GDS 301 User manual

GDS301
SINGLE POINT SAMPLE UNIT
OPERATING HANDBOOK
TECHNOLOGIES LTD
C923
Manual No. 008DIC
Issue C
www.gds-technologies.co.uk
Tel. +44 (0)113 286 0166 Fax. +44 (0)113 287 8178
Email. [email protected]

2
Contents
System overview..........................................................................................................3
Installation, Set Up ......................................................................................................4
Operation, Testing, Operational Notes ........................................................................5
Terminal Details ..........................................................................................................6
Technical Data ..........................................................................................................7-8
Service/Routine Attention ............................................................................................9
Project modifications..................................................................................................10
This document is non contractual and the equipment specification and detail may be modified at any time without prior notice.

System Overview
The GDS 301 system is designed to monitor gas levels and provide alarms for the
presence of gas in a wide range of environments. The system consists of a sampling
unit with the sample tube run out to the target area.
A sample pump is used to extract a continuous sample for analysis by a range of sensor
devices. The pumping circuit incorporates a flow-sensing device, which provides indication
of pump failure or sample line blockage.
When gas is detected, the digital display will indicate the gas level, with the relevant alarm
LED illuminating and a buzzer sounding to alert the operator of the hazard. Relay contacts
are provided for control functions. Alarm repeater panels and remote audio-visual devices
are available for remote annunciation.
Pump failure or line blockage is indicated by an amber LED indicator located on the front
panel, the sounder is muted by pressing the mute button located on the internal flow fail
alarm board.
The system is supplied factory programmed and pre-calibrated to enable immediate
operation by connection of a mains voltage supply and sample line.
3
High
Low
Fault
Power
Reset
Test
Gas Alarm Sample Monitor 301 GDS 301
InOut
Sample
Flow fail

4
Installation
The unit should be mounted in a position which is accessible and in the field of vision. Mains
should be from a fused supply (2A) and connected to the mains input terminals of the power
supply unit, see page 6.
The vent port should be piped to atmosphere without reduction, this will prevent possible
back pressure affecting the sensor reading.
The positioning of the sample tube depends upon the type of gas to be monitored and its
density with respect to air.
Heavy gases (LPG, Propane, Butane, Refrigerant Gases) – locate at 15 to 20 cm from the
floor.
Lighter gases (Methane, Natural Gas, Town Gas) – locate at 5 to 10 cm from the ceiling.
Carbon Monoxide – locate at 1.5 to 2 metres from floor level.
Where appropriate the end of line filter nozzle should be positioned directly in the target
area and away from any risk of water contamination.
All equipment should be mounted away from direct heat.
Setting up
Having connected the sample pipe and terminated all cables, switch on the power and
allow 3 minutes warm up time, if necessary zero the instrument. Using a small terminal
screwdriver and with the sensor sampling in clean air adjust the zero potentiometer until the
digital meter reads zero for toxic/flammable gases or for oxygen, adjust the calibration
potentiometer until the meter reads 20.8% vol, the system is now set up.
Alarm levels are factory set but may be re-adjusted as follows:-
1. For toxic/flammable gases zero the instrument in clean air using the zero potentiometer
(for ambient oxygen monitoring the meter should be adjusted to read 20.8 using the
calibration potentiometer).
2. Press the alarm set switch for approximately 5 seconds the sounder will bleep and the
low alarm indicator will come on, the green power indicator will turn off, release the
alarm switch.
3. Using the zero potentiometer adjust the digital display for the required low trip level
reading, press the alarm set switch until the high alarm indicator comes on, release the
alarm set switch.
4. Adjust the digital display to read the required high trip level reading and again press the
alarm set switch both alarm indicators will come on.
5. Zero digital display (toxic/flammable) of 20.8 for oxygen and press alarm set switch,
alarm indicators will turn off and the green power indicator will turn on.
For sensor signal transmitter set up see data sheet.

5
Operation
On power up the green power indicator will flash for 60 seconds indicating that the sensors
are stabilising, during this period all alarms are held in the off position.
After the stabilisation period any gas detected by the sensor will be indicated on the digital
display with any alarm level being exceeded resulting in the sounder and appropriate red
LED and relay activating.
Pressing the reset pad will result in the sounder being silenced, alarm indicators and relays
may only be reset when the indicated gas level has reduced to below that of the alarm trip
points.
Testing
The unit may be electrically tested by pressing the test pad for 15 seconds after which the
gas alarm indicators and sounder will activate intermittently, maintaining pressure on the
pad for a further 15 seconds will result in constant sounder/indicators and activation of
alarm relays.
During servicing alarm relays may be isolated by pressing the reset pad for 15 seconds
after which the fault indicator will come on indicating inhibit mode, to remove inhibit press
the reset pad for 15 seconds the fault indicator will turn off.
To ensure that the system responds correctly to the presence of gas, the sensor should be
gas tested by injecting an appropriate test gas sample into the system at point (A) see detail
on page 8). It is advisable to carry out this test at six monthly intervals (Minimum).
Operational notes
Water Drain: - where a catch pot is fitted water may collect within the bowl, this will be more
noticeable where hot samples are being drawn along the sample line and condensing along
its path - water should not be allowed into the system - damage to the sensor will occur.
Sensor
Sample
Pump
Power
Board
Flow
Monitor
Particulate
Filter
standard layout

6
GDS 100 Control Unit – PCB Detail
Power Board
Not
Used
123
Voltage Input Alarm Relays
4 5 6789101112
1Live or + DC
2Neutral or - DC
3Earth
4N/C
5C
6N/O
7N/C
8C
9N/O
10 N/C
11 C
12 N/O
Low Alarm
High Alarm
Fault
Field Terminals
Optional Field Terminals

7
Technical
CE Cert. No. Ref C914
Sensor Points One
Sensor Type Catalytic, Electrochemical, Infra-red, Semiconductor
Measurements Combustible gas – L.E.L. % vol.
Toxic gas PPM, % vol.
Oxygen - % vol. – depletion/enrichment
Refrigerant – ppm
Power Supply Input - 230/115v AC – 50/60 Hz - 24v DC – Special 50v DC
Consumption 70W full alarm
Field Terminals Screw Type – accepting up to 2.5 mm cable
Indicators Gas level readout 31
/2 digital display
Power – green L.E.D
Low alarm – red L.E.D
High alarm – red L.E.D
System fault – amber L.E.D
Flow fail – amber L.E.D - (Pump fail/line blockage)
User Interface Panel mounted push buttons (two)
Reset – Mute sounder, reset alarms, initiate alarm relay inhibit
Test – check alarm indicators, sounder and relay action
Alarm Settings Digital setting (fully adjustable between zero and full scale)
Normally latched – option auto reset
Outputs Relay – high level gas alarm S.P.C.O.
Relay – low level gas alarm S.P.C.O.
Relay – system fault S.P.C.O.
Relay – flow fail S.P.C.O. – flow fail alarm board
All contacts rated 5A 230v AC
All relay contacts used to switch inductive loads (relays etc)
should have suppressors fitted, typical device Farnell 772-756
4~20mA analogue output or 1~5v
Optional data logger
24v DC @ 100mA - Available for auxiliary equipment
Audible Alarm Lo, hi, fault flow fail alarms 98dB @ 38cm
Dimensions H 265mm x W 315mm x D 75mm
Cable Entry Base – Rear
Weight 3.7 kg

8
Finish Epoxy coated steel
Ingress Protection IP 52 Standard IP65 option
Pump Sample pump – 24v DC brushless diaphragm
Sample Line Material – Nylon, PTFE, Stainless Steel, Copper
Size – 6 mm OD, 4 mm ID – push fit coupling
Maximum length – 30 m – see options
Sample Line Length 1 – 100m
Sample Particulate Filter End of sample line filter – large particulate removal
Catch pot – removal to 40um – option
In line filter
Sample Vent 8 mm – push fit
Operating Temperature -10 to +40˚C
Sample Temperature -10 to + 50˚C – high temperature versions available
Response Time 20 to 80 seconds
Options Catch pot
Water auto drain
Sensor
Exhaust
Sample Pump Flow monitorparticulate filter
Sample in
Power
board Alarm
Panel
24v DC
Supply
Voltage
Auto
drain
(option)
(A)
X

9
Service routine attention
The owner or occupier of the site should place the supervision of the system in the charge
of a responsible executive, whose duty it should be to ensure the day to day operation of
the system and to lay down the procedure for dealing with a gas alarm or fault warning.
The operating instructions should be kept available preferably with the control unit, all faults,
service test and routine attention given should be recorded.
DAILY: A check should be made that any fault condition which may be indicated is in fact
being attended to and that all other indicators are normal.
WEEKLY: Check the catch pot for high levels of particulate or water contamination, replace
filters as neccesary. On sites involving a high risk process or having gases which may cause
loss of sensitivity a check on calibration should be carried out.
Twice yearly maintenance schedule
1. Zero check to sensor
2. Sensor to be gas tested and reading logged (sensitivity checked).
3. Field indicators to be tested.
4. Alarm trip points checked and re-aligned.
5. All faulty parts replaced where required.
6. All filter elements checked and replaced as necessary (catch pot filter – end of line filter
– in line filter).
7. Power supply – voltage check.
8. Visual inspection made to confirm that the sample line fittings and equipment is secure,
undamaged and adequately protected.
9. Logger batteries replaced (if fitted).
12 Monthly maintenance schedule
1. Twice yearly schedule.
2. Draw pump overhaul (diaphragm replacement).
3. Auto drain – pressure tube replacement (if fitted)
24 Monthly maintenance schedule
1. Pump replacement
Recommended test gas:

Project Modifications
10


ISO 9001 TECHNOLOGIES LTD
GDS Technologies Ltd
Fusion Point, Ash Lane
Garforth, Leeds LS25 2GA
Tel +44 (0)113 286 0166
Fax +44 (0)113 287 8178
www.gds-technologies.co.uk
Table of contents
Other GDS Measuring Instrument manuals
Popular Measuring Instrument manuals by other brands
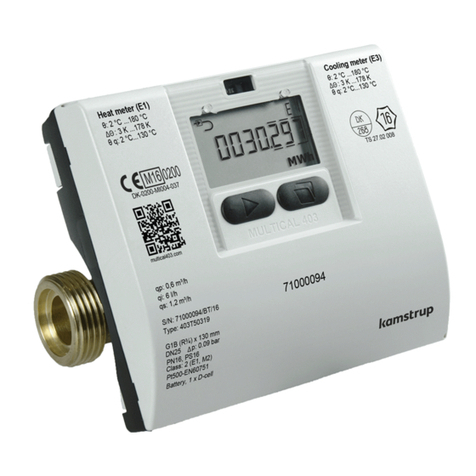
Kamstrup
Kamstrup MULTICAL 403 Technical description

Anton Paar
Anton Paar DMA 4100 M instruction manual
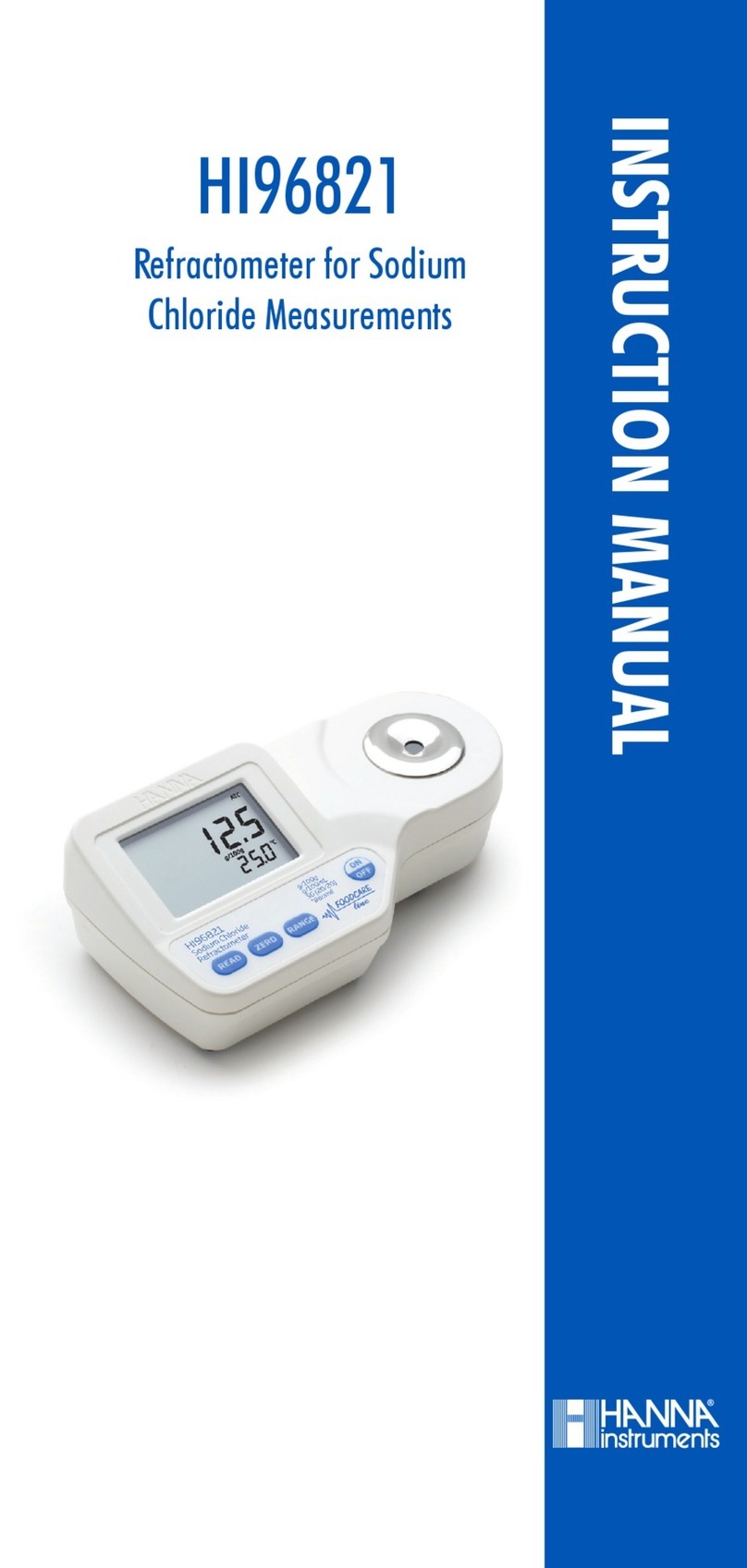
Hanna Instruments
Hanna Instruments HI 96821 instruction manual

Franklin Fueling Systems
Franklin Fueling Systems EVO 200 Operation guide
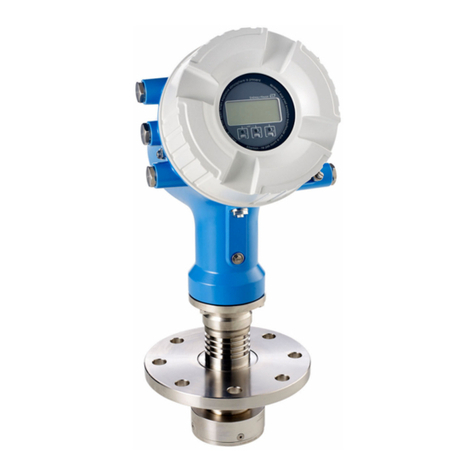
Endress+Hauser
Endress+Hauser Micropilot NMR84 Brief operating instructions
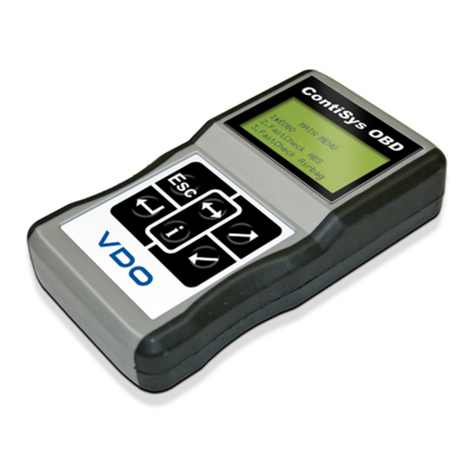
VDO
VDO CONTISYS OBD - Quick reference guide