Fröling SPS 4000 User manual

Operating Instructions
Boiler controller SPS 4000
Version 01.06
Translation of the original German operating instructions for technicians
Read and follow the instructions and safety information!
Technical changes, typographical errors and omissions reserved!
B0960417_en | Edition 16/02/2018
Fröling GesmbH | A-4710 Grieskirchen, Industriestraße 12 | www.froeling.com

1 General 5
1.1 Safety information 6
2 Electric components and wiring 7
2.1 SPS 7
2.1.1 Display 8
Ports and displays
8
Changing the Compact Flash
10
Replacing the battery
11
2.1.2 X20 – module layout 12
2.1.3 X20 module types 15
BR9300
15
PS2100
17
BT9100
20
CS1012
22
CS1030
24
DI2377
25
DI9371
26
DO9322
28
DO8332
30
DO6639
32
DO2633
34
AI4622
36
AI4222
38
AO4622
40
AO2622
42
AT6402
44
AT4222
46
2.2 Sensor characteristic line PT100 48
2.3 Sensor characteristic line type K 49
2.4 Frequency converter 51
2.4.1 Operating elements 51
2.4.2 Changing parameters 52
2.5 Cascade / Modbus 54
2.5.1 Terminating resistor at communication
module
56
2.6 M-bus 56
3 Overview of the basic functions 57
3.1 Touch display 57
3.2 Control icons 58
4 Initial startup 59
4.1 Before switching on for the first time 59
4.2 Switching on for the first time 59
4.3 Changing the language 60
4.4 Performing a software update 61
4.5 Perform hardware detection manually 62
4.6 Configuring the boiler 64
4.6.1 Setting the boiler type 64
4.6.2 Setting the boiler-specific parameters 65
List of possible parameters
65
4.7 Configure fuel feed 67
4.7.1 Chamber discharge system 67
4.7.2 Fuel feed: general information 68
4.8 Configure hydraulic system 70
4.8.1 Sample configuration 71
4.9 Configure additional system options 73
4.9.1 Backup boiler 73
4.9.2 Cascade 73
4.9.3 Flue gas treatment 73
4.10 I/O configuration 74
4.10.1 I/O configuration according to circuit
diagram
76
4.11 Setting the parameters of the
frequency converter
77
4.12 Finishing configuration 77
4.13 Performing the first start / Checking
the settings
77
5 Operation 79
5.1 Switching the boiler on/off 79
5.2 Navigation within the system menu 79
5.2.1 Navigating within submenus 80
5.3 Displaying/changing parameters 81
5.3.1 Displaying parameter info 82
5.3.2 Changing the parameter value 83
5.4 Quick menu 85
5.5 Activating manual operation 85
5.6 Setting the date and time 86
5.7 Setting times 87
5.7.1 Applying the time setting for several days 88
5.8 Switching user level 89
6 Menus and parameters 90
6.1 Heating circuits & system 90
6.1.1 Backup boiler / Swivel burner 90
Backup boiler – Configuration
90
Swivel burner – Configuration
91
Table of Contents
2 Fröling GesmbH | A-4710 Grieskirchen, Industriestraße 12 | www.froeling.com

6.1.2 Cascade 92
Cascade - Temperatures
92
Power demand in cascade mode
92
Cascade - Configuration
93
6.1.3 Flue gas treatment 93
Configuration for flue gas filter
93
Configuration for flue gas heat exchanger
94
6.1.4 Hydraulics: general information 95
6.1.5 Feeder pumps 95
Configuration
95
6.1.6 Boiler distributor 96
Configuration
96
Assigned components
97
6.1.7 Distributor 1 - 6 97
Configuration
97
Assigned components
98
6.1.8 Heating circuits 98
Heating circuits - Temperatures
98
Heating circuits - Times
99
Heating circuits - Configuration
100
6.1.9 DHW tank 100
DHW tank - Temperatures
100
DHW tank - Times
101
DHW tank - Configuration
102
6.1.10 Storage tank 103
Boiler behaviour
103
Buffer tank - Temperatures
103
Buffer tank - Times
105
Storage tank - Configuration
105
6.2 Boiler 106
6.2.1 Mode 106
6.2.2 Boiler times 106
6.2.3 Boiler settings 107
6.2.4 Water temperatures 108
6.2.5 Ignite 110
6.2.6 Air flaps/blower fan 111
Configuration
111
Frequency converter
114
Test
115
6.2.7 Flue gas 115
6.2.8 Combustion chamber 116
6.2.9 Heat exchanger cleaning 118
6.2.10 FGR 119
Configuration
119
Frequency converter
121
6.2.11 Grate 121
6.2.12 Ash Removal 122
6.2.13 Joint ash removal 123
6.2.14 Slide-on duct 123
6.2.15 Special mode 124
6.2.16 External boiler control 124
6.2.17 Control parameters 125
6.3 Fuel feed 126
6.3.1 Stoker 126
6.3.2 Feed screw/feeder 127
6.3.3 Hopper 129
6.3.4 Chamber discharge system 130
6.3.5 Sliding floor 131
6.3.6 Suction system 132
Cyclone 1
132
Cyclone 2
132
6.3.7 Rotary valves 133
6.4 PLC 134
6.4.1 Software 134
6.4.2 Connections 134
Network
134
Field bus
135
6.4.3 Display 137
Display settings
137
Calibrate touchscreen
137
6.4.4 Hardware 138
6.4.5 SPS restart 138
6.5 Diagnosis 139
6.5.1 Error 139
Current faults
139
Fault log
139
Clear error
140
6.5.2 Inputs and outputs 140
6.5.3 System 141
6.5.4 Message forwarding 141
6.5.5 Diagnostic data 142
6.5.6 USB recording 142
Configuration
143
6.5.7 Current values 143
6.5.8 Operating times 143
6.6 System configuration 145
6.6.1 Hydraulic system 145
6.6.2 Heating circuits & system 145
Heating circuits
145
DHW tank
146
Buffer tank
146
Backup boiler
147
Cascade
147
Exhaust gas treatment
147
Pumps
148
6.6.3 Boiler type 148
6.6.4 Boiler 148
6.6.5 Fuel feed 149
Chamber discharge system
149
Fuel feed
149
6.6.6 Inputs and outputs 150
6.6.7 Operating times 151
6.6.8 Operator data 151
6.6.9 Backup 152
Save configuration
152
Load configuration
152
6.6.10 Specification values 153
Boiler specifications
153
Fuel specifications
153
Own templates
153
Factory setting
154
Table of Contents
Operating Instructions SPS 4000 | B0960417_en 3

7 Troubleshooting 155
7.1 Fault handling 155
7.2 Fault message list 156
8 Appendix 170
8.1 FAQ 170
8.1.1 Changes - control cabinet H 3000 to SPS
4000
170
Regulating flaps
170
Sensors
170
Multi-sensor storage tank management
170
Flue gas temperature sensor
170
Casing cooling
170
Separation of fault contacts
170
Grate hydraulics LM 750/1000 control
170
Lambda probe 0-10V
171
8.1.2 Boiler program (Start-shut down) 172
8.1.3 Back up/restore memory card 173
8.1.4 Performing a software update 180
8.1.5 Connecting to the SPS with PC 182
Connection via a local network (LAN)
182
Direct connection to SPS 4000
183
SPS 4000 network settings
184
PC network settings
186
8.1.6 System Diagnostic Manager (SDM) 191
Saving log file to data medium
192
Create system dump
193
8.2 Addresses 194
8.2.1 Address of manufacturer 194
Customer service
194
8.2.2 Address of the installer 194
Table of Contents
4 Fröling GesmbH | A-4710 Grieskirchen, Industriestraße 12 | www.froeling.com

1 General
Thank you for choosing a quality product from Froling. The product features a state-of-the-art design and
conforms to all currently applicable standards and testing guidelines.
Please read and observe the documentation provided and always keep it close to the system for reference.
Observing the requirements and safety information in the documentation makes a significant contribution to
safe, appropriate, environmentally friendly and economical operation of the system.
The constant further development of our products means that there may be minor differences from the pictures
and content. If you discover any errors, please let us know: [email protected].
Subject to technical change.
About these instructions
The range of functions of the SPS 4000 depends on the user level currently set. These instructions show all the
parameters that are available with full functionality in the "Service" user level (maximum configuration with all
possible system components). The range available varies according to the user level set.
NOTICE
The values given in the parameter lists are examples, and should not be used as standard
values!
General 1
Operating Instructions SPS 4000 | B0960417_en 5

1.1 Safety information
DANGER
When working on electrical components:
Risk of electrocution!
When work is carried out on electrical components:
❒ Only have work carried out by a qualified electrician
❒ Observe the applicable standards and regulations
➥Work must not be carried out on electrical components by unauthorised people
WARNING
When touching hot surfaces:
Severe burns are possible on hot surfaces and the flue gas pipe!
When work is carried out on the boiler:
❒ Shut down the boiler in a controlled way (operating status "Boiler off") and allow it to cool
down
❒ Protective gloves must generally be worn for work on the boiler, and it should only be
operated using the handles provided
❒ Insulate the flue pipes or simply avoid touching them during operation.
The information on safety, standards and guidelines in assembly and operating instructions for the boiler should
also be observed.
1General
Safety information
6 Fröling GesmbH | A-4710 Grieskirchen, Industriestraße 12 | www.froeling.com

2 Electric components and wiring
2.1 SPS
The controller consists of two main components. The CPU/display unit and the input/output rack. In addition, the
frequency converters are connected to the controller by modbus.
Electric components and wiring 2
SPS
Operating Instructions SPS 4000 | B0960417_en 7

2.1.1 Display
Power Panel PP65, 5.7" QVGA colour TFT display with touch screen (resistive), 128
MByte DRAM, 232 kByte SRAM, CompactFlash slot, Ethernet 10/100, 1x X2X link, 2x
USB, protection class IP65 (front)
Ports and displays
APower supply
BEthernet port (RJ45 shielded, transfer rate 10/100 MBit/s)
CTwo USB ports (type A, USB 1.1, USB 2.0)
DX2X link
Assign the plugs as follows (see also the connection instructions on the back of the display):
24V power supply Terminal connections X2X link
2Electric components and wiring
SPS
8 Fröling GesmbH | A-4710 Grieskirchen, Industriestraße 12 | www.froeling.com

Setting the node number
The display has a dedicated node number switch, which also allows you to define the subscriber address in the
network. If there are several displays in one network (multi-boiler systems), you will need to set a node number,
which is unique to the network, in addition to the IP address.
The node numbers E0 to FF are reserved, and must not be set.
NOTICE! For displays only the address range 00 to DF should be used!
HEX DEZ
0 0
1 1
2 2
3 3
4 4
5 5
6 6
7 7
8 8
9 9
A 10
B 11
C 12
D 13
E 14
F 15
Converting the HEX number at the node number switch to a decimal number:
The value set at node number switch "x16" is multiplied by 16 and added to the value
set at node number switch "x1":
e.g. 12 hex (1 x 16 + 2) = 18 dec
e.g. EA hex (14 x 16 + 10) = 234 dec
Converting a decimal number to a hexadecimal number for setting the node number
switch:
The decimal number is divided by 16 with remainder and set at the node number switch
"x16”; the remainder from the division is set at the "x1" node number switch:
e.g. 33 dec (33 / 16 -> 2 + 1 remainder) = 21 hex (x16 = 2, x1 = 1)
e.g. 180 dec (180/16 -> 11 + 4 remainder) = B4 hex (x16 = B, x1 = 4)
Electric components and wiring 2
SPS
Operating Instructions SPS 4000 | B0960417_en 9

Status displays
The following status LEDs are below the node number switches:
LED Colour Status Description
Status Red On Error/reset
Orange On Boot / ready mode
User Green On/off LED being operated by the application
X2X Orange On The module is sending data via the X2X interface
CF Orange On Access to the Compact Flash medium
Changing the Compact Flash
❒ Turn the locking lever (1) 90°
❒ Push in the eject button (2) with pin
➥CF card pops out
❒ After you have inserted the new CF card, secure it with the locking lever
2Electric components and wiring
SPS
10 Fröling GesmbH | A-4710 Grieskirchen, Industriestraße 12 | www.froeling.com

Replacing the battery
❒ Switch off the power supply to the display
❒ Discharge any electrostatic on the housing / earth connection
❒ Remove the battery cover (1) on the top of the display
❒ Carefully remove the battery from the holder by pulling the ribbon attached (2)
❒ Insert the new battery with the correct polarity
➥Do not touch the battery using pliers or uninsulated tweezers due to the risk of short circuit
➥Only handle the battery by the faces
➥When inserting the battery, ensure that the ribbon for removing it again is correctly positioned
❒ Replace the battery cover and switch on the power supply
Electric components and wiring 2
SPS
Operating Instructions SPS 4000 | B0960417_en 11

2.1.2 X20 – module layout
The X20 input/output rack is a modular system, consisting of several modules, which in
turn are made up of three components.
ABus module
BElectronic module
CTerminal block
Assembling the module
Top view Front view
❒ Slide the bus modules together to make a rack
2Electric components and wiring
SPS
12 Fröling GesmbH | A-4710 Grieskirchen, Industriestraße 12 | www.froeling.com

❒ Position the electronic modules beside the bus module as shown and push in until they engage
❒ Hook the terminal block onto the electronic module
❒ Push the terminal block into the electronic module until it engages
Electric components and wiring 2
SPS
Operating Instructions SPS 4000 | B0960417_en 13

Fitting the modules to the top hat rail
Top hat rail lever unlocked
(module can be removed)
Top hat rail lever locked
(module fixed to top hat rail)
❒ Tilt up the top rail lever of all modules in the rack
❒ Place the entire rack on the top hat rail and secure with the individual top hat rail levers
Removing the modules
To remove a module, carry out the steps above in the reverse order:
Remove the terminal block:
❒ Push the locking lever of the terminal block down
❒ Tilt the terminal block down until you can pull it out
Remove the electronic module:
❒ Push down the locking knob and pull the electronic module straight out
2Electric components and wiring
SPS
14 Fröling GesmbH | A-4710 Grieskirchen, Industriestraße 12 | www.froeling.com

2.1.3 X20 module types
BR9300
This module is the start of the rack. The module supplies the necessary power supply for bus
communication to the SPS via X2X link and the first input/output modules.
NOTICE! The BR9300 may only be used with the BM01 bus module!
LED Colour Status Description
r Green Off Not in operation (no power supply)
Quick flashes Reset mode
Flashing Preoperative mode
On Module in operation
e Red Off No error / no supply to module
Double flashing LED indicates one of the following operating statuses:
▪ The X2X link supply by the power supply unit is
overloaded
▪ I/O supply too low
▪ Input voltage for X2X link supply too low
e+r Red illuminated (e)
Green flashing (r)
Incorrect firmware
X Orange Off No communication at X2X link
On Communication at X2X link OK
I Red Off X2X link supply OK
On Power supply unit overloaded (additional supply
modules required)
Electric components and wiring 2
SPS
Operating Instructions SPS 4000 | B0960417_en 15

NOTICE! Connection 1-5 does not have to be wired as there is an internal jumper between terminal 1-4 and
terminal 1-5.
The connection diagram below shows how the module is wired:
1Wire jumper for supplying the X2X link
2Electric components and wiring
SPS
16 Fröling GesmbH | A-4710 Grieskirchen, Industriestraße 12 | www.froeling.com

PS2100
Additional module for the feed at the bus and for input/output modules.
LED Colour Status Description
r Green Off Not in operation (no power supply)
Quick flashes Reset mode
Flashing Preoperative mode
On Module in operation
e Red Off No error / no supply to module
Double flashing LED indicates one of the following operating statuses:
▪ I/O supply too low
▪ Input voltage for X2X link supply too low
e+r Red illuminated (e)
Green flashing (r)
Incorrect firmware
Electric components and wiring 2
SPS
Operating Instructions SPS 4000 | B0960417_en 17

For this module, you will need to decide whether it is to be used as an additional supply or as a separate feed
from the rest (e.g. to create interlocking voltages). It is mainly used with the SPS4000 to create interlocking
voltages. These are required, for example, for the emergency stop and drop box cover. To ensure that all
subsequent modules switch off, a BM01 must be used as the bus module.
BM01 BM11
Module for interlocking voltages
Distinctive features:
▪ Name BM01
▪ No gold contacts at bottom
▪ Module colour: light grey
Module for additional supply
Distinctive features:
▪ Name BM11
▪ Gold contacts at bottom
▪ Module colour: dark grey
2Electric components and wiring
SPS
18 Fröling GesmbH | A-4710 Grieskirchen, Industriestraße 12 | www.froeling.com

The image below shows one possible setup:
1Start of the rack with the BR9300 module. The inputs/outputs are supplied up to point 2.
2A PS2100 module needs to be inserted here to supply the subsequent inputs/outputs with 24V up to point 3. This
setup could, for example, be a locking unit.
3A PS2100 module is inserted again here to supply the remaining inputs/outputs with 24V. This setup could, for
example, be another locking unit.
Electric components and wiring 2
SPS
Operating Instructions SPS 4000 | B0960417_en 19

BT9100
The BT9100 is a bus transmitter module and is used to seamlessly expand the X20 system. The
stations can be up to 100 metres apart.
NOTICE! The bus transmitter module must only be operated with the BM11 bus module! If the feed for
the internal I/O supply is used, this potential group must not be powered by any other module. An I/O
module with bus module BM01 must be used to separate the potential group.
LED Colour Status Description
r Green Off Not in operation (no power supply)
Quick flashes Reset mode
Flashing Preoperative mode
On Module in operation
e Red Off No error / no supply to module
Double flashing LED indicates one of the following operating statuses:
▪ I/O supply too low
▪ Input voltage for X2X link supply too low
e+r Red illuminated (e) / Green flashing (r) Incorrect firmware
X Orange Off No communication at X2X link
On Communication at X2X link OK
2Electric components and wiring
SPS
20 Fröling GesmbH | A-4710 Grieskirchen, Industriestraße 12 | www.froeling.com
Other manuals for SPS 4000
2
Table of contents
Popular Controllers manuals by other brands
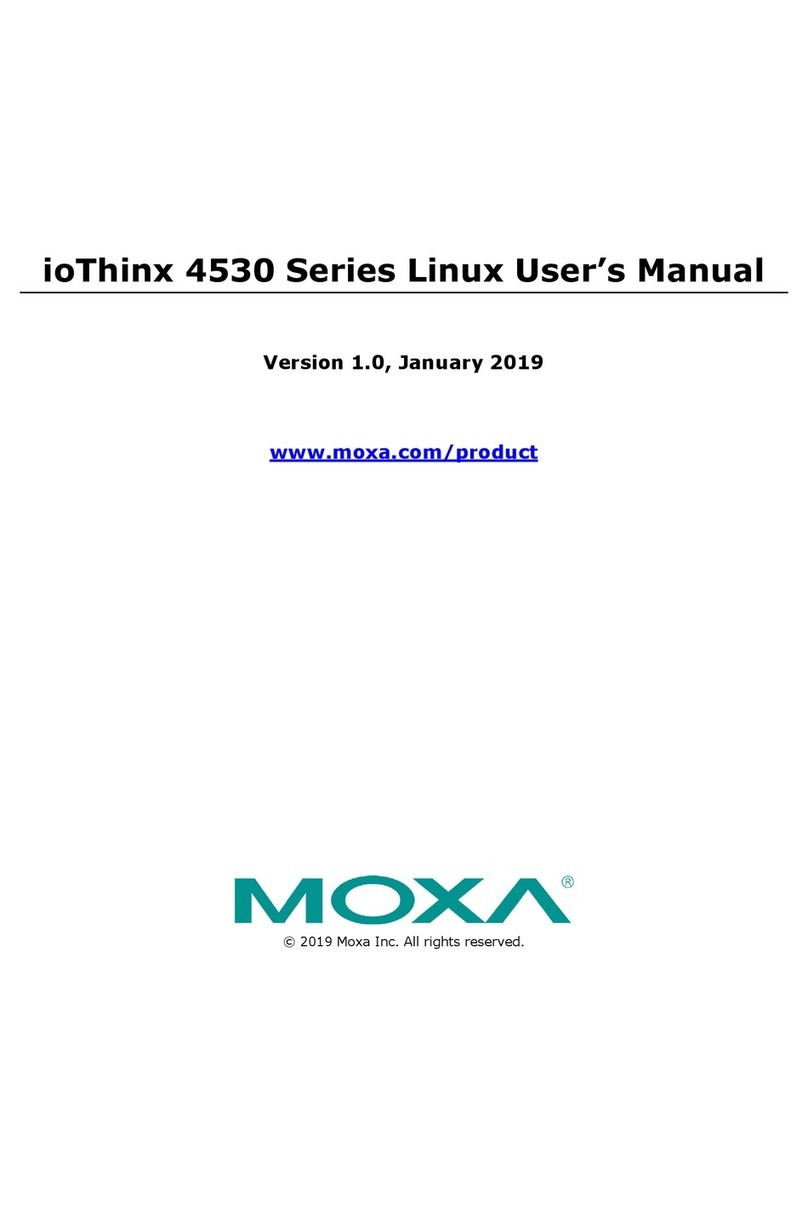
Moxa Technologies
Moxa Technologies ioThinx 4530 Series user manual
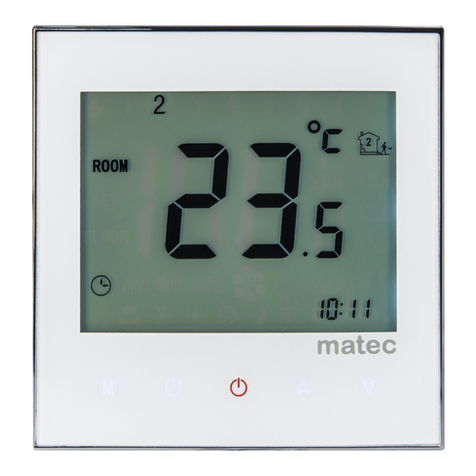
Zamel
Zamel RTD-02 Manual instruction
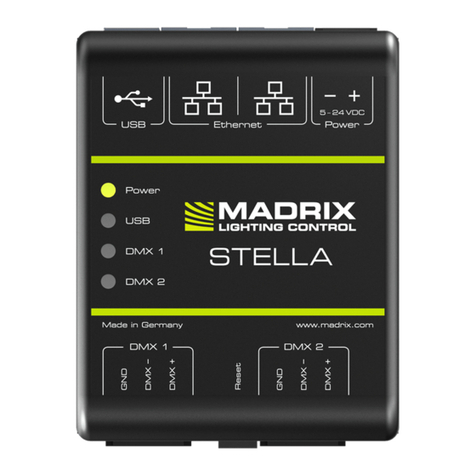
MADRIX
MADRIX STELLA Technical Manual & Quick Start Guide
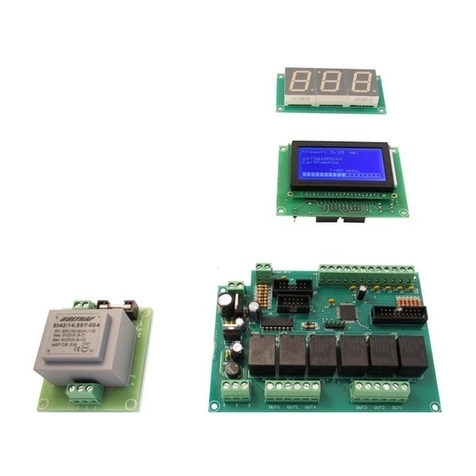
Intiel
Intiel INT0193 user manual
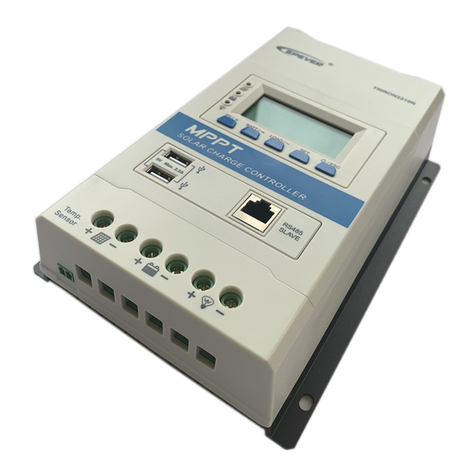
Epever
Epever SolarV TRIRON Series user manual
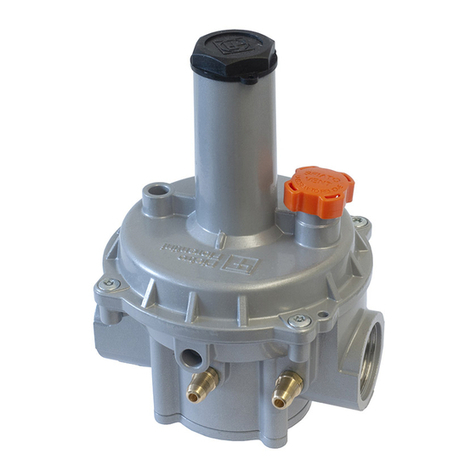
PIETRO FIORENTINI
PIETRO FIORENTINI GOVERNOR Operating and maintenance manual