GKD 1S Series User manual

SLEW LIMITER
M1000008 V1.4 - 11/2021
COPYRIGHT NOTICE
Intended audience: This document contains sensitive
information. It may not be shared with other parties without
the express written permission of GKD Technologies Ltd.
INSTALLATION MANUAL

M1000008 V1.4 - 11/2021
www.gkdtechnologies.com 2
CONTENTS
Page
1 INTRODUCTION 4
1.1 Overview 4
1.2 Display mounting 4
2 SLEW MODULE MOUNTING 5
2.1 Motion cut solenoids 5
3 PROXIMITY SWITCHES (TOOTH COUNTING) 6
3.1 Proximity Switch Installation - clearance 6
3.2 Tooth Count Proximity Switch Spacing 7
3.3 Reset proximity switch 7
4 SYSTEM LAYOUT 8
5 SLEW MODULE CONNECTION TABLE 9
6 SLEW MODULE CONNECTIONS 10
6.1 +V and 0V Supply to slew module 10
6.2 Motion cut solenoid valve connections 10
6.3 Proximity sensor connections 10
7 TESTING THE INSTALLATION 11
8 CHECKING THE TOOTH COUNT SEQUENCE 12
9 CALIBRATION 13
10 GUIDE TO KEY SWITCH / LED MODES 14

www.gkdtechnologies.com M1000008 V1.4 - 11/2021
3

M1000008 V1.4 - 11/2021
www.gkdtechnologies.com 4
1 INTRODUCTION
This manual contains the installation instructions for the Series 1-S slew limiting system.
Installation should only be carried out by competent and trained sta as this product is a
safety product.
During installation it is assumed that industry standards will be observed and all cabling will
be protected against damage either from the movement of the machine or from collisions
that may occur during normal operations ( trees & branches, etc.).
All welding or bare metalwork should be treated to ensure that rust does not form.
1.1 Overview
Series 1-S is a stand alone slew limiter intended for use on hydraulic excavators and similar
machines where an upper structure rotates relative to the base structure, and where slew
limits are required.
Series 1-S monitors the slew position of the machine by means of counting of the teeth on
the slew ring, and limits the slew movement of the machine to between two slew points
which are set by the machine operator.
Pre-emptive stop algorithms will monitor the speed of approach to the limit and will
progressively apply the motion cut earlier the faster the speed of approach, ensuring the
machine stops before the limit is breached.
The Series 1-S system consists of an in cab display mounted at the operator station and
external slew module.
Communication between the slew module and the display is by means of a 4 connection
CAN cable with 12mm screw connectors at each end.
The slew module has two 12 way Deutsch connectors for connection to +V and 0V, three
proximity switches (slew ring tooth counting and reset), and two motion cut outputs for
connection to solenoid valves to motion cut the slew left and slew right controls.
1.2 Display mounting
The in cab display should be mounted at the operator station in direct line of sight of the
operator and should be positioned so the machine operator can easily reach the device.
A RAM type swivel mount is provided to enable the device to be orientated towards the
operator. Mount the bracket to a firm surface in the cab, bearing in mind the loads likely to
be imposed on the mount by vibration and movement.
Ensure that no machine controls are obscured, and that windows, doors and access panels
can be opened and closed without fouling the Series 1-S display..

www.gkdtechnologies.com M1000008 V1.4 - 11/2021
5
2 SLEW MODULE MOUNTING
The slew module should be mounted in a position where it is protected from direct rainfall
and jet washing etc, and where it is unlikely to be damaged mechanically. It is useful if the
LEDs within the module can be seen to assist in setup and fault finding. The slew module
may be mounted in any orientation. Ideally it should be fixed to a suitable panel using the
two mounting lugs and suitable 6mm bolts.
2.1 Motion cut solenoids
Two motion cut solenoid valves are typically used, to cut motion to the slew left and slew
right circuits. The motion cut valves are typically mounted in the pilot circuit between the
hydraulic controls of the machine and the main valve block, and should cut pilot pressure to
the valve block when not energized, and allow normal operation when energized.
The solenoid valves should be installed in the pilot control line to the slew left and slew right
hydraulic circuits, and should connect the control levers to the valve block when energized.
When not energized (motion cut) the supply from the control levers must be blocked and
the line to the high pressure valve block must be connected to tank to dump any residual
pressure, thus cutting motion.
Solenoid Energized (Motion Allowed)
Solenoid NOT Energized (Motion Cut)
From Control Lever
Pressure Dump to Tank
To Main Valve Block
From Control Lever
Pressure Dump to Tank
To Main Valve Block

M1000008 V1.4 - 11/2021
www.gkdtechnologies.com 6
3 PROXIMITY SWITCHES (TOOTH COUNTING)
Two proximity switches must be installed in such
a way as to count the movement of the upper
structure against the slew ring teeth. The teeth are
typically accessed through an inspection hatch,
and it is usually possible to mount the proximity
switches into the inspection plate so that they
are able to detect the slew ring teeth as they
pass beneath. It is possible that a custom bracket
may need to be fabricated to hold the proximity
switches in a position where the slew ring teeth
may be counted. Where no access to the slew ring
teeth is possible, an external toothed ring may be
fitted as a register.
It may also be possible to count the bolts holding
the slew assembly together, although this solution
generally provides a lower count resolution,
which is less desirable.
3.1 Proximity Switch Installation - clearance
The proximity switches must be installed so that
the clearance between the sensor head and the
target being detected is approximately 5mm. The
proximity switches have a maximum detection
distance of 8mm.
Clearance between
proximity switch
head and target
approx. 5mm
Min
spacing
20mm
between
teeth
Proximity
switch
position
When determining the position for
installation of the two tooth counting
sensors, ensure that there is at least
20mm of clear space between teeth
as they are seen by the proximity
switches. This clearance is important
because the proximity switch needs to
have a period between teeth where no
tooth is detected

www.gkdtechnologies.com M1000008 V1.4 - 11/2021
7
3.2 Tooth Count Proximity Switch Spacing
The tooth counting proximity switch spacing is important, as by the sequence of switches
detecting teeth, the Series 1-S is able to determine the direction of slew.
The proximity switches must be
mounted 90 degrees out of phase, or
in other words, the spacing between
the two switches should be 75% of
the full tooth spacing, as shown in the
diagram alongside.
The detection of teeth by the
switches can be monitored by looking
at the LEDs within the slew module
associated with Input 1 and Input
2. These LEDs can be seen through
the orange translucent cover of the
module.
When registered on the slew module LEDs (input 1 and input 2) as the machine slews, there
must be a period when both prox switch LEDs are OFF. One LED should come on, then the
second (both ON together) then first one o, then second one o (both OFF together). This
sequence is important, if necessary adjust the spacing between the two proximity switches
to achieve this sequence.
3.3 Reset proximity switch
The third proximity switch is a Reset switch. The reset switch should be mounted in such
a way as to be momentarily triggered by a suitable target as the machine passes over 0
degrees of slew (upper structure in line with the undercarriage over the front end)..
Prox switch
spacing =
3/4 of full
tooth spacing
Tooth spacing -
1 full tooth

M1000008 V1.4 - 11/2021
www.gkdtechnologies.com 8
4 SYSTEM LAYOUT
RED: = +V Ignition switched
BLACK = 0V (Chassis)
YELLOW = Not used
GREEN = Not used
BLUE = Not used
+V IN, 0V IN
Proximity Switches
Motion Cut Valve Outputs
(see separate connection table)
CAN bus lead between
display and module
Display Tooth Counting
Proximity Switches
Reset Proximity
Switche
Slew
Module
Slew Left
Motion Cut
Valve
Slew Right
Motion Cut
Valve

www.gkdtechnologies.com M1000008 V1.4 - 11/2021
9
5 SLEW MODULE CONNECTION TABLE
Grey Black Function
1 Not used
2 Not used
3 Not used
4Slew proximity switch 2 Slew tooth count proximity switch 2 input
5 Not used
6 Not used
7Slew Reference switch Slew reference proximity switch input
8 Not used
9 Not used
10 Slew proximity switch 1 Slew tooth count proximity switch 1 input
11 POS +24V supply OUT +V out for proximity switches
12 0V OUT 0V out for proximity switches
1 Not used
2 Not used
3Slew Motion Cut Left +V output to solenoid valve
4POS +24V supply IN Switched by ignition and protected by a 5A Fuse
5POS +24V supply OUT +V out for proximity switches
60V OUT 0V out for proximity switches
7 Not used
8 Not used
9POS +24V supply IN Switched by ignition and protected by a 5A Fuse
10 Slew Motion Cut Right +V output to solenoid valve
11 Travel Allow Output +V output. Cuts travel when slew limits are active
12 0V IN 0V input, connect to chassis (ground)
GREY BLACK

M1000008 V1.4 - 11/2021
www.gkdtechnologies.com 10
6 SLEW MODULE CONNECTIONS
6.1 +V and 0V Supply to slew module
The slew module internal electronics are powered through the 12mm CAN bus connector
from the display. The solenoid valves driven from the slew module derive their power from
the +V inputs into the slew module deutsch connectors (black connector, pins 4 and 9).
If the total current draw of the two solenoid valves is less than 5A it is not necessary to
connect both pins 4 and 9 to +V, only one (either one of the two) needs to be connected.
The external power supply to the module should be connected to an ignition switched
supply, and fused. A 5A fuse is recommended on a 24V machine, a 10A fuse will be required
for a 12V machine.
The black connector, pin 12 should be connected to 0V, a direct connection to the vehicle
chassis is recommended.
6.2 Motion cut solenoid valve connections
The two motion cut valves are connected to the Slew module as per the table on the
previous page. The slew module provides +V out to the solenoids when slew movement is
allowed, and cuts the +V output to each valve individually when motion cut is required.
The 0V connection to each motion cut solenoid should be directly to the vehicle chassis.
6.3 Proximity sensor connections
The cables from the proximity switches should have their insulation removed at the
connection end to expose the internal coloured wires.
For each switch the brown, blue and black wires are used, the white wire is not used and can
be cut back.
> BROWN = +V
> BLUE = 0V
> BLACK = SIGNAL
The BROWN wires from all three sensors should be combined and powered from an ignition
switched power source. This can be from the same power source as the +V input to the
module.
Alternatively, the proximity switches can be powered from GREY pin 11 and BLACK pin 5 on
the slew module deutsch connectors. Please note that the power source from the module
(grey 11 / black 5) is a low current power source, do not connect anything else to these pins.
The BLACK wires from the three proximity switches should be connected individually to the
appropriate inputs on the Slew module deutsch connectors, as per the connection table on
the previous page.
The BLUE wires from all three sensors should be combined and connected to an external
chassis ground, or alternatively to GREY pin 12 and BLACK pin 6 on the slew module
deutsch connectors.

www.gkdtechnologies.com M1000008 V1.4 - 11/2021
11
7 TESTING THE INSTALLATION
Once installation has been completed, turn the ignition on and check that the green “ON”
LED lights to signify power. The red “FAULT” LED will blink slowly (1 sec ON, 1 sec OFF) with
the key switch in the “No Limits” position, as the module has not yet learned the number of
teeth on the slew ring. Turning the key switch to “operational” or “Set Limits” should cause
the red Fault lamp to go out.
If the “FAULT” LED blinks very slowly (3 seconds ON, 3 seconds OF) with the key switch in
all positions, a CAN bus fault between the display and module is likely. Check the CAN bus
connections to the slew module.
Check that the green LED marked “EXT V+” is ON, this shows that the external +V supply
to the module through the deutsch connectors is working. The green LED marked “V In”
should also be ON, this LED shows that power is being received from the display through
the CAN bus lead.
+V input - CANbus - also
powers proximity switches
+V input for solenoid outputs
- derived from deutsch
connector +V inputs
Check also that the two LEDs corresponding with Out 1
(Output 1) and Out 2 (Output 2) are on - these will be on
when the solenoid valves for slew left and slew right motion
cut are powered.
Turn the key switch on the display to “NO LIMITS”.
If safe to do so, operate the machine slew to rotate the upper structure SLOWLY, and
observe the slew module LEDs associated with Inputs 1,2 and 3.
Inputs 1 and 2 should be flashing on and o regularly as teeth are counted by the proximity
switches mounted against the slew ring, and the sequence of the two LEDs should be LED1
ON - LED2 ON (both on together) - LED1 OFF (LED2 still on), LED2 o (both o together).
When the direction of slew is reversed, the sequence will reverse.
Slew the machine over 0 degrees, LED3 should light up momentarily as the reset switch is
triggered.

M1000008 V1.4 - 11/2021
www.gkdtechnologies.com 12
8 CHECKING THE TOOTH COUNT SEQUENCE
Identify the LEDs associated with input 1 and input 2. The LEDs can be identified from the
label on the module. The input 1 and 2 LEDs will light up when a slew tooth is detected by
the two tooth counting proximity switches. The LED associated with Input 3 will light up
over 0 degrees of slew when the slew reset proximity switch detects the target post over 0
degrees.
Slewing slowly at a constant speed, check the sequence of the two LEDs identified as
In1 and In2 as the teeth are counted. The sequence should be as follows:
LEDs for proximity switch inputs:
In1 / In2 / In3
Both LEDs OFF
LED 1 ON, LED 2 OFF
Both LEDs ON
LED 1 OFF, LED 2 ON
Both LEDs OFF
Note that the sequence will be reversed as the direction of slew reverses - in other words
LED2 will come on first, then LED1, then LED2 will go out, then LED1 will go out.
LED 1
LED 1
LED 1
LED 1
LED 1
LED 2
LED 2
LED 2
LED 2
LED 2

www.gkdtechnologies.com M1000008 V1.4 - 11/2021
13
9 CALIBRATION
The following procedure highlights the process required to teach the Slew Module the
number of teeth it will be counting on a slew ring or similar counting setup. It is assumed at
this point that there is no CAN Bus errors and the Series 1-S is indicating a state of No Slew
Data.
1) Switch the key-switch is in the “No Limits” position.
2) Position the turret so that the slew reset block is to one side of the slew reset sensor -
in other words, not over the reset position.
3) Press and hold both limit buttons together.
4) The left & right limit LED’s will alternate between yellow for a second and o for a
second.
5) Wait for 10 seconds unit the left and right limit LED’s stay on Yellow.
6) While still holding both limit buttons, switch the key-switch to the “Operational” then
“Set Limits” position.
7) Release the two limit buttons.
8) The left & right limit LED’s will alternate between red for 1/5 of a second and green for
1/5 of a second.
9) Slew the turret through the slew reset position and then continue to slew at a constant
speed for a further 2 complete revolutions.
10) If the Error LED comes on flashing at 1/5 of a second then the Learn mode has detected
a fault, return to step 1 and. Ensure the vehicle is rotated in the same direction without
stopping.
11) After the 2 full revolutions the left & right limit LED’s will come on Red only.
12) This completes teeth counting with the slew module.
Once the calibration procedure above has been completed, turn the key switch to the “SET
LIMITS” position, and set Left and Right slew limits by moving the machine slew to the
desired limit position and pressing the “SET LEFT” or “SET RIGHT” button as appropriate.
Turn the key switch to the “OPERATIONAL” position and slew towards each limit. The Series
1-S SlewGuard
system should cut the slew hydraulic function as the limit is approached, but allow the slew
to operate back to the “safe” zone between the limits. As the speed of approach to the limit
increases, the Series 1-S should cut the slew function progressively earlier to ensure that the
machine stops before the limit is reached, without overshooting the limit.
NOTE: Should the Series 1-S cut the slew very early and not allow the limit to be
approached, it is possible that the signals from the two tooth counting sensors need to be
reversed.

M1000008 V1.4 - 11/2021
www.gkdtechnologies.com 14
10 GUIDE TO KEY SWITCH / LED MODES
R = RED O = OFF
Y = Yellow (Red / Green together) S = Static colour only
G = Green T = Toggles between colours
Key Switch LEDs Comment
Fault (R) Left Limit Right Limit
All S Te s t Te s t
Along with the buzzer this is the standard start up test mode and will show
the fault LED for a short time while communications is established with the
Slew Module.
All 3 Sec/TO O O No detected Slew Module or the CAN Bus is in fault due to no connected
devices or a wiring/component issue.
No Limits 1 Sec/TO GS GS The Slew module is reporting there is no slew teeth data and can not operate
accordingly, Slew Cuts will be enabled.
Operational
/ Set Limits O 3 Sec/YTO 3 Sec/YTO The Slew module is reporting there is no slew teeth data and can not operate
accordingly, Slew Cuts will be disabled.
All 1/5 Sec/TO Ignore Ignore
The Slew module is reporting an error, retesting of limits is recommended.
To cancel the error condition, switch the keywitch to the “No Limits” position
then test for correct functionality of the system and limits. This could be
caused by miscalculation of the slew teeth, adjust the sensor positions or an
attempt to learn a slew teeth count and reversing direction before the end of
the learn process.
All O Ignore Ignore No detected faults, slew cuts will be dependent on mode set by the
keyswitch.
No Limits Ignore 1 Sec/YTO 1 Sec/YTO Learn slew teeth mode stage 1, both limits button should be pressed to cause
this.
No Limits Ignore YS YS Learn slew teeth mode stage 2, with both limit buttons held the keywitch can
be switched to “Set Limits”. Slew Cuts will be enabled.
Operational Ignore YS YS Learn slew teeth mode stage 2, with both limit buttons held the keywitch can
be switched to “Set Limits”. Slew Cuts will be disabled.
Operational Ignore 1 Sec/RS 1 Sec/RS Learn slew teeth mode stage 2, when one or both limit buttons is released,
cancels the learn teeth mode.
Set Limits Ignore YS YS Learn slew teeth mode stage 2, when both limit buttons are release the learn
slew teeth will change to mode 3. Slew Cuts will be enabled.
Set Limits O 1/5 Sec/RTG 1/5 Sec/RTG
Learn slew teeth mode stage 3, Slew Cuts will be enabled, 2 complete
revolutions in the same direction are required, passing the reset detector a
total of 3 times to complete the mode.
Set Limits 1/5 Sec/TO 1/5 Sec/RTG 1/5 Sec/RTG
Learn slew teeth mode stage 3 detected an error, the direction of travel was
reversed during one of the two revolutions, switch the keywitch to the “No
Limits” position and repeat. If repeated errors occur check the detector mark/
space ratio.
No Limits O GS GS Slew System may be used without limits, there is a known tooth and no errors
are being detected. Slew Cuts will be enabled.
Operational O O O There is a known tooth count but no limits have been set yet, the slew cuts
are kept disabled.
Set Limits O RS RS
If either of the Limit LED’s shows in red then there has never been a set limit
in that direction, move vehicle to a suitable position and set one limit with its
button then repeat for the other limit. Slew Cuts are enabled.
Set Limits O YS GS or RS Yellow LED lights while limit button is held, on release new limit set.
Set Limits O GS or RS YS Yellow LED lights while limit button is held, on release new limit set.
Set Limits O GS GS Both limits are set suitable for operational use. Slew Cuts are enabled.
Operational O GS GS Operating within accepted Slew Limits, Slew Cuts are active by Slew Module.
Operational O 1/5 Sec/RTO GS Slew Limit reached at the left indicated position, Slew Left Cut disabled.
Operational O GS 1/5 Sec/RTO Slew Limit reached at the right indicated position, Slew Right Cut disabled.
Operational O 1/5 Sec/RTO 1/5 Sec/RTO Slew Limits set to closely together, Slew Left Cut and Slew Right Cut
disabled.

www.gkdtechnologies.com M1000008 V1.4 - 11/2021
15
INSTALLER NOTES

©GKD Technologies 11-2021
GKD Technologies reserve the
right to change these instructions in
line with the policy of continuous improvement.
DISCLAIMER
Incorrect installation of any part and or incomplete calibration
will aect the correct operation of the Series 1-S.
If in doubt contact GKD Technologies.
17 Cobham Road, Ferndown Industrial Estate, Wimborne, Dorset, UK. BH21 7PE
+44 (0)1202 861 961 sales@gkdtec.com www.gkdtechnologies.com
Other manuals for 1S Series
1
Table of contents
Popular Control Unit manuals by other brands

Campbell
Campbell CELL200-Series quick guide
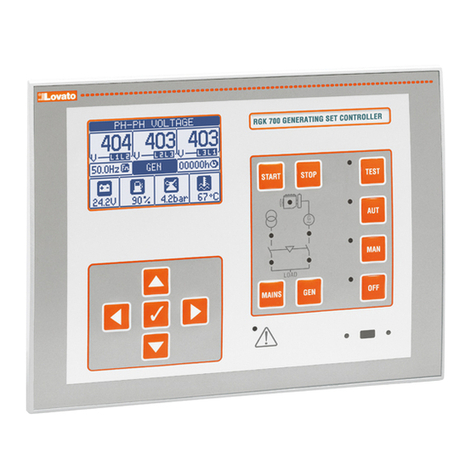
LOVATO ELECTRIC
LOVATO ELECTRIC RGK800 installation manual
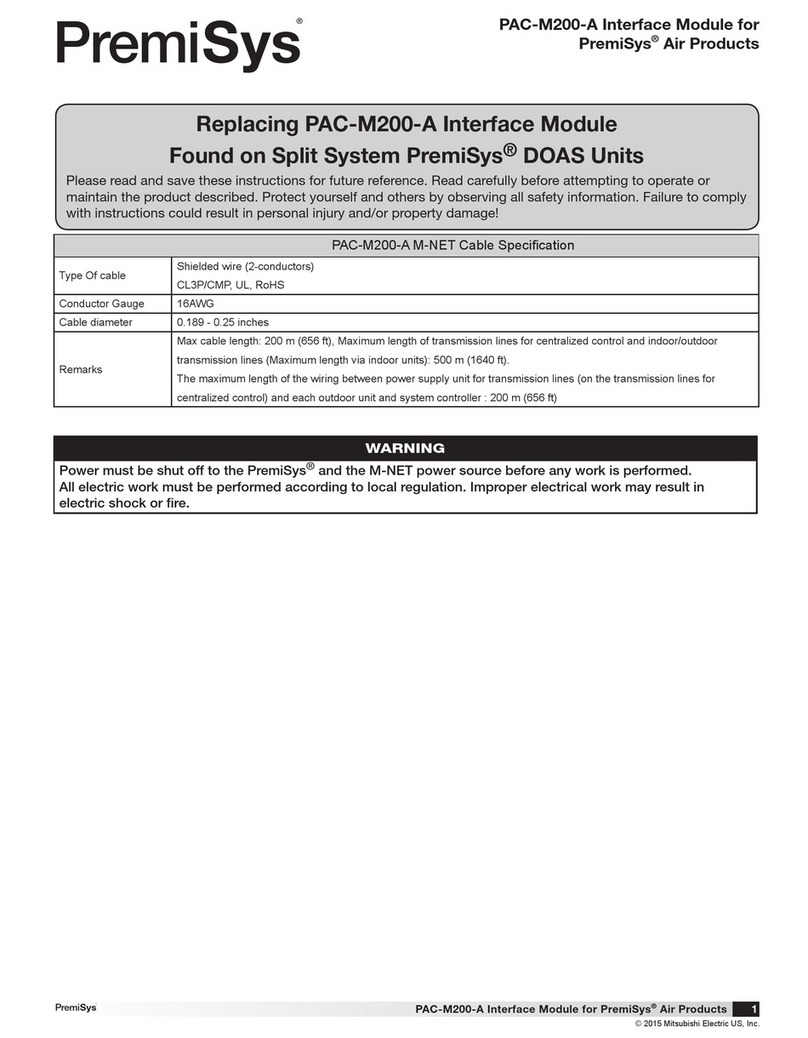
Premisys
Premisys PAC-M200-A manual
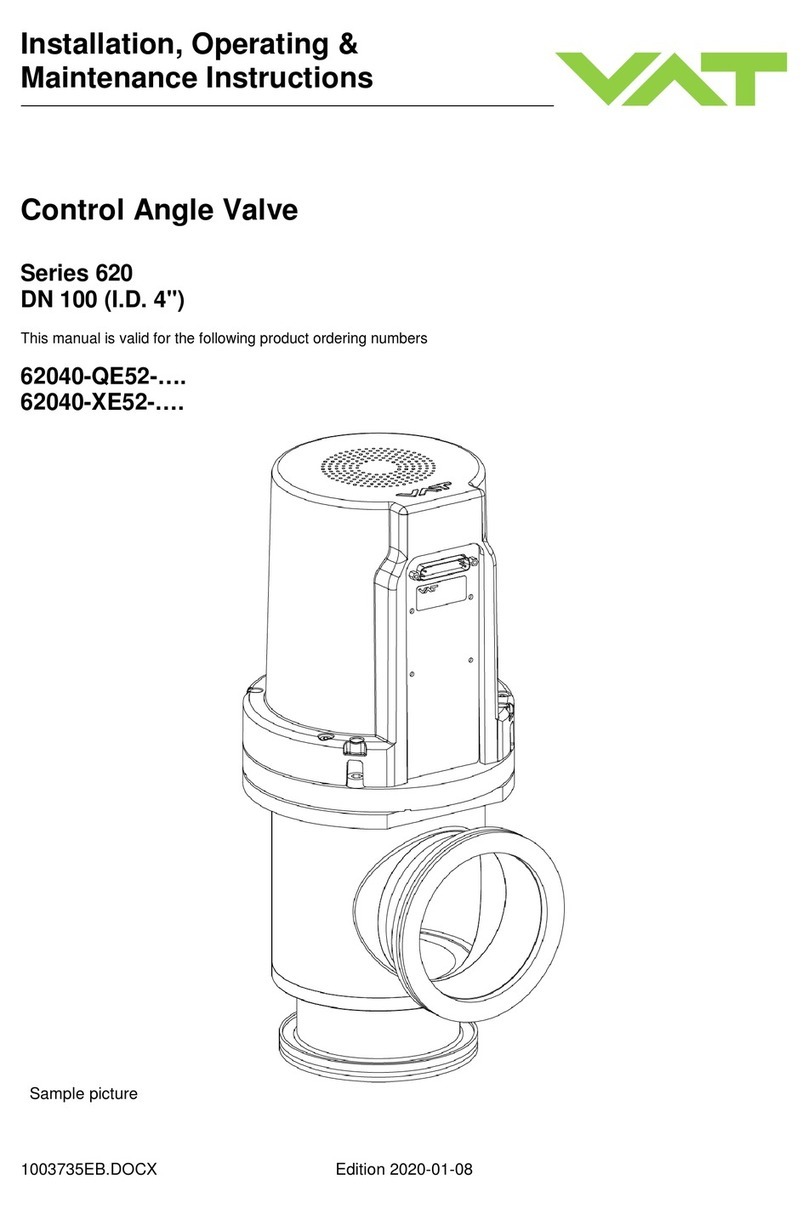
VAT
VAT 620 Series Installation, operating, & maintenance instructions
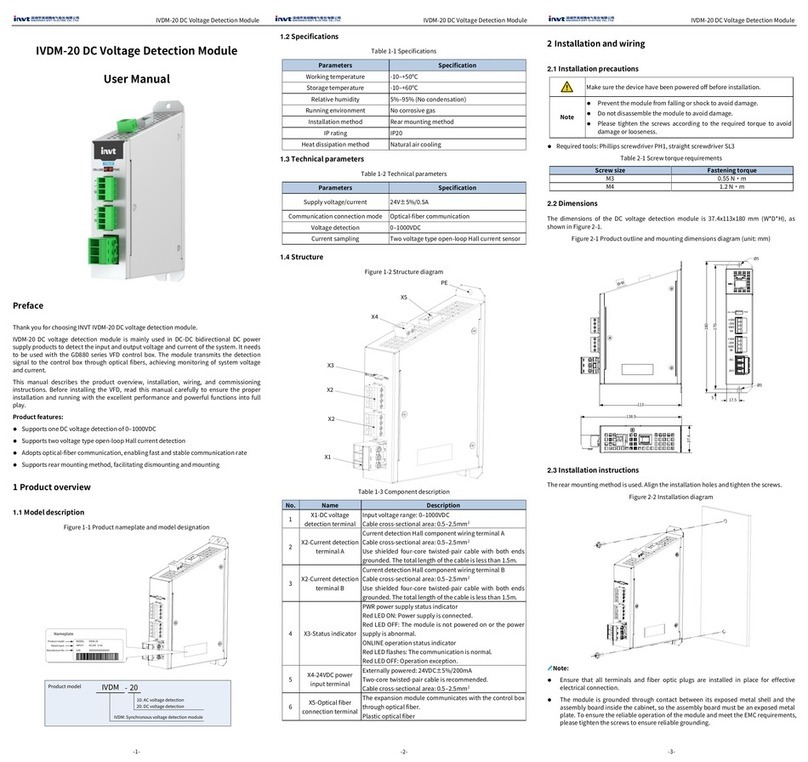
INVT
INVT IVDM-20 user manual
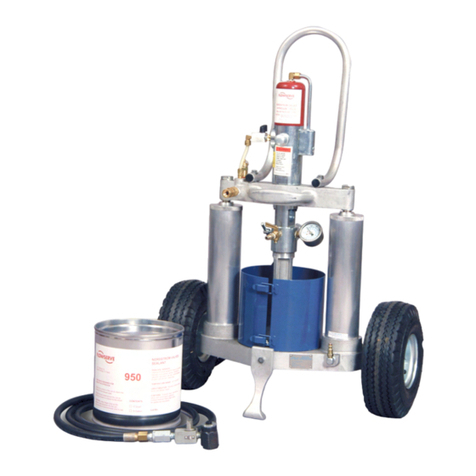
Flowserve
Flowserve NORDSTROM HYPREGUN PLUS 5Q Assembly, Operation and Maintenance Manual