Dantherm NF-8HD User manual

MANUAL FOR
NF-8HD / NF-16HD CONTROLLER
(AUG 2005 Vers. 1005)
CONTENTS:
Safety Instructions Tab. 05.51 Page 06.01-06.02
Installation Manual Tab. 05.91 Page 05.01-05.12
Operating Instructions Tab. 05.91 Page 07.01-07.04
Maintenance Instructions Tab. 05.91 Page 08.01
Spare parts Tab. 05.91 Page 09.01

01SEP05 1004GB Cat. 20 / Tab. 05.51 / Page 06.01
SAFETY REGULATIONS NF10
Disregarding Dantherm Filtration safety regulations entails a heavy safety risk.
Maintenance.
Maintenance must be performed to Dantherm Filtration maintenance directions.
Open fire, sparking or other form of heat generation such as: Welding, grinding, boring/drilling or
smoking etc. may not take place closer than 3 metres to filters, fans, pipe components, waste containers,
etc. working with explosive atmosphere, such as dust laden air.
It must be ensured that cleaning be performed on and around the system components to prevent
inflammable and explosive dust waste from igniting and causing heavy damage.
To prevent static electricity generation in systems with an inflammable and explosive atmosphere, it must
be ensured that such systems with connected ducts etc. be duly earthed.
Maintenance work may not commence until the total system has stopped properly, and the power supply
cut in a safe manner, for instance by locking the main switch.
Inspection inside the system by opening inspection doors and similar may not be performed until after the
usual cleaning periods have been run, until filters are free of dust accumulation, and dust/waste has been
carried to silo/waste bin.
In this connection, it must be checked whether the filter regeneration has been adequate, by examining
the residual dust accumulation on the sleeves.
Inspection by opening inspection doors and similar may be performed only when personal safety
equipment, adapted to the particular conditions, is used.
If a movable ladder is used for the work, the ladder must be secured properly for stability before
commencing the work.
Service and Repair.
Service and repair may be performed by specially trained staff only.
Before any work is begun, the energy supply must be cut by the main switch, and it must be ensured that
no unintended restart may occur, for instance by locking the main switch. Accumulated energy, such as
in a compressed air system, must also be interrupted, possibly discharged altogether, before commencing
the work.
For service and repair work making it necessary to stay in dust laden air, for instance in the filter, as a
minimum the following safety equipment must be used. For toxic dust, supplemented by own special
equipment, the following must be used:

01SEP05 1004GB Cat. 20 / Tab. 05.51 / Page 06.02
1 Respiratory Protective Device, possibly with fresh air supply.
2 Goggles, possibly shield mask in connection with fresh air supply.
For fire/explosive dust, the following must also be used:
3 Fire Retardant Suit.
4 Fire Retardant Working Gloves.
5 Safety Footwear.
6 Safety Helmet.
7 Sparkless tools wherever possible.
Inspection of filters from the clean air side/in the clean air chamber may be performed only when the
filter system has stopped.
For this, also the personal safety equipment referred to above must be used.
If cleaning is performed using a vacuum cleaner, protection must be provided against static electric
charging in the suction arrangement.
Boring of holes in filter housing or adjoining pipe ducts may be performed only when the system has
stopped and been cleaned, while taking great care and without any heat generation.
If any faults occur in the electric system which make the system stop, and restart has been cut, the faulty
component may not be removed to allow for further operation. Proper troubleshooting and repair prior to
restarting must be performed.
Disposal of replaced components, dust/waste from cleaning, as well as other waste, must be performed to
the guidelines for the particular materials. These guidelines will usually have been laid down by the local
authorities. In case of doubt, the person responsible for company safety should be consulted.

01AUG 1005GB Cat.20 / Tab. 05.91 / Page 05.01
INSTRUCTIONS for installing filter control systems NF-8HD and NF-16HD
Safety Precautions.
In order to ensure work safety, the following precautionary measures are recommended in ad-
dition to those usually stipulated for operations on electrical installations:
•Installation of control systems may only be undertaken by professional personnel, accord-
ing to the standards for electrical materials.
•At the installation site, all the conventional rules, stipulations, precautions and instruc-
tions for electrical installation must be observed.
•Adjustment of electrical controllers with the casing removed may only be carried out by
specialised personnel and in full accordance with the stipulated safety rules.
•In the mains supply, 230 V AC is applied to the terminals L230 (1) and N (3) (Fig. 5, 3.1).
For the 110V AC supply the terminals L110 (2) and N (3) are to be used (or the special
voltage ordered in conformity with the label and terminal specification).
In addition the safety recommendation NF10 must be observed.
General.
The filter control system NF-8HD / NF-16HD is an electrical controller for control of filter
plants with pressure pulse air cleaning using 24V DC magnetic coils at the valves.
When the voltage supply is turned on, the filter control automatically operates for previously
specified cleaning periods without any need of external intervention.
The filter controllers NF-8HD / NF-16HD have a differential pressure transmitter built-in.
The filter control system is enclosed in an electrical box with an IP65 safety classification.
The filter controllers are suitable for outdoor installation and can be installed directly on the
pressure vessel (with installation mountings).
The control system is entirely assembled and tested.
Connection.
The filter control system NF-8HD is mounted right in front of the first 8 valves. If more than
8 valves are present, an NF-8E expansion unit is mounted immediately in front of the next 8
valves or a NF-16HD can be used. There may be up to 9 NF-8E / NF-16E expansion units at-
tached to the main control NF-8HD / NF-16HD. Where there are more than 160 valves in the
filter, several NF-8HD / NF-16HD and NF-8E systems must be used.
After the control boxes have been set up, the valves can be attached to the terminals V1, + to
V8, + (at NF-8HD) or to V16, + (at NF-16HD).
Subsequently, in the case where NF-8E is used, the electrical controllers can be interlinked as
shown in Fig. 7. (WARNING ! No bridge may be connected to the output terminals of the last
unit, the terminals remain open).

01AUG 1005GB Cat.20 / Tab. 05.91 / Page 05.02
For installation of the controller, connect the mains voltage to the terminals in accordance
with the regulations. If a different mains voltage was not expressly ordered and was not given
on the voltage label, mains voltage of 230V AC 50-60 Hz (terminals L230, N, PE) or 110V
AC 50-60 Hz (terminals L110, N, PE) is always to be connected.
In order to attain a proper plant operation, the filter controller should be turned on and off via
the terminals E1(10) and E2 (11) or select DTC Mode 3. Application of the down-time-
cleaning functions is a condition on all Dantherm Filtration guarantees. The set of con-
tacts is potentialfree and is activated most appropriately by an auxiliary relay in the fan con-
trol system:
•Connecting the contacts E1, E2 sets the controller in operation.
•Disconnecting the contacts E1, E2 in DTC mode 1 means that the down-time-cleaning
process starts and when finished the filter controller stops. In DTC mode 2 starts the
down-time-cleaning-process only if the Delta-P DTCmax limit is exceeded in the last op-
erating period.
•In DTC mode 3 starts the down-time-cleaning process when the Delta-P DTCmax limit is
exceeded in the last operating period and the pressure afterwards reached the Delta-P
DTCmin limit.
Where the dust removal system includes automatic components, these should also function
during down-time-cleaning periods. Signals for this purpose are available at the terminals S1
and S2. (Signal if compressed air cleaning is activated, no signal if e.g. Delta P is below DP-
MIN during operation).
The hose connections P1 and P2 are to be connected to the hose connections on the filter as
shown in fig. 8. The hose connection is for hoses with 4 mm internal and 6 mm external di-
ameter.
The pressure gauge cell is suitable only for measuring non-aggressive, dry gases and must be
shielded against pressures exceeding 12.000 Pa.
Cable installation
All unused cable plugs should be taken off and replaced with dummy plugs.
Care should be taken to tighten the screws on all cable plugs firmly, to place them directly
against the cable and to prevent any penetration of moisture.
Displaying and parameter setting
Selecting the parameter:
To change from the operating mode to the parameter selecting mode press the ∆and ∇-
buttons (Fig. 4, 2.1 and 2.3) for more than 3 seconds. Go through the parameters by pressing
the ∆-button.
Parameter setting:
To change the value of the selected parameter, go to the parameter setting mode by pressing
the M button for more than one second.
The ∆button Change the value to a higher value
The ∇button Change the value to a lower value

01AUG 1005GB Cat.20 / Tab. 05.91 / Page 05.03
To save the new values, press the M button for more than 3 seconds. The controller automati-
cally returns from the parameter setting mode to the parameter-selecting mode when the val-
ues are saved.
Returning to the operating mode:
Before returning to the operating mode, change from the parameter setting mode to the pa-
rameter-selecting mode as described above. To return from the parameter-selecting mode
(from any parameter) to the operating mode, press both the ∆and the ∇button for more than 3
seconds. If no buttons are activated, the operating mode is automatically returned to after 4
minutes (evt. new parameter limits are not saved).
Param.
No. Text in LCD Function Ex works setting Range
00 DP-MIN ∆P –MIN 700 Pa 260-4000 Pa
01 DP-MAX ∆P – MAX 1300 Pa 280-4400 Pa
02 DP-ALARM ∆P Alarm 2300 Pa 300-5000 Pa
03 Pulse time# Puls time 60 ms 30-300ms
04 Interval time Interval time 10 4-500 s
05 DTC Interval time DT interval time 6s 2-100 s
06 Total valve no..# # of valves 0 0-160
07 DTC Down Time Cl.# Down-time cycles 6 0-32
08 DTCmax# Parameter for Down-time
Method 2
1000 280-4000 Pa
09 DTCmin# Parameter for Down-time
Method 3
260 260-2000 Pa
10 Hours in operati## Operating hours 0-250000 h
11 Text Language Languages ** Different languages are
available
12 DP-Display range Display range Pa Pa – Inch / WC
13 DTC Cleaning Mod# 3 different Down-time modes available 2 1-3
14 Test mode 0=Test off
1=Valve test
2=Start up test
3=∆p-trimming test
4-7=test of relays and display
0 7
15 Display Contrast 68 10-200
16 Service Run Hours Service – operating hours
17 Ser. Run Hours Al. Service – operating hours – alarm 3000 h 0-25000 h
18 Ser. Run Hou. Code Service – operating hours – code ## ##
19 ∆p-Mode ∆p-Mode On On / Off
20 Setting Lock Parameters cannot be changed - Code ## ##
** Presently English, Danish, French, German.
# Locked if parameter no. 20 is ON
## Cannot be changed.
Setting of the valves on the main unit takes place in the setting mode.

01AUG 1005GB Cat.20 / Tab. 05.91 / Page 05.04
State of Operation
The state of operation is indicated by the 3 light emitting diodes (LEDs) (Fig. 4, 1.1, 1.2, and
1.3) and the filter differential pressure is indicated in plain text.
LED 1.1 (ON): is illuminated if the unit is operational.
LED 1.2 (> ∆pMIN) is illuminated if the differential pressure is higher than ∆pMIN.
LED 1.3 (>∆pMAX) is illuminated if the differential pressure is higher than ∆pMAX.
LED 1.1 + 1.2 + 1.3 flashes: Alarm – ∆pMAX is exceeded.
Alarm - caused by other reasons: is only indicated by the terminals A1, A2 and A3 (Fig. 5,
3.2).
∆p-text field: The differential pressure is displayed in plain text.
Test operation
Go to the parameter “test operation” and select one of the following testmodes:
In Test mode 0
The test operation is de-activated.
In Test mode 1
Testing the valves. The valves are tested one by one and are displayed in the text field.
In Test mode 2
The state of operation is displayed in the text field.
In Test mode 3
For technical purposes. The value for the AD-converter is displayed.
In Test mode 4-7
The LED’s and the relays are tested and displayed.
∆p-Mode
The ∆p-MIN and ∆p-MAX limits control the filter cleaning.
Setting of ∆p–MODE. See “ Displaying and setting parameters” – parameter no. 19.
If the cleaning procedure controlled by the differential pressure is de-activated, the following
text is displayed “Delta-P Mode OFF”.

01AUG 1005GB Cat.20 / Tab. 05.91 / Page 05.05
DTC Down-Time Cleaning
The DTC is activated differently dependent of the selected method.
DTC Mode 1:
Fig. 1: In DTC Mode 1 the down-time cleaning procedure is started on the terminals E1 and E2
(Fan stops: E1-E2 open)
DTC Mode 2:
Fig. 2: In DTC Mode 2 the down-time cleaning procedure is only started after stopping the fan and if the
∆p-DTCmax limit is exceeded during operation. (Fan stop: E1-E2 open)

01AUG 1005GB Cat.20 / Tab. 05.91 / Page 05.06
DTC Mode 3:
Fig. 3: In DTC Mode 3 the down-time cleaning procedure is started when the pressure comes under the ∆p-
DTCmin limit, but only if the ∆p-DTCmax has been exceeded. The terminals E1 and E2 are not taken
into account.
Cleaning in connection with the start/stop output (external ∆p-terminal):
The terminals D1 and D2 can be bridged with a potentialfree switch. The cleaning procedure
can be seen from the below table:
„∆p-Mode OFF“
Switch (terminals D1,D2) Cleaning
open ON
closed OFF
„∆p-Mode ON“
Switch (terminals D1,D2) Differential pressure ∆p Cleaning
open ∆p > ∆p MAX ON
closed ∆p > ∆p MAX OFF
open ∆p < ∆p MIN OFF
closed ∆p < ∆p MIN ON
Delta-P DTCmax

01AUG 1005GB Cat.20 / Tab. 05.91 / Page 05.07
Final inspection after installation.
•Check that the circuit voltage is 230V AC 50-60 Hz.
•Monitoring of valve and unit function by starting the test operation.
•The down-time-cleaning procedure is tested by briefly opening and closing the terminals
E1 and E2 (first select DTC mode 1)
•The pressure difference action can be tested or simulated. By squeezing the top hose (in-
side the control box) with the fingers until the text indicates an increasing pressure, its ef-
fect can be simulated. When ∆p-MAX is exceeded the cleaning procedure is activated.
When the pressure sinks below ∆p-MIN , the cleaning procedure is stopped until Delta p-
MAX is once again exceeded.
•Check whether the covers on the electrical controllers are properly and tightly mounted.
Specifications
Application Specifications Terminals
Mains voltage 230 V AC +/-10%
110 V ... 120 V AC +/-10%
1, 3
2, 3
Output voltage Approx. 24 V DC 15 - 29 and
37 - 51
Signal input 24 V DC, potentialfree operation 10 - 13
Signal output Relay-output, max. 2 A, 250 V
or 1 A, 30 V DC
5- 9
Outputs for valves 1 ... 16, 24 V / DC, expansible to 160 outputs,
Output power 42 Watt
14 - 28 and
36 - 50
Output for extension unit Supply voltage and puls wire connection to the
extension units
30 - 33
Optional output F1, F2 4 ... 20 mA; 0 ... 5000 Pa;
internal resistance 500 Ω
No earth connection to the 4-20-mA-Signal
34, 35
∆p-range 0 ... 5000 Pa
Sensor Piezoelectrically secured against positive pres-
sure until 120 kPa
Fuse 0,4 A / T, 5 x 20 mm, 250 V
Temperature range -20°C to + 60°C
Protection Housing IP65
Dimensions W x H x D 250 x 160 x 90 mm
Weight ca. 0,8 kg
Mounting height max. 3000 m N.N.

01AUG 1005GB Cat.20 / Tab. 05.91 / Page 05.08
ON
>
pMAX
>
pMIN
1.1
1.2
1.3
2.1
2.2
2.3
D04001.cdr
1.1 LED “ON”, is illuminated if the unit is in operation.
1.2 LED “>∆p-MIN” is illuminated if the differential pressure is higher than ∆p MIN.
1.3 LED “>∆p-MAX” is illuminated if the differential pressure is higher than ∆p-MAX.
2.1 ∆-button
2.2 M-button
2.3 ∇-button
Fig. 4: LED’s and buttons on the front of the controller
1 2 3 4 5 6 7 8 9 101112131415161718192021222324252627282930313233
NPEA1A2A3S1S2E1E2D1D2
L230
L110
V1 + V2 + V3 + V4 + V5 + V6 + V7 + V8 + B1 B2 B3 B4
24V DC
. . . Ventile 2 bis 8
34 35 36 37 38 39 40 41 42 43 44 45 46 47 48 49 50 51 52 53
S3 S4 V9 +
V10
+
V11
+
V12
+
V13
+
V14
+
V15
+
V16
+
+
_
F1 F2
24V DC
. . . Ventile 10 bis 16
+24V DC
+24V DC
3.1 3.2 3.3 3.4 3.5 3.6 3.7
3.6
3.8 3.9
D04002.cdr
3.1 Power supply;1-3: 230 V AC, 2-3 110 V AC
3.2 Alarm relay, A1, A2, A3
3.3 Outfeeder in DTC operation, S1-S2
3.4 Down-time-cleaning E1-E2 (Fan start / stop signal inputs)
3.5 Start / Stop-input (external ∆p-switch)
3.6 Valve outputs; NF-8HD valves 1-8 ; NF-16HD valves 1-16
3.7 Data link to expansion units B1, B2, B3, B4
3.8 Data link to programming output signal (only NF-16HD)
3.9 Data link to Delta P external display 4-20 mA (only NF-8HD 4-20mA and NF-16HD)
Fig. 5:Terminals in the filter controller NF-8HD / NF-16HD

01AUG 1005GB Cat.20 / Tab. 05.91 / Page 05.09
1 2 3 4 5 6 7 8 9 10 11 12 13 14 15 16 17 18 19 20 21 22 23 24
X1 X2 X3 X4 V1 + V2 + V3 + V4 + V5 + V6 + V7 + V8 + B1 B2 B3 B4
24V DC
. . . Ventile 2 bis 8
4.1 4.2
NF-8E / DC
4.3
D04003.cdr
4.1 Data input terminals from main unit
4.2 Terminals for connection of 1 – 8 solenoid valves
4.3 Data output terminals for the following expansion units
Fig. 6: Terminals for the expansion unit NF-8E
30 313233 12345 789101112131415161718196 2021222324 1 2 3 4 5 6 7 8
-Y1 -Y8-Y2 ... -Y7 -Y9
B1 B2 B3 B4 X1 X2 X3 X4 V1 + V2 + V3 + V4 + V5 + V6 + V7 + V8 + B1 B2 B3 B4 X1 X2 X3 X4 V1 + V2 +
NF-8HD
(NF-16HD) NF-8E
(NF-16E) NF-8E
(NF-16E)
ON ON
OFF OFF
1234 567-
R E S E T R E S E T
S1 S2
D04004.cdr
Hinweis
Bei Erweiterungsgeräten älteren Typs muß die Anzahl
der anzuschließenden Ventile an den beiden DIP-Schaltern
eingestellt werden.
Rechts ist zum Beispiel die Einstellung für 6 Ventile dargestellt.
Fig. 7: Connection of expansion unit
Note
If old versions of the NF-8E expansion units are
used, the number of valves must be set on both
DIP-switches.
To the right there is an example, showing the set-
tin
g
of 6 valves.

01AUG 1005GB Cat.20 / Tab. 05.91 / Page 05.010
P1
M20
M20
M20
M25
M25
P2
D04005.cdr
12345678910111213
N
250 V AC
0,4 A
Alarm
ON / OFF
p extern
ON / OFF
Nur bei DTC-Modi 1 oder 2
230 V
50-60 Hz
PE A1 A2 A3 S1 S2 E1 E2 D1 D2
L230
L110
NF-8HD
M
A1
A2
A1
L1
N
A2
Fig. 8: Connection of compressed air hoses for NF-8HD
P1
P2
D04006.cdr
12 345678910111213
N
250 V AC
0,4 A
Alarm
ON / OFF
p extern
ON / OFF
Nur bei DTC-Modi 1 oder 2
230 V
50-60 Hz
PE A1 A2 A3 S1 S2 E1 E2 D1 D2
L230
L110
NF-16HD
M
A1
A2
A1
L1
N
A2
34 35
S3 S4
M20
M25
M25
M20
M25
M25
M20
Fig. 9: Connection of compressed air hoses for NF-16HD

01AUG 1005GB Cat.20 / Tab. 05.91 / Page 05.011
Resume
To reach the parameter selecting mode:
Press the ∇-button and the ∆-button for more than 3 seconds.
To select a parameter within the parameter selecting mode:
∇-button →Select a lower parameter
∆-button →Selects a higher parameter
To check the selected parameter
Shortly press the M-button. The parameter value is displayed for 1 second
To change the value of the selected parameter
Press the M-button for more than 1 second
Press the ∇-button select a lower parameter value
Press the ∆-button select a higher parameter value
Press the M-button again for more than 1 second and the new parameter value is saved.
To return to the operating mode
Press the ∇-button and the ∆-button for more than 3 seconds to return to the operating mode.
Parameter list; NF-8HD standard values in the ( ).
•∆p -MIN (700 Pa)
•∆p -MAX (1300 Pa)
•∆p -Alarm (2300 Pa)
•Puls time (60 ms) #
•Interval time (10s)
•Down-time-cleaning interval (6 s)
•Number of valves #
•Down-time cleaning DTC, number of cycles (6)#
•Delta-P DTCmax only in DTC mode 2 or 3 (1000 Pa)#
•Delta-P DTCmin only in DTC mode 3 (260 Pa)#
•Operating hours
•Languages
•Display range (Pa)
•DTC-mode (2) #
1. Fan solo
2. Fan + Delta-P DTCmax
3. Delta-P DTCmax + Delta-P DTCmin
•Test mode
0: Test OFF
1: Valve test
2: Start test
3: DP-trimming test
4-7: Relay and display test
•Display contrast (68)
•Service – operating hours
•Service – operating hours – alarm limit (3000 h)
•Service – operating hours – code (0)
•∆p – mode (ON)
•Parameter protection (ON): Marked with #

01AUG 1005GB Cat.20 / Tab. 05.91 / Page 05.012
D04008.cdr
>3 s
>3 s
>1 s
>1 s
∆
p
1 s
∆
p
2 s
n
max min
10 s
t
M
M
5 s
Fig. 10: Short description of how to check and change the parameters.

01AUG 1005GB Cat.20 / Tab. 05.91 / Page 07.03
Error diagnostics
Error Possible cause Recommended action
LED 1.1 Fig. 1 is not illuminated
and E1 and E2 are bridged.
•Power failure
•Fuse in controller defect
•The plant’s emergency stop is
activated
•Internal control error
•Check the circuit voltage
•Check the fuses.
•Replace the fuse.
•Check the emergency stop.
•Contact Dantherm Filtration
service
No valve activation •Defect lead connection
•Defect magnet coil
•Cycle interrupt
•Check cables and cable connec-
tions
•Replace magnet coil.
•Detach pressure difference me-
ter, change the settings and
check the hose connections, etc.
No down-time-cleaning •DTC cycle = 0
•No signal from fan
(DTC mode 1-2)
•Set other value
•Apply signal to terminals E1
and E2.
The cleaning is inefficient •Pause period too long
•Cleaning pressure too low
•Valve defect
•Pulse duration too short
•Cleaning cycle often disrupted
•Defect filter system
•Large-scale filters (>160 valves)
where only a part of the filter is
cleaned
•Reduce pause interval 04
•Adjust the pressure to 6-8 bar
(min. 5 bar).
•Pause too short, so pressure is
not reached.
•Check/replace valve.
•Can be modified in setting mode
after consultation with Dan-
therm Filtration.
•Check pressure difference meter
and hose connection.
•Check the filter’s operation in-
structions.
•Set the two main controllers to
the same setting values.
•Check if ∆p -MAX and ∆p -
MIN switching points are set
correctly.
Faulty display of the pressure differ-
ence
•Failure in the hose connections •Empty the hoses.
•Clean the hose connection on
the filter housing with com-
pressed air (blow direction fil-
ter, never in sensor direction).
•Remove any bending on the
hoses.
•Check the hoses inside the con-
trol unit for water, or the like.
NF-8E / NF-16E alarm •Valve setting wrong
•NF-8E / NF-16E controller de-
fect
•Check the number of valves
•Replace the defect controller

01AUG 1005GB Cat.20 / Tab. 05.91 / Page 07.04
ON
>
pMAX
>
pMIN
1.1
1.2
1.3
2.1
2.2
2.3
D04001.cdr
1.1 LED “ON”, is illuminated if the unit is in operation.
1.2 LED “>∆p-MIN” is illuminated if the differential pressure is higher than ∆p MIN.
1.4 LED “>∆p-MAX” is illuminated if the differential pressure is higher than ∆p-MAX.
2.4 ∆-button
2.5 M-button
2.6 ∇-button
Fig. 1: LED’s and buttons on the front of the controller
1 2 3 4 5 6 7 8 9 101112131415161718192021222324252627282930313233
NPEA1A2A3S1S2E1E2D1D2
L230
L110
V1 + V2 + V3 + V4 + V5 + V6 + V7 + V8 + B1 B2 B3 B4
24V DC
. . . Ventile 2 bis 8
34 35 36 37 38 39 40 41 42 43 44 45 46 47 48 49 50 51 52 53
S3 S4 V9 +
V10
+
V11
+
V12
+
V13
+
V14
+
V15
+
V16
+
+
_
F1 F2
24V DC
. . . Ventile 10 bis 16
+24V DC
+24V DC
3.1 3.2 3.3 3.4 3.5 3.6 3.7
3.6
3.8 3.9
D04002.cdr
3.1 Power supply;1-3: 230 V AC, 2-3 110 V AC
3.2 Alarm relay, A1, A2, A3
3.3 Outfeeder in DTC operation, S1-S2
3.4 Down-time-cleaning E1-E2 (Fan start / stop signal inputs)
3.5 Start / Stop-input (external ∆p-switch)
3.6 Valve outputs; NF-8HD valves 1-8 ; NF-16HD valves 1-16
3.7 Data link to expansion units B1, B2, B3, B4
3.8 Data link to programming output signal (only NF-16HD)
3.9 Data link to Delta P external display 4-20 mA (only NF-8HD 4-20mA and NF-16HD)
Fig. 2:Terminals in the filter controller NF-8HD / NF-16HD

01AUG 1005GB Cat.20 / Tab. 05.91 / Page 08.01
MAINTENANCE INSTRUCTIONS for the filter control unit NF-8HD / NF-16HD
Safety precautions
Adjustment of electrical controllers with the casing removed may only be carried out by spe-
cialised personnel and in full accordance with the stipulated safety rules.
The top cover of the electrical control unit is shielded at low voltage except at the connection
terminals for the voltage supply.
230 V AC or 110 V AC are applied at the terminals to the voltage supply L230 (1), L110 (2)
and N (3) (or possibly another especially prescribed voltage)
In addition the safety recommendation NF10 must be observed.
Maintenance
A stable operating filter control system is achieved by regular maintenance.
•Check the pressure drop on LED’s Daily on plant operation start up
•Acoustic valve control Monthly / after every 300 hours of operation#
•Check that down-time-cleaning is active Monthly / after every 300 hours of operation
•Clean the controller with a moist cloth Monthly / after every 300 hours of operation
•Activate ∆p-MAX
Activate / de-activate ∆p-MIN
Monthly / after every 300 hours of operation
#The shorter of the two periods is to be taken.

01AUG 1005GB Cat.20 / Tab. 05.91 / Page 09.01
LIST OF SPARE PARTS for the filter control NF-8HD / NF-16HD
Whenever there is an error in the control system itself, then either the set of fuses or the whole
constrol unit has to be replaced.
Fuses Type: T 0,4 A, 250V DC, 5x20 mm
Main controller Type: NF-8HD (art. no. 388015.090)
NF-16HD (art. no. 388015.095)
Extension unit Type: NF-8E (art. no. 388015.065)
NF-16E (art. no. 388015.067)
Chip for West European languages: Art. no. 388015.098
Chip for East European languages: Art. no. 388015.099
When ordering please provide the circuit voltage.
In the presence of a fault the whole combination is to be changed.
This manual suits for next models
1
Table of contents
Other Dantherm Controllers manuals
Popular Controllers manuals by other brands
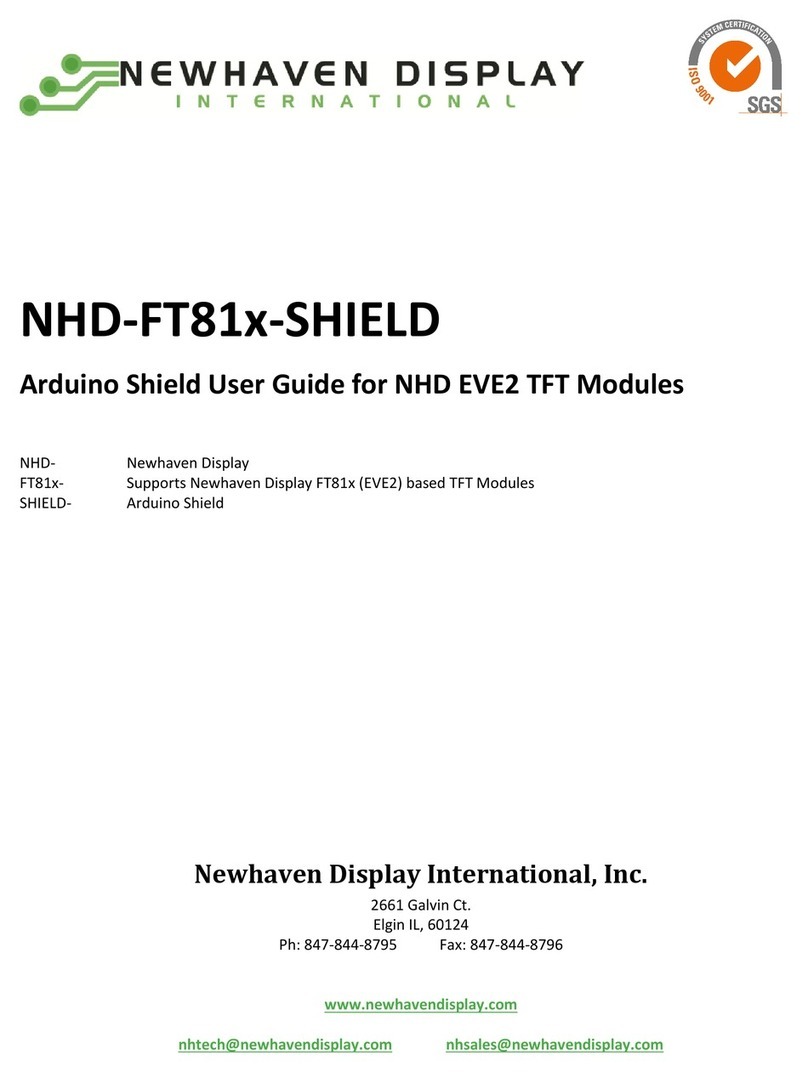
Newhaven Display International
Newhaven Display International NHD-FT81x-SHIELD user guide
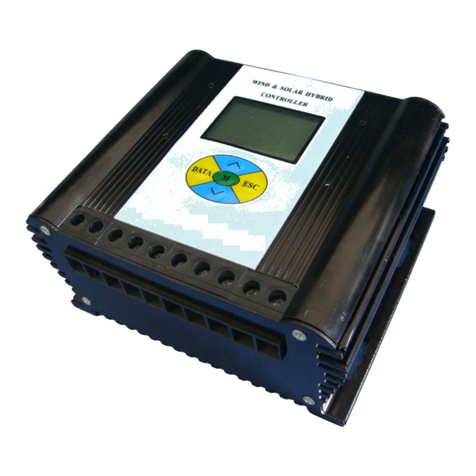
Capa Energy
Capa Energy DWSC602 Series Operating instructions manual

Spreco
Spreco S401 Installation and operating instructions
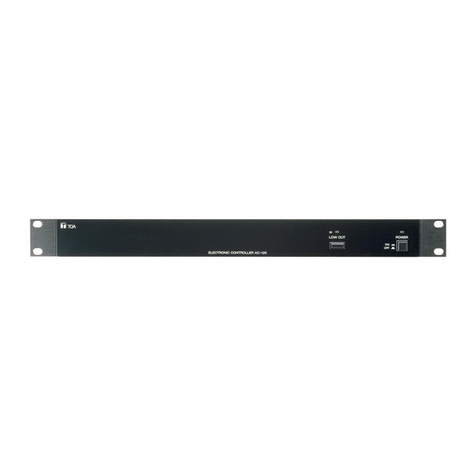
Toa
Toa AC-120 operating instructions
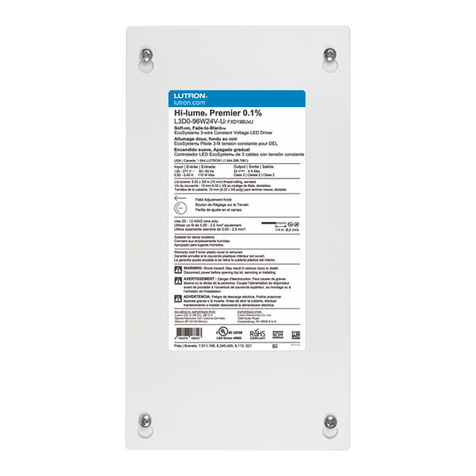
Lutron Electronics
Lutron Electronics LHD0-96W24V-U UL Installation

Danfoss
Danfoss AME 10 operating guide
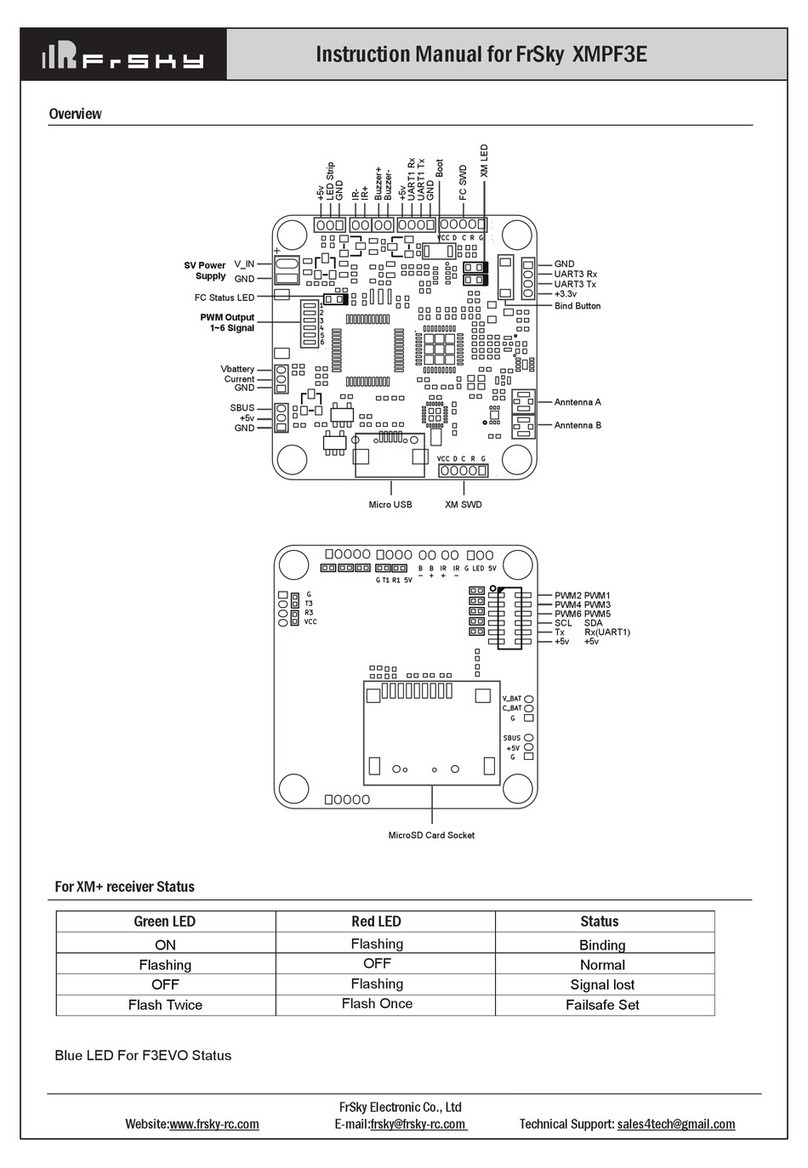
FrSky
FrSky XMPF3E instruction manual
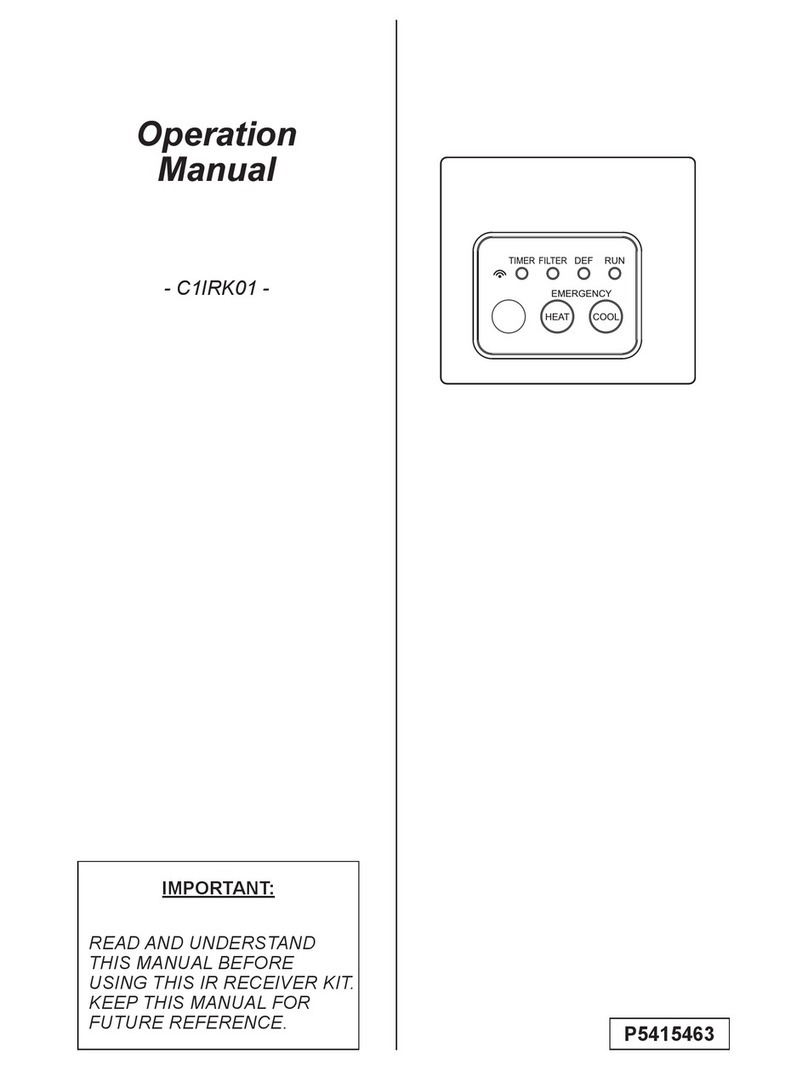
Johnson Controls
Johnson Controls Hitachi C4IRK01 Operation manual
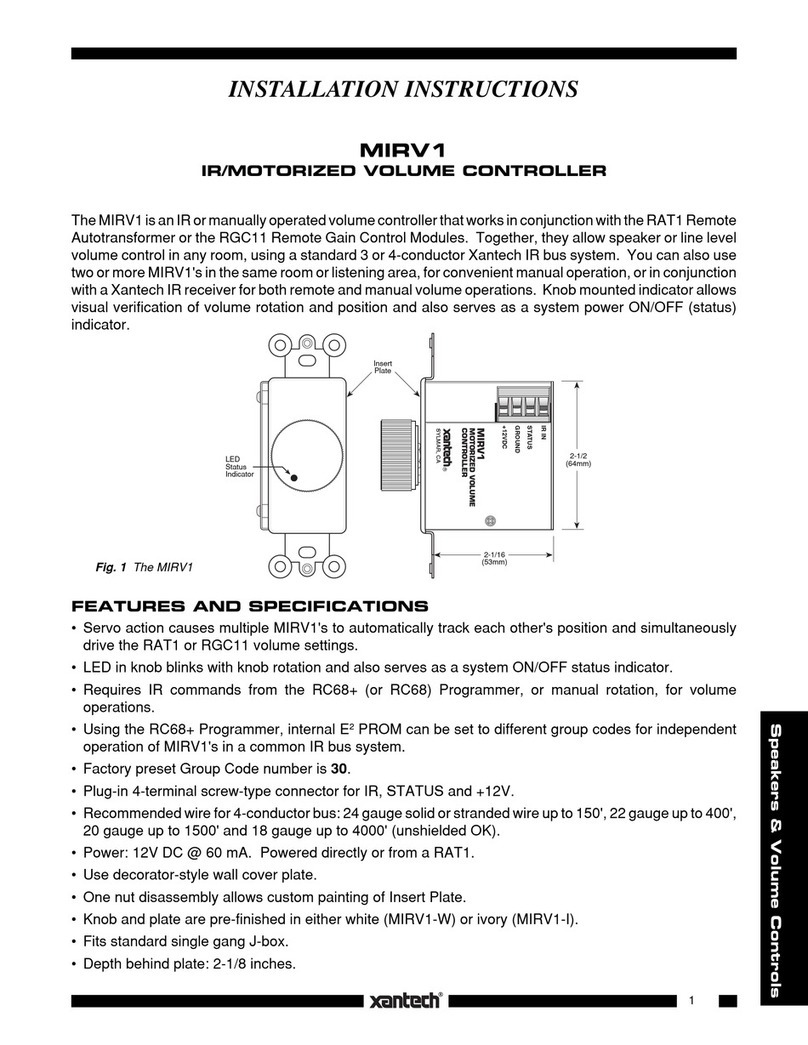
Xantech
Xantech MIRV1 installation instructions
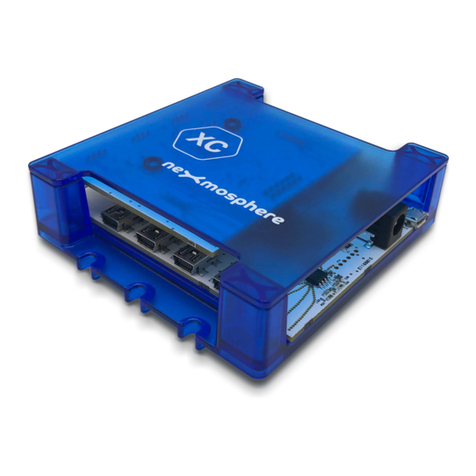
Nexmosphere
Nexmosphere XC-741 quick start guide
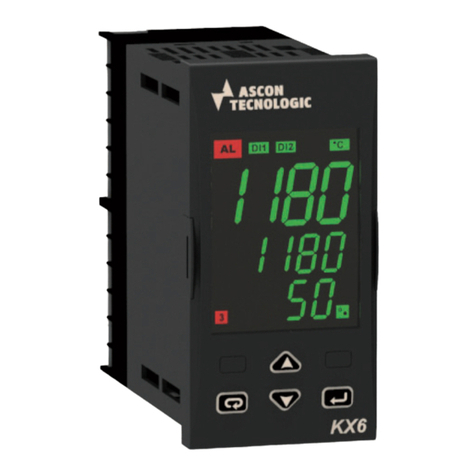
Ascon tecnologic
Ascon tecnologic KX6 Series Engineering manual
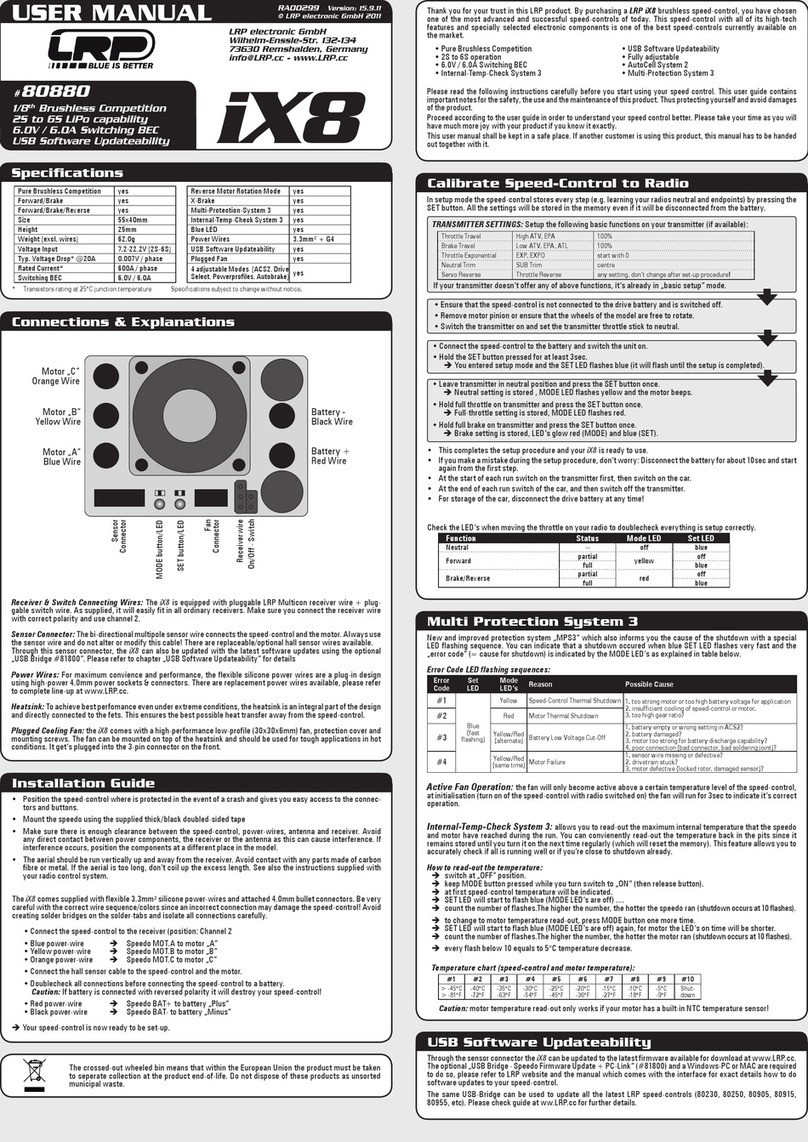
LRP electronic
LRP electronic iX8 user manual