Garnet SPILLSTOP 815 User manual

Page 1815 Manual
Printed in Canada
www.garnetinstruments.com
TM
SPILLSTOP
Overll Prevention System
MODEL 815 MANUAL

Page 2 815 Manual
Table of Contents
CHAPTER 1 - OVERVIEW ...................................................................... 3
CHAPTER 2 - FEATURES AND OPERATION......................................... 4
CHAPTER 3 - INSTALLATION GUIDE ................................................... 7
CHAPTER 4 - WIRING DIAGRAMS...................................................... 11
CHAPTER 5 - TROUBLESHOOTING GUIDE......................................... 12
CHAPTER 6 - SERVICE AND WARRANTY INFORMATION................ 13
MAIL IN WARRANTY .......................................................................... 15
GARNET
SPILLSTOP
Overll Prevention System
MODEL 815 MANUAL
815 Manual_v4.0 25-Jan-18
TM

Page 3815 Manual
C
ongratulations on purchasing the Garnet Instruments Model
815 SPILLSTOP overll prevention system. The SpillStop
represents the state of the art in spill control for crude oil and
chemical hauling. The SpillStop is designed to work in conjunction
with the Garnet Model SEELEVEL PROSERIES
™
and 808P2 SEELEVEL
SPECIAL
™
gauges to assist the truck operator with truck tank
overll protection in applications where the uid is loaded with a
PTO driven pump.
The system is dependent upon the operator to determine
SEELEVEL
oat movement, and is intended as an emergency backup system
in the event that the operator is unable to shut down loading
when the tank is full.
The
815
is easy to install and operate, and is designed to withstand
the rigors of mobile applications. It consists of a truck mounted
controller and a small module that inserts into the
SEELEVEL
gauge
(the module is built in to the
SEELEVEL
SPECIAL
™ gauge). An optional
indicator is available to verify proper plug connections for tractor
trailer applications. The system can shut down the truck engine or
hydraulically operated loading pumps. A horn alarm is provided
to warn of an impending shut down condition.
The Model 916 Programmer is used to set the alarm points in the
SEELEVEL
gauge, which determines the horn alarm and shutdown
points. These points can be reprogrammed as required for
different hauling applications.
CHAPTER 1 - OVERVIEW

Page 4 815 Manual
The following sketch shows the basic components and
connections of the SpillStop for a tractor trailer application.
A body truck application would be similar except that the 7 pin
plug & socket would not be required since the tank is never
disconnected from the truck.
SPILLSTOP
INDICATOR
PLUG MODULE
IN-CAB SPILLSTOP
CONTROLLER
7 PIN PLUG
& SOCKET
810PS2 SEELEVEL CONTAINING
SPLLSTOP GAUGE MODULE
OR 808P2 SEELEVEL SPECIAL
WIRING
810-X Bar
SHUT
DOWN
BYPASS
SHUT
DOWN
BYPASS
UNPLUGGED
SPILLSTOPALARM CONTROLLER
SHUTDOWN
ENGINE PUMPON
HORNALARM
TANKEMPTY
RE-ARM
HORN
BYPASS
HORN
BYPASS
SHORTCIRCUIT MANUAL
RE-ARM
GARNET
MADEINCANADA
The SpillStop consists of three main components: the controller
in the cab of the truck, the optional plug module inside the 7
pin socket housing on the trailer, and the gauge module inside
the SeeLeveL truck gauge (the gauge module is built into the
808P2 and 810PS2 displays).
The gauge module installs inside the SeeLeveL gauge display,
and converts the alarm signals from alarms 1, 2, and 3 in the
SeeLeveL gauge to a pulse signal that is sent along a single wire
to the controller. The plug module monitors the signal between
the gauge module and the controller and turns on the SpillStop
indicator only if the 7 pin plug is connected and the signal is
getting from the gauge to the controller. The controller monitors
and displays the alarm status of the gauge, and activates a horn
if the uid level in the truck tank is at the full point, and shuts off
the vehicle engine if a spill is imminent. The standard controller
can accommodate 2 compartments, and the double controller
can accommodate up to 4 compartments. Each compartment
is treated independently and has its own controls, so full spill
protection is maintained for each compartment even if another
compartment has already been lled.
CHAPTER 2 - FEATURES AND OPERATION

Page 5815 Manual
WARNING: The SPILLSTOP TM is intended as an emergency
backup system only, and is not intended as a substitute for
operator diligence during the loading process.
The operation of the SpillStop during the loading operation is as
follows: When the tank is empty, the green TANK EMPTY indicator
is on, the horn is off, and the engine is allowed to run. As the
uid level rises, the empty indicator goes out. When the horn
alarm point is reached, the yellow HORN ALARM indicator comes
on and the horn is activated with a 0.5 second on, 0.5 second
off cycle. Depressing the horn alarm BYPASS at this point will
silence the horn. If the uid level continues to rise and reaches
the engine shutdown point, the red SHUTDOWN indicator will
come on, the green ENGINE ON indicator will go out, and the
truck engine will be shut off. Depressing the shutdown BYPASS
at this point will re-light the ENGINE ON indicator and allow the
engine to be restarted. When a BYPASS switch is depressed, the
alarm indicator stays on and the red bypass indicator comes on.
As the tank is unloaded the alarm indicators will go out when the
uid level drops below the alarm points, and the bypasses will be
cleared (the system is re-armed) when the TANK EMPTY indicator
comes back on. There is no need for the operator to re-arm the
system, removing the possible operator error of forgetting to re-
arm. If the tank is not lled to the alarm point, the system can
still be bypassed to prevent sloshing from sounding the horn or
shutting down the engine during driving. If a single tank is to be
lled from more than one location, the alarms can be bypassed
during driving between loading sites, and the system re-armed
with the MANUAL RE-ARM switch to re-establish spill protection
for the second load.
The SpillStop has a number of convenience and safety features
built into the system. When the tank is empty, the bypasses will
not work, preventing accidental bypassing when the driver is
leaving the cab to begin loading. Delays are incorporated into the
system to prevent noise spikes or momentary bad connections
from disrupting operation. A short circuit in the wiring to the
gauge, or plugging the SpillStop plug into the trailer lighting
socket, lights the red SHORT CIRCUIT indicator and shuts down
the engine. An open circuit in the wiring to the gauge, or a
disconnection of the plug to the trailer, lights the red UNPLUGGED
indicator, sounds the horn, and shuts down the engine. These
alarms can be bypassed to allow operating the tractor without the
trailer connected. The pulse signal between the gauge and the
controller cannot be corrupted by poor connections or moisture in
the wiring; if the signal is too badly degraded it defaults directly to
an open or short circuit condition. A failure of the SeeLeveL gauge
defaults to the engine shutdown alarm condition. The gauge and

Page 6 815 Manual
plug modules cannot be damaged by short circuits or by plugging
the trailer light plug into the SpillStop socket. The controller will
operate at truck voltages from 8 to 16 volts, and draws less than
1/4 amp so it can operate from any convenient 12 volt circuit.

Page 7815 Manual
Refer to the appropriate wiring diagram during installation of
the SpillStop system. The wiring diagrams are in section D).
1. Pick a spot in the cab of the truck for the SpillStop controller
box to be mounted. Do not mount the controller where it can
be kicked. It is recommended that the controller be mounted
to the right of the PTO control. Use the existing studs in the
box walls to mount the controller, do not put additional screws
into the box as they may contact and damage the circuitry
inside. If the wiring connections on the back of the box are
hard to access after the box is mounted, leave it unmounted
for now until it is wired up.
2. Remove the front panel of the SeeLeveL gauge(s) and silicone
the gauge module into the base of the enclosure. Note that
one side of the display face sticks down into the enclosure so
you will need to mount the gauge module so that the display
face can still be mounted properly. Connect the YELLOW,
ORANGE, BLACK and GREEN wires to the matching coloured
wires on the display. The RED wire, the gauge module signal
wire, will connect to the SpillStop compartment terminal. If
an 808PA SeeLeveL Special is being used rather than an 810PS
SeeLeveL, no gauge module is required since it is built into
the SeeLeveL Special display where the signal wire is the
GREEN wire. If you are connecting a gauge module to an
older 810 SeeLeveL with a terminal block mounted on a circuit
board in the base of the box then connect YELLOW to Alarm 1,
ORANGE to Alarm 2, and BLACK to Alarm 3. The GREEN wire
is ground. Note that Alarms 1, 2 and 3 are the 2nd, 3rd, and
4th terminals from the left on the terminal block. Ground is
on the far right side of the terminal block.
IMPORTANT: When connecting wiring, all terminal ends should
be soldered to the wire. Any multiple wire hookups to the controller
terminal blocks must at least be twisted together, and preferably
soldered. When tightening terminal block screws which retain the
wires, retorque the terminals after 1/2 hour to allow the terminals
to take a “set”.
Follow these instructions for a tractor trailer installation:
3. Mount a standard 7 pin socket to the front of the trailer and
a 7 pin plug and cable from the tractor. Make sure there is
room inside the socket housing for the plug module.
CHAPTER 3 - INSTALLATION GUIDE

Page 8 815 Manual
4. Mount the SpillStop indicator light (not supplied -- use a
standard clearance light) in a convenient location. Label the
indicator as an equipment monitoring light.
5. Route a single wire from each gauge to the socket housing.
Connect the gauge end of this wire to the wire coming out of
the gauge module. From the inside, seal the wire entry into
the enclosure with RTV silicon rubber. Make sure that the RTV
fully surrounds the wire where it goes though the tting.
6. Route a single wire from the socket housing to the SpillStop
indicator light. Connect this wire to the hot side of the light,
and ground the other light terminal.
7. Insert the plug module into the socket housing and connect
the YELLOW plug module wire to the wire from the SpillStop
indicator.
8. Wire the socket as follows:
a. White socket terminal to ground and to the GREEN plug
module wire.
b. Blue socket terminal to the RED plug module wire.
c. Brown socket terminal to the wire from gauge #1, and to
one of the GREY plug module wires.
d. Green socket terminal to the wire from gauge #2, and to
one of the GREY plug module wires.
e. Red socket terminal to the wire from gauge #3, and to one
of the GREY plug module wires.
f. Yellow socket terminal to the wire from gauge #4, and to
one of the GREY plug module wires.
Note: If there are left over GREY plug module wires, connect
them to one of the used ones. If this is not done the indicator will
not work. For one or two gauge applications, there are two GREY
plug module wires, and for three or four gauge applications, there
are four GREY plug module wires.
9. Wire the plug so that the socket colors can be identied at the
other end of the 7 conductor cable. Route the cable to the
SpillStop controller.
Follow these instructions for a body truck installation:
1. Route a single wire from each gauge to the SpillStop controller.
Connect the gauge end of this wire to the wire coming out of
the gauge module. From the inside, seal the wire entry into
the enclosure with RTV silicon rubber. Make sure that the RTV
fully surrounds the wire where it goes though the tting.

Page 9815 Manual
2. Make sure that the gauge(s) are well grounded to the same
ground as the controller.
Follow these instructions for all installations:
1. Connect the wire from each gauge module to the
corresponding compartment terminal on the back of the
controller.
2. If there are unused controller compartment channels, connect
a dummy gauge module between the unused compartment
terminal and ground. The RED wire goes to the terminal,
and the green or black wire to ground. This will simulate an
EMPTY condition on the unused compartment.
3. Connect a controller GROUND terminal to ground. All of
the controller GROUND terminals are internally connected
together.
4. Connect the controller 12V INPUT terminal to a 12 volt source.
All of the controller 12V INPUT terminals are internally
connected together. This 12 volt source should be an ignition
source so the truck battery is not drained when the truck is off.
Jumper the 12V INPUT to one of the SHUTDOWN terminals.
5. Locate an electrical shutoff switch (such as the key switch) in
the truck. Break the connection to the switch and connect
the two wire ends to the contact terminals (#30 & #87) of the
auxiliary ESD relay (supplied). Connect one of the auxiliary
ESD relay coil terminals (#86) to ground and the other coil
terminal (#85) to the remaining SHUTDOWN terminal on the
SpillStop controller. It is a good idea to mount the auxiliary
ESD relay close to the existing shutoff wiring to minimize any
extra wire length in the truck shutoff circuit.
6. Connect the PTO sense relay (supplied) as shown in the wiring
diagram. Use a standard clearance lamp (not supplied) as the
PTO indicator light. The PTO sense relay functions so that the
ESD (Engine Shutdown) relay cannot operate unless the PTO
is engaged. This prevents the engine from being accidentally
shutdown if uid sloshing occurs and raises the oat above
the engine shutdown point.
7. Connect the HORN terminal to the electrical horn switch (or
button).
8. Program the alarm points in the gauges. Program alarm #1
as SHUT DOWN at the point where the engine should be shut
down. Program alarm #2 as SHUT DOWN at the point where
the horn alarm should come on. Program alarm #3 as SHUT
DOWN at the point where the tank is considered empty. See
the 810PS Shop or 916 manuals for programming details.

Page 10 815 Manual
Example: The tank is 58 inches high, with a bottom reading of 4.6
inches. Suggested points would be alarm #1 at 55 inches, alarm
#2 at 53 inches, and alarm #3 at 6 inches.
WARNING: To properly determine the ESD point, raise the
SeeLeveL oat to the top of the tank, and then lower the oat by
at least one inch. Record this point as the ESD value. Ensure
that the truck operator is aware of this value. Ensure that
this value and the empty reading are recorded in the provided
area in the operator’s manual. The truck operator must be
given the owners manual upon delivery with all front page
data lled in.
9. Put the covers back on the SeeLeveL gauges, and test the
system for proper operation by lifting the oat(s). As the oat
is raised, the horn should turn on rst, and then the engine
or hydraulic pump should shut off with the oat at least one
inch below the top of the tank. Bypass the horn and ESD and
ensure that the bypasses are removed with the oat at least
one inch above the bottom of the tank.
EXISTING
KEY
SWITCH
FROM +12 VOLT
BREAK
BODY TANK WITH PUP WIRING DIAGRAM
#85#86
#30#87
AUX
ESD
RELAY
- COIL -
- CONTACTS -
UNITS BUILT SINCE SN 0049
EXISTING
HORN
SWITCH
12V INPUT
COMP 1
COMP 2
GROUND
SHUTDOWN +
HORN
GROUND
SPILL STOP CONTROLLER
12V INPUT
GROUND
SHUTDOWN -
12V INPUT
12V INPUT
7 PIN
PLUG
7 PIN
SOCKET
PLUG BETWEEN TRAILER
BLACK GREEN
SeeLeveL
Special
GAUGE
BLACK GREEN
SeeLeveL
Special
GAUGE
LIGHT
INDICATOR
PTO
PTO PRESSURE SWITCH
(CLOSED WHEN PTO ENGAGED)
#85#86
#30
#87
PTO
SENSE
RELAY
COIL
CONTACTS
#87A
NOTE: Relay contacts 30 and 87A are the
normally closed (NC) contacts.
Relay contacts 30 and 87 are the
normally open (NO) contacts.
TO FUEL SHUTOFF
FROM HORN
Use Brake Light Switch
Existing Ground
Existing Ground
Use blue wire for this circuit. This must be
a dedicated line (unshared).
Note 1: Use 12 gauge wire on this circuit.
See Note 1 below
Note 2: 12V input must be common with fuel circuit
to provide uninterrupted power during startup.
See Note 2 below
Mount both relays under dash to
minimize length of heavy wire.
Gauges may be substituted with
810PS with 815 Gauge Modules
installed.

Page 11815 Manual
CHAPTER 4 - WIRING DIAGRAMS
EXISTING
KEY
SWITCH
FROM +12 VOLT
BREAK
BODY TANK WITH PUP WIRING DIAGRAM
#85#86
#30#87
AUX
ESD
RELAY
- COIL -
- CONTACTS -
UNITS BUILT SINCE SN 0049
EXISTING
HORN
SWITCH
12V INPUT
COMP 1
COMP 2
GROUND
SHUTDOWN +
HORN
GROUND
SPILL STOP CONTROLLER
12V INPUT
GROUND
SHUTDOWN -
12V INPUT
12V INPUT
7 PIN
PLUG
7 PIN
SOCKET
PLUG BETWEEN TRAILER
BLACK GREEN
SeeLeveL
Special
GAUGE
BLACK GREEN
SeeLeveL
Special
GAUGE
LIGHT
INDICATOR
PTO
PTO PRESSURE SWITCH
(CLOSED WHEN PTO ENGAGED)
#85#86
#30
#87
PTO
SENSE
RELAY
COIL
CONTACTS
#87A
NOTE: Relay contacts 30 and 87A are the
normally closed (NC) contacts.
Relay contacts 30 and 87 are the
normally open (NO) contacts.
TO FUEL SHUTOFF
FROM HORN
Use Brake Light Switch
Existing Ground
Existing Ground
Use blue wire for this circuit. This must be
a dedicated line (unshared).
Note 1: Use 12 gauge wire on this circuit.
See Note 1 below
Note 2: 12V input must be common with fuel circuit
to provide uninterrupted power during startup.
See Note 2 below
Mount both relays under dash to
minimize length of heavy wire.
Gauges may be substituted with
810PS with 815 Gauge Modules
installed.

Page 12 815 Manual
IF problems are encountered, check the following:
1. Is the controller getting at least 8 volts?
2. Are all the wires properly connected, with no short circuits?
3. Are the 808P2 or 810PS2 SeeLeveL gauges working properly?
4. Are the 808P2 or 810PS2 gauges programmed properly?
5. If the horn is not sounding, does the horn itself work?
To test the various components, substitute a known good
component to see if the rest of the system is working. If the
engine will not start, ground the green wire from the controller.
If the engine still does not start, the problem is in the relay or
associated wiring. If the engine now starts, and the controller
indicates no shutdown alarm (or is bypassed), then the controller
is bad. If the horn will not sound, ground the orange wire from
the controller. If the horn still does not sound, the problem is in
the horn or associated wiring. If the horn now sounds, and the
controller indicates a horn alarm that is not bypassed, then the
controller is bad.
CHAPTER 5 - TROUBLESHOOTING GUIDE

Page 13815 Manual
CHAPTER 6 - SERVICE AND WARRANTY INFORMATION
T
he warranty will only apply only if the warranty card that is shipped with the equipment
has been returned to Garnet Instruments Ltd.
DISCLAIMER OF WARRANTY ON HARDWARE
Garnet Instruments Ltd. warrants equipment manufactured by Garnet to be free from defects
in material and workmanship under normal use and service for a period of one year from the
date of sale from Garnet or an Authorized Dealer. The warranty period will start from the date
of purchase or installation as indicated on the warranty card. Under these warranties, Garnet
shall be responsible only for actual loss or damage suffered and then only to the extent of
Garnet’s invoiced price of the product. Garnet shall not be liable in any case for labor charges
for indirect, special, or consequential damages. Garnet shall not be liable in any case for
the removal and/or reinstallation of defective Garnet equipment. These warranties shall not
apply to any defects or other damages to any Garnet equipment that has been altered or
tampered with by anyone other than Garnet factory representatives. In all cases, Garnet will
warrant only Garnet products which are being used for applications acceptable to Garnet and
within the technical speci cations of the particular product. In addition, Garnet will warrant
only those products which have been installed and maintained according to Garnet factory
speci cations.
LIMITATION ON WARRANTIES
These warranties are the only warranties, expressed or implied, upon which products are
sold by Garnet and Garnet makes no warranty of merchantability or tness for any particular
purpose in respect to the products sold. Garnet products or parts thereof assumed to be
defective by the purchaser within the stipulated warranty period should be returned to the
seller, local distributor, or directly to Garnet for evaluation and service. Whenever direct
factory evaluation, service or replacement is necessary, the customer must rst, by either
letter or phone, obtain a Returned Material Authorization (RMA) from Garnet Instruments
directly. No material may be returned to Garnet without an RMA number assigned to it or
without proper factory authorization. Any returns must be returned freight prepaid to: Garnet
Instruments Ltd, 286 Kaska Road, Sherwood Park, Alberta, T8A 4G7. Returned warranted
items will be repaired or replaced at the discretion of Garnet Instruments. Any Garnet items
under the Garnet Warranty Policy that are deemed irreparable by Garnet Instruments will be
replaced at no charge or a credit will be issued for that item subject to the customer’s request.
If you do have a warranty claim or if the equipment needs to be serviced, contact the
installation dealer. If you do need to contact Garnet, we can be reached as follows:
CANADA UNITED STATES
Garnet Instruments Ltd. Garnet Technologies Inc.
286 Kaska Road 201 M&M Ranch Road
Sherwood Park, AB T8A 4G7 Granbury, TX 76049
CANADA USA


MODEL NO. SERIAL NO.
DATE PURCHASED DATE INSTALLED
YR/MO/DAY YR/MO/DAY
COMPANY NAME
PRINCIPAL CONTACT
ADDRESS
TELEPHONE FAX
IN CANADA RETURN TO:
Garnet Instruments Ltd.
286 Kaska Road
Sherwood Park, AB T8A 4G7
CANADA
SENDER BAR SERIAL NO. (if applicable)
IMPORTANT: WITHOUT THE SERIAL NUMBER OF EACH UNIT IT IS
DIFFICULT TO DETERMINE WARRANTY VALIDITY
DEALERS NAME
WARRANTY CONTACT
ADDRESS
TELEPHONE FAX
IN UNITED STATES RETURN TO:
Garnet Technologies Inc.
201 M&M Ranch Road
Granbury, TX 76049
USA
IMPORTANT: RETURNING THIS CARD WILL ENABLE US TO NOTIFY YOU IN THE EVENT OF A PRODUCT RECALL OR TO SUPPLY YOU WITH REQUIRED PRODUCT SAFETY INFORMATION.
TO MAXIMIZE YOUR WARRANTY PLEASE REGISTER ONLINE AT www.garnenstruments.com OR MAIL THIS FORM IN TO GARNET.
LIMITED WARRANTY REGISTRATION
MAIL IN WARRANTY



Printed in Canada
www.garnetinstruments.com
CANADA
Garnet Instruments Ltd.
286 Kaska Road
Sherwood Park, AB T8A 4G7
USA
Garnet Technologies Inc.
201 M&M Ranch Road
Granbury, TX 76049
P: 780-467-1010
F: 780-467-1567
TF: 1-800-617-7384
P: 817-578-8601
F: 817-573-0005
TF: 1-877-668-7813
Table of contents
Other Garnet Controllers manuals
Popular Controllers manuals by other brands

Eaton
Eaton xComfort CAAE-01/03 Instruction leaflet
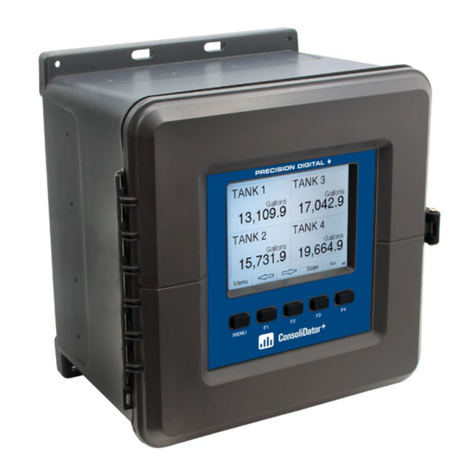
Precision Digital Corporation
Precision Digital Corporation ConsoliDator+ instruction manual
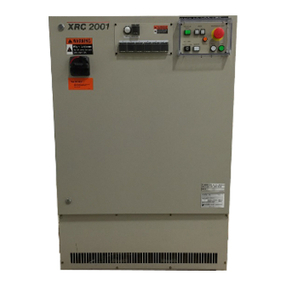
Motoman
Motoman XRC 2001 Concurrent I/O and Parameter Manual
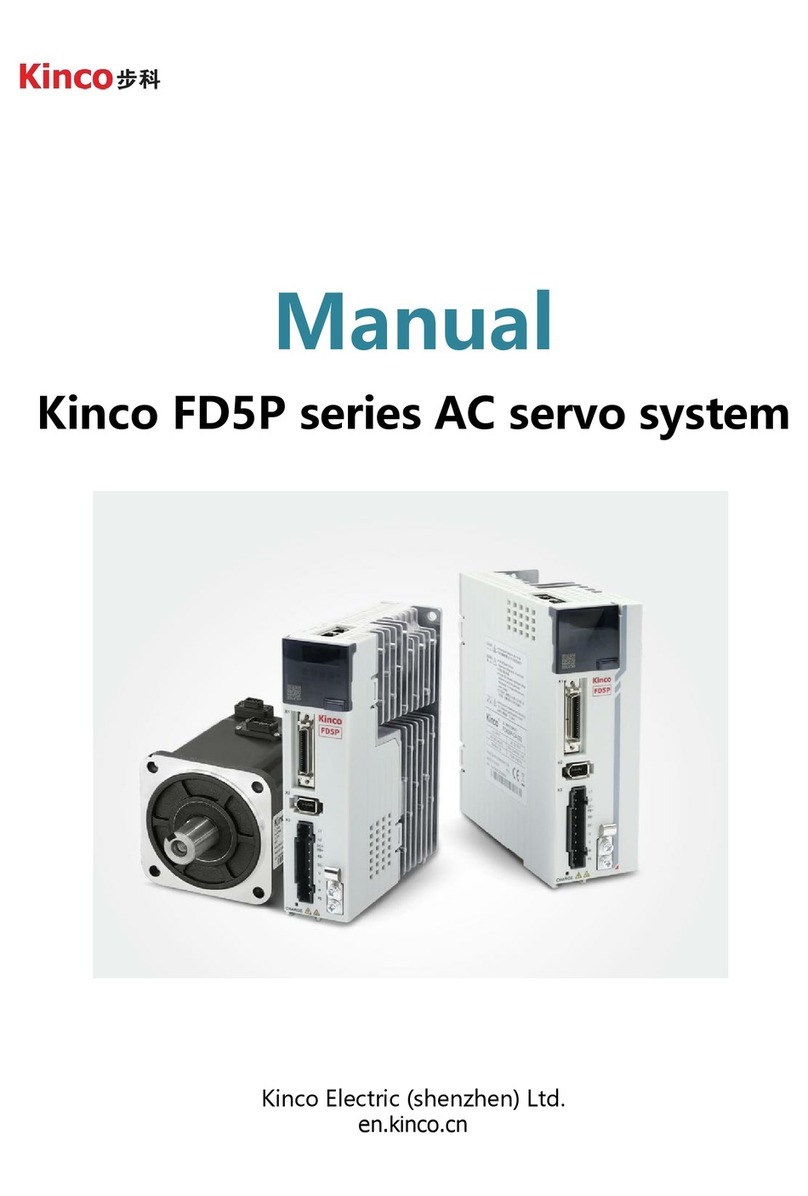
Kinco
Kinco FD5P Series manual
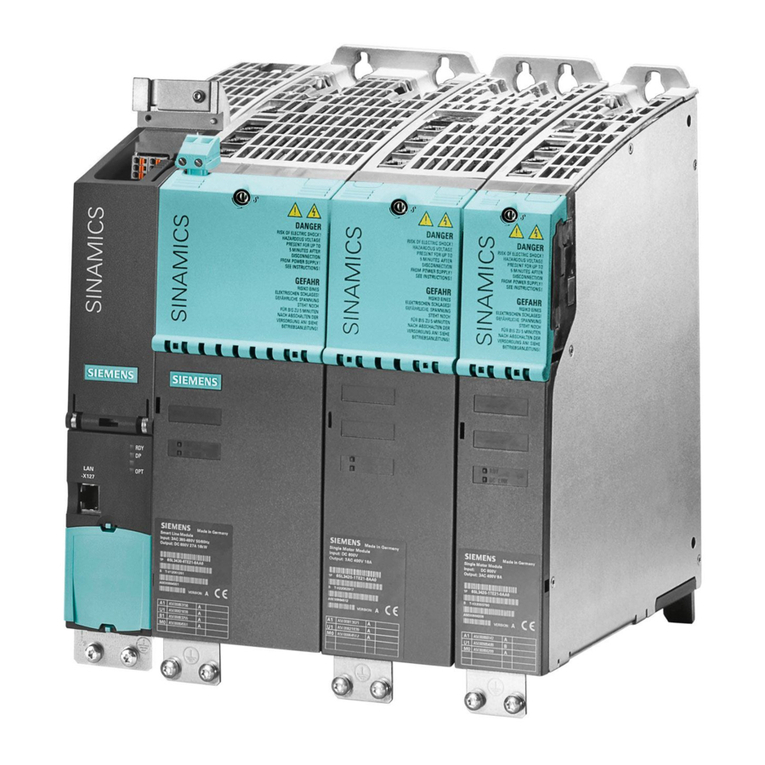
Siemens
Siemens SINAMICS S120 System manual
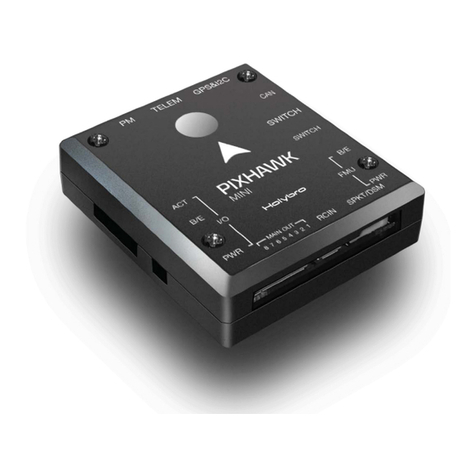
Holybro
Holybro PIXHAWK MINI quick start guide