FloCat C-TJ60 Smart Series User manual

Operator's Manual for the
C-TJ60 Smart Series
Flowmeters
8 Leroy Road
PO Box 1073
Williston, VT 05495 USA
voice: 888-FLOW-888 or 802-863-0085
fax: 800-775-3179 or 802-863-1193
email: sales@flocat.com
www.flocat.com
Revision E

Warranty Agreement
FloCat warrants this product to be in good working order for a period of twelve (12) months
from installation. This warranty period will not exceed eighteen (18) months from the date
of purchase and is valid only if the enclosed warranty form is returned validating the date of
installation. If the warranty form is not received by FloCat within six months of the date of
sale, noting the date of installation, the warranty period will be 12 months from the date of
purchase.
Should this product fail to be in good working order at any time during the warranty period,
FloCat will, at its option, repair or replace it at no additional charge, except as set out below.
This warranty does not cover products damaged from accident, disaster, misuse, abuse or
unauthorized modifications. The user is responsible for determining the suitability of the
purchased product for their system application.
FloCat does not guarantee the operability of the equipment under the user’s conditions
except that it will operate according to the published specifications and without electronic or
mechanical failure. In the event of failure, proof that the operating conditions were in fact
within the specifications of the equipment and/or those submitted by the user in soliciting a
bid for the unit, as incorporated into the purchase order/contract, is upon the user/buyer.
Technical installation assistance or field repair, if practical, is available for a per diem fee.
Contact FloCat’s Customer Service Department if this assistance is desired.
Warranty service may be obtained by delivering this product to an authorized dealer along
with proof of purchase date and/or installation date. If the product is shipped to FloCat, the
buyer must obtain a Return Material Authorization (RMA) number from FloCat and send it
freight prepaid. Buyer assumes the risk of loss or damage in transit and must return it in its
original shipping container or equivalent, with adequate protection against shipping dam-
age.
All expressed warranties for this product are limited to twelve (12) months from the date of
installation, not to exceed eighteen (18) months from the date of purchase. No other warran-
ties, whether expressed or implied, except those described herein apply. If this product has
been damaged or used in a manner contrary to the instructions herein or not in accordance
with the published specifications of the equipment, Buyer’s sole remedy shall be repair or
replacement at the Buyer’s expense. In no event will FloCat be liable to Buyer for damages
arising out of the use or inability to use this product.

Receiving Inspection
Inspect the shipping package for signs of damage which may have occurred
during shipping. After removing the equipment from the package, carefully
examine it for mechanical damage. If the equipment is found to be damaged,
immediately notify both the carrier and FloCat or their representative.
DO NOT ATTEMPT
TO OPERATE ANY EQUIPMENT
WHICH HAS BEEN DAMAGED DURING SHIPPING!!!
Examine the shipping list to verify that the items listed correspond to those
ordered. If discrepancies between the equipment and the documentation are
found, immediately notify FloCat or their representative.

REVISION B
iii
TABLE OF CONTENTS
HEADING
PAGE
INTRODUCTION ......................................................................................................................
SPECIFICATIONS ....................................................................................................................
INSTALLATION ........................................................................................................................
Mechanical Installation .......................................................................................................
Installation Location ............................................................................................................
Sensor Installation ..............................................................................................................
Electrical Installation ...........................................................................................................
Flowmeter Wiring ................................................................................................................
OPERATION .............................................................................................................................
Power Terminals .................................................................................................................
Current Output ...................................................................................................................
Hart Communication ...........................................................................................................
TROUBLESHOOTING .............................................................................................................
Preliminary Checks .............................................................................................................
1
2
4
4
4
4
9
11
11
11
11
11
16
16

REVISION A
iv
LIST OF FIGURES
FIGURE TITLE PAGE
Internal Alignment of C-TJ60 Series Flowmeters ............................................
Outline Dimensions for C-TJ60 Series Flowmeters .......................................
Flowmeter Terminal Functions .......................................................................
Load Resistance Chart ..................................................................................
Sensor Wiring Diagram .................................................................................
Sensor Wiring Diagram .................................................................................
Hart Communication Menu Tree ................................................................
Hot Tap Configuration for Insertion Style .......................................................
Turbulence Caused by Bend or Obstruction .................................................
Swirl Caused by Two Bends in Different Planes and in Close Proximity to
One Another ..................................................................................................
Upstream/Downstream Sonic Noise Caused by Slightly Opened
Control Valves ...............................................................................................
Insertion Flowmeter Installed in a Reduced Pipe ..........................................
A
B1-B4
C
D
E
F
G
H-J
K
L
M
N
4
5-8
10
11
13
14
15
20
21
21
21
24

REVISION B
v
LIST OF TABLES
TABLE TITLE PAGE
1 Specifications ..................................................................................................
2-5 Flow Range Charts .........................................................................................
6 Flow Profile (Raw Data) ...................................................................................
7 Flow Profile (Normalized Data) ........................................................................
LIST OF APPENDIXES
APPENDIX TITLE PAGE
A ADDITIONAL INSTALLATION REQUIREMENTS ...........................................
Introduction ..............................................................................................
Turbulence ................................................................................................
Swirl ..........................................................................................................
Sonic Noise ...............................................................................................
Velocity Profile...........................................................................................
Straight-Run Piping Considerations ..........................................................
Temperature and Pressure Tap Locations ................................................
Wafer-Style Sensor Installation .................................................................
Insertion-Style Sensor Installation ............................................................
Fixed Insertion Flowmeter Installation ......................................................
Hot Tap Insertion Flowmeter Installation ...................................................
Flow Profiling .............................................................................................
Reducing the Pipe Diameter .....................................................................
2
3
23
23
17
17
17
17
17
17
18
18
18
18
18
19
22
22

vi
REVISION E
REVISION STATUS OF SHEETS
PAGE
iii
iv
v
vi
1
2
3
4
5
6
7
8
9
10
11
12
13
14
15
REVISION
B
A
B
E
-
B
A
-
-
A
-
A
C
B
C
B
C
C
-
PAGE
16
17
18
19
20
21
22
23
24
REVISION
-
A
A
A
A
-
-
-
A

1
REVISION
The Insertion style Flowmeters are retract-
able flowmeters that are installed through the
walls of a pipe or duct larger than four inches.
These Flowmeters can be installed through a
2-inch full port valve, which permits the unit
to be retracted or inserted manually without
shutting down the system.
NOTE: Caution should be used when
inserting or retracting at pressures exceed-
ing 60 PSIG (4.14 BAR G).
Flow rates for the Insertion style Flowme-
ters are indicated in Tables 4 and 5.
INTRODUCTION
This family of flowmeters is designed to
provide accurate and repeatable gas flow
measurement. The sensors employ a patented
ultrasonic technique to measure a form of
turbulence created in the flow stream. This
turbulence, known as the Von Karman Vor-
tex Street, is related to the flow through the
pipe.
These flowmeters are microprocessor-
based devices, with HART compatible
communication. The primary output of the
flowmeter is a 2 wire 4-20 milliampere (mA)
current which is proportional to the flow.
With the HART communications, us-
ers have the capability to remotely configure
the meter. Typical operations, like rescaling
the analog output, can be performed from a
comfortable location using a standard PC or
HART 375 Communicator.
The Wafer style Flowmeters are for pipe
diameters four inches or less, and are installed
between 150 lb. flanges, or are manufactured
with pipe extensions and 300 lb flanges welded
on the ends. These flowmeters are calibrated
in volumetric flow rates, i.e. Actual Cubic Feet
per Minute (ACFM). Flow rates for the wafer
style Flowmeters are indicated in Tables 2
and 3.
-

REVISION
2
TABLE 1
Specifications
PARAMETER Wafer-Style
GAS/AIR
Wafer-Style
STEAM
Insertion-Style
STEAM
Insertion-Style
GAS/AIR
Accuracy +1% +1%
+1% +1%
Mounting Requirements Mount between two 150 lb. flanges Mounting plate is standard 2-inch, 150lb flange
Repeatability +0.5% Reading
Input Power +15 to +24 VDC *
Output PRIMARY: 4 to 20 mA, 2 wire
Operating Pressure -5 to 250 PSIG
(-0.34 to 17 BAR G)
Operating Temperature -20oF to 360oF (-28 to 182oC) -20oF to 300oF (-28 to 148oC)
Ambient Temperature -20oF to 155oF (-28 to 68oC)
Load Limits See Figure D
SPECIFICATIONS
B
*The meter requires a minimum voltage of 21 VDC for HART communication with a 250 ohm series resistor and no load.
-5 to 125 PSIG (-0.34 to 8.6 BAR G) -5 to 250 PSIG
(-0.34 to 17 BAR G)

REVISION
3
3” (76mm)
4” (102mm)
13 (17)
23 (34)
320 (544)
480 (816)
1 1/2” (38mm)
2” (51mm)
3 (4)
5 (9)
100 (170)
160 (272)
1/2” (13mm)
1” (25mm)
0.4 (0.7)
1.3 (2)
10 (17)
35 (59)
FLOW RANGE
STEAM APPLICATION
PIPE SIZE
inch (mm) MIN MAX
3” (76mm)
4” (102mm)
10 (16)
20 (32)
400 (642)
600 (964)
1 1/2” (38mm)
2” (51mm)
2 (4)
5 (8)
100 (160)
200 (321)
1/2” (13mm)
1” (25mm)
0.4 (1)
1.2 (2)
16 (25)
45 (72)
FLOW RANGE
GAS/AIR APPLICATION
PIPE SIZE
inch (mm) MIN MAX
Flow Range is measured in
SCFM @ 14.69 PSIA, 60oF
(Nm3/HR @ 1.013 BAR, 16oC)
10” (254mm)
12” (305mm)
5 (1)
5 (1)
125 (38)
125 (38)
6” (152mm)
8” (203mm)
5(1)
5(1)
125 (38)
125 (38)
MIN MAX
FLOW RANGE
STEAM APPLICATION
PIPE
SIZE
TABLE 2
Flow Range Chart for
Wafer-Style Gas
Flowmeters
TABLE 3
Flow Range Chart for
Wafer-Style Steam
Flowmeters
Flow Range is measured in
SCFM @ 14.69 PSIA, 60oF
(Nm3/HR @ 1.013 BAR, 16oC)
8” (203mm)
10” (254mm)
2(0.6)
2(0.6)
140(43)
140(43)
4” (102mm)
6” (152mm)
2(0.6)
2(0.6)
140(43)
140(43)
MIN MAX
FLOW RANGE
GAS/AIR APPLICATION
PIPE
SIZE
Flow Range is measured in
Feet Per Second @ 14.69 PSIA, 60oF
(Meter Per Second @ 1.013 BAR, 16oC)
TABLE 4
Flow Range Chart for
Insertion-Style Gas
Flowmeters
TABLE 5
Flow Range Chart for
Insertion-Style Steam
Flowmeters
* NOTES FOR TABLE 5:
When pressure is 0 to 25 PSIG, the range is 5 to 125 FPS (1 to 38 MPS).
When pressure is 25 to 60 PSIG, the range is 5 to 158 FPS (1 to 48 MPS).
When pressure is greater than 60 PSIG, the flow range is 5 to 175 FPS (1 to
53 MPS).
Flow Range is measured in
Feet Per Second @ 14.69 PSIA, 60oF
(Meter Per Second @ 1.013 BAR, 16oC)
A

REVISION
4
CORRECT
(METER CENTERED IN PIPE)
INCORRECT
(METER NOT CENTERED IN PIPE)
FIGURE A
Internal Alignment of flowmeter
If these ultrasonic noise sources cannot
be eliminated, the meter should be mounted
with at least one elbow between the flowmeter
and the noise source.
The sensor should be installed with at least
20 pipe diameters of straight pipe upstream
and 10 pipe diameters downstream. This
condition provides a fully developed, sym-
metrical flow profile that is necessary to obtain
accurate and repeatable results. Shorter
upstream/downstream piping may be used
although a shift in calibration may occur. If
severe turbulence or distorted flow profiles are
present, flow straighteners should be used.
Consult FloCat for shorter upstream/down-
stream configurations. See Appendix C for
additional installation information.
Sensor Installation
The wafer-style flowmeters are designed
to mount between two ANSI 150 lb. flanges.
The flowmeter should be mounted so its inside
diameter is centered inside the pipe (see Fig-
ure A below). The labeling of the flow direction
on the flowmeter should be aligned with the
flow in the pipe. If liquids or condensation can
be present in the flow, the sensor should be
installed so that liquids will not accumulate on
the ultrasonic transducers (the small buttons
on either side of the vortex strut).
INSTALLATION
Mechanical Installation
The flowmeter has been shipped com-
pletely assembled, tested and ready to install
and operate in its permanent location. See
Figures B1 thru B4 for the applicable outline
dimensions for the flowmeter.
Installation Location
These flowmeters use a patented ultrasonic
technique to measure flow. An ultrasonic noise
can interfere with this technique, therefore high
intensity ultrasonic noise sources should not
be located upstream or downstream from the
sensor. Common ultrasonic noise sources
include the following:
1. Slightly cracked valves operating with large
pressure drops.
2. Small pipe leaks in high pressure sys-
tems.
3. Venturies operating at near-sonic flow
rates.
4. Sonic nozzles.
-

REVISION
5
FIGURE B1
Outline Dimensions for Wafer-Style Flowmeters
0.50 (12.69)
4.72 (119.80)
3.97 (100.76) 0.88 (22.34) 5.78 (146.70) 9.65 (245.11)
1.38 (35.03) 6.34 (160.91) 10.21 (259.33)
3.50 (88.83) 5.60 (142.13) 9.47 (240.53) 2.38 (60.41) 2.25 (57.11)
3.12 (79.19) 2.12 (53.81)
3.88 (98.48) 2.12 (53.81)
1.38 (35.03)
2.00 (50.76)
2.88 (73.10)
GAS/AIR STEAM
DIM C
DIA
A
DIA
B
DIM
D
DIM
E
DIM
F
5.22 (132.49) 2.75 (69.80) 6.62 (168.02) 10.49 (266.44)
11.39 (289.30)
3.97 (100.76) 1.75 (44.42) 5.92 (150.25) 9.79 (248.66)
7.52 (190.86)3.75 (95.18)6.87 (174.37)
4.55 (115.60)
3.15 (80.00)
6.19 (157.20)
GAS/AIR STEAM
DIM C
DIA
A
DIA
B
DIA
D
All dimensions are in inches (mm)
All dimensions are in inches (mm)
-

REVISION
6
FIGURE B2
Outline Dimensions
9.88 - 10.00 (250 - 254)
9.88 -10.00 (250 - 254) 5.78 (146.70) 9.65 (245.11)
9.88 -10.00 (250 - 254) 6.34 (160.91) 10.21 (259.33)
5.60 (142.13) 9.47 (240.53)
GAS/AIR STEAM
DIM A
DIM B
11.88 - 12.00 (301 - 304) 6.62 (168.02) 10.49 (266.44)
11.39 (289.30)
9.88 -10.00 (250 - 254) 5.92 (150.25) 9.79 (248.66)
7.52 (190.86)11.88 - 12.00 (301 - 304)
All dimensions are in inches (mm)
A
B
4.50
5.75
4.69
A
3/4-14 NPT

REVISION
7
FIGURE B3
Outline Dimensions for Insertion-Style Steam Flowmeters
All dimensions are in inches (mm)
24.00 (609.14)
36.00 (913.71)
12.00 (304.57)
27.0 (685.28) 33.5 (850.25)
15.0 (380.71) 21.5 (545.69)
45.5 (1154.82)39.0 (989.85)
48.00 (1218.27) 51.0 (1294.42) 57.5 (1459.39)
DIM
A
DIM
B
DIM
C
-

REVISION
8
33.50 (850.9)
21.50 (546.1)
24.88 (631.95)
12.88 (327.15)
24.00 (609.14)
12.00 (304.57)
All dimensions are in inches (mm)
DIM
A
DIM
B
DIM
C
FIGURE B4
Outline Dimensions for Insertion-Style Gas Flowmeters
36.00 (913.71) 36.88 (936.75) 45.50 (1155.7)
57.50 (1460.5)
69.50 (1765.3)60.88 (1546.35)
48.88 (1241.55)48.00 (1218.27)
60.00 (1524)
A

REVISION
9
Sensor Installation (continued)
Gaskets (not provided) are necessary between
the sensor and the ANSI flanges. Insure that
these gaskets are properly installed and do
not protrude into the flow stream.
CAUTION: Avoid bending the vortex strut
or damaging the transducers during installa-
tion. Do not remove cover plates while unit
is operating in the system.
The Insertion-Style Flowmeters are de-
signed to mount on a standard ANSI 150 lb.,
2-inch pipe flange. The measuring window
should be installed in the center of the line
for line sizes 12 inches or less. For line sizes
larger than 12 inches, the measuring window
should be installed 25% to 50% of the way
into the pipe. It is recommended that the
internal dimensions of the line be measured
for accurate readings.
The labeling of the flow direction on the
sensor should be aligned with the flow in the
pipe. If liquids or condensation can be present
in the flow, the sensor should be installed so
that liquids will not accumulate on the ultra-
sonic transducers (the small buttons on either
side of the vortex strut).
Insertions can be used in any size pipe
larger than three or four inches in diameter.
In order to calculate accurate volumetric,
mass, and standard flow measurements, it
is recommended to enter the exact pipe size
into the meter. Normally this operation, along
with overall meter configuration, is performed
at the factory. However, the user can enter
the pipe diameter on site using TecView or a
Hart 375 communicator.
NOTE: The torque requirement for the conax
fitting is 90-100 ft. lbs. (see Figure B3 & B4).
See Appendix A for additional installation
information and flow profiling.
The Wafer-Style Flowmeters are designed
to mount between two ANSI 300 lb flanges
(see Figure B2). The labeling of the flow
direction on the flowmeter should be aligned
with the flow in the pipe.
Gaskets (not provided) are necessary
between the ANSI flanges. Insure that these
gaskets are properly installed and do not
protrude into the flow stream.
Electrical Installation
Electrical connections for the flowmeter
are made using screw-type terminals located
inside the enclosure. To access these termi-
nals, remove the lid from the enclosure. The
function of these terminals are illustrated in
Figure C. To install the cable in the flowmeter,
route the cable through the cable entry located
on either side of the enclosure. Attach the
wires to the appropriate terminals.
It is recommended a wire be attached
from the external flowmeter ground terminal
to chassis ground, if the pipe is not connected
to chassis ground.
C

REVISION
10
B
TERMINAL
DESIGNATOR FUNCTION
4-20MA -
EP RTN
EP PWR
EP OUT
EP IN
4-20MA +
NC
POWER OUT TO PRESSURE SENSOR
PRESSURE SENSOR POWER
PRESSURE SENSOR INPUT
PRESSURE SENSOR
POWER SUPPLY RETURN
not used
LOOP POWER (+15-24 VDC)
LOOP POWER (-)
FIGURE C
Flowmeter Terminal Functions
CHASSIS GROUND
CABLE SHIELD
GROUND
4-20MA
EP RTN
EP PWR
EP OUT
EP IN
NC

REVISION
11
Flowmeter Wiring
A two conductor foil shielded cable made
of 14 to 22 AWG solid or stranded wire is re-
quired to make connections to the flowmeter
(e.g. Consolidated Wire P/N 5573-CL).
The shield is required to be attached to the
chassis ground points as illustrated in Figure
C.
The flowmeter requires a minimum of +15
VDC for proper operation. The maximum load
resistance for the power depends on the sup-
ply voltage (see Figure D).
The external pressure sensor and external
RTD are limited to a 5 foot cable length.
Various wiring configurations are shown
in Figures E & F.
OPERATION
Power Terminals
The 4-20MA terminals (“+” and “-”) are
used for the flowmeter’s power supply. This
power supply should be +15 to +24 VDC.
Current Output
Current Output is realized through the 4-
20MA “+” and “-” terminal loop and provides
an output current proportional to the flow
measured by the flowmeter. This output is a
standard 4 to 20 mA output, where 4 mA cor-
responds to no flow and 20 mA indicates 100
percent (full scale) flow. The current output
will not be accurate if the load resistance on
the current output terminal is too high. The
maximum load resistance that the meter can
drive versus the power supply voltage is shown
in Figure D. The formula to determine load
resistance is:
RL = 46Vs - 690
where: RL is load resistance
Vs is supply voltage
MAXIMUM LOAD
RESISTANCE (OHMS)
POWER SUPPLY VOLTAGE (VDC)
C
FIGURE D
The value of the resistor can range from 250 to
350 ohms and rated at 1/4 watt or larger. The
placement of the resistor is illustrated in the wir-
ing diagrams. The resistor will add to the total
loop resistance and will raise the value of the
required power supply voltage. With a resis-
tor in place, a maximum of 24 VDC supply is
recommended. This power supply voltage will
accommodate 164 ohms of loop resistance in
addition to a 250 ohm communication resistor.
For high loop resistance, consult Figure D for
the required supply voltage.
MAX LOAD resistance with 250Ω
resistor installed for HART communication
MAX LOAD resistance w/out 250Ω HART resistor
HART Communication
This Smart meter has the capability of HART
communication. However, it is not required that
one use it. In most cases, the meter is configured
at the factory per the customer’s specifications.
The user need only install the meter and connect
power.
If HART communication is desired, it is
required that a resistor be placed in the current
loop.
16
020 24
100
450
250

REVISION
12
This program will provide access to all the
settings that can be configured by the customer.
It also provides tools for diagnositcs and trim-
ming the analog output.
TecView requires a HART modem to con-
vert the HART modulation to the RS-232 com-
munication standard. See the TecView User’s
Manual for more information about TecView.
The HART 375 Communicator is a hand-
held device that can communicate with any
HART device that is registered with HART
Communication Foundation. The HART 375
Communicator also provides access to all set-
tings that can be configured by the customer.
The 375 provides a menu driven interface. See
Figure G to view the menu map for the HART
375 Communicator.
There are two ways to communicate to the
meter via the HART interface: TecView and
HART 375 Communicator. TecView is a PC
based software program that runs on Windows
98, NT, ME, and XP.
B

REVISION
13
C
FIGURE E
FLOW
INDICATOR
- OR -
CONTROL
SYSTEM
FLOW
INDICATOR
- OR -
CONTROL
SYSTEM
+
-
+
+-
-
SUPPLY
POWER
15 - 24 VDC
-
+FLOW
INDICATOR
- OR -
CONTROL
SYSTEM
SYSTEM
CONTROL
- OR -
INDICATOR
FLOW
-+
HART
HART
-
+FLOW
INDICATOR
- OR -
CONTROL
SYSTEM
SYSTEM
CONTROL
- OR -
INDICATOR
FLOW
-+
250 OHM
250 OHM
24 VDC
SUPPLY
-
+
POWER
24 VDC
SUPPLY
-
+
POWER
4-20MA +
4-20MA -
EP RTN
EP PWR
EP OUT
EP IN
NC
4-20MA +
4-20MA -
EP RTN
EP PWR
EP OUT
EP IN
NC
4-20MA +
4-20MA -
EP RTN
EP PWR
EP OUT
EP IN
NC
WIRING DIAGRAM
The wiring diagrams illustrated below are for installations where no 4-20mA pressure sensor is used.
Table of contents
Popular Measuring Instrument manuals by other brands
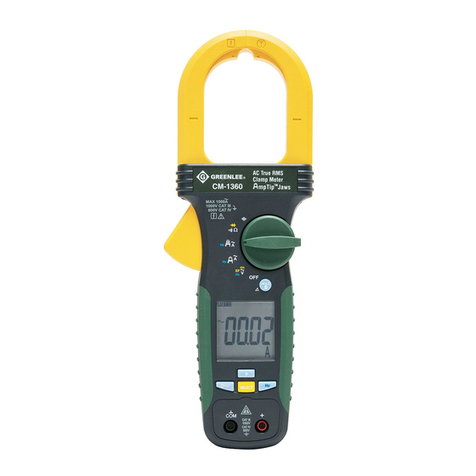
Textron
Textron Greenlee CM-1360 instruction manual
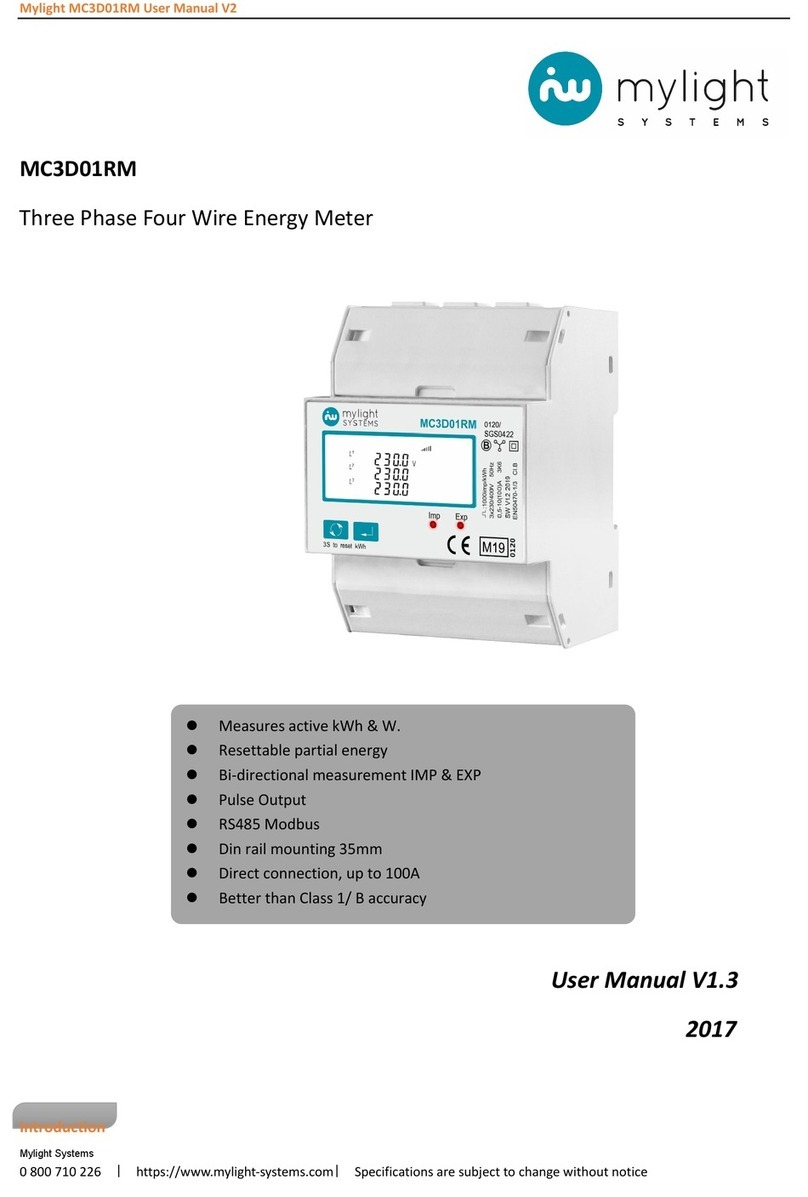
MyLight
MyLight MC3D01RM user manual

Bosch
Bosch GLM 50 C Operating/safety instructions
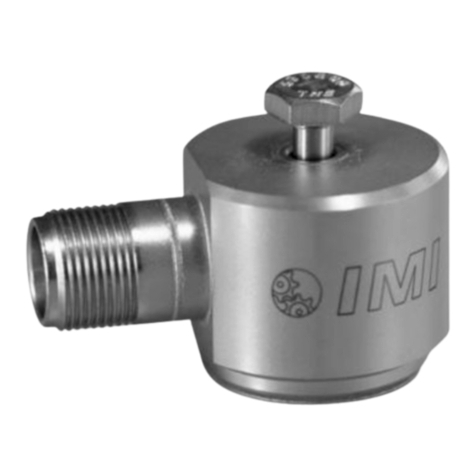
PCB Piezotronics
PCB Piezotronics IMI SENSORS M624B01 Installation and operating manual
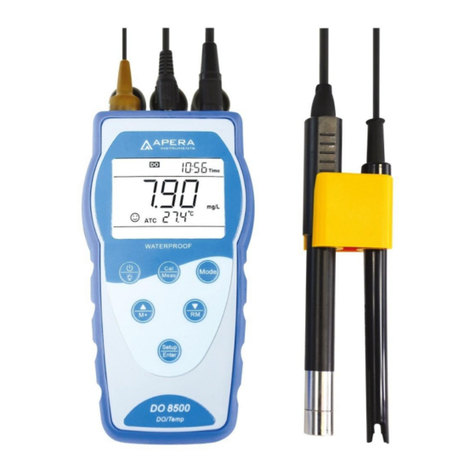
Apera Instruments
Apera Instruments DO8500 instruction manual
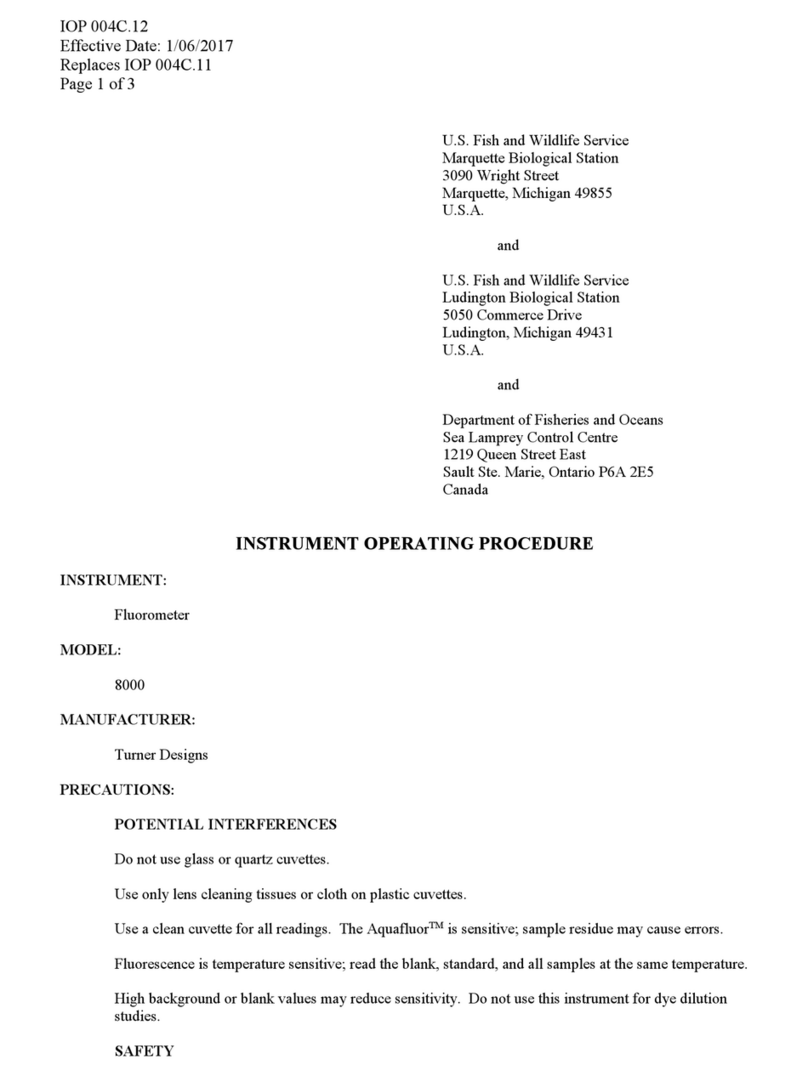
Turner Designs
Turner Designs 8000 Operating procedure
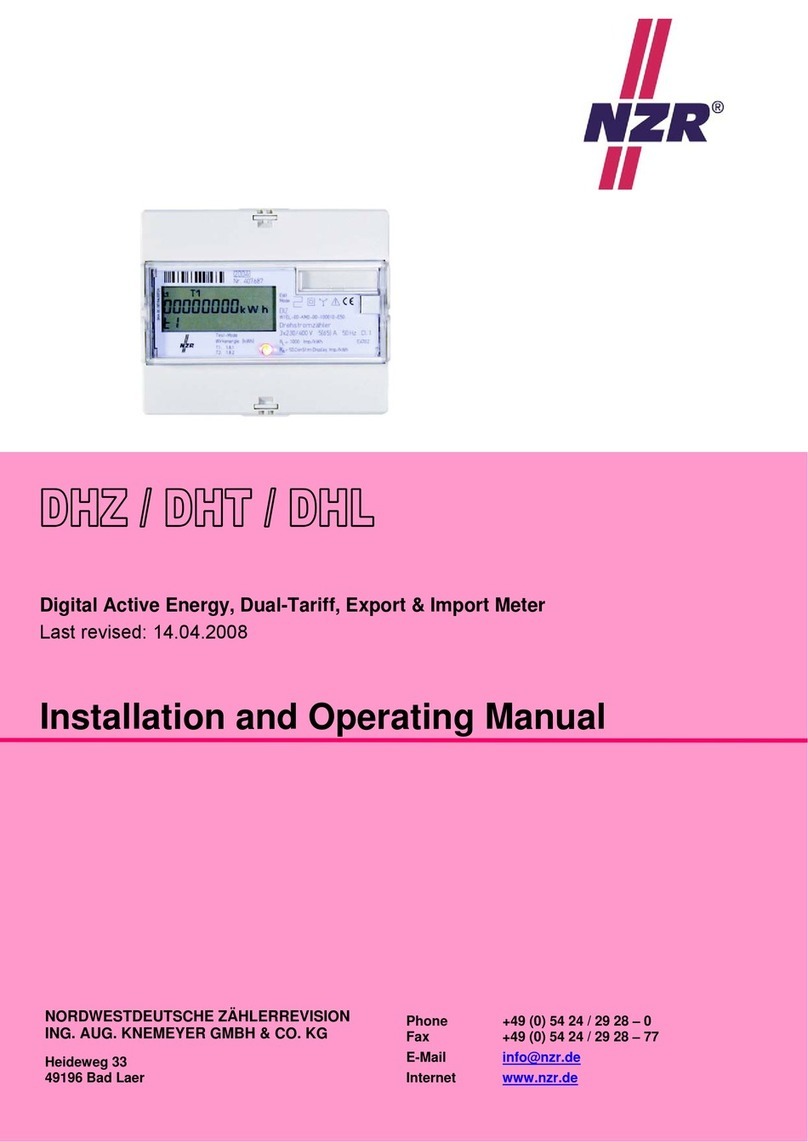
NZR
NZR DHZ Series Installation and operating manual
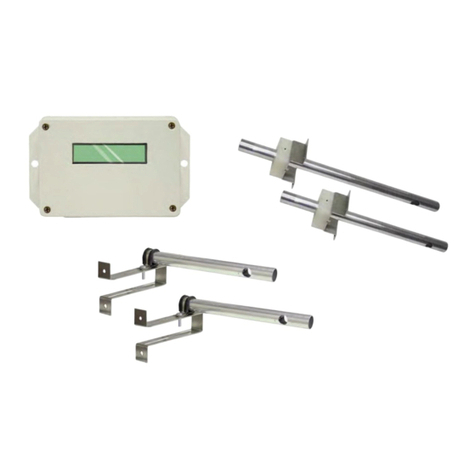
Greentrol Automation
Greentrol Automation GreenFlow 2000 Series Installation, Operation and Maintenance Technical Manual
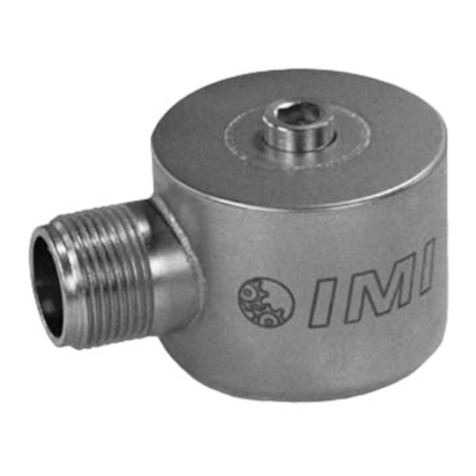
PCB Piezotronics
PCB Piezotronics IMI SENSORS 606B01/ICS-14 Installation and operating manual
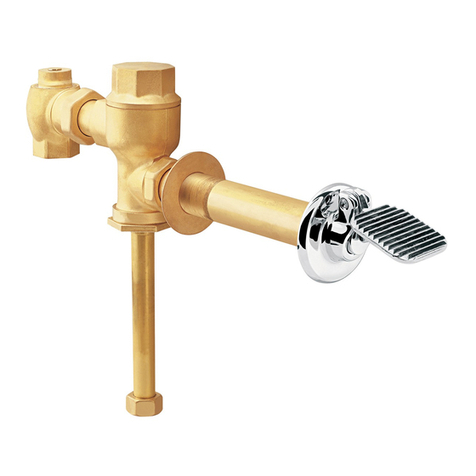
Helvex
Helvex 323-19-1 installation guide
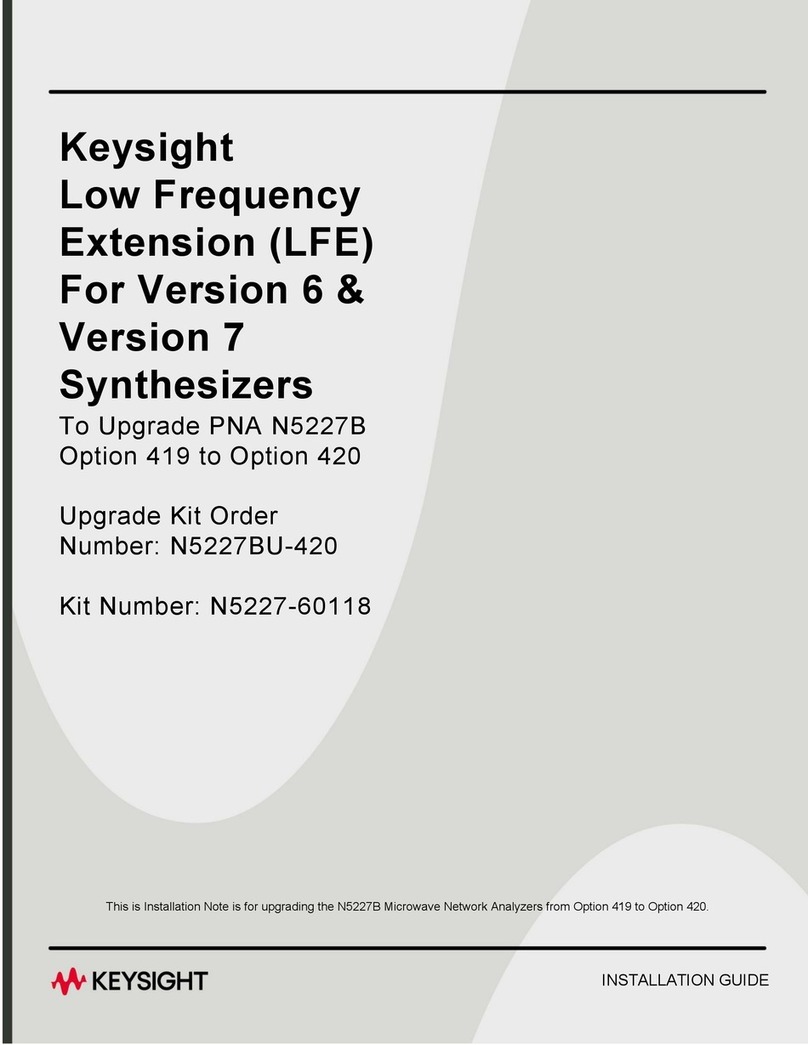
Keysight
Keysight N5227BU-420 manual

SATO KEIRYOKI
SATO KEIRYOKI SK-660PH Series instruction manual