GFS Deluxe User manual

Deluxe Control Panel
Operator Manual
Document Number: 1056655 rev 0
Publication date 12/02/2021
Read and keep this manual for future reference. All personnel operating the equipment described in this manual should review and understand
all instructions before use.

Table of Contents
Introduction ............................................................................................................................................ 3
About Global Finishing Solutions LLC .............................................................................................. 3
Contacting Global Finishing Solutions .............................................................................................. 3
Conventions used in this manual ...................................................................................................... 4
Safety notices ......................................................................................................................... 4
Information notices ................................................................................................................. 4
General safety ........................................................................................................................................ 5
Product safety ........................................................................................................................................ 7
Deluxe control panel ............................................................................................................................... 8
Operating modes and controls ................................................................................................................. 9
Optional equipment setup ...................................................................................................................... 11
Common device setup ................................................................................................................... 11
If applicable: Manual balance setup ....................................................................................... 11
If applicable: Consta-Flow setup ............................................................................................ 12
Device setup for spray booths ........................................................................................................ 16
If applicable: Auto Balance setup ........................................................................................... 16
If applicable: Air proving switch setup ..................................................................................... 18
If applicable: Dirty filter alert setup ......................................................................................... 20
Device setup for powder and dust booths ....................................................................................... 21
If applicable: Pulse control board setup .................................................................................. 21
If applicable: Redundant filter alert setup ................................................................................ 23
Using the spray booth ........................................................................................................................... 25
Starting the booth ......................................................................................................................... 25
If applicable: Economy mode ......................................................................................................... 25
Shutting down the booth ................................................................................................................ 26
Using the dust or powder booth ............................................................................................................. 27
Starting the booth ......................................................................................................................... 27
Filter cleaning ............................................................................................................................... 27
Auto cleaning ....................................................................................................................... 27
Continuous cleaning ............................................................................................................. 27
Downtime cleaning ............................................................................................................... 27
Redundant filter monitoring ............................................................................................................ 28
Shutting down the booth ................................................................................................................ 28
Troubleshooting .................................................................................................................................... 29
Global Finishing Solutions 2 1056655 rev 0

Introduction
About Global Finishing Solutions LLC
Leading the Industry in Paint Booth and Finishing System Technology
With decades of experience, Global Finishing Solutions is the leading manufacturer of paint booths and
finishing systems for many industries, including automotive refinish, aerospace and defense, industrial
manufacturing, woodworking, and large equipment. By combining high-quality components, strong
relationships with paint manufacturers, and our experienced distribution network, GFS provides the best
equipment and support to set your business up for success.
Contacting Global Finishing Solutions
General information
• Toll-free: 800-848-8738
• Fax: 715-597-2193
• Online: www.globalfinishing.com
Technical support
• Toll-free: 800-848-8738
• Fax: 715-597-8818
Parts and filters
• Toll-free: 800-848-8738
• Fax: 888-338-4584
Introduction
Global Finishing Solutions 3 1056655 rev 0

Conventions used in this manual
This section describes how information is presented, organized, and referenced within this manual.
Safety notices
This manual uses the following standards to identify conditions related to safety hazards and equipment
damage.
Table 1. Safety notices
Symbol Description
DANGER Indicates an imminent hazard that will result in death.
WARNING Indicates a hazard that can result in serious personal injury or death.
CAUTION Indicates a hazard that can result in personal injury.
NOTICE Indicates a situation that can result in equipment or property damage, but poses no risk
of personal injury.
Information notices
In addition to the safety notices described above, this manual uses a boldface keyword to identify certain
other types of information.
Table 2. Information notices
Keyword Description
NOTE Denotes general information that provides additional context or guidance.
Important Denotes information to which you should pay special attention.
Reference Directs you to related content in a separate document.
Prerequisites Specifies other tasks that must be completed or conditions that must exist before you
perform the current task.
Scope Describes limitations to the current task or conditions under which the task applies or
does not apply to the procedure.
Introduction
Global Finishing Solutions 4 1056655 rev 0

General safety
Follow all safety guidelines when assembling, operating, or servicing this product.
WARNING
There are inherent hazards associated with the operation and service of this equipment. For your personal
safety, observe all safety information. Failure to observe these safety practices can result in personal injury
or death.
WARNING
Operation and maintenance of this product must be performed properly by qualified personnel who observe
the warnings in all documentation and notes provided with and on the product.
WARNING
Follow all general standards for installation and safety for work on installations. Follow all good practices for
the proper use of lifting tackle and equipment. The use of protective equipment such as safety goggles and
protective footwear must be considered.
WARNING
All persons who will operate, service, inspect, or otherwise handle this product must read and understand
the safe operating practices, safety precautions, and warning messages in this documentation.
WARNING
The roofs of GFS equipment are not designed or intended to be walked upon or to support weight of any
kind. As designed and manufactured, equipment roofs do not meet the minimum requirements of a safe
walking and/or working surface under OSHA 1910.22. Under no circumstances should the roof be used by
maintenance personnel or others for walking, standing, or storage of any kind. When necessary, roof
access should be secured through the use of a properly supported platform that satisfies the minimum load
requirements specified by ASCE 7 (Minimum Design Loads and Associated Criteria for Buildings and Other
Structures) and ASCE 37 (Design Loads on Structures during Construction). Additionally, personnel should
always utilize appropriate fall safety protocols when using an elevated platform. Use of the roof in a contrary
manner may result in injury and/or death.
WARNING
Comply with OSHA guidelines and with all applicable local electrical, safety, and fire codes and standards.
WARNING
All field wiring provided must comply with local codes or, in the absence of local codes, the National
Electrical Code (NFPA 70).
WARNING
Electrical installation should be completed by a qualified electrician. Installation must meet all applicable
national, state, and local electrical codes.
WARNING
Ensure that all electrical components are grounded to a central ground.
General safety
Global Finishing Solutions 5 1056655 rev 0

WARNING
Disconnect and lock out the main electrical service before installing, adjusting, or servicing the product.
WARNING
Guards and covers that prevent contact with electrically energized or moving parts are required and must
not be removed or left open during operation.
CAUTION
Read and save these instructions before attempting to install, operate, or maintain the product described.
Protect yourself and others by observing all safety information. Failure to comply with instructions could
result in personal injury and/or property damage. Retain these instructions for future reference.
CAUTION
This manual contains statements that relate to worker safety. Read this manual thoroughly and comply as
directed. Operate this equipment in accordance with the guidelines set forth in this manual. It is impossible
to list all potential hazards of this equipment. Instruct all personnel involved with this equipment in the safe
conduct and operation of the system. GFS recommends that only qualified personnel operate and maintain
this equipment.
CAUTION
Safety signs, panels, and labels that are normally affixed to the product must be replaced immediately if
illegible or missing.
CAUTION
New or replacement parts that are installed during repair or maintenance must include all safety signs,
panels, and labels as specified by the manufacturer. These must be affixed to the new or replacement parts
as specified by the manufacturer.
CAUTION
Where applicable, use earplugs or take other safety measures for hearing protection.
NOTICE
The product must be installed and serviced only by a trained, qualified service technician. Incorrect
installation may void the warranty.
NOTICE
If you have questions about the warranty, please contact your distributor prior to contacting GFS.
General safety
Global Finishing Solutions 6 1056655 rev 0

Product safety
For product safety information, refer to the documentation that accompanied your equipment.
Product safety
Global Finishing Solutions 7 1056655 rev 0

Deluxe control panel
The Deluxe control panel provides pushbuttons and indicator lights for operating a wide variety of
equipment while monitoring for safety and performance.
NOTE
The Deluxe control panel is available for single or three phase power circuits and all standard North
American voltages. Custom voltages are available.
The control panel is mounted on the outside of the booth or on a nearby wall in a convenient position for the
operator.
Figure 1. Deluxe control panel
Deluxe control panel
Global Finishing Solutions 8 1056655 rev 0

Operating modes and controls
The front of the Deluxe control panel provides the following controls and indicator lights:
NOTE
Some of these controls are optional and may not be present on every control panel.
Table 3. Spray booth operating states and controls
Displayed Text Description
Main Power Disconnect Provides a means to disconnect power, along with the ability to add lockout/tagout safety
devices.
Booth Lighting On/Off Two-position selector switch that operates the booth lights.
System Start Starts the exhaust ventilation.
System Stop Stops the exhaust ventilation.
System Energized Indicates that the system is energized when lit.
Exhaust Unit On Indicates that the exhaust fan is operating when lit.
Post Purge Indicates that the booth is running a post-spray purge cycle when lit.
AMU Burner Two position selector switch that operates the AMU burner.
AMU Blower On Indicates that the AMU blower is on when lit.
AMU Burner On Indicates that the AMU burner is on when lit.
AMU Flame Failure Indicates that the AMU burner has experienced a flame failure when lit.
AMU Dirty Filter Indicates that the AMU filter is dirty when lit.
Fire System Fault Indicates a fire protection system fault or alarm when lit.
Keypad with Dial Used to set the airflow in booths with manual balance.
Airflow Controller Pressure gauge with setpoint needles used for setting airflow in booths with Consta-
Flow systems.
Booth Balance Controller Pressure gauge with setpoint needles used for setting airflow in booths with Auto Bal-
ance systems.
Temperature Selector Dial Used to select booth temperature.
Temperature Controller LCD Dis-
play Used to set high and low temperature setpoints and monitor booth temperature.
Dirty Filter Indicates that filters are loaded and air solenoid valve is disabled.
Table 4. Powder and dust booth operating states and controls
Displayed Text Description
Main Power Disconnect Provides a means to disconnect power, along with the ability to add lockout/tagout safety
devices.
Booth Lighting On/Off Two-position selector switch that operates the paint booth lights.
System Start Starts the exhaust ventilation.
System Stop Stops the exhaust ventilation.
System Energized Indicates that the system is energized when lit.
Exhaust Unit On Indicates that the exhaust fan is operating when lit.
Filter Fault Indicates that the system has faulted due to redundant filter loading.
Operating modes and controls
Global Finishing Solutions 9 1056655 rev 0

Displayed Text Description
Intake Unit On Indicates that the intake fan is operating when lit.
Fire System Fault Indicates a fire protection system fault or alarm when lit.
Keypad with Dial Used to set the airflow in booths with manual balance.
Airflow Controller Pressure gauge with setpoint needles used for setting airflow in booths with Consta-
Flow systems.
Auto/Continuous Cleaning Mode Two-position selector switch that operates the cleaning methods for primary filters for
Powder and Dust Collection Modules. See “Filter cleaning” (page 27) for more informa-
tion.
Downtime Cleaning Start Pulses primary filters in Powder and Dust Collection Modules. See “Filter cleaning”
(page 27) for more information.
Operating modes and controls
Global Finishing Solutions 10 1056655 rev 0

Optional equipment setup
Common device setup
If applicable: Manual balance setup
Scope: This task applies to spray, powder, and dust booths if the site purchased the optional manual
balance system.
Prerequisites:
• Filters must be installed in the booth.
• During setup, perform measurements in an empty booth.
NOTE
A velometer is required to test the airflow and properly set up manual balance.
Deluxe control panels equipped with optional manual balance systems have a keypad with a dial that
controls the variable frequency drive (VFD). You can use the keypad and dial to manually increase the fan
frequency as the filters load. After filter replacement, the fan frequency should be returned to the initial
setting.
Figure 2. Manual balance keypad
Perform the steps below to configure manual balance:
Optional equipment setup
Global Finishing Solutions 11 1056655 rev 0

1. Use the keypad and dial to set the fan frequency.
NOTE
The typical startup frequency for the fan is 54 Hertz (Hz).
2. Press the Set button.
3. Enter the booth and use a velometer to test the airflow.
NOTE
For spray booths, refer to the paint manufacturer's recommended airflow.
4. Repeat steps 1-3 to adjust the fan frequency until your booth reaches the desired airflow.
5. Record the clean-filter fan frequency in Hertz.
NOTE
This is the setting that the VFD should be returned to every time the filters are replaced.
6. As the booth’s filters begin to load, manually increase the VFD’s frequency setting to maintain the
desired airflow.
If applicable: Consta-Flow setup
Scope: This task applies to spray, powder, and dust booths if the site purchased the optional Consta-Flow
system.
Prerequisites:
• Filters must be installed in the booth.
• During setup, perform measurements in an empty booth.
NOTE
A velometer is required to test the airflow and properly set up Consta-Flow.
Deluxe control panels equipped with optional Consta-Flow systems automatically adjust the fan speed and
maintain consistent airflow throughout the life of the filter.
NOTE
Consta-Flow systems may be configured with either a sensor installed in the exhaust stack on site or with a
flow ring built into the exhaust fan. Refer to the following diagrams:
Optional equipment setup
Global Finishing Solutions 12 1056655 rev 0

H
D
F
C
G
E
AB
A: Low-pressure bulkhead fitting
B: High-pressure bulkhead fitting
C: Low-pressure sensing tube
D: High-pressure sensing tube
E: Exhaust stack
F: Consta-Flow sensor
G: Control panel
H: Outside booth (minimum 3 feet from any opening)
Figure 3. Consta-Flow sensor
Optional equipment setup
Global Finishing Solutions 13 1056655 rev 0

A: Low-pressure bulkhead fitting
B: High-pressure bulkhead fitting
C: Exhaust fan
D: Motor
E: Flow ring (Sure-Aire or Piezometer)
F: Exhaust stack
G: Control panel
H: Outside booth (minimum 3 feet from any opening)
Figure 4. Consta-Flow flow ring
Perform the steps below to configure the Consta-Flow airflow controller (Photohelic):
1. With the booth off, ensure that the black indicator needle on the Photohelic is set to zero.
To adjust the indicator needle, use a small screwdriver to turn the zero adjustment screw.
Optional equipment setup
Global Finishing Solutions 14 1056655 rev 0

2. Using the provided tool, twist the knobs on either side of the Photohelic so that the left-most orange
needle is positioned all the way to the left and the right-most orange needle is positioned all the way to
the right.
Figure 5. Photohelic adjustment tool
3. Start the booth.
The VFD ramps the exhaust fan up and the black indicator needle moves into position between the two
orange needles.
4. Use the velometer to test the booth’s airflow.
NOTE
Refer to the equipment's Design Drawings to determine the recommended airflow.
5. If the airflow is acceptable, use the adjustment tool to move the orange needles to either side of the
indicator needle, establishing the VFD setpoint.
Optional equipment setup
Global Finishing Solutions 15 1056655 rev 0

6. If the airflow is unacceptable, use the adjustment tool to move the orange needles to the desired
location. The indicator needle will adjust automatically to be within the setpoints.
NOTE
Move the orange needles lower on the Photohelic for less airflow in the booth and higher for more
airflow.
The Consta-Flow system is now configured. The VFD will ramp the exhaust fan up or down to maintain
consistent airflow.
Device setup for spray booths
If applicable: Auto Balance setup
Scope: This task applies only to pressurized booths if the site purchased the optional Auto Balance
system.
Prerequisites:
• Filters must be installed in the booth.
• During setup, perform measurements in an empty booth.
NOTE
A velometer is required to test and properly set up intake airflow.
Deluxe control panels equipped with optional Auto Balance systems automatically adjust the fan speed and
maintain consistent airflow throughout the life of the filter.
Optional equipment setup
Global Finishing Solutions 16 1056655 rev 0

NOTE
The Auto Balance system should be installed as shown in the Electrical Drawings and in the following
diagram.
A: High-pressure air-sensing pressure tip (Locate inside the booth a minimum of 84 inches from the floor at at least 24 inches from
any corner.)
B: High-pressure air-sensing tube
C: Low-pressure air-sensing pressure tip (factory installed)
D: Control panel
E: Outside booth
Perform the steps below to configure the booth balance controller (Photohelic):
1. With the booth off, ensure that the black indicator needle on the Photohelic is set to zero.
To adjust the indicator needle, use a small screwdriver to turn the zero adjustment screw.
Optional equipment setup
Global Finishing Solutions 17 1056655 rev 0

2. Using the provided tool, twist the knobs on either side of the Photohelic so that the left-most orange
needle is positioned at zero and the right-most orange needle is positioned at positive 0.03 inches w.c.
3. Start the booth.
4. Use the velometer to test the booth's airflow.
NOTE
Refer to the equipment's Design Drawings to determine the recommended airflow.
5. If the airflow is unacceptable, adjust the intake or air make-up unit fan speed accordingly. The indicator
needle will adjust automatically to maintain the booth pressure within the setpoints.
NOTE
Move the orange needles on the Photohelic lower for a more negative booth pressure and higher for a
more positive booth pressure.
The Auto Balance system is now configured. The VFD will ramp the exhaust fan up or down to maintain
consistent airflow and booth pressure.
If applicable: Air proving switch setup
Scope: This task applies to spray booths if the site purchased the optional air proving switch.
Prerequisites:
• The air solenoid valve must already be installed.
• Filters must be installed in the booth.
• During setup, perform measurements in an empty booth.
NOTE
A velometer is required to test and properly set up the air proving switch.
Optional equipment setup
Global Finishing Solutions 18 1056655 rev 0

The optional air proving switch is part of the booth’s ventilation system and is used to prove airflow across
the exhaust fan. Loss of exhaust airflow causes the air solenoid valve to shut off, turning off spray air in the
booth.
Figure 6. Air proving switch
NOTE
The desired mounting location of the switch is near the fan(s) being monitored. If necessary, the switch can
be mounted remotely and a maximum of 50 feet of tubing can be used to connect the fan(s) to the switch.
Perform the steps below to configure the air proving switch(es):
1. Ensure that the ventilation system is in operation at the airflow referenced in the Design Drawings.
2. Remove the cover from the air proving switch and locate the adjustment screw. Carefully turn the screw
until it is fully counterclockwise.
3. Slowly turn the adjustment screw clockwise until the switch trips.
NOTE
When the switch is open, measure the control voltage (24 volts DC or 120 volts AC) across the switch.
When the switch trips, the voltage will go to 0 volts.
4. Carefully rotate the adjustment screw 1-1/2 turns counterclockwise from the trip point.
The air proving switch is now set.
Optional equipment setup
Global Finishing Solutions 19 1056655 rev 0

If applicable: Dirty filter alert setup
Scope: This task applies only to spray booths if the site purchased the optional dirty filter alert.
Prerequisites:
• The air solenoid valve must already be installed.
• Filters must be installed in the booth.
The optional dirty filter alert will sense the differential pressure across the exhaust filters. When properly set
up, this alert will light the dirty filter light and prevent any additional spraying if the differential pressure
exceed the specification.
Figure 7. Differential pressure switch
Perform the steps below to configure the dirty filter alert:
1. In the junction box, carefully turn the differential pressure switch adjustment screw fully
counterclockwise.
NOTE
A manometer or similar device should be used to adjust the switch correctly.
2. Turn the adjusting screw four complete turns clockwise to engage the spring.
NOTE
Refer to the filter manufacturer’s recommendations for filter loading. This example uses a typical paint
arrest filter with a recommended final filter load pressure of 1/2-inch w.c. when the filter is dirty. Actual
filter loading values vary based on manufacturer, material, and performance.
3. Set the pressure switch trip point equal to the desired final filter pressure loading.
Optional equipment setup
Global Finishing Solutions 20 1056655 rev 0
Table of contents
Popular Control Panel manuals by other brands
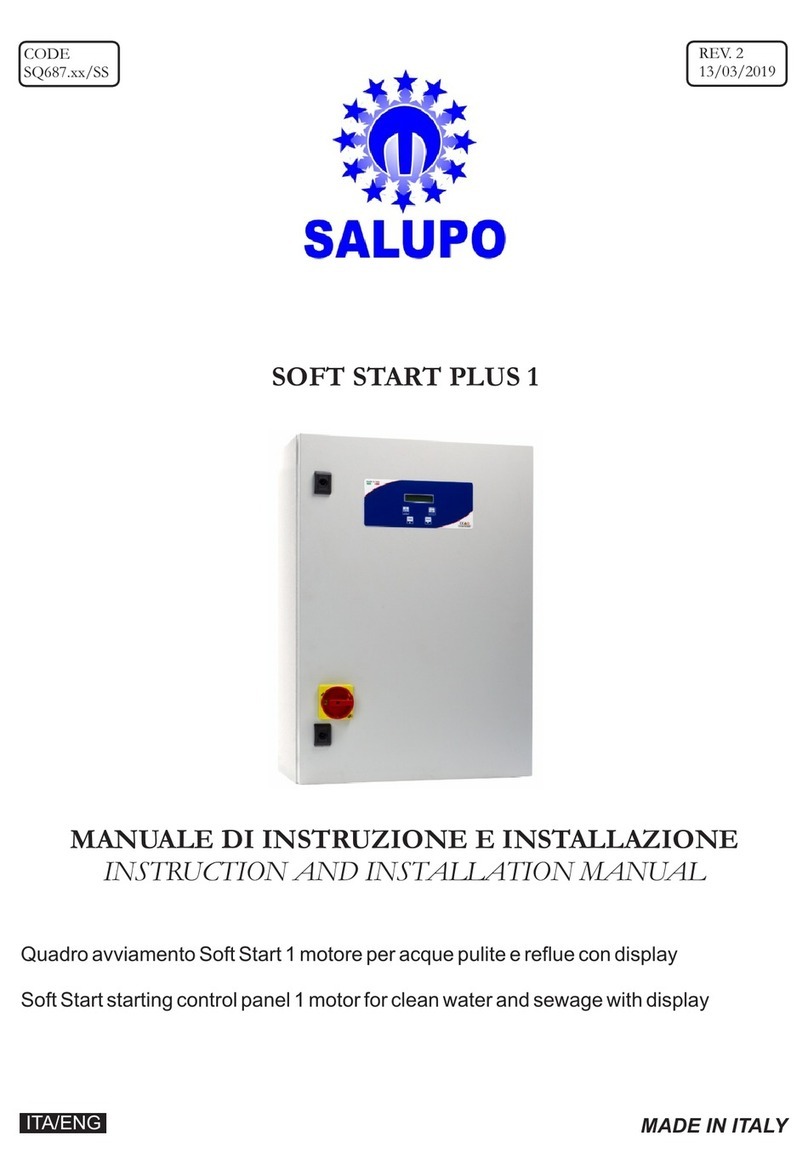
SALUPO
SALUPO SOFT START PLUS 1 Instruction and installation manual
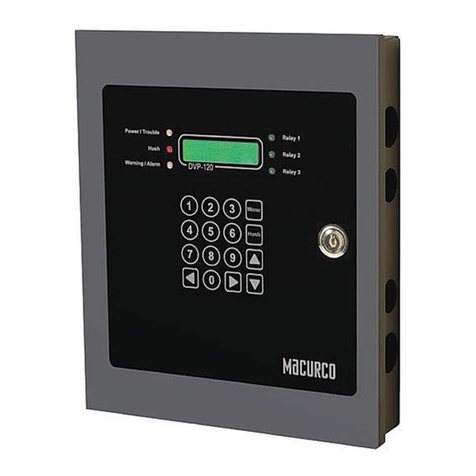
Macurco
Macurco DVP-120 User instructions
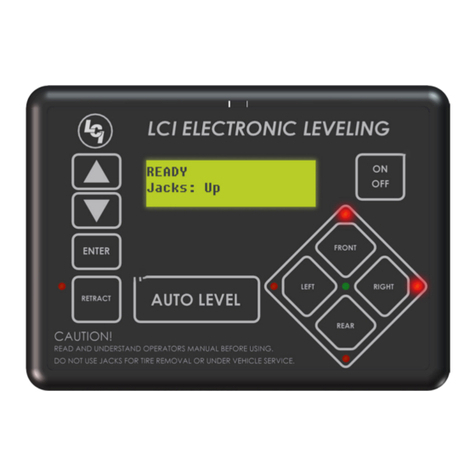
Lippert Components
Lippert Components LCI Level-Up owner's manual
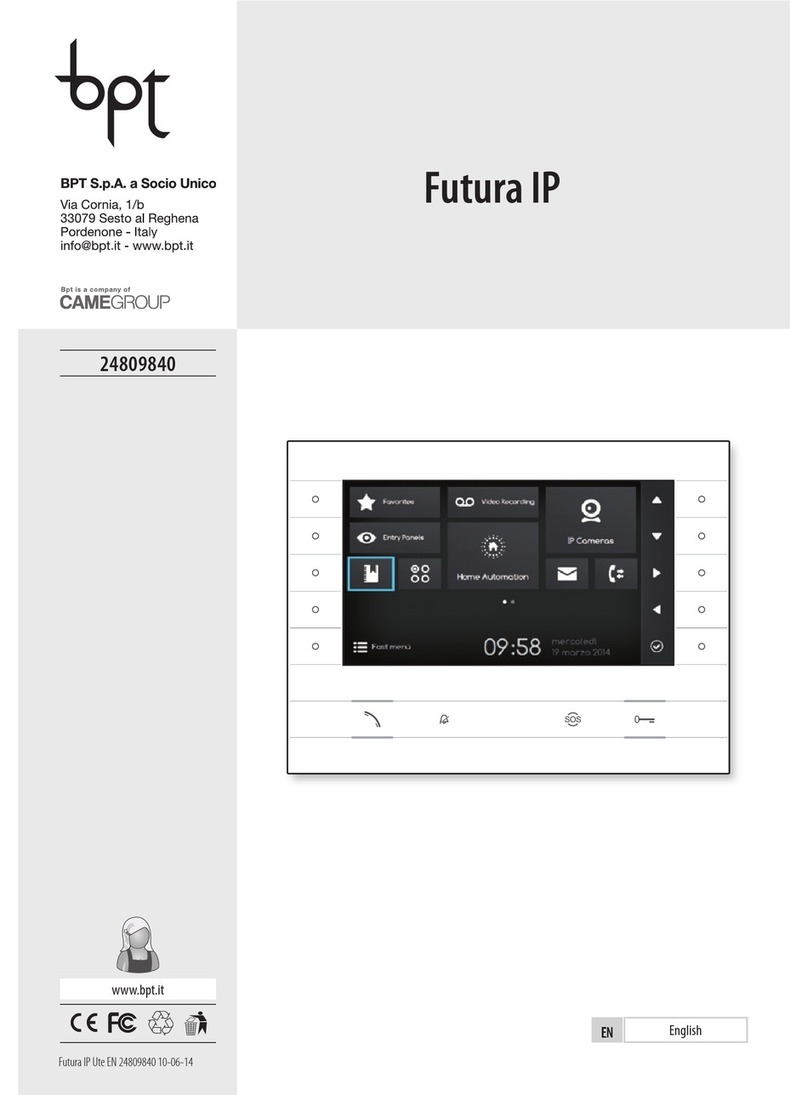
Bpt
Bpt Futura IP manual

HeatLink
HeatLink HEP025RT Installation, operation and maintenance manual
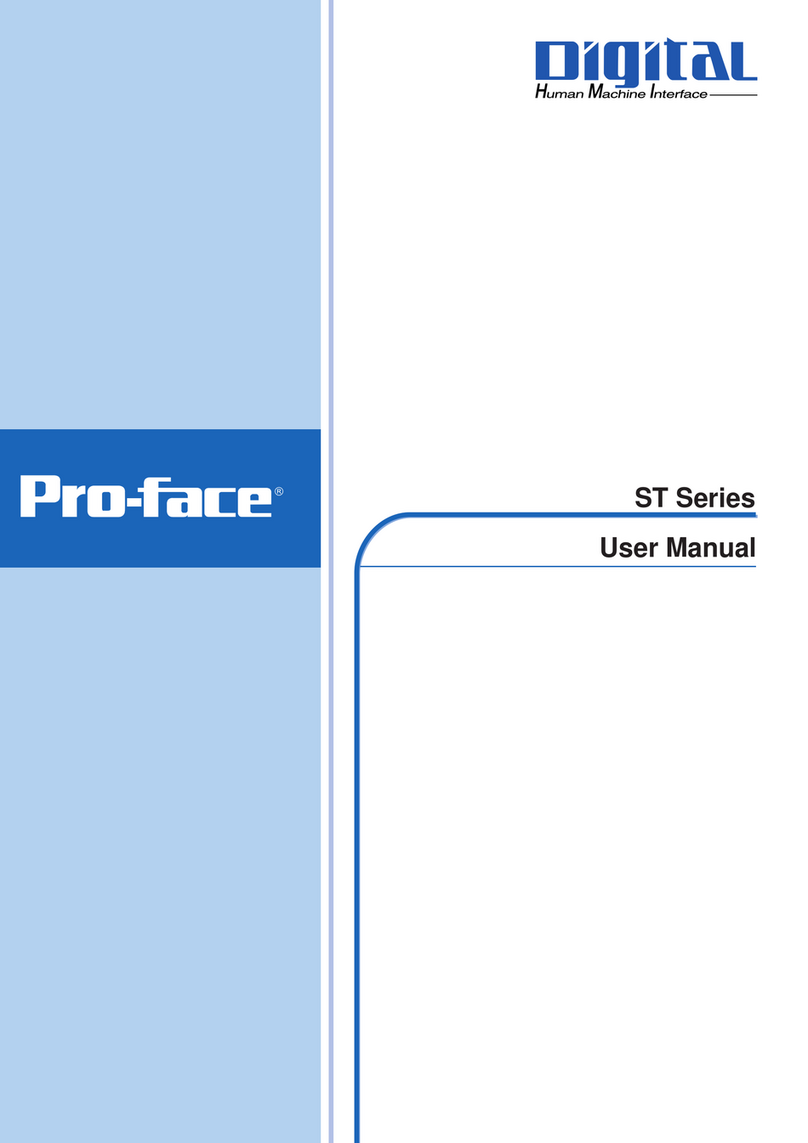
Pro-face
Pro-face Pro-face ST Series user manual

Tecnocontrol
Tecnocontrol CITY CE400 User instructions
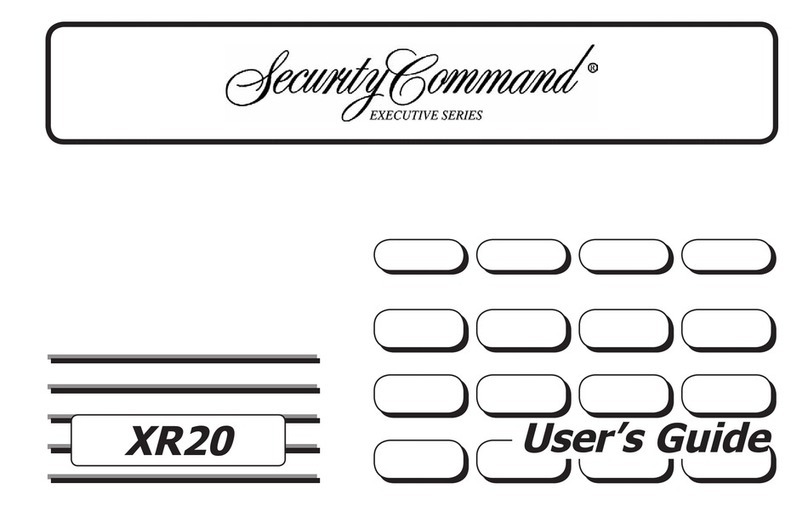
Security Command
Security Command XR20 Executive Series user guide
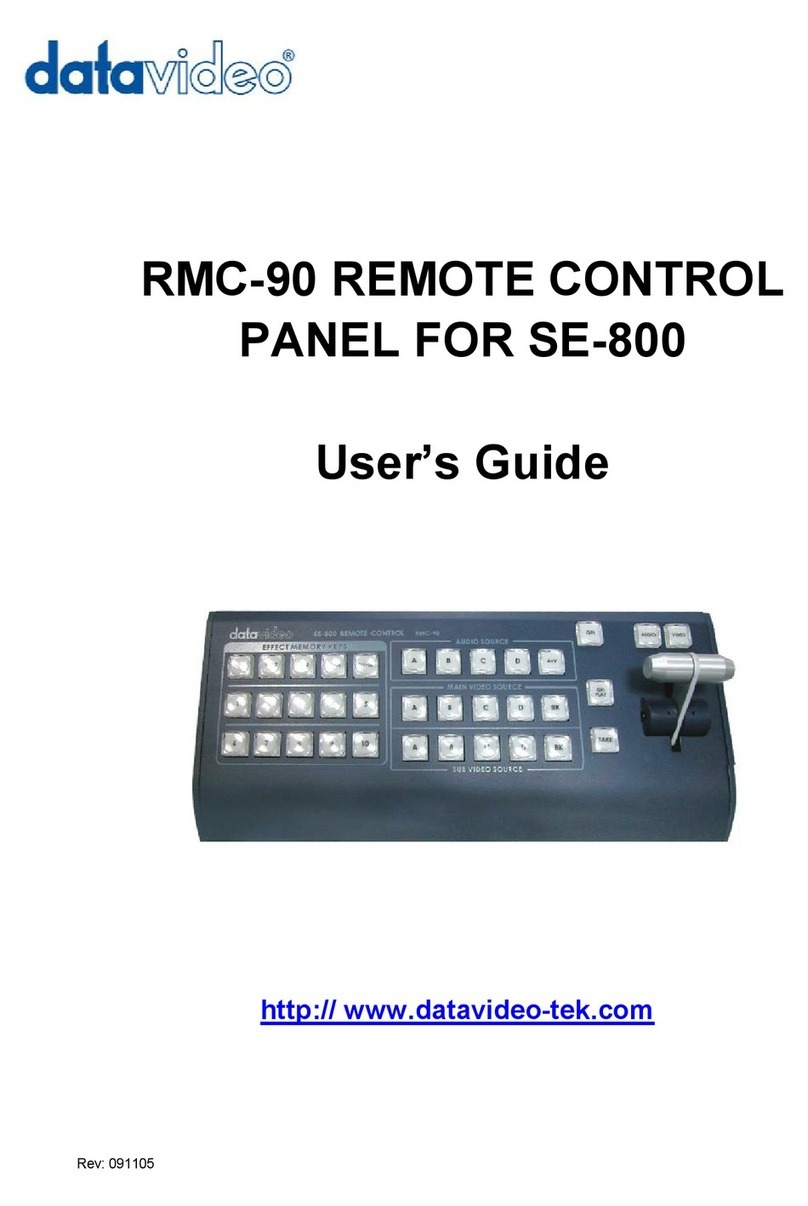
Data Video
Data Video RMC-90 user guide

LUNATONE
LUNATONE 24035465 manual

Pro-tec
Pro-tec 6100 Installation and commissioning manual
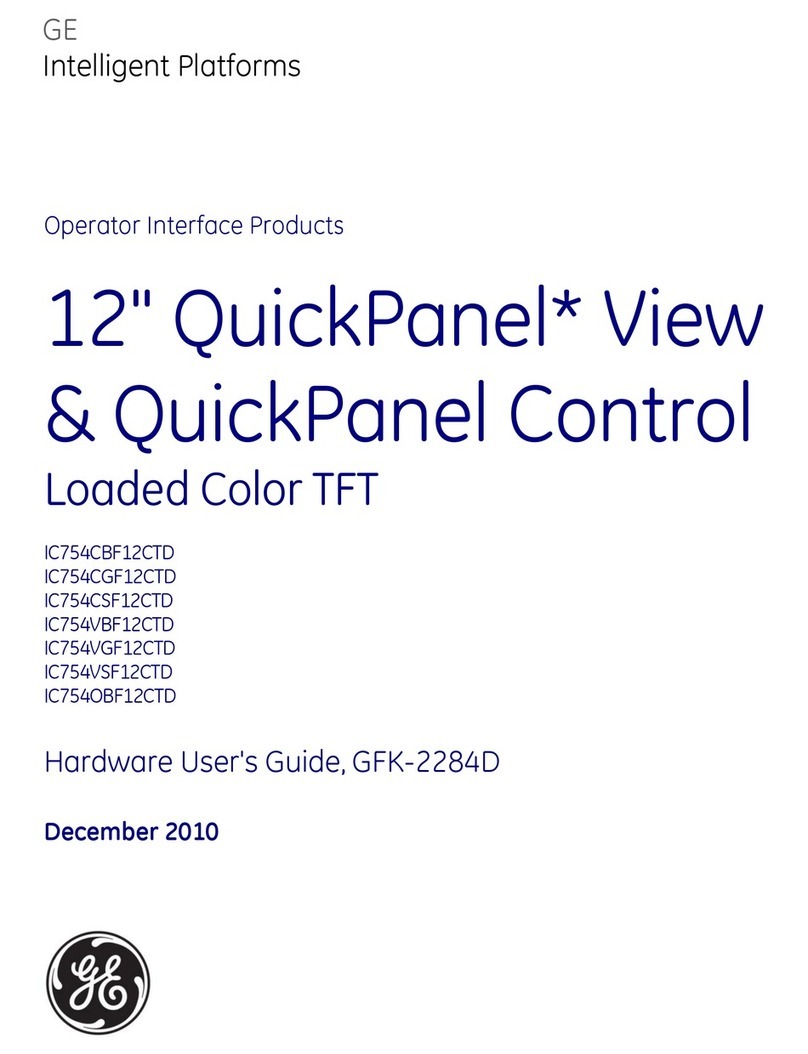
GE Intelligent Platforms
GE Intelligent Platforms QuickPanel IC754CBF12CTD Operator Interface Products