G&L MMC-A2 User manual

Standalone MMCTM
Hardware Manual
Version 15.0
G & L Motion Control Inc.


NOTE
Progress is an on-going commitment at G & L Motion Control Inc. We continually strive to offer the
most advanced products in the industry; therefore, information in this document is subject to change
without notice. The illustrations and specifications are not binding in detail. G & L Motion Control
Inc. shall not be liable for any technical or editorial omissions occurring in this document, nor for any
consequential or incidental damages resulting from the use of this document.
DO NOT ATTEMPT to use any G & L Motion Control Inc. product until the use of such product is
completely understood. It is the responsibility of the user to make certain proper operation practices
are understood. G & L Motion Control Inc. products should be used only by qualified personnel and
for the express purpose for which said products were designed.
Should information not covered in this document be required, contact the Customer Service
Department, G & L Motion Control Inc., 672 South Military Road, P.O. Box 1960, Fond du Lac, WI
54936-1960. G & L Motion Control Inc. can be reached by telephone at (920) 921–7100 or (800) 558-
4808 in the United States or by e-mail at glmotion.support@danahermotion.com
Release Date: 09-01-06
Catalog Part Number M.1300.7620
Printed Part Number M.3000.0067
Electronic Part Number M.3000.0066
© 1999-2006 G & L Motion Control Inc.

Belden®is a registered trademark of Cooper Industries, Inc.
IBM is a registered trademark of International Business Machines Corp.
Windows 95, 98, NT, Microsoft, and MS-DOS are registered trademarks of Microsoft Corporation.
MOD HUB is a trademark of Contemporary Control Systems, Inc.
ARCNET®is a registered trademark of Datapoint Corporation.
ST is a trademark of AT&T Bell Labs.
Temposonics™is a trademark of Contemporary Control Systems, Inc.
DeviceNet™is a trademark of Open DeviceNet™Vendor Association. Inc.
Pentium and PentiumPro are trademarks of Intel Corporation.
PiC900, PiCPro, MMC, PiCServoPro, PiCTune, PiCProfile, LDO Merge, PiCMicroTerm and PiC Programming Pendant are
trademarks of G & L Motion Control Inc.

G & L Motion Control Inc. MMC Hardware Manual i
Table of Contents: MMC Hardware Manual
1 Introduction to the Standalone MMC.................................................................... 1
1.1 Overview....................................................................................................... 1
1.2 Contents of This Manual............................................................................... 1
1.3 Software and Manuals .................................................................................. 2
1.3.1 Required Software and Manuals ......................................................... 2
1.3.2 Suggested Manuals ............................................................................. 2
1.4 G&L Motion Control Support Contact......................................................... 2
2 Safety Precautions.................................................................................................. 3
2.1 System Safety ............................................................................................... 3
2.1.1 User Responsibility ............................................................................. 3
2.1.2 Safety Instructions .............................................................................. 3
2.2 Safety Labels................................................................................................. 4
2.2.1 Hazard Warning .................................................................................. 4
2.2.2 Danger, Warning, or Caution Warning ............................................... 5
2.2.3 Hot Surface Warning .......................................................................... 5
2.3 Safety First.................................................................................................... 6
2.4 Safety Inspection........................................................................................... 6
2.4.1 Before Starting Operations ................................................................. 6
2.5 After Shutdown............................................................................................. 6
2.6 Operating Safely ........................................................................................... 6
2.7 Electrical Service & Maintenance Safety..................................................... 7
2.8 Safe Cleaning Practices ................................................................................ 8
3 Installation, Operation, & Maintenance................................................................. 9
3.1 Mounting the MMC Control......................................................................... 9
3.2 Adding an Option Module to the MMC Control.......................................... 10
3.3 Dimensions and Mounting of MMC with Option Modules Attached.......... 12
3.4 System Power and Environment Requirements............................................ 13
3.4.1 General Power and Environment Requirements ................................. 13
3.4.2 Control Cabinet Specifications ........................................................... 14
3.4.3 Power Distribution Diagram ............................................................... 14
3.4.4 Grounding the System ........................................................................ 16
3.4.5 Controlling Heat Within the System ................................................... 17
3.4.6 Handling an MMC .............................................................................. 18
3.5 System Wiring Guidelines............................................................................ 19
3.5.1 Recommended Signal Separation ....................................................... 19
3.5.2 Differential Devices for Analog and Encoder Signals ........................ 22
3.6 Starting an Application................................................................................. 23
3.7 Basic Setup and Maintenance Procedures .................................................... 24
3.8 System Status Lights..................................................................................... 24
3.8.1 Power Status ....................................................................................... 25
3.8.2 Battery Status ...................................................................................... 25
3.8.3 Scan Status .......................................................................................... 25
3.8.4 Power-up Diagnostics Status .............................................................. 25

ii MMC Hardware Manual G & L Motion Control Inc.
3.8.5 Run-time Diagnostic Status ................................................................ 26
3.8.6 Diagnostic Error Codes ....................................................................... 27
4 Standalone MMC Control...................................................................................... 29
4.1 Introduction................................................................................................... 29
4.2 Features......................................................................................................... 29
4.3 Overview....................................................................................................... 29
4.4 Major Components ....................................................................................... 30
4.4.1 Machine Control Board ...................................................................... 31
4.4.2 Motion Control Board ......................................................................... 32
4.4.2.1 Analog Servo board............................................................. 32
4.4.2.2 SERCOS board.................................................................... 33
4.5 Power Supply Requirements......................................................................... 33
4.6 Machine Control Connection & Operation................................................... 37
4.6.1 PiCPro Port ......................................................................................... 38
4.6.2 Block I/O Port ..................................................................................... 39
4.6.3 User Port ............................................................................................. 43
4.6.4 General I/O Port .................................................................................. 49
4.6.4.1 DC Output Operation........................................................... 53
4.6.4.2 DC Input Operation ............................................................. 56
4.6.5 Power Connection ............................................................................... 57
4.7 Analog Motion Control Connections & Operation....................................... 59
4.7.1 Axis I/O Ports ..................................................................................... 59
4.7.1.1 Axis I/O Port DC Outputs ................................................... 64
4.7.1.2 Axis I/O Port DC Input........................................................ 66
4.7.1.3 Axis I/O Port Analog Output............................................... 67
4.7.1.4 Axis I/O Port Encoder Input................................................ 67
4.7.2 Aux I/O Port ........................................................................................ 68
4.7.2.1 Isolated Breakout Box Details............................................. 74
4.7.2.2 Aux I/O Port Fast Inputs...................................................... 76
4.7.2.3 Aux I/O Port DC Inputs....................................................... 77
4.7.2.4 Aux I/O Port Encoder Input................................................. 79
4.7.2.5 Aux I/O Port Analog Input.................................................. 80
4.8 SERCOS Motion Control Connections & Operation ................................... 81
4.8.1 SERCOS Receive and Transmit Ports ................................................ 81
4.8.2 Loader Port ......................................................................................... 83
4.9 Replacing the MMC Battery......................................................................... 85
4.10 Specifications ............................................................................................. 87
5 Standalone Digital MMC Control.......................................................................... 91
5.1 Introduction................................................................................................... 91
5.2 Features......................................................................................................... 91
5.3 Overview....................................................................................................... 91
5.4 Power Supply Requirements......................................................................... 92
5.5 Connectors & Operation............................................................................... 93
5.5.1 Block I/O Port ..................................................................................... 95
5.5.2 User Port ............................................................................................. 98
5.5.3 PiCPro Port ......................................................................................... 104

G & L Motion Control Inc. MMC Hardware Manual iii
5.5.4 Ethernet Port ....................................................................................... 106
5.5.5 Digital Link Ports ................................................................................ 108
5.5.6 User USB Port .................................................................................... 111
5.5.7 User USB Port .................................................................................... 111
5.5.8 Power Connection ............................................................................... 111
5.6 Replacing the MMC Battery......................................................................... 112
5.7 Specifications ............................................................................................... 114
6 MMC Ethernet TCP/IP Option Module................................................................. 117
6.1 Introduction................................................................................................... 117
6.2 Connections .................................................................................................. 118
6.2.1 The Ethernet Port ................................................................................ 119
6.2.2 The RS232 COMM Ports ................................................................... 121
6.3 LEDs............................................................................................................. 123
6.4 Firmware Update .......................................................................................... 124
6.5 Theory of operation ...................................................................................... 124
6.6 Specifications Table...................................................................................... 126
6.7 Useful Internet Links .................................................................................... 126
7 MMC DeviceNetTM Option Module........................................................................ 129
7.1 Introduction................................................................................................... 129
7.2 Connections .................................................................................................. 130
7.2.1 The DeviceNet Port ............................................................................ 131
7.2.2 The Configuration (RS232) Port ......................................................... 131
7.3 LEDs............................................................................................................. 132
7.4 Theory of Operation...................................................................................... 133
7.5 Specifications................................................................................................ 134
8 MMC ProfibusOption Module.............................................................................. 135
8.1 Introduction................................................................................................... 135
8.2 Connections .................................................................................................. 136
8.2.1 The Profibus Port ................................................................................ 137
8.2.2 The Configuration (RS232) Port ......................................................... 137
8.3 LEDs............................................................................................................. 138
8.4 Theory of Operation...................................................................................... 139
8.5 Specifications for Profibus Module.............................................................. 140
9 MMC Axis I/O Option Module ............................................................................. 141
9.1 Specifications................................................................................................ 142
10 MMC 32In/32Out Option Module....................................................................... 145
10.1 Introduction................................................................................................. 145
10.2 Connections & Operation ........................................................................... 147
10.2.1 DC Output Operation ........................................................................ 150
10.2.2 DC Input Operation .......................................................................... 153
10.3 Specifications.............................................................................................. 155
11 CE and EMC Guidelines...................................................................................... 157
11.1 Background on EMC (Electromagnetic Compatibility) Compliance......... 157
11.2 Background on Low Voltage Compliance.................................................. 157

iv MMC Hardware Manual G & L Motion Control Inc.
11.3 RFI Emission and Immunity....................................................................... 158
11.4 Classes of EMC Operating Environments.................................................. 159
11.5 Conformance with the EMC Directive....................................................... 160
11.6 Conformance With the Low Voltage Directive.......................................... 160
11.7 Changes to the PiC Products....................................................................... 160
11.7.1 Changes Affecting the User .............................................................. 161
11.8 Using CE/EMC and Non-CE/EMC Modules ............................................ 164
11.9 Declarations of Conformity ........................................................................ 166
Appendix A - Operation Details............................................................................... 171
A.1 Introduction.................................................................................................. 171
A.2 DC Inputs..................................................................................................... 171
A.3 DC Outputs .................................................................................................. 173
A.3.1 Inductive Loads .................................................................................. 174
A.4 Encoder Inputs ............................................................................................. 175
INDEX..................................................................................................................... 179

Introduction to the Standalone MMC
G & L Motion Control Inc. MMC Hardware Manual 1
1 Introduction to the Standalone MMC
1.1 Overview
The Standalone Machine and Motion Control (MMC) product line consists
of three distinct products:
•The Standalone MMC Control, which is available in two configu-
rations to control:
•Analog Interfaced drives (such as the Analog Interfaced
MMC-SD) via a +10V analog output.
•SERCOS Interfaced drives.
•The Standalone Digital MMC Control, which controls Digital
Interfaced drives (such as the Digital MMC-SD) via a digital con-
nection (Digital Link).
•MMC Option Modules, which provide various added functional-
ity to the Standalone MMC Control and the Standalone Digital
MMC Control.
Unless otherwise noted, all of the information in this manual applies to both
the Standalone MMC Control and the Standalone Digital MMC Control.
1.2 Contents of This Manual
This manual includes the following major topics:
•Information to safely operate and maintain the equipment in a
safe manner.
•User responsibilities for product acceptance and storage.
•Power and environmental information for general power, control
cabinet, grounding, heat control and handling.
•Procedures for mounting, wiring, and connecting the MMC Con-
trol.
•The function, location, and signal descriptions of connectors on
the MMC Control.
•Physical, electrical, environmental and functional specifications/
dimensions.
•Description of the minimal maintenance necessary.
•A troubleshooting chart of potential problems and possible solu-
tions.

Introduction to the Standalone MMC
2 MMC Hardware Manual G & L Motion Control Inc.
•Part numbers and descriptions for the MMC Control, MMC
Option Modules, and related equipment.
1.3 Software and Manuals
1.3.1 Required Software and Manuals
•For use with the Standalone MMC Digital Control, V16.0 or
higher of one of the following, and for use with the Standalone
MMC Control, V11.0 or higher of one of the following:
•Professional Edition
•MMC Limited Edition
•Monitor Edition
1.3.2 Suggested Manuals
•Function/Function Block Reference Guide
•Motion Application Specific Function Block Manual
•Ethernet Application Specific Function Block Manual
•General Purpose Application Specific Function Block Manual
1.4 G&L Motion Control Support Contact
Contact your local G&L Motion Control representative for:
•Sales and order support
•Product technical training
•Warranty support
•Support service agreements
G&L Motion Control Technical Support can be reached:
•In the United States, telephone (800) 558-4808
•Outside the United States, telephone (920) 921-7100
•E-mail address, [email protected]

Safety Precautions
G & L Motion Control Inc. MMC Hardware Manual 3
2 Safety Precautions
READ AND UNDERSTAND THIS SECTION IN ITS ENTIRETY
BEFORE UNDERTAKING INSTALLATION OR
ADJUSTMENT OF MMC CONTROL EQUIPMENT
The advice contained in this section will help users to operate and maintain the
equipment in a safe manner at all times.
PLEASE REMEMBER THAT SAFETY IS EVERYONE'S RESPONSIBILITY
2.1 System Safety
The basic rules of safety set forth in this section are intended as a guide for
the safe operation of equipment. This general safety information, along with
explicit service, maintenance and operational materials, make up the
complete instruction set. All personnel who operate, service or are involved
with this equipment in any way should become totally familiar with this
information prior to operating.
2.1.1 User Responsibility
It is the responsibility of the user to ensure that the procedures set
forth here are followed and, should any major deviation or change
in use from the original specifications be required, appropriate
procedures should be established for the continued safe operation
of the system. It is strongly recommended that you contact your
OEM to ensure that the system can be safely converted for its new
use and continue to operate in a safe manner.
2.1.2 Safety Instructions
1. Do not operate your equipment with safety devices bypassed
or doors removed.
2. Only qualified personnel should operate the equipment.
3. Never perform service or maintenance while automatic con-
trol sequences are in operation.
4. To avoid shock or serious injury, only qualified personnel
should perform maintenance on the system.

Safety Precautions
4 MMC Hardware Manual G & L Motion Control Inc.
5. ATTENTION - DANGER TO LIFE
Do not touch the main power supply fuses or any components
internal to the power modules while the main power supply
switch is ON. Note that when the main power switch is OFF,
the incoming supply cable may be live.
6. GROUNDING (Protective Earth)
The equipment must be grounded (connected to the protective
earth connection) according to OEM recommendations and to
the latest local regulations for electrical safety. The grounding
(protective earth) conductor must not be interrupted inside or
outside the equipment enclosures. The wire used for equip-
ment grounding (connection to protective earth) should be
green with a yellow stripe.
7. If there is any doubt at all as to the safety of the equipment,
you should set the main power switch to OFF and contact
your OEM for advice.
2.2 Safety Labels
The purpose of a system of safety labels is to draw attention to objects and
situations which could affect personal or plant safety. It should be noted that
the use of safety labels does not replace the need for appropriate accident
prevention measures. Always read and follow the instructions based upon the
level of hazard or potential danger.
2.2.1 Hazard Warning
When you see this safety label on a system, it gives a warning of a
hazard or possibility of a hazard existing. The type of warning is
given by the pictorial representation on the label plus text if used.
The label color is yellow with black text and graphics. To ignore
such a caution could lead to severe injury or death arising from an
unsafe practice. If voltage levels are included in the text they must
indicate the maximum level of the hazard in normal or fault
condition.
Danger Electric
Shock Risk

Safety Precautions
G & L Motion Control Inc. MMC Hardware Manual 5
2.2.2 Danger, Warning, or Caution Warning
When you see this safety label on a system, it gives a warning of a
hazard or possibility of a hazard existing. This type of warning is
given by the pictorial representation on the label plus text if used,
and provides information intended to prevent potential injury and/
or equipment damage.
2.2.3 Hot Surface Warning
Symbol plus DANGER,
WARNING or CAUTION
Hot Surface

Safety Precautions
6 MMC Hardware Manual G & L Motion Control Inc.
2.3 Safety First
G&L Motion Control equipment is designed and manufactured with
consideration and care to generally accepted safety standards. However, the
proper and safe performance of the equipment depends upon the use of sound
and prudent operating, maintenance and servicing procedures by trained
personnel under adequate supervision.
For your protection, and the protection of others, learn and always follow
these safety rules. Observe warnings on machines and act accordingly. Form
safe working habits by reading the rules and abiding by them. Keep these
safety rules handy and review them from time to time to refresh your
understanding of them.
2.4 Safety Inspection
2.4.1 Before Starting Operations
1. Ensure that all guards and safety devices are installed and
operative and all doors which carry warning labels are closed
and locked.
2. Ensure that all personnel are clear of those areas indicated as
potentially hazardous.
3. Remove (from the operating zone) any materials, tools or
other objects that could cause injury to personnel or damage
the system.
4. Make sure that the control system is in an operational condi-
tion.
5. Make certain that all indicating lights, horns, pressure gauges
or other safety devices or indicators are in working order.
2.5 After Shutdown
Make certain all controlled equipment in the plant is safe and the associated
electrical, pneumatic or hydraulic power is turned off. It is permissible for
the control equipment contained in enclosures to remain energized provided
this does not conflict with the safety instructions found in this section.
2.6 Operating Safely
1. Do not operate the control system until you read and understand the
operating instructions and become thoroughly familiar with the system
and the controls.
2. Never operate the control system while a safety device or guard is
removed or disconnected.

Safety Precautions
G & L Motion Control Inc. MMC Hardware Manual 7
3. Where access to the control system is permitted for manual operation,
only those doors which provide that access should be unlocked. They
should be locked immediately after the particular operation is com-
pleted.
4. Never remove warnings that are displayed on the equipment. Torn or
worn labels should be replaced.
5. Do not start the control system until all personnel in the area have been
warned.
6. Never sit or stand on anything that might cause you to fall onto the con-
trol equipment or its peripheral equipment.
7. Horseplay around the control system and its associated equipment is
dangerous and should be prohibited.
8. Know the emergency stop procedure for the system.
9. For maximum protection when carrying out major servicing requiring
the system to be powered down, the power source should be locked
using a lock for which only you have the key. This prevents anyone
from accidentally turning on the power while you are servicing the
equipment.
10. Never operate the equipment outside specification limits.
11. Keep alert and observe indicator lights, system messages and warnings
that are displayed on the system.
12. Do not operate faulty or damaged equipment. Make certain proper ser-
vice and maintenance procedures have been performed.
2.7 Electrical Service & Maintenance Safety
1. ALL ELECTRICAL OR ELECTRONIC MAINTENANCE AND
SERVICE SHOULD BE PERFORMED BY TRAINED AND
AUTHORIZED PERSONNEL ONLY.
2. It should be assumed at all times that the POWER is ON and all condi-
tions treated as live. This practice assures a cautious approach which
may prevent accident or injury.
3. To remove power:
LOCK THE MAIN SWITCH IN THE OPEN POSITION.
USE A LOCK TO WHICH ONLY YOU HAVE THE KEY.
4. Make sure the circuit is safe by using the proper test equipment. Check
test equipment regularly
5. Capacitors take time to discharge. Care should be taken in manual dis-
charging of capacitors
6. There may be circumstances where troubleshooting on live equipment
is required. Under such conditions, special precautions must be taken:

Safety Precautions
8 MMC Hardware Manual G & L Motion Control Inc.
• Make sure your tools and body are clear of the areas of equipment
which may be live.
• Extra safety measures should be taken in damp areas.
• Be alert and avoid any outside distractions.
• Make certain another qualified person is in attendance.
7. Before applying power to any equipment, make certain that all per-
sonnel are clear of associated equipment.
8. Control panel doors should be unlocked only when checking out elec-
trical equipment or wiring. On completion, close and lock panel
doors.
9. All covers on junction panels should be fastened closed before leav-
ing any job.
10. Never operate any controls while others are performing maintenance
on the system.
11. Do not bypass a safety device.
12. Always use the proper tool for the job.
13. Replace the main supply fuses only when electrical power is OFF
(locked out).
2.8 Safe Cleaning Practices
1. Do not use toxic or flammable solvents to clean control system
hardware.
2. Turn off electrical power (lock out) before cleaning control system
assemblies.
3. Keep electrical panel covers closed and power off when cleaning an
enclosure.
4. Always clean up spills around the equipment immediately after they
occur.
5. Never attempt to clean a control system while it is operating.
6. Never use water to clean control equipment unless you are certain that
the equipment has been certified as sealed against water ingress. Water
is a very good conductor of electricity and the single largest cause of
death by electrocution.

Installation, Operation, & Maintenance
G & L Motion Control Inc. MMC Hardware Manual 9
3 Installation, Operation, & Maintenance
3.1 Mounting the MMC Control
Mount the unit to your cabinet using the mounting slots on the MMC as
shown. (Note: the Standalone MMC Digital Control requires a minimum of
1/2 in clearance on the left side, for proper fan air movement). The MMC
unit must be mounted vertically. The recommended size of mounting
hardware is #10 bolts with #10 star washers (to ensure proper ground
connection) as shown in Figure 3-1 below.

Installation, Operation, & Maintenance
10 MMC Hardware Manual G & L Motion Control Inc.
Figure 3-1: MMC Mounting Dimensions
3.2 Adding an Option Module to the MMC Control
Several Option Modules are available to add functionality to the MMC
system. These modules are described in the later sections of this manual.
The standard Standalone MMC Control (MMC-A2, MMC-A4, and MMC-
S8) accepts up to two MMC Option Modules. The Standalone MMC Control
MMC
.55" (13.97 mm)
1.00"
(25.4 mm)
2.10" (53.34 mm)
9.59" (243.59 mm)
8.75" (222.25 mm)
.218" (5.54 mm)
1.05" (26.67 mm)
.55"
Side Cover
Screw Head
.040" Thickness
.080" Thickness
NOTE: Add the side
cover and screw head
thicknesses to the
unit’s dimensions for
total width.
.500" (12.70 mm) clearance required
for Standalone Digital MMC Control
(13.97 mm)
Note: Unit is 5.3”
(134.62 mm) deep.

Installation, Operation, & Maintenance
G & L Motion Control Inc. MMC Hardware Manual 11
Plus (MMC-A2 Plus and MMC-A4 Plus), as well as the Standalone Digital
MMC Control (MMC-D32 and MMC-D64), accepts up to four MMC Option
Modules.
Option modules are shipped with a 50-pin square post connector and screws
needed to attach the module to the MMC (or to another option module).
Follow the procedure below to add an option module to the MMC (or to
another option module).
1. Place the MMC and the option module on a static free surface. Ground
yourself using a properly grounded wrist strap before you begin. These
are standard precautions before handling any electronic components.
2. Remove the five screws securing the MMC cover using a #1 Phillips
screwdriver and set them aside. There are two screws on the top, two
screws on the bottom, and one screw on the side of the module.Lift the
side cover off and set aside.
3. Locate the 50-pin square post socket at the top of the MMC board.
Press one side of the 50-pin square post male connector into this socket
ensuring that the pins are aligned and it is firmly seated.
4. Pick up the option module. Line up the socket on the option module
with the male end of the connector extending from the MMC ensuring
that the pins are aligned. Press firmly into place. Be sure to align the
screw tabs on the top and bottom of the option module with the screw
slots on the top and bottom of the MMC module so that the modules
slide together easily.
5. Screw four screws (of the five included in your package) into the screw
tabs to attach the option module to the MMC.
6. Lay the unit on the bench. Place the cover you set aside in Step 3 on the
option module. Be sure to align the screw tabs on the top and bottom of
the cover with the screw slots on the top and bottom of the option mod-
ule.
7. Screw the five screws removed in Step 2 back into place to secure the
cover.

Installation, Operation, & Maintenance
12 MMC Hardware Manual G & L Motion Control Inc.
Figure 3-2: Location of Screws on the MMC Control
(MMC A-4 Servo Unit Shown)
3.3 Dimensions and Mounting of MMC with Option
Modules Attached
After attaching option modules to the MMC module, mount the unit to your
cabinet using the mounting slots on the MMC and the option module. The
recommended size of mounting hardware is #10 bolts with #10 star washers
(to ensure proper ground connection).
Cover Side of Module
Side Screw
Top Screws
Bottom Screws
+24
COM
This manual suits for next models
7
Table of contents
Popular Controllers manuals by other brands
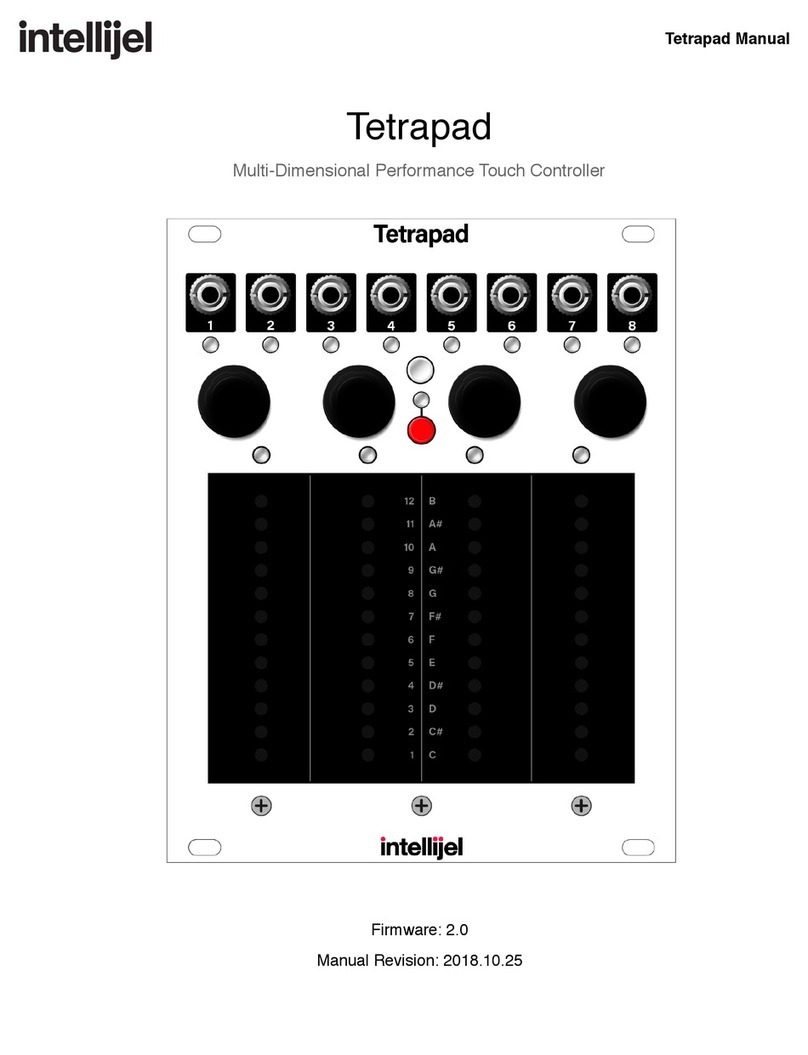
Intellijel
Intellijel Tetrapad user manual
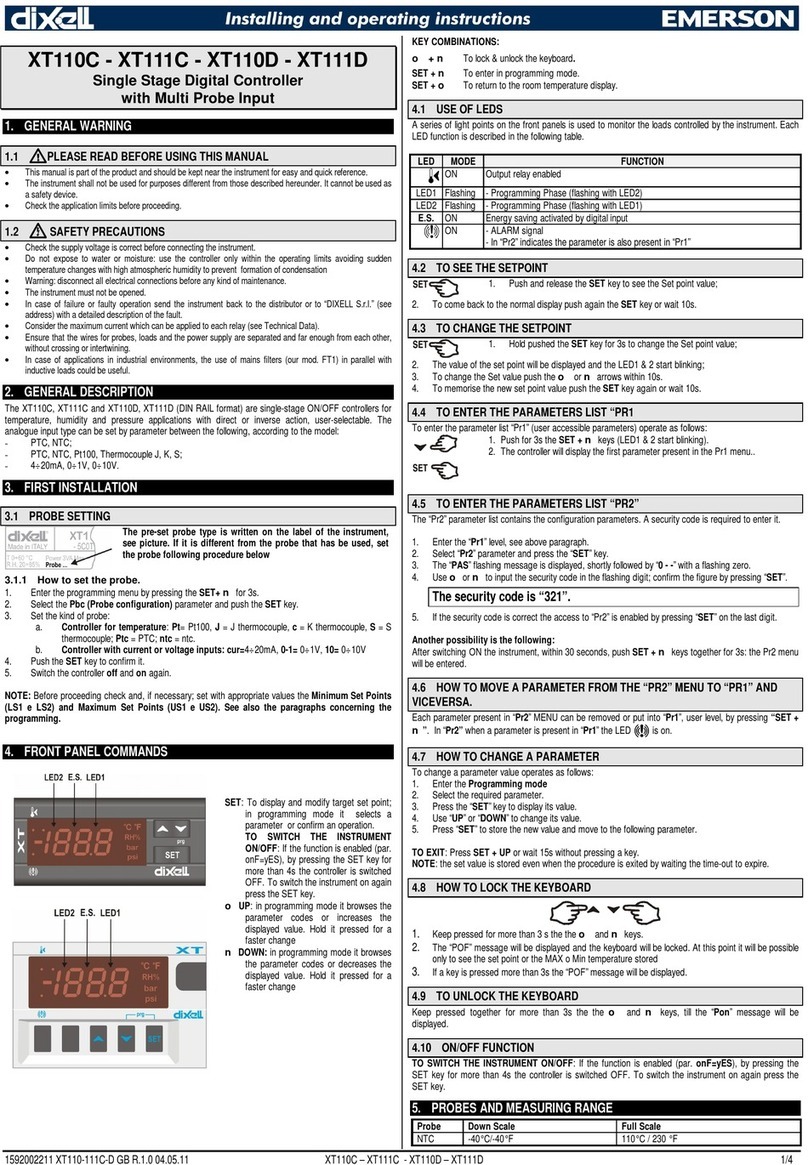
Emerson
Emerson dixell XT111D Installing and operating instructions
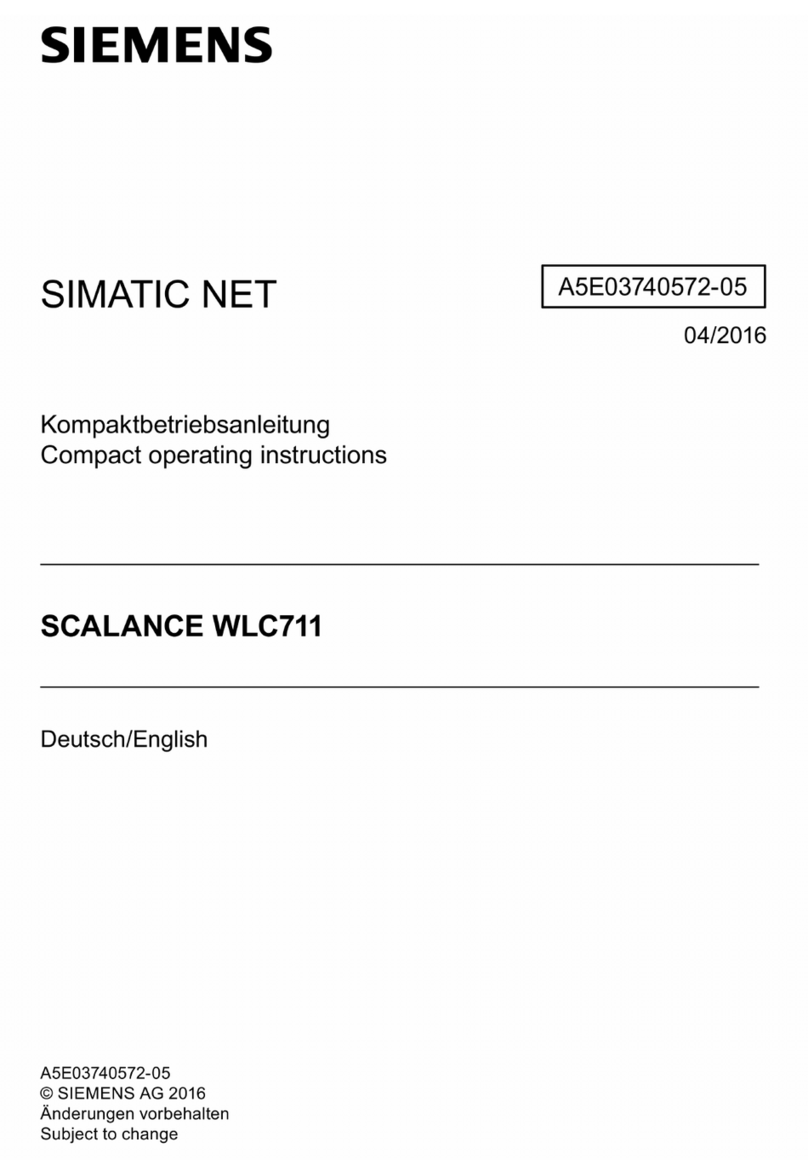
Siemens
Siemens scalance WLC711 Compact operating instructions
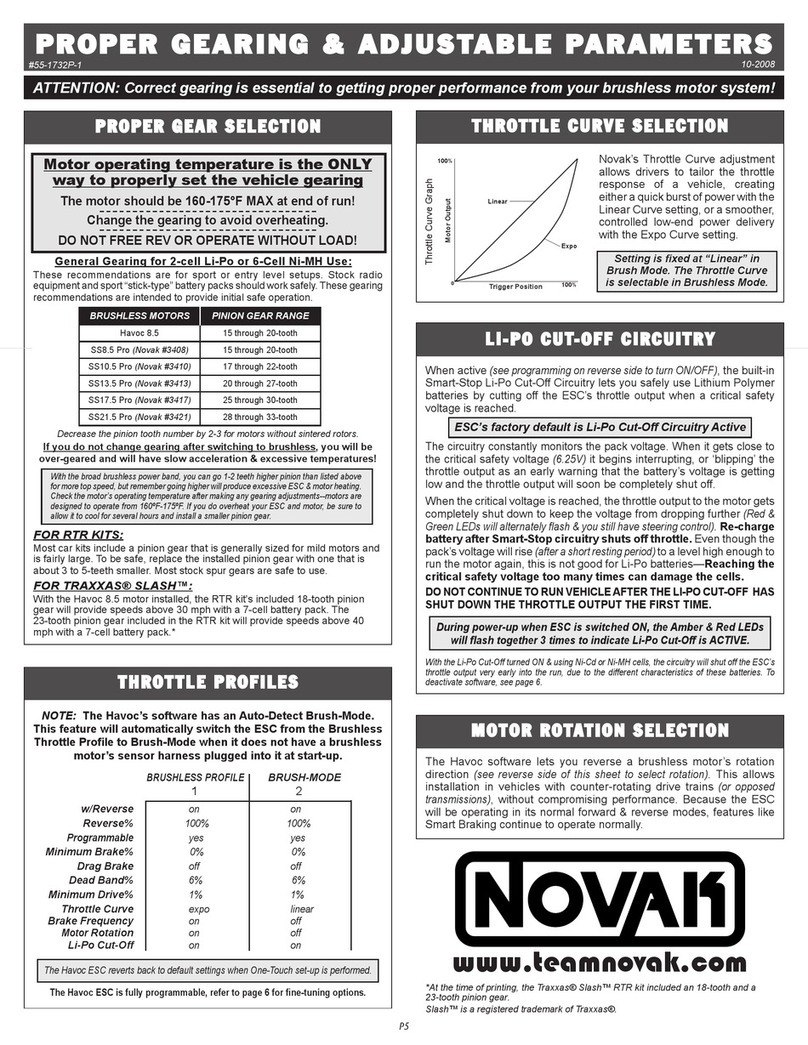
NOVAK
NOVAK HAVOC SPORT ESC - CUSTOM PROGRAMMING AND... instructions
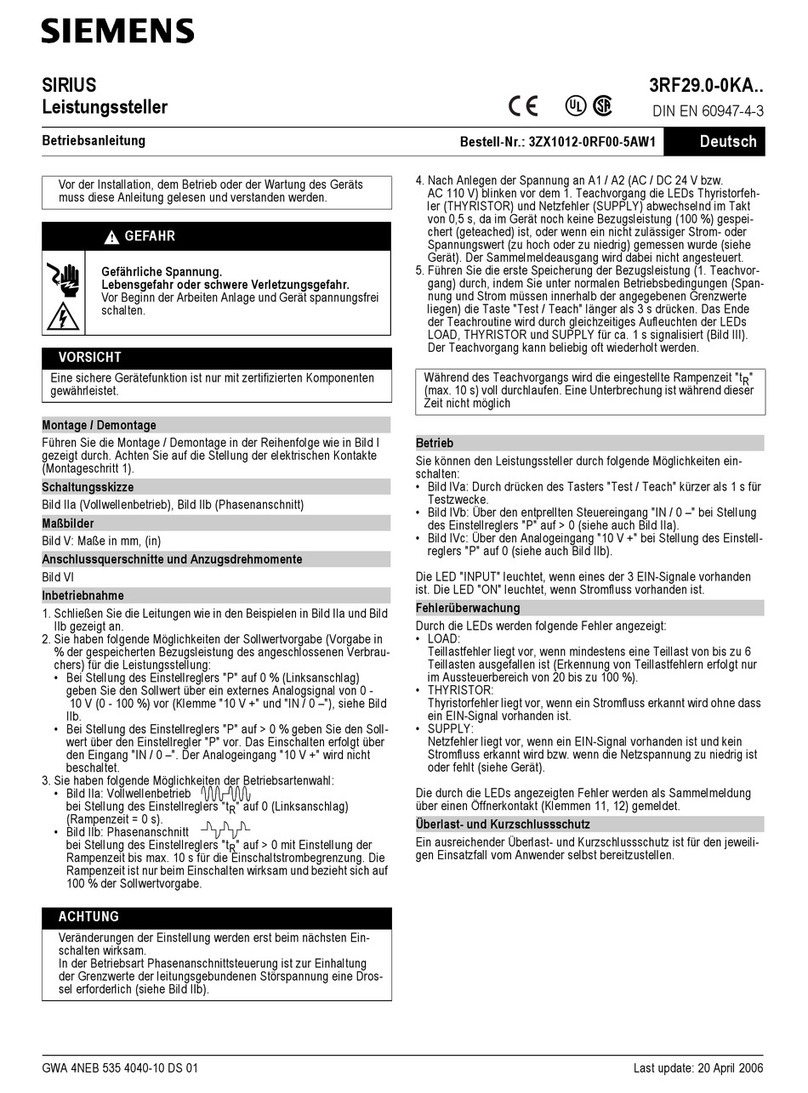
Siemens
Siemens SIRIUS 3RF29 0-0KA Series operating instructions
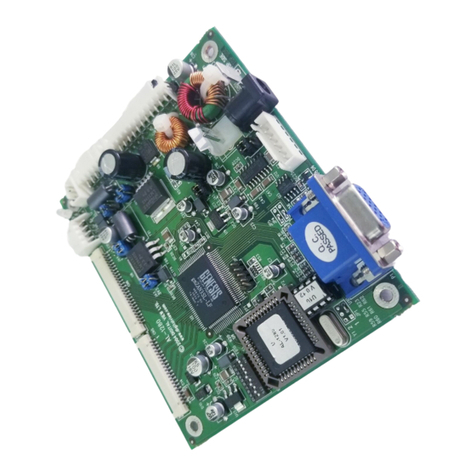
digitalview
digitalview AL-1280 instructions