Gigarise SetPro MV Series User manual

SetPro
MV Series Controllers RS-485 Communication Instruction Manual
MODBUS Protocol Reference Guide
1. COMMUNICATION FUNCTIONS
1.1 General -----------------------------------------------------------------------------1
2. SPECIFICATIONS
2.1 Communication Specifications ----------------------------------------------------2
3. CONNECTION
3.1 Terminal Allocation ----------------------------------------------------------------3
3.2 Wiring ------------------------------------------------------------------------------3
4. SETTING OF COMMUNICATION CONDITION
4.1 Set Items ---------------------------------------------------------------------------4
4.2 Setting Operation Method --------------------------------------------------------5
5. MODBUS COMMUNICATION PROTOCOL
5.1 General -----------------------------------------------------------------------------6
5.2 Composition of Message ----------------------------------------------------------6
5.3 Response of Slave Station ---------------------------------------------------------7
5.4 Function Code ---------------------------------------------------------------------8
5.5 Calculation of Error Check Code (CRC-16) ----------------------------------------8
5.6 Transmission Control Procedure --------------------------------------------------9
6. DETAILS OF MESSAGE
6.1 Read-out of Word Data [Function Code: 03] -------------------------------------11
6.2 Read-out of Read-Only Word Data [Function Code: 04] -------------------------12
6.3 Write-in of Word Data (1 word) [Function Code: 06] -----------------------------13
7. ADDRESS MAP AND DATA FORMAT
7.1 Data Format -----------------------------------------------------------------------14
7.2 Data Address Map ----------------------------------------------------------------15
8. TROUBLESHOOTING
8.1 Troubleshooting ------------------------------------------------------------------17

Version 4.0
- 1 -
1. Communication Functions
1.1 General
zMV-D94 provides a communication function by RS-485 interface, by which it can
transmit and receive data to and from host computer, programmable controller,
graphic display panel, etc.
zThe communication system consists of master station and slave stations. Up to
255slave station can be connected per master station.
zIn order that the master station and slave station can communicate, the format of
the transmit/receive data must coincide. For the MV-D94, the format of the
communication data is determined by the MODBUS protocol (RTU mode).
zPlease use an RS-232C→RS-485 converter in case of designating a personal
computer or other devices which have an RS-232C interface as a master station.

Version 4.0
- 2 -
2. Specifications
2.1 Communication Specifications
Item Specification
Electrical specification Based on EIA RS-485
Transmit system 2-wire, semi-duplicate
Synchronizing system Asynchronous mode
Connection format 1 : N
Number connection unit Up to 255 units
Transmission distance 500m max
Transmission speed 2400 / 4800 / 9600 / 19200 selectable
Start bit 1 bit
Data length bit 8 bits
Parity bit None
Data format
Stop bit 2 bits
Transmission code HEX value (MODBUS RTU mode)
Error detection CRC-16 bits
Isolation Functional isolation between transmission circuit
and others (with stand voltage: 500V AC).
A typical MODBUS protocol character is shown below:
1 2 3 4 5 6 7 8 9 10 11
Start bit Data bits Stop bits
One character is including 1 Start bit and 8 Data bits and 2 Stop bits.

Version 4.0
- 3 -
3. Connection
WARNING !!
For avoiding electric shock and malfunctions, don’t turn on the power supply until
all wiring has been completed.
3.1 Terminal Allocation
Terminal number Signal name
13 TX+
14 TX-
3.2 Wiring
zUse twisted pair cables with shield. Recommended cable: UL2464, UL2448, etc.
zThe total extension length of the cable is up to 500m. A master station and up to
255 units of the MV-D94 can be connected per line.
zBoth ends of the cable should be connecting with terminate resistors 100Ω 1/2W.
zThe shield wire of the cable should be grounded at one place on the master
station unit side.

Version 4.0
- 4 -
4. SETTING OF COMMUNICATION CONDITION
zIn order that the master station and MV-D94 can correctly communicate,
following settings are required.
zAll communication condition settings of the master station are the same as those
of MV-D94.
zMV-D94 connected on a line are set to address (ADDR), which are different from
each other.
4.1 Set Items
The parameters to be set are shown in the following table. Set them by operating the
front panel keys.
Parameter Item Value at
delivery Setting range Remarks
Transmission
speed 9600 2400/4800/9600/19200
Data length 8 bits Fixed (can’t be changed)
Stop bit 2 bit Fixed (can’t be changed)
BAUD
Parity setting None Fixed (can’t be changed)
Set the same
communication
condition to the
master station
and all slave
station.
ADDR Address 1 1 to 255
Set a different
value to each
station.

Version 4.0
- 5 -
4.2 Setting Operation Method
The following example shows how to set the communication condition.
Example: Setting a transmission speed is 9600 bps and address at 12 on a station.
Key operation Indication Description
Power ON 25/100 Power on running state (PV/SV indication)
SET (5 seconds) PB Press SET key simultaneously for approximately 5
seconds to get level parameter.
SET (5 seconds) TYPE Press SET key simultaneously for approximately 5
seconds to get level parameter.
SET Press SET key to go into level.
SET ADDR Press SET key repeatedly until ADDR is display.
△ or ▽ ADDR/12 Press △ or ▽ key to setting “ADDR=12"
SET BAUD Press SET key again to select next parameter “BAUD"
△ or ▽ BAUD/9.6K Press △ or ▽ key to setting “BAUD=9.6K"
SET BAUD Press SET key to save “BAUD".
SET + ▽ 25/100 Press SET +▽ one time to return the normal indication
(PV/SV indication).

Version 4.0
- 6 -
5. MODBUS COMMUNICATION PROTOCOL
5.1 General
The communication system by the MODBUS protocol is that the communication is
always started from the master station and a slave station responds to the received
message.
Transmission procedures is as shown below.
1. The master station sends a command message to a slave station.
2. The slave station checks that the address in the received message matches with the
own address or not.
3. If matched, the slave station executes the command and sends back the response
message.
4. If mismatched, the slave station leaves the command message and wait for the next
command message.
5. The master station can individually communicate with any one of slave stations
connected on the same line upon setting the address in the command message.
5.2 Composition of Message
Command message and response message consist of 4 fields; Address, Function
code, Data and CRC check code. And these are sends in this order. The allowable
character transmitted for all fields are hexadecimal 0-9, A-F
RTU mode framing
START ADDRESS FUNCTION DATA CRC CHECK END
T1-T2-T3-T4 8 BITS 8 BITS N × 8 BITS 16 BITS T1-T2-T3-T4
In the following, each field is explained.
1. Start
In RTU mode, messages start with a silent interval of at least 3.5 character times.
This is most easily implemented as a multiple of character times at the baud rate
that is being used on the network (shown as T1-T2-T3-T4 in the figure above). The
first field then transmitted is the device address.
2. Address
Address is the number specifying a slave station. Valid slave device addresses are in
the range 0f 1-255 decimal. A master addresses a slave by placing the slave address
in the address field of the message. When the slave sends its response, it places its
own address in this address field of the response to let the master know which slave
is responding. Address 0 is used for the broadcast address, which all slave stations
recognize. When the broadcast address (address 0) is applied on the command
message, no any response message will be sent from the slave stations.

Version 4.0
- 7 -
3. Function
This is a code to designate the function executed at a slave station. When a
message is sent from a master to a slave device the function code field tells the
slave what kind of action to perform. When the slave responds to the master, it uses
the function code field to indicate either a normal response or that some kind of
error occurred. For normal response, the slave simply echoes the original function
code. For an exception response, the slave returns a code that is equivalent to the
original function code with its most-signification bit set to a logic 1.
4. Data
Data are the data required for executing function codes. The composition of data
varies with function codes. Refer to chapter 6 for details.
A data address is assigned to each data in the temperature controller. For
reading/writing the data by communication, designate the data address.
5. CRC check
This is the code to detect message errors (change in bit) in the signal transmission.
On the MODBUS protocol (RTU mode), CRC-16 (Cyclical Redundancy Check) is
applied. For CRC calculation method, refer to section 5.5.
6. End
Following the last transmitted character, a similar interval of at least 3.5 character
times marks the end of message. A new message can begin after this interval.
5.3 Response of Slave Station
1. Response for normal command
To a relevant message, the slave station creates and sends back a response
message, which corresponds to the command message. The composition of
message in this case is the same as in section 5.2. Content of the data field depend
on the function code. For details, refer to Chapter 6.
2. Response for abnormal command
If contents of a command message have an abnormality (for example, non-actual
function code is designated) other than transmission error, the slave station does
not execute that command but creates and sends back a response message at error
detection. The composition of response message at error detection is shown on
below, the value used for function field is function code of command message plus
80H.

Version 4.0
- 8 -
ADDRESS FUNCTION (Function code + 80H) ERROR CODE CRC CHECK
8 BITS 8 BITS 8 BITS 16 BITS
Error Code Contents Description
01 Illegal function The function code received is not an allowable
action for the slave.
02 Illegal data address The data address received is not an allowable
address for the slave.
03 Illegal data value A value contained in the data field is not an
allowable value for the slave.
5.4 Function Code
The listing below shows the function codes supported by MV-D94 controllers.
Function code
Code Function Object
03 Read-out Holding Register
04 Read-out Input Register
06 Write-in Holding Register
5.5 Calculation of Error Check Code (CRC-16)
CRC-16 is the 2-bytes (16-bits) error check code. From the top of the message
(address) to the end of the data field are calculated.
The slave station calculates the CRC of the received message, and does not respond if
the calculated CRC is different from the contents of the received CRC code.
A procedure for generating a CRC is:
1. Load a 16-bits register with FFFF hex (all 1's). Call this the CRC register.
2. Exclusive OR the first 8-bit byte of the message with the low-order byte of the
16-bit CRC registers, putting the result in the CRC register.
3. If the LSB is 0: Shift the CRC register one bit to the right (toward the LSB),
Zero-filling the MSB.
If the LSB is 1: Shift the CRC register one bit to the right (toward the LSB),
Zero-filling the MSB. Exclusive OR the CRC registers with the polynomial value
A001 hex.

Version 4.0
- 9 -
4. Repeat step 3 until 8 shifts have been performed. When this is done, a complete
8-bit byte will have been processed.
5. Repeat step 2 through 5 for the next 8-bit byte of the message. Continue doing this
until all bytes have been processed.
6. The final content of the CRC register is the CRC value. The CRC field is appended to
the message as the last field in the message. When this is done, the low-order byte
of the field is appended first, followed by the high-order byte.
The CRC high-order byte is the last byte to be sent in the message.
5.6 Transmission Control Procedure
1. Transmission procedure of master station
The master station must proceed to a communication upon conforming to the
following items.
1-1. Before sending a command message, provide 44 bits time or more vacant
status.
1-2. For sending, the interval between bytes of a command message is below 22
bits time.
1-3. Within 22 bits time after sending a command message, the receiving status is
posted.
1-4. Provide 44 bits time or more vacant status between the end of response
message reception and beginning for next command message sending (same
as in 1-1).
1-5. For ensuring the safety, make a confirmation of the response message and
make an arrangement so as to provide 3 or more retries in case of no response,
error occurrence, etc.
Note: The above definition is for most unfavorable value. For ensuring the safety,
it's recommended the program of the master to work with safety factors of
2 to 3. Concretely, it is advised to arrange the program for 9600 bps with
10ms or more for vacant status (1-1), and within 1ms for byte interval (1-2)
and changeover from sending to receiving (1-3).
2. Description
(1). Detection of the message frame Since the communication system uses the
2-write RS-485 interface, there may be 2 statuses on a line below.
(a) Vacant status (no data on line)
(b) Communication status (data is existing) Instruments connected on the line
are initially at a receiving status and monitoring the line. When 22 bits time
or more vacant status has appeared on the line, the end of preceding frame
is assumed and, within following 22 bits time, a receiving status is posted.
When data appears on the line, instruments receive it while 22 bits time or

Version 4.0
- 10 -
more vacant status is detected again, and the end of that frame is assumed.
Data, which appeared on the line from the first 44ms time or more vacant
status to the next 44 bits time or more vacant status is fetched as one frame.
1-1. 44 bits time or more vacant status precedes the command message
sending.
1-2. Interval between bytes of 1 command message is smaller than 22 bits time.
(2). Response of this instrument
After a frame detection (22 bits time or more vacant status), this instrument
carries out-processing with that frame as a command message. If the command
message is destined to the own station, a response message is returned. Its
processing time is 1 to 10ms (depends on contents of command message). After
sending a command message, therefore, the master station must observe the
following.
1-3. Receiving status is posted within 22 bits time after sending a command
message.

Version 4.0
- 11 -
6. DETAILS OF MESSAGE
6.1 Read-out of Word Data [Function Code: 03]
Read the contents of holding registers (0000~ 007D) in the slave. Broadcast is not
possible.
1. Message composition
Command message composition
Address Function Starting Address Word Number* CRC-16
01~FF 03 0xxx 0001~007E Low-order
byte
High-order
byte
1 byte 1 byte 2 byte 2 bytes 2 bytes
*Maximum word number = 7E
Response message composition
Address Function Byte Number * Word Data CRC-16
01 ~ FF 03 02~FC Low-order
byte
High-order
byte
1 byte 1 byte 1 bytes N bytes 2 bytes
*Byte number = Word number × 2
2. Message transmission (example)
The following show an example of reading the Set point Value (1000) from address
No.1 controller.
Command message composition
Address Function Starting Address Word Number CRC-16
01 03 0000 0001 840A
Response message composition
Address Function Byte Number Word Data CRC-16
01 03 02 03E8 B8FA

Version 4.0
- 12 -
6.2 Read-out of Read-Only Word Data [Function Code: 04]
Read the contents of input registers (1000~1002) in the slave. Broadcast is not
possible.
1. Message composition
Command message composition
Address Function Starting Address Word Number CRC-16
01~FF 04 1xxx 0001~007E Low-order
byte
High-order
byte
1 byte 1 byte 2 bytes 2 bytes 2 bytes
Response message composition
Address Function Byte Number Word Data CRC-16
01 ~ FF 04 02~FC Low-order
byte
High-order
byte
1 byte 1 byte 1 byte N bytes 2 bytes
2. Message transmission (example)
The following show an example of reading the Process Value (27) from address No.1
controller.
Command message composition
Address Function Starting Address Word Number CRC-16
01 04 1000 0001 350A
Response message composition
Address Function Byte Number Word Data CRC-16
01 04 02 001B F93B

Version 4.0
- 13 -
6.3 Write-in of Word Data (1 word) [Function Code: 06]
1. Message composition
Command message composition
Address Function Starting Address Word Data CRC-16
1 ~ FF 06 0xxx 0xxx Low-order
byte
High-order
byte
1 byte 1 byte 2 bytes 2 bytes 2 bytes
Response message composition
Address Function Starting Address Word Data CRC-16
1 ~ FF 06 0xxx 0xxx Low-order
byte
High-order
byte
1 byte 1 byte 2 bytes 2 bytes 2 bytes
2. Message transmission (example)
The following show an example of writing the Set point Value to address No.1
controller.
Command message composition
Address Function Starting Address Word Data CRC-16
01 06 0000 01F4 89DD
Response message composition
Address Function Starting Address Word Data CRC-16
01 06 0000 01F4 89DD

Version 4.0
- 14 -
7. ADDRESS MAP AND DATA FORMAT
7.1 Data Format
1. Transmission data format
The MODBUS protocol used in this instrument is RTU (Remote Terminal Unit)
mode.
Transmitted data is “numeric value" and not “ASCII code".
2. Internal calculation value and engineering unit
There are 3 different kinds of set value in the MV-D94 controllers.
Normal value:
The data value is transfer into Hexadecimal regardless of decimal. For example:
1000 ℃ will be transfered to 03E8(hex), However, such as output percentage
and Pb (proportional band), 100.0 % will be transfered to 03E8(hex).
Index code:
Some parameters value are set by index code. For example, to change the unit
to ℃ via communication. The data value would be 0017(hex).
Code English Code English Code English Code English
00 J 0F ENG 1E 9.6K 2D 1101
01 K 10 0000 1F 19.2K 2E 1110
02 T 11 000.0 20 0000 2F 1111
03 E 12 00.00 21 0001 30 HI
04 B 13 0.000 22 0010 31 LO
05 R 14 REV 23 0011 32 DIF.H
06 S 15 DIR 24 0100 33 DIF.L
07 N 16 NONE 25 0101 34 BD.HI
08 C 17 STDY 26 0110 35 BD.LO
09 D-PT 18 LATH 27 0111 36 T.ON
0A J-PT 19 ST.LA 28 1000 37 T.OFF
0B LINE 1A HH.MM 29 1001 38 NONE
0C ℃ 1B MM.SS 2A 1010 39 LO
0D ℉ 1C 2.4K 2B 1011 3A HI
0E ENG 1D 4.8K 2C 1100 3B HI.LO

Version 4.0
- 15 -
7.2 Data Address Map
Word data (read-out/write-in) : Function code [03, 06]
Data
Address
PM
Designer Parameter Range Unit
0000 40001 SV HiLt~LoLt ℃/℉
0001 40002 SPOF -1000~1000 ℃/℉
0002 40003 PVOF -1000~1000 ℃/℉
0003 40004 A1SP -1000~1000 ℃/℉
0004 40005 A2SP -1000~1000 ℃/℉
0005 40006 A3SP -1000~1000 ℃/℉
0006 40007 PB 0.0~300.0 %
0007 40008 TD 900 Sec
0008 40009 CT 0~100 Sec
0009 40010 HYST 0~2000 ℃/℉
000A 40011 A1HY 0~2000 ℃/℉
000B 40012 A2HY 0~2000 ℃/℉
000C 40013 A3HY 0~2000 ℃/℉
000D 40014 LOCK 0000~1111
000E 40015 TYPE J/K/B/R/S/T/E/N/C/DPT/JPT/LINE
(English code)
000F 40016 UNIT ℃ / ℉ / ENG (English code)
0010 40017 DP 0000/000.0/00.00/0.000 (English code)
0011 40018 ACT REV / DIR (English code)
0012 40019 LOLT -1999~9999 ℃/℉
0013 40020 HILT -1999~9999 ℃/℉
0014 40021 FILT 0.0~-100.0
0015 40022 A1FU None/Hi/Lo/dif.H/dif.L/bd.Hi/bd.Lo/T.S
NL (English code)
0016 40023 A1MD None/Stdy/Lath/St.La/T.End
(English code)
0017 40024 A2FU None/Hi/Lo/dif.H/dif.L/bd.Hi/bd.Lo/T.S
NL (English code)

Version 4.0
- 16 -
0018 40025 A2MD None/Stdy/Lath/St.La/T.End
(English code)
0019 40026 A3FU None/Hi/Lo/dif.H/dif.L/bd.Hi/bd.Lo/T.S
NL (English code)
001A 40027 A3MD None/Stdy/Lath/St.La/T.End
(English code)
001B 40028 ADDR 0~255 0
001C 40029 BAND
001D 40030 CH01 0~2000
001E 40031 CL01 0~2000
001F 40032 RTSH 0~3000
0020 40033 RTSL 0~3000
0021 40034 MR 0.0~100.0 %
Word data (read-out only) : Function code [04]
Data
Address
PM
Designer Parameter Contents Unit
1000 34097 PV Process value
PM Designer Driver : Modicon Corp. / Modicon 984 Device Slave (RTU).

Version 4.0
- 17 -
8. TROUBLESHOOTING
8.1 Troubleshooting
If the communication is unavailable, check the following items.
□ Whether all devices related to communication are turned on.
□ Whether connections are correct.
□ Whether the number of connected instruments and connection distance are as
specified.
□ Whether communication conditions coincide between the master station (host
computer) and slave station (MV-D94).
□ Transmission speed : □ 2400 bps □ 4800 bps □ 9600 bps □ 19200 bps
□ Address :01 ~ FF (master and slave station must be match)
□ Whether send/receive signal timing conforms to Section 5.4 in the manual.
□ Whether more than one instrument connected on the same transmission line share
the same address.
This manual suits for next models
1
Table of contents
Other Gigarise Controllers manuals
Popular Controllers manuals by other brands

HORA
HORA M135 operating instructions

Schluter Systems
Schluter Systems DH E RT2/BW instructions
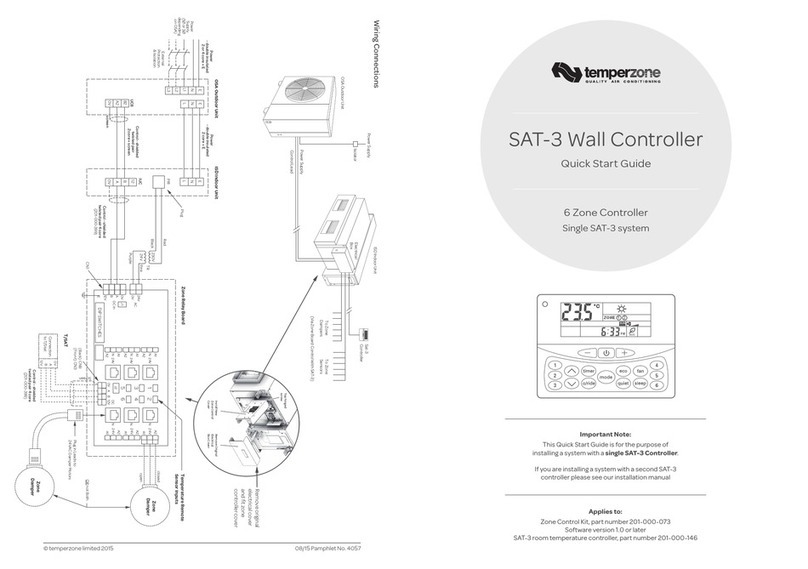
TemperZone
TemperZone SAT-3 quick start guide
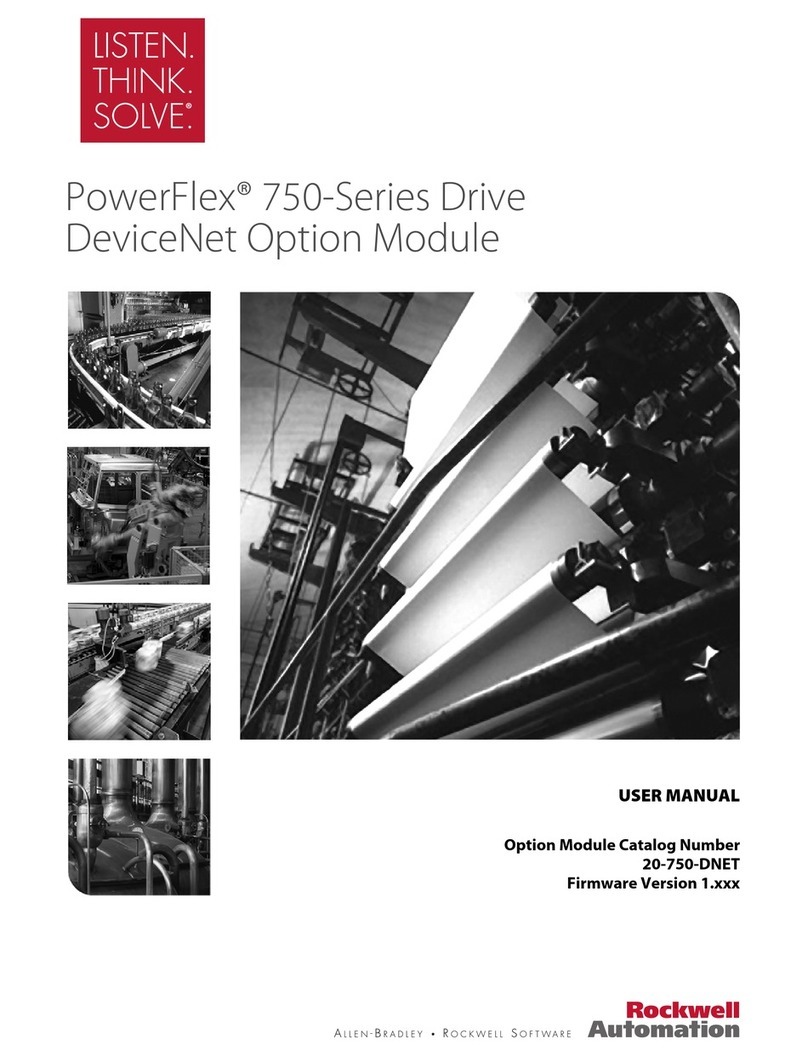
Rockwell Automation
Rockwell Automation PowerFlex 750-Series user manual
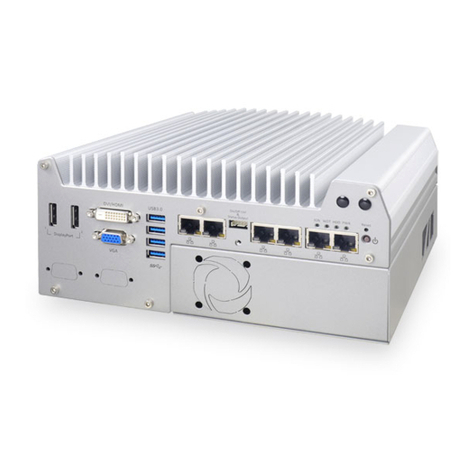
Neousys Technology
Neousys Technology Nuvo-5026E user manual
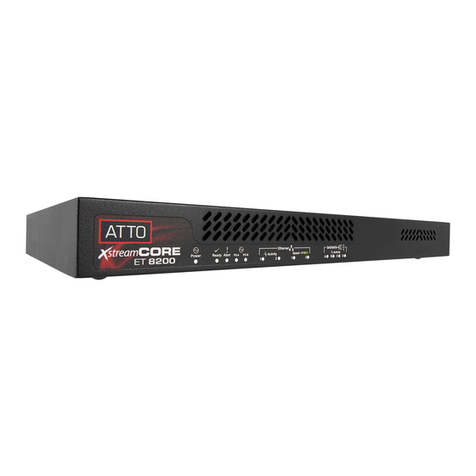
ATTO Technology
ATTO Technology XstreamCORE ET 8200 Installation and operation manual