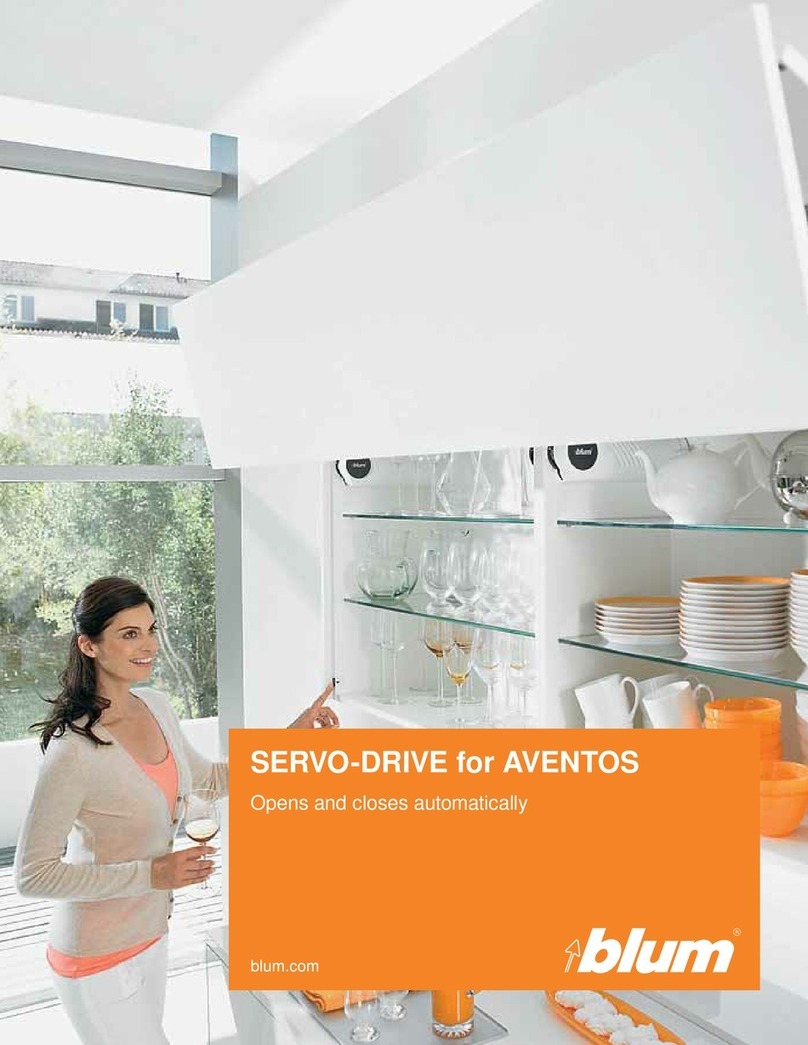
BLUM
BLUM 21KA000 manual