Garrard 301 User manual


MANUAL
for the
GARRARD MODEL 301
TRANSCRIPTION
MOTOR
******
The Garrard Engineering and Manufacturing Company, Limited
Swindon : England

Introduction
Transcription Motor you have a unit whose perfor
mance is supreme in its class and this manual has
been prepared to enable you to enjoy and maintain
the high performance which this motor can achieve.
Should you require any further information
or advice not covered by this manual, please do not
hesitate to ask your nearest Garrard agent or write
to our Technical Service Department, Newcastle
Street, Swindon, who will be pleased to help you.
S the owner of this Garrard Model 301

FIRST EDITION 1954
SECOND EDITION 1956
THIRD EDITION 1957
FOURTH EDITION 1958
FIFTH EDITION 1959
SIXTH EDITION 1961

THE GARRARD MODEL 301 TRANSCRIPTION MOTOR
6

is the culmination of over 40 years’ experience in the
design and manufacture of high quality gramophone
equipment, and this motor has been designed to
provide the professional user and quality enthusiast
with a unit supreme in its class.
The Model 301 Transcription Motor has
three controls, the speed range knob on the right
hand side, speed adjusting control in the centre and
the on-off knob on the left hand side.
It has extremely low wow and flutter content,
rumble being almost non existent. Each of the three
speeds is adjustable by means of a knob which
operates a specially designed eddy current brake to
enable the precise speed to be obtained.
Great attention has been given to details
appreciated by the connoisseur, such as a sup
pressor unit to avoid switch clicks, a heavy
turntable diecast in aluminium and accurately
balanced, a robust hardened and super finished turn
table spindle, a fully retracting intermediate wheel
and a brake to reduce the free revolutions of the
turntable on switching off.
The unit is supplied complete with strobo
scope, record adaptor for 7" large hole records and
clip, a bottle of special oil, all fixing screws, set of
spring suspensions, template, manual, and test report.
7
HE Garrard Model 301 Transcription Motor
Description

Operation
To operate the Garrard Model 301 Transcription
Motor proceed as follows:—
(1) Move speed range knob to desired speed
Diagram 1
(2) Place record on turntable
Diagram 2
8

(3) Switch on
Diagram 3
To set speed place a record on the turntable and
then place the stroboscope on the record. Start motor.
Place pickup on record and turn the speed adjusting knob
until the ring of lines applying to that speed for which
you are setting appear to remain stationary when
illuminated under an appropriate A.C. light source.
Diagram 4.
For highly accurate transcription work where the
slightest speed deviation is critical it is desirable to let the
motor run for approximately 10 minutes so that it may
reach its normal working temperature. For such critical
work, speed should be re-checked on changing the speed
range.
9

Diagram 4
To protect the intermediate wheel from damage the
speed change knob is interlocked with the on-off knob. To
change the speed range the motor must be switched off
by means of the on-off knob.
The turntable must not be held stationary with the
motor switched on and the on-off switch on the motor
should always be used for stopping.
10

Technical Details
Turntable - Diecast Aluminium 12" diameter
machined all over and accurately
balanced.
Weight 6 lbs. Fitted with rubber mat.
A three speed stroboscopically engraved
turntable is available at extra cost.
Unit Plate - Diecast Aluminium.
Motor - Shaded pole induction in heavy cast
casing suspended on six tensioned
springs. Magnetically screened.
Voltage - Dual Range 100 to 130 and 200 to 250
volts.
Frequency - 50 or 60 cycles according to motor pulley
fitted. Alternative pulley available.
Consumption
Wow
Flutter
- 16 watts maximum.
/ Instrumentation:—
I Gaumont-Kalee Wow
- Less than 0.2%. 1 and Flutter Meter
/ Type 564.
\ 3,000 cycle constant
Less than 0.05 % j frequency records at
f 331, 45 and 78 r.p.m.
Rumble - Almost non existent.
Speed Range - 32 to 34, 44 to 46 and 76 to 80 r.p.m.
approx.
Finish - High quality broken white enamel with
black accessories.
Size - Motor Unit 1
4}"
back to front, 13 wide
2\”
above and
3\"
below under surface
of unit plate. Recommended size for
motor board 18" x 18".
Weight - Nett. 16 lbs. Gross 20 lbs.

Maintenance
The Turntable Spindle, motor and intermediate
wheel bearings being of the oil retaining type rarely need
lubricating. When however the need for oil is apparent
remove the turntable and sparingly lubricate these bearings
with a few drops of the oil supplied afterwards removing
all surplus and making sure that no oil is present on
the motor pulley or intermediate wheel before replacing
the turntable.
These oiling points are indicated on Diagram 5,
the oil recess in the top motor bearing being accessible
through one of the three holes in the aluminium disc of
the eddy current brake.
The motor must be in the switched off position
before removing or replacing the turntable. The turntable
is an accurate taper fit on its spindle and if difficulty is
experienced in removing it the spindle top should be given
a downward tap with a small block of wood, such as the
handle of a screwdriver, while the turntable is lifted.
Diagram 6
12

Installation
The Garrard Model 301 Transcription Motor
should be assembled to a substantial wooden motor board
which should be cut out and drilled to the template sup
plied with each unit or to the dimensions given on
Diagram 11. The motor should be assembled to the board,
using the rubber washers supplied, between the unit plate
and the board to prevent any distortion of the plate due
to any possible inaccuracies in the board.
Insert the screws and assemble the washers and nuts
as indicated in Diagram 5 tightening up the nuts equally
a little at a time, then securely tightening up the lock nuts.
To protect the electric motor during transit it is
firmly clamped by means of two transit screws, Diagram 5.
These screws, the heads of which are coloured red,
must be unscrewed as far as they will go to release the
motor clamp plate which allows the motor to float freely
on its suspension springs. To clamp the motor for transit
purposes the two motor transit screws should be tightened
up.
The pickup to be used should be mounted on the
board according to the manufacturers’ instructions.
The motor should be fixed to the motor board as
described above. This, however, may not always be
possible due to the presence of extraneous vibration
caused by shutting the cabinet lid or drawer or walking
across the floor on which the cabinet is standing.
In these cases, the motor board should be spring
mounted in the cabinet with the spring mounting assembly
provided as illustrated on Diagram 7. The cabinet board
being as shown in Diagram 8. With the motor and turn
table in position, there should be a gap of about to
between two boards. A reduced dimension template for
this board is given in Diagram 12.
13

Diagram 7
14

On final installation the motor should be levelled
by adjusting the inner nuts of the spring suspensions,
removing the lower mit, triangular washer, and lock nut
to do so, replacing them when the unit is level.
The level should be checked by means of a spirit
level placed on a record on the turntable.
A suitable set of four spring mounting assemblies
is supplied with each transcription motor and they
should be assembled as shown on Diagram 6. Should
the motor board be thicker than the fixing holes should
be recessed
\\"
diameter from underneath to bring the
thickness of the board to from the top.
Before assembling the motor into the cabinet con
nect the power supply lead, if not already fitted, to the
power supply terminal block situated at rear of motor,
making sure that the lead is securely clamped in the cord
grip adjacent to the block. Check that the voltage range
is set correctly for the power supply to be used; the links
should be set as shown on terminal block cover and
Diagrams 9 and 10. The motor pulley should also be
Set for 100/130 volts Set for 200/250 volts
Diagram 9 Diagram 10
checked to see that the correct one for>the frequency of
the power supply is in position on the motor, a nickel
finished one for 50 cycles, a brass one for 60 cycles.
15

Should the motor pulley require changing, remove
the pulley on the motor by loosening the two grub screws
holding it to the shaft and on fitting the other pulley
check that it is in its correct position before tightening
the screws, by moving the intermediate wheel inward,
making sure that the rubber tyre runs in the centre of the
appropriate step and its side face is clear of the pulley
step face by
jz"
when set on 331 or 45 r.p.m.
The motor should be earthed by connecting a lead
from the earthing tag on the motor. Diagram 5, to a good
earth connection. For preference three core power supply
lead should be used, two connections being made to the
power supply terminals and the other to the motor earth
ing tag.
On final installation it is essential that the leads from
the motor are not strained tight but should be very loosely
looped so that the motor remains freely suspended on its
springs.
The shaft of the speed range knob is extended so
that a standard wafer switch may be fitted if required.
16

Service Adjustments
The Garrard Model 301 Transcription Motor has
been designed to give reliable service with continuous use
and these instructions have been included to enable the
user to make the few minor adjustments which may become
necessary after long periods of use in order to maintain
the high standard of performance which this motor is
capable of producing.
Intermediate Wheel.
The accuracy of the rubber tyred intermediate
wheel is of supreme importance in maintaining the high
standard of performance of the unit and should any wow
or flutter be suspected check the intermediate wheel after
first making sure the record is not at fault. Flutter or
bump in the reproduction may be caused by flats on the
intermediate wheel. These may result from the turntable
being held stationary with the motor switched on, for this
reason the turntable must never be stopped with the hand,
but the unit switched off by means of the on-off switch on
the unit plate. Should the intermediate wheel become
damaged it should be replaced with a new one.
Flutter and wow can also be caused by the side
face of the rubber tyre on the intermediate wheel rubbing
on the side of one of the motor pulley steps, the position of
the pulley on the motor shaft should be such that there is
Jz"
clearance between the side faces of the intermediate
wheel and motor pulley steps. Wow can be caused by oil
or grease on the motor pulley, intermediate wheel tyre
or the driving surface of the turntable. In this case
thoroughly clean all driving surfaces with a clean rag.
Should hum, originating from the motor, be sus
pected, see that the motor is freely suspended on its
springs and that the motor transit fixing screwS Diagram
5 have been unscrewed. Also see that the power supply
and earth leads are slack and not straining the motor on
17

its springs, these leads, if too rigid, will transmit the motor
vibration to the cabinet and so be reproduced.
Should the motor fail to start on switching on,
first make sure that the power supply is reaching the ter
minals in the terminal block. If found to be correct
switch off at the power supply then check that the
voltage range change over links are tight, also remove the
switch cover and check that the switch contact moves each
of the two switch blades as it moves between them when
switching on. The switch blades and the contact should be
thoroughly cleaned and a faint trace of vaseline placed
on each of the two blades before replacing the cover.
Should the motor still fail to start check the circuit
of the coils. The total resistance should be 460 ohms if set
on the 200 to 250 volt range or 115 ohms on the 100 to
130 volt range.
If the turntable continues to revolve for several
revolutions after switching off by means of the switch on
the unit, the turntable brake pad probably needs adjust
ing. To make this adjustment, remove the turntable as
described on page 12, loosen the turntable brake adjusting
screw. Diagram 5, move the brake a small amount out
ward toward the rim and retighten the screw. Make sure
that the brake is not set too far out because it can prevent
the switch breaking contact if so set.
18

Spare Parts List
No. on Drawing
Diagram No. Name of Part
1A.51397 Turntable Spindle.
2A.40151 Screw.
3A.55967 Housing with Bearings A.43551.
5 A.51888 Circlip.
u
A.52493 Thrust Pad Assembly.
8A.52075 Gasket.
9A.51802 Thrust Plate.
10 A.40132 Screw.
14 A.42501 Spring Washers.
15 A.40132 Screw.
16 A.40458 Screw.
17 A.40085 Screw
18 A.40254 Screw.
19 C.51447 Motor Plate with Speed Plate A.51370,
On-Off Plate A.51371, Name Plate
B.55957 and Rivets A.42147. (State
colour).
20 A.51779 Stop Pin.
21 A.51778 Pivot Pin.
22 A.40768 Rubber Washer.
23 A.40678 Washer.
24 A.41058 Nut.
25 A.41061 Nut.
26 A.41737 Spring Clip.
27 A.42520 Spring Washer.
28 A.41006 Nut.
29 A.51814 Knob.
30 A.51813 Spindle.
31 B.51424 Control Knob Speed Change.
32 B.51206A Control Knob On-Off.
33 A.42539 Friction Spring.
34 A.42144 Rivet. , „
35 A.40514 Washer.
19

Spare Parts List — continued
V'
No. on Drawing
Diagram No. Name of Part
36 ■"A.51854 Pad Spring with Brake Pad A.45064
and Spring Clip A.41722.
37 A.40055 Screw.
38 A.40519 Washer.
39 A.50448 Collar.
40 A.51856 Catch Lever.
41 A.40643 Washer.
42 A.42042 Rivet.
43 A.51851 Brake Lever Assembly.
44 A.52004 Interlocking Lever Assembly.
45 A.41695 Spring fixing to items 40 and 43.
46 A.40519 Washer.
47 A.42503 Spring Washer.
48 A.40014 Screw.
49 A.51847 Switch Lever.
50 A.42006 Rivet.
51 A.50448 Collar.
52 A.51850 On-Off Lever.
53 A.51849 Link for Switch Lever.
54 A.40018 Screw.
55 A.45210 Collar.
56 A.51843 Intermediate Lever.
57 A.51844 Speed Change Lever.
58 A.42006 Rivet.
59 A.51841 Link ‘A’.
60 A.47594 Collar.
61 A.40560 Washer.
62 A.41012 Nut.
63 A.51840 Link ‘B’.
64 A.51837 Index Lever Assembly with Pin
A.43303.
65 A.51836 Spindle.
66 A.51886 Collars.
67 A.43101 Grommet.
68 A.40051 Screw.
20
Other manuals for 301
2
Table of contents
Other Garrard Turntable manuals
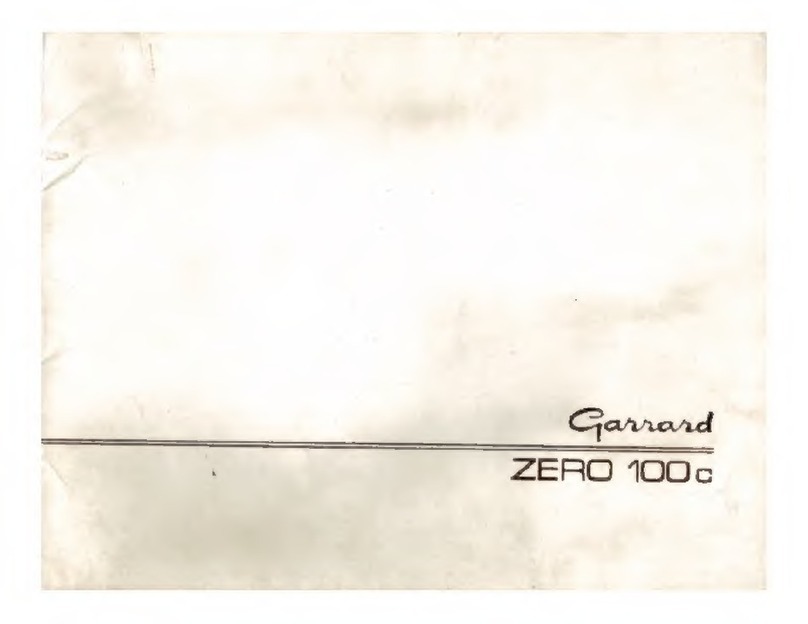
Garrard
Garrard ZERO 100C User manual

Garrard
Garrard 301 User manual
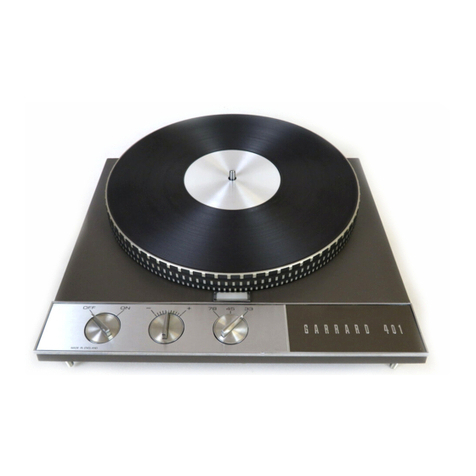
Garrard
Garrard 401 User manual
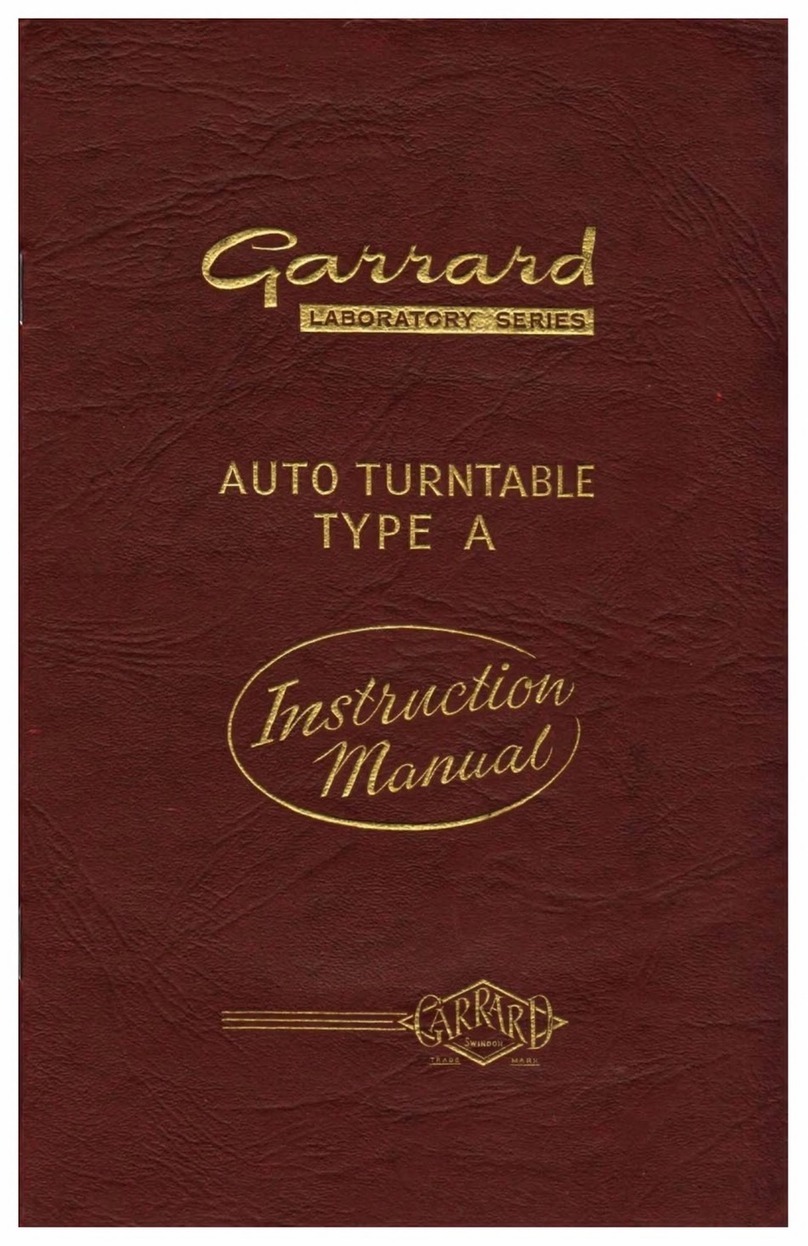
Garrard
Garrard A User manual
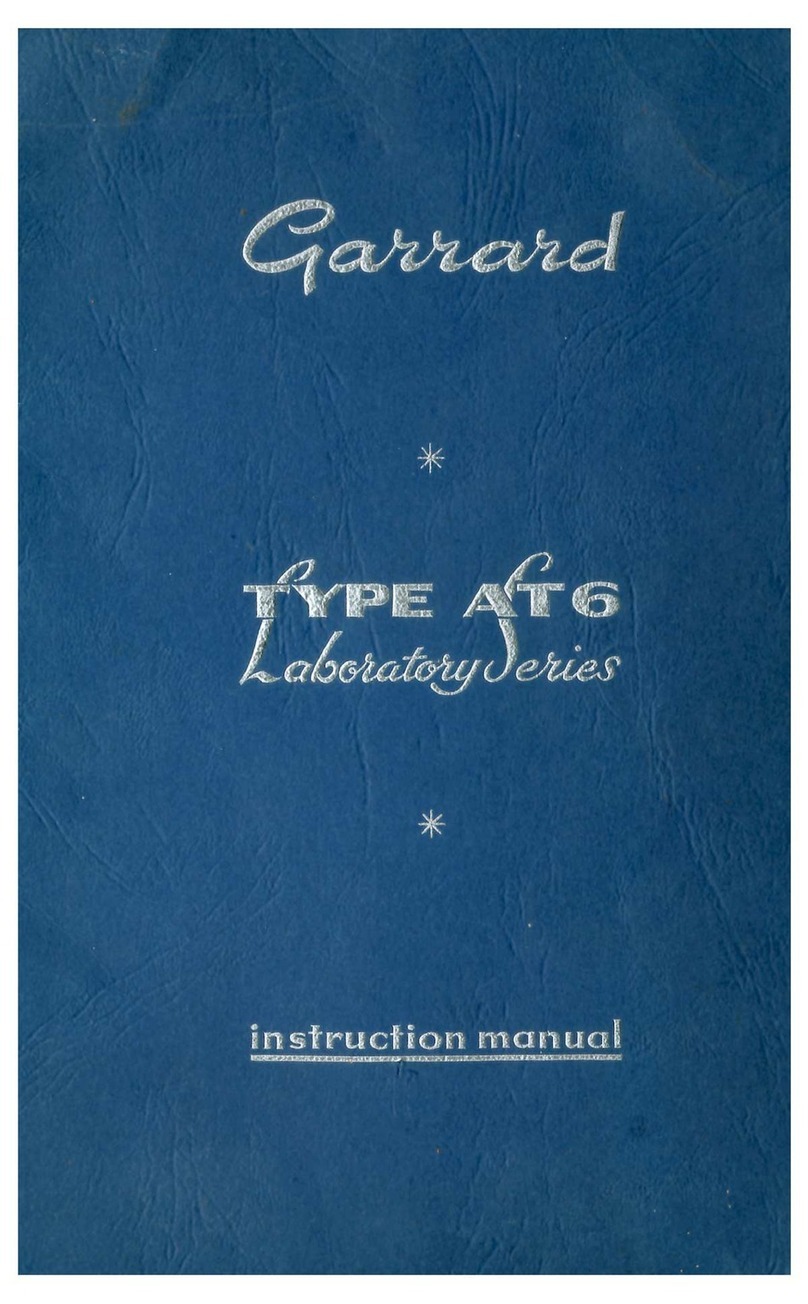
Garrard
Garrard AT6 User manual
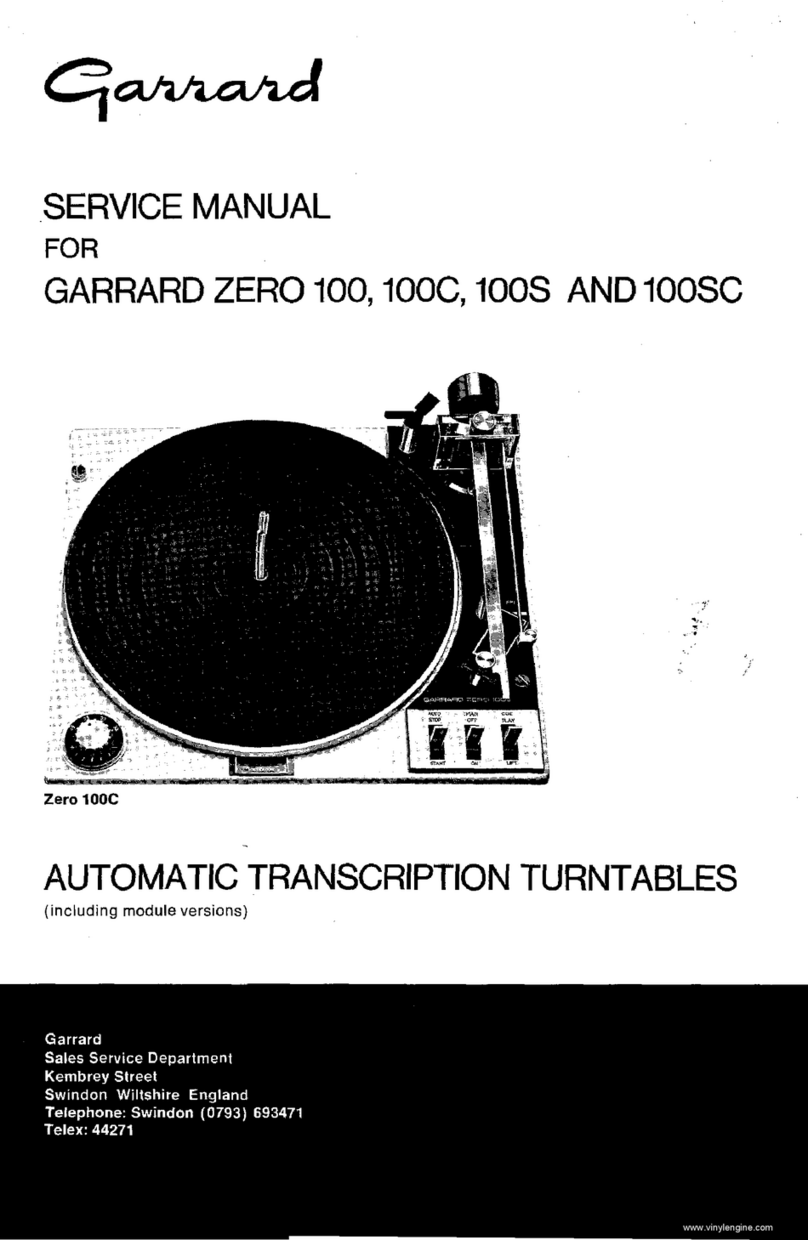
Garrard
Garrard ZERO 100 User manual

Garrard
Garrard 440 User manual

Garrard
Garrard TA/MK II Operation manual

Garrard
Garrard 210 User manual
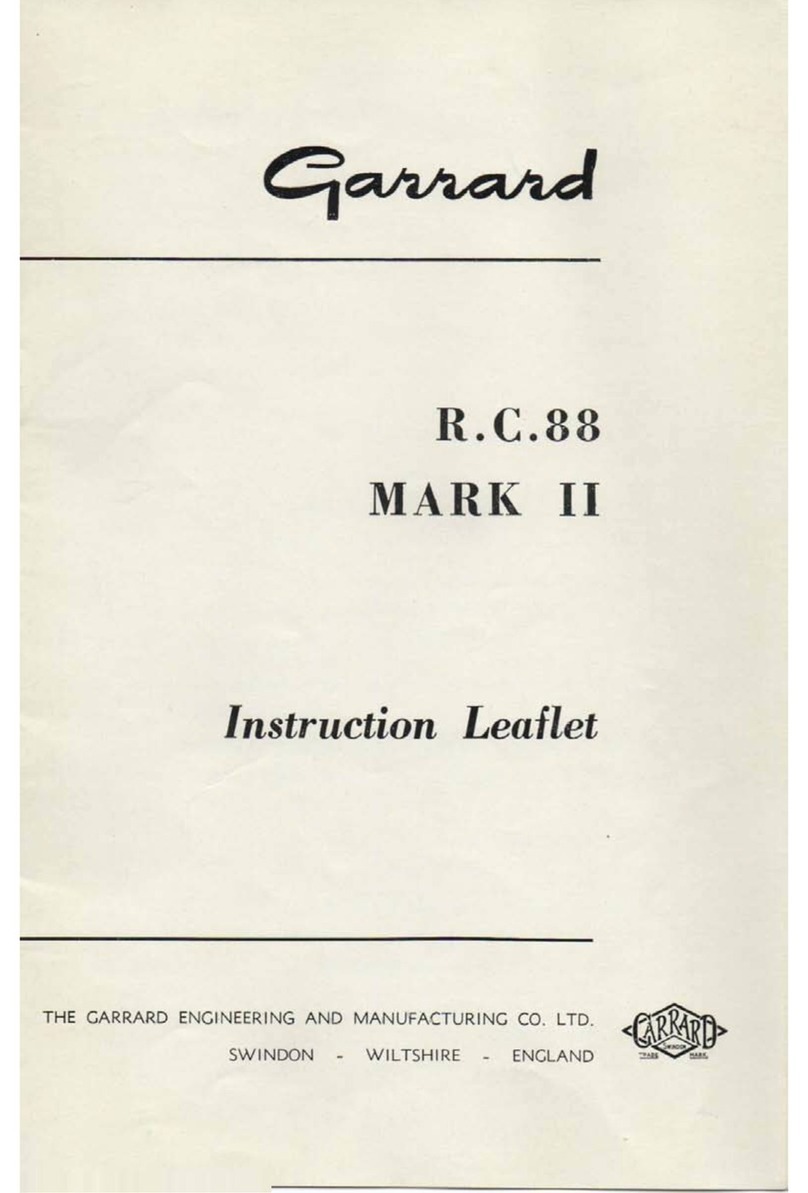
Garrard
Garrard r.c.88 mark II Manual