GEODEVICE MiniMag User manual

OPERATION MANUAL
Overhauser magnetometer
MiniMag

2
Overhauser magnetometer MiniMag
Contents
INTRODUCTION.............................................................................................................................................................4
1. DESCRIPTION AND PRINCIPLES OF OPERATION ........................................................................................................6
1.1 Description of the product..................................................................................................................................6
1.1.1 Designation ..................................................................................................................................................6
1.1.2 Technical characteristics, parameters and dimensions................................................................................6
1.1.3 Package contents .........................................................................................................................................7
1.1.4 Structure and Functioning............................................................................................................................8
1.1.4.1 Principle of operation................................................................................................................................8
1.1.4.2 Measurement cycle...................................................................................................................................8
1.1.5 Storage & shipping case...............................................................................................................................8
1.2 Magnetometer description and principles of operation.....................................................................................9
1.3 Operating controls and operator control chart.................................................................................................11
1.3.1 Operating controls .....................................................................................................................................11
1.3.2 Operator control chart...............................................................................................................................12
2 INTENDED USE .........................................................................................................................................................14
2.1 Operating limitations ........................................................................................................................................14
2.2 Preparation for use ...........................................................................................................................................15
2.2.1 General safety instructions for use ............................................................................................................15
2.2.2 The procedure and workflow to prepare the device for use......................................................................15
2.3 USAGE ...............................................................................................................................................................18
2.3.1 Initial setup window, viewing GNSS data and entering the main menu.....................................................20
2.3.1.1 Initial setup window............................................................................................................................20
2.3.1.2 Viewing GNSS data..............................................................................................................................20
2.3.1.3 Exit to the main menu.........................................................................................................................21
2.3.2 Operating modes .......................................................................................................................................21
2.3.2.1 Test mode ...........................................................................................................................................21
2.3.2.2 Manual mode......................................................................................................................................22
2.3.2.3 Automatic mode .................................................................................................................................25
2.3.3 Viewing information...................................................................................................................................26
2.3.4 Erasing information from the magnetometer memory (clearing memory) ...............................................28
2.3.5 Magnetometer settings control .................................................................................................................28
2.3.5.1 Signal search .......................................................................................................................................29
2.3.5.2 Language choice..................................................................................................................................30
2.3.5.3 Time zone............................................................................................................................................30
2.3.5.4 Information about device....................................................................................................................30
2.3.5.5 Corrections..........................................................................................................................................31

3
Overhauser magnetometer MiniMag
2.3.6 Safety measures during device using .........................................................................................................31
2.3.7 Procedure for completing operation with the device ................................................................................32
2.3.8 Data export from the magnetometer memory to a PC..............................................................................33
2.3.9 Real-time data output to PC.......................................................................................................................36
2.4 Actions during extreme conditions ...................................................................................................................41
2.5 List of possible malfunctions.............................................................................................................................42
3 REPAIR......................................................................................................................................................................44
4 STORAGE..................................................................................................................................................................45
5 TRANSPORTATION....................................................................................................................................................46
6 RECYCLING ...............................................................................................................................................................47
7 APPENDIX.................................................................................................................................................................48
7.1 General recommendations for magnetic survey fulfillment with Overhauser Magnetometers MiniMag........48
7.1.1 Installation of a Base station ......................................................................................................................48
7.1.2 Magnetic survey with Rover.......................................................................................................................48
7.2 Earth’s magnetic field inclination and total intensity maps ..............................................................................50
7.2.1 Main field inclination map..........................................................................................................................50
7.2.2 Main field total intensity ............................................................................................................................51
7.3 Li-ion battery.....................................................................................................................................................52
7.3.1 Battery specifications.................................................................................................................................52
7.3.2 Charge........................................................................................................................................................52
7.3.3 Precautions ................................................................................................................................................52
7.4 Li-ion battery charger........................................................................................................................................54
7.4.1 Charger specifications................................................................................................................................54
7.4.2 Charge........................................................................................................................................................54
7.4.3 Precautions ................................................................................................................................................55
7.5 Pinout scheme of the magnetometer cables ....................................................................................................56
7.5.1 Cable “Control Unit to Magnetometer Unit” .............................................................................................56
7.5.2 USB cable ...................................................................................................................................................56
7.5.3 Remote start cable.....................................................................................................................................57
7.5.4 Li-ion battery cable ....................................................................................................................................57
7.6 Material Safety Data Sheet for Li-ion battery....................................................................................................58

4
Overhauser magnetometer MiniMag
INTRODUCTION
This operation manual (hereinafter referred to as OM) is designed for studying the device, its
principle of operation and proper use of the Overhauser magnetometer MiniMag (hereinafter —
magnetometer / device / product) by the operating personnel.
This OM contains information about the configuration, design, principle of operation, technical
characteristics of the magnetometer, operational limitations; instructions for preparing for
operation, usage, transportation and storage; safety precautions; disposal instructions and other
information regarding the magnetometer necessary for its correct usage in order to maintain the
operational reliability and safety of the device.
ATTENTION: REPAIR OF THE MAGNETOMETER IS CARRIED OUT EXCLUSIVELY BY THE
MANUFACTURER (GEODEVICE) or by specialized services and professionals who have been trained
and have a certificate for the right to carry out repairs, issued by GEODEVICE.
The requirements of this OM are mandatory for all persons involved in the operation, storage,
transportation, further disposal and other manipulations with the magnetometer.
This OM should always be in close proximity to the place of operation of the device and be
accessible to operating personnel.
The operational reliability and safety of the magnetometer is guaranteed only if all of the following
conditions are met at the same time:
- usage of the device for its intended purpose;
- operation of the magnetometer in acceptable environments and conditions in accordance with
the OM;
- compliance with the instructions for use, safety measures and all other recommendations and
requirements of this OM.
IT IS PROHIBITED TO OPEN / DISASSEMBLE THE MAGNETOMETER, AS WELL AS TO MAKE
MODIFICATIONS IN THE DESIGN OF THE DEVICE, DEVELOP IT WITHOUT DUE APPROVAL OBTAINED
FROM THE MANUFACTURER.
In case of violation (non-compliance) of the requirements given in this OM, the manufacturer is
not responsible for the consequences arising in connection with this (accident, damage to
property, injury, etc.)
Manufacturer is constantly improving its equipment and reserves the right to make changes to the
design of the magnetometer, change its technical characteristics and completeness. In this regard,
there may be insignificant differences between what is described in this OM and the supplied
magnetometer, which do not fundamentally affect the conditions of its operation.

5
Overhauser magnetometer MiniMag
The following abbreviations and notations are used in this OM:
SEU —signal excitation unit,
HFG —high-frequency generator,
GPS —Global Positioning System,
DNP —dynamic nuclear polarization,
MU —magnetometer unit,
ETF —Earth’s total field,
CU —control unit,
OS —operating system,
PC —personal computer,
SE —sensitive element,
SC —signal conditioner.

6
Overhauser magnetometer MiniMag
1. DESCRIPTION AND PRINCIPLES OF OPERATION
1.1 Description of the product
1.1.1 Designation
Overhauser magnetometer MiniMag is designed for high-precision measurements of the module
of the full vector of the geomagnetic field. The sensor used in the design of the magnetometer (the
principle of which is based on the Overhauser effect application), does not require maintenance
and operates steadily for at least 10 years without deterioration of technical characteristics.
MiniMag can be used as a rover hand-held magnetometer, autonomous or remote base station.
Increased absolute accuracy and real-time data transfer allow MiniMag to be used in magnetic
observatories. Integrated GPS/GLONASS receiver enables automatic coordinate gridding of
measurement stations and time synchronization with the base station making convenient the
survey implementation as well as data processing.
1.1.2 Technical characteristics, parameters and dimensions
Table 1. Technical characteristics, parameters and dimensions
Parameter
Value
Principle of operation
based on the Overhauser effect application
Range
20 000 ÷ 110 000 nT
Absolute accuracy
0.2 nT
Sensitivity
0.015 nT in cycle 3 s / 0.026 nT/√Hz
Resolution
0.001 nT
Optimal angle between the axis of the sensor and
the field vector
90°
The working range of inclination relative to the
optimal angle
±45°
Orientation error
0.5 nT (±45°)
Gradient tolerance
10 000 nT/m
Minimum measurement cycle
0.5 s
Radical stability
10 years at standard conditions
Communication interface with PC
USB
Memory capacity
1 000 000 (in base magnetic station mode),
250 000 (with coordinate referencing)
Power
10 ÷16.8 V, Li-ion or Pb battery
Power consumption
3.7 W in 2 s cycle
3.2 W in 3 s cycle
1.4 W in 10 s cycle
Operating temperature range
−40 ÷ +60 °C, readability of the display is provided
at temperatures above −20 °C
Weight
3.1 kg (with battery)
Nominal voltage of Li-ion battery
14.6 V
Nominal capacity of the battery
4 A·h
Continuous operation time with a fully charged
battery and a 20 °C temperature
15.9 h in 2 s cycle
18.7 h in 3 s cycle
42 h in 10 s cycle

7
Overhauser magnetometer MiniMag
1.1.3 Package contents
The following components are included in the delivery:
•MiniMag magnetometer
•Console
•Set of cables
•Remote start module
•Li-ion battery with power cable
•Charger
•External power supply (for lead battery);
•Backpack harness;
•Rugged shipping / storage container;
•Data storage software
•Calibration certificate issued by authorized organization
•Operation manual
Figure 1 –Overhauser magnetometer MiniMag
Transportation of the Overhauser magnetometer MiniMag is carried out in a sealed, shockproof
casing made of bakelite plywood.

8
Overhauser magnetometer MiniMag
1.1.4 Structure and Functioning
1.1.4.1 Principle of operation
For measuring the geomagnetic field in a magnetometer, the phenomenon of protons’ free
precession of a prepolarized working agent in the ETF is used. In this case, the polarization of nuclei
is enhanced by the Overhauser effect (dynamic polarization of nuclei).
The Overhauser effect is a phenomenon that deploys the electron-proton interaction in order to
achieve the polarization of protons. To realize this effect, a specially developed compound is used
in the magnetometer, which contains a free radical atom (an atom with an unbound electron),
which is added to a proton-rich liquid. Unbound electrons in a solution can be easily excited by
high-frequency radio frequency radiation, which corresponds to a transition between energy
levels. Instead of re-releasing this energy in the form of emitted radiation, unbound electrons
transfer it to neighboring protons, which allows to polarize these protons without the need to
create a large artificial magnetic field. Therefore, such sensors can generate large-amplitude signals
with a high signal-to-noise ratio, with a power consumption of just a few watts. Standard proton
sensors cannot generate signals of this magnitude and quality, even when consuming several
hundred watts.
1.1.4.2 Measurement cycle
Each measurement cycle essentially consists of two steps:
1. Polarization —proton fluid of the sensitive element (SE) is excited by both constant and high-
frequency magnetic fields, thus, orienting the proton spins normally to the magnetic field of the
earth (ETF).
2. Measurement —after the exciting field is turned off, it begins free precession of protons in the
ETF. Attenuating sine-shape EMF proportional to ETF value is induced in the low-frequency coils of
SE:
where —precession frequency,
—total field,
—proton gyromagnetic ratio.
1.1.5 Storage & shipping case
Magnetometer is delivered in the special case which protects the device from precipitation and
dust.

9
Overhauser magnetometer MiniMag
1.2 Magnetometer description and principles of operation.
Figure 2 –Overhauser magnetometer MiniMag: package contents
1 –magnetometer unit (MU);
2 –control unit (CU);
3 –sensitive element (SE);
4 –signal excitation unit (SEU);
5 –battery with cable;
6 –CU-to-MU connection cable;
7 –remote start module;
8 –charger;
9 –USB-cable;
10 –backpack harness.

10
Overhauser magnetometer MiniMag
Magnetometer unit
MU is intended for ETF measurement and consist of SE and SEU joined together using the non-
magnetic rode.
SE is intended for generating a signal from free precession of protons of working agent placed in
the magnetic field measured. SE contains a glass ampoule with a working agent placed in a high-
frequency circuit (HF circuit), on top of which low-frequency coils are wound that are designed for
recording the precession signal.
SEU is designed to provide a proton precession signal. In terms of construction, SEU is made in the
form of a separate unit, which includes HFG and SC
Control unit (CU)
Used to control the magnetometer, perform basic and auxiliary operations, record the results of
field measurements in non-volatile memory, followed by the information output of to PC.
Battery with power cable
Intended to power the electronic components of the magnetometer. A Li-Ion rechargeable battery
with a voltage of 14.8 V and a capacity of 4 A·h is used as a power source. Also, a 12 V lead-type
battery Delta CT 12025 can be used as a source, to connect which a power cable for connecting a
lead battery is present in the configuration of the device.
CU-to-MU connection cable
Designed for data transfer between the control panel and MU.
Cable with remote start button
Designed for remote start of magnetometer measurements.
Charger
Designed for charging the battery from AC 220 V, 50 Hz.
USB cable
Designed for connecting CU to PC.
Backpack harness
Designed for carrying the magnetometer during survey.

11
Overhauser magnetometer MiniMag
1.3 Operating controls and operator control chart
1.3.1 Operating controls
The operating controls of the magnetometer are 2 keyboards located in the control panel: the main
one, located on the front panel, and two additional ones, located on the side faces of the CU.
In order to control operation, pressing any key is accompanied by a short beep.
Figure 3 –Main keyboard of CU
Figure 4 –Additional keyboards of CU
- keyboard keys for digital data;
- key of priority exit to the main menu from any mode, to the initial
setup window from the main menu and to the settings menu from any
settings mode;
- entering a command and starting the clock after setting the time;

12
Overhauser magnetometer MiniMag
- graphic display mode key;
- graph offset key;
- setting the + or −sign, also shifting the frame when viewing memory;
- return to the previous window;
- re-measurement in manual measurement mode;
- data shift;
- LCD backlight on.
1.3.2 Operator control chart
The functionality of the magnetometer is realized using a microprocessor control system and by
sending due commands. To facilitate the formation of these commands, the magnetometer
control circuit was designed according to the dialog principle, in which each subsequent
command is selected from the menu or prompt displayed on the screen. A complete list of
commands and the operations performed in this process is shown on Figure 5.

13
Overhauser magnetometer MiniMag
Figure 5 –MiniMag control circuit

14
Overhauser magnetometer MiniMag
2 INTENDED USE
2.1 Operating limitations
MiniMag is designed for operation in the field at ambient temperatures from −20 to +50 °С.
In winter, the magnetometer can be switched on after transportation or storage in an unheated
warehouse only after 2 hours at a temperature of +15 °C to +25 °C.
Avoid sudden fluctuations in temperature that can cause forming condensation.
MiniMag is a high-precision instrument and requires careful handling. When working with the
device, falls and bumps should be avoided.

15
Overhauser magnetometer MiniMag
2.2 Preparation for use
2.2.1 General safety instructions for use
The magnetometer is powered by a 14.8 V Li-Ion battery, the operation of which must be carried
out in accordance with the attached instructions (see APPENDIX) or by a 12 V lead-acid battery of
the Delta CT 12025 type, for which a power cable is supplied with the device to connect a lead
battery.
In case of using a DC power source, the housing and the negative terminal of the source must be
reliably grounded.
2.2.2 The procedure and workflow to prepare the device for use
1. Perform an external inspection of all parts of the device and make sure:
−complete set of the magnetometer corresponds to OM in the volume necessary for work;
−mechanical damages on the magnetometer blocks are absent;
−mechanical damages on the connecting cables and connectors are absent;
−pollution and soaking are absent.
IT IS PROHIBITED TO USE THE MAGNETOMETER IF DAMAGES ARE PRESENT, AS WELL AS WATER
OR SIGNIFICANT POLLUTION.
2. If necessary, recharge the battery in accordance with the attached battery operating instructions
(see APPENDIX).
3. Fasten the functional blocks of the magnetometer in the backpack harness.
Figure 6 –Magnetometer and battery in the backpack harness
4. Tether the CU-to-MU connection cable to the corresponding connector on magnetometer.

16
Overhauser magnetometer MiniMag
Figure 7 –Connector for a communication cable
on the magnetometer case
Figure 8 –CU-to-MU connection cable
5. Connect the battery to the due magnetometer connector.
Figure 9 –Battery connector on the
magnetometer case
Figure 10 –Battery with power cable
6. Put the backpack harness on the operator and adjust it to his height.
7. Tether the CU-to-MU connection cable to the corresponding CU connector.
Figure 11 –Connector for connecting cable on the
CU case
Figure 12 –CU-to-MU connection cable
8. If necessary, connect a cable with a remote start button to the CU.

17
Overhauser magnetometer MiniMag
Figure 13 –Connector for connecting a cable with
a remote start button on the CU housing
Figure 14 –Cable with remote start button
9. Wait for synchronization of GNSS coordinates with time on a CU.
When starting for the first time after a long period of inactivity or a significant change in the
coordinates of the starting point since the last measurement (more than 200 km), the
magnetometer needs to obtain the coordinates and time from GNSS satellites. This procedure can
take up to 20 minutes, depending on the reception conditions of the satellite signal. The best result
is achieved in an open area without interference for radio waves in the form of trees or buildings.
The magnetometer console must be fixed motionless in a horizontal position. Do not change the
date before synchronizing GNSS coordinates. For correct synchronization of GNSS coordinates, it
is necessary that the date consists of zeros.
Using LED on the front panel, one can determine the current status of the lock-on. When you turn
on the power and initialize the CU, the LED flashes red-blue. Further, if the LED blinks with an
aquamarine colour —there is no lock-on to GNSS coordinates. If blinking with green colour —
reception conditions and lock-on accuracy are optimal. If the LED blinks in red, then the GNSS
receiver is malfunctioning. It is worth noting that time synchronization occurs regardless of the
lock-on to coordinates and does not affect the LED display in any way.

18
Overhauser magnetometer MiniMag
2.3 USAGE
IMPORTANT Do not start using the magnetometer without reading OM. The actual operation of
the magnetometer is allowed only after the implementation of the steps taken to prepare the
device for operation, described in this OM.
IMPORTANT The magnetometer operator is prohibited from carrying any objects that include
magnetic materials (knives, tools, coins, keys, lighters, etc.) as well as any electronic devices (radio
stations, telephones, navigators, headphones, etc.) In addition, the appointment of a
magnetometer operator with medical implants made of magnetic materials, pacemakers, as well
as earrings, piercings, etc., should be avoided. Clothing elements of the magnetometer operator
should also consist of non-magnetic materials: buttons, zippers, eyelets, fasteners, snap hooks,
metal strings from mosquito nets and many more items of such a kind may influence the
magnetometer readings. Before starting measurements, special attention must be paid to the
selection of work clothes and shoes.
IMPORTANT Before starting operation, the magnetometer sensor should be oriented in the right
way to ensure the most effective ETF registration. The need for orientation of the sensor depends
on the survey area (Figure 15). The optimal position of the sensor is the one when the SE axis is
oriented at an angle of 90 ± 5 degrees to the direction of the ETF vector. Its slope of the Earth’s
can be estimated from the latitude at which the survey is being carrying out (ETF vector in the
equator is parallel to the Earth’s surface, and at the poles it is subvertical) (see paragraph 7.2). One
can estimate the inclination of the ETF vector using an online web service (e.g.
https://www.ngdc.noaa.gov/geomag/calculators/magcalc.shtml#igrfwmm) or a smartphone
application with a three-axis compass. It should be noted, that the working area of the MiniMag
sensor is ± 45 degrees relative to the optimal angle between the axis of the sensor and the ETF
vector (Figure 16).

19
Overhauser magnetometer MiniMag
Figure 15 –MiniMag sensor orientation map
Figure 16 –Visualization of the working area of MiniMag sensor.
Inactive areas of magnetometer are shown in gray

20
Overhauser magnetometer MiniMag
2.3.1 Initial setup window, viewing GNSS data and entering the main menu
2.3.1.1 Initial setup window
After turning on the power, the initial setup window should appear on the display screen
(Figure 17) with an option to set the date, time and number of the work area, as well as indicating
the amount of free memory (after clearing the memory, this value should be 4194304 bytes).
Information about the amount of free memory is necessary to make a decision on preliminary
cleaning of the memory before starting operations or on continuing survey with the remaining
memory. Before starting survey, it is recommended to erase previously recorded data (see
paragraph 2.3.4).
Figure 17 –Initial setup menu
To set the date, current time and number of the work area, the cursor «|»is used, and typing could
be done using numeric keypad . The cursor moves automatically after entering the value.
Keys and may be used to move the cursor in one direction or another, regardless of the
value of previously set values.
The date data is entered in the format “date / month / year” (DD / MM / YY), and time data −in
the format “hours: minutes: seconds” (hh: mm: ss.s). When seconds are set, the clock stops. To
start the clock with set time and send the information typed to the memory, press the key .
When used to determine the planimetric coordinates of a satellite navigation system, the
installation and synchronization of time should be carried out according to the GNSS receiver data.
By default, the date remains undefined, and the start of the clock will start from the moment when
the device is turned on.
If there is a signal from the GNSS satellite system, the time is automatically synchronized in the UTC
± 0 zone. User does not need to enter the time and date manually; for the local time zone, the time
will be adjusted when writing data to the computer.
2.3.1.2 Viewing GNSS data
GNSS data can be viewed by moving from the main menu via command . At the same time,
a window with GNSS data in WGS-84 system (Figure 18) will appear on the display screen: latitude
(Lat), longitude (Lon), absolute height relative to sea level in meters (Alt (msl)), velocity between
pickets in km / h, horizontal dilution of precision (HDOP), measurement mode (2D or 3D depending
on the number of satellites used), as well as the number of visible and used satellites.
Table of contents
Other GEODEVICE Measuring Instrument manuals
Popular Measuring Instrument manuals by other brands

Brainstorm Electronics
Brainstorm Electronics SR-15+ Operation manual
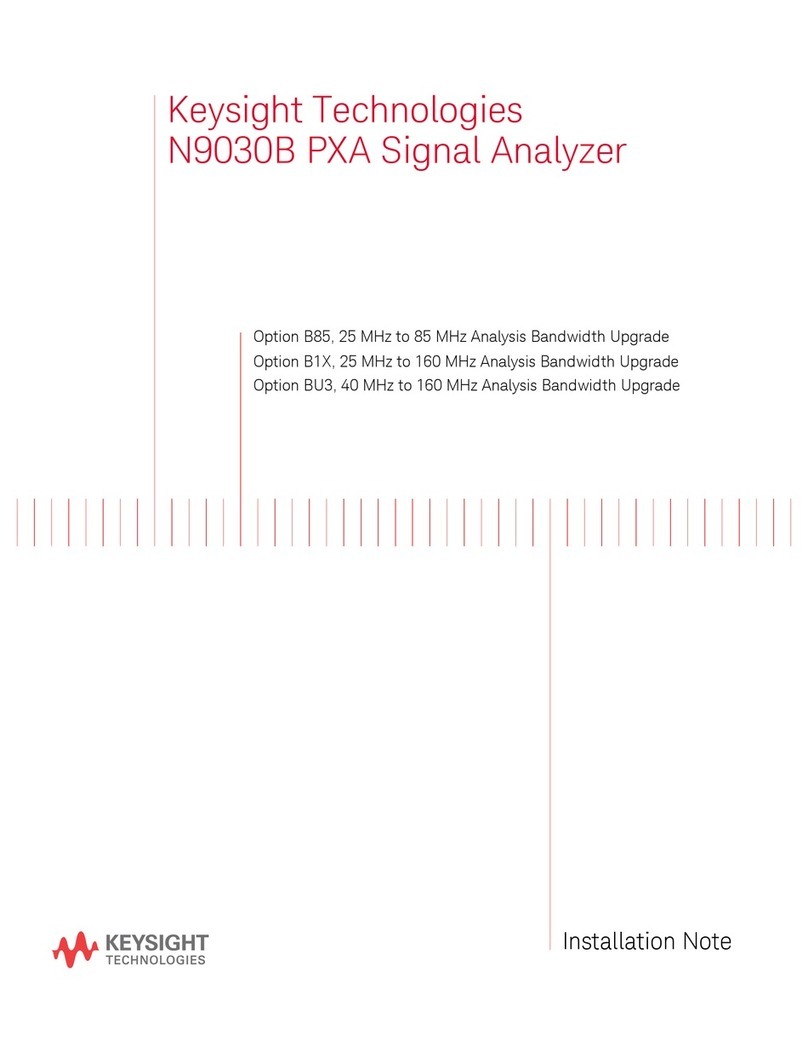
Keysight Technologies
Keysight Technologies N9030B Installation notes

Eastern Energy
Eastern Energy 7752 Operation manual
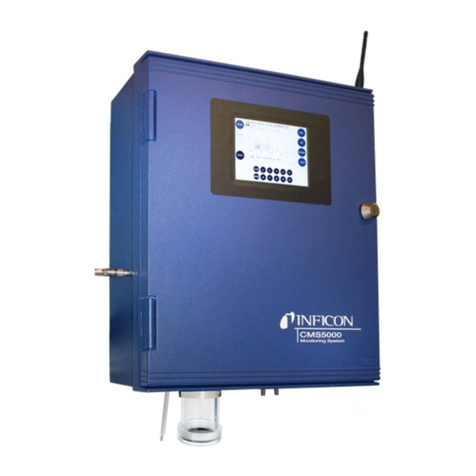
Inficon
Inficon CMS5000 instruction sheet

Nielsen
Nielsen PPM 360 METER Equipment manual
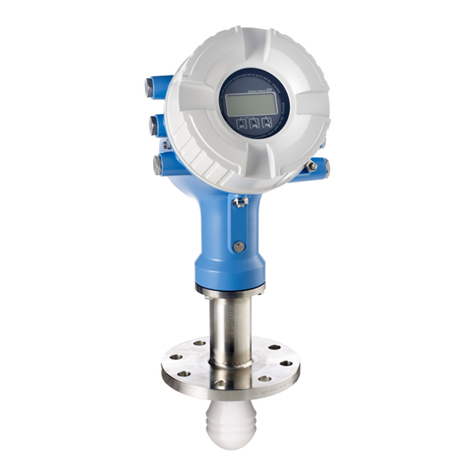
Endress+Hauser
Endress+Hauser Micropilot NMR81 Brief operating instructions