FMA Direct Super 30 User manual

4
060727
FMA limited warranty
FMA, Inc. warrants this product to be free of manufacturing defects for the term of 90 days from the date of pur-
chase. Should any defects covered by this warranty occur, the product shall be repaired or replaced with a unit of
equal performance by FMA or an authorized FMA service station.
Limits and exclusions
This warranty may be enforced only by the original purchaser, who uses this product in its original condition as
purchased, in strict accordance with the product’s instructions. Units returned for warranty service to an FMA
service center will be accepted for service when shipped postpaid, with a copy of the original sales receipt or war-
ranty registration form, to the service station designated by FMA.
This warranty does not apply to:
Consequential or incidental losses resulting from the use of this product.
Damage resulting from accident, misuse, abuse, neglect, electrical surges, reversed polarity on connectors,
lightning or other acts of God.
Damage from failure to follow instructions supplied with the product.
Damage occurring during shipment of the product either to the customer or from the customer for service
(claims must be presented to the carrier).
Damage resulting from repair, adjustment, or any alteration of the product by anyone other than an authorized
FMA technician.
Installation or removal charges, or damage caused by improper installation or removal.
Call (301) 668-7614 for more information about service and warranty repairs.
Tips for using the ESC
If you store throttle corrections as described in step 1 at the bottom of page 2, then you don’t have to repeat
the procedure before each ight. The ESC is ready to go (using stored EPAs) when you turn it on, and the mo-
tor will turn as soon as you move the throttle stick away from the off position.
If you fast-charge your battery pack, wait at least 5 minutes before using it to power the ESC. This assures the
ESC can properly determine the number of cells in the pack.
After you connect your charged battery pack to the ESC and turn power on, wait about 3 seconds before ad-
vancing the throttle. This gives the ESC time to accurately determine the number of cells in the battery pack.
If the motor cuts off in ight:
1. Move throttle stick to off.
2. Move throttle stick back up.
If the battery pack is in good condition, the ESC should provide 2 restarts.
Super 30 ESC cell detect and auto low voltage cutoff specs
For initial voltage Pack type/size* is assumed to be And cutoff voltage (when enabled) is
5.30 to 7.15 V NiCd/NiMH, 5 cells 5.3 ±0.1 V
7.16 to 8.55 V NiCd/NiMH, 6 cells; or LiPo, 2 cells 5.3 ±0.1 V
8.56 to 9.95 V NiCd/NiMH, 7 cells 5.4 ±0.1 V
9.96 to 11.20 V NiCd/NiMH, 8 cells 7.5 ±0.1 V
11.21 to 12.45 V NiCd/NiMH, 9 cells; or LiPo, 3 cells 8.4 ±0.1 V
12.46 to 14.50 V NiCd/NiMH, 10 cells 10.0 ±0.1 V
14.51 to 16.05 V NiCd/NiMH, 11 cells 10.3 ±0.1 V
16.06 up NiCd/NiMH, 12 cells; or LiPo, 4 cells 11.0 ±0.1 V
*number of cells connected in series
Super 30 ESC specications
Model ASC30
Functions Proportional throttle, throttle end point adjustment
(EPA), brake, battery eliminator circuit (BEC), low
voltage cutoff (LVC, both automatic and custom
voltage), restart
Input 2 to 4 Lithium Polymer cells in series,
or 5 to 12 NiCd/NiMH cells in series (LVC enabled),
or 3 to 12 NiCd/NiMH cells (LVC disabled)
Input operating voltage 2.1 to 18 VDC
Motor support 1 DC motor, up to 30Acurrent draw
(does not support brushless motors)
Frequency 1.5 kHz
Continuous output current 30A
Peak output current 400 A (FET rating)
Internal resistance 2.75 milliohm
BEC output 5.0 ±0.5 VDC at 1A maximum
Dimensions 1.35" x 0.75" x 0.40"
(34.3mm x 19mm x 10.2mm)
FMA, Inc.
5716A Industry Lane
Frederick, MD 21704
Sales: (800) 343-2934
Technical: (301) 668-7614
www.fmadirect.com
Super 30 Auto Cell Detect
Electronic Speed Control
Model ASC30 for electric-powered aircraft using
Lithium Polymer, NiCd or NiMH battery packs
Features
Works with NiCd, NiMH and Lithium Polymer (LiPo) packs.
User switchable brake.
Two user switchable Low Voltage Cutoff (LVC) options. Auto LVC, when enabled, automati-
cally cuts off motor at minimum voltage calculated from initial battery pack voltage. Custom
LVC, when enabled, automatically cuts off motor at a minimum voltage you set.
Throttle End Point Adjustment (EPA) for better tracking from throttle stick to motor speed.
Battery Eliminator Circuit (BEC) powers receiver from motor battery.
Heavy-duty diode reduces electrical noise.
Note: When using LiPo batteries in fuel-powered models, use an FMA voltage regula-
tor/LED indicator, such as the Sport VRLI.
Cellpro Lithium Polymer packs are the next-generation replacement for NiCd, NiMH and Lith-
ium Ion packs. This unique power technology offers high energy density, low weight, long life,
safe operation and environmentally-friendly chemistry. Order Cellpro packs through the FMA
Direct Web site, www.fmadirect.com. LiPo technical and application information is available in
the Support section of the Web site.
Precautions
Follow all instructions in this manual to assure safe operation.
Observe frequency control. If someone else is operating a radio controlled model on the same
channel as your transmitter, do not turn on your transmitter—even for a short time. Your
transmitter has a channel number marked somewhere on its case. When a model receives sig-
nals from two transmitters on the same channel at the same time, it cannot be controlled and
will crash—possibly causing personal injury or property damage. For safety, most RC ying
elds have formal frequency control rules. Follow them carefully.
Donotoperateyourradiocontroltransmitterwithin3milesofayingeld.Evenatadis-
tance, your transmitter can cause interference.
MakesureyourLiPopacksarenotfullydischargedwhenyourstconnectthemtotheESC
and apply power. The ESC sets its Auto Low Voltage Cutoff by measuring initial pack volt-
age. If the LiPo pack voltage is too low, the Auto Low Voltage Cutoff may be set too low, and
cells could be over-discharged. Charge state is less critical for NiCd/NiMH packs, but it’s
always a good idea to start with a freshly charged pack.
The Super 30 ESC works with packs of 5 to 12 NiCd/NiMH or 2 to 4 LiPo cells in series. If
Auto Low Voltage Cutoff is disabled, the ESC supports packs with 3 to 4 NiCd/NiMH cells in
series (however, your receiver/servos may stop operating at the lower voltage near the end of
a run). Never disable the Low Voltage Cutoff when using the ESC with LiPo packs.

2 3
Installing the ESC
You must supply:
Batteryconnectorratedforexpectedcurrentow(upto
30A) from battery pack. Recommended: Deans Ultra
or Sermos connector. Don’t use a servo connector, as it
can’t handle the high current.
3 0.01µF capacitors (FMA No. C0.01UFPOLY).
Optional: 30A fuse and inline fuse holder.
1. Cut a small opening in ESC cover so you can set
switches.
2. Optional: Cut red and black battery wires, and/or blue
and white motor wires, to a length appropriate for your
installation.
3. Optional: Cut white ( + ) wire and solder in fuse
holder. Insert fuse into fuse holder.
4. Solder red ( + ) wire to battery connector positive ter-
minal.
5. Solder black ( – ) wire to battery connector negative
terminal.
Note: Double-check battery connector polarity.
Damage caused by reversing battery polarity is
not covered by the warranty!
6. Insert blue wire into motor’s negative ( – ) terminal.
7. Insert white wire into motor’s positive ( + ) terminal.
8. Insert capacitors as shown at right: one between motor
terminals and one from each terminal to the motor can.
9. Solder wires and capacitors to terminals, and solder
capacitors to motor can.
10. Attach servo connector to throttle channel on receiver
(observe polarity!).
11. Set on/off switch to off position.
12. Attach battery connector to battery pack.
Setting up the ESC
1. Throttle End Point Adjustment (EPA) provides better tracking between throttle stick posi-
tion and actual motor speed. With EPA correctly set, the motor is off when the throttle stick is
all the way down, and reaches maximum speed when the throttle is all the way up.
Tip: The ESC doesn’t care whether the throttle channel is reversed or not. EPA as-
sumes the initial throttle stick position (normally all the way down) is “motor off.”
To set up EPA:
a. Set transmitter’s throttle to 100%, and center throttle trim.
b. With the ESC off, set Switch 3 on (see diagram on page 3).
c. Move your transmitter’s throttle stick all the way down.
d. Turn on your transmitter, then turn on the ESC/receiver. The motor will not rotate until
step d is complete.
e. Wait 3 seconds for the ESC to determine the number of cells in the pack.
f. Move the throttle stick all the way up (or to the desired position for maximum motor speed)
and hold it there for at least 3 seconds. Then move the throttle stick all the way down.
CAUTION: The motor is now active and will rotate if you move the throttle stick up.
Solder red and blackwires to
batteryconnector (not supplied)
Black wireRed wire+ –
Blue wireWhite wire
+–
Motor
Attachto
receiver
throttle
channel
On/off
switch
Switches
(seetext)
SUPER
ESC
Capacitor
( – to can)
Capacitor
( + to can)
continued
g. Test throttle operation: Hold the aircraft securely and clear of the propeller, then move the
throttle stick full up. The motor should turn at maximum RPM. Move the throttle stick all
the way down to turn off the motor.
h. Store EPA settings: Set Switch 3 off. The settings are now stored and will be available for
futureights.
If you forget to set switch 3 to off in step h above, you will have to repeat the EPA
setup each time you cycle power on the ESC.
Because the ESC is optimized for your throttle, there will be very little deadband
when throttle is off (moving the throttle stick just a little causes instant response). If
the motor turns unexpectedly when throttle is off, reduce throttle trim slightly.
2. Low Voltage Cutoff (LVC) turns off the motor when battery voltage gets low. This enables
the battery to maintain radio system functions for a short time—enough time to glide the
aircraft to landing. Low voltage cutoff also prevents cell damage from deep discharge. Two
LVC options are provided. With Auto Low Voltage Cutoff, the ESC automatically deter-
mines the cutoff voltage based on initial pack voltage. With Custom Low Voltage Cutoff,
you set the voltage at which cutoff occurs. You must enable low voltage cutoff when using
LiPo batteries, which can be permanently damaged by low voltage conditions.
To enable Auto Low Voltage Cutoff: set Switch 2 on.
or
To disable Auto Low Voltage Cutoff: set Switch 2 off.
To enable and set Custom Low Voltage Cutoff:
Note: The ESC can be used with 3 or 4 cell NiCd/NiMH packs when Auto Low Voltage
Cutoff is disabled. CAUTION: If you disable ALVC, the ESC cannot safeguard against
depleting the battery to the point where you won’t be able to control the aircraft.
Tip: For safety, have another person help you with this procedure.
a. With the ESC off, set Switch 2 off.
b. Connect a partially discharged battery pack. (Pack can be fully charged, but it will take
longer to reach the target cutoff voltage).
c. Connect a voltmeter between battery + and – .
b. Move your transmitter’s throttle stick all the way down.
d. Turn on your transmitter. Hold the aircraft securely and clear of the propeller, then move
the throttle stick full up.
e. Watch the voltmeter. When the voltage drops to the desired cutoff point, carefully set
Switch 2 on. This sets the cutoff voltage and turns the motor off.
The ESC will use this cutoff voltage until you repeat the above procedure, or you disable Cus-
tom Low Voltage Cutoff.
To disable Custom Low Voltage Cutoff and enable Auto Low Voltage Cutoff:
a. Move your transmitter’s throttle stick all the way down.
b. Turn on your transmitter.
c. Set Switch 2 off.
d. Turn the ESC on. Don’t move the throttle stick.
e. Set Switch 2 on.
f. Turn off the ESC.
g. Turn off your transmitter.
3. The Brake stops motor rotation when the throttle is off and when the Low
Voltage Cutoff (see step 2, above) cuts power to the motor. Braking is often
used when the aircraft is equipped with a folding propeller.
To enable the brake: set Switch 1 on.
or
To disable the brake: set Switch 1 off.
ON
1 2 3 4
This manual suits for next models
1
Popular Controllers manuals by other brands
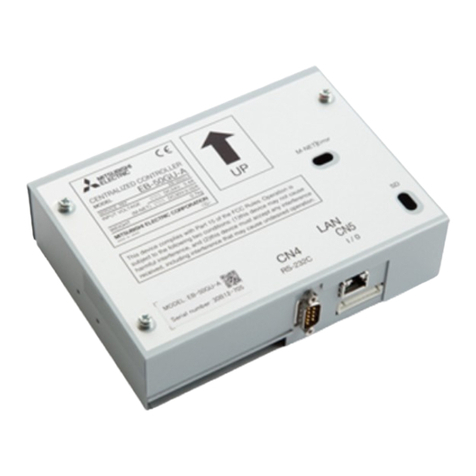
Mitsubishi Electric
Mitsubishi Electric EB-50GU-A Operation manuals
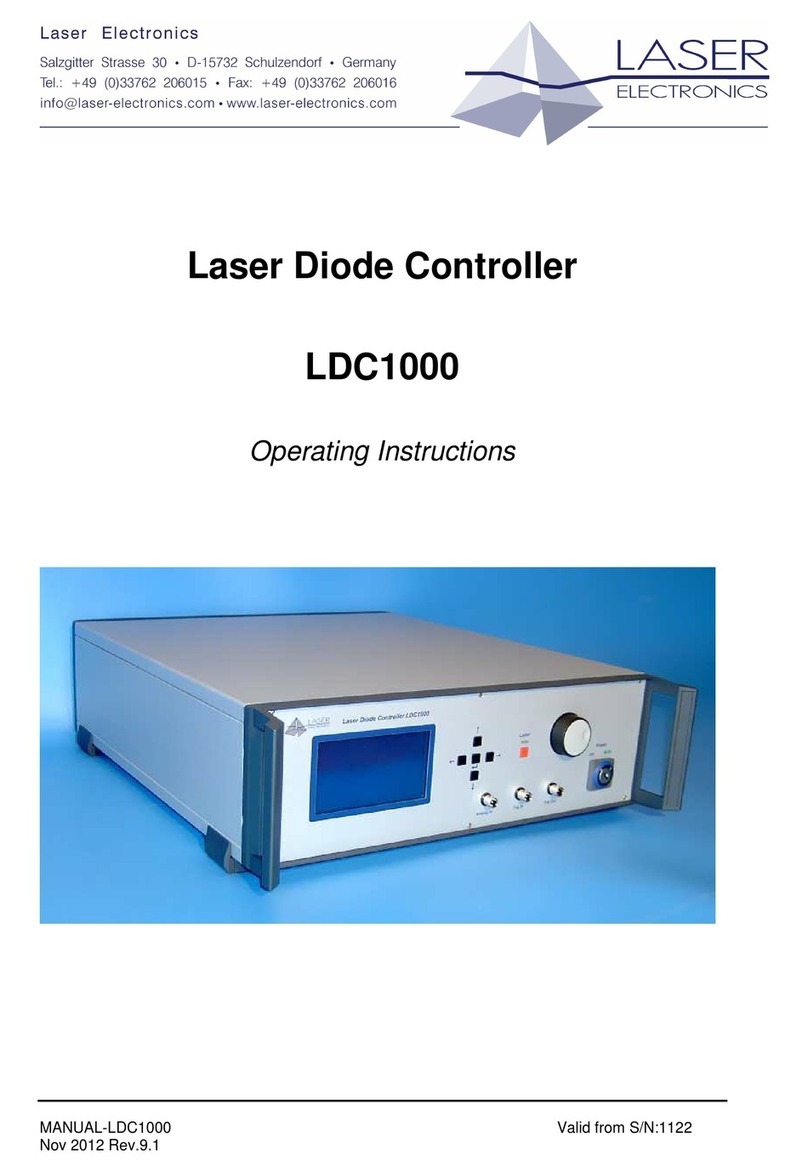
Laser electronics
Laser electronics ldc1000 operating instructions
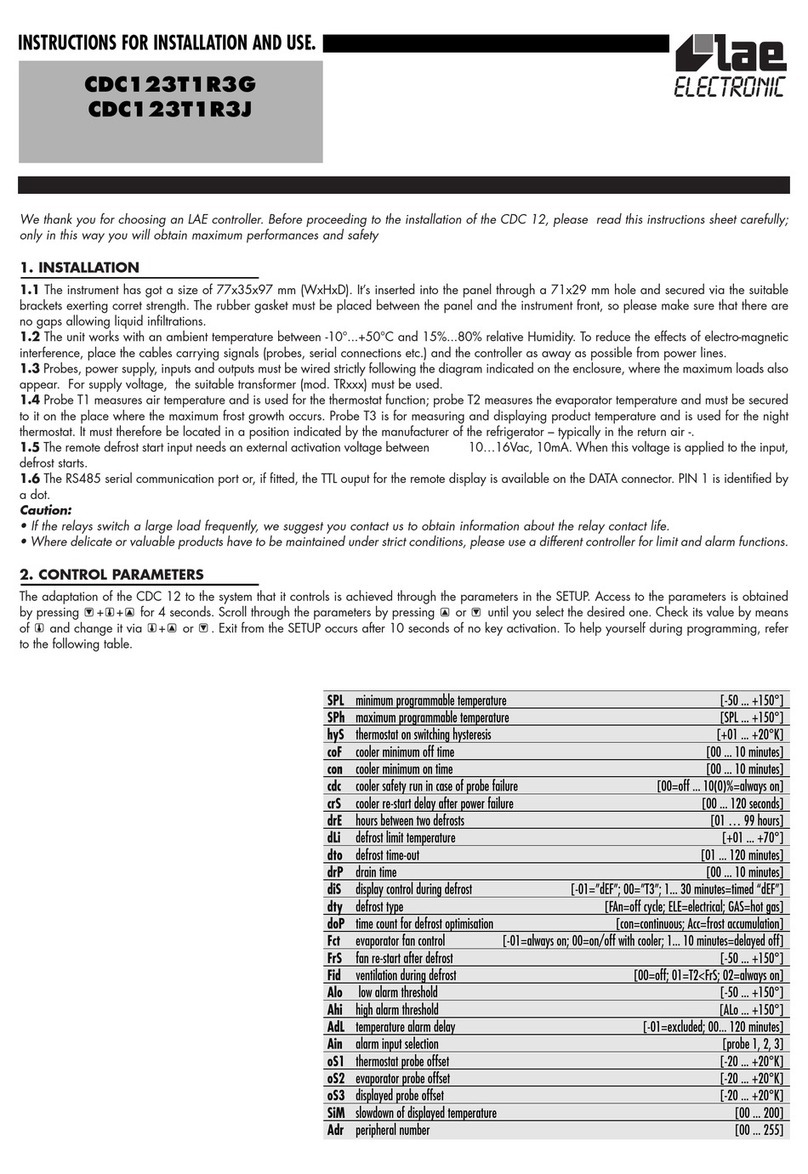
LAE electronic
LAE electronic CDC123T1R3G Instructions for installation and use
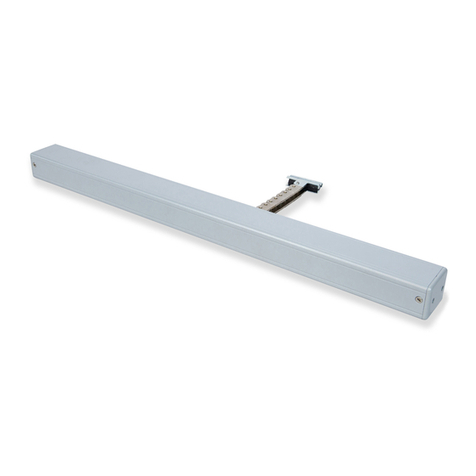
SE Controls
SE Controls Seco Ni 40 Technical information and operating instructions
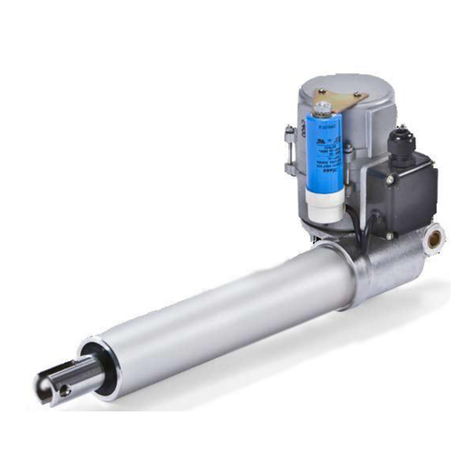
SKF
SKF Magforce DSP Series Installation, operation and maintenance manual
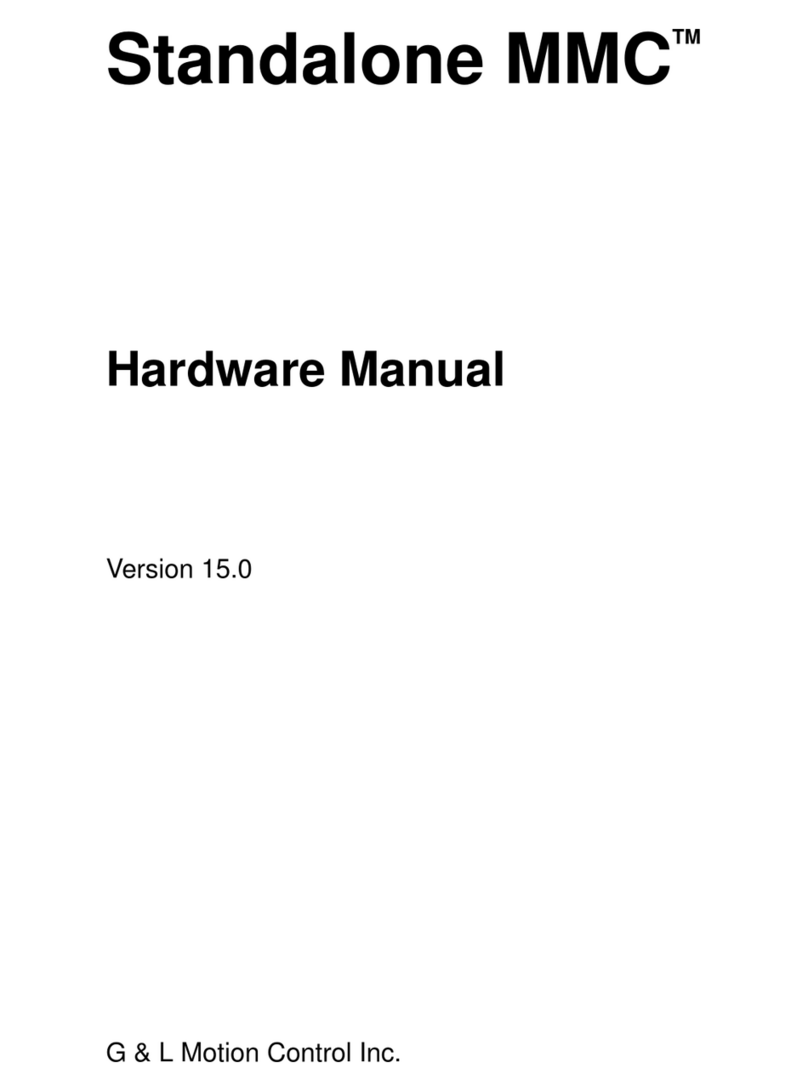
G&L
G&L MMC-A2 Hardware manual