Flama ZB Series Instruction manual

FEATURES:
!
!simple design
!unidirectional, uniform flow
!triggered elecromagneticly
!available with two types of solenoid triggers:
WE (12V DC) or EZB-12,6G (230V AC)
!low weight (mass)
!bistable - in lack of voltage condition the valve could stay in one of stable
position: open or close.
Control voltage is necessary or valve closing only.
!opened only manualy (“memory” function)
!closed with electrical impulse
!has the option for manual closing with botton
!permanent strainer built-in
!adapted for external application
!conforms to
!
poppet valve
PN-EN 161:2011+A3:2013
meets applicabe requirments of Regulation (UE) 2016/426 (GAR) from
9 march 2016 y. and Directives UE:
2014/35/UE (LVD); 2014/30/UE (EMC)
12
coil connection
plug-in socket
ELECTRICAL TERMINATION
AC, DC
2
1
21 The plug can be fixed in 3
positions towards the socket
O
(each 90 )
!
public utility buidings, domestic installations (i.e.one family houses and
multi-family houses, farmsteads, private use recreational buildings),
reducing -measuring stations, biogas plants, etc. itp. - as an actuator
that surely and effectively cuts off the gas supply to faulty installations
when a gas presence is detected in supervised by System compartments
!in gas installations supplied in conformance with appropriate regulations
from low pressure gas grid
!additionally valve can be used as manual stopcock, however it can not act
as gas installation main stopcock
!together with gas detection system, valve can perform a function of lock-
up for devices that burn gas fuels and are intended for use inside the
buildings and utility compartments. Such a lock-up prevents from
accumulation of burning gas in mentioned buildings and compartments
in Gas Safety Systems installed: gas boiler rooms, industrial facilities,
APPLICATION:
2
1
Mp
P
DC
max
3x1,5
Conductor wires polarization-indifferent (apart from PE);
recommended - as on figure
AC
2
1
N
PE
L
max
3x1,5
PG11
Schematic symbol
P
A
TECHNICAL DATA
Valve
maximum operating pressure......... P = 0,25 bar
MAX
safe static pressure ........................ P = 5 bar
S
closing time ................................... < 1s
o o
ambient and media temperature ... -25 C ¸ 60 C
pipe threaded connection .............. Rp - internal straight thread
compliant with PN-EN 10226
pipe flanged connection ................
mounting direction ......................... any
keeps compatibility of flange
connection dimensions [PN16, 01, B]
in acc. with PN-EN 1092-1
Solenoid trigger
trigger type..................................... WE EZB-12,6G
control voltage....................... ........ 12V DC 230V AC
voltage tolerance ........................... -15%; +10%
power consumption........................ 26 W 46 VA
coil resistance ............................... 5,5 W134 W
safety class ................................... III I (earthing)
impulse minimum time duration..... 0,2s -0,3s
(necessary for closing the valve)
operation type ............................... S1 continuous 100%
o o
ambient temperature .................... -30 C ¸ 60 C
electrical connection ..................... tri-contact terminal block
degree of protection (acc. PN-EN 60529) IP65
design (integrated) ............................ resin-molded coil
Connection wire size depends on the distance to
control module - see Service Manual of applied
control module.
Size and allowable lenght could be also
determined assuming as admissible10% voltage
drop on conductor (calculated from rated voltage
12 V)
1015
2/2 way type ZB
klasa B
Ň
Diameters range DN Rp 3/4 ¸ Rp 2 1/2 (DN20 ¸ DN65) DN50 ¸ DN100
Media
threaded connection flanged connection
gas fuels (gases as per PN-EN 437)
Group 1
B - DN80 i DN100
Class
A - DN20¸DN65
Shut-off poppet valve,
designed to operate with gas detectors
page 1/4ZB - data sheet release 02/2019/KK

OVERALL DIMENSIONS (mm), WEIGHT (kg)
ZB-25 ZB-32 ZB-40 ZB-50 ZB-65 ZB-50k ZB-65k ZB-80k ZB-100k
25 32 40 50 65 50 65 80 100
1 1 1/4 1 1/2 2 2 1/2
137 155 180 188 218 225 243 307 318
28 37 48 40 61 78 83 94 103
79 100 112 142 170 165 185 200 222
115 144 178 193 240 230 270 310 350
92 92 92 92 92
11 11 11 11 11 11
4,06 5,82 9,80 11,82
11 11 11
1,35 1,96 2,62 3,18 4,81
valves with threaded connection
(internal straight thread in acc. with PN-EN 10226)
valves with flanged connection [PN16, 01, B]
(conforms to PN-EN 1092-1)
116 126 143 158 170 157 171 231 239
92 92 95 95
L
P
Pg
E
Rp
Pg
L
A
C
B
P
E
DN
DN
Rp
A
B
(1)
C
E
L
P
Pg
Weight
ZB-20Type
20
3/4
127
22
77
105
92
11
1,20
112
C
B
A
INSTALLATION - basic assembly requirments:
MMAX
MMAX
TMAX
MMAX
MMAX
TMAX
[Nm] t 10s
Ł
MMAX
3/4
20
85
90
1
25
125
160
1 1/4
32
160
260
1 1/2
40
200
350
2
50
250
520
2 1/2
65
325
630
80
400
780
100
400
950
[Nm] t Ł10s
TMAX
Rp
DN
TABLE 1
valve class Avalve class B
!ensure that valve is mounted rigidly so as to avoid any
vibration
!
!
!tighten the flange screws crosswise Attention: maximum
torque of 50 Nm (~5 kGm)
!a strainer which protects from mechanical impurities should
be fitted upstream the valve in the gas installation.
Maximum dimension of strainer openings should not
exceed 0,2 mm
!valve’s assembly should be finalized with carrying out an
leaktightness test of installation including ZB valve using
compressed air or inert gas (oxygen use is forbidden)
Test pressure cannot exceed P = 5 bar
S
!during operation valve
- cannot be exposed to dilatation nor dynamic forces
- need to have ensured correct operating temperature
(ambient and media)
- should be protected against strong dustiness and
water flooding
in valves with threaded connections pipe should be screw in
that way so that 10 second torque not exceed values of
T given in TABLE 1
MAX
use appropriate thread sealant to esure tightness of the
connections
!valve can be installed:
Řoutside the buildings - in the junction box protecting
against direct influence of atmospheric factors
Attention! Valve is not waterproof!!!
It should be installed in such a box and in such a
way that it is completely protected against
dripping water during rain and snowfall.
Ř inside the buildings
!install downstream the main tap, upstream or downstream
the gas meter (according to the gas flow arrow on the valve)
!it is necessary to anticipate and take into account the
pressure surplus that may occure at the valve inlet in case of
failure to components in the system located upstream the
valve
!mounting position - any
!direct contact of the valve with wall, ground, etc. is
unacceptable; keep the minimum distance - about 1 cm
!location of the valve should be selected so as to ensure free
access needed to its operation (for persons authorized to do
so)
!attention should be paid so that after valve installation there
is enough space left (maneuvering area) for ease coil
replacemet
!ensure proper rigidity of the installation in the place where
the valve is installed (Group 1 valve).
This can be achieved by using rigid supports to the bending
and torsional stress exerted by the piping system in the
installation (eg due to the lack of alignment of the of the
pipeline at the inlet and outlet of the valve)
!maximum moments: turning T and bending M
MAX MAX
cannot exceed the values given in TABLE 1
page 2/4ZB - data sheet release 02/2019/KK

valve manual open hand grip
pilot sleeve
poppet pin
slide rings
pull spring
sealing ring (o-ring)
bonnet
sealing ring (o-ring)
pressing spring
filter
poppet
poppet gasket
valve seat
valve body
fastening screw
plug-in socket
impedance coil Pg11
power supply socket
trigger movable core
valve manual close button
solenoid trigger
interlock ball
seating stud
plug G1/8 lub G1/4
limit switch for example K01/1type from DUNGS
impedance coil Pg11
obique bush
limit switch push rod
pushing ball
1.
2.
3.
4.
5.
6.
7.
8.
9.
10.
11.
12.
13.
14.
15.
16.
17.
18.
19.
20.
21.
22.
23.
24.
25.
26.
27.
28.
29.
CONSTRUCTION
2
3
4
5
8
9
10
11
12
13
14
15
18
19
21
20
22
23
16
6
7
1
PP A
Valve head* position sensor
(valve closing)
12
3
F
Switchning function
Constructional materials
valve body aluminium alloy
poppet pin stainless steel
pilot sleeve aluminium alloy
springs galvanized or
stainless steel
poppet body aluminium alloy
poppet gasket NBR (nitrile-butadiene rubber)
valve seat aluminium alloy
sealings NBR (nitrile-butadiene rubber)
slide rings PTFE
filter stainless steel - filter gauze
solenoid coil copper
24
25 26 27 28 29 3
17
(*) - valve head: movable part of valve which shuts-off gas fow
page 3/4ZB - data sheet release 02/2019/KK

FLAMA-GAZ ELEKTROZAWORY S.C.
phone +48 33 856-85-70, fax +48 33 856-85-62, www.flamagaz.com, e-mail: [email protected]
Modification without prior notice of technical specification reserved
43-418 Pogwizdów k/Cieszyna, ul. Szkolna 3
page 4/4ZB - data sheet
Necessary information for ZEG valve order:
!valve type
!control voltage
!possible option and accessories
ORDERING
Example:
ZB-32/12V DC
it means:valve with threaded connection DN32
control voltage DC 12V
standard design
FLOW CHARACTERISTIC
!plugs G1/8 or G1/4 (position 24) with gaskets
Note that standard version does not have holes for
above plugs.
!counterflages with connector pipe (for valves with flanged
connection)
!stub pipe for inlet and/or outlet pressure measurment
(Ć9, G1/8 lub G1/4 together with gaskets)
- used alternatively with plugs
!gas pressure sensor (at the inlet anr/or outlet of a valve)
Pressure sensors are assembled as marked on figure,
position 24
!valve head position sensor (position 25) from DUNGS type
K01/1
ACCESSORIES - options (available upon request)
!plug with voltage presence indicator
!colour
Dp
[mbar]
3
Q [m /h]
3
Q [m /h]
3
Q [m /h]
2 3 4 10865 20 30 40 100806050 200 300 400 800600
3 4 865 10 20 30 40 100806050 200 300 400 800600
2 3 4 10865 20 30 40 100806050 200 300 400 600
12 3 4 10865 20 30 40 80
60
air dv =1
natural gas (methane) dv =0,65
propane-butane dv =1,56
ZB - 100
ZB - 20
ZB - 25
ZB - 32
ZB - 40
ZB - 65
ZB - 50
ZB - 80
Base conditions
O
+15 C
1,013 bar
dry
release 02/2019/KK
This manual suits for next models
10
Popular Control Unit manuals by other brands

Metso
Metso NELES XH Series Installation maintenance and operating instructions

Mallory
Mallory 605 instruction manual
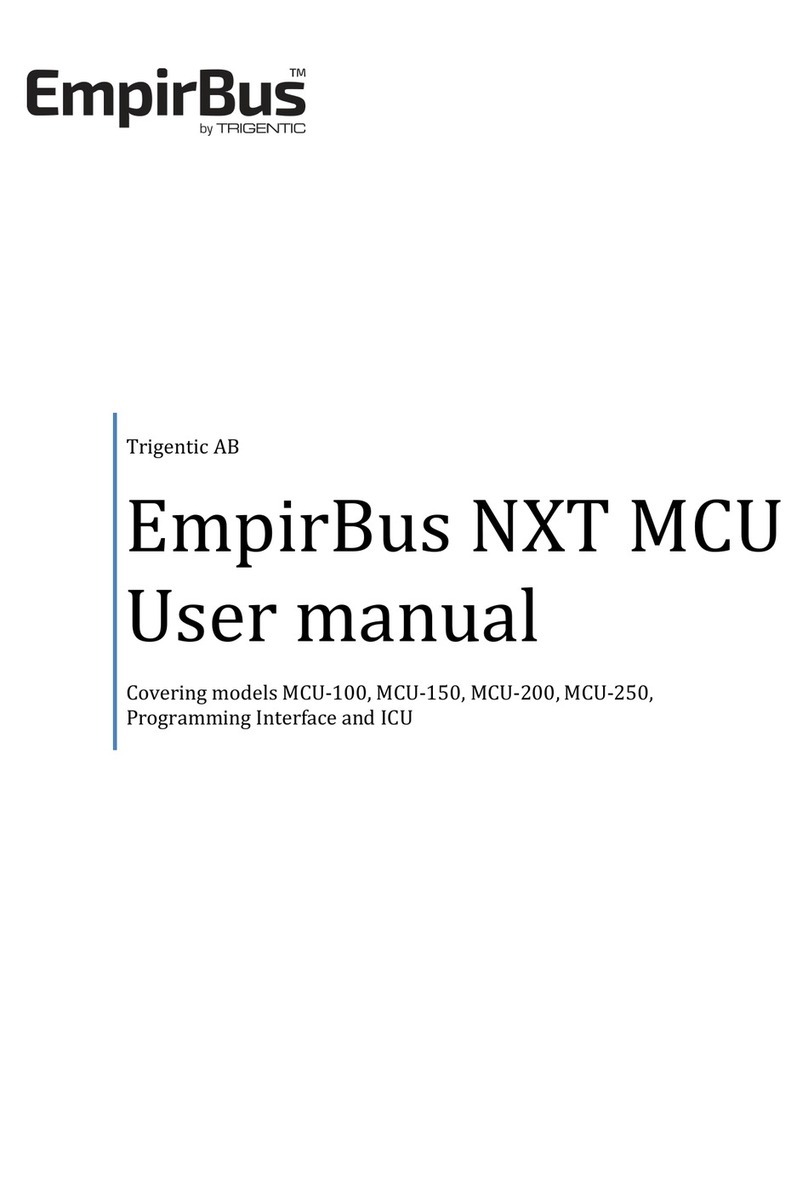
EmpirBus
EmpirBus NXT MCU user manual

Kutai electronics
Kutai electronics ATS-33 Operation manual
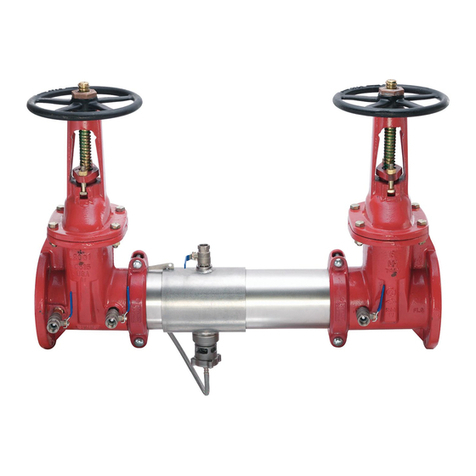
Watts
Watts 994 Series Installation, maintenance & repair
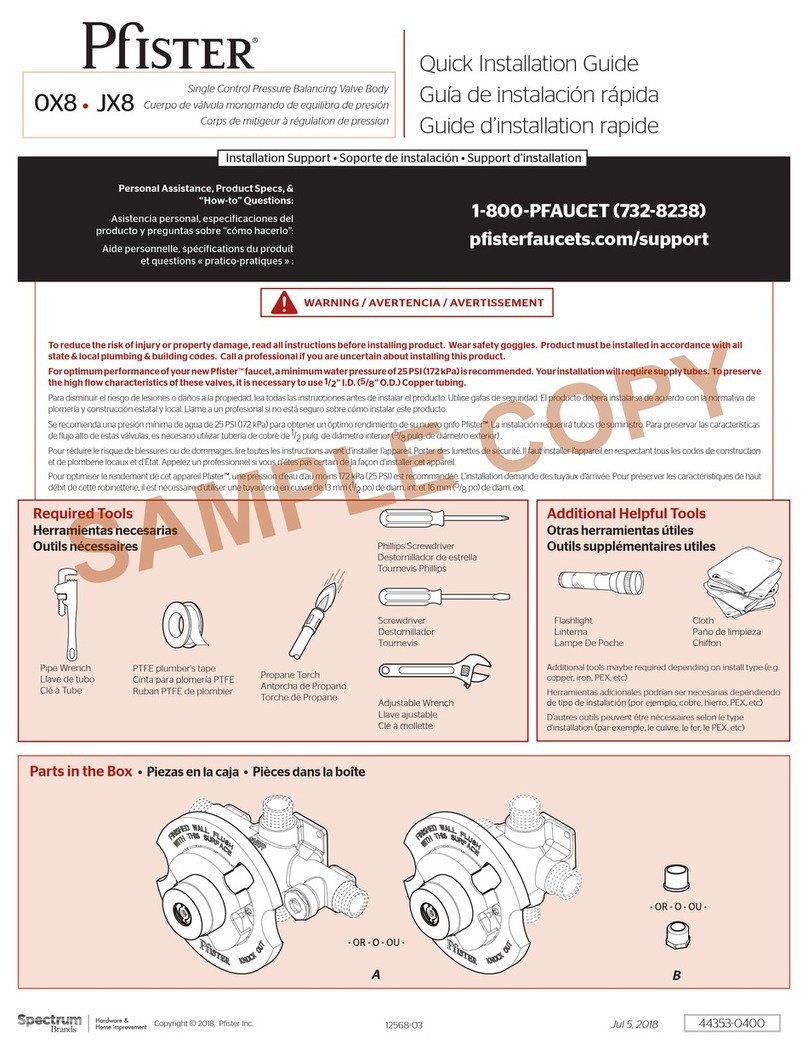
Pfister
Pfister OX8 Quick installation guide
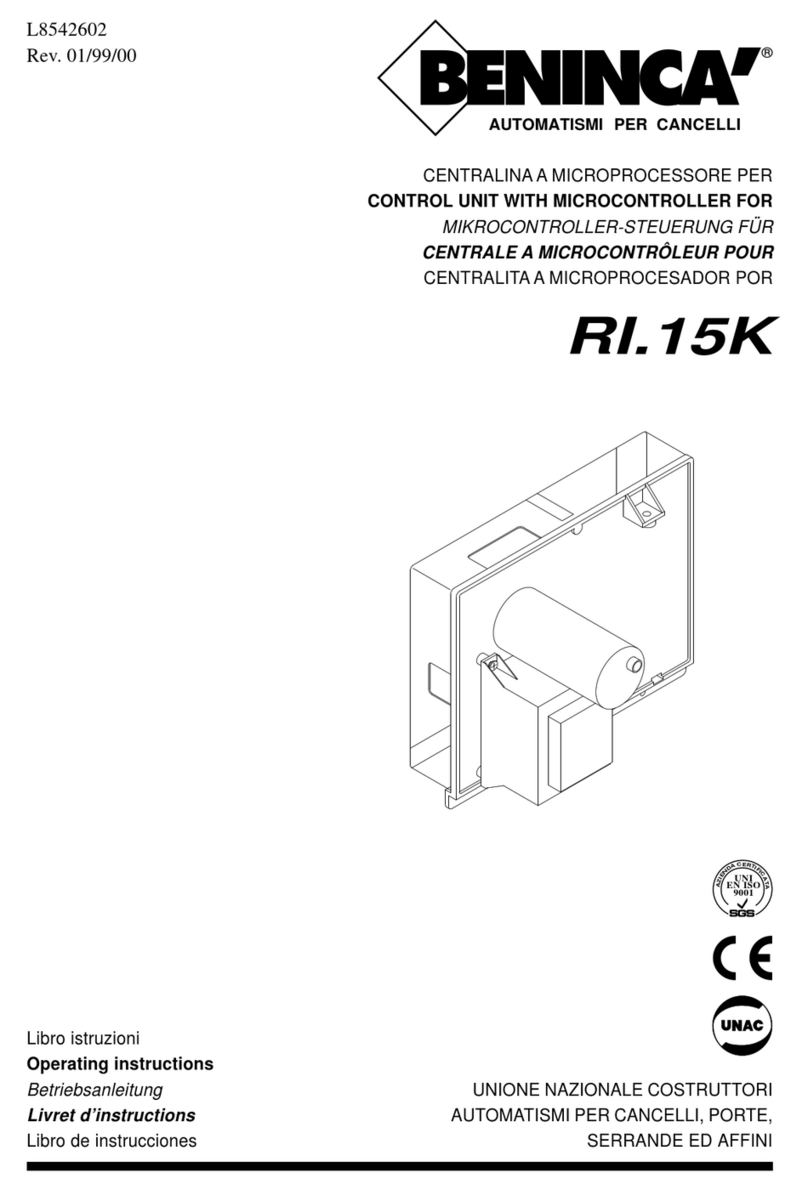
Beninca
Beninca RI.15K operating instructions
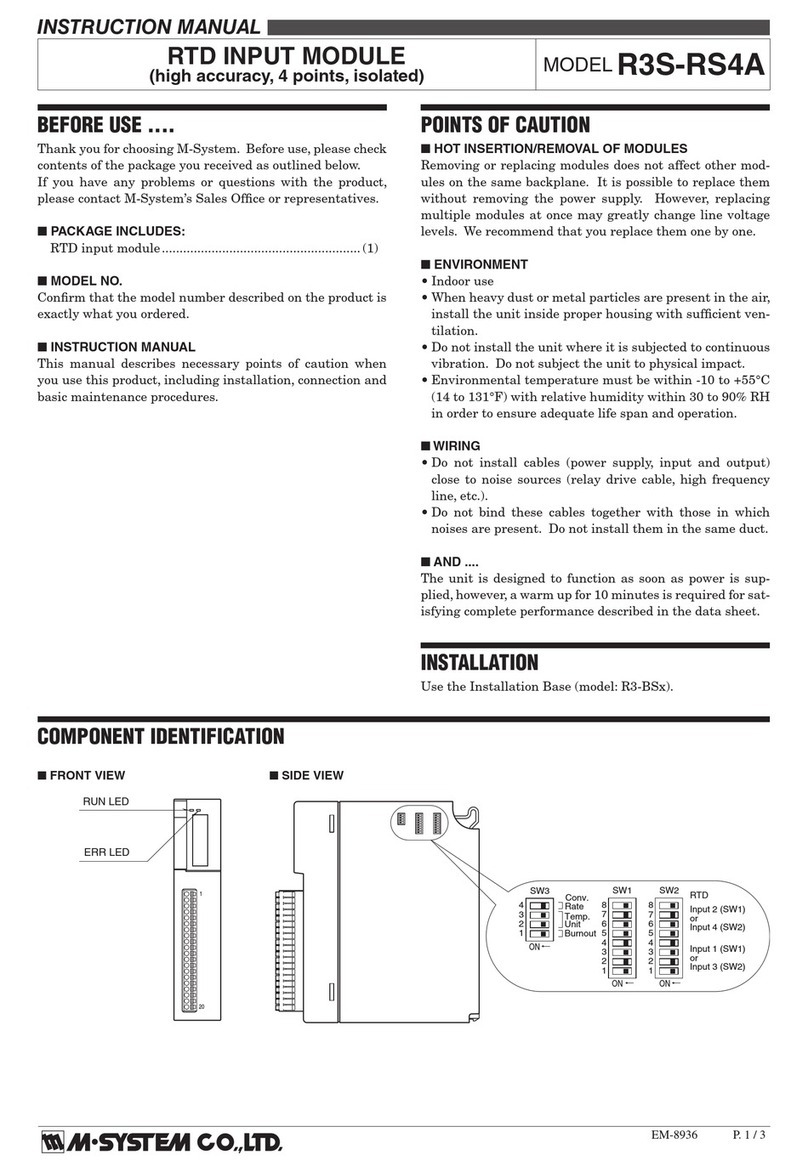
M-system
M-system R3S-RS4A instruction manual
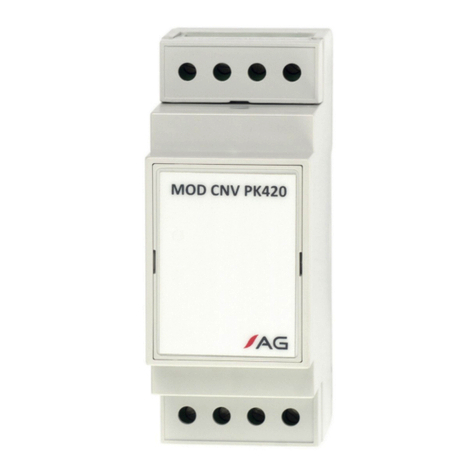
Atest Gaz
Atest Gaz MOD CNV PK420 user manual
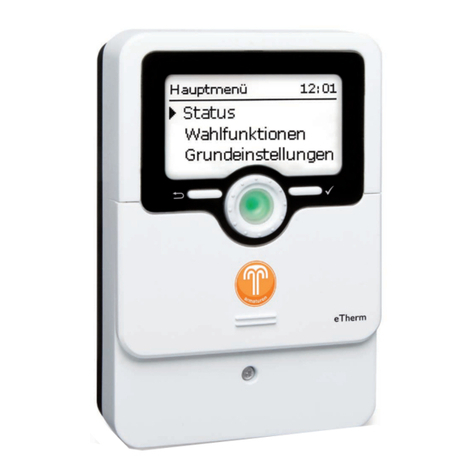
Tuxhorn
Tuxhorn tubra-eTherm manual
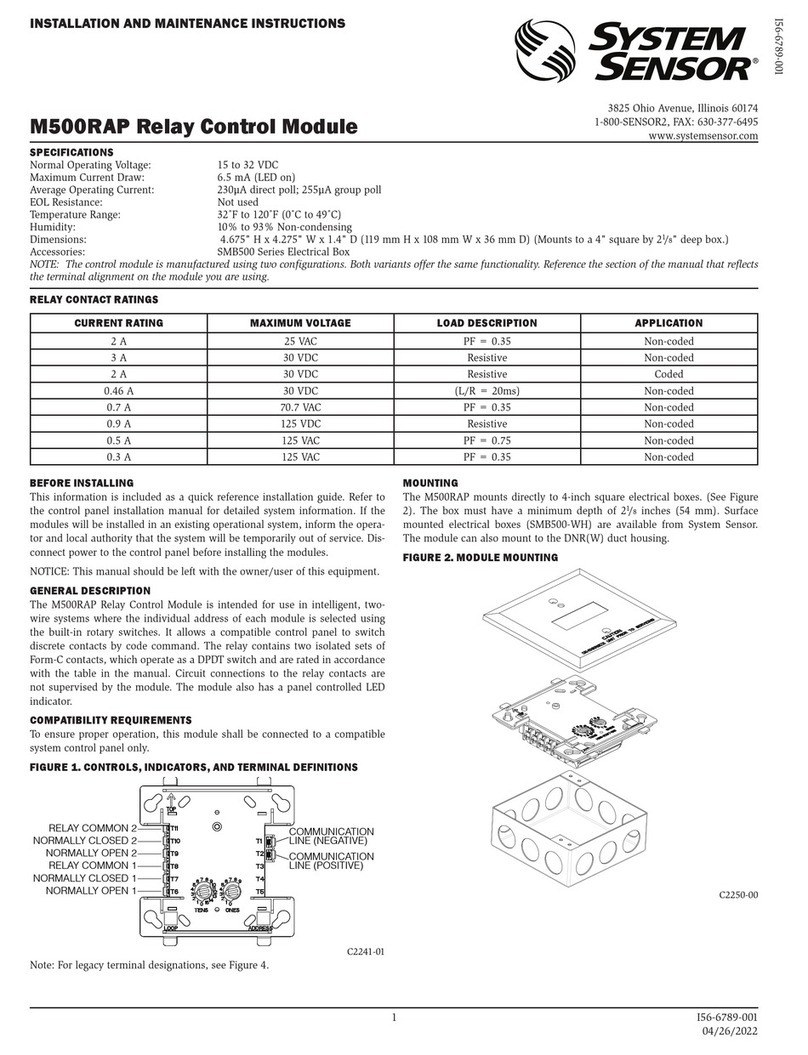
System Sensor
System Sensor M500RAP Installation and maintenance instructions

Rittal
Rittal SK 5503.010 Assembly and installation instructions